Yamaha FLIP-X Series User manual

EMA0185150
E51
Ver. 1.50
YAMAHA SINGLE-AXIS ROBOT
Maintenance Manual
FLIP-X Series
T4L/T4LH/T5L/T5LH/T6L/T9/T9H
F8/F8L/F8LH/F10/F10H/F14/F14H/F17/F17L/F20/F20N
GF14XL/GF17XL
N15/N15D/N18/N18D
B10/B14/B14H
R5/R10/R20
FLIP-X_maint_E_V1.50.indb 1 18/05/15 15:00

FLIP-X_maint_E_V1.50.indb 2 18/05/15 15:00

CONTENTS FLIP-X
Maintenance Manual
T-1
Safety Instructions
1. Safety Information S-1
2. Signal words used in this manual S-2
3. Warning labels S-3
3.1 Warning labels S-3
3.1.1 Warning label messages on robot and controller S-3
3.1.2 Supplied warning labels S-8
3.2 Warning symbols S-9
4. Important precautions for each stage of the robot life cycle S-10
4.1 Precautions for using robots and controllers S-10
4.2 Essential precautions for the linear conveyor module S-11
4.3 Design S-12
4.3.1 Precautions for robots S-12
4.3.2 Precautions for robot controllers S-12
4.4 Moving and installation S-13
4.4.1 Precautions for robots S-13
4.4.2 Precautions for robot controllers S-14
4.5 Safety measures S-16
4.5.1 Safety measures S-16
4.5.2 Installing a safety enclosure S-17
4.6 Operation S-18
4.6.1 Trial operation S-18
4.6.2 Automatic operation S-20
4.6.3 Precautions during operation S-20
4.7 Inspection and maintenance S-22
4.7.1 Before inspection and maintenance work S-22
4.7.2 Precautions during service work S-23
4.8 Disposal S-24
5. Emergency action when a person is caught by robot S-25
6. Cautionsregardingstrongmagneticelds S-25
7. Using the robot safely S-26
7.1 Movement range S-26
7.2 Robot protective functions S-27
7.3 Residual risk S-28
7.4 Special training for industrial robot operation S-28
7.5 KC mark S-29
FLIP-X_maint_E_V1.50.indb 1 18/05/15 15:00

CONTENTS FLIP-X
Maintenance Manual
T-3T-2
7.5.1 EMC standards S-29
7.5.2 Examples of EMC countermeasures S-29
Warranty
Chapter 1 Overview
1. Overview 1-1
Chapter 2 Periodic inspection
1. Before beginning work 2-1
2. Periodic inspection 2-2
2.1 Daily inspection 2-2
2.2 Three-month inspection 2-3
2.3 Six-month inspection 2-5
2.4 Three-year inspection 2-6
3. Applying the grease 2-7
3.1 T4L/T4LH/T5L/T5LH/T6L 2-8
3.2 T9/T9H/F10/F10H/F14/F14H/F17/F17L/F20/F20N/GF14XL/GF17XL 2-9
3.3 F8/F8L/F8LH 2-10
3.4 N15/N15D/N18/N18D 2-11
3.5 B10/B14/B14H 2-12
Chapter 3 Adjustment
1. Adjusting the alignment (B10/B14/B14H) 3-1
2. Adjusting the timing belt tension (B10/B14/B14H) 3-2
2.1 Adjusting the drive belt tension 3-3
2.2 Adjusting the speed reduction belt tension 3-4
3. Adjusting the timing belt tension (F20N) 3-6
3.1 Installing and removing the cover 3-6
3.1.1 Stroke cover 3-6
3.1.2 Belt cover 3-8
3.1.3 Motor cover 3-9
3.2 Adjusting the timing belt tension 3-10
4. Adjusting shutter looseness (T4L/T4LH/T5L/T5LH/T6L) 3-11
FLIP-X_maint_E_V1.50.indb 2 18/05/15 15:00

CONTENTS FLIP-X
Maintenance Manual
T-3T-2
Chapter 4 Replacement
1. Replacing the shutter (T4L/T4LH/T5L/T5LH/T6L) 4-1
2. Replacing the motor 4-3
2.1 T4L/T4LH/T5L/T5LH/T6L 4-3
2.2 F8/F8L/F8LH 4-5
2.3 B10/B14/B14H 4-8
2.4 F20N 4-9
2.5 N15/N15D/N18/N18D 4-11
2.6 GF14XL/GF17XL 4-15
2.6 Checking the grid position 4-17
3. Replacing the insert (T4L/T4LH/T5L/T5LH/T6L) 4-18
4. Replacing the drive and speed reduction belts (B10/B14/B14H) 4-20
4.1 Replacing the drive belt 4-20
4.2 Replacing the speed reduction belt 4-22
5. Replacing the slider 4-23
5.1 B10/B14/B14H 4-23
5.2 F20N 4-24
6. Replacing the coupling (GF14XL/GF17XL) 4-25
7. Replacing the bushings (GF14XL/GF17XL) 4-27
8. Maintenance parts 4-28
8.1 Consumable parts 4-28
Chapter5 Wiringspecications
1. ACservomotorspecications 5-1
1.1 AC servo motor termination (T4L/T5L) 5-1
1.2 AC servo motor termination (T4LH/T5LH/T6L) 5-2
1.3 AC servo motor termination (F8/F8L/F8LH) 5-3
1.4 AC servo motor termination (T9/T9H/F10/F10H/F14/F14H/F17/F17L/F20) 5-4
1.5 AC servo motor termination (B10/B14/B14H/R5/R10/R20/F20N/N15/N18) 5-5
1.6 Brakecablespecications 5-6
2.Robotcables(DC24Vspecications) 5-7
( T4L / T5L )
2.1 Single-axis robot cables 5-7
2.1.1 Cables for ERCD 5-7
FLIP-X_maint_E_V1.50.indb 3 18/05/15 15:00

CONTENTS FLIP-X
Maintenance Manual
T-4
3. Robotcables(200Vspecications) 5-8
(T4LH/T5LH/T6L/T9/T9H/F8/F8L/F8LH/F10/F10H/F14/F14H/F17/F17L/F20/B10/B14/B14H/R5/R10/R20)
3.1 Single-axis robot cables 5-8
3.1.1 Cables for TS-X 5-8
3.1.2 Cables for SR1-X 5-9
3.1.3 Cables for RDV-X (robot with brake and sensor) 5-10
3.1.4 Cables for RDV-X (robot without brake) 5-12
3.2 Multi-robot cables 5-13
3.2.1 Cables for single-axis multi-robot 5-13
3.2.2 Cables for two-axis multi-robot 5-14
4. Machine harness 5-20
4.1 N15/N15D/N18/N18D 5-20
4.2 F20N 5-21
5. Cables models 5-22
5.1 Single-axis robot cables 5-22
5.2 Multi-robot cables 5-23
FLIP-X_maint_E_V1.50.indb 4 18/05/15 15:00

Contents
1. Safety Information S-1
2. Signal words used in this manual S-2
3. Warning labels S-3
3.1 Warning labels S-3
3.1.1 Warning label messages on robot and controller S-3
3.1.2 Supplied warning labels S-8
3.2 Warning symbols S-9
4.
Important precautions for each stage of the robot life cycle
S-10
4.1 Precautions for using robots and controllers S-10
4.2 Essential precautions for the linear conveyor module S-11
4.3 Design S-12
4.3.1 Precautions for robots S-12
4.3.2 Precautions for robot controllers S-12
4.4 Moving and installation S-13
4.4.1 Precautions for robots S-13
4.4.2 Precautions for robot controllers S-14
4.5 Safety measures S-16
4.5.1 Safety measures S-16
4.5.2 Installing a safety enclosure S-17
4.6 Operation S-18
4.6.1 Trial operation S-18
4.6.2 Automatic operation S-20
4.6.3 Precautions during operation S-20
4.7 Inspection and maintenance S-22
4.7.1 Before inspection and maintenance work S-22
4.7.2 Precautions during service work S-23
4.8 Disposal S-24
5.
Emergency action when a person is caught by robot
S-25
6. Cautions regarding strong magnetic fields S-25
7. Using the robot safely S-26
7.1 Movement range S-26
7.2 Robot protective functions S-27
7.3 Residual risk S-28
7.4 Special training for industrial robot operation S-28
Safety Instructions
FLIP-X_maint_E_V1.50.indb 1 18/05/15 15:00

Safety Instructions
S-1
1. Safety Information
Industrial robots are highly programmable, mechanical devices that provide a large degree of freedom when
performing various manipulative tasks. To ensure safe and correct use of YAMAHA industrial robots and con-
trollers*, carefully read and comply with the safety instructions and precautions in this "Safety Instructions"
guide. Failure to take necessary safety measures or incorrect handling may result in trouble or damage to the
robot and controller, and also may cause personal injury (to installation personnel, robot operator or service
personnel) including fatal accidents.
* The descriptions about the controller stated in this manual also include the contents of the robot driver.
Before using this product, read this manual and related manuals and take safety precautions to ensure cor-
rect handling.
The precautions listed in this manual relate to this product. To ensure safety of the user’s final system that in-
cludes YAMAHA robots, please take appropriate safety measures as required by the user’s individual system.
To use YAMAHA robots and controllers safely and correctly, always comply with the safety rules and instruc-
tions.
• Forspecificsafetyinformationandstandards,refertotheapplicablelocalregulationsandcomplywith
the instructions.
• WarninglabelsattachedtotherobotsarewritteninEnglish,Japanese,ChineseandKorean.Thismanual
isavailableinEnglishorJapanese(orsomepartsinChinese).Unlesstherobotoperatorsorservice
personnel understand these languages, do not permit them to handle the robot.
• CautionsregardingtheofficiallanguageofEUcountries
ForequipmentthatwillbeinstalledinEUcountries,thelanguageusedforthemanuals,warninglabels,
operationscreencharacters,andCEdeclarationsisEnglishonly.
WarninglabelsonlyhavepictogramsorelseincludewarningmessagesinEnglish.Inthelattercase,
messagesinJapaneseorotherlanguagesmightbeadded.
It is not possible to list all safety items in detail within the limited space of this manual. So please note that
it is essential that the user have a full knowledge of safety and also make correct judgments on safety proce-
dures.
Refer to the manual by any of the following methods when installing, operating or adjusting the robot
and controller.
1. Install, operate or adjust the robot and controller while referring to the printed version of the
manual (available for an additional fee).
2. Install, operate or adjust the robot and controller while viewing the disc version of the manual
on your computer screen.
3. Install, operate or adjust the robot and controller while referring to a printout of the necessary
pages from the disc version of the manual.
FLIP-X_maint_E_V1.50.indb 1 18/05/15 15:00

Safety Instructions
S-2
2. Signal words used in this manual
This manual uses the following safety alert symbols and signal words to provide safety instructions that must
be observed and to describe handling precautions, prohibited actions, and compulsory actions. Make sure
you understand the meaning of each symbol and signal word and then read this manual.
wDANGER
This indicates an immediately hazardous situation which, if not avoided, will result in death or serious injury.
wWARNING
This indicates a potentially hazardous situation which, if not avoided, could result in death or serious injury.
cCAUTION
This indicates a potentially hazardous situation which, if not avoided, could result in minor or moderate injury, or
damage to the equipment.
nNOTE
Explains the key point in the operation in a simple and clear manner.
FLIP-X_maint_E_V1.50.indb 2 18/05/15 15:00

Safety Instructions
S-3
3. Warning labels
Warninglabelsshownbelowareattachedtotherobotbodyandcontrollertoalerttheoperatortopotential
hazards. To ensure correct use, read the warning labels and comply with the instructions.
3.1 Warning labels
wWARNING
If warning labels are removed or difficult to see, then the necessary precautions may not be taken, resulting in an
accident.
outside the safety enclosure.
3.1.1 Warning label messages on robot and controller
Word messages on the danger, warning and caution labels are concise and brief instructions. For more specific
instructions, read and follow the "Instructions on this label" described on the right of each label shown below.
See “7.1 Movement range” for details on the robot’s movement range.
■Warning label 1 (SCARA robots, Cartesian robots)
wDANGER
Serious injury may result from contact with a moving robot.
Instructions on this label
• Alwaysinstallasafetyenclosuretokeepallpersons
awayfromtherobotmovementrangeandprevent
injuryfromcontactingthemovingpartoftherobot.
•
Installaninterlockthattriggersemergencystopwhen
thedoororgateofthesafetyenclosureisopened.
• Thesafetyenclosureshouldbedesignedsothatno
onecanenterinsideexceptfromthedoororgate
equippedwithaninterlockdevice.
• Warninglabel1thatcomessuppliedwitharobot
shouldbeaffixedtoaneasy-to-seelocationonthe
doororgateofthesafetyenclosure.
Potential hazard to human body Seriousinjurymayresultfromcontactwithamovingrobot.
To avoid hazard •Keepoutsideoftherobotsafetyenclosureduringoperation.
•Presstheemergencystopbuttonbeforeenteringthesafetyenclosure.
90K41-001470
■Warning label 2 (SCARA robots, Cartesian robots, single-axis robots*)
* Warning label 2 is not attached to some small single-axis robots, but is supplied with the robots.
wWARNING
Moving parts can pinch or crush hands.
Keep hands away from the movable parts of the robot.
Instructions on this label
Usecautiontopreventhandsandfingersfrombeing
pinchedorcrushedbythemovablepartsoftherobot
whentransportingormovingtherobotorduring
teaching.
Potential hazard to human body Movingpartscanpinchorcrushhands.
To avoid hazard Keephandsawayfromthemovablepartsoftherobot.
90K41-001460
FLIP-X_maint_E_V1.50.indb 3 18/05/15 15:00

Safety Instructions
S-4
■Warning label 3 (SCARA robots, Cartesian robots, controllers*)
* Some models
wWARNING
Improper installation or operation may cause serious injury.
Before installing or operating the robot, read the manual and instructions on the warning labels and understand
the contents.
Instructions on this label
• Besuretoreadthewarninglabelandthismanual
carefullytomakeyoucompletelyunderstandthe
contentsbeforeattemptinginstallationandoperation
oftherobot.
• Beforestartingtherobotoperation,evenafteryou
havereadthroughthismanual,readagainthe
correspondingproceduresand"SafetyInstructions".
• Neverinstall,adjust,inspectorservicetherobotin
anymannerthatdoesnotcomplywiththe
instructionsinthismanual.
Potential hazard to human body Improperinstallationoroperationmaycauseseriousinjury.
To avoid hazard Beforeinstallingoroperatingtherobot,readthemanualandinstructionsonthe
warninglabelsandunderstandthecontents.
90K41-001290
■Warning label 4 (SCARA robots*)
* This label is not attached to omnidirectional type SCARA robots.
cCAUTION
Do not remove the parts on which Warning label 4 is attached.
Doing so may damage the ball screw.
Instructions on this label
TheZ-axisballscrewwillbedamagediftheupperend
mechanicalstopperontheZ-axissplineisremovedor
moved.Neverattempttoremoveormoveit.
90K41-001520
■Warning label 5 (Cartesian robots*, single-axis robots*)
* Some robot models
wWARNING
Ground the controller to prevent electrical shock.
Ground terminal is located inside this cover.
Read the manual for details.
Instructions on this label
• Highvoltagesectioninside
• Topreventelectricalshock,besuretogroundthe
robotusingthegroundterminal.
Potential hazard to human body Electricalshock
To avoid hazard Groundthecontroller.
90K41-001480
FLIP-X_maint_E_V1.50.indb 4 18/05/15 15:00

Safety Instructions
S-5
■Warming label 6 (Robot drivers RDV-X/RDV-P)
wWARNING
10 minutes or longer to prevent electrical shock. Otherwise, burn or electrical shock may result.
Instructions on this label
• Thisindicatesahighvoltageispresent.
Touchingtheterminalblockorconnectormaycause
electricalshock.
• Thisindicatesimportantinformationthatyoumust
knowisdescribedinthemanual.
Beforeusingtherobotdriver,besuretoreadthe
manualthoroughly.
• Besuretogroundthegroundterminaltoavoid
electricalshock.
• Usenonflammablemetalplatesforthematerialof
theinstallationwallsurface.
Otherwise,firemayresult.
Potential hazard to human body To avoid hazard
Electricalshock Donottouchtheterminalsectionfor10minutesafterpower-off.
Improperinstallationoroperationmaycause
seriousinjury.
Beforeinstallingoroperatingtherobot,readthemanualandinstructions
onthewarninglabelsandunderstandthecontents.
Electricalshock Besuretogroundthegroundterminal.
3T034156-1/NE63012
■Warming label 7 (controllers TS-X/TS-P)
wWARNING
10 minutes to avoid burns or electrical shock.
cCAUTION
Instructions on this label
• Thisindicatesahighvoltageispresent.
Touchingtheterminalblockorconnectormaycause
electricalshock.
• Thisindicatestheareaaroundthissymbolmay
becomeveryhot.
Motorsandheatsinksbecomehotduringandshortly
afteroperation.Donottouchthemtoavoidburns.
• Thisindicatesimportantinformationthatyoumust
knowisdescribedinthemanual.
Beforeusingthecontroller,besuretoreadthe
manualthoroughly.
Whenaddingexternalsafetycircuitsorconnectinga
powersupplytothecontroller,readthemanual
carefullyandmakechecksbeforebeginningthe
work.
• Besuretogroundthegroundterminaltoavoid
electricalshock.
Potential hazard to human body To avoid hazard
Electricalshock Donottouchtheterminalsectionfor10minutesafterpower-off.
Donottouchthemtoavoidburns. Donottouchthemotorsandheatsinksduringpower-on.
Improperinstallationoroperationmaycause
seriousinjury.
Beforeinstallingoroperatingtherobot,readthemanualandinstructions
onthewarninglabelsandunderstandthecontents.
Electricalshock Besuretogroundthegroundterminal.
90K41-000950
FLIP-X_maint_E_V1.50.indb 5 18/05/15 15:01

Safety Instructions
S-6
■Warming label 8 (controllers RCX240, controllers RCX340, controllers RCX340XE)
wWARNING
These are precautions for YAMAHA and distributors' service personnel.
Customers must not attempt to open the covers.
wWARNING
Wait at least 100 seconds after power-off before opening the covers.
Instructions on this label
• Waitatleast100secondsafterpower-off
beforeopeningthecovers(*).
• Somepartsinthecontrollerstillretainahigh
voltageevenafterpower-off,soelectrical
shockmayoccurifthosepartsaretouched.
Potential hazard to human body Electricalshock
To avoid hazard Waitatleast100secondsafterpower-offbeforeopeningthecovers(*).
* These are precautions for YAMAHA and distributors' service personnel. Customers must not attempt to open the covers.
90K41-001390
■Warning label 9 (single-axis linear motor robots)
cCAUTION
A magnetic scale is located inside this cover. Bringing a magnet close to it may cause malfunction.
Instructions on this label
• Topreventtherobotfromoperatingimproperlydue
tomagneticscalemalfunction,donotbringastrong
magnettothecover.
• Donotbringtoolsclosetothemagneticscale.
90K41-001510
■Warning label 10 (single-axis linear motor robots)
cCAUTION
Powerful magnets are installed in the robot.
Do not attempt to disassemble the robot to avoid possible injury.
Do not bring any device that may malfunction due to magnetic fields close to the robot.
Instructions on this label
Besuretoread"6.Cautionsregardingstrongmagnetic
fields"in"SafetyInstructions"andmakesureyoufully
understanditscontentsbeforehandlingoroperating
therobot.
Potential hazard to human body Injuryordeathmayresultinsomecases.
To avoid hazard Makeyouunderstandtheprecautionsregardingstrongmagneticfields.
90K41-001500
FLIP-X_maint_E_V1.50.indb 6 18/05/15 15:01

Safety Instructions
S-7
■Warning label 11 (Controller)*
* This label is attached to the front panel.
cCAUTION
Refer to the manual.
取扱説明書参照
READ INSTRUCTION
MANUAL
Instructions on this label
Thisindicatesimportantinformationthatyoumust
knowandisdescribedinthemanual.
Beforeusingthecontroller,besuretoreadthemanual
thoroughly.
Whenaddingexternalsafetycircuitsorconnectinga
powersupplytothecontroller,readthemanual
carefullyandmakechecksbeforebeginningthework.
Connectorshaveanorientation.Inserteachconnector
inthecorrectdirection.
93005-X0-00
■Warning label 12 (single-axis robots, Cartesian robots*)
* Some robot models
wWARNING
If a load is applied to the motor cover, this may cause breakage.
The robot may drop at installation, causing personal injury.
Instructions on this label
• Donottransporttherobotbyholdingthemotor
cover.
Potential hazard to human body Personalinjurymayresult.
To avoid hazard Donotholdthemotorcover.
90K41-001850
FLIP-X_maint_E_V1.50.indb 7 18/05/15 15:01

Safety Instructions
S-8
3.1.2 Supplied warning labels
Some warning labels are not affixed to robots but included in the packing box. These warning labels should be
affixed to an easy-to-see location.
Warning label is attached to the robot body.
Warning label comes supplied with the robot and should be affixed to an easy-to-see location on the door or gate of the
safety enclosure.
Warning label comes supplied with the robot and should be affixed to an easy-to-see location.
SCARA
robots
Cartesian
robots
Single-axis
robots
Warning
label 1
*1
Warning
label 2 *1*2
Warning
label 3 *1
*1: See "Part names" in each SCARA robot manual for label positions.
*2: This label is not attached to some small single-axis robots, but is supplied with the robots.
FLIP-X_maint_E_V1.50.indb 8 18/05/15 15:01

Safety Instructions
S-9
3.2 Warning symbols
Warningsymbolsshownbelowareindicatedontherobotsandcontrollerstoalerttheoperatortopotential
hazards. To use the YAMAHA robot safely and correctly always follow the instructions and cautions indicated
by the symbols.
1. Electrical shock hazard symbol
wWARNING
Touching the terminal block or connector may cause electrical shock, so use caution.
Instructions by this symbol
Thisindicatesahighvoltageispresent.
Touchingtheterminalblockorconnectormaycause
electricalshock.
93006-X0-00
2. High temperature hazard symbol
wWARNING
Motors, heatsinks, and regenerative units become hot, so do not touch them.
Instructions by this symbol
Thisindicatestheareaaroundthissymbolmaybecome
veryhot.
Motors,heatsinks,andregenerativeunitsbecomehot
duringandshortlyafteroperation.Toavoidburnsbe
carefulnottotouchthosesections.
93008-X0-00
3. Caution symbol
cCAUTION
Always read the manual carefully before using the controller.
!
Instructions by this symbol
Thisindicatesimportantinformationthatyoumust
knowandisdescribedinthemanual.
Beforeusingthecontroller,besuretoreadthemanual
thoroughly.
Whenaddingexternalsafetycircuitsorconnectinga
powersupplytothecontroller,readthemanual
carefullyandmakechecksbeforebeginningthework.
Connectorsmustbeattachedwhilefacingacertain
direction,soinserteachconnectorinthecorrect
direction.
93007-X0-00
FLIP-X_maint_E_V1.50.indb 9 18/05/15 15:01

Safety Instructions
S-10
4.
Important precautions for each stage of the robot life cycle
This section describes major precautions that must be observed when using robots and controllers. Be sure to
carefully read and comply with all of these precautions even if there is no alert symbol shown.
4.1 Precautions for using robots and controllers
General precautions for using robots and controllers are described below.
1. Applications where robots cannot be used
YAMAHA robots and robot controllers are designed as general-purpose industrial equipment and cannot be used for the
following applications.
wDANGER
YAMAHA robot controllers and robots are designed as general-purpose industrial equipment and cannot be used
for the following applications.
2. Qualification of operators/workers
Operators or persons who perform tasks for industrial robots (such as teaching, programming, movement check, inspec-
tion, adjustment, and repair) must receive appropriate training and also have the skills needed to perform the tasks
correctly and safely.
Those tasks must be performed by qualified persons who meet requirements established by local regulations and stan-
dards for industrial robots. They must also read the manual carefully and understand its contents before attempting the
robot operation or maintenance.
wWARNING
robots.
above qualifications. Any attempt to perform such tasks by an unqualified person may cause an accident
resulting in serious injury or death.
FLIP-X_maint_E_V1.50.indb 10 18/05/15 15:01

Safety Instructions
S-11
4.2 Essential precautions for the linear conveyor module
The linear conveyor module is a YAMAHA robot so safety measures must be followed and safety equipment
must be installed just as required for other YAMAHA robots.
This section describes essential precautions for handling the linear conveyor module. Precautions for each
stage in the robot life cycle are listed from the next section, so be sure to read the whole section of this "Safety
Instructions".
1. Slider ejection
wDANGER
The slider and workpieces ejected at high SPEED from the linear conveyor module may strike persons, causing
serious and POSSIBLY fatal injuries. Please comply with the following points.
conveyor guide
slider and workpieces from the linear conveyor are not ejected outside of the enclosure.
2. Preventing electrical shock
wDANGER
Always comply with the instructions in this manual when installing, operating and inspecting the linear conveyor
module. Failure to do so may lead to electrical shock, serious injury or even death. Please comply with the
following items:
the termination module.
power before starting maintenance tasks.
turn off the power.
3. Strong magnetic field
wWARNING
The linear conveyor module contains powerful permanent magnets and electromagnets that generate strong
magnetic fields. Always comply with the precautions listed in this manual when using the linear conveyor
module. Those persons wearing medical electronic devices such as cardiac pacemakers or hearing aids are at
particular risk of major injury or even death.
removing it from the linear conveyor module’s guide rails.
Do not place any tools near the slider magnets and the linear conveyor motor while the power is on.
4. High temperature hazard
wWARNING
The motor for the linear conveyor module is mounted on the module, and so it is easy to come into contact with.
To allow heat generated during operation to DISSIPATE, install the module on a base made from good heat
conducting material such as metal.
The motor reaches high temperatures during and IMMEDIATELY after operation, so touching it at those times may
cause burns.
Before touching the motor, first turn off the controller power, then wait a while and check that the temperature
has DROPPED sufficiently.
FLIP-X_maint_E_V1.50.indb 11 18/05/15 15:01

Safety Instructions
S-12
4.3 Design
4.3.1 Precautions for robots
1. Restricting the robot moving speed
wWARNING
Restriction on the robot moving speed is not a safety-related function.
To reduce the risk of collision between the robot and workers, the user must take the necessary protective
measures such as enable devices according to risk assessment by the user.
2. Restricting the movement range
See “7.1 Movement range” for details on the robot’s movement range.
wWARNING
Soft limit function is not a safety-related function intended to protect the human body.
To restrict the robot movement range to protect the human body, use the mechanical stoppers installed in the
cCAUTION
3. Provide safety measures for end effector (gripper, etc.)
wWARNING
protection taking into account the object size, weight, temperature, and chemical properties.
4. Provide adequate lighting
Provide enough lighting to ensure safety during work.
5. Install an operation status light
wWARNING
4.3.2 Precautions for robot controllers
1. Emergency stop input terminal
wDANGER
Each robot controller has an emergency stop input terminal to trigger emergency stop. Using this terminal, install
a safety circuit so that the system including the robot controller will work safely.
For the robot driver without emergency stop input terminal, construct a safety circuit including the emergency
2. Maintain clearance
cCAUTION
Do not bundle control lines or communication cables together or in close to the main power supply or power
lines. Usually separate these by at least 100mm. Failure to follow this instruction may cause malfunction due to
noise.
FLIP-X_maint_E_V1.50.indb 12 18/05/15 15:01
Other manuals for FLIP-X Series
1
This manual suits for next models
30
Table of contents
Other Yamaha Robotics manuals
Popular Robotics manuals by other brands

Artec
Artec Robo 2.0 manual
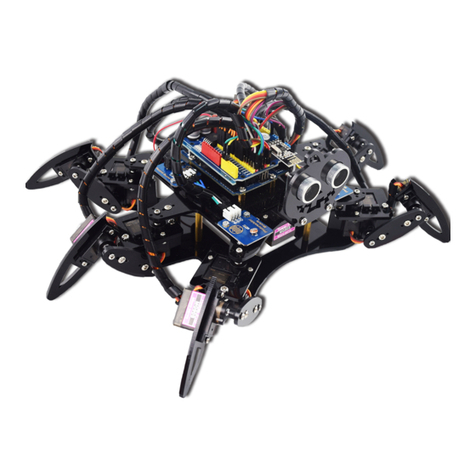
ADEEPT
ADEEPT Hexapod 6 Legs Spider Robot manual

Robosen
Robosen OPTIMUS PRIME ELITE user manual
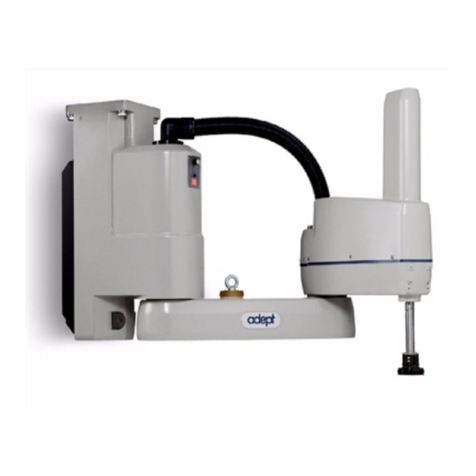
adept technology
adept technology Cobra s800 user guide
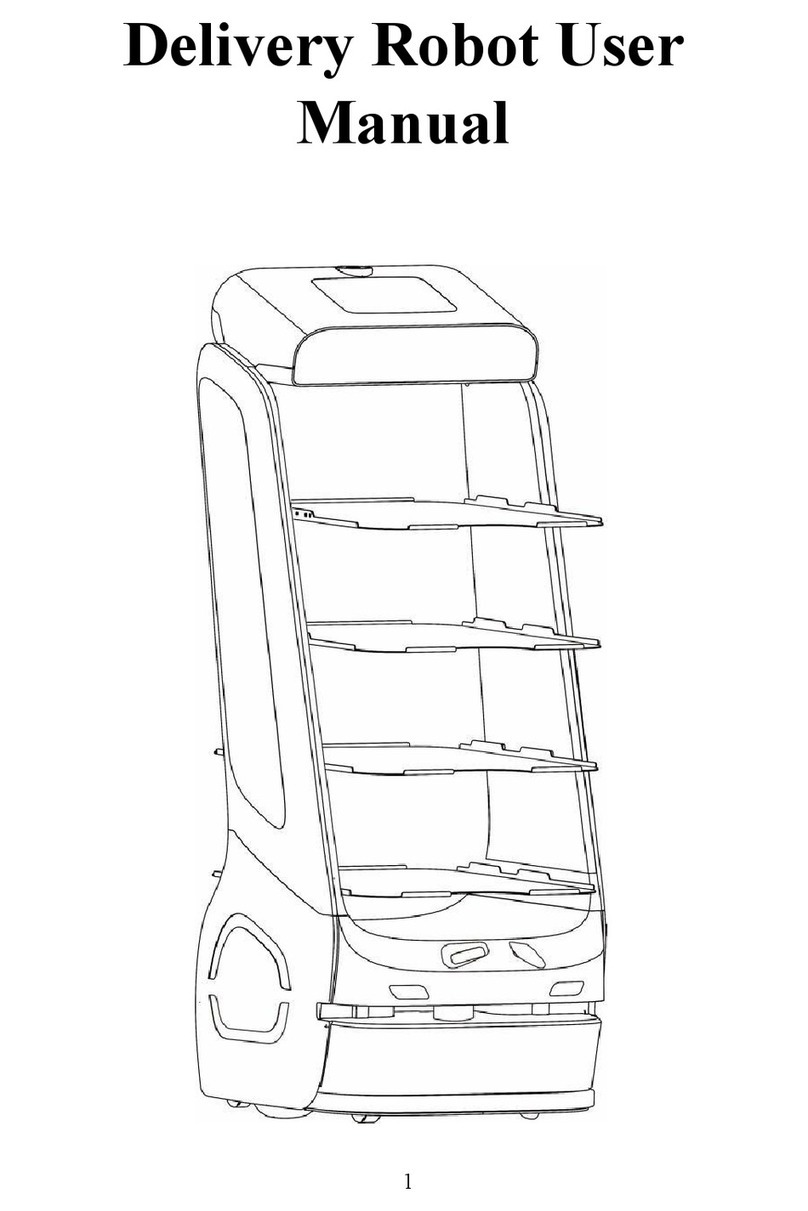
Keenon Robotics
Keenon Robotics T5LS user manual

Mitsubishi Electric
Mitsubishi Electric MELFA RV-SD Series Installation description