AnaPico APPH6000 User manual

APPH6000 User Manual V1.0
2010
- | Introduction to the APPH6000 1
APPH6000 User’s Manual
Version 1.0, January 2011

APPH6000 User Manual V1.0
2010
- | Introduction to the APPH6000 2
Copyright
This manual is copyright by AnaPico AG and all rights are reserved. No portion of this
document may be reproduced, copied, transmitted, transcribed stored is a retrieval system, or
translated in any form or by any means. Electronic, mechanical, magnetic, optical, chemical,
manual or otherwise, without written permission of AnaPico AG.
AnaPico and the AnaPico logo are internationally registered trademarks of AnaPico AG.
AnaPico acknowledges the following product names as trademarks of their respective owners:
Microsoft, Windows, LabVIEW, MATLAB.
Disclaimer
AnaPico AG makes no representation or warranties with respect to the contents hereof and
specifically disclaims any implied warranties of merchantability for any particular purpose.
AnaPico AG reserves the right to revise this publication and to make changes from time to time
in the content thereof without obligation of AnaPico AG to notify any person of such revision
or change.

APPH6000 User Manual V1.0
2010
- | Introduction to the APPH6000 3
Contents
Introduction to the APPH6000 .........................................................................................................5
General Features and Functions....................................................................................................5
Options............................................................................................................................................6
Front Panel Overview .................................................................................................................... 7
Rear Panel Connections .................................................................................................................9
Getting Started .................................................................................................................................11
System Requirements ................................................................................................................... 11
Unpacking the APPH6000............................................................................................................. 11
Initial Inspection............................................................................................................................ 11
Starting the APPH6000 ................................................................................................................. 11
Applying Power.............................................................................................................................12
Connecting to LAN via DHCP Router ...........................................................................................12
Connecting via LAN without DHCP Router .................................................................................12
Connecting though USBTMC........................................................................................................12
Installing the APPH6000 Remote Client ......................................................................................13
Troubleshooting the LAN Interconnection..................................................................................13
Shutting Down the APPH6000.................................................................................................... 14
Perform Firmware Upgrade......................................................................................................... 14
Serial Number............................................................................................................................... 14
Measurement using the Graphical User Interface (GUI) .............................................................. 15
Start the APPH6000 GUI ...............................................................................................................15
Phase Noise Measurement ...........................................................................................................18
Post processing and displaying results....................................................................................... 22
Advanced Measurement Settings............................................................................................... 24

APPH6000 User Manual V1.0
2010
- | Introduction to the APPH6000 4
Measurement time....................................................................................................................... 25
Baseband Noise Measurement.................................................................................................... 28
Transient Measurement...............................................................................................................30
Remote Programming the APPH6000.............................................................................................31
Access via LAN...............................................................................................................................31
Using and Configuring VXI-11.......................................................................................................31
Using the USB-TMC Interface with VISA (Firmware 1.0 and up) .............................................. 32
Using the GPIB Interface (Firmware 1.0 and up)........................................................................33
Using SCPI for APPH6000.............................................................................................................33
Type and Structure of Commands.............................................................................................. 33
APPH6000 commands ..................................................................................................................33
IEEE common commands .............................................................................................................33
Concepts of the command tree...................................................................................................34
User Calibration (Firmware 1.0 and up)......................................................................................35
Product Information.....................................................................................................................36
5.Maintenance and Warranty Information ........................................................................... 37
Adjustments and Calibration ...................................................................................................... 37
Repair ............................................................................................................................................ 37
Upgrading the Firmware via USB flash drive or LAN................................................................ 37
Safety ............................................................................................................................................ 37
Warranty Information..................................................................................................................38
Equipment Returns.......................................................................................................................38
Company Details ..........................................................................................................................40

APPH6000 User Manual V1.0
2010
- | Introduction to the APPH6000 5
Introduction to the APPH6000
Your APPH6000 Signal analyzer kit contains the following items:
APPH6000 mainframe
Universal power adaptor (AC 100 – 240V) with UK, US, EU plugs
Ethernet & USB Cable
APPH6000 software CD
It is strongly recommended to use the original power adaptor (as supplied with the device) to
guarantee save and reliable operation of the APPH6000.
General Features and Functions
The Anapico APPH6000 Signal Analyzer provides:
10 MHz to 6.2 GHz input frequency analysis range
0.1 Hz to 2 MHz frequency offset range
Phase noise and amplitude noise analysis capability
Baseband noise analysis
Transient measurements
Long-term support: Software upgrades (firmware and PC based) are available to
download from www.anapico.com. You can also call our technical specialists for
support. You can continue to use both of these services free of charge for the lifetime
of the product.
Universal LAN and USB 2.0 interface
18 months calibration cycle

APPH6000 User Manual V1.0
2010
- | Introduction to the APPH6000 6
Options
The following options are available for the APPH6000 signal analyzer:
HP: high-power detector (5 MHz to 1500 MHz)
IS: internal tuneable low noise reference (10 MHz to 6.2 GHz)
IS400: internal tuneable low noise reference (5 MHz to 380 MHz)
CC: two channel cross-correlator
CCIS400: two channel cross-correlator with internal sources
EO: frequency analysis to 40+ MHz offset
Unless noted otherwise, this manual describes the basic version of the instrument.

APPH6000 User Manual V1.0
2010
- | Introduction to the APPH6000 7
Front Panel Overview
Depending on the APPH6000 product configuration, the front panel can contain up to four
female SMA connectors and five female BNC connectors. A green LED indicates the power
on/off status of the instrument. Figure 1 shows the front panel of the APPH6000 with option
CC. For a single channel model, the second channel IOs are sealed.
RF IN(1) connector This female SMA connector is the DUT signal input. The impedance is 50
ohm. The damage level is +36 dBm maximum. The maximum allowed DC level is +/- 10 V.
RF IN2 connector (optional) This female SMA connector is the second DUT signal input in case
the two-channel cross-correlation option is installed. When using the cross-correlator, the DUT
signal is split to provide equal amplitudes at RF1 and RF2 inputs. The impedance is 50 ohm. The
damage level is +36 dBm maximum. The maximum allowed DC level is +/- 10 V.
REF IN(1) connector This female SMA connector is the reference LO input. The impedance is 50
ohm. The damage level is +36 dBm maximum. The maximum allowed DC level is +/- 10 V.
Figure 1 APPH6000 Front Panel View (APPH6000 instrument with option CC)

APPH6000 User Manual V1.0
2010
- | Introduction to the APPH6000 8
REF IN2 connector (optional) This female SMA connector is the second reference LO input in
case the two-channel cross-correlation option is installed. The impedance is 50 ohm. The
damage level is +36 dBm maximum. The maximum allowed DC level is +/- 10 V.
REF OUT (1) connector This female SMA connector is the reference LO output in case a first
internal reference source is installed (option IS, IS400 or CCIS400). The impedance is 50 ohm.
REF OUT2 connector (optional) This female SMA connector is the reference LO output in case a
second internal reference source is installed (option CCIS400). The impedance is 50 ohm.
TUNE(1) connector Female BNC connector is the DC tune voltage output if a tuneable DUT or
tuneable external reference is used.
TUNE2 connector (optional) Female BNC connector is the DC tune voltage output if the
optional cross-correlator (option CC or CCIS400) is installed and a second tuneable external
reference is used.
SUPPLY connector Female BNC connector is the programmable low-noise DC supply voltage
output. Output voltage range is -5 to +15 V, maximum available current is 80 mA.
BANDBAND IN connector Female BNC connector is the baseband signal input. To make
baseband noise measurement mode useful for power supply noise measurement, this port is
well protected for DC voltage application. The maximum allowed DC level is +/- 15 V.
Power switch The power switch disconnects the instrument from the DC input completely.
Caution:
Do not apply a DC voltage or current to the individual ports of the DC Control,
DC Power and RF Port. Applying a DC voltage or current may lead to the
breakdown of this product. In particular, there is the risk of the capacitor
remaining charged. Connect the measurement sample (DUT) to the port (or the
test fixture, cables, etc. connected to the port) after discharging DUT's
electricity enough.

APPH6000 User Manual V1.0
2010
- | Introduction to the APPH6000 9
Rear Panel Connections
1 RJ-45 host connector (8 Pin) Used for connecting via Ethernet with a controller, such as a PC or
Labtop. 10Base-T/100Base-T Ethernet (automatic data rate selection)
2 USB Device Used for connecting with a controller such as a PC or Laptop. Communication is
via USBTMC protocol. Through this port, you can control the APPH6000 from external
controllers. For more information on the measurement system using the USB port, see the
programmer’s manual.
3 USB Host Used for connecting USB devices such as Memory sticks.
4 TRIG IN connector Female BNC connector, accepts a TTL signal from an external trigger source.
The input impedance is 1 Mohm.
Figure 2 APPH6000 Rear Panel View
6
7
1
4
5
2
3

APPH6000 User Manual V1.0
2010
- | Introduction to the APPH6000 10
5 FUNCT OUT connector Female BNC connector is used as a multiple purpose output. It can be
programmed as trigger output, as video output during pulse modulation, and as output for the
low frequency function generator (standard on instruments with serial no. above xx00100).
6 Power switch The power switch disconnects the signal generator from the DC input
completely, including the internal high-stability reference. After switching on this switch, the
signal generator enters into standby with the OCXO warming up and RF out switched off. The
red power LED (option HC only) on the front panel is turned on.
7 DC IN power receptacle The power receptacle accepts a two-pin plug from the external 6 V DC
power adapter
8 GPIB (optional) connector The connection of an external controller through General Purpose
Interface Bus (GPIB) connector allows you to configure an automatic measurement system.
This GPIB connector is used only for controlling the APPH6000 from an external controller. You
cannot control other devices from the APPH6000 through this GPIB connector.
10 REF IN (optional) The reference signal input connector for phase-locking the measurement
signal from the APPH6000 to the external frequency reference signal. Inputting the reference
signal to this connector improves the accuracy and frequency stability of the measurement
signal from the APPH6000. Input frequency range is 1 200 MHz, 0 dBm
10 REF OUT (optional) A connector for outputting the internal frequency reference signal from
the APPH6000. By connecting this output connector to the external reference signal input
connector of another device, the device can be phase-locked to the internal reference signal of
the APPH6000 and used under this condition. Output Signal is 10 MHz, +3 dBm
11 Serial Number Plate The seal showing the serial number of the product.

APPH6000 User Manual V1.0
2010
- | Getting Started 11
Getting Started
System Requirements
To ensure that your APPH6000 signal analyzer operates correctly with the remote control
interface software, you must have a computer with at least the minimum system requirements
to run one of the supported operating systems.
Operating system Windows™ 2000 SP4, XP SP2 or Vista (32-bit versions only)
Ethernet Port 10/100/1000M LAN
USB 2.0 Port
Unpacking the APPH6000
Remove the APPH6000 materials from the shipping containers. Save the containers for future
use.
The standard APPH6000 package includes:
1 Signal Analyzer Generator
1 Ethernet Cable
1 Universal DC power adapter
1 APPH6000 Software & Manual CD
Initial Inspection
Inspect the shipping container(s) for damage. If container is damaged, retain it until contents of
the shipment have been verified against the packing list and instruments have been inspected
for mechanical and electrical operation.
Starting the APPH6000
The follwoing sections describes installation instructions and APPH6000 verification tests.

APPH6000 User Manual V1.0
2010
- | Getting Started 12
Applying Power
1. Place the APPH6000 on the intended workbench and connect the appropriate DC power
supply to the receptacle on the rear of the unit. Make sure you use the included DC power
supply. The APPH6000 requires 6 V DC at 3 A maximum. Using other supplies may lead to
malfunction and damage of the APPH6000.
2. Press the Line on/off switch on the rear panel. The front panel green LED will illuminate. The
instrument will initialize and boot within a few seconds and be ready for operation.
Connecting to LAN via DHCP Router
Connect the APPH6000 to your local area network (LAN) or using the provided Ethernet cable.
The instrument is configured to accept its dynamic IP number from the DHCP server of your
network. If configured properly, your network router will assign a dynamic IP number to the
instrument. Your instrument is now ready to be controlled.
Connecting via LAN without DHCP Router
If you want to connect the instrument directly to your computer you can use the Ethernet cable
directly between instrument and computer. To work properly, the network card (NIC) of your
computer shall be set to a fixed IP beginning with 169.xxx.xxx.xxx.
Connection with a NIC that is configured to use DHCP is also possible, but depending on the
configuration the connection may take several minutes. After a short time, the instrument will
detect that no DHCP server is present and assign itself a default IP number.
Connecting though USBTMC
Connect the APPH6000 to the PC using the USB cable. The PC must be configured with a VISA
runtime environment (NI or Agilent, or comparable Linux VISA). If connected properly, the VISA
will detect the APPH6000 and you can use VISA Write to send the *IDN? query and use VISA
Read to get the response. The USBTMC protocol supports service request, triggers and other
GPIB specific operations.

APPH6000 User Manual V1.0
2010
- | Getting Started 13
VISA now allows you to communicate as a controller to the APPH6000. To use such the device,
plug it in and Windows should detect the new hardware and launch the New Hardware Wizard.
Instruct the wizard to search for the driver, which in this case is VISA. If the VISA runtime library
is properly installed, the device will be installed as a USB Test & Measurement Class Device.
Open Measurement & Automation Explorer (MAX). The new device will appear in MAX under
Device and Interfaces » USB Devices. You can then use this resource name as you would use any
GPIB resource.
Installing the APPH6000 Remote Client
AnaPico’s graphical user interface provides an intuitive control of the APPH6000. The Java
based application runs under any Operating System including Windows™ 2000, XP, Vista or
Windows 7 with minimum requirements. Only the Java runtime environment must be installed
on the PC.
To install the GUI on the computer, insert the APPH6000 Software and Manual CD into the
CD/DVD drive. If the setup doesn’t start automatically double click on the setup.exe to run the
auto-installer.
The self-extracting setup provides easy installation and de-installation of the software. The
setup program guides you in a few steps though the installation process. In case the Java
Runtime Environment is not installed on the current operating system, the setup procedure
automatically will assist you to install the required version. For this you will need an internet
connection.
Troubleshooting the LAN Interconnection
Software does not install or start properly
Make sure your installation CD is not damaged.
Verify that the Java Runtime Environment is installed
Software cannot detect any APPH6000:
Make sure you have connected both PC and APPH6000 to a common network.

APPH6000 User Manual V1.0
2010
- | Getting Started 14
If a direct connection is used, make sure you use an appropriate crossover Ethernet
cable (10 and 100Mbit LAN only). Note that detection of the APPH6000 can take several
seconds if your PC is configured to work with an external DHCP server. In some cases
the connection may even fail completely. Use a fixed IP instead.
Make sure that your (software) firewall enables the APPH6000 software to setup a
TCP/IP connection within the LAN. Under Windows XP you can do that like this:
Open Control Panel under Settings in your Start menu. Then go to Windows Firewall.
Click on Exceptions and then add Program. If the APPH6000 Software is in this list
choose it and click OK otherwise you have to browse for the path to AnaPico Software.
Finally close all open dialogs with OK. Now your Windows™ Firewall is ready for
APPH6000.
Shutting Down the APPH6000
Press the Line on/off switch on the rear panel to off.
Perform Firmware Upgrade
A firmware upgrade of the APPH6000 can be done directly via the GUI. Make sure you are
connected to the right device and have the correct firmware binary ready. Then go to Controller
Update Firmware and select the appropriate binary (tar.file) that you have received from
AnaPico or downloaded from the AnaPico website. The update will take a few seconds, and
after completion the device will reboot. Reconnect to the device and continue using the device.
Serial Number
Each instrument own a unique serial number which is shown on the sticker on the rear panel.
This serial number determines the instrument configuration and guides the software
accordingly.

APPH6000 User Manual V1.0
2010
- | Measurement using the Graphical User Interface (GUI) 15
Measurement using the Graphical User Interface (GUI)
AnaPico’s graphical user interface provides an intuitive control of the APPH6000. It runs under
any operating system supporting the Java runtime library. Make sure the software is installed
and the computer’s firewall configured as required.
Start the APPH6000 GUI
Double-click the APPH6000 shortcut that will appear on your desktop after the software has
been successfully installed. Make sure that the APPH6000 is turned on and is connected to the
computer using either Ethernet or USB connectivity.
After start, the software will automatically detect existing APPH6000 instruments and will
establish connection to the first detected device. Manual selection of the APPH6000 device can
be done though Controller Connect menu. A window with all detected APPH6000 devices
pops up. Clicking on one of the devices will instantly establish connection. Clicking on a
different device will disconnect the old device, and connect to the selected device. By clicking
on the Refresh button, a scan for new devices is started. If no device is found, the software will
ask to launch additional search or connect manually by providing a known device IP. (see Figure
3).
The measurement window is organized as shown in Figure 4.
File Setting (Save, Load, Reset) allows storage of user defined setting.
Figure 3 Message if no device was detected

APPH6000 User Manual V1.0
2010
- | Measurement using the Graphical User Interface (GUI) 16
Controller Connect automatically detects available APPH devices in the LAN or attached
though USB and allows reconnection.
Controller Set IP establishes connection to a user given IP.
Controller Update Firmware performs automatic firmware update.
The measurement tabs are available: Phase Noise, Amplitude Noise, and Baseband Noise.
Clicking on them switches to the respective noise measurement setup. The following sections
describe each measurement setup.
The GUI window consists of four sections:
Figure 4 GUI after start with no device detected (tab set to phase noise measurement)

APPH6000 User Manual V1.0
2010
- | Measurement using the Graphical User Interface (GUI) 17
On the upper left side the measurement configuration menu, where user input is required to
prepare for the measurement.
On the bottom left the status window are located, where messages about the progress are
displayed and errors reported.
On the upper right the plot window configuration menu is located. That is where the user can
configure, save and load measurement plots and raw data.
On the lower right the measurement plot window is located, where measurements are shown
in real time and connectivity schematics helps user to prepare for measurement. Change
between the two settings by clicking on the appropriate measurement tab.
The right side is exactly the same for all measurement types, while the upper left side
(measurement configuration menu) changes depending on the selected measurement.

APPH6000 User Manual V1.0
2010
- | Measurement using the Graphical User Interface (GUI) 18
Phase Noise Measurement
This function locks on the DUT’s output signal and measures the phase of the signal in the
specified offset frequency range. The following section describes the basic measurement
method of the DUT’s phase noise corresponding to the offset frequency from the carrier by
using the APPH6000’s GUI phase noise measurement window. This section describes the
following topics:
Setting Phase Noise Measurement Parameters
Perform Measurement and Visualize Results
Follow the steps below to measure the phase noise in the phase noise measurement tab of the
GUI.
A) Select measurement configuration (see Fig 2)
DUT versus tunable internal or external reference: select this mode to measure the DUT
against a reference source. Either the DUT or the reference may be tuned by the TUNE1
output voltage. This measurement assumes that the reference phase noise is
substantially better than the DUT’s. The reference can be internal (option IS or IS400) or
external.
DUT versus tunable DUT comparison measurement: select this mode if two identical
DUTs are measured against each other. The 3 dB correction is taken into account.
Figure 5 Choice of supported phase noise measurements

APPH6000 User Manual V1.0
2010
- | Measurement using the Graphical User Interface (GUI) 19
Cross-Correlator measurement with DUT versus two internal or external sources (option
CC or CCIS400): select this mode for low noise sources if lowest noise floor is required.
The two references can be internal or external and may be equal or even worse in phase
noise than the DUT. The residual and reference noise will be suppressed by 5 dB with 10
averages, 10 dB with 100 averages, etc.
B) Enter estimated DUT CW frequency or select “auto” for auto-detection of frequency
(requires option IS or IS4000).
Figure 6 Setup for phase noise measurement

APPH6000 User Manual V1.0
2010
- | Measurement using the Graphical User Interface (GUI) 20
a. If an external reference is used, the frequency must still be specified to fall
within a certain band: enter 100 MHz if frequency is below 160 MHz, enter 1 GHz,
if frequency is larger 160 MHz but lower than 3 GHz, otherwise enter 5 GHz if
frequency is larger than 3 GHz.
b. If an internal source is used, the frequency value must be known to within an
accuracy of a few PPM (pars-per-milion) unless “auto” is selected to allow the
instrument to search for the DUT frequency.
C) Select frequency offset range to measure. Select start and stop frequency. The start
frequency will mainly determine the measurement time.
D) Set the APPH6000 locking bandwidth to the desired value. Recommended is to leave
this setting on “auto” for automatic setting of bandwidth based on DUT sensitivity,
optimum dynamic range and measurement accuracy.
E) Choose the desired number of averages.
F) Select the RF input attenuator (values 0 to 30 dB in 1 dB steps) or select “auto” to auto-
adjust input amplitude to avoid beat compression. This will give maximum dynamic
range with best measurement accuracy.
G) Select external reference by checking the box. Otherwise the internal source is used
(requires option IS or option IS400). For each external reference the tuning compliance
range must be provided. Caution: the maximum tuning range is -5 to + 22V. Make sure
that the compliance ranges are set to match your external reference or DUT and do not
surpass maximum rating otherwise permanent damage may occur.
H) If DUT or external sources are to be tuned, enter sensitivity (Hz/Volt) or select “auto” for
automated detection of sensitivity.
I) Enable internal supply voltages and set output voltage, if your DUT shall be powered by
the internal low noise DC supply. Note the maximum current is restricted to 150 mA.
Table of contents
Other AnaPico Signal Processor manuals
Popular Signal Processor manuals by other brands
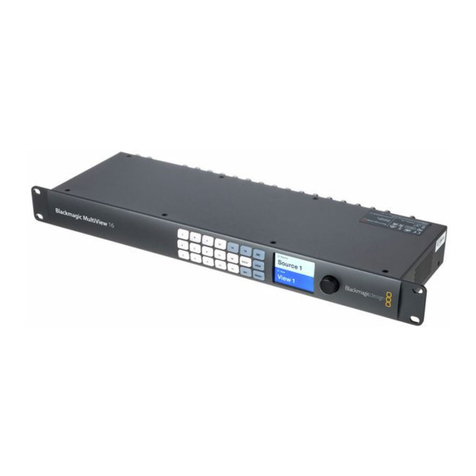
Blackmagicdesign
Blackmagicdesign Blackmagic MultiView 4 Installation and operation manual
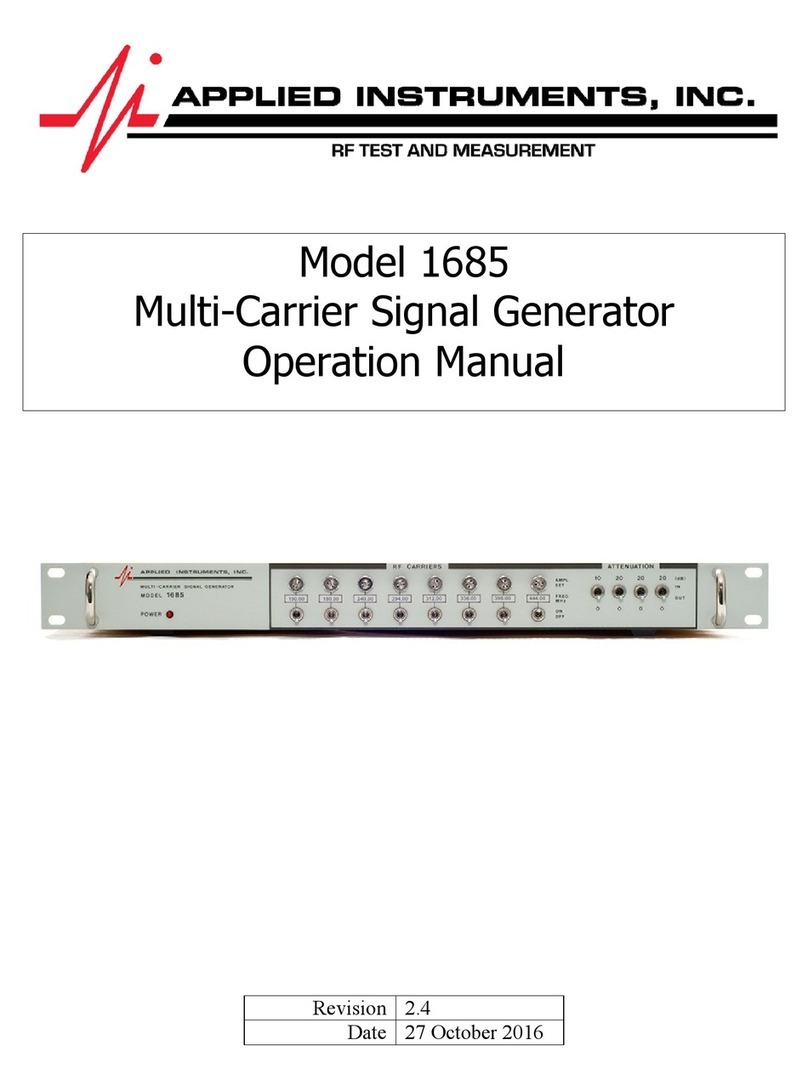
Applied Instruments
Applied Instruments 1685 operating manual
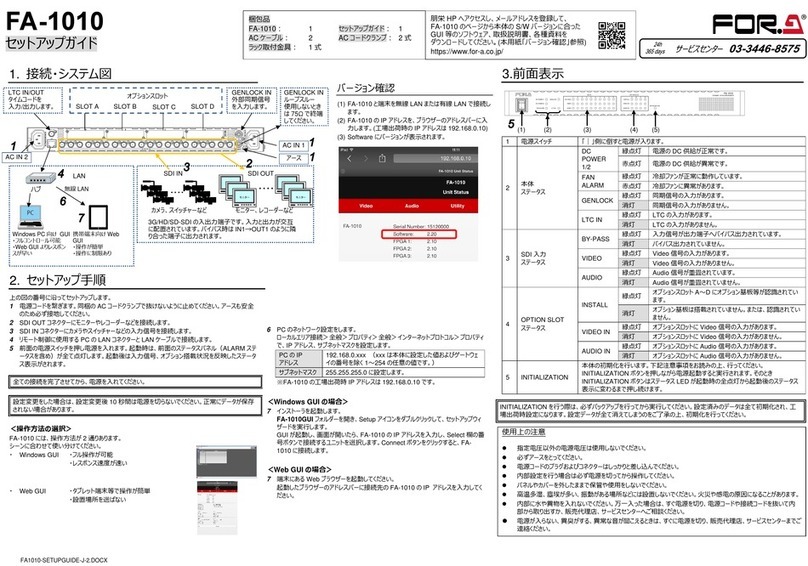
FOR-A
FOR-A FA-1010 Quick setup guide

FeelTech
FeelTech SGP10 S Series user manual
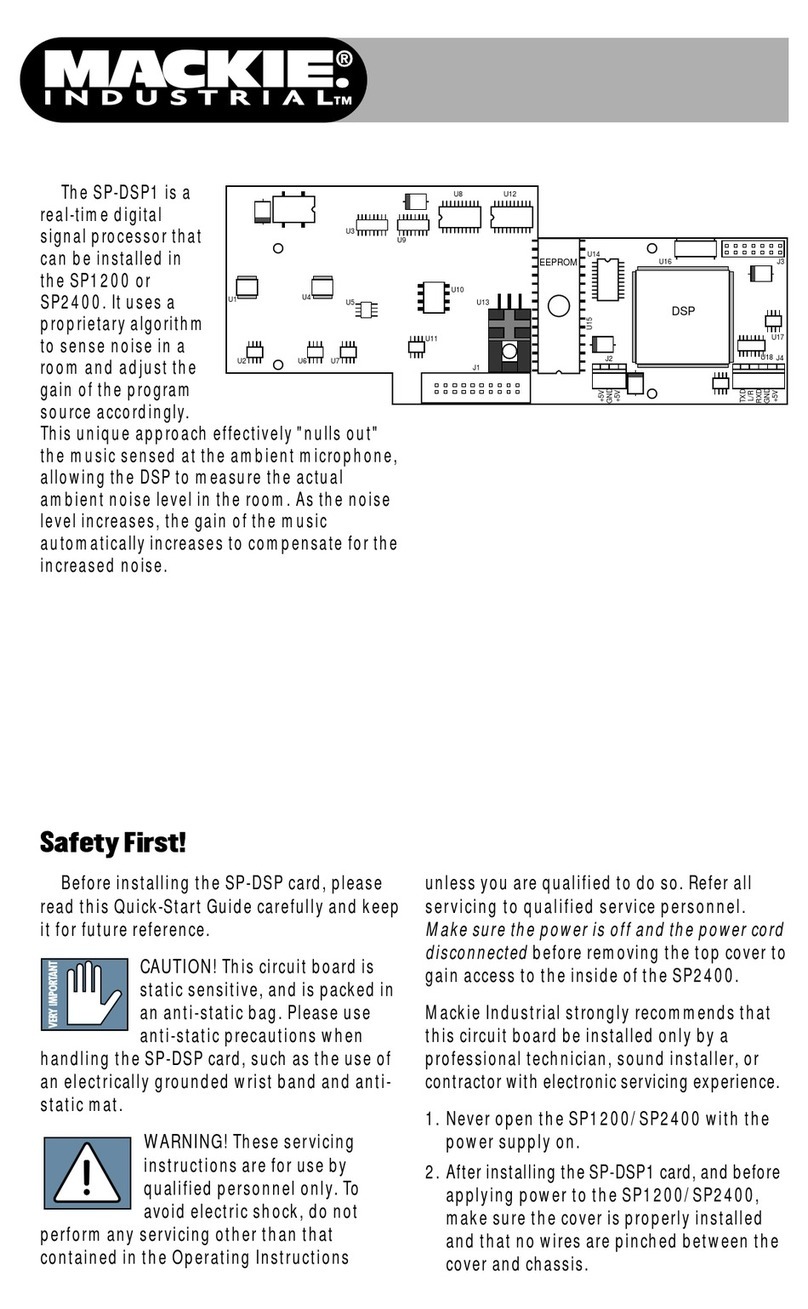
Mackie
Mackie SP-DSP1 quick start
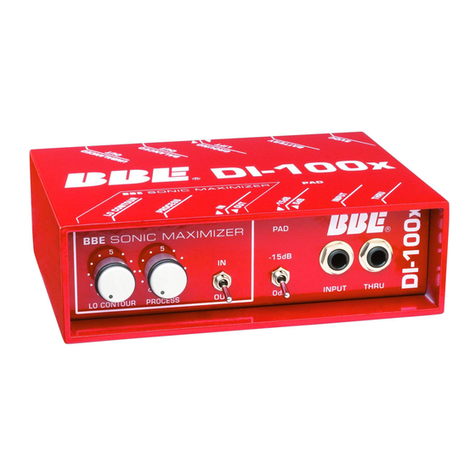
BBE
BBE Sonic Maximizer DI-100x user manual