XMODUS XM8200S Series User manual

XM8200S Designer’s Guide
XM8200S-E00-100 xmodus swiss GmbH Seite 1 / 22
WLAN Socket Modem
XM8200S-5V, XM8200S-3V
Designer’s Guide
Version 100
Released 29. March 2011

XM8200S Designer’s Guide
XM8200S-E00-100 xmodus swiss GmbH Seite 2 / 22
Information provided by xmodus swiss is believed to be accurate and reliable. However, no
responsibility is assumed by xmodus swiss for its use, nor any infringement of patents or
other rights of third parties which may result from its use. No license is granted by implication
or otherwise under any patent rights of xmodus other than for circuitry embodied in xmodus
products. Xmodus swiss reserves the right to change circuitry at any time without notice. This
document is subject to change without notice. Please read carefully the safety precautions
for a terminal based on the XM8200S Socket Modem.
Product names or services listed in this publication are for identification purposes only, and
may be trademarks or registered trademarks of their respective companies. All other marks
mentioned herein are the property of their respective owners.
© 2011 xmodus swiss GmbH
Printed in Switzerland
All Rights Reserved

XM8200S Designer’s Guide
XM8200S-E00-100 xmodus swiss GmbH Seite 3 / 22
Table of Contents
1. INTRODUCTION..........................................................................................................5
1.1 Models Description .......................................................................................................5
1.2 Summary ......................................................................................................................5
1.3 Typical Applications......................................................................................................6
1.4 Product Specifications ..................................................................................................7
2. TECHNICAL OVERVIEW ............................................................................................8
2.1 Block Diagram of Wi-Fi Module ....................................................................................8
2.2 Supported Interfaces ....................................................................................................8
3. HARDWARE INTERFACE...........................................................................................9
3.1 Interface Signals...........................................................................................................9
3.2 Signal Description.........................................................................................................9
3.3.1 Signal Description...............................................................................................11
3.4 Antenna Interface (RF) ...............................................................................................14
3.4.1 RF Connector: ....................................................................................................14
3.4.2 Antenna Installation ............................................................................................15
3.4.3 User Operation ...................................................................................................15
3.5 RESET Signal.............................................................................................................16
3.5.1 Recommended Reset Circuit..............................................................................16
4. POWER SUPPLY.......................................................................................................17
4.1 Power Loss shut down ...............................................................................................17
5. DESIGN GUIDELINES...............................................................................................18
5.1 Electromagnetic Interference (EMI) Considerations...................................................18
5.1.1 Grounding ...........................................................................................................19
5.1.2 RF Antenna.........................................................................................................19
5.2 Manufacturing Considerations....................................................................................19
6. MODULE DIMENSIONS ............................................................................................20
7. REGULATORY APPROVALS...................................................................................21
7.1 Considerations for Regulatory Approvals ...................................................................21
7.1.1 Regulatory Requirements ...................................................................................21
7.1.2 Regulatory Statement .........................................................................................21
7.2 Safety Precautions .....................................................................................................22
7.2.1 User Operation ...................................................................................................22
7.2.2 Antenna Installation ............................................................................................22
7.2.3 Antenna care and replacement...........................................................................22
7.2.4 Electronic devices...............................................................................................22

XM8200S Designer’s Guide
XM8200S-E00-100 xmodus swiss GmbH Seite 4 / 22
List of Tables & Figures
TABLE 3-1. SERIAL TTL SIGNALS ......................................................................... 10
TABLE 3-2. SIGNAL DESCRIPTIONS ..................................................................... 11
TABLE 3-3. SIGNAL DESCRIPTIONS (CONT'D) ........................................................
TABLE 3-3. SIGNAL DESCRIPTIONS (CONT'D) ........................................................
TABLE 3-4. DIGITAL ELECTRICAL CHARACTERISTICS ...................................... 13
TABLE 3-5. ABSOLUTE MAXIMUM RATINGS........................................................ 13
Figure 2-1. Interface Block Diagram ........................................................................... 8
Figure 3-1. Serial Pinout........................................................................................... 10
Figure 6-2. Mechanical drawings.............................................................................. 20

XM8200S Designer’s Guide
XM8200S-E00-100 xmodus swiss GmbH Seite 5 / 22
1
1.
.
I
IN
NT
TR
RO
OD
DU
UC
CT
TI
IO
ON
N
1.1 Models Description
Models Modulation Interface Connectors Interfaces / Power
XM8200S-5V 802.11b and 802.11g DIL-64 Header (RM2)
U.FL RF Connector
RS232 TTL Level
5 VDC Power
XM8000S-3V 802.11b and 802.11g DIL-64 Header (RM2)
U.FL RF Connector
RS232 TTL Level
3.3 VDC Power
1.2 Summary
The Xmodus XM8200S Socket Modem provides the OEM with a complete WLAN 802.11b and
802.11g modem in a compact socket-mountable module. The compact size and high level of
integration of the Socket Modem minimizes real estate and cost for motherboard and box
modem applications. Its low power consumption makes it ideal for portable applications such
as pocket modems and for a wide variety of embedded control applications. The pin
compatibility between the full ranges of all the xmodus socket modems allows upgrading and
production configurability without hardware changes.
This designer's guide describes the modem hardware. AT commands and S registers are
defined in the AT Command Reference Manual.
The XM8200S is a secure embedded Wireless LAN bridge that easily connects embedded
devices to 802.11b/g Wireless LANs. It includes the iChip™ CO2144 IP Communication
Controller™ chip and Marvell 88W8686 WiFi chipset. This module makes adding WiFi
connectivity to embedded devices a breeze. It does not require any kind of WiFi driver
development on the host CPU, and its multiple interface (UART and USB) minimize the need
to redesign the host device hardware. The high-level AT+i™ API eliminates the need to add
WiFi drivers, security and networking protocols and tasks to the host application. The firmware
supports the SSL3/TLS1 protocol for secure sockets, HTTPS and FTPS, WEP, WPA/WPA2
(PSK and Enterprise) WiFi encryption. The firmware and configuration parameters are stored
in on-board flash memory. The module is power-efficient: the core operates at 1.2V, while I/Os
operate at 3.3V. Power Save mode further reduces power consumption.

XM8200S Designer’s Guide
XM8200S-E00-100 xmodus swiss GmbH Seite 6 / 22
1.3 Typical Applications
Adding WiFi to serial embedded devices
Replacing LAN cable using WiFi
Adding SSL security to M2M solutions
The XM8200S supports several operation modes:
-SerialNetTM Serial to WiFi Bridge - allowing transparent bridging of Serial over WiFi,
using the 3Mbps fast UART. This is a true plug-and-play mode that eliminates any
changes to the host application.
-PPP modem emulation – allowing existing (e.g. modem) designs currently using PPP
to connect transparently over WiFi
-Full Internet Controller mode – allowing simple MCU to use the rich protocol and
application capabilities to perform complex Internet operations such as E-mail, FTP,
SSL, embedded web server and others. It also acts as a firewall, providing a security
gap between the application and the network.

XM8200S Designer’s Guide
XM8200S-E00-100 xmodus swiss GmbH Seite 7 / 22
1.4 Product Specifications
Hardware Description:
Size: 64.5 x 26.5 x 10.5 mm
Core CPU: 32-bit RISC ARM7TDMI, low-
leakage, 0.13 micron, at 48MHz
Operating Voltage: +3.3V/5.0V
Operating Humidity: 90% maximum (non-
condensing)
Operating Temperature Range:
-20°c to
+75°c (-4° to 167°F)
Power Consumption:
Transmit –250mA@16dbm,
235mA@12dbm (typical)
Receive – 190mA (typical)
Power Save mode – 8mA
RF Connector: U.FL of Hirose
Connector: Pin Header (2mm pitch)
Host Interface: Serial and USB device.
RoHS-compliant; lead-free
Wireless Specifications:
Standards supported: IEEE 802.11b/g
Frequency: Europe – 2.412-2.472GHz USA
– 2.412-2.462GHz
Channels: Europe – 13 channels USA – 11
channels.
Performance Specifications:
Host Data Rates:
-UART: Up to 3Mbps
-Serial Data Format (AT+i mode):
Asynchronous character; binary; 8
data bits; no parity; 1 stop bit
Serial Data Format (SerialNET mode):
Asynchronous character; binary; 7 or 8 data
bits; odd, even, or no parity; 1 stop bit
Flow Control: Hardware (-RTS, -CTS) and
software flow control.
Internet Protocols:
ARP, ICMP, IP, UDP, TCP, DHCP, DNS,
NTP, SMTP, POP3, MIME, HTTP, FTP and
TELNET
Security protocols: SSL3/TLS1, HTTPS,
FTPS, RSA, AES-128/256, 3DES, RC-4,
SHA-1, MD-5, WEP, WPA/WPA2 (PSK and
Enterprise)
Protocols accelerated in hardware: AES,
3DES and SHA
Application Program Interface:
AT+i protocol for Internet Controller mode
SerialNET mode for transparent serial data-
to-Internet bridging
LAN-WiFi transparent bridging
PPP operation mode for Modem-WiFi
conversion
Warranty:
One year
Certifications:
• Radio & EMC:
-USA
FCC Modular Approval, FCC ID: XM5-
SM2144N1 o CFR Title 47 FCC Part 15,
Subpart B and C
-Canada
Industry Canada Module Approval IC:
8516A-SM2144N2 o Industry Canada
ICES-003, RSS-Gen, RSS-210
-EU
EN 300 328 (R&TTE Directive 1999/5/EC)
o EN 301 489 (EMC Directive
2004/108/EC)
• Safety:
UL 60950
CAN/CSA-C22.2 No. 60950
EN 60950, Low Voltage Directive
(2006/95/EC)
Installation Requirements:
The XM8200S must be installed within a full-
enclosure device that is safety certified.

XM8200S Designer’s Guide
XM8200S-E00-100 xmodus swiss GmbH Seite 8 / 22
2
2.
.
T
TE
EC
CH
HN
NI
IC
CA
AL
L
O
OV
VE
ER
RV
VI
IE
EW
W
2.1 Block Diagram of Wi-Fi Module
2.2 Supported Interfaces
The major hardware signal interfaces of the xmodus Series Socket Modem are illustrated
in Figure 1-1.
Figure 2-1. Interface Block Diagram
The RS232 Interface is connected via eight pins to the module.
The Indicators are connected via one pin to the module.
The power supply is connected via one pin to the module.
The USB Interface is connected via 2 pins to the module.
Socket
WLAN
Modem
Module
Serial / USB
Interface
Antenna
Interface
5
3
Leds 1
1

XM8200S Designer’s Guide
XM8200S-E00-100 xmodus swiss GmbH Seite 9 / 22
3
3.
.
H
HA
AR
RD
DW
WA
AR
RE
E
I
IN
NT
TE
ER
RF
FA
AC
CE
E
3.1 Interface Signals
The Socket Modem pin assignments with DTE serial TTL interface, SIM Card and Analog
Interface are shown in Figure 3-1 and are listed in Table 3-1.
3.2 Signal Description
The Socket Modem interface signals are described in Table 3-3.
The digital electrical characteristics are listed in Table 3-4.
The analog electrical characteristics are listed in Table 3-5.

XM8200S Designer’s Guide
XM8200S-E00-100 xmodus swiss GmbH Seite 10 / 22
Figure 3-1. SERIAL PINOUT
Table 3-1. Serial TTL Signals
PIN NAME I/O TYPE PIN NAME I/O TYPE
1 NC Not connected 33 #RTS Input
2 NC Not connected 34 #RXD Output
3 No pin 35 #TXD Input
4 No pin 36 #RI Output
5 No pin 37 #DSR Output
6 No pin 38 #CTS Output
7 No pin 39 #DCD Output
8 No pin 40 #DTR Input
9 No pin 41 GND GND digital
10 No pin 42 USB (-) Bidir.
11 No pin 43 USB (+) Bidir.
12 No pin 44 USB-VCC Input
13 No pin 45 No pin
14 No pin 46 No pin
15 No pin 47 No pin
16 No pin 48 No pin
17 No pin 49 No pin
18 No pin 50 No pin
19 No pin 51 No pin
20 No pin 52 No pin
21 No pin 53 No pin
22 No pin 54 No pin
23 No pin 55 No pin
24 RESET Input 56 No pin
25 MSEL Input 57 No pin
26 GND GND Digital 58 No pin
27 NC Not connected 59 No pin
28 NC Not connected 60 No pin
29 NET-LED Output 61 VCC VDC POWER
30 NC Not connected 62 NC
31 NC Not connected 63 GND GROUND
32 NC Not connected 64 NC
SERIAL TTL
INTERFACE
USB
INTERFACE
POWER
SUPPLY
LED / RESET
INTERFACE
Notes: Pins 3-23 and 45-60 are not installed.
DTR# 40
NC
27
NC
1
CTS# 38
USB (+) 43
RTS# 33
DSR# 37
NC 62
TXD# 35
NC 64
NC
32
NC
30
USB (-) 42
NC
28
NC
2
GND 41
DCD# 39
GND
26
RXD# 34
VCC 61
RESET
24
RI# 36
GND 63
MSEL
25
USB-VCC 44
NC
31
NETLED
29
To
p
View

XM8200S Designer’s Guide
XM8200S-E00-100 xmodus swiss GmbH Seite 11 / 22
3.3.1 Signal Description
Table 3-3-1. Signal Descriptions
Label Pin I/O I/O Type Signal Name/Description
VCC 61 I PWR
+5 VDC. A standard 5V +/- 5% - 0.5 A power supply is
strictly required to supply this module (5V Versions).
Chapter 4 should be considered.
+3.-3 VDC. A standard 3.3V – 0.5 A power supply is
strictly required to supply this module (3V Versions).
Chapter 4 should be considered.
GND
26
41
63
I GND
Digital Ground Connect to Digital Ground on the
interface circuit.
RESET 24 I IC
Module Reset. The active low RESET input resets the
modules logic and returns the module to the original factory
default values and to "stored values" in NVRAM. RESET is
connected to a built-in reset circuit on the Socket Modem.
Reset must be held low for at least 5mS to activate the reset
logic. The modem is ready to use 200mS after the reset.
Connect the reset line to ground through a 1nF capacitor to
ensure good ESD immunity and to comply with ESD tests
according to EN 61000-4-2.
This signal is active low (on the module is a pull-up
resistor of 47K).
MSEL 25 I IC MSEL Signal. Not used currently. Leave open.
NET-
LED 29 O OC
NET-LED Signal: The Wi-Fi output signal indicates when
the module is transmitting over the WLAN network. This
signal follows the WLAN transmit bursts. This signal is set
high during transmission burst, and set low when no
transmission is in progress.
LED driver lines are open-drain inverter-driven (74HCT05)
lines.

XM8200S Designer’s Guide
XM8200S-E00-100 xmodus swiss GmbH Seite 12 / 22
Table 3-3-2. Signal Descriptions
Label Pin I/O I/O Type Signal Name/Description
The Serial interface signals are TTL-level signals.
TXD 35 I IB
Transmitted Data (EIA BA/ITU-T CT103). The DTE uses
the TXD line to send data to the module for transmission
over the WLAN network or to transmit commands to the
modem.
RXD 34 O OA
Received Data (EIA BB/ITU-T CT104). The module uses
the RXD line to send data received from the WLAN
network to the DTE and to send module responses to the
DTE. During command mode, RXD data represents the
module responses to the DTE.
CTS 38 O OA
Clear To Send (EIA CB/ITU-T CT106). CTS output ON
(low) indicate that the modem is ready to accept data from
the DTE. In normal mode, RTS/CTS flow control is
selected.
DCD 39 O OA Data Carrier Detected (EIA CF/ITU-T CT109). During
normal operation, DCD is always active (low).
RI 36 O OA Ring Indicator (EIA CE/ITU-T CT125). RI output is always
inactive (high).
DTR 40 I IB Data Terminal Ready (EIA CD/ITU-T CT108). The DTR
input is turned ON (low) by the DTE when the DTE is ready
to transmit or receive data.
RTS 33 I IB
Request To Send (EIA CA/ITU-T CT105). RTS input ON
(low) indicates that the DTE is ready to send data to the
modem. In the command state, the modem ignores RTS.
The modem ignores RTS unless RTS/CTS flow control is
selected.
DSR 37 O OA Data Set Ready (EIA CC/ITU-T CT107). DSR is always
set active (low).

XM8200S Designer’s Guide
XM8200S-E00-100 xmodus swiss GmbH Seite 13 / 22
Table 3-4. Digital Electrical Characteristics
Parameter
Symbol
Min.
Typ.
Max.
Units
Test Conditions
Input High Voltage
pins 33,35,40
VIH
2
-
5.5
Vdc
Input Low Voltage
pins 33,35,40
VIL
0
-
0.8
Vdc
Output High Voltage
pins 34,36,37,38
VOH
3.3 – 0.4
3.3 – 0.2
3.3
3.3
-
-
Vdc
ILOAD= - 2 mA
ILOAD = -0 mA
Output Low Voltage
pins 34,36,37,38
VOL
-
-
0
0
0.4
0.2
Vdc
ILOAD = 2 mA
ILOAD = 0 mA
max Reset Low Input
Voltage, pin 24
VIL
-
-
0.8
internally pulled up
to VCC by 47kΩ
Table 3-5. Absolute Maximum Ratings
Parameter Symbol Min. Typ. Max. Units Test Condition
Supply Voltage
VDD
-0.3
-
+6.0
Vdc
Input Voltage
VIN
-0.5
-
+7.0
Vdc
Nominal Supply Voltage
5V Version
3V Version
VDD
4.75
3.20
-
-
5.25
3.45
Vdc
Static Discharge Voltage
@ 25°C
VESD
-
+/- 2500
V
Operating Temperature Range
Operational
Functional
TA
-20
-20
-
-
+75
+75
°C
Storage Temperature Range
TSTG
-40
-
+85
°C
Supply Current
Average WiFi active Tx
Average Idle
Sleep mode
ID
190
125
9
250
150
12
mA
@ 3.3V
Notes:
Test Conditions: VCC = 5VDC +/- 5%, TA = 25°C,

XM8200S Designer’s Guide
XM8200S-E00-100 xmodus swiss GmbH Seite 14 / 22
3.4 Antenna Interface (RF)
The XM8200S antenna connector is the RF interface to the WLAN network. The antenna
interface consist of an U.FL type connector, which has impedance matched to 50Ωat the
relevant WLAN 802.11 b/g frequencies. The antenna or antenna application must be installed
properly to achieve best performance.
Table 3-15 gives the antenna interface specifications.
Antenna Interface Specifications
WLAN 802.11b/g band 2400 MHz - 2483.5 MHz
Gain 0 dBi
Impedance 50Ω
VSWR Less than: 2.5:1
It is the Integrator's responsibility to design the antenna or antenna assembly used with the
XM8200S. This will highly affect the RF performance of the XM8200S (signal quality, current
consumption etc.). The following guidelines should be followed:
Make sure that the antenna or antenna assembly matches the Antenna Interface
Specifications.
Use low loss RF cable and connectors keeping cable runs to a minimum.
In order to prevent mutual interference between the GSM and the WLAN antennas in
stacked configuration, a minimum distance that provides a 30dB isolation is required.
To achieve the required 30dB isolation between the antennas, a distance of about
7cm from each other should be kept when using a monopole isotropic antenna with
0dBi and appropriate return loss.
3.4.1 RF Connector:
The Antenna-jack of the WLAN module is an U.FL type. It has a snap-in connection. For the
antenna cable RG178, RG1.37 o.a. are recommended.
RF Connector
Module Connector Mating Cable
Standard U.FL
Hirose:
U.FL-R-SMT(01
Standard U.FL cables
Hirose:
U.FL-LP-SMA

XM8200S Designer’s Guide
XM8200S-E00-100 xmodus swiss GmbH Seite 15 / 22
3.4.2 Antenna Installation
A minimum separation distance of 20 cm needs to be maintained between the antenna and
all persons.
The transmitter effective radiated power must be less than 3.0 Watts ERP (4.9 Watts or
36.9 dBm EIRP). This requires that the combination of antenna gain and feed line loss
does not exceed 16 dBi.
3.4.3 User Operation
Do not operate your unit when a person is within 8 inches (20 centimeters) of the antenna. A
person or object within 8 inches (20 centimeters) of the antenna could impair call quality and
may cause the phone to operate at a higher power level than necessary.
IMPORTANT: The unit must be installed in a manner that provides a minimum separation
distance of 20 cm or more between the antenna and persons to satisfy FCC RF exposure
requirements for mobile transmitting devices.
IMPORTANT: To comply with the FCC RF exposure limits and satisfy the categorical
exclusion requirements for mobile transmitters, the following requirements must be met:

XM8200S Designer’s Guide
XM8200S-E00-100 xmodus swiss GmbH Seite 16 / 22
3.5 RESET Signal
3.5.1 Recommended Reset Circuit
This signal is used to force a reset procedure by providing low level during at least 100uS.
This signal has to be considered as an emergency reset only. A reset procedure is already
driven by an internal hardware during the power-up sequence.
If no external reset is necessary this input can be left open. If used (emergency reset), it has to
be driven by an open collector or an open drain.
Switch Reset Reset (Pin 24) Reset Status
1 0 Active
0 1 Inactive
Additional comments on RESET:
The reset process is activated either by the external Reset signal OR by an internal signal
(coming from the internal RESET generator). This automatic reset is activated at power-up.
The module remains in reset mode as long as the reset signal is held low. As soon as the
reset is complete, the command line interface answers “OK” to the application.
SWITCH
RESET: PIN 24
NPN

XM8200S Designer’s Guide
XM8200S-E00-100 xmodus swiss GmbH Seite 17 / 22
4
4.
.
P
PO
OW
WE
ER
R
S
SU
UP
PP
PL
LY
Y
The XM8200S power supply must be a single external DC voltage source of 3.3V or 5V
(depending on model). It is recommended that the user application or usage scenario avoid
power cuts, in particular during the initialization process of the unit after power on. Please
follow the Designers Guide in respect to the Power supply levels in order to operate the unit
within specifications.
Table 4-1: Power Supply Signals:
Pin Nr. Signal name Description
26, 41 GND Main ground connection for module.
61 VCC
VIN = 3.3 V or 5 V
IRMS = 190 mA during receive
IMAX = 280 mA during transmit bursts
4.1 Power Loss shut down
A low power shut down occurs when the WLAN module senses the external power supply is
below the minimal operating limit. The module will respond by powering down automatically
without notice.
This form of power-down is not recommended for regular use since the unexpected power
loss may result in loss of data and unstable power-on sequences.

XM8200S Designer’s Guide
XM8200S-E00-100 xmodus swiss GmbH Seite 18 / 22
5
5.
.
D
DE
ES
SI
IG
GN
N
G
GU
UI
ID
DE
EL
LI
IN
NE
ES
S
Good engineering practices must be adhered to when designing a printed circuit board (PCB)
containing the WLAN Socket Modem module. Suppression of noise is essential to the proper
operation and performance of the modem itself and for surrounding equipment.
Two aspects of noise in an OEM board design containing the WLAN Socket Modem module
must be considered: on-board/off-board generated noise that can affect analog signal levels
and analog-to-digital conversion (ADC)/digital-to-analog conversion (DAC), and on-board
generated noise that can radiate off-board. Both on-board and off-board generated noise that
is coupled on-board can affect interfacing signal levels and quality, especially in low level
analog signals. Of particular concern is noise in frequency ranges affecting modem
performance.
On-board generated electromagnetic interference (EMI) noise that can be radiated or
conducted off-board is a separate, but equally important, concern. This noise can affect the
operation of surrounding equipment. Most local governing agencies have stringent certification
requirements that must be met for use in specific environments.
Proper PC board layout (component placement, signal routing, trace thickness and geometry,
etc.), component selection (composition, value, and tolerance), interface connections, and
shielding are required for the board design to achieve desired modem performance and to
attain EMI certification.
5.1 Electromagnetic Interference (EMI) Considerations
The EMC tests have to be performed as soon as possible on the application to
detect any possible problem. When designing, special attention should be paid to:
Possible spurious emission radiated by the application to the RF receiver in the receiver
band.
Metallic case or plastic casing with conductive paint are recommended
The following guidelines are offered to specifically help minimize EMI generation. Some of
these guidelines are the same as, or similar to, the general guidelines but are mentioned again
to reinforce their importance. In order to minimize the contribution of the Socket Modem-based
design to EMI, the designer must understand the major sources of EMI and how to reduce
them to acceptable levels.
1. Keep traces carrying high frequency signals as short as possible.
2. Provide a good ground plane or grid. In some cases, a multilayer board may be required
with full layers for ground and power distribution.
3. Decouple power from ground with decoupling capacitors as close to the Socket Modem
module power pins as possible.
4. Eliminate ground loops, which are unexpected current return paths to the power source
and ground.
5. Locate high frequency circuits in a separate area to minimize capacitive coupling to other
circuits. Distribute high frequency signals continuously on a single trace rather than several
traces radiating from one point.
6. Locate cables and connectors so as to avoid coupling from high frequency circuits.
7. If a multilayer board design is used, make no cuts in the ground or power planes and be
sure the ground plane covers all traces.
8. Minimize the number of through-hole connections on traces carrying high frequency
signals.

XM8200S Designer’s Guide
XM8200S-E00-100 xmodus swiss GmbH Seite 19 / 22
9. Avoid right angle turns on high frequency traces. Forty-five degree corners are good,
however, radius turns are better
5.1.1 Grounding
Pins 26 and 41 are for grounding. Connect all of them to the same ground-layer or a big
ground-area on your board. The ground-area should completely cover the area below and
around the module and the regulator. Make the connections as wide as possible. For better
RF-performance, connect the metal housing to ground, very near the ground-pins of the
module.
5.1.2 RF Antenna
Antenna sub-system and integration in the application is a major issue.
Attention should be paid to:
Choice of the antenna cable (type, length, performance, thermal resistance, etc)
Antenna connector (type + losses). These elements could affect WLAN performances such
as sensitivity and emitted power
The antenna should be isolated as much as possible from the digital circuitry (including the
interface signals)
It is strongly recommended to shield the terminal.
On terminals including the antenna, a poor shielding could dramatically affect the sensitivity
of the terminal. Moreover, the power emitted through the antenna could affect the
application.
Warning:
Xmodus swiss strongly recommends working with an antenna manufacturer either to
develop an antenna adapted to the application or to adapt an existing solution to the
application. The antenna adaptation (mechanical and electrical adaptation) is one of the key
issues in the design of a WLAN terminal.
The antenna-cable and the antenna should be as far as possible away from other circuitry,
specially switching-regulators, analog- and uC digital circuits. It is recommended to place the
antenna-jack near a metal enclosure and go through this one with the antenna-cable.
5.2 Manufacturing Considerations
The Socket Modem has been designed to be mounted onto the host board in one of two ways.
The first method consists of soldering two 32-pin strip sockets to the host board and inserting
the Socket Modem into the sockets. A suggested part number for the 32-pin socket is Sam
Tec SMM-132-01-F-S.
The second way is to solder the Socket Modem directly to the host board. The most efficient
way to do this is through a wave solder process. The recommended hole size for the Socket
Modem pins is 0.036 in. ±0.003 in. in diameter. Spacers can be used to hold the Socket
Modem vertically in place during the wave solder process. A spacer should be placed on pin
32 and pin 64 of the Socket Modem. A suggested part number for the spacer is BIVAR 938-
0.130 for P1(0.310in) option Socket Modems. The spacers can be left on permanently and will
not effect operation.
Socket Modems can be put through a water wash process.

XM8200S Designer’s Guide
XM8200S-E00-100 xmodus swiss GmbH Seite 20 / 22
6
6.
.
M
MO
OD
DU
UL
LE
E
D
DI
IM
ME
EN
NS
SI
IO
ON
NS
S
FIGURE 6-2. MECHANICAL DRAWINGS
26.5 mm
Pin 1
2.0
Top View
Dimensions in Millimeters
64.5
mm
Top View
7.0 mm
6.5 mm
This manual suits for next models
2
Table of contents
Other XMODUS Modem manuals
Popular Modem manuals by other brands
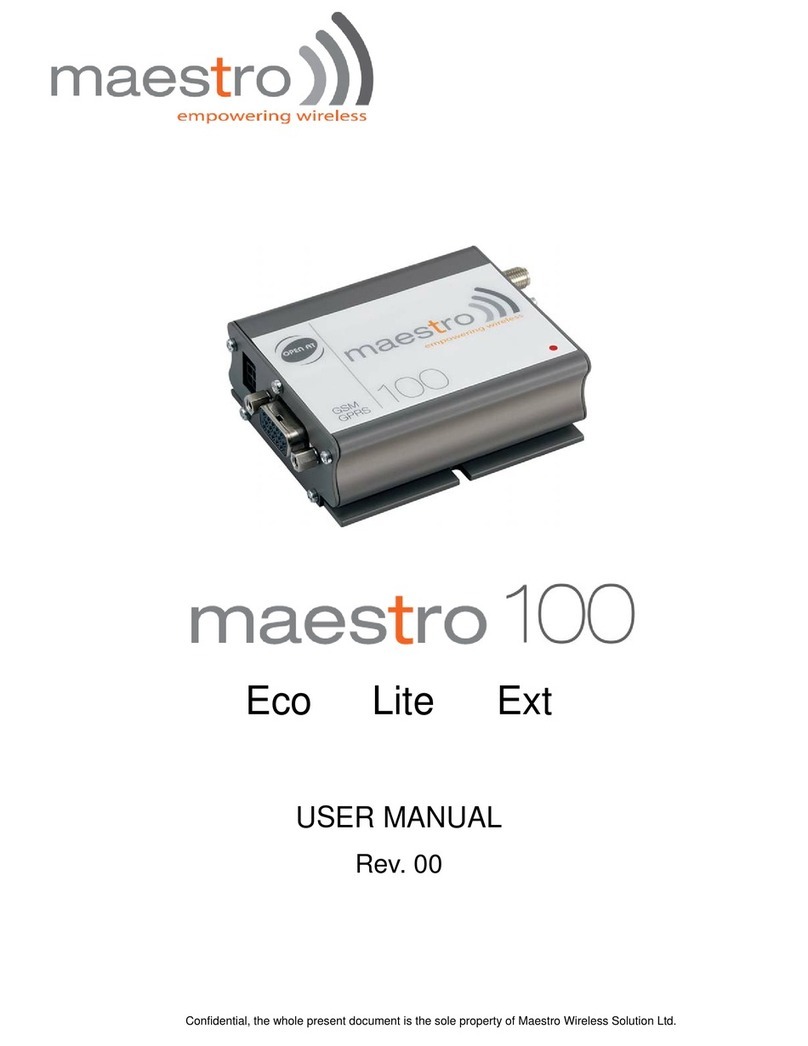
Maestro Wireless Solution
Maestro Wireless Solution M100 user manual
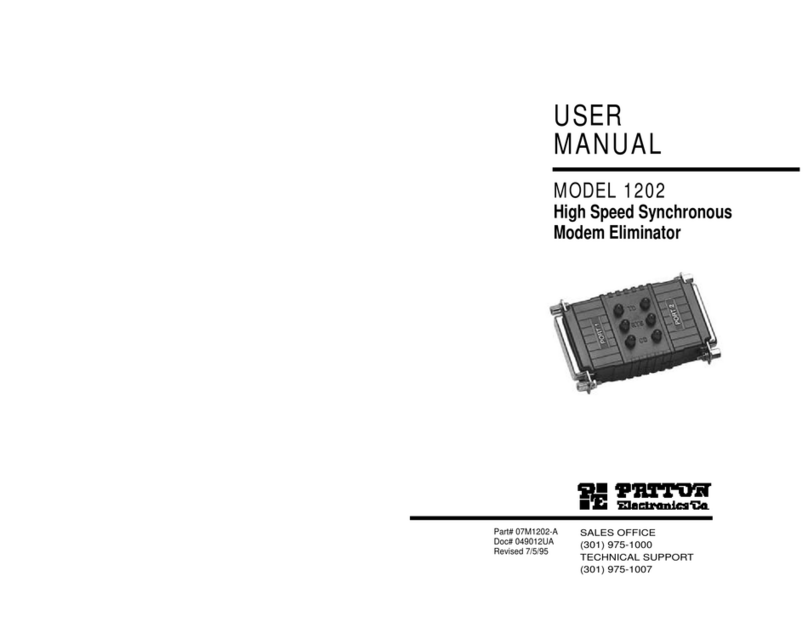
Patton electronics
Patton electronics 1202 user manual
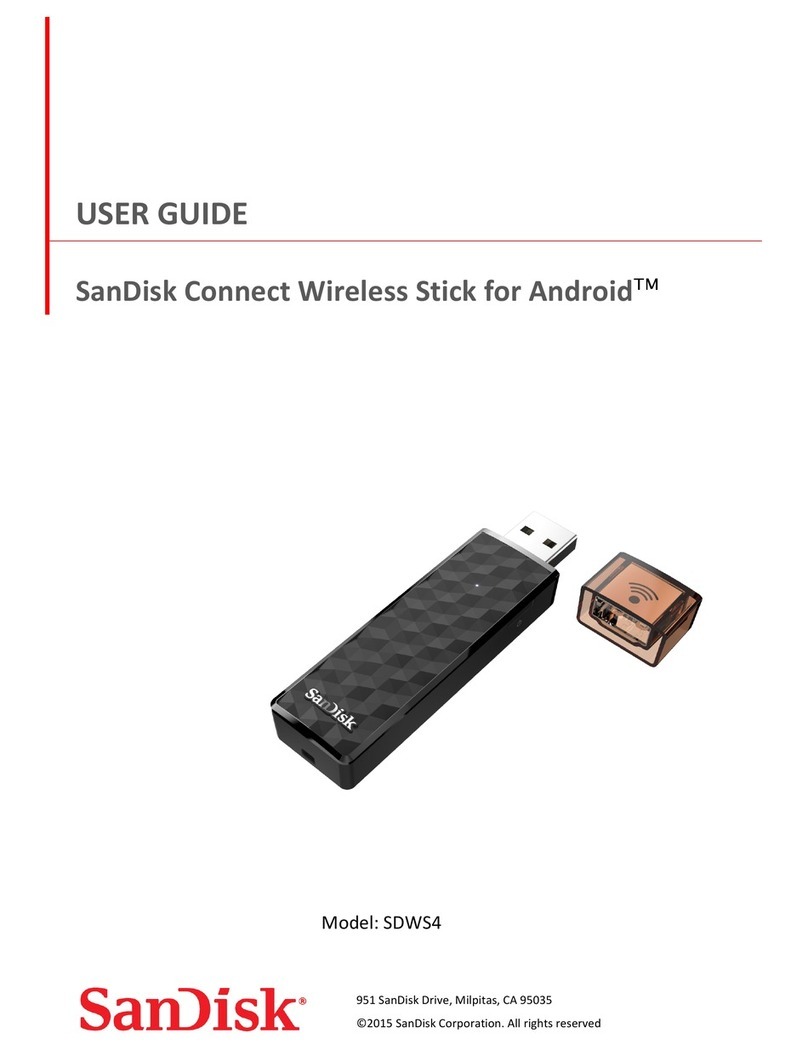
SanDisk
SanDisk SDWS4 user guide
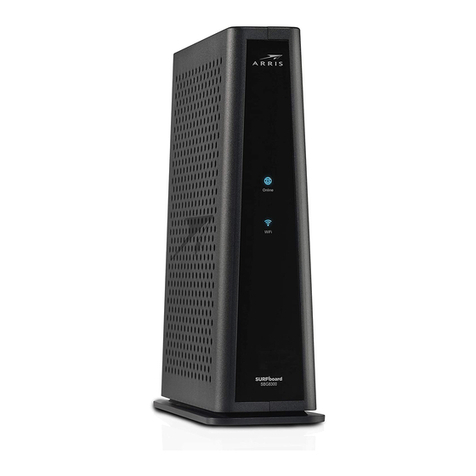
CommScope
CommScope SURFboard SBG8300 user guide
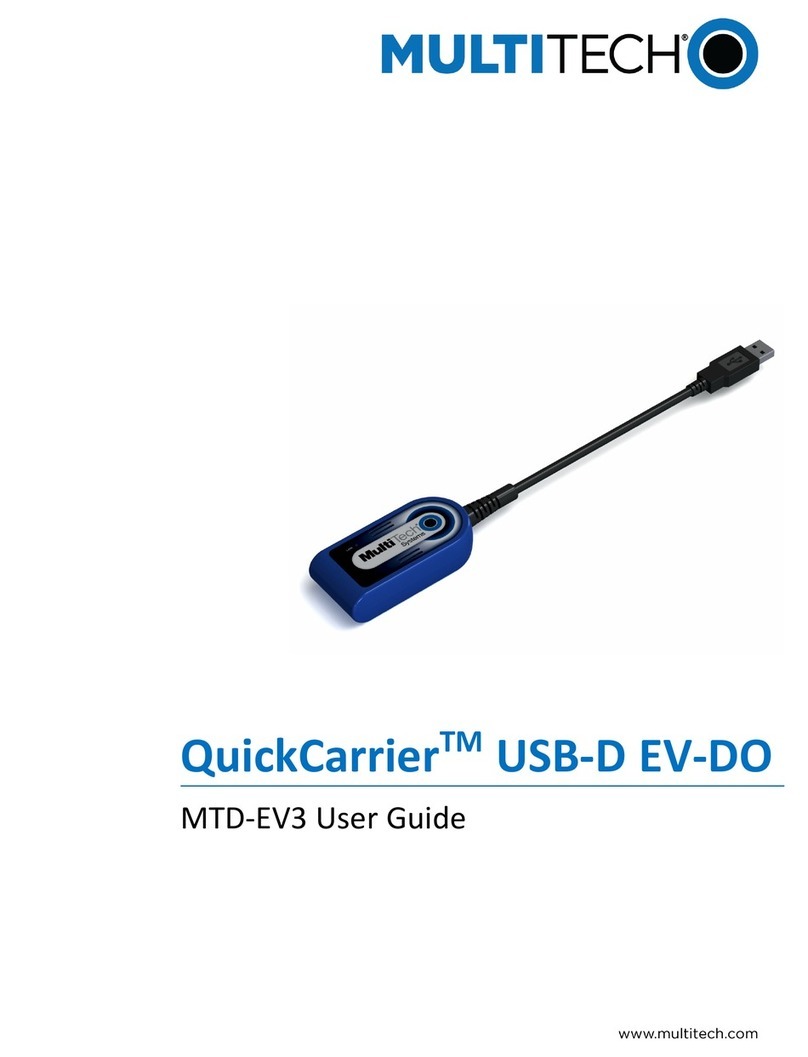
Multitech
Multitech QuickCarrier USB-D EV-DO user guide
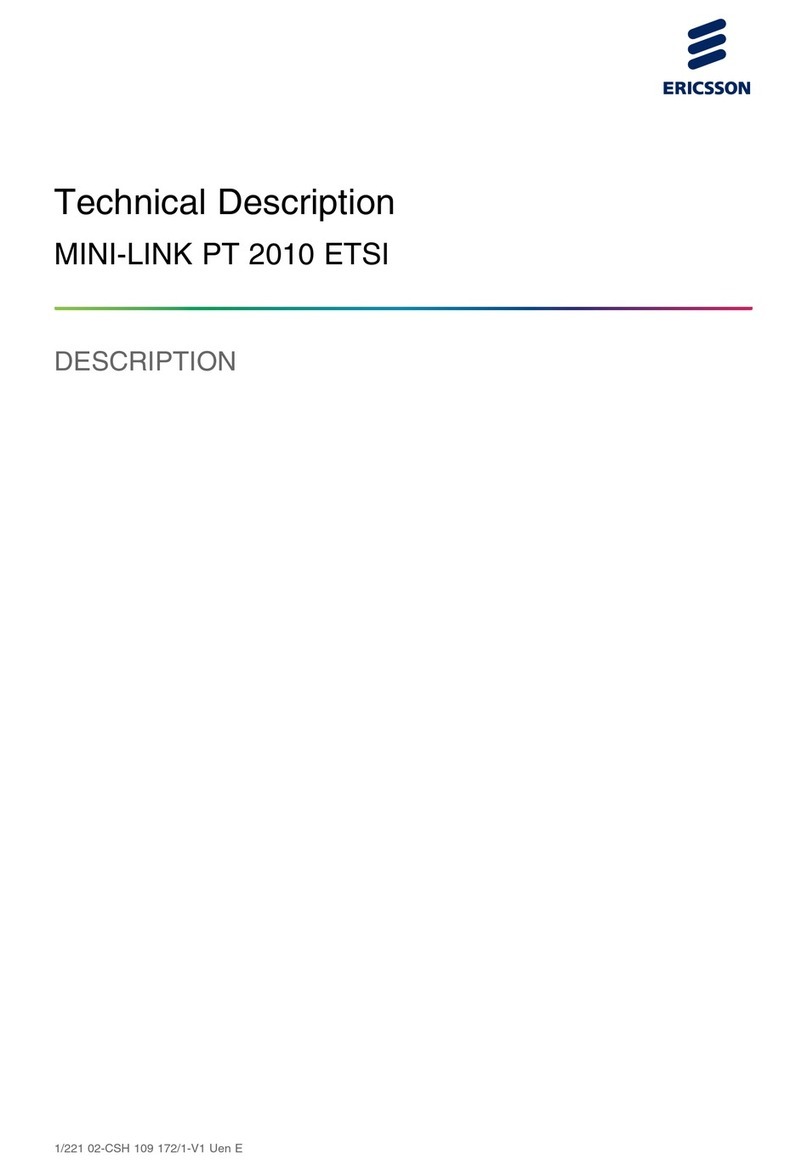
Ericsson
Ericsson MINI-LINK PT 2010 ETSI Technical description