AB Quality SLC 500 User manual

Publication 1746-IN008C-EN-P - May 2004
Installation Instructions
SLC™ 500 4-Channel Analog I/O Modules
(Catalog Numbers 1746-NI4, -NIO4I, -NIO4V, -NO4I, -NO4V, -FIO4I, and
-FIO4V)
Inside… ........................................................................................... page
Important User Information...................................................................... 2
For More Information ............................................................................. 3
Types of Analog Modules....................................................................... 4
Hazardous Location Considerations....................................................... 7
Environnements dangereux.................................................................... 7
Choosing a Slot in the Chassis............................................................. 10
Installing Your Module ......................................................................... 11
Wiring Considerations.......................................................................... 12
Wiring the Analog Module................................................................... 14
Labeling and Installing the Terminal Block .......................................... 16
Minimizing Electrical Noise on Analog Modules................................. 17
Specifications....................................................................................... 21
@JO$&/QQE@JO$&/QQE ".".

2SLC™ 500 4-Channel Analog I/O Modules
Publication 1746-IN008C-EN-P - May 2004
Important User Information
Solid state equipment has operational characteristics differing from those of electromechanical equipment.
Safety Guidelines for the Application, Installation and Maintenance of Solid State Controls (Publication
SGI-1.1 available from your local Rockwell Automation sales office or online at
http://www.ab.com/manuals/gi) describes some important differences between solid state equipment and
hard-wired electromechanical devices. Because of this difference, and also because of the wide variety of
uses for solid state equipment, all persons responsible for applying this equipment must satisfy themselves
that each intended application of this equipment is acceptable.
In no event will Rockwell Automation, Inc. be responsible or liable for indirect or consequential damages
resulting from the use or application of this equipment.
The examples and diagrams in this manual are included solely for illustrative purposes. Because of the many
variables and requirements associated with any particular installation, Rockwell Automation, Inc. cannot
assume responsibility or liability for actual use based on the examples and diagrams.
No patent liability is assumed by Rockwell Automation, Inc. with respect to use of information, circuits,
equipment, or software described in this manual.
Reproduction of the contents of this manual, in whole or in part, without written permission of Rockwell
Automation, Inc. is prohibited.
Throughout this manual we use notes to make you aware of safety considerations.
WARNING Identifies information about practices or circumstances that can cause an explosion in a
hazardous environment, which may lead to personal injury or death, property damage,
or economic loss.
IMPORTANT Identifies information that is critical for successful application and understanding of the
product.
ATTENTION Identifies information about practices or circumstances that can lead to personal injury
or death, property damage, or economic loss. Attentions help you:
•identify a hazard
•avoid a hazard
•recognize the consequence
@JO$&/QQE@JO$&/QQE ".".

SLC™ 500 4-Channel Analog I/O Modules 3
Publication 1746-IN008C-EN-P - May 2004
For More Information
Related Publications
If you would like a manual, you can:
•download an electronic version from the internet:
www.theautomationbookstore.com
•order a printed manual by:
–contacting your local distributor or Rockwell Automation representative
–visiting www.theautomationbookstore.com
and placing your order
–calling 1.800.963.9548 (USA/Canada) or 001.330.725.1574 (Outside
USA/Canada)
For Refer to this Document Pub. No.
A more detailed description on how to configure the
SLC 500 Analog I/O Modules.
SLC 500 Analog I/O Modules User
Manual
1746-UM005
A more detailed description on how to install and
integrate SLC 500 Fast Analog I/O Modules.
SLC 500 Fast Analog I/O Modules
User Manual
1746-6.9
A more detailed description on how to install and use
your modular SLC 500 system.
SLC 500 Modular Hardware Style
User Manual
1747-UM011
A reference manual that contains status file data,
instruction set, and troubleshooting information.
SLC 500 Instruction Set Reference
Manual
1747-RM001
@JO$&/QQE@JO$&/QQE ".".

4SLC™ 500 4-Channel Analog I/O Modules
Publication 1746-IN008C-EN-P - May 2004
Types of Analog Modules
1746-NI4 Analog Input Module
The NI4 Analog Input module contains 4 analog input channels that are user
selectable per channel for voltage or current to support a variety of monitoring and
controlling applications.
1746-NO4I and NO4V Analog Output Modules
The NO4I and NO4V Analog Output Modules provide 4 analog output channels.
The NO4I module contains 4 current outputs. The NO4V module contains 4 voltage
outputs. Both of these modules support a variety of control applications.
1746-NIO4I and NIO4V Analog Combination Modules
The NIO4I and NIO4V Analog Combination I/O modules provide 2 input and 2
output channels in a single-slot module. The 1746-NIO4I module contains 2 current
or voltage inputs (user selectable per channel) and 2 current outputs. The
1746-NIO4V module contains 2 current or voltage inputs (user selectable per
channel) and 2 voltage outputs.
1746-FIO4I and FIO4V Fast Analog Combination Modules
The FIO4I and FIO4V Fast Analog Combination modules are 2-input/2-output
combination modules ideal for high speed applications with more rapidly changing
analog signals. These fast response modules are best suited for control of pressure
and position in equipment such as hydraulic presses and molding machines.
@JO$&/QQE@JO$&/QQE ".".

SLC™ 500 4-Channel Analog I/O Modules 5
Publication 1746-IN008C-EN-P - May 2004
Analog Modules Operation
The module converts analog input signals to 16-bit binary values for storage in the
SLC processor’s input image table. The decimal range, number of significant bits,
and converter resolution depend on the input range that you use for the channel.
Analog Input A/D Characteristics
Analog Output D/A Characteristics
The analog modules have the same output characteristics.
NI4, NIO4I, & NIO4V Input
Range
Decimal Range (input
image table)
Number of
Significant Bits
Nominal Resolution
±10V dc -1 LSB -32,768 to +32,767 16 305.176 µV/LSB
0 to 10V dc -1 LSB 0 to 32,767 15
0 to 5V dc 0 to 16,384 14
1 to 5V dc 3,277 to 16,384 13.67
±20 mA ±16,384 15 1.22070 µA/LSB
0 to 20 mA 0 to 16,384 14
4 to 20 mA 3,277 to 16,384 13.67
FIO4I and FIO4V Input
Range
Decimal Range (input
image table)
Number of
Significant Bits
Nominal Resolution
0 to 10V dc -1 LSB 0 to 4095 12 2.4414 mV/LSB
0 to 5V dc 0 to 2047 11
1 to 5V dc 409 to 2047 10.67
0 to 20 mA 0 to 2047 11 9.7656 µA/LSB
4 to 20 mA 409 to 2047 10.67
Module Output Range Decimal Range (output
image table)
Significant Bits Resolution
FIO4I
NIO4I
NO4I
0 to 21 mA - 1 LSB 0 to 32,764 13 bits 2.56348 µA/LSB
0 to 20 mA 0 to 31,208 12.92 bits
4 to 20 mA 6,242 to 31,2089 12.6 bits
FIO4V
NIO4V
NO4V
±10V dc - 1 LSB -32,768 to +32,764 14 bits 1.22070 mV/LSB
0 to 10V dc -1 LSB 0 to 32,764 13 bits
0 to 5V dc 0 to 16,384 12 bits
1 to 5V dc 3,277 to 16,384 11.67 bits
@JO$&/QQE@JO$&/QQE ".".

6SLC™ 500 4-Channel Analog I/O Modules
Publication 1746-IN008C-EN-P - May 2004
Analog Module Hardware Features
The module contains a removable terminal block providing connection for the
analog input and/or output channels, which is specifically designed to interface
with analog current and voltage input signals. The channels can be wired as either
single-ended or differential inputs. There are DIP switches on the circuit board for
selecting voltage or current input.
Hardware Feature Function
Function Label Indicates input, output, or both.
Power Status LED Indicates when backplane power is applied to the module.
Removable Terminal Block Provides physical connection to input devices.
Door Label Permits easy terminal identification.
Door Protects terminal connections and label.
(5) ANL COM
(6) NOT USED
(7) OUT 0
(8) ANL COM
(9) NOT USED
(10) OUT 1
(11)ANL COM
ANALOG
POWER
OUTPUT INPUT
(4) IN 1±
(3) IN 1+
(2) ANL COM
(1) IN 0±
(1) IN 0+
Power Status LED
Door Label
Door
Removable Terminal Block
Function Label
@JO$&/QQE@JO$&/QQE ".".

SLC™ 500 4-Channel Analog I/O Modules 7
Publication 1746-IN008C-EN-P - May 2004
Hazardous Location Considerations
This equipment is suitable for use in Class I, Division 2, Groups A, B, C, D or
non-hazardous locations only. The following WARNING statement applies to use in
hazardous locations.
Environnements dangereux
Cet équipement est conçu pour être utilisé dans des environnements de Classe 1,
Division 2, Groupes A, B, C, D ou non dangereux. La mise en garde suivante
s’applique à une utilisation dans des environnements dangereux.
WARNING EXPLOSION HAZARD
•Substitution of components may impair suitability for Class
I, Division 2.
•Do not replace components or disconnect equipment
unless power has been switched off.
•Do not connect or disconnect components unless power
has been switched off.
•All wiring must comply with N.E.C. article 501-4(b).
AVERTISSEMENT DANGER D’EXPLOSION
•La substitution de composants peut rendre cet
équipement impropre à une utilisation en
environnement de Classe 1, Division 2.
•Ne pas remplacer de composants ou déconnecter
l'équipement sans s'être assuré que l'alimentation est
coupée.
•Ne pas connecter ou déconnecter des composants sans
s'être assuré que l'alimentation est coupée.
@JO$&/QQE@JO$&/QQE ".".

8SLC™ 500 4-Channel Analog I/O Modules
Publication 1746-IN008C-EN-P - May 2004
Determining Your Power Requirements for a Modular Controller
Analog modules require both 5V dc and 24V dc power from the backplane of the
SLC 500 system. However, the NO4I and NO4V analog modules can use an external
24V dc power supply. This eliminates the 24V dc backplane power requirements,
providing configuration flexibility if SLC power supply loading is critical. These two
modules provide user-supplied external 24V dc power supply connections.
The following table shows the power requirements for each analog module using
backplane power. Use this table to calculate the total load on the modular system
power supply. For more information refer to the SLC 500 Modular Hardware Style
User Manual, publication 1747-UM011.
Determining Your Power Requirements for a Fixed Controller
IMPORTANT The analog modules do not supply loop power for the input
device. You must supply the appropriate loop power for
loop-powered input devices.
Catalog Number 5 Volt Current 24 Volt Current
1746-NI4 35 mA 85 mA
1746-NIO4I 55 mA 145 mA
1746-NIO4V 55 mA 115 mA
1746-NO4I 55 mA 195 mA(1) (2)
(1) The 24V dc user power connection on a fixed SLC 500 can power an NO4I or NO4V analog module. However, the regulation
of the 24V dc user connection on a modular SLC 500 power supply, catalog number 1746-P1, -P2, and -P4 is outside of the
requirements of the NO4I and NO4V analog modules and cannot be used.
(2) Omit these values from your SLC power supply loading calculations if you decide to use an external power supply.
1746-NO4V 55 mA 145 mA(1) (2)
1746-FIO4I 55 mA 150 mA
1746-FIO4V 55 mA 120 mA
IMPORTANT The 2-slot, SLC 500 fixed I/O expansion chassis (1746-A2) will
support only specific combinations of modules. If you wish to
use an I/O module in a 2-slot expansion chassis with another
SLC I/O or communication module, refer to the SLC 500
Analog I/O Modules User Manual, publication 1746-UM005 for
valid combinations of modules.
@JO$&/QQE@JO$&/QQE ".".

SLC™ 500 4-Channel Analog I/O Modules 9
Publication 1746-IN008C-EN-P - May 2004
Configuring Your Module
The NI4, NIO4I, NIO4V, FIO4I, and FIO4V analog modules have user-selectable
DIP switch settings, which allow you to configure the input channels as either
current or voltage inputs. The switches are located on the analog module board.
The following illustration shows the ON and OFF switch settings. Switch orientation
is also provided on the nameplate of the module.
Switch Settings for the 1746-NI4
The NI4 has 4 individual DIP switches that control the input mode of channels 0
through 3. A switch in the ON position configures the channel for current input. A
switch in the OFF position configures the channel for voltage input.
ATTENTION Care should be taken to avoid connecting a voltage source
without a current transmitter, etc. to a channel configured for
current input. Improper module operation or damage to the
module can occur.
ON - Configures channel for current input
OFF - Configures channel for voltage input
Switch 1 = Channel 0
Switch 2 = Channel 1
Switch 3 = Channel 2
Switch 4 = Channel 3
1234
N
O
Current
Voltage
@JO$&/QQE@JO$&/QQE ".".

10 SLC™ 500 4-Channel Analog I/O Modules
Publication 1746-IN008C-EN-P - May 2004
Switch Settings for the 1746-NIO4I, -NIO4V, -FIO4I, and -FIO4V
The NIO4I and NIO4V have 2 individual switches labeled 1 and 2. These switches
control the input mode of channel 0 and 1. A switch in the ON position configures
the channel for current input. A switch in the OFF position configures the channel
for voltage input.
External Power Switch for the 1746-NO4I and -NO4V
The NO4I and NO4V analog output modules have an external 24V dc power
switch, SW1, which gives you the option of using an external power supply. In the
UP position, power is drawn from an external power source. In the DOWN
position, power is drawn from the backplane of the module. The switch is located
on the analog module board. Switch orientation is also provided on the nameplate
of the module.
Choosing a Slot in the Chassis
Two factors determine where the analog module should be located in the chassis:
ambient temperature and electrical noise. Consider the following conditions when
selecting a slot for an analog module. Position the module:
•in a slot away from an ac or high voltage dc modules
•in the chassis closest to the bottom of the enclosure where the SLC 500
system is installed
•away from the chassis power supply if installed in a modular system
Switch 1 = Channel 0
Switch 2 = Channel 1
12
N
O
Current
Voltage
External
Backplane
24V dc
Power
Selector
SW1
@JO$&/QQE@JO$&/QQE ".".

SLC™ 500 4-Channel Analog I/O Modules 11
Publication 1746-IN008C-EN-P - May 2004
Installing Your Module
All modules are mounted in a single slot. Remember that in a modular system the
processor always occupies the first slot of the first chassis.
1. Verify that all switches are set correctly for the application.
2. Align the circuit board of the analog module with the card guide of the
chassis as shown on page 12.
3. Slide the module in until both top and bottom retaining clips are secured.
4. To remove the module, depress the retaining clips at the top and bottom of
the module and slide the module out.
ATTENTION Never install, remove, or wire modules with power applied to
the chassis. Also, do not expose analog modules to surfaces or
other areas that may typically hold an electrostatic charge.
Electrostatic charges can destroy the analog circuitry.
IMPORTANT The potentiometer sets the voltage during factory calibration to
2.5 volts. It is set and sealed at the factory and does not
require any adjustments.
ATTENTION Care should be taken to avoid connecting a voltage source
without a current transmitter, etc. to a channel configured for
current input. Improper module operation or damage to the
module can occur.
@JO$&/QQE@JO$&/QQE ".".

12 SLC™ 500 4-Channel Analog I/O Modules
Publication 1746-IN008C-EN-P - May 2004
Wiring Considerations
The following section provides system wiring guidelines, how to ground your
Belden™ cable, and how to determine the cable length.
ATTENTION Before wiring any analog module, disconnect power from the
SLC 500 system and from any other source to the analog
module.
Top and Bottom Module
Release (s)
Card Guide
@JO$&/QQE@JO$&/QQE ".".

SLC™ 500 4-Channel Analog I/O Modules 13
Publication 1746-IN008C-EN-P - May 2004
System Wiring Guidelines
Use the following guidelines in planning the system wiring for the analog modules:
•all analog common terminals (ANL COM) are electrically connected inside
the module. ANL COM is not connected to earth ground inside the module.
•voltages on IN+ and IN- terminals must remain within ± 20 Volts with
respect to ANL COM to ensure proper input channel operation. This is true
for current and voltage input channel operation.
•voltage outputs (OUT 0 and OUT 1) of the NIO4V and NO4V are referenced
to ANL COM. Load resistance (R1) for a voltage output channel must be
greater than or equal to 1K ohms.
•current output channels (OUT 0 and OUT 1) of the NIO4I and NO4I source
current that returns to ANL COM. Load resistance (R1) for a current output
channel must remain between 0 and 500 ohms.
After the analog input module is properly installed in the chassis, follow the wiring
procedure below using Belden 8761 cable.
Grounding Your Cable
Belden cable #8761 has two signal wires (black and clear), one drain wire and a foil
shield. Refer to illustration on page 14 for Belden cable #8761. The drain wire and
foil shield must be grounded at one end of the cable. Do not earth ground the drain
wire and foil shield at both ends of the cable.
Input Channel - Use a chassis mounting tab as a ground for the drain wire and foil
shield.
Output Channel - Ground the drain wire and foil shield at the analog load.
ATTENTION Care should be taken to avoid connecting a voltage source
without a current transmitter, etc. to a channel configured for
current input. Improper module operation or damage to the
module can occur.
IMPORTANT If you cannot ground the output channel at the load, ground
the drain wire and foil shield at the chassis mounting tab. Do
not connect the foil shield or drain wire to the analog terminal
block. They must be connected to an earth ground, which is
not provided at the analog module.
@JO$&/QQE@JO$&/QQE ".".

14 SLC™ 500 4-Channel Analog I/O Modules
Publication 1746-IN008C-EN-P - May 2004
Determining the Cable Length
Determine the length of cable you will need to connect a channel to its input or
output device. Remember to leave additional length to route the drain wire and foil
shield for earth grounding.
Wiring the Analog Module
After the analog module is properly installed in the chassis, use the following
wiring procedure. Belden cable #8761 is recommended when wiring analog
modules. This section assumes that you have properly installed the analog module.
To wire your analog module, follow these steps and refer to the illustrations on
page 15.
1. Designate the end of the cable where the drain wire and foil shield is earth
grounded as END 1. Designate the other end as END 2.
2. At each end of the cable, strip some casing to expose the individual wires.
3. Trim the signal wires to 50 mm (2 inch) lengths. Strip 5 mm (about 3/16
inch) of insulation away to expose the end of the wire.
ATTENTION Before wiring any analog module, disconnect power from the
SLC 500 system and from any other source to the analog
module.
Belden Cable #8761 Foil Shield
Black Wire
Drain Wire
Clear Wire
@JO$&/QQE@JO$&/QQE ".".

SLC™ 500 4-Channel Analog I/O Modules 15
Publication 1746-IN008C-EN-P - May 2004
4. At END 1, twist the drain wire and foil shield together, bend them away from
the cable, and apply shrink wrap.
5. At END 2, cut the drain wire and foil shield back to the cable and apply
shrink wrap.
6. Connect the signal wires (black and clear) to the terminal block and the
input and output devices. The recommended maximum torque is 0.57 Nm (5
lb-in) for all terminals.
•Input channels - connect END 1 at module. Use a chassis mounting tab
as a ground for the drain wire and foil shield.
•Output channel- connect END 2 at the module. Ground the drain wire
and foil shield at the analog load.
7. Repeat steps 1 through 6 for each channel on the analog module. Jumper
the unused plus (+), minus (-) and common terminals of each input channel
individually. Unused output and common terminals should be left
unconnected.
The following illustrations depict the proper cable preparation for END 1 and END
2. Shrink wrap is applied to each cable end. Make sure the foil shield and drain
wires on END 1 are long enough to reach their designated earth ground points.
Cable Preparation END 1 Foil Shield and
Drain Wire
Black Wire
Black Wire
Clear Wire
Clear Wire
Insulation
Insulation
Cable Preparation END 2
@JO$&/QQE@JO$&/QQE ".".

16 SLC™ 500 4-Channel Analog I/O Modules
Publication 1746-IN008C-EN-P - May 2004
Labeling and Installing the Terminal Block
The terminal block has a write-on label. Labeling the terminal block will help
ensure that it is installed on the correct module.
When installing the analog module in a chassis, it is not necessary to remove the
terminal block from the module. However, if the terminal block is removed, use the
write–on label located on the side of the terminal block to identify the module
location and type.
Once you have wired your analog module and properly labeled the terminal block,
install the terminal block on the analog module. To install the terminal block:
1. Align the terminal block with the receptacle.
2. Insert the terminal block and press firmly at the top and bottom until it is
properly secured.
To remove the terminal block, grasp it on the top and bottom and pull outward and
down.
TIP The black dot on the terminal block label indicates the
position of terminal 0.
SLOT ____ RACK ____
MODULE _____
Terminal Block
@JO$&/QQE@JO$&/QQE ".".

SLC™ 500 4-Channel Analog I/O Modules 17
Publication 1746-IN008C-EN-P - May 2004
Minimizing Electrical Noise on Analog Modules
Inputs on analog modules employ digital high frequency filters that significantly
reduce the effects of electrical noise on input signals. However, because of the
variety of applications and environments where analog modules are installed and
operating, it is impossible to ensure that all environmental noise will be removed
by the input filters.
Although it is not the purpose of this installation instruction to address SLC 500
system procedures, several specific steps can be taken to help reduce the effects of
environmental noise on analog signals:
•Install the SLC 500 system in a properly rated (i.e., NEMA) enclosure. Make
sure that the SLC 500 system is properly grounded.
•Use Belden cable #8761 for wiring the analog modules making sure that the
drain wire and foil shield are properly earth grounded.
•Route the Belden cable separate from any other wiring. Additional noise
immunity can be obtained by routing the cables in grounded conduit.
•Group analog and low voltage dc modules away from ac I/O or high voltage
dc modules.
A system may malfunction due to a change in the operating environment after a
period of time. Periodically check system operation, particularly when new
machinery or other noise sources are installed near the SLC 500 system. For further
details on system installation and start-up refer to:
•SLC 500 Modular Hardware Style User Manual, publication 1747-UM011
•SLC 500 Fixed Hardware Style User Manual, publication 1747-6.21
•Safety Guidelines for the Application, Installation Maintenance of Solid State
Control, publication SGI-1.1.
@JO$&/QQE@JO$&/QQE ".".

18 SLC™ 500 4-Channel Analog I/O Modules
Publication 1746-IN008C-EN-P - May 2004
Wiring Diagram (showing differential inputs)
0
1
2
9
10
11
+
-
+
-
3
4
5
6
7
8
0
1
2
9
10
11
3
4
5
6
7
8
0
1
2
3
4
5
6
7
0
1
+
-
NI4
analog
source
analog
source
analog
source
earth
ground
earth
ground Jumper
unused
inputs.
earth
ground Jumper
unused
inputs.
LOAD
earth
ground
NIO4I, NIO4V, FIO4I, and
FIO4V
Do not jumper
unused
NO4I and NO4V
24V dc power supply if external power
is selected. Cable length from external
24V dc power supply to analog module Ext. pwr
sup.
LOAD
LOAD
earth
ground
earth
ground
Do not jumper
unused outputs.
Analog commons are internally
connected in the module. Channels
are not isolated from each other.
IN 0+
IN 0-
ANL COM
IN 1+
IN 1-
ANL COM
IN 2+
IN 2-
ANL COM
IN 3+
IN 3-
ANL COM
IN 0+
IN 0-
ANL COM
IN 1+
IN 1-
ANL COM
not used
OUT 0
ANL COM
not used
OUT 1
ANL COM
+24V dc
dc COM
OUT 0
ANL COM
OUT 1
ANL COM
OUT 2
ANL COM
OUT 3
ANL COM
@JO$&/QQE@JO$&/QQE ".".

SLC™ 500 4-Channel Analog I/O Modules 19
Publication 1746-IN008C-EN-P - May 2004
Wiring Schematics for 2, 3, and 4-Wire Analog Input Devices
ATTENTION Any individual single-ended input device can be connected to any
single differential input shown on page 18. The single-ended
input common is connected to the negative differential input
point.
IMPORTANT The module does not provide loop power for analog inputs.
Use a power supply that matches the transmitter specifications.
+-
+
-
+
-
+
-
+
-
+
-
2-Wire Transmitter
Transmitter
Transmitter
Transmitter
Module
IN +
IN -
ANL COM
Power
Supply
Power
Supply
Power
Supply
Supply Signal
GND
Supply Signal
Module
IN +
IN -
ANL COM
Module
IN +
IN -
ANL COM
3-Wire Transmitter
4-Wire Transmitter
@JO$&/QQE@JO$&/QQE ".".

20 SLC™ 500 4-Channel Analog I/O Modules
Publication 1746-IN008C-EN-P - May 2004
Wiring Schematic for Single-Ended Analog Input Connections
When wiring single-ended analog input devices to the analog input card, the
number of total wires necessary can be limited by using the ANALOG COMMON
terminal. Note that differential inputs are more immune to noise than single-ended
inputs.
+
+
+
-
+
+
Power
Supply
Transmitter
Transmitter
Transmitter
Transmitter
Signal
Signal
Signal
Signal
Supply
Ground
IN 0+
IN 0-
IN1+
IN 1-
IN 2-
IN 2+
IN 3-
IN 3+
ANL COM
ANL COM
ANL COM
ANL COM
NI4
@JO$&/QQE@JO$&/QQE ".".
Table of contents
Other AB Quality Control Unit manuals
Popular Control Unit manuals by other brands

LSR
LSR TiWi-uB1 user guide
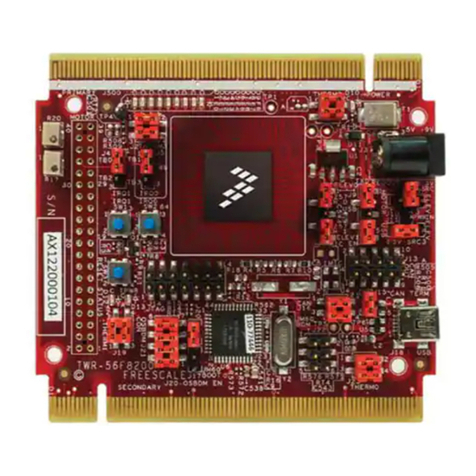
NXP Semiconductors
NXP Semiconductors freescale TWR-56F8200 quick start guide
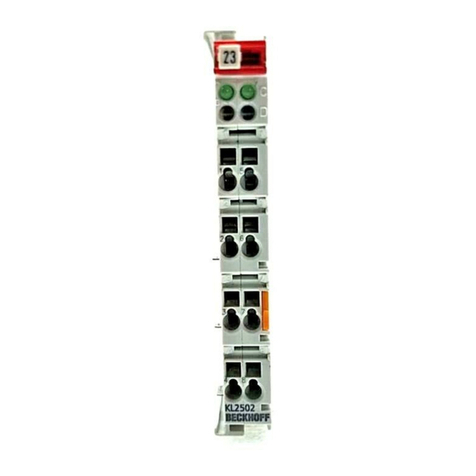
Beckhoff
Beckhoff KL2502 Documentation
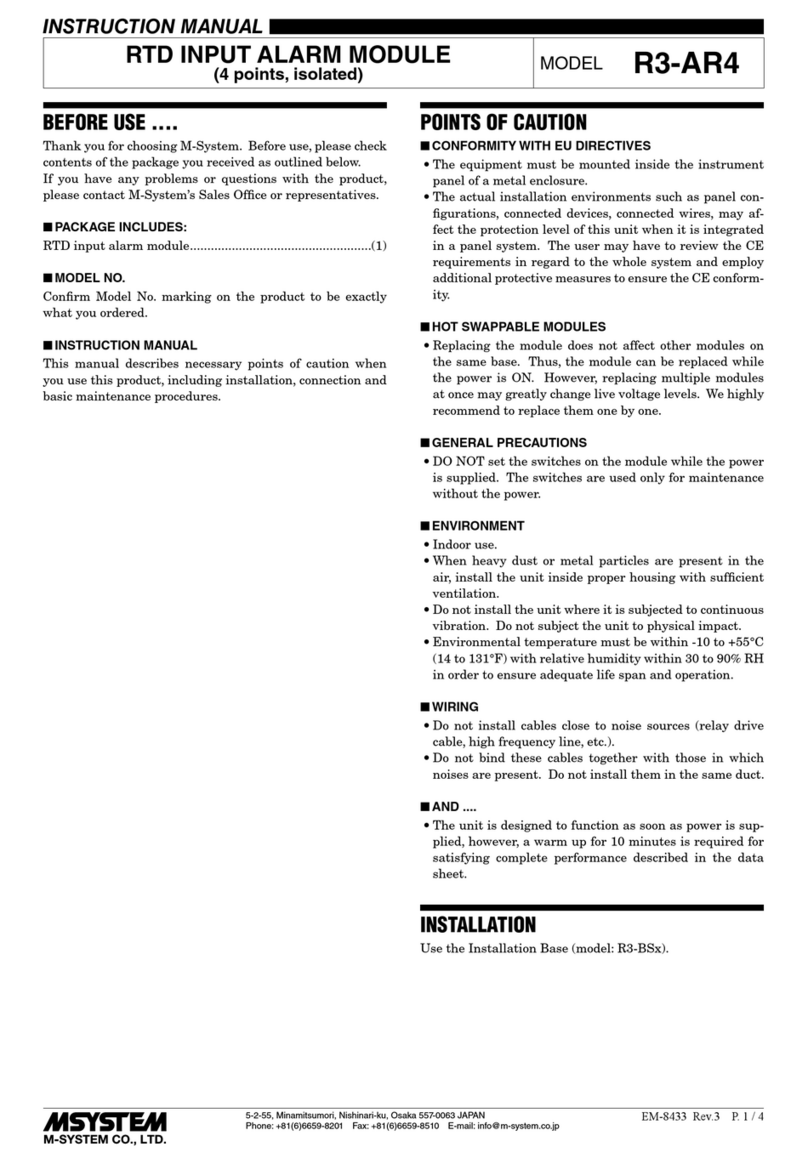
M-system
M-system R3-AR4 instruction manual
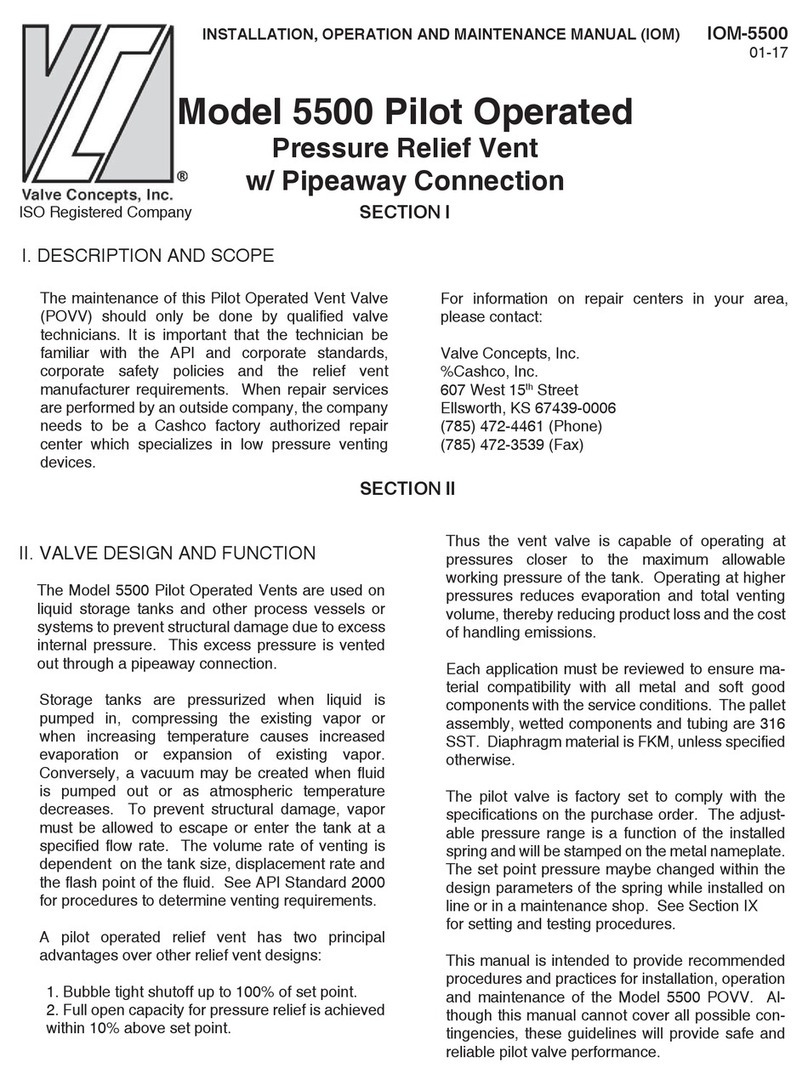
Valve Concepts
Valve Concepts 5500 Installation, operation and maintenance manual
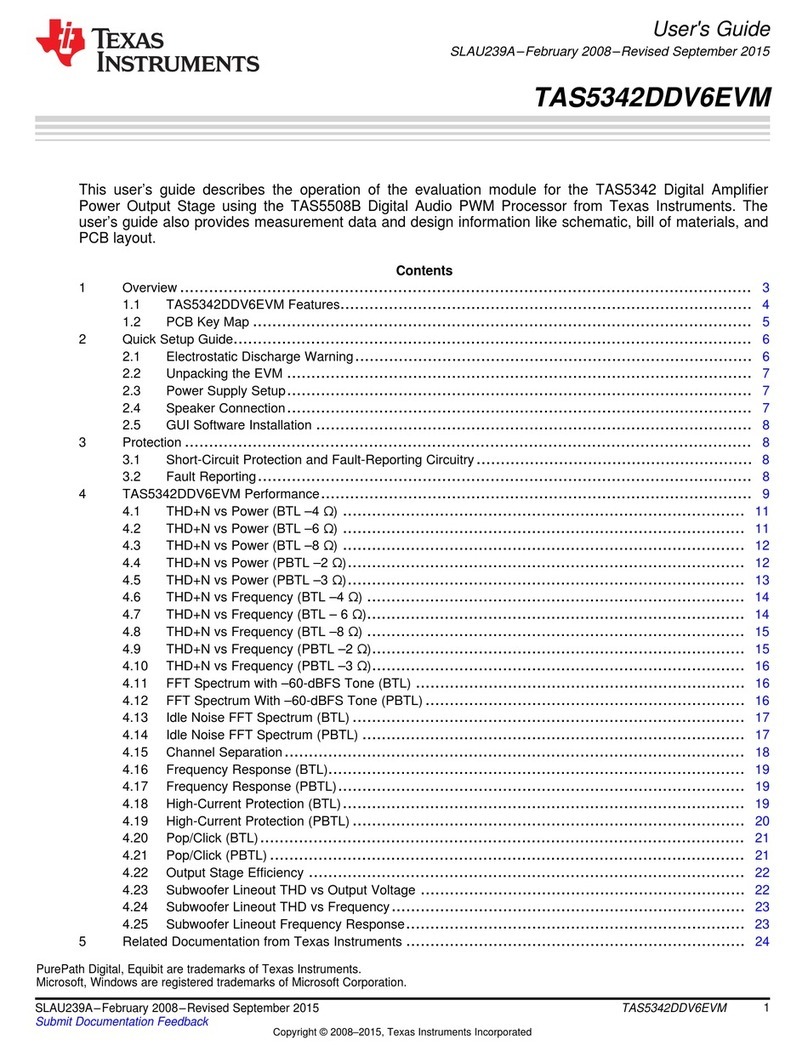
Texas Instruments
Texas Instruments PurePath Digital TAS5342DDV6EVM user guide
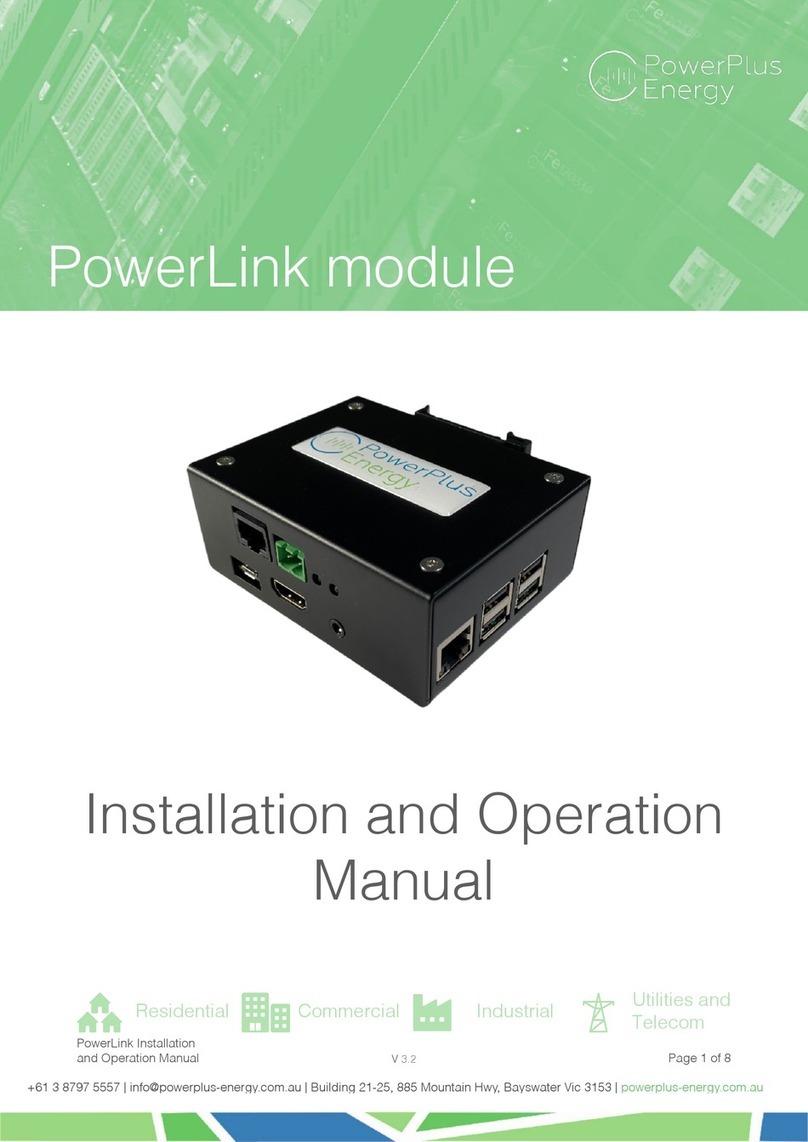
PowerPlus Energy
PowerPlus Energy PowerLink Installation and operation manual
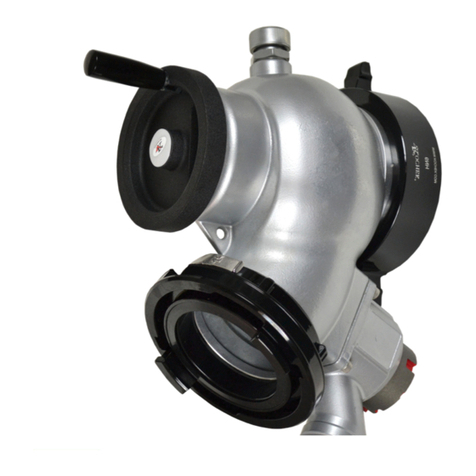
Kochek
Kochek 70K instruction manual
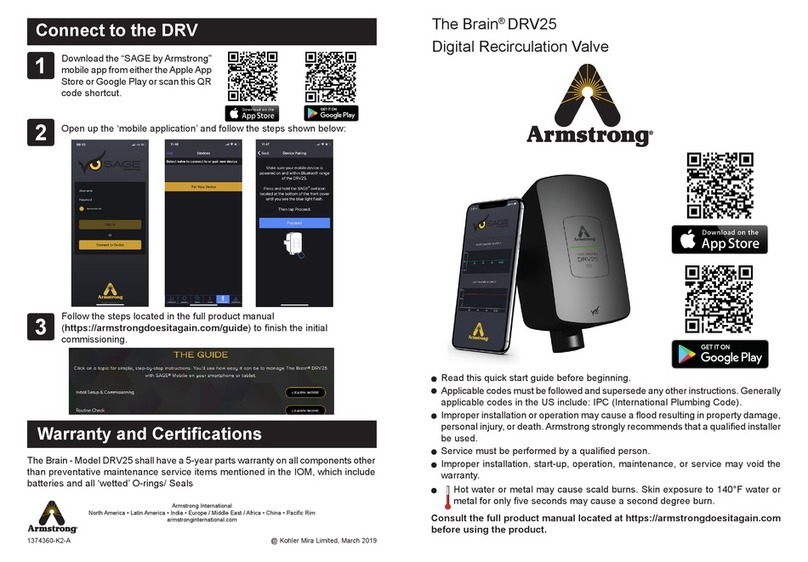
Armstrong
Armstrong The Brain DRV25 quick start guide
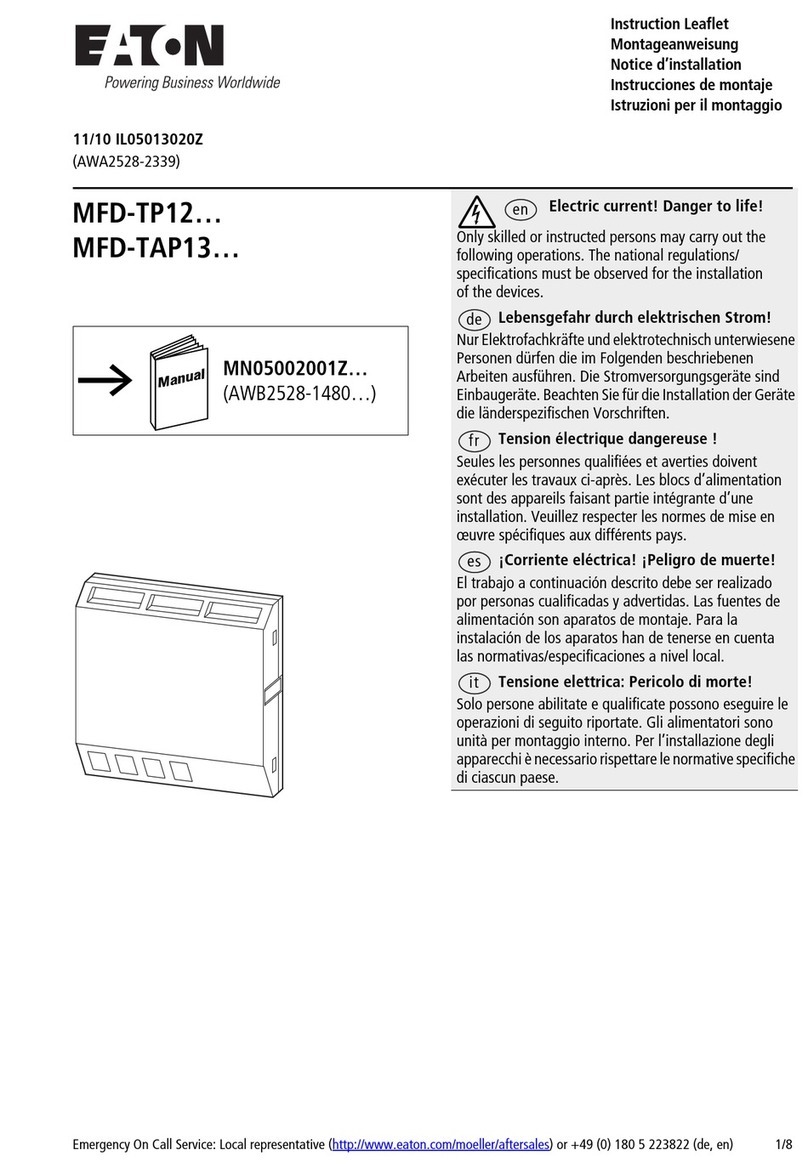
Eaton
Eaton MFD-TP12 Series Instruction leaflet
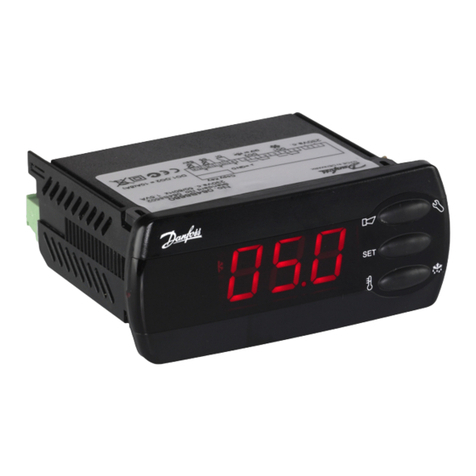
Danfoss
Danfoss EKC 102D instructions

LOVATO ELECTRIC
LOVATO ELECTRIC EXP10 15 instruction manual