Allied Motion TCI V1K Kit User manual

V1K Kit
Installation Guide
Revision 1.0 Part # 31259 06/06/2022
TCI, LLC
W132 N10611 Grant Drive,
Germantown, Wisconsin 53022
800-824-8282 | www.transcoil.com
Field Wiring Connection Terminals
Compression type terminals are available for all line wiring
connections. The wire size capacity ranges and tightening
torque for the reactor power terminals are listed in the
table.
General Safety Instructions
All electrical connections must be re-torqued annually.
See www.transcoil.com for component drawings and dimensions.
Please contact TCI Technical Support or your TCI distributor for
application information regarding the use of V1K output lters on
the output side of the VFD.
• Current Rating: 2 - 750 Amps, 208 V - 600 V, .75 - 600 HP
• UL Listed
• Eciency > 98%
• Insulation Rating: 600V Class
• Insulation Class: Class H (180°C or better)
• Maximum Altitude: 2000 m (6,000 ft) Derating necessary
above 2000 m
• Lead Length: up to 1,000 ft (Specic applications could
reach longer lead lengths.)
• Ambient Temp: Min -25°C, Max 40°C
• For use with three phase VFDs operating at 2 kHz - 4 kHz
PWM carrier frequency and with a maximum motor cable
size necessary to achieve a 5% voltage drop at 1,000 ft.
• Optional thermal switch electrical rating: 120 V/6 A
• Switch opens on temperature rise
• 2 A to 12 A standard 195°C trip
• 2 A to 12 A EX version 160°C trip
• 16 A to 110 A 160°C trip
Product Specications
Installation Checklist
• Access V1K installation drawings on the TCI website
for unit dimensions, mounting hole pattern, mounting
orientation, wire locations, unit weights, and other
unit specic installation notes. https://transcoil.com/
products/v1k-motor-protection-lter/
• Ensure installation location is not exposed to corrosive
liquids or gases, explosive or combustible gases or
dust, excessive airborne dirt and dust, or excessive
vibration.
• Select mounting area that allows adequate cooling air
and maintenance access.
• Ensure all wiring conforms to requirements of the
National Electric Code (NEC) and\or other applicable
electrical codes.
• Ground V1K output lter to a dedicated system
ground to ensure safety and lter performance. Use
properly sized grounding conductor.
• Wire output power terminals of the VFD to the input
terminals of the V1K: U, V, & W.
• Wire the output power terminals of the V1K, T1, T2, &
T3 to the motor power connections.
• Ensure VFD is set for operating modes and ranges
that are compatible with the V1K.
• Check entire system thoroughly before energizing and
operating any equipment.
When you receive the unit, immediately inspect the
shipping container and report any damage to the
shipping carrier who delivered the unit.
Warning Be sure to read, understand, and follow all safety
instructions.
Warning Only qualied electricians should carry out all
electrical installation and maintenance work on
V1K drive output lters.
Warning All wiring must be in accordance with the National
Electrical Code (NEC) and/or any other codes that
apply to the installation site.
Warning Disconnect all power before working on the
equipment. Do not attempt any work on a powered
V1K output lter.
Warning The V1K, VFD, motor, and other connected
equipment must be properly grounded.
Warning The VFD terminals and connected cables are at a
dangerously high voltage when power is applied to
the VFD, regardless of motor operation.
!
!
!
V1K Kit
Part Num. Current
Rating
Reactor Terminal Block/
Optional Lug Kit Terminals Board
Part
Num.
Lug
Kit
Wire Size Torque
(lb-in)
V1K2A0K 2 12 - 14 AWG 10 25009 N/A
V1K3A0K 3 12 - 14 AWG 10 25009 N/A
V1K4A0K 4 12 - 14 AWG 10 25009 N/A
V1K6A0K 6 12 - 14 AWG 10 25009 N/A
V1K8A0K 8 12 - 14 AWG 10 25009 N/A
V1K12A0K 12 12 - 14 AWG 10 25009 N/A
V1K16A0K 16 4 - 12 AWG 20 25009 N/A
V1K18A0K 18 4 - 12 AWG 20 25009 N/A
V1K21A0K 21 4 - 12 AWG 20 25009 N/A
V1K25A0K 25 4 - 8 AWG 20 25009 N/A
V1K27A0K 27 4 - 8 AWG 20 25009 N/A
V1K35A0K 35 6 - 8 AWG 30 25011 N/A
V1K45A0K 45 6 AWG 30 25011 N/A
V1K55A0K 55 1 - 4 AWG 35 25011 N/A
V1K80A0K 80 1 - 3 AWG 35 25011 N/A
V1K110A0K 110 2/0 - 1/0 AWG 50 25011 SLK10
V1K130A0K 130 2/0 AWG 50 25011 SLK10
V1K160A0K 160 250 kcmil - 3/0 AWG 375 25012 SLK21
V1K200A0K 200 (2) 2/0 - 1 AWG 50 25012 SLK22
V1K250A0K 250 (2) 2/0 AWG 50 25012 SLK22
V1K305A0K 305 (2) 350 kcmil - 3/0 AWG 375 25012 SLK13
V1K362A0K 362 (2) 350 kcmil - 4/0 AWG 375 25012 SLK13
V1K420A0K 420 (2) 600 - 300 kcmil 500 25012 SLK14
V1K480A0K 480 (2) 600 - 350 kcmil 500 25012 SLK14
V1K600A0K 600 (2) 600 - 500 kcmil 500 25012 SLK14
V1K750A0K 750 (3) 600 - 400 kcmil 500 25012 SLK16
TCI, LLC
W132 N10611 Grant Drive,
Germantown, Wisconsin 53022
800-824-8282 | www.transcoil.com
Wiring Diagram

Lug Kit Fig.
Number Lug Wire Range For Lug Torque Bolt Assembly
Torque
See Website For Lug On
Reactor Drawings
SLK10 1 2/0 - 14 AWG See Table S2/0 66 lb-in (7.5 N-m) See Drawing (LK10-DWG)
SLK13 2 (2) 350 kcmil - 6 AWG See Table 2S350 450 lb-in (50.8 N-m) See Drawing (LK13-DWG)
SLK14 2 (2) 600 kcmil - 4 AWG See Table 2S600 450 lb-in (50.8 N-m) See Drawing (LK14-DWG)
SLK16 3 (3) 600 kcmil - 2 AWG See Table T3A2-600N 450 lb-in (50.8 N-m) See Drawing (LK16-DWG)
SLK21 1 250 kcmil - 6 AWG See Table S250 66 lb-in (7.5 N-m) See Drawing (LK21-DWG)
SLK22 4 (2) 2/0 - 14 AWG See Table S2/0 66 lb-in (7.5 N-m) See Drawing (LK22-DWG)
Table S2/0 IHI Connectors
Wire Size Copper (solid
to semi-rigid stranded
and metric mm, ##)
Rating
C
Wire Size FLEX
Copper (#)
Wire Size
Aluminum
Torque
(all drive means)
N/A 90 1/0 - 1 AWG N/A 75 lb-in (8.5 N-m)
N/A 90 1 - 4 AWG N/A 55 lb-in (6.2 N-m)
2/0 - 3 AWG 90 4 - 8 AWG 2/0 - 3 AWG 50 lb-in (5.6 N-m)
4 - 6 AWG 90 8 - 10 AWG 4 - 6 AWG 45 lb-in (5.1 N-m)
8 AWG 90 10 - 14 AWG 8 AWG 40 lb-in (4.5 N-m)
10 - 14 AWG 90 N/A 10 - 12 AWG 35 lb-in (4.0 N-m)
Table S250 IHI Connectors
250 kcmil-2 AWG 90 3/0-2 AWG; 70-50 mm2250 kcmil - 2 AWG 375 lb-in (42.4 N-m)
(1),(2) 25-16 mm2(1) 35
mm290 2-6 AWG; 35-16 mm22 - 6 AWG 275 lb-in (31.1 N-m)
Table 2S350 IHI Connectors
350 kcmil- 2 AWG 90 262 kcmil - 2 AWG 350 kcmil - 2 AWG 375 lb-in (42.4 N-m)
2 - 6 AWG 90 2 AWG - 4 AWG 2 - 6 AWG 275 lb-in (31.1 N-m)
Table 2S600 IHI Connectors
BNVN 90 444 kcmil - 2 AWG 600 kcmil - 4 AWG 500 lb-in (56.5 N-m)
CSA, 200116
UL Listed 84JM ZMVV E129884
(#) FLEX-covers stranding classes within G, H, I/DLO, Metric
class 5 and K/MTW, (##) mm2sizes within AWG/kcmil ranges are
included
Table T3A2-600N Ilsco
• T3A2-600N;
• CSA Certied
• UL 486A/B Listed, UL File E6207
• Must be mounted with a minimum of 2 bolts
Item ID Conductor Range Bolt/Stud Size Hex Size Tightening Torque
T3A2-600N 600 kcmil-2AWG 1/2 1/2 500 lb-in (56.5 N-m)
KDR Reactor Lug Kits
Follow NEC guidelines to determine acceptable wire ampacity requirements.
Lug Torque Tables
Figure 1
Figure 4
Verify the Application
Ensure V1K is correct for the application. Current
rating of the V1K should be sized to handle the FLA
rating of the motor but not exceed 110% of the drive
output current rating. This V1K is best applied matched
closely to the load. The V1K is not selected by the drive
input current rating. Properly sized and applied, TCI
guarantees that the V1K will limit motor terminal peak
input votage to 150% of bus voltage with a wire lead
length of 1,000 feet and a carrier frequency of 4kHz. Max
lead length and carrier frequency can vary depending on
wire lead type. For best performance, the V1K should be
installed within 10 feet of the drive.
Power Wiring
The conduit and wiring from the output of the VFD to the
motor must be routed to the V1K and then to the motor.
TCI recommends a separate dedicated conduit run for
each drive/lter/motor run unless properly shielded and
segregated wiring procedures are practiced. Parasitic
and induced capacitance can greatly reduce the
eectiveness of the lter. Under no circumstances should
you wire both control and power wire in the same conduit
unless the wireway is specically designed for this
practice. The line reactor temperature is sensitive to lead
wire oversizing. Avoid lead wires more than ve times
oversized by copper cross sectional area regarldess of
the material used. Use 75°C copper conductors only or
the equivalent, unless the wire connector is marked for
AI/Cu, then the use of aluminum wire is permitted. Use
only copper conductor on units rated above 80 amps.
Grounding
The V1K lter must be connected to the ground of the
premises wiring system. Connect the lter to a known
ground nearby the lter or run a special ground wire
dedicated for the application. The ground connection
must be made using a wire conductor. Metallic conduit
is not a suitable grounding conductor. The integrity of all
ground connections should be periodically checked.
Variable Frequency Drive Settings
Make sure that the VFD will be set for operation modes
and ranges that are compatible with the V1K:
• Maximum output frequency: 60 Hz
• PWM switching frequency: 2 kHz and 4 kHz
• Mode of operation: Do not use lter on 600 VAC
systems with Dynamic DC braking resistors or
Active Front End drives
• Do not use on overhauling loads without bus
voltage control.
Figure 3
Figure 2
Other Allied Motion Water Filtration System manuals
Popular Water Filtration System manuals by other brands
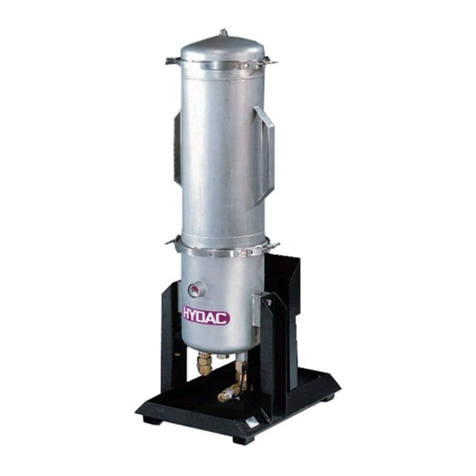
Hydac
Hydac OLF 15 Operating and maintenance instructions
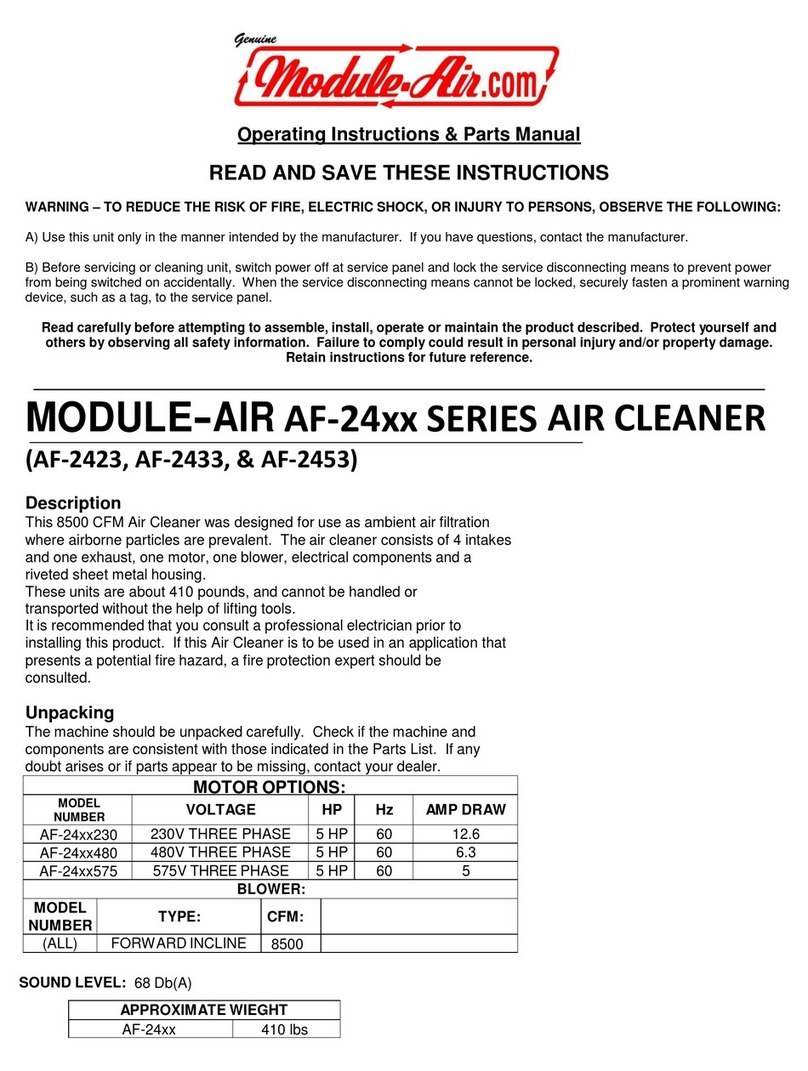
MODULE-AIR
MODULE-AIR AF-24 Series Operating instructions & parts manual
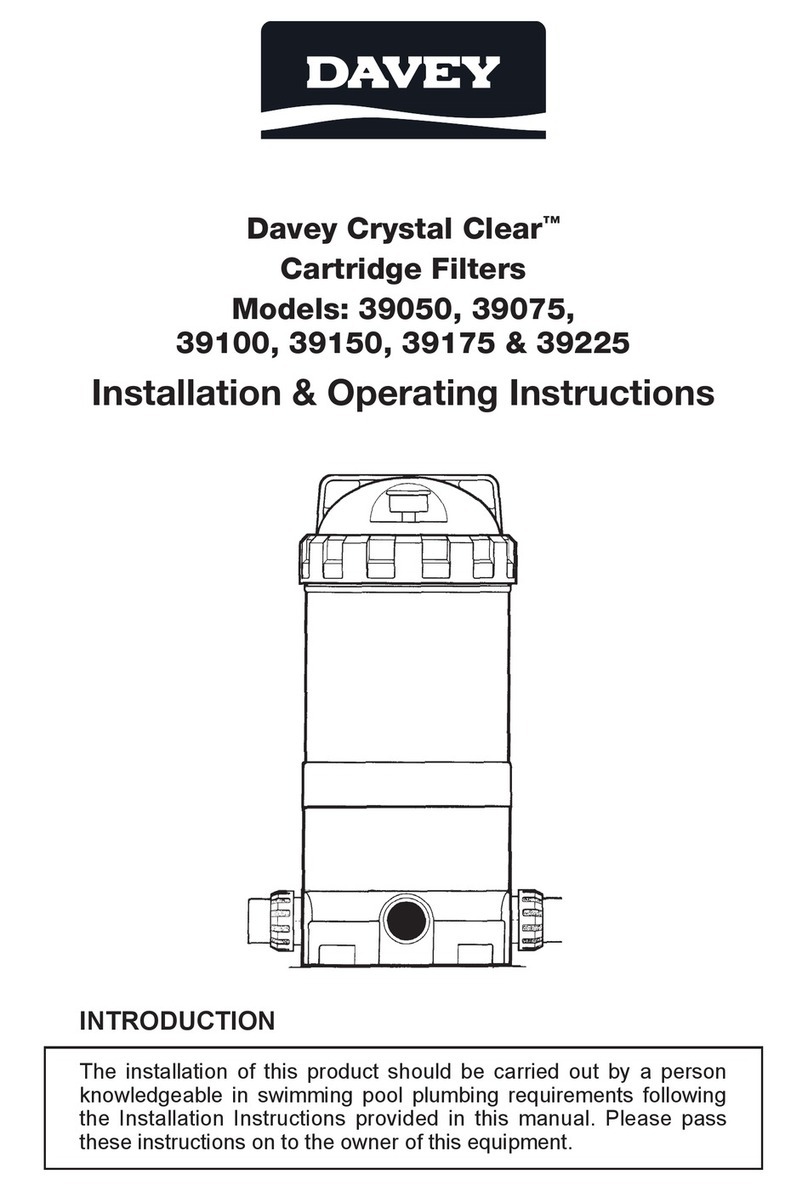
Davey
Davey Crystal Clear 39075 Installation & operating instructions
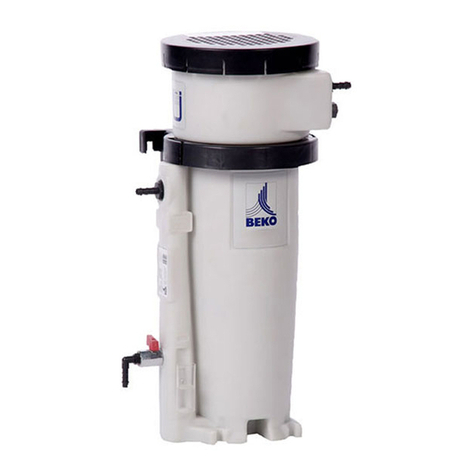
Beko
Beko QWIK-PURE 25 Instructions for installation and operation
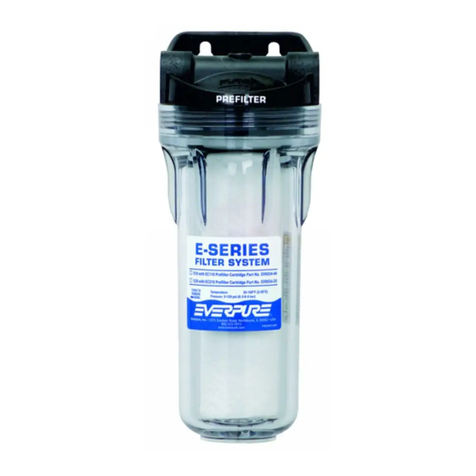
Everpure
Everpure E10 Installation and operation guide

Kessel
Kessel 93007.120 Installation and operating instructions