ZEKS Eclipse 90ZPB User manual

TECHNICAL MANUAL
ZEKS Compressed Air Solutions
1302 Goshen Parkway
West Chester, PA 19380
Phone: 610-692-9100
800-888-2323
Fax: 610-692-9192
Web: www.zeks.com
Form: ZEKS ZPB V0121
ZPB Heatless Purge
Desiccant Compressed Air Dryers
90-5,000 scfm
NOTICE
Those operating the machine or performing
maintenance should read and understand
the decals positioned on the machine and
the contents of this Technical Manual.
Ensure that this Technical Manual is not
removed permanently from the machine.
TM

ZEKS EclipseTM 90-5,000ZPB Desiccant Dryers
www.zeks.com

ZEKS EclipseTM 90-5,000ZPB Desiccant Dryers
www.zeks.com
TABLE OF CONTENTS
SECTION CONTENT PAGE
1. INTRODUCTION ...................................................... 2
2. ABBREVIATED WARRANTY ................................... 2
3. ZPB HEATLESS DRYER NOMENCLATURE .......... 3
4. RECEIVING AND INSPECTION .............................. 3
5. SAFETY AND OPERATION PRECAUTIONS .......... 4
6. PRINCIPLES OF OPERATION ................................ 5
7. ALARMS AND INDICATORS ................................... 15
8. INSTALLATION/INITIAL START-UP ......................... 18
9. SCHEDULED MAINTENANCE ................................ 22
10. TROUBLESHOOTING ............................................. 25
11. PURGE CHARTS ..................................................... 26
12. GENERAL ARRANGEMENT DRAWINGS ............... 30
13. WIRING DIAGRAMS ................................................ 53
14. FLOW DIAGRAM ..................................................... 56
15. SPARE PARTS .......................................................... 64
16. ENGINEERING SPECIFICATIONS ........................... 70
1

ZEKS Eclipse™ ZPB Heatless Desiccant Dryers are designed to
adsorb moisture from compressed air. The dryers are constructed
with two towers, each containing desiccant beads, that alternate
between online (drying) and offline (regenerating) modes,
yielding a continuous stream of dry air at the dryer’s outlet.
During normal operation, wet air passes through the online
tower and water vapor from the air is adsorbed (collected) on the
desiccant beads. While air is being adsorbed in the online tower,
the moisture on the desiccant in the offline tower is removed by
a process called desorption (regeneration). After an initial rapid
depressurization, a portion of dried air from the online tower
passes over the desiccant bed and carries the moisture offthe
bed and out the dryer’s exhaust.
The continuous, alternating process of adsorption and desorption
is controlled using a timer that switches the towers in a specific
timed sequence. Very dry compressed air dew points are
achieved through the continuous switching and operation of this
dryer. ZEKS offers dryers to provide either -40°F, -80°F or -100°F
pressure dew point outlet air.
1.0 INTRODUCTION
ZEKS EclipseTM 90-5,000ZPB Desiccant Dryers
www.zeks.com
2
2.0 ABBREVIATED WARRANTY
ZEKS Eclipse™ heatless desiccant dryer products are warranted
to be free from defects in material and workmanship for a period
of 12 months from the original date of shipment from the factory.
To allow the warranty to be in effect for 12 months from the date
of equipment start-up, the Warranty Registration Card must
be completed and returned to ZEKS. Alternately, the Warranty
Registration Card may be completed online at www.zeks.com.
The total warranty period cannot exceed 18 months from the
original date of shipment from the factory.
Equipment must be installed and operated in accordance with
ZEKS’ recommendations. ZEKS liability is limited to repair of,
refund of purchase price paid for, or replacement in kind at
ZEKS’ sole option, during the warranty time period stated above.
IN NO EVENT SHALL ZEKS BE LIABLE OR RESPONSIBLE
FOR INCIDENTAL OR CONSEQUENTIAL DAMAGES, even
if the possibility of such incidental or consequential damages
has been made known to ZEKS Compressed Air Solutions. In
addition, the usual maintenance and replacement type products
are not covered by this warranty. See SECTION 9.
The warranties expressed above are in lieu of and exclusive of
all other warranties. There are no other warranties, expressed or
implied, except as stated herein. There are no implied warranties
of merchantability or fitness for a particular purpose, which are
specifically disclaimed.
Valves – After the Basic Warranty noted above expires, the
valves on the ZPB heatless dryers are warranted (parts only)
for a total of 5 years from the date the dryer is shipped from the
ZEKS factory. The following applies to this warranty:
A. Check valves are excluded
B. Not applicable to dryers provided for -80°F and
-100°F dew point applications
C. Valves must be rebuilt every two years. Refer to
SECTION 9 of this manual
D. Element in Control Air Filter (NEMA 1) or Filter/Regulator
(NEMA 4) must be replaced once per year.

ZEKS EclipseTM 90-5,000ZPB Desiccant Dryers
www.zeks.com
3
Nominal Flow Type/Design Voltage Electrical
SCFM* Series (Dew Point) NEMA Option
3.0 NOMENCLATURE
4.1 INSPECTION
Upon receiving your ZEKS air dryer, please inspect the unit
closely. If evidence of rough handling is detected, note it on
your delivery receipt, especially if the dryer will not be uncrated
immediately. Obtaining the delivery person’s signed agreement
to noted damages will facilitate submission of insurance claims.
4.2 UNPACKING AND HANDLING
Refer to labels on the dryer for the appropriate means for lifting
or moving the dryer. When lifting the dryer, ensure that no stress
is applied to the piping or the valves. Refer to SECTION 8.2 for
locating and mounting of the dryer.
The dryer can be rigged using the forklift rails that are welded to
the upper cross member that spans between the two vessels.
Use care when inserting fork tongs beneath these rails to avoid
damaging piping at the rear of the dryer.
4.0 RECEIVING AND INSPECTION
!NOTICE
Nomenclature shown above represents standard
price sheet options. Other options are available -
refer to nomenclature insert specific to your dryer
for details.
!NOTICE
Under no circumstances should any person attempt
to lift heavy objects without proper lifting equipment
(i.e.: crane, hoist, slings or fork truck). Lifting any unit
without proper lifting equipment can cause serious
injury.
90
120
160
200
250
300
400
500
600
800
1,000
1,200
1,500
1,800
2,100
2,700
3,300
4,000
5,000
1 = 115-1-60 (-40°F)
G = 115-1-60 (-80°F)
B = 115-1-60 (-100°F)
2 = 230-1-60 (-40°F)
C = 230-1-60 (-100°F)
3 = 220-1-50 (-40°F)
E = 220-1-50 (-100°F)
0 = NEMA 1
H = NEMA 4
S = NEMA 4X
Stainless Steel
ZPB = Pressure Swing
* Nominal Flows indicated are for 100°F inlet temperature, 100°F ambient temperature and 100 psig compressed air pressure.
0 = Standard
A = Failure-To-Shift (FTS)
B = High Humidity (HH)
C = FTS + HH
E = Dew Point Display
+ MLC (NEMA 4/4X)
G = Dew Point Display + MLC
+ FTS (NEMA 4/4X)
M = Moisture Load Control (MLC)
+ FTS (NEMA 1 only)
N = MLC + HH (NEMA 1 only)

5.1 SAFETY PRECAUTIONS LIST
Because an air dryer is pressurized and contains mechanical
parts, the same precautions should be observed as with any
piece of machinery of this type where carelessness in operation
or maintenance is hazardous to personnel. In addition to the
many obvious safety rules that should be followed with this type
of machinery, the safety precautions as listed below must be
observed:
1. Only qualified personnel shall be permitted to adjust, perform
maintenance or repair this air dryer.
2. Read all instructions completely before operating unit.
3. Pull main electrical disconnect switch and disconnect any
separate control lines, if used, before attempting to work or
perform maintenance on the unit.
4. Do not attempt to service any part while dryer is in an
operational mode.
5. Do not attempt to remove any parts without first relieving the
entire air system of pressure.
6. Do not operate the dryer at pressures in excess of its
rating.
7. Inspect unit daily to observe and correct any unsafe
operating conditions.
OSHA Heading Descriptions
5.0 SAFETY AND OPERATION PRECAUTIONS
ZEKS EclipseTM 90-5,000ZPB Desiccant Dryers
www.zeks.com
4
!NOTICE
The user of any air dryer manufactured by ZEKS Compressed
Air Solutions, is hereby warned that failure to follow the above
Safety and Operation Precautions can result in personal
injuries or equipment damage. However, ZEKS Compressed
Air Solutions does not state as fact, nor does it mean to imply,
that the preceding list of Safety and Operation Precautions is
all inclusive, and further, that the observance of this list will
prevent all personal injuries or equipment damage.
!WARNING
“WARNING” is used to indicate a hazardous situation which
has some probability of death or severe injury. Warning should
not be considered for property damage accidents unless
personal injury risk is present.
!CAUTION
“CAUTION” is used to indicate a hazardous situation which
may result in minor or moderate injury.
!NOTICE
“NOTICE” is used to indicate a statement of company policy
as the message relates directly or indirectly to the safety of
personnel or protection of property. Notice should not be
associated directly with a hazard or hazardous situation and
must not be used in place of “DANGER,” “WARNING,” or
“CAUTION.”

ZEKS EclipseTM 90-5,000ZPB Desiccant Dryers
www.zeks.com
5
6.1 INTRODUCTION
As described in SECTION 1, the ZPB series dryer is used to
remove water vapor from compressed air by diverting the air
flow alternately between two towers that are filled with desiccant
material. While one tower processes the compressed air stream,
adsorbing water vapor, the opposite tower is regenerated by
desorbing the water vapor accumulated in the previous cycle
and venting it to atmosphere. Refer to SECTION 14, PROCESS
AND INSTRUMENTATION DIAGRAMS (P&ID) for a visual
representation of the drying and regenerating cycles.
Timing of the drying and regenerating cycles is automatically
controlled by a Solid State Timer (SST). An optional
programmable dryer controller is available.
Inlet flow to the dryer is directed to the bottom manifold and the
outlet flow exits through the upper manifold. The manifolds are
comprised of both pneumatically actuated valves and check
valves that direct compressed air flow through the dryer. The
INLET connection is located on the lower manifold while the
OUTLET connection is located on the upper manifold.
6.2 DRYING CYCLE
Saturated compressed air enters the dryer and is directed to the
appropriate drying tower by the corresponding inlet flow valves.
The inlet flow valves are normally-open and one of the valves
will be actuated closed to direct the flow of compressed air to
the designated drying tower. It is important to note that only one
inlet valve is closed during this process. The P&ID in SECTION
14 of this Technical Manual depicts the scenario where the left
tower is being regenerated and the drying process is occurring
with the right tower. In this example, wet compressed air enters
the dryer and is directed to the right tower for drying when the left
tower, normally-open flow valve is actuated to a closed position.
The normally-closed, right tower purge valve is closed while the
left tower purge valve is actuated to an open position during
this period. As the compressed air flows through the desiccant
material on the right tower, removal of water vapor from the air
stream begins to occur through adsorption.
6.3 REGENERATION CYCLE
Previously adsorbed moisture, removed from the process
stream, gets stripped or desorbed from the desiccant material in
the regeneration process. The first stage of regeneration is tower
depressurization. After the normally-closed Inlet Flow Valves are
switched to divert air flow away from the regenerating tower, the
appropriate normally-open Purge Valve will be opened and the
tower will be depressurized. Through rapid depressurization,
a significant portion of the previously adsorbed water vapor
is stripped offof the desiccant material and exhausted to
atmosphere.
The second stage of regeneration uses a portion of the
dry, compressed air, expanded to atmospheric pressure to
complete the desorption process. As depicted in the P&ID, the
compressed air exits the drying tower and a portion of the air
flows through the Purge Adjustment Valve and the Purge Orifice.
Once the air has passed through the Purge Orifice, it expands to
atmospheric pressure and continues the regeneration process.
Desorption occurs as the desiccant releases water vapor into
the regeneration air that is then exhausted through the Purge
Muffler.
EclipseZPB Heatless Dryers are equipped with a Downstream
Purge feature as standard. Downstream Purge enables use air
from a downstream source to purge the regenerating tower. This
feature is useful for applications with downstream (dry) storage
tanks, as pulling air from a downstream source can minimize
cycling of the air compressor.
6.4 SETTING THE REGENERATION AIR FLOW
To enable the desiccant media within the towers to be thoroughly
regenerated and to get proper dryer performance, it’s necessary
to manually set the purge air flow. Setting the purge flow too high
will waste compressed air and if set too low, the dryer will not
achieve proper dew point performance.
The purge flow must be set when the left tower is operating
as the drying tower (pressurized) and the right tower is
being regenerated (de-pressurized).
The purge adjustment manifold consists of the Purge Adjustment
Valve, the Purge Pressure Gauge and the Purge Orifice. When
the left tower is the drying tower (pressurized) and the right tower
is depressurized (less than 7 PSIG), manually adjust the Purge
Adjustment Valve until the gauge reading on the purge pressure
gauge matches the Purge Pressure Gauge setting listed on
the laminated tag that’s affixed to the Orifice Plate Assembly.
SECTION 11 of this Technical Manual also includes the proper
Purge Pressure Gauge setting value.
6.5 TOWER RE-PRESSURIZATION
Upon completion of tower regeneration, and prior to the Inlet
Flow Valves changing position to switch towers, the regenerated
tower must be repressurized.
6.0 PRINCIPLES OF OPERATION
!NOTICE
When setting purge flow, the left tower must be the drying
tower for proper purge adjustment setting. When the right
tower is the drying tower, the Purge Adjustment Gauge will
read close to line pressure.
!NOTICE
On dryers equipped with the optional NEMA 4/Digital Controller
Package, or when using the optional Moisture Load Control
(MLC) feature, the purge valve MUST be adjusted to the
factory set point to ensure proper operation of these
features.
!NOTICE
Failure to re-pressurize prior to tower switch-over will result
in shocking the desiccant material and cause premature
desiccant dusting.
!NOTICE
Do not restrict purge exhaust flow in any way. Keep Purge
Mufflers clean. If exhaust flow must be piped away from the
dryer, consult factory for correct pipe sizing and configuration
guidance.

ZEKS EclipseTM 90-5,000ZPB Desiccant Dryers
www.zeks.com
6
Re-pressurization is accomplished when the appropriate Purge
Valve closes. Closing the Purge Valve allows the regeneration air
to begin to pressurize the tower. In addition to the regeneration
air, the Re-pressurization Valve, (standard on -80°F and -100°F
dew point and high pressure dryers; optional on -40°F dew
point dryers) opens allowing some additional air from the outlet
of the dryer to ensure adequate pressurization. This valve is
pneumatically operated.
6.6 VALVES
Control Air Solenoid Valves are used to actuate the Main Flow
Valves and Purge Valves. The Inlet Flow Valves and the optional
Re-pressurization Valve are normally-open valves, while the
Purge Valves are normally-closed valves. This arrangement
permits air to flow through the dryer in the event of power failure.
The Control Air Solenoid Valves are located below the Main
Control Box.
Outlet Check Valves are single direction check valves that will
allow flow in the direction shown on the P&ID, but not allow flow
in the opposite direction.
6.7 TIMING SEQUENCE
All timing functions on the standard NEMA 1 equipped dryers are
performed by a Solid State Timer (SST). For dryers equipped
with the NEMA 4 option, a Digital Controller controls all dryer
timing functions. Regardless of controller, the timing of ZEKS
-40°F, -80°F and -100°F dryers is outlined as follows:
6.7.1 TIMING CYCLE FOR -40°F DEW POINT DRYERS
The standard timing cycle for -40°F operation switches
the Inlet Flow Valve position every five minutes which
alternates the drying tower. At the same time as a tower
Inlet Valve opens, the appropriate tower Purge Valve
opens to depressurize the regenerating tower. Tower
regeneration occurs for 4 minutes and 15 seconds,
at which time the Purge Valve closes to initiate re-
pressurization.
6.7.2 TIMING CYCLE FOR -80°F AND -100°F DEW POINT
DRYERS
The standard timing cycle for both -80°F and -100°F
operation switches the Inlet Flow Valve position every 2
minutes which alternates the drying tower. At the same
time a tower Inlet Valve opens, the appropriate tower
Purge Valve opens to depressurize the regenerating
tower. Tower regeneration occurs for 1 minute and 50
seconds, at which time the Purge Valve closes to initiate
re-pressurization. The Re-pressurization Valve opens to
assist tower re-pressurization for the last 10 seconds prior
to Inlet Flow Valve switching.
The re-pressurization valve is pneumatically operated by
a shuttle valve. For -100ºF applications, the timing cycle
can be adjusted from -100ºF to -40ºF or +4ºF by entering
TECHNICIAN MODE, SCREEN 6/12, when the dryer
cycle is turned off.
6.8 PURGESYNC™FUNCTION (with NEMA 4/Digital
Controller option)
The PurgeSync™function enables the dryer to reduce the timing
of the purge cycle based on compressed air demand. When this
function is activated through the TECHNICIAN MODE within
the Digital Controller, the Controller will monitor the cycle rate
of the air compressor load / unload relay. The dryer will need to
be wired to the normally-open contact of the air compressor to
allow the controller to monitor the cycle rate. The PurgeSync™
connections are depicted on the dryer wiring diagram.
It is important to note that the PurgeSync™function is designed
to be operated independent of the Moisture Load Control (MLC)
option. For dryers equipped with the optional dew-point monitor,
PurgeSync™must be set to “OFF” in order to activate the MLC
function. Setting PurgeSync™to “ON” in TECHNICIAN MODE
will disable the MLC function.
For dryers equipped with the MLC option, the PurgeSync™
function can be used as a backup method of minimizing purge
air consumption when the Dew Point Monitor is removed
for calibration or for service. It is important to note that the
performance of the dryer is based on the inlet air temperature
and pressure conditions, in addition to flow. If the temperature of
the compressed air being supplied to the dryer is above 100oF at
the dryer inlet, the user must exercise caution in order to prevent
the desiccant beds from becoming overloaded, possibly requiring
the PurgeSync™function to be de-activated. Consult factory for
higher inlet temperatures, 101°F - 120°F. Dryer sizing is affected
by increased inlet temperatures.
When the dryer is placed into operation and the PurgeSync™
function is activated, the Digital Controller will monitor the cycle
rate of the air compressor load / unload relay contact over a
fixed time period to determine the Load Time Average (LTA)
percentage. The time period can be adjusted from 30-90 minutes
by accessing SCREEN 12 in TECHNICIAN MODE. The purge
timing cycle will be adjusted by the Controller at the completion
of the initial time interval. The table below outlines the purge time
reduction based on the Load Time Average values:
NOTE: It is important to verify that the field wiring connections
are properly installed during commissioning of the dryer in order
to prevent operational issues. If the PurgeSync™wiring is not
installed, this function must be set to “OFF” within TECHNICIAN
MODE in order to prevent operational problems. In the event that
this were to occur, the dryer would operate with a reduced purge
timing cycle that will result in desiccant overloading and failure
that would void the dryer Warranty.
6.0 PRINCIPLES OF OPERATION
Purge Cycle Time Reduction
Purge Time
Load Time Average, Reduction
LTA % Percentage
Greater than 90% 0%
70% - 89% 10%
50% - 69% 25%
30% - 49% 40%
0% - 29% 65%

ZEKS EclipseTM 90-5,000ZPB Desiccant Dryers
www.zeks.com
7
6.0 PRINCIPLES OF OPERATION
6.9 DRYER CONTROLS
Operation of ZEKS ZPB Series dryers in standard NEMA 1
configuration is automatically controlled by a Solid State Timer
(SST) in conjunction with pneumatically actuated valves. Timing
functions are performed by the SST to control all steps of the
drying Operating Cycle.
Dryers that are equipped with the NEMA 4/Digital Controller
option are controlled by a Digital Controller that includes an
illuminated display and keypad, accessible on the dryer Main
Panel.
6.9.1 OPERATING THE OPTIONAL DIGITAL CONTROLLER
The illustration shown below summarizes the Controller keypad
functions included with the NEMA 4/Digital Controller option.
When power is first applied to the dryer, this microprocessor
controller will illuminate and briefly display an INITIALIZATION
SCREEN before changing to the default HOME SCREEN. From
this screen the user can navigate to start, stop, monitor or alter
the dryer Operating Cycle and test dryer functions.
CONTROLLER BUTTONS AND KEYS
• i INFORMATION BUTTON
Restricted Level access - for factory use only.
• ON/RESUME BUTTON
Initiates Dryer Operating Cycle. Begins system
monitoring and valve switching functions.
• OFF/PAUSE BUTTON
Stops Dryer Operating Cycle. Stops valve switching
functions. Initiates Shutdown Sequence. Dryer remains
pressurized. Hold for 5 seconds for OFF function.
When Remote START/STOP is enabled, OFF button
is disabled. Compressor Shutdown will terminate dryer
operation.
• NUMERAL KEYS
Allow the operator to enter values for selectable
settings and assignments.
• ESC BUTTON
Description.
• + / - BUTTON
Used to toggle or change multistate variables. Also
allows entering negative numbers in numeric input
variables.
• ENTER BUTTON
Used to change and accept set point values.
• NAVIGATION KEYS (ARROWS)
Enables navigation between screens and lines.
INFORMATION ACCESS
DRYER ON
DRYER OFF
NUMERIC ENTRY KEYS
EXIT CURRENT SCREEN
INCREASE/DECREASE VALUE
ENTER VALUE
ACCEPT SELECTION
NAVIGATION KEYS
ILLUMINATED
DISPLAY SCREEN

6.0 PRINCIPLES OF OPERATION
ZEKS EclipseTM 90-5,000ZPB Desiccant Dryers
www.zeks.com
8
6.9.2 DIGITAL DRYER CONTROLLER DISPLAY
PARAMETERS
The controller display is a graphical interface that allows user
access to information and settings through use of UP/DOWN/
RIGHT/LEFT Navigation Keys. Information is organized under
Menu Icons as listed in the Table below.
Menu Icons are visible at the top of the display screen. Press the
RIGHT or LEFT Navigation Keys to scroll through the Icons. The
selected Icon will be highlighted (darken) when active.
Multiple SCREENS can be viewed within each Icon. Use the UP
and DOWN Navigation Keys to navigate within each Icon. The
second row of the display indicates which SCREEN is visible. NOTE: Following any period of inactivity, the display will
revert to the HOME SCREEN as shown above.
PARAMETER CHANGE INSTRUCTIONS
To Make Numeric Value Changes:
1. Use UP/DOWN Navigation Keys to highlight the value that
needs to be changed.
2. Press ENTER Button and enter a revised value using
numeric entry keys.
3. Press ENTER Button again to save the new value. The
Dryer Operating Program will then use the new value.
Text Value Changes or TEST Button Changes:
1. Use UP/DOWN Navigation Keys to highlight the value that
needs to be changed.
2. Press the +/- button to change the value to the new setting.
ZPB Controller Display
Display of dryer status, program sequence information, alarm status and
drain test information.
Location to adjust/change dryer operation settings. Password is required
to access.
View historical information related to alarms, power up condition.
General reminders to replace filter elements, inspect drains, and others.
Time & Date; Language (English is default); Backup solenoid drain
adjustment; MLC adjustment (optional)
Establish remote communication settings.
DISPLAY PARAMETER
HOME
TECHNICIAN MODE
ALARM INDICATION/EVENT LOG
MAINTENANCE ALERTS
GENERAL SETTINGS
Displays information related to sensors, valve activation, drain status, etc.
COMMUNICATIONS
STATUS
DESCRIPTIONMENU ICON
6.9.2.1 TOWER STATUS INDICATION LEGEND
LT: Left Tower
RT: Right Tower
DRY: Tower is pressurized and drying the compressed air
REGEN: Tower is depressurized and the desiccant bed
is being regenerated
VLV CHG: Valve change sequence in process to direct
compressed air and purge air through proper flow
paths
REG*: Tower is pressurized without flow. This occurs when
the tower that’s designated for regeneration is not
required to be depressurized when either, 1) MLC
set-point is satisfied and purge air is not required, or
2) PurgeSync™function is activated and the reduced
purge time cycle is completed.

6.0 PRINCIPLES OF OPERATION
ZEKS EclipseTM 90-5,000ZPB Desiccant Dryers
www.zeks.com
9
DEW PT: Indication of outlet air quality
Dryer Operation: Displays “ON”, “OFF” or “Shutting Down”
Status: “OK” if no active alarms; “ALARM” if an alert or alarm is triggered
Cycle: Indicates operation in standard “Timed” cycle or “MLC” cycle
HOME
SCREEN 1/2
Tower Status: Indication of Left Tower and Right Tower operating status
Step: Step in operating cycle and time remaining within that Step
HOME
SCREEN 2/2
6.9.3 HOME
Display of dryer status, program sequence information, alarm status and drain test information.
Enter Password: This Mode is Password protected
Password: 2010 (Use Numeral Keys to enter Password)
TECHNICIAN
MODE
SCREEN 1/12
6.9.4 TECHNICIAN MODE
Enables trained users to set parameters for triggering alarms, enable specific operating functions, and troubleshooting (including
jogging the sequence and valve output test function).
For values in this screen to be displayed, dryer must be pressurized
Tower Status: Indication of Left Tower and Right Tower operating status
Step: Step in operating cycle and time remaining within that Step
Jog Step: Use +/– key to jog the primary steps in the operating sequence
TECHNICIAN
MODE
SCREEN 2/12
Dryer must be turned OFF and system or Control Air Circuit must be
pressurized before initiating this function
Valve Test: Individual valve test function
Select Valve: Choose from four main actuated valves
Press +/–: Use the ▼(Down) Navigation Key to index through the valves
TECHNICIAN
MODE
SCREEN 3/12
Dryer must be turned OFF and system or Control Air Circuit must be
pressurized before employing this function
Select Valve: Use Navigation Buttons to select individual valves
LTIV - Left tower inlet valve RTIV - Right tower inlet valve
LTPV - Left tower purge valve RTPV - Right tower purge valve
Press +/–: Press button to test controller output
Pressure for towers will be displayed on dryers with Fail-To-Shift option.
TECHNICIAN
MODE
SCREEN 4/12
Dryer must be turned OFF and system or Control Air Circuit must be
pressurized before employing this function
Press +/–: Press key to test controller output
Pressure for towers will be displayed on dryers with Fail-To-Shift option.
(* Repressurization valves are pneumatically operated on 90-600 ZPB
models. Depressurization valves do not apply to 90-600 ZPB models. )
TECHNICIAN
MODE
SCREEN 5/12
!WARNING
Only trained Technicians should manually operate Control Valves.

6.0 PRINCIPLES OF OPERATION
ZEKS EclipseTM 90-5,000ZPB Desiccant Dryers
www.zeks.com
10
Operation Mode: “HL”, Heatless
Dew Point Adjust: Choose “-40”, “-80”* or “-100”††Changes timing
cycle by pressing +/- key. -100ºF setting can only be selected
the dryer is equipped with the -100ºF option.
-40ºF-equipped dryers - can select -40ºF or -4ºF Timing Cycle
-100ºF-equipped dryers - can select -100ºF, -40ºF or -4ºF Timing Cycle
Timing Cycle can only be adjusted when the dryer is off.
Press +/–: Press button to select “ON” or “OFF” for this feature
PurgeSyncTM requires the dryer be connected to a normally-open relay contact
from the air compressor.
††NOTICE - Requires addition of molecular sieve to desiccant bed.
TECHNICIAN
MODE
SCREEN 6/12
Differential Transmitter Setting: Set point to trigger alarm and alarm relay
on dryers equipped with optional inlet and outlet filter transducers
RESTART LAST: OFF-Dryer will need to be manually restarted following
a power outage.
RESTART AUTO: ON-Dryer will automatically restart upon a power outage.
TECHNICIAN
MODE
SCREEN 7/12
To be applicable, Dryer must be furnished with optional dew point sensor
HI DEWPT ALARM: Choose “ON” or “OFF”. When set to “ON”, alarm will
trigger when measured value exceeds the high Dew Point setting
HI DEWPT SETPOINT: Value establishes the Alarm trigger point
LO DEWPT ALM: Choose “ON” or “OFF”. In certain cases during low flow
operation, outlet dew point may fall below the low limit of the sensor. When
set to “OFF”, the Controller will disregard the Dew Point value when this
occurs.
TECHNICIAN
MODE
SCREEN 8/12
To be applicable, Dryer must include optional compressed air inlet
temperature sensor and be configured to be activated remotely
INLET TEMP ALARM: Choose “ON” or “OFF”
HI INLET TEMP SETPOINT: Value establishes the Alarm trigger point
REM START STOP: Choose “ON” or “OFF”. When Remote Start/Stop
function is activated (“ON”), dryer cannot be activated from the ON button
on the Digital Controller.
TECHNICIAN
MODE
SCREEN 9/12
For dryers equipped with the optional Fail-To-Shift function, this allows a
user to either, enable this feature when the parameter is set to “ON”, or
disable it by pressing the +/- button to display “OFF” in the selection field.
If the dryer is not equipped with this option, the selection will display “N/A”.
FAIL TO SHIFT: Choose “ON” or “OFF”
LOW PRES SETPOINT: Value establishes the Alarm trigger point. Press
“ENTER” to highlight the field, then use numeric keys to enter desired
value. Select British (PSI) or Metric (BAR) values.
Permissible setting range is displayed
TECHNICIAN
MODE
SCREEN 10/12

6.0 PRINCIPLES OF OPERATION
ZEKS EclipseTM 90-5,000ZPB Desiccant Dryers
www.zeks.com
11
Each event is logged on a single screen. UP and DOWN Navigation Buttons
are used to view each event.
Event Type (Alarm, Reminder, ON, OFF, etc.), Step Number at which the
event occurred, Time and Date Stamp will be noted.
ALARMS
EVENT LOG
SCREEN 1/2
6.9.5 ALARM INDICATION/EVENT LOGGING
The event history function logs each event that occurs during operation of the dryer. This includes alarms, maintenance reminders
and alerts, time & date stamp of dryer activation and shut-down.
The HI PRESS SETPT enables the user to set the high pressure set-point
for the Fail-To-Shift function. Once completed, press the ENTER button to
set the new value. Select either British (PSI) or Metric (BAR) values.
HIGH PRES SETPOINT: Value establishes the Alarm trigger point. Press
“ENTER” to highlight the field, then use numeric keys to enter desired value.
Press ENTER again to set the value.
Permissible setting range is displayed
The high pressure set-point will trigger a Fail-To-Shift alarm if the value
does not rise above this set-point during the pressurization cycle for the
tower that is designated for drying.
TECHNICIAN
MODE
SCREEN 11/12
This screen permits the user to set the Date and Time format that will be
depicted on certain screens and the Load Time parameter settings for the
PurgeSync™function.
DATE FORMAT: Choose desired format.
LTA TIME: Set interval for determination of average air compressor load.
TECHNICIAN
MODE
SCREEN 12/12
When an alarm occurs, an Alarm Screen appears.
Use the UP and DOWN Navigation Keys to acknowledge correction of the
alarm condition. In certain cases, if the alarm is not acknowledged, the
dryer sequence will pause or not operate until the alarm is resolved. The
Alarm Screen will indicate the alarm type. The specific time & date of the
alarm can be viewed through the Event Log.
ALARMS
EVENT LOG
SCREEN 2/2
% REMAIN: Part life remaining before replacement is recommended.
STAT: Status of Part CHG: Part should be inspected & replaced
OK: Part functioning as intended
INLET FILTER: Filter element status based on operating hours
OUTLET FILTER: Filter element status based on operating hours
MAINTENANCE
ALERTS
SCREEN 1/5
6.9.6 MAINTENANCE ALERTS
General reminders for replacement of filter elements, inspection of drains as well as others.

6.0 PRINCIPLES OF OPERATION
ZEKS EclipseTM 90-5,000ZPB Desiccant Dryers
www.zeks.com
12
% REMAIN: Part life remaining before replacement is recommended.
STAT: Status of Part CHG: Part should be inspected & replaced
OK: Part functioning as intended
DESICCANT: Useful desiccant life remaining based on operating hours.
Recommended time for inspection and determination of replacement
requirement.
FILTER REGULATOR ELEMENT: Condition of filter element based on
operating hours. Filter element should be inspected periodically and
replaced as required to ensure proper operation of Control Air Valves.
MAINTENANCE
ALERTS
SCREEN 2/5
OPERATING HOURS: Total operating hours since Dryer startup date.
PURGE HOURS: Total hours Purge Valves have been active.
PURGE TIME %: Percentage of dryer operating time Purge Air is utilized.
This is dependent upon operating conditions and the demand on the dryer.
MAINTENANCE
ALERTS
SCREEN 3/5
SERVICE REMINDER: Enables user to setup Service Reminder Interval
for key components. An alert will be displayed indicating that inspection &
replacement may be required when the time Interval is reached.
INLET FILTER: Reminder Interval (Weeks)
OUTLET FILTER: Reminder Interval (Weeks)
MAINTENANCE
ALERTS
SCREEN 4/5
SERVICE REMINDER: Enables user to setup Service Reminder Interval
for key components. An alert will be displayed indicating that inspection &
replacement may be required when the time Interval is reached.
DESICCANT: Reminder Interval (Weeks)
CONTROL AIR FILTER/REG ELEMENT: Reminder Interval (Weeks)
MAINTENANCE
ALERTS
SCREEN 5/5
LANGUAGE: Press +/- key to select desired language.
UNITS: Press +/- key to choose either Imperial or Metric units.
GENERAL
SETTINGS
SCREEN 1/3
6.9.7 GENERAL SETTINGS
Access for setting Time & Date; Language (English is default); Backup Solenoid drain adjustment.
TIME: Time is displayed in 24 hour format (Military Time).
DATE: MM/DD/YY can be altered to DD/MM/YY in TECHNICIAN MODE
Screen 12.
Press Return key to highlight value to be changed then press ENTER
button to set desired value. Use Right Navigation key to move cursor to
change the value in each row.
GENERAL
SETTINGS
SCREEN 2/3
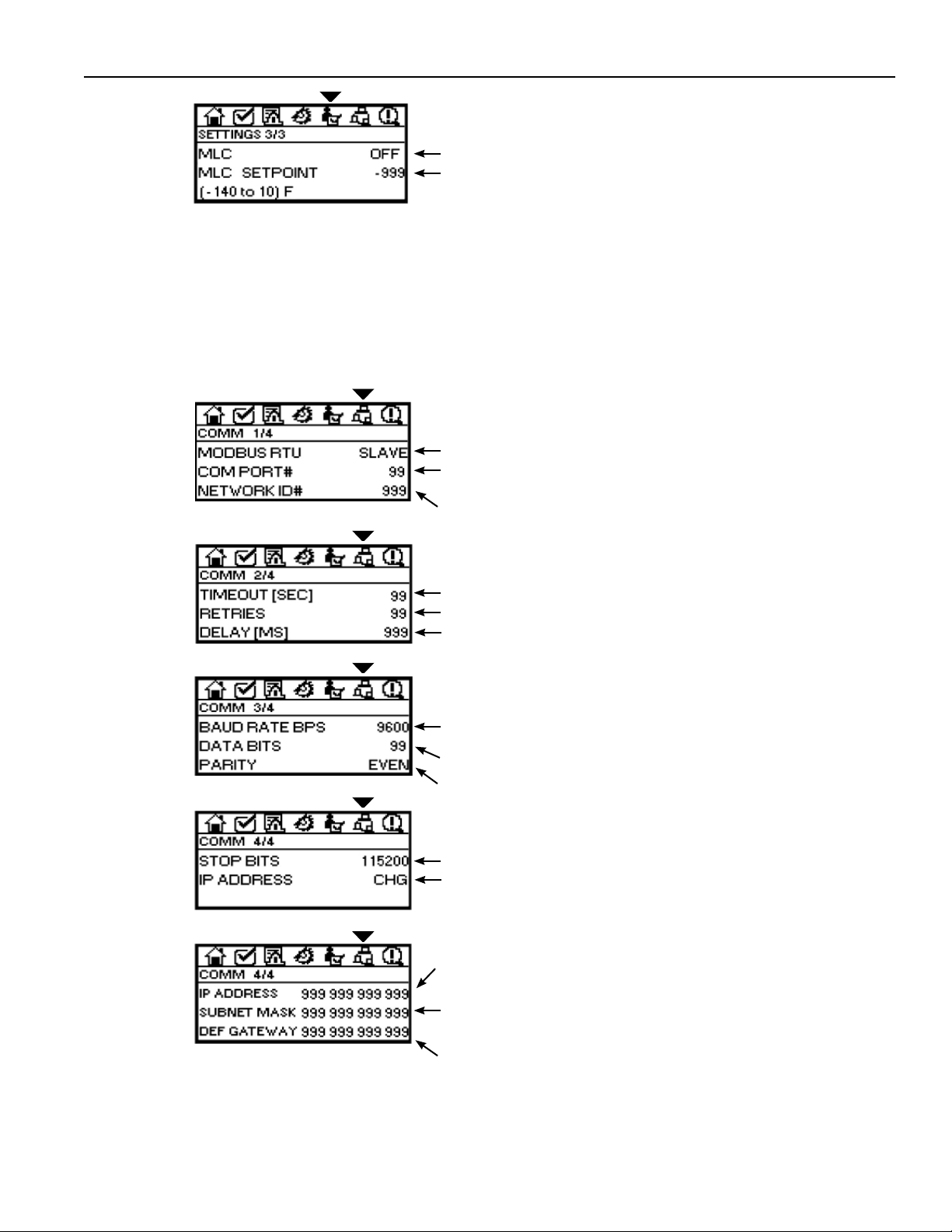
6.0 PRINCIPLES OF OPERATION
ZEKS EclipseTM 90-5,000ZPB Desiccant Dryers
www.zeks.com
13
For dryers equipped with optional Moisture Load Control (MLC) functionality.
Dryer must be equipped with Dew Point Sensor:
MLC: Press +/- key to activate or de-activate MLC function. Value will
display ON when activated.
MLC Setpoint: Highlight the value and press ENTER button to choose from
pre-defined values.
NOTE: PurgeSync™Function is de-activated when MLC function is active.
GENERAL
SETTINGS
SCREEN 3/3
MODBUS RTU: Controller is configured to be a slave.
COM PORT: Port 1 is dedicated to Communications. For information only
(non-adjustable).
NETWORK ID#: To set: press Enter Button; use numeric keys to enter
value; press Enter Button to save value.
COMMUNICATIONS
SCREEN 1/4
6.9.8 COMMUNICATIONS
Establish remote communication settings.
For information only (non-adjustable).
TIMEOUT: Default - 1 seconds.
RETRIES: Default - 3 attempts.
DELAY: Default - 10 minutes.
COMMUNICATIONS
SCREEN 2/4
BAUD RATE: Press Enter key to highlight field. Press +/- to select from
preset values.
DATA BITS: Default - 8. For information only (non-adjustable).
PARITY: Default - None. For information only (non-adjustable).
COMMUNICATIONS
SCREEN 3/4
STOP BITS: Default - 1. For information only (non-adjustable).
IP ADDRESS: Press +/- key to access Setup Screen.
COMMUNICATIONS
SCREEN 4/4
IP ADDRESS: Default - 192.168.192.10. To change number, use UP/
DOWN Navigation Keys to position Cursor where change is needed, press
Enter key, use Numeral Keys to enter 3 digit number, press Enter to save.
SUBNET MASK: Default - 255.255.255.0. To change number, use UP/
DOWN Navigation Keys to position Cursor where change is needed, press
Enter key, use Numeric Keys to enter 3 digit number, press Enter to save.
DEF GATEWAY: Default - 192.168.192.254. To change number, use UP/
DOWN Navigation Buttons to position Cursor where change is needed,
press Enter Button, use Numeral Keys to enter 3 digit number, press Enter
to save.
COMMUNICATIONS
SCREEN 4/4
(Setup)

6.0 PRINCIPLES OF OPERATION
ZEKS EclipseTM 90-5,000ZPB Desiccant Dryers
www.zeks.com
14
LT, RT: Left Tower and Right Tower operating status.
STEP, TIME: Step in Operating Cycle and time remaining within Step.
LTA%, Status: Load Time Average based on air compressor Load/Unload
relay output on fixed time interval. LTA STATUS: ON or OFF - LTA function
can only be active when dew point monitoring function is not activated.
OPERATING
STATUS
SCREEN 1/7
6.9.9 OPERATING STATUS
Displays information related to sensors, valve activation, drain status, etc.
LTIV, RTIV: Position of normally-open Left Tower and Right Tower Inlet
Valves. Control outputs are de-energized when valves are open.
LTPV, RTPV: Position of normally-closed Left Tower and Right Tower Purge
Valves. Control outputs are energized when valves are open.
LT, RT: Indication of Left Tower and Right Tower Pressure (PSI) when dryer
is equipped with Fail To Shift option.
OPERATING
STATUS
SCREEN 2/7
LT, RT: Indication of Left Tower and Right Tower Pressure (PSI) when dryer
is equipped with Fail-To-Shift option.
OPERATING
STATUS
SCREEN 3/7
LT, RT: Left and Right Tower operating status - DRYING or REGENERATING
MLC, SETPT: Status of Moisture Load Control option - ON or OFF. Indication
of Setpoint: -40, -80, -100. Display of NA if option is not installed.
DRYER INLET TEMP: (Optional) Indication of compressed air temperature
at dryer Inlet. Display of NA if option is not installed.
OPERATING
STATUS
SCREEN 4/7
LT, RT: Left and Right Tower operating status - DRYING or REGENERATING
LT, RT: Left and Right Tower pressures with Fail To Shift Tower Pressure
Monitoring (Optional). Display of NA if option is not installed.
LT, RT: Display of ALARM if Left or Right Tower does not achieve proper
pressure during normal operation or at time of tower shift.
OPERATING
STATUS
SCREEN 5/7
INLET FLT: Optional Inlet Filter Delta P Alarm. Actuated by either differential
pressure switch or transducer. Displays: CHG for dp switch; DP value for
transducer.
OUTLET FLT: Optional Outlet Filter Delta P indication. Display of NA if
option is not installed.
OPERATING
STATUS
SCREEN 6/7
FILTER DRAIN STATUS: Displays the status of the optional Electronic No-
Air Loss Drain provided for the Inlet Filter. Display of NA if option is not
installed.
OPERATING
STATUS
SCREEN 7/7

ZEKS EclipseTM 90-5,000ZPB Desiccant Dryers
www.zeks.com
15
7.1 MOISTURE INDICATOR
The Blue Moisture Indicator (BMI) analyzes a sample of the
control air supply that is taken from the dryer outlet. If dryer
performance deteriorates, the BMI provides a visual indication of
compromised dew point. Under normal operating conditions, the
beaded media in the BMI appears blue in color. In the event of a
dryer malfunction or prolonged dryer shut down, it will turn gray
in the presence of moisture.
The dryer sequence will not start if the tower pressures are below
80 PSI at time of dryer startup. For dryers equipped with the
Fail-To-Shift and NEMA 4 options, the valves will not operate
if the line pressure is less than 75 PSIG. For dryers equipped
with the Moisture Load Control option, the Dew Point Transmitter
must not be installed until the dryer has continuously operated
for 24 hours and the Blue Moisture Indicator (BMI) appears blue
in color. NOTE: The MLC function must be turned offduring
this period to avoid unnecessary alarms.
NEMA 1 CONFIGURATION ALARMS AND INDICATORS
7.2 HIGH HUMIDITY ALARM (Optional)
The purpose of the High Humidity Alarm is to provide the
operator an indication if the equipment fails to supply air at
its designed dew point. This is accomplished by passing a
sample of dried air from the control line across a sensing
element. If the sensing element is exposed to air with a dew
point of -10°F or higher (for -40°F dryers), the sensor sends
a signal to the humidistat. Power is then supplied to the red
alarm light on the NEMA 1 enclosure. This light will remain
illuminated until the problem is corrected and the sensing
element has dried out.
7.3 FAILURE-TO-SHIFT ALARM (Optional)
The Failure-to-Shift Alarm provides an indication of valve
switching failure that could occur when the towers transition
between the drying and regeneration steps. Pressure
transducers are utilized to constantly monitor the pressure of
the towers during the drying and regeneration steps to ensure
that the correct pressure values are maintained.
NEMA 4 CONFIGURATION ALARMS AND INDICATORS
7.4 FAIL-TO-SHIFT AND TOWER PRESSURE ALARM
MONITORING (with NEMA 4/Digital Controller option)
The optional Fail-To-Shift alarm provides an indication of
a valve failure that could occur when the towers transition
between the drying and regeneration steps. Pressure
transducers are utilized to constantly monitor the pressure
of the towers during the drying and regeneration steps to
ensure correct tower pressure values are maintained during
each step.
The tower designated for regeneration should be under 7 PSI
during this step while the other tower should be maintained
at line pressure. When the mufflers are properly serviced
and maintained, regenerating tower pressure will typically be
under 3 PSI. An alarm will be triggered under the following
conditions:
1.De-pressurization Fault: The tower designated for
regeneration does not de-pressurize below 7 PSI within a
designated time period immediately after the designated
purge valve is energized AND/OR...
2.Pressurization Fault: The previously regenerated tower
that switches to drying does not pressurize above a high
pressure set-point within a designated time period.
The Fail-To-Shift option can be de-activated by accessing
SCREEN 10 in TECHNICIAN MODE. The function can be
turned offif a fault occurs with a pressure transducer.
During normal dryer operation, the Controller will also monitor
the tower pressure value of the Drying tower to ensure the
system is operating properly. The dryer must be equipped
with the Fail-To-Shift control option for this to operate
properly. TABLE 7.6 ALARM STATES details a list of Alarms
& Controller actions that occur if an irregular pressure value is
detected during normal ZPB dryer operation.
7.5 MOISTURE LOAD CONTROL (with NEMA 4/Digital
Controller option)
The Moisture Load Control (MLC) feature is designed to
minimize the use of purge air during low flow or low water
loading conditions. On -40°F units, a sensor samples the
moisture content from the online tower and provides a signal
to the Controller. This function utilizes a Dew Point Transmitter
to monitor the dew point of the air exiting the dryer. Note that
the Dew Point Transmitter must not be installed on a new
start-up and not until the dryer has continuously operated for
a minimum of 24 hours and the BMI appears blue in color.
When the MLC function is activated, a 30 minute delay will be
initiated to allow the dryer to regenerate. If the MLC set-point is
satisfied for more than eight continuous hours, the Controller
will revert to a fixed cycle for a period of 60 minutes in order to
prevent the desiccant beds from becoming overloaded during
rapid changes in compressed air demand.
See TABLE 7.6 ALARM STATES for a list of Alarms, Causes and
Recommended Actions.
7.0 ALARMS AND INDICATORS
!NOTICE
Do not restrict purge exhaust flow in any way. Keep Purge
Mufflers clean. If exhaust flow must be piped away from the
dryer, consult factory for correct pipe sizing and configuration
guidance.

ZEKS EclipseTM 90-5,000ZPB Desiccant Dryers
www.zeks.com
16
7.0 ALARMS AND INDICATORS
ALARM
Fail-To-Shift
(Dryer must be equipped
with this Option).
Low Tower Pressure
(Dryer must be equipped
with Fail-To-Shift Option)
Muffler Clog Warning
(Dryer must be equipped
with Fail-To-Shift Option)
Inlet filter Pressure Drop
Warning (Optional)
Outlet filter Pressure
Drop Warning (Optional)
High Inlet Temperature
(Optional)
ITEM
1
2
3
4
5
6
CAUSE
1. De-pressurization Fault: The tower
designated for regeneration does not
de-pressurize below 7 PSI within a
designated time period immediately
after the designated purge valve is
energized.
2. Re-pressurization Fault: The previously
regenerated tower that switches to
drying does not pressurize above a high
pressure set-point within a designated
time period.
1. Right & Left Tower pressure values are
below 80 PSI prior to initiating dryer
operation.
2. Pressure of the drying tower falls below
80 PSI after the tower shift has been
completed. The alarm will be triggered
if the pressure value remains below 80
PSI for 10 seconds continuously.
Pressure value of regeneration tower rises
above 7 PSI after the de-pressurization
step is completed.
(Regeneration tower pressure should be
below 7 PSI.)
Filter element clogged and activates either
pressure switch or pressure transducer.
Filter element clogged and activates either
pressure switch or pressure transducer.
Alarm is triggered if the temperature of
the compressed air exceeds the set-point
value established in the technician mode.
Continues
To Operate
X
X
X
X
Stopped /
Paused
Paused
Stopped
Paused
Paused
Alarm
Contact
Activated while
alarm condition
is true
Activated while
alarm condition
is true
Activated while
alarm condition
is true
Activated while
alarm condition
is true
Activate while
alarm condition
is true
Activate while
alarm condition
is true
Activated while
alarm condition
is true
RECOMMENDED ACTION
1. Troubleshooting Sequence:
a. Verify operation of purge valve. Use
test button on control air solenoid to
verify operation.
b. Inspect and verify control air solenoid
valves are functioning properly & pilot
air lines are not clogged.
c. Verify pressure transducer readout
values. Values should read close to
gauge values.
d. Inspect mufflers for clogging. Proper
safety procedures must be followed
when servicing mufflers.
e. Inspect control air filter regulator and
verify element is not clogged.
2. Verify the following:
a. Appropriate purge valve is closed.
b. Inspect and verify control air solenoid
valves are functioning properly & pilot
air lines are not clogged.
c. Pressure transducer readout matches
tower pressure gauge values.
d. Repress valve is operating properly
(-100oF PDP) applications only.
e. Inspect control air filter regulator and
verify element is not clogged.
1. Dryer must be allowed to pressurize prior
to starting the dryer sequence.
2. The check valves should be inspected
and the system pressure should be
verified.
a. Restart dryer after pressure values
have been verified. The dryer will
restart from the initial step.
1. Shut-down dryer and follow proper safety
precautions.
2. Inspect & replace mufflers.
3. Restart the dryer and verify regenerating
tower pressure is below 3 PSI.
1. Shut down dryer and follow proper
safety precautions. System must be de-
pressurized prior to servicing.
2. Inspect & replace filter elements.
3. Restart the dryer and verify alarm is
resolved.
1. Shut down dryer and follow proper
safety precautions. System must be de-
pressurized prior to servicing.
2. Inspect & replace filter elements.
3. Restart the dryer and verify alarm is
resolved.
Inspect air compressor after-cooler and
blower for cooler. Clean if clogged. High inlet
temperatures will reduce dryer performance.
CONTROL SEQUENCE ACTION
7.6 ALARM STATES
For dryers equipped with NEMA 4/Digital Controller option

7.0 ALARMS AND INDICATORS
ZEKS EclipseTM 90-5,000ZPB Desiccant Dryers
www.zeks.com
ALARM
Low Inlet Temperature
Warning (Optional)
Inlet Temperature Fault
(Optional)
Filter Drain Alarm
(Optional - Electronic
No Air Loss Drain)
Dew Point (DP) Sensor
Fault (Optional)
High Dew-point Warning
(Must be equipped with
MLC Option)
MLC Off Warning
(Must be equipped with
MLC Option)
Pressure Sensor fault
Inlet Filter Service
Reminder
Outlet Filter Service
Reminder
Desiccant Service
Reminder
Filter/Regulator Element
Service Reminder
ITEM
7
8
9
10
11
12
13
14
15
16
17
CAUSE
If the Inlet temperature falls below 70oF, a
Warning will be displayed.
Fault occurs if the temperature sensor is
operating out of the normal measurement
range.
Electronic no air loss drain alarm contact
is triggered.
Fault occurs if the DP sensor is operating
outside the normal measurement range.
Warning is triggered if the measured
dew point exceeds the set-point value
established in SCREEN 8 of the
TECHNICIAN MODE.
Warning is triggered if the DP sensor is
out of range.
Warning is triggered if the tower pressure
transducer is out of range.
If fault condition occurs, Fail-To-Shift
function will stop operating.
Maintenance Alert: A pop-up ALERT will
display indicating that the Inlet Filter element
should be replaced. If the user selects “NO”,
the reminder will be acknowledged and will
re-appear in two weeks.
Maintenance Alert: A pop-up ALERT will
display indicating that the Outlet Filter element
should be replaced. If the user selects “NO”,
the reminder will be acknowledged and will
re-appear in two weeks.
Maintenance Alert: A pop-up ALERT
will display indicating that the desiccant
charge should be inspected. If the
user selects “NO”, the reminder will be
acknowledged and will re-appear in two
weeks.
Maintenance Alert: A pop-up ALERT will
be displayed to indicate that the Filter/
Regulator element should be replaced. If
the user selects “NO”, the reminder will be
acknowledged and will re-appear in two
weeks.
Continues
To Operate
X
X
X
X
X
X
X
X
X
X
X
Stopped /
Paused
Paused
Alarm
Contact
No Alarm
No Alarm
Activated while
alarm condition
is true
No Alarm
Activated while
alarm condition
is true
No Alarm
Activated while
alarm condition
is true
No Alarm
No Alarm
No Alarm
No Alarm
RECOMMENDED ACTION
Low inlet temperatures to the dryer may lead
to performance problems.
Check wiring and verify that correct resistor
is installed. Replace sensor as required.
Inspect drain sump for debris and test-fire
drain. Verify that drain is operating properly
by using Test Button after drain has been
inspected.
Remove and inspect DP sensor. MLC will
stop operating when this occurs.
• NOTE: DP sensor should not be installed
within the first 24 hours of continuous
dryer operation.
Inspect wiring connections and resistor
Refer to information related to Elevated Dew
Point in SECTION 10 TROUBLESHOOTING.
• Remove and inspect DP sensor to
determine condition of sensor.
• Refer to information related to
Elevated Dew Point in SECTION 10
TROUBLESHOOTING.
• Compare value displayed on Controller
with corresponding Tower Pressure
Gauge.
• Inspect wiring and resistor values.
• Determine if sensor needs to be replaced.
• Inspect valve operation.
Follow proper safety shutdown practices and
replace the Inlet Filter element.
Follow proper safety shutdown practices and
replace the Outlet Filter element.
Follow Dryer Shutdown Sequence to
shutdown and depressurize dryer. Visually
inspect desiccant charge in each tower
and submit sample to ZEKS for testing.
Determine if desiccant media replacement
is necessary.
Follow proper safety shutdown practices and
replace the Filter/Regulator element.
CONTROL SEQUENCE ACTION
7.6 Alarm States (continued)
17

8.0 INSTALLATION AND START-UP
ZEKS EclipseTM 90-5,000ZPB Desiccant Dryers
www.zeks.com
18
8.1 APPLICATION AND CHECK ANALYSIS
To achieve the best dryer performance, carefully check and verify
that each design and installation requirement outlined below is
satisfied.
The dryer is designed to operate with a compressed air inlet
temperature ranging from 80ºF to 120ºF and an operating
pressure ranging between 80 PSI and 150 PSI. The air
compressor that feeds air to the dryer must be sufficiently sized
to meet the process air demand as well as provide the volume
necessary for desiccant regeneration.
The standard ZPB series heatless desiccant dryer is rated for a
maximum allowable working pressure of 150 PSIG. If the dryer
is to be operated at pressures below 80 PSIG, the factory should
be consulted to verify sizing and configuration.
The standard dryer is rated to operate at an inlet temperature
and pressure of 100ºF @ 100 PSI. Installations with elevated
inlet air temperatures may require a dryer with greater capacity to
achieve expected dew point performance. When compressed air
at lower temperatures is supplied to the dryer, performance will
be reduced. The compressed air supply must have a minimum
temperature of 80ºF at the dryer inlet to assure proper dryer
operation. The operating conditions should be verified prior to
dryer installation and operation to ensure it is properly sized.
The dryer should be installed indoors where the ambient
temperature does not drop below 50ºF or rise above 120ºF.
Consult factory for outdoor installations where additional
provisions may be required for low ambient temperatures.
8.2 LOCATING AND MOUNTING
Using a forklift, lift the dryer only at the lift points identified with
labeling. Use care to avoid damage to manifold.
Bolt the dryer to the foundation using the bolt holes provided in
the base frame. Anchor bolts should project a minimum of 3.5
inches above the foundation. Refer to SECTION 12, GENERAL
ARRANGEMENT DRAWINGS, for details.
8.3 PIPING
Pipe the compressed air lines to the dryer inlet and outlet
connection points. Locate a prefilter as close as possible to the
dryer inlet. Ensure the positioning allows access and room to
service and maintain the dryer. Refer to the General Arrangement
drawing.
Note that the wet air inlet is at the dryer’s lower manifold, while
the dry air outlet is at the dryer’s upper manifold. In situations
where air supply is required 24 hours a day (where it is
undesirable to interrupt the airflow), a three valve by-pass system
is recommended to bypass the dryer. To keep pressure drop at
a minimum, use the fewest number of elbows possible. THE
BYPASS SHOULD BE USED WHEN TROUBLESHOOTING
THE AIR COMPRESSOR OR WHEN SERVICING THE ZPB
DRYER TO PREVENT FLOODING OF THE DESICCANT BED.
When all piping is connected, all joints, including those on the
dryer, should be soap bubble tested at line pressure to ensure
no joints have been damaged in transit or during site placement.
All installed piping must be self-supported. The dryer manifold
piping cannot be used to support interconnecting piping.
8.4 FILTRATION
NOTE: A Prefilter and an Afterfilter must be provided in your
dryer installation.
A coalescing Prefilter, mounted before the dryer, will protect
desiccant beds from contamination by oil, entrained water and
pipe scale to extend dryer desiccant life and assure proper dryer
operation. Locate Prefilter as close to the dryer as possible.
Prefilter drain must be inspected periodically to ensure proper
operation. Drain maintenance is not covered in the Warranty.
It is recommended that a mechanical separator with a properly
functioning drain be installed immediately preceding the Prefilter
to remove bulk liquid and entrained water.
Installation of a Particulate Afterfilter mounted after the dryer will
help eliminate carryover of desiccant dust into the air system.
8.4.1 FILTER DRAIN VALVE (With Factory Installed Filters)
When 90-1,500 SCFM dryers come from the factory with filters
installed,the Automatic Drains (PN: 24335028) must be checked
for correct configuration prior to pressurization of the dryer:
• Filters must be oriented vertically for proper operation.
• The drain stem must be properly adjusted as follows:
Twist the drain stem (No. 18 in Figure 2) to set for AUTOMATIC
(Normal) or MANUAL (Test) operation (See Figure 1 below).
• Twist the stem fully clockwise (when viewed from bottom
of filter bowl) for AUTOMATIC draining of condensate.
This is the Normal position.
• Twist the stem fully counter-clockwise (when viewed from
bottom of filter bowl) for MANUAL draining of condensate
(Test/Bleed) or if connected to an external drain.
Minimum operating pressure of 22 psig is required for the float
that’s within the drain assembly to seat properly. Pressures
below 22 psig will allow air to escape from the drain. This will
occur when the compressed air system is being pressurized.
!NOTICE
The standard dryer is not rated for any gas other than air.
!NOTICE
ZEKS recommends the mufflers be cleaned after initial dryer start-
up to remove desiccant dust that may have been generated during
dryer shipment. Following the first 30 minutes of dryer operation,
de-energize and depressurize the dryer and remove the mufflers.
Disassemble and clean the removable insert inside each muffler
core. Reassemble and reinstall mufflers prior to resuming dryer
operation. To prevent additional clogging, periodic inspection of
mufflers is recommended.
!NOTICE
All ZPB model dryers must have proper filtration. Liquid water
and oil must be removed before compressed air enters the
dryer. Ensure separators, Prefilters and drains are in good
working order. Failure to do so will void warranty.
Figure 1
AUTOMATIC
MANUAL
This manual suits for next models
18
Table of contents
Other ZEKS Dehumidifier manuals