AQUARIUS ULTIMA User manual

1
Instruction Manual v.1.1
Cooling Tower Controllers

2
Table of contents
Warnings 3
Introduction 4
Installation Guidelines 5
Before you start 5
System requirements 5
To install 6
Maintenance and Care of Sensors 6
Accessories and Spare Parts 7
Routine Testing 7
Regular Inspection and Maintenance 7
Electrical Wiring 8
Connections 9
System Configuration 11
Turning ULTIMA controller ON 11
Main Screen 12
Setting System Preferences 12
Advanced Settings 14
Importing/Exporting Settings and Exporting Data 14
Component Settings 15
General Layout 15
TDS/Conductivity Configuration 16
ORP Configuration 17
pH Configuration 18
pH B Configuration 20
Inhibitor Configuration 20
Dispersant Configuration 21
Timers Configuration 22
Outputs Configuration 23
Bio B Timer Example 25
Attachments
Installation diagrams 27

3
Warnings
Refer to AS/NZS 3000 WIRING RULES when installing electrical equipment on and around the
cooling towers and HVAC equipment. The power cover is to be removed by Aquarius Technologies
Pty Ltd, an authorized service agent or a licensed electrician only, and must be replaced before the
controller is connected to the power supply. Do not open the controller enclosure except as
required for maintenance purposes. Once maintenance is complete, the enclosure is to be closed
and resealed. If the supply cord is damaged, it shall be replaced by Aquarius Technologies Pty Ltd
or an authorized service agent to avoid a hazard. This appliance is not intended for use by young
children or infirm persons unless they have been adequately supervised by a responsible person to
ensure they can use the appliance safely. Young children should be supervised to ensure they do
not play with the appliance.
This marking indicates that this product should not be disposed of with other household
wastes throughout the EU. To prevent possible harm to the environment or human health from
uncontrolled waste disposal, recycle it responsibly to promote the sustainable reuse of material
resources. To return your used device, please use the return and collection systems or contact the
retailer where the product was purchased. They can take this product for environmental safe
recycling.
Chemicals used as part of the treatment program may be hazardous. Refer to the Material Safety
Data Sheets provided by your chemical supplier and ensure all personnel involved are aware of
the handling and safety procedures.
It is a requirement to provide protection for accidental spills of chemicals and that includes any
leaks that can develop from pump pressure lines. Please read and understand all safety warnings
on chemical containers before servicing any dosing equipment. Some chemicals will damage
materials used in construction of buildings, particularly roofing. Never assume that the equipment
will not leak, under certain conditions that will occur. It is the responsibility of the installer to ensure
that such events do not create damage that should have been avoided by correct site selection
and the provision of adequate bunding at the time of installation.
Wear as a minimum - safety goggles and gloves when servicing the dosing equipment. Do not mix
concentrated acids and oxidising agents as explosion, and/or toxic and lethal gas may be evolved,
and/or fire result. Keep all chemical containers sealed and free from contamination.
Bleed solenoid and BCD solenoid leads should not be left unattended due to the risk of high
voltage hazards. All solenoids must be connected to their leads before turning the controller ON. It
is a full responsibility of the installer and user to ensure the leads are not exposed to the open air
or water ingress.

4
INTRODUCTION
Ultima advanced cooling tower controllers model incorporates the following key features:
• TDS/Conductivity Control
• Inhibitor timer Control
• Oxidizing biocide Control through ORP
• Non-Oxidizing biocide control through timers
• Single and Dual pH Control
• Dispersant dosing Control
• Temperature Monitoring
• Comprehensive timers to regulate
• On Board Data logging
• Accessory timers for the better performance of each individual timer
• High and Low alarms for pH, ORP & TDS
• Extensive Internet Communication choice (Modem, Wi-Fi, Ethernet)
Where to find the serial number
Serial Identification Label
All Aquarius Technologies Controllers are manufactured with a Serial Identification Label (SIL).
This will be affixed to the wall of the controller, on the outside face on the right side.
The label is the best reference for making inquiries for service or Technical Assistance.
Any controller that does not show evidence of the SIL may have the warranty voided.
Key data being:
Model: e.g. ULTIMA. This is actual Controller model and indicates the configuration.
Build: e.g. Mar-15. Would indicate this controller was manufactured in March 2015
Serial No: e.g. 1503ULT000694 is the specific serial number for this Controller

5
Installation Guidelines
Please refer to this section for typical installation guidelines, typical layout and Housing Installation
diagrams.
Before you start
Select a suitable location for installation - preferably in close proximity to the main system, protected
from the public and environmental factors such as direct sunlight. The suitable location must not
be on top of a source producing large amounts of heat (e.g. metal fence or shed) and ideally not
be in direct sunlight. The Ultima LCD screen must be covered by the flap lid for UV protection on
all outdoor installation. A wall area of approx. 0.75 m. wide by 1.0 m. high is ideal for mounting
your controller. Mount the unit at eye-level to allow good navigation of the controller. A minimum
floor area of approx. 1.5 m x 0.6 m below the controller is required for the chemical tanks. This
will vary according to the number and type of chemicals being used for dosing.
It is important to consider environmental elements when installing. It is a requirement to
provide protection for accidental spills of chemicals and that includes any leaks that can
develop from pump pressure lines. Some chemicals will damage materials used in construction of
buildings, particularly roofing. Never assume that the equipment will not leak, under certain
conditions that will occur. It is the responsibility of the installer to ensure that such events do not
create damage that should have been avoided by correct site selection and the provision of
adequate bunding at the time of installation.
System requirements
There are several minimum requirements that should be established BEFORE the controller is
installed;
• Minimum 20 mm (3/4) take-off and in line to supply sample water to the system,
• Minimum 12 litres/minute supply flow to ensure proper operation of sample readings, dosage and
bleed off rates.
• Adequate bunding is provided for the system and chemical drums to prevent spills causing
damage.
• Availability of approved connection to power. A ‘clean’ 220 - 250 VAC 50 Hz @10
amps supply (some options may need more than one outlet, or increased current capability).
Users of the Ultima are prevented from contact with hazardous voltages by the protection cover
(Picture 1 and Picture 2). Only a certified electrician or Aquarius Approved Service Technician may
remove the protection cover to access the hazardous voltage area. It is required to disconnect the
controller from the supply before removing the cover or performing any electrical work, including
unplugging and/or replacing all circuit boards.
Picture 1. Protection cover Picture 2. Warning on the protection cover

6
To install
Unpack the equipment and check for any damage. Ensure all parts are accounted for.
Assemble the inlet and outlet PVC valves on the sensor manifold. Remove the protective cap
and fit the pH/ORP probe and other probes into the manifold.
Install the BLEED solenoid on the manifold and wire the power cable supplied from ULTIMA.
(Never leave the bleed solenoid cable unplugged when turning ULTIMA ON)
Connect a 20 mm line from the circulating pump discharge line, or system common discharge
header, to the inlet of the manifold. Connect a return line from the manifold outlet valve,
preferably in PVC pipe to the pump suction or common suction header or to the tower basin.
If installing a BCD Feeder, assemble the BCD feeder as per its separate instructions and floor
mount in the vicinity of the system. Plumb from the BCD control solenoid to the inlet of the BCD
feeder and from feeder to the system.
Install the BCD solenoid as required and wire its power cable before plugging into the sockets
supplied inside the controller box. (Never leave the BCD solenoid cable unplugged when turning
ULTIMA ON)
Install chemical tanks as required, and ensure each dose pump’s discharge tubing is connected
to the manifold injection points provided.
Run a flow of water through the system under normal operating pressures. Check for, and repair
any leaks. The Ultima Controller is now ready for use.
Liaise with your chemical specialist for advice regarding any bunding requirements, floor
drainage requirements and fresh water supply in the vicinity of chemical tanks. In addition
check on local authority regulations for discharge of trade waste, chemical storage and hazards
control etc.
Maintenance and Care of Sensors
Foulants can lead to inaccurate sensor readings. Sensors should be cleaned and calibrated
regularly using the following procedures.
Cleaning of Flow/Conductivity/Temp Sensor
Isolate the flow to the manifold. Remove the locking nut from the Flow/Conductivity/Temp sensor.
Abrade the sensor surface with 300–400 grade wet–and–dry paper until the surface is clean, the
two carbon electrode surfaces are clearly visible, and the surface wets out freely.
Ensure flow paddle is free from debris. Rinse the sensor in fresh water and replace it in the
manifold.
Cleaning of pH/ORP sensor
Isolate flow to the manifold. Remove the sensors from the manifold by loosening the lock
nut and withdrawing the sensor from the manifold.
Rinse the sensors in fresh tap water and remove any visible fouling. This should be done carefully
by lightly scrubbing with a soft tooth brush or similar.
Place the sensors in the Electrode Cleaner solution ( AS9500) for about 5 minutes to completely
dissolve any trace of inorganic foulants.
Remove and rinse thoroughly in fresh water before replacing it in the manifold. Proceed to
calibration or verification of sensors as outlined in the commissioning section.

7
Accessories and Spare Parts
Reagents
AS1413 -1413 µcm conductivity solution
AS7004 - pH 4 buffer solution
AS7007 - pH 7 buffer solution
AS5475 - 475 mV ORP solution
AS4250 - pH 4.01/250 mV combo solution
Sensor
s
PR_FCT – Combination Conductivity, Flow and Temperature Sensor.
PR_pHRG – Combination pH, ORP and Ground reference Sensor
Peristaltic Pumps
AP_PERI_S_KIT – AP PERI SERVICE KIT (Maximum service interval - 12 months). Included in
this Kit are the following
• AP_TUBE4824 (1)
• AP_INJECT (1)
• TUBESUCTION (2 mt)
• TUBEDISCHARGE (2 mt)
AP_PERI_O_KIT – AP PERI OVERHAUL KIT (Maximum service interval - 2 years)
Included in this Kit are the following
• AP_TUBE4824 (1)
• AP_INJECT (1)
• AP_ROLLBLOCK (1)
• AP_DWEIGHT (1)
• AP_LID (1)
• TUBESUCTION (2 mt)
• TUBEDISCHARGE (2 mt)
Routine Testing
The use of an Aquarius control system will automatically vary the dosages and maintain
good conductivity, ORP and pH control, even where there are wide fluctuations in system load
or demand. The principles of “Best Practice” and “Duty of Care” that are the responsibility of the
system owner dictate that all systems should be routinely serviced and tested chemically and
the results logged.
Regular Inspections and Maintenance
For optimum results and continued accuracy, the complete operation of the controller system
should be verified at least on a monthly service basis.
All sensors should be inspected, cleaned and calibrated as necessary every month.
All sensors age with time and temperature, and have a typical life span of 12-36 months
depending on the application in which they are operating and should be replaced accordingly.
Where fitted, flow sensors and wire strainers should be checked for correct operation and
cleaned of any debris every month so they work efficiently.
Injection non-return valves and pumps should be cleaned and checked at least monthly.

8
Sodium Hypochlorite being highly alkaline may lead to scale formation on its dose injector and
this may require acid cleaning on a frequent basis.
On the peristaltic dose pumps, the squeeze tubes and roller block should be checked at least
annually and should be replaced every 12-24 months.
More regular maintenance may be required for the larger 3.0 l/hr pumps, due to increased
pumping rates.
Chemical suction and discharge tubes should be inspected monthly and replaced as necessary
Maintenance schedule 1 month 3 months 6 months
12 months
Clean and Calibrate FCT Probe √
Verify Flow ON/OFF √
Clean and Calibrate FAC Probe √
Clean pH/ORP Probe √
Verify / Calibrate ORP √
Test Outputs √
Test Pumps/Solenoid Operation √
Calibrate pH Probe √
Check/Clean Injectors √
Inspect Suction/Discharge Tubing
√
Check/Clean Solenoids √
Peri. Pump - AP Service Kit √
Peri. Pump - AP Overhaul Kit √
Electrical Wiring
Refer to AS/NZS 3000 WIRING RULES when installing electrical equipment in and around water
areas.
The hazardous voltage area of this controller is under the protection cover (see Pictures 1 and 2).
Only Safety Extra Low Voltage (SELV) is supplied to the accessible circuit boards inside the
enclosure. Sensors may be maintained while the controller is powered.
CAUTION: Only a certified electrician or Aquarius Approved Service Technician may remove the
protection cover to access the hazardous voltage area. It is required to disconnect the controller
from the supply before removing the cover or performing any electrical work, including unplugging
and/or replacing SELV circuit boards such as the Motherboard or Probeboard.
Fuses are easily accessible:
Equipment fuse F1: Output fuse: 5A/250VAC 20 x 5mm
Relay fuse F2: - Only if additional relay for output 8 is installed.
Control fuse F3: 0.125A/250VAC Time-delay 20 x 5mm

9
Connections
The motherboard is located on the internal side of the front controller lid.
The diagrams below show the connections to the Ultima controller motherboard circuitry:
1 – Power cable connector
2 – Probe-board power cable connector
3 – USB connector
4 – USB connector
CAUTION: When front controller door is open it sits on two hinges on the left hand side of the
controller. (Picture 3) Please take extra care when operating with an open front door. Do not push
the front lid upwards without holding onto the door, as this could detach the door from the support
hinges. Always close the front panel on completion of maintenance work and fasten screws.
Note: Please ensure the O-ring is in good condition and seated properly within the groove.
Picture 3. Left – hand side support hinges

10
The Probe-board is located above the protection cover on the bottom left hand corner of the
controller.
The diagrams below show the connections to the Ultima Probe-board circuitry:
1 – Power cable connector between Probe board and Motherboard
2 – BNC pH connector (if fitted)
3 – BNC ORP connector (if fitted)
4 – Combination Probe (PR_PHRG) connector
5 – FCT probe (PR_FCT) connector
6 – FAC probe connector
7 – Dip switches for FAC Probe Gain regulation
8 – 4-20mA connector and Water meter connector
9 – 5 x Analogue inputs
10 – 3 x 5V DC and 2 x 12V DC power supply connectors
11 – 5 x jumpers for tank alarm sensors connected to the analogue inputs

11
System configuration
The ULTIMA controller has a 7” touch screen and navigation is similar to that of any smart phone,
PC monitor, GPRS navigator or other modern device. Operating the controller is done by
touching the screen and navigating using your finger. The ULTIMA controller screen is covered
with a protective film.
CAUTION: Do not operate the controller with dirty or wet fingers. Do not touch the controller
screen with metal or sharp object. Always close the screen flap cover down on completion.
All Aquarius controllers come loaded with preset default values for all of the treatment program
parameters. On start up the controller will operate according to those defaults. However, every
application should have a planned treatment program developed. Decisions should be made on
what values are most appropriate for ORP, pH, TDS/ Conductivity, Inhibitor, Secondary Biocide
and Dispersant dosing requirements.
Once the customized program has been determined, it may be set in the Aquarius controller, as
described in the following sections.
Turning the ULTIMA controller ON
When you plug the controller into 240 VAC supply it turns ON. It takes about 30 seconds for the
controller to open its program. During this time AQUARIUS animation logo will appear on the
screen.
CAUTION:
All provided solenoid cables are wired to 240V electricity source and must not be left unattended
when turning the controller ON
- Do not turn the controller ON until the bleed solenoid cable is wired to a proper solenoid
- Do not turn the controller ON until BCD solenoid cable is wired to a proper solenoid or it is
unplugged from the controller (if BCD solenoid cable is included)
When the program is fully loaded the front lock screen will appear. (Picture 4) To start using the
controller, press the UNLOCK.
Picture 4. UNLOCK Screen

12
Main Screen
The Main Screen display (Picture 5)
Picture 5. MAIN Screen
- Top bar with Connection Status, Date, Time, Flow ON/OFF parameters
- Menu with icons on the left side of the screen. Icons are SYSTEM, LOCK SCREEN and NEXT
- Six main parameters with Component information. Component information displayed is as
follows: Name, Current Value and Set point. If the relay is ON, the POWER icon turns blue in the
left top corner of each component box. If the Component is in LOCK OUT, a RED PADLOCK
sign will be active on the left top corner. If the Component is in ALARM, the top part of the
component box will flash RED. Some Component boxes display icons for easy identification of
the Component.
The red light signal on the top right of the screen shows that at least one parameter is in alarm.
Setting System Preferences
To set system preferences press SYSTEM icon on the left-side Menu of main screen. The
SYSTEM screen will appear (Picture 6). This is the original ANDROID screen. It displays the
controller’s details and user preferences.
The user can choose communication options to be used, depending on your hardware
configuration: NONE, ETHERNET, WI-FI or MODEM by activating appropriate circles on the
screen.
Picture 6. SYSTEM Screen

13
The left-side Menu has the following icon boxes: ADVANCED, SAVE, IMPORT/EXPORT,
RETURN. There are a further two icon boxes on the bottom right hand corner of the SYSTEM
SCREEN: RESTORE DEFAULTS and REBOOT.
ADVANCED icon is used for setting Date and Time, Language and Wi-Fi preferences. Date and
Time should only be adjusted if the controller is not connected to the server. Otherwise Date and
Time settings should be made by changing the time zone of the controller via the webpage. The
controller may need to reconnect to the server for the time zone change to take effect. If the date
and time is changed through advanced settings, the screen lock may be automatically activated
and "Exit" will have to be pressed to resume normal operation.
SAVE icon is used to save preferences after editing.
IMPORT/EXPORT icon is used for downloading data and settings from the controller to USB
drive or for uploading previously exported settings from a USB drive to the controller.
RESTORE DEFAULT icon is used for restoring all settings and preferences to factory settings.
REBOOT icon is used for restarting the controller without unplugging it from the 240 VAC power
supply.
The SYSTEM SCREEN displays an option for a Screen Lock Password. If the checkbox next to it
is ticked, a new checkbox SET PASSWORD will appear together with a Read Only Login
checkbox. When this option is checked the controller screen can be unlocked in Read Only mode
by pressing SKIP on the pop-up screen. This will give users access to the controller without the
ability to change settings. Read Only users may calibrate the controller. If this option is not
ticked, the user can unlock the controller ONLY by using the password.
To set up a password press SET PASSWORD. The pop-up screen will appear (Picture 7). Input
4 digits and repeat to confirm. To clear, press CLR button on the pop-up screen. If user does not
wish to proceed, press CANCEL. If this is the case, the pop-up screen will disappear and the
Screen Lock Password checkbox on the SYSTEM SCREEN will remain un-ticked. The same will
occur if the user does not enter a matching 4 digit number when creating passwords.
Picture 7. SET PASSWORD Screen

14
Advanced Setting
When pressing the ADVANCED icon on the SYSTEM screen, an ADVANCED screen will appear
(Picture 8). This screen has standard ANDROID options for setting Date and Time, Language
and communication preferences. These preferences are to be set in accordance with standard
procedures for ANDROID operating systems. Press EXIT on the top right hand side of the
screen, when all preferences have been set.
Picture 8. ADVANCED Screen.
Importing/Exporting Settings and Exporting Data
When pressing IMPORT/EXPORT on the SYSTEM screen, the pop-up screen
IMPORT/EXPORT will appear (Picture 9). Before Exporting/Importing, secure the front panel with
one hand and insert the USB drive into one of the USB drive connectors on the Motherboard
(refer to item 3 and 4 of the Motherboard circuitry diagram).
Note: It is recommended to use a USB cable extension to access the USB port from the
glands on the controller to provide easy access.
Picture 9. IMPORT/EXPORT Screen
Once the Import or Export operation is complete, a confirmation message will appear. Press
EJECT USB before Ejecting the USB drive from the USB drive connector on the Motherboard. To
return to SYSTEM screen, press CLOSE.

15
Component settings
General layout:
On the main screen (Picture 5) touch the component which you would like to configure. Most
component screens have a similar structure: the left-side menu, Current value and Output
active/inactive icon, the performance Chart in the middle of screen and Settings values on the
right-hand.
The following icons are situated on the left-side menu: SYSTEM, CALIBRATION, SAVE,
RETURN.
SYSTEM icon is for System Configuration.
CALIBRATION icon allows the option of: QUICK and PRECISE calibration. Choose between
QUICK calibration using a known pre-measured value and PRECISE calibration using
calibration solutions. Follow the instructions on the screen to complete the calibration. It is
recommended to perform PRECISE calibrations on commissioning, every month and when a
new probe is installed.
Press the SAVE icon for saving new settings after editing. A pop-up screen with confirmation of
savings of new settings will appear. New settings will also be saved when pressing RETURN icon
and returning to the MAIN screen.
The performance Chart has historical values on the current date; week or month (Double click on
chart area to load the desired component). Also shown on the graph are indications of dosing
duty values for those periods.
OUTPUT: This allows you to CHOOSE OUTPUT screen (PICTURE 10). Press the chosen output
to use that output instead of the currently assigned one if required.
CAUTION: Use outputs 1 to 4 only as they are wired to the GPO plugs 1 to 4 labelled on the
protection cover inside the controller (Refer to the Picture 1. Protection cover) Outputs 5-8 should
be used only if they are wired according to the purchase order. Outputs 9 to 13 are low power
(can switch up to 50V/0.5A/10W peak) signal relays for use with switching dosing pumps or
similar applications.
Picture 10. Choose Output Screen

16
TDS/Conductivity Configuration
The TDS/Conductivity screen will appear (Picture 11) when TDS component is pressed on the
main screen.
Picture 11. TDS/Conductivity Screen
Setting values include CONTROL MODE, SETPOINT, TDS CF, MAKEUP COND, MODE, DOSE
TYPE, ALARM MODE, ALARM RANGE and OUTPUT. Press each parameter to input a value or
chose pre-determined options.
CONTROL MODE: is provided to use either TDS or Conductivity mode for control.
OUTPUT: Bleed solenoid is wired to output 5 on the power board. Any changes to the
TDS/CONDYCTIVITY output must be made by Aquarius agents, certified electricians or an
authorised service technician.
CALIBRATION: Calibration of TDS sensor is always performed using a pre-measured value. It is
highly recommended to use calibrated tester or certified solution to obtain Conductivity values.
Part Number: AS1413: 1,413 µS/cm conductivity solution
Temperature calibration through Temperature screen is recommended before performing
conductivity calibrations (Picture 12).
Picture 12. Temperature Screen
The Temperature component has no setting values as it is not controlled.

17
ORP Configuration
On the main screen touch the ORP parameter box. The ORP screen will appear (Picture 13).
Picture 13. ORP screen
Setting values include SETPOINT, PUMP DUTY, MODE, ALARM MODE, ALARM RANGE,
LOCKOUT DELAY and OUTPUT. Press each parameter to input a value or chose pre-
determined options.
CALIBRATION: Choose between QUICK and PRECISE calibrations and follow the instructions. A
PRECISE calibration is recommended on commissioning, every month and when a new probe
is installed. (Picture 14)
Picture 14. ORP Calibration Screen
Picture 15. Quick ORP Calibration Screen

18
For PRECISE calibration the following calibration solutions are required:
Part Number: AS4250 - 250 mV
Part Number: AS5475 - 475 mV
Press the SAVE icon for saving new settings after editing. A pop-up screen with confirmation of
savings of new settings will appear. New settings will also be saved when pressing RETURN icon
and returning to the MAIN screen.
The performance Chart has historical values on the current date; week or month (Double click on
chart area to load the desired component). Also shown on the graph are indications of dosing
duty values for those periods.
Setting values include SETPOINT, PUMP DUTY, MODE, ALARM MODE, ALARM RANGE,
LOCKOUT DELAY and OUTPUT. Press each parameter to input a value or chose pre-
determined options. OUTPUT box shows the CHOOSE OUTPUT screen (Picture 16).
Picture 16. Choose Output Screen
Press the chosen output to use that output instead of the currently assigned one if required.
CAUTION: Use outputs 1 to 4 only as they are wired to the GPO plugs 1 to 4 labelled on the
protection cover inside the controller (Refer to the Picture 1. Protection cover) Outputs 5-8 should
be used only if they are wired according to the purchase order. Outputs 9 to 13 are low power
(can switch up to 50V/0.5A/10W peak) signal relays for use with switching dosing pumps or
similar applications.
pH Configuration
On the main screen, touch the pH parameter box. The pH screen will appear (Picture 17).
Picture 17. pH screen

19
CALIBRATION icon allows the option of: QUICK and PRECISE calibration (Picture 18).
Picture 18. pH CALIBRATION Screen
Choose between QUICK calibration using a known pre-measured value or PRECISE
calibration using calibration solutions. Follow the instructions on the screen to complete the
calibration. It is recommended to perform PRECISE calibrations on commissioning, every
month and when a new probe is installed.
Part Number: AS7004 - pH 4.01
Part Number: AS7007 - pH 7.01
Press the SAVE icon for saving new settings after editing. A pop-up screen with confirmation of
savings of new settings will appear. New settings will also be saved when pressing RETURN icon
and returning to the MAIN screen.
The performance Chart has historical values on the current date; week or month (Double click on
chart area to load the desired component). Also shown on the graph are indications of dosing
duty values for those periods.
Setting values include SETPOINT, PUMP DUTY, MODE, DOSE TYPE, ALARM MODE, ALARM
RANGE, LOCKOUT DELAY and OUTPUT. Press each parameter to input a value or chose pre-
determined options. OUTPUT box shows the CHOOSE OUTPUT screen (Picture 19).
Picture 19. Choose Output Screen
Press the chosen output to use that output instead of the currently assigned one if required.
CAUTION: Use outputs 1 to 4 only as they are wired to the GPO plugs 1 to 4 labelled on the
protection cover inside the controller (Refer to the Picture 1. Protection cover) Outputs 5-8 should
be used only if they are wired according to the purchase order. Outputs 9 to 13 are low power
(can switch up to 50V/0.5A/10W peak) signal relays for use with switching dosing pumps or
similar applications.

20
pH B Configuration
This is used to control pH between two limits using Acid and Base. Push NEXT and pHB to
configure this. For more details refer to pH configuration.
Inhibitor Configuration
On the main screen, touch the Inhibitor parameter box. The Inhibitor screen will appear to allow
the user to set inhibitor settings. Setting values include MODE (including Disabled, Bleed,
Continuous, Flow, Water Meter, Corrosion and Flow (not available for all models)), PUMP SIZE,
DOSE RATE and OUTPUT. Press each parameter to input a value or chose pre-determined
options. (Picture 20)
Picture 20. Inhibitor screen
When Water Meter mode is selected, the system asks for PUMP SIZE and PPM (Part Per Million
of inhibitor). (Picture 21)
Picture 21. Inhibitor screen
OUTPUT box allows a different output for Inhibitor to be chosen. Please note CAUTION for ORP
and pH before setting OUTPUT.
Table of contents
Other AQUARIUS Controllers manuals
Popular Controllers manuals by other brands
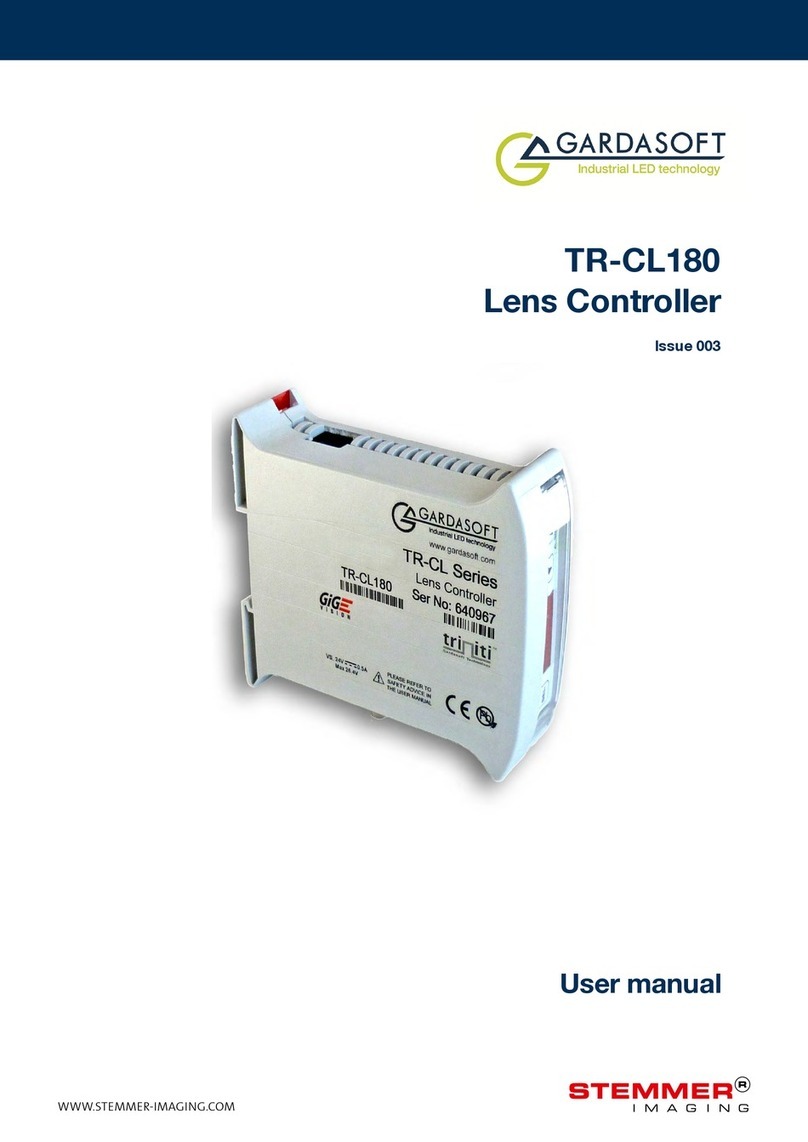
GARDASOFT
GARDASOFT TR-CL Series user manual
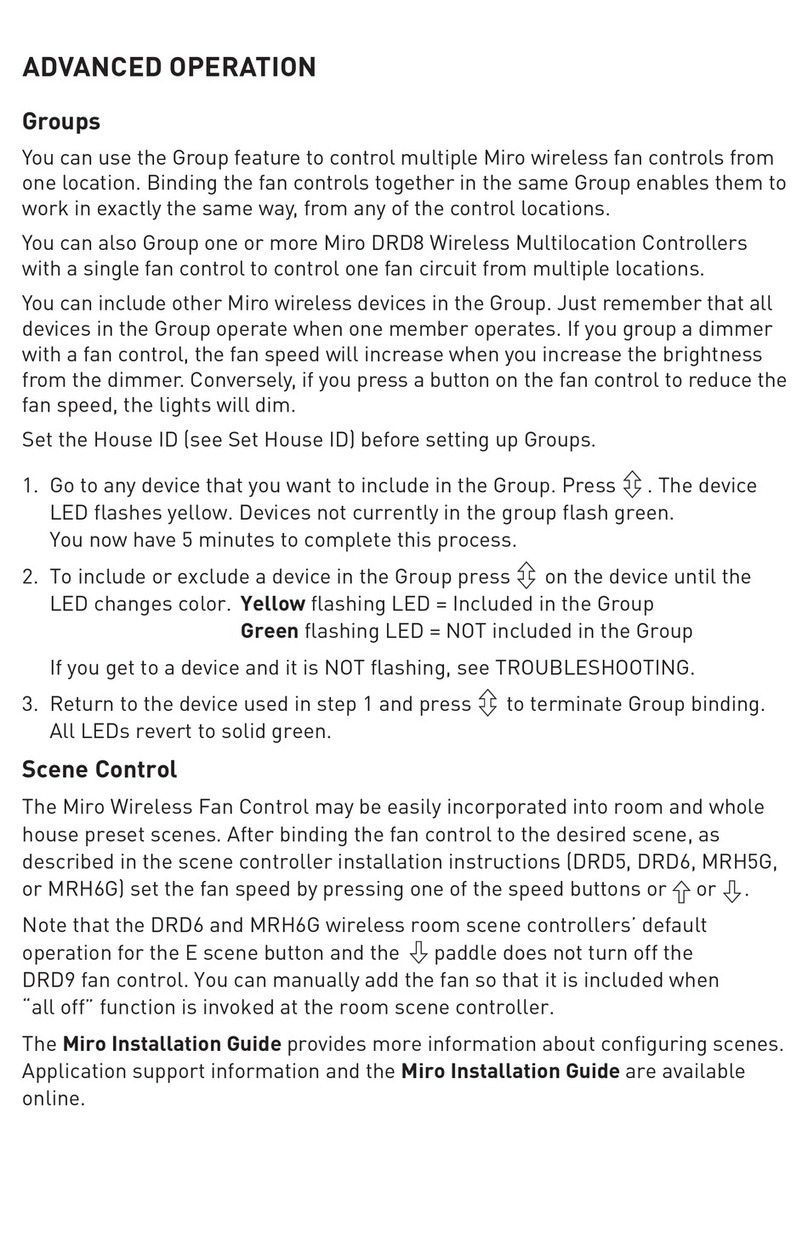
LEGRAND
LEGRAND DRD9 installation guide
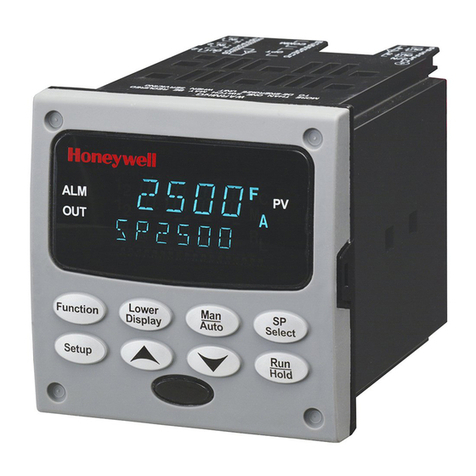
Honeywell
Honeywell UDC2500 product manual
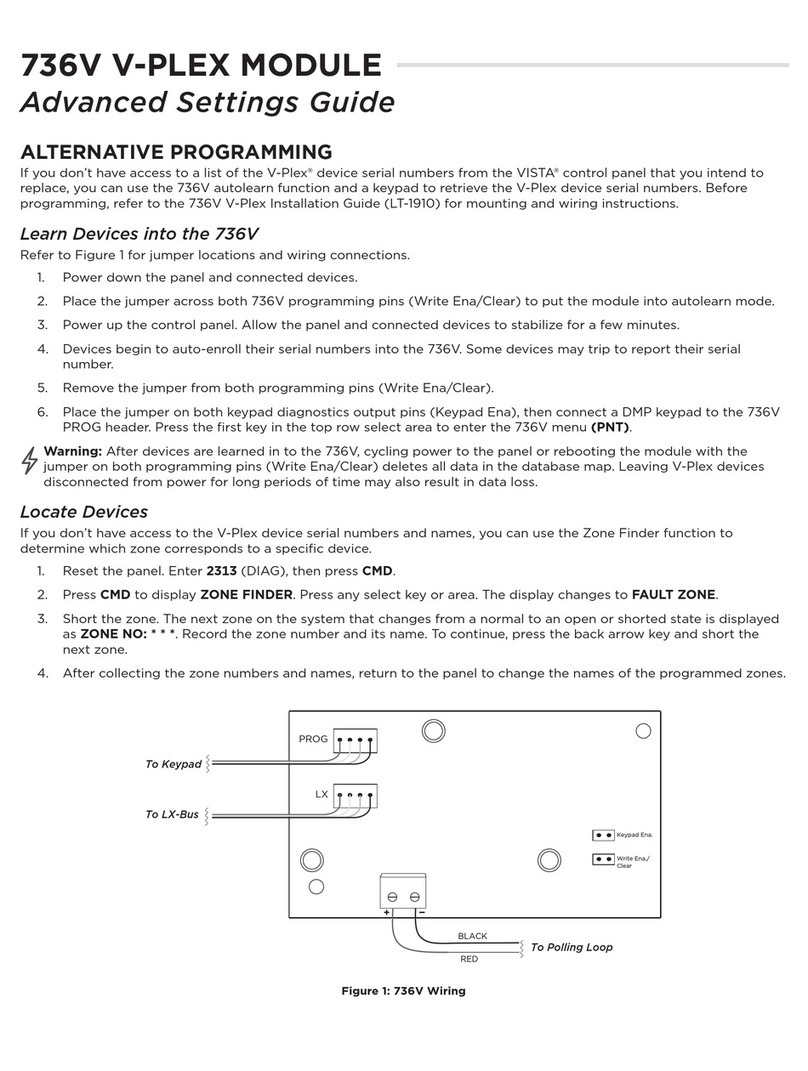
DMP Electronics
DMP Electronics 736V V-PLEX Module Advanced Settings Guide

Mitsubishi Electric
Mitsubishi Electric MELSEC FX Series Programming manual
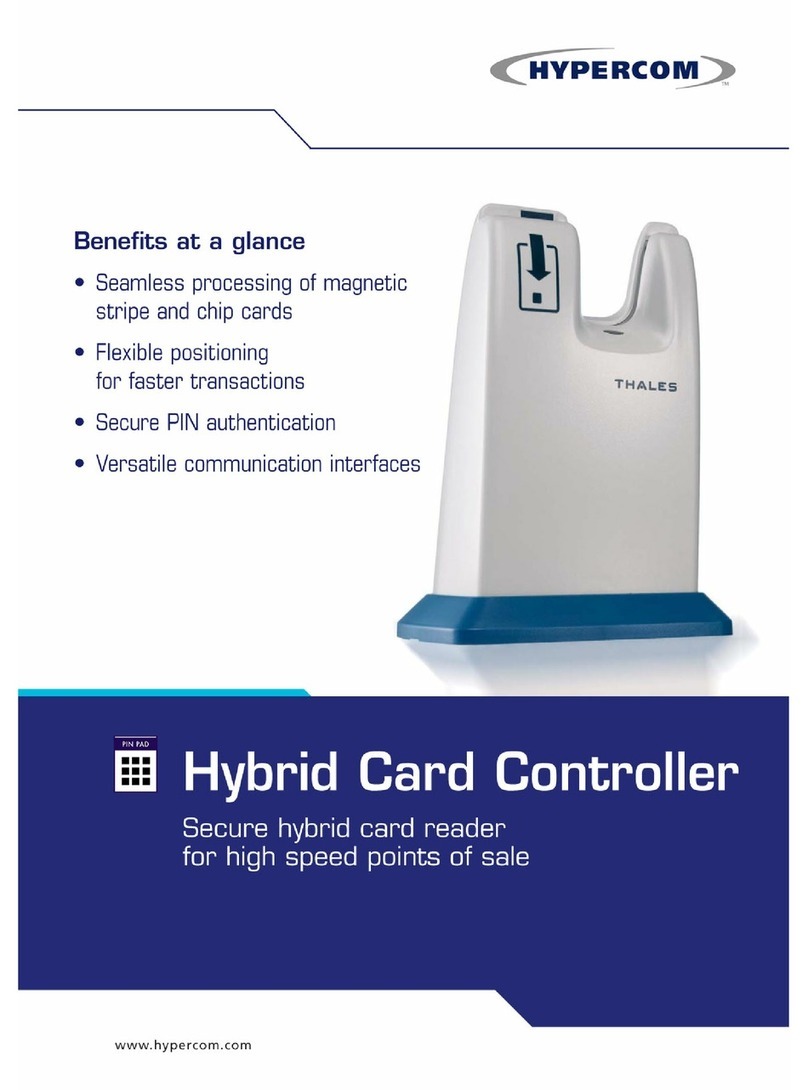
Hypercom
Hypercom Thales Specification sheet