Anywire ASLINKER BL2LN87SB-02D CC20 Series User manual

-BL2LN87SB02D*CC20 1/20-
IN0
IN1
LINK
ALM
IN1
IN0
BL2LN87SB-02D□-CC20
Ver.1.1
ASLINKER [Smart ASLINKER]
AnyWireASLINK System Products Guide
BL2LN87SB-02DS-CC20
BL2LN87SB-02D-CC20
[Type]
A WARNING indicates a potentially hazardous
situation which, if not handled correctly, could
result in death or serious injury.
[Warranty]
■Warranty period
The warranty on the delivered Product shall continue to be effective for one (1)
year after the delivery thereof to a location as designated by the original owner.
■Scope of warranty
Should a defect occur in any part of the Product during the foregoing warranty
period when it is used normally in accordance with the specications described
in this Products Guide, the Company shall replace or repair the defect free of
charge, except when it arises as a result of:
[1] Misuse or abuse of the Product by the owner;
[2] Fault caused by other than the delivered Product;
[3] The unauthorized modication or repair of the Product by any person other
than the Company’s personnel;
[4] Any unusual force of nature, disaster or other cause beyond the Company’s
control.
The term “warranty,” as used herein, refers to the warranty applicable to the
delivered product alone. The Company shall not be liable for consequential or
incidental damages resulting from any malfunction.
■Repair at cost
After the expiration of the warranty period, the owner shall be responsible for all
costs and expenses incurred for the troubleshooting and repair of the Product.
Even during the warranty term, the Company shall repair any defects arising
from causes other than within the scope of the warranty as specied above, at
the owner’s cost.
■Changes in the product specications and the descriptions in the manual
The descriptions in this manual may be subject to change without notice.
Precautions that must be observed in order to use this system safely are indicated as shown below.
You must observe these precautions.
[Notes on Safety]
A CAUTION indicates a potentially hazardous situation
which, if not handled correctly, may result in personal
injury or property damage.
■Note on use ⇒
A separate Address Writer is required to set addresses and other data.
*
For more information, refer to [Various Settings] on page 9.
NPN input
PNP input
CAUTION
WARNING
○
System power supply
Use a stable, 24V DC power supply. Use of an unstable power supply may cause problems with the system.
○
Separately route high-voltage and power cables
Although the AnyWireASLINK has a high noise margin, install the transmission line and I/O cables away from high-voltage and power
cables.
○
Connectors and terminals
-
Pay careful attention to the length and installation of cable wiring to ensure that connectors and cables are neither overloaded nor disconnected.
- Make sure to prevent any metal objects from getting inside the connectors or the terminal blocks.
- Short-circuits caused by metal objects or mis-wiring are likely to damage the device.
○
Do not impose any external loads on the units. Doing so may cause a failure.
○
Do not disconnect or reconnect between the transmission line and slave units when the transmission line is active. A malfunction may occur.
○
Use the AnyWireASLINK within the range of the specications and conditions shown below.
○
System Safety
This system is intended for general industrial applications. It does not have functions for supporting applications requiring higher
levels of safety such as safety-related devices or accident prevention systems. The product must not be used for these purposes.
○
Always turn off the power in installing or replacing the system.
○
Prolonged continuous ow of a rated load current or higher or a transit current due to load short-circuit, etc., in the hybrid unit including
the output unit and the output circuit may result in smoking or ring. An external safety device such as a fuse must be installed.
CAUTION
WARNING
[About Pictogram*1]
Ver. 1.0*2Compatible with
Ver. 1.1*3
*1 The pictogram may not be marked (or stuck) depending on the product.
*2 AnyWireASLINK device not compatible with Ver. 1.1 (word transmission and
single unit simplified replacement functions)
Some products, not marked with the Ver. 1.1 pictogram, are compatible with
the functions included in Ver. 1.1. Refer to the lot No. and the product guide
for ultimate confirmation.
*3 For details of Ver. 1.1, refer to the subsequent pages.

-BL2LN87SB02D*CC20 2/20-
A
1
B
2
C
3
D
4
E
5
F
6
G
7
H
8
I
9
J
10
K
11
L
12
Lot No. 19ECBNB
As a result of the addition of functions, indication of lot No. has been changed from 3 digits (conventional format:
year and month only) to 6 digits or 7 digits.
The master unit compatible with the word transmission function provides areas for transmission and receiving of word
data (numerical information) such as analog data and sensing level data.
Using this function enables reduction of occupancy of bit information area by word data.
To enable word transmission, it is necessary that the system should be congured only with slave units compatible with
the word transmission function.
A slave unit incompatible with the word transmission function cannot be connected to the AnyWireASLINK system to
conduct word transmission.
For slave units that handle word data, word address settings are required.
[About AnyWireASLINK Ver. 1.1]
[About Lot No.]
[About Word Transmission]
*3 Some products have no indication of function version.
Year: Numbers
(Lower two digits of the Christian era)
Month: Alphabet (as per the table below)
“19E” means May 2019.
Single unit simplied replacement*1
Word transmission*1*2
Functions available with Ver. 1.1
*1 To use these functions, the master unit compatible with each function is required.
For details, refer to this manual together with the manual for the master unit.
*2 You can use this function with the word-transmission AnyWireASLINK unit connected.
To handle word data, word address settings are required for slave units.
It depends on slave units whether word address setting is enabled or not.
New functions have been added to AnyWireASLINK products in May 2019 onward. Also, for the purpose of
differentiation of compatible functions, indication of product lot number (lot No.) has been changed.
Compatible functions vary depending on lot No. Please understand the following description thoroughly to use each
product.
Functions added to Ver. 1.1 are as follows:
Example:
S/W version
Year and month H/W version
Alphabet
Month
Function version*3

-BL2LN87SB02D*CC20 3/20-
NEW
CAUTION
Function version:
When an equipment parameter is changed due to functional upgrading, etc., the function
version will be updated (for example: A→B→C).
When a slave unit of a new function version is replaced with that of an old function version,
the single unit simplied replacement function cannot be used.
[About Single Unit Simplified Replacement]
During replacement of a slave unit, this function enables automatic settings of address and parameters of the existing
slave unit into a new slave unit. (After replacement of the slave unit, address and parameter setting procedure using the
address writer is not required.)
■Step 1 Turn OFF the 24V DC power supply for the master unit.
■Step 2 Disconnect a slave unit to be replaced.
■Step 3 Connect a new slave unit.
■Step 4 Turn ON the 24V DC power supply to the master unit.
- It is necessary that both the master unit and slave unit should be compatible with the single unit simplied replacement function.
- Before disconnection and connection of the slave unit, be sure to turn OFF the power supply.
- For compatibility of a slave unit with the single unit simplied replacement function, see the lot No. and the manual for the slave unit.
- When a slave unit of a new function version is replaced with that of an old function version, the single unit simplied replacement
function cannot be used.
- Operation is enabled in the case where the model of the slave unit before replacement is the same as that after replacement.
- If the model of the slave unit before replacement is different from that after replacement, a model mismatching error occurs, disabling
address and parameter settings.
- Operation is enabled in the case where the address of the slave unit for replacement is the factory-set address (bit address 511).
- Several slave units cannot be simultaneously replaced. For replacement of several slave units, conduct the replacement procedure for
each unit one by one.
- For a slave unit incompatible with the single unit simplied replacement function, set an address and parameters by using the address
writer as in the conventional manner.
- For details of the single unit simplied replacement function (limitations, conditions, etc.), refer to the manual for the master unit.
■Identication of function version
Function version information is given on the lot label.
*
The design and contents of the lot label may vary depending on the product model and lot No.
ASLINK
master unit
ASLINK
master unit

-BL2LN87SB02D*CC20 4/20-
○ ○ ○ ×
○
○○
○
○○○ ×○
Lot No. 19ECBNB
Connection targetsSpecicationsModel Functions
Functions
Address
*1 It depends on lot No. whether this function is available or not.
*2 This terminal can be used in connection to the AnyWireASLINK unit for word transmission. Note that this terminal cannot handle word data by setting a word address.
*3 To use these functions, a master unit that supports each function is required. For details, refer to the manual for the master unit together with this manual.
*4 This terminal can be used in connection to the AnyWireASLINK unit for word transmission. Note that this terminal cannot handle word data by setting a word address.
*5 The single unit simplied replacement function works even if the lot No. does not support the LED indication for the single unit simplied replacement function.
(When the master unit executes the single unit simplied replacement function, addresses/parameters will be written, if specied conditions are satised.)
[Functions]
Bit
transmission
ASLINKER
4-wire (isolated)
cable type
General-purpose
sensors
General-purpose
switches
Word
*1*2
transmission
Single unit
simplied
replacement
*3
Remote
address
change*3
Detection of sensor cable
disconnection
2-wire type
sensor
3-wire type
sensor
Bit
address
setting
Slave unit voltage
drop Sensing level drop I/O disconnection I/O short-circuit I/O power supply
drop
Word
address
setting
■Detecting functions (Status details)
Lot No. is indicated on the lot label.
Example:
■How to check
Word transmission*4
LED indication for single unit
simplied replacement function*5
Alarm bit setting
(Equipment parameters 5 and 13)
Lot No.
Available with S/W version “B” or later version
(If lot No. is indicated in 3 digits (year and
month only), these functions are not available.)
This unit has undergone addition of functions and change of specications according to version upgrading.
Available functions and specications of the unit vary depending on lot No.
[Function Compatibility by Lot No.]
Back of this unit
Function
S/W version
Function version
H/W version
NPN input: 2 points
PNP input: 2 points
Alarm bit: 2 points*1

-BL2LN87SB02D*CC20 5/20-
+
-
+
OUT
-
+
OUT
-
+
-
IN0
IN1
LINK
ALM
IN1
IN0
IN0
IN1
LINK
ALM
IN1
IN0
IN0
IN1
LINK
ALM
IN1
IN0
IN0
IN1
LINK
ALM
IN1
IN0
The branching
has no limitation.
AnyWireASLINK
master
Black:
DN
Red: DP
Black: DN
Red: DP
Black: DN
Black: DN
Red: DP
Red: DP
Black: DN Red: DP
2 points
2 points
2 points
2 points
2 points
2 points
2 points
2 points
2 points
8 points
8 points
24V DC*
Black: DN
Red: DP
Black: DN
Red: DP
24V DC*
*Make sure to use a 24V DC
stabilized power supply for
the power supply to be
connected.
*When complying with the
UL Standard, make sure to
use a 24V DC stabilized
power supply of “NEC
Class 2 Output.”
4P link connector is
convenient for
branching.
Dedicated at cable
1.25mm2(4-wire)
The sum of the
portions of DP, DN is
the total line length.
If the load current consumption
is large, a four-wire (isolated)
terminal can be selected.
This terminal can correspond
to I/O of the controller with an
external power supply.
[Installation Location]
- Locations where this product is not directly subject to vibration
or shock
- Locations where this product is not directly exposed to dust
- Locations where this product is not directly exposed to
conductors, such as metal chips or spatters
- Locations without condensation
- Locations where the atmosphere is free of corrosive gases,
ammable gases, and sulfur
- Locations far from high-voltage or high-current cables
- Locations far from servos, inverters, and other cables and
controllers that generate high-frequency noise
The AnyWireASLINK can employ a two-wire or four-wire terminal selectively depending on the load current.
If the load current is small, using a two-wire (non-isolated) terminal allows for achieving simplied wiring without local power supply.
In the case of prioritizing the sites of concentrated loads and/or the number of connections, hybridization with a four-wire (isolated)
terminal, which supports local power supply, is also possible.
Make sure to use a four-wire (isolated) terminal in the case of input and load driving using an external power supply.
[How to Connect AnyWireASLINK]
AnyWireASLINK terminator
One terminator should be connected to the DP, DN terminal farthest
from the AnyWireASLINK master unit.
Connect it correctly so as not to set the wrong polarity.
CAUTION
- Refer to Table 1 so that the size and length of the transmission
line and the allowable supply current lie within an appropriate
range.
- Connect the same symbols (DP, DN) correctly between the
AnyWireASLINK master unit and each device.
- The branching length or branch number has no limitation.
- Include the length of the cable provided with the terminal in the
“total line length.”
-
Connect the terminator (with polarity) on the transmission line
terminal farthest from the AnyWireASLINK master unit.
To connect loads (e.g. I/O ports) that are
controlled with a power supply other than the
one used for the AnyWireASLINK system,
always use a 4-wire (isolated) terminal.
Otherwise, malfunction may be caused.
CAUTION
1.25mm2
0.75mm2
MAX 2A
MAX 1.2A
MAX 1A
MAX 0.6A
MAX 0.5A
MAX 0.3A
0.5mm2MAX 0.8A MAX 0.4A MAX 0.2A
■
Relationship between the size and length of
the transmission line and the supply current (Table 1)
Size of
the transmission
line (DP, DN)
Supply current on the transmission line (DP, DN)
Total length:
50m or less
Total length: Over 50m,
no longer than 100m
Total length: Over 100m,
no longer than 200m
[System Configuration Example]
■Connection example of load
NPN
2-wire type sensor
Black: DN
Red: DP
White: 0V
Green: 24V
Black: DN
Red: DP
White: 0V
Green: 24V
Black: DN
Red: DP
White: 0V
Green: 24V
Black: DN
Red: DP
White: 0V
Green: 24V
NPN
3-wire type sensor
PNP
2-wire type sensor
PNP
3-wire type sensor
5m max.
BL2LN87SB-02D –
BL2LN87SB-02DS –
BL2LN87SB-02D –
BL2LN87SB-02DS –
3-wire type sensor
2-wire type sensor
Contact
24VL (Brown)
IN(Black)
24VL (Brown)
IN(Black)
0VL
(Blue)
0VL
(Blue)
24VL (Brown)
No connection:
Be careful not to touch.
IN(Black)
24VL (Brown)
IN(Black)
0VL (Blue)
No connection:
Be careful not to touch.
5m max.
5m max.
5m max.
0VL (Blue)
ASLINK lter
General-purpose
power supply lter
General-purpose
power supply lter

DP
DN
24V
0V
POWER IN SLAVE
LG
24V
0V L
N
FG
~
DP
DN
24V
0V
DP
DN
DP
DN
24V
0V
DP
DN
ANF-01
24V
0V L
N
FG
~
24V
0V
24V
0V
PE
ANF-01
ANF-01
DP
DN
24V
0V
LG
DP
DN
24V
0V
DP
DN
DP
DN
24V
0V
DP
DN
DP
DN
DP
DN
24V
0V
DP
DN
24V
0V
24V
0V
L
N
FG
24V
0V
24V
0V
PE 24V
0V
24V
0V
PE
DP
DN
24V
0V
DP
DN
24V
0V
A
B
POWER IN SLAVE
POWER IN SLAVE
~
-BL2LN87SB02D*CC20 6/20-
Terminator
Terminator
General-purpose power
supply lter
(Use it if necessary.)
24V DC stabilized
power supply
If the total length of the section where all the DP, DN, 24V, and 0V lines run in parallel is more than 50m
AnyWireASLINK master
AnyWireASLINK master
[Notes on Use of 4-Wire (Isolated) Terminal]
General-purpose power
supply lter
(Use it if necessary.)
24V DC stabilized
power supply
If the total length of the sections where all the DP, DN, 24V, and 0V lines run in parallel in the power supply system is more than 50m, connect an
ASLINK lter (Type ANF-01) or a lter manufactured by COSEL Co., Ltd. (Type EAC-06-472) in series to the 24V and 0V lines at a position where
these four lines start running in parallel.
This will improve noise resistance, suppress the adverse effects of crosstalk caused by transmitted signals, and stabilize signals.
The above lters must be inserted regardless of whether power is supplied to all terminals collectively from the power supply for the master or
power is supplied to each terminal individually from their local power supply.
Insert the “ASLINK lter [Type ANF-01]” regardless of installation method and distance when complying with CE Standard.
ANF-01
Filter of COSEL Co., Ltd. EAC-06-472 MAX 6A/24V DC
MAX 5A/24V DC
Product Type Allowable power current
ASLINK lter
②Local power supply/branching
If the total length of the
section where all the
DP, DN, 24V, and 0V
lines run in parallel is
more than 50m
24V DC
stabilized
power supply
2-wire
terminal
2-wire
terminal
4-wire
terminal
4-wire
terminal
4-wire
terminal
4-wire
terminal
4-wire
terminal
4-wire
terminal
If the total length of the sections (A + B)
where all the DP, DN, 24V, and 0V lines
run in parallel is more than 50m
■Filter allowable current
■AnyWire Type: ANF-01 Connection example
①Power supply to the entire system
2-wire
terminal
4-wire
terminal
4-wire
terminal
General-purpose
power supply lter
(Use it if necessary.)

DP
DN
24V
0V
LINELOAD
LG
24V
0V L
N
FG
~
DP
DN
24V
0V
DP
DN
DP
DN
24V
0V
DP
DN
24V
0V L
N
FG
~
24V
0V
24V
0V
PE
DP
DN
24V
0V
LG
DP
DN
24V
0V
DP
DN
DP
DN
24V
0V
DP
DN
DP
DN
DP
DN
24V
0V
DP
DN
24V
0V
24V
0V
24V
0V
PE 24V
0V
24V
0V
PE
DP
DN
24V
0V
DP
DN
24V
0V
A
B
LINELOAD
LOAD LINE
24V
0V
L
N
FG
~
-BL2LN87SB02D*CC20 7/20-
EAC-06-472
*
If the total length of the section where all the DP, DN, 24V, and 0V lines run in parallel is more than 50m
AnyWireASLINK master
24V DC stabilized
power supply
General-purpose
power supply lter
(Use it if necessary.)
2-wire
terminal
4-wire
terminal
4-wire
terminal
AnyWireASLINK master
If the total length of the
section where all the
DP, DN, 24V, and 0V
lines run in parallel is
more than 50m
24V DC stabilized
power supply
General-purpose
power supply lter
(Use it if necessary.)
2-wire
terminal
2-wire
terminal
4-wire
terminal
24V DC
stabilized
power supply
General-purpose power
supply lter
(Use it if necessary.)
4-wire
terminal
4-wire
terminal
4-wire
terminal
4-wire
terminal
4-wire
terminal
If the total length of the sections (A + B)
where all the DP, DN, 24V, and 0V lines
run in parallel is more than 50m
■COSEL Co., Ltd. Type: EAC-06-472 Connection example
①
Power supply to the entire system
②
Local power supply/branching
*
When using this lter, please be careful of the positions of LOAD and LINE.
*
When using this lter, please be careful of the positions of LOAD and LINE.
Terminator
Terminator
EAC-06-472
*
EAC-06-472
*

24V
0V
0V
OUT
OUT
A B
B
C
C
IN0
IN1
ALM
LINK
-BL2LN87SB02D*CC20 8/20-
①Power supply line disconnection monitoring function
3-wire type sensor: Applied to 24VL line (A) and 0VL line (C)
2-wire type sensor: Applied to IN line (B) and 0VL line (C) (NPN)
Applied to 24VL line (A) and IN line (B) (PNP)
②Signal line disconnection monitoring function
3-wire type sensor: Applied to IN line (B) and 0VL line (C)
2-wire type sensor: Applied to IN line (B) and 0VL line (C) (NPN)
Applied to 24VL line (A) and IN line (B) (PNP)
[Detection of Sensor Cable Disconnection and Short-circuit]
Conditions of
target sensor
[Disconnection monitoring function]
[2-wire type sensor ]
- Applied to ON/OFF sensor with 0.35mA or
more leak current
[3-wire type sensor]
- Applied to ON/OFF sensor incorporating
Zener diode output protection (breakdown
voltage: 47V or less)
*For information on sensors proven to be compatible with the
disconnection detecting function, please access our website.
http://www.anywire.jp
<Operation during disconnection>
①The power supply line disconnection monitoring function works for IN0 and IN1 individually.
No differentiate between 24VL line (A) disconnection and of 0VL line (C) disconnection.
②The signal line disconnection monitoring function works for IN0 and IN1 individually.
NPN type: No differentiation between IN line (B) disconnection and 0VL line (C) disconnection
PNP type: No differentiation between 24VL line (A) disconnection and IN line (B) disconnection
*
When 0VL line disconnection occurs with NPN type sensor, or when 24VL line disconnection occurs with PNP type sensor, it is
possible that both power supply line disconnection and signal line disconnection are brought into detection status.
At occurrence of disconnection, it is indicated with the LED on the unit, equipment parameter and alarm bit*1.
*1
It depends on lot No. whether alarm bit settings are enabled or not.
<Operation during restoration>
①Power supply line disconnection error will be automatically reset by eliminating the cause of disconnection.
②Signal line disconnection error will be retained even after the cause of disconnection is eliminated.
To reset this error, it is necessary that the reset command should be written with the relevant parameter.
Note: Even while the signal line disconnection error is retained, signal transmission is enabled.
- Do not connect an analog output sensor (4-20mA, 1-5V, etc.). Otherwise, a fault occurs
with the analog sensor.
- The cable length between this unit and a sensor should be 5m max.
- Transmission line 0V and I/O line 0VL must not be used in common. Otherwise, the
disconnection detecting function does not work.
- To use a mechanical contact (such as a switch), disable the monitoring function.
- This function is intended to detect disconnection of 24V, OUT and 0V lines of
general-purpose sensors, not to detect a fault of sensors.
[Short-circuit monitoring function]
③Power supply line short-circuit monitoring function
This function detects short-circuit between 24VL line (A) and 0VL line (C).
<Operation at occurrence of short-circuit>
When these lines are short-circuited, all data are turned OFF. Short-circuit is indicated with the LED on the unit, and the
status detail area.
<Operation during restoration>
For operation to eliminate the cause of short-circuit, manual restoration or automatic restoration can be selected
depending on the parameter setting.
While the short-circuit error is activated (retained), signal transmission and power supply to sensors are disabled.
!Precautions for Use - Transmission line 24V and I/O line 24VL must not be used in common. Otherwise,
the short-circuit detecting function does not work.
!Precautions for Use
24VL
IN
0VL (Current monitoring)
24VL
IN
0VL (Current monitoring) 2-wire type sensor
3-wire type sensor
*The gure shows an
example of NPN type.
ASLINKER unit
IN0 input/disconnection
indication
IN1 input/disconnection
indication

-BL2LN87SB02D*CC20 9/20-
IN0
IN1
LINK
ALM
IN1
IN0
4 3 2 1
AB
C
① ②
⑤ ⑥
③ ④
Black: DN
Red: DP
Green:
24V
White: 0V
[Connection Method]
1
2
3
4
Black (DN)
Red (DP)
White (0V)
Green (24V)
Dedicated tool: LP-TOOL
Place the wires in the grooves so
that the black wire (DN) is on the
hinge side of the cover, fold A over B
and engage the hook C to fasten it.
The condition in which
the cover is tted.
Ensure that the hooks
①and ②are engaged.
Pressure-bond using a
dedicated tool by guiding the
metal bracket on the connector
body into the hole of the cover.
After pressure-bonding, ensure
that the hooks ③to ⑥are
securely engaged.
Red: DP
Black: DN
Green: 24V
White: 0V
Brown: 24VL
Black: IN0
Blue: 0VL
Red: DP
Black: DN
Green: 24V
White: 0V
Transmission line connection wire
Brown: 24VL
Black: IN1
Blue: 0VL
LED indicators
Setting port
LINK
IN0
IN1
ALM
: Transmission indicator (Green)
: Input indicator (Orange)
: Input indicator (Orange)
: Alarm indicator (Red)
[Name of Each Part]
Input line
connection wires
Pin No.Wire color
Applicable LP connector: LP4-WW-10P
■Example of tting the LP connector at the end of transmission line
* For the power supply to be
connected, be sure to use
a 24V DC stabilized
power supply.
Transmission
signal
AnyWireASLINK
master
24V DC*
CAUTION
Make sure that the 24VL wire (brown) and 0VL wire
(blue) are not short-circuited while power is supplied.
Short-circuit may cause a fault of the equipment.
Connect this unit to the AnyWireASLINK master unit.
With the transmission signal (DP/DN) and power supply (24V/0V) being connected, set
parameters with the address writer.
■Common procedure for address writer operation
Address setting Parameter setting
[Various Settings]
Cover
Be sure to connect to the AnyWireASLINK master unit to use.
ARW-04 (address writer) of Rev. (Ver.) 1.01 or later version is required for address setting.
For the details of the operating method, refer to the product guide of ARW-04.

-BL2LN87SB02D*CC20 10/20-
0
1
2
0
1
2
3
0
1
S/W version
Address setting
An address number is set as a beginning number from which part of the transmission frame is occupied to the terminal.
Set the address number within the range of bit address “0 to 254.”
- Set the address number so that the area occupied by the terminal does not exceed the transmission points of the master unit.
- Make sure that the address number setting is not duplicated.
- Also, use the address writer to read an address number that has been written in the terminal.
The factory-set address is “bit address 255” or “bit address 511,” which indicates that an address
has not been set.
The factory-set address varies depending on lot No., as follows:
For S/W version “B” or later version: Bit address 511
For S/W version “A” or 3-digit lot No.: Bit address 255
Input and output operations are disabled with the factory-set
address.
CAUTION
CAUTION
Example:
Parameter setting
This parameter is used to specify whether the disconnection detecting function is enabled or disabled, and the target
for monitoring.
Although the unit can be used with the setting of “monitor both power supply and signal lines” with the
connection of 2-wire type sensors, I/O disconnection may be caused depending on the sensor to be connected.
If that happens, change the setting as follows.
Example 1: “Signal line disconnection” occurs all the time. →Set to “Monitoring enabled for power supply
line only.”
Example 2: “Power supply line disconnection” occurs all the time. →Set to “Monitoring enabled for signal
line only.”
Example 3: Both “power supply line disconnection” and “signal line disconnection” occur. →Turn OFF the
disconnection detecting function (disconnection detection disabled).
*
It is not possible to change the setting channel by channel. Pay attention to the setting if both 2-wire and
3-wire type sensors are used.
This parameter is used to specify channels supporting the disconnection detecting function.
This parameter is used to specify how to clear short-circuit status after short-circuit is detected.
Variable Description
Variable Description
Variable Description
Disconnection detecting function OFF
Monitoring enabled for power supply line only
Monitoring enabled for signal line only
Factory setting: 3
Factory setting: 0
Factory setting: 0
Monitoring enabled for both power supply and signal lines
Both IN0 and IN1
IN0 only
IN1 only
Automatic restoration
Manual restoration
■Disconnection monitoring function setting [Equipment parameter 1]
■Disconnection detection enabled CH setting [Equipment parameter 2]
■Short-circuit notication cancel setting [Equipment parameter 12]
Lot No. 19ECBNB

-BL2LN87SB02D*CC20 11/20-
0
1
15 14 13 12 11 10 9 8 7 6 5 4 3 2 1 0
31 30 29 28 27 26 25 24 23 22 21 20 19 18 17 16
・
・
n+0 n+1 n+2 n+3
n+0 n+1
15 14 13 12 11 10 9 8 7 6 5 4 3 2 1 0
31 30 29 28 27 26 25 24 23 22 21 20 19 18 17 16
47 46 45 44 43 42 41 40 39 38 37 36 35 34 33 32
63 62 61 60 59 58 57 56 55 54 53 52 51 50 49 48
◆Subsequent to input signal
■Alarm information output destination setting [Equipment parameter 5]
This parameter is used to specify alarm information output destination in the bit input information area of the master unit.
For alarm information, two bits are used. *
For alarm information output, setting equipment parameter 13 is required.
Alarm information is output to address n+2 or n+3 subsequent to corresponding input signal address setting.
Example: When this unit is set to address “4”
Variable
Address
Description CH0 input CH1 input
Bit input information area of master unit
CH1 input CH0 input
ALM bit 0
ALM bit 0
ALM bit 1
ALM bit 1
◆Latter half of input information area
Alarm information is output to the latter half of the input information area corresponding to the setting of the number of bit
transmission points for the master unit.
Example: When the number of bit transmission points for the master unit is “input: 64 points, output: 64 points,” and this unit is
set to address “4”
Address
Description CH0 input CH1 input
Bit input information area of master unit
CH1 input CH0 input
ALM bit 0
n + (number of input points /2) + 0 n + (number of input points /2) + 1
ALM bit 0
ALM bit 1
ALM bit 1
Description
Subsequent to input signal
Latter half of input information area Factory setting: 0

-BL2LN87SB02D*CC20 12/20-
Variable Description
4
3
2
1
6
5
0
Normal OFF
-
-
ON
ON
-
-
-
ALM bit 1
OFF
I/O power supply drop
Slave unit voltage drop
I/O short-circuit ON
Disconnection of CH1
Disconnection of CH0 ON
ON
ALM bit 0
ON
-
-
OFF
OFF
-
-
-
ALM bit 1
ON
OFF
OFF
OFF
ALM bit 0
Normal OFF
ON
ON (0.25 sec.) ⇔OFF (0.25 sec.)
ON (1 sec.) ⇔OFF (1 sec.)
ON (1 sec.) ⇔OFF (1 sec.)
ON (1 sec.) ⇔OFF (1 sec.)
ON (1 sec.) ⇔OFF (1 sec.)
-
ALM bit 1
OFF
I/O power supply drop
Slave unit voltage drop
I/O short-circuit ON
Disconnection of CH1 -
Disconnection of CH0
ON (0.25 sec.) ⇔OFF (0.25 sec.)
ALM bit 0
ON
OFF
OFF (0.25 sec.) ⇔ON (0.25 sec.)
OFF (1 sec.) ⇔ON (1 sec.)
OFF (1 sec.) ⇔ON (1 sec.)
OFF (1 sec.) ⇔ON (1 sec.)
OFF (1 sec.) ⇔ON (1 sec.)
-
ALM bit 1
ON
OFF
-
OFF (0.25 sec.) ⇔ON (0.25 sec.)
ALM bit 0
OFF
Normal OFF
ON
I/O power supply drop ON
ON
Slave unit voltage drop ON
ON
I/O short-circuit ON
ON
Disconnection of CH1 -
-
ALM bit 1
Disconnection of CH0 ON
ALM bit 0
When ALM bit is normal: OFF mode
ON
ON
OFF
OFF
OFF
OFF
OFF
OFF
OFF
-
-
ALM bit 1
OFF
ALM bit 0
When ALM bit is normal: ON mode
When ALM bit is normal: OFF mode When ALM bit is normal: ON mode
When ALM bit is normal: OFF mode When ALM bit is normal: ON mode
Alarm notification OFF
Notification by differentiating disconnected CH (When ALM bit is normal: OFF mode)
Notification by differentiating disconnected CH (When ALM bit is normal: ON mode)
Notification by differentiating disconnected CH and short-circuit/power supply drop (When ALM bit is normal: OFF mode)
Notification by differentiating disconnected CH and short-circuit/power supply drop (When ALM bit is normal: ON mode)
Notification by differentiating sensor cable error/voltage drop (When ALM bit is normal: OFF mode)
Notification by differentiating sensor cable error/voltage drop (When ALM bit is normal: ON mode)
When this unit is disconnected from the trunk line of the AnyWireASLINK system (at occurrence of
DP-DN disconnection), input signals and ALM bits are all turned OFF.
In the ALM bit normal-ON mode, ALM bits are ON in normal status, and at occurrence of DP-DN
disconnection, ALM bits are OFF. Thus, this function enables monitoring of trunk line disconnection.
Factory setting: 0
Key point
At occurrence of I/O disconnection, the ALM bit corresponding to a disconnected channel is alternately turned ON and OFF for
0.25 seconds each.
At occurrence of I/O short-circuit, both ALM0 and ALM1 are turned ON. At occurrence of voltage drop, both ALM0 and ALM1 are
alternately turned ON and OFF for 1 second each.
■Alarm information notification pattern setting [Equipment parameter 13]
◆Notification by differentiating sensor cable error/voltage drop
◆Notification by differentiating disconnected CH and short-circuit/power supply drop
◆Notification by differentiating disconnected CH
This parameter is used to output detected alarm information (I/O disconnection, I/O short-circuit, slave unit voltage drop, I/O power
supply drop) into the bit input information area. To set this parameter, select one of six patterns. Alarm information bits are two bits.
Contents of information vary depending on the notification pattern.
Priority of alarm events is fixed in the order of “slave unit voltage drop”→“I/O short-circuit”→“I/O disconnection”→“I/O power
supply drop.” When several alarm events are simultaneously detected, an alarm event with higher priority is notified.
At occurrence of I/O disconnection, the ALM bit corresponding to a disconnected channel is turned ON.
At occurrence of I/O short-circuit or voltage drop, both ALM0 and ALM1 are turned ON.
At occurrence of I/O disconnection or I/O short-circuit, ALM0 is turned ON.
At occurrence of voltage drop, ALM1 is turned ON.

-BL2LN87SB02D*CC20 13/20-
0
1
2
3
0
1
0
1
0
1
2
3
This parameter is used to check power supply line information when disconnection is detected.
Variable Description
Normal
Disconnection of IN0 only
Disconnection of IN1 only
Disconnection of both IN0 and IN1
■Power supply line disconnection information [Equipment parameter 3] *
For read only
Factory setting: 0
This parameter is used to check signal line information when disconnection is detected.
This parameter is used to clear a signal line disconnection error.
*
The signal line disconnection clear command is active only when the error signal is turned from OFF to ON.
This parameter is used to clear a short-circuit error when short-circuit notication cancel setting (equipment parameter 12) is
“manual restoration.”
*
After execution of the short-circuit notication cancel command, set this parameter to OFF.
Otherwise, operation of the short-circuit notication cancel setting (equipment parameter 12) is the same as that of the
automatic restoration setting.
Variable Description
Normal
Disconnection of IN0 only
Disconnection of IN1 only
Disconnection of both IN0 and IN1
■Signal line disconnection information [Equipment parameter 4] *
For read only
Factory setting: 0
Variable Description
Clear command OFF
Clear command ON
Variable Description
Cancel command OFF
Cancel command ON
Factory setting: 0
■Signal line disconnection clear command [Equipment parameter 6]
*When power is supplied, this unit will always start with the “0” setting.
*When power is supplied, this unit will always start with the “0” setting.
■Short-circuit notication cancel command [Equipment parameter 14]
Factory setting: 0

-BL2LN87SB02D*CC20 14/20-
n+1
IN1
n
IN0
ALM
bit 1
ALM
bit 0
n+1
IN1
n
IN0
n+3
ALM
bit 1
n+2
ALM
bit 0
b3b4b5b7 b6 b2 b1 b0b11b12b13b15 b14 b10 b9 b8
n+1
IN1
n
IN0
15 14 13 12 11 10 9 8 7 6 5 4 3 2 1 0
31 30 29 28 27 26 25 24 23 22 21 20 19 18 17 16
47 46 45 44 43 42 41 40 39 38 37 36 35 34 33 32
63 62 61 60 59 58 57 56 55 54 53 52 51 50 49 48
ALM bit 0ALM bit 1
IN0IN1
Address
offset
[Data Configuration]
*n = Bit address number assigned to this unit
Bit input information area
<When alarm bits are not used>
Address
offset
Bit input information area
<When alarm bits are used*1, Subsequent to input signal>
Address
offset
<When alarm bits are used*1, Latter half of input area>
Description
Description
Description
Bit input information area
(Number of bit input points /2) + (n+1) (Number of bit input points /2) + n
Example: When the number of bit transmission points for the master unit is “input: 64 points, output: 64
points,” and this unit is set to address “4”
Bit input information area of master unit
*1
It depends on lot No. whether alarm bit settings are enabled or not.
*2
This can be used on the master unit having the status detail area. For details, refer to the manual for the master unit.
Status
details
Status detail area of the master unit
b0: Slave unit voltage drop (DP-DN-side voltage drop)
b2: I/O disconnection
b3: I/O short-circuit
b5: I/O power supply drop (24V-0V-side voltage drop)
■Status details
The contents of an alarm issued by this unit can be checked with the unit’s ALM indicator and the “status detail area*2”
on the master unit.
A bit corresponding to the status detail area turns ON depending on the contents of the alarm.

-BL2LN87SB02D*CC20 15/20-
LINK (Green)
IN0 (Orange)
IN1 (Orange)
ALM (Red)
ALM
LINK
I/O
If an error is indicated, identify a cause of the
error by checking lit/ashing status with the
table on the left, and eliminate the cause of
the error.
LED indicators
Setting port
LED name
*1 This indication appears when the use of the single unit simplied replacement function fails.
(This operation occurs on the S/W version “B” or later version.)
*2 This condition is detected when the master unit executes automatic address recognition.
*3 For S/W version “B” or later version: This indication appears when transmission signal and
power supply are normally connected, and the unit is set to the factory-set address.
For S/W version “A” or 3-digit lot No.: This condition is detected when the master unit
executes automatic address recognition.
LINK
(Green)
ALM
(Red)
Flashing
Lit
Unlit
Flashing
Lit
Lit
Unlit
Unlit
Display status
Alternate ashing
Model mismatching error*1
Description
I/O disconnection, I/O short-circuit, I/O power supply drop
No ALM available
Transmission signal received
Slave unit voltage drop
Model mismatching error*1
Transmission signal error
Model mismatching error*1
ID duplicated*2or ID unregistered*3
No transmission signal (disconnection and
reverse connection of DP and DN lines included)
[Monitor Display]
I/O
(Orange)
LINK
ALM
LINK
ALM
LINK
ALM
ON
OFF
LINK
ALM
When I/O flashes in synchronization with LINK
while ALM is lit, it indicates I/O disconnection.

-BL2LN87SB02D*CC20 16/20-
<LINK does not ash>
Remedy
Check the connection of this unit.
Check conditions of the master unit
and slave unit.
Disconnect this unit once, and then reconnect it.
[Troubleshooting]
Things to be checked
Remedy
Things to be checked
Remedy
Things to be checked
Remedy
Things to be checked
Remedy
Things to be checked
1) If LINK on the master unit is ashing and LINK on the slave unit is lit, it is possible that the master
unit has a fault or power supply (24V-0V) is directly connected to the DP-DN pins of the slave unit.
*
If LINK is lit while ALM is ashing, it means a failure in single unit simplied replacement.
2) If LINK on the master unit is ashing and LINK on the slave unit is unlit, it is possible that the power
(24V DC) is not supplied to the master unit, there is a disconnection on the transmission line (DP,
DN), or the slave unit has been damaged.
3) If LINK on the master unit is not ashing, check the power supply to the master unit. Also, since there
is a possibility that some system error has occurred, refer to the user’s manual of the master unit.
4) A slave unit incompatible with Ver.1.1 cannot be used in connection to the AnyWireASLINK system
for word transmission. Check the setting of the master unit, and lot No. of the slave unit.
<ALM is lit>
<ALM is ashing>
<LINK and ALM ashes alternately>
<LINK is lit and ALM is ashing: Model mismatching error (Failure in single unit simplied replacement)>
Check the connection of I/O terminals
on the slave unit.
When IN ashes in synchronization with LINK while ALM is lit, the unit has I/O disconnection.
If only ALM is lit, the unit has I/O short-circuit or I/O voltage drop.
Check information by reading the status detail area*.
1) Make sure that the slave unit I/O line and load are normally connected. Use caution about
disconnection of the wiring and insufcient screw tightening.
2) To connect a mechanical contact (relay, switch, etc.) as load, OFF signal cannot be differentiated
from disconnection. In this case, set the equipment parameter for the disconnection detecting
function to OFF.
3) Check wiring of the slave unit terminals to ensure that the connected load meets the power supply
and output specications of ASLINKER, and adjust it as required.
4) Adjust the power supply voltage of an external power source connected to the slave unit I/O line, so
that the power supply voltage does not exceed the rated voltage range (21.6V to 27.6V). Make sure
that wires of the transmission line do not touch each other. Check for incorrect wiring of the terminals.
*
Refer to the manual for the master unit.
Adjust the voltage of external power supply to the master unit so that it will be in the range from 21.6 to
27.6V. (Recommended voltage is 26.4V.) Check the total length.
Review the total length and wire diameter of transmission line so that the load will not exceed the current
limit supplied by the transmission line and adjust the connected load. (In the case of the wire size of
1.25mm2and total length of 50m or less, the current supplied by the transmission line is 2A.)
*
If ALM is ashing while LINK is lit, it means a failure in single unit simplied replacement.
Check if the replacement slave unit is of the same type as that of the slave unit before the replacement.
Check if the function version for the replacement slave unit is older than that of the slave unit before the
replacement.
*
If the function version of the replacement slave unit is older, the single unit simplied replacement function does not
work.
The address of the slave unit is either unregistered or duplicated.
Take the following actions.
*
The slave unit cannot be used with the factory-set address.
1) Set a bit address correctly in a range of 0 to 254.
2) Check if there is a slave unit on which the indicator lamps are ashing in the same manner and reset
the addresses so that they are not duplicated.
Check the address of the slave unit.
Check the address of the slave unit.
Check the model of the slave unit.
Check the lot No. of the slave unit.
Check the connection of the slave
unit.
Check the voltage (24V DC) of
external power supply to the master
unit.
Check if the address of the replacement slave unit is the same as the address before shipment (a bit
address of 511).
*
If the address of the replacement slave unit is not the same as the address before shipment, the single unit simplied
replacement function does not work.
Defective connections and the like may have caused single unit simplied replacement to fail.
Remove the slave unit after replacement, and make connections again.
*
When two or more replacement slave units are simultaneously connected, the single unit simplied replacement
function does not work.

-BL2LN87SB02D*CC20 17/20-
6.8k
6.8k
[Configuration and Electrical Characteristics of Input Circuit]
24V (Green)
IN
(Black)
0VL
(Blue)
24VL
(Brown)
Main circuit
of sensor
DN (Black)
DP (Red)
0V (White)
Smart ASLINKER side Sensor side
(This circuit diagram shows a typical example.)
Internal
circuit
Control circuit
BL2LN87SB-02D-CC20
IN
(Black)
0VL
(Blue)
24VL
(Brown)
Main circuit
of sensor
<Circuit conditions>
Rated input voltage:
Max. switching current:
ON current:
OFF current:
ON voltage:
OFF voltage:
Allowable current at 24VL:
24V DC
3.5mA
2.2mA or more
1mA or less
16V or more (24VL-IN)
8V or less (24VL-IN)
50mA max. (24VL-0VL) (per point)
Internal
circuit
4-wire (isolated) NPN input
DN (Black)
DP (Red)
24V (Green)
0V (White)
Smart ASLINKER side Sensor side
(This circuit diagram shows a typical example.)
Current detection
Control circuit
BL2LN87SB-02DS-CC20
<Circuit conditions>
Rated input voltage:
Max. switching current:
ON current:
OFF current:
ON voltage:
OFF voltage:
Allowable current at 24VL:
24V DC
3.5mA
2.2mA or more
1mA or less
16V or more (IN-0VL)
8V or less (IN-0VL)
50mA max. (24VL-0VL) (per point)
4-wire (isolated) PNP input
Current detection

-BL2LN87SB02D*CC20 18/20-
1
0000
Factory setting: 0003
0001
0002
0003
3
0000
0001
0002
0003
13
0000
0001
0002
0003
0005
0004
0006
4
0000
0001
0002
0003
2
0000
Factory setting: 0000
Factory setting: 0000
7 to 11
0001
12
0000
0001
Factory setting: 0000
6
0000
0001
Factory setting: 0000
5
0000
0001
Factory setting: 0000
0002
15 to 19
Factory setting: 0000
14
0000
0001
Disconnection
monitoring function
setting
Disconnection
detection enabled
CH setting
Power supply line
disconnection
information
*
For read only
Signal line
disconnection
information
*
For read only
Alarm information
output destination
setting
Signal line
disconnection
clear command
Short-circuit
notication cancel
setting
Alarm information
notication
pattern setting
Short-circuit
notication
cancel command
Spare
Used to specify whether the
disconnection detecting function is
enabled or disabled.
Used to specify a number of input
channels subject to this function when the
disconnection detecting function is used.
Used to check power supply line
information when disconnection is
detected.
Used to check signal line information
when disconnection is detected.
Used to specify alarm information
output destination in the input area of
the resend unit.
Used to clear a signal line
disconnection error.
Used to specify how to clear
short-circuit status after short-circuit is
detected.
Notication by differentiating disconnected
CH (When ALM bit is normal: OFF)
Notication by differentiating disconnected
CH (When ALM bit is normal: ON)
Notication by differentiating disconnected
CH and short-circuit/power supply drop
(When ALM bit is normal: ON)
Notication by differentiating sensor cable
error/voltage drop
(When ALM bit is normal: OFF)
Notication by differentiating sensor cable
error/voltage drop
(When ALM bit is normal: ON)
Notication by differentiating disconnected
CH and short-circuit/power supply drop
(When ALM bit is normal: OFF)
Used to specify an alarm information
notication pattern.
Used to clear a short-circuit error when
short-circuit notication cancel setting
is “manual restoration.”
Spare
[Equipment Parameters and Their Settings]
Equipment
parameter Setting item Description
Variable
Description
Disconnection detecting function OFF
Monitoring enabled for power supply line only
Monitoring enabled for signal line only
Monitoring enabled for both power supply and signal lines
Both IN0 and IN1
IN0 only
IN1 only
Normal
Disconnection of IN0 only
Disconnection of IN1 only
Disconnection of both IN0 and IN1
Normal
Disconnection of IN0 only
Disconnection of IN1 only
Disconnection of both IN0 and IN1
Subsequent to input signal
Latter half of input information area
Clear command OFF
Clear command ON
Automatic restoration
Manual restoration
Alarm notication OFF
Cancel command OFF
Cancel command ON

-BL2LN87SB02D*CC20 19/20-
①
②
IN0
IN1
LINK
ALM
IN1
IN0
(200)
6.5
10.2
56
(200)4.5
7.1
4.5
13.4
9.2
17
5.5
60
4
DP (Red)
DN (Black)
24V
(Green)
0V (White)
AWG24 φ1.1mm 3AWG26 φ1.0mm
IN (Black),
24VL (Brown),
0VL (Blue)
■Individual specications
Number of
occupied points
Current
consumption
Detection
function
Slave unit voltage drop (DP-DN voltage drop)
I/O disconnection
I/O short-circuit
I/O power supply drop (24V-0V voltage drop)
Weight
Response time*51ms max.
Operating ambient
temperature/humidity
Storing ambient
temperature/humidity
Vibration resistance
Shock resistance
Atmosphere
Operating altitude*1
Pollution level*2
0 – +55°C, 10 – 90%RH No condensation
-25 – +75°C, 10 – 90%RH No condensation
Based on JIS B 3502 and IEC 61131-2
Based on JIS B 3502 and IEC 61131-2
No corrosive gas
0 – 2000m
2 or less
Service power supply voltage
Transmission method
Synchronization method
Transmission procedure
Connection mode
Number of
connection points
*3
Number of connection units
RAS function
24V DC +15% to -10% (21.6 to 27.6V DC)
with a ripple of 0.5Vp-p or less
DC power supply superimposed
total frame/cyclic method
Frame/bit synchronization method
AnyWireASLINK protocol
Bus type (Multi-drop method, T-branch
method, Tree branch method)
Number of bit points:
512 points max.
(Input: 256 bits, Output: 256 bits)
Number of word points:
1024 words max.
(Input: 512 words, Output: 512 words)
Up to 128 units
Detection of transmission line disconnection,
transmission line short-circuit, transmission
power supply drop, and
duplicated/unregistered ID
■Transmission specications
*1 Do not use or store AnyWireASLINK devices in an environment where the pressure exceeds
the atmospheric pressure at an altitude of 0 meters. Doing so may result in malfunction.
*2“Pollution level” is an index that indicates the degree of occurrence of conductive substances
in the environment where the device is used.
Pollution level 2 means the occurrence of only pollution by non-conductive substances.
In such an environment, however, electrical conduction could occur due to accidental
condensation.
*3 The number differs depending on the master unit. Be sure to refer to the manual of the
master unit for the number.
②Input side①Transmission side
*4 It depends on lot No. whether alarm bits can be used or not.
*5 Indicates an internal processing time required for this unit to recognize a signal change,
apart from transmission delay time (2-cycle time).
*6 Indicates a value assumed when all IN-0VL pins (NPN) or 24VL-IN pins (PNP) are
short-circuited. To connect a 3-wire type sensor, add a total current consumption of the
sensor.
[Specifications]
■General specications
Bit input: 2 to 4 points
(Input: 2 points + Alarm bit: 2 points*4)
Transmission side (DP-DN): 1.6mA
I/O side*6(24V-0V): 11.6mA
60g
■Specications of the cable included in ASLINKER
Number of
core wires Core wire sizeSignal name Core wire sheath
outer diameter
Number of
core wires Core wire sizeSignal name Core wire sheath
outer diameter
[Outside Dimensions] Unit: mm

Printed in Japan 2018,2019,2020 UMA-16324AK-EN
-BL2LN87SB02D*CC20 20/20-
Anywire Corporation
Headquarters :1 Babazusho, Nagaokakyo-shi, Kyoto 617-8550 JAPAN
:Contact by website http://www.anywire.jp
[Address]
This manual suits for next models
2
Table of contents
Popular Adapter manuals by other brands
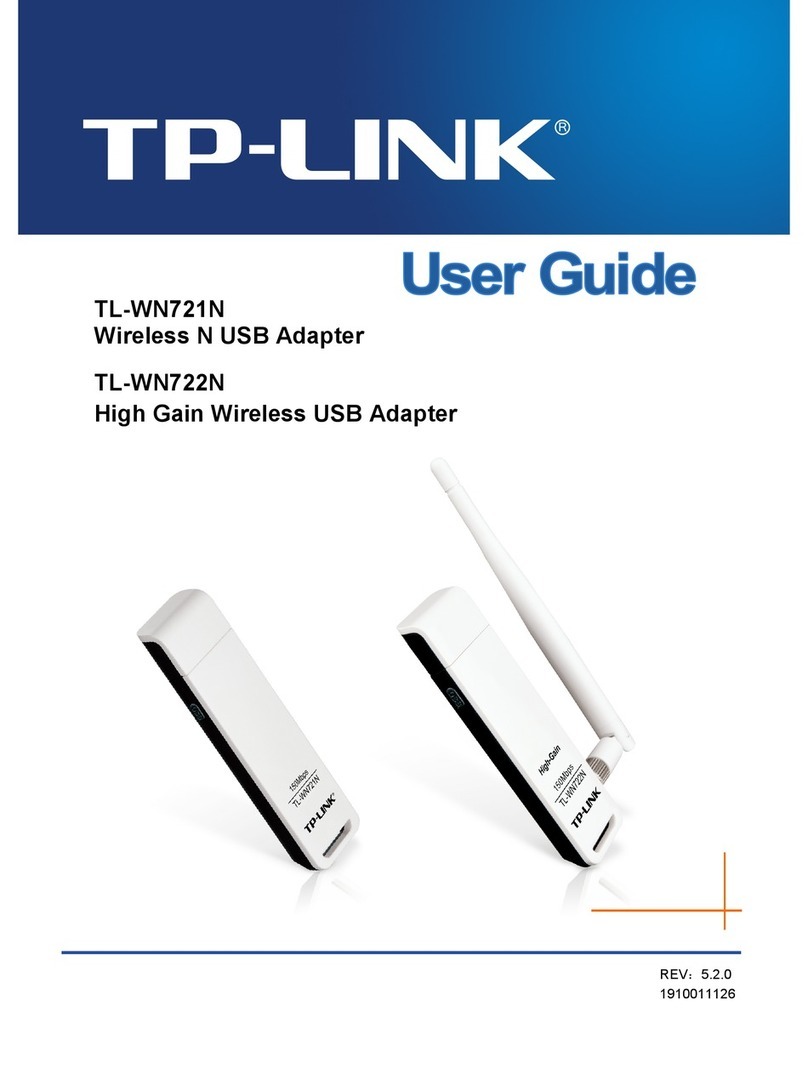
TP-Link
TP-Link TL-WN721N user guide
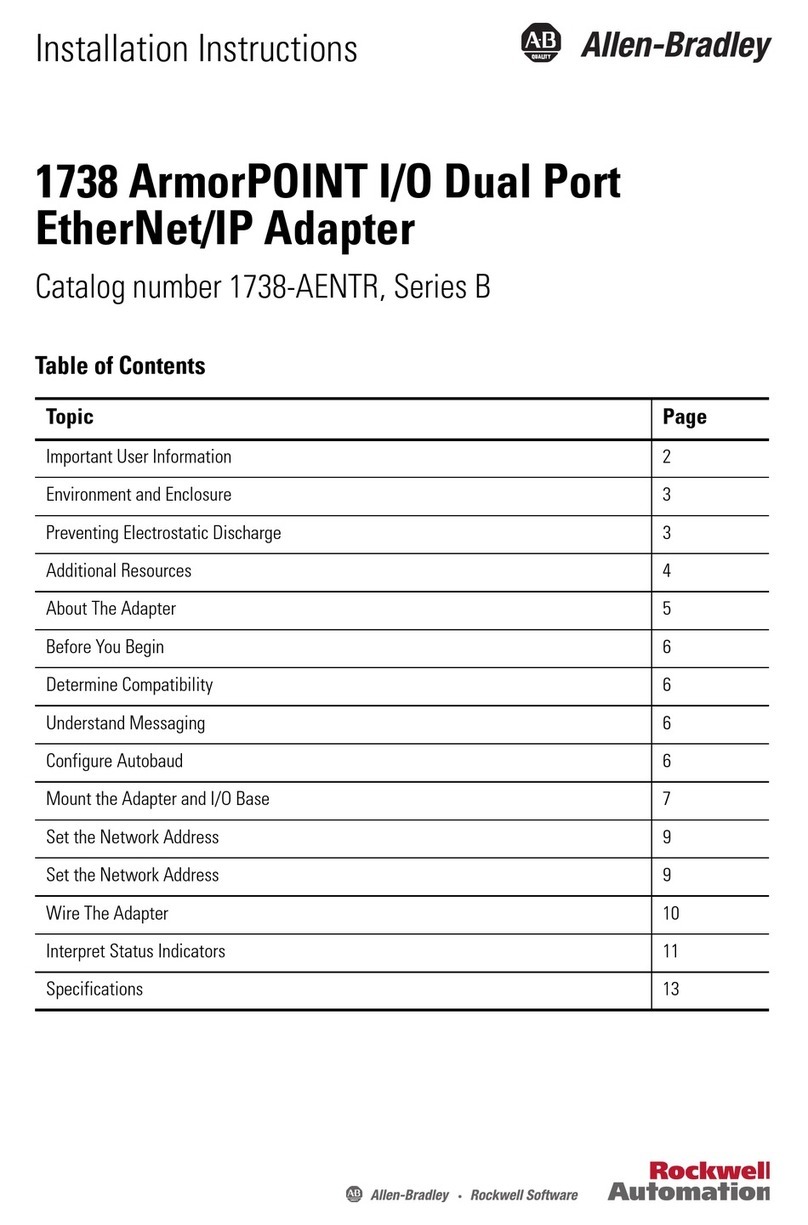
Allen-Bradley
Allen-Bradley 1738 ArmorPOINT installation instructions
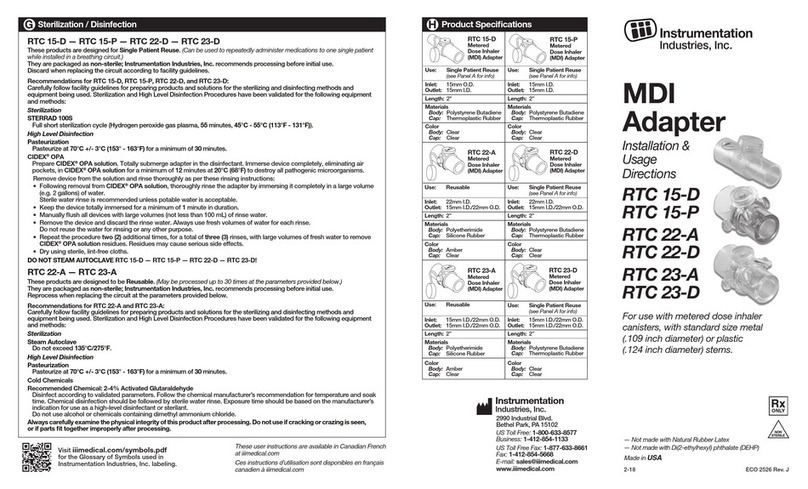
Instrumentation Industries
Instrumentation Industries RTC 15-D Installation & Usage Instructions

Hawg Wired
Hawg Wired HMA 150 installation guide
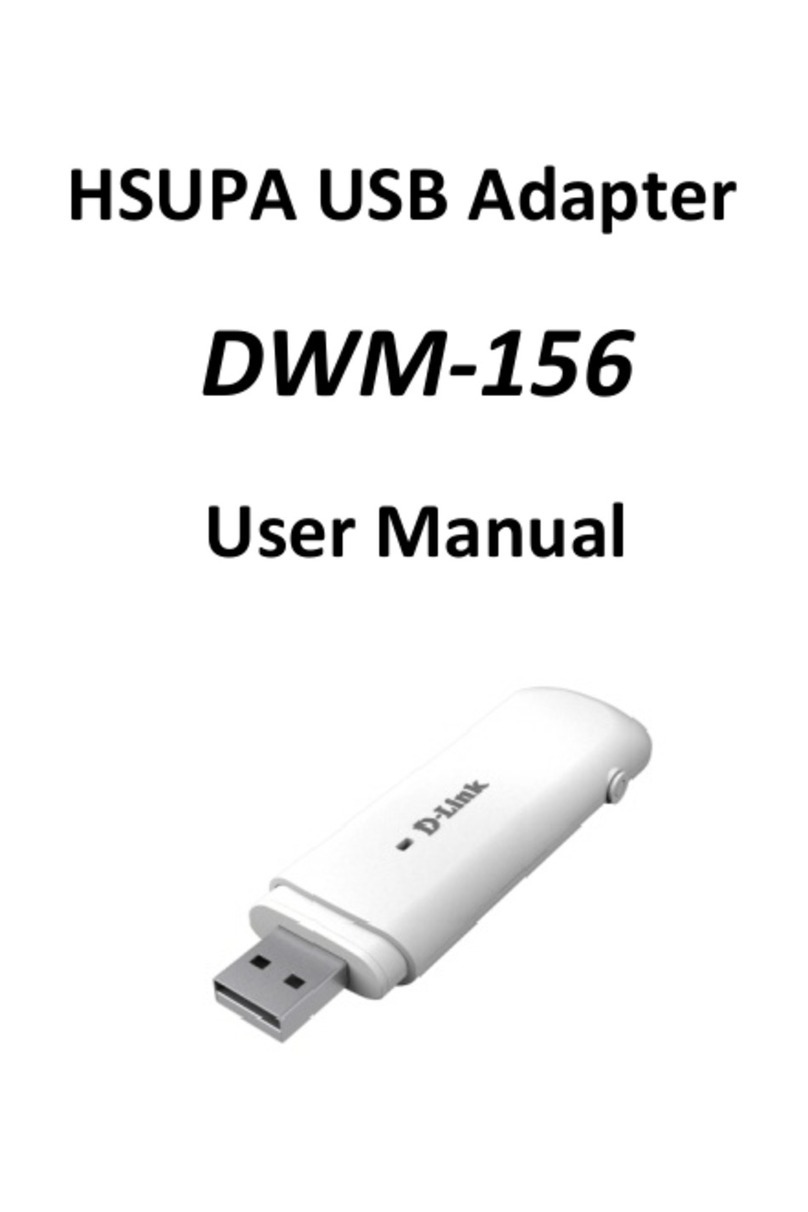
D-Link
D-Link DWM-156 user manual

CHIEF
CHIEF MAC-251 installation instructions