Alpha AS100 Series User manual


Preface
1
Preface
We appreciate your support for choosing the AS100 Series AC Servo System of
ALPHA. This Manual is formulated to help you apply this product in a correct manner.
It introduces the naming rules, supporting recognition, wiring, utilization, parameter
setting, precautions, and fault diagnosis of the servo drive and the motor.
AS100 Series AC Servo System consists of the AC drive and the permanent magnet
synchronous servo motor. AS100 AC Servo Drive is equipped with Digital Signal
Processor (DSP), Complex Programmable Logic Devices (CPLD) and latest IPM,
giving its advantages of high integration, limited volume, comprehensive protection,
great performance, etc. The optimum PID arithmetic is employed for regulation and
control over the electric current loop, the speed loop and the position loop with high
speed and great precision. AS100 is applicable to numerically-controlled machine tool,
printing and packaging machinery, textile machinery, automatic production line, etc.
For any problem encountered during the operation, please contact us or our dealers.
For sake of safety of yours and the product, please read this Manual before using our
product and preserve the Manual properly for future use.
Special attention should be paid to safety specifications and warnings in the Manual as
well as warning signs attached on the equipment while you read it for your safety and
proper operation of the equipment to prolong its servicing life. In the course of
operation, please pay special attention to running state of the driving machinery and
inform yourself of all safety precautions.

Preface
2
Danger!
◆This equipment is with hazardous voltage. Operations against
warnings or this Manual may incur life risk and personal injury.
Therefore only professionals familiar with safety precautions are
allowed to operate the equipment after completion of its
installation.
◆Power off during wiring and inspection. Do not touch the circuit
board or any part before the indication light on the printed circuit
board goes out or within 5 minutes since the keyboard display
goes out. Perform operations within the machine only when
completion of discharging has been confirmed by the special
instrument to exclude hazard of electric shock.
◆It is forbidden to connect the AC power supply to output terminal
U, V, W of the servo drive. Please perform earth connection of
the grounding terminals of the servo drive in a correct and
reliable manner in accordance with electric safety regulations of
IEC or other similar standards.
◆It is forbidden to connect the AC power supply to servo motor U,
V, W, to avoid possible equipment damage or personal injury.
Warning!
◆Unauthorized change to wiring within the machine or utilization
of auxiliaries purchased from illegal manufacturers may incur
fire disaster, electric shock or personal injury.
◆As the static electricity from human body will cause serious
damage to static electricity susceptible device, please do not
touch the printed circuit board and IGBT module with your
hands when anti-static precautions are not taken, or there may be
a fault.
◆Do not mount the servo drive and servo motor on
incombustibles. If mounted on or around combustibles, the servo
drive or servo motor may be exposed to fire disasters.
Caution!
◆The servo drive shall be used along with compatible servo motor
with supporting performance.
◆Users who intend to employ their own servo motor should
contact our technicians to make sure that such motor will run
normally.

Preface
3
◆Please make sure that all signs and tags are legible and fill in new
tags for missing or worn ones.
◆Please place the Manual where it is easily accessible and
disseminate it to all users for reading.
Our Company reserves the right to modify this Manual without notice; for any
doubt or problem, please do not hesitate to contact us or our dealers; feedbacks
are appreciated by us.

Contents
4
Contents
Preface............................................................................................................................ 1
Chapter I Purchase Inspection ..................................................................................... 7
1.1 Unpacking Inspection....................................................................................... 7
1.2 Naming Rules................................................................................................... 8
1.3 Servo Drive Nameplate .................................................................................. 10
1.4 Servo Motor Nameplate ................................................................................. 10
1.5 Servo System Constitution............................................................................. 11
Chapter II Installation and Wiring............................................................................. 12
2.1 Outline Dimension and Installation Dimension of Servo Drive..................... 12
2.2 Installation Site Requirements and Management........................................... 12
2.2.1 Installation Site........................................................................................ 13
2.2.2 Ambient Conditions ................................................................................ 13
2.2.3 Preventive Measures ............................................................................... 13
2.3 Installation Direction and Space..................................................................... 13
2.4 EMC Installation Conditions.......................................................................... 14
2.5 Main Circuit Terminal Wiring........................................................................ 15
2.6 Control Circuit Terminal Wiring.................................................................... 20
2.6.1 Encoder Single Wiring CN1.................................................................... 20
2.6.2 I/O Signal Wiring CN2 ........................................................................... 22
2.6.3 Communication Signal Wiring CN3/CN4............................................... 26
2.7 Basic Block Diagram of Servo System .......................................................... 27
2.8 Standard Wiring Diagram of Servo Drive...................................................... 27
2.9 Interface Circuit Principle .............................................................................. 31
2.10 Holding Brake Wiring.................................................................................. 38
2.11 Wiring Precautions....................................................................................... 38
Chapter III Display and Operation............................................................................. 40
3.1 Introduction to Operation and Display Interface............................................ 40
3.1.1 Key Functions ......................................................................................... 40
3.1.2 LED Display............................................................................................ 41
3.2 Keyboard Operation....................................................................................... 41
3.2.1 Shift between Function Code Groups...................................................... 41
3.2.2 Parameter Setting .................................................................................... 42
3.3 Monitor Display ............................................................................................. 43

Contents
5
3.4 System Parameter Initialization...................................................................... 46
Chapter IV Operation ................................................................................................ 47
4.1 Power Connection .......................................................................................... 47
4.2 Trial Operation............................................................................................... 50
4.1.1 The Checking Points Before Trial Operation.......................................... 50
4.1.2 The Checking Points During Operation.................................................. 51
4.1.3 Commissioning When Connecting to Power .......................................... 51
4.3 Adjustment..................................................................................................... 55
4.3.1 Basic Gain Adjustment............................................................................ 56
4.3.2 Basic Parameter Adjustment................................................................... 58
4.3.3 The Setting of Electronic Gear Ratio ...................................................... 58
Chapter V List of Functional Parameters...................................................................... 61
Chapter VI Specified Function Introduction................................................................. 80
6.1 Basic Function (Group P00)........................................................................... 80
6.2 Auxiliary Operation (Group P01)................................................................... 89
6.3 Monitor and Display (Group P02).................................................................. 95
6.4 I/O and Analog Control (Group P03)............................................................. 95
6.5 Position Control Parameters (Group P04).................................................... 102
6.6 Speed Control Parameters (Group P05) ....................................................... 106
6.7 Torque Control Parameters (Group P06)...................................................... 109
6.8 MODBUS Communication (Group P07)..................................................... 110
6.9 Parameters of Origin Search and Multistage Position (Group P10)............. 111
6.10 Parameters of Multistage Speed Function (Group P11)............................. 120
Chapter VII Diagnosis of Malfunctions................................................................... 125
7.1 Alarm Display and Description.................................................................... 125
7.2 Diagnosis of Malfunctions and Correction................................................... 126
7.3 Motor Failure and Corrective Action ........................................................... 131
Chapter VIII Maintenance....................................................................................... 137
8.1 Maintenance................................................................................................. 139
8.1.1 Daily Maintenance ................................................................................ 139
8.1.2 Periodic Maintenance............................................................................ 140
8.1.3 Regular Replacement of Devices .......................................................... 141
8.2 Storage and Protection.................................................................................. 141

Contents
6
Chapter IX Quality Guarantee................................................................................. 143
Annex 1 Appearance Dimensions and Installation Dimensions of Drive................ 145
Annex 2 Technical Specification of Servo Drive .................................................... 148
Annex 3 Matching Selection of Servo Motor and Drive (220V series)................... 151
Annex 4 Matching Selection of Servo Motor and Drive (380V series)................... 152
Annex 5 Specification of Braking Resistor ............................................................. 153
Annex 6 Main Input/Output Cable Selection........................................................... 154
Annex 7 MODBUS Communication Protocol ........................................................ 155
Annex 8 Parameters and Size of Servo Motor......................................................... 162
Annex 9 Servo Drive Warranty ............................................................................... 177

Chapter I Purchase Inspection
7
Chapter I Purchase Inspection
1.1 Unpacking Inspection
The servo drive system has been tested and checked strictly before delivery. However,
please check the purchased product of the following items to avoid unnecessary
mistakes during purchasing and transport.
Whether the purchased product is the expected one: for this, the product model on
the nameplates of the motor and drive should be checked with reference to model
description outlined in the next section.
Whether the motor shaft rotates in a smooth manner: for this, manually rotate the
motor shaft to see whether it is able to run smoothly. If yes, it is deemed normal.
However, the inspection manner of manual rotation is not applicable to the motor
with an electromagnetic holding brake.
Damage inspection: for this, conduct visual inspection on the product for damage
or scratching.
Unreliable screws: check whether any screw is not fixed in a reliable manner or is
loosening.
In any of above mentioned cases, do not hesitate to contact the dealer for problem
solving.
Operable complete servo components include:
Name
Qty.
Unit
Remarks
Servo motor
1
Set
Servo drive
1
Set
Motor power line
connector
1
Set
Standard configuration: one 4P
aviation plug, one 4P quick
connector. Optional power cable
Encoder signal line
connector
1
Set
Standard configuration: one 15P
aviation plug, one DB15 RP-SMA
Male
Optional coder signal line
Spring opener
2
Pcs.
Standard configuration: for spring
connector wiring
Instruction Manual
1
Copy

Chapter I Purchase Inspection
8
Name
Qty.
Unit
Remarks
SCSI 50P connector
1
Pcs.
Standard configuration: for I/O
cable connection
5P quick connector
1
Pcs.
Standard configuration: for drive’s
input power supply wiring
MINI DIN 8P
communication
connector
Optional configuration: for
communication cable wiring
Note: aforesaid components may vary with different powers of the drives. The specific
configuration should be determined based on the packing list within the packing box.
1.2 Naming Rules
Naming rules of the servo drive are as follows:
AS100 A - 5R5 M2 U
Encoder Type
U: 2500CPR standard inc. Enc.
V: 2500CPR wire-saving inc. Enc.
W: 20-bit inc. Enc.
A: 17-bit absolute Enc.
Series Code
Alpha Servo 100
Series
Model Code
A: standard model (analog and
pulse command with RS485)
B: standard model with RS232
C: standard model with CAN
Rated Output Current
2R8: 2.8A 3R8: 3.8A 5R5: 5.5A
7R6: 7.6A012: 12A 3R5: 3.5A
5R4: 5.4A 8R4: 8.4A
Input Voltage
S2: Single-phase 220V
T2: Three-phase 220V
T3: Three-phase 380V
M2: Single/three-phase 220V

Chapter I Purchase Inspection
9
Naming rules of the servo drive are as follows:
①Series Code:
ASMG=Medium InertiaAC Servo Motor of Alpha
ASMH=High InertiaAC Servo Motor of Alpha
ASMS=Low InertiaAC Servo Motor of Alpha
②Output Power:
Three figures or two figures plus R (decimal point) are employed to represent the
rated output power of the motor, which is in KW.
e.g.: R75 refers to 0.75KW, 1R0 to 1.0KW, and 1R5 to 1.5KW.
③Voltage class:
One letter is used to represent the voltage class.
A=100V, B=220V, C=380V.
④Rated Speed:
Two figures are used to express rated speed. To be specific, rated speed= the
double digit ×100, in rpm.
⑤Encoder Type:
Encoder type is represented by one letter.
U: 2500 CPR standard incremental encoder
V: 2500 CPR wire-saving incremental encoder
W: 20-bit serial incremental encoder
A: 17-bit serial absolute encoder
⑥Design Sequence:
Design sequence is represented by a figure or a letter.
1=standard S-type design, 2=standard E-type design, others: non-standard designs
ASMG –R75 B20 U2P
①
②
③
④
⑤
⑥
⑦

Chapter I Purchase Inspection
10
⑦Option
Option is represented by a letter.
Option code
No oil seal
No brake
No oil seal
With brake
With oil seal
No brake
With oil seal
With brake
Circular shaft (with
screw holes )
A
B
C
D
Keyway
E
F
G
H
Keyway (with screw
holes )
P
Q
R
S
1.3 Servo Drive Nameplate
Fig. 1-1 Servo Drive Nameplate
1.4 Servo Motor Nameplate
Fig. 1-2 Servo Motor Nameplate
Specification of input power supply
Specification of output power supply
Serial No.
Model of Servo motor
Specification of input power supply
Specification of output power supply
Serial No.
Date of Manufacture
Model of Servo drive

Chapter I Purchase Inspection
11
1.5 Servo System Constitution
1Ф/3Ф
220V/380V
Circuit Breaker
EMC filter
Magnetic
Contactor
Ext. Brake Resistor
(Remove the jumper
between B2 and +
when this resistor is used)
Encoder
Feedback
Cable
I/O Cable
Communication
Cable
Motor
Drive
Cable
ASM Servo Motor
AS100 series
Servo Driver
PC
Motion
controller
Fig. 1-3 Servo System Constitution

Chapter II Installation and Wiring
12
Chapter II Installation and Wiring
2.1 Outline Dimension and Installation Dimension of Servo Drive
See Appendix 1 for details on outline dimension and installation dimension of servo
drive.
2.2 Installation Site Requirements and Management
Caution
•Do not exert any force on the operation panel and the cover plate in the course of
handling; otherwise the falling of the servo drive will result in personal injury or
property loss.
•The servo drive shall be installed in a position capable of bearing its weight;
otherwise the falling of the servo drive will result in personal injury or property
loss.
•Do not install the drive around a water pipe and other positions that may suffer
water splashing; otherwise it may entail the risk of property loss.
•Do not make such foreign matters as screws, gaskets and metal bars fall into the
servo drive; otherwise it may result in fire and property loss.
•Do not install or use the servo drive if it is damaged or its components are
incomplete; otherwise it may result in fire and personal injury.
•Do not install the drive in a place with direct sunlight; otherwise it may entail the
risk of property loss.
•The main circuit terminal and the conductor terminal must be firmly connected;
otherwise it may entail the risk of property loss.
•Do not connect the input power cord to the output ends U, V and W; otherwise it
may entail the risk of property loss.
•Please connect the output ends U, V and W to the three-phase input of the motor
in proper phase sequence; otherwise the motor will operate in an abnormal
manner.
•Do not directly connect the braking resistor between the (+) and (-) terminals of
the DC bus; otherwise it may cause fire and property loss.
•The short circuit line must be connected between B2 and + terminal when using
an internal braking resistor; otherwise it may cause fire.

Chapter II Installation and Wiring
13
2.2.1 Installation Site
The IP code of AS100 servo drive is IP20, and the installation site shall meet the
following requirements:
Keep the indoor environment well ventilated;
Do not install the drive on a wood material or other combustibles;
Avoid direct sunlight;
Do not install the drive in a place with inflammable, explosive and corrosive gases
or liquids;
Keep it free of dust, oily dust, floating fiber and metal particles;
The installation base shall be firmly secured to prevent vibration;
Electromagnetic interference and other interference sources shall be avoided.
If the altitude is over 1,000m, the thin air may result in poorer radiating effect,
please lower the rated output. The altitude increases 1,000m, 6% of the rated
output shall be lowered.
2.2.2 Ambient Conditions
Temperature range: 0℃~45℃. Please lower the rated output if the temperature is
above 45℃. The highest temperature is 60℃(idle running);
Humidity range: 5%~95% RH; no condensed water droplets or rainwater dripping;
Vibration: below 4.9m/s2.
2.2.3 Preventive Measures
During installation, please put a dust shield on the servo drive cover. Do not make any
metal fragments produced during drilling and other operations fall into the servo drive.
Upon the completion of installation, remove the dust shield.
2.3 Installation Direction and Space
The standard installation requirements are as follows: the drive shall be installed in a
well-ventilated electric control cabinet. As for the installation modes, bottom plate
installation or panel installation shall be selected. The structure of the servo drive is not
protected, thus the drive must be installed in a well-protected electric cabinet; moreover,
measures shall be taken to avoid contacting with corrosive and inflammable gases and
to prevent conductive objects, metal dusts, oil fog, and liquid from entering the drive,
as shown in Fig. 2-1:

Chapter II Installation and Wiring
14
Fig. 2-1 Installation Direction and Space
To achieve good cooling and circulation effects, adequate space must be reserved
between the upper, lower, left and right parts and the adjacent objects or baffle
plates (wall).
If it is installed side by side, it is recommended to reserve a spacing of above
10mm between adjacent articles. A spacing of above 40mm should be reserved for
two horizontal sides, and a spacing of above 100mm should be reserved for two
longitudinal sides.
The product is a precision device, so do not make it fall or suffer strong impact in
the process of installation, please.
Do not obstruct the air intake and air outlet; otherwise it will cause failure.
Please install a fan for cooling in the upper part of the servo drive. To ensure that
the temperature around the drive will not rise continuously, the temperature in the
electric cabinet must be kept uniform.
2.4 EMC Installation Conditions
Before delivery, the servo drive has been strictly tested in accordance with the
requirements of IEC61000-4, IEC61000-3-2-2000, IEC61000-3-4-1998 and
Above
40mm
Above
100mm
Above 10mm
Fan
Fan
Above 10mm
Above 10mm
Above
40mm
Above
100mm

Chapter II Installation and Wiring
15
GB/T17626.2-6. In order to avoid any possible influence of external strong
electromagnetic interference source, to ensure normal operation of the servo system,
and to prevent the adverse impacts of the actions of the high -frequency electronic
switch on the sensitive equipment nearby, the following EMC measures should be
taken during the installation of the servo system:
Install the servo drive in a shield box;
Ensure that the servo drive and the servo motor are reliably grounded;
The input and output signal cables shall be shielded twisted pair, and ferrite beads
(winding two coils) shall be used;
The encoder cables shall be shielded twisted pair, and ferrite beads (winding one
coil) shall be used;
The main circuit cables shall be shielded cables if possible, and the shielding layer
shall be reliably grounded.
2.5 Main Circuit Terminal Wiring
Fig. 2-2 Main Circuit Terminal Interface
Main Circuit Terminal

Chapter II Installation and Wiring
16
Table 2-1 Function and Description of Main Circuit Terminal
Terminal Code
Terminal Name and Function Description
L1, L2, L3
Main circuit power supply input terminal:
The drive shall be connected to three-phase 220V or three-phase
380V or single-phase 220V power supply according to different
models; as for single-phase input, it can only be connected to L1
and L2 terminals, and L3 shall not be wired; the drive of some
model are applicable to three-phase 220V and single-phase 220V
power supplies, and the single-phase power supply should be
connected to L1 and L3 terminals. Refer to the nameplate of the
drive for detailed information about the power supply specification.
LC1, LC2
Control power supply input terminal:
220V series drive: AC 220V (+/-15%), 50/60HZ
380V series drive: AC 380V (-15%~+10%), 50/60HZ
B1, B2, +
External braking resistor connecting terminal:
If a built-in braking resistor is used, B2 and + are in short
connection;
If an external braking resistor is used, the external braking resistor
is connected to B1 and + end, and the jumper between B2 and +
shall be removed.
U, V, W
Three-phase AC output terminal: connected with U, V and W of
the servo motor
PE,
Grounding terminal: connected with the power supply grounding
terminal and the motor grounding terminal
Notes: the figure shows the terminal arrangement for 220V5.5A drive; the terminal
arrangement for drives of other specifications may be different from this; the actually
marked terminal code shall prevail.
Wiring Steps for Spring Type Main Circuit Terminal:
Take the spring type main circuit terminal from the servo drive.
Strip the insulating layer of the wire to be connected as shown in the figure.

Chapter II Installation and Wiring
17
Use proper wire noses, and press it on the wire of which the insulating layer is
stripped with a proper crimping tool.
Insert the wire of the terminal connector into the opening on the hole with a tool.
Two methods may be applied:
■Use a spring opener: operate as shown in the illustrations.
■Use a slotted screwdriver: operate as shown in the illustrations.
Notes: the actually used connector may be totally different from that of the connector as
shown in the figures in appearance. Please note that during the actual operation.

Chapter II Installation and Wiring
18
Typical Wiring Diagram of Main Circuit
●Single-phase/three-phase 220V Power Supply:
Notes: AS100A-1R6M2U and AS100A-2R8M2U do not have a jumper between B2
and +.
The above figure is applicable to the following drives:
AS100A-1R6M2U AS100A-2R8M2U AS100A-3R8M2U
AS100A-5R5M2U AS100A-7R6T2U AS100A-012T2U

Chapter II Installation and Wiring
19
●Three-phase 380V Power Supply:
Notes: the above figure is applicable to the following drives:
AS100A-3R5T3U AS100A-5R4T3U AS100A-8R4T3U
Table of contents
Other Alpha Controllers manuals
Popular Controllers manuals by other brands
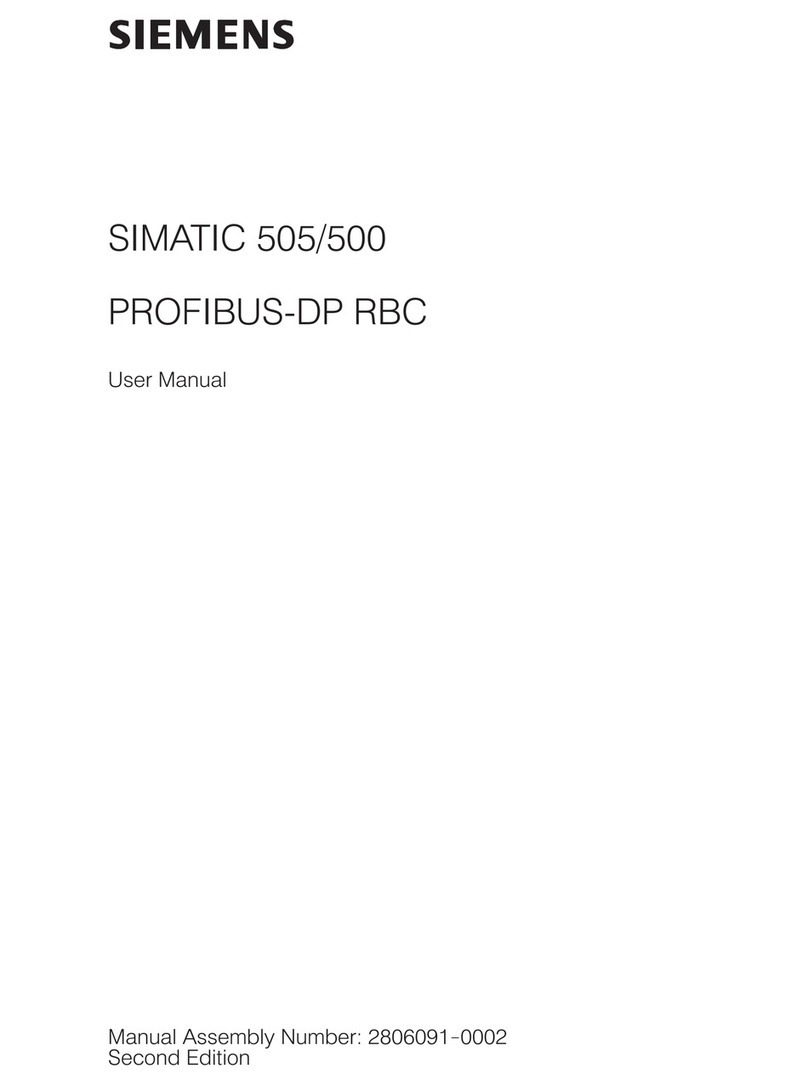
Siemens
Siemens SIMATIC 500 user manual
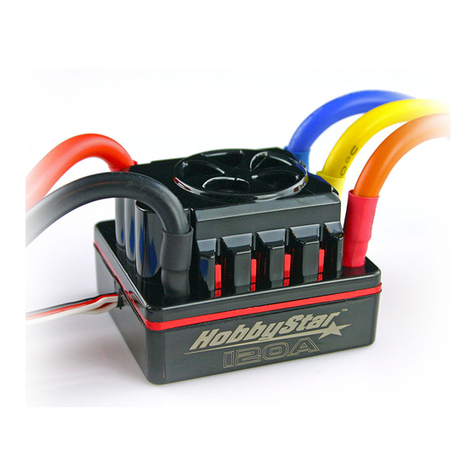
HobbyStar
HobbyStar 80A product manual
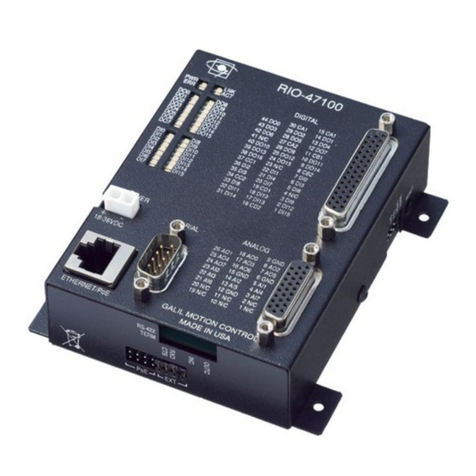
Galil Motion Control
Galil Motion Control RIO-47 seriesRIO-47100 user manual
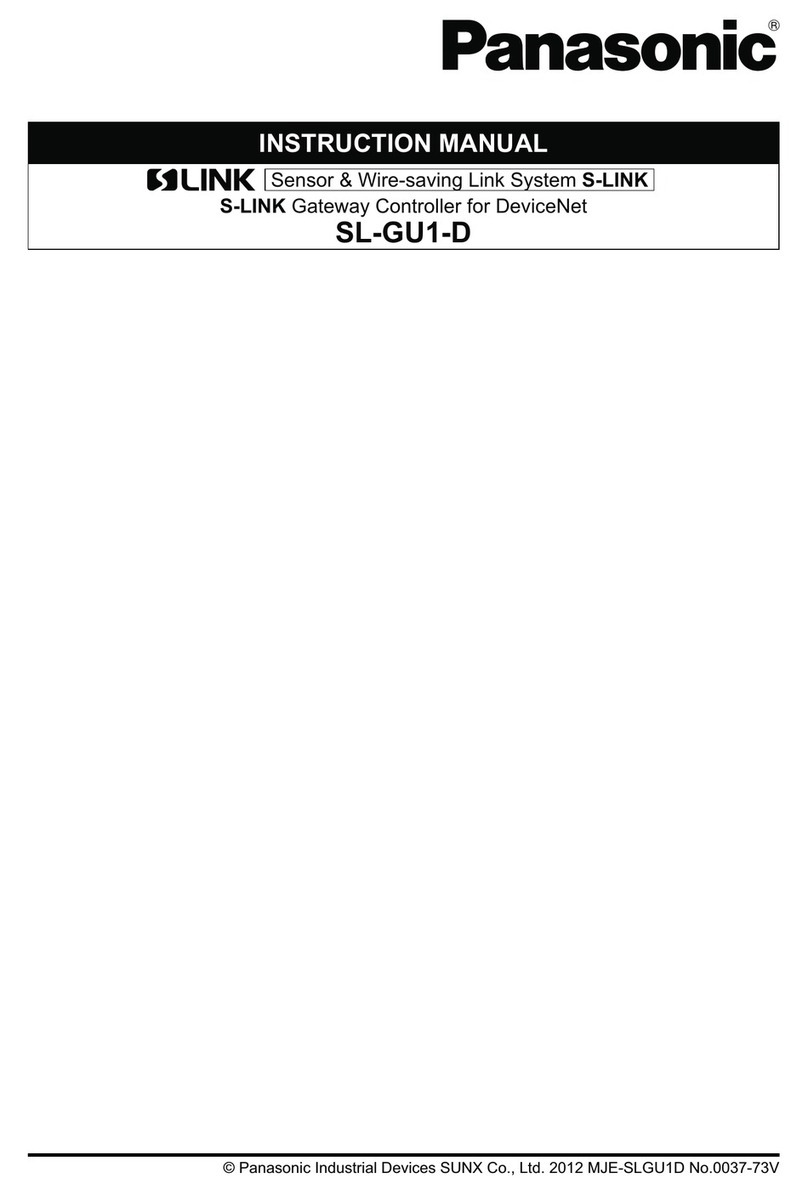
Panasonic
Panasonic SL-GU1-D instruction manual
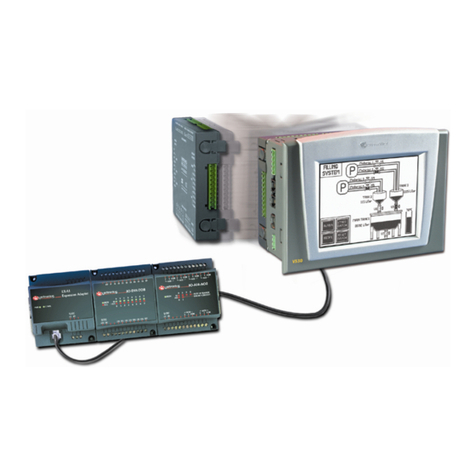
Klinkmann
Klinkmann Unitronics Vision V530-53-B20B installation guide
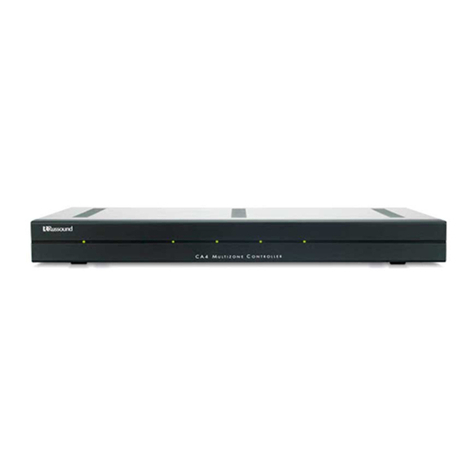
Russound
Russound CA4 installation manual