Assured Automation ESOV Manual

INSTALLATION, OPERATION AND
MAINTENANCE MANUAL
263 Cox Street
Roselle, New Jersey 07203 ESOV(EMERGENCY SHUTOFF VALVES)
1800 899-0553 sales@aa-fs.com www.assuredautomation.com
Doc No.IOM 2010 Rev
01
1
FOREWORD
The following instructions are offered as a reference to aid the valve user when installing,
maintaining or operating ESOV (Emergency Shutoff Valves). This document, consisting
of basic information, should be of interest to the layman as well as the experienced
valve user; however, it does not replace the need for an understanding of the
particular application, and is not intended to be a complete instruction for the
inexperienced valve user.
1. RECEIVING & HANDLING
A. Upon receipt of valves, they should be inspected for shipping damage. The areas
to inspect are the pressure retaining shell, valve ends, and valve operating
mechanisms such as handwheel, actuator, stem, etc.
B. If valves show no sign of shipping damage, they should be stored in a sheltered
area to protect them from weather, dirt and damage. Materials attached to protect
valves during shipment should not be removed until time of installation in the line.
C. Each valve should behandled only with apparatus that will safely support the valve
assembly weight. Slings should never be placed around the handwheel, stem or
gland adjustment parts. Protect valve ends by leaving end protectors in place until
their removal is necessary. Valves are shipped in the open or closed position,
depending on the valve type, to protect seating surfaces and should be left in these
positions, if possible, until completion of installation. Check valves will be shipped
with material blocking the disc from swinging during transit.
2. VALVE TRANSPORTATION / STORAGE
A. Check the packaging of valve before transportation according to standard. If the
packaging is damaged, repair it so that the valve can be safely stored and
transported.
B. The paint, the nameplate and the sealing face of flange shall be protected during
transportation. No part of the valve can be dragged on the ground, and the valve
must be adequately protected from abrasion and impact during transport.
C. The valve shall be stored at a safe location to protect against rain and dust if it will
not be installed immediately. Valve shall be stored in ventilated and dry storehouse
for protection. It is not permitted to store the valve outdoors. Valve end flanges
shall be covered.
D. If the valve is electrically triggered, care shall be taken to protect the electrical
components from moisture.
E. Check and clean the valve if the it has been stored over six months, and pressure
test before using the valve if the valve has been stored over twelve months.

2
3. PREPARATION FOR INSTALLATION
A. Prior to installing the valve, clean out any dirt or foreign matter from inside the
piping system. Wherever possible, the line should be blown out with clean
compressed air or flushed out with water to remove any dirt and grit. The valve
should be cleaned in a similar manner.
B. Check for adequate clearance around the valve to ensure that it may be operated
properly and that enough free space is available for maintenance of the valve.
4. INSTALLATION
Precautions: The valve body is a rugged structure, but is not intended to be a
means of aligning improperly fitted pipe. Care must be taken to ensure that any
stresses caused by improper pipe alignment are relieved elsewhere in the piping
system. Piping should be supported by hangers placed on either side of the valve
and large heavy valves should be independently supported.
A. The following general rules should be followed when installing the valve in the pipe
line:
1. Keep pipe ends free of dirt, spatter and grit.
2. Install the valve with flow in the proper direction with regard to valve internals
and flow indicators on the valve body.
3. Handle valve only with apparatus that will adequately support it, using a safe
and proper technique.
4. Install the valve using good piping practices as governed by the applicable
code or specification.
5. ESOVsare usually shipped with disc blocked to prevent damage in shipping.
Remove blocking before installation in the line.
6. Flanged End Valves
a. Check and align pipe flanges before valve installation.
b. Use proper type and size gaskets.
c. Clean debris, dirt and other particles off the surface of the flanges.
d. Do not attempt to fit two flanges that are not alike together. Plain face with
plain face or raised face with raised face is the proper procedure.
e. Do NOT TIGHTEN BOLTS IN ROTATION: they must be tightened in a
crossover or star pattern to load the bolts evenly.
7. Butt-Weld End Valves
a. Valve, pipe and weld rod must all be of materials that are mutually
compatible.
INSTALLATION, OPERATION AND
MAINTENANCE MANUAL
263 Cox Street
Roselle, New Jersey 07203 ESOV(EMERGENCY SHUTOFF VALVES)
1800 899-0553 sales@aa-fs.com www.assuredautomation.com Doc No.IOM 2010 Rev
01

3
b. Make certain valve is in the open position before applying heat. Check
valves may be in the closed position.
c. Welding should be performed by a qualified welder using the correct
welding equipment and following an acceptable procedure.
d. After completion of the weld, it should be stress relieved if required by the
welding procedure and subjected to a pressure test to ensure a sound
weld.
5. POST INSTALLATION
A. After installation of the valve, the line should be flushed or blown out to remove dirt
and foreign objects.
B. Check for tightness of body/bonnet joint.
C. Pressure test the joint to prove quality of flange bolting, welding, etc.
Note: Use of caustics or other chemical agents to flush pipe and valve may
require the removal of the valve packing and gasket based on compatibility
of flushing agent, gasket and packing material.
6. MAINTENANCE & TROUBLE SHOOTING
Valves do not need much attention, but to assure the best operating life and a lower
incidence of maintenance, a program for periodic inspection should be established.
Items to check on a periodic basis are:
A. Glands should be kept tight to prevent leakage. Avoid over-tightening stuffing nuts
or stuffing box packing. This excessively compresses the packing, which
considerably shortens its life and increases operating torque. The gland should
be only as tight as is necessary to seal.
B. Observe valve for leakage taking special note of the body/bonnet joint area, the
end connections and the pressure retaining shell. If leakage at the body/bonnet
joint is evident, check tightness of bolts.
If leakage is at the end connections, check the tightness of the flange bolts in a
flanged valve or the weld in a welded valve.
After determination of joint tightness and leakage is still evident, the joint must be
disassembled and the gasket replaced and/or sealing surfaces repaired.
C. Ensure integrity and cleanliness of fusible link and exposed hinge pins as well as
ensuring that the spring is unobstructed and correctly operating.
Note: Use of a tacky lubricant can pick up abrasive particles. Dry film lubricants
are preferred.
INSTALLATION, OPERATION AND
MAINTENANCE MANUAL
263 Cox Street
Roselle, New Jersey 07203 ESOV(EMERGENCY SHUTOFF VALVES)
1800 899-0553 sales@aa-fs.com www.assuredautomation.com Doc No.IOM 2010 Rev
01

4
D. Open and close valve to check for possible obstruction to travel.
E. Check tightness of packing gland on the hinge pin.
7. REPAIRS
The following general instructions are offered to make limited repairs to the valve.
For major repairs, contact an authorized WILLIAM E. WILLIAMS VALVE
CORPORATION Distributer for special instructions. Always give the
information shown on the identification plate affixed to the valve.
A. When holding a valve in a vise to work on it, always put the valve ends against the
vise jaws. Never hold the valve with the vise jaws pressing against the valve body
since this will cause distortion.
B. Replacing Bonnet Gasket –
1. Isolate and de-pressurize valve prior to attempting to disassemble valve.
2. Mark the body and bonnet flanges so they may be mated in the same position
when reassembled.
3. Valves having large or heavy top works will require the use of a hoist or crane
to support and lift the top works away from the valve body.
4. Loosen the bonnet joint and lift the bonnet and top works away from the body
in a direct straight line.
5. Reassemble in reverse order of above instructions.
6. Prior to re-pressurizing the valve, recheck the tightness of the body/bonnet
joint.
C. No periodic maintenance is necessary besides routine inspections. If gasket leaks
are detected, correct using the following procedure:
1. Disassemble all cover bolts and nuts.
2. Check that the hinge, nut, and pin are in good condition and firmly connected.
Replace damaged parts as necessary.
3. Lift and remove the disc-hinge assembly. Movement should be free and not
hindered by any malfunction of the hinge pin. Where disc travel is not
sufficiently smooth, remove plugs or blind flanges and then remove hinge pin.
Check surface for seizure marks. If marks are less than 0.8 mm (1/32”); re-
machine hinge pin and re-assemble, if marks are greater than 0.8 mm (1/32”)
a new hinge pin is necessary. When reassembling hinge pin, it is
recommended that the disc be removed by loosening nut.
INSTALLATION, OPERATION AND
MAINTENANCE MANUAL
263 Cox Street
Roselle, New Jersey 07203 ESOV(EMERGENCY SHUTOFF VALVES)
1800 899-0553 sales@aa-fs.com www.assuredautomation.com Doc No.IOM 2010 Rev
01

5
D. When leakage is due to deterioration of seal surfaces caused by corrosion or
foreign substances, it must be determined whether the disc or seat seal are the
cause.
1. Deterioration of disc surfaces - Disassemble disc by removing nut and
washer. Repair surface by grinding and lapping using fine grain abrasive
paste.
2. Deterioration of seat seal surfaces - When seal surfaces are damaged and
defects are confined to a small are but are not deeper than 0.8 mm (1/32”),
the seal surface can be repaired. The recommended method is to use a cast
iron strap with an outside diameter matching the valve’s raceway. Then
using a fine grain abrasive paste between the strap and raceway, it is rotated
on the seat to restore original tightness. When defects are deeper than 0.8
mm (1/32”) and found on the entire seal surface, a new seat is required. To
replace the seat, use preferably a pneumatic tool with a shape to match the
dimensions of the valve seat. It is recommended that an anti-seizing
compound be used when installing the replacement seat to make threading it
in to the body easier
CAUTION: Always be sure that the valve is de-pressurized and isolated prior to
performing any maintenance work.
8. TOOLS & EQUIPMENT
Standard wrenches and tools are generally suitable for servicing
Valves. They are:
A. One set box, open end or socket wrenches.
B. One set Allen-type hex key wrenches.
C. Combination oilstone, coarse and fine grit, to polish disc and seat ring faces.
D. Hammer and punches to drive out pins.
E. Hoist to lift large or heavy items.
INSTALLATION, OPERATION AND
MAINTENANCE MANUAL
263 Cox Street
Roselle, New Jersey 07203 ESOV(EMERGENCY SHUTOFF VALVES)
1800 899-0553 sales@aa-fs.com www.assuredautomation.com Doc No.IOM 2010 Rev
01
Table of contents
Other Assured Automation Control Unit manuals
Popular Control Unit manuals by other brands
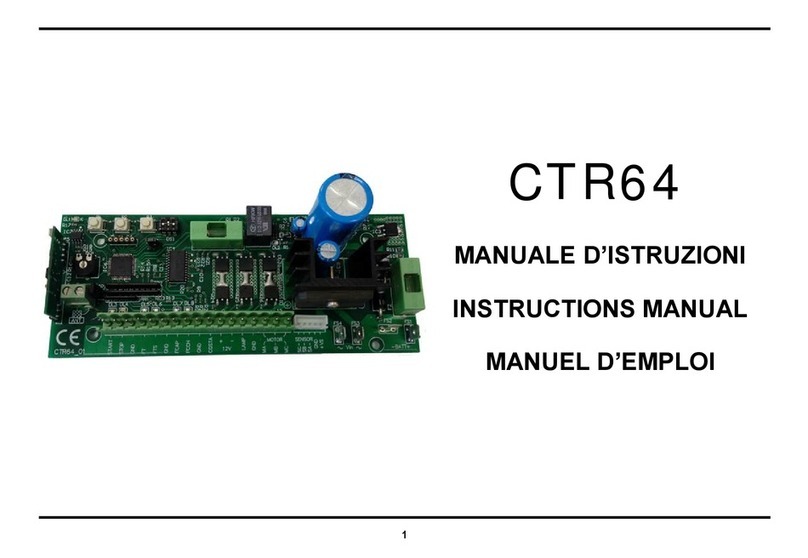
Leb Electronics
Leb Electronics CTR64 instruction manual
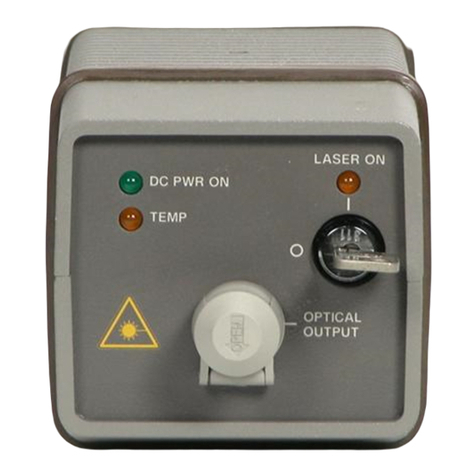
Agilent Technologies
Agilent Technologies 83400 Series user guide
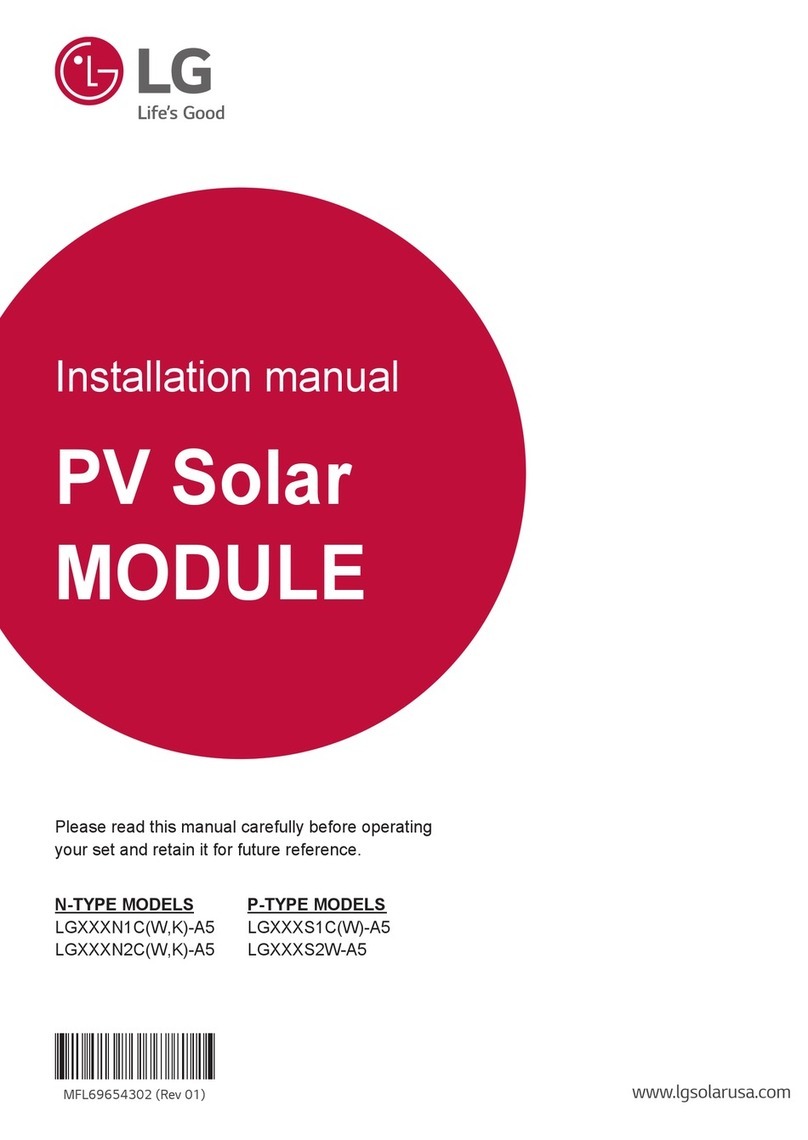
LG
LG N1C-A5 Series installation manual
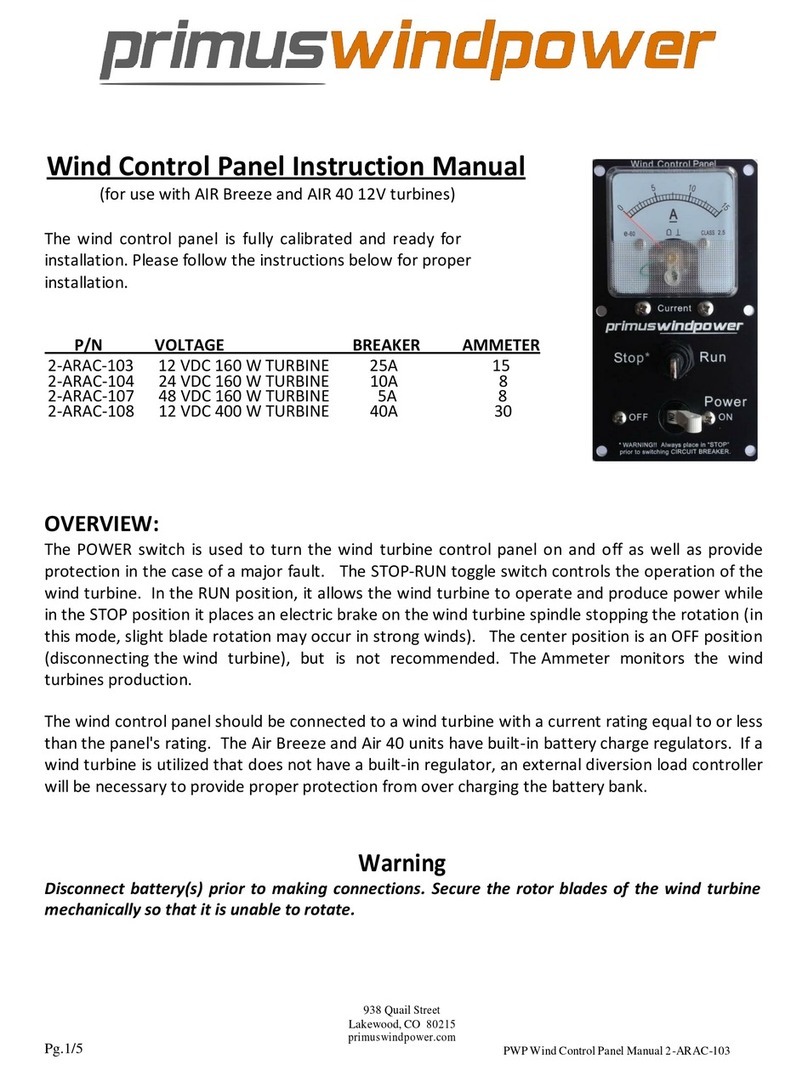
Primus Wind Power
Primus Wind Power 2-ARAC-103 instruction manual
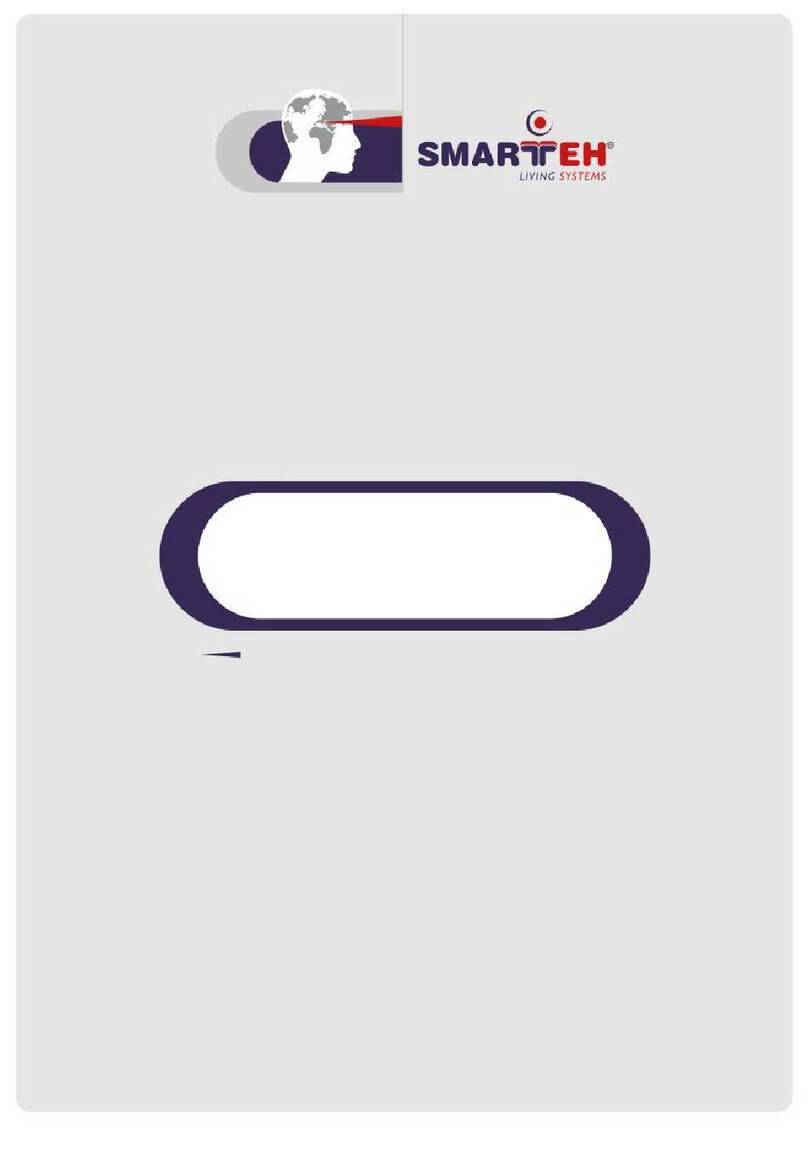
Smarteh
Smarteh LPC-2.CX1 user manual
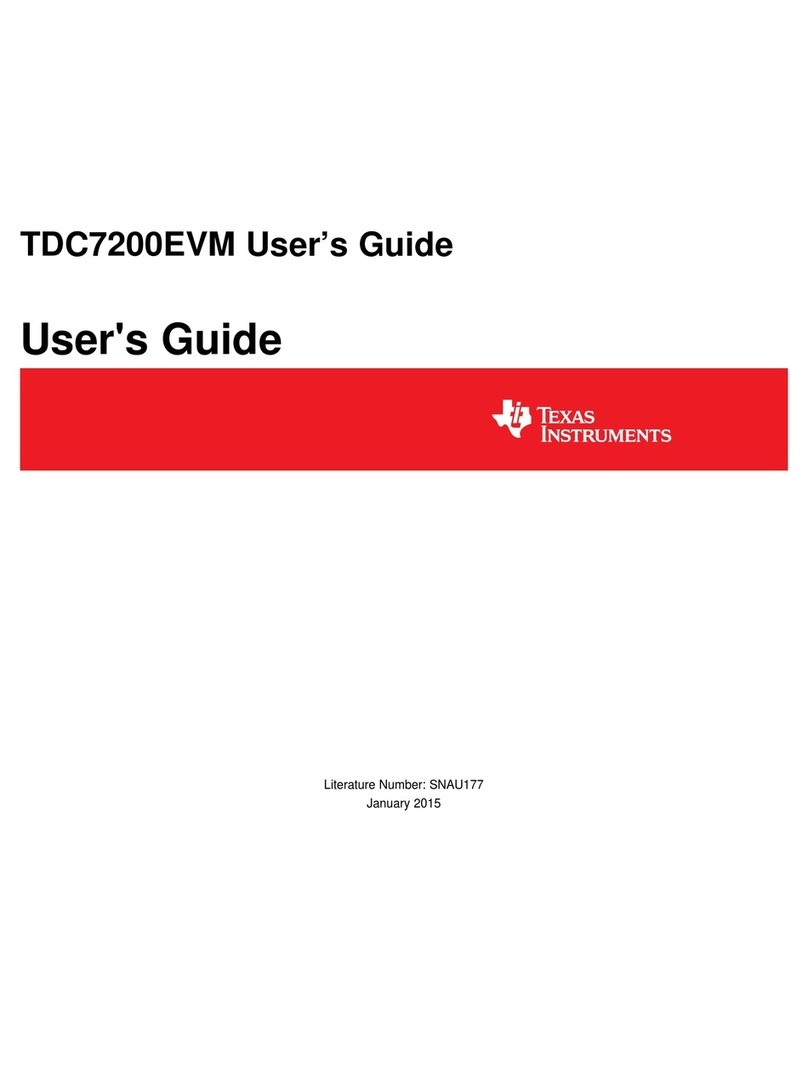
Texas Instruments
Texas Instruments TDC7200EVM user guide