ADMET eP2 User manual

51 Morgan Drive Norwood, MA 02062 1
Tel: (781) 769-0850 Fax: (781) 769-0884
eP2 Controller
Operators Manual

51 Morgan Drive Norwood, MA 02062 2
Tel: (781) 769-0850 Fax: (781) 769-0884
eP2 Controller
Operators Manual
LIMITED WARRANTY
ADMET, Inc. (The Company) warrants that hardware and software/firmware products manufactured by The Company,
when properly installed, used, and maintained, will be free from defects in material and workmanship. ADMET, Inc.
warrants a) the SOFTWARE/FIRMWARE will perform Substantially in accordance with the accompanying written
materials and b) the HARDWARE will be free from defects in materials and workmanship under normal use and service
for a period of (1) one year from date of receipt. The Company’s obligations under this warranty will be limited to
repairing or replacing , at The Company’s option, the part or parts of the hardware and software/firmware which
prove defective in material and workmanship within one (1) year from the date of delivery, provided the buyer gives
The Company prompt notice of any defect or failure and satisfactory proof thereof. Products may be returned to The
Company’s factory. The Company will deliver replacements for defective products to the Buyer, freight prepaid to the
destination provided for in the original order. With respect to any product or part thereof not manufactured by The
Company, only the warranty, if any given by the manufacturer thereof, will apply. It is the responsibility of the Buyer
to determine the suitability and safety of this product for any particular purpose. The Company disclaims all liability
for incidental or consequential damages. In no case will The Company’s liability exceed the original purchase price.
THE COMPANY MAKES NO OTHER OR FURTHER WARRANTY, EXPRESS OR IMPLIED, INCLUDING ANY WARRANTY OF
FITNESS FOR A PARTICULAR PURPOSE OR WARRANTY OF MERCHANTABILITY.
COPYRIGHT NOTICE
The contents of this manual copyright (c) 2018. All rights reserved. Nothing in this manual may be reproduced in any
manner, either wholly or in part for any purpose whatsoever without written permission from ADMET, Inc.

51 Morgan Drive Norwood, MA 02062 3
Tel: (781) 769-0850 Fax: (781) 769-0884
eP2 Controller
Operators Manual
eP2 Controller LICENSE AGREEMENT
This is a legal agreement between you, the end user, and ADMET, Inc. (The Company). By using the eP2 Controller you are agreeing
to be bound by the terms of this agreement.
1.0 License Grant. The Company hereby grants the end user a personal, nontransferable and non-exclusive license to use one copy
of the software/firmware and related documentation on a single indicating system.
2.0 Intellectual Property Rights. The Company is the sole owner of all right, title and interest to the eP2 CONTROLLER and all
copyrights, trademarks, and trade secrets therein. The Company is protected by United States copyright laws and international
treaty provisions. Therefore, the end user must treat the software/firmware like any other copyrighted material and may not copy
the written materials accompanying the eP2 CONTROLLER.
3.0 Restrictions. This Agreement and the Licensed Software/Firmware may not be assigned, Sublicensed or otherwise transferred
by the Customer. The end user must not reverse engineer, decompile, or disassemble the Licensed Software/Firmware or attempt
to do so. The Licensed Software/Firmware may not be modified without the written consent of The Company.
4.0 Termination. The Company may terminate the license contained in this Agreement by written notice upon any breach of any
term by the end user. Upon termination, the end user shall immediately return the eP2 CONTROLLER to the factory. Section 2.0 of
this Agreement shall survive termination of this Agreement.
5.0 Purchase by Governmental Agencies. If the end user is a federal, state or local governmental agency or unit, then as a matter of
contract, the end user will accord The Company and the Licensed Program the same rights The Company would have had under the
Copyright Act of 1976, as amended.
6.0 Governing Law. This Agreement shall be governed by and construed in accordance with the laws of the Commonwealth of
Massachusetts.

51 Morgan Drive Norwood, MA 02062 4
Tel: (781) 769-0850 Fax: (781) 769-0884
eP2 Controller
Operators Manual
Contents
FORWARD .............................................................................................. 4
1.0 INTRODUCTION ................................................................................ 5
1.1 Using the eP 2 Digital Controller to Run a Test ....................................................................... 6
2.1 THE LCD DISPLAY ....................................................................................................................7
2.0 eP 2 CONTROLLER Front Panel ......................................................... 7
3.0 THE KEYS .......................................................................................... 9
3.1 The <Home> Key .................................................................................................................... 9
3.2 The <STORE> Key ................................................................................................................. 9
3.3 The <ENTER/Start> Key ........................................................................................................ 9
3.4 The <ESC/STOP> Key .............................................................................................................. 9
3.5 The <Jog UP & Jog Dn> Keys ................................................................................................... 9
3.6 The ID# Key ............................................................................................................................ 9
3.7 E-STOP (RED BUTTON ON TOP OF UNIT)- ............................................................................ .. 9
4.0 THE MENUS and KEYS ..................................................................... 10
4.0.1 Test Method Specific Menu Selections ............................................................................... 10
4.0.2 Global Menu Selections ..................................................................................................... 11
4.1 The Test Method Menu ........................................................................................................ 12
4.2 The Data Acq Menu .............................................................................................................. 12
4.3 The Analysis Menu ............................................................................................................... 13
4.4 The PRINT Menu ................................................................................................................... 15
4.5 The UTILS Menu .................................................................................................................... 15
4.6 The Control Menu ................................................................................................................. 16
4.7 The Zero Menu ..................................................................................................................... 17
5.0 CALIBRATION .................................................................................. 18
5.1 Transducer Autorecognition .................................................................................................. 18
5.2 How to Calibrate Analog Transducers .................................................................................... 18
5.3 What Occurs During Calibration ........................................................................................... 19
5.4 Saving Calibration Data ......................................................................................................... 19
5.5 Setting Gage Length for an Adjustable Extensometer ............................................................ 19
6.0 TROUBLESHOOTING ........................................................................ 20
7.0 DIMENSIONS .................................................................................. 22
8.0 REAR PANEL CONNECTIONS ............................................................. 22
9.0 FACTORY PASSWORD ...................................................................... 24

51 Morgan Drive Norwood, MA 02062 5
Tel: (781) 769-0850 Fax: (781) 769-0884
eP2 Controller
Operators Manual
Forward
ADMET's eP 2 CONTROLLER has been designed and constructed with great care in every phase of assembly. In order to insure
reliability, both the mechanical and electrical components have been built with the best available materials. Nevertheless, it has
been proven that a thorough understanding of the machine, together with proper attention, will pay big dividends. The sections of
this manual provide description and instruction on the operation and maintenance of the mechanical, electrical and software
components.
You as a customer are our most valued asset. We take pride in our systems and are proud that you have become an owner. We
welcome your comments about our products and wish that you express them. It is the only way that we can continue to build the
best available test systems to satisfy your needs. Thank-you for your support.
HOW TO USE THIS MANUAL
This manual is intended to instruct you on the capabilities, operation and maintenance of the eP 2 CONTROLLER. In addition, it is
to be used as a supplement for any information supplied by the load frame manufacturer. Maintenance procedures specified by
the load frame manufacturer should be followed unless specifically noted herein. Read this manual and become familiar with the
operation of your test machine prior to operating the eP 2 CONTROLLER.
TECHNICAL SUPPORT
If a problem should occur with your testing machine:
1) Check that all external inputs are properly connected.
2) Call the supplier/manufacturer of your test machine.
3) Call ADMET's technical support at (781) 769-0850 x31 (9AM to 5PM EST).

51 Morgan Drive Norwood, MA 02062 6
Tel: (781) 769-0850 Fax: (781) 769-0884
eP2 Controller
Operators Manual
1.0. Introduction
The state-of-art electronics supplied in the eP2 Controller utilizes a 32-bit microprocessor that makes it possible for fast, accurate
data acquisition and automatic control to be applied to material and product test applications.
The eP 2 Digital Controller electronics includes inputs for force and position measurement plus limit switches for over travel
protection, digital outputs for machine interaction and a servo control analog output. A 24 bit (1 part in 16777216) A/D converter
provides unparalleled force resolution and accuracy while a high accuracy rotary encoder measures position changes in the microns.
The control output connects to an integral pulse width modulated (PWM) motor amplifier that controls machine movement. A PID
algorithm, including user definable tuning parameters (factory preset), ensures precise control from in both directions by using
continuous control feedback.
Control can be Single segment, Dual segment or Cyclic with the speeds programmed into memory ahead of time and recalled
whenever that test is to be run. Single segment control is a single speed test from beginning to end and can be either in the pull
(tensile) or push (compression) direction. On the testing machines equipped with the eP 2 Controller, as the force increases the
speed will not drop off, the PID control algorithm corrects automatically keeping the speed constant, even up to the capacity of
the testing machine. The test will stop upon either automatically based upon the Specimen Break or Test Time, or if the Stop key
is pushed. Over travel protection is provided by means of independent limit switches.
Dual Segment control provides a means of more complex control including a true hold force feature, and Cyclic control provides the
means to cycle between either two (2) load values or two (2) position values from to 1 –300,000 times.
Six Test Methods can be predefined and stored in internal nonvolatile memory for later recall and execution. Test Methods are
named M1 - M6. The control, analyses, engineering units, data acquisition, and alarm functions are all stored within the specific Test
Method. Changing options within one Test Method does not change another Test Method, but changes made within the Utils Menu
does affect all Test Methods.
The eP2 controller can store up to four multipoint load cell calibrations. The controller features automatic transducer recognition so
that the correct calibration table is automatically loaded for the currently connected transducer.
The eP2 control panel consists of a four (4) line by twenty (20) character LCD display, a twenty four (24) key keypad and an
Emergency Stop button.
The Emergency Stop will stop all movement of the testing machine and end the test, if currently active.
The Display consists of four (4) lines of twenty (20) characters that are used to display measurements and test status during testing
and calculated results after the test has concluded.
The Keypad consists of twenty four (24) keys which are used for initial test setup and data entry, Starting and Stopping the test,
Jogging the machine Up and Down, Zeroing measurements at test start, returning the machine to the Home position, initiating ABS
and selecting Test Methods.
The automatic calculation capabilities are extremely powerful and flexible. Included are calculations of Load at Displacement, Max
Load, Minimum Load, Average Load between Displacements, Load at Break, Displacements Load, Energy, Stiffness and Free Height.

51 Morgan Drive Norwood, MA 02062 7
Tel: (781) 769-0850 Fax: (781) 769-0884
eP2 Controller
Operators Manual
1.1 Using the eP2 Digital Controller to Run a Test
This is a general overview for using the eP2 controller to run tests and get test results. See the individual sections for more detailed
description.
1. Set up Test Method:
•Use the Data Acquisition menu (section 4.2) to specify data logging threshold, sample break, specimen type and engineering
units.
•Use the Analysis menu (section 4.3) to specify the analysis to be calculated and the appropriate parameters for the selected
analyses.
•Use the Control menu (section 4.6) to specify how you want the machine to move during test.
2. Run Test
•Move crosshead to appropriate position using Jog keys and then set Home position and/or zero load by using the Zero menu.
•Press START button to begin the test. The test will run until either sample break is tripped, the programmed control profile is
completed, OR test is stopped manually.
•You can automatically stream live XY data during test to a computer via USB (see Log Rate in Data Acq menu, section 4.2) and
automatically transmit test results to a computer via USB (see Analysis menu, section 4.3).
3. Storing Test Results and Data.
• Use the PRINT menu to specify information to transfer. You can transfer stored test results or test XY data via USB connection to
a computer running the GaugeSafe PLUS software.
NOTE: You can also transfer Calibration data and Test Methods via USB to a computer running the GaugeSafe
PLUS software.

51 Morgan Drive Norwood, MA 02062 8
Tel: (781) 769-0850 Fax: (781) 769-0884
eP2 Controller
Operators Manual
2.0. Controller Front Panel
2.1 THE LCD DISPLAY
Figure 2.0 depicts the front panel for the eP2 DIGITAL CONTROLLER. The LCD Display is a 4 line by 20 character display. Shown in
Figure 2.0 is the arrangement of information on the LCD Display while in the Live Indicating mode. The Live Indicating mode will
always be active while running a test. On the left side of the Live Indicating display there are two letter codes:
•Calibration Table
The active load calibration table is displayed in the upper left of the live screen.
The eP2 digital controller holds up to 4 calibration tables: C0 - C3
•Test Method
Select the Test Method to run for the test. There are six possible selections: M1 - M6
•STATUS.
The Status codes consist of two (2) characters and are listed in Table 2.0.
Figure 2.0 - The eP2 CONTROLLER Front Panel
Data
Acq
Utils
Jog Up
Test
Method
ID#
ESC
Stop
Analysis
1
Store
Jog Dn
Control
0
Zero
(-)
Home
Print
.
Freeze
ENT
Start
C0-M1
RS
Status(A,B)
Load value
4
2
3
8
7
6
5
9
Active Load Cell
Test Method
-
Position value
Rate Indication
9252
LBF
0.2511
in
0.15
/min

51 Morgan Drive Norwood, MA 02062 9
Tel: (781) 769-0850 Fax: (781) 769-0884
eP2 Controller
Operators Manual
Status Display
Test Status (A)
Servo Status (B)
D
Done
P
Touch
R
Ready
A
Segment A
T
Testing
B
Segment B
X
Buffer Full
W
Pause
C
Calculating
H
Moving Home
S
Stop
+
Jogging Up
-
Jogging Down
Table 2.0 –Status Table
First Character (A) is the Test Status, which reports on data collection and handling from transducer
measurements.
•(R) Ready: System is awaiting the start of data logging.
•(T) Testing: Active logging of data.
•(C) Calculating: Selected analyses are being calculated with the data.
Note that this takes little time for most tests and may never actually be seen by the operator.
•(D) Done: Data collection has stopped.
•(X) Buffer Full: Data logged during tests exceeds the memory storage limit.
Second Character (B) is the Servo Status.
•(P) Touch: Machine moving to set ABS Zero with Set ABS Zero function
•(S) Stopped: Machine is not moving.
•(A): Machine is in Segment A of control profile
•(B): Machine is in Segment B of control profile
•(W): Pause after Segment A or Segment B
•(H) Homing: Sends the machine to the zero position location as determined at the start of the test.
Note that homing can occur either automatically at the end of a test or it can be initiated manually
using the Home key.
•+: Machine is jogging up via pressing the <Jog Up> key.
•-: Machine is jogging down via pressing the <Jog Dn> key.

51 Morgan Drive Norwood, MA 02062 10
Tel: (781) 769-0850 Fax: (781) 769-0884
eP2 Controller
Operators Manual
3.0. The Keys
3.1 The <Home> Key
Sends the crosshead to specified home location
3.2 The <STORE> Key
The STORE key writes the current test result to permanent memory. Results are stored according to Test Method. Up to 50 results
can be stored per test method. All results stored to memory downloaded to a remote computer running GaugeSafe Basic, Plus, or
Live software.
3.3 The <ENTER/Start> Key
•Accepts /assigns the value in a data entry field to that field.
•Initiates a menu function. For example: If the screen displays PRN CURRENT TEST, pressing <ENTER> will cause the current test
results to be printed.
•Turns ON/OFF a menu option.
•Starts new test when controller in ready status.
3.4 The <ESC/STOP> Key
•Returns the LCD to the Live Indicating mode from any menu.
•Clears a data entry mistake by restoring the original number in a data entry field.
•Stops Test and Crosshead movement when machine in testing mode.
3.5 The <Jog UP & Jog Dn> Keys
•Move up and down between selections in menu when in menu view.
•Jog crosshead up and down at user specified rate when display is on live screen.
3.4 The <Freeze> Key
•Freeze the strain channel (Strain Channel optional)
3.6 The ID# Key
The ID# key is used to set the Specimen ID# and specify specimen dimensions.
This key is only active when the LCD is in the Live Indicating mode.
3.7 E-STOP (RED BUTTON ON TOP OF UNIT) - Emergency Stop
Stops cross head movement.

51 Morgan Drive Norwood, MA 02062 11
Tel: (781) 769-0850 Fax: (781) 769-0884
eP2 Controller
Operators Manual
4.0. The Menus and Keys
4.0.1 Test Method Specific Menu Selections
The eP2 Controller can store up to six test methods.
These menu items apply to the current selected test method and need to be set for each test method being used.
Data Acq
Up, Down Arrows to scroll
through menu:
1)
Threshold
2)
Sample Break
3)
Specimen Type
4)
Log Rate
5)
Local Overload
6)
Engineering Units
Control
Up, Down Arrows to scroll through menu:
1)
Test Profile
SegA (in/min)
End CH SegA
End AmtA
Create SegB? (Yes/No)
SegB (in/min)
End CH SegB
End AmtB
1) Cycle Btwn Seg (On/Off)
2)
Post Test (Home/Stop)
3)
Jog Rate
4)
Home Location
5)
6)
Pre Load
7)
8)
ID#
1)
Specimen ID#
Analysis
Up, Down Arrows to scroll
through menu:
1)
Select Analysis
2)
Set Limits
3)
Calculate Results
4)
Send XY Data
5)
Send Current Result
1-6)
Test Method
Select Test Method
Set ABS Zero
7)
Home Rate
Pre Rate
Control Gains
Dir (Tension/Compression)
7)
8)
Freeze Strain
*Optional Feature

51 Morgan Drive Norwood, MA 02062 12
Tel: (781) 769-0850 Fax: (781) 769-0884
eP2 Controller
Operators Manual
4.0.2 Global Menu Selections
These menu items are not procedure specific.
UTILS
Up, Down Arrows to scroll
through menu:
1)
Clear Results
2) Store (Auto/Manual)
3)
Set Date/Time
4)
Stiffness Factor
5)
Install Defaults
6) Diagnostics
7)
Transducer
8)
Supervisor (On/Off)
PRINT
USB Host Menu:
Up, Down Arrows to scroll
through menu:
1)
XY Data-> Host
2)
Stored Res-> Host
3)
Test Method -> Host
4)
Calibration -> Host
5)
Current Res -> Host
Store
Store test data manually
Zero
1)
Both
2)
Load
3)
Position

51 Morgan Drive Norwood, MA 02062 13
Tel: (781) 769-0850 Fax: (781) 769-0884
eP2 Controller
Operators Manual
4.1 The Test Method Menu
1) Set Test Method - Toggle the 1) key to select one of the six test methods. The active method is displayed on the Live Indicating
Screen in the upper left hand corner of the LCD. For example, "M2", would mean that test method 2 is active. A test method includes
all of the user-specified parameters in the Data Acq, Analysis and Control menus. In general, it is used to define how a test is run and
what results are calculated and displayed.
2) Set ABS Zero Pos- Usually used in compression test to define absolute zero position as the point when the two platens touch. This
is required for free height measurements. The absolute zero position is stored to permanent memory so that it is remembered on
power cycles. The plates of the testing machine move till they reach a preset force value, then retract to the user set Home position.
The Absolute Zero Function will determine the zero position to be used for subsequent measurements.
4.2 The Data Acq Menu
Press the <Data Acq> key with the LCD in the Live Indicating mode to enter the Data Acq Menu. Use the <ARROW> keys to scroll to
other menu items. Use the number keys to select options. The following functions are provided in the Data Acq Menu.
1) Threshold - Set the Start Test Threshold in units of force. Data logging for test starts when load crosses threshold. Once the
START Button is pressed on the front panel and the load exceeds the Start Test Threshold the Test Status will change to "T" and
the eP2 Controller will begin logging data.
2) Sample Break - Used to specify the end of test. User specifies sample break as a percentage drop from maximum load. The
controller must record the percentage drop on three consecutive collection points before a break is registered. Setting sample
break to 100% disables it.
3) Specimen Type - Set the specimen geometry and dimensions for stress calculations. Select specimen geometries by tapping the
#1 key, choices are NONE, ROUND, FLAT, BEAM CTR, BEAM CTR - RECT TUBE, BEAM 3RD, AREA and WIDTH. After selecting the
shape of the specimen you are given the opportunity to enter the specimen's dimensions. Dimension selections vary with
specimen shape (type).
4) Log Rate - Set the data logging rate/test length AND specify whether to stream XY data to USB during test. Change log rate/test
length by pressing 1) key:
Logging Rate
Maximum Logging Duration
1000 Hz (1000/second)
15 seconds
500 Hz (500/second)
30 seconds
250 Hz (250/second)
60 seconds
100 Hz (100/second)
150 seconds
50 Hz (50/second)
5 minutes
25 Hz (25/second)
10 minutes
10 Hz (10/second)
25 minutes
5 Hz (5/second)
50 minutes
2 Hz (2/second)
125 minutes
1 Hz (1/second)
250 minutes
1
2Hz (30/minute)
500 minutes
1
6Hz (10/minute)
25 hours
1
30 Hz (2/minute)
125 hours
Toggle the 2) key to turn live streaming of XY data ON/Off.

51 Morgan Drive Norwood, MA 02062 14
Tel: (781) 769-0850 Fax: (781) 769-0884
eP2 Controller
Operators Manual
5) Local Overload - User inputs a value less than or equal to full scale value of the attached load cell. Program will terminate test if
the local overload force value is exceeded.
6) Engineering Units - Press 1 to select Load units (LBF, N, KN, mN, gf, Kgf, ozf).
Press 2 to select Stress units (PSI, KPa, MPa, ksc)
Press 3 to select Length units (in, mm, cm)
Press 4 to select Time Units (sec, min)
Press 5 to select Rate Channel (Load, Position, Strain)
Press 6 to select Position (in, %)
Press 7 to select Strain (in, in/in, %)
7) Set Test Direction- Toggle between Tension and Compression by pressing the 7) key.
8) Freeze Strain- Freezes Strain channel and asks user to remove extensometer when yield data has been collected.
4.3 The Analysis Menu
1) Select Analysis - Scrolling list of available analyses. Use the UP and Down arrows to scroll through the list. Enable Analysis by
pressing the 1) key when the analysis is displayed. After the desired group of analyses have been selected, press the ENT key to
set the analysis parameters, if applicable. If none of the analyses you have selected have parameters, then pressing the ENT key
will return the focus to the main Analysis menu. If any of the active analyses require setup parameters then the program will
prompt for them accordingly. For example, if the Average Load analysis is active, you will be asked to specify the two
displacement values to fix the data range to be used for the calculation. An analysis can have 0, 1 or 2 parameters associated
with it. After all of the analysis parameters have been defined the program will return to the Analysis menu.
NOTE: Parameters are specific to an individual analysis AND several parameters for different analyses have the same
name. If you have several analyses selected, which have parameters of the same name you will be prompted to enter
the parameter values for each analysis. For example, if you have both the Load at Break and the Disp at Break analyses
selected you will be prompted to enter 2 Load Change %'s; one for each of these two analyses.
See Table 4.0 for complete list of eP2 analyses and analysis parameters.
2) Set Limits- Set low and high limits for each active analysis. LCD screen will report any out of limit results after each test.
3) Calculate Results- Useful if analysis parameters were not entered correctly. After the test, you can change the analysis
parameters and then recalculate the results by pressing the 3) key in the analysis menu.
4) Send XY Data- Set to OFF or End of Test to transmit XY data to GaugeSafe at the end of the test.

51 Morgan Drive Norwood, MA 02062 15
Tel: (781) 769-0850 Fax: (781) 769-0884
eP2 Controller
Operators Manual
Analysis
Description
Parameter 1
Parameter 2
Max Load
Maximum Load in specified displacement range
Displacement1
Displacement 2
Local Maximum
Maximum Load in specified displacement range
Displacement1
Displacement 2
Max Ld/Width
Maximum Load/Sample Width specified displacement
range
Displacement1
Displacement 2
Max Stress
Maximum Stress
None
None
Min Load
Minimum Load in specified displacement range
Displacement1
Displacement 2
AVG Ld1 <> Disp
Average Load in specified displacement range
Displacement1
Displacement 2
AVG Ld2@Ld-Dp
Average Load in specified displacement range measured
from displacement at specified load threshold
Load
Displacement
Window
Load at Break
Load at specified break point
Load Change%
None
Disp at Break
Displacement at specified break point
Load Change
None
Percent Elong
Percent Elongation, length at specified break point divided
by original gage length.
Load Change%
Gage Length
Load at Disp
Load at specified displacement
Displacement
None
Disp at Load
Displacement at specified load
Load
None
Stiffness
Force/displacement between two specified displacements
Displacement1
Displacement 2
Energy <> Disp
Area beneath force displacement curve between two
specified displacements
Displacement1
Displacement 2
Free Height *
Cross head position at threshold relative to ABS zero
None
None
Static Us**
Static coefficient of friction
Sled Weight
None
Kinetic Uk***
Kinetic coefficient of friction
Sled Weight
None
Table 4.0 Analyses and Analysis Parameters
*Free Height: You MUST set the Absolute zero position when using the free height analysis.
** Static Us: You MUST have the Max Load analysis active with Displacement 1 set to 0 in. and Displacement 2 set
to 0.1 in.
*** Kinetic Uk: You MUST have the average load in displacement range analysis (AVG Ld1 <> Disp) active with the specified
displacement window after the max load analysis.

51 Morgan Drive Norwood, MA 02062 16
Tel: (781) 769-0850 Fax: (781) 769-0884
eP2 Controller
Operators Manual
4.4 The PRINT Menu
Press the <PRINT> key with the LCD in the Live Indicating mode to enter the PRINT Menu. USB Host Menu will be displayed prior to
display of menu options below. Use the <ARROW> keys to scroll to other menu items. Use the number keys to select options. The
following functions are provided in the PRINT Menu.
1) XY Data-> Host - Transmit XY Data via the USB port to a remote computer running GaugeSafe.
2) Stored Res-> Host - Transmit stored test results and statistics via the USB port to a remote computer running GaugeSafe.
3) Test Method -> Host - Transmit Test Method settings to computer running GaugeSafe.
4) Calibration -> Host - Transmit calibration data to computer running GaugeSafe.
If the optional USB port is included on the controller a secondary set of options will appear for transfering to a flash drive.
4.5 The UTILS Menu
Press the <UTILS> key with the LCD in the Live Indicating mode to enter the UTILS Menu. Use the <ARROW> keys to scroll to other
menu items. Use the number keys to select options. The following functions are provided in the UTILS Menu.
1) Clear Results - Clear all stored results for the active test method or for all test methods.
2) Store - Set to store test results automatically or manually
3) Set Date/Time - Set the eP2 Controller's date and time clock.
4) Stiffness Factor- Enter a value for machine compliance. Compensates logged and transmitted position data based on load. Set to
zero to disable stiffness correction.
5) Install Defaults (password protected) - Reset the eP2 Controller to its default state. If defaults are installed, all test setup
information must be reentered. Password required.
6) Diagnostics - view analog channel and digital I/O information.
7) Transducer - Calibrate the load and position channels and set the maximum speed for the position channel. The load channel can
also be calibrated from the Zero Menu. The calibration menu is password protected. The shunt calibration is used to span the load
calibration. See Section 5.0 for calibration instructions.
8) Supervisor (password protected) - Toggles Supervisor ON/OFF. When Supervisor is ON changes can be made to the settings of the
Test Methods and Calibration. When Supervisor is OFF changes cannot be made to Test Methods or Calibration, but the
previously stored Procedures can be selected via the Test Method key.

51 Morgan Drive Norwood, MA 02062 17
Tel: (781) 769-0850 Fax: (781) 769-0884
eP2 Controller
Operators Manual
4.6 The Control Menu
A variety of machine control profiles can be programmed in the eP2 Controller. For example:
•Move at a constant crosshead rate until reaching a specified displacement value then terminate the test.
•Move at a constant crosshead rate until reaching a specified force value. Then hold the force value for specified amount of
time
•Cycle between two displacement limits at constant crosshead rate a specified amount of times.
1. Set Test Profile-
•CONTROL CH SegA: Select control channel, Position control or Load Control
•SegA ( ): Enter the rate for segment A and press ENT. The rate will be in units appropriate to control channel. For example if
CONTROL CH SegA is Load then the rate units will be force/time and if the CONTROL CH SegA is Position then the rate units
will be in displacement/time.
•END CH SegA: Choose load, position or time as end channel by pressing 1) key and press ENT.
•END Amt A ( ): Enter end amount for segment A and press ENT. Units will be based on value for END CH SegA. Value of
zero means segment will continue until sample break or the user stops test by pressing STOP.
•Create SegB: Press No, the program will return to the Control menu.
Press Yes, you will be prompted for SegB profile:
•CONTROL CH SegB: Select control channel, Position control or Load Control
•SegB ( ): Enter the rate for segment B and press ENT. The rate will be in units appropriate to control channel. For example if
CONTROL CH SegB is load then the rate units will be force/time and if the CONTROL CH SegB is Position then the rate units
will be in displacement/time.
•END CH SegB: Choose load, position or time as end channel by pressing 1) key and press ENT. END Amt B ( ): Enter end
amount for segment A and press ENT. Units will be based on value for END CH SegA. Value of zero means segment will
continue until sample break or the user stops test by pressing STOP.
•Cycle between segments? If no, the program will return to the Control Menu. If yes:
Number of Cycles (1-300,000): Input the number of cycles then press “ENT”. If Number of Cycles is greater than
one, the user will be asked to select on which cycles to log data. Return to Control Menu.
2. Post Test- Toggle between Stop and hold current position OR go to Home position at the end of test.
3. Jog Rate- Specify crosshead speed for manual jogging.
4. Home Location- Define home position. By default this is set to zero and home is where the position channel is zeroed. In some
tests such as certain compression test it is necessary to put cross-head a certain distance above the zero position to allow sample
placement for next test. Programming a negative value for Home Location will provide this function.
5. Home Rate- Specify crosshead rate for returning to home position.
6. Pre Load- Specify force value that when achieved, program will zero the position channel and begin executing control segment A.
Displacement will be zeroed after preload completes.
7. Pre Rate- Specify the crosshead rate for achieving Pre Load force.

51 Morgan Drive Norwood, MA 02062 18
Tel: (781) 769-0850 Fax: (781) 769-0884
eP2 Controller
Operators Manual
NOTE: Pre Load and Pre Rate defined from the control menu are always executed first when START button is pressed to begin test.
If either Pre Load OR Pre Rate is set to zero, then the Pre function will be by passed and control segment A will start immediately
upon pressing the START button.
8. Control Gains- Specify PID gains for automatic control. Position gain should be factory preset. Crosshead movement with eP2
controller is always under position control. Load gain needs to be set if you are running procedure where you want to hold load.
4.7 The Zero Menu
1.Both- Resets both the load and position readings to zero. The home location is relative to zero position.
NOTE: The absolute position zero is not affected by this action.
2.Load- Resets the load readings to zero.
3.Position- Resets the position readings to zero. The home location is relative to zero position.
NOTE: The absolute position zero is not affected by this action.
4.Strain - Resets the strain readings to zero, only appears if strain option is installed.
5.0. Calibration
5.1. Transducer Autorecognition
The eP2 controller features transducer autorecognition. When calibrated load cell is connected to the eP2, the controller identifies
the transducer's serial number and loads the appropriate calibration into eP memory for testing.
5.2. How to Calibrate Analog Transducers
You can calibrate up to 4 load cells to the eP2. There can be up to 5 points in each calibration. The first point in the calibration MUST
be zero load.
There are two options for calibrating analog transducers to the eP2 Digital Controller.
A) Multipoint Calibration
Adjust the transducer to multiple known engineering unit values and enter the points into the eP2 Digital Controller
B) Two Point Shunt Calibration
Two point shunt calibration with zero load as first point and second point set by selecting 1) Shunt in the
calibration menu. Depressing the shunt button puts resistance across bridge that simulates exercising the
transducer to known value.

51 Morgan Drive Norwood, MA 02062 19
Tel: (781) 769-0850 Fax: (781) 769-0884
eP2 Controller
Operators Manual
Step 1: Turn on the system and allow it to run for 10 minutes before calibrating.
Step 2: Unload the machine or place the transducer at its zero point. If calibrating a hydraulic machine, float the piston before
taking any readings. Press <ENTER> to take the zero reading. The left side of the display will indicate PT1 has been read.
Step 3: Select the Engineering Units for calibration from the Data Acq Menu.
Step 4: Select Transducer from the Utils Menu.
Step 5: Enter the password. Contact ADMET technical support if you have lost the password.
Step 6: Select Transducer Type. Load, for example.
Step 7: Enter the load cell number. Use zero if your system has only one load cell.
NOTE: Smart Ducer ID will flash if available between these steps.
Step 8: Input the full scale range or the capacity of the machine. The range should be input in the currently active engineering units.
Step 9: Input the resolution (minimum load increment).
Step 10: Input the transducer serial number
Step 11: Calibrate to enter the measure mode or <ESC> to exit.
NOTE: If you decide to exit the Calibration Menu at this time the values entered for Full Scale and Resolution
will be saved.
Required Information Before Continuing Calibration
NOTE: The first calibration point must be at zero load.
It may be beneficial to take a few more calibration readings in areas of greatest inaccuracy. The number next to "Set PT No" on the
display will indicate how many calibration readings have been taken. As the calibration points are entered, write down the
corresponding load value. After all five calibration points have been taken, or the <STORE> key is pressed when using less than five
points, the EP2 automatically switches to engineering input mode. Input the load value corresponding to each calibration point reading
stored. The calibration points are stored sequentially. The first point is zero followed by the second, third and so forth. Once an
engineering unit value has been entered for each calibration point stored, the unit will automatically save the calibration.

51 Morgan Drive Norwood, MA 02062 20
Tel: (781) 769-0850 Fax: (781) 769-0884
eP2 Controller
Operators Manual
Multipoint Calibration
Step 12: Load the machine to a desired load and press <ENTER> to set a calibration point (voltage measurement). The voltage value
is NOT displayed but it has been saved to nonvolatile memory. Write down the corresponding engineering unit value for
each calibration point. Repeat this step until all readings are taken.
Step 13: Press <STORE> to exit the measurement mode if fewer than five calibration points are used. (The program will
automatically proceed from Step 12 to Step 14 after the fifth reading.
Two Point Shunt Calibration
Step 12: Toggle Shunt to ON by pressing the 1) key and then and press <ENTER> to set a calibration point (voltage measurement).
The voltage value is NOT displayed but it has been saved to nonvolatile memory.
Step 13: Press <STORE> to exit the measurement mode.
Step 14: Input the corresponding engineering unit value for each measurement point. After all values have been entered, the
program will automatically generate the corresponding scale factors and store them to permanent memory.
DONE! READY TO VERIFY CALIBRATION
Step 15: To verify the calibration, exit out to the Indicating Screen and apply specific loads to the machine and compare the reading
on the controller with the standard.
5.3. What Occurs During Calibration
The calibration procedure allows up to five calibration points to be entered. Each successive pair of points is connected by a straight
line and the slope of each line is the calibration scale factor used for that region. This results in a piecewise linear function which
maximizes accuracy.
5.4. Saving Calibration Data
All calibration data can be transferred to and from the GaugeSafe Data Exchange software.
5.5. Setting Gage Length for an Adjustable Extensometer
Select Utils --> Transducer --> Cailbration. Enter the password. Contact ADMET techincal support if you have lost the password.
Select Strain (Encoder) press enter to leave pulses as is. Set the gage length to the current actual value and press enter to exit the
calibration screen.
Table of contents
Popular Controllers manuals by other brands
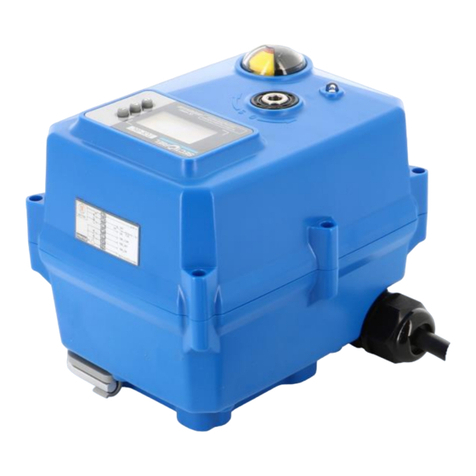
Sectoriel
Sectoriel TCR-05-11-T-KT manual
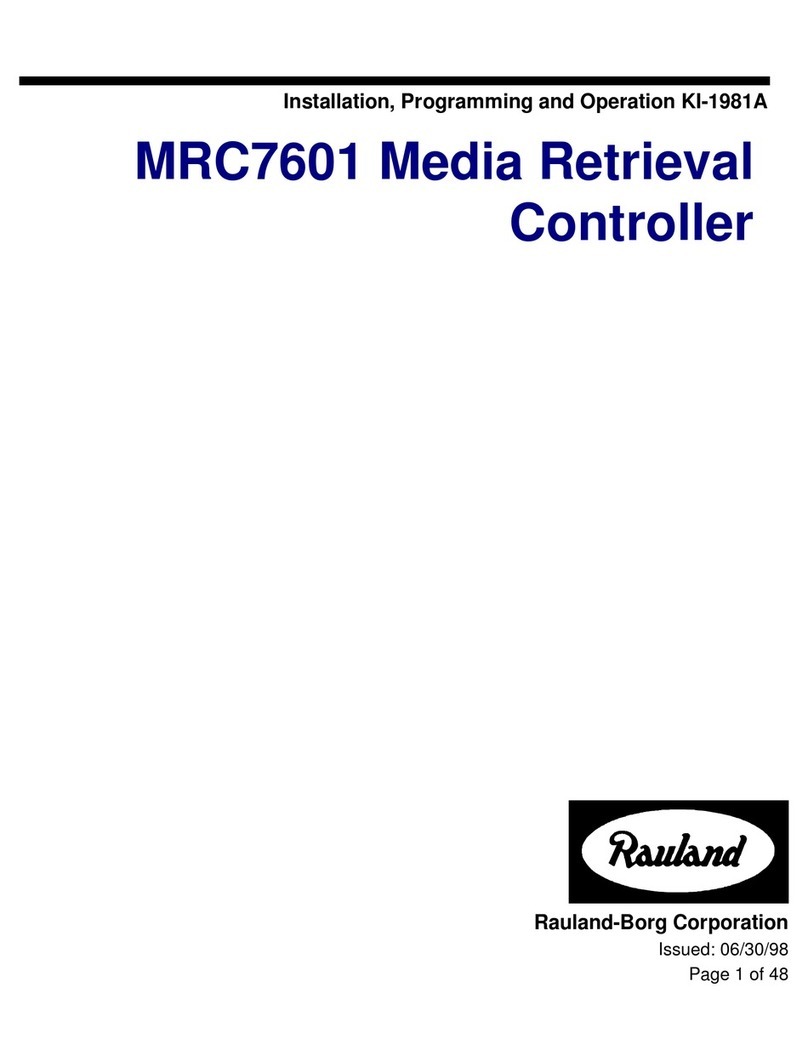
Rauland-Borg
Rauland-Borg MRC7601 Installation, programming and operation instructions
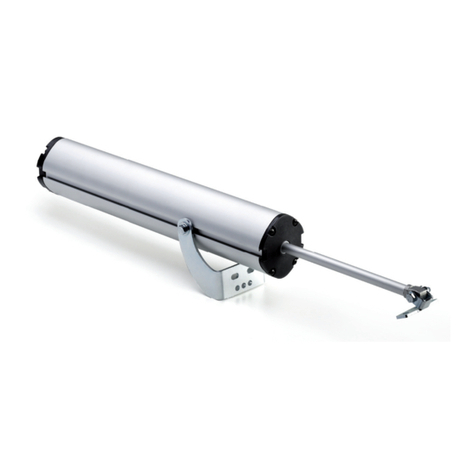
Comunello
Comunello MOWIN FAST 50/160 instruction manual
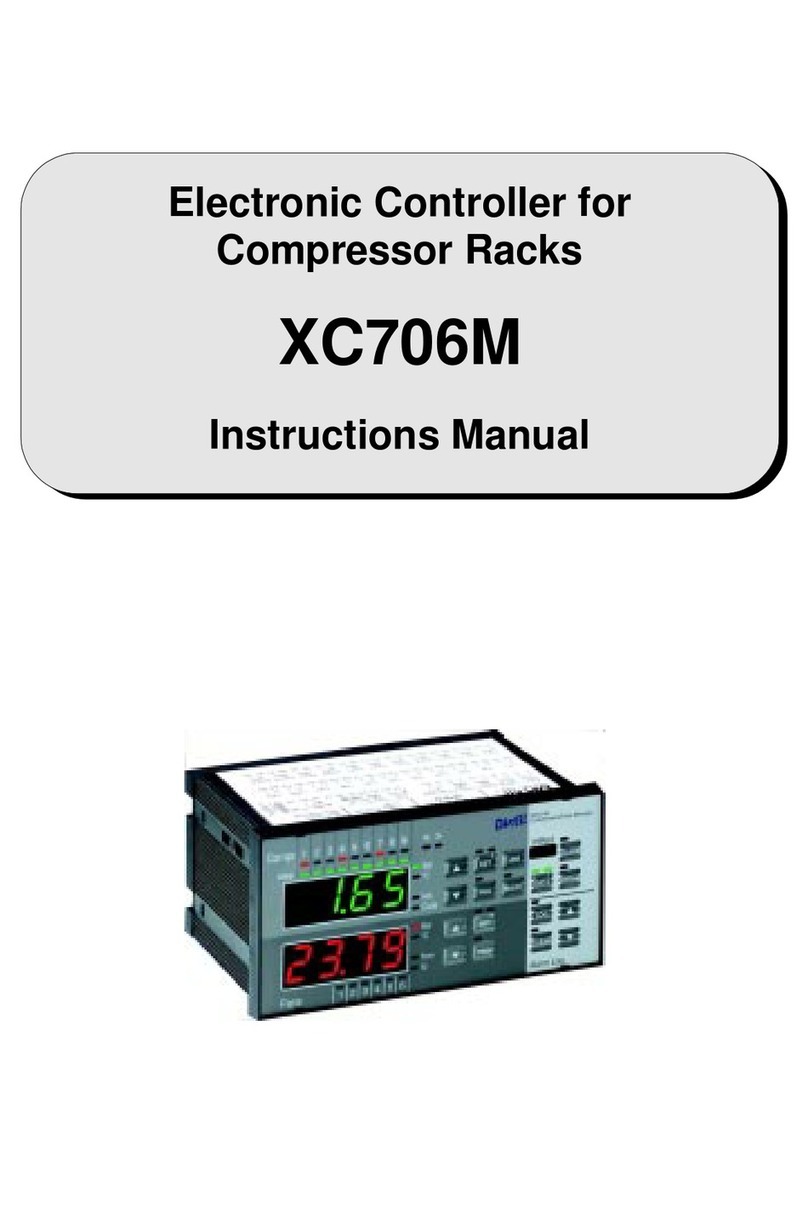
dixell
dixell XC706M instruction manual
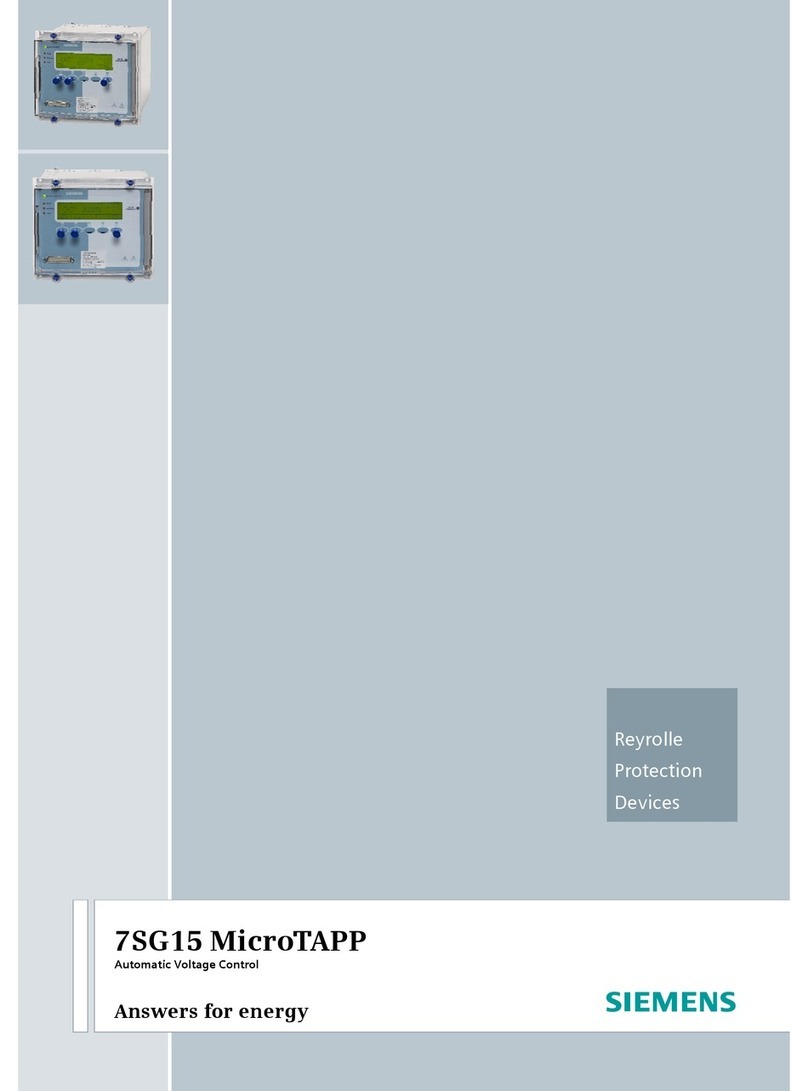
Siemens
Siemens 7sg15 microtapp Operation manual
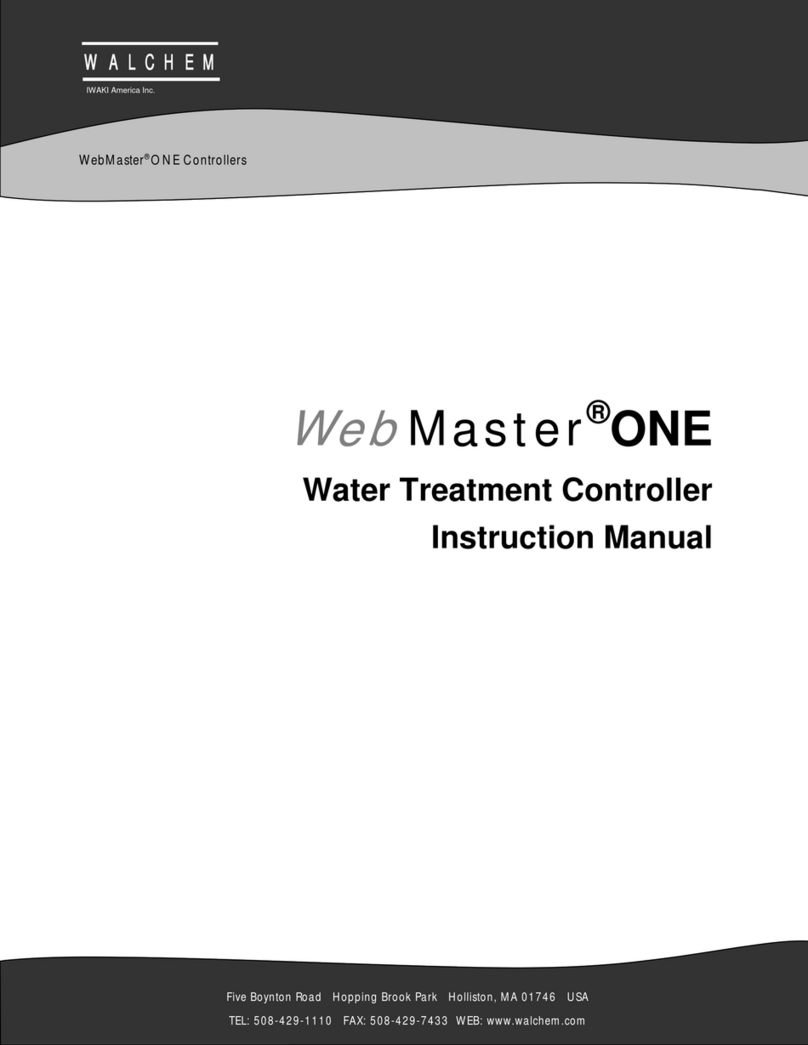
Walchem
Walchem WebMaster instruction manual