YASKAWA CACR-SR BE Series User manual

CONTENTS
1. SWITCH OPERATION /1
2. FUNCTIONS OF MONITOR PANEL /2
3.STATUS INDICATION MODE /3
4. SETTING MODE /5
4.1 USER CONSTANT (DATA) SETUP AND MONITOR /5
4.2 USER CONSTANT (MEMORY SWITCH) SETUP AND MONITOR /7
4.3 MONITOR PANEL JOG OPERATION MODE
SELECTION AND OPERATING PROCEDURE /10
4.4 SPEED REFERENCE OFFSET ADJUSTMENT /12
4,5 CLEARING FAULT TRACEBACK DATA /13
4,6 SPEED REFERENCE OFFSET MANUAL ADJUSTMENT/14
4,7 CURRENT DETECTION OFFSET MANUAL ADJUSTMENT/16
4,8 CHECK OF MOTOR PARAMETERS /18
5, MONITOR MODE /20
6. FAULT TRACEBACK MODE /22

1 SWITCH .OPERATION
Fig. 1.1shows the monitor panel. The monitor panel has various functions as
listed by modes in Par. 2. "Monitor Panel Functions" (P. 2). The functions al-
lotted to SW1 through SW4 vary with monitor panel mode. A description of
switch functions according to modes, such as in Fig. 1.2is provided, and f. 1
through f.7 in the description show switch functions in the setup mode.
Notes:
1. The monitor panel's constant setup data are retained even after the power is turned off.
2. Even if the power is turned off after fault occurrence, the fault data is retained in memory.
Therefore, itis possible tocheck the fault data after the power" is turned back on.
3. The monitor mode carl be changed even during operations.
.................................................. 1
MONITOR PANEL
,,
LD1 LD2 LD3 LD4 LD5 . [
[CODE INDICATOR
i
*
i
SW1 'SW2SW3sw 4 i
i
i
O T O.S ,TOH
.................................................. i
Fig. 1.1 Monitor Panel
SWI SWl $ SW2
_-_ • _o, _ ..._,,, _,
SW2 SW I SW 3
_..._ _... _,, _
SW 3SW 1SW 4
_ ..._, F:_ ...D_,,_
SW 4
_ ..._,,
• : Indicatesthat SW2is pressedas SW1is pressed.
Fig. 1.2 Description of Switch Function

2 FUNCTIONS OF MONITOR PANEL
Table 2.1shows the monitor panel functions. The status display is the default
when control power is turned ON. To change the mode, use switch SW4 as
shown in Fig. 2.1.
Table 2,1 Monitor Panel Functions
Mode Function
Various States Indication
° BaseBlock
State Indication o On Operation (See Par, 3.)
Mode eFault
For details, refer to Table 1.2
Refer to "User Constant Setting." (See Par. 4.2.)
Setting Mode ., Operation (JOG) from Monitor Panel (See Par. 4,3,)
• Speed Reference Offset Adjustment (See Par. 4.4.)
Various Monitoring
• Speed
• Speed Reference
Monitor Mode ° TorqueReference
• Number of Pulses from Origin (Phase-U) (For test by YASKAWA)
• Electrical Equipment (For test by YASKAWA)
• Interior Status Bit (For test by YASKAWA) (See Par, 5.)
Alarm Traceback Fault History (See Par.6,)
Indication Mode
IControlPower I
Supply ON
PANELINDICATION
SW4
SW4
I J E]EE] D
Fig. 2.1 Mode Changeover

3. STATUS INDICATION MODE
Whenthis mode is selected, the condition of Servopack is indicated withbit and
code as shown in Fig..3.1. Table 3.1 shows the bits and the conditions. Fig.
4.1 shows the function allocations of switches.
_ST--]: Becomes alarm reset switch. Alarm R. ,u'n(overcurrent) cannot
be reset.
: Changes status indication mode into setting mode.
Panel Display
*TGON
*When brake reference functions is ON (bit Eof Cn-01 is set), brake reference ON/OFF
signal is displayed.
SW1 SW2 SW3
SW4
Fig. 3.1 Status Indication
3

3.STATUS INDICATION MODE (Cont'd)
Table 3.1Bit Data Contents
BitData Contents
Control ONLight turns ON with control power ON.
B8 Light turns ON with base block, and turns OFF with Servo ON.
TGON Light turns ON with motor rotating speed equat to or higher than
TGON level (standrad : 20 r/Tin),
tN-A Input Light turns ON with IN-A input equal to or higher than TGON level.
IN-B Input Light turnsON with IN-B input equal to or higher than TGON level.
Power Ready Light turns ON with mainpower ON.
Table 3.2 Codes and Status
CodeStatus
b b Base Block
J- (.._i_ On Operation
p,
I._C Forward Running Prohibited
O_ Reverse Running Prohibited
R,t_n
UU
Alarm Contents
R. _j_ _ Refer to Table 6.1.
t

4. SETTING MODE
In this mode, the following operations call be performed.
• User constant setup and monitor
• Jog operations from the monitor panel
•Speed reference offset adjustment
• Fault traceback data clearing
4.1 USER CONSTANT (DATA) SETUP AND MONITOR
The switch functions are indicated in Fig. 4.1.
Panel Display [] [] ,,_,NK
"_T/.
SETTING MODE ITEM No. _/_ DATA
II
SWl sw2
SW4 SWI SW4
Fig. 4.1 SwitchFunctionsfor UserConstantSetting
[] Set up the item number with the [-A--] , IV-I, [_-], or _ key.
•With the _ or _ key, choose a setup digit. The chosen digit then
starts blinking to indicate that its numerical value can be changed.
• With the _ or _ key, increase or decrease the numerical value until
the desired value is obtained.
[] With the _ key,display the data related to the selected item number.
[] With the [_, [_, [-_, or _ key, set up the data. (The same oper-
ation as stated in [] .)
[] Store the data with the _ key.
[] With the [.)3ATA Ikey, return to the item No. display state..
[] Repeat steps [] through [] as needed.
[] Using the _ key, switch from the setting mode to the monitor mode.
5

4.1 USER CONSTANT (DATA) SETUP AND MONITOR (Cont'd)
Table 4.1 shows user constants (constant setting).
Table 4.1 UserConstantsCn-03throughCn-12(ConstantSetting)List
User Symbol Name Unit Lower Upper SettingPrior
Constant Limit Limit toShipping Remarks
Speed Reference (r/min)N 0 3000 Rating/t0V SRK006
Cn-03 INBGN Adjustment Gain 10 SRK008or later
_ 20 500 40 SRK006
;_ _ Cn-04" LOOPHZ Speed Loop Gain Hz
1
SRK008
of
later
o
"o Speed Loop integration 2 512 SRK006
Cn-05* PITIME ms 20
Time Constant 1 10000 SRK008or later
Cn-06 EMGTRQ Emergency Stop Torque % 0 Max.Torque Max.Torque OT Mode
Cm08 TLMTF Forward Running Torque % 0 Max.Torque Max.Torque
Limit
E ReverseRunning Torque
Cn-09 TLMTR % 0 Max Torque Max.Torque
Limit
8
1
Cn-13 TCRFGN Torque Reference Gain _/Rating 10 100 30
l;r
a
_- 0n-14 TCRLMT Speed Limit witl_ Torque r/min 0 Max.Speed Max.Speed
Control 1
Cn-17 TRQFIL Torque Reference Filter
Time Constant 100/_s 0 250 4
Cn-07 SFSACC SoftStartTime ms 0 10000 0
_" Cn-0B TGONLV Zero-speed Level r/rain 10Max.Speed 20r/min
E
"_ Cn-0F ZCLVL Zero-clamp Level r/min 0 t00 10
Delay Time from Braking 10 ms 0 50 20
O Cn-12 BRKTIM Command to SVOFF
Cn-15 BRKSPD Brake Timing at Motor r/min 0 Max.Speed 100
Rotation
co
Cn-16 BRKWAI Brake Timing at Motor 10 ms 10 100 50
Rotation
_ E_e_Numbe_En_e_N_
Cn-0A_ PGRAT PG Division Ratio pulses/rev 1 d R_ises of_ses
,_ Cn-11 PULSNO Number of Encoder Pulses Er_c0de(Numbez E_0defNumSer
d Pulses 0lPdses
Mode Switch
Cn-0C TRQMSW (Torque Reference) % O Max.Torque 200
Cn-0D REFMSW Mode Switch r/min 0 Max.Speed 0
(SpeedReference)
Mode Switch (Motor 10 (r/rain)Is 0 3000 0
Cn-0E
ACCMSW
--_ Acceleration Detection)
O
Cn-10 JOGSPD JOG Speed (r/min) 0 Max.Speed 100
*In Cn-04 and Cn-05, upper/lower limit values differ according to software version number.(SRK006 and SRK008 are
software version numbers).
t In Cm0A, turn thecontrol power ON again after setting.
6

4.2 USER CONSTANT (MEMORY SWITCH) SETUP
(On-01 .to Cn-02) AND MONITOR
User constants Cn-01 and Cn-02 can be set up or checked as memory switch bits.
The procedures for item number setup and data display are the same as indicat-
ed in Par. 4.1 [] and I_1.
The, switch functions provided after bit data display are indicated in
Fig. 4.2.
When changing constants Cn-01 and Cn-02, functions become available
by turning ON control power supply again.
Panel Display
....................................
•
Sw4SWl SW3
5] SETTING BiT NO. swt Sw4
Fig. 4.2 SwitchFunctionsProvidedafterBitDataDisplay
[] With the _ or [-_ key, enter the setup memory switch number at the
far right end of the panel.
[] With the [--6_ key, set the memory switch to ON or OFF (either switch SW2
or SW3 can be used). The panel indication comes on when the switch is
ON, and goes off when the switch is OFF.
[] Repeat steps [] and [] as needed.
[] With the _ key, return to the item No. display staCe.
[] Using the _ key, switch from the setting mode to the monitor mode.
Table 4,2shows memory switches of user constant Cn-01, and Table 4.3
those of user constant Cn-02.
7 \

4.2 USER CONSTANT (MEMORY SWITCH) SETUP
(Cn-01 to On-02) AND MONITOR (Cont'd)
Table 4.2 User Constant Cn-01 (Memory Switch)
Selection Bit No. Setting Conditions Standard
0 Servo ON/OFF by external input (SV-ON).
0 0
1 The servo is ON at all times.
0 The external input (SEN) is used.
1
Sequence (SP,SBY0nf_) 1 Regardless of the SEN signal presence,the Servopack automatically 0
Input concludes that the "H" level prevails.
Selection 0 The P-OT signal prohibits forward running.
2 0
1 Forward running is permitted at all times.
3 0 The N-OT signal permits reverse running.
0
I Reverse running is permitted at all times.
0 The IN-A input is used.
4 Regardless of the IN-A input presence, the Servopack concludes that 0
Input1 the IN-A input is 0.
Signal
Selection0 The IN-B input is used.
5 Regardless of the IN-B input presence, theServopaek concludes that 0
I the IN.B input is 0.
<DB stop>
0 The dynamic brake stops the motor.
6 0
<Coasting to stop>
1 Themotor is freed and brought to a stop.
<DB OFF after DB stop>
0 Thedynamic brake is turned OFF after themotor is stopped.
Abnormal 7 <DB continuously ON after O8 stop> 0
Stop 1 The dynamic brake remains activated after the motor is stopped.
Selection
0 The overtravel state stop method agrees with bit 6.
8"o_T <Over[ravelzerospeedstop> 0
1 In the overtravel state, the motor is stopped at thetorque setting defined by
user constant Cn-06.
_" _ 0 In the overtravel state, base blocking (BB) is implemented after the motor stops.
9 0
t In the overtravel state, zero clamping is effected after zero speed stop.
<Torque reference>
Mode 0.0 Based on the torque reference level defined by user constant Cn-0C.
Switch <Speed Reference>
Selection _o_e3 0. t
D.C Based on the speed reference level defined by user constantCn-OD. 00
(for Speed
< Acceleration >
Control t .0
only) Based on the acceleration level defined by user constant Cn-0E.
1.1 < None > Themode switch functionis not provided.
Presence0 The braking command function is not provided.
ofExternal E 0
Brake 1 The braking command function is provided.
Overload 0 Theoverload alarm function is not provided.
Alarm F 0
Selection 1 The overload alarm function is provided.
Notes: 1. The abnormal stop method in the torque control mode complies with bit 6.
2. Selects the status based on thestop method selected for the overtravel state (bit 8),
3.Selects amode switch operating condition.When the modeswitch operates, the speed control mode changes
to P Control.However, this is effective for speed control only.
8

Table 4.2 User Constant Cn-01 (Memory Switch) List (Cont'd)
No.I Setting Description Reference Input
Selection
Bit
Sequence
Signal Input Standard
ControlB • A 0 • 0 <Speed control>Speed reference (IN-A) P-CON 0 • 0
ModeAuxiliary reference input
Selection • Regular speed control. (IN-B) i OFF: PI control.
•TheP-CONsignal (1CN-24)isused ON: P control
to effectP/PI control changeover.
0 • 1 <Zero clamp speed control> P-CON
•After the motor is stopped (ZCLVL). OFF: Zero clamp
the speed reference is disconnected function OFF
to execute Ihe zero speed stop ON: Zeroclamp
function, function ON
• The P-CON signal (1CN-24) is used
to turn ON and OFF thezero clamp
function.
I • 0 <TorquecontrolI> Torquereference0N-A) None
• The motor output torque is controlled
by the torquereference (IN-A).
• The IN-B cannot be used.
1 • 1 <Torque control I1> Torque control modeP-CON
• The P-CON signal (1CN-24) is used Torque reference 0N-B) OFF: Torque con-
fortorque/speed control mode Speed limil (IN-A) trol
changeover. ON: Speed con-
trol
Torque control modeSpeed control mode
• The motoroutput torque is controlled Speed reference(IN-A)
by the torque reference (IN-B).
•The speed limit can be entered from
Outside (IN-A). Noles:
• Whenthespeed isoutsidethe
The IN-A voltage (+) limits both the speedcOntrolrange,Ihetorque
torward and reverse running speeds, proportionaltothespeeddiffer-
encefromthelimitis negatively
fed back to place thespeed
] MOTOR SPEEDI withinthelimit.Therefore,the
actualmotorrotating speed
' _ limitvarieswi_htheload COndi-
t!ons.
:_'__'?_'_f • Incase otcontinuousregener-
ation(tension COntrol).
: ContactyourYASKAWA
Orepresentative.
IN'A
Speed control mode
• Thespeed referenceis entered from
the IN-A.
• The IN-Elcannot be used.
Pc,me0, CCW: Forward Running
I:lo=_nhlcde0
Seem= I CW: Forward Running
ForEnc_ef 1 0 Detects an enceder error. O
On-02E,r.[_"YIDete_m 1 Does notdetectan encoder error•
Spare 2 to F Do not adjust.

4.3 MONITOR PANEL JOG OPERATION MODE SELECTION
AND OPERATING PROCEDURE
(1) Monitor Panel Jog Operation ModeSelection
When user constant Cn-00 is set to 00, the operations are to be controlled from
the monitor panel. The switch functions are indicated in Fig. 4.3.
Panel Display
SETTING MODEITEM No.DATA
(SwitchFUnctions)
$W2SWI SW2
SW4 SWI SW4
Monitor Panel Jog Operation Mode Display
Fig. 4.3 SwitchFunctionsin MonitorPanelJogOperationMode
[] Select item number 00 with the [_--_, _-], _-_ or r-_ key.
[] With the I DATA Ikey, display the data related to the selected item number.
[] With the E_], [-_, [-_ or _ key, select the number 00.
[] With the _ key, turn ON or OFF the monitor panel jog operation mode.
[] With the _ key, return to the item No. display status.
[] Using the _ key, switch from the setting mode to the monitor mode.
--10--

(2) Monitor Panel Jog Operation Procedure
For speed reference adjustment, use user constant Cn-lO (see Par. 4.1).
The switch functions provided for monitor panel jog operations are indi-
cated in Fig. 4.4.
SWI SW3
SW2 SW4
Fig. 4.4 Switch Functions for Monitor Panel Jog Operations
[] With the [ SVON/OFF [switch, effect SVON/SVOFF changeover.
[] The motor runs in the forward direction while the [ FORWARD Ikey is held
down.
[] The motor runs in the reverse direction while the [ REVERSE Ikey is held
down.
[] The _ key is used to switch from the monitor panel jog operation mode
to the user constant Cn-00 data display status.
[] With the _ key, return tothe item No. display status.
[] Using the _ key, switch from the setting mode to the monitor mode.
--11 h

4.4 SPEED REFERENCE OFFSET ADJUSTMENT
When user constant Cn-O0 is set to 01,the system enters the speed reference
offset adjustment mode. The switch functions are indicated in Fig. 4.5.
ITEM No. DATA
O
F..ctio@
SW2 SWt SW2
SW3SWI SW3 .5<
loblab+lab
SW4 SWl SW4
Fig. 4.5 Speed Reference Offset Adjustment
[] Select the itemnumber 00 with the [-_, _, _ or _-_ key.
[] With the _ key, display the data related to the selected item number.
[] With the [--_-], [7_, [_ or _ key,select the number 01.
[] Apply a-desired zero speed reference voltage between speed reference in-
put terminals IN-A and IN-B (a voltage of 0V should normally be applied).
[] With the _ key, make speed reference offset adjustment and return to
the user constant Cn-00 data display status.
With the l DATA Ikey, return to the item No. display status.
U Using the [-_ key,switch from the setting mode to the monitor mode.
--12--

4.5 CLEARING FAULT TRACEBACK DATA
When user constant Cn-00 is set to 02, fault traceback data are cleared. The
switch functions are indicated in Fig. 4.6.
.. j, \/
ITEM No. DATA
SW2-"SWI SW2
SW3 SWl SW3i
SW4 SWI SW4
[_ " _'_ _ "'" I_+I_ClearingFaultTracebackOata
Fig. 4.6Speed Reference Offset Adjustment
[] Select the item number 00 with the _, _, [-_ or _ key.
[] With the [_ key, display the data related to the selected item number.
[] With the [_, _V], [-_ or [-_ key, select the number 02.
[] With the _ key, clear fault traceback data and return to the user con-
stant Cn-00 data display status.
[] With the _ key, return to the item No. display status.
Using the _ key, switch from the setting mode to the monitor mode.
F13--

4.6 SPEED REFERENCE OFFSET MANUAL ADJUSTMENT
(1) Mode Setting in Speed Reference Offset Manual Adjustment
When user constant Cn-00 is set to 03,the system enters the speed reference
offset manual adjustment mode. The switch functions are shown in Fig. 4.7.
Panel Indication
n N n
SWZ $Wl SWZ
_--J '" _ _ -" _-h _ IN-A INPUT OFFSET ADJUSTMENT MODE/
SW3 SWI SW3 /
SW4 SWL SW4
IN-B INPUT OFFSET ADJUSTMENT MODE
Fig. 4.7 SwitchFunctionsin SpeedRefe_'enceOffsetManualAdjustmentMode
[] Set up item number O0 with _-_, [--_-_, f-_, or _ key.
[] With the _ key, display the data related to the selected item number.
[] With the _-_, F-_, [--_, or [-_ key, select the number 03.
[] With the _ key, switch the adjustment mode.
[] With the D_A---_ key, return to the item No. display status.
[] Using the _ key, switch from the setting mode to the monitor mode.
--14--

(2) Speed Reference Offset Manual Adjustment
Input a voltage that will obtain zero speed reference to the speed reference in-
put terminals IN-A and IN-B (Normally 0V).
The switch functions in the reference offset manual adjustment mode are
shown in Fig. 4.8.
SW3
...
SW2 SW4
Fig. 4,8 Switch Functions in Speed Reference Offset
Manual Adjustment Mode
Ill While the [ FORWARD ]key is held down, the offset is added to the forward
running side.
[] While the] REVERSE ]key is held down, the offset is added to the reverse
running side.
[] Use the 1-_ key, store offset data, then enter the next mode.
Offset adjustment is performed so that the LED indication may basically be-
come zero; however, the perfectzero state of indication does not always offer
optimum adjustment. Therefore, adjust tile offset carefully, taking actual
motor motion into consideration.
-- 1,5--

4.7 CURRENT DETECTION OFFSET MANUAL ADJUSTMENT
(t) Mode Setting in CurrentDetection Offset Adjustment
When user constant Cn-00 is set to 04, the system enters the current detection
offset adjustment mode. The switch functions are shown in Fig. 4.9.
Panel Indication
in B! n
SETTING MODEITEM No.{ _ DATA
SW2 SWI SW2
_-] "'" I_ [_ '"I_+I_U-PHASECURRENT OFFSETADJUSTMENT MODE|
SW3SWl SW3 l
_ -I:_, _ -nu_,+Im _, U
V-PHASE CURRENT OFFSET ADJUSTMENTMODE
Fig.4.9 Switch Functions in Current Detecrtion Offset Adjustment Mode
IllSet up item number O0with [--_-], [-V-I, [-_--], or _ key.
[] With the.DA[-_-A-TA-_key, display the data related to the selected item number.
!_! With the [--_--_,_, [-_-], or _ key, select the number 03.
[] With the _ key,switch the adjustmentmode.
[] With the _ key,return to the item No. display status.
[] Using the _ key, switch from the setting mode to the monitor mode.
--16--

(2) Current Detection Offset Adjustment
The current detection offset is adjusted at the factory prior to shipment: the
user, in principal, doesn't need to adjust it.
However, if adjustment of higher accuracy is required due to a Servopack-
motor combination, perform adjustment as follows:
The switch functions in the current detection offset adjustment mode are
shown in Fig. 4.10.
SW3
SW2 SWd
Fig. 4.10 Switch Functions in Current Detection Offset Adjustment Mode
[] Rotate the motor at about 100r/min, and monitor the torque monitor termi-
nal MON1 using an oscilloscope.
[] Depressing the _ or l DOWN Ikey, perform adjustment so as to have a
minimum torque ripple. LED indication shows offset data.
[] With the _ key, store offset data, then enter the nextmode.
[] Because torque ripple must be adjusted with a good balance between U-phase
and V-phase offsets,repeat steps [] and [] several times, to make sure of
an optimum value.
--17--

4.8 CHECK OF MOTOR PARAMETERS
(1) Check Method of MotorParameters
When user constant Cn-00 is set to 05, the system enters the motor parameter
check mode.
PanelDisplay n u n
_,,_oo_ ,_o. [!_ U o_
SW2 SWl SW2
_] "'" _'_N _ "'" _'_ MOTOR PARAMETER DISPL.AY
SW3 SWl SW3 l
|
r<...=:_ _ ---+=_v_ [7_, n
SW4 SWI SW4
MODIFICATIONDISPLAY
<tm
PAFIAMETER VERSIONDISPLAY
_m
Fig. 4.11 SwitchFunctionsin MotorParameterCheck
[] Set up item number 00 with _-}, _-_, _-], or _ key.
[] With the _ key, display the data related to the selected item number.
[] With the _, [-_, _, or [-_ key, select the number 05.
[] With the _ key, check the motor parameter.
[] With the I DATA Ikey,return to the item No. display status.
[] Using the _ key, switch from the setting mode to the monitor mode.
--18--
This manual suits for next models
2
Table of contents
Popular Control Panel manuals by other brands

Protect America
Protect America Simon XT installation manual
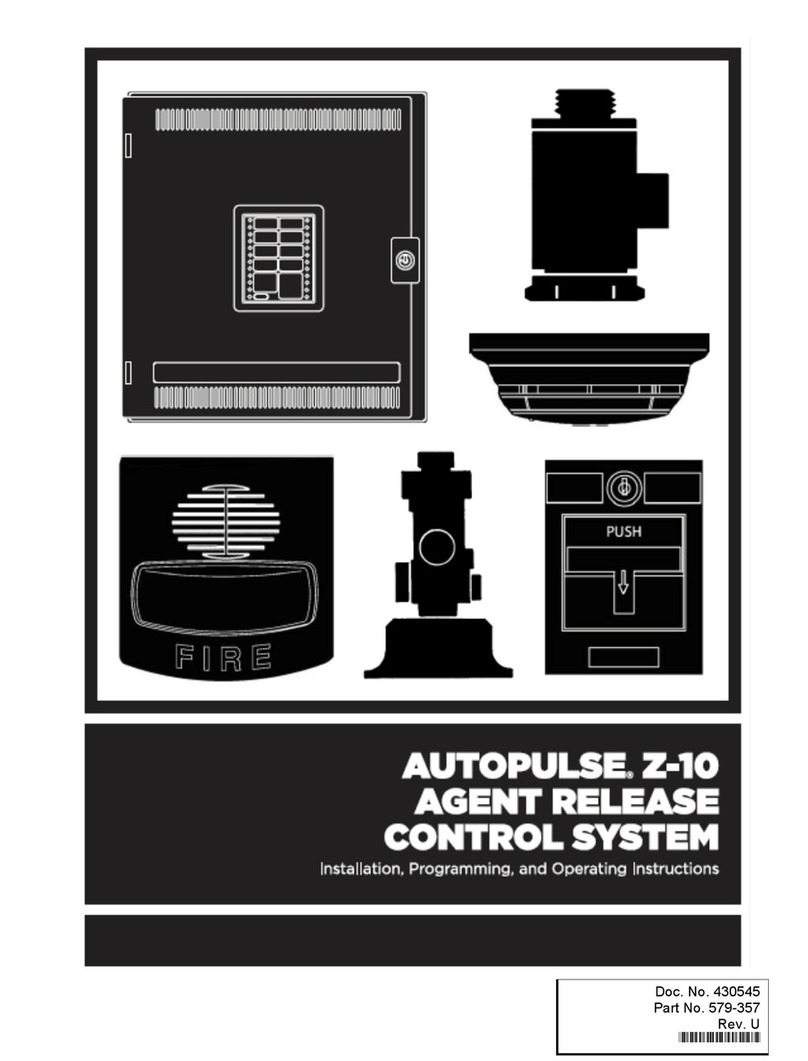
Tyco
Tyco AutoPulse Z-10 Installation, Programming and Operating Instructions
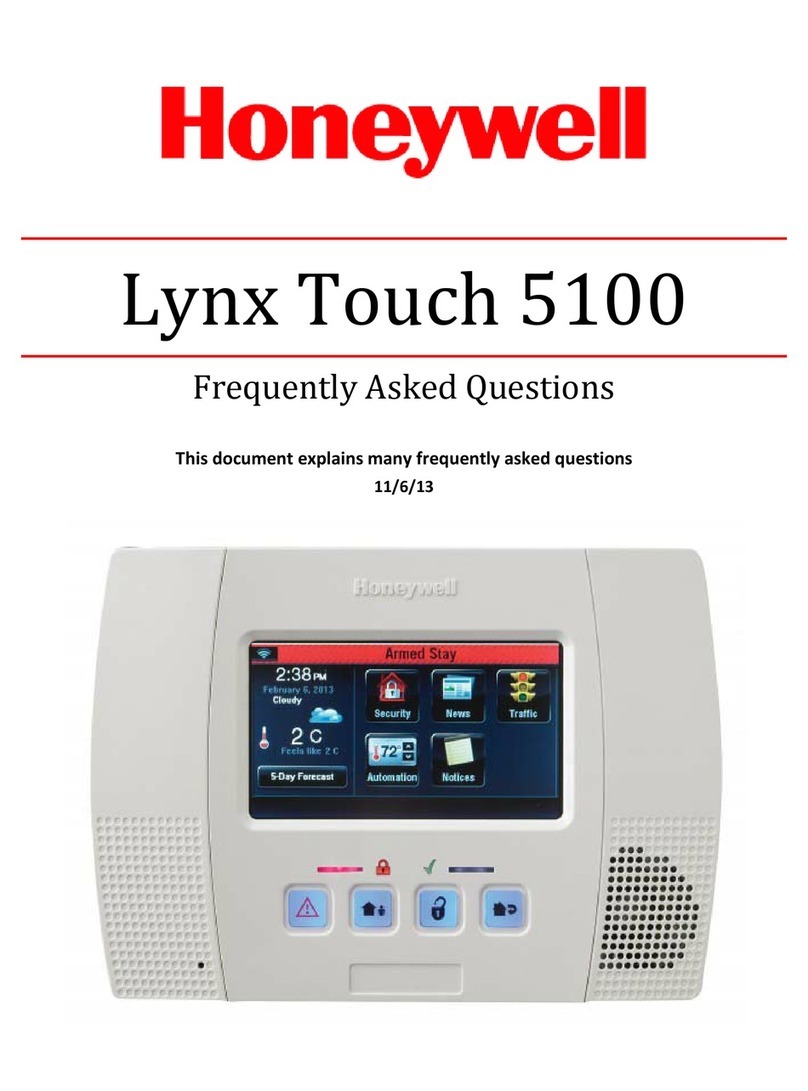
Honeywell
Honeywell LYNX Touch 5100 Frequently asked questions
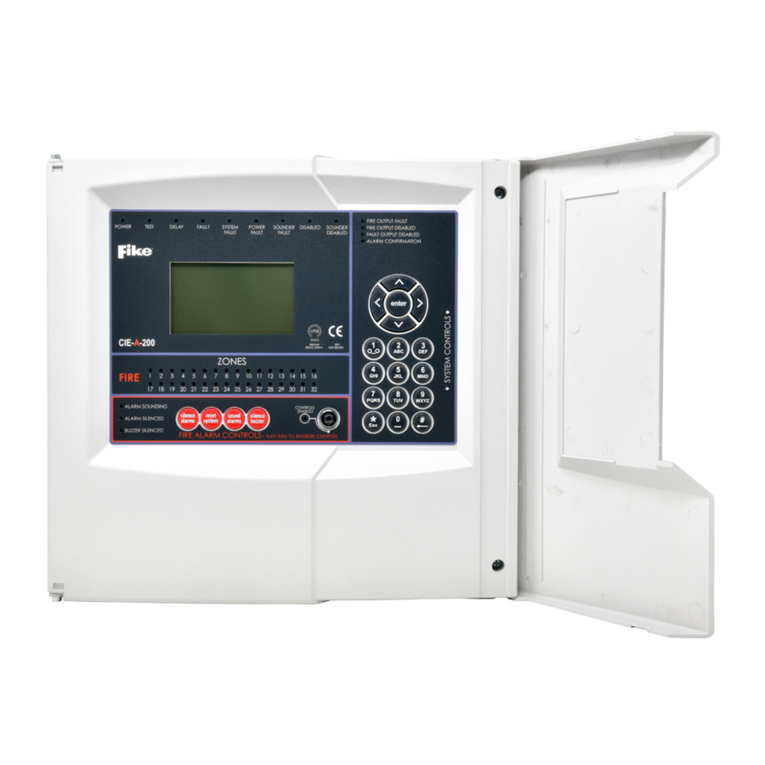
Fike
Fike CIE-A-200 Engineering and Commissioning Manual
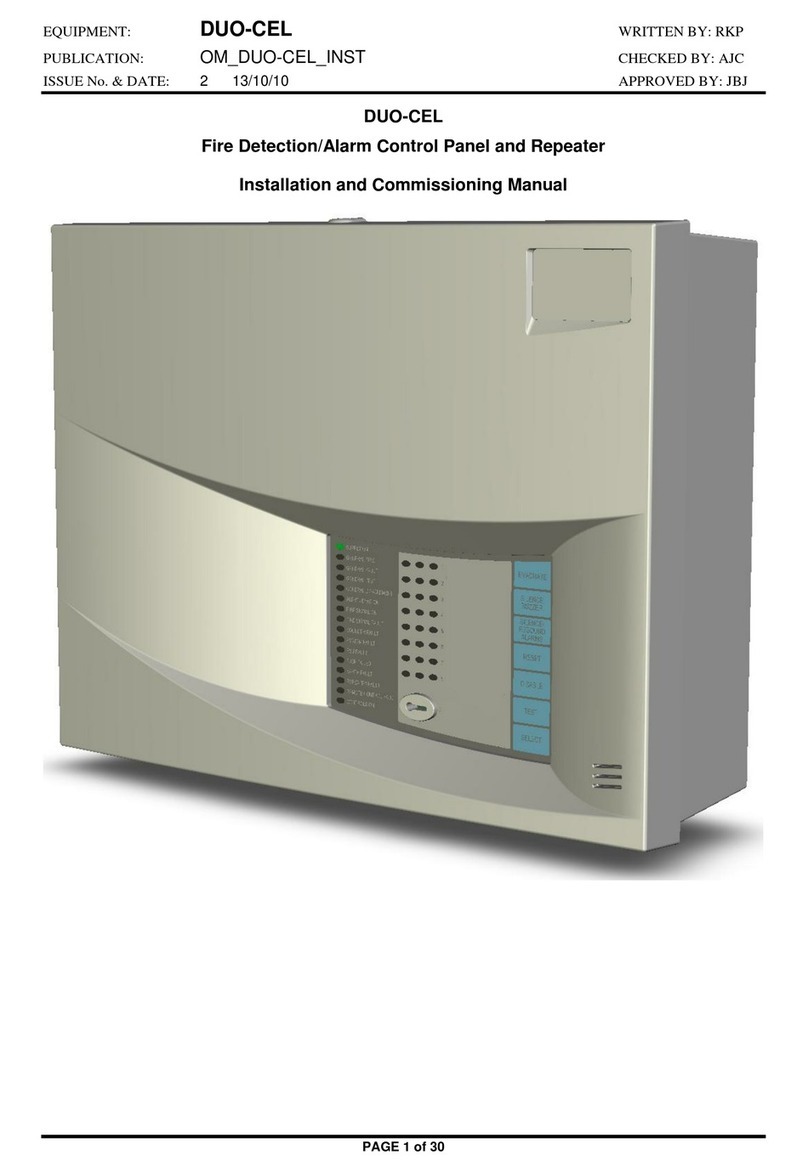
FireClass
FireClass DUO-CEL installation manual
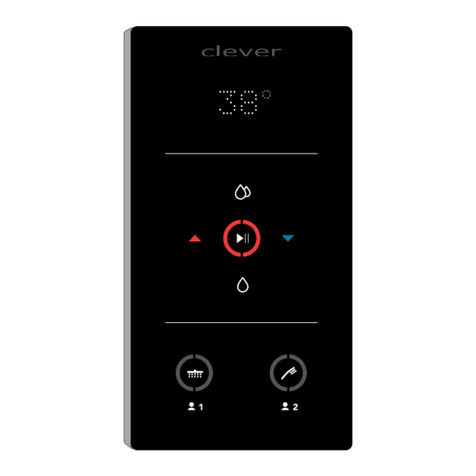
Clever
Clever iCLEVER PLUS user manual
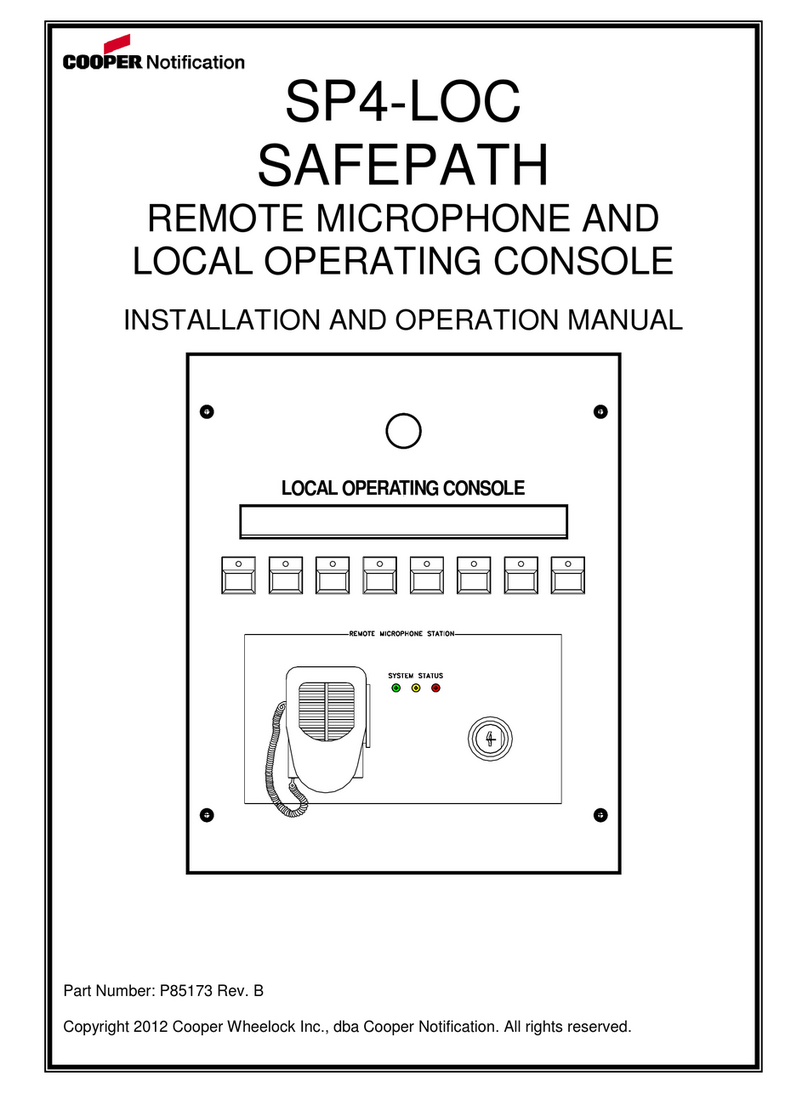
Cooper
Cooper SAFEPATH SP4-LOC Installation and operation manual
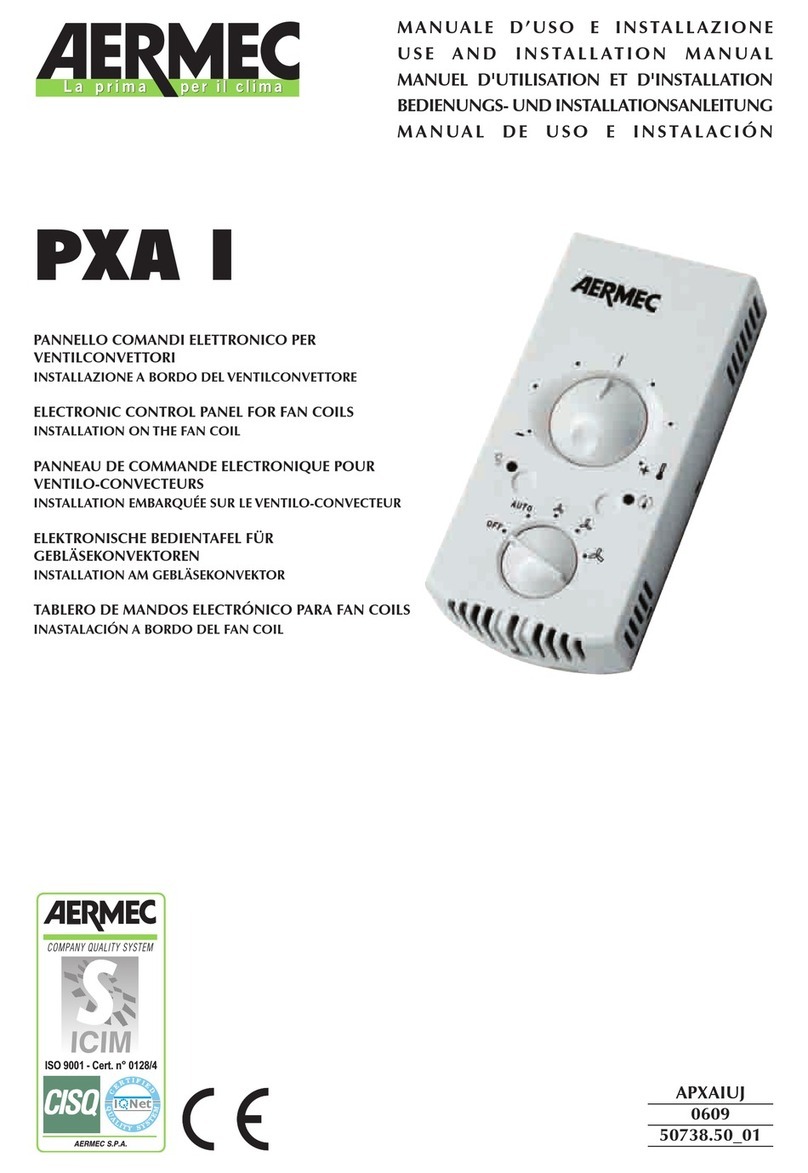
AERMEC
AERMEC PXA I Use and installation manual
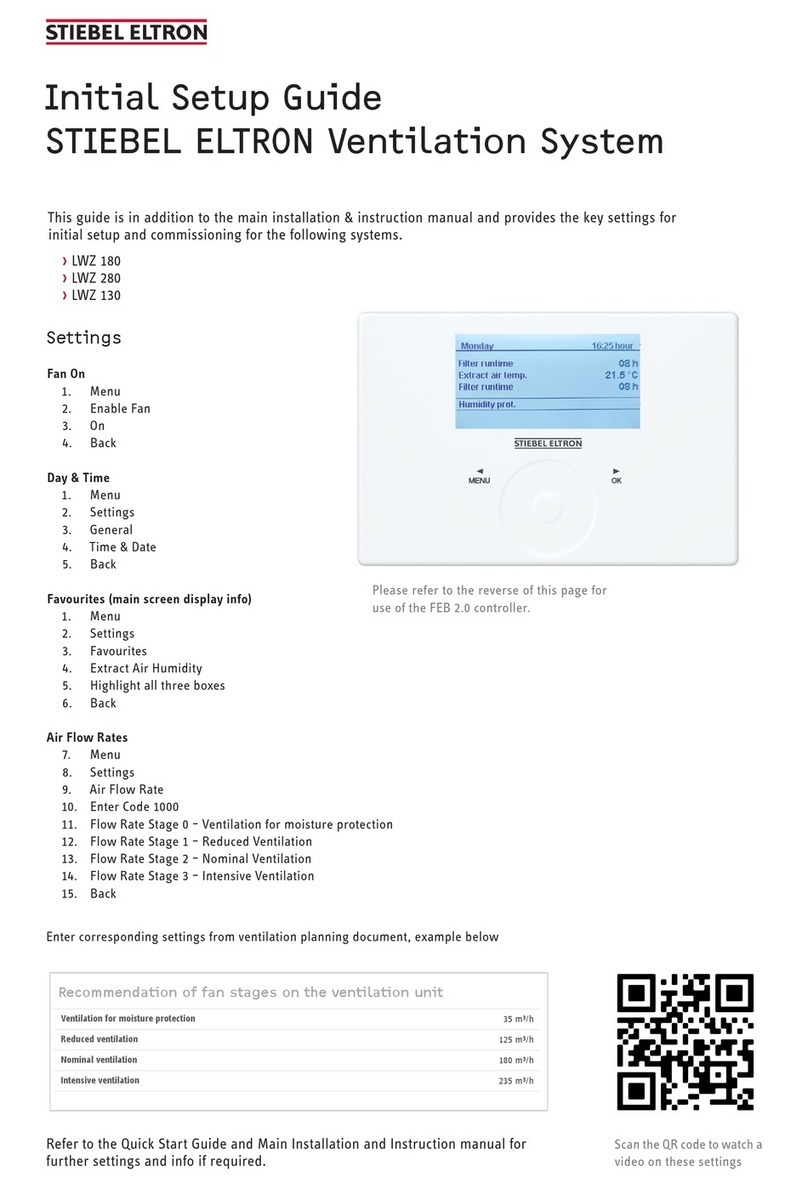
STIEBEL ELTRON
STIEBEL ELTRON LWZ 180 Initial setup guide
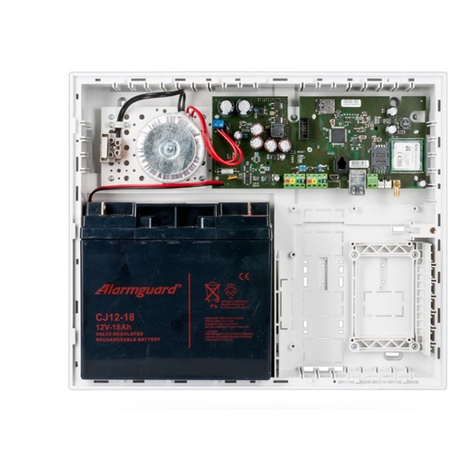
jablotron
jablotron JA-101K manual
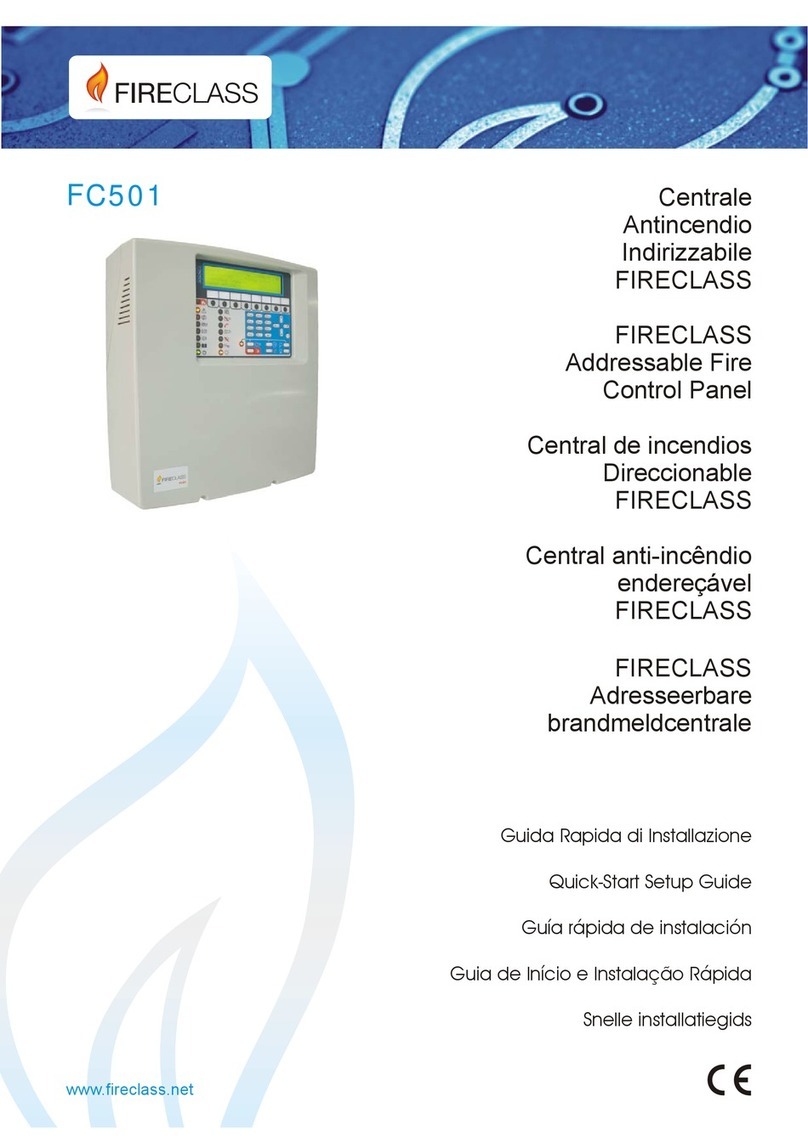
FireClass
FireClass FC501-L Quick start setup guide
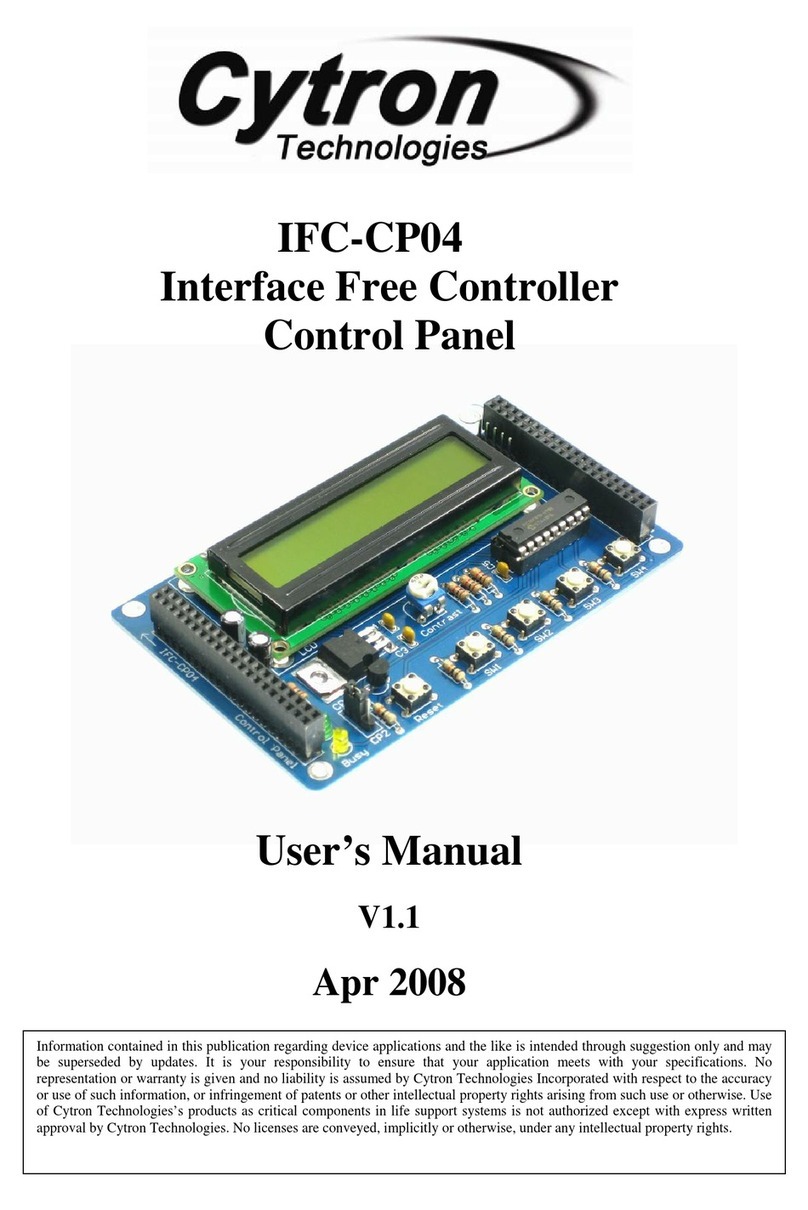
Cytron Technologies
Cytron Technologies IFC-CP04 user manual