Aerovent ATBR series Manual

©2006 Aerovent
Receiving, Inspection & Unpacking
General Installation
When the equipment is received all items should be
carefully checked against the bill of lading to be sure all
crates and cartons have been received. Before accept-
ing delivery, carefully inspect each carton or crate for
visible shipping damage. If any damage is noticed, the
carrier should make the proper notation on the delivery
receipt acknowledging the damage. Make notations of all
damage on all copies of the bill of lading and have all
copies countersigned by the delivering carrier. The car-
rier should also fill out a Carrier Inspection Report. The
factory Traffic Department should then be contacted.
File claim for damage with the carrier. Physical damage
to the unit after acceptance is not the responsibility of
Twin City Fan Companies, Ltd.
Unpack each carton or crate and verify that all required
parts and proper quantities of each item have been
received. Refer to drawings for part descriptions. Report
shortages or missing items to your local representative
to arrange for replacement parts.
Due to availability of carriers and truck space, it is not
possible to guarantee that all items will be shipped
together. Verification of shipments must be limited to
only those items on the bill of lading.
The unit nameplate must be checked to make sure the
voltage agrees with the power supply available.
CAUTION: Sheet metal parts, screws, clips and similar
items inherently have sharp edges, and it is necessary
that the installer and service personnel exercise
caution.
The installation of this equipment shall be in accordance
with the regulations of authorities having jurisdiction and
all applicable codes.
This equipment is to be installed by an experienced
installation company and fully trained personnel.
The mechanical installation of the exhaust ventilator con-
sists of making final connections between the unit and
building services, duct connections.
Centrifugal Powered Roof & Wall Exhausters
Models ACX, ATB, ATBR, AWX, AWXR
Aerovent Bulletin 102 provides additional information on this equipment. These bulletins can be found at www.aerovent.
com or by contacting your local Aerovent sales representative.
General Installation, Operation and Maintenance Instructions For Aerovent Products
IM-115
June 1997
General Installation, Operation and Maintenance Instructions For Aerovent Products
IM-121
November 2006

2 Aerovent IM 121
Dimensions and Weights
SIZE FAN DIMENSIONS CANTED
CURB SIZE
DAMPER
SIZE
AVG. SHIP
WT. (LBS.)
A B C E
070/075
25.88 22.75 2.64 17.00 15.5 x 15.5 10 x 10 58
085 27.88 25.50 3.16 17.00 15.5 x 15.5 10 x 10 67
100 27.88 26.50 3.16 20.00 18.5 x 18.5 14 x 14 74
120 30.94 30.88 3.81 20.00 18.5 x 18.5 14 x 14 78
140 30.94 30.75 3.81 2400 22.5 x 22.5 18 x 18 90
160 33.81 32.75 4.00 26.00 24.5 x 24.5 20 x 20 107
180 39.56 37.75 5.00 30.00 28.5 x 28.5 24 x 24 130
210 39.56 37.75 5.00 30.00 28.5 x 28.5 24 x 24 160
240 43.00 35.88 4.83 34.00 32.5 x 32.5 28 x 28 220
300 52.00 39.38 4.83 40.00 38.5 x 38.5 34 x 34 270
360 61.50 45.88 6.83 46.00 44.5 x 44.5 40 x 40 360
420 65.75 49.13 8.25 52.00 50.5 x 50.5 46 x 46 420
480 74.00 51.63 9.00 58.00 56.5 x 56.5 50 x 50 475
Model ACX
ROOF OPENING
(DAMPER SIZE + 0.50 INCHES)
CURB SIZE CURB
DAMPER
2.50"
B
C
E SQUARE
A DIA.
MODEL DAMPER CANTED SELF FLASH ROOF
ATB ATBR SIZE CURB SIZE CURB SIZE OPENING
110 110 18 x 18 221⁄2 x 221⁄2 231⁄2 x 231⁄2 181⁄2 x 181⁄2
120 120 18 x 18 221⁄2 x 221⁄2 231⁄2 x 231⁄2 181⁄2 x 181⁄2
140 140 18 x 18 221⁄2 x 221⁄2 231⁄2 x 231⁄2 181⁄2 x 181⁄2
160 160 18 x 18 221⁄2 x 221⁄2 231⁄2 x 231⁄2 181⁄2 x 181⁄2
180 180 24 x 24 281⁄2 x 281⁄2 291⁄2 x 291⁄2 241⁄2 x 241⁄2
210 210 28 x 28 321⁄2 x 321⁄2 331⁄2 x 331⁄2 281⁄2 x 281⁄2
240 240 28 x 28 321⁄2 x 321⁄2 331⁄2 x 331⁄2 281⁄2 x 281⁄2
300 300 34 x 34 381⁄2 x 381⁄2 391⁄2 x 391⁄2 341⁄2 x 341⁄2
360 360 40 x 40 441⁄2 x 441⁄2 451⁄2 x 451⁄2 401⁄2 x 401⁄2
420 — 46 x 46 501⁄2 x 501⁄2 511⁄2 x 511⁄2 461⁄2 x 461⁄2
480 — 50 x 50 561⁄2 x 561⁄2 571⁄2 x 571⁄2 501⁄2 x 501⁄2
MODEL A B C E AVG. UNIT
ATB ATBR WT. (LB.)
110 110 31.00 30.00 28.00 24.00 96
120 120 31.00 30.00 28.00 24.00 99
140 140 31.00 32.00 28.00 24.00 110
160 160 31.00 35.00 28.00 24.00 116
180 180 37.00 37.00 30.00 30.00 139
210 210 46.00 38.00 28.25 34.00 157
240 240 46.00 39.00 28.25 34.00 169
300 300 55.00 40.00 31.00 40.00 266
360 360 64.00 46.00 34.00 46.00 391
420 — 70.00 49.00 36.00 52.00 478
480 — 76.00 52.00 39.00 58.00 523
Models ATB/ATBR
ROOF OPENING
(DAMPER SIZE + 0.50 INCHES)
DAMPER
CURB
2.50
B
E SQUARE
CURB SIZE
A DIA.
C
Note: Self-flashing roof curbs are to be sized 1" larger than canted
curbs.
Notes:
1. Self-flashing, vented restaurant curbs are sized the same as canted
curbs (for use with hinge).
2. Dampers are not to be used with restaurant fans.

Aerovent IM 121 3
Dimensions and Weights
Models AWX/AWXR
MOUNTING BRACKET
HOLE MOUNTING PATTERN
5/16" ANCHOR
STUD (8)
6.78 6.78
D
SQUARE
A DIA.
B
2.50
MOUNTING
BRACKET
E
SQUARE
WALL
OPENING
H
4.00 STD
& 10.00
W/DAMPER
WALL
C
F
MODEL A B C D E F AVG. UNIT DAMPER WALL MTG. WALL
AWX AWXR WT. (LB.) SIZE BRACKET OPENING (H)
110 110 31.00 30.00 28.00 25.56 24.00 12.00 135 17 x 17 233⁄4 x 233⁄4 171⁄2 x 171⁄2
120 120 31.00 30.00 28.00 25.56 24.00 12.00 135 17 x 17 233⁄4 x 233⁄4 171⁄2 x 171⁄2
140 140 31.00 32.00 28.00 25.56 24.00 12.00 145 17 x 17 233⁄4 x 233⁄4 171⁄2 x 171⁄2
160 160 31.00 35.00 28.00 25.56 24.00 12.00 180 17 x 17 233⁄4 x 233⁄4 171⁄2 x 171⁄2
180 180 37.00 37.00 30.00 31.56 30.00 18.00 180 24 x 24 293⁄4 x 293⁄4 241⁄2 x 241⁄2
210 210 46.00 38.00 28.25 35.56 34.00 22.00 245 27 x 27 333⁄4 x 333⁄4 271⁄2 x 271⁄2
240 240 46.00 39.00 28.25 35.56 34.00 22.00 245 27 x 27 333⁄4 x 333⁄4 271⁄2 x 271⁄2
300 300 55.00 40.00 31.00 41.56 40.00 28.00 365 33 x 33 393⁄4 x 393⁄4 331⁄2 x 331⁄2

4 Aerovent IM 121
Roof Fan Installation
1. Position the fan with its wiring conduit in line with
the wiring coming up through the roof curb and
damper (if present). If the fan has an external dis-
connect switch (standard on restaurant units), posi-
tion the fan with the junction box towards the power
supply.
2. Run wires through the conduit to the switch. Leave
some slack in the wire in the motor compartment
so the motor and wheel assembly can be lifted for
inspection and cleaning.
3. Bolt the fan base to the roof curb through the holes
provided on the base using eight (8) lag bolts.
4. Make connection to the disconnect switch per
above electrical instructions.
5. Restaurant fan installation must be in compliance
with local codes and the National Fire Protection
Association’s NFPA-96.
Wall Fan Installation
1. Your wall fan is shipped with a wall mounting brack-
et. Refer to the wall fan dimensional drawing on
page 3 for mounting hole locations. Consideration
should be taken when choosing wall fan location
with regard to other buildings, parking lots, etc.
2. After drilling pilot holes, bolt the wall mounting
bracket to the wall through the holes provided on
the bracket flange using eight (8) lag bolts.
3. Position fan with the motor compartment breather
tube facing downward.
4. Run wires through conduit to switch. Leave some
slack in the wire in the motor compartment so that
the motor and wheel assembly can be lifted for
inspection and cleaning. If fan has an external dis-
connect switch (standard on restaurant units) bring
power to switch.
5. Bolt the fan base to the wall bracket using hardware
provided.
6. Make connection to the disconnect switch per
above electrical instructions.
7. Restaurant fan installation must be in compliance
with local codes and the National Fire Protection
Association’s NFPA-96.
Electrical Connection
1. Connect supply wiring to the disconnect switch
(non-fused standard). Check the wiring diagrams on
the motor for connections.
2. The motor is factory set at the voltage marked on
the fan nameplate. Check the line voltage with the
nameplate voltage and wiring diagrams.
3. The main power wiring should be sized for the
ampacity shown on the dataplate. Size wires in
accordance with the ampacity tables in Article 310
of the National Electrical Code. If long wires are
required, it may be necessary to increase wire size
to prevent excessive voltage drop. Wires should be
sized for a maximum of 3% voltage drop.
CAUTION: Use copper conductors only.
CAUTION: Protect wiring from sharp edges. Leave
some slack in the line to prevent damage.
4. Disconnect switches are not fused. The power leads
must be protected at the point of distribution in
accordance with the fan dataplate.
5. On fans without a thermal protector integral to the
motor (refer to unit or motor dataplate to determine
if protector is present) a separate overload device
is required. Refer to Sections 430-32 of the N.E.C.
for sizing.
6. All units must be electrically grounded in accordance
with local codes or, in the absence of local codes,
with the latest edition of the National Electrical
Code (ANSI/NFPA 70). A ground lug is provided as
standard in the unit terminal box. Size grounding
conductor in accordance with Table 250-95 of the
National Electrical Code. DO NOT use the ground
lug for connecting a neutral conductor.
7. Supply voltage to the power ventilator should not
vary by more than 10% of the value indicated
on the unit dataplate. Phase unbalance must not
exceed 2%.
WARNING: Failure of motor due to operation on
improper line voltage or with excessive phase unbal-
ance constitutes product abuse and may cause
severe damage to the unit’s electrical components.

Aerovent IM 121 5
Table 2. Wheel to Inlet Venturi
MODEL GAP OVERLAP
ACX 070/075 --- 0.25
ACX* --- 0.50
ATB/ATBR/AWX/AWXR 0.06 ---
*all sizes except 070 and 075.
Check, Test & Start Procedure
WARNING
Electric shock hazard. Could cause severe injury or
death. Failure to bond the frame of this equipment
to the building electrical ground by use of the
grounding terminal provided or other acceptable
means may result in electrical shock. Disconnect
electric power before servicing equipment. Service
to be performed only by qualified personnel.
BEFORE START-UP: Disconnect power to this unit
before servicing the unit.
1. Check to verify that the wheel is free to rotate.
2. For optimum fan performance make sure that the
wheel to inlet venturi gap or overlap is maintainted.
See Table 2.
3. Verify that supply voltage on the line side of discon-
nect agrees with voltage on fan data plate and is
within the 10% utilization voltage.
4. Apply power to unit and check rotation of wheel with
the directional arrow on the unit. See Table 1.
WARNING: Rotation is critical. If allowed to operate
in the wrong direction, the motor will overload and
burn out.
WARNING: Especially check three-phase units for
rotation. For three-phase, rotation can be changed by
interchanging any two of the three line leads. If unit is
checked on temporary wiring, it should be rechecked
when permanently installed. Motor burn-out or tripped
overload protection devices are usually the result of
wrong rotation.
5. Electrical Input Check: Perform check of fan ampere
draw and verify that motor nameplate amps are not
exceeded. Take into account the service factor range
if motor is nameplated above a 1.0 service factor.
6. Fan RPM should be checked and verified with a
tachometer.
7. Units with Speed Control (Direct Drive): Verify that
speed controller gives desired operating range of
RPM. If minimum speed value is not desired, it may
be adjusted. See page 6.
NOTE: The fan should not need balancing, as it was
balanced at the factory to be within stringent vibration
levels before shipment. However, there are several
things that may cause vibration, such as rough han-
dling in shipment and installation, weak foundations
and alignments.
Table 1. Wheel Rotation*
MODEL CW CCW
ACX all other 070, 075
ATB/ATBR/AWX/AWXR all other 160, 180
* Wheel rotation is determined when viewed from top of fan
(opposite air intake).
Note: On fans with three phase motors the wheel rotation can
be changed by reversing any two power leads.
Figure 1. Fan Wheel Rotation - View from Exhaust End
W
H
E
E
L
R
O
T
A
T
I
O
N
CURB
BASE
FAN
WHEEL
HOUSING
Note: CCW rotation shown, CW rotation is similar but opposite.

6 Aerovent IM 121
Figure 4. Eliminate Slack Figure 5. Belt Deflection
Figure 6. Mounting Belts Figure 7. Sheaves
Figure 8. Belts
Deflection
Deflection = Belt Span
64
Belt Span
Slack belts wear excessively, cause slippage
and deliver less power. For longest belt life,
always provide proper tension
Mount belts straight. Shafts must be parallel
and sheaves in alignment to prevent unnec-
essary belt wear.
Two-groove variable pitch
sheaves must be opened the
same number of turns on
both sides; otherwise, slip-
page occurs, wearing belts
rapidly,
Do not force belt. Forcing the belt will
break the cords and cause belt failure.
V-Belts
V-belts on these belt driven fans are oil, heat, and static
resistant type and oversized for continuous duty. With
proper installation and maintenance, years of operating
efficiency can be added to the lifespan of the V-belt
drive.
The condition of V-belts and the amount of belt ten-
sion should be checked prior to start-up (see Figure
4). When it becomes necessary to adjust belt tension,
do not over-tension as bearing damage will occur.
Recommended belt tension should permit 1⁄64" deflection
per inch of span of the belt at the center of the belt
span. To find this point, measure halfway between the
pulley centerlines as shown in Figure 5. Extreme care
must be exercised when adjusting V-belts as not to mis-
align the pulleys. Any misalignment will cause a sharp
reduction in belt life and will also produce squeaky,
annoying noises (see Figure 6). On units equipped with 2
groove pulleys, adjustments must be made so that there
is equal tension on all belts (see Figure 7).
1. Where tensioning rods are not provided, adjustment is
more easily obtained by loosening and adjusting one
side of the motor bracket at a time.
2. Always loosen tension adjustment enough to place
belts on sheaves without running belts over the edge
of either sheave. A new belt may be seriously dam-
aged internally by careless handling (see Figure 8).
WARNING: When removing or installing belts, never force
belts over pulleys without loosening motor first to relieve
belt tension. The fan has been checked for mechanical
noises at the factory prior to shipment. If mechanical
noise should develop, then some suggestions are offered
here as a guide toward remedying the cause.
1. Check rotating members for adequate clearance.
2. Check proper belt tension and pulley alignment.
3. Check installation and anchoring.
4. Check fan bearings.
CORRECT
INCORRECT

Aerovent IM 121 7
Fan Troubleshooting Chart
PROBLEM POSSIBLE CAUSES
FAN DOES NOT OPERATE 1. Wrong voltage.
2. Electricity turned off or not wired properly.
3. Tripped overload protector.
4. Blown fuses.
5. Loose pulleys.
6. Broken belts.
TOO LITTLE AIR 1. Wheel rotating in wrong direction.
2. Fan speed lower than design.
3. System is more restrictive (more static pressure) than expected.
4. Restricted fan inlet or outlet.
5. Inlet or outlet screens clogged.
6. Filters (if applicable) are dirty or clogged.
TOO MUCH AIR 1. Fan speed higher than design.
2. System is less restrictive (less static pressure) than expected.
EXCESSIVE HORSEPOWER 1. Wheel rotating in wrong direction.
2. Wheel rubbing on inlet venturi.
3. Fan speed higher than design.
4. Worn fan bearings.
EXCESSIVE NOISE 1. Wheel or sheaves loose.
2. Bearing or drive misalignment.
3. Accumulation of material on wheel.
4. Worn or corroded wheel.
5. Wheel out of balance.
6. Wheel hitting housing.
7. Bent shaft.
8. Bearings need lubrication.
9. Loose bearing bolts.
10. Loose or worn bearings.
11. Mismatched belts.
12. Belts too loose or too tight.
13. Belts oily or dirty.
14. Belts worn.
15. Loose fan mounting bolts.
16. Rattle of components in high velocity airstream.
17. Electrical noise.
18. Noise from high velocity air system.
19. Vibrating parts not isolated from building.
20. Vibrating ductwork.
EXCESSIVE VIBRATION 1. Wheel or sheaves loose on shaft.
2. Wheel out of balance.
3. Excessive buildup of dirt/dust on wheel.
4. Belts too loose or too tight.
5. Mismatched belts.
6. Bent shaft.
7. Bearing or drive misalignment.
8. Loose or worn bearings.
9. Fan mounting bolts loose.
10. Weak mounting base for fan.
11. Structures not cross-braced (wall fans).
12. Curb not flat and level.
It is recommended that the users and installers of this shipment familiarize themselves with AMCA Publication #201,
“Fans and Systems” and publication #202, “Troubleshooting” which are published by the Air Movement and Control
Association (AMCA), 30 West University Drive, Arlington Heights, Illinois 60004. www.amca.org

8 Aerovent IM 121
Maintenance
Installation and maintenance are to be performed only
by qualified personnel who are familiar with local codes
and regulations and experienced with this type of equip-
ment.
CAUTION: Sharp edges and screws are a potential injury
hazard. Avoid them.
WARNING
Hazardous moving parts. Unit may contain pro-
tected fan motor which may start automatically
and cause injury. Allow time for reset. Disconnect
power before servicing.
Preventive maintenance is the best way to avoid unnec-
essary expense and inconvenience. Routine maintenance
should cover the following items:
a. Tighten all setscrews, bolts and wire connections.
b. Check belt tension and sheaves for wear.
c. Lubricate fan bearings (see Tables 5 and 6).
d. Cleaning of unit, wheel and damper (if present).
All motors containing ball bearings are permanently
lubricated from the factory. No additional maintenance
is required.
1. Before performing any maintenance on the fan, be
sure power is turned off and locked in the OFF
position at the service entrance.
2. Ventilators should be carefully checked at least once
a year. For critical or rugged applications, a routine
check every two or three months is suggested.
3. All motors supplied with Aerovent ventilators carry
a one-year limited warranty from date of shipment.
For repairs within the warranty period, the motor
must be taken to the motor manufacturer’s autho-
rized service dealer. Contact your representative for
additional warranty details.
4. A periodic motor check should consist of spinning
the motor shaft with the power off to be sure the
motor turns freely and the bearings run smoothly.
The belt on belt driven units should be removed
from the motor sheave.
5. When removing or installing a belt, do not force
the belt over the sheave. Loosen the motor mount
so that the belt can be easily slipped over the
sheave.
6. The belt on belt driven units should be removed and
carefully checked for glazing, cracks, ply separation
or irregular wear. A small irregularity in the contact
surface of the belt will result in noisy operation. If
any of these defects are apparent, the belt should
be replaced. Check the sheaves also for chipping,
dents or rough surfaces which could damage the
belt.
7. The correct belt tension is important. Too tight of
a belt will result in excess bearing pressure on the
motor bearings and shaft pillow blocks and may
also overload the motor. Too loose of a belt will
result in slippage which will quickly “burn” out belts.
A belt should feel “live” when thumped, approxi-
mately 1⁄4" belt deflection (3 to 5 lb.) when subject
to finger pressure at midpoint between sheaves.
8. The belt alignment should also be checked to be
sure the belt is running perpendicularly to the rotat-
ing shafts. Fan and motor shafts must be paral-
lel. Improper alignment will result in excessive belt
wear.
9. Check sheave setscrews to ensure tightness. Proper
keys must be in keyways.
10. Do not readjust fan RPM. If sheaves are replaced,
use only sheaves of identical size and type.
11. If unit is to be left idle for an extended period, it is
recommended that belts be removed and stored in
a cool, dry place to avoid premature belt failure.
12. The standard pillow block bearings on belt driven
ventilators are factory lubricated and are provided with
external grease fittings. Lubrication annually is recom-
mended, or more frequently if needed (see Table 5).
Do not over-grease. Use only 1 or 2 shots of
a recommended lubricant with a hand gun in most
cases (see Table 6). Maximum hand gun rating 40
P.S.I. Rotate bearings during lubrication where good
safety practice permits.
CAUTION: Greases of different soap bases
(lithium, sodium, etc.) may not be compatible when
mixed. Prevent such intermixing by completely purg-
ing the bearing of old greases.
The most frequent causes of bearing failure are
not greasing often enough, using an excessive
quantity of grease, or using incompatible greases.
Excessive vibration, especially if the bearing is not
rotating, will also cause bearings to fail. Bearings
must also be protected from water and moisture to
avoid internal corrosion.
13. During the first few months of operation it is rec-
ommended that the bearing setscrews be checked
periodically to ensure that they are tight.
14. The rotating wheel requires particular attention since
materials in the air being handled can build up on
the blades to cause destructive vibration or weaken
the structure of the wheel by corroding and/or erod-
ing the blade metal. Regular inspection and correc-
tive action at intervals determined by the severity of
each application are essential to good service life
and safety.
INTERVAL TYPE OF SERVICE
(MONTHS)
12 to 18 Infrequent operation or light duty in clean atmosphere.
6 to 12 8 to 16 hrs./day in clean, relatively dry atmosphere.
3 to 6 12 to 24 hrs./day, heavy duty, or if moisture is present.
1 to 3 Heavy duty in dirty, dusty locations; high ambient
temperatures; moisture laden atmosphere; vibration.
Table 5. Suggested Fan Bearing Greasing Intervals
MANUFACTURER GREASE (NLGI #2)
U.S. Electric Motors Grease No. 83343
Chevron U.S.A. Inc. Chevron SRI Grease #2
Mobil Oil Corporation Mobilith
Texaco, Inc. Premium BRB #2
Amoco Oil Co. Rykon Premium #2
Table 6. Grease Manufacturers

Aerovent IM 121 9
Motor Lubrication
Motors which contain ball bearings are permanently
lubricated from the factory. No additional maintenance
is required.
Motors which contain sleeve bearings require lubrication
every six (6) months. Use SAE-20W lubricant and add
five (5) drops to each location shown in Figure 9. DO
NOT OVER LUBRICATE.
OIL TUBES
Figure 9. Sleeve Bearing Motor Oil Tube Location
Storage
If fans are stored for any length of time, they should
be stored in a clean, dry location to prevent rust and
corrosion. Outdoor storage is not recommended. When
outdoor storage is necessary, fans should be protected
from the elements as completely as possible. Cover the
fan inlet and outlet and keep motors dry and clean.
For extended storage (more than 3 months) motor shafts
and bearings should be rotated monthly. If stored longer
than 6 months, bearing grease in motor and fan should
be purged and replaced with compatible grease. Belts
should be rechecked for proper tension. Storage records
should be kept to assure proper maintenance. The fac-
tory can advise warranty centers to provide motor and
bearing service if needed.

10 Aerovent IM 121
Seller warrants to the original purchaser that the goods
sold hereunder shall be free from defects in workman-
ship and material under normal use and service (except
in those cases where the materials are supplied by the
buyer) for a period of one year from the date of original
installation or eighteen (18) months from the date of
shipment, whichever occurs first. The liability of seller
under this warranty is limited to replacing, repairing, or
issuing credit (at cost, F.O.B. factory and at seller’s
discretion) for any part or parts which are returned by
buyer during such period provided that:
a. seller is notified in writing within ten (10) days fol-
lowing discovery of such defects by buyer, or within
ten (10) days after such defects should reasonably
have been discovered, whichever is less;
b. the defective unit is returned to seller, transportation
charges prepaid by buyer.
c. payment in full has been received by seller or said
products; and
d. seller’s examination of such unit shall disclose to its
satisfaction that such defects have not been caused
by misuse, neglect, improper installation, repair,
alteration, act of God, or accident.
No warranty made hereunder shall extend to any seller
product whose serial number is altered, effaced or
removed. Seller makes no warranty, express or implied,
with respect to motors, switches, controls, or other
components of seller’s product, where such components
are warranted separately by their respective manufac-
turers. THIS WARRANTY IS EXPRESSLY IN LIEU OF
ALL OTHER WARRANTIES, EXPRESS OR IMPLIED,
WHETHER STATUTORY OR OTHERWISE, INCLUDING
ANY IMPLIED WARRANTY OF MERCHANTABILITY OR
FITNESS FOR A PARTICULAR PURPOSE. In no event
shall seller be liable to buyer for indirect, inciden-
tal collateral, or consequential damages of any kind.
(BUYER’S FAILURE TO PAY THE FULL AMOUNT DUE
WITHIN SIXTY (60) DAYS OF DATE OF INVOICE SHALL
OPERATE TO RELEASE SELLER FROM ANY AND ALL
LIABILITY OR OBLIGATION ARISING PURSUANT TO
ANY WARRANTY, EXPRESS OR IMPLIED, WHETHER
STATUTORY OR OTHERWISE, INCLUDING ANY IMPLIED
WARRANTY OR MERCHANTABILITY OR FITNESS FOR
A PARTICULAR PURPOSE, MADE IN CONNECTION
WITH ANY CONTRACT FORMED HEREUNDER. BUYER
AGREES THAT SUCH FAILURE TO PAY SHALL
CONSTITUTE A VOLUNTARY WAIVER OF ANY AND ALL
SUCH WARRANTIES ARISING PURSUANT TO SUCH
CONTACT.)
Limitation of Warranties and Claims

Aerovent IM 121 11

TM
®
This manual suits for next models
54
Table of contents
Other Aerovent Fan manuals
Popular Fan manuals by other brands
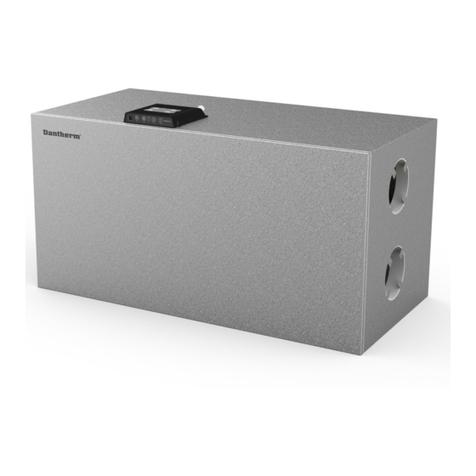
Dantherm
Dantherm HCH 5 MKII manual

Fanco
Fanco Infinity-ID DC installation manual

Hunter
Hunter 90436 owner's guide
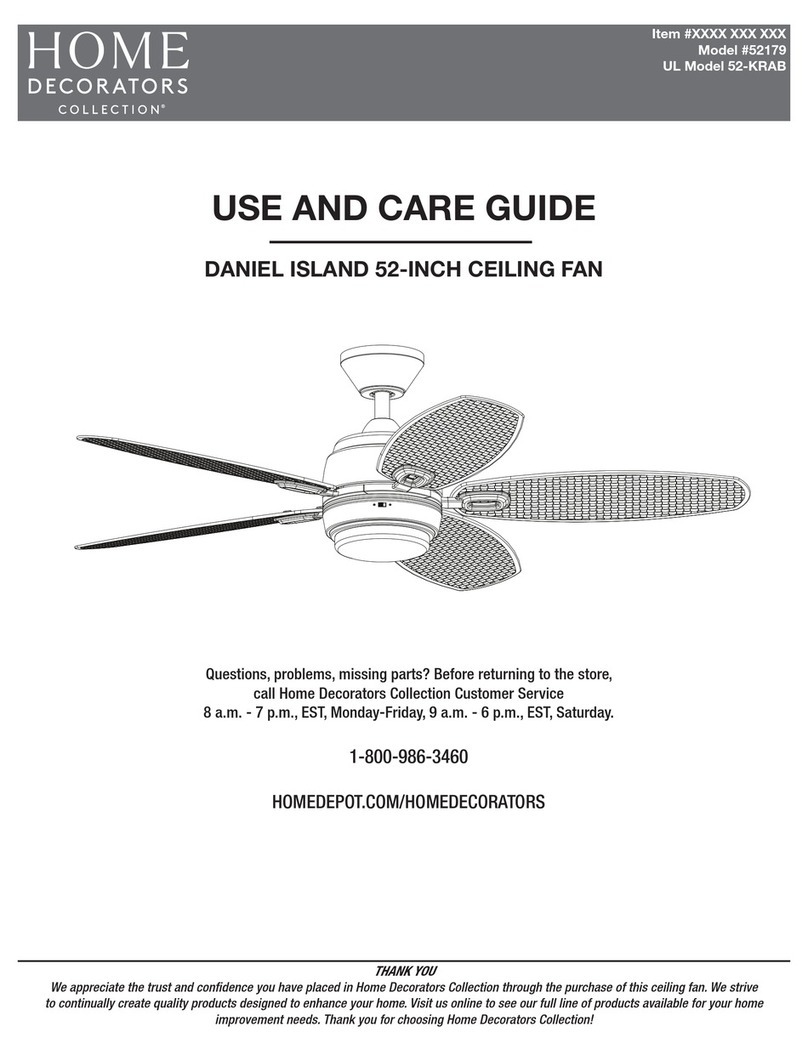
Home Decorators Collection
Home Decorators Collection DANIEL 52179 Use and care guide
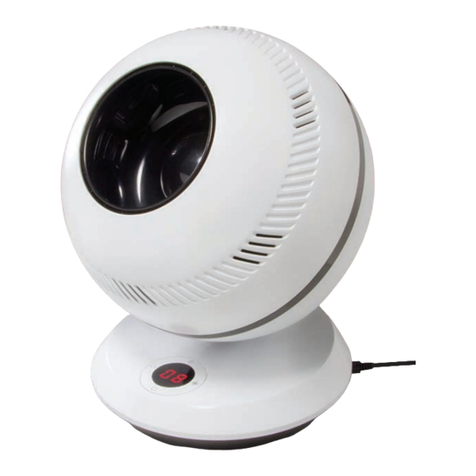
GreenTech
GreenTech pureFlow QT7 owner's manual
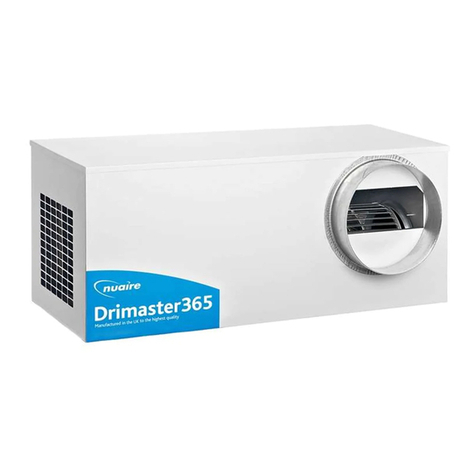
NuAire
NuAire DRIMASTER 365 Installation and Maintenance Details