XJTAG XJAccelerator User manual

[email protected]XJTAG-XACC-Guide-24A-05.4 www.xjtag.com
XJTAG®
XJAccelerator Hardware
User Guide
Version 2

page 2 of 10XJTAG-XACC-Guide-24A-05.4 www.xjtag.com
www.xjtag.com XJAccelerator Hardware .User Guide
Table of Contents
SECT ON PAGE
1. Introduction ..........................................................................................................3
2. XJAccelerator Block Diagram ...............................................................................4
3. Powering the XJAccelerator..................................................................................4
4. XJLink2 Connector Pinout (P1) .............................................................................5
5. I/O Connectors.....................................................................................................5
6. I/O Pinout .............................................................................................................6
7. I/O Voltage Domains.............................................................................................7
8. I/O Electrical Characteristics .................................................................................7
9. Setting the I/O into a Tristate Condition.................................................................8
10. Routing TDO ......................................................................................................8
11. Passthrough ode .............................................................................................9
12. Programming FPGA Images .............................................................................10
13. Protection Boards.............................................................................................10
Figure 1 – XJAccelerator Board................................................................................................................3
Figure 2 – XJAccelerator Block Diagram ..................................................................................................4
Figure 3 – DC Power Input.......................................................................................................................4
Figure 4 – XJLink Connector....................................................................................................................5
Figure 5 – I/O Connector .........................................................................................................................5
Figure 6 – Rotary switches and connectors..............................................................................................7
Figure 7 – TDO Routing ...........................................................................................................................8
Figure 8 – Locating the Links to Configure Passthrough ode.................................................................9
Figure 9 – XJAccelerator with 3 protection boards .................................................................................10
Table 1 – XJLink2 Input Connector Pinout................................................................................................5
Table 2 – P2 I/O Pinout ............................................................................................................................6
Table 3 – P3 I/O Pinout ............................................................................................................................6
Table 4 – P4 I/O Pinout ............................................................................................................................6
Table 5 – I/O Logic Thresholds (LVC OS standards) ...............................................................................7
Table 6 – FPGA Drive Strength Options....................................................................................................8
Table 7 – Placing the I/O into a Tristate ode...........................................................................................8
Table 8 – Selecting the Source of TDO.....................................................................................................8
Table 9 – Hardware Configuration to Route Directly to the XJLink2 ..........................................................9
Table 10 – XJAccelerator Active Protector ratings ..................................................................................10

1. Introduction
The XJAccelerator is a configurable FPGA board with three I/O connectors that can run on different voltage
domains. The board’s main uses are:
• high-speed programming of flash memories when a PCB doesn’t have
a suitable FPGA for accelerated programming.
• high-speed programming of multiple devices concurrently, including when
they are different device types with different interfaces.
• to act as a JTAG ultiplexer (scan bridge).
• to act as a mini I/O expander.
Figure 1 – XJAccelerator Board
The board’s interfaces are:
XJLink2 connector•
5-12 V DC power inputs (use either)•
P2 I/O connector to UUT•
P3 I/O connector to UUT•
P4 I/O connector to UUT•
When used for accelerated programming, the data can be streamed to the FPGA using JTAG, or retrieved
from a micro SD card. The I/O connectors provide the interfaces to the devices to be programmed.
When used as a JTAG multiplexer, the UUT’s JTAG chains are connected to the XJAccelerator’s I/O
connectors, and the TDO Switch should be set so that the XJLink2 receives JTAG data from the FPGA’s
logic instead of its JTAG port (see Routing TDO on page 8).
page 3 of 10XJTAG-XACC-Guide-24A-05.4 www.xjtag.com
www.xjtag.com XJAccelerator Hardware .User Guide
P4 I/O onne tor to UUT
Rotary swit hes to set I/O voltages
P2 I/O onne tor to UUT
5-12 V DC power inputs
“FPGA Configured” LED
Power header for
voltage prote tion board
P3 I/O onne tor to UUT
XJLink2 onne tor

page 4 of 10
2. XJAccelerator Block Diagram
Figure 2 – XJAccelerator Block Diagram
3. Powering the XJAccelerator
The board can be powered from either a DC input socket or screw down terminals. In either case, the
input voltage must be between 5 and 12 V DC.
Connector type: 2.1 mm central pin, 5.5 mm outer diameter, 9.5 mm barrel length.
Suitable mating plug: Farnell 224923, Digi-Key EP501A-ND, RS 487-858.
Figure 3 – DC Power Input
*500 mA is suitable for most setups. However, the current requirement may exceed this depending on output loading and how the
FPGA is configured.
XJTAG-XACC-Guide-24A-05.4 www.xjtag.com
www.xjtag.com XJAccelerator Hardware .User Guide
JTAG
port
TMS
TCK
TDI
TDO
SPI flash
SWITCH
µSD card
PIO
TRISTATE
I/O connectors
Internal
gates
XJLink2 connector
FPGA
FPGA configured
I/O P2
I/O P3
I/O P4
+5 – 12 V ± 10%
500 – 900 mA*
1

4. XJLink2 Connector Pinout (P1)
The XJLink2 connects to the board using P1. The JTAG interface and this connector’s PIO operate at
3.3 V, which cannot be changed. The pinout is shown in Table 1.
Ta le 1 – XJLink2 Input Connector Pinout
Connector type: keyed 20-pin 0.1” pitch.
Suitable mating connector: Farnell 1200505, Digi-Key 1195-7010-ND, RS 426-3766.
Figure 4 – XJLink Connector
5. I/O Connectors
The board has three I/O connectors, P2 – P4, that connect to PIO on the FPGA.
Pins 10 and 20 are connected to ground.
Connector type: keyed 20-pin 0.1” pitch.
Suitable mating connector: Farnell 1200505, Digi-Key 1195-7010-ND, RS 426-3766.
Figure 5 – I/O Connector
page 5 of 10XJTAG-XACC-Guide-24A-05.4 www.xjtag.com
www.xjtag.com XJAccelerator Hardware .User Guide
1
2
1
2
Pin Signal Function
1 TR STATE High: puts FPGA /O into tristate mode. (PCB has a 4k7 pulldown)
2 SW TCH Low: TDO comes from the FPGA’s JTAG port only
High: TDO comes from the FPGA’s internal logic
3 TDO From either the FPGA’s JTAG port or the FPGA’s internal logic depending on state of signal SW TCH
4 P O 4 P O connected to FPGA bank 2 pin 66
5 TD JTAG TD signal from the XJLink2
6 P O 6 P O connected to FPGA bank 2 pin 62
7 TMS JTAG TMS signal from the XJLink2
8 P O 8 P O connected to FPGA bank 2 pin 61
9 TCK JTAG TCK signal from the XJLink2
10 GND
11 P O 11 P O connected to FPGA bank 2 pin 59
12 P O 12 P O connected to FPGA bank 2 pin 58
13 P O 13 P O connected to FPGA bank 2 pin 57
14 P O 14 P O connected to FPGA bank 2 pin 56
15 P O 15 P O connected to FPGA bank 2 pin 55
16 P O 16 P O connected to FPGA bank 2 pin 51
17 P O 17 P O connected to FPGA bank 2 pin 50
18 P O 18 P O connected to FPGA bank 2 pin 48
19 P O 19 P O connected to FPGA bank 2 pin 47
20 GND

6. I/O Pinout
Ta le 2 – P2 I/O Pinout
Ta le 3 – P3 I/O Pinout
Ta le 4 – P4 I/O Pinout
page 6 of 10XJTAG-XACC-Guide-24A-05.4 www.xjtag.com
www.xjtag.com XJAccelerator Hardware .User Guide
Connector Pin
FPGA Pin
( ank 0) Connector Pin
FPGA Pin
( ank 0)
1 143 2 142
3 141 4 111
5 138 6 117
7 134 8 118
9 127 10 GND
11 119 12 123
13 124 14 126
15 132 16 133
17 137 18 139
19 140 20 GND
Connector Pin
FPGA Pin
( ank 1) Connector Pin
FPGA Pin
( ank 1)
1 104 2 102
3 101 4 100
5 99 6 98
7 97 8 94
9 93 10 GND
11 88 12 92
13 85 14 87
15 83 16 84
17 81 18 82
19 80 20 GND
Connector Pin
FPGA Pin
( ank 3) Connector Pin
FPGA Pin
( ank 3)
1 35 2 34
3 33 4 32
5 30 6 29
7 26 8 24
9 23 10 GND
11 12 12 14
13 10 14 11
15 6 16 7
17 2 18 5
19 1 20 GND

page 7 of 10XJTAG-XACC-Guide-24A-05.4 www.xjtag.com
7. I/O Voltage Domains
The three I/O connectors can have their voltages configured independently to match the I/O standard
required. These voltages provided by the hardware are adjusted by changing the rotary switches near the
connectors, as shown in Figure 6. The switches and connectors all have labels (e.g. P4 and P4 voltage)
to allow you to easily identify which switch corresponds to which connector. These switches can be
adjusted with a flathead screwdriver so that the arrow on the groove points to the required voltage.
The factory default setting for every bank is 3V3.
Figure 6 – Rotary switches and connectors
8. I/O Electrical Characteristics
The characteristics of the signals on the three I/O connectors will be determined by how the FPGA has
been configured. However, it is normal to use the LVC OS standards for the I/O, in which case the
logic thresholds will be as listed in Table 7 (voltages stated are valid across all possible drive strengths).
Their values are dependent on the voltage domain that has been selected for that bank of I/O.
Ta le 5 – I/O Logic Thresholds (LVCMOS standards)
The maximum current capability of the pins is dependent on the drive strength set when the FPGA was
configured. Possible options are listed in Table 8; they are dependent on the I/O interface voltage and the
connector being used.
www.xjtag.com XJAccelerator Hardware .User Guide
Voltage Domain VIL (min) VIL (max) VIH (min) VIH (max) VOL (max) VOH (min)
3V3 -0.5 0.80 2.0 4.1 0.40 2.90
2V5 -0.5 0.70 1.7 4.1 0.40 2.10
1V8 -0.5 0.38 0.8 4.1 0.45 1.35
1V5 -0.5 0.38 0.8 4.1 0.38 1.13

page 8 of 10
Ta le 6 – FPGA Drive Strength Options
9. Setting the I/O into a Tristate Condition
The FPGA’s I/O can be placed into a tristate condition using the TRISTATE signal on the XJLink2
connector (pin 1) provided the FPGA has been configured and its image has been designed to support
this feature. The board has a 4k7 pulldown on the TRISTATE control input.
Ta le 7 – Placing the I/O into a Tristate Mode
10. Routing TDO
The TDO signal can be returned to the XJLink2 either directly from the FPGA’s JTAG port (e.g. when using
the XJAccelerator for programming) or from the FPGA’s internal logic (e.g. when using it as a JTAG
multiplexer) as shown in Figure 7.
Figure 7 – TDO Routing
The TDO source is determined by the state of the SWITCH signal on the XJLink2 connector as described
in Table 10.
Ta le 8 – Selecting the Source of TDO
XJTAG-XACC-Guide-24A-05.4 www.xjtag.com
www.xjtag.com XJAccelerator Hardware .User Guide
Voltage Domain P2 (mA) P3 (mA) P4 (mA)
3V3 2, 4, 6, 8, 12, 16, 24 2, 4, 6, 8, 12, 16, 24 2, 4, 6, 8, 12, 16, 24
2V5 2, 4, 6, 8, 12, 16 2, 4, 6, 8, 12, 16, 24 2, 4, 6, 8, 12, 16, 24
1V8 2, 4, 6, 8, 12, 16 2, 4, 6, 8, 12, 16, 24 2, 4, 6, 8, 12, 16, 24
1V5 2, 4, 6, 8 2, 4, 6, 8, 12, 16 2, 4, 6, 8, 12, 16
TRISTATE (pin 1) I/O Pins’ condition
Low Normal use
High (+3V3) Tristate mode
JTAG port
XJLink2 connector
TDI
TDO
TDO
FPGA
I/O connector
Internal
logic
105 67
SWITCH (pin 2) TDO source
Low FPGA’s JTAG port
High (+3V3) FPGA’s internal logic

page 9 of 10XJTAG-XACC-Guide-24A-05.4 www.xjtag.com
11. Passthrough ode
The XJAccelerator can be configured in hardware so that some of the signals to/from the XJLink2 are routed
directly to connectors P2 and P3. This can be used, for example, to utilise the XJLink2’s frequency or
analogue voltage measuring capabilities. Table 11 lists the locations where 0603 0 Ωlinks need to be placed.
Note: voltages applied in passthrough mode must not exceed the limits set by the FPGA because the
signals are still applied to the FPGA in this mode (see the Voltage Domains section on page 7).
To avoid the FPGA attempting to drive nets that are eing used as passthrough, a suita le
FPGA image should e used, or Disa le Values or Constant pins should e set in the project.
Ta le 9 – Hardware Configuration to Route Directly to the XJLink2
The links are located on the underside of the board at the positions shown in Figure 8.
Figure 8 – Locating the Links to Configure Passthrough Mode
www.xjtag.com XJAccelerator Hardware .User Guide
XJLink Pin P2 Pin P2 Link P3 Pin P3 Link P4 Pin P4 Link
VCC 1 R66 1 R52 1 R53
4 4 R65 4 R51 4 R78
6 6 R64 6 R50 6 R77
8 8 R63 8 R49 8 R76
11 11 R62 11 R48 11 R75
12 12 R61 12 R47 12 R74
13 13 R60 13 R46 13 R73
14 14 R59 14 R45 14 R72
15 15 R58 15 R44 15 R71
16 16 R57 16 R43 16 R70
17 17 R56 17 R42 17 R69
18 18 R55 18 R41 18 R68
19 19 R54 19 R40 19 R67
P2 links (R54-R65)
P4 links (R67-R78)
P3 links (R40-R51)

page 10 of 10
12. Programming FPGA Images
The XJAccelerator uses a Xilinx®Spartan®-6 SLX9 FPGA in a 144-pin footprint. It can be programmed
over the JTAG interface or from the on-board SPI flash memory.
The board’s LED indicates that the FPGA has been configured. When the image is stored in the on-board
flash memory, the LED should illuminate shortly after power-up; if the board is unprogrammed, the LED
will remain off.
It is advisable to write the associated XJEase tests so that it automatically commences programming if an
unconfigured FPGA is detected (NB: when used as a mini I/O board, no programming is needed). When
written in this way, it is helpful if the code implements the following sequence:
1. Confirm the XJAccelerator FPGA is accessible via JTAG.
2. Check if the FPGA has been configured from the correct image.
3. If the FPGA is unprogrammed or does not contain the expected image, automatically program
the on-board flash with the required image and then force the FPGA to reload from it.
XJTAG can supply the XJAccelerator together with an XJDeveloper board file and the associated XJEase
files to provide this functionality.
13. Protection Boards
XJTAG also provides optional XJAccelerator Active Protectors which can be placed inline between the
XJAccelerator and the system under test to provide additional protection to the XJAccelerator board from
potentially damaging voltages. These boards are intended to be sacrificial and to fail without passing
out-of-range voltages on to the XJAccelerator.
To use XJAccelerator Active Protectors, simply
connect them to the 20-pin headers on the
XJAccelerator board and plug in the power cable
to the adjacent pin header as shown in Figure 9.
It’s now ready for you to connect the normal
ribbon cable from the test system to the connector
on the other side of the Active Protector board.
Ta le 10 – XJAccelerator Active Protector ratings
XJTAG-XACC-Guide-24A-05.4 www.xjtag.com
www.xjtag.com XJAccelerator Hardware .User Guide
Protection Board ratings
DC input voltage -0.5 V to 5.5 V
DC input current ±10 mA
DC output current
Pins 1, 11: +50 mA
-50 mA, +50 mA, including
power and ground pins
Temperature range +5 °C to +45 °C (operational)
Humidity < 95% (non-condensing)
Figure 9 – XJAccelerator with 3 protection oards
Table of contents
Popular Control Unit manuals by other brands
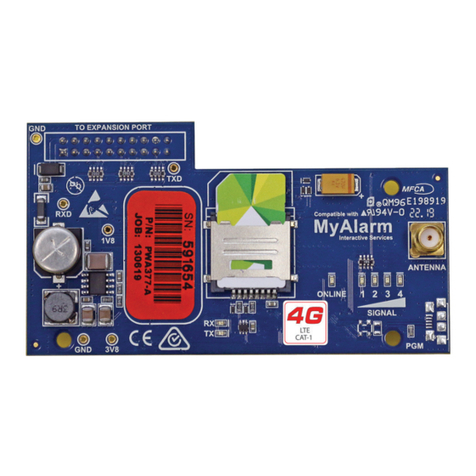
Bosch
Bosch CM746B Installer's reference guide

National Instruments
National Instruments FIeldPoint FP-AO-200 operating instructions

Motorline professional
Motorline professional MC70 EVO User& installer's manual
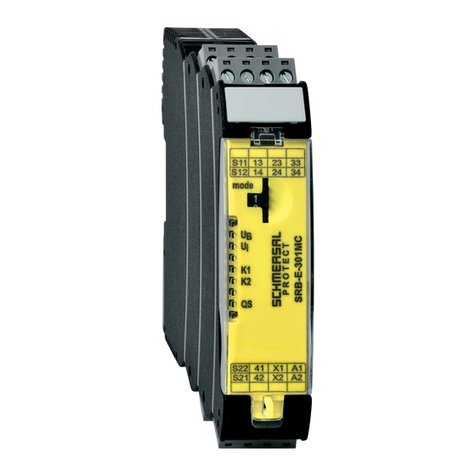
schmersal
schmersal SRB-E-301MC operating instructions

Midcontinent
Midcontinent MD302-3 Installation manual and operating instructions
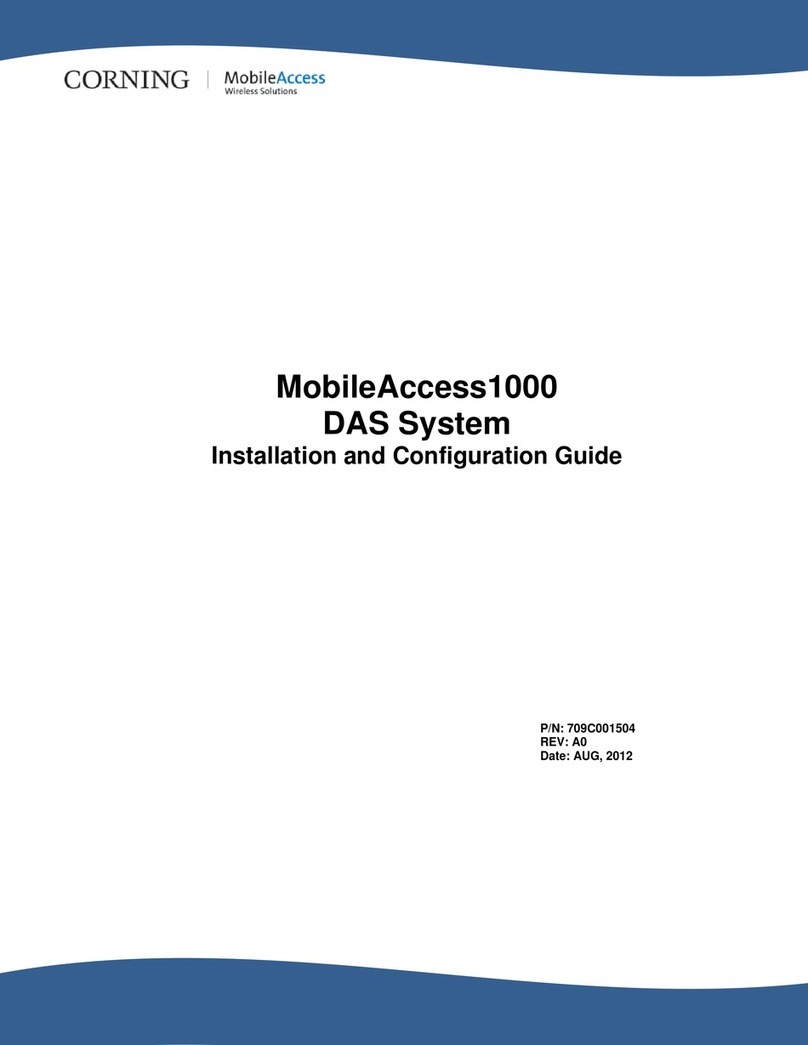
CORNING
CORNING MobileAccess1000 Installation and configuration guide