aikron Mini LCD User manual

Driven by Innovation
Mini LCD
DIGITAL READOUTS
Operation Manual
(Version 2.0)

Softkey Indication
ABS
INC
MM
INCH
SDM
1/2
+COMP.
45°
x
Y
a
z
ABS/INC Conversion
Metric/Imperial
Conversion
SDM Coordinate
Value Half
Set
Enter
Exit
Radius/Diameter
Conversion
Axis Summing
System Parameter
Setting
Taper Measuring
Grid Hole Function
Bolt Hole Function
Vectoring Function
EDM Function
Sleep
REF Function
Compensation
Softkey Indication

ZERO ZERO ZERO
C
ENT
Value Zero Button
Function Button
Return
Button
Direction Button
Enter Button
Keypad Layout
Keypad Layout

Content
Content
1.1 DRO Setting 1
1.2 Axis Setting 2
1.3 Axis Summing 3
1.4 Data Clear 3
1.5 Keypad Test 4
1.6 RPM Setting 4
1. System Parameter Setting
2. Fundamental Function
2.1 Zero,Value Recovery 6
2.2 Imperial and Metric Conversion 6
2.3 Coordinate Inputting 6
2.4 1/2 Function 6
2.5 ABS and INC Conversion 6
2.6 Power-off Memory 7
2.7 REF Function 7
2.8 100 sets of SDM Coordinates 9
2.9 Compensation Function 10
3. Special Function
3.1 Grid Hole Function 15
3.2 Bolt Hole Function 16
3.3 Radius and Diameter Conversion 17
3.4 Vectoring Function 17
3.5 Taper Measuring Function 18
3.6 EDM Function 19
4. Appendix
4.1 Parameter 21
4.2 Dimension 22
4.3 Troubleshooting 23

1.1 DRO Setting
DRO setting includes:
·Machine Type
·Number of Axis
·Decimal digits under inch mode
·Value Recovery
·Brightness
·Background
·Dynamic Displaying
·Language
·Buzzer
. Machine Type:
Press set button to switch.(Milling,Lathe,Grinder,EDM)
2. Number of Axis:
Press set button to set the number of axis to be displayed.
3. Decimal Digits:
Press set button to set the decimal digits under inch mode.
. Value Recovery:
Press set button to enable or disable value recovery.
5. Brightness:
Press set button to adjust the brightness of the screen.
. Background:
Press set button to switch background.(Day or Night)
. Buzzer:
Press set button to enable or disable the buzzer.
. Dynamic Display:
Press set button to switch the dynamic displaying.(Dynamic Preposition
or OFF)
. Language:
Press set button to switch the language.
Page 1
1. System Parameter Setting
DRO Setting
Axis Setting
Axis Summing
Data Claer
Keypad Test
Brightness
Milling
3
5
ON
20
Machine
NO. of Axis
Decimal
Value Recovery

1.2 Axis Setting
Axis setting includes:
·Axis Selection
·Encoder Selection
·Resolution Setting
·Direction Setting
·Thread Pitch
·Decimal Digits
·Port Mapping
1. Axis Selection:
Press set button to switch the axis which shall be set.
2. Encoder Selection:
Press set button to switch the encoder type for the corresponding axis.
·Linear Scale:Connect linear scale to measure the linear length.
·1-Rotary Encod:Connect with rotary encoder to measure the degree,
displaying as degree.
·2-Rotary Encod:Connect with rotary encoder to measure the degree,
displaying as degree/minute/second
·3-Rotary Encod:Connect with rotary encoder,basing the thread pitch,
to measure the linear length.
3. Resolution Setting:
·When the encoder type has been set as linear scale.Here we could switch
the resolution to the target one.
(Range:0.1,0.2,0.5,1.0,2.0,2.5,5.0,10,20,25,50,100μm)
·When the encoder type has been set as 1-Rotary Encod,2-Rotary
Encod,3-Rotary Encod,press numerical button and set button to
input the corresponding resolution.
. Direction Setting:
Press set button to set.
(0 indicates positive direction,1 indicates negative direction)
Page 2
Thread Pitch
X
Linear Scale
5.0
0
NA
Axis
Encoder
Resolution
Direction
1. System Parameter Setting

5. Decimal Digits:
Press set utton to set the ecimal igits uner metric moe.
6. Port Mapping:
Press set utton to change the alue isplaying on another axis
For examplewhen the encoer has een connecte with axis
portyou coul set here to isplay the alue on axis.
1.3 Axis Summing
Axis summing inclues:
·Axis Selection
·Summing Selection
·Switch ON or OFF
1. Axis Selection:
Press set utton to switch the axis which shall e set.
2. Axis Summing:
Press set utton to select the axis which shall e summe.
3. Switch ON or OFF:
Press set utton to enale or isale.
1.4 Data Clear
Data clear inclues:
·SDM Clear
·Factory Reset
1. SDM Clear:
Clear all memorie SDM coorinates.
2. Factory Reset:
Clear all ata memorie in DRO.
Page 3
1. System Parameter Setting
NA
OFF
Axis
Axis Summing
Switch
SDM Clear
Factory Reset
ersion:2.

Operation:
eetteiteanpreteetttoneOireiniitiarrot
teataearretenitioorataearreOteOi
itearin
1.5 Keypad Test
Operation:
Oneentertintionreteeaniattontotetitore
tentettononreenianeooritetproetettonon
reenireainitotane
1.6 RPM Setting (Optional)
eenororteoeaenororrotarenoer
ettinine:
·ipa
·enoreetion
·ettinorreotionorotar
enoerorneroanet
·eeteroaterear
·eeteroinion
Page 4
tarttetet
ipa O
enor aenor
Ooanet
eetO
eetO
1. System Parameter Setting

1. RPM Display:
Press set button to enable or isable the RPM isplayin.
2. Sensor Selection:
Press set button to sitch the sensor.all Sensor or Rotary ncoer
hen the sensor has been set as rotary encoerpress numeric an set
button to input the resolution.hen the sensor has been set as hall
sensorpress numeric to input the number of manets.
3. Teeth Number of Master Gear:
Press numeric to input the ear number.
4. Teeth Number of Pinion:
Press numeric to input the ear number.
Page 5
1. System Parameter Setting

2.1 Zero,Value Recovery
·Zero
ressing the zero button,operator could zero the value on windows.
·Value Recovery
When the value displayed on windows has been zeroed wrongly,
press zero button again could get back the former value.
Note: When the zero function has been switched off in DRO Setting,the value
could not be get back.
2.2 Imperial and Metric Conversion
ress the MM/INCH button to switch the displaying under imperial or metric
unit.
2.3 Coordinate Inputting
ress the ais button,and press the numeric button to input the value.Once
input,press ENT to confirm.
2.4 2 Function
ress the ais button and 1/2 button to half the value for corresponding ais.
2.5 ABS and INC Conversion
he DRO gets two sets of standard coordinate system,namely ABSAbsolute
and INC Relative Coordinate.ser could set the zero point of workpiece in ABS
coordinate,then switch to INC coordinate for machining.Zeroing at any position
in INC coordinate would not affect the length value from zero point to current
point in ABS coordinate.he process in ABS would change according to the
machining status.ser could switch the coordinate back to ABS for checking.
ress ABSINC button to switch.
Page 6
2. Fundamental Function

2.6 Power-off Memory
n ce of uen ower off urin te mcinin rocete R et te
t memorie function.nce te ower onte te efore ower off wi
recoer utomticy.
2.7 REF Function
n iy mcininoertor my encounter ower fiure.f oin te ero
oint of te wor-iecewe e to retriee te ero oint in.For te
conenience to retriee te ero ointte R cou memorie te mecnic
ero reference oint of iner ce.i ene te uer to retriee te ero
oint of wor-iece uicy.
Note: o ue te REF functionwe nee to et te mecnic ero reference
oint of iner ce in R.n ti wyte R cou memorie te ero oint
of wor-iece.For te foowin eroincentre n ue inut for re-octe te
ero oint of wor-iece uner moete R wi memorie te itnce
etween new ero oint of wor-iece n mecnic ero reference oint of
iner ce.nce te mecnic reference oint of iner ce een et
weoertor cou retriee te ero oint of wor-iece ery uicy.
Page 7
2. Fundamental Function
wor-iece
Mecnic ero reference
oint of iner ce iner ce
ero oint of wor-iece cemtic irm
e note ti itnce.urn on te R to fin te
mecnic reference oint of iner ceten we
cou ccute out te reet ero reference oint
of wor-iece.

While DRO is powered on,press the
REF function button.In the function
interface,select the target item for
parameter setting by pressing up and
down direction button.
·Axis
Press set button to select the corresponding axis for setting.
·Function
press set button to switch the function to set the reference point or find
reference point.
Set the Reference Point Steps
Step Press the set button to select the axis which shall be set.
Step Press down direction button to switch to function setting,and press
set button to set the function to find the reference point.Press ENT
button to enter next interface,then traverse the linear scale to find
the reference point.Once the point has been found,the DRO will
remind with the messages of found the reference point.At this
moment,the reference point setting of this axis is completed.
Retrieve the Zero Point of Work-piece
Step Take note of X,Y and Z axis under ABS model once the DRO
self-checking process completed.
Step Enter the REF function,select the axis which shall be set,then press
down direction button for function setting.Set the function to find the
reference point.Then press the ENT button to enter the finding
interface.Traverse the linear scale.Once the reference point has been
found.The DRO will remind with the message of found of reference
point. At this moment,the reference point of this axis has been found
successfully.
Page 8
2. Fundamental Function
Axis
Function
X
Set Ref. Point
REF Function

Page 9
2. Fundamental Function
Step 3: raerse te linear scale of tis ais to e te ale ic e too
note.At tis tietis point is te one e stopped for last acinin.
ote: nl operator as set te reference point for eac ais efore
acinin
ten te ero point of orpiece cold e et ac.
2.8 100 sets of SDM Coordinates
D proides AS and C coordinate.t soeties it is not eno for
dail acinin.is D proides 100 rops of SDM ailiar coordinate to
copensate te sortae of AS and C fnction.t SDM is not st a siple
additional C coordinate.e elo is te difference eteen ASC and
SDM.
·C is copletel independent.o atter o ero point in AS caned
te ero point in C ill not cane.t te ero point of SDM is asin
on AS.en te ero point in AS canedall coordinate in SDM ill
cane accordinl.
·e distance eteen SDM and AS coordinate cold e inpt directl.
Applications for SDM Coordinates:
perator cold eorie te acinin points of orpiece in SDM
coordinates.ress p or don direction tton to sitc.
ero point of orpiece
nder AS ode.
SDM1
SDM2
SDM3
SDM

Page 10
2. Fundamental Function
SDM application during medium or small batch machining:
SDM unction could memorie a batch o oring point.ser could input these
oring points hen machining the irst orpiece.hen adust the ero point
in S mode or machining the olloing orpieces.he SDM coordinate is
basing the ero point in S mode.
hen the D is under SDM modelpress SDM button to input the SDM
coordinateor press up and don direction button to sitch the coordinate.
raerse the linear scale until the alue on each ais become .t this moment
this point is the machining point.
2.9 Compensation Function
Compensation unction enable operator input the linear compensation
nonlinear and baclash compensation alue to improe the machining
accurac.
ress compensation unction button to enter the interace.
ress the up or don direction button to select the item or setting.
SDM SDM
SDM2
SDM
S
ero point o
orpiece .
is
Compensation Function
Comp.pe linear
aclash
ctual ength .

Page 11
2. Fundamental Function
1. Linear Compensation
·Axis:
Select the axis for setting.
·Comp. Type:
Select the compensation type(Linear or Non-linear)
·Backlash:
Only the encoder type has een set as -Rotary ncodthere could e set.
·Actual Length:
ress numeric utton to input the actual moving length of tale.This
length value is getting from more accurate measuring instrument than
linear scale.
·Comp. Value:
ress numeric utton to input the compensation value.
Note: Formula for compensated value:
Compensation Value =
(Actual length-DRO Displayed length) / (Actual Length/1000) mm/m
Compensation range: -1.9mm/m to +1.9mm/m
Take axis as an example (same operation to other axis)
ove the tale of axis direction for 1000.000mm of actual moving length.
The displayed value on DRO is 999.0mm.
The calculation of compensation value is like the elo:
Compensation Value=(1000.000-999.0)/(1000.000/1000.000)=0.120
Step 1: Confirm the starting point
ero the value of axispress the CO utton to enter the function.
Then set the axis to e .
Step 2: Select the compensation type
ress don direction utton to sitch the compensation type setting
and select it as Linear Compensation.

Axis X
Compensation Function
Comp.Type Non-linear
Backlash NA
Comp.Segment 0
Page 12
2. Fundamental Function
Step 3 Input the compensation value
Move the table of X axis direction to be exact 1000mm(basing other
more accurate measuring instrument).Then press the up or down
direction button to select the actual measuring length,and input 1000.
Or select the compensation value to input 0.120.
Note hen selecting to input the actual measuring length.e need ero the
value of corresponding axis first.Otherwise the compensation value will be
calculated wrongly.
2. Non-linear compensation
·Axis
Select the axis for setting.
·Comp. Type
Select the compensation type(Linear or Non-linear)
·Backlash
Only the encoder type has been set as 3-Rotary Encod,there could be set.
·Comp. Segment
Press the numeric button to input the compensation segments.The
maximum could be 100.
·Comp. Length
Press numeric button to input the actual length of every segment.This
length should be get from more accurate measuring instrument.
·Start Point
Press set button to select
the start point.
(Endpoint or mechanical
reference point of linear scale)

Page 13
2. Fundamental Function
Non-linear compensation function takes the mechanical reference point or
endpoint of linear scale as the starting point.The DRO will compensate the
displayed value according the input err list.Please note Linear compensation
and Non-linear compensation function could not be used at the same time.
The DRO gets two ways for non-linear compensation.
1. Take the linear scale end point as the starting point for compensation.
(Figure 1)
2. Take the first mechanical zero reference point of linear scale as the
starting point for compensation.(Figure 2)
Take X axis setting as an example(same operation to other axis)
Step 1 Press the COMP. Button to enter the compensation function,and select
the axis as X.
Step 2 Select the compensation type to be Non-linear.
Step Input the Compensation segments as 6.
Step Input the compensation length for every segment as 10.000
Step Select the starting point as the endpoint of linear scale.
And press ENT to go for next .
Step 6 Move the table of X axis direction to one of the endpoint,and press
ENT to confirm the point.(When the start point has been set as
mechanical reference point of linear scale,once the point has been
captured,the DRO will enter next step automatically).
0 10 20 30 40 50 10 20 30 40 50
(Figure 1) (Figure 2)
L
L1
L
L2
L1
Mechanical zero reference
point of linear scale

Page 14
2. Fundamental Function
Step 7: sing other more accurate measuring instruments as reference to
moe the table to be the alue as input in compensation length which
is .,and press EN to confirm.
Step 8: Repeat the operation of step 7 to complete all segments.Once the
compensation finished,the RO will eit compensation automatically.
Note: When the start point has been set as endpoint,the data in REF function
will be cleared.Only the start point has been set as mechanical reference
point,the REF and non-linear compensation could be used together.
3. Backlash Compensation
his setting could be set with the condition of encoder has been set 3-Rotary
Encod.ress the numeric button to input the compensation alue.

3.1 Grid Hole Function
This function is for drilling equal hole on vertical and horizontal direction.Once
operator input the required parameter,the DRO will calculate the position of
each hole,and set the coordinate of each hole to be (0.000,0.000).Operator
could move the table to the target position for machining the hole.
There are two ways for grid hole function:
1. Length way:Input the total length of the line
2. Step way:Input the length between two holes
Press the grid hole function button to enter the interface.
Press up and down direction button to select the parameter for setting.
·Drawing No.: DRO could memorize 4 sets of drawing.
Press set button to switch.
·Plane: Select the plane for machining.2 axis DRO only gets XY plane.
For DRO with 3 or more axis,it could be switch among XY,XZ,YZ.
·Mode A: Press set button to set the mode to be Length or Step way for
horizontal direction.
·Length A: Press set button to input the length of horizontal direction.
Page 15
3. Special Function
Drawing No. 1
Grid Hole Function
Plane XY
Mode A Length Way
Length A 0.000

·No. Of Holes A: ess set utton to nut the hole nue of
hoontal deton.
·Mode B: ess set utton to set the ode to e Length o te a fo
etal deton.
·Length B: ess set utton to nut the length of etal deton.
·No. Of Holes B: ess set utton to nut the hole nue of etal
deton.
·Rotate Angle: ess set utton to nut the otated angle of dang.
One the aaete has een setess ENT to ente the ahnng ntefae.
ess ght o left utton to sth the hole.
3.2 Bolt Hole Function
hs funton s fo dllng equal hole on a le.One oeato nut the
equed aaetethe RO ll alulate the oston of eah holeand set
the oodnate of eah hole to e 0.0000.000.Oeato ould oe the tale
to the taget oston fo ahnng the hole.
hee ae 3 as fo olt hole funton.
1. 360°Equal: llng equal holes on a le.
2. Equal Angle: llng holes th sae angle eteen to holes.
3. Rand. Angle: llng equal holes on an ando angle.
ess olt hole funton utton to
ente the ntefae.
ess u and don deton utton
to selet the aaete fo settng.
Page 16
3. Special Function
ang No. 1
Bolt Hole unton
lane
ente 0.000
0.000 ente
Table of contents
Popular Measuring Instrument manuals by other brands
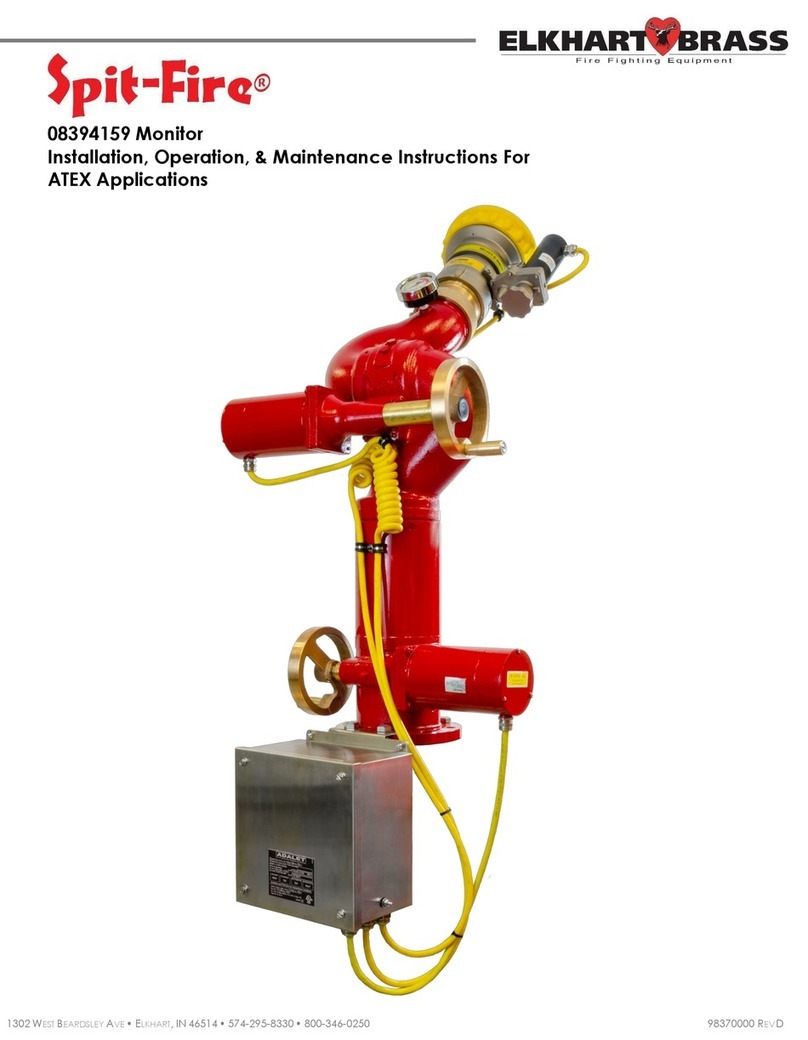
ELKHART BRASS
ELKHART BRASS Spit-Fire 08394159 Installation, operation & maintenance instructions
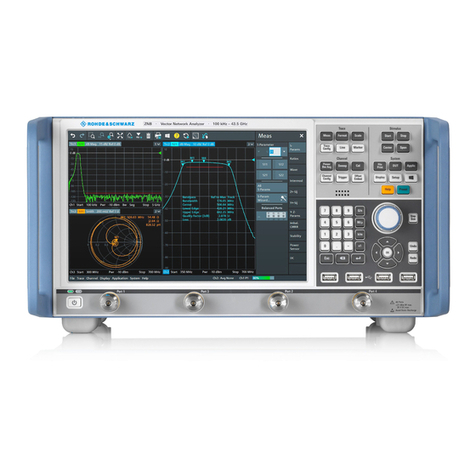
R&S
R&S ZNB Series user manual

F.W. Bell
F.W. Bell 8000 series instruction manual
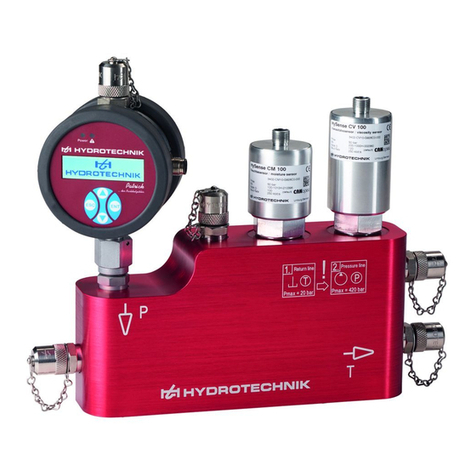
Hydrotechnik
Hydrotechnik HySense CX 197 operating instructions

Teledyne
Teledyne TIENet 360 LaserFlow Ex Installation and operation guide
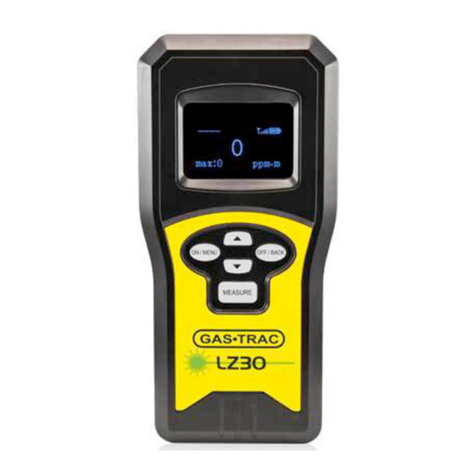
SENSIT Technologies
SENSIT Technologies GAS-TRAC LZ-30 Quick start instructions