Allison Transmission 1000 Series User manual

Allison Transmission, General Motors Corporation
P.O. Box 894 Indianapolis, Indiana 46206-0894
www.allisontransmission.com
Printed in USA Copyright © 2004 General Motors Corporation
Allison Transmission
VOCATIONAL MODELS
Service
Manual
2004 DECEMBER
SM3191EN
1000 EVS 2100 EVS 2200 EVS 2500 EVS B 210
1000 HS 2100 HS 2200 HS 2500 HS B 220
1000 MH 2100 MH 2200 MH 2500 MH
1000 PTS 2100 PTS 2200 PTS 2500 PTS
1000 RDS 2100 RDS 2200 RDS 2500 RDS
1000 SP 2100 SP 2200 SP 2500 SP

INTRODUCTION
ii Copyright © 2004 General Motors Corp.
NOTE:
This publication is revised periodically to include improvements,
new models, special tools, and procedures. A revision is indicated
by the date on the title page. Check with your Allison
Transmission service outlet for the currently applicable
publication. Additional copies of this publication may be
purchased from authorized Allison Transmission service outlets.
Look in your telephone directory under the heading of
Transmissions — Truck, Tractor, etc.
TRADEMARK USAGE
The following trademarks are the property of the companies indicated:
•Biobor JF®is the registered trademark for a biological inhibitor manufactured by Hammonds
Fuel Additives Company.
•DEXRON®is a registered trademark of General Motors Corporation.
•Loctite®is a registered trademark of the Loctite Corporation.
•Spiralock®is a registered trademark of Spiralock of Michigan.
•Teflon®is a registered trademark of the DuPont Corporation.
•TranSynd™ is a trademark of Castrol Ltd.
•1000 Series™ is a trademark of General Motors Corporation.
•2000 Series™ is a trademark of General Motors Corporation.
•2400 Series™ is a trademark of General Motors Corporation.
•Windows™ is a trademark of Microsoft Corporation.
•Allison DOC™ and Allison Diagnostic Optimized Connection™ are trademarks of General
Motors Corporation.

WARNINGS, CAUTIONS, AND NOTES
Three types of headings are used in this manual to attract your attention:
NOTE:
is used when an operating procedure, practice, etc.,
is essential to highlight.
WARNING!
is used when an operating procedure, practice,
etc., which, if not correctly followed, could result
in personal injury or loss of life.
CAUTION:
is used when an operating procedure, practice,
etc., which, if not strictly observed, could result
in damage to or destruction of equipment.
Copyright © 2004 General Motors Corp. iii
IT IS YOUR RESPONSIBILITY to be completely familiar with the Warnings and
Cautions described in this Service Manual. These Warnings and Cautions advise against
the use of specific service methods that can result in personal injury, damage to the
equipment, or cause the equipment to become unsafe. It is, however, important to
understand that these Warnings and Cautions are not exhaustive. Allison Transmission
could not possibly know, evaluate, and advise the service trade of all conceivable ways in
which service might be done or of the possible hazardous consequences of each way.
Consequently, Allison Transmission has not undertaken any such broad evaluation.
Accordingly, ANYONE WHO USES A SERVICE PROCEDURE OR TOOL WHICH IS
NOT RECOMMENDED BY ALLISON TRANSMISSION MUST first be thoroughly
satisfied that neither personal safety nor equipment safety will be jeopardized by the
service methods selected.
Proper service and repair are important to the safe, reliable operation of the equipment.
The service procedures recommended by Allison Transmission and described in this
Service Manual are effective methods for performing service operations. Some of these
service operations require the use of tools specifically designed for the purpose. The
special tools should be used when and as recommended.
IMPORTANT SAFETY NOTICE

iv Copyright © 2004 General Motors Corp.
LIST OF WARNINGS
This manual contains the following Warnings —
IT IS YOUR RESPONSIBILITY TO BE FAMILIAR WITH ALL OF THEM.
Operation with excessive loads can cause transmission damage and unexpected vehicle movement.
To help avoid injury, property damage, and/or transmission damage, do not exceed 11 800 kg
(26,000 lbs) GCW or the OEM vehicle rating, whichever is less.
If ignition is turned “OFF” and then “ON” while the CHECK TRANS light is displayed, the
transmission may remain in neutral until the code is cleared. Leave ignition “ON” until you are in
a safe place to stop.
For vehicles containing 1000 and 2000 Product Families transmissions with park pawl, each time
you park the vehicle or leave the operator’s station with the engine running, do the following.
• Bring the vehicle to a complete stop using the service brake.
• Make sure the engine is at low idle rpm.
• Put the transmission in P (Park).
• Engage the P (Park) range by slowly releasing the service brake.
• Apply the emergency brake and/or parking brake, if present, and make sure it is properly
engaged.
• If the operator’s station will be unoccupied with the engine running, chock the wheels and
take any other steps necessary to keep the vehicle from moving.
If this procedure is not followed, the vehicle can move suddenly and you or others could be injured.
For vehicles containing 2000 Product Family transmissions with auto-apply parking brakes, each
time you park the vehicle or leave the operator’s station with the engine running, do the following.
• Bring the vehicle to a complete stop using the service brake.
• Make sure the engine is at low idle rpm.
• Put the transmission in PB (Auto-Apply Parking Brake). Make sure that the parking brake is
properly engaged.
• Apply the emergency brake, if present, and make sure it is properly engaged.
• If the operator’s station will be unoccupied with the engine running, chock the wheels and
take any other steps necessary to keep the vehicle from moving.
If this procedure is not followed, the vehicle can move suddenly and you or others could be injured.
For vehicles containing 2000 Product Family transmissions without auto-apply parking brakes,
each time you park the vehicle or leave the operator’s station with the engine running, do the
following.
• Bring the vehicle to a complete stop using the service brake.
• Make sure the engine is at low idle rpm.
• Put the transmission in N (Neutral).
• Apply the emergency brake and/or parking brake and make sure they are properly engaged.
• If the operator’s station will be unoccupied with the engine running, chock the wheels and
take any other steps necessary to keep the vehicle from moving.
If this procedure is not followed, the vehicle can move suddenly and you or others could be injured.
Observe safety precautions during hydraulic pressure check procedures. All personnel must stand
clear of the vehicle. Take precautions against movement of the vehicle. Be sure that gauges
(vacuum, pressure, tachometer) have extended lines so that they can be read from inside the
vehicle.

Copyright © 2004 General Motors Corp. v
LIST OF WARNINGS
This manual contains the following Warnings —
IT IS YOUR RESPONSIBILITY TO BE FAMILIAR WITH ALL OF THEM.
To help avoid injury or property damage caused by sudden and unexpected vehicle movement, do
not start a stationary stall test until you:
• Put the transmission in P (Park) or N (Neutral)…and
• Apply the parking brake and service brake…and
• Chock the vehicle wheels and take any other steps necessary to keep the vehicle from
moving…and
• Warn personnel to keep clear of the vehicle and its path.
Use appropriate safety equipment such as safety glasses, safety shoes, and gloves.
Do not burn discarded Teflon
®
seals; toxic gases are produced by burning Teflon
®
.
Never dry bearings by spinning them with compressed air. A spinning bearing can disintegrate,
allowing balls or rollers to become lethal flying projectiles. Also, spinning a bearing without
lubrication can damage the bearing.
Avoid contact with the hot fluid or the sump when draining transmission fluid. Direct contact with
the hot fluid or the hot sump may result in bodily injury.
Chock wheels to prevent vehicle from moving when driveline is disconnected. This is not necessary
if vehicle is on a lift or jackstands.
Be sure the torque converter is moving rearward with the transmission as it is removed. Do not
allow the torque converter to become disengaged from the oil pump or to fall and injure yourself
or others.
The torque converter must be held to the torque converter housing by a retaining device such as
shipping brackets. Without the retaining device, the torque converter may slide forward,
disengaging the oil pump, or may fall completely out of the transmission causing personal injury
and/or property damage.
The 1000 and 2000 Product Families transmission dry weights are approximately 150 kg (330 lb).
To help avoid personal injury and/or property damage:
• Use caution when installing, removing, or moving the transmission.
• Get help when lifting the transmission. Assistance from a hoist or another person may be
required.
• Make sure that the lifting equipment can properly support the transmission.
If the transmission is not secured properly to the adapter plate, it could fall. To help avoid personal
injury and/or property damage:
• Use at least 5 bolts to support the transmission.
• Use M10 x 1.5 bolts with 19–25 mm (
3⁄4
–1 inch) thread engagement. If the proper bolt is not
used, the PTO bolt holes may be damaged.

vi Copyright © 2004 General Motors Corp.
LIST OF WARNINGS
This manual contains the following Warnings —
IT IS YOUR RESPONSIBILITY TO BE FAMILIAR WITH ALL OF THEM.
The 1000 and 2000 Product Families torque converter dry weights are approximately 29 kg (63 lb).
To help avoid personal injury and/or property damage:
• Use caution when installing, removing, or moving the torque converter.
• Get help when lifting the torque converter. Assistance from a hoist or another person may be
required.
• Make sure that the lifting equipment can properly support the torque converter.
The 1000 and 2000 Product Families converter housing/front support module dry weights are
approximately 27 kg (60 lb). To help avoid personal injury and/or property damage:
• Use caution when installing, removing, or moving the converter housing/front support
module.
• Get help when lifting the converter housing/front support module. Assistance from a hoist or
another person may be required.
• Make sure that the lifting equipment can properly support the converter housing/front
support module.
Always remove or install the P3 planetary carrier assembly by holding onto the output shaft.
Holding onto the P3 carrier assembly instead of the output shaft may allow the output shaft to fall
causing personal injury and/or property damage.
Exhaust all pressure from the torque converter before loosening the test fixture nut. Failure to
relieve the pressure could cause personal injury and/or property damage.
The rotating clutch housing and turbine shaft are held together by a retaining ring. Removal of the
retaining ring will allow the turbine shaft and the rotating clutch housing to move freely. Ensure
that the rotating clutch housing and the turbine shaft are restrained from moving when removing
the retaining ring. Personal injury and/or property damage may result from the movement of the
rotating clutch housing or the turbine shaft.
Pressing the P3 planetary carrier from the bearing race requires the P3 carrier to fall from the
bearing race. Ensure that the P3 carrier is safely caught when freed from the bearing race. An
uncontrolled fall of the P3 carrier could cause personal injury and/or property damage.

Copyright © 2004 General Motors Corp. vii
Paragraph Page Paragraph Page
Section 1. GENERAL INFORMATION
1–1. SCOPE OF MANUAL
a. Transmission Product Families And
Model Years. . . . . . . . . . . . . . . . . . . . . . . 1–1
b. Model Year 04 (MY04) . . . . . . . . . . . . . . 1–1
c. MY04 Parts Changes . . . . . . . . . . . . . . . . 1–1
d. Model Year 04i (MY04i). . . . . . . . . . . . . 1–1
e. MY04i Parts Changes . . . . . . . . . . . . . . . 1–1
f. Improved Shift Valve Body Casting . . . . 1–1
g. Vocational Models. . . . . . . . . . . . . . . . . . 1–1
h. Vocational Model Nomenclature. . . . . . . 1–2
i. Content and Organization . . . . . . . . . . . . 1–2
j. Illustrations. . . . . . . . . . . . . . . . . . . . . . . . 1–2
k. Maintenance Information . . . . . . . . . . . . 1–2
1–2. SUPPLEMENTARY INFORMATION . . . . 1–2
1–3. ORDERING PARTS
a. Transmission Nameplate . . . . . . . . . . . . . 1–2
b. Parts Catalog . . . . . . . . . . . . . . . . . . . . . . 1–2
1–4. GENERAL DESCRIPTION
a. Transmission Design Features. . . . . . . . . 1–5
b. General Description . . . . . . . . . . . . . . . . 1–7
1–5. DIAGNOSIS
a. Before Starting . . . . . . . . . . . . . . . . . . . . . 1–7
b. CHECK TRANS Light . . . . . . . . . . . . . . 1–7
c. Range Inhibit Indicator . . . . . . . . . . . . . . 1–7
d. Allison DOC™ Personal Computer
(PC)-Based Diagnostic System . . . . . . . . 1–8
e. Troubleshooting When No Diagnostic
Codes are Present. . . . . . . . . . . . . . . . . . . 1–8
f. Troubleshooting Intermittent
Diagnostic Codes . . . . . . . . . . . . . . . . . . . 1–8
1–6. PRESERVATION AND STORAGE
a. Storage (New Transmissions,
Before Installation) . . . . . . . . . . . . . . . . . 1–9
b. Preservation Methods . . . . . . . . . . . . . . . 1–9
c. One Year Storage (Without Fluid). . . . . . 1–9
d. One Year Storage (With Fluid) . . . . . . . . 1–9
1–7. RESTORING TRANSMISSION
TO SERVICE
a. Transmission Exterior . . . . . . . . . . . . . . 1–10
b. Sealed Vent Assembly and Openings . . 1–10
c. New Transmissions . . . . . . . . . . . . . . . . 1–10
d. Stored Without Fluid . . . . . . . . . . . . . . . 1–10
e. Stored With Fluid. . . . . . . . . . . . . . . . . . 1–10
1–8. OPERATING INSTRUCTIONS . . . . . . . . 1–10
1–9. SPECIFICATIONS AND DATA . . . . . . . . 1–10
1–10. ELECTROMAGNETIC/RADIO
FREQUENCY INTERFERENCE . . . . . . . 1–21
Section 2. PREVENTIVE MAINTENANCE
2–1. SCOPE . . . . . . . . . . . . . . . . . . . . . . . . . . . . . . 2–1
2–2. PERIODIC INSPECTIONS AND CARE
a. Transmission Inspection . . . . . . . . . . . . . 2–1
b. Vehicle Inspection . . . . . . . . . . . . . . . . . . 2–1
c. Welding . . . . . . . . . . . . . . . . . . . . . . . . . . 2–1
2–3. IMPORTANCE OF PROPER
TRANSMISSION FLUID LEVEL. . . . . . . . 2–1
2–4. TRANSMISSION FLUID CHECK
a. Fluid Check Procedure . . . . . . . . . . . . . . 2–2
b. Cold Check Procedure . . . . . . . . . . . . . . . 2–4
c. Hot Check Procedure . . . . . . . . . . . . . . . . 2–4
d. Consistency of Readings . . . . . . . . . . . . . 2–5
2–5. KEEPING FLUID CLEAN. . . . . . . . . . . . . . 2–5
2–6. FLUID RECOMMENDATIONS . . . . . . . . . 2–5
2–7. TRANSMISSION FLUID AND FILTER
CHANGE INTERVALS
a. Frequency. . . . . . . . . . . . . . . . . . . . . . . . . 2–6
b. Abnormal Conditions. . . . . . . . . . . . . . . . 2–6
c. Fluid Analysis . . . . . . . . . . . . . . . . . . . . . 2–6
2–8. TRANSMISSION FLUID CONTAMINATION
a. Fluid Examination . . . . . . . . . . . . . . . . . . 2–6
b. Water . . . . . . . . . . . . . . . . . . . . . . . . . . . . 2–6
c. Engine Coolant. . . . . . . . . . . . . . . . . . . . . 2–9
d. Flush Oil Cooler. . . . . . . . . . . . . . . . . . . . 2–9
TABLE OF CONTENTS

viii Copyright © 2004 General Motors Corp.
1000 AND 2000 PRODUCT FAMILIES SERVICE MANUAL
Paragraph PageParagraph Page
2–9. TRANSISSION FLUID AND FILTER
CHANGE PROCEDURE
a. Drain Fluid . . . . . . . . . . . . . . . . . . . . . . . 2–9
b. Replace Control-Main Filter . . . . . . . . . . 2–9
c. Refill Transmission . . . . . . . . . . . . . . . . . 2–9
2–10. VENT ASSEMBLY
a. Location and Purpose . . . . . . . . . . . . . . 2–10
b. Maintenance . . . . . . . . . . . . . . . . . . . . . 2–10
2–11. MAIN PRESSURE CHECK
PROCEDURE. . . . . . . . . . . . . . . . . . . . . . . 2–10
2–12. TRANSMISSION STALL TEST AND
NEUTRAL COOL-DOWN CHECK
a. Purpose . . . . . . . . . . . . . . . . . . . . . . . . . 2–12
b. Stall Testing Preparation . . . . . . . . . . . . 2–12
c. Performing a Transmission
Stall Test . . . . . . . . . . . . . . . . . . . . . . . . 2–12
d. Driving Transmission Stall Test . . . . . . 2–13
e. Driving Transmission Stall Testing
Preparation. . . . . . . . . . . . . . . . . . . . . . . 2–13
f. Performing a Driving Transmission
Stall Test . . . . . . . . . . . . . . . . . . . . . . . . 2–14
g. Neutral Cool-Down Check Procedure . 2–14
h. Transmission Stall Test Results . . . . . . 2–14
2–13. FLUID LEAK DIAGNOSIS
a. Finding the Leak . . . . . . . . . . . . . . . . . . 2–15
b. Powder Method . . . . . . . . . . . . . . . . . . . 2–15
c. Black Light and Dye Method . . . . . . . . 2–16
d. Repairing the Leak . . . . . . . . . . . . . . . . 2–16
2–14. ON-VEHICLE MAINTENANCE . . . . . . . 2–16
Section 3. GENERAL OVERHAUL
INFORMATION
3–1. SCOPE . . . . . . . . . . . . . . . . . . . . . . . . . . . . . 3–1
3–2. TOOLS AND EQUIPMENT
a. Improvised Tools and Equipment . . . . . 3–1
b. Special Tools . . . . . . . . . . . . . . . . . . . . . 3–1
c. Mechanic’s Tools and
Shop Equipment . . . . . . . . . . . . . . . . . . . 3–1
3–3. REPLACEMENT PARTS
a. Ordering Information . . . . . . . . . . . . . . . 3–9
b. Parts Normally Replaced
at Overhaul . . . . . . . . . . . . . . . . . . . . . . . 3–9
3–4. CAREFUL HANDLING . . . . . . . . . . . . . . . 3–9
3–5. CLEANING AND INSPECTION
a. Dirt Causes Malfunction . . . . . . . . . . . . . 3–9
b. Cleaning Parts . . . . . . . . . . . . . . . . . . . . 3–9
c. Cleaning Bearings . . . . . . . . . . . . . . . . . 3–9
d. Keeping Bearings Clean. . . . . . . . . . . . . 3–9
e. Inspecting Bearings . . . . . . . . . . . . . . . . 3–10
f. Inspecting Cast Parts and
Machined Surfaces . . . . . . . . . . . . . . . . 3–10
g. Inspecting Bushings and
Thrust Washers . . . . . . . . . . . . . . . . . . . 3–10
h. Inspecting Sealrings and Gaskets. . . . . 3–10
i. Inspecting Gears. . . . . . . . . . . . . . . . . . 3–11
j. Inspecting Splined Parts. . . . . . . . . . . . 3–11
k. Inspecting Threaded Parts . . . . . . . . . . 3–11
l. Inspecting Retaining Rings . . . . . . . . . . 3–11
m. Inspecting Springs. . . . . . . . . . . . . . . . . 3–11
n. Inspecting Clutch Plates . . . . . . . . . . . . 3–11
o. Inspecting Swaged and
Interference-Fit Parts . . . . . . . . . . . . . . 3–12
p. Inspecting Sealing Surfaces . . . . . . . . . 3–12
3–6. ASSEMBLY PROCEDURES
a. Parts Lubrication . . . . . . . . . . . . . . . . . . 3–12
b. Grease Used for Assembly. . . . . . . . . . 3–12
c. Sealing Compounds and
Nonsoluble Greases . . . . . . . . . . . . . . . 3–12
d. Clutches and Pistons . . . . . . . . . . . . . . 3–12
e. Threaded Plugs and Hydraulic
Fittings. . . . . . . . . . . . . . . . . . . . . . . . . . 3–12
f. Lip-Type Seals . . . . . . . . . . . . . . . . . . . 3–12
g. Butt-Joint/Overlap Sealrings . . . . . . . . 3–13
h. Bearings. . . . . . . . . . . . . . . . . . . . . . . . . 3–13
i. Electrical Components . . . . . . . . . . . . . 3–13
3–7. REMOVING (OR INSTALLING)
TRANSMISSION
a. Draining Transmission . . . . . . . . . . . . . 3–13
b. Disconnecting Controls . . . . . . . . . . . . 3–14
c. Uncoupling From Driveline,
Engine, and Vehicle . . . . . . . . . . . . . . . 3–14
d. Removing the Transmission. . . . . . . . . 3–14
e. Transmission Installation . . . . . . . . . . . 3–15
3–8. WEAR LIMITS. . . . . . . . . . . . . . . . . . . . . . 3–15
3–9. SPRING SPECIFICATIONS . . . . . . . . . . . 3–15
3–10. TORQUE SPECIFICATIONS . . . . . . . . . . 3–15

Copyright © 2004 General Motors Corp. ix
TABLE OF CONTENTS
Paragraph Page Paragraph Page
Section 4. TRANSMISSION DISASSEMBLY
4–1. INSTALLATION OF TRANSMISSION
INTO REPAIR STAND . . . . . . . . . . . . . . . . 4–1
4–2. INPUT SPEED SENSOR REMOVAL
(IF PRESENT). . . . . . . . . . . . . . . . . . . . . . . . 4–2
4–3. TURBINE SPEED SENSOR REMOVAL . . 4–3
4–4. OUTPUT SPEED SENSOR REMOVAL
(2WD TRANSMISSIONS ONLY). . . . . . . . 4–3
4–5. NSBU SWITCH REMOVAL
(IF PRESENT). . . . . . . . . . . . . . . . . . . . . . . . 4–3
4–6. VENT REMOVAL . . . . . . . . . . . . . . . . . . . . 4–4
4–7. TORQUE CONVERTER REMOVAL. . . . . 4–5
4–8. CONVERTER HOUSING/FRONT
SUPPORT MODULE REMOVAL . . . . . . . 4–6
4–9. ROTATING CLUTCH ASSEMBLY
REMOVAL . . . . . . . . . . . . . . . . . . . . . . . . . . 4–7
4–10. OIL PAN AND SUCTION FILTER
REMOVAL . . . . . . . . . . . . . . . . . . . . . . . . . . 4–8
4–11. WIRING HARNESS ASSEMBLY
REMOVAL . . . . . . . . . . . . . . . . . . . . . . . . . . 4–9
4–12. CONTROL VALVE ASSEMBLY
REMOVAL . . . . . . . . . . . . . . . . . . . . . . . . . 4–10
4–13. REAR BALL BEARING REMOVAL . . . . 4–12
4–14. REAR COMPONENTS REMOVAL . . . . . 4–14
4–15. PARK PAWL REMOVAL . . . . . . . . . . . . . 4–16
4–16. P2 PLANETARY MODULE AND MAIN
SHAFT REMOVAL . . . . . . . . . . . . . . . . . . 4–16
4–17. C5 CLUTCH REMOVAL. . . . . . . . . . . . . . 4–17
4–18. P1 PLANETARY MODULE . . . . . . . . . . . 4–17
4–19. C4 CLUTCH REMOVAL. . . . . . . . . . . . . . 4–18
4–20. C4 CLUTCH PISTON ASSEMBLY
REMOVAL . . . . . . . . . . . . . . . . . . . . . . . . . 4–20
4–21. C3 CLUTCH REMOVAL. . . . . . . . . . . . . . 4–21
4–22. C3 CLUTCH PISTON ASSEMBLY
REMOVAL . . . . . . . . . . . . . . . . . . . . . . . . . 4–23
Section 5. MODULE REBUILD
5–1. TORQUE CONVERTER ASSEMBLY
a. Preliminary Inspection. . . . . . . . . . . . . . . 5–1
b. End Play Check . . . . . . . . . . . . . . . . . . . . 5–1
c. Leak Test . . . . . . . . . . . . . . . . . . . . . . . . . 5–2
d. Inspection of Torque Converter. . . . . . . . 5–3
5–2. ELECTRONIC COMPONENT
INSPECTION . . . . . . . . . . . . . . . . . . . . . . . . 5–5
5–3. CONVERTER HOUSING/FRONT
SUPPORT MODULE DISASSEMBLY . . . 5–6
5–4. TORQUE CONVERTER HOUSING
(WITHOUT COOLER MANIFOLD)
a. Disassembly . . . . . . . . . . . . . . . . . . . . . . . 5–9
b. Assembly . . . . . . . . . . . . . . . . . . . . . . . . 5–10
5–5. TORQUE CONVERTER HOUSING (DIRECT
MOUNT; WITHOUT COOLER MANIFOLD)
a. Disassembly . . . . . . . . . . . . . . . . . . . . . . 5–11
b. Assembly. . . . . . . . . . . . . . . . . . . . . . . .5–11
5–6. TORQUE CONVERTER HOUSING
(WITH COOLER MANIFOLD)
a. Disassembly . . . . . . . . . . . . . . . . . . . . . . 5–12
b. Assembly . . . . . . . . . . . . . . . . . . . . . . . . 5–13
5–7. MAIN PUMP ASSEMBLY
a. Main Pump Disassembly. . . . . . . . . . . . 5–15
b. Main Pump Inspection . . . . . . . . . . . . . . 5–16
c. Main Pump Bushing Replacement . . . . 5–19
d. Main Pump Dowel Pin Replacement. . . 5–20
e. Wear Plate Inspection . . . . . . . . . . . . . . 5–21
f. Main Pump Assembly . . . . . . . . . . . . . . 5–21
5–8. FRONT SUPPORT ASSEMBLY
a. Front Support Disassembly . . . . . . . . . . 5–22
b. Ground Sleeve Inspection . . . . . . . . . . . 5–27
c. Ground Sleeve Replacement . . . . . . . . . 5–28
d. Ground Sleeve Needle Bearing
Replacement. . . . . . . . . . . . . . . . . . . . . . 5–30
e. Ground Sleeve Bushing Replacement . . 5–31
f. Front Support Thrust Washer
Inspection . . . . . . . . . . . . . . . . . . . . . . . . 5–32
g. Front Support Assembly . . . . . . . . . . . . 5–32
5–9. CONVERTER HOUSING/FRONT
SUPPORT MODULE ASSEMBLY. . . . . . 5–37

x Copyright © 2004 General Motors Corp.
1000 AND 2000 PRODUCT FAMILIES SERVICE MANUAL
Paragraph PageParagraph Page
5–10. ROTATING CLUTCH MODULE
a. Disassembly of Rotating Clutch
Module. . . . . . . . . . . . . . . . . . . . . . . . . . 5–40
b. Turbine Shaft Inspection . . . . . . . . . . . . 5–47
c. Turbine Shaft Bushing Replacement . . 5–48
d. Rotating Clutch Housing Inspection . . . 5–49
e. Rotating Clutch Housing Bushing
Replacement . . . . . . . . . . . . . . . . . . . . . 5–50
f. Rotating Clutch Housing Tone Wheel
Replacement . . . . . . . . . . . . . . . . . . . . . 5–51
g. C1 Clutch Friction Plate Inspection . . . 5–53
h. C1 Clutch Reaction Plate Inspection . . 5–54
i. C1 Clutch Backplate Inspection . . . . . . 5–55
j. C2 Clutch Friction Plate Inspection . . . 5–56
k. C2 Clutch Reaction Plate Inspection . . 5–57
l. C1 Piston Housing Inspection. . . . . . . . 5–57
m. Rotating Clutch Thrust Washer
Inspection . . . . . . . . . . . . . . . . . . . . . . . 5–58
n. Assembly of Rotating Clutch Module . 5–58
5–11. MAIN HOUSING ASSEMBLY
a. Disassembly of Selector Shaft
and Detent Lever . . . . . . . . . . . . . . . . . . 5–68
b. Assembly of Selector Shaft and
Detent Lever . . . . . . . . . . . . . . . . . . . . . 5–71
c. Nameplate Replacement . . . . . . . . . . . . 5–73
d. Main Housing Dowel Pin
Replacement . . . . . . . . . . . . . . . . . . . . . 5–74
e. Replacement of Fill Tube Plug . . . . . . . 5–74
f. Replacement of Vent Assembly . . . . . . 5–75
5–12. RING GEAR AND CLUTCH COMPONENT
INSPECTIONS
a. C3 Clutch Component Inspection . . . . 5–75
b. C3 Clutch Backplate Assembly
Thrust Plate Replacement . . . . . . . . . . . 5–79
c. C4 Clutch Component Inspection. . . . . 5–80
d. C5 Clutch Component Inspection . . . . . 5–83
e. P1 Ring Gear Inspection . . . . . . . . . . . . 5–85
5–13. MAIN SHAFT INSPECTION . . . . . . . . . . 5–85
5–14. P1 PLANETARY MODULE
a. P1 Planetary Module Disassembly . . . . 5–86
b. P1 Planetary Carrier Assembly
Inspection . . . . . . . . . . . . . . . . . . . . . . . 5–86
c. P2 Planetary Ring Gear Inspection . . . . 5–87
d. P1 Planetary Carrier Bushing
Replacement . . . . . . . . . . . . . . . . . . . . . 5–87
e. P1 Planetary Carrier Thrust Washer
Inspection . . . . . . . . . . . . . . . . . . . . . . . 5–88
f. P1 Planetary Module Assembly . . . . . . 5–88
5–15. P2 PLANETARY MODULE
a. P2 Planetary Module Disassembly . . . 5–89
b. P2 Planetary Carrier Assembly
Inspection . . . . . . . . . . . . . . . . . . . . . . . 5–89
c. P3 Planetary Ring Gear Inspection . . . . 5–90
d. P2 Planetary Carrier Bushing
Replacement . . . . . . . . . . . . . . . . . . . . . 5–90
e. P2 Planetary Module Assembly . . . . . . 5–91
5–16. P3 PLANETARY CARRIER ASSEMBLY
a. P3 Planetary Carrier Assembly
Inspection . . . . . . . . . . . . . . . . . . . . . . . 5–91
b. P3 Planetary Carrier Bearing Race
Replacement . . . . . . . . . . . . . . . . . . . . . 5–92
5–17. REAR COVER ASSEMBLY
a. Disassembly. . . . . . . . . . . . . . . . . . . . . . 5–94
b. Rear Cover Retaining Ring
Replacement . . . . . . . . . . . . . . . . . . . . . 5–96
c. Output Shaft Bushing Inspection
(2WD Transmissions Only) . . . . . . . . . 5–96
d. Output Shaft Bushing Inspection
(4WD Transmissions Only) . . . . . . . . . 5–96
e. Output Shaft Bushing Replacement . . . 5–97
f. Assembly of Rear Cover . . . . . . . . . . . . 5–98
5–18. OUTPUT YOKE INSPECTION . . . . . . . . 5–99
5–19. CONTROL VALVE MODULE
a. Disassembly of Control
Valve Assembly . . . . . . . . . . . . . . . . . 5–100
b. Disassembly of Shift Valve Body. . . . 5–104
c. Disassembly of Modulated Main Valve
Body . . . . . . . . . . . . . . . . . . . . . . . . . . 5–107
d. A/B Solenoid Bracket Inspection . . . . 5–108
e. Assembly of Shift Valve Body . . . . . . 5–108

Copyright © 2004 General Motors Corp. xi
TABLE OF CONTENTS
Paragraph Page Paragraph Page
f. Disassembly of the Main Valve
Body. . . . . . . . . . . . . . . . . . . . . . . . . . . 5–111
g. Dowel Pin Replacement . . . . . . . . . . . 5–113
h. Assembly of the Main Valve Body . . . 5–114
i. Assembly of Control Valve
Assembly . . . . . . . . . . . . . . . . . . . . . . . 5–115
j. Assembly of Modulated Main Valve
Body . . . . . . . . . . . . . . . . . . . . . . . . . . . 5–120
Section 6. TRANSMISSION ASSEMBLY
6–1. C3 CLUTCH INSTALLATION . . . . . . . . . . 6–1
6–2. P1 PLANETARY MODULE AND
C4 CLUTCH INSTALLATION . . . . . . . . . . 6–3
6–3. C5 CLUTCH REACTION PLATE
SELECTION . . . . . . . . . . . . . . . . . . . . . . . . . 6–7
6–4. P2 PLANETARY MODULE AND
MAIN SHAFT INSTALLATION . . . . . . . . 6–9
6–5. C5 CLUTCH INSTALLATION . . . . . . . . . 6–10
6–6. PARK PAWL INSTALLATION . . . . . . . . 6–11
6–7. OUTPUT SHAFT AND P3 PLANETARY
CARRIER ASSEMBLY
INSTALLATION . . . . . . . . . . . . . . . . . . . . 6–12
6–8. REAR COVER ASSEMBLY
INSTALLATION . . . . . . . . . . . . . . . . . . . . 6–12
6–9. CONTROL VALVE ASSEMBLY
INSTALLATION . . . . . . . . . . . . . . . . . . . . 6–15
6–10. WIRING HARNESS ASSEMBLY
INSTALLATION . . . . . . . . . . . . . . . . . . . . 6–17
6–11. OIL PAN AND SUCTION FILTER
INSTALLATION . . . . . . . . . . . . . . . . . . . . 6–18
6–12. ROTATING CLUTCH ASSEMBLY
INSTALLATION . . . . . . . . . . . . . . . . . . . . 6–19
6–13. CONVERTER HOUSING/FRONT
SUPPORT MODULE INSTALLATION . . 6–20
6–14. REAR COVER SELECTIVE
SPACER INSTALLATION
(2WD TRANSMISSIONS ONLY). . . . . . . 6–22
6–15. REAR COVER SELECTIVE
SPACER INSTALLATION
(4WD TRANSMISSIONS ONLY). . . . . . . 6–23
6–16. TRANSMISSION END PLAY CHECK . . 6–25
6–17. TORQUE CONVERTER
INSTALLATION . . . . . . . . . . . . . . . . . . . . 6–26
6–18. NSBU SWITCH INSTALLATION
(IF PRESENT). . . . . . . . . . . . . . . . . . . . . . . 6–28
6–19. REAR SEAL INSTALLATION
(2WD TRANSMISSIONS ONLY). . . . . . . 6–31
6–20. OUTPUT NUT INSTALLATION
(4WD TRANSMISSIONS ONLY). . . . . . . 6–31
6–21. VENT INSTALLATION . . . . . . . . . . . . . . 6–33
6–22, INPUT SPEED SENSOR
INSTALLATION . . . . . . . . . . . . . . . . . . . . 6–33
6–23. TURBINE SPEED SENSOR
INSTALLATION . . . . . . . . . . . . . . . . . . . . 6–34
6–24. OUTPUT SPEED SENSOR
INSTALLATION
(2WD TRANSMISSIONS ONLY). . . . . . . 6–34
6–25. REMOVAL OF TRANSMISSION FROM
REPAIR STAND. . . . . . . . . . . . . . . . . . . . . 6–35
Section 7. WEAR LIMITS AND
SPRING DATA
7–1. WEAR LIMITS DATA
a. Maximum Variations . . . . . . . . . . . . . . . . 7–1
b. Cleaning and Inspection. . . . . . . . . . . . . . 7–1
7–2. SPRING DATA
a. Spring Replacement. . . . . . . . . . . . . . . . . 7–1
b. Inspection . . . . . . . . . . . . . . . . . . . . . . . . . 7–1
Section 8. CUSTOMER SERVICE
8–1. OWNER ASSISTANCE . . . . . . . . . . . . . . . . 8–1
8–2. SERVICE LITERATURE. . . . . . . . . . . . . . . 8–2

xii Copyright © 2004 General Motors Corp.
1000 AND 2000 PRODUCT FAMILIES SERVICE MANUAL
LIST OF FOLDOUT ILLUSTRATIONS
(Back of Service Manual)
CROSS-SECTION VIEWS
Foldout
1 1000 Product Family
2 2000 Product Family
3 2000 Product Family with Park Pawl
4 1000 Product Family Direct Mount with Transfer Case Adapter
EXPLODED VIEWS
5A SAE No. 3 Torque Converter Housing with Integral Cooling Ports
5B SAE No. 2 Torque Converter Housing with Manifold
5C SAE No. 3 Torque Converter Housing with Manifold
5D Direct Mount—Torque Converter Housing
6 Converter Housing/Front Support Module, Rotating Clutch Housing, and C3 Clutch Components
6A Converter Housing/Front Support Module Components
7 Front Support Module Components
8 Main Pump Assembly Components
9 Front Support Assembly Components
10 Rotating Clutch Assembly Components
11 Oil Pan and Suction Filter Components
12 Main Housing Components
13 C4 and C5 Clutch Components
14,A P1 Planetary Module, P2 Planetary Module, and Main Shaft Components
14,B P2 Planetary Module Components
14,C P3 Planetary Module
15,A P1 Planetary Carrier Assembly Components
15,B P2 Planetary Carrier Assembly Components
16,A P3 Planetary Assembly, Output Shaft, C5 Piston Return Assembly, and Park Pawl Components
16,B Rear Cover Assemblies
17 P3 Planetary Carrier Assembly
18A Rear Cover Assembly Components, 10 x 3
18B Rear Cover Assembly Components, Non-Park Brake
18C Rear Cover Assembly Components, Transfer Case
18D Rear Cover Assembly Components, 9 x 3
19A Control Valve Assembly Components
19B Shift Valve Body Assembly Components
19C Main Valve Body Assembly Components
19D Modulated Main Valve Body
20 Vent Hose and Yokes/Flanges
21 1000 and 2000 Product Families Hydraulic Schematic—Neutral/Park
22 1000 and 2000 Product Families Hydraulic Schematic—First Range
23 1000 and 2000 Product Families Hydraulic Schematic—Second Range
24 1000 and 2000 Product Families Hydraulic Schematic—Third Range
25 1000 and 2000 Product Families Hydraulic Schematic—Fourth Range
26 1000 and 2000 Product Families Hydraulic Schematic—Fifth Range
27 1000 and 2000 Product Families Hydraulic Schematic—Reverse (With N04 Software and Later)
28 1000 and 2000 Product Families Hydraulic Schematic—Reverse (Prior to and Including N04 Software)
29 1000 and 2000 Product Families Hydraulic Schematic—Default Reverse (“Limp Home”)
30 1000 and 2000 Product Families Hydraulic Schematic—Default Forward (3rd Range “Limp Home”)

Copyright © 2004 General Motors Corp. 1–1
1–1. SCOPE OF MANUAL
a. Transmission Product Families And Model
Years.
The 1000 and 2000 Product Families include
the 1000/2000/2400 Series. The following provides
guidance in distinguishing between the various
1000 and 2000 Product Families transmissions and
1000/2000/2400 Series transmissions models and the
content of the various model years. Model Year and se-
rial number breaks identify engineering changes.
b. Model Year 04 (MY04
) (refer to SIL 13-1K2K-03)
.
MY04, June 2003, introduced modulated main pres-
sure hardware and the associated calibration software.
The serial number breaks for MY04 are:
•
Indianapolis units:
— 6310292155 through 6310292563
6310296468 through 6310296471
6310301450 through 6310301451
6310303122 through 6310303124
6310307722—start of MY04 production
•
Baltimore units:
— 6320218358 through 6320218387
6320247492 through 6320248001
6320269500—start of MY04 production
c. MY04 Parts Changes.
MY04 parts and former
parts are not interchangeable. Parts changed by MY04
are:
•
Internal Wiring Harness
•
Separator Plate
•
Modulated Main Body Assembly
•
Modulated Main Body
•
Shift Valve Body
•
Main Valve Body
•
Control Main Valve
•
Control Main Regulator and Control Main
Relief Spring
•
Main Pressure Regulator Valve
d. Model Year 04i (MY04i)
(refer to SIL 3-1K2K-04).
1000 and 2000 Product Families MY04i serial number
breaks are:
•
S/N 6310374684 (Indianapolis)
•
S/N 6320367833 (Baltimore)
e. MY04i Parts Changes.
MY04i parts and former
parts are not interchangeable. Parts changed by MY04i
are:
•
Front Support Assembly and Bearing
•
Main Regulator Valve
•
Converter Relief Valve
•
Lube Regulator Valve
•
Lube Regulator Spring
•
Lube Regulator Stop
•
Lube Regulator O-ring deleted
•
C1 Clutch Backfill Valve
•
C1 Clutch Backfill Spring
•
C1 Clutch Backfill Stop
•
Converter Flow Valve
•
Retaining Clip replaces a retaining pin
•
Converter/Main Housing Separator Plate
•
Pump Assembly
•
Pump Wear Plate
f. Improved Shift Valve Body Casting
. Serial
number breaks for 1000 and 2000 Product Families
improved Shift Valve Body casting are:
•
Indianapolis Units—6310368401
•
Baltimore Units—6320354862
g. Vocational Models
(refer to WATCH 309)
.
Be-
ginning January 2004, Allison Transmission began
shipping new 1000 and 2000 Product Families trans-
mission models for North America. 1000 and 2000
Product Families models are:
•
Emergency Vehicle Series—1000 EVS,
2100 EVS, 2200 EVS, 2500 EVS
•
Highway Series—1000 HS, 2100 HS,
2200 HS, 2500 HS
•
Motorhome Series—1000 MH, 2100 MH,
2200 MH, 2500 MH
•
Pupil Transport/Shuttle Series—1000 PTS,
2100 PTS, 2200 PTS, 2500 PTS
•
Rugged Duty Series—1000 RDS, 2100 RDS,
2200 RDS, 2500 RDS
•Specialty Series—1000 SP, 2100 SP, 2200 SP,
2500 SP
•Bus Series—B210, B220
SECTION 1—GENERAL INFORMATION

1–2 Copyright © 2004 General Motors Corp.
1000 AND 2000 PRODUCT FAMILIES SERVICE MANUAL
h. Vocational Model Nomenclature. The first digit
of the nomenclature indicates the product family—
1000, 2000. The second digit (0–4) indicates close
ratio, or (5) wide ratio.
i. Content and Organization. This Service Manual
describes overhaul procedures for 1000 and 2000 Prod-
uct Families automatic transmissions (Figures 1–1 and
1–2). All 1000 and 2000 Product Families vocational
models are included in this manual as are all 1000/
2000/2400 Series transmissions.
•Major transmission components are described
and their functions explained.
•Detailed instructions are provided for
disassembly, rebuild, and re-assembly.
•Part inspection instructions are in Section 3.
•Wear limits and spring data are in Section 7.
j. Illustrations
1. The text is supported with line drawings, ex-
ploded, and cross-sectional views. Overhaul
procedures are illustrated by line drawings.
Cross-sections show the relationship of assem-
bled parts. Cross-sections and exploded views
are on foldout pages in the back of the manual.
2. Illustrations show correct procedures for all
models—including models not illustrated.
k. Maintenance Information. Each task described
in this manual has been successfully completed by
service organizations and individuals. Not every
service organization or individual possesses the
required special tooling, training, or experience to
perform all described tasks. However, any task may be
performed if the following conditions are met:
1. The organization or individual has the required
knowledge of the task through:
•Formal instruction at Allison Transmission
or a Distributor training facility.
•On-the-job instruction by an Allison
Transmission or Distributor representative.
•Experience in performing the task.
2. The work environment is suitable to prevent
contamination or damage to transmission parts
or assemblies.
3. The required tools and fixtures, listed in
Table 3–1 (Section 3 of this manual), are avail-
able.
4. Reasonable and prudent maintenance prac-
tices are used.
NOTE:
Service organizations and individuals are
encouraged to contact their local Allison
Transmission Distributor for information and
guidance on any task outlined in this manual.
1–2. SUPPLEMENTARY
INFORMATION
Supplementary information will be issued, as required,
if any changes occur after publication of this manual.
Check with your dealer or distributor to be sure you
have the latest information.
1–3. ORDERING PARTS
a. Transmission Nameplate. The nameplate (1)
(Figure 1–3) is located on the right side of the
transmission. The nameplate will be one of two styles
(Figures 1–4 and 1–5). Both nameplates are imprinted
with the transmission model, serial number,
transmission identification number, engineering group
number, engineering feature configuration number,
and date of manufacture. Use all of these numbers
when ordering replacement parts or requesting service
information.
b. Parts Catalog. Replacement parts are listed in
Parts Catalog PC3062EN. Do not order by the item
numbers used on exploded views in this manual. Use
the Parts Catalog to determine the correct part number.
Order all replacement parts from your distributor or
authorized dealer. Check the Yellow Pages for your
nearest authorized service outlet. Listings are under
Transmission—Truck, Tractor, Etc.

Copyright © 2004 General Motors Corp. 1–3
GENERAL INFORMATION
Figure 1–1. 1000 and 2000 Product Families Transmission—Left-Front View
Figure 1–2. 1000 and 2000 Product Families Transmission—Right-Rear View
TURBINE SPEED
SENSOR
OIL VENT
(BREATHER)
INPUT SPEED
SENSOR
NSBU SWITCH
PARKING BRAKE
MOUNTING PROVISION
OUTPUT SPEED SENSOR
SELECTOR SHAFT
CONTROL MAIN OIL FILTER
V04779.03.00
SAE 6-BOLT
PTO PAD
(DRIVE GEAR OPTIONAL)
AVAILABLE
OIL FILL TUBE
LOCATION
TURBINE SPEED
SENSOR
OUTPUT SPEED
SENSOR
OIL VENT
(BREATHER)
INPUT SPEED
SENSOR
MOUNTING PAD
(SAE #3 HOUSING ONLY)
MAIN ELECTRICAL
CONNECTOR
V04780.01.04
SAE 6-BOLT
PTO PAD
(DRIVE GEAR OPTIONAL)
AVAILABLE
OIL FILL TUBE
LOCATION
COOLER PORTS
PROVISION FOR
CUSTOMER-SUPPLIED
SPEED SENSOR OR
TACHOGRAPH
(OPRIONAL)

1–4 Copyright © 2004 General Motors Corp.
1000 AND 2000 PRODUCT FAMILIES SERVICE MANUAL
Figure 1–3. 1000 and 2000 Product Families Transmission Nameplate Location
Legend
Figure 1–4. 1000 and 2000 Product Families Transmission Nameplate Components
(1) Model (Series) (4) Transmission Identification Number
(2) Date of Manufacture (5) Engineering Group Number
(3) Engineering Feature Configuration Number (6) Serial Number
1
V06183
DIV. OF GENERAL MOTORS CORP.
DIV. OF GENERAL MOTORS CORP.
INDIANAPOLIS,INDIANA, USA
INDIANAPOLIS,INDIANA, USA
XX–XXXX
XX–XXXX
XX–XXXX
XXXXXXXXXX XXXXXXXX
XXXXXXXXXX XXXXX
XX
XX–XXXX
XX–XXXX
XX–XXXX
XX–XXXX
XX–XXXX
XX–XXXX
XX–XXXX
XX–XXXX
XX–XXXX
MODEL
SERIAL NO. EFCN TID
DATE
DIV. OF GENERAL MOTORS CORP.
DIV. OF GENERAL MOTORS CORP.
INDIANAPOLIS,INDIANA, USA
INDIANAPOLIS,INDIANA, USA
XX–XXXX
XX–XXXX
XX–XXXX
XXXXXXXXXX XXXXXXXX
XXXXXXXXXX XXXXX
XX
XX–XXXX
XX–XXXX
XX–XXXX
XX–XXXX
XX–XXXX
XX–XXXX
XX–XXXX
XX–XXXX
XX–XXXX
MODEL
SERIAL NO. EFCN TID
DATE
V06533

Copyright © 2004 General Motors Corp. 1–5
GENERAL INFORMATION
Legend
Figure 1–5. 1000 and 2000 Product Families Transmission Nameplate Components (Before March, 2000)
(1) Model (Series) (4) Engineering Feature Configuration Number
(2) Engineering Group Number (5) Serial Number
(3) Transmission Identification Number (6) Date of Manufacture
E
C
A
P
S
O
R
E
A
E
L
I
B
O
M
O
T
U
A
D
E
T
I
N
U
A
C
I
R
E
M
A
F
O
S
R
E
K
R
O
W
T
N
E
M
E
L
P
M
I
L
A
R
U
T
L
U
C
I
R
G
A
D
N
A
UAW
UAW
933
DIVISION OF GENERAL MOTORS CORP.
DIVISION OF GENERAL MOTORS CORP.
INDIANAPOLIS,INDIANA
INDIANAPOLIS,INDIANA
SERIAL NO.
MODEL
EFCN
DATE TID
XX–XXXX
XX–XXXX
XX–XXXX
XX–XXXX
XX–XXXX
XX–XXXX
XX–XXXX
XX–XXXX
XX–XXXX
XX–XXXX
XXXXXXX
XXXXXXXXXX
XXXXX XX
1000SERIES
1–4. GENERAL DESCRIPTION
a. Transmission Design Features. Allison 1000 and
2000 Product Families (Figures 1–1 and 1–2) are
torque-converter driven, electronically controlled,
fully automatic transmission systems. The 1000 and
2000 Product Families transmissions have up to five
forward speeds, neutral, and reverse. The fifth range
has an overdrive gear ratio. The 1000 and 2000 Product
Families incorporate a variety of standard and optional
design features.
1. Transmission-to-Engine Coupling. The con-
verter housings of 1000 and 2000 Product Fami-
lies transmissions mate directly to SAE No. 2
or No. 3 flywheel housings or to the engine
block in some cases. Flexplate drive is used for
engine-to-transmission torque transfer.
2. Torque Converter. Several torque converters are
available to match the transmissions to a wide
variety of diesel and gasoline engines. The
torque converter is a single-stage, polyphase,
three-element unit, consisting of a pump, sta-
tor, and turbine. At lower output speeds, the
torque converter multiplies torque and provides
a fluid coupling to the engine. At higher speeds,
the torque converter clutch (TCC) is automati-
cally engaged to provide direct drive from the
engine to the transmission. Hydraulic fluid for
converter charging pressure comes from the
sump and is supplied by the input pump. The
torque converter clutch is applied or released by
changing direction of fluid in the torque con-
verter. An integral converter damper minimizes
the need for additional engine vibration control.
3. Planetary Gearing. The planetary gear train in-
cludes three constant-mesh, helical gear plane-
tary sets. By the engagement of clutches in
various combinations, the planetary sets act
singly or together to provide five forward
ranges, neutral, and reverse.
4. Clutches. Five clutches (two rotating and three
stationary) direct the flow of torque through
the transmission. All range clutches are hy-
draulically-actuated and spring-released, with
automatic wear compensation. Clutches are
cooled by the transmission fluid. The transmis-
sion electronic control module signals solenoid
valves to apply and release clutches based on
speed and power combinations and the range
selected by the operator.

1–6 Copyright © 2004 General Motors Corp.
1000 AND 2000 PRODUCT FAMILIES SERVICE MANUAL
5. Hydraulic System. A common hydraulic sys-
tem serves the torque converter and the trans-
mission. Transmission fluid for all hydraulic
operations, lubrication, and cooling comes
from the sump and is supplied by the charging
pump.
6. Transmission Fluid Filtration. Fluid filtration
is provided by two filter systems. A suction fil-
ter, located in the sump, provides general pro-
tection to the entire hydraulic system by
filtering large particulates. A spin-on filter pro-
vides full-time protection for the control sole-
noids and multipass protection for the entire
system. The spin-on filter is externally located
on the converter housing at the lower left front
of the transmission.
7. Electronic Controls
•A microcomputer provides electronically-
controlled automatic gear selection and
automatic engagement of the torque
converter clutch. The microcomputer is an
independent controller and is referred to as
a Transmission Control Module, or TCM.
•The electronic control system uses adaptive
logic to provide optimum shift quality.
Driving efficiency is improved by shifting
at the exact programmed transmission shift
point for every engine/transmission/vehicle
combination. The electronic controls can be
customized for four-speed or five-speed
operation to meet vocational requirements.
8. Remote Oil Cooler. Ports for remote-mount oil
cooler lines are located on the bottom surface
of the converter housing near the converter
housing/main housing splitline or on the right
side of the direct-mount converter housing.
Remote oil-to-water coolers require plumbing
for transmission fluid and engine-cooling
water. Remote oil-to-air coolers may also be
used and only transmission fluid lines need to
be provided. Heat is transferred from the
transmission fluid to either water or air
depending upon the cooler type used.
9. Oil Fill Tube/Dipstick Provisions. All 1000 and
2000 Product Families models have a fill tube/
dipstick provision on both sides of the
transmission. The fill tube and dipstick are
OEM-installed and adapted as specified by the
vehicle manufacturer. A plug is installed in the
unused location.
10. Parking Pawl/Parking Brake
•All 1000 models, 2200 models, 1000 Series™,
and 2400 Series™ transmissions have a
park pawl. The internal parking pawl is
engaged by selection of the P(Park)
position on the shift selector. The parking
pawl is not available on 2100 and 2500
models and 2000 Series™ models.
•Some 1000 and 2000 Product Families
models are available with an optional rear
cover that accommodates an OEM-installed
two-shoe, expanding-type drum brake. All
parking brake controls and linkages are OEM-
supplied.
11. Power Takeoff. 1000 and 2000 Product
Families transmissions, except Highway Series
and Pupil Transport/Shuttle Series, and all
1000/2000/2400 Series transmissions have a
provision to drive a power takeoff (PTO) unit
mounted on the left and/or right side of the
transmission housing. The optional PTO drive
gear is driven by the transmission torque
converter turbine, with speed and torque
reflecting engine input and the characteristics
of the torque converter. PTO units and
associated controls are provided by the vehicle
manufacturer and/or body builder.
12. Output Yokes/Flanges. A variety of output
yokes or flanges are available to meet vehicle
driveline requirements. Yokes or flanges are
OEM-installed and are adapted as specified by
the vehicle manufacturer.
WARNING!
Operation with excessive loads can cause trans-
mission damage and unexpected vehicle move-
ment. To help avoid injury, property damage,
and/or transmission damage, do not exceed
11 800 kg (26,000 lbs) GCW or the OEM vehicle
rating, whichever is less.

Copyright © 2004 General Motors Corp. 1–7
GENERAL INFORMATION
b. General Description. Several transmission
configurations are available within the 1000 and 2000
Product Families.
1–5. DIAGNOSIS
NOTE:
Refer to the TS3192EN, 1000 and 2000 Product Fam-
ilies Troubleshooting Manual, for in-depth trouble-
shooting procedures.
a. Before Starting. Before attempting to repair the
transmission, identify the faulty condition and its
probable cause.
b. CHECK TRANS Light
1. The CHECK TRANS light is original equip-
ment manufacturer (OEM)-supplied and usu-
ally located on the vehicle’s instrument panel.
2. The CHECK TRANS light is illuminated
briefly during vehicle start-up as a bulb check.
NOTE:
The CHECK ENGINE light may serve the CHECK
TRANS function for vehicles which are compliant
to industry On Board Diagnostics II (OBD-II) re-
quirements.
3. When the CHECK TRANS light is “ON”,
shifts may be restricted by the Transmission
Control Module (TCM) as follows:
•When the TCM senses abnormal
conditions.
•The transmission may be locked in the
range it was in when the problem was
detected.
•The transmission may continue to operate
with inhibited shifting.
•The TCM may not respond to shift selector
requests.
•Direction changes and shifts from neutral-
to-range may not occur.
•Whenever the CHECK TRANS light is
displayed, the TCM logs a diagnostic code
in memory. These diagnostic codes can be
accessed through the PC-based Allison
DOC™ diagnostic systems.
NOTE:
Diagnostic codes can be logged without illuminating
the CHECK TRANS light. This occurs when the
TCM senses a problem, but determines the problem
won’t cause immediate transmission damage or
dangerous performance.
c. Range Inhibit Indicator
1. Some conditions detected by the TCM cause
the transmission to be locked in one range.
When this occurs, the torque converter clutch
is automatically disengaged. Shifts out of
N(Neutral) may be inhibited.
1000* Heavy-duty automatic transmission with
parking pawl
Maximum GVW 19,850 lb
Maximum GCW 26,000 lb
2000
2100
2500*
Heavy-duty automatic transmission
without parking pawl
Maximum GVW 30,000 lb
Maximum GCW 30,000 lb
2100 MH
2500 MH*
Heavy-duty automatic transmission with-
out parking pawl
Limited release in motorhome
applications only
Maximum GVW 28,000 lb
Maximum GCW 28,000 lb
1000 MH
2200 MH*
Heavy-duty automatic transmission with
parking pawl
Limited release in motorhome
applications only
Maximum GVW 28,000 lb
Maximum GCW 28,000 lb
2200
2400*
Heavy-duty automatic transmission with
parking pawl
Maximum GVW 26,000 lb
Maximum GCW 26,000 lb
* GVW rating, GCW rating, or OEM axle rating, whichever is less.
WARNING!
If ignition is turned “OFF” and then “ON” while
the CHECK TRANS light is displayed, the trans-
mission may remain in neutral until the code is
cleared. Leave ignition “ON” until you are in a
safe place to stop.

1–8 Copyright © 2004 General Motors Corp.
1000 AND 2000 PRODUCT FAMILIES SERVICE MANUAL
2. At the same time these events occur, a required
OEM-supplied RANGE INHIBITED light,
mounted on the dash or near the shift selector,
is illuminated. This notifies the driver that
shifting is inhibited and the shift selector may
not respond to shifts requested.
d. Allison DOC™ Personal Computer (PC)-
Based Diagnostic System. Allison Diagnostic Opti-
mized Connection™ (Allison DOC™) provides tabu-
lar, graphical, and chart displays of real-time and re-
corded TCM data. A Help system is incorporated into
the Allison DOC™ software. Allison Diagnostic Opti-
mized Connection™ (Allison DOC™) software and
interface devices are available through Allison Trans-
mission tool sources.
1. A PC serves as the receiver/transmitter/display
medium that allows the service technician to
communicate with the TCM. Typical trouble-
shooting activities performed are installation
checkout and diagnostic trouble code (DTC)
retrieval.
2. The Allison DOC™ Help system contains in-
formation for performing the following:
•Display (retrieve) DTCs. Transmission
diagnostic codes begin with P0, P1, U1, or
U2 followed immediately by three
additional numbers. For a complete list of
codes and more detailed information, refer
to 1000 and 2000 Product Families
Electronic Troubleshooting Manual
TS3192EN.
•Clear diagnostic codes
•Obtain transmission data such as input
speed or sump fluid temperature
•A solenoid test
•Clutch diagnostics (including torque
converter clutch)
e. Troubleshooting When No Diagnostic Codes
Are Present
•Always start with the basics:
— Make sure the shifter is in the appropriate
range.
— Check the fluid level.
— Make sure batteries are properly connected
and charged.
— Make sure throttle is closed and engine
speed is below 900 rpm.
— Make sure electrical connections are
properly made.
— Check support equipment for proper
installation and operation.
•If the shifting process is rough, give the shifts
time to adapt to “converged” state before
assuming there is a problem.
•Refer to Section 7 “General Troubleshooting
of Performance Complaints” in the 1000 and
2000 Product Families Troubleshooting
Manual TS3192EN.
— These troubleshooting charts list a variety
of conditions that may or may not relate to
the TCM.
— Some conditions and suggested checks
include mechanical and hydraulic items.
•If the troubleshooting charts refer you to a
TCM check, use the diagnostic code
troubleshooting information that best applies
to the situation.
f. Troubleshooting Intermittent Diagnostic
Codes. Intermittent codes are a result of conditions
which are not always present.
1. When conditions causing the code exist, the
code is logged in memory. The code stays in
memory until it is manually cleared or cycled
out by forty code-free warm-up cycles.
2. When intermittently occurring codes exist,
check for the following items:
•Dirty, damaged or corroded harness
connectors and terminals
•Terminals not fully seated in connectors
•Damaged harnesses (due to poor routing,
chafing, excessive heat, tight bends, etc.)
•Improperly mounted electronic control
components
•Poor connector seals (where applicable)
•Exposed harness wires
•EMI generating components and
accessories
•Loose ground connections
This manual suits for next models
28
Table of contents
Other Allison Transmission Microphone System manuals
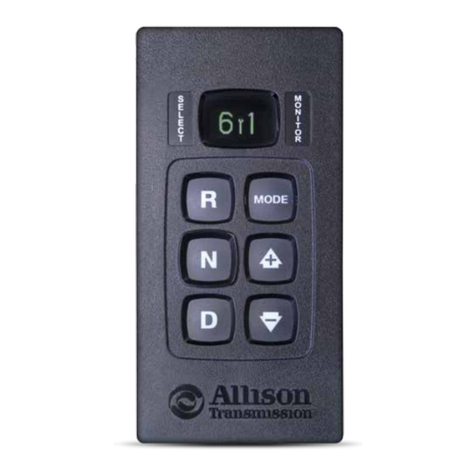
Allison Transmission
Allison Transmission shift selector User manual
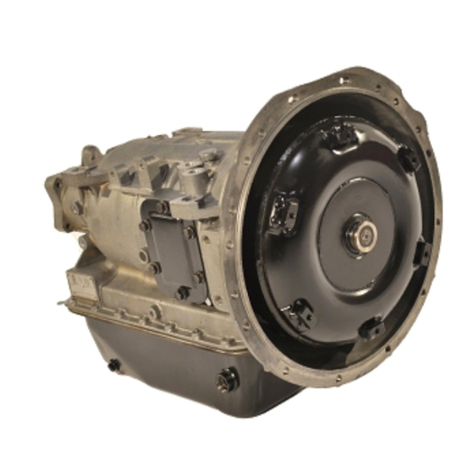
Allison Transmission
Allison Transmission AT 540 User manual
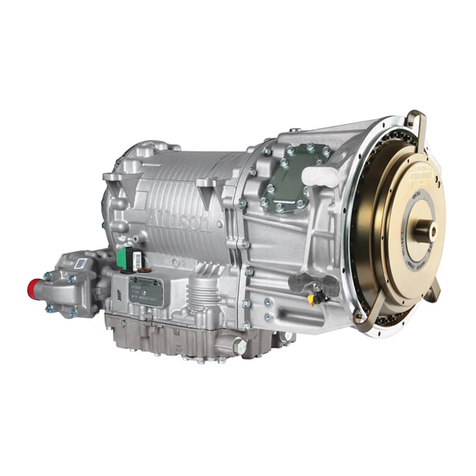
Allison Transmission
Allison Transmission AT Series User manual
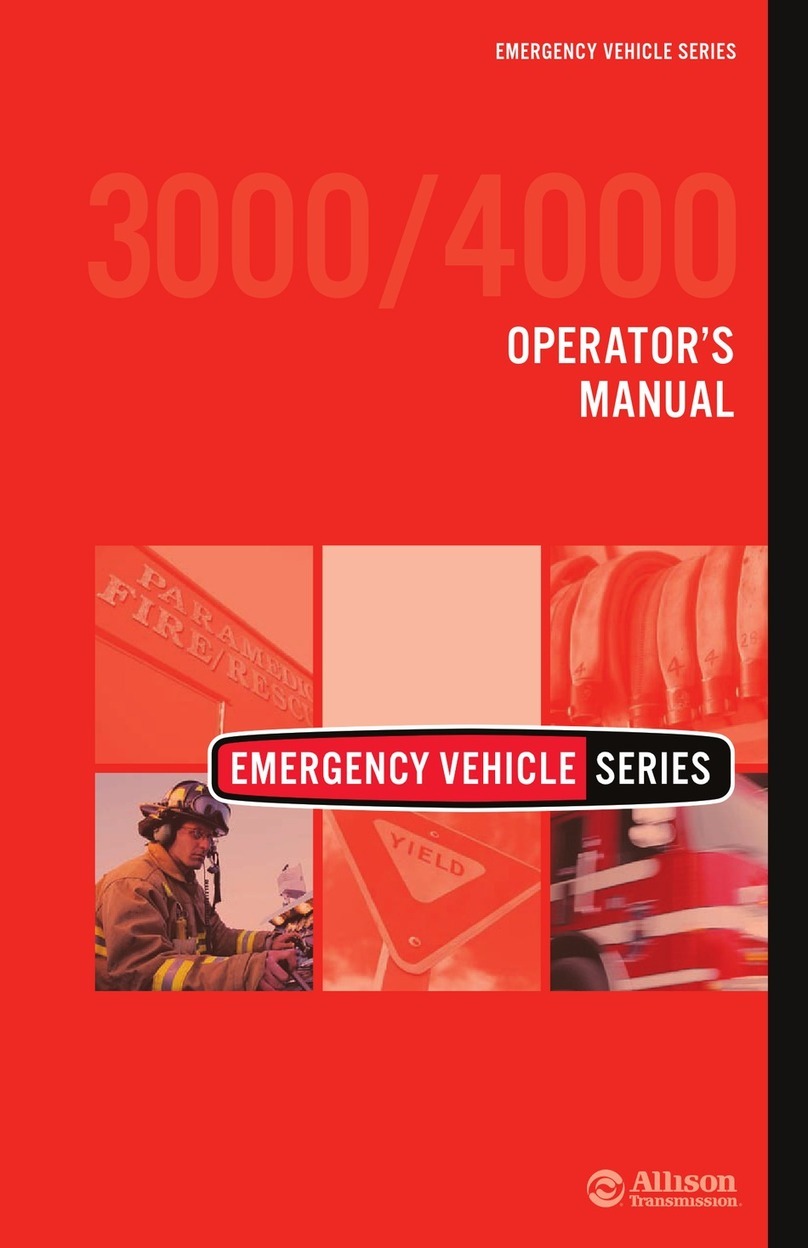
Allison Transmission
Allison Transmission Emergency Vehicle Series User manual

Allison Transmission
Allison Transmission Motorhome Series User manual
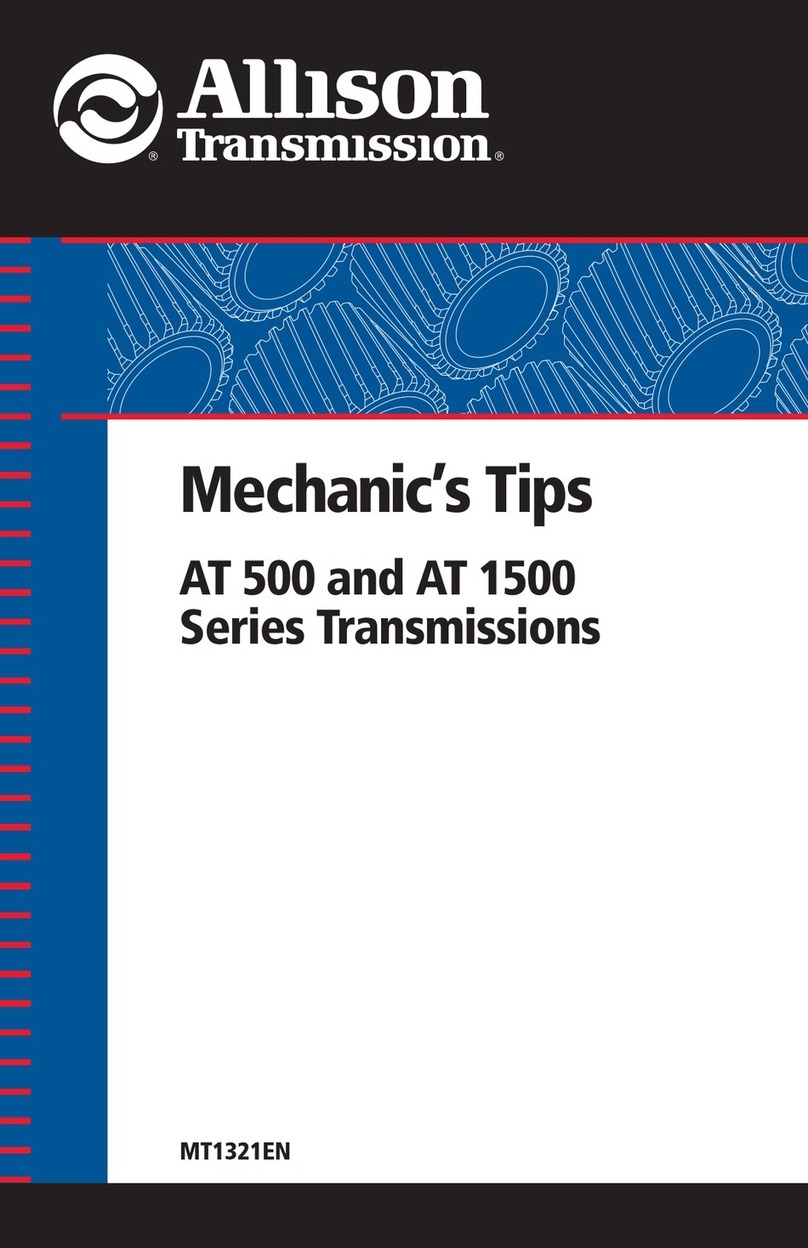
Allison Transmission
Allison Transmission AT 500 Series User manual
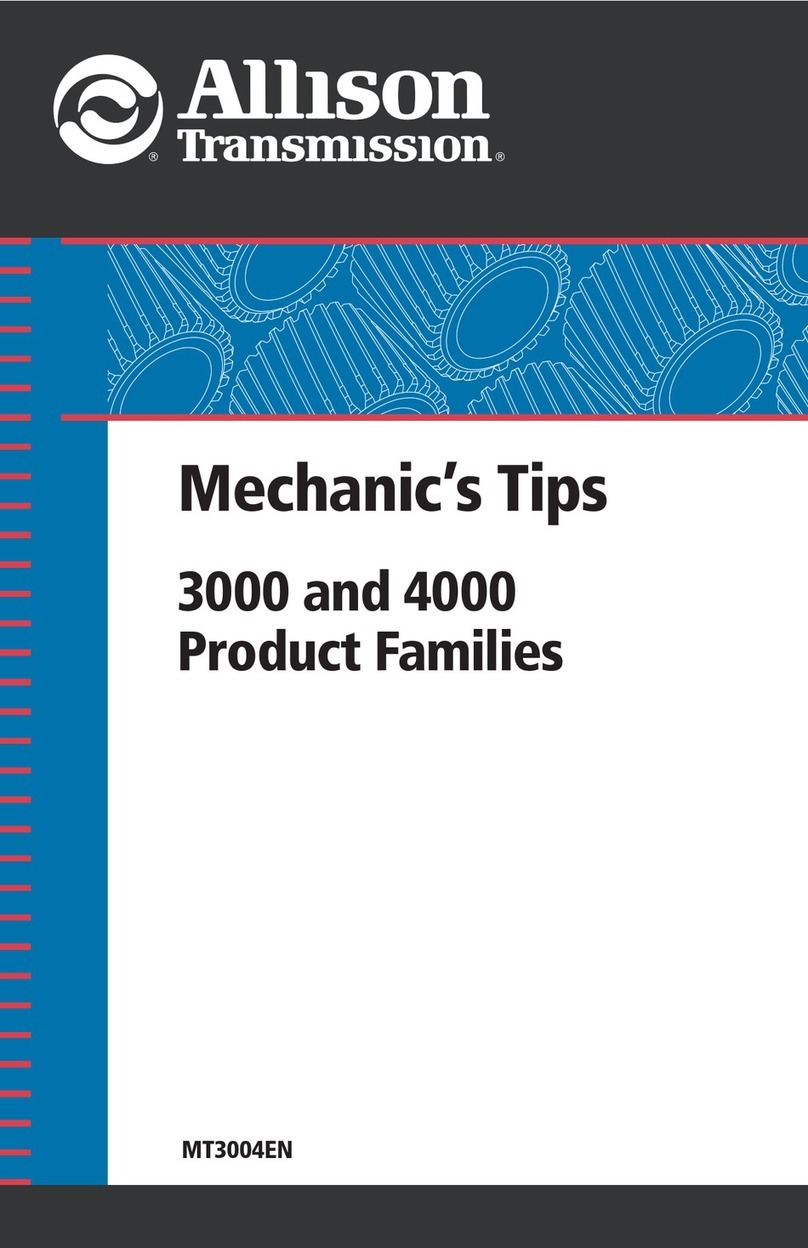
Allison Transmission
Allison Transmission 3000 Assembly instructions

Allison Transmission
Allison Transmission 3000 MH Series User manual