XS Scuba PN RG100 Installation and operating manual

Service & Repair Manual
SERVICE AND REPAIR MANUAL
SPIRIT REGULATOR
PN RG100
Revised - 02/11

Spirit Regulator
2
Spirit Regulator Service and Repair Manual
Contents
Section 1 - Introduction
Warnings, Cautions, & Notes ................................................................................................................ 3
Scheduled Service................................................................................................................................. 3
EAN/ Nitrox Service............................................................................................................................... 3
Facility Requirements............................................................................................................................ 4
Specialty Tools....................................................................................................................................... 5
Section 2 - Preliminary Inspection
External Inspection................................................................................................................................ 6
Immersion / Leak Test ........................................................................................................................... 6
Intermediate Pressure Test.................................................................................................................... 7
Section 3 - Disassembly Procedures
General Guidelines................................................................................................................................ 8
First Stage Disassembly........................................................................................................................ 9
Second Stage Disassembly................................................................................................................. 12
Section 4 - Reassembly Procedures
General Guidelines.............................................................................................................................. 15
First Stage Reassembly ...................................................................................................................... 16
Second Stage Reassembly ................................................................................................................. 19
Secton 5 - Final Testing Procedures
First Stage Intermediate Pressure Test ............................................................................................... 22
Second Stage Adjustment and Flow Test ............................................................................................ 23
Subjective Breathing Test .................................................................................................................... 24
Flowbench Testing (optional)............................................................................................................... 25
External Leak Test ............................................................................................................................... 25
Troubleshooting Guide
First Stage ........................................................................................................................................... 26
Second Stage...................................................................................................................................... 27
Schematic & Parts Lists
Spirit First Stage.................................................................................................................................. 28
Spirit Second Stage............................................................................................................................. 29

Service & Repair Manual
3Copyright ©2011 XS Scuba
This manual provides factory prescribed procedures for the correct service and repair of the
Spirit™ regulator, including the rst and second stage. It is not intended to be used as an in-
structional manual for untrained personnel. The procedures outlined within this manual are to
be performed only by personnel who have received factory authorized training through a repair
seminar that has been directly sponsored by XS Scuba.
If you do not completely understand all of the procedures outlined in this manual, contact XS
Scuba to speak directly with a Technical Advisor before proceeding any further.
Warnings, Cautions, & Notes
Pay special attention to information provided in Warnings, Cautions, and Notes that are ac-
companied by one of these symbols:
A WARNING indicates a procedure or situation that may result in serious injury or death if instruc-
tions are not followed correctly.
A CAUTION indicates any situation or technique that will result in potential damage to the prod-
uct, or render the product unsafe if instructions are not followed correctly.
A NOTE is used to emphasize important points, tips, and reminders.
Scheduled Service
Because the Spirit™ regulator is considered to be a life-supporting product, it is extremely
critical that it receives service according to the procedures outlined in this manual on a regularly
scheduled basis; at least once a year with normal or infrequent use.
NOTE: A unit that receives heavy or frequent use, such as in rental, instruction, or
commercial applications, should be serviced at least twice each year - or more often
- depending on the conditions of use and the manner in which it is maintained. (Refer
to the care and maintenance procedures outlined in the Spirit User's Guide.)
When performing service, whether it is a routine overhaul or a repair of a specic problem, it
is important to understand how the regulator is designed and how it operates. If you have any
questions, please consult your XS Scuba representative.
EAN/ Nitrox Service
Newly manufactured XS Scuba regulators are assembled and packaged to be compatible
with oxygen enriched air (EAN/ Nitrox), not to exceed 40% oxygen content. If the regulator is
going to be used for this application, however, it must be dedicated and clearly labled as such,
in order to prevent any crossover use with standard compressed air. Refer to the instructions
provided in the XS Scuba Authorized Service Document, titled - Regulator Parts Cleaning
Procedures.
CAUTION: It is important to avoid using, testing, or otherwise pressurizing a dedicated
EAN regulator with standard compressed air, which contains hydrocarbon contaminants.
Introduction
1
SECTION

Spirit Regulator
4
Spirit Regulator Service and Repair Manual
Facility Requirements
As an Authorized XS Scuba Dealer, your customers expect you
to provide top-notch overhaul service, both before and after the sale.
Next to airlls and gas blending, it is the single most important com-
modity your store can provide.
The service department is therefore the most important part of
your store. It should be clean and well lighted, and stocked with a
complete inventory of parts and all the specialty tools you will need
to get the job done right. As a minimum requirement, your service
facility should be equipped with the following items:
❏Ultrasonic Cleaner – Select the right size model that can keep
up with the volume of equipment that your store services. A
built in timer and heater will help control the cleaning time and
temperature of the solution, since most solutions work best
when heated.
❏Bench Mounted Vise – A vise is sometimes needed to hold
the regulator secure – especially when removing the rst stage
yoke retainer. Special care must be taken, however, to avoid
damage that can result from improper use of this tool. Be sure
to follow the instructions provided in this manual.
NOTE: XS Scuba especially endorses and recommends the
Jaws Gripmaster Bench Vise, available from Peter Built Co.
It is designed specically for the professional dive store service
bench, and will prevent damage that can easily be caused by a
conventional vise.
❏Magnication Lamp – Strong lighting and magnication are
essential requirements for performing a thorough parts inspec-
tion - especially when locating the source of a small leak.
❏Quality Wrenches & Sockets – When working with brass
parts, it is especially critical to use the correct size wrench
and to ensure that it ts properly over the part. The use of an
adjustable wrench is very likely to cause damage to your cus-
tomer's equipment, and should be strictly avoided at all times.
❏Calibrated Inch-Pound and Foot-Pound Torque Wrenches –
It is important to follow the manufacturer's torque values
whenever they are specied, in order to avoid overtightening or
undertightening a part. This is especially important for smaller
parts and ttings, when overtightening can easily damage the
part. Torque wrenches that can be set for both inch-pound
and foot-pound measurements tend to be less accurate than
wrenches that are designed to measure torque within a specic
range.
"Jaws" Gripmaster Vise
Ultrasonic Cleaner

Service & Repair Manual
5Copyright ©2011 XS Scuba
Specialty Tools
For the nest tools, xtures, and supplies that are designed and manufactured specically for
servicing SCUBA equipment, we recommend one source for all your service facility’s needs.
Peter Built Co., in Galion, Ohio, is dedicated to serving the diving industry, and offers a wide se-
lection of the most innovative specialty tools found anywhere to help you get the job done efciently
- and done right.
Illustrations courtesy of Peter Wolfinger.
Galion, OH 44833
Phone: 419-468-2212
www.scubatools.com
Required Tools/ Lubricant
No. 4 Hook Spanner Wrench PN #20-404-200
Dual Drive Adjusting Tool PN #20-500-200
Tech Driver IPG PN #20-165-111
O-ring Tool Set PN#10-125-400
1/4" Slotted Screwdriver PN #11-465-500
1/4" Nut Driver PN #11-168-500
Small (.02) Blade Screwdriver PN #11-133-500
Cristo Lube PN #MS150
Hakko Side Cuts, 5" PN #16-020-500
Snap Ring Pliers
11/16" Open End Wrench
3/4" Open End Wrench
(419) 468-2212
Breaker Bar # 20-157-500
PETER BUILT
1" - SIX POINT
3/8"
Drive
I” Yo ke Nut Socket #20-155-500
Custom (narrow diameter)
3/8" x 3" Drive Extension #20-156-500
100
200
80
60
40
20 180
160
120
IP RANGE
125-150 PSI
PSI
PETER BUILT
"Quality in the making"
(419) 468-2212
USE NO OIL
140
25
50
150
125
100
75
175
200
225
250
275
300
0
IP RANGE
125-150 PSI
PSI
USE NO OIL
PETER BUILT CO.
"Quality in the making"
(419) 468-2212
260
3.5 x 60
260
2.0 x 50
Select Tool Kit (5 pcs) # 11-090-500
Poppet Align/ Orifice Preset Tool, #20-785-400
Intermediate Pressure
Te st Gauge, #20-510-100
Snap Ring Pliers # 10-101-500
O-ring Tool Set #10-102-100
No. 4 Hook Spanner, #20-404-200
Dual Drive In-Line Adjusting Tool # 20-500-200 Second Stage Rim Clamp #20-790-200
M
Piston Installation Bullet

Spirit Regulator
6
Spirit Regulator Service and Repair Manual
Preliminary Inspection
External Inspection
1. Closely examine the conical lter to check for any signs
that contaminants have entered the system, including sea
water, rust, or aluminum oxide.
NOTE: A green discoloration of the lter indicates
that moisture has entered the regulator, and internal
corrosion has possibly occurred. Other types of dis-
coloration may indicate that the regulator has been
used with a corroded cylinder. Advise the customer
of this, and the possible need to obtain service for
the cylinder.
2. Slide back the hose protectors, if present, to visually
inspect the condition of the hoses, especially at their t-
tings.
3. Closely examine the nish of the rst stage to check for
any chips, scratches, or other damage that exposes the
brass beneath the nish.
CAUTION:Do not clean any parts that show damage
to their nish inside an ultrasonic cleaner.
4. Closely examine all parts of the rst stage for any other
signs of external corrosion.
Immersion / Leak Test
1. Check to ensure that the regulator is fully assembled and
connected to a second stage, and that there are no open
ports or hoses. Connect the rst stage to a cylinder that
is lled with 3,000 psi, and open the cylinder valve to
pressurize the regulator.
2. If leakage cannot be heard, or if the source of leakage
detected audibly is not obvious, immerse the rst stage in
fresh water to check further for any signs of air leakage,
especially at the ttings of hoses.
3. Note the source of any leakage found and refer to
the Troubleshooting Guide to determine its possible
cause.
4. Close the cylinder valve and depress the second stage
purge button to depressurize the regulator before per-
2
SECTION

Service & Repair Manual
7Copyright ©2011 XS Scuba
forming the next procedure.
Intermediate Pressure Test
NOTE: It is not necessary to perform this test unless
a problem has been reported that requires diagnostic
troubleshooting and repair. When performing routine
overhaul service, proceed directly to the following
section, Disassembly.
1. Connect a calibrated intermediate pressure test gauge
to the regulator, either with a quick-disconnect inator
hose or with the female tting of a second stage LP hose,
depending on the connection of the test gauge.
CAUTION:To provide a safety relief valve in the
event that intermediate pressure exceeds 155-170
psi, ensure that a fully assembled and properly ad-
justed second stage is connected to the rst stage
before pressurizing. Failure to relieve intermediate
pressure that exceeds 400 psi may result in damage
or rupture of the test gauge or LP hose, and could
cause serious personal injury.
2. Slowly open the supply valve to pressurize the rst stage.
Closely monitor the IP test gauge to determine whether
the intermediate pressure rises above 145 psi.
3. Note the intermediate pressure indicated by the test
gauge, and purge the second stage several times to
determine whether lockup is achieved without creeping or
uctuating back and forth.
4. If the intermediate pressure creeps up or otherwise uc-
tuates after cycling the regulator, wait for it to stabilize (if
possible) before making a nal note of the intermediate
pressure.
NOTE: Correct intermediate pressure for the rst
stage is 140 (±5) psi, with an inlet pressure between
2,500 - 3,000 psi.
5. Close the supply valve and depress the second stage
purge button to depressurize the system before at-
tempting to perform any disassembly.
▼After completing the Preliminary Inspection, proceed
to Section 3 – Disassembly

Spirit Regulator
8
Spirit Regulator Service and Repair Manual
Disassembly Procedures
General Guidelines
▼Prior to performing any disassembly, check to ensure that
the service facility is well equipped with all the tools and
parts needed to perform a complete service from start to
nish. DO NOT attempt to perform the service unless all
of the required tools and parts are available.
▼ All o-rings are classied as being either dynamic or
static. Dynamic o-rings are those which sustain friction
and movement, as they are either mounted directly onto
a moving part, or create a seal against a moving part.
Static o-rings simply create a seal between two non-
moving parts, and are therefore less subject to wear than
dynamic o-rings. After passing close inspection, static
O-rings may sometimes be reused, although this is not
necessarily recommended. Dynamic O-rings must be
automatically discarded and replaced with every service,
regardless of age or appearance.
▼Refer to the schematic and parts list while performing
these procedures. Each part is identied by its reference
number shown on the drawing the rst time it is referred
to in the procedure.
▼ Do not attempt to reuse parts that are designated to
be automatically discarded and replaced with the parts
provided in the overhaul parts kit. These parts should be
shown to the customer, however, to ensure their con-
dence and satisfaction that complete overhaul service has
been performed.
▼Inspect all reusable parts as directed, either during or im-
mediately following the disassembly procedures. When
in doubt, compare the part with one that is new to best
determine its condition.
3
SECTION

Service & Repair Manual
9Copyright ©2011 XS Scuba
First Stage Disassembly
CAUTION: Whenever possible, use only plastic or brass
O-ring tools for removing O-rings in order to prevent
damage to the sealing surface. Steel instruments, such
as dental picks, can easily damage the sealing surface
of a softer brass part, causing irreparable leakage and
requiring the part to be replaced with new.
1. Before disassembling the rst stage, remove the low
pressure second stage hose with a b" open end wrench,
the high pressure hose with a s" open end wrench, and
the low pressure inator hose with a 2" (or other size
required) open end wrench. Remove all remaining port
plugs(13&15) with a ®" (4mm) hex key.
2. Remove and inspect the O-rings(12&14) on these items
to determine their condition, and discard them if any signs
of decay are found.
3. Loosen the yoke screw(2) as needed to remove the dust
cap(4) from the yoke(3).
NOTE:It will be necessary to use a bench mounted
vise to hold the rst stage secure throughout the
next procedure. This ensures the best protection
against slippage and accidental damage to soft
metal parts. If an ordinary bench vise will be used,
the rst stage must be mounted outside the vise
with the use of a vise mounting tool fastened into
the high pressure port. To ensure the best available
protection against damage, XS Scuba specifically
recommends the Gripmaster Vise, available from
Peter Built Co.
4. Secure the rst stage inside the Gripmaster Vise, so that
the piston cap(23) faces straight up and the yoke screw
faces down. Fit the #4 Hook Spanner (Peter Built PN
20-404-200) onto the piston cap to mate the pin inside
one of the bore holes (see Fig. 1). While holding the tool
securely engaged, turn the piston cap counter-clockwise
to loosen no more than 4 turn (90 degrees) so that it can
later be removed by hand. Do not loosen it further than 4
turn at this time.
5. Loosen the vise, and resecure the rst stage in the op-
posite position, so that the yoke or DIN adapter faces
straight up.
Fig. 1 – Loosening the Piston Cap

Spirit Regulator
10
Spirit Regulator Service and Repair Manual
6. Disassembly of the Yoke Connector
a. Loosen the yoke screw several turns counter-clock-
wise. Place a 1" Yoke Retainer Socket (Peter Built PN
20-156-500) inside the yoke and over the hex fea-
tures of the yoke retainer(8). Pass a Breaker Bar (PN
20-157-500) through the yoke, and tighten the yoke
screw lightly snug over the dimpled feature (see Fig.
2). Then, grasp the breaker bar with both hands on
opposite ends and turn the socket counter-clockwise
with steady force to loosen the yoke retainer. Do not
use impact.
CAUTION: The socket and breaker bar combination
provide the best insurance against damage while
removing the yoke retainer, using the procedure de-
scribed above. DO NOT, under any circumstances,
use an adjustable wrench or an open end wrench
that does not t completely over the ats on both
sides. Doing so may result in permanent damage to
the yoke retainer, requiring its replacement.
b. Turn the yoke screw counter-clockwise to remove, and
set aside the breaker bar and socket.
c. Unscrew the yoke retainer counter-clockwise to re-
move from the body, along with the yoke.
d. Remove the main seal O-ring(9) from the yoke retain-
er. Discard the O-ring and do not reuse, regardless of
its condition.
e. While holding the yoke retainer secure, apply a pair of
Snap Ring Pliers to remove the retaining ring(5) from
the yoke retainer (see Fig. 3). Tap out the lter(6), and
remove the O-ring(7) with a brass O-ring tool. Discard
the lter and O-ring, and do not reuse these parts
regardless of their condition.
7. Disassembly of the DIN Connector
a. Apply a 4" hex key to the lter retainer(3b), andturn it
counter-clockwise to loosen and remove (see Fig. 4).
Remove and discard both O-rings(3a&3c).
b. Lift the handwheel(3f) off the lter housing(3g), and
closely inspect the condition of the threads to ensure it
is free of any burrs or other damage that could prevent
proper threading.
c. Apply a m" open-end or box wrench to the lter hous-
ing, and loosen it counter-clockwise with steady force
to remove from the rst stage body. Remove and dis-
card the lter(3d) and both O-rings(3e).
Fig. 3 – Removal of Filter Retaining Ring
Fig. 4 – Removal of DIN Retainer
Fig. 2 – Loosening the Yoke Retainer

Service & Repair Manual
11 Copyright ©2011 XS Scuba
8. Remove the saddle(10) and check for any signs of dam-
age. Set it aside to be reused if none are found.
9. Remove the rst stage from the vise. While holding the
rst stage body secure with one hand, unscrew the piston
cap (pre-loosened in Step 4) counter-clockwise with the
other. Lift the piston cap with the piston(21) straight up
and off the rst stage body and spring(17). Remove the
collar(22) and discard or set it aside to be reused, de-
pending on its condition.
10. Pull the piston straight out of the piston cap, being care-
ful to avoid rocking or twisting it in order to prevent metal
against metal contact. Remove and discard both dynam-
ic O-rings(19&20).
11. To remove the high pressure seat(18) from the end of the
piston shaft, carefully insert a slim rod through the head
and shaft of the piston. Firmly press the rod against the
underside of the seat to press it out of the piston shaft
(see Fig. 5). Discard the seat, and do not attempt to re-
use.
12. Remove the high pressure valve spring and spring isola-
tors(16) from the body. Inspect the spring isolators for
any signs of damage or distortion, and discard if any
is found. Closely inspect the spring with a magnier
to check for any signs of damage or corrosion that has
permeated the wall of the metal. Set the spring aside to
be reused if it is determined to be in satisfactory condition
with no signs of permanent corrosion or damage.
CAUTION: If damage is found, or if the intermediate
pressure was measured lower than 135PSI during
preliminary inspection, replace the spring. DO NOT
attempt to raise the intermediate pressure by adding
spring isolators to compensate for a damaged spring.
13. Under strong lighting, closely inspect the inner bore and
all sealing surfaces of the rst stage body with a magni-
er, including the intermediate and high pressure ports,
and especially, the machined orice cone (see Fig. 6).
Check to ensure there are no scratches or other damage
that could contribute to leakage. If damage is found that
is determined to cause irreparable leakage, it will be nec-
essary to discard the rst stage body and replace it with
new. Do not attempt to polish the sealing surface of the
orice cone.
▼After completing the disassembly of the rst stage,
proceed to the following procedure - Second Stage
Disassembly. Fig. 6 – HP Cone Inspection
Fig. 5 – Removal of HP Seat

Spirit Regulator
12
Spirit Regulator Service and Repair Manual
Second Stage Disassembly
CAUTION:Whenever possible, use only plastic or
brass O-ring tools for removing O-rings in order to
prevent damage to the sealing surface. Steel instru-
ments, such as dental picks, can easily damage the
sealing surface of a softer brass part, causing irrepa-
rable leakage and requiring the part to be replaced
with new.
1. Slide back the hose cover to expose the connection of the
LP hose.
2. While holding the inlet tting(20) secure with an n" open-
end wrench, apply a 17mm open-end wrench to the tting
of the LP hose. Turn the hose tting counter-clockwise to
loosen and remove.
3. Using a plastic or brass O-ring tool, carefully remove the
O-ring(25) from the post inside the hose tting.
CAUTION: When performing the above step, be
very careful to avoid scratching the O-ring sealing
surface. Doing so may cause a permanent leak that
will require the replacement of the LP hose.
4. Using an n" open end wrench, turn the inlet tting coun-
ter-clockwise to loosen from the second stage hous-
ing(12), and unscrew it completely by hand to remove.
5. Snip the plastic tie-strap(21) that holds the mouth-
piece(23), and gently pull the mouthpiece off the second
stage housing. Inspect the mouthpiece to ensure that it is
supple and free of any tears or corrosion. If any damage
is found that could result in discomfort or leakage, discard
the mouthpiece and do not reuse.
6. While holding the second stage secure with one hand,
rmly grasp the retaining ring(17) with the other, and turn
the ring counter-clockwise to loosen and remove it, along
with the diaphragm cover(16).
NOTE: If the retaining ring is difcult to loosen, XS
Scuba recommends using the Rim Clamp (P/N 20-
790-200), available from Peter Built Co. Complete
instructions are provided with the tool.
7. Separate the diaphragm cover from the retaining ring,
and closely inspect the cover to ensure that it is perfectly
round and free of damage. If any damage is found, dis-
card the cover and replace with new.
8. Lift out the diaphragm(14) and thrust washer(15) from the

Service & Repair Manual
13 Copyright ©2011 XS Scuba
second stage housing. Inspect the diaphragm to ensure
that it is supple and free of any pinholes, tears, corrosion,
or other damage. If any damage is found, discard it and
replace with new.
9. Using a small at blade screwdriver, rotate the metal retain-
ing clip(13) over the groove of the housing plug(1) inside
the second stage housing until the notch in the center faces
up. Place the tip of a 2mm at blade screwdriver inside this
notch, and gently lift the clip off the groove. (See Fig. 7.)
10. Apply a c" hex key to turn the housing plug counter-clockwise
until loosened, and remove it from the housing. Carefully
remove the O-ring(2) with a plastic tool, and discard. Closely
xamine the condition of the housing plug, especially around
the threads and O-ring seating groove. Discard if any dam-
age is found that may cause leakage, or set it aside to be
reused.
11. While holding the lever(18) lightly depressed, press the inlet
end to slide the entire valve assembly out of the other end of
the second stage housing (see Fig. 8). Remove and discard
the inlet tting O-ring(19).
12. Turn the air barrel over to allow the balance shuttle cap(3)
and LP spring(4) to drop out (see Fig. 9). Inspect the spring
closely with a magnier to check for any signs of corrosion.
Discard it if corrosion is found, and do not reuse.
13. Gently remove the lever from the air barrel by lifting out one
leg rst, and then the other. Be careful to avoid bending or
stretching either leg.
14. Turn the air barrel over to allow the poppet(6) to drop out.
Using ngernails or a plastic tool, carefully remove the LP
seat(7) and small O-ring(5). Discard both soft parts, and
do not reuse. Closely inspect the poppet around all seating
surfaces, and compare it with new to ensure no damage is
visible. If damage is found, discard the poppet and replace
with new.
15. Remove the white lever pad(9) from the air barrel. Discard,
and do not reuse.
16. While holding the air barrel secure, apply a medium blade
screwdriver to the slotted head of the adjustable orice(10),
and turn it counter-clockwise to disengage its threads.
NOTE: The orice is O-ring sealed, and it will remain
inside the air barrel after it has been unthreaded. The
following step must be performed to remove the orice
without damaging its polished sealing surface.
Fig. 7 – Removal of Retaining Clip
Fig. 9 – Removal of LP Spring
Fig. 8 – Removal of Valve Assembly

Spirit Regulator
14
Spirit Regulator Service and Repair Manual
17. When the orice has been unthreaded from the air barrel,
carefully insert a small wooden or plastic dowel through
the opposite end of the valve body, directly over the seal-
ing edge of the orice. Gently press out the orice. (See
Fig. 10.)
18. To avoid using a sharp tool that can damage the orice,
squeeze the O-ring(11) between thumb and forenger to
remove it from the orice head. Discard the O-ring and
do not reuse.
19. Closely examine the orice with the use of a magnier,
checking for any scratches or other damage to the seal-
ing edge and the groove that holds the O-ring (see Fig.
11). If any damage or wear is found, discard the orice
and do not attempt to reuse. If it is in reusable condition,
set it aside on a soft surface to keep it isolated from other
metal parts.
20. Remove the exhaust deector(24) from the second stage
housing to expose the exhaust valve(22) for inspection.
NOTE: To facillitate the removal of the exhaust de-
ector, rst place it in hot (120°-150°F) water for 2-3
minutes and allow it to soften.
21. Closely inspect the exhaust deector to check for any
signs of damage that may have been caused by abuse
or improper disassembly. If found, discard it and replace
with new,
22. Closely inspect the condition of the exhaust valve to
ensure that it is evenly seated against the second stage
housing on all sides, and free of any tears, holes, or other
signs of decay. Peel back the lip on all sides to ensure it
is supple and returns to its original position. If any wear
or damage is detected, or if the material feels stiff or de-
cayed, pull the exhaust valve straight out of the housing
and discard it.
NOTE: It is not necessary to remove the exhaust
valve diaphragm unless it shows signs of wear or
decay upon inspection. Once the diaphragm is
removed, however, it will be permanently stretched
and then must be replaced with new.
▼After completing the disassembly of the rst and
second stages, refer to the instructions provided in
the XS Scuba Authorized Service Document, titled -
Regulator Parts Cleaning Procedures.
Fig. 11 – Orifice Inspection
Fig. 10 – Removal of Adjustable Orifice

Service & Repair Manual
15 Copyright ©2011 XS Scuba
Reassembly Procedures
General Guidelines
▼Refer to the schematic parts list, that highlights automatic
replacement parts which should be discarded and replaced
with new during reassembly. These parts are provided in the
Annual Service Kit.
▼Before performing any reassembly, it is important to individu-
ally inspect all parts, both new and those that are being reused,
to ensure that each part and component is perfectly clean and
free of any dust, decay, or blemishes.
▼ If the regulator has been serviced for use with EAN/Nitrox, it is
important to don powderless latex gloves before handling any
parts, including O-rings, in order to avoid contaminating the
parts with skin oil.
▼ Prior to dressing, inspect all O-rings with magnication to en-
sure they are supple, clean, and completely free of any scoring
or decay that would impair proper sealing.
▼XS Scuba recommends Christo-Lube® MCG-11 (PN MS150)
to be used exclusively for the lubrication and dressing of O-
rings and other internal parts. Christo-Lube®provides superior
lubrication to that of silicone grease, especially in high pressure
(DIN) systems greater than 3,000 psi, and extreme tempera-
ture conditions. It is also non-reactive to oxygen, and is ap-
proved for use with EAN/Nitrox.
CAUTION:Silicone grease is not compatible with oxygen
enriched air, and must be strictly avoided when servic-
ing a regulator that will be used with EAN/ Nitrox. The
entire regulator will otherwise become contaminated,
and rendered unsafe for use with any mixture of oxygen
enriched air.
▼ Dress all O-rings with a visible lm of Christo-Lube, but avoid
applying excessive amounts, as this may attract particulate
matter that can cause accelerated wear or damage to the
O-ring.
CAUTION: The use of aerosol spray or petroleum based
lubricants must be strictly avoided. The propellant gas
or petroleum base may attack or weaken plastic or rub-
ber parts.
▼Use all replacement parts provided in the XS Scuba Authorized
Dealer parts kit.
4
s e c t i o n

Spirit Regulator
16
Spirit Regulator Service and Repair Manual
First Stage Reassembly
WARNING:DO NOT attempt to use any other manu-
facturer's part as a substitute for any XS Scuba part,
regardless of any similarity in shape, size, or appear-
ance. Doing so may render the product unsafe, and
could result in serious injury or death.
1. Generously lubricate and install the piston head O-
ring(20) onto the head of the piston(21), and install the
piston shaft O-ring(19) onto the piston shaft.
2. Install the high pressure seat(18) into the end of the pis-
ton shaft, and check to ensure it is seated ush with no
visible protrusion (see Fig. 12).
3. Set the piston cap(23) on a at surface with the open end
facing up. Place the head of the piston inside the cap so
that it rests perfectly level above the threads, and then
gently press the piston straight down into place until it is
fully seated.
CAUTION: Be careful to prevent the piston from
becoming cocked at an angle as the head travels
past the threads of the piston cap. The O-ring could
otherwise become unseated or damaged, and metal
on metal contact could cause damage to the piston
or the piston cap.
4. Fit the collar(22) over the open end of the piston cap, so
that it seats ush aginst the shoulder.
5. Over the support post inside the intermediate pressure
chamber of the rst stage body, install the same color
(thickness) and number of spring isolators(16) that were
disassembled from the high pressure chamber.
CAUTION: Unless the spring has been replaced
with new, it is very important to reinstall the same
number and color combination of spring isolators
as the original quantity that was removed during the
disassembly procedure. No more than two spring
isolators may be used between the spring and the
body, and no more than one spring isolator may be
used between the spring and the piston.
6. Apply a light lm of lubricant to both ends of the high
pressure spring(17), and place the spring down over the
support post inside the high pressure cavity of the body.
Fig. 16 – Swivel Retainer w/ O-rings
Fig. 12 – HP Seat Installation

Service & Repair Manual
17 Copyright ©2011 XS Scuba
Fig. 13 – Installing Piston Cap
7. Place the remaining spring isolator directly over the top of
the spring.
8. Hold the body secure with the open intermediate pressure
end facing straight up, and position the piston cap over
the body so that the piston shaft is aligned through the
center of the spring. Mate the piston cap onto the body
and rmly press downward while turning it clockwise to
engage the threads (see Fig. 13). Continue turning by
hand until snug.
9. Fit the saddle(10) onto the high pressure (inlet) end of the
rst stage.
10. Secure the rst stage inside the Gripmaster Vise with the
high pressure end facing straight up.
11. Reassembly of the Yoke Connector
a. Install the O-ring(7) into the yoke retainer(8), followed
by the conical lter(6). Closely examine the retain-
ing ring(5) to identify which side is at and which side
is slightly rounded. Using snap ring pliers, install the
retaining ring into the groove above the lter, with the
at side facing out.
b. Lubricate and install the main seal O-ring(9) into the
groove in the bottom of the yoke retainer.
c. Being careful to ensure that the O-rings remain prop-
erly seated, insert the threaded end of the yoke re-
tainer through the bottom of the yoke(3), and mate the
yoke retainer into the inlet port of the rst stage body.
Turn the retainer clockwise by hand until snug.
d. Apply a torque wrench with the 1" Yoke Nut Socket
(PN 20-155-500) and 3"x a" Socket Drive Extension
(PN 20-156-500). Tighten the yoke retainer to a mea-
surement of 24 foot-lbs (±1). (See Fig. 14.)
e. Install the dust cap(4) onto the yoke, and mate the
yoke screw(2) into the yoke. Turn the screw one to
two revolutions clockwise to engage the threads.
12. Reassembly of the DIN Connector
a. Install both O-rings(3e) and lter(3d) into the lter
housing(3g).
b. Mate the lter housing into the inlet port of the rst
stage body, and turn clockwise by hand until snug.
Apply a torque wrench with a m" deep socket to tight-
en the lter housing to a torque measurement of 17
foot-lbs (±1). (See Fig. 15.)
Fig. 14 – Torquing Yoke Retainer

Spirit Regulator
18
Spirit Regulator Service and Repair Manual
c. Fit the handwheel(3f) over the lter housing with the
male threaded side facing up.
d. Install both O-rings(3c&3a) onto the lter retainer(3b).
Mate the lter retainer into the lter housing, and turn
clockwise by hand until snug. Apply a torque wrench
with 4" hex key socket to tighten the lter retainer to a
torque measurement of 130 inch-lbs (±10).
13. Resecure the rst stage inside the Gripmaster Vise, so
that the piston cap faces straight up.
14. Fit the #4 Hook Spanner (Peter Built PN 20-404-200)
over the piston cap(23) to engage the pin with one of the
bore holes, and hold the tool securely engaged. While
holding the tool securely engaged, turn the piston cap
clockwise only until it has reached the extent of its thread
engagement, and do not tighten beyond snug.
15. Loosen the vise to remove the rst stage, and remove the
vise mounting tool.
16. Lubricate and install the O-rings(12&14) onto all
hoses and port plugs. Install the LP hoses and port
plugs(13&15) into their respective ports in the rst stage.
Apply a calibrated torque wrench with ®" (4mm) hex key
socket (or appropriate size crow foot for hoses) to tighten
the port plugs and hoses to a torque measurement of 38
inch-lbs (±2).
▼After completing the reassembly of the rst stage, pro-
ceed to the following procedure - Second Stage Reas-
sembly.
Fig. 15 – Torquing DIN Housing

Service & Repair Manual
19 Copyright ©2011 XS Scuba
Second Stage Reassembly
WARNING:DO NOT attempt to use any other manu-
facturer's part as a substitute for any XS Scuba part,
regardless of any similarity in shape, size, or appear-
ance. Doing so may render the product unsafe, and
could result in serious injury or death.
1. Install the exhaust valve(22) into the second stage hous-
ing(12) by gently pulling the stem through the hole in
the center of the sealing area, until the barb has passed
through and is securely seated inside.
NOTE: Prior to installing the exhaust deector(24),
place it in hot (120°-150°F) water for 2-3 minutes and
allow it to soften.
2. Fit the exhaust deector(24) over the top ridge of the sec-
ond stage housing, so that the two corners are securely
seated, and then stretch the lower portion down until it
snaps securely into place.
CAUTION: Do not use a tool to install the exhaust
deector. Doing so may cause serious damage to the
seating ange, requiring replacement of the housing.
3. Closely examine both sides of the white lever pad(9) to
identify that the mounting tabs on both legs are rounded
on one side and at on the other. (See Fig. 21.) Hold
the air barrel with the at cut facing down, and place the
clip over the tube with the rounded side facing toward
the ange, so that one tab engages in the hole next to it.
Then, gently press the opposite leg into place so the the
other tab engages in the opposite hole. When done cor-
rectly, the lever pad should rest ush against the ange,
with both tabs securely seated. (See Fig. 22.)
CAUTION:Do not stretch the legs of the lever pad,
or attempt to install it if damage has occurred.
4. Insert the stem of the LP seat(7) into the large end of the
poppet(6). DO NOT use adhesive.
5. Lubricate and install the small O-ring(5) over the groove
on the opposite end of the poppet, being careful to avoid
stretching it excessively. Closely examine the shape and
features of the poppet. (See Fig. 23.)
6. While holding the air barrel with the at cut facing straight
up, guide the poppet into the tube, LP seat rst, with the
ears facing straight down. (See Fig. 24.)
Fig. 21 – Lever pad Features
Fig. 24 – Correct Poppet Orientation
Fig. 23 – Poppet Features
Fig. 22 – Air Barrel Orientation
Fig. 25 – Poppet Correctly Installed

Spirit Regulator
20
Spirit Regulator Service and Repair Manual
7. Closely examine both holes where the lever pad is in-
stalled, to ensure that the ears of the poppet are prop-
erly aligned as shown (see Fig. 25). While holding the
air barrel with the at cut facing up, insert one leg of the
lever(18) into one hole, so that it engages with the poppet
(see Fig. 26). Being careful to avoid stretching or bending
the lever, rotate it over the air barrel until the opposite leg
engages with the opposite side. Check to ensure that the
lever is properly seated on both sides, securely engaging
the poppet ears. (See Fig. 27.)
NOTE: To better control the orientation of the poppet
inside the air barrel while the lever is being installed,
XS Scuba recommends using the Poppet Align/
Orice Preset Tool (P/N 20-785-400), available from
Peter Built Co. (See Fig. 28.)
8. While holding the second stage housing right side up with
the front facing you, slide the valve assembly into the
opening in the right side of the housing. Gently depress
the lever, and then slide the valve assembly through the
opening on the inlet side. Be careful to ensure that both
lever arms t squarely between the two anges inside the
housing, and then slide fully in place so that the lever pad
is seated ush. (See Fig. 29.)
9. Apply a light coat of lubricant to both ends of the poppet
spring(4), and place the spring inside the air barrel, over
the small end of the poppet.
10. Insert the small end of the shuttle cap(3) into the end of
the poppet spring.
11. Install the O-ring(2) onto the housing plug(1). Mate the
housing plug directly over the shuttle cap, and screw the
plug clockwise by hand to engage the threads of the air
barrel. Apply a c" hex key to tighten only until snug. DO
NOT OVERTIGHTEN.
12. Install the retaining clip(13) over the groove of the hous-
ing plug inside the housing, so that it snaps securely into
place. (See Fig. 30.)
13. Install the O-ring(19) over the threaded inlet of the air
barrel, being careful to avoid stretching it or rolling over
the threads. Use a smooth instrument to ensure that it is
seated at the base of the threads, against the wall of the
housing.
14. Mate the inlet tting(20) over the threads of the air barrel,
and turn it clockwise by hand until nger snug. Apply a n"
open end wrench to tighten it further by exactly 8 turn.
Fig. 26 – Lever Installation
Fig. 27 – Correct Lever Orientation
Fig. 29 – Valve Assembly Completely Installed
Fig. 28 – Poppet Alignment/ Preset Tool
Table of contents
Popular Controllers manuals by other brands
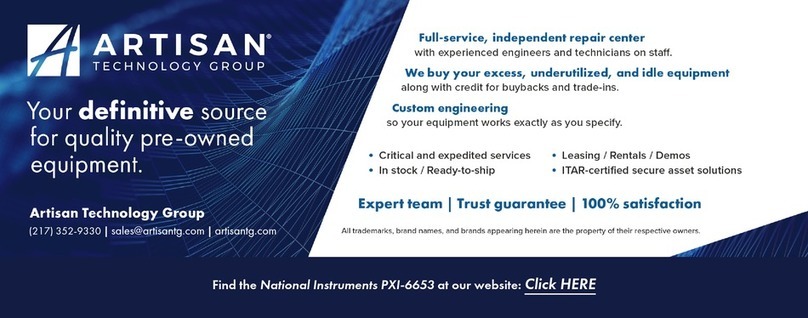
National Instruments
National Instruments NI PXI-6653 installation guide
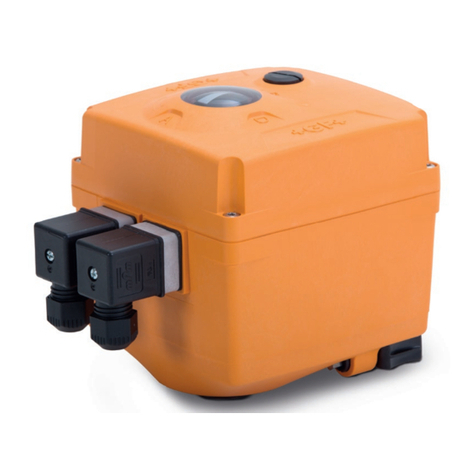
GF
GF EA15 instruction manual

Mitsubishi Electric
Mitsubishi Electric AJ61BT11 user manual
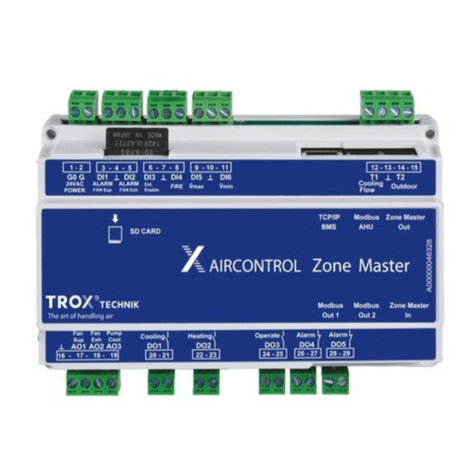
Trox Technik
Trox Technik X-AIRCONTROL Installation, commissioning and service manual
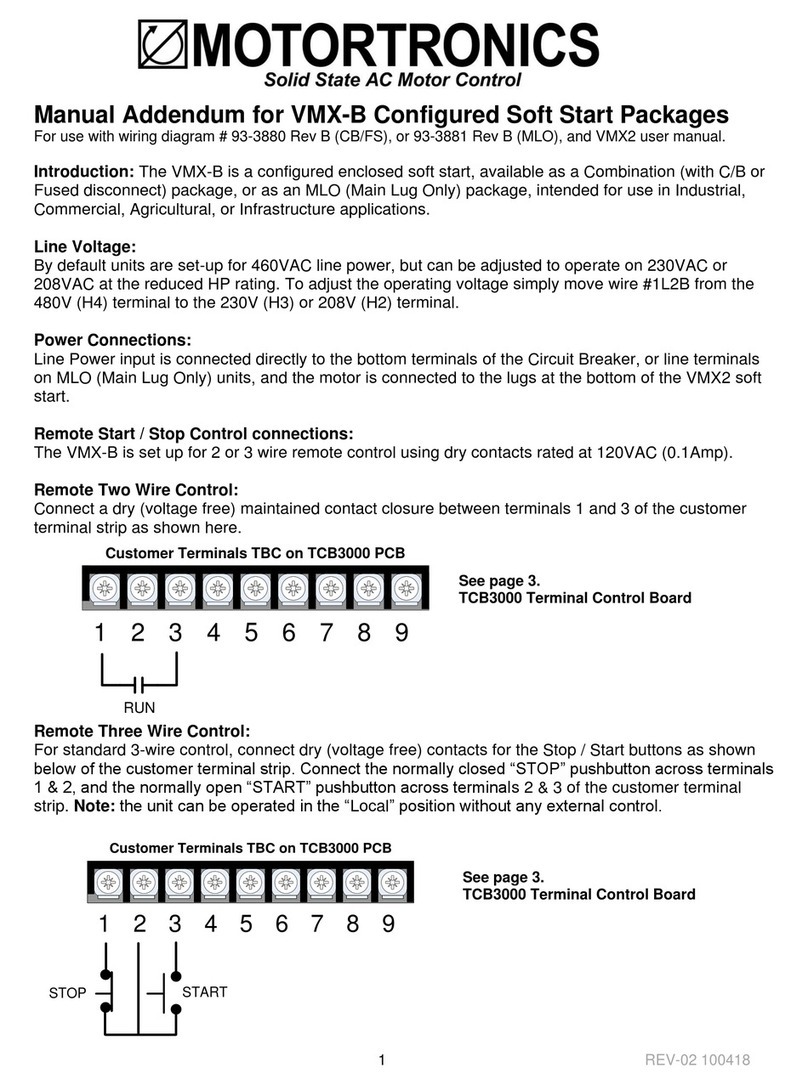
motortronics
motortronics VMX-B Soft Start Packages Manual addendum
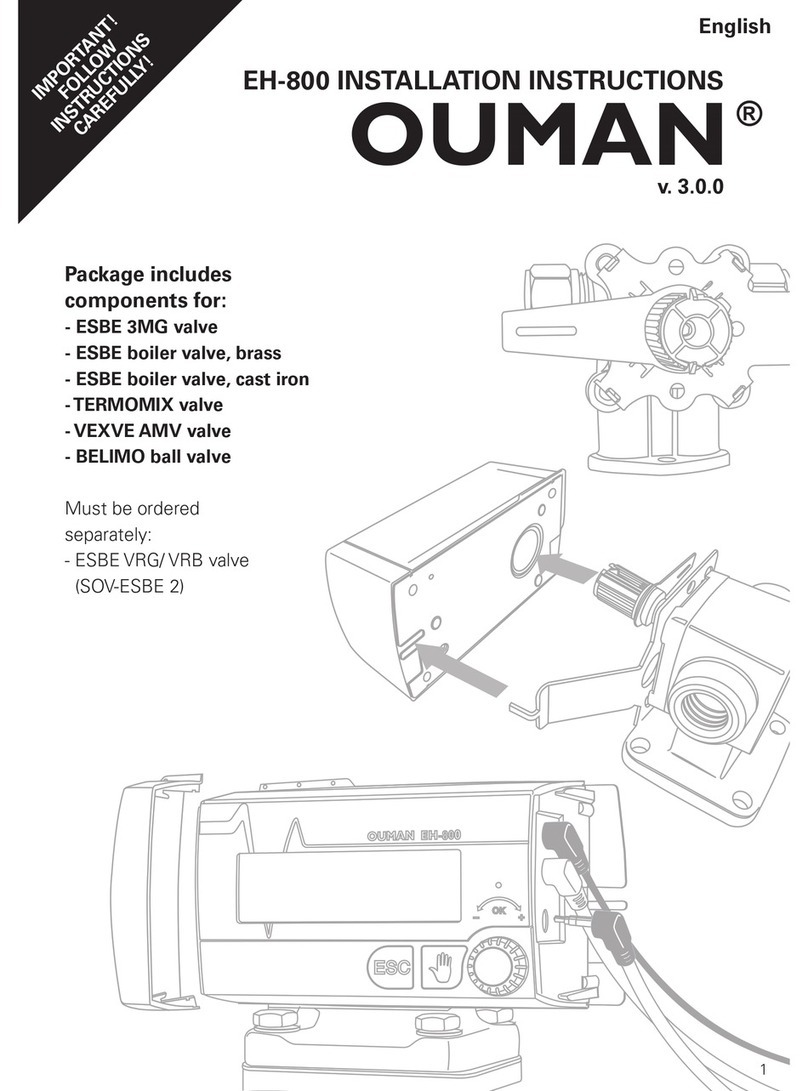
OUMAN
OUMAN EH-800 installation instructions