AMS AMS KCU Operation manual

L0243A
i
AUTOMATED MERCHANDISING SYSTEMS INC.
255 WEST BURR BLVD.
KEARNEYSVILLE, WV 25430
(304) 725-6921
(304) 725-6983 FAX
www.amsvendors.com
INTERNATIONAL A.M.S. S DE RL DE CV
KM. 9 CARR. AL CASTILLO NO. 8200
MPIO. DE EL SALTO, JAL. MEXICO 45680
5233-36-88-07-17
5233-3-6-88-13-14 FAX
www.amsint.com.mx
OPERATION AND SERVICE
MANUAL,
KCU CONTROL BOX
L0243 REV A

L0243A
ii
LIMITED WARRANTY
Automated Merchandising Systems, Inc. (AMS) warrants this equipment to the Original Purchaser only, for a
period of one (1) year from the date of shipment, to be free under normal use and service from defects in material
or workmanship. Lights, plastic doors, and painted surfaces are not covered by this warranty.
Should any part prove defective within the warranty period, AMS will repair or replace (at its option) the defective
component. AMS will provide normal ground shipment for parts replaced under warranty. This warranty does not
cover the labor or other costs associated with removal and reinstallation of a defective component. All defective
components, at the option of AMS, are to be returned, properly packaged, freight prepaid, to AMS or to the
authorized dealer or distributor from whom the equipment was purchased for verification of the defect. Prior to
returning any parts for replacement, the customer is to contact the AMS Service Department at (304) 725-6921 for
return authorization. AMS reserves the right to refuse any collect shipment.
This warranty applies only if the equipment has been serviced and maintained in strict accordance with the
instructions presented in the AMS service manual and no unauthorized repair, alteration, or disassembly has been
done. Any defects caused by improper power source, abuse of the product, accident, alteration, vandalism,
improper service techniques, or damage incurred during return shipment due to improper packaging will not be
covered by this warranty. Likewise, any equipment that has had the serial number removed, defaced or otherwise
altered will not be coved by this warranty.
AMS reserves the right to make changes or improvements in its products without notice and without obligation, and
without being required to make corresponding changes or improvements in equipment already manufactured or
sold.
AMS SHALL NOT BE BOUND BY ANY REPRESENTATION OR WARRANTY MADE BY ANY
PERSON, INCLUDING BY EMPLOYEES OF AMS, EXCEPT AS SET FORTH IN THIS
LIMITED WARRANTY.
AMS DISCLAIMS ANY AND ALL OTHER EXPRESS OR IMPLIED WARRANTIES OF ANY
NATURE, INCLUDING WITHOUT LIMITATION, WARRANTIES OF MERCHANTABILITY,
FITNESS OF A PARTICULAR PURPOSE OR OTHER IMPLIED WARRANTIES.
Publicaon Noce
It is our intent to assist our customers with up-to-date documentation: however, this manual may not
contain all updates and is subject to revision without notice.
Please contact our Service Department with your requests or comments.

L0243A
iii
TABLE OF CONTENTS
TITLE Page
LIMITED WARRANTY ii
PUBLICATION NOTICE iii
1 INTRODUCTION 1
MODEL IDENTIFICATION
GENERAL SPECIFICATIONS
Operating Environment
Cabinet Dimensions
Shipping Weight
Unit Capacity
Power Requirements
Patent Disclosure
2 SAFETY 3
COMMITMENT TO SAFETY
SAFETY PRECAUTIONS
To Protect Yourself from Injuries
High Voltage Contact
Grounding
Ground Fault Circuit Interrupter
Latch Motor
Locker Tipping
To Safely Move Machine
Unattended Open Doors
Other Improper Conditions
Wire Harnesses
TEST STANDARDS
3 PREPARATION AND INSTALLATION 5
INTRODUCTION
PREPARATION
Inspection
INITIAL CONNECTIONS AND POWER-UP
Initial Power-up
Configuring Motors
Test Loading and Configuration
ON-SITE INSTALLATION
Mounting the Control Box to the Locker
Installing additional lockers
Removing a control box from a locker
Mounting the Locker to the Wall
4 TROUBLESHOOTING 7
MACHINE TROUBLESHOOTING CHART
5 MAINTENANCE 8
CLEANING THE CABINET
MANUALLY UNLOCKING DOORS
6 WIRING DIAGRAM 9
WIRING DIAGRAM
Power-down before disconnecting anything!
TABLE OF FIGURES
NUMBER NAME PAGE
Figure 1.1 Serial Plate 1
Figure 1.2 Cabinet Dimensions 2
Figure 3.1 Lower Support Plates 6
Figure 3.2 Installation of Wall Anchors 7
Figure 5.1 Manually open Locker Door 9
Figure 6.1 Wiring Diagram 10-11
.

L0243A
1
1-1602-1156
Built Year Month Sequence
AMS KCU
Manufacturer Model
Congratulations on the purchase of your new AMS KCU control
box. AMS machines are designed, tested, and built to provide
years of reliable, low-maintenance service in an indoor
environment.
MODEL IDENTIFICATION
When requesting service, replacement parts or technical
assistance, please refer to the Serial Plate. (See Figure 1.1) It is
located at the top of the rear panel. The information contained on
this plate is necessary to determine what parts, kits, or main-
tenance should be applied to your specific model.
AMS KCU
Manufacturer Model
Figure 1.1 Serial Plate
Serial Numbering and Date Code System. (See Figure 1.1)
The first digit identifies where the locker was manufactured.
Those built in the U.S. start with the number 1. Those lockers
built in Mexico start with the number 2.
The next two digits identify the year of manufacture. These
numbers are 19 (for 2019) and so forth.
The next two digits identify the month. The first month of the year
is 01 and the last month is 12.
The last four digits identify the number assigned to each locker
during production. Numbering starts with 0001 and continues
through 9999.
An example of the numbering system in use is as follows:
1-1602-1156
This unit was manufactured at the Kearneysville, W.V. plant in
2016, in February, and was the 1,156th machine manufactured.
GENERAL SPECIFICATIONS
Operating Environment
These AMS control boxes are designed for indoor use only.
Indoor temperatures must be between 33°F (1°C) and 110°F (43°
C). The control box should not be located in an area where it may
be subjected to water or rain.
Cabinet Dimensions:
See Figure 1.2
The KCU are normally shipped attached to a standard vendor or
locker. This is shipped on a pallet that measures
33” wide, and 54” deep.
Unit Weight:
Model AMS KCU = Approx. 205 lbs. (93kg.)
Unit Capacity:
This unit will control up to 4 of the KLx-series lockers.
Power Requirements:
120VAC, 3A is supplied to the control box, and then supplies up
to four lockers at 28volts DC controlling locking latches, and
12Volts DC to power the LED lights.
Patent Disclosure:
This locker and/or certain of its components may be covered by
one or more of the following U.S. and International patents:
U.S.
6,145,699 6,384,402 6,520,373
6,708,079 6,794,634 7,191,915
7,343,220 7,742,837 7,446,302
8,003,931
Canada Mexico
2,329,314 230,714
1
INTRODUCTION

L0243A
2
1 INTRODUCTION
Figure 1.2 AMS KCU Dimensions (For Reference Only)
10.854
65.848
28.897

L0243A
3
COMMITMENT TO SAFETY
Automated Merchandising Systems Inc. is committed to
designing and producing a safe product. As with all electrical or
mechanical pieces of equipment, some potential hazards exist.
It is the intent of Automated Merchandising Systems, through
this manual and service technician training, to alert individuals
who will be servicing our equipment to these potential hazards,
and to provide basic safety guidelines.
To reduce the risk of serious injury or death, please read and
follow all warnings in this manual. It is important we point out
that these warnings are not comprehensive. Automated
Merchandising Systems cannot possibly anticipate all of the
ways that service may be conducted, or all of the possible safety
hazards that may result from service. Therefore at all times we
urge you to beware of hazards such as electrical shock,
mechanical entrapment, and tipping a locker during movement.
Automated Merchandising Systems strongly recommends a
commitment to safety on the part of all servicing personnel or
organizations. Only personnel properly trained in locker
servicing should attempt any service to the internal components
of the locker. Automated Merchandising Systems has no control
over the locker once it leaves our factory.
Maintaining the control box and lockers in a safe condition
is the sole responsibility of the owner.
If you have questions concerning safety or service, or would like
more information, please contact the Automated Merchandising
Systems Service Department at 304-725-6921 or email
SAFETY PRECAUTIONS
Safety precautions and safe practices to follow to avoid injury
from specific hazards are listed below. This list cannot possibly
cover all hazards, therefore please remember to
To Protect Yourself from Injuries
Plan ahead to employ proper personal protective equipment
(PPE), including safety glasses, slip resistant steel-toed boots
and leather/protective gloves. Don’t place hands against edges
of metal openings or bare parts inside the machine. Beware that
parts on the inside of the enclosure can be sharp.
High Voltage Contact
All electrical power comes from either single phase 115VAC
60Hz or 220-240VAC 50-60Hz, depending on the country. The
voltage is specified on the serial plate. High voltage areas
include the space behind the electrical panel. It is important to
understand that contact with the high voltage wiring can result in
injury or death.
• Always test the outlet for proper voltage, polarity
and grounding before plugging in the control box.
• Always disconnect power at the receptacle before
servicing. Allow only fully trained service
technicians to service the merchandiser.
• Always keep electrical connections dry. Do not
place the control box or operate the lockers in or
near standing water.
• Never use a worn or damaged power cord.
Grounding
Some electrical components in the control box have a green or
green/yellow ground wire attached to a grounding point If it
becomes necessary to remove a ground wire during service,
note how the wire is attached, including the locations of any
washers. After servicing, make sure that the wires and washers
are replaced exactly as they were. Note that the control box and
lockers may appear to work normally without the ground wires,
but there will be a potential shock hazard from ungrounded
components.
• Always test the outlet for proper grounding before
plugging in the merchandiser.
• Always reconnect ground wires after servicing.
• Test the ground fault circuit interrupter (GFCI)
periodically to insure proper operation.
Ground Fault Circuit Interrupter
The control box is equipped with a Ground Fault Circuit
Interrupter (GFCI), in compliance with UL 943, as required by
ANSI/UL 751.
Latch Motor
Energized latch motors can turn with considerable torque,
creating a possible entrapment hazard.
• Always disconnect power to the control board
before servicing the latch motors.
• Always wear hand and eye protection when
servicing the merchandiser.
• Always keep hands, hair, loose clothing and tools
away from moving parts.
Locker Tipping
The weight of an empty locker is over 350 pounds, and can be
more than 900 pounds when loaded! A falling locker can cause
serious injury or death. Caution should always be taken to avoid
THINK SAFETY FIRST!
2
SAFETY

L0243A
4
dropping or tipping a locker. We strongly recommend fastening
the machine to an adjacent wall. See MOUNTING THE
LOCKER TO THE WALL in Section 3.
• Never rock or tip the locker. It must be kept
horizontal for safe operation.
• Never place the locker in an inclined position,
such as on a ramp or with all the legs not on the
same horizontal surface.
• Never place the locker in a moving environment
such as on a ship without properly securing it in
place.
• Never place the locker in a location where it may
be struck by a vehicle.
• Never transport an unsecured locker, or a locker
still containing product.
• Never attempt to lift or move the locker by hand.
Always use equipment with the proper load rating.
To Safely Move Machine
If you need to move your locker, you’ll want to use a material
handling device, such as a pallet jack, appliance dolly or forklift
to position it. Make certain that the doors are shut and secured.
Unattended Open Locker Doors
Never leave doors open when not in use. Open doors can be a
hazard to those walking by. Always close door after a
transaction. Also when filling the machine, be wary of open
doors when reaching down to pick up items to fill the machine.
Other Improper Conditions
Hazardous conditions can be created by improper use or
service of the locker.
• Always reinstall any parts removed during service
to their original locations.
• Never make unauthorized modifications to any
part of the locker.
• Always replace components that are worn,
broken, or otherwise unfit for use.
• Never use unauthorized parts, or use parts for
anything other than their intended use.
Wire Harnesses
All components of this locker are UL recognized (if applicable),
including the wire harnesses. Care should be taken when
connecting or disconnecting, and protecting all wires from
pinching or sharp metal edges.
TEST STANDARDS
The AMS control box bearing the ETL mark has been tested
and complies with
UL 62368-1:2019 Ed 3
Audio/Video, Information and communication
Technology Equipment—Part 1: Safety Requirements
CSA C22.2#62368-1:2019 Ed3
Audio/Video, Information and communication
Technology Equipment—Part 1: Safety Requirements
AMS merchandisers bearing the CE mark have been tested and
comply with
CE (European Conformity)
European Union
European Economic Area
IEC 62368-1 2018
Audio/Video, Information and communication
Technology Equipment—Part 1: Safety Requirements
Always wear hand and eye
protection when servicing
the locker.

L0243A
5
INTRODUCTION
The KCU Control Box is designed to attach to the side of a KLx
locker cabinet, and can control up to three additional lockers
using this one consolidated power and control system.
PREPARATION
Inspection
Inspect the Locker and control box carefully for shipping damage
prior to signing the carrier’s delivery receipt. Check for dents on
the top, back or sides of the Locker, bent legs or feet, or other
damage on the exterior of the machine. Check the interior for
components that may have been knocked loose or other
damage.
INITIAL CONNECTIONS AND POWER-UP
After ensuring the control box is safely attached to the locker
cabinet, open the door and familiarize yourself with the basic
components. The VMC (control board), display, keypad, and
some harnesses are similar to those used in other AMS vendors.
The high-voltage components are located behind the front panel:
loosen the two bottom screws, and remove the top screw to
access this area. This area should only be accessible when the
vendor is unplugged, and only by qualified Service Personnel.
Initial Power-Up
1. Plug in the control box.
2. Check that the lights inside the lockers come on.
3. Enter the service mode and check that all settings
are correct. Run Tray Setup | Configure (see next
paragraph). All trays should be set to Motor Type
“HOME ONLY/3.”
4. Check error codes for problems.
5. Open all doors, using Test Motors, and then close
them to verify operation.
6. When product is loaded, load the bottom-most
lockers first, one at a time. To avoid risk of colliding
with open doors, close the door after filling before
opening next locker door.
7. Ensure vendor is operating properly.
Configuring Motors
The motors MUST BE CONFIGURED after any changes in the
arrangement or numbers of motors have been made.
1. Press the service mode switch on the VMC of the
control merchandiser.
2. Using the # or the * key, scroll through the menu to
“TRAY SETUP”.
3. Press 6 to configure the motors. Each switched
motor is moved to the home position (moving the
motor only if it is not at home) in addition to
detecting connected motors.
4. If the number of motors displayed does not match the
number of latches in the vendor plus selections on
the control vendor, press 1 * 0 7 from tray setup to
open all the doors in the vendor.
5. Watch the display for missing motors that should be
connected.
6. The vendor will not open a given door when the
motor is missing, jammed or has home switch
problems.
Finally, test locker operation by selecting one of the selections
through the normal purchasing process.
NOTE: Disconnect Extension Harness to any additional lockers
before moving machines to permanent location.
Test Loading and Configuration
Before putting the Locker on location, it is a good idea to
determine the placement of products in the compartments.
Place several products in each compartment to check for fit.
Make sure the product can slide in and out of the locker
compartment easily, or place it in a larger locker.
Mounting the Control Box to the Locker
If the control box is unmounted, or needs to be transferred, the
following procedure may be used .
There are two plates sandwiched between the lower legs and
the cabinet. If these are not present, carefully jack up the locker
and remove the two legs on the right side of the cabinet. Install
with the two top plates as shown. See figure 3.1
Using two people, move the control box near the locker, and
carefully place it on the lower support plates. There are 4 slotted
holes in the bottom of the control box that align with the four
threaded studs in the lower plates.
Next, rotate the control box fully upright, and place two carriage
bolts in the upper square holes. Loosely attach the two nuts, so
that the control box will remain in place.
Align the two carcasses and tighten the two top and four bottom
nuts with a 7/16” wrench or socket.
Installing additional lockers
A total of four lockers can be connected to a KCU Control Box.
1. Place additional lockers on either side of the
primary unit. Connecting harnesses are designed
to reach past one locker only, so no more than two
lockers on either side of the Control Box.
2. Adjust the leveling legs so that there is a uniform
space between cabinets.
3. Connect motor and LED power harness at the
lower rear of the locker. Secure with provided
strain relief.
4. Remove either of the lower wire covers and thread
the locker harness through kydex edge protector
as shown (Figure 3.2). Up to two harnesses can
be routed through each of the lower openings (one
from the left & one from the right side).
5. Re-attach the cover with four screws. Be sure the
wires are not pinched.
6. Connect the locker harness inside the control box
to two of the numbers connectors in the bottom of
the control box. The two connectors selected will
3
PREPARATION AND INSTALLATION

L0243A
6
be the two ‘trays’ in the software for that locker.
7. Connect the LED power connector to the small
connector to the right of the tray harness
connections.
8. Enter the Service mode in the AMS software, by
pressing the yellow button in the bottom right
corner of the control board.
9. Use the # key to scroll to Tray Setup, then press 6 to
register the new motors in the software.
Removing a Control Box from a locker
This requires two people, and a 7/16” wrench or socket.
1. Ensure all wire harnesses are disconnected, and
any loose parts are removed from the cabinet.
2. Loosen and remove the four 1/4-20 nuts from the
inside bottom of the Control Box with 7/16”
wrench.
3. With someone else steadying the unit, remove the
two carriage bolts and 2 security screws from the
inside top of the control box.
4. Rotate the top of the Control Box away from the
locker, then carefully lift it off the bottom threaded
studs.
Assembly is the reverse of above.
Mounting the Locker to the Wall
For safety, we strongly recommend installing the machine with
wall anchors. You will need wall anchors for the specific wall you
are mounting to and brackets to mount to the machine. Please
call the service department to order the brackets.
1. Place the bracket with the long side down and the
short side up. See Figure 3.3.
2. Line up the holes on top of the vendor according to
the desired location.
3. Insert the screws provided through the holes of the
bracket so they line up with the holes in the locker,
and then screw them into place.
4. Position the locker against the wall and use the
holes in the brackets to mark the locations for the
wall anchors.
5. Install appropriate wall anchors (not provided) and
attach the brackets to the wall.
Figure 3.1 Lower Support Plates
Figure 3.2 Installation of Wall Anchors
Figure 3.3 Installation of Wall Anchors
3 PREPARATION AND INSTALLATION

L0243A
7
4
TROUBLESHOOTING
MACHINE TROUBLESHOOTING CHART
IF A REPLACEMENT PART IS NECESSARY, PLEASE CONTACT YOUR DISTRIBUTOR
The following troubleshooting chart may be used to find quick remedies for electrical or mechanical
failures in the vendor.
Symptom Possible Cause Remedy
LED lights not working Broken/disconnected harness
Starng at rear of locker, check for 12VDC at
the connector, working back to LED power
supply in control box..
No power evident Disconnected wire harness Using wiring schemac, trace harnesses back
from unpowered part to the power cord.
Opposite door is opening (select
82 and 72 opens).
Extension harness backwards or
Motor harness connected incorrectly
Swap motor connectors at the rear of the lock-
er cabinet.
Were two lock modules replaced at the same
time? Swap motor wires.
Door closes but doesn’t latch. Latch plate damaged. Adjust or replace latch plate in door.
Motor not at home position. Make selection again, and wait for motor to
‘home’. Check Motor Type setting.
Door will not shut.
Door blocked by parts or product. Clear obstruction.
Door hinge is bent or damaged. Replace door and /or hinge.
Motor not at home posion. Set motor type to ‘Home Only-3’
Door will not open.
Spring loose on door pusher. Adjust push nuts to get desired spring force.
Move the nut towards the spring to increase
the force to open the door.
Latch jammed, or too tight. Latch plate on door bent. Re-adjust or replace.
Motor doesn’t run (listen for motor
noise). Motor disconnected. Access from rear door.

L0243A
8
press down here
(Le column shown)
5
MAINTENANCE
CLEANING THE CABINET
Clean the Locker cabinet as necessary using mild household
cleaners and water. Apply the cleaning solution to a cloth or
sponge and gently wipe the Locker surfaces to clean.
1. Do not use chemicals or solvents. These can dam-
age the paint and plastic trim.
2. Do not use abrasive cleaners.
3. Do not use a water jet.
4. Do not let water or cleaning solutions contact electri-
cal or electronic components.
MANUALLY UNLOCKING LOCKER DOORS
The following steps may be used to gain access to the internal
parts of the Locker if it becomes inoperative.
Access latch through rear door:
For doors in the left column, reach in and press down on the
plastic latch hook.
For doors in the right column, reach in and press up on the plas-
tic latch hook.
Figure 5.1 Manually unlocking doors

L0243A
9
6
WIRING DIAGRAM
Figure 6.1 Wiring Diagram

L0243A
10
6
WIRING DIAGRAM
Figure 6.1 Wiring Diagram (Cont)
This manual suits for next models
1
Table of contents
Other AMS Controllers manuals
Popular Controllers manuals by other brands

HIMA
HIMA HIMatrix GEH 01 manual
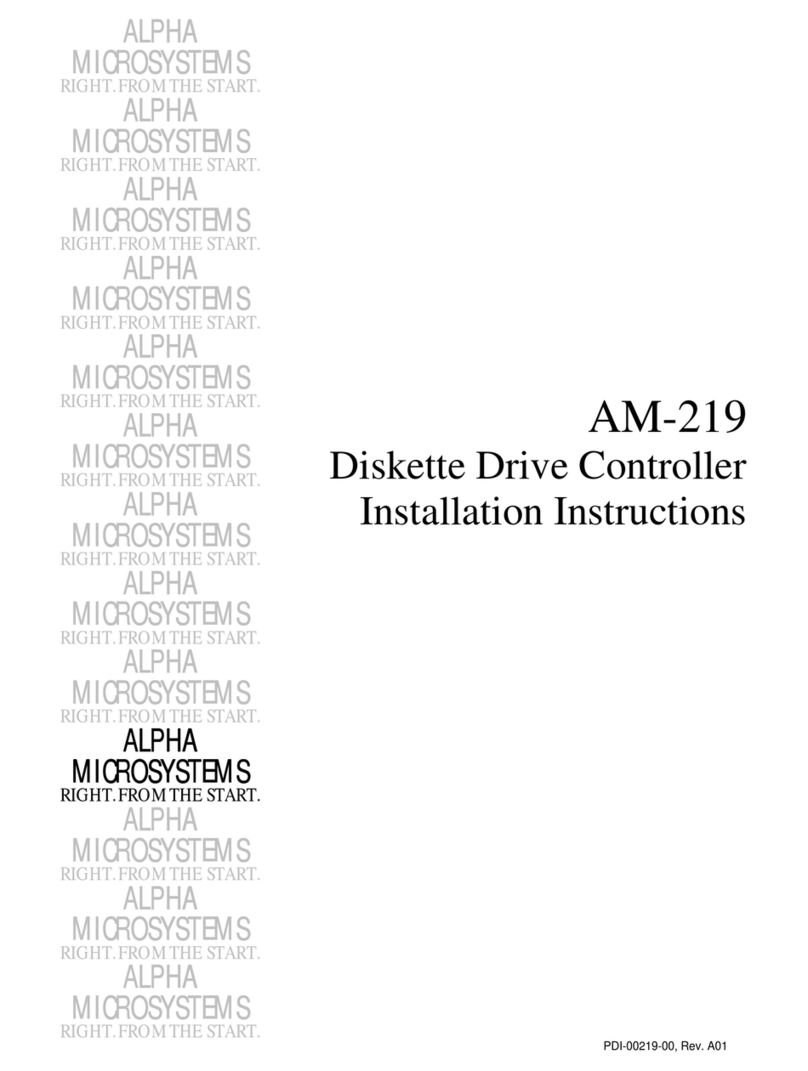
Alpha Microsystems
Alpha Microsystems AM-219 installation instructions
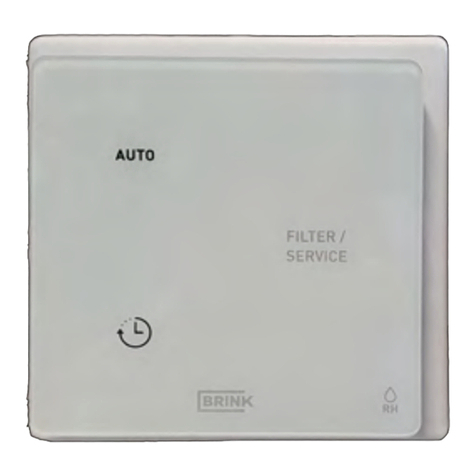
Brink
Brink Air for life Installation regulations
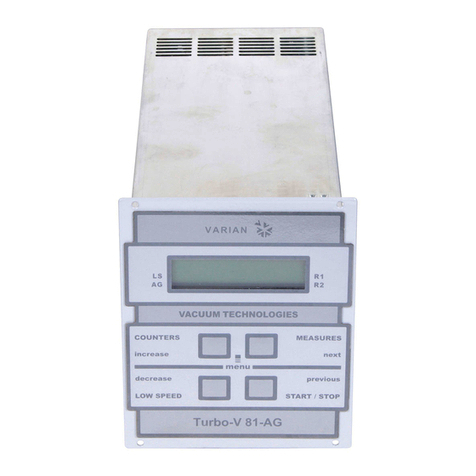
Varian
Varian Turbo-V 81-AG instruction manual
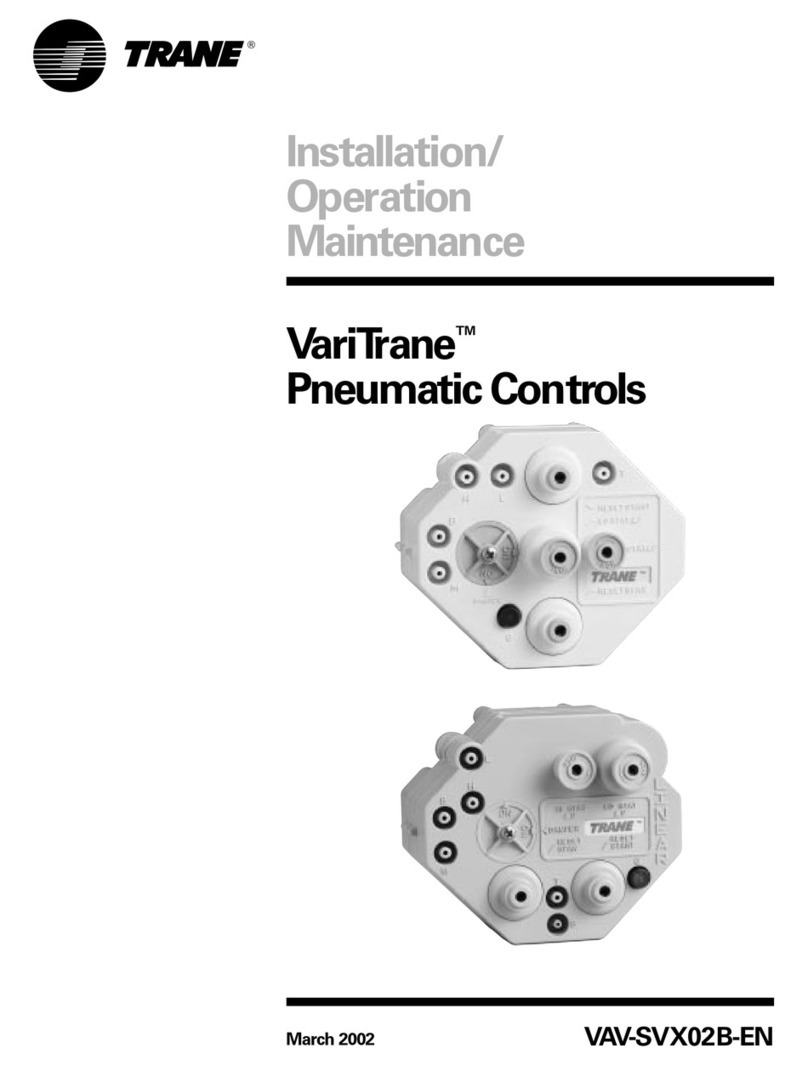
Trane
Trane VariTrane VAV-SVX02B-EN Installation operation & maintenance
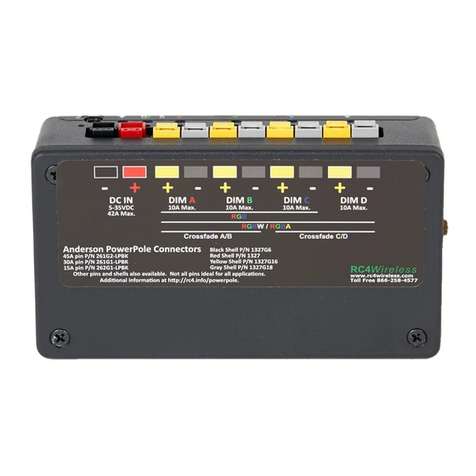
RC4 Wireless
RC4 Wireless LumenDim4 quick start guide