amig AMIG-LST Series Operator's manual


(3) Connect arc voltage
feedback wire with work piece
(4) Plug the torch into the torch
connector of the wire feeder
Warning! An electric shock can be fatal. If the machine is plugged into the mains electricity supply during installation, there is a high risk of very serious injury and damage. Only carry out work on the machine when
you have read the “Safety Rules” and when: the mains switch is on the “OFF” position; the machine is unplugged from the mains.
- MIG welding process and operating
(1) Screw shielding gas regulator onto
the gas cylinder and tighten it; connect
gas hose with flow meter
(2) Connect work piece with welding
machine negative output terminal by
ground cable
(6) Fix the selected wire
Shielding
gas
regulator
Gas hose
Gas cylinder
Valve
(5) Water cooled mode) Plug the
water hoses of the welding torch to
connectors in the wire feeder
(
AMIG-LST Series Quick Instructions (This quick instruction is based on AMIG350-LST model)
5-15
Direction o f Tr avel
Longit udinal A n gle
(15) Press the torch trigger and start
welding
Front panel
Work piece
Work piece
L1
L2
L3
GND
(9) Select torch’s operating mode (press the
“Mode” button, light corresponds to selected
mode is on ): 2-step/ 4-step/ Special 4-step/
Spot welding
(7) Power on (8) Select the needed welding process (press
the “Process” button, light corresponds to
selected welding process is on): MIG/LST
(1 ) Select the wire diameter (press “Wire
diameter” button, light corresponds to selected
wire diameter is on): Φ0.8/ Φ1.0/ Φ1.2/ Φ1.6
1
(10) Select the filler metal and shielding gas type
(press “Material” button, light corresponds to
selected filler metal and shielding gas is on)
θ
3~380V
UP
mm
a
cm
V
JOB
DIAMETER
steel
6
5
4
3
2
1
8
10
12
11
9
7
L S T
MIG
CO
2
18%
Ar 82%
CO
2
100%
CALL
F1 F2
φ
WIRE MATERIAL&GAS
MODE
φ0.8
φ1.0
φ1.2
φ1.6
OP1
OP2
OP3
OP4
OP5
OP6
OP7
OP8
OP9
OP10
steel
SAVE
mm
a
cm
V
JOB
DIAMETER
steel
6
5
4
3
2
1
8
10
12
11
9
7
L S T
M I G
CO2
18%
Ar 82%
CO2
100%
CALL
F1 F2
φ
WIRE MATERIAL&GAS
MODE
φ0.8
φ1.0
φ1.2
φ1.6
OP1
OP2
OP3
OP4
OP5
OP6
OP7
OP8
OP9
OP10
steel
SAVE
mm
a
cm
V
JOB
DIAMETER
steel
6
5
4
3
2
1
8
10
12
11
9
7
LST
MIG
CO
2
18%
Ar %82
CO
2
100%
CALL
F1 F2
φ
WIRE MATERIAL&GAS
MODE
φ0.8
φ1.0
φ1.2
φ1.6
OP1
OP2
OP3
OP4
OP5
OP6
OP7
OP8
OP9
OP10
steel
SAVE
mm
a
cm
V
JOB
DIAMETER
steel
6
5
4
3
2
1
8
10
12
11
9
7
L S T
M I G
CO
2
18%
Ar 82%
CO
2
100%
CALL
F1 F2
φ
WIRE MATERIAL&GAS
MODE
φ0.8
φ1.0
φ1.2
φ1.6
OP1
OP2
OP3
OP4
OP5
OP6
OP7
OP8
OP9
OP10
steel
SAVE
( ) Specify the desired welding power with reference
to any of the following parameters: a-dimension/
Sheet thickness/ Welding current/ Wire feed speed
12
mm
a
cm
V
JOB
DIAMETER
steel
6
5
4
3
2
1
8
10
12
11
9
7
L S T
MIG
CO2
18%
Ar 82%
CO2
100%
CALL
F1 F2
φ
WIRE MATERIAL&GAS MODE
φ0.8
φ1.0
φ1.2
φ1.6
OP1
OP2
OP3
OP4
OP5
OP6
OP7
OP8
OP9
OP10
steel
SAVE
( ) Turn the welding voltage button of the wire feeder into the standard position, adjust proper
welding current, the voltage will auto match with current, then adjust the voltage adjustment knob
for fine adjustment
13
Wa t e r nIle t
Wa t e r Otul e t
A
1
2
3
4
5
6
7
8
9
10
WELDING UCR.ADJ
-5 5V
0
-1
-2
-4
1
2
3
4
LO W HIGH
-3
WELDING VLOT.ADJ
0
Wa t e r nIle t
Wa t e r Otule t
A
1
2
3
4
5
6
7
8
9
10
WELDING UCR.ADJ
-5 5V
0
-1
-2
-4
1
2
3
4
LO W HIGH
-3
WELDING VLOT.ADJ
Wa t e r nIl e t
Water Outelt
A
1
2
3
4
5
6
7
8
9
10
WELDING CUR.ADJ
-5 5
V
0
-1
-2
-4
1
2
3
4
LOW HIGH
-3
WELDING VOLT.ADJ
(1 ) Open the gas cylinder valve4
P
O
E
N
90%d Transverse Angle

Note: All settings are approximate/welds should be tested to comply to your specifications.
MIG /MAG-Steel Welding Parameters
THICKNESS
(mm)OF
MATERIAL
WIRE FEEDING
SPEED(m/min)
VOLTAGE(V)
CURRENT
(A)
0.8mm
0.8
0.9
1.2
1.5
2.0
1.0mm
1.2mm
2.3-2.9
2.9-3.2
3.8-4.5
5.4-6.9
7.3-8.2
-
1.7-2.0
2.2-2.4
3.0-3.9
4.5-5.1
-
-
1.8
2.0-2.5
2.7-3.0
CO2
Ar82%+CO 18%
2
16-17
17-18
18-19
19-20
20-21
15-16
15-16
16-17
17-18
17-18
40-55
50-60
70-80
90-110
120-130
-
-
-
-
-
5.3-5.7
6.1-6.8
7.4-8.3
9.4-10.2
11.2-14.0
3.6-3.8
4.1-4.5
4.7-5.0
5.3-5.6
5.9-8.0
21-22
21-22
23-24
23-24
24-25
18-19
18-19
21-22
21-22
23-24
140-150
160-170
180-190
200-210
220-250
3.2
5.0
6.3
8.0
9.5
MIG-Stainless Steel Welding Parameters
THICKNESS (mm)
OF MATERIAL
WIRE FEEDING
SPEED(m/min)
VOLTAGE(V)
CURRENT(A)
1.0mm
1.2mm
1.2
1.5
2.0
2.5
3.1-3.5
3.8-4.2
5.6-6.0
6.9-7.3
1.8-2.4
2.4-2.8
2.8-3.2
4.0-4.4
19-20
19-20
20-21
20-21
-
-
-
-
He+Ar+CO2
Ar+2%CO2
He+Ar+CO2
Ar+2%CO2
-
-
-
-
50-60
70-80
90-110
120-130
4.8
6.3
8.0
9.5
9.1-9.5
10.0-10.4
11.2-11.6
-
6.8-7.2
7.3-7.7
8.1-8.5
8.8-9.2
21-22
21-22
21-22
-
-
-
200-210
220-250
-
-
24-25
25-26
140-150
160-170
180-190
-
11.1
12.7
14
-
-
-
9.4-9.8
10.4-10.8
11.4-11.8
-
-
-
300
325
325
26-27
27-29
29-32
-
-
-
Welding Standard

1
Dear Customer
This instruction manual will help you get to know your new machine. Read the manual
carefully and you will soon be familiar with all the many great features of your new
product. Meanwhile, please remember well safety rules and operate as instruction.
If you treat your product carefully, this definitely helps to prolong its enduring quality
and reliability things which are both essential prerequisites for getting outstanding
results.
Production specification may change without advance notice.
The model you purchase is :
AMIG350 LST
Please find corresponding models from the "Contents".
Important:
Please take special note of safety rules and operate as instruction in case of damage
and serious injury.

2
Safety Rules
“Danger”indicates an imminently hazardous situation which, if not avoided, will result in death or
serious injury.
“Warning!”indicates a possible hazardous situation which, if not avoided, could result in death or
serious injury. The possible hazards are explained in the text.
“Caution”indicates a possible hazardous situation which, if not avoided, may result in slight or
moderate injury.
“Note!”indicates a situation which implies a risk of impaired welding result and damage to the
equipment.
“Important!” indicates practical tips and other useful special-message. It is no signal word for a
harmful or dangerous situation.
Utilization for intended purpose only
•The machine may only be used for jobs as defined by the “Intended purpose”.
•Utilization for any other purpose, or in any other manner, shall be deemed to be “not in accordance
with the intended purpose”. The manufacturer shall not be liable for any damage resulting from such
improper use.
Safety signs
•All the safety instructions and danger warnings on the machine must be kept in legible condition, not
removed, not be covered, pasted or painted cover.
Safety inspection
•The owner/operator is obliged to perform safety inspection at regular intervals.
•The manufacturer also recommends every 3-6 months for regular maintenance of power sources.
Electric shock can kill
•Touching live electrical parts can cause fatal shocks or severe burns. The electrode and work circuit
is electrically live whenever the output is on. The input power circuit and machine internal circuits are
also live when power is on. In MIG/MAG welding, the wire, drive rollers, wire feed housing and all
metal parts touching the welding wire are electrically live. Incorrectly installed or improperly grounded
equipment is a hazard.
•Do not touch live electrical parts of the welding circuit, electrodes and wires with your bare skin or wet
clothing.
•The operator must wear dry hole-free insulating welding gloves and body protection while performs
the welding.
•Insulate yourself from work and ground using dry insulating protection which is large enough to
prevent you full area of physical contact with the work or ground.
•Connect the primary input cable according to rules. Disconnect input power or stop machine before
installing or maintenance.
•If welding must be performed under electrically hazardous conditions as follow: in damp locations or
wearing wet clothing; on metal structures such as floors, gratings, or scaffolds; when in cramped
positions such as sitting, kneeling, or lying; or in occasion when there is a high risk of unavoidable or
accidental contact with the work piece or ground. Must use additional safety precautions:
semiautomatic DC constant voltage (wire) welder, DC manual (Stick) welder and AC welder with
reduced open-load voltage.
•Maintain the electrode holder, ground clamp, welding cable and welding machine in good, safe
operating condition. Replace damaged part immediately.
Electric and magnetic fields (EMF) may be dangerous
•If electromagnetic interference is found to be occurring, the operator is obliged to examine any
possible electromagnetic problems that may occur on equipment as follow:
-mains, signal and data-transmission leads
-IT and telecoms equipment
-measurement and calibration devices
-Wearers of pacemakers
•Measures for minimizing or preventing EMC problems:
-Mains supply
If electromagnetic interference still occurs, despite the fact that the mains connection in accordance
with the regulations, take additional measures
-Welding cables
Keep these as short as possible
Connect the work cable to the work piece as close as possible to the area being welded.
Lay term well away from other cables.

3
Do not place your body between your electrode and work cables.
-Equipotential bonding
-Workpiece grounding (earthing)
-Shielding
Shield the entire welding equipment and other equipment nearby.
ARC rays can burn
•Visible and invisible rays can burn eyes and skin.
•Wear an approved welding helmet or suitable clothing made from durable flame-resistant material
(leather, heavy cotton, or wool) to protect your eyes and skin from arc rays and sparks when welding
or watching.
•Use protective screens or barriers to protect other nearby personnel with suitable, non-flammable
screening and/or warn them not to watch the arc nor expose themselves to the arc rays or to hot
spatter or material.
Fumes and gases can be dangerous
•Welding may produce fumes and gases, breathing these fumes and gases can be hazardous to your
health.
•When welding, keep your head out of the fume. If inside, ventilate the area at the arc to keep fumes
and gases away from the breathing zone. If ventilation is not good, wear an approved air-supplied
respirator.
•Work in a confined space only if it is well ventilated, or while wearing an air-supplied respirator.
•Welding fumes and gases can displace air and lower the oxygen level causing injury or death. Always
use enough ventilation, especially in confined areas, to insure breathing air is safe.
Welding and cutting sparks can cause fire or explosion
•When not welding, make sure the electrode circuit is not touching the work or ground. Accidental
contact can cause sparks, explosion, overheating, or fire. Make sure the area is safe before doing
any welding.
•Welding and cutting on closed containers, such as tanks, drums, or containers, can cause them to
blow up. Make sure proper steps have been taken.
•When pressure gas is used at the work site, special precautions are required to prevent hazardous
situations.
•Connect work cable to the work as close to the welding zone as practical to prevent welding current
from passing too long and creating fire hazards or overheat.
•Wear oil-free protective garments such as leather gloves, heavy shirt, cuffless trousers, high shoes,
and a cap. Wear ear plugs when welding out of position or in confined places. Always wear safety
glasses with side shields when in a welding area.
•Be attention that welding sparks and hot materials from welding can easily go through small cracks
and openings to adjacent areas and start a fire. Remove fire hazardous from the welding area, if not
possible, cover them thoroughly. Do not weld where flying sparks can strike flammable material and
where the atmosphere may contain flammable dust, gas, or liquid vapors (such as gasoline).
•Protect yourself and others from flying sparks and hot metal. Remove any combustibles from
operator before perform any welding.
•Keep a fire extinguisher readily available.
•Empty containers, tanks, drums, or pipes which have combustibles before perform welding.
•Remove stick electrode from electrode holder or cut off welding wire at contact tip when not in use.
•Apply correct fuses or circuit breakers. Do not oversize or bypass them.
Cylinder can explode if damaged
•Pressure gas cylinders contain gas under high pressure. If damaged, a cylinder can explode. Since
gas cylinders are normally part of the welding process, be sure to treat them carefully.
•Cylinders should be located away from areas where they may be struck or subjected to physical
damage. Use proper equipment, procedures, and sufficient number of persons to lift and move
cylinders.
•Always install cylinders in an upright position by securing to a stationary support or cylinder rack to
prevent falling over or tipping.
•Keep a safe distance from arc welding or cutting operations and any other source of heat, sparks, or
flame.
•No touching cylinder by welding electrode, electrode holder or any other electrically “hot” parts. Do
not drape welding cables or welding torches over a gas cylinder.
•Use only correct compressed gas cylinders, regulators, hoses, and fittings designed for the process
used; maintain them and associated parts in good condition.
•Use only compressed gas cylinders containing the correct shielding gas for the and properly
operating regulators designed for the gas and pressure used. All hoses, fittings, etc. should be
suitable for the application and maintained in good condition.
•Open the cylinder valve slowly and keep your head and face away from the cylinder valve outlet.
•Valve protection caps should be kept in place over valve expect when the cylinder is in use or
connected for use.

4
Hot parts can burn
•Do not touch hot parts with bare hand or skin.
•Ensure equipment is cooled down before perform any work.
•If touching hot parts is needed, use proper tools and/or wear heavy, insulated welding gloves and
clothing to prevent burns.
Flying metal or dirt can injure eyes
•When welding, chipping, wire brushing, and grinding can cause sparks and flying metal. It can hurt
your eyes.
•Remember wear appropriate safety glasses with side shields when in welding zone, even under your
welding helmet.
Noise can damage hearing
•Noise from some processes or equipment can damage hearing.
•Remember wear approved ear protection to protect ears if noise level is high.
Moving parts can injure
•Stay away from moving parts such as fans.
•Stay away from pinch points such as drive rolls.
•Keep all doors, panels, covers, and guards closed and securely in place.
•Have only qualified persons remove doors, panels, covers, or guards for servicing and maintenance.
•Reinstall doors, panels, covers, or guards when servicing and maintenance is finished and before
reconnecting input power.
Overuse can cause overheating
•Use machine follow duty cycle. Reduce current or reduce duty cycle before starting to weld again.
•Allow cooling period.
•Do not block or filter airflow to unit.
Static can damage PCB
•Always wear wrist straps before touching PCB or parts.
•Use proper static-proof bags and package to store or move PCB.
Safety markings
•Equipment with CE-markings meets the basic requirements of the Low-Voltage and Electromagnetic
Compatibility Guideline (e.g. relevant product standards according to EN 60 974).
Safety markings
•The equipment with the CCC mark meets the basic requirements stipulated in the Chinese standards
GB / T15579.1-2013 and GB / T8118.
Safety markings
•This marking means that the product is certified for both the U.S. and Canadian markets, to the
applicable U.S. and Canadian standards. The preferred location of the indicators is as shown.

5
Contents
1 - GENERAL REMARKS............................................................................................................................................... 6
1-1 Power source features............................................................................................................................................... 6
1-2 Functional principle.....................................................................................................................................................6
1-3 Output characteristics.................................................................................................................................................7
1-4 Duty cycle.....................................................................................................................................................................7
1-5 Applications..................................................................................................................................................................8
1-6 Warning label...............................................................................................................................................................8
2 –VERSIONS BRIEFS.................................................................................................................................................... 8
3 -BEFORE COMMISSIONING...................................................................................................................................... 9
3-1 Utilization for intended purpose only........................................................................................................................9
3-2 Machines set-up regulations..................................................................................................................................... 9
3-3 Power source connection.......................................................................................................................................... 9
3-4 Welding cables instruction.........................................................................................................................................9
4- AMIG350LST...............................................................................................................................................................11
4-1 System components.................................................................................................................................................11
4-2 Basic equipments for welding................................................................................................................................. 11
4-3 Control panel............................................................................................................................................................. 11
4-4 Sub menu...................................................................................................................................................................15
4-5 Job mode................................................................................................................................................................... 21
4-6 Interface..................................................................................................................................................................... 23
4-7 Installation..................................................................................................................................................................24
4-8 MIG/LST welding process....................................................................................................................................... 26
4-9 Technical data........................................................................................................................................................... 27
4-10 Dimension................................................................................................................................................................ 27
4-11 Disassembly and reassembly...............................................................................................................................28
5-TROUBLE SHOOTING...............................................................................................................................................30
5-1 Error code.................................................................................................................................................................. 30
5-2 Trouble shooting....................................................................................................................................................... 32
6-CARE AND MAINTENANCE.....................................................................................................................................33

6
1 - GENERAL REMARKS
1-1 Power source features
This series of power sources apply IGBT soft switch inverter technology. Its internal control system applies DSP which
ensures quick response to any change during the welding process so as to achieve precise control of welding process
and ensure optimal welding results. The strong ability of arc self-adjustment ensures a highly stable welding current
against grid fluctuation and arc length change to get optimal results.
This series has 3 core system, almost can communicate with all robots on market by digital /analogue interface. Perform
welding work easily.
Features and benefits:
High speed DSP+FPGA+MCU multi-core system, can shorten control period to control arc effectively;
Periodic molten drop control technology, molten pool is more stable, with beautiful welding seam formation;
Welding spatter for carbon steel decreases 80%, reduce spatter clean work; heat input reduces 10%~20%, small
deformation;
With precise pulse waveform control technology, and lower heat input to avoid burn through and deformation, also
reduce 80% spatter, realize very thin plate low spatter welding. This technology is widely used in bicycle, fitness
equipment, automobile component, and furniture industries;
Built-in start point test function, can achieve welding seam start point test without adding robot hardware (Optional).
1-2 Functional principle
This series of power sources adopt IGBT soft switch inverter technology. 3-phase input voltage are rectified by rectifier,
inverted into HF AC, reduced by HF transformer, rectified and filtered by HF rectifier, chopped and then output DC power
suitable for welding. After this process, the welding machine dynamical responsive speed has been greatly increased, so
the size and weight are reduced noticeably result in energy saving. The control circuit's closed-loop control makes the
power source enjoy strong ability against power grid fluctuation and perfect welding performance. The schematic diagram
is as shown in Fig. 1-2-1:
Fig.1-2-1: Schematic diagram

7
1-3 Output characteristics
Fig. 1-3-1: Output characteristics
1-4 Duty cycle
Duty cycle is percentage of 10 minutes that a machine can weld at rated load without overheating. If overheats,
thermostat(s) will open, output stops. Wait for fifteen minutes for the machine to cool down. Reduce amperage or duty
cycle before welding.
NOTE! Exceeding duty cycle can damage unit and void warranty.
Fig. 1-4-1: Duty cycle

8
1-5 Applications
AMIG350LST series can realize thin plate (less than 3mm thickness) welding of stainless steel, galvanized sheet, carbon
steel.
The power source is designed for the following applications:
- Automated application
- Automobile and components supply industry
- Chemical plant construction
- Boiler and pressure vessel
- Shipyards
- Power plant construction
- Vehicle manufacturing
- Machinery industry
- Robot application (Optional)
- Others
1-6 Warning label
The warning label is affixed onto the top of the power source, and it must not be removed or painted over.
Fig. 1-6-1: Warning label
2 –VERSIONS BRIEFS
Professional welding of special materials requires special welding parameters. Different models of the power sources are
matched to different welding
●AMIG350 LST
AMIG350LST is fully digital MIG series with new Low Spatter technology. Due to high end DSP + FPGA and waveform
control technology. It provides outstanding control of arc and weld pool and bring spatter free welding quality and high
efficient productivity. It has MIG, LST (low spatter technology) welding processes.

9
3 -BEFORE COMMISSIONING
Warning! Operating the equipment incorrectly can cause serious injury and damage. Do not use the functions
described here until you have read and completely understood “safety rules”.
3-1 Utilization for intended purpose only
This series may only be used for MIG, LST. Utilization for other purposes, or in any other manner, shall be deemed to be
"not in accordance with the intended purpose". The manufacturer shall not be liable for any damage resulting from such
improper use. Operate, inspect and maintain should follow all the instructions given in this manual.
3-2 Machines set-up regulations
According to test, protection degree of this power source is IP23. However, the internal key components must be
protected from direct soaking.
Warning! A machine that topples over or falls from its stand can cause injury. Place equipment on an even,
firm floor in such a way that it stands firmly.
The venting duct is very important for safety protections. When choosing the machine location, make sure it is possible for
the cooling air to freely enter and exit through the louvers on the front and back of machine. Any electro conductive
metallic dust like drillings must not be allowed to get sucked into the machine.
3-3 Power source connection
- The power source is designed to run on the voltage given on the nameplate.
- The mains cables and plugs must be mounted in accordance with the relevant technical standards.
- The power supply sockets that come with power source are designed to use strictly according to the marked voltages.
Note! Incorrect installations can lead to protection fails or partial fails. The fuse of mains plug and socket must be
suitable for local power supply.
3-4 Welding cables instruction
When welding, please pay attention to the followings:
a. The welding cables should be kept as short as possible;
b. If extended cable is used, please do as shown in Fig. 3-4-1.

10
Fig. 3-4-1: Welding cables instruction
Wrong
Coil the excess ground cable and welding cable in
same direction respectively.
Correct
Straighten the ground cable and welding cable and
make them close to each other.
Bundle the ground cable and welding cable
together, running the wires close to the ground.
Correct
When the excess cables are only be used by
rolling up, coiling the cables to two windings in
reverse direction and overlap them.
The number of turns for A is same as the number of
turns for B.
Handle the welding cable and ground cable
according to the above-mentioned method.

11
4- AMIG350LST
4-1 System components
This machine can be equipped with many different accessories and can be used in various sites with different
configurations.
Fig. 4-1-1: System components
4-2 Basic equipments for welding
Only be equipped with the necessary accessories, can the power source operates well. The following is the needed
accessories list.
-Power source
-Ground cable
-Welding torch
-Gas regulator, gas hose, gas cylinder (to supply the machine with shielding gas)
-Wire feeder
-Welding wire
4-3 Control panel
The functions on the control panel are all arranged in a very logical way. The various modes and parameters needed for
welding are easy to select by pressing the appropriate button; parameters are easy to adjust by rotating encoder.
Note! You may find that your machine has certain functions or some parameters that are not described in this
operating manual. Also, certain illustrations may be very slightly different from the actual controls on your
machine. However, these controls function in exactly the same way.
Warning! Operating the equipment incorrectly can cause serious injury and damage. Do not use the functions
described here until you have read and completely understood all content of this manual.

12
Note! Control panel of welding machine is for function selection and some parameters setting. Welding
parameters can be adjusted by panel control (sub-menu parameter P09 is ON) and remote control
(sub-menu parameter P09 is OFF).
Fig. 4-3-1: Control panel
1.Adjustment knob
Adjust the parameters. When the light is on, this knob can be used to adjust parameters of selected item.
Reset:Press adjustment knob (1) for about 5 seconds, it comes back to factory set.
Important! Values increase in clockwise direction while values decrease in anti-clockwise rotation. To turn the knob left or
right while pressing it will achieve quick adjustment.
2. Parameters selection button F2
Press this button, one parameter indicator light is on, the corresponding parameter is chosen; keep pressing this button
can switch among the following parameters:
- Arc length adjustment
- Welding voltage
- Job (Channel) No.
If both the indicators of parameter selection button and the adjustment knob (1) are on, the indicated/ selected parameter
can be adjusted with the knob (1).
3.Parameters selection button F1
Press this button, one parameter indicator light is on and the corresponding parameter is chosen; keep pressing this
button can switch among the following parameters:
- Welding current
- Wire speed
- Arc force/ Arc stiffness
Important!On Panel control mode, press F1 to choose one of the above parameters, and value of the parameter can be
adjusted by the knob (1).
4. CALL button

13
Load stored set of parameters.
5.STORE button
- For accessing the sub-menu parameter set-up menu or (in job mode) for storing parameter settings.
- During creating or correcting a job, store parameter settings.
6.Wire diameter button
For selecting wire diameter.
7.Wire material selection button(s)
For selecting the filler metal and shielding gas type. OP is used for upgrade.
8.Torch operation modes button(s)
For selecting the operating mode of the torch.
- 2-step mode (standard operating mode)
- 4-step mode (the trigger lock mode)
- Special 4-step mode (arc-starting and crater-filler parameters are adjustable)
- Spot welding mode
Operating mode of welding torch
Graphic symbol
Fig. 4-3-2: Press torch trigger Fig. 4-3-3: Hold torch trigger Fig. 4-3-4: Release torch trigger
P01…….Burn back time
P03…….Gas pre-flow time
P04…….Gas post-flow time
P05…….Initial period: the base metal can be heated up rapidly, despite the fast thermal dissipation at the start of welding
P06…….Crater filler parameter: Prevent burn-through caused by too much heat at the welding ends.
P07…….Transitional period: the time from welding current to crater-filler current.
P08…….Spot welding time
I………..Welding current: Uniform thermal input for the preheated base metals.
- 2-step mode
Fig. 4-3-5: 2-step mode
- 4-step mode

14
Fig. 4-3-6: 4-step mode
- Special 4-step mode (arc-starting and crater-filler parameters are adjustable)
Fig. 4-3-7: Special 4-step mode
- Spot welding mode
Fig. 4-3-8: Spot welding mode
9.Process button
For select welding process.
- MIG
- LST
10. F2 selection button indicator

15
When the indicator lights up, F2 works
11. “JOB” No.
For receiving parameter records/job numbers that were previously saved with “Store” button.
12.Welding speed indicator
When the light is on, the right display shows the preset welding speed (cm/min) , and the wire speed and welding current
& voltage are calculated as a function of the “a”-dimension parameter (20)
13. Welding voltage indicator
When the indicator lights up, the right display shows the preset or actual welding voltage.
Important! Power source open circuit voltage is variable. In STICK mode, open circuit voltage displayed is about 23V
before welding; after starting arc, it increases as the real situation, and may be up to 79V, so as to get ideal arcing
characteristic.
14. Arc-length correction parameter
For correcting the arc length (-5.0-+5.0) by adjustment knob (1) when indicator is on, the right display shows the arc length
value when the indicator lights up.
- shorter arc length
0 neutral arc length
+ longer arc length
Important!The range (-5.0-+5.0) means that, when preset welding current, the arc length value is -50%~+50%of the
corresponding welding voltage.
15. Temperature Indicator
This is reserved function, cannot operate right now.
16. Arc force/ Arc stiffness
Change the arc stiffness during short circuit transition.
-The arc is hard and stable
0 Medium arc
+ Soft arc and small splash
17.Wire feeding speed indicator
When the indicator is on, the left display shows the wire feeding speed (M/min), when adjust this button, the relevant
parameters will change automatically
18.Welding current indicator
When the indicator is on, the left display shows the preset or real welding current values
19.Sheet thickness indicator
When the indicator is on, the left display shows the preset sheet thickness (mm). The relevant parameters will change
automatically when this value is changed.
20. “a” dimension indicator
When the indicator is on, the left display shows “a” dimension (mm). Wire speed and welding current & voltage are
calculated as a function of the “a”-dimension parameter
21. F1 selection button indicator
When the indicator lights up, F1 button works.
22.CALL program mode indicator
When the indicator is on, power source is in call program mode.
23. Sub menu parameters regulation indicator
This indicator is on when in sub menu parameters adjustment.
4-4 Sub menu
Sub-menu parameter
In order to achieve an optimum welding result, it is necessary in some cases to make corrections of the arc-length, arc
force as well as parameters like pre-gas time, post-gas time and slow wire feeding. For details of how to set the Sub-menu
parameters, please refer to “Sub-menu parameter set”.

16
Item
Parameters
Setting Range
Min. Value
Factory Setting
P01
Burn back time
0.01~2.00s
0.01s
0.10s
P02
Slow wire feeding
1.0~21.0M/min
0.1 M/min
1.5 M/min
P03
Gas pre-flow time
OFF/0.1~10.0s
0.1s
0.20s
P04
Gas post-flow time
0.1~10.0s
0.1s
1.0s
P05
Initial period
1~200%
1%
135%
P06
Crater filler period
1~200%
1%
50%
P07
Transitional period
0.1~10.0s
0.1s
2.0s
P08
Spot welding time
0.01~9.99s
0.01s
3.0s
P09
Digital/Analog signal selection
OFF/ON
――
OFF
P10
Water cooling selection
OFF/ON/ONo
――
ON
P11
Double pulse frequency
OFF/0.5~5.0Hz
0.1Hz
OFF
P12
High pulse group arc length
adjustment
-5.0~+5.0
0.1
0
P13
Double pulse speed offset
0~2m
0.1m
2m
P14
High pulse group duty cycle
10~90%
1%
50%
P15
Pulse mode
OFF/UI/II/UU
――
OFF
P16
Fan-on demand cooling time
5~15min/ON
5min
5min
P17
Special 2-step arc start time
OFF/0.1~10s
0.1s
OFF
P18
Special 2-step arc stop time
OFF/0.1~10s
0.1s
OFF
P19
Separate adjustment mode
OFF/ON
――
OFF
P22
Pulse current when start arc
-50%~50%
1%
0
P23
Pulse time when start arc
-50%~50%
1%
0
P24
Short circuit rise rate
-50%~50%
1%
0
P25
Short circuit rise knee point
-50%~50%
1%
0
P26
Arcing peak value
-50%~50%
1%
0
P27
Arcing peak time
-50%~50%
1%
0
P30
Inch wire feeding speed
1.0~21.0m/min
0.1
3m/min
P31
Molten drop transition time 1
-50%~50%
1%
0
P32
Molten drop transition time 2
-50%~50%
1%
0
P33
Spatter adjust
-50%~50%
1%
0
P34
Ball removing voltage
-50%~50%
1%
0
P35
Ball removing time
-50%~50%
1%
0
Table 4-4-1: Sub menu parameter
Note! P11-P14 is available on double pulse function; P20-P21 is available on twin wire welding mode.
- P01 Burn back time
If too long time, the wire will burn back too much with too large melting ball at the end of wire; if too short time, the wire will
stick with the work piece
- P02 Slow wire feeding
With too quick feeding speed, the wire will be easily exploding with failed arc-starting; if the feeding speed is slower than
the melting speed, the long arc will cause conductive tip burned.
- P03 Gas pre-flow time
Longer time will cause waste of gas and low efficiency; shorter time will cause air hole during arc-starting
- P04 Gas post-flow time

17
Longer time will cause waste of gas; shorter time will cause air hole during crater filler period
- P05 Initial period
Special 4-step mode and set the percentage between initial period and preset parameters. When adjust the initial period,
press F2 and then adjust dial (1), make correction of the arc length of the initial period. Press F2 again to exit.
- P06 Crater filler period
4-sept or special 4-step mode, set the percentage between crater filler period and preset parameters. When adjust the
crater filler, press F2 and then adjust dial (1), make correction of arc length of the crater filler. Press F2 again to exit.
- P07 Transitional period
During the special 4-step mode, the time cost from starting current to normal welding current and then to post current
- P08 Spot welding time
Choose spot welding process and set the welding time
- P09 Digital/Analog signal selection
In ON mode, welding parameters can be adjusted by welding machine control panel, digital wire feeder control panel; in
OFF mode, welding parameters can be adjusted by analog controller.
- P10 Water cooling selection
OFF: gas cooled mode, choose gas cooled torch, no water shortage protection;
ON: water cooled mode, choose water cooled torch, there is water shortage protection.
- P16 Fan-on demand cooling time
Set the time that fan continues to work after power source stops welding.
- P17 Arc start time
On special 2-step mode, time for start period. When choose at number, it is time for start period, when reach to this time,
will turn to welding standard; when choose at OFF, the function closes.
- P18 Arc stop time
On special 2-step mode, time for crater filler time. When choose at number, it is time for crater filler, when reach to this
time, will turn to stop welding standard; when choose at OFF, the function closes.
- P19 Separate adjustment mode
In OFF mode, current and voltage is synergic adjusted; in ON mode, current and voltage is separately adjusted.
- P22 Pulse current when start arc
Too small will cause wire touches with work piece, and arc start fails. Too large will cause large energy when start arc, and
arc has defect.
- P23 Pulse time when start arc
Too short will cause difficult to start arc; too long will cause large energy when start arc, and arc has defect.
- P24 Short circuit rise rate
The higher the short circuit current rise rate is, the harder the arc is, and the large spatter is; otherwise, arc will be softer,
spatter will be lesser. Too small will cause unstable welding.
- P25 Short circuit rise knee point
The higher the short circuit rise knee point is, the harder the arc is; otherwise, the softer the arc is. Recommend to use
factory setting parameter value.
- P26 Arcing peak value
The higher the arcing peak value is, the longer the arc length is, the stronger the directivity is; otherwise the shorter the arc
is, the weaker the arc directivity is. Too low value of this parameter will cause unstable welding.
- P27 Arcing peak time
The longer the arcing peak time is, then the larger arc energy is, the larger welding heat affected zone is; otherwise, the
smaller arc energy is, the smaller welding heat affected zone is. Too low value of this parameter will cause deformed weld.
- P30 Inch wire feeding speed
Set manual wire feeding speed.
- P31 Molten drop transition time 1
This parameter is used together with P32, the longer the time is, the larger arc energy is, the longer droplet transfer time is,
the softer arc is; otherwise, the smaller arc energy is, the shorter droplet transfer time is, the harder arc is. Recommend to
use factory setting parameter value.
- P32 Molten drop transition time 2
This parameter is used together with P31, the longer the time is, the larger arc energy is, the longer droplet transfer time is,
This manual suits for next models
1
Table of contents
Popular Power Supply manuals by other brands

Good Will Instrument
Good Will Instrument PSH Series manual
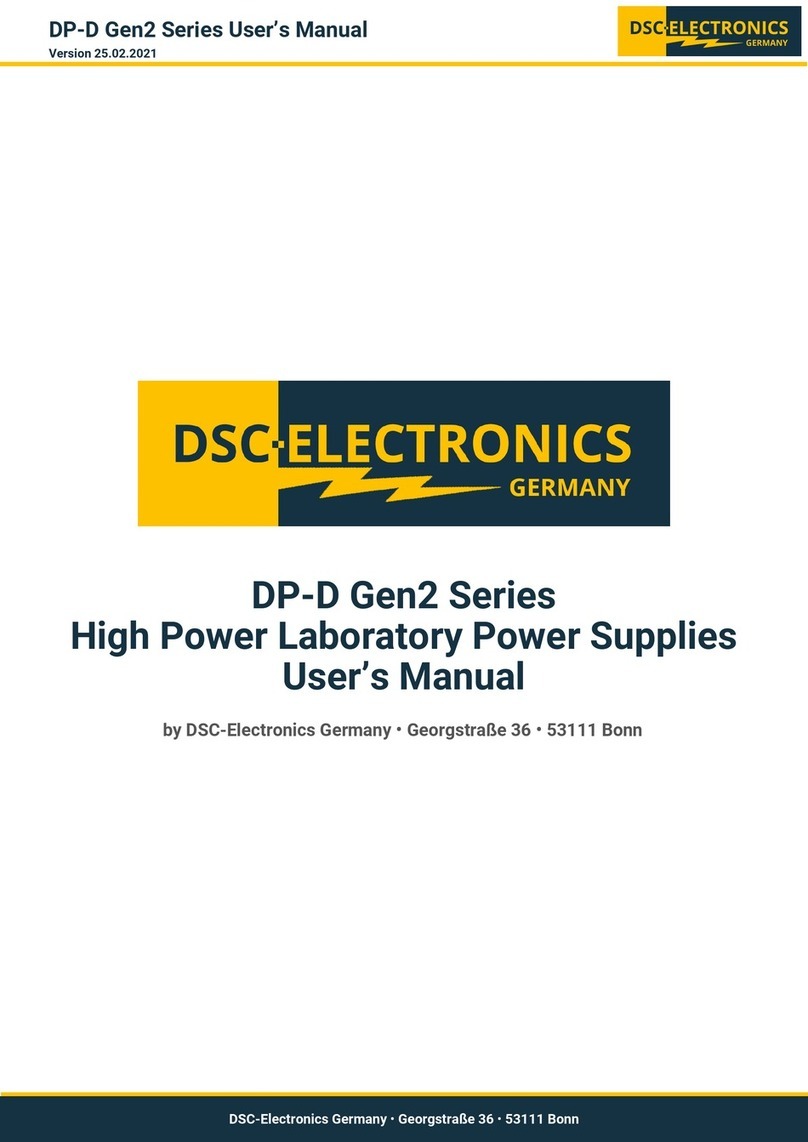
DSC ELECTRONICS
DSC ELECTRONICS DP-D Gen2 Series user manual

Maynuo Electronic
Maynuo Electronic M88 Series user manual
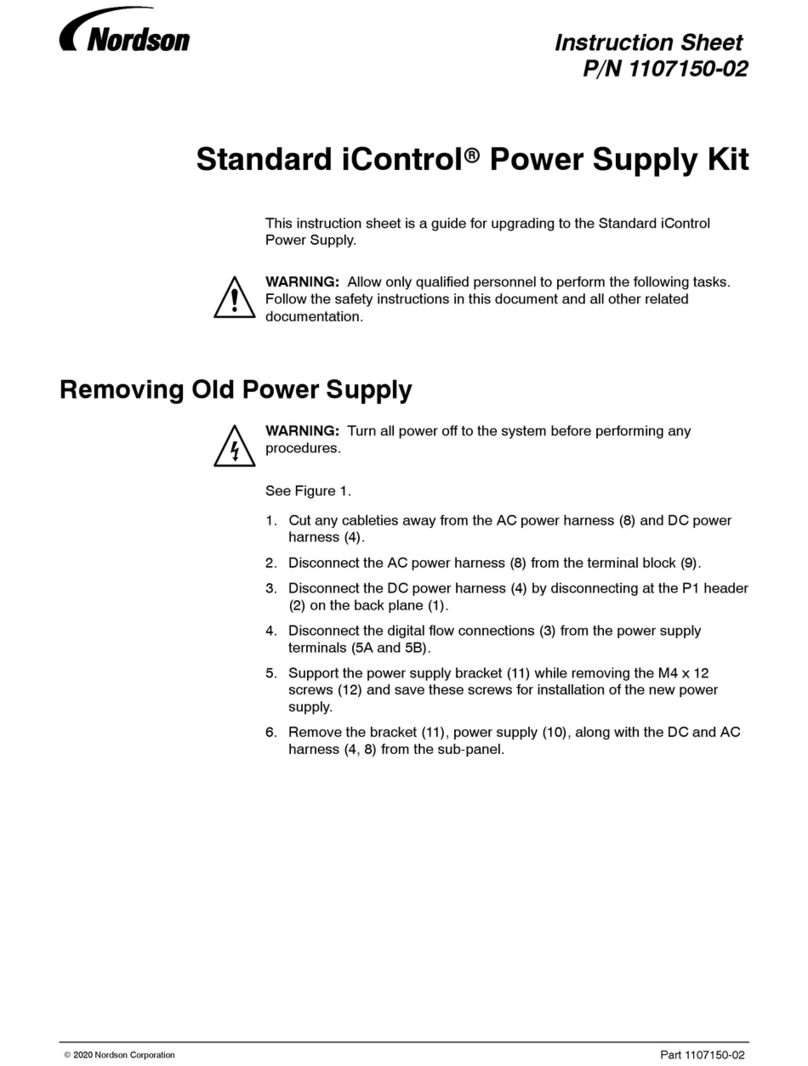
Nordson
Nordson Standard iControl instruction sheet

kenall
kenall MEDMASTER MRIPS Series installation instructions
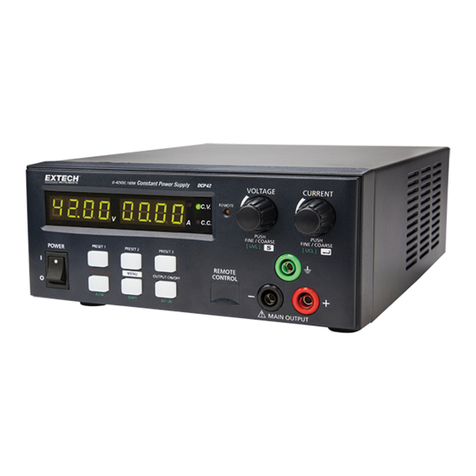
Extech Instruments
Extech Instruments DPC42 user guide