Allied Motion TCI HarmonicGuard Series User manual

HarmonicGuard®Series
Drive-Applied Harmonic Filter
Installation, Operation, and Maintenance Manual
TCI, LLC
W132 N10611 Grant Drive
Germantown, Wisconsin 53022
Phone: 414-357-4480
Fax: 414-357-4484
Helpline: 800-824-8282
Web Site: www.transcoil.com
© 2019 TCI, LLC All rights reserved
ADD The part # box
Product No: 28557-1
Effective: 9/15/23
Version: R

No part of this publication may be reproduced, stored in a retrieval system, or transmitted in any form or by any
means, mechanical, electronic, photocopying, recording, or otherwise, without the prior written permission of TCI,
LLC. The information in this manual is subject to change without notice. Every precaution has been taken in the
preparation of this manual. TCI, LLC assumes no responsibility for errors or omissions. Neither is any liability
assumed for damages resulting from the use of the information contained in this publication.

Revision
Description
Date
A
Release
10/16/13
B
Added Fuse Monitor Option
02/03/14
C
Added Heater & Vibration Pad Options
09/10/14
D
Added 600V Option
Changed P/N to 28557-1
11/24/14
E
Updated Part Numbering System
Added Floor Stand Option
01/04/16
F
Updated 480V Watts Loss
Updated tables
03/28/17
G
Updated 600V and 400V Fuse
Recommendation Table
06/19/17
H
Updated 480V and 600V Watt Loss
Updated Part Numbering System
Update Fuse Tables
01/31/18
I
Added PQconnect information
Modbus
Register Maps
PQconnect Hardware/Software
Troubleshooting the board
11/01/18
J
Edits to PQconnect Hardware/Software
Edits to PQconnect parameters tables
1/23/19
K
Reformat of Manual and addition of 50Hz
option
7/11/19
L
Addition of Bluetooth PQconnect App
10/23/19
M
Updates to PQconnect section
01/06/20
N
Updates to PQconnect Section
Updates to part numbering
07/29/20
O
Updates to PQconnect Parameter tables
01/27/21
P
Updates to Installation Checklist and Over-
Temperature Switch, minor updates to
PQconnect section
04/06/21
Q
Updates to PQconnect Parameter tables
and addition of Torque Values
06/10/22
R
Added EtherNet/IP Information
Updated PQConnect Parameter
Databases
Updated Bluetooth PQvision App
9/15/23

Performance Guarantee
Select and install the appropriate HarmonicGuard®Passive Harmonic
Filter in a variable torque, variable frequency AC drive application, within
our published technical specifications and we guarantee that the input
current distortion will be less than or equal to 5% THID for standard
HarmonicGuard Series filters at full load, and less than 8% at 30% load.
If a properly sized and installed filter fails to meet its specified THID level,
TCI will provide material for necessary modifications or replacement
filter at no charge.
HarmonicGuard filters can also provide similar performance in other
drive applications such as constant torque, DC drives and other phase-
controlled rectifiers, but actual THID levels can vary by load and/or
speed and therefore cannot be guaranteed. Consult factory for
assistance when applying HarmonicGuard filters on these types of
equipment.
MINIMUM SYSTEM REQUIREMENTS:
The guaranteed performance levels of this filter will be achieved
when the following system conditions are met:
Frequency: 50 Hz / 60Hz ± 0.75Hz
System Voltage: Nominal System Voltage (line to line) ±10%
Balanced Line Voltage: Within 0.5%
Background Voltage Distortion: < 0.5% THVD
The input VFD current waveform shall be consistent with that of a
VFD with 3% AC line reactance at full load.
NOTE: The presence of background voltage distortion will cause motors
& other linear loads to draw harmonic currents.
Additional harmonic currents may flow into the HarmonicGuard filter if
there is harmonic voltage distortion already on the system.
If higher levels of harmonic voltage distortion (2%-5%) are present,
please use the high background distortion version of the
HarmonicGuard filter.
*For PQconnect: To run PQvision software, minimum system
requirements are Windows 7 and 1280x720 resolution.

HarmonicGuard Filter Manual
Table of Contents
1.0 SAFETY................................................................................................................................................................7
SAFETY INSTRUCTIONS OVERVIEW ............................................................................................................................7
WARNINGS AND CAUTIONS ........................................................................................................................................7
GENERAL SAFETY INSTRUCTIONS ..............................................................................................................................8
2.0 GENERAL INFORMATION..................................................................................................................................9
INTENDED AUDIENCE.................................................................................................................................................9
HARMONICGUARD FAMILY DESCRIPTION ....................................................................................................................9
RECEIVING INSPECTION.............................................................................................................................................9
STORAGE INSTRUCTIONS...........................................................................................................................................9
TCI LIMITED WARRANTY POLICY ............................................................................................................................ 10
3.0 PRE-INSTALLATION PLANNING.................................................................................................................... 11
VERIFY THE APPLICATION ....................................................................................................................................... 11
HARMONICGUARD DRIVE-APPLIED FILTER .............................................................................................................. 11
NAMEPLATE DATA.................................................................................................................................................. 11
PART NUMBERING SYSTEM .................................................................................................................................... 12
HARMONICGUARD FILTER OVERVIEW ..................................................................................................................... 14
HARMONICGUARD OPTIONS ................................................................................................................................... 14
4.0 INSTALLATION GUIDELINES ......................................................................................................................... 17
INSTALLATION CHECKLIST....................................................................................................................................... 17
SELECT A SUITABLE LOCATION ............................................................................................................................... 17
MOUNTING............................................................................................................................................................. 18
WIRING ................................................................................................................................................................. 18
Cable Entry Locations...................................................................................................................................... 18
Field Wiring Connection Terminals.................................................................................................................. 18
Grounding ........................................................................................................................................................ 18
Filter’s Schematic ............................................................................................................................................ 19
Torque Values ................................................................................................................................................. 20
SCCR FUSING REQUIREMENTS.............................................................................................................................. 23
Provisional Fuse Tables .................................................................................................................................. 23
5.0 PQCONNECT CONNECTIVITY........................................................................................................................ 33
HARMONICGUARD FILTER WITH PQCONNECT OVERVIEW......................................................................................... 33
COMMUNICATION OPTIONS AND CONNECTIONS ....................................................................................................... 34
PCB Connections ............................................................................................................................................ 34
Wiring and Configuration ................................................................................................................................. 36
MODBUS RTU ....................................................................................................................................................... 38
PQvision PC application Screen Elements...................................................................................................... 38
Example Application Using “Simply Modbus Master 8.1.0”............................................................................. 46
Example Setup Instructions to Read Data from the PQconnect Unit .............................................................. 47
PQconnect Quick Start Unit Software Setup ................................................................................................... 48
Modbus RTU Register Map ............................................................................................................................. 49
Waveform Data................................................................................................................................................ 74
BLUETOOTH WIRELESS TECHNOLOGY..................................................................................................................... 75
ETHERNET/IP........................................................................................................................................................ 77
Wiring for EtherNet/IP communication ............................................................................................................ 78
IP Address Configuration for EtherNet/IP communication .............................................................................. 79
Viewing EtherNet/IP Data on a Website.......................................................................................................... 81
Using PQConnect Board with RSLogix 5000 VIA EtherNet/IP........................................................................ 82
EtherNet/IP EDS File and Conformance Info .................................................................................................. 92
EtherNet/IP Register Map................................................................................................................................ 93

HarmonicGuard Filter Manual
Assembly Objects .......................................................................................................................................... 122
Waveform Data.............................................................................................................................................. 126
6.0 PQCONNECT TROUBLESHOOTING ............................................................................................................ 127
HARMONICGUARD PASSIVE FILTER STATUS WARNING .......................................................................................... 127
RECEIVING INSPECTION........................................................................................................................................ 127
CONNECTIVITY BOARD PROBLEM.......................................................................................................................... 127
COMMUNICATION PROBLEMS ................................................................................................................................ 129
DEBUG STATUS CONDITIONS................................................................................................................................ 130
CONTACTOR PROBLEM......................................................................................................................................... 131
ETHERNET/IP PROBLEM ...................................................................................................................................... 134
7.0 MAINTENANCE AND SERVICE .................................................................................................................... 136
HARMONICGUARD FILTER RELIABILITY AND SERVICE LIFE...................................................................................... 136
PERIODIC MAINTENANCE ...................................................................................................................................... 136
TROUBLESHOOTING ............................................................................................................................................. 136
WARNING ............................................................................................................................................................ 136
REPLACEMENT PARTS.......................................................................................................................................... 136
FACTORY CONTACTS AND TECH SUPPORT ............................................................................................................ 136

HarmonicGuard Filter Manual 1.0 Safety
1.0 Safety
Safety Instructions Overview
This section provides the safety instructions which must be followed when installing, operating,
and servicing the HarmonicGuard Passive filter. If neglected, physical injury or death may follow,
or damage may occur to the filter or equipment connected to the HarmonicGuard filter. The
material in this chapter must be read and understood before attempting any work on or with the
product.
The HarmonicGuard filter is intended to be connected to the input terminals of one or more VFDs.
Three-phase power is connected to the input terminals of the HarmonicGuard, and power is
supplied to the VFD or VFDs through the filter. The instructions, and particularly the safety
instructions for the VFDs, motors, and any other related equipment must be read, understood,
and followed when working on any of the equipment.
Warnings and Cautions
This manual provides two types of safety instructions. Warnings are used to call attention to
instructions that describe steps that must be taken to avoid conditions that can lead to a serious
fault condition, physical injury, or death.
Cautions are used to call attention to instructions that describe steps that must be taken to avoid
conditions that can lead to a malfunction and possible equipment damage.
Warnings
Readers are informed of situations that can result in serious physical injury and/or serious
damage to equipment with warning statements highlighted by the following symbols:
Warning
Dangerous Voltage Warning: warns of situations where
high voltage can cause physical injury and/or damage
to equipment. The text next to this symbol describes
ways to avoid the danger.
Warning
General Warning: warns of situations that can cause
physical injury and/or damage to equipment by means
other than electrical. The text next to this symbol describes
ways to avoid the danger.
Warning
Electrostatic Discharge Warning: warning of situations in
which an electrostatic discharge can damage equipment.
The text next to this symbol describes ways to avoid the
danger.
Cautions
Readers are informed of situations that can lead to a malfunction and possible equipment damage
with caution statements:
Caution
General Caution: identifies situations that can lead to a
malfunction and possible equipment damage. The text
describes ways to avoid the situation.

HarmonicGuard Filter Manual 1.0 Safety
General Safety Instructions
These safety instructions are intended for all work at the HarmonicGuard. Additional safety
instructions are provided at appropriate points in other sections of this manual.
Warning
Be sure to read, understand, and follow all safety
instructions.
Warning
Only qualified electricians should carry out all
electrical installation and maintenance work on the
HarmonicGuard filter.
Warning
All wiring must be in accordance with the National
Electrical Code (NEC) and/or any other codes that apply
to the installation site.
Warning
Disconnect all power before working on the
equipment. Do not attempt any work on a powered
filter.
Warning
The HarmonicGuard filter, drive, motor, and other
connected equipment must be properly grounded.
Warning
After switching off the power, always allow 5 minutes for
the capacitors in the HarmonicGuard filter and in the drive
to discharge before working on the HarmonicGuard, the
drive, the motor, or the connecting wiring. It is a good idea
to check with a voltmeter to make sure that all sources of
power have been disconnected and that all capacitors
have discharged before beginning work.

HarmonicGuard IOM
Manual
9
HarmonicGuard Filter Manual 2.0 General Information
2.0 General Information
Thank you for selecting the HarmonicGuard Passive filter. TCI has produced this filter for use in
many variable frequency drive (VFD) applications that require input power line harmonic current
reduction. This manual describes how to install, operate, and maintain the HarmonicGuard filter.
Please contact TCI Technical Support or visit TCl Support for additional information.
Intended Audience
This manual is intended for use by all personnel responsible for the installation, operation, and
maintenance of the HarmonicGuard filters. Such personnel are expected to have knowledge of
electrical wiring practices, electronic components, and electrical schematic symbols.
HarmonicGuard Family Description
The HarmonicGuard (HG) passive filter offers an array of harmonic mitigation solutions designed
for specific applications and industry. The HarmonicGuard Standard solution (HGP), and
HarmonicGuard Low Capacitance solution (HGL). Throughout this document, the
HarmonicGuard passive filter lineup will be abbreviated as HarmonicGuard.
The HGP Solution is the industry leading solution for harmonic mitigation solution with remote
connectivity and intelligent control for nonlinear loads such as VFDs and UPS Systems. Offering
5% Total Current Demand Distortion (iTDD) performance for any load conditions.
The HGL Solution is the industry leading solution for harmonic mitigation solution on generators.
Offering 5% Total Current Demand Distortion (iTDD) performance for any load conditions.
Receiving Inspection
The HarmonicGuard filter has been thoroughly inspected and functionally tested at the factory
and carefully packaged for shipment. When you receive the unit, you should immediately inspect
the shipping container and report any damage to the carrier that delivered the unit. Verify that the
part number of the unit you received is the same as the part number listed on your purchase
order.
Storage Instructions
If the HarmonicGuard filter is to be stored before use, be sure that it is in a location that conforms
to published storage humidity and temperature specifications stated in the Table 1:
HarmonicGuard Technical Specifications. Store the unit in its original packaging.

HarmonicGuard IOM
Manual
10
HarmonicGuard Filter Manual 2.0 General Information
TCI Limited Warranty Policy
TCI, LLC (“TCI”) warrants to the original purchaser only that its products will be free from defects
in materials and workmanship under normal use and service for a period originating on the date
of shipment from TCI and expiring at the end of the period described below:
Product Family
Warranty Period
KLR, KDR
For the life of the drive with which they are installed.
HGA, KMG, MSD,
V1K
One (1) year of useful service,
not to exceed 18 months from the date of shipment.
PF Guard, HGP,
HGL, HSD, HSE,
HSL, KRF
Three (3) years from the date of shipment.
KCAP, KTR
Five (5) years from the date of shipment.
All Other Products
One (1) year of useful service,
not to exceed 18 months from the date of shipment.
The foregoing limited warranty is TCI’s sole warranty with respect to its products and TCI makes
no other warranty, representation, or promise as to the quality or performance of TCI’s products.
THIS EXPRESS LIMITED WARRANTY IS GIVEN IN LIEU OF AND EXCLUDES ANY AND ALL
EXPRESS OR IMPLIED WARRANTIES INCLUDING, WITHOUT LIMITATION, ANY IMPLIED
WARRANTY OF MERCHANTABILITY OR FITNESS FOR A PARTICULAR PURPOSE.
This warranty shall not apply if the product was:
a) Altered or repaired by anyone other than TCI.
b) Applied or used for situations other than those originally specified; or
c) Subjected to negligence, accident, or damage by circumstances beyond TCI’s control,
including but not limited to, improper storage, installation, operation, or maintenance.
If, within the warranty period, any product shall be found in TCI’s reasonable judgment to be
defective, TCI’s liability and the Buyer’s exclusive remedy under this warranty is expressly limited,
at TCI’s option, to (i) repair or replacement of that product, or (ii) return of the product and refund
of the purchase price. Such remedy shall be Buyer’s sole and exclusive remedy. TCI SHALL
NOT, IN ANY EVENT, BE LIABLE FOR INCIDENTAL DAMAGES OR FOR CONSEQUENTIAL
DAMAGES INCLUDING, BUT NOT LIMITED TO, LOSS OF INCOME, LOSS OF TIME, LOST
SALES, INJURY TO PERSONAL PROPERTY, LIABILITY BUYER INCURS WITH RESPECT TO
ANY OTHER PERSON, LOSS OF USE OF THE PRODUCT OR FOR ANY OTHER TYPE OR
FORM OF CONSEQUENTIAL DAMAGE OR ECONOMIC LOSS.
The foregoing warranties do not cover reimbursement for removal, transportation, reinstallation,
or any other expenses that may be incurred in connection with the repair or replacement of the
TCI product.
The employees and sales agents of TCI are not authorized to make additional warranties about
TCI’s products. TCI’s employees’ and sales agents’oral statements do not constitute warranties;
these shall not be relied upon by the Buyer and are not part of any contract for sale. All warranties
of TCI are embodied in this writing and no other warranties are given beyond those set forth
herein.
TCI will not accept the return of any product without its prior written approval. Please consult TCI
Customer Service for instructions on the Return Authorization Procedure.

HarmonicGuard IOM
Manual
11
HarmonicGuard Filter Manual 3.0 Pre-Installation Planning
3.0 Pre-Installation Planning
Verify the Application
Make sure that the HarmonicGuard filter is correct for the application. The voltage rating of the
filter must match the input voltage rating of the connected drive. The horsepower and current
ratings of the filter must be appropriate for the connected load.
HarmonicGuard Drive-Applied Filter
The HGP and HGL are drive-applied harmonic filters designed and developed by TCI to reduce
the harmonic currents drawn from the power source by VFDs with six-pulse diode bridge rectifier.
The published filter’s voltage, Power (HP or kW) and current ratings apply to matching power (Hp
or kW) rated standard VFDs with six-pulse diode bridge rectifiers. The harmonic filter may also
be sized to filter other loads such as SCR six-step drives, SCR Direct Current (DC) motor drives,
thyristor furnaces, battery chargers, electroplating supplies, or other types of nonlinear loads. In
many cases, the filter power rating (HP or kW) will differ from load power rating (HP or kW).
Please contact TCI Technical Support for additional information and support on sizing HGP
harmonic filters for your non-six-pulse diode front end VFD applications.
The HGP and HGL are passive filters connected in series with the input terminals of a VFD or
several VFDs that operate as a group. It is designed to provide a low impedance path for the
major harmonic currents demanded by the driver. The filter is a stand-alone device that can be
furnished in its own enclosure and mounted adjacent to the drive. It is also available on an open
panel for mounting within an enclosure with the drive or other equipment.
The HGP and HGL filters consist minimally of the following features and components:
•A KDR tuned series reactor to prevent system interaction and improve filter
performance.
•A tuned filter circuit with:
•A TCI three-phase tuning reactor specifically designed for the harmonic filter.
•High-endurance, harmonic-rated capacitors
•Larger filters may have multiple tuned circuits. Consult fuse tables to determine if
the filter in question has “parallel” branches.
•Bleeder resistors to ensure safe capacitor discharge upon filter shutdown.
•Cooling fans (on select models) to ensure adequate cooling and safe
operating temperatures.
•Compression terminals for ease and integrity of all power and control wiring
•Fuses - sized to protect the capacitor wiring.
Nameplate Data
The following information is marked on the nameplate:
•Part number: encoding is explained on the following page.
•FLA: the rated continuous operating motor current (RMS amps)
•System Voltage: the rated three-phase line voltage (RMS volts)
•Hz: the rated frequency
•Phase: 3 –The HGP/HGL filter is designed for use only with three-phase power
•Serial #: Filter serial number for Bluetooth pairing
•Drawing #: outline and mounting dimension drawing number
•Schematic #: schematic diagram drawing number.
•Manufacturing #: for TCI internal use
•Enclosure Type: UL designation or "Open" panel construction

HarmonicGuard IOM
Manual
12
HarmonicGuard Filter Manual 3.0 Pre-Installation Planning
Part Numbering System
Figure 1 below identifies the significance of each character in the HarmonicGuard part number.
The example part number, HGP0150AW1C2000 designates an HGP filter that is rated 150 HP,
480 volts, 60 Hz, Type 1 Enclosure, with contactor, PQconnect with EtherNet/IP, no other options.
It includes a line reactor, tuning reactor, and capacitors in a UL Type 1 enclosure. It is designed
for use with a 150 HP drive.
Figure 1: HarmonicGuard Part Number Encoding
HarmonicGuard includes optional thermal switches installed in both the KDR line reactor and
KTR tuning reactor monitored by the PQconnect board. Contactor operation is controlled by
settings stored in the PQconnect via PQvision. For more information on thermal switches, see
section Figure 2: Terminal Block.

HarmonicGuard IOM
Manual
13
HarmonicGuard Filter Manual 3.0 Pre-Installation Planning
Table 1: HarmonicGuard Technical Specifications
*When configured for High Voltage Background Distortion.
Electrical Characteristics
Voltage / Frequency Ratings
60 Hz, 3 Phase: 480, 600 VACs
60 Hz, 3 Phase: 208, 240 VACs
50 Hz, 3 Phase: 380, 415 VACs
Phase
3Ø
kVAR Ratings
With Contactor as low as 0.0 kVAR/HP
Without Contactor 0.15 kVAR/HP (HGL)
Without Contactor 0.30 kVAR/HP (HGP)
Load Types
3-phase diode bridge rectifier loads such as PWM AC drives
Input Power Ratings
208, 240 VAC: 5 - 100 HP
380 - 415 VAC: 4 - 1000 kW
480, 600 VAC: 5 - 1250 HP
THID
Less than 5% at full load
TDD
<5% when sized appropriately at input to Load array
SCCR (Short Circuit Current Rating)
100 kA
Immunity from Voltage
Distortion
Less than 5% THID at full load
with THVD as high as 5%*
Efficiency
Greater than 99%
Overload Capability
200% of current rating for up to 3 minutes/hour
Communication Options
Modbus RTU over RS485
EtherNet/IP
Environmental Conditions
Operating Temperature
Open: -40°C (-40°F) - 50°C (122°F),
Enclosed: -40°C (-40°F) - 40°C (104°F)
Storage Temperature
-40°C (-40°F) - 60°C (140°F)
Elevation
Up to 2,000 m without derating. Consult factory for higher
elevations.
Humidity
95% non-condensing
Protection Category
Open Chassis, UL Type 1, UL Type 3R, and UL Type 12
enclosure
Cooling Method
Natural or Forced Air Convection
Agency Approvals

HarmonicGuard IOM
Manual
14
HarmonicGuard Filter Manual 3.0 Pre-Installation Planning
HarmonicGuard Filter Overview
The HarmonicGuard®Passive Filter provides a low impedance path for the major harmonic
currents demanded by Variable Frequency Drives (VFDs). This greatly reduces the number of
harmonic currents flowing through the electrical power distribution system, bringing those
harmonic currents in line with the IEEE-519 standard for harmonic distortion mandated by an
increasing number of utilities.
The HarmonicGuard Filter includes branch fuses on the harmonic trap circuit capacitors. These
fuses are included in the design to prevent damage to the capacitors in the event of excessive
harmonic trap current if the filter is misapplied.
HarmonicGuard Options
Contactor Option (C)
This option includes a contactor, control power transformer and connection terminals in the filter
circuit which allows the VFD user to control the insertion of this circuit with a relay contact in the
VFD. It is recommended that the VFD contact be programmed to open the contactor below 33%
motor power. For variable torque (fan) loads this will be approximately below 70% speed, so at-
speed contact may be used. This reduces the possibility of leading power factor interacting with
other devices on the power system. Contactor logic should also maintain the contactor closed in
cases where the VFD is bypassed, and the filter is not bypassed. However, TCI recommends the
filter to be bypassed when the VFD is bypassed, to avoid low motor or VFD bypass voltage during
startup.
No Contactor Option (S)
This option includes high quality harmonic-grade capacitors and line reactors. This filter will meet
most application requirements found today. This cost-effective product is available as an open
panel version, in a UL Type 1 or UL Type 12 enclosure, or in an UL Type 3R enclosure. The open
panel is perfect for inclusion in an MCC section or easy installation into industry standard
enclosures. The UL Type 1 enclosed units maintain the same vertical profile as the open panel
design. This design is perfect for applications where floor space is at a premium. The UL Type
3R enclosure protects the filter from harsh conditions.
PQConnect w/ Modbus RTU Option (1)
This option includes a PQConnect board with Modbus RTU capability, control power transformer
and connection terminals in the filter circuit which allows the user to control the insertion of this
circuit with a relay contact in the VFD or PQVision Software. For an intelligent passive harmonic
that autonomously controls its tuning circuit contactor based on your input system to ensure worry
free operation. Allowing multiply forms of data capture to your SCADA system or directly to your
PLC. Field upgraded to EtherNet/IP option not available.
PQConnect w/ Modbus RTU & EtherNet/IP Option (2)
This option includes a PQConnect board with Modbus RTU and EtherNet/IP capability, control
power transformer and connection terminals in the filter circuit which allows the user to control
the insertion of this circuit with a relay contact in the VFD or PQVision Software. For an intelligent
passive harmonic that autonomously controls its tuning circuit contactor based on your input
system to ensure worry free operation, perfect for generator-based systems. The PQConnect with
Modbus RTU operation provides monitoring and status data to your SCADA system. EtherNet/IP
Protocol Conformance refer to EtherNet/IP section.

HarmonicGuard IOM
Manual
15
HarmonicGuard Filter Manual 3.0 Pre-Installation Planning
Floor Stand Option (F)
The Floor Stand Option is intended for use in applications which require the HG enclosure to be
elevated from the floor. The Floor Stand option consists of 12” steel feet available for Type 3R
enclosures 150 HP and below only.
Typical Voltage Distortion Option (0)
The Typical Voltage Distortion Option, intended for applications with levels of background voltage
distortion less than 2%, is a configuration that enables the HG filter to achieve lower levels of
current harmonic distortion in applications with low background voltage distortion.
This performance option is available in all the package options.
High Voltage Distortion Option (1)
The High Voltage Distortion Option, intended for applications with levels of background voltage
distortion of 2% or higher, is a configuration that enables the HG filter to achieve lower levels of
current harmonic distortion in applications with high background voltage distortion.
This performance option is available in all the package options.
Heater Option (H)
The Heater Option is intended for use in applications which require the environmental protection
of a NEMA 3R enclosure. The heater is mounted to the interior of the enclosure and protects
sensitive electronic equipment from the harmful effects of corrosion and condensation.
The Heater option is available for all 3R enclosures. When using a Type 12 or Type 3R Enclosure
and in a high humidity environment, set thermostat to 37°C (100°F) or max temperature below 37°C
(100°F).
Vibration Pad Option (V)
The Vibration Pad Option is intended for use in applications which require environmental noise
protection. The resilient mounting material is placed between the reactor and the interior of the
enclosure and dampens noise produced by the reactor.
The Vibration Pad option is available for all enclosure types.
Oilfield Duty Option (P)
The Oilfield Duty Option features components designed specifically for oil and gas field applications
to handle the additional electrical stress. Designed for cyclical loads these units will be available in
Type 3R enclosures and will be for use with HP ranges from 40 to 200.

HarmonicGuard IOM
Manual
16
HarmonicGuard Filter Manual 3.0 Pre-Installation Planning
Over-temperature/Thermal Switch (T)
This option includes an over-temperature switch installed on both the Line Reactor and the
Tuning Reactor. On each reactor, over-temperature switches are wired to a terminal block
separate from the power terminals. The over-temperature switch opens if unpredicted heating
occurs. An interlocking circuit should be used with the over-temperature switch to turn off the VFD
to prevent filter damage in the event of filter overheating. The over-temperature switch contact is
rated 6 amps at 120 VAC. The over-temperature switches are normally closed, open on
temperature rise and typically have the following trip points:
•On a Class R 220°C insulation reactor, the switch opens on rise above 200°C
•On a Class H 180°C insulation reactor, the switch opens on rise above 160°C
Wire the over-temperature switches according to the reactor schematic using T1 and T2 locations
on the over-temperature switch terminal block.
Figure 2: Terminal Block
If this option is ordered with the PQconnect, the Thermal switch feedback will be wired to the
PQconnect board, and the PQconnect will indicate whether there is an over-temperature problem.
The PQconnect fault relay (J10 header) can be used to be alerted when there is an Over-temp
issue as an additional measure. For further detail please refer to the pin out references in section
PCB Connections.

HarmonicGuard IOM
Manual
17
HarmonicGuard Filter Manual 4.0 Installation Guidelines
4.0 Installation Guidelines
Installation Checklist
The following are the key points to be followed for a successful installation. These points
are explained in detail in the following sections of this manual.
Make sure that the installation location will not be exposed to corrosive or
combustible airborne contaminants.
Select a mounting area that will allow adequate cooling air and maintenance access.
Make sure that all wiring conforms to the requirements of the National Electrical Code
(NEC) and/or other applicable electrical codes.
Connect the harmonic filter equipment-grounding lug to the system ground of the
premises wiring system.
Use a properly sized grounding conductor.
Connect three-phase power to the input terminals of the harmonic filter, L1, L2 & L3.
Connect the output power terminals of the HG, T1, T2 & T3, to the input power terminals of
the VFD.
Select a Suitable Location
Environment
Locating the harmonic filter in a suitable environment will help ensure proper performance and a
normal operating life. Refer to the environmental specifications listed above and/or noted on the
drawings furnished with the unit.
Warning
Unless specifically labeled as approved for such use, this equipment
is not suitable for use in an explosive atmosphere or in a "Hazardous
(Classified) Location" as defined in article 500 of the National
Electrical Code (NEC).
The unit must be installed in an area where it will not be exposed to:
•Rain or dripping liquids (unless filter is in a Type 3R enclosure)
•Corrosive liquids or gasses
•Explosive or combustible gases or dust
•Excessive airborne dirt and dust
•Excessive vibration
Working Space
Provide enough access and working space around the unit to permit ready and safe installation,
operation, and maintenance. Make sure that the installation conforms to all working space and
clearance requirements of the National Electrical Code (NEC) and/or any other applicable codes.
Provide enough unobstructed space to allow cooling air to flow through the unit. Keep the widest
or deepest portion of the unit enclosure having ventilation openings a minimum of six inches from
adjacent walls or other equipment. The unit enclosure sides that do not have ventilation openings
should be kept a minimum of three inches from adjacent walls or other equipment.

HarmonicGuard IOM
Manual
18
HarmonicGuard Filter Manual 4.0 Installation Guidelines
Mounting
The harmonic filter must be mounted vertically on a smooth, solid surface, free from heat,
dampness, and condensation.
If you are mounting an open panel unit in your own enclosure, you must provide an enclosure
that is adequately sized and ventilated sufficiently to prevent overheating. The rating and
dimension tables for open panel units list the watts of heat loss dissipated by the harmonic filter.
The maximum temperature of the air around the harmonic filter’s capacitors, line reactor, and
tuning reactor should not exceed 50°C (122°F).
Wiring
When selecting a mounting location for the harmonic filter, plan for the routing of the power wiring.
Route the conduit and wiring from the power source to the filter and then to the VFD. The harmonic
filter is provided with internal fuses.
Cable Entry Locations
The enclosed harmonic filters are not provided with enclosure wiring knockouts. A location can
be selected at the time of installation. Typical or recommended cable entry locations are shown
on the drawings which can be found on the TCI website.
HarmonicGuard HGP Solution: https://www.transcoil.com/ratings_table/hgp-ratings-table/
HarmonicGuard HGL Solution: https://www.transcoil.com/ratings_table/hgl-ratings-table/
Field Wiring Connection Terminals
Compression type terminals (Lug Options) are provided for all field wiring connections. The wire
size capacity ranges and tightening torque for all field wiring connections are listed in Table 2-
Table 4.
Grounding
The HarmonicGuard filter panel equipment-grounding lug must be connected to the ground of the
wiring system. The equipment-grounding connection must conform to the requirements of the
National Electrical Code (NEC) and/or any other codes that apply to the installation site. The
ground connection must be made using a wire conductor. Metallic conduit is not a suitable
grounding conductor. The integrity of all ground connections should be periodically checked.
Caution
Use copper wire that is appropriate for the voltage and current rating of the
equipment. The wire selection must conform to the requirements of the National
Electrical Code (NEC) and/or other applicable electrical codes.
For units rated less than 100 amps, use wire with an insulation temperature rating
of 60°C or higher.
For units rated 100 amps or more, use wire with an insulation temperature rating
of 75°C or higher.
Connect the three-phase power of the appropriate voltage and current capacity to the circuit
protective device to the filter’s input power terminals.
Note: In large HP filters, the input and output power conductors are connected directly to the input
and output terminals on the line reactor.
Connect the output terminals of the filter to the input power terminals of the VFD.

HarmonicGuard IOM
Manual
19
HarmonicGuard Filter Manual 4.0 Installation Guidelines
Filter’s Schematic
Inspect the installation to make sure that all equipment has been completely and correctly installed
in accordance with the Installation Guidelines section of this manual.
•Check to see that the cooling fan(s) are operating in units so equipped.
•Check to make sure power connections are torqued to recommended torque value.
Since all HG products are passive filters, it is always operating whenever the drive is operating.
The Schematic shown below is an illustration of typical HG filter wiring.
Figure 3: Typical HarmonicGuard (HG) Filter Wiring for up to 480 V/800 HP
Always refer to the drawings and other information shipped with your unit. Consult applicable wiring
codes, UL, and NEC, for current limiting and disconnect requirements.
Warning
Exercise caution when connecting the filter to the VFD. Internal filter components
may carry dangerous voltage which can cause death or serious injury upon
contact. Remove all power to the HarmonicGuard filter in compliance to
standardized 26 CFR 1920.147 lockout/tagout policies.
!

HarmonicGuard IOM
Manual
20
HarmonicGuard Filter Manual 4.0 Installation Guidelines
Torque Values
Table 2: HarmonicGuard (HG) 480V Terminal Wire Size Capacity Range and Tightening Torque (CU)
Line/Load Connections
Ground Connection
HP Rating
Wire Range
Torque Lbs-in (N-m)
Wire Range
Torque Lbs-in (N-m)
3
18 AWG to 4 AWG
20 lbs-in (2.26 N-m)
14 AWG to One 10 AWG
35 lbs-in (4.0 N-m)
5
18 AWG to 4 AWG
20 lbs-in (2.26 N-m)
One 8 AWG
40 lbs-in (4.5 N-m)
8
18 AWG to 4 AWG
20 lbs-in (2.26 N-m)
6 AWG to One 4 AWG
45 lbs-in (5.1 N-m)
10
18 AWG to 4 AWG
20 lbs-in (2.26 N-m)
2 AWG to One 1/0 AWG
50 lbs-in (5.6 N-m)
15
14 AWG to 6 AWG
30 lbs-in (3.39 N-m)
One 8 AWG
40 lbs-in (4.5 N-m)
20
14 AWG to 6 AWG
30 lbs-in (3.39 N-m)
One 8 AWG
40 lbs-in (4.5 N-m)
25
14 AWG to 6 AWG
30 lbs-in (3.39 N-m)
One 8 AWG
40 lbs-in (4.5 N-m)
30
14 AWG to 6 AWG
30 lbs-in (3.39 N-m)
6 AWG to One 4 AWG
45 lbs-in (5.1 N-m)
40
14 AWG to 6 AWG
30 lbs-in (3.39 N-m)
6 AWG to One 4 AWG
45 lbs-in (5.1 N-m)
50
14 AWG to 6 AWG
30 lbs-in (3.39 N-m)
2 AWG to One 1/0 AWG
50 lbs-in (5.6 N-m)
60
14 AWG to 6 AWG
30 lbs-in (3.39 N-m)
One 8 AWG
40 lbs-in (4.5 N-m)
75
3 AWG to One 2/0 AWG
50 lbs-in (5.6 N-m)
3 AWG to One 2/0 AWG
50 lbs-in (5.6 N-m)
100
3 AWG to One 2/0 AWG
50 lbs-in (5.6 N-m)
3 AWG to One 2/0 AWG
50 lbs-in (5.6 N-m)
125
One 250kcmil to 2 AWG
375 lbs-in (42.4 N-m)
One 250kcmil to 2 AWG
375 lbs-in (42.4 N-m)
150
One 250kcmil to 2 AWG
375 lbs-in (42.4 N-m)
One 250kcmil to 2 AWG
375 lbs-in (42.4 N-m)
200
Two 350kcmil to 2 AWG
375 lbs-in (42.4 N-m)
Two 350kcmil to 2 AWG
375 lbs-in (42.4 N-m)
250
Two 350kcmil to 2 AWG
375 lbs-in (42.4 N-m)
Two 350kcmil to 2 AWG
375 lbs-in (42.4 N-m)
300
Two 350kcmil to 2 AWG
375 lbs-in (42.4 N-m)
Two 350kcmil to 2 AWG
375 lbs-in (42.4 N-m)
350
Two 350kcmil to 2 AWG
375 lbs-in (42.4 N-m)
Two 350kcmil to 2 AWG
375 lbs-in (42.4 N-m)
400
Two 350kcmil to 2 AWG
375 lbs-in (42.4 N-m)
Two 350kcmil to 2 AWG
375 lbs-in (42.4 N-m)
450
Two 600kcmil to 4 AWG
500 lbs-in (56.5 N-m)
Two 600kcmil to 4 AWG
500 lbs-in (56.5 N-m)
500
Two 600kcmil to 4 AWG
500 lbs-in (56.5 N-m)
Two 600kcmil to 4 AWG
500 lbs-in (56.5 N-m)
600
Four 600kcmil to 2 AWG
550 lbs-in (62.14 N-m)
Four 600kcmil to 2 AWG
550 lbs-in (62.14 N-m)
700
Four 600kcmil to 2 AWG
550 lbs-in (62.14 N-m)
Four 600kcmil to 2 AWG
550 lbs-in (62.14 N-m)
800
Four 600kcmil to 2 AWG
550 lbs-in (62.14 N-m)
Four 600kcmil to 2 AWG
550 lbs-in (62.14 N-m)
900
Four 600kcmil to 2 AWG
550 lbs-in (62.14 N-m)
Four 600kcmil to 2 AWG
550 lbs-in (62.14 N-m)
1000
Four 600kcmil to 2 AWG
375 lbs-in (42.4 N-m)
Four 600kcmil to 2 AWG
375 lbs-in (42.4 N-m)
This manual suits for next models
2
Table of contents
Other Allied Motion Water Filtration System manuals
Popular Water Filtration System manuals by other brands
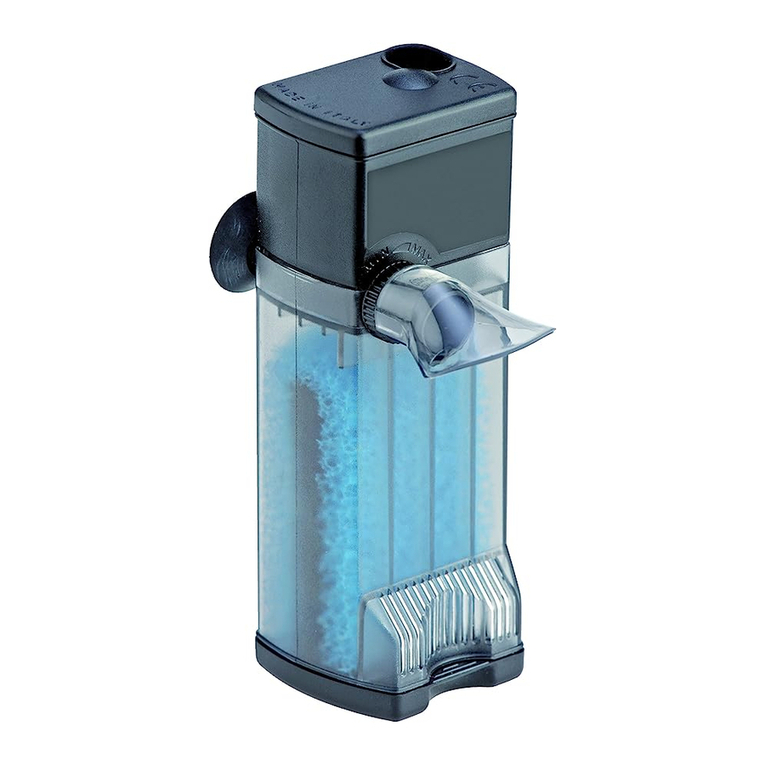
Eden
Eden 304S user manual

Bosch
Bosch Ethylene Absorber user manual
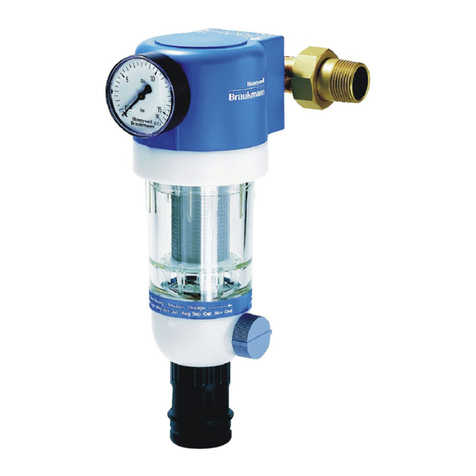
Honeywell
Honeywell BRAUKMANN F74C user manual
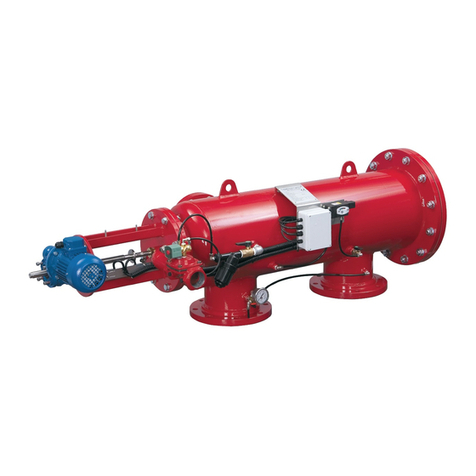
amiad
amiad SAF-4500 Installation, operation and maintenance instructions
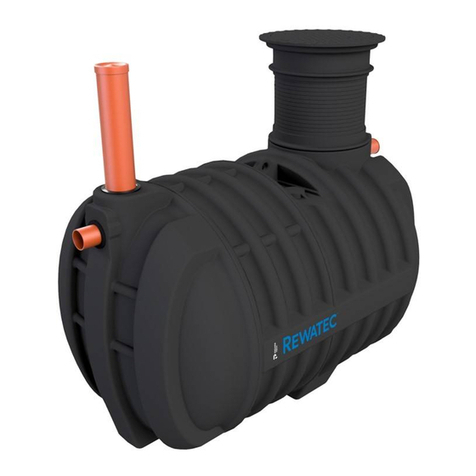
PREMIER TECH
PREMIER TECH Solido SMART Operating Manual Including Operations Logbook, Manual for Installation, Commissioning and Maintenanc
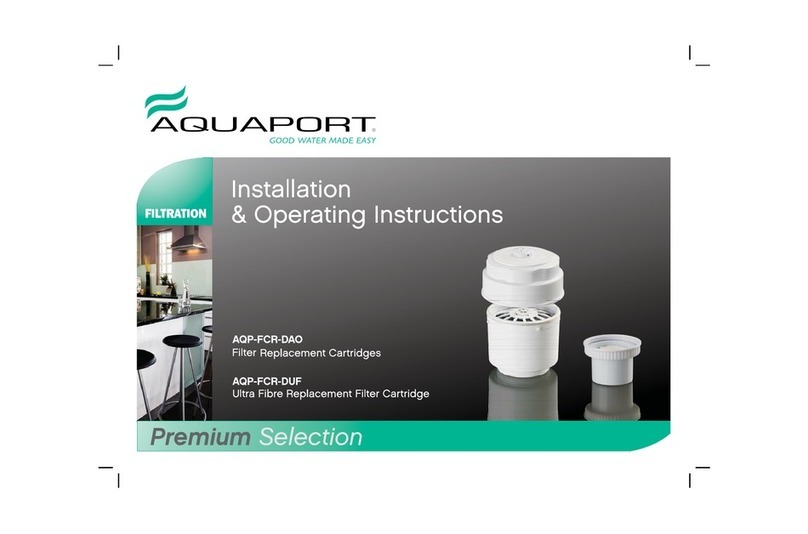
Aquaport
Aquaport AQP-DCR-DAO Installation and operating instrictions