6K Products DH0600 Guide

OPERATION AND PARTS MANUAL
DH0600 10G24 Connect and Cut Hydraulic Chain
Information subject to change without notice.

2
SAFETY PRECAUTIONS
⇒The unit you have purchased may require you to install additional guarding to meet State and
Federal safety requirements.
⇒Do not move the log when it is being cut or when the saw is down. This action may damage the
bar, chain or other components or could cause bodily harm or injury.
⇒The log must be clamped before cutting. The bar, chain or other components could be damaged.
You could suffer bodily harm or injury.
⇒Do not make repairs or adjustments to this product other than those listed in this manual except
when directed to do so by 6K Products.
⇒All persons working near this machine must wear eye protection and hearing protection.
⇒Use extreme caution around the cutting chain. It is sharp and may cause bodily harm or injury.
⇒Petroleum products are used with this product. Use appropriate caution when operating or
servicing. These products are flammable and may cause eye or skin irritation.
⇒Always use 6K Products approved parts when making repairs. Replacement parts must meet or
exceed the specifications of the original equipment manufacturer.
⇒The information in this manual is subject to change without notification.
⇒This manual is intended for safe operation and maintenance of the 6K Products, 10G24 Connect
and Cut Hydraulic Chain Saw. 6K Products, welcomes any and all suggestions on how to improve
this manual or the 10G24 Connect and Cut Hydraulic Chain Saw.

3
Table of Contents
Cover page ....................................................................................................................................................................... 1
Safety Precaution ......................................................................................................................................................... 2
Table of Contents ......................................................................................................................................................... 3
Introduction.................................................................................................................................................................. 4
Warranty....................................................................................................................................................................... 4
Installation.................................................................................................................................................................... 4
Hydraulic Connections.................................................................................................................................................. 5
Chain Tension and Sharpening ..................................................................................................................................... 6
Sprocket Removal and Replacement............................................................................................................................ 7
Feed Control Adjustment ............................................................................................................................................. 8
Bar Oil Pump Adjustment ............................................................................................................................................. 9
Operating Instruction ................................................................................................................................................. 10
Parts and Service Information .................................................................................................................................... 10
Main Sub Assembly Parts ........................................................................................................................................... 11
Bar Plate Assembly Parts ............................................................................................................................................ 12
Feed Cylinder Assembly Parts .................................................................................................................................... 13
Bar Oil Pump Assembly Parts ..................................................................................................................................... 14
Feed and Motor Control Manifold Parts .................................................................................................................... 15
Bar Oil Tank Assembly Parts ....................................................................................................................................... 16
Hose Layout ................................................................................................................................................................ 17

4
Introduction
Thank you for purchasing a 6K Products product. Our goal is to provide quality products for your job. This manual
contains warranty information, installation information, operation instructions, parts ordering information, and
service contact information.
Warranty
This 6K Products product carries a one year or 2000 hour warranty on the 6K Products designed and built
components covering material and workmanship. Purchased components carry the manufactures warranty. This
warranty does not cover normal wear from use, damage from abuse or misuse, damage from contamination,
damage from natural disasters, fire damage or incorrect installation. This warranty does not cover labor to remove
and replace parts, shipping and handling of parts, or shipping and handling for items returned for repair. If any
component fails you must contact 6K Products at (360)264-2141 before doing any repair work. We will provide
assistance to obtain warranty from other manufactures on their components.
Installation
When you receive the two boxes containing parts, you will need to reassemble the unit. The larger box (Fig. 2)
contains the main frame sub assembly, (Fig.1, items 1 and 2). The smaller long box (Fig. 3) contains the feed cylinder
(Fig. 1, item 3), feed and motor control valve (Fig. 1, item 4), bar oil tank (Fig. 1, item 5), bar guard (Fig. 1, item 6),
bar oil pump (Fig. 1, item 7), saw bar (Fig. 1, item 8), saw chain (Fig. 1, item 9), weld down mount plate (Fig. 1, item
10), and assembly fasteners.
Fig. 1
Fig. 2
Fig. 3

5
After assembling the components as shown in figure 1, position the saw bar square to the log, at the correct height
with clearance between the bar guard and the side of the largest log and weld down solidly (Fig. 4).
Hydraulic Connections
The hydraulic requirements to operate the saw are 9 to 11 gallons per minute at 2000 psi from a directional control
valve that has port A and B blocked in the neutral position. These pictures are examples of valve spool that will
work. The hydraulic valve can be manual or electric control. Figure 5 shows hose
connections for correct operation.
Fig. 4
Fig. 5

6
The return hose can be #8 or 1/2” diameter for the first three feet, if a longer hose is required it must be #12 or 3/4”
up to thirty feet. If the total return hose length is greater than thirty three feet #16 or 1” hose should be used. The
filter must be rated for 20 GPM plus any additional pump flowing into it. The saw motor should run between 4000
RPM and 5500 RPM. At this speed the pressure at the return to filter connection should not exceed 80 psi when the
saw motor is running. We do not recommend using quick disconnects but if you choose to use quick disconnects in
the tank line, first consult the manufacture to determine the correct size to keep the back pressure low enough in
cold temperatures. Failure to properly size the hose and filter or properly connect the return hose to a filter and
tank will shorten the motor shaft seal life and will not be covered by warranty.
Chain Tension and Sharpening
Figure 6 shows the chain tensioning screw. A #2 or #3 Phillips screwdriver is required to turn the tension screw. With
the supplied saw bar, correct tension is when the cutters come off the rails roughly 1/8” with a tug of finger
pressure. Refer to the Oregon Mechanical Timber Harvesting Handbook for more tensioning information and
sharpening information.
Fig. 6

7
Sprocket Removal and Replacement
The chain saw sprocket is connected to the shaft with a tapered bushing. To remove the sprocket remove the Cap
Screws (Fig. 7, Item 3) and screw them into the Threaded Holes, tighten up to 36 inch pounds to push the Sprocket
(Fig. 7, Item 1) off the bushing. You may need to tap the Sprocket towards the motor with a hammer to assist in
getting the Sprocket loose from the Bushing (Fig. 7 Item 2). Lightly drive a flat blade screwdriver into the slot of the
Bushing.
Pry between the Bushing and the Sprocket to get the Bushing off the shaft. Watch that the Drive Key (Fig. 7, item 4)
does not get lost.
To install the Sprocket, slide the Sprocket (Fig. 7, item 1) over the motor shaft, slide the Bushing (Fig. 7, item 2) onto
the shaft with the Drive Key (Fig. 7, item 4) aligned. Position the sprocket groove offset towards the motor about the
width of the bar groove with the Bushing just contacting the Sprocket. Insert the Cap Screws (Fig. 7, item 3) through
the large hole in the Bushing and screw them into the threaded holes of the Sprocket. Torque the Cap Screws (Fig. 7,
item 3) to 36 inch pounds. Check to make sure the sprocket groove is aligned with the bar groove. If the alignment is
not correct, remove and replace the sprocket and bushing by adjusting the position before tightening the cap
screws.
Fig. 7

8
Feed Control Adjustments
Connect and Cut saw systems have a control manifold with cartridge valves to limit flow to the saw motor and feed
cylinder, and a feed modulating valve to adjust the feed speed based on the saw motor pressure. We have tested
the operation of your system to set the valves before shipping so your system should cut any diameter, species, or
hardness of wood without stalling the chain in the cut. The feed modulating valve will make the bar pulsate in the
cut on larger or harder wood as it is trying to cut as fast as possible. It may be possible to fine tune the cutting for
your application by adjusting the saw feed speed adjustment valve (Fig. 8, item 11). For larger or harder wood
loosen the jam nut with a 9/16” wrench and screw the adjustment screw out with a 5/32” hex key wrench (Allen
wrench), this will slow the bar movement down, lock the jam nut down when done adjusting. For smaller softer
wood you may want to speed up the bar movement by screwing the adjustment screw in. Having the bar move too
fast may cause the chain to stick when starting into the cut if the chain hits a knot. It is possible to tune the feed
modulating valve (Fig. 8, item 2) by loosening the jam nut with a 9/16” wrench and adjusting the screw with a 3/16”
hex key. A smoother cut may be possible by screwing the adjustment screw out, but this may increase the cutting
time in larger or harder wood. If the wood is dry and hard screwing the feed modulating adjustment in may decrease
cutting time. Screwing the feed modulating adjustment in too far will cause the chain to stall. Be sure to lock the jam
nut after adjusting a valve.
Fig. 8

9
Bar Oil Pump Adjustments
The DH0144 bar oil pump (Fig. 9) is a single acting pump that can pump up to 32 cc, or 1.08 oz., of bar oil per cycle,
enough for about 30 seconds of cutting. There is a hose connected to the feed and motor control valve manifold
(Fig. 8, item 6) that connects to the fitting (Fig. 9, hydraulic pressure in) on the bar oil pump. When a cut is started
flow and pressure from the manifold pushes on the pumping rod and piston to force a metered amount of oil to the
bar. Very little rotational adjustment is needed for the metering valve in Figure 9. Turning it clockwise reduces the
speed oil is pumped and turning it counterclockwise increases the speed the oil comes out. If you run the tank out of
oil you may need to prime the pump. To prime the pump remove the barrel nut and pull out the pumping chamber,
pumping piston, and pumping rod. Fill the barrel with bar oil up to the vent hole. Reinstall the pumping rod
assembly into the pumping chamber with care to not damage the rod seal. Reinstall the pumping chamber and
pumping rod assembly into the barrel, with care to not damage the piston or the O-ring, and retighten the barrel
nut. To reduce the chance of seal damage make sure the seals are oiled and wiggle in a circular motion as you push
the parts together.
Fig. 9

10
Operating Instructions
Before, and periodically during, operation you must check the bar oil level and chain tension. We recommend using
a good quality bar oil of the correct viscosity for your areas operating temperatures. Because of the wide
temperature range between winter and summer two different viscosity oils may be required. Tension the chain as
described on page 6. The log being cut must be clamped prior to sawing. Once the log is positioned and clamped the
saw control valve needs to be opened for full flow to cut. After completing the cut reverse the valve and raise the
saw bar. The saw motor only runs when the bar is being lowered. The bar will only receive up to 32 cc of oil when
the saw motor is operating or the bar is feeding down.
Parts and Service Information
For parts and service contact 6K Products. Our hours of operation are 8:00 AM to 4:30 PM, Monday through Friday,
Pacific Time excluding holidays.
Phone: 360-264-2141
Fax: 360-264-5105
Email ed@6kproducts.com
Mail and shipping address:
6K Products
1006 143rd Ave. S.E.
Tenino, WA 98589

11
MAIN SUB ASSEMBLIES
ITEM No. QTY. PART No. DESCRIPTION REMARKS
1 1 DH0066 HARVESTER BAR, 75 CM OREGON 752HSFN114
2 1 DH0055 SAW CHAIN, 80 gauge, 89 drive links OREON 18HX
3 1 DH0130 MAIN FRAME
4 1 FDTD10 DRILLED WELD DOWN PLATE
5 1 DH0347 BAR PLATE ASSEMBLY
6 1 DH0162 FEED CYLINDER ASSEMBLY
7 1 DH0166 BAR GUARD WELDMENT
8 1 DH0144 BAR OIL PUMP ASSEMBLY
9 1 VMH002 SAW MOTOR, CONCENTRIC/HALDEX
10 1DH0169 FEED & MOTOR CONTROL MANIFOLD
11 1DH0152 BAR OIL TANK ASSEMBLY

12
DH0621 BAR PLATE ASSEMBLY

13
DH0162 FEED CYLINDER ASSEMBLY

14
DH0144 BAR OIL PUMP ASSEMBLY

15
DH0169 FEED and MOTOR CONTROL MANIFOLD

16
DH0152 BAR OIL TANK ASSEMBLY

17
HOSE LAYOUT
ITEM No.
QTY. PART No. DESCRIPTION REMARKS
1 1 DH0182 SAW MOTOR HOSE #8 - 3000 PSIHOSE
2 1 DH0185 MANIFOLD TOBAROIL PUMP HOSE, 24.5" OAL #4 - 3000 PSIHOSE
3 1 DH0180 OIL TANK TO BAROIL PUMP HOSE,12" OAL 4LOLB
4 1 DH0181 BAROIL PUMP TO BARPLATE HOSE, 24.5" OAL #4 -3000 PSIHOSE
5 1 DH0183 CUT HOSE, 20.5" OAL #4 - 3000 PSIHOSE
6 1 DH0184 RETRACTHOSE,20.5" OAL #4 - 3000 PSIHOSE
Table of contents
Other 6K Products Industrial Equipment manuals
Popular Industrial Equipment manuals by other brands

Bühler technologies
Bühler technologies GAS 222.20 DH Brief instructions
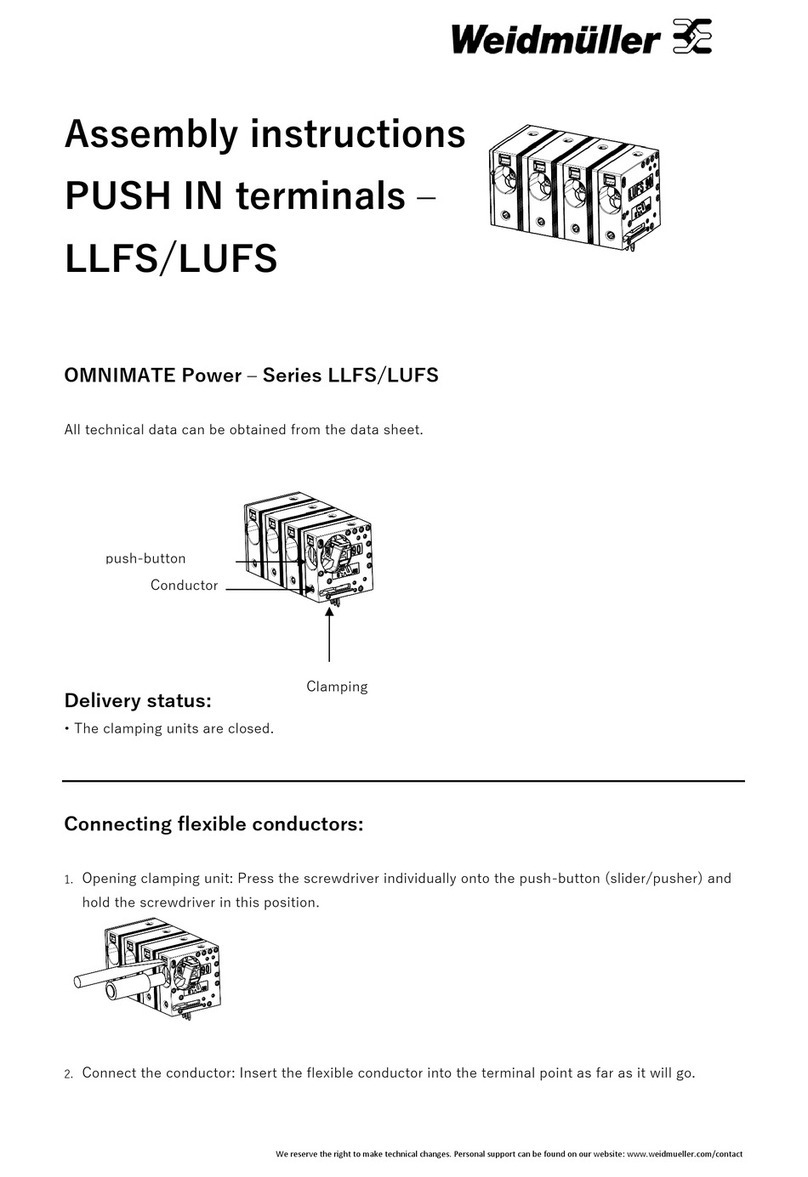
Weidmüller
Weidmüller LLFS Series Assembly instructions
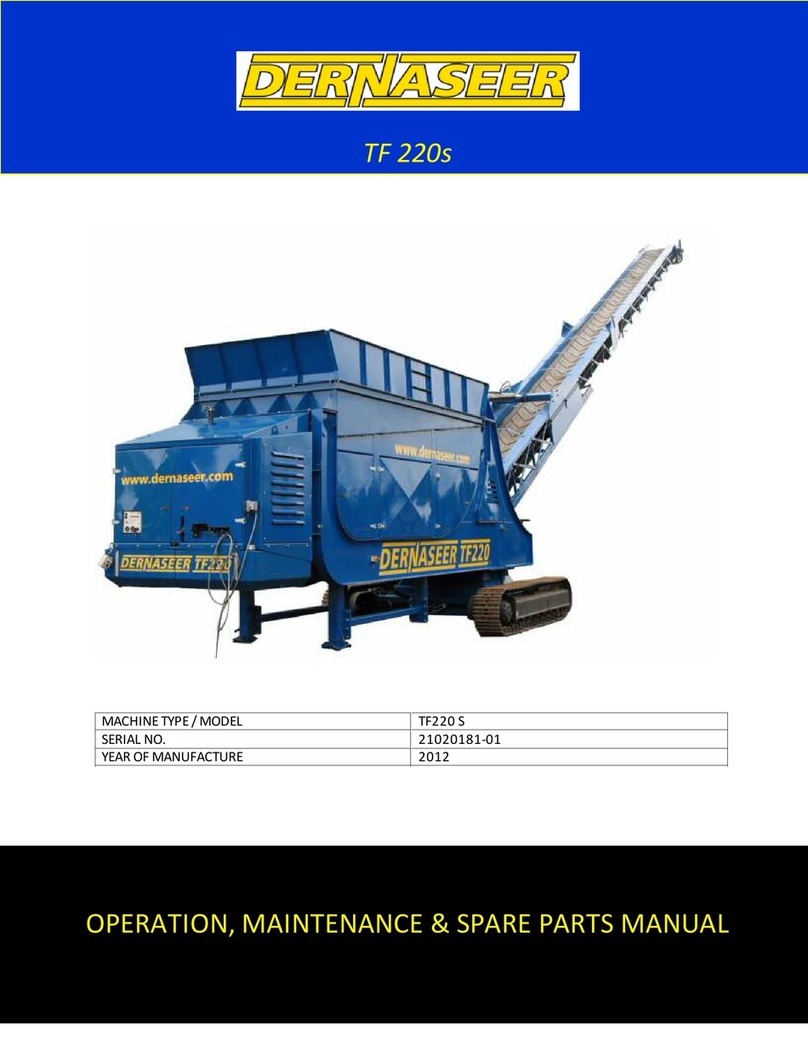
DERNASEER
DERNASEER TF 220s manual

Ferroli
Ferroli BLUEHELIX B 35 Instructions for use, installation and maintenance
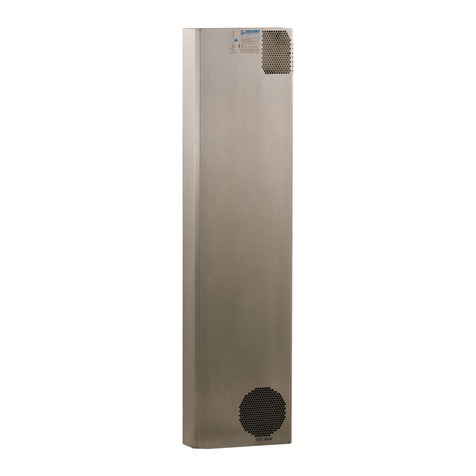
Seifert
Seifert 4274002 manual
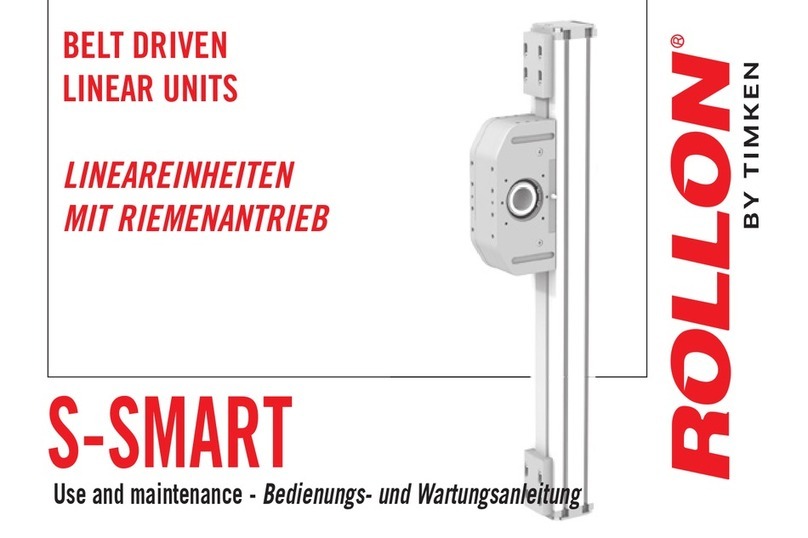
Timken
Timken ROLLON S-SMART Use and maintenance
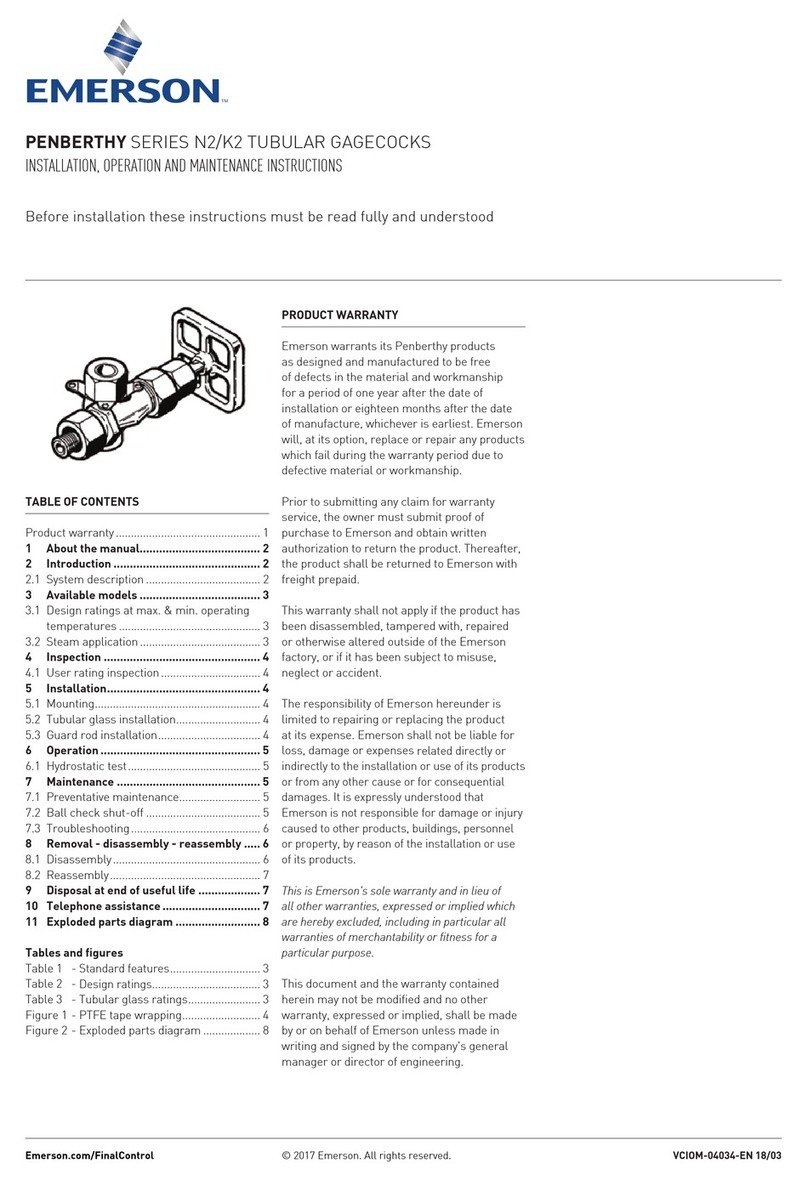
Emerson
Emerson Penberthy N2 Series Installation, operation and maintenance instructions

CEMO
CEMO DT-MOBIL 2.000 Installation and operating instructions

TMG
TMG TMG-PC90 product manual

GENERAL RADIO COMPANY
GENERAL RADIO COMPANY 874-GAL operating instructions

Dodge
Dodge SLEEVOIL RXT instruction manual
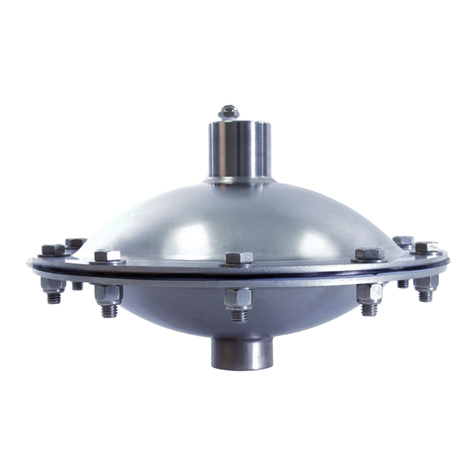
Blacoh
Blacoh AODDampener Installation and operation manual