Amit RRU-WTB/AN01 User manual

rru-wtban01_g_en_100
RRU-WTB/AN01
WTB analyser
Operation manual
Version 1.00

RRU-WTB/AN01
rru-wtban01_g_en_100 2/28
AMiT, spol. s r.o. does not provide any warranty concerning the contents of this
publication and reserves the right to change the documentation without
obligation to inform any body or authority about it.
This document can be copied and redistributed under following conditions:
1. The whole text (all pages) must be copied without any changes.
2. All redistributed copies must retain the AMiT, spol. s r.o. copyright notice
and any other notices contained in the documentation.
3. This document must not be distributed for purpose making of profit.
The names of products and companies used herein can be trademarks or
registered trademarks of their respective owners.
AMiT is a registered trademark.
Copyright (c) 2014, AMiT, spol. s r. o.
Producer: AMiT, spol. s r. o.
Naskové 1100/3, 150 00 Praha
www.amit.cz

RRU-WTB/AN01
3/28 rru-wtban01_g_en_100
Contents History of revisions.........................................................................................4
Related documentation...................................................................................4
1. Definition of used abbreviations ........................................................5
2. Definition of used terms......................................................................6
3. Introduction..........................................................................................7
4. Technical parameters..........................................................................8
4.1. Dimensions...................................................................................................11
4.2. Recommended drawing symbol ...................................................................12
4.3. Block diagram...............................................................................................13
5. Conformity assessment ....................................................................14
5.1. Other tests....................................................................................................15
6. Power supply......................................................................................16
6.1. Powering from DC network...........................................................................16
7. Communication lines.........................................................................17
7.1. WTB .............................................................................................................17
7.1.1 WTB line state indication..............................................................................18
7.2. Ethernet........................................................................................................19
7.2.1 Ethernet line state indication ........................................................................20
8. Indications and settings....................................................................21
8.1. System LEDs................................................................................................21
8.2. Service mode and factory setting .................................................................22
8.3. Commissioning.............................................................................................22
9. Mounting, installation rules ..............................................................23
9.1. Mounting instructions....................................................................................23
9.2. Holes for mounting into frame ......................................................................25
9.3. Installation rules............................................................................................25
10. Ordering information and completion .............................................26
10.1. Ordering information.....................................................................................26
10.2. Completion ...................................................................................................26
11. Maintenance .......................................................................................27
12. Waste disposal...................................................................................28

RRU-WTB/AN01
rru-wtban01_g_en_100 4/28
History of revisions
Document name: rru-wtban01_g_en_100.pdf
Author: Jiří Březina
Revision
Date
Changes
100
14. 8. 2014
New document
Related documentation
1. Programmers manual WTB analyser Programmer’s manual
file: tcn-wtb-an_ms_en_xxx.pdf
2. Application Note AP0037 –Principles of using Ethernet network
file: ap0037_en_xx.pdf

RRU-WTB/AN01
5/28 rru-wtban01_g_en_100
1. Definition of used abbreviations
Bus Administrator
Electric Middle Distance
Medium Attachment Unit
To Be Defined
Train Communication Network
Wire Train Bus
BA
EMD
MAU
TBD
TCN
WTB

RRU-WTB/AN01
rru-wtban01_g_en_100 6/28
2. Definition of used terms
Bus Administrator
MVB device with Bus Administrator functionality is able to work as MVB bus
Master. This function supposes the device is able to transfer the process data
and reports as well as transmit and receive the Device Status type information.
Electric Middle Distance
This is a type of physical interface of MVB line, where a shielded twisted pair is
used for interconnection and where transformer coupling is used for galvanic
separation. EMD medium is used for up to 32 nodes and for distances to 200 m.
End Setting
The node in this state is physically connected on the end of WTB line or
between two independent segments. One of the MAU channels is connected in
direction 1 and the second in direction 2. The WTB line segments, connected in
direction 1 and 2 are disconnected. Terminating resistors are connected in both
directions.
Intermediate Setting
The node in this state is physically connected in the middle of WTB line. The
main MAU channel is connected in direction 1 or in direction 2, the auxiliary
MAU channel is deactivated. The WTB line segments, connected in direction 1
and 2 are interconnected. Terminating resistors are disconnected in both
directions.
Line gate (Line Unit)
All HW resources, providing the electrical connection of MAU to the WTB line.
Medium Attachment Unit
Part of node, which arranges the link to transmission medium.
Sleep Mode
In this mode the node goes to End Setting state. Only part of MAU is active.
The node detects valid frames on line.
To Be Defined
Information will be completed in document revision.
TCN Analyser
MVB device with TCN Analyser function is able to access to other buses. This
function supposes the device is able to transfer the process data and reports as
well as transmit and receive the Device Status type information.

RRU-WTB/AN01
7/28 rru-wtban01_g_en_100
3. Introduction
RRU-WTB/AN01 is WTB bus analyser, hereinafter analyser or WTB analyser.
Analyser is intended to be mounted in to the 19“ subrack, or it could be
mounted in to other suitable frame structure. Analyser is equipped with doubled
WTB interface and working Ethernet line with M12 connector.
1 × WTB interface (doubled line)
1 × Ethernet 100 Mbps (connector M12)
Mounting in to the 19“ subrack or in to the frame structure
Basic features

RRU-WTB/AN01
rru-wtban01_g_en_100 8/28
4. Technical parameters
Number of WTB lines
1 (doubled line)
Operation indication
16 × LED
Galvanic separation
Yes, 1000 V AC / 1 minute 1)
Fritting
No
Communication rate
1 Mbps 0,01 %
Max. number of devices
32
Max. segment length without repeater
860 m
Characteristic impedance
120 Ω 2)
Connection points
4 × D-sub DE-9,
according to IEC 61375-1:2007,
connector fixing by M3 bolt
Standards
IEC61375-1:2007 (Ed. 2.0)
UIC CODE 556:2010 (Ed. 5.0)
1) Galvanic separation must not be used for dangerous voltage separation.
2) Terminator is included in unit. Connection of terminator at end node is
provided automatically by unit firmware.
Number of interfaces
1
Operation indication
2 × LED (LNK and ACT)
Galvanic separation
Yes, 1000 V AC / 1 minute 1)
Data transmission rate
100 Mbps
Recommended cabling
UTP CAT5
Maximum segment length
100 m
Operation indication
LED (LNK and ACT)
Connection point
M12 connector
according to IEC 61375-3-4:2012 (Ed.1.0)
D-coding
1) Galvanic separation must not be used for dangerous voltage separation.
Power supply voltage range
(permanent)
16.8 V to 30 V DC
Maximum power consumption
Max. 0.6 A at 24 V DC
Max. 1.0 A at 16.8 V DC
Starting peak current
Max. 30 A at 24 V DC
Max. 48 A at 30 V DC
Galvanic separation
Yes, 1000 V AC / 1 minute 1)
Connection point
Connector WAGO 769-663/003-000
Connector counterpart
Connector WAGO 769-103/021-000
Wire cross section
0.75 mm2to 2.5 mm2
1) Galvanic separation must not be used for dangerous voltage separation.
WTB
Ethernet
Power supply

RRU-WTB/AN01
9/28 rru-wtban01_g_en_100
Mechanical design
Compact aluminium tube, anodized black
Front and rear panel made of aluminium
alloy with anti-corrosion coating 1)
Mounting
Into 19“ subrack
Ingress protection rate
IP30 2)
Weight –netto
–brutto
1.55 kg ±5 %
1.85 kg ±5 %
Dimensions in standard units (w × h)
28 HP × 3 U 3)
Dimensions (w × h × d)
(142 × 129 × 204) mm 4)
1) Front panel is made from aluminium alloy without detail specifying of
additives composition. Surface is naturally anodized.
2) After all cable connectors are connected.
3) 1 HP (horizontal pitch) = 0.2 inch (5.08 mm),
1U (rack unit) = 1.75 inch (44.45 mm).
4) Depth, including inserted power supply connector.
Unit overall mass of plastics
213 g
Included mass of self-extinguishing
plastics
213 g
Device does not contain
PUR, PVC, Asbestos
Device conforms
2011/65/EU (ROHS)
1907/2006EU (REACH)
Operating temperature range
-40 °C to 70 °C
Operating temperature range
-40 °C to 70 °C
Maximum ambient humidity
< 95 % non-condensing
Reliability (MTBF) min.
180 000, at 40 °C ambient temperature,
methodology acc. to MIL HDBK217F2 Part
Stress 1)
1) Contact manufacturer for updated values.
None
Analyser is supplied with loader, which enables software downloading by application
ADS Manager via Ethernet line.
WTB analyser is intended to operate up to 1 400 m above the sea level.
WTB analyser is designed to meet the Temperature Class TX.
According to EN 61373:2010 standard, the equipment is classified in terms of
vibrations into Category 1, Class A (mounting to vehicle body).
Permissible supplying voltage drop-outs duration: max 10 ms (Class S2 according to
Chapter 3.1.1.2 of EN 50155:2007.
For supply voltage switching –conditions of C1 and C2 Class are permissible.
Mechanics
Dangerous
materials
Temperatures
Others
Components
with reduced
lifetime
Software
Claims of EN
50155:2007

RRU-WTB/AN01
rru-wtban01_g_en_100 10/28
The equipment meets the SWSIL0 classification according to EN 50128:2011
Railway applications –Communications, signalling and processing systems –
Software for railway control and protection systems.
The equipment meets the SIL0 classification according to EN 50129:2003 Railway
applications –Communication, signalling and processing systems –Safety-related
electronic systems for signalling.
Safety
classification

RRU-WTB/AN01
11/28 rru-wtban01_g_en_100
4.1. Dimensions
142
139
168,5
171
204
129
33
Fig. 1 - Analyser mechanical dimensions

RRU-WTB/AN01
rru-wtban01_g_en_100 12/28
4.2. Recommended drawing symbol
Following drawing symbol is recommended for RRU-WTB/AN01 module.
X1
24 V
WAGO 769-663
RRU-WTB/AN01
X2
X3
X4
X5
X6
Ethernet
M12
WTB A1
D-sub DE-9
WTB A2
D-sub DE-9
WTB B1
D-sub DE-9
WTB B2
D-sub DE-9
Fig. 2 - Recommended drawing symbol

RRU-WTB/AN01
13/28 rru-wtban01_g_en_100
4.3. Block diagram
FPGA
Power
supply
DDR2
WTB
interface
Ethrenet
interface
X2 X3 X4 X5 X6
WTB A1 WTB A2 WTB B1 WTB B2Ethernet
2.5 V ss.
1.8 V ss.
1.2 V ss.
X1
Power
24 V ss. Power
supply
5 V ss.
5 V ss.
Fig. 3 - RRU-WTB/AN01 analyser block scheme

RRU-WTB/AN01
rru-wtban01_g_en_100 14/28
5. Conformity assessment
Providing that RRU-WTB/AN01 analyser is correctly used, it will comply the
requirements of Czech governmental decree NV616/2006. The conformity
assessment has been carried out in accordance with harmonized standard EN
50121-3-2:2006.
Tested in accordance
with standard
Type of test
Classification
EN 55011:2009
Industrial, scientific and medical
equipment –Radio-frequency
disturbance characteristics –Limits and
methods of measurement
Complies
EN 61000-4-2:2009
Electromagnetic compatibility (EMC) –
Part 4-2: EMC –Testing and
measurement techniques –Indirect
electrostatic discharge immunity test,
contact discharge
Complies
8 kV
EN 61000-4-2:2009
Electromagnetic compatibility (EMC) –
Part 4-2: EMC –Testing and
measurement techniques –Indirect
electrostatic discharge immunity test,
aerial discharge
Complies
16 kV
EN 61000-4-3:2006
Electromagnetic compatibility (EMC) –
Part 4-3: Radiated, radio-frequency,
electromagnetic field immunity test,
800 MHz to 1000 MHz
Complies
20 V/m
EN 61000-4-3:2006
Electromagnetic compatibility (EMC) –
Part 4-3: Radiated, radio-frequency,
electromagnetic field immunity test,
1000 MHz to 2100 MHz
Complies
10 V/m
EN 61000-4-3:2006
Electromagnetic compatibility (EMC) –
Part 4-3: Radiated, radio-frequency,
electromagnetic field immunity test,
2100 MHz to 2500 MHz
Complies
5 V/m
EN 61000-4-4:2012
Electromagnetic compatibility (EMC) –
Part 4-4: Testing and measurement
techniques –Electrical fast
transient/burst immunity test / WTB,
CAN
Complies
2 kV
EN 61000-4-5:2006
Electromagnetic compatibility (EMC) –
Part 4-5: Testing and measurement
techniques –Part 5: Electrostatic
discharge –immunity test
Complies
2 kV
EN 61000-4-6:2009
Electromagnetic compatibility (EMC) –
Part 4-6: Testing and measurement
techniques –Immunity to conducted
disturbances, induced by radio-
frequency fields
Complies
10 V

RRU-WTB/AN01
15/28 rru-wtban01_g_en_100
5.1. Other tests
RRU-WTB/AN01 WTB analyser has been assessed and approved for use in
railway applications according to standards:
Tested in accordance
with standard
Type of test
Result
EN 50155:2007
Electronic equipment used on rolling stock.
Complies
EN 50121-3-2:2006
Electromagnetic compatibility (EMC) –
Part 3-2 Rolling stock –equipment
Complies
EN 61373:2010
Railway applications –Rolling stock
equipment –Shock and vibration tests.
Category 1,
Class B
EN 61000-4-29:2000
Electromagnetic compatibility (EMC) –Part
4-29: Testing and measurement
techniques –Voltage dips, short
interruptions and voltage variations
immunity tests
S2, C1, C2
EN 60068-2-1:2007
Environmental testing –Part 2-1: Test –
Test A: Cold
Complies
EN 60068-2-2:2007
Environmental testing –Part 2-2: Test B:
Dry heat
Complies
IEC61375-1:2007
(Ed 2.0)
Electric railway equipment –Train bus –
Part 1: Train Communication Network
Complies
IEC61375-2:2007
(Ed 1.0)
Electric railway equipment –Train bus –
Part 2: Train communication network
conformance testing
Complies
UIC CODE 556:2010
(Ed 5.0)
Information transmission in the train (train
bus)
Complies
MIL HDBK217F2
Military handbook –Reliability prediction of
electronic equipment
Complies
ČSN EN 45545-2
Railway applications –Fire protection on
railway vehicles
HL3

RRU-WTB/AN01
rru-wtban01_g_en_100 16/28
6. Power supply
The RRU-WTB/AN01 WTB analyser can be powered by 24 V DC vehicle
on-board network.
6.1. Powering from DC network
Power supply is connected to X1 WAGO 769-663 (X-COM®), plug.
Fig. 4 - Power supply connector location
Connector WAGO 769-663/003-000
Terminal
Signal
Signal wiring on RRU-WTB/AN01
1
PE
Unit chassis
2
GND
Power supply, ground
3
Vcc
Power supply, +24 V DC
PWR X1
connector
wiring

RRU-WTB/AN01
17/28 rru-wtban01_g_en_100
7. Communication lines
7.1. WTB
RRU-WTB/AN01 WTB analyser has available a WTB interface with doubled
line, according to IEC 61375-1 ed. 2 standard.
Both lines are connected through D-sub DE-9 connectors. Connectors are fitted
with M3 threaded nuts, that secures cable against extraction or falling off due to
vibrations.
Fig. 5 - Location of WTB line connectors
Connector type: D-sub DE-9, plug
Connector
PIN
Signal wiring on RRU-WTB/AN01
X3, X5
1
WTB line positive wire
2
WTB line negative wire
3
Not used
4
Not used
5
Not used
6
Not used
7
Not used
8
Not used
9
Not used
WTB line
connectors
wiring
54321
9876

RRU-WTB/AN01
rru-wtban01_g_en_100 18/28
Connector type: D-sub DE-9, socket
Connector
PIN
Signal wiring on RRU-WTB/AN01
X4, X6
1
WTB line positive wire
2
WTB line negative wire
3
Not used
4
Not used
5
Not used
6
Not used
7
Not used
8
Not used
9
Not used
7.1.1 WTB line state indication
Indication of WTB line state is provided by 16 LEDs in the middle part of front
panel. Six of these LEDs in WTB A area indicate the state of line A, six LEDs in
WTB B area indicate the state of line B and remaining four LEDs indicate the
node state. Following table describes meaning of the individual LEDs:
Fig. 6 - LEDs front panel detail (WTB)
LED
Color
Meaning
TL1
Green
Trusted Line, direction 1
TL2
Green
Trusted Line, direction 2
RX1
Green
Data reception from direction 1
RX2
Green
Data reception from direction 2
D1
Yellow
Disturbance, direction 1
D2
Yellow
Disturbance, direction 2
WMS
Green
Node is in Master composition
SLP
Green
Node is in Sleep Mode
END
Green
Node is in End Setting state
INT
Green
Node is in Intermediate Setting state
Meaning of
LED
12345
6789

RRU-WTB/AN01
19/28 rru-wtban01_g_en_100
7.2. Ethernet
The Ethernet 100 Mbps interface allows the WTB analyser to connect to LAN
network. Ethernet interface is fitted with M12 connector according to
IEC 61375-3-4:2014.
Fig. 7 - Location of Ethernet line connector
M12 type connector according to EN 61375-3-4:2014
Connector
PIN
Signal
X1
1
Tx+
2
Rx+
3
Tx-
4
Rx-
M12 type
Ethernet
connector
wiring

RRU-WTB/AN01
rru-wtban01_g_en_100 20/28
7.2.1 Ethernet line state indication
Indication of Ethernet line state is provided by two LEDs, located above the
RJ45 connector.
Fig. 8 - Front panel LEDs detail (Ethernet)
LED
Color
Meaning
LNK
Green
Analyser connected to the Ethernet network
ACT
Green
Frame reception or transmission
Meaning of
LED
Table of contents
Other Amit Measuring Instrument manuals
Popular Measuring Instrument manuals by other brands
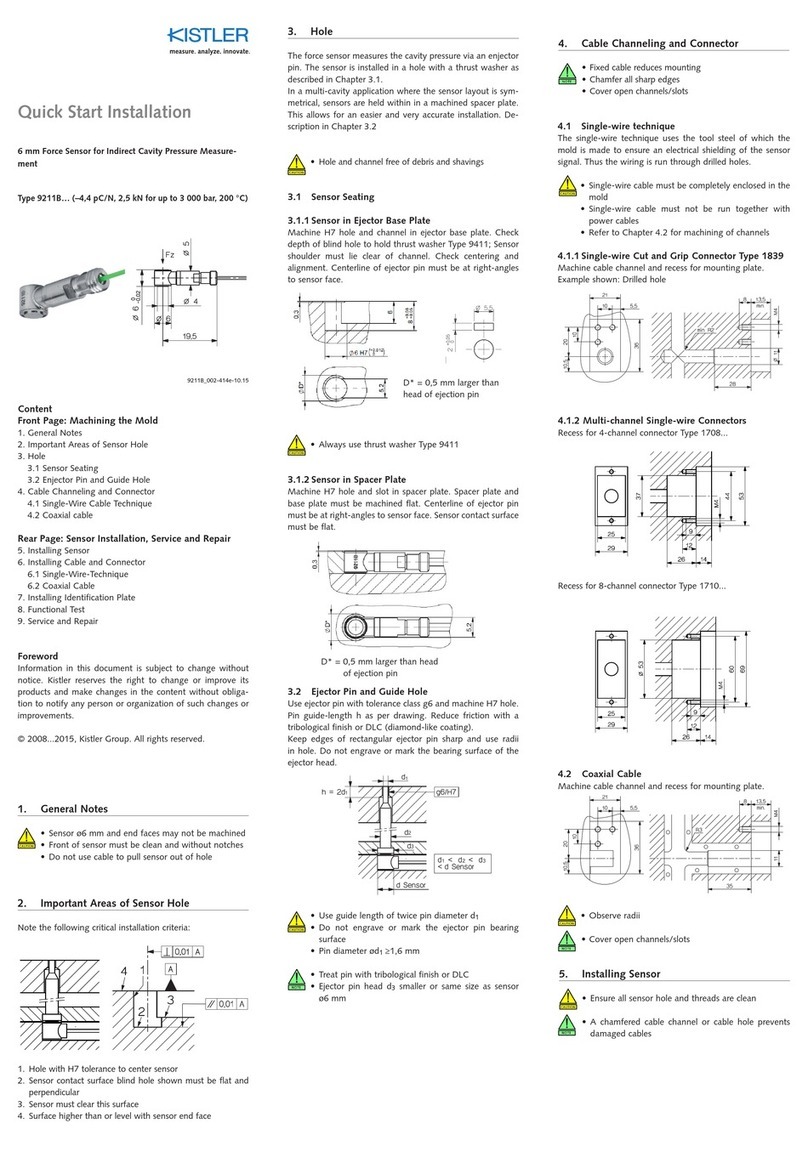
Kistler
Kistler 9211B Series Quick Start Installation

TED
TED Pro Commercial installation manual

Ronde & Schwarz
Ronde & Schwarz ZVH4 quick start guide
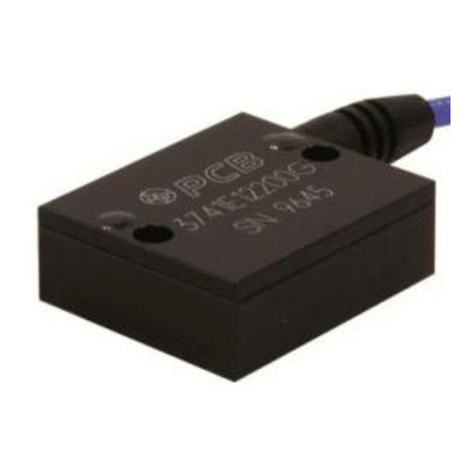
PCB Piezotronics
PCB Piezotronics 3741E1250G Installation and operating manual

Hioki
Hioki CM4142-20 instruction manual
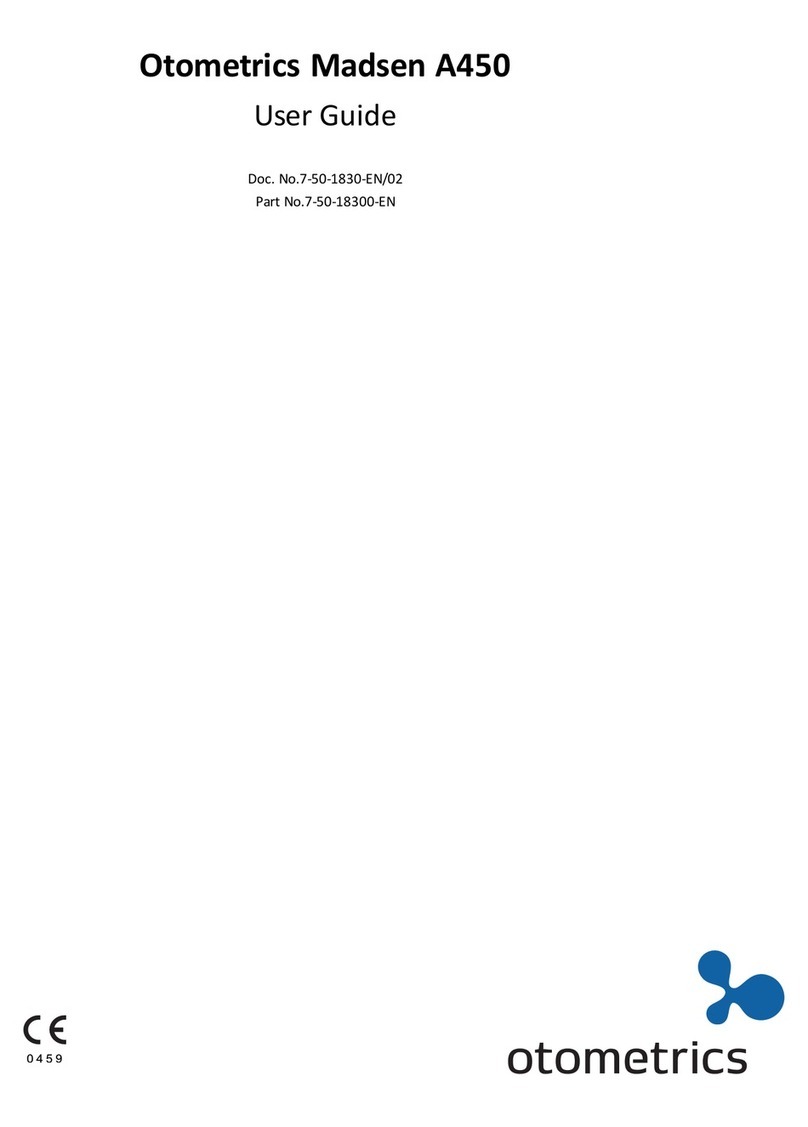
Ottometrics
Ottometrics A450 user guide
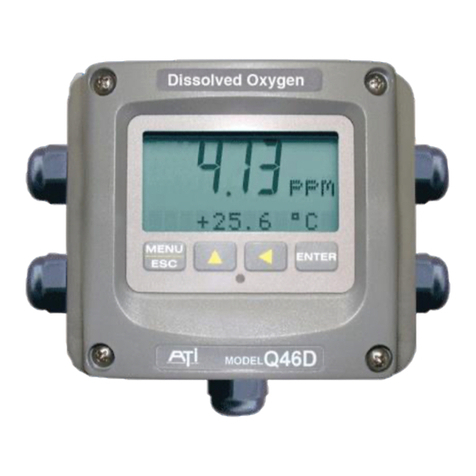
ATI Technologies
ATI Technologies Q46 Series O & M Manual
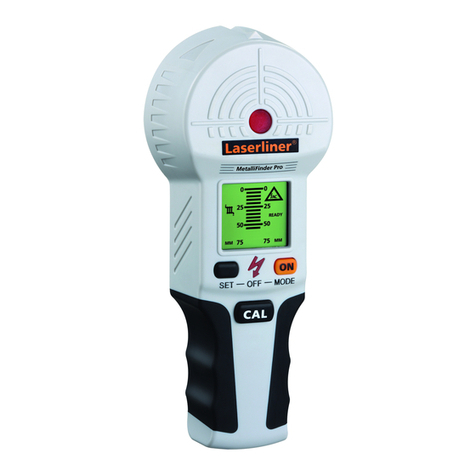
LaserLiner
LaserLiner MetalliFinder Pro manual
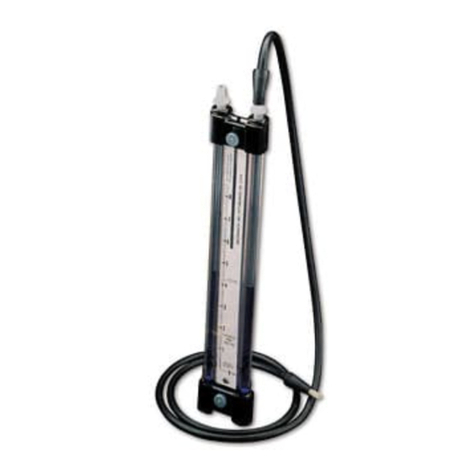
Bacharach
Bacharach MANOMETER GAS PRESSURE GAUGE manual
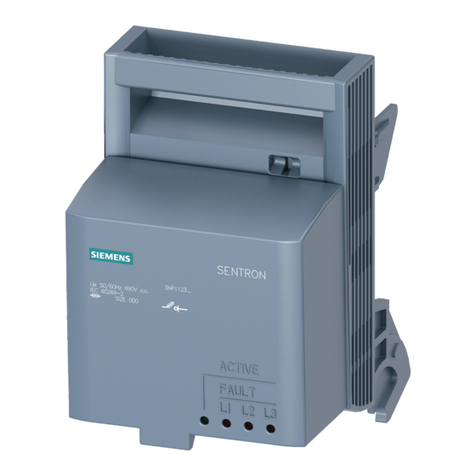
Siemens
Siemens 3NP19-1GB Series operating instructions

Endress+Hauser
Endress+Hauser Levelflex FMP56 operating instructions
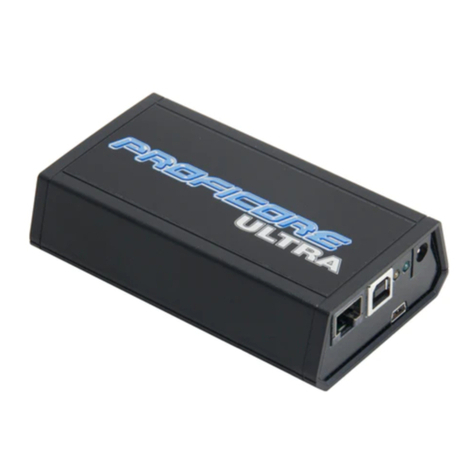
Procentec
Procentec ProfiTrace 2 user manual