Air TEc RE-46 User manual

PPROFINET fieldbus instructions
Valve Terminal RE-46 PROFINET
Additional fieldbus instructions to the
user manual RE-46
Version: 12/20
Art.-No.: 54-RE-46-EN-PN
STATUS:
ENTWURF
FREIGABEEXEM
P.
FREIG
EGEBE
N
KUNDE:
AIRTEC INTERN
JLE/KH
RT
PROJEKT-
NR. 2390-08-
AS5
ERSTELLER: JLE
DATUM:
16.03.2007
VERSI
ON:
06
BESCHREIB
UNG:
DATENBLATT RE-10 BUSSYSTEME UND AIR-LINK SYSTEM
BEMERKUN
GEN:
ZUR FREIGABE DURCH DEN KUNDEN . TECHN. ÄNDERUNG
VORBEHALTEN!
STATUS:
ENTWURF
FREIGABEEXEM
P.
FREIG
EGEBE
N
KUNDE:
AIRTEC INTERN
JLE/KH
RT
PROJEKT-
NR. 2390-08-
AS5
ERSTELLER: JLE
DATUM:
16.03.2007
VERSI
ON:
06
BESCHREIB
UNG:
DATENBLATT RE-10 BUSSYSTEME UND AIR-LINK SYSTEM
BEMERKUN
GEN:
ZUR FREIGABE DURCH DEN KUNDEN . TECHN. ÄNDERUNG
VORBEHALTEN!
STATUS:
ENTWURF
FREIGABEEXEM
P.
FREIG
EGEBE
N
KUNDE:
AIRTEC INTERN
JLE/KH
RT
PROJEKT-
NR. 2390-08-
AS5
ERSTELLER: JLE
DATUM:
16.03.2007
VERSI
ON:
06
BESCHREIB
UNG:
DATENBLATT RE-10 BUSSYSTEME UND AIR-LINK SYSTEM
BEMERKUN
GEN:
ZUR FREIGABE DURCH DEN KUNDEN . TECHN. ÄNDERUNG
VORBEHALTEN!
STATUS:
ENTWURF
FREIGABEEXEM
P.
FREIG
EGEBE
N
KUNDE:
AIRTEC INTERN
JLE/KH
RT
PROJEKT-
NR. 2390-08-
AS5
ERSTELLER: JLE
DATUM:
16.03.2007
VERSI
ON:
06
BESCHREIB
UNG:
DATENBLATT RE-10 BUSSYSTEME UND AIR-LINK SYSTEM
BEMERKUN
GEN:
ZUR FREIGABE DURCH DEN KUNDEN . TECHN. ÄNDERUNG
VORBEHALTEN!

2
Content
1. General __________________________________________________ 5
2. Electrical data_____________________________________________ 7
3. Connections and elements of the RE-46 PROFINET _____________ 8
3.1 Connections of the RE-46 PROFINET (Front view)..........................8
3.2 Indicators and elements of the RE-46 PROFINET (top view)........10
3.3 Indictator LEDs fieldbus status (PROFINET)..................................11
3.3.1 Inicator LEDs for Link & Activity Status (P1 L/A & P2 L/A).......12
3.3.2 Indicator LEDs for module status (MD OK & MD ERR)............12
3.3.3 Indicator LEDs for PROFINET Status (FB OK & FB ERR).......12
3.4 Arrangement of valves + solenoids ................................................13
3.5 Controlling the valves by a PLC or IPC ..........................................14
4. Installation of the RE-46 CANopen___________________________ 15
4.1 IP protection code ............................................................................15
4.1.4 IP protection code against dust (first digit)...............................15
4.1.5 IP protection code against water (second digit) .......................15
4.2 POWER cable....................................................................................16
4.3 PROFINET cables .............................................................................17
4.5 Fieldbus topology.............................................................................18
4.5.1 Structure of the fieldbus...........................................................18
4.5.2 EMC-Considerations................................................................19
5. Commissioning the RE-46 PROFINET ________________________ 20
5.1 Electrical connections......................................................................20
5.2 Commissioning the PROFINET Controller .....................................22
5.3 Commissioning the PROFINET-Device...........................................26
5.4 Trouble shooting ..............................................................................39
6Contact and support _________________________________________ 40

3
Used abbreviations and their explanations
API .................................................................................Application Process Identifier
Byte wise .....................................................Data is handled as units of 1 byte (8 bits)
Controller............................................................................................PROFINET Master
DAP .....................................................................................................Data Access Point
Device ................................................................................................... PROFINET Slave
EMC................................................................................... electromagnetic compliance
FB .................................................................................................................... Fieldbus
GSDML-File ........................................General Station Description File (XML-Format)
HF ............................................................................................................. Hi frequency
IPC ..............................................................................................................Industrial PC
I/O ......................................................................................................Input/Output Data
LED ..................................................................................................Light emitting diode
LSB ................................................................................Least significant bit (of a byte)
MSB.................................................................................Most significant bit (of a byte)
Offline ................................................................... No data exchange between devices
Online.....................................................Data exchange between devices established
PLC ....................................................................................Programmable logic control
Valve station............................................................................ Slot for a solenoid valve
Revision 00 29.03.18 Author: JLE
Revision 01 09.12.20 Author: MBR
Subject to change without notice in the course of
technical improvement.

4
Used depictions in these instructions
Normal text Normal text
Text + bold face Emphasis
Text + bold face + italics Proper names
Hyperlinks Reference to other text areas
ADVICE/HINT:
Text….
Advices in a green box do not have any safety-relevant importance. The background colour
is just a help to find important information easier.
ADVICE:
Text…..
Advices in a yellow box have a low safety-relevant importance, but disobeying these ad-
vices may lead to damages at the valve terminal or its periphery.
WARNING:
Text….
Warnings in a red box have a high safety-relevant importance. Disobeying these warnings
may lead to serious damages of the valve terminal, its periphery or even harm human be-
ings.
Text
Text in a red frame is any other important information like formulas etc.

5
1. General
The pneumatical data and the mounting of the RE-46 PROFINET are identical to the RE-
46 Multipin version.
WARNING:
For installation and commissioning of the pneumatic part of the valve ter-
minal, please read the “Instructions for use Valve terminal RE-46”
(Article-No. 54-RE-46-GB)
Please consider the safety hints in this user manual
HINT:
These instructions are to be considered as a supplement to the standard user
manual for the RE-46. They describe especially the bus specific settings and
methods for PROFINET fieldbus system.
HINT:
The device description file (GSDML) can be found at: www.airtec.de

6

7
2. Electrical data
RE-46 PROFINET
Parameter
Value
Valve Stations
6, 8, 10, 12 ... 24
Fieldbus connectors
2 x M12 5-pin female D-coded
Power connector
M12 5-pin male A-coded
Power consumption (each sole-
noid)
1 W (solenoid) plus 0,3 W for the status LED
Power consumption of the
fieldbus system
2,9 W at 24 V DC
Address setting
DHCP / manually by DCP-Protocol
Voltage
DC 24 V ±10%
Total current
No valves activated: approx. 120 mA
Valves activated: depending on the numer acti
vated valves
Bitrate
100 Mbit/s (Fast-Ethernet)
Status indicators at the fieldbus
system
24V_1 (LED Green)
24V_2 (LED Green)
24V_3 (LED Green)
P1 L/A (LED Green)
P2 L/A (LED Green)
MD OK (LED Green)
MD ERR (LED Red)
FB OK (LED Green)
FB ERR (LED Red)
Status indicators at the valves
14/12 (LED Yellow) solenoid active

8
3. Connections and elements of the RE-46 PROFINET
3.1 Connections of the RE-46 PROFINET (Front view)
1 Flange header M12 5-pin A-coded (POWER)
Pin
Designation
Description
1
+24V
Supply voltage for bus electronics
Fuse: 1A slow blow
2
+24V_1
Supply voltage for valves 1-12 (solenoids1-24)1
Fuse: 3,15A slow blow
3
GND
Ground for +24V, +24V_1, +24V_2
4
GND
Ground for +24V, +24V_1, +24V_2
5
+24V_2
Supply voltage for valves 13-24 (solenoids 25-48)2
Fuse: 3,15A slow blow
2 + 3 Flange receptacle M12 4-pin D-coded (PROFINET Port 1 + Port 2)
Pin
Designation
Description
1
TD+
Transmit Data +
2
RD+
Receive Data +
3
TD-
Transmit Data -
4
RD-
Receive Data -
1
This pin should be powered always. Otherwise the solenoids will not work.
2
This pin has to be powered if the valve terminal has more than 12 valve stations. Otherwise it is not necessary to apply
power.
1
2
3
6
4
7
5
8
9

9
HINTS:
For the installation of the PROFINET network use PROFINET compliant cable links
only!
Detailed information can be read at the following site:
http://www.profibus.com/ (Cabling and Interconnection Technology / Order No.: 2.252)
4 Compressed air supply for all valves (connection 1)
5 Grounding connection (PE) at the valve terminal. After mechanical installation,
connect a grounding strap to the grounding screw at the left front side of the
valve terminal. This screw is marked with a ground symbol. Connect the other
end of the strap to a well grounded metal conductor.
6 Air outlet (connection 2)
7 Air outlet (connection 4)
8 Connection for external control air (connection E1). This connection is normally
sealed with a plug. Control air is drawn from connection 1. For special operating
conditions (pressure level below 3 bars), the control air can be supplied here
9 Connection for secondary compressed air supply (connection 1 right side). This
connection is normally sealed with a plug.
Secondary air supply has to be connected, if the valve terminal has an internal
pressure zone splitting (option) or if very high air flow rates are required. (see
chapter 8.4 in "Instructions for use Valve terminal RE-46")

10
3.2 Indicators and elements of the RE-46 PROFINET (top view)
10 Cover:
This cover normally can be removed to set manually the fieldbus address of the
RE-46. For PROFINET no manual address setting is required! Anyway this cover
may not be removed to guarantee IP65 protection code.
11 Indicator LEDs bus status (PROFINET):
These LEDs signalize the status of the bus system and the valve terminal. De-
tailed description see chapter 3.3
12 Indicator LEDs valves:
LED 14 on: valve is in position 14, i. e. air flows from connection 1 to
connection 4
LED 12 on: valve is in position 12, i. e. air flows from connection 1 to
connection 2
The number of LEDs and the designation can vary for each valve type. For pneu-
matical function of the valve see printed symbol on the front side of the valve.
LEDs off: valve is in idle position
13 Air outlet 82
At this connection the control air for the solenoids is exhausted (connection 82).
To reduce the noise for exhausting air use a silencer or connect a tube.
14 Air outlet 3
At this connection the compressed air of the valves is exhausted (connection 3).
To reduce the noise for exhausting air use a silencer.
15 Air outlet 5
At this connection the compressed air of the valves is exhausted (connection 5).
To reduce the noise for exhausting air use a silencer.
16 Air outlet 84
At this connection the control air for the solenoids is exhausted (connection 84).
To reduce the noise for exhausting air use a silencer or connect a tube.
10
12
11
16
15
14
13

11
3.3 Indicator LEDs fieldbus status (PROFINET)
These indicator LEDs can be found on the left top side of the RE-46
Indicator LEDs (PROFINET):
Designation
Color
Description
24V_1
green
Supply voltage LED
+24V for fieldbus electronics
24V_2
green
Supply voltage LED
+24V for valve station 1-12
24V_3
green
Supply voltage LED
+24V for valve station 13-24
P1 L/A
green
Port 1 Link/Activity
Shows the link status of Port 1
(see Table 3.3.1)
P2 L/A
green
Port 2 Link/Activity
Shows the link status of Port 2
(see Table 3.3.1)
MD OK
green
Module OK
Shows the status of fieldbus module
(see Table 3.3.2)
MD ERR
red
Module ERROR
Shows the status of the fieldbus module
(see Table 3.3.2)
FB OK
green
Fieldbus OK
Shows the status of PROFINET
(see Table 3.3.3)
FB ERR
red
Fieldbus ERROR
Shows the status of PROFINET
(see Table 3.3.3)

12
3.3.1 Indicator LEDs for Link & Activity Status (P1 L/A & P2 L/A)
3.3.2 Indicator LEDs for module status (MD OK & MD ERR)
3.3.3 Indicator LEDs for PROFINET Status (FB OK & FB ERR)

13
3.4 Arrangement of valves + solenoids
The following drawing shows the arrangement of valves + solenoids:
Station:
Slot for a monostable, bistable or center position valve. Depending on the valve
type, either one or two solenoids can be present.
Monostable 5/2-way valves have only one solenoid on the top position. (odd
numbers, solenoid 1, 3, 5,.. and so on).
3/2-way-, bistable and center position valves have two solenoids on top and
bottom position (solenoid 1+2, 3+4,... and so on).
Numbering of the solenoids starts top left and ends right bottom (see figure above).
The „14“ on the label in the middle of the valve means, that air is flowing from
connection 1to connection 4when activated.
Group:
A group consists of 4 stations (valves) or 8 solenoids. The groups are numbered
from left to right. Each group is linked with one byte output data (8 bits) of the PLC,
i.e. output byte 1 controls group 1, output byte 2 controls group 2 and so on.
HINT:
For valve types with one solenoid (odd numbers), the second solenoid is not present.
Therefore the output bits with straight numbers have no effect, they are "don't care".
Solenoid 1
Solenoid 2
Solenoid 39
39
Solenoid 40
40
Station 1
Station 20
20
Group 1
Group 2
Group 3
Group n
Group n +1

14
3.5 Controlling the valves by a PLC or IPC
In the table below you will find the assignment of bits and bytes of the output data
to the valves / solenoids:
Group
1 (output byte 1)
2 (output byte 2)
3 (output byte 3)
Station
1
2
3
4
5
6
7
8
9
10
11
12
Solenoid
No. (top)
1
3
5
7
9
11
13
15
17
19
21
23
Value bin.
20
22
24
26
20
22
24
26
20
22
24
26
Value
dec.
1
4
16
64
1
4
16
64
1
4
16
64
Solenoid
No. (bot-
tom)
2
4
6
8
10
12
14
16
18
20
22
24
Value bin.
21
23
25
27
21
23
25
27
21
23
25
27
Value
dec.
2
8
32
128
2
8
32
128
2
8
32
128
Table: Assignment of output bytes 1-3 to the valves / solenoids, shown at a 12
station valve terminal
Significance:
Each output byte controls 8 solenoids, where the least significant bit (LSB) is as-
signed to solenoid 1, the most significant bit (MSB) is assigned to solenoid 8.
The following rules apply:
1= 24V on = solenoid active (active position of the valve)
0= 24V off = solenoid inactive (idle position of the valve)
Example for 1 byte output data (all even solenoids on):
27
26
25
24
23
22
21
20
1
0
1
0
1
0
1
0
MSB
LSB
Sole-
noid
8
Sole-
noid
7
Sole-
noid
6
Sole-
noid
5
Sole-
noid
4
Sole-
noid
3
Sole-
noid
2
Sole-
noid
1
WARNING:
When using 5/2-way pulse valves or 5/3-way with center position, make sure that
only one of the two solenoids is activated at the same time, i.e. the „odd“ or the
„even“ solenoid. If both solenoids are activated simultaneously, the valve posi-
tion is undetermined!

15
4. Installation of the RE-46 CANopen
4.1 IP protection code
The IP protection code determines the protection class against dust (first digit) and
liquids (second digit).
IP65 can only be achieved if all air connections are plugged either with a tube or a
sealing plug. Connection cables must be plugged in also and should fulfill at least
the same protection code (IP65 or higher).
AIRTEC offers ready-to-use standard cables in different lengths for this purpose
as accessories.
ADVICE:
When using cables of low quality or with reduced IP protection code the valve ter-
minal might be damaged by penetration of dust and/or liquids.
The AIRTEC warranty will be lost in this case.
4.1.4 IP protection code against dust (first digit)
4.1.5 IP protection code against water (second digit)
Digit
Protection against dust
6
no entrance of dust possible
Digit
Protection against water
5
Protection against hose water under any angle

16
4.2 POWER cable
Standard sensor cables with 5-pin circular female connector, M12 thread, A-
coded
Straight or angled connectors can be used
Diameter of each conductor strand min. 0,25mm² (AWG 24)
Cables can be shielded or not shielded. A shield is not absolutely necessary but
improves the EMC performance of the valve terminal.
When using shielded cables, both sides of the shield should be grounded. Do
not forget to connect a grounding strap to the grounding screw of the valve ter-
minal.
ATTENTION:
Current load per copper strand: max. 2.5 A @ 0,25mm² [AWG 24]
max. 3.4 A @ 0,34mm² [AWG 22]
IP protection code: IP65 or higher
Material of cable jacket: PUR or PVC. Resistant against environmental influ-
ences and chemicals (oil, detergents, temperatures, dust etc.)
For use in drag chains use special drag chain cables only. Consider the mini-
mum bending radius also.
Example of an M12 sensor cable (M12 female connector 5-pin and open wires)

17
4.3 PROFINET cables
For the PROFINET cables only the following cable types should be used:
PROFINET cable compliant to specifications of the PNO3F
3
with circular M12
4-pin connectors D-coded
Threaded or fast-lock
Straight or angled versions can be used (straight is recommended5)
The RE-46 has 2 PROFINET ports with an integrated Ethernet Switch (Fieldbus
cable can be looped from one to the next device)
Category 5 compliant to IEC 11801
Protection code IP65 or higher
Cable jacket PUR or PVC. Resistant against environmental influences and
chemicals (oil, detergents, temperatures, dust etc.)
For use in drag chains use special drag chain cables only. Consider the mini-
mum bending radius also.
Example for a typical PROFINET-Cable:
3
PNO. Infos under http://www.profibus.com/
5The use of straight versions simplyfies the cabling

18
4.5 Fieldbus topology
4.5.1 Structure of the fieldbus
The structure of the PROFINET network is flexible. All types of network structures
are supported (linear bus, star or ring structures).
For the use in a linear bus structure the PROFINET cable is looped from one to
the next device.
For the use in a star structure, the PROFINET cable is connected to Port 1. Port
2 is left open in this case. An additional PROFINET switch is required
For the use in a ring structure, the cable is looped from one to the next device,
but the last device will close the ring with a cable link to the first device. In this case
the controller and devices must have at least PROFINET conformance class B.
The cable link has a redundant path.
Con-
trol-
ler
De-
vice 1
De-
vice 2
De-
vice n
Con-
trol-
ler
De-
vice 1
De-
vice 2
De-
vice n
PROFINET
switch
De-
vice 2
De-
vice 1
Con-
trol-
ler
De-
vice n

19
WARNING:
Use certified PROFINET cable links only!
The maximum length of one cable link might not exceed 100m (328 feet)
Detailed planning & installation hints can be found here:
https://www.profibus.com/download/profinet-installation-guidelines/
4.5.2 EMC-Considerations
In industrial environment, the grounding and shielding of the cables and devices is
very important for safe operation.
Cable shields should be connected on both ends of the cable to a low impedance
drain. Devices should be grounded properly at their ground connections. If this is
disobeyed, the shielding and protection methods of the devices will not work cor-
rectly and the device might radiate electromagnetical interfering signals.
Detailed EMC recommendations can be found here
https://www.profibus.com/download/profinet-installation-guidelines/

20
5. Commissioning the RE-46 PROFINET
5.1 Electrical connections
Switch off the fieldbus segment where the RE-46 PROFINET should be installed.
Prepare the power cable (+24V DC) connection, but do not yet connect it!
1 POWER cable 24V
2 Fieldbus Port 1
3 Fieldbus Port 2
Connect the RE-46 PROFINET with your PROFINET fieldbus network (see chap-
ter 4.5.1).
This can either be doneby ready-to-use link cables (recommended) or if necessary
by the use of field mountable connectors and cables.
HINT:
When using field mountable connectors and cables, an electronic cable test
should be applied after the installation to make sure the cabling fulfills the Ether-
net standards and is free of connection failures.
When installing ready-to-use cables, this test is not required.
1
2
3
Table of contents
Popular Touch Terminal manuals by other brands
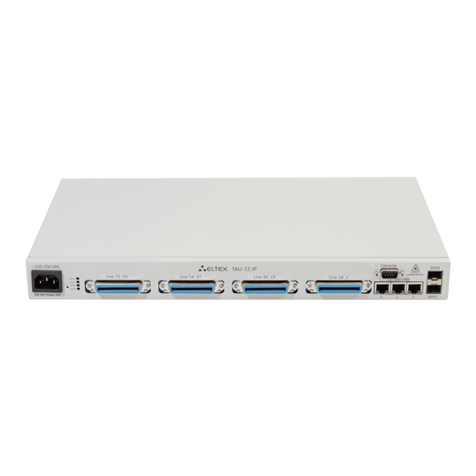
ELTEX
ELTEX TAU-36.IP Operation manual
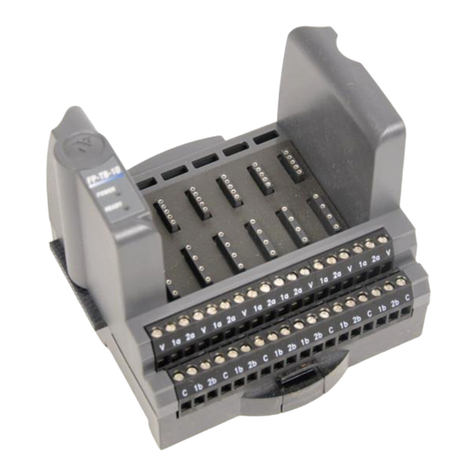
National Instruments
National Instruments FieldPoint FP-TB-10 operating instructions
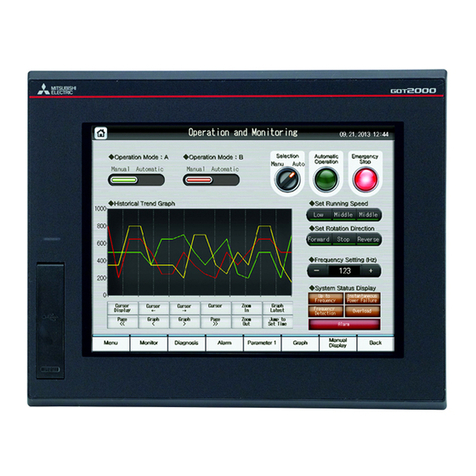
Mitsubishi Electric
Mitsubishi Electric GOT2000 Series Connection manual
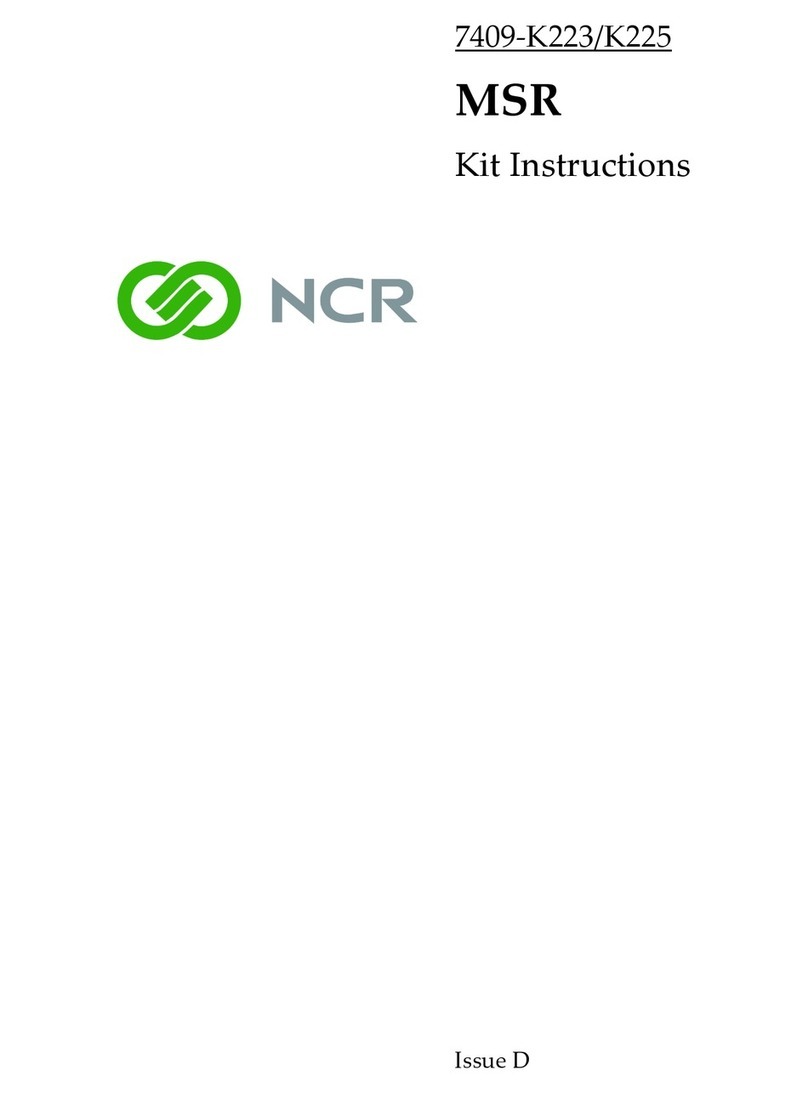
NCR
NCR 7409-K223 Kit instructions
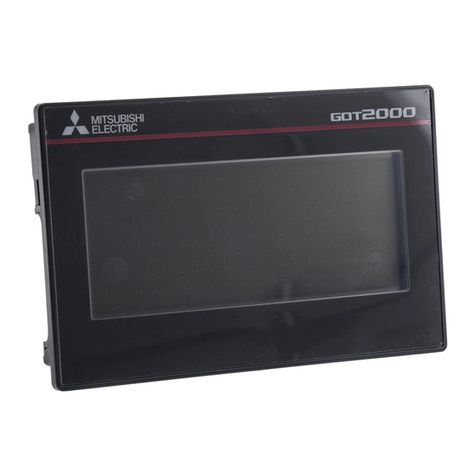
Mitsubishi Electric
Mitsubishi Electric GOT2000 Series user manual

Cattron
Cattron REMTRON 325 OCU quick start guide