AEM Performance Electronics 30-8300 User manual

INSTRUCTION
MANUAL
P/N 30-8300
8 CH POWER DISTRIBUTION UNIT
STOP! - READ THIS BEFORE INSTALL OR USE!
WARNING:
IT IS THE R ESPONSIBILITY OF THE INSTALLER TO ULTIMATELY CONFIRM THE
CONFIGURATION USED FOR ANY P ARTICULAR INSTALLATION IS SAFE FOR ITS
INTENDED USE. AEM HOLDS N O RESPONSIBILITY F OR ANY D AMAGE THAT
RESULTS FROM THE MISUSEOF THIS P RODUCT.
Working on Electric Vehicle tractive systems with high voltage battery packs requires special experience
and training. Doing this safely is entirely the responsibility of the installer. AEM has done everything it can
to ensure the VCU has appropriate fault detection and failsafe logic but that does not mean that your
installation will be safe or that your VCU installation will not interfere with other systems on your vehicle and
create a hazardous situation. It is the responsibility of the installer to understand the implications of each
stage of tractive system installation and testing, and to know what might be unique about your application
that presents an unintended hazard or potential safety issue – and to solve it.
Following is a brief list of recommended practices. This is not a comprehensive list; as noted below, if you
are not well-versed in the appropriate installation and testing procedures, you should refer the installation
and calibration to a reputable installation facility or contact AEM EV for a referral in your area.
When access is required near the battery pack, the cell segments must be separated by using an
appropriate maintenance disconnect plug.
When working on the battery pack or tractive system, safety glasses with side shields and
appropriate insulated tools must be used.
Always wear Class 0 gloves rated at 1000V with leather protectors.
Only use a CAT III rated digital multi-meter (DMM) and test leads.
When working on the battery pack or tractive system, use the one hand rule: work with one hand
keeping the other behind your back whenever possible.
During initial system power up and testing, the vehicle must be raised off the ground and supported
appropriately. Wheels/tires should be removed.
During the VCU firmware upgrade process, battery cell segments must be separated by using an
appropriate maintenance disconnect plug.
Do not make calibration changes while the inverter PWM is enabled.
USE THIS PDU WITH EXTREME CAUTION. MISUSE AND/OR IMPROPER INSTALLATION CAN CAUSE
SIGNIFICANT DAMAGE TO YOUR VEHICLE AND PROPERTY BELONGING TO YOU OR OTHERS, AS
WELL AS PERSONAL INJURY OR DEATH. IF YOU ARE NOT WELL VERSED IN THE INSTALLATION
OF TRACTIVE SYSTEMS OR CONFIGURING THE CALIBRATIONS IN THE AEM EV VCU THAT ARE
NECESSARY TO CONTROL THE VEHICLE, YOU SHOULD REFER THE INSTALLATION AND VCU
CALIBRATION TO A REPUTABLE INSTALLATION FACILITY, OR CONTACT AEM EV FOR A
REFERRAL IN YOUR AREA. IT IS THE RESPONSIBILITY OF THE INSTALLER TO ULTIMATELY
CONFIRM THAT THE INSTALLATION AND CALIBRATIONS ARE SAFE FOR ITS INTENDED USE.
AEM Performance Electronics, 2205 126th Street Unit A, Hawthorne, CA 90250 - Phone: (310) 484-2322
http://www.aemelectronics.com

The PDU-8 is a very high current, small, and lightweight module designed to be mounted near the devices
requiring power. Its design philosophy is for multiple units to be part of a vehicle installation and to
distribute the power throughout the vehicle rather than having it concentrated in a central area.
The PDU-8 is not a stand-alone device. It is designed to be operated as a satellite unit and controlled via
CAN by either an AEM Vehicle Control Unit or a programmable 3rd
party
device that
can
generate the
required
CAN
control
messages.
As such,
the
PDU-8 module
itself
is not
programmable in
any
way and
only
carries out
commands issued
by
other
devices.
Specific
PDU’s are identified
by
grounding
different combinations of
configuration pins
on
the
PDU
connector
and
8 unique
combinations are available. Since
the
pin configurations
are
part
of
the
harness
no
software ID
configuration
is needed
to
be
stored
within the
PDU,
meaning units
are field interchangeable.
Specifications
Parameter
Value
8 Outputs
Switched 12V
4 Channels continuous 20A max per channel
4 Channels continuous 10A max per channel
Multiple channels can be combined for higher currents
Duty Cycle
Any channel, 100hz fixed, 0-100% duty
Total Unit Maximum Current
90A
CAN Bus
CAN 2.0, 500 kbps, up to 8 units per bus
Status LED
Solid when powered up and OK, Flashing when CAN is lost
Casing
Sealed Billet Aluminium
Size
105 x 67 x 33 mm
Weight
216 grams (7.6 oz)
NOTE: Use 2 pins for each output for full current capacity.
6/9/2020 – Document Number: 10-8300-EV © 2020 AEM Performance Electronics

Connectors
ID
Connector
Loom/Mating Connector
1
TE SUPERSEAL 6437288-6
TE 3-1437290-7
2
M6 threaded power pin
M6 ring terminal (recommended)
A mating connector kit is available separately from AEM (P/N 30-3711, PDU Plug & Pin Kit). It contains 1x
mating connector, 26x terminals, 10x blanking seals, 1x M6 Ring terminal, and 1x Ping Terminal cover.
Pin Out
Connector
1, TE Superseal
Pin
Name
Function/Notes
1
High Side Driver 1
20 Amp Max
2
3
CAN Low
Unterminated
4
CAN High
Unterminated
5
Ground
6
High Side Driver 5
20 Amp Max
7
8
High Side Driver 2
10 Amp Max
9
10
Config 3
Ground for Unit ID’s 5,6,7,8
11
Ground
12
High Side Driver 6
10 Amp Max
13
14
High Side Driver 3
10 Amp Max
15
16
Config 2
Ground for Unit ID’s 3,4,7,8
17
Not Used
18
High Side Driver 7
10 Amp Max
19
20
High Side Driver 4
20 Amp Max
21
22
Not Used
23
Not Used
24
Config 1
Ground for Unit ID’s 2,4,6, 8
25
High Side Driver 8
20 Amp Max
26
Connector
2, M6 Threaded Power Pin
Pin
Name
Function/Notes
1
12V Power
6/9/2020 – Document Number: 10-8300-EV © 2020 AEM Performance Electronics

CAN Control
If you are using the PDU-8 module with an AEM VCU then no specific CAN setup is required. Refer to the
VCU instructions to activate the PDU within the control strategy used by the VCU.
If you are controlling the PDU-8 with a 3rd
party device the following CAN control information will be needed.
A CAN DBC file is available from AEM to aid in entering the CAN setup.
The PDU-8 will continuously transmit 2 messages at 20hz containing the current status of the 8 channels.
Tx Message 1 is for Channels 1 to 4, Tx Message 2 is for Channels 5 to 8.
PDMMeasuredCurrent0# is an unsigned 10 bit number with a scale of 0.1A an d an offset of 0 (0-102.3A).
Note that the individual channels are assumed to be used to drive high current loads, in some cases up to
20A per channel. The current measurement is designed for use above 2 amps and currents below this are
unreliable.
PDMErrorStatus0# is a 3 bit unsigned number with a scale of 1 and an offset of 0 (0 to 7). The possible
values for the PDMErrorStatus0# are:
4 = Short Circuit
2 = Current Limit Exceeded
1 = Open Circuit
0 = OK
The Open Circuit detection only works when the channel is commanded off. Once the channel is turned on
the measured current should be used to identify errors.
PDU-8 Tx Message 1, 0x000A0610 (for unit 1) continuous transmit at 20 hz
6/9/2020 – Document Number: 10-8300-EV © 2020 AEM Performance Electronics

PDU-8 Tx Message 2, 0x000A0610 (for unit 1) continuous transmit at 20 hz
The PDU-8 is controlled by 2 CAN received messages;
Rx Message 1 receives the control information to the PDU-8 unit. Each message consists of 8 bytes. Each
byte controls 1 of the 8 output drives. Byte 1 controls drive 1... Byte 8 controls drive 8. If the value is set to
0 then the output is off. A non 0 value sets the current limit for the output. If a value higher than the allowed
maximum is selected then the current limit is set to the max allowed for that channel. If the PDU-8 unit does
not receive the command message within 500mS it will switch off all the outputs and flash the Status LED.
PDMMaxCurrent0# is an unsigned 8 bit number with a scale of 0.4A and an offset of 0 (0-102A).
PDU-8 Rx Message 1, 0x000A0620 (for unit 1) timeout if not updated within 500mS
6/9/2020 – Document Number: 10-8300-EV © 2020 AEM Performance Electronics

Rx Message 2 receives the PWM duty value for the output. The PWM control of the outputs is designed to
regulate the speed of devices like pumps and fans. If message 2 is present then all of the outputs will
become PWM duty cycle outputs with a base frequency of 100hz.The requested duty cycle can vary
between 0 – 100%. Any outputs that you do not want to have a PWM should have a value of 255. If this
message does not update within 500mS then the PDU-8 will treat all channels with simple ON/OFF control.
PDMDutyOut0# is an unsigned 8 bit number with a scale of 0.392157 and an offset of 0 (0-100%).
PDU-8 Rx Message 2, 0x000A0630 (for unit 1) timeout if not updated within 500mS
6/9/2020 – Document Number: 10-8300-EV © 2020 AEM Performance Electronics

Multi -Unit Configuration
There can be up to 8 PDU modules units on the same CAN bus. If more than one PDU is used on a CAN
bus then the unit ID for each module needs to be set. If only 1 unit is to be used simply leave all the Config
pins disconnected and ignore the rest of this section.
For multiple units to function in a single CAN bus, the PDU’s need to be assigned one of 8 Unit ID’s, each
using unique receive and transmit CAN message addresses. To assign the Unit ID, the 3 config pins on the
main connector (pins 10, 16 and 24) are either left open circuit (O/C) or connected to GND (Pin11).
The following table lists the configuration pin settings and the resulting 8 possible unit IDs.
Unit
ID
Config 1
Pin 24
Config 2
Pin 16
Config 3
Pin 10
TX Msg 1
Address
TX Msg 2
Address
RX Msg 1
Address
RX Msg 2
Address
1
O/C
O/C
O/C
0x000A0610
0x000A0611
0x000A0620
0X000A0630
2
Gnd
O/C
O/C
0x000A0612
0x000A0613
0x000A0621
0X000A0631
3
O/C
Gnd
O/C
0x000A0614
0x000A0615
0x000A0622
0X000A0632
4
Gnd
Gnd
O/C
0x000A0616
0x000A0617
0x000A0623
0X000A0633
5
O/C
O/C
Gnd
0x000A0618
0x000A0619
0x000A0624
0X000A0634
6
Gnd
O/C
Gnd
0x000A061A
0x000A061B
0x000A0625
0X000A0635
7
O/C
Gnd
Gnd
0x000A061C
0x000A061D
0x000A0626
0X000A0636
8
Gnd
Gnd
Gnd
0x000A061E
0x000A061F
0x000A0627
0X000A0637
6/9/2020 – Document Number: 10-8300-EV © 2020 AEM Performance Electronics

Mounting
The PDU-8 has four 4.5mm mounting holes in a 51mm x 111mm (2.0” x 4.4”) rectangular pattern and is
suitable for use with either an M4 or a #8 mounting fastener.
If the total power provided by any one PDU-8 is expected to exceed 50A continuous then the unit should be
mounted with the bottom flush against a surface which can act as a heat dissipation path.
Dimensions
6/9/2020 – Document Number: 10-8300-EV © 2020 AEM Performance Electronics

PROCEDURES FOR ISSUANCE OF A RETURN MERCHANDISE AUTHORIZATION (RMA) NUMBER–
Notice
Advanced Engine Management Co., inc. (“AEM”) and its affiliates, shareholders, directors, officers, agents,
representatives, successors and assigns (collectively, the “AEM Parties”) hold no responsibility for any
damage or injury that results from installation or misuse of any AEM products. Except for, to the extent
applicable to the products you have purchased, AEM’s 12 month limited warranty (see below), all AEM
products are provided “as is” and the AEM Parties expressly disclaim all warranties, whether express,
implied, statutory or otherwise. The AEM Parties specifically disclaim all implied warranties of
merchantability and fitness for a particular purpose, and all warranties arising from course of dealing,
course of performance, usage or trade practice.
Under no circumstances shall any AEM Party be liable to you or any other person or entity for any
damages of any amount or character (including, without limitation, any general, indirect, special, incidental,
exemplary, consequential or punitive damages) arising out of, related to, or in connection with (1) your
installation of any AEM products or (2) your misuse of any AEM products. In no event shall any AEM Party
be liable to you or any other person or entity for any lost or corrupted data, lost profits, lost revenues, loss
of use, diminution in value, loss of other intangibles or any special, incidental, indirect, exemplary, punitive
or consequential damages, whether arising out of breach of contract, tort (including negligence) or
otherwise, regardless of whether such damages were foreseeable and whether or not the AEM Parties
were advised of the possibility of such damages. Some jurisdictions may not allow the exclusion or
limitation of incidental or consequential damages, so the above exclusions shall only apply to the extent
permissible under applicable law.
12 Month Limited Warranty
AEM Performance Electronics warrants to the consumer that all AEM Electronics products will be free from defects in material and
workmanship for a period of twelve months from the date of the original purchase. Products that fail within this 12-month warranty
period will be repaired or replaced when determined by us that the product failed due to defects in material or workmanship. This
warranty is limited to the repair or replacement of the AEM Electronics part. This warranty applies only to the original purchaser of
the product and is non-transferable. All implied warranties shall be limited in duration to the said 12-month warranty period.
Improper use or installation, accident, abuse, unauthorized repairs or alterations performed by the user on any AEM Electronics
products voids this warranty.
In no event shall this warranty exceed the original purchase price of the AEM Electronics part nor shall AEM Electronics be
responsible for special, incidental or consequential damages or cost incurred due to the failure of this product.
AEM Electronics disclaims any liability for consequential damages due to breach of any written or implied warranty on all of its
products.
Warranty returns will only be accepted by AEM Electronics when accompanied by a valid Return Merchandise Authorization (RMA)
number and a dated proof of purchase. The product must be received by AEM Electronics within 30 days of the date the RMA is
issued. Warranty claims to AEM Electronics must be shipped to us prepaid (we recommend a shipping service with package
tracking capability). Once your package is received by our warranty and repairs department you will be notified and provided with
updates.
Please note that before AEM Electronics can issue an RMA for any product, it is first necessary for the installer or end-user to
contact our technical support team to discuss the problem. Most issues can be resolved over the phone. Under no circumstances
should a system be returned, or an RMA requested before our support team is contacted. This will ensure that if an RMA is needed
that our team is able to track your product through the warranty process.
You can reach our Tech Support Team for support on all AEM Electronics performance products by phone at 1-800-423-0046. To
contact us by email for engine management systems, email us at emste[email protected]. For all other products, email us at
AEM Electronics will not be responsible for products that are installed incorrectly, installed in a non-approved application, misused,
or tampered with. In the case of AEM Electronics Fuel Pumps, incorrect polarity (+&- wires crossed) will not be warranted. Proper
fuel filtration before and after the fuel pump is essential to fuel pump life. Any pump returned with contamination will not be
warranted.
PRODUCTS OUTSIDE OF WARRANTY PERIOD
Any AEM Electronics product, excluding discontinued products, can be returned for repair if it is out of the warranty period. There is
a minimum charge of $50.00 for inspection and diagnosis of AEM Electronics parts. Parts used in the repair of AEM Electronics
components will be extra. AEM Electronics will provide an estimate of repairs and must receive written or electronic authorization
from you before repairs are made to a product.
6/9/2020 – Document Number: 10-8300-EV © 2020 AEM Performance Electronics
Table of contents
Popular Power Distribution Unit manuals by other brands
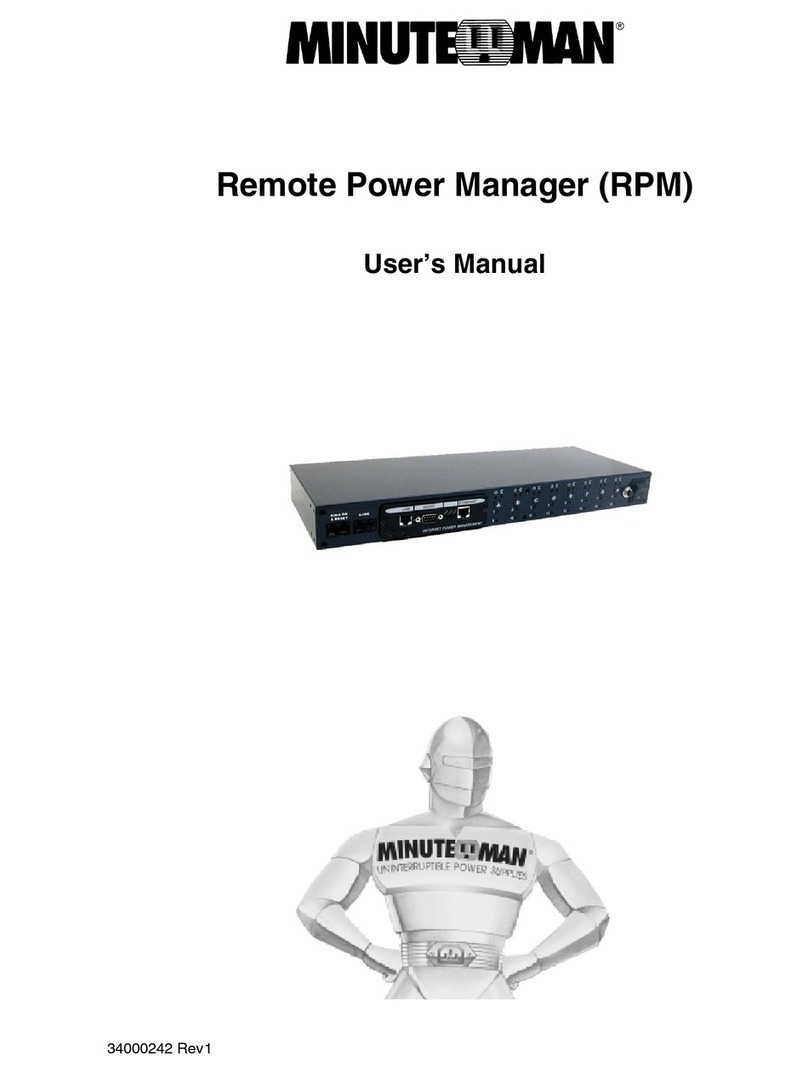
Minuteman
Minuteman RPM 1609 user manual

D&R ELECTRONICS
D&R ELECTRONICS PDU-16SS user manual
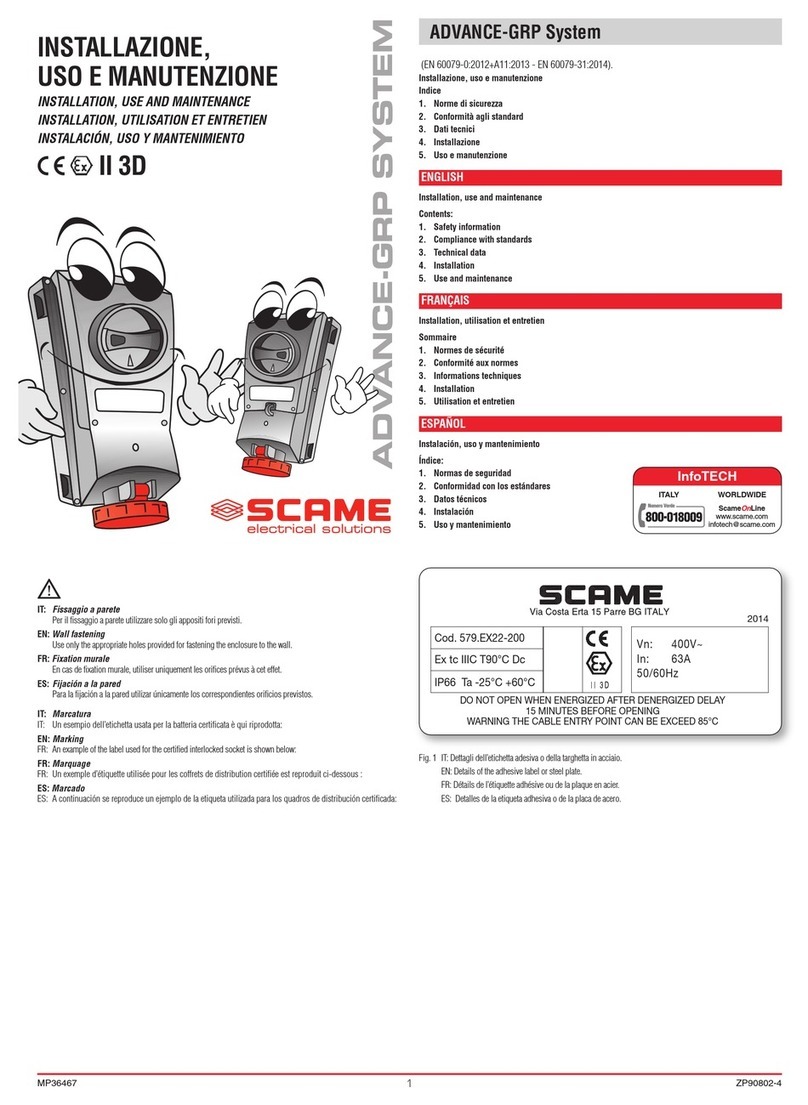
Scame electrical solutions
Scame electrical solutions ADVANCE-GRP Series Installation, use and maintenance
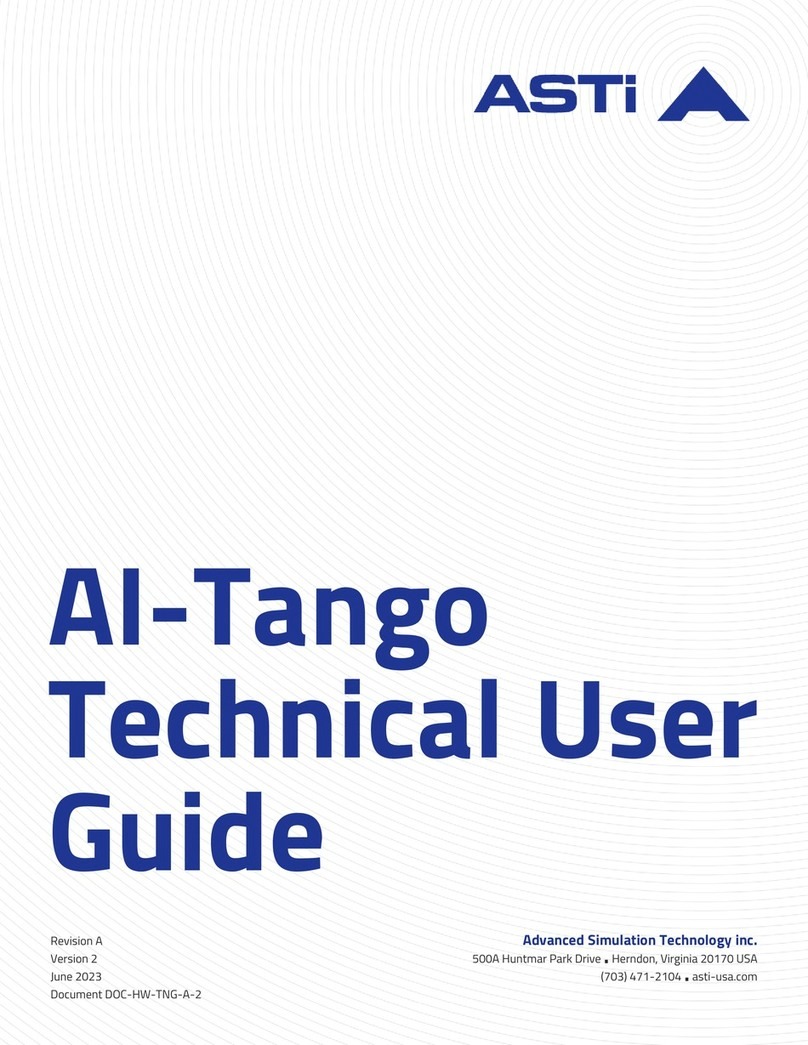
ASTi
ASTi AI-Tango Technical user guide
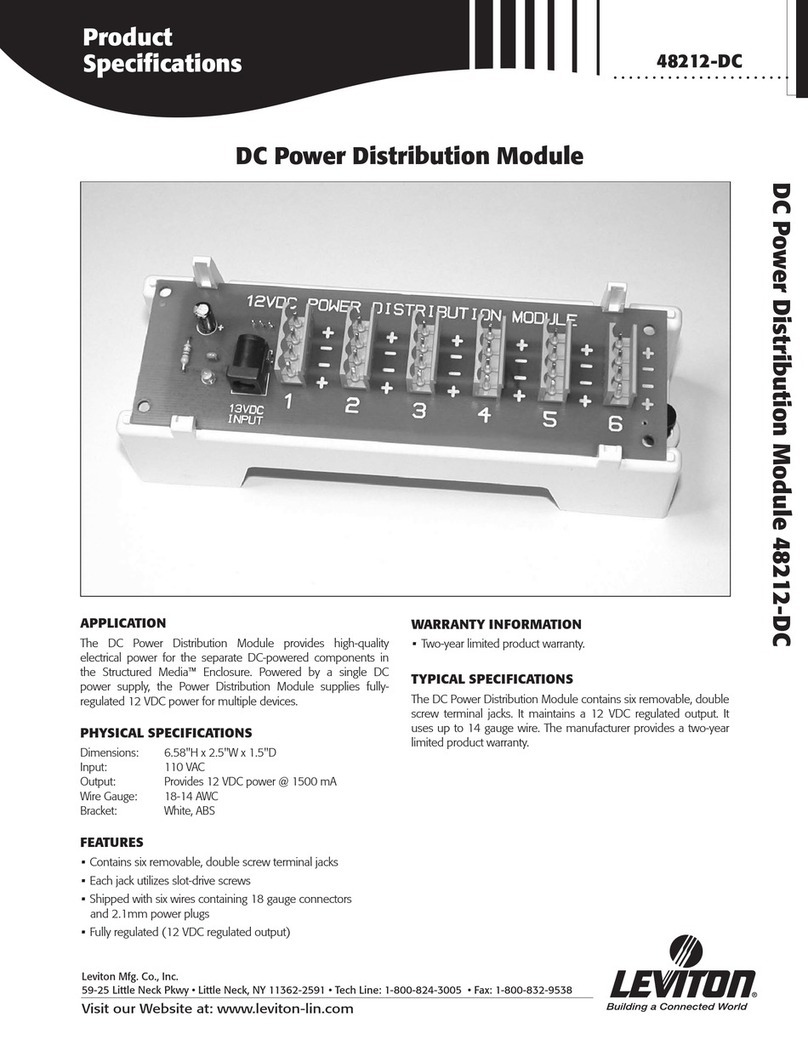
Leviton
Leviton DC Power Distribution Module 48212-DC Product specifications
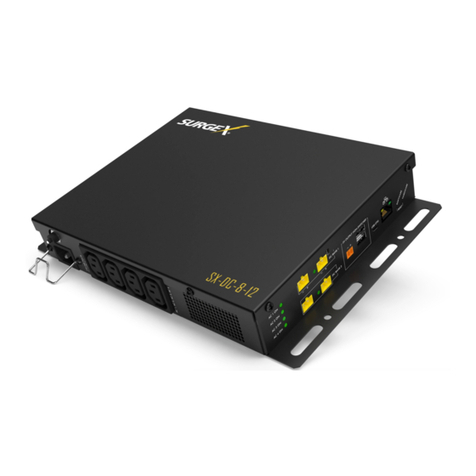
Ametek
Ametek SurgeX Squid SX-DC-8-12-120 user manual