Yamaha YP-X Series User manual

OWNER'S MANUAL


Before using the “YP-X” series robot
(Be sure to read the following notes.)
At this time, our thanks for your purchase of this YAMAHA “YP-X” series robot.
The “YP-X” series robot use absolute position detectors that do not require return-to-origin
after turning on the controller power. However, when the controller power is turned on in the
following cases, return-to-origin must be performed just the very first time.
(1) When robot cable was first connected after delivery from YAMAHA.
(2) When robot cable was disconnected from the controller and then reconnected.
(3) When no absolute battery is connected.
(4) When a motor or cable was replaced.
At this point, any of the following errors is issued immediately after controller power is turned
on, but this is not a malfunction. The controller will operate normally by restarting.
When using DRCX or TRCX controllers:
15 : FEEDBACK ERROR 2
23 : ABS.BAT.L-VOLTAGE
24 : ABS.DATA.ERROR
When using a QRCX controller:
17.80 : D?.ABS.encoder backup error
17.81 : D?.ABS.encoder battery alarm
17.85 : D?.ABS.encoder system error
17.92 : D?.ABS.cable disconnected
17.93 : D?.ABS.data overflow
17.94 : D?.ABS.Battery degradation
[1] X, Y, Z axes
X, Y, Z axes use the stroke end origin detection method.
Set the origin position while referring to the following section in the robot controller
instruction manual.
When using DRCX or TRCX controllers:
See “9-1-1 Return-to-origin by the search method” in Chapter 9.
When using a QRCX controller:
See “11-9 Absolute Reset” in Chapter 11.
!
CAUTION
Changing the origin position may cause a positional shift or robot breakdowns,
and should be avoided. Changing the origin detection method might also create
a dangerous situation and should be avoided. If these must be changed, consult
our sales office or dealer.

[2] R axis
On the above robots, the customer should set the origin at the desired position.
Move the robot to the desired position and set it as the origin while referring to the
following section in the robot controller instruction manual.
When using DRCX or TRCX controllers:
See “9-1-1 Return-to-origin by the search method” in Chapter 9.
When using a QRCX controller:
See “11-9 Absolute Reset” in Chapter 11.
After setting the origin position, affix the stickers (triangular stickers supplied with the
robot) to both the tool side and workpiece side so that they can be used as the alignment
marks. Use these marks as the reference position the next time the origin must be set.

Introduction
Our sincere thanks for your purchase of this YAMAHA robot and controller.
The YP-X Series were designed and developed as compact and highspeed Pick
and Place (P&P) robots.
This manual contains important information on items such as an overview, han-
dling, adjustment, and service of YP-X Series robots to ensure correct and effi-
cient use. Please be sure to read this manual before installing the equipment.
Please refer to the "YAMAHA Robot Controller DRCX, TRCX, QRCX Instruc-
tion and Owner's Manual" for detailed information on operation and program-
ming.
NOTES
◆We reserve the right to make future product changes that might not be incorpo-
rated into this manual.
◆We request the customer contact concerning any possible errors, omissions or
misprints etc.
YAMAHA MOTOR CO., LTD.
IM Company

MEMO

CONTENTS
CHAPTER 1 Using the Robot Safely
1 Safety Information................................................... 1-1
2 Essential Caution Items ........................................... 1-2
3 Special Training for Industrial Robot Operation ...... 1-8
4 Robot Safety Functions............................................ 1-9
5 Safety Measures for the System ............................. 1-10
6 Trial Operation ...................................................... 1-11
7 Work Within The Safeguards................................. 1-12
8 Automatic Operation ............................................ 1-13
9 Adjustment and Inspection.................................... 1-13
10 Repair and Modification........................................ 1-13
11 Warranty ............................................................... 1-14
12 CE Markings .......................................................... 1-15
13 Precautions ........................................................... 1-16
CHAPTER 2 Functions
1 P & P robot unit....................................................... 2-1
2 P & P robot controller ............................................. 2-2
CHAPTER 3 Installation
1 Robot Installation Conditions .................................. 3-1
1-1 Installation environments ............................................................... 3-1
2 Installation .............................................................. 3-3
2-1 Installation frame ........................................................................... 3-3
2-2 Installing the robot ......................................................................... 3-4
3 Connection of robot cables ..................................... 3-7
4 Protective Bonding .................................................. 3-9

CHAPTER 4 Adjustment
1 Outline .................................................................... 4-1
1-1 Robot parameter settings ................................................................ 4-2
2 Setting the origin position ....................................... 4-3
2-1 Mark method (R-axis) ..................................................................... 4-4
2-2 Stroke end method (X, Z, Y axes) ................................................... 4-5
3 Adjustment of the belt tension ................................ 4-6
3-1 Adjustment of X,Y, Z axis motor belt tension .................................. 4-6
3-2 Adjustment of Z axis tip belt tension
(YP320X, YP320XR, YP330X, YP340X) .......................................... 4-7
3-3 Adjustment of Z axis tip belt tension (YP220BX, YP220BXR) .......... 4-8
3-4 Adjust the X-axis belt tension (YP220BX, YP220BXR)..................... 4-9
CHAPTER 5 Periodic Inspecition
1 Introduction ............................................................ 5-1
2 Inspection ............................................................... 5-3
2-1 Daily Checklist .............................................................................. 5-3
2-2 Six Month Inspection ..................................................................... 5-4
3 Replacement of Motor ............................................ 5-5
3-1 Replacement of X, Y, Z axis motors
(YP320X, YP330X, YP340X, YP320XR) .......................................... 5-5
3-2 Replacement of X and Z axis motor (YP220BX, YP220BXR) ........... 5-7
3-3 Replacement of R axis motor (YP220BXR, YP320XR, YP340X) ....... 5-8
4 Belt replacement method ........................................ 5-9
4-1 Replacement of the X and Z axis belts
(YP320X, YP330X, YP340X, YP320XR) .......................................... 5-9
4-2 Replacement of Y axis belt (YP330X, YP340X) ............................. 5-10
4-3 Replacement of Z axis belt (YP220BX, YP220BXR) .......................5-11
4-4 Replacement of X axis belt (YP220BX, YP220BXR) ...................... 5-12
4-5 Replacement of Z axis tip section belt
(YP320X, YP330X, YP340X, YP320XR) ........................................ 5-13
4-6 Replacement of Z axis tip section belt (YP220BX, YP220BXR) ..... 5-14
5 Sample troubleshooting......................................... 5-15
6 Spare parts list....................................................... 5-17

CHAPTER 6 Specifications
1 P & P robot unit....................................................... 6-1
1-1 Basic specifications ........................................................................ 6-1
1-2 Robot External Views ..................................................................... 6-2
1-3 Table of robot control signals ......................................................... 6-8
1-4 Piping and wiring of robot ........................................................... 6-14
2 R axis allowable moment/inertia moment ............. 6-18
2-1 R axis allowable moment/inertia moment .................................... 6-18
2-2 Equation for moment of inertia calculation .................................. 6-19
2-3 Example of moment of inertia calculation .................................... 6-21
3 Robot allowable duty ............................................ 6-23
4 Allowable overhang .............................................. 6-24
5 X-axis droop .......................................................... 6-25
6 Mechanical stopper ............................................... 6-26

MEMO

1 Safety Information ......................................... 1-1
2 Essential Caution Items .................................. 1-2
3
Special Training for Industrial Robot Operation ....
1-8
4 Robot Safety Functions .................................. 1-9
5 Safety Measures for the System ................... 1-10
6 Trial Operation ............................................ 1-11
7 Work Within The Safeguards ....................... 1-12
8 Automatic Operation................................... 1-13
9 Adjustment and Inspection .......................... 1-13
10 Repair and Modification .............................. 1-13
11 Warranty ..................................................... 1-14
12 CE Markings................................................. 1-15
13 Precautions .................................................. 1-16
CHAPTER 1
Using the Robot Safely

MEMO

CHAPTER 1 Using the Robot Safely
1-1
1 Safety Information
Industrial robots are highly programmable, mechanical devices that provide a
large degree of freedom when performing various manipulative tasks.
To ensure correct and safe use of YAMAHA industrial robots, carefully read this
manual and make yourself well acquainted with the contents. FOLLOW THE
WARNINGS, CAUTIONS AND INSTRUCTIONS INCLUDED IN THIS
MANUAL. Failure to take necessary safety measures or mishandling due to not
following the instructions in this manual may result in trouble or damage to the
robot and injury to personnel (robot operator or service personnel) including fatal
accidents.
Warning information in this manual is shown classified into the following items.
Failure to follow DANGER instructions will result in severe injury or
death to the robot operator, a bystander or a person inspecting or
repairing the robot.
Failure to follow WARNING instructions could result in severe in-
jury or death to the robot operator, a bystander or a person inspect-
ing or repairing the robot.
Failure to follow CAUTION instructions may result in injury to the robot
operator, a bystander or a person inspecting or repairing the robot, or dam-
age to the robot and/or robot controller.
It is not possible to detail all safety items within the limited space of this manual.
So it is essential that the user have a full knowledge of basic safety rules and also
that the operator makes correct judgments on safety procedures during operation.
This manual and warning labels supplied with or affixed to the robot are written
in English. If the robot operator or service personnel does not understand Eng-
lish, do not permit him (or her) to handle the robot.
!DANGER
WARNING
!
CAUTION

CHAPTER 1 Using the Robot Safely
1-2
2 Essential Caution Items
Particularly important cautions for handling or operating the robot are described
below. In addition, safety information about installation, operation, inspection
and maintenance is provided in each chapter. Be sure to comply with these in-
structions to ensure safe use of the robot.
(1) Observe the following cautions during automatic operation.
Warning labels 1 (Fig. 1-1) are affixed to the robot.
• Install a safeguard (protective enclosure) to keep any person from entering
within the movement range of the robot and suffering injury due to being
struck by moving parts.
• Install a safety interlock that triggers emergency stop when the door or
panel is opened.
• Install safeguards so that no one can enter inside except from doors or
panels equipped with safety interlocks.
• The warning labels 1 shown in Fig. 1-1 are supplied with the robot and
should be affixed to a conspicuous spot on doors or panels equipped with
safety interlocks.
!DANGER
Serious injury or death will result from impact with moving robot.
• Keep outside of guard during operation.
• Lock out power before approaching robot.
(2) Use caution to prevent hands or fingers from being pinched or crushed.
Warning labels 2 (Fig. 1-2) are affixed to the robot.
WARNING
Moving parts can pinch or crush.
Keep hands away from robot arms.
■Fig. 1-1 Warning label 1 ■Fig. 1-2 Warning label 2
DANGER
Serious injury or death
will result from impact
with moving robot.
•Keep outside of guard
during operation.
•Lock out power before
approaching robot.
Moving parts can
pinch or crush.
Keep hands away
from robot arms.
WARNING

CHAPTER 1 Using the Robot Safely
1-3
(3) Follow the instructions on warning labels and in this manual.
Warning label 3 (see Fig. 1-3) is supplied with the robot and should be af-
fixed to the robot or a conspicuous spot near the robot.
• Be sure to read the warning label and this manual carefully and make your
thoroughly understand the contents before attempting installation and op-
eration of the robot.
• Before starting the robot operation, even after you have read through this
manual, read again the corresponding procedures and cautions in this manual
as well as descriptions in the this chapter (Chapter 1, “Using the Robot
Safely”).
• Never install, adjust, inspect or service the robot in any manner that does
not comply with the instructions in this manual.
WARNING
Improper installation or operation can result in serious injury or
death.
Read owner’s manual and all warning labels before operation.
■Fig. 1-3 Warning label 3
Improper Installation or operation
can result in serious injury or
death.
Read owner's manual and all
warning labels before operation.
WARNING

CHAPTER 1 Using the Robot Safely
1-4
(4) Do not use the robot in environments containing inflammable gas, etc.
WARNING
•This robot was not designed for operation in environments where
inflammable or explosive substances are present.
•Do not use the robot in environments containing inflammable gas,
dust or liquids. Explosions or fire could otherwise result.
(5) Do not use the robot in locations possibly subject to electromagnetic
interference, etc.
WARNING
Avoid using the robot in locations subject to electromagnetic inter-
ference, electrostatic discharge or radio frequency interference.
Malfunction may otherwise occur.
(6) Use caution when releasing the Z-axis (vertical axis) brake.
WARNING
The Z-axis will slide down when the Z-axis brake is released, caus-
ing a hazardous situation.
•Press the emergency stop button and prop up the Z-axis with a
support stand before releasing the brake.
•Use caution not to let your body get caught between the Z-axis
and installation base when releasing the brake to perform direct
teach.
(7) Provide safety measures for end effector (gripper, etc.).
WARNING
•End effectors must be designed and manufactured so that they
cause no hazards (for example, loosening of workpiece) even if
power (electricity, air pressure, etc.) is shut off or power fluctua-
tions occur.
•If there is a possible danger that the object gripped by the end
effector may fly off or drop, then provide appropriate safety pro-
tection taking into account the object size, weight, temperature
and chemical properties.

CHAPTER 1 Using the Robot Safely
1-5
(8) Use the following caution items when removing the Z-axis motor.
WARNING
The Z-axis will drop when the Z-axis motor is removed, possibly
resulting in injury.
•Turn off the controller and set a support stand under the Z-axis
before removing the motor.
•Use caution not to allow hands or body to be squeezed or crushed
by moving parts on the Z-axis or between the Z-axis and the in-
stallation base.
(9) Use the following caution during inspection of controller.
WARNING
•When you need to touch the terminals or connectors on the out-
side of the controller during inspection, always first turn off the
controller power switch and also the power source in order to
prevent possible electrical shock.
•Never touch any internal parts of the controller.
•For more specific safety items on the controller, refer to the
YAMAHA Robot Controller Owner’s Manual.
(10) Consult us for corrective action when the robot is damaged or malfunc-
tion occurs.
WARNING
If any part of the robot is damaged or any malfunction occurs, con-
tinuous operation may be very dangerous. Please consult YAMAHA
dealer for corrective action.
Damage or Trouble Possible Danger
Damage to machine harness or robot cable Electrical shock, malfunction of robot
Damage to exterior of robot Flying outwards of damaged parts during robot
operation
Abnormal operation of robot
(positioning error, excessive vibration, etc.) Malfunction of robot
Z-axis brake trouble Dropping of load

CHAPTER 1 Using the Robot Safely
1-6
(11) Use caution not to touch the cooling fan on the controller rear panel.
WARNING
•Bodily injury may occur from coming into contact with the cool-
ing fan while it is rotating.
•When removing the fan cover for inspection, first turn off the con-
troller and make sure the fan has stopped.
(12) Use caution not to touch the high temperature part of the motor.
WARNING
The motor is extremely hot after automatic operation, so burns may
occur if it is touched.
Before touching the motor during inspections or servicing, turn off
the controller, wait for a while and check that the temperature has
cooled.
(13) Do not remove, alter or stain the warning labels.
WARNING
If warning labels are removed or difficult to see, necessary cau-
tions may not be taken, resulting in an accident.
•Do not remove, alter or stain the warning labels on the robot.
•Do not allow the warning labels to be hidden by the device in-
stalled to the robot by the user.
•Provide proper lighting so that the symbols and instructions on
the warning labels can be clearly seen even from the outside of
safeguards.
(14) Protective bonding
WARNING
Be sure to ground the robot and controller to prevent electrical
shock.

CHAPTER 1 Using the Robot Safely
1-7
(15) Be sure to make correct parameter settings.
!
CAUTION
The robot must be operated with correct tolerable moment of inertia and
acceleration coefficients according to the manipulator tip mass and mo-
ment of inertia. If this is not observed, premature end to the life of the drive
units, damage to the robot parts or residual vibration during positioning
may result.
(16) Do not use the robot for tasks requiring motor thrust.
!
CAUTION
Avoid using the robots for tasks which make use of motor thrust (press-
fitting, burr removal, etc.). These tasks may cause malfunctions of the ro-
bot.

CHAPTER 1 Using the Robot Safely
1-8
3 Special Training for Industrial Robot Operation
Companies or factories using industrial robots must make sure that every person,
who handles the robot such as for teaching, programming, movement check, in-
spection, adjustment and repair, has received appropriate training and also has
the skills needed to perform the job correctly and safely.
Since the YAMAHA YP-X Series pick-and-place robots fall under the industrial
robot category, the user must observe local regulations and safety standards for
industrial robots, and provide special training for every person involved in robot-
related tasks (teaching, programming, movement check, inspection, adjustment,
repair, etc.).
This manual suits for next models
6
Table of contents
Other Yamaha Robotics manuals
Popular Robotics manuals by other brands
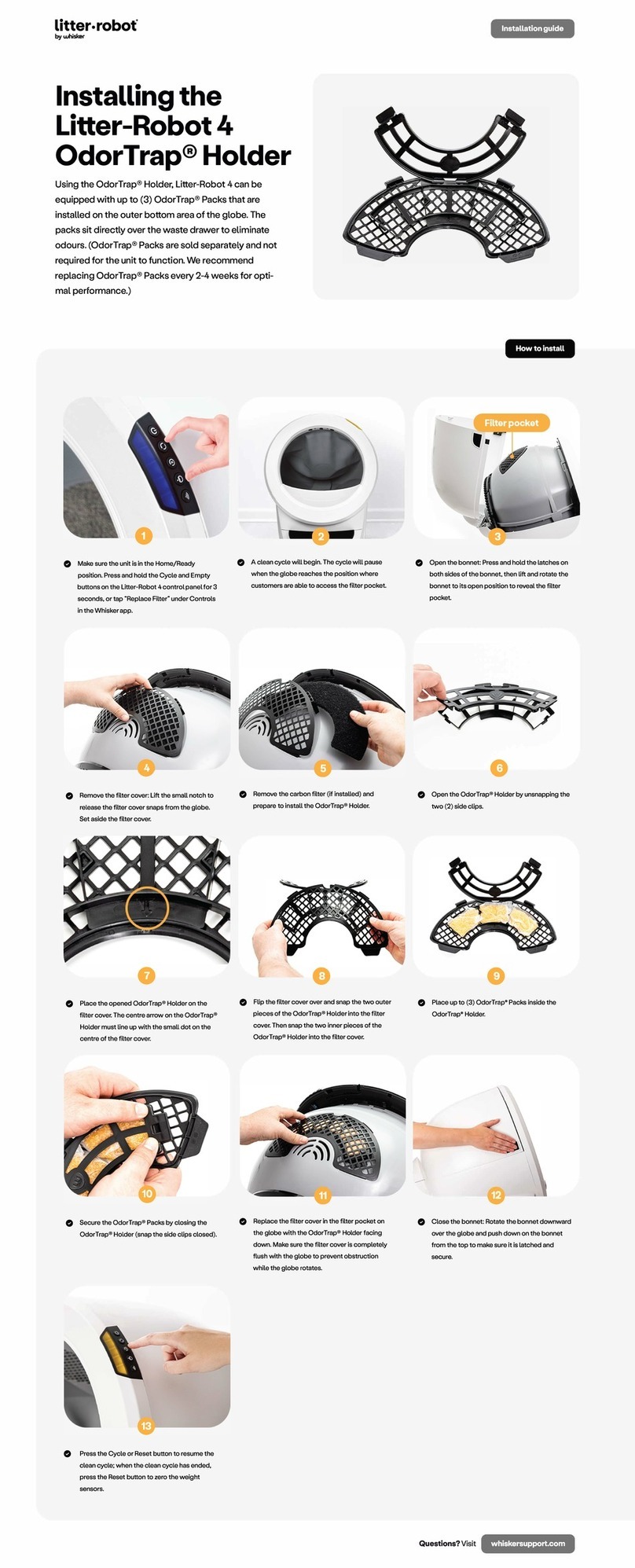
whisker
whisker Litter-Robot 4 OdorTrap Holder 4 installation guide
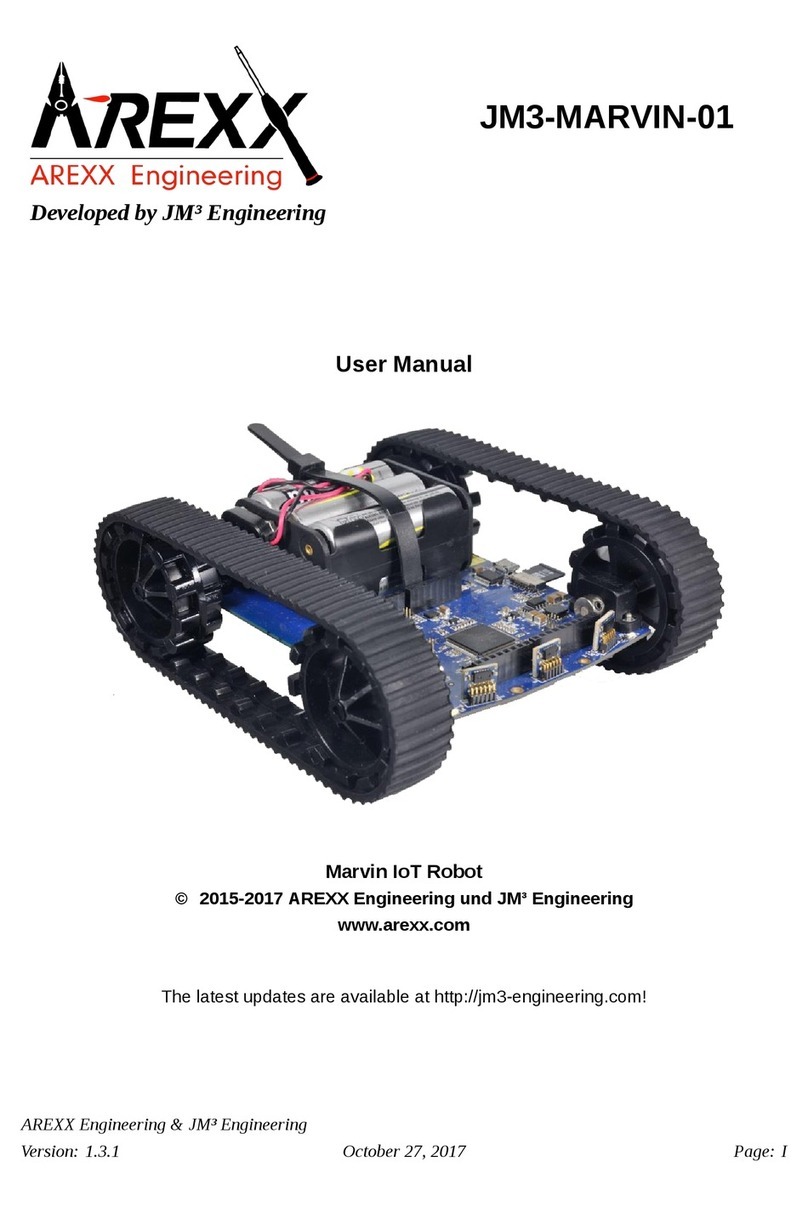
AREXX Engineering & JM3 Engineering
AREXX Engineering & JM3 Engineering Marvin user manual
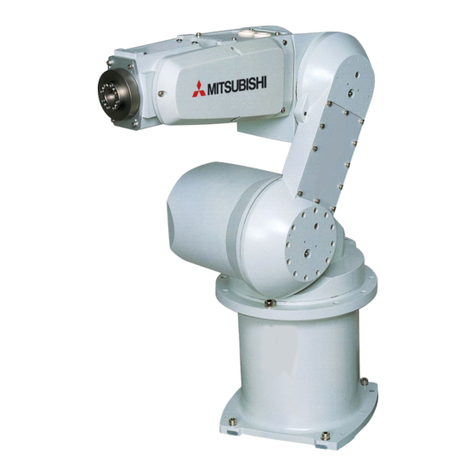
Mitsubishi
Mitsubishi RV-3SJ Series Standard Specifications Manual
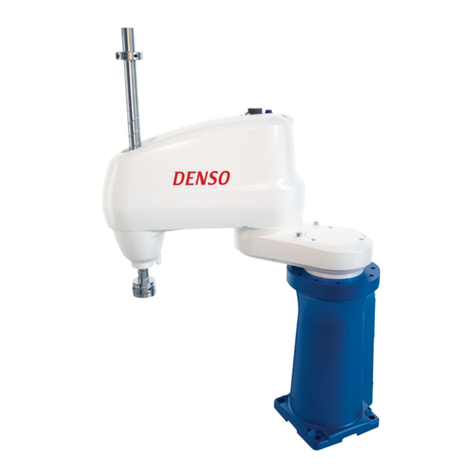
Denso
Denso HS-G Series Installation & maintenance guide
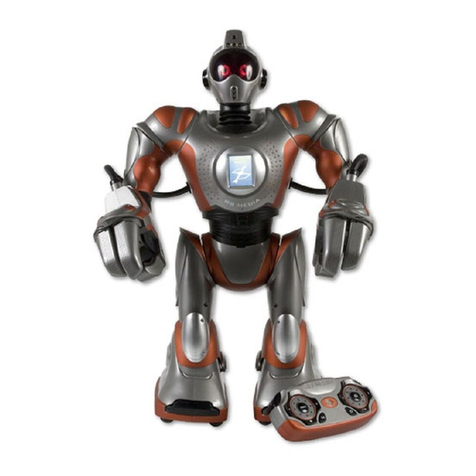
WowWee
WowWee RS Media user manual
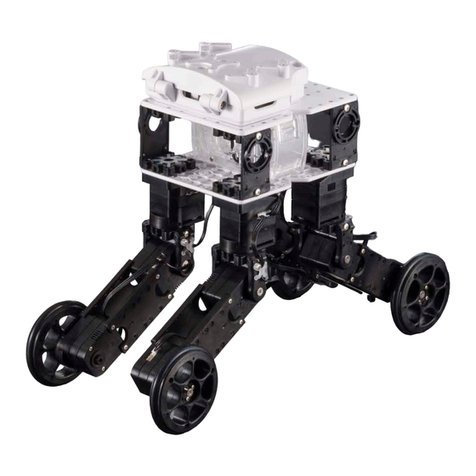
Kondo
Kondo KXR-R4LL Assembly manual

Eddyfi Technologies
Eddyfi Technologies INUKTUN MAGGHD user manual
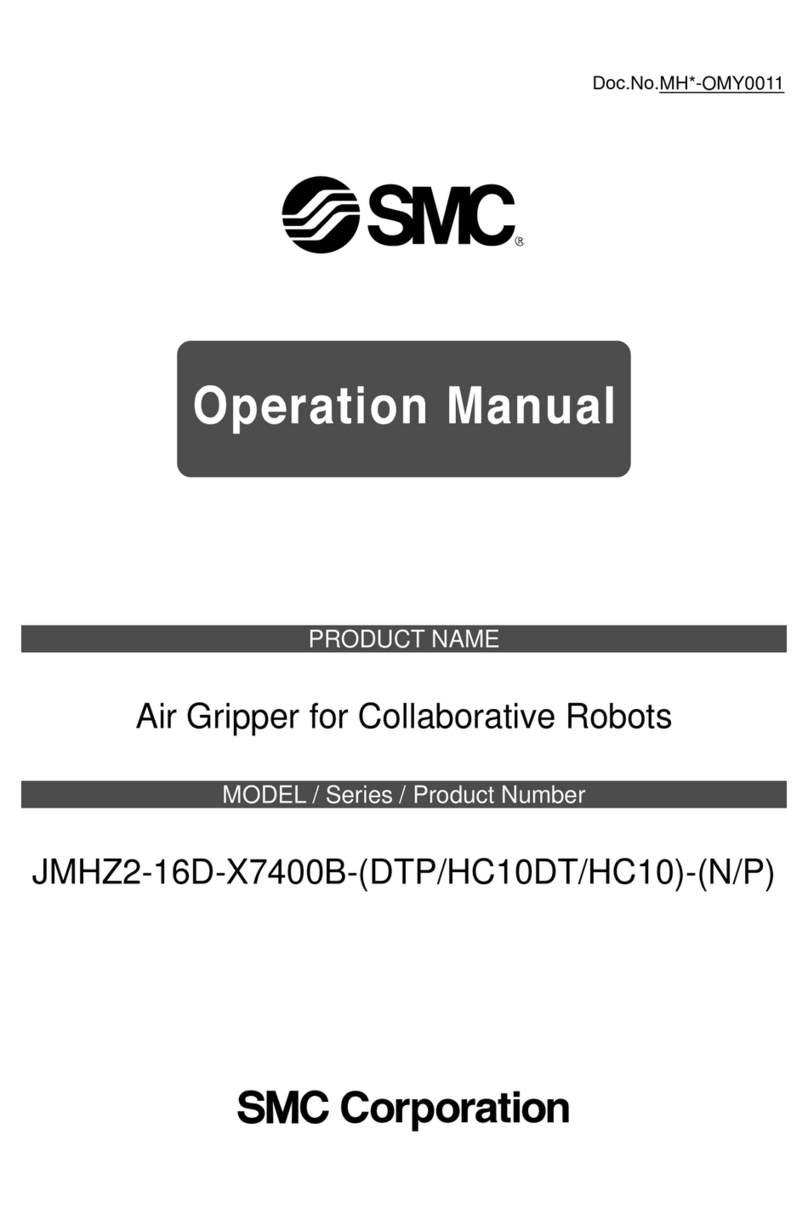
SMC Networks
SMC Networks JMHZ2-16D-X7400B-DTB-N Operation manual
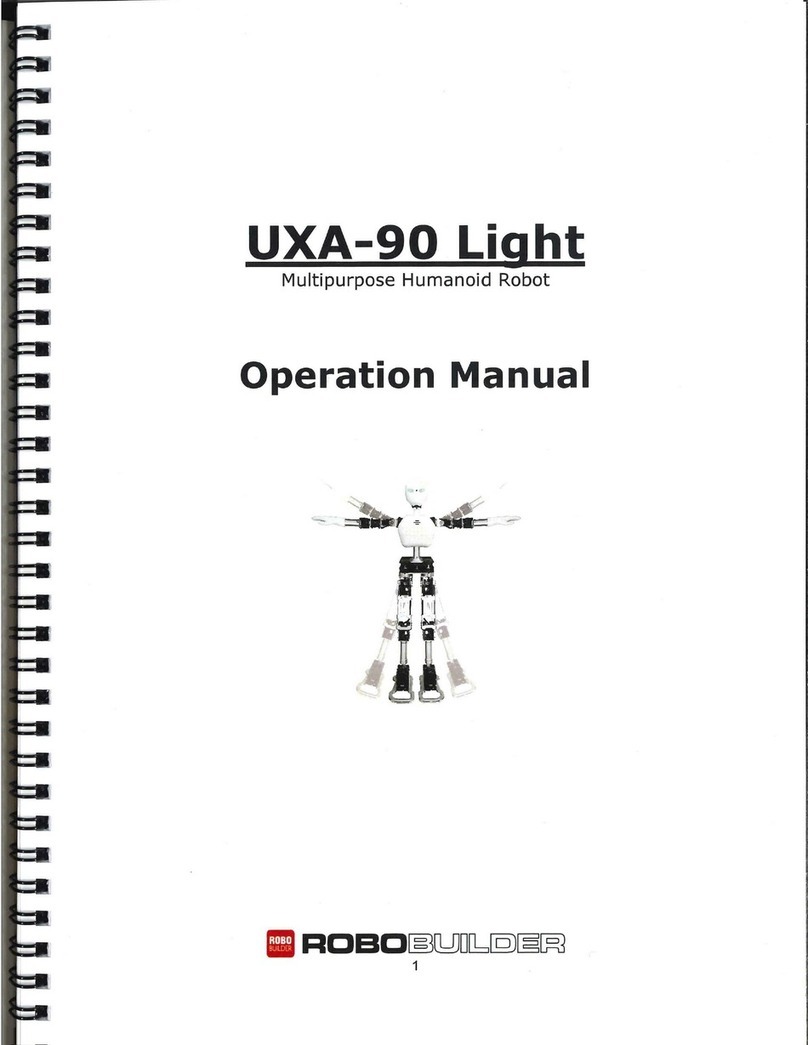
RoboBuilder
RoboBuilder UXA-90 Light Operation manual
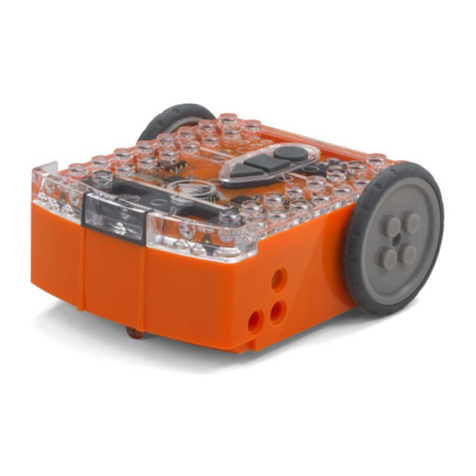
Microbric
Microbric Edison EdMat instructions
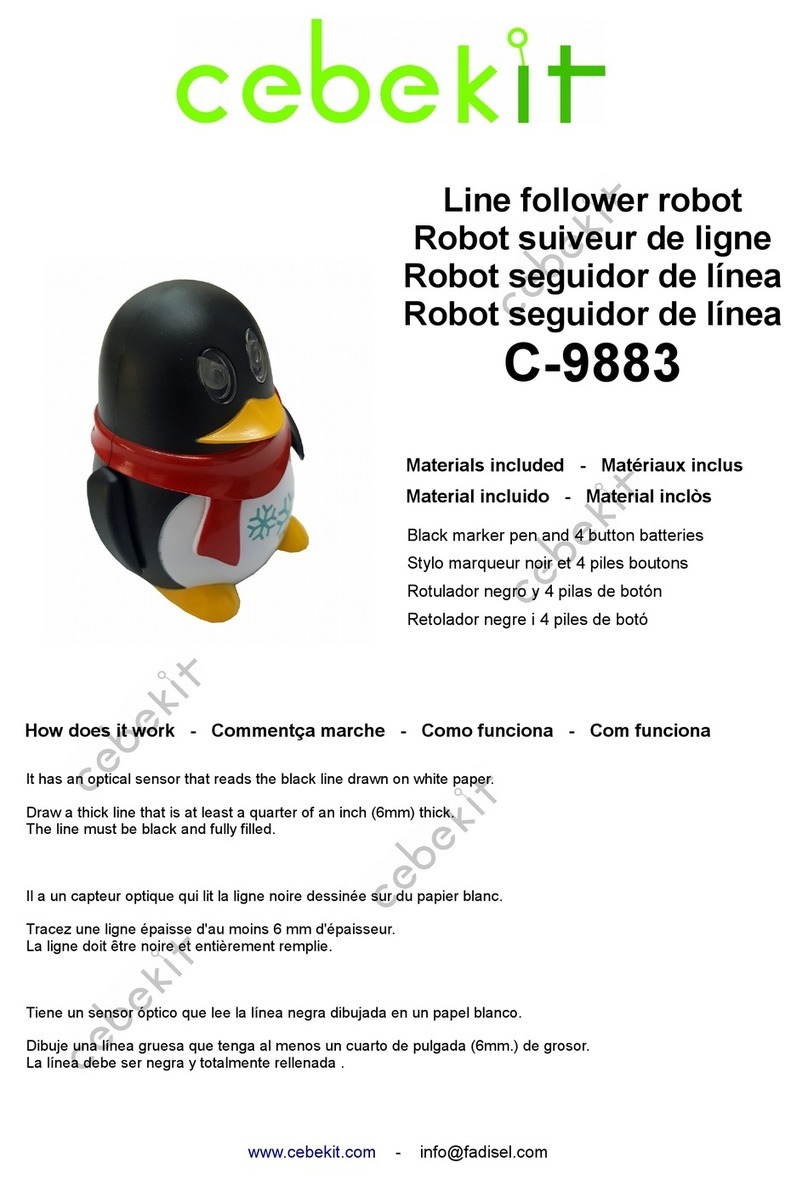
Cebekit
Cebekit C-9883 quick start guide
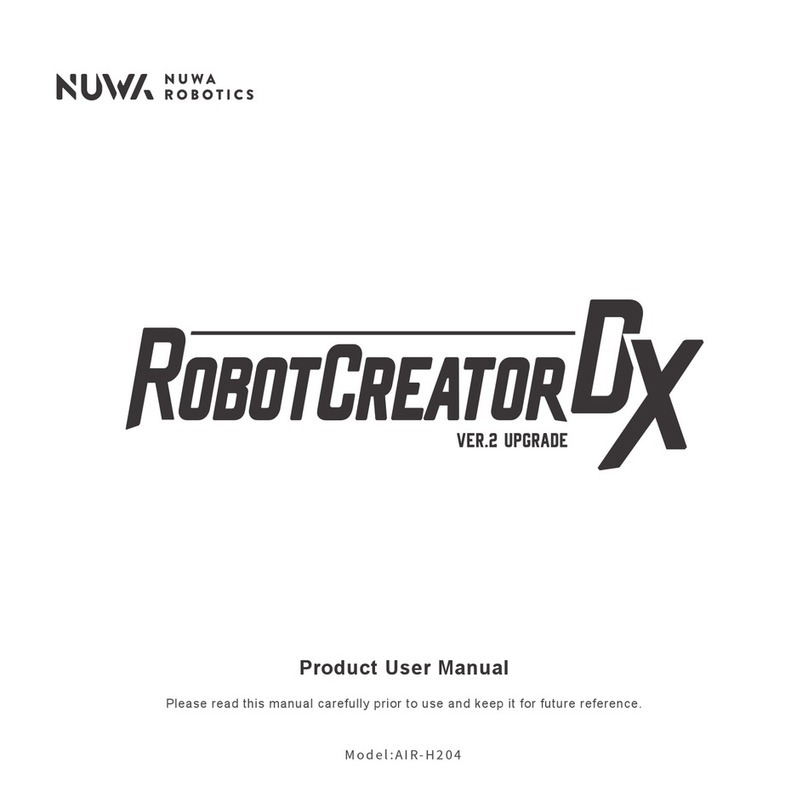
NUWA
NUWA RobotCreator DX Product user manual