Algodue ELETTRONICA UPT210 User manual

UPT210
UNIVERSAL POWER TRANSDUCER
USER MANUAL
1. INTRODUCTION
This manual provides information on the installation, configuration and use of the main instrument
functions.
The manual is not intended for general use, but for qualified technicians.
This term indicates a professional and skilled technician, authorised to act in accordance with the safety
standards relating to the dangers posed by electric current.
This person must also have basic first aid training and be in possession of suitable Personal Protective
Equipment.
WARNING!
It is strictly forbidden for anyone who does not fulfill the above-mentioned requirements
to install or use the instrument.
The instrument complies with the European Union directives in force, as well as with the technical standards
implementing these requirements, as certified by the CE mark on the device and on this Manual.
Using the meter for purposes other than intended ones, understood by the manual content, is strictly
forbidden. The information herein contained shall not be shared with third parties. Any duplication of this
manual, either partial or total, not authorised in writing by the Manufacturer and obtained by photocopying,
duplicating or using any other electronic means, violates the terms of copyright and is punishable by law.
Any brands quoted in the publication belong to the legitimate registered owners.
WARNING!
In case of 25A instrument version, pay attention as it is designed for direct connection
with 25A nominal current, without external CTs. CT ratio usually programmable in the
device is factory preset to 5 and FSA to 5A. Do not change these values.
NOTE. This manual describes the use of the main instrument functions.
1MAUXX210015

2
2. GRAPHIC SYMBOLS
Some instructions in the manual and on the device are highlighted by graphic symbols to draw the reader’s
attention to the operational dangers. The following graphic symbols are used:
DANGER!
This warning indicates the possible presence of voltage exceeding 1kV on the marked
terminals (even if for short periods).
WARNING!
This warning indicates the possible occurrence of an event which may cause a serious
accident or considerable damage to the device if suitable precautionary countermeasures
are not taken.
ATTENTION!
This warning indicates the possible occurrence of an event which may cause a light accident
or damage to the device if suitable precautionary countermeasures are not taken.
NOTE. This warning indicates important information which must be read carefully.
3. DESCRIPTION
UPT210 is a digital meter able to measure the electrical parameters on three-phase systems.
It provides accurate measurements even by distorted waveform.
LCD display provides the three-phase quantities. The working parameters can be easily set up by instrument
keypad.
UPT210 is a compact, cost effective meter operating both as a stand-alone device or as an integral part of
a more extensive energy monitoring and management network.
UPT210 replaces multiple analog meters as well as single function meters such as voltmeters, ammeters,
wattmeters, varmeters, frequency-meters, powerfactor-meters, energy-meters, etc.
4. PRELIMINARY VERIFICATION
NOTE. At the opening of the box, check that the instrument has not been damaged during
transport.
If the instrument appears to be damaged, contact the technical after-sales service.
The box contains:
the instrument•
the user manual•

3
5. INSTALLATION
NOTE. The equipment complies with the 89/366/EEC, 73/23/EEC standards and following
amendments. However, if not properly installed, it may generate a magnetic field and radio
interference. This is why compliance with EMC standards on electromagnetic compatibility
is essential.
5.1 ENVIRONMENTAL REQUIREMENTS
The environment in which the instrument is installed must satisfy the following features:
no vibrations•
indoor area•
operating temperature between -15°C and +60°C (+5°F and +140°F)•
storage temperature between -25°C and +75°C (-13°F and +167°F)•
max humidity 80% (no condensation)•
altitude up to 2000m•
NOTE. The instrument must not be exposed to sun rays.
5.2 MOUNTING
Fastening to DIN EN 50022-rail is provided for the instrument. To mount
it on the DIN-rail, you simply need to use a screw driver as a lever on
the plastic hook on the base of the instrument itself.
This operation will allow the instrument to fit on the rail.
6. SAFETY MEASURES
DANGER!
This warning means that a voltage exceeding 1kV (even if for short periods) may be
present on the terminals.
WARNING!
Electrical instrument connections must be carried out only by skilled technicians who
are aware of the risks involved to the presence of voltage. Before connecting, check the
following:
the conductor wires are not powered1.
the instrument is connected according to the appropriate diagram (see section 7.3)2.
the power supply corresponds to the values on the instrument label3.
the instrument has been installed in a vibration-free and a suitable temperature environment (see4.
section 5.1)
the terminals are no longer accessible after being connected5.
the wiring is carried out in accordance with the standards in force in the country where the instrument6.
is to be installed
an isolator and an over-current device (eg. fuse) are installed between the instrument power supply7.
and the electrical system
the connections are made respecting the polarities.8. Important: L1 of the voltage input = L1 of the
amperometric input
input and output polarities are respected when using current/voltage transformers9.
the connectors are fixed in such a way that they cannot be accidentally disconnected10.

4
3
5 6
1
PNP NPN
ACOM OUT1
BOUT1 OUT2
COUT2 COM
A B C + -
2
4
7. ELECTRICAL CONNECTIONS
The instrument must be installed according to the following order:
WARNING!
Before making any connection, check that the
control panel main switch is OFF.
Digital outputs. See section 7.21.
19÷60V2. d c power supply (option on request). See section 7.4
Serial port (option on request). See section 7.13.
FTT-10 port (LONBUS option on request)4.
Current inputs. See section 7.35.
Voltage inputs. See section 7.36.
7.1 SERIAL COMMUNICATION PORT (optional)
The serial port allows PC connection. The RS485 communication port is supplied.
7.1.1 RS485
The easiest and cheapest way to connect different measuring devices in a network is the RS485 serial line.
The RS485 standard interface allows a multi-point connection. Between PC and the network, it is required a
Serial RS232 to RS485 Converter. If more than 32 instruments are to be connected, insert a signal repeater.
Each repeater can manage up to 32 instruments. For the connection among the different modules, use a
cable with a twisted pair and a third wire. The type of connection shown in the following picture uses the
third conductor to ensure that all the devices on the network have the same reference level and improve
the reliability of communication. When there are strong electromagnetic disturbances, which may affect
communication, a shielded cable should be used. The Rt termination resistance must be installed on the
PC and the last instrument connected along the line. Thanks to these resistances, the reflected signal
along the line is reduced.
For a typical telephone pair, Rt can have values
from 120 to 150 Ohm.
NOTE. The value of each resistance must
notbelowerthan120Ohminordertoavoid
an overload of line drivers.
The max. recommended distance for a connection
is 1200 m at 9600 Baud. For longer distances,
lower baud rates or low-attenuation cables or
signal repeaters are needed.

5
7.2 DIGITAL OUTPUTS
The instrument is equipped with two digital outputs.
The digital outputs can be used for pulse emission.
WARNING!
Before connecting or disconnecting
the digital outputs, be sure that the
instrument is not powered. The power
supply line, the measurement inputs
and any other voltage source must be
disconnected.
7.2.1 Digital outputs connection
The digital outputs can be used, for example,
for pulse emissions. The needed function is
programmed through instrument setup.
Maximum withstandable voltage: 50 Vd c
Maximum load current: 100 mA
WARNING!
The outputs are not protected against
overloads and short-circuits.
WARNING!
On request, the unit is supplied with
the digital outputs for wiring A, B, C
or D. Refer to the label on the left side
of the meter in order to identify its
configuration.
7.3 VOLTAGE AND CURRENT INPUTS
Thebasicinstrumentisprovidedwithtwoselectable
wiring modes (3.4.3 and 1phase). On request, it is
also available the instrument provided with only
3.3.3 wiring mode (fixed).
WARNING!
Check:
if the instrument must carry out bi-directional measurements to obtain correct measurements, the1.
connections must respect the polarities
the connections are made according to the diagrams in the following section, respecting the cyclic2.
order of phases (important: L1 of the voltage input = L1 of the current input)
be sure to respect input and output polarities when using current transformers (CT)3.
before disconnecting current input the load power supply is cut off. If this is not possible, the secondary4.
CT must be short-circuited
A) PNP wiring (10-50V)
B) NPN wiring (10-50V)
C) PNP wiring (5-50V)
D) NPN wiring (5-50V)

6
WIRING DIAGRAM: 3 PHASES - 4 WIRES / 3 CURRENT TRANSFORMERS (3.4.3) connection
Pict. A: direct connection (3.4.3) Pict. B: direct connection (3.4.3) *
with serial communication port
WIRING DIAGRAM: 1 PHASE (1ph) connection
Pict. C: direct connection (1ph) Pict. D: direct connection (1ph) *
with serial communication port
WIRING DIAGRAM: 3 PHASES - 3 WIRES / 3 CURRENT TRANSFORMERS (3.3.3) connection (on request)
Pict. E: connection with VT (3.3.3) Pict. F: connection with VT (3.3.3) *
with serial communication port
WIRING DIAGRAM: 3 PHASES - 4 WIRES / 3 ROGOWSKI COILS (3.4.3) connection (on request)
Pict. G: direct connection (3.4.3) Pict. H: direct connection (3.4.3) *
with serial communication port
NOTE. In case of Rogowski coils, please check that YELLOW cable edge is connected to S1 (signal)
and the WHITE cable edge is connected to S2 (common).
* FN=100mAT T type - only with serial communication port

7
25A INSTRUMENT VERSION
WARNING!
Every wiring diagram must be provided with fuses (F1, F2, F3, FN) or another similar
protection as indicated in the picture. The F1/F2/F3 value will depend on the load. The FN
value is 100mA and it is required only when the instrument is provided with serial port.
WIRING DIAGRAM: 3 PHASES - 4 WIRES / 3 CURRENT TRANSFORMERS (3.4.3) connection
WIRING DIAGRAM: 1 PHASE (1ph) connection
WIRING DIAGRAM: 3 PHASES - 3 WIRES / 3 CURRENT TRANSFORMERS (3.3.3) connection (on request)

8
7.3.1 Voltage specifications
The standard meter is designed for measurements on 230/400 V 3-phase systems with neutral wire. Other
voltages and configurations are available on request.
Input impedance ›1,3 MOhm
Burden max 0,15 VA per phase
7.3.2 Current specifications
The phase and polarity of the current input is an essential parameter for proper parameters indication.
The standard current specifications are listed below:
Rated current (Ib) 1 / 5 Ar m s programmable
Min / Max measurable current 20mA / 7Ar m s
Maximum overload 10 Ar m s continuous - 100 Ar m s for 1 second
Input impedance 0,02 Ohm approximately
Burden max 0,5 VA per phase
Insulation voltage 480Va c max between phases
Rogowski coils input (optional) 200÷49995 A (according to the requested value-refer to the instrument label)
7.4 POWER SUPPLY
The instrument is directly powered from all the 3 phases. The standard measuring, counting and display
functions are guaranteed also by only one phase. The serial communication is interrupted if phase 1 (1 or
2 in case of 3-3-3 connection) fails, except for 19÷60Vd c external power supply (option, available only on
request). The installer must protect the instrument with an external fuse or other 100 mA delayed protection
device (only on phase 1 for instruments with serial communication port - see wiring diagrams Pict. B-D-F).
In case of 19÷60Vd c external power supply (option, available only on request), carry out the connections as
shown in the picture of the chapter "Electrical Connections".
WARNING!
Before connecting the instrument to the network, check the network voltage corresponds
to the value on the label. Any insertion of the power supply connector into the serial output
would seriously damage the instrument.

9
8. USE AND CONFIGURATION
NOTE. The pages described in this manual refer to the instrument for 3PHASES, 4WIRES,
3CTs connection. Some pages may differ or disappear if the wiring mode is different.
8.1 DISPLAYED PAGES
All displayed pages are structured in four loops:
loop 1: energy counters•
loop 2: instantaneous values (V, A, P, PF, ...),• symbol ON
loop 3: DMD and Peak values (optional),• symbol flashes
loop 4: S• ETUP, symbol ON
8.2 CONTROL PANEL DESCRIPTION
The instrument is equipped with a LCD display and with a keypad (2 keys). The keys functions are the following:
(UP key)
a) It scrolls all the available pages in the selected loop.
b) In programming (SETUP mode), it changes the value of the flashing figure (or group of figures). Keeping
it pressed, it scrolls automatically the figures.
c) Press and hold for at least 3 seconds, to enable/disable, on the current page, the Main Page [identified
by symbol ON].
(SHIFT / ENTER key)
a) Press once to select the desired loop.
b) Pressed and held for at least 3 seconds, it allows to display the Main Page previously programmed.
c) In programming (SETUP mode), it allows to access to the parameter to be changed. Pressing the SHIFT/
ENTER key, the first digit starts to flash and it can be modified.
+ (UP + SHIFT keys)
a) Pressed and held together for at least 3 seconds, allow to enter in SETUP mode.
8.3 INSTRUMENT SWITCHING ON
When it is powered, the instrument switches ON automatically. A first page with
the instrument name and a second page with the firmware release are shown in
sequence. Then, it is shown the latest page displayed before the switching OFF. After
two minutes, the Main Page is displayed (if it was previously set).
8.3.1 Symbols
Some symbols on the display give additional information. The number of displayed symbols depends on
the instrument configuration. A flashing symbol indicates diagnostic information.
Peak and demand information Measuring unit
kilo, Mega, Giga multiplier
Inductive load, capacitive
load, negative value or expor-
ted energy indication
Phase number, phase rotation, digital output status,
setup condition, alternate pages, Main Page

10
8.4 PRELIMINARY INSPECTIONS
At the end of the installation check that the setting corresponds to the wiring: enter the instrument setup
according to the content of next chapter and set the wiring diagram, the CT ratio and the PT ratio.
8.5 SETUP
8.5.1 Access to SETUP
It allows to configure the device to fit the application. From any displayed page, press
UP + SHIFT keys at the same time and hold for at least 3 seconds to enter the SETUP
mode.A passwordkeycombination willberequested; press UP key twice,then SHIFT
key twice and finally UP key twice again. Each SETUP page is identified by the symbol " ".
NOTE. The procedure must be done in less than 5 seconds.
To scroll the SETUP pages, press the UP key. The pages sequence is:
CT transformation ratio [Ct]
This page allows to set the ratio between the primary and secondary value of the
current transformer (CT) used on the system. The values are among 1 and 9999.
The default value is 0001 (Example: 1500A / 5 A = 0300). The display formats and
multiplying factors depend on the set CT value. The DO pulse weight set page is automatically updated
considering the new CT value, i.e. the pulse weight changes according to the new CT value (see diagnostic
functions, chapter 9, case 8). Set the value following section 8.5.2.
WARNING!
For 25A instrument version, CT ratio usually programmable in the device is factory preset
to 5. Do not change this value.
NOTE. CT value is factory preset in case of instruments with Rogowski inputs.
Current Fullscale [FSA]
This parameter allows to connect current transformers with 1 or 5 A secondary
value. Set the value following section 8.5.2.
WARNING!
For 25A instrument version, FSA value usually programmable in the device is factory
preset to 5A. Do not change this value.
NOTE. FSA page is not displayed in case of instruments with Rogowski inputs.
PT transformation ratio [Pt]
NOTE: The Pt setup page availability depends on the instrument model.
This page allows to set the ratio between the primary and secondary value of the
voltage transformer (PT) used on the system. The values are among 1 and 9999.
The default value is 0001 (Example: 20000V / 100V = 200). Check the instrument nominal voltage on the
external label for the correct setup of PT. Set the value following section 8.5.2.

11
Integration time [DMD]
NOTE: The Integration time page availability depends on the instrument model.
This page allows to set the integration time for demand values calculation. The
demand values are calculated only on positive values and in a programmed period
(e.g. 15'). At instrument reset, all demand values will be cleared. To set the integration time, insert one of
the following values: 01, 03, 05, 10, 15, 30, 60 minutes. Set the values following section 8.5.2.
Wiring mode [Wr]
This page allows to select the wiring mode. The available diagrams are:
3.4.3 = 3 phases, 4 wires, 3 CTs•
1ph = single phase•
Set the values following section 8.5.2.
NOTE. On request, the instrument can be provided with only the 3phases, 3wires, 3CTs wiring
mode.
Serial communication port [bAU/Addr] (optional)
Two pages allow to set the communication parameters. Set the values following section 8.5.2.
NOTE. On request, the instrument can be provided with only the LONBUS protocol. In this case,
after the Baud rate page, another page, showing "Lon", is displayed.
Baud rate page (bAU)
The set protocol and communication speed are displayed in this page. S, A or
r letter is shown next to the communication speed according to the protocol
type. The selectable protocols are:
A2 ASCII [• S] - data communication format fixed to 8-N-1
MODBUS ASCII [• A] - data communication format fixed to 7-E-1
MODBUS RTU [• r] - data communication format fixed to 8-N-1
The following communication speed values are available: 2400, 4800, 9600,
19200,38400, 57600 bps.In case of LONBUS protocol (availableonlyon request),
the communication speed is fixed at 78 kbps.
Logic address page (Addr)
The values are among $01÷$FF for A2 ASCII protocol and $01÷$F7 for MODBUS
protocol. This page is not available in case of LONBUS protocol.
Clear [CLr]
This page allows to clear the measured values. To reset the values, insert one of
the following code:
430=clear Energy counters•
330=clear DMD values (optional)•
980=clear all Peak and DMD Peak values (optional)•
981=clear DMD Peak values (optional)•
982=clear only Peak values (optional)•
Set the value following section 8.5.2
Digital outputs [OUT1/OUT2]
This page allows to set the digital output pulse weight and the relevant variable
(scroll the pages to display the OUT1 or OUT2 page).
Available variables (imported and on request exported energy):
Wh=active energy•
VAh=apparent energy•
varh=reactive energy (lagging and leading)•

12
In case of bidirectional values, option on request, exported energy variables can be selected for digital
output pulse weight setup.
The multiplying factor ([ ] none, [k] kilo, [M] mega) and the decimal point depend on the selected CT and
PT value. The pulse length is 100 ms. Set the values following section 8.5.2.
Example:
Selected values: Variable = Wh; pulse = 1000; multiplier = [k];
Digital output: 1kWh / pulse (active energy)
For further information on how to determine the pulse value, see section 8.5.3.
Firmware release [rEL]
This page shows the firmware release of the instrument.
Exit from SETUP [SAVE]
This page allows to quit the SETUP mode and to save the modifications.
There are three possibilities:
NO: quit without saving the modifications•
YES: quit saving the modifications•
CONT: remain in SETUP mode•
Set the value following section 8.5.2.
8.5.2 Modifying the values
The following procedure must be followed to set/modify the SETUP values.
From any SETUP page:
Press1. SHIFT key to enable the modification. The value or the first digit will start to flash.
Press2. UP key until the appropriate value is displayed.
Confirm the choice with3. SHIFT key. The value or the digit stops flashing.
Repeat point 2 and 3 for all the values/digits.4.
8.5.3 Considerations on the pulse value calculation
The maximum pulse re-emission rate is 1 pulse/sec (3600 pulse/h).
The minimum value assignable to the pulse to prevent the overlapping is:
emin = Pmax / 3600
Pmax is the maximum power on the measuring point controlled by the meter. The pulse value (emin) is
expressed in Wh, varh or VAh depending on the selected variable (P, Q or S).
Example 1
Pmax = 5MW
emin = 5000000/3600 = 1389 Wh/pulse (1.389 kW/p)
Example 2
Pmax = 800kW
emin = 800000/3600 = 222 Wh/pulse (0.222 kWh/p)
The result can be rounded off to a higher value for an easier calculation or totalization of the energy
consumption.
For example no. 1 it is possible to select 1.5 or 2 or 10 kWh/p.
For example no. 2 it is possible to select 0.5 or 1 kWh/p.
The pulse emission frequency will be proportionally lower.
Higher pulse weight = lower emission frequency.

13
9. DIAGNOSTIC FUNCTIONS
The diagnostic functions allow to check if there is any error in the instrument connections or one of the
measured voltage and/or current is out of range; the instrument can display some symbols with a specific
meaning. Hereafter the description of the available diagnosis:
N. Function Condition Display Description
1 Under Voltage VL-N ‹ 75% of nominal
value
See notes *, **, ***
The VL-N page, relating to the
out-of-range phase, displays
an error message as shown.
The 1,2,3 and V symbols are
flashing.
2 Over Voltage VL-N › 120% of nominal
value
See notes *, **
The VL-N page, relating to the
out-of-range phase, displays
an error message as shown.
The 1,2,3 and V symbols are
flashing.
3 Wrong phase order The phase sequence is
not 1-2-3. The symbol " " flashes.
4 Wrong current
wiring (inverted
current sense)
NOTE: the error is
displayed only in case of
monodirectional type.
In case of bidirectional
instrument, "-" sign is
displayed before the
values.
The phase current page,
relating to the out-of-range
phase, displays an error
message as shown. The 1,2,3
and A symbols are flashing.
5 Over current A › 120% of fullscale The phase current page, rela-
tingtotheout-of-rangephase,
displays an error message
as shown. The 1,2,3 and A
symbols are flashing.
6 Frequency out of
range
65 Hz ‹ f ‹ 45 Hz The frequency page displays
an error message as shown.
The 1,2,3 and Hz symbols are
flashing.
7 Pulse emission
(frequency too
high)
fPULSE › 3pulses / second The " " and / or " "
symbol flashes.
8 The pulse
weight of digital
output cannot
be automatically
modified
The new selected CT
value is too high to
mantain the old pulse
value.
In programming mode the
pulse weight flashes.
* : Nominal value depends on the instrument model.
** : In case of 3 phases, 3wires, 3 CTs model, the threshold values are referred to VL-L voltages.
*** : On 3 phases, 3wires, 3 CTs model, the first diagnostic case "Under Voltage" has a second meaning:
i.e. the instrument serial communication is not possible.

14
10. MAINTENANCE
The instrument is maintenance-free.
Clean the display and keyboard, if required, using a clean cloth and non-aggressive cleaning liquid.
Do not use solvents or detergents which may damage plastic parts.
11. TECHNICAL FEATURES
AUXILIARY POWER SUPPLY
Rated voltage powered from measuring inputs (1)
external power supply 19÷60Vd c (on request)
Consumption 0.8VA max
VOLTAGE INPUTS
Rated voltage A) 3x230/400Va c +15% -20%, 4 wires
B) 3x120/208Va c +15% -20%, 4 wires
c) 3x400Va c +15% -20%, 3 wires
d) 3x2084230Va c +15% -20%, 3 wires
E) 3x1004120Va c +15% -20%, 3 wires
Input impedance ›1.3 MOhm
Burden max 0,15 VA per phase
Frequency 45 - 65 Hz
CURRENT INPUTS
Rated current (Ib) 1 / 5 Ar m s programmable
Min / Max measurable current 20 mA / 7 Ar m s
Maximum overload 10Ar m s continuous - 100 Ar m s for 1 second
Input impedance 0.02 Ohm approximately
Burden max 0.5 VA per phase
Insulation voltage 480 Va c max between phases
Rogowski coils input (optional) 200÷49995A (according to the requested value-refer to the instrument label)
TYPICAL ACCURACY
Voltage ± 0.3% reading ± 0.05% full scale
Current ± 0.5% reading ± 0.05% full scale
Active power ± 1% reading ± 0.1% full scale (PF=1)
Power factor 1.5% reading (0.5 inductive - 0.8 capacitive)
Active energy class 2 according to EN61036 and EN62053 standards
class 1 (ENH version)
Frequency ± 0.05% reading ± 2 digits from 45 to 65 Hz
DISPLAY AND OPERATING CONTROLS
Display high contrast LCD display 43 x 19 mm
8 digits for energies and other parameters + symbols
Keypad 2 push-buttons
COMMUNICATION PORT (2) (optional)
Type RS485 on request, optoisolated
Baud Rate 2400 to 57600 bps
78 kbps in case of LONBUS protocol (on request)
DIGITAL OUTPUTS
Type no. 2 optoisolated (50V-100mADC)
(1) The basic instrument is powered from L1, L2, L3 and N (4-wires version) or L1, L2, L3 (3-wires version). The presence of only one
of the three phases (4-wires version) or two phases (3-wires version) ensures the normal counting and displaying operations.
(2) The serial port is powered from L1 and N (4-wires version) or L1 and L2 (3-wires version). The communication function is
ensured only if the L1 phase (or L1 and L2 for 3-wires) is present and within the specified power supply range.

15
ENVIRONMENTAL CONDITIONS
Operating temperature between -15°C and +60°C (+5°F and +140°F)
Storage temperature between -25°C and +75°C (-13°F and +167°F)
Relative humidity 80% max without condensation
MECHANICAL CHARACTERISTICS
Material plastic enclosure - noryl UL94-V0
Protection degree IP51 (front panel); IP20 (terminals)
Terminals conductors 2.5mm2
Size / Weight 106 x 90 x 57mm, 6 DIN-RAIL modules, 300gr
STANDARDS COMPLIANCE
Safety 73/23/EEC and 93/68/EEC directives, EN61010.1 safety standard
EMC 89/366/EEC directive and following modifications 93/31/EEC and 93/68/
EEC, EN50081-2, EN50082-2, EN61326/A1
INSTANTANEOUS MEASUREMENTS
PHASE VOLTAGE * V1- V2- V3[V]
LINE VOLTAGE V12 - V23 - V31 [V]
SYSTEM VOLTAGE V [V]
LINE CURRENT * & NEUTRAL CURRENT * I1- I2- I3- IN[A]
SYSTEM CURRENT I [A]
POWER FACTOR * PF1- PF2- PF3
SYSTEM POWER FACTOR PF
APPARENT POWER * S1- S2- S3 [VA]
SYSTEM APPARENT POWER S [VA]
ACTIVE POWER * P1- P2- P3 [W]
SYSTEM ACTIVE POWER P [W]
REACTIVE POWER * Q1- Q2- Q3 [var]
SYSTEM REACTIVE POWER Q [var]
FREQUENCY f [Hz]
PHASE REVERSAL 123 / 132
DEMAND VALUES 4xIDMD - SDMD - PDMD
STORED DATA
SYSTEM ACTIVE ENERGY [Wh]
SYSTEM APPARENT ENERGY [VAh]
SYSTEM LAGGING REACTIVE ENERGY [varh ind]
SYSTEM LEADING REACTIVE ENERGY [varh cap]
PEAK VALUES 3xVL-N - 3xVL-L - 3xIL- 3xIDMD - PDMD - SDMD
= Standard = Optional = Bi-directional value (BIDIR option only)
* Parameters not available in case of 3-3-3 connection.

16
DISPLAYED PAGES
ENERGY COUNTERS PAGES [1° loop]
Imported active energy [Wh]
Exported active energy[Wh]
(optional)
Imported apparent energy [VAh]
Exported apparent energy [VAh]
(optional)
Exported lagging reactive energy
[varh ind] (optional)
Imported lagging reactive energy
[varh ind]
Exported leading reactive energy
[varh cap] (optional)
Imported leading reactive energy
[varh cap]

17
INSTANTANEOUS VALUES PAGES [2° loop]
L-N phase 1 voltage [V]
L-N phase 2 voltage [V]
L-N phase 3 voltage [V]
L-L line 12 voltage [V]
L-L line 23 voltage [V]
L-L line 31 voltage [V]
System voltage [V]
Phase 1 current [A]
Phase 2 current [A]
Phase 3 current [A]
System current [A]
Neutral current [A]
Phase 1 active power [W]
Phase 2 active power [W]
Phase 3 active power [W]
System active power [W]
Frequency [Hz]
System powerfactor
Phase 1 powerfactor
Phase 2 powerfactor
Phase 3 powerfactor
System reactive power [var]
Phase 1 reactive power [var]
Phase 2 reactive power [var]
Phase 3 reactive power [var]
System apparent power [VA]
Phase 1 apparent power [VA]
Phase 2 apparent power [VA]
Phase 3 apparent power [VA]

18
DMD & PEAK VALUES PAGES [3° loop] (optional)
Peak of system apparent power DMD [VA]
Peak of system active power DMD [W]
System apparent power DMD [VA]
System active power DMD [W]
System current DMD [A]
Peak of L-N phase 1 voltage [V]
Peak of L-N phase 2 voltage [V]
Peak of L-N phase 3 voltage [V]
Peak of L-L line 12 voltage [V]
Peak of L-L line 23 voltage [V]
Peak of L-L line 31 voltage [V]
Peak of phase 1 current [A]
Peak of phase 2 current [A]
Peak of phase 3 current [A]
Phase 1 current DMD [A]
Phase 2 current DMD [A]
Phase 3 current DMD [A]
Peak of phase 1 current DMD [A]
Peak of phase 2 current DMD [A]
Peak of phase 3 current DMD [A]

19

Table of contents
Popular Transducer manuals by other brands
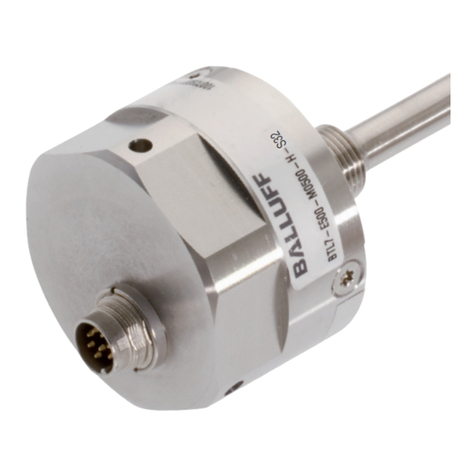
Balluff
Balluff BTL7 Series Condensed guide
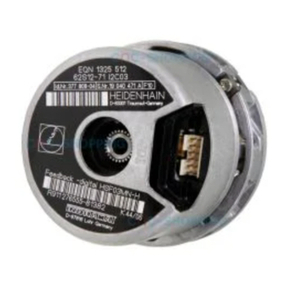
Siemens
Siemens ERN 1387 Assemble & disassemble
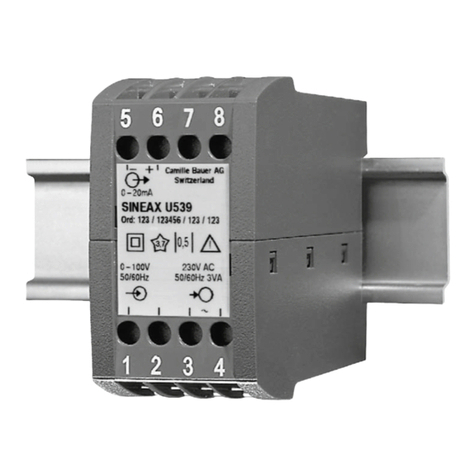
Camille Bauer
Camille Bauer SINEAX U 539 operating instructions
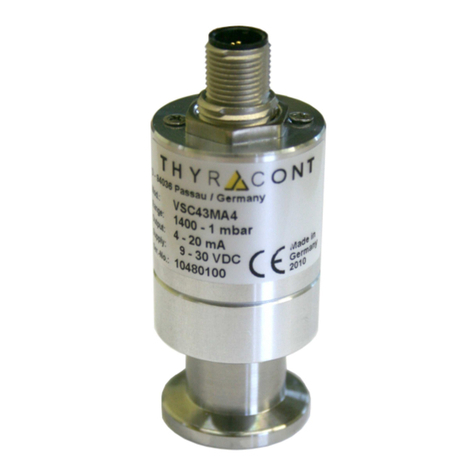
Thyracont
Thyracont VSC43MA4 operating instructions
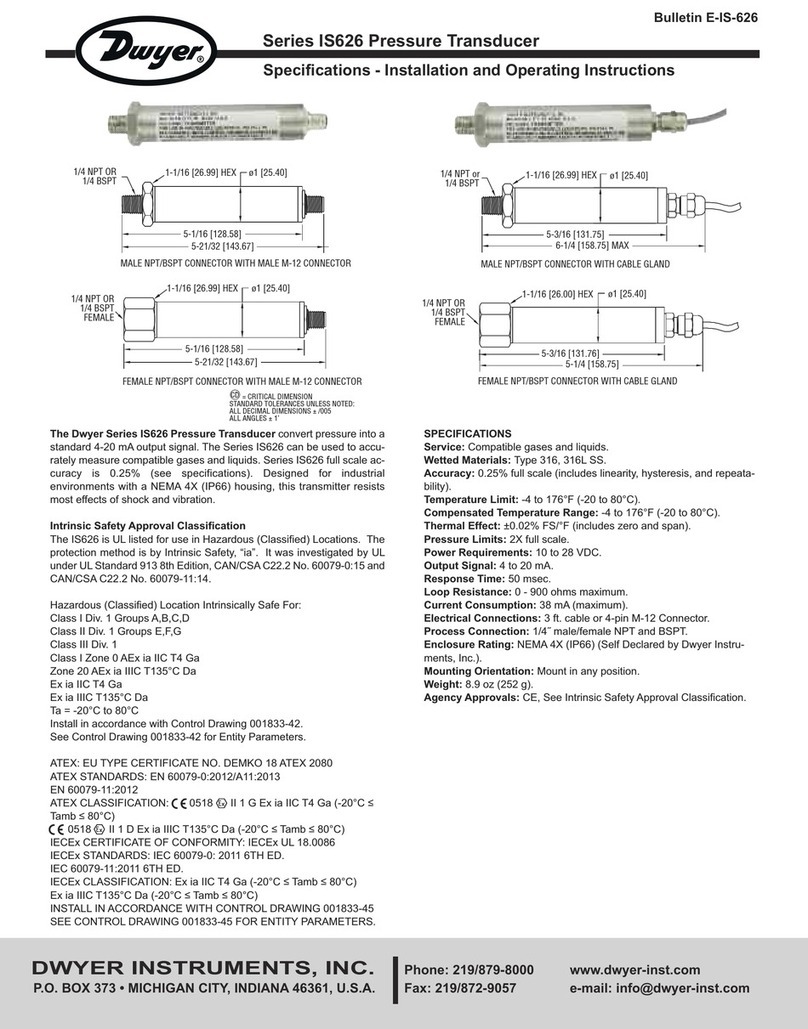
Dwyer Instruments
Dwyer Instruments IS626 Series Installation and operating instructions

Balluff
Balluff Micropulse BTL5-A series user guide