PERSTA DVA 200 BZ User manual

High pressure globe valve
DVA and DVR
Operating instructions
Read the instructions prior to performing any task!

Dok.-Nr. 6404.DE.STD.03.2013, 2, en_GB
Translation of the original operating instructions
© Stahl-Armaturen PERSTA GmbH 2013
Stahl-Armaturen PERSTA GmbH
Mülheimer Str. 18
59581 Warstein-Belecke, Germany
Telephone: +49 2902 762-02
Fax: +49 2902 767-03
Email: [email protected]
Internet: www.persta.com
20.05.2021High pressure globe valve DVA and DVR2

These instructions enable the safe and efficient handling of the
high pressure valve.
The manual is a component of the product and must be kept in the
vicinity of the high pressure valve where it is available to personnel
at all times.
The personnel must have carefully read and understood these
instructions before starting any work. The basic prerequisite for
safe work is compliance with all the specified safety notices and
instructions.
In addition, the local occupational safety regulations and general
safety regulations must be complied with for the high pressure
valve’s area of use.
The illustrations in this manual are provided as examples only and
may deviate from the actual version.
Although the size and pressure ratings of the valve
types vary, the information in these instructions
applies generally to all valves, provided nothing to
the contrary is specified.
This manual applies to the following versions of the high pressure
globe valves DVA and DVR:
Designation Series Nominal diameter (DN)
[mm]
Pressure rate Class*
DVA 200 BZ
202 BZ
204 BZ
80–250 PD 25 £1500
DVA 200 BZ
202 BZ
204 BZ
65–200 PD 40 £2500
DVR 210 KZ
212 KZ
214 KZ
80–250 PD 25 £1500
DVR 210 KZ
212 KZ
214 KZ
65–200 PD 40 £2500
* Assignment number in the pipe construction
Information about the operating
manual
Scope of the document
Supplemental directives
20.05.2021 High pressure globe valve DVA and DVR 3

nIgnition hazard assessment GA004
nConnection diagram provided
nRisk analysis according to Pressure Equipment Directive
nRisk analysis according to Machinery Directive
nActuator instructions
nTechnical data sheet
nBolt tightening torques according to the website:
www.persta.com
nAs well as the other documents included in the delivery
Mülheimer Str. 18
59581 Warstein
Telephone: +49 2902 762-02
Fax: +49 2902 767-03
E-mail: [email protected]
Revision number Change/Supplemented informa-
tion
Date
1 Updates to chapter
“
Intended
use”.
05/05/2021
Other applicable documents
Customer Service - Stahl-Arma-
turen PERSTA GmbH
Revision overview
Supplemental directives
20.05.2021High pressure globe valve DVA and DVR4

Table of contents
1 Overview.............................................................................. 7
2 Safety................................................................................... 9
2.1 Symbols in this manual................................................. 9
2.2 Intended use............................................................... 11
2.3 Safety signs................................................................ 12
2.4 Safety devices............................................................ 13
2.5 Residual risks............................................................. 14
2.5.1 Basic dangers at the workplace............................... 14
2.5.2 Electric shock hazard............................................... 15
2.5.3 Danger due to hydraulics......................................... 15
2.5.4 Hazards associated with the pneumatic system...... 16
2.5.5 Mechanical hazards................................................. 16
2.5.6 Thermal dangers...................................................... 17
2.5.7 Dangers due to hazardous substances and oper-
ating materials......................................................... 17
2.6 Behaviour in the event of an emergency.................... 20
2.7 Responsibility of the operating company.................... 20
2.8 Personnel requirements.............................................. 21
2.9 Personal protective equipment................................... 24
2.10 Spare parts............................................................... 25
2.11 Environmental protection.......................................... 26
3 Functional description..................................................... 27
3.1 Mode of operation of the high pressure globe valve... 27
3.2 Seal to the outside...................................................... 28
3.3 Versions of the high pressure globe valve.................. 29
3.3.1 Shut-off element variants......................................... 29
3.3.2 Actuator variants...................................................... 30
3.3.3 Body shape.............................................................. 32
3.3.4 Display elements..................................................... 32
3.3.5 Connections............................................................. 32
4 Transport and storage...................................................... 35
4.1 Safety notices for transport and storage..................... 35
4.2 Transport of packages................................................ 36
4.3 Storage of the valve.................................................... 37
4.4 Storage of spare parts................................................ 37
5 Installation......................................................................... 39
5.1 Safety notices for installation...................................... 39
5.2 Before the installation................................................. 41
5.3 Installing the valve...................................................... 41
5.4 For electric actuators, connect the power supply....... 42
5.5 For a hydraulic actuator, connecting the hydraulic
system........................................................................ 43
Table of contents
20.05.2021 High pressure globe valve DVA and DVR 5

5.6 For a pneumatic actuator, connecting the pneumatic
system........................................................................ 43
5.7 After the installation.................................................... 44
5.7.1 Pickling the valve..................................................... 45
5.7.2 Painting the valve.................................................... 45
5.7.3 Executing the system pressure test and leak test... 45
5.7.4 Applying thermal insulation...................................... 46
6 Commissioning................................................................. 47
6.1 Safety notices for commissioning............................... 47
6.2 Prior to commissioning............................................... 50
6.3 Executing the commissioning process........................ 51
7 Operation........................................................................... 53
7.1 Safety instructions for operation................................. 53
7.2 Operating the valve..................................................... 55
7.2.1 Valve with manual actuator (handwheel)................. 55
7.2.2 Valve with electric actuator...................................... 55
7.2.3 Valve with hydraulic or pneumatic actuator ............ 56
7.3 Operating the valve in an emergency......................... 57
7.3.1 Valve with manual actuator (handwheel)................. 57
7.3.2 Valve with electric actuator...................................... 58
7.3.3 Valve with hydraulic or pneumatic actuator............. 58
8 Maintenance...................................................................... 59
8.1 Safety instructions for maintenance............................ 59
8.2 Maintenance schedule................................................ 65
8.3 Maintenance tasks...................................................... 66
8.3.1 Visually checking the valve...................................... 66
8.3.2 Lubricating moving parts (stem thread)................... 66
8.3.3 Replacing the gland packing.................................... 68
8.3.4 Replacing the gasket of the pressure sealing
bonnet...................................................................... 75
8.3.5 Dismounting and checking the stem........................ 80
8.4 After maintenance....................................................... 81
9 Faults and fault correction............................................... 83
9.1 Safety notices for fault correction............................... 83
9.2 Fault table................................................................... 86
10 Dismantling, disposal....................................................... 89
10.1 Safety notice for dismantling and disposal............... 89
10.2 Dismantling............................................................... 92
10.3 Disposal.................................................................... 93
11 Index................................................................................... 95
Table of contents
20.05.2021High pressure globe valve DVA and DVR6

1 Overview
Fig. 1: High pressure globe valve (shown: model DVA)
1 Actuator (in the example: handwheel)
2 Stem
3 Anti-twist device
4 Bonnet
5 Gland follower flange
6 Gland packing
7 Cover
8 Shut-off element (shown here: throttling valve
cone)
9 Body
The valve designated as high pressure globe valve is designed for
installation in pipes.
The shut-off element is
nFor the DVA a throttling valve cone,
nFor the DVR a regulating cone.
In the closed position, the shut-off element (Fig. 1/8) prevents the
pipeline medium from flowing through the valve.
If the high pressure globe valve DVR is used for regulation, the
flow of the pipeline medium is influenced by the position of the reg-
ulating cone.
The shut-off element is driven in or out via the stem (Fig. 1/2).
The body (Fig. 1/9) of the valve is flanged or welded in the pipe-
work, depending on the version.
Brief description
Overview
20.05.2021 High pressure globe valve DVA and DVR 7

The stem is moved differently depending on the version:
nmanually via handwheel
nelectrically
nhydraulically
npneumatically
Depending on the version of the high pressure globe valve, it can
be used for water, steam, oil, and other non-aggressive media.
The following tools are required for the tasks described in the oper-
ating instructions:
Forklift
Forklift with sufficient load-bearing capacity for transport of valves.
Hoist
Hoist with sufficient load-bearing capacity for transporting valves
and components.
Hook wrench
Hand tool for activating the threaded bush or mounted electric
actuator.
Knock-out tool
Pin-like tool for driving the tension pin out of the stem.
Packing extractor
Tool for removing gland packing elements.
Pin puncher
Mandrel-like tool for punching out the segment rings.
Sling gear
Functional and approved gear for attaching valves and compo-
nents on the hoist.
Actuator variants
Media
Tools
Overview
20.05.2021High pressure globe valve DVA and DVR8

2 Safety
2.1 Symbols in this manual
Safety instructions are indicated by symbols in this manual. The
safety instructions are introduced by signal words that indicate the
scope of the hazard.
DANGER!
This combination of symbol and signal word indi-
cates a hazardous situation that, if not avoided, will
result in death or serious injury.
WARNING!
This combination of symbol and signal word indi-
cates a potentially hazardous situation that, if not
avoided, may result in death or serious injury.
CAUTION!
This combination of symbol and signal word indi-
cates a potentially hazardous situation that, if not
avoided, may result in minor or moderate injury.
NOTICE!
This combination of symbol and signal word indi-
cates a potentially hazardous situation that, if not
avoided, may result in damage to property.
ENVIRONMENT!
This combination of symbol and signal word indi-
cates potential hazards for the environment.
Safety instructions may refer to specific, individual instructions.
Such safety instructions are integrated into the specific instruction,
so that the flow of reading is not interrupted during performance of
the task. The signal words described above are used.
Safety instructions
Safety instructions in specific
instructions
Safety
Symbols in this manual
20.05.2021 High pressure globe valve DVA and DVR 9

Example:
1. Loosen the bolt.
2.
CAUTION!
Risk of getting trapped by the cover!
Close the cover carefully.
3. Tighten the bolt.
The following symbols are used in the safety instructions to indi-
cate special hazards:
Warning signs Type of danger
Warning – high-voltage.
Warning – danger zone.
This symbol indicates useful tips and recommen-
dations as well as information on efficient and
trouble-free operation.
The following symbols are used throughout these instructions to
highlight specific instructions, results, lists, references and other
elements:
Symbol Explanation
Step-by-step instructions
ðResults of an action
References to sections of these operating
instructions and other applicable docu-
ments
Lists without a defined sequence
Special safety instructions
Tips and recommendations
Additional symbols
Safety
Symbols in this manual
20.05.2021High pressure globe valve DVA and DVR10

2.2 Intended use
High pressure globe valves of the specified DVA and DVR series
are designed for installation in pipes under the following condi-
tions:
nValve with throttling valve cone: Normal operation of the valve
as open/close valve. Brief operation of the valve as throttling
valve with increased probability of wear.
nValve with regulating cone: Operation of the valve for regu-
lating the flow, up to completely open/closed.
nOperation of the valve with pressure via the shut-off element.
nInstallation in horizontal or vertical pipes.
nMaximum number of 1000 load cycles between a depressur-
ized state and the maximum permissible pressure PS.
nAny number of load cycles at pressure fluctuations of up to
10 % of the maximum permissible pressure PS.
nOperation of the valve with liquid or gaseous media, without
particular corrosive, chemical or abrasive impact.
nTemperature change speeds of maximum 6 K/min (6°C/min).
nGenerally used flow rates depending on the type of medium
and the application for which the valve is used.
nOperation of the valve without additional external influences,
such as pipe forces, vibrations, wind loads, earthquakes, cor-
rosive environments, fires, traffic loads, decomposition pres-
sures of unstable fluids.
nThe valve must only be operated within the limits specified on
the type plate (
Ä
“Rating plate” on page 12).
nIf the valve is operated in the creep range, the valve is
designed for a maximum operating time of 100,000 h. The
valve must be replaced afterwards.
nNo temperature increases were considered. In case of use in
the hot vapour area, temperature increases must be consid-
ered according to the regulations of the operating company.
nThe test pressure for a recurring test must not exceed the
maximum permitted pressure PS multiplied by 1.3.
nThe valve may only be operated if internal pressure loading is
predominantly dormant. Additional loads (e.g. stationary
thermal stress, unsteady pressure and temperature loads in
case of alternating loads or pipe loads) were not considered.
Intended use includes compliance with all the information con-
tained in this manual.
Any use that deviates from the intended use or any other form of
use constitutes misuse.
Safety
Intended use
20.05.2021 High pressure globe valve DVA and DVR 11

WARNING!
Danger in the event of misuse!
Misuse of the valve can cause dangerous situa-
tions.
– Do not use the valve as a throttling valve in
normal operation.
– Connect the pipes so that they are free of ten-
sion.
– Pay attention to the correct installation position
of the valve.
– Do not use valves as an anchor point.
– Never operate valves at temperatures near or
below the freezing point of the pipeline medium.
– Do not exceed the number of permitted load
cycles (
Ä
Chapter 2.2 “Intended use”
on page 11).
2.3 Safety signs
The following symbols and instruction signs are in the work area.
These symbols and instruction signs refer to the immediate vicinity
in which they are affixed.
WARNING!
Danger if signs are illegible!
Over time, stickers and signs can become fouled
or can become illegible in some other manner, so
that dangers are not recognised and necessary
operating instructions cannot be complied with.
This results in a danger of injury.
– Keep all safety, warning, and operating instruc-
tions that are affixed to the device in legible con-
dition.
– Replace damaged signs or stickers immediately.
The rating plate is on the valve. Depending on the version, the fol-
lowing information is on the rating plate:
nConfirmation number
nArticle number
nYear of manufacture
nNominal diameter
nNominal pressure/design data
Misuse
Rating plate
Safety
Safety signs
20.05.2021High pressure globe valve DVA and DVR12

The flow direction is marked on the valve with an arrow (Fig. 2/1).
In the arrow direction, medium flows against the shut-off element
from above (
Ä
Chapter 2.2 “Intended use” on page 11).
The handwheel (Fig. 3/3) shows the opening (Fig. 3/1) and closing
directions (Fig. 3/2).
nOpen
nShut
Additional markings (e.g. max. temperature limits) are available on
customer request.
2.4 Safety devices
The opening process of the valve with electric actuator is ended via
limit switches. After a permanently set distance the actuator
switches off and the valve is opened.
Flow direction arrow
Fig. 2: Flow direction arrow
Opening direction / closing direc-
tion indication for manual actuator
Fig. 3: Opening direction and closing
direction indication
Customer-specific markings
Limit switch
Safety
Safety devices
20.05.2021 High pressure globe valve DVA and DVR 13

With an optional electric actuator, in addition to the limit switch,
torque switches are also mounted. At a permanently set torque, the
actuator shuts down and the valve is closed. This protects the
valve from excessive torque.
The optional electric actuator also has a handwheel (Fig. 4/1). If
the actuator is defective or if the controller fails, the valve can be
operated via the handwheel.
2.5 Residual risks
The valve has been developed and manufactured to the state-of-
the-art and in accordance with generally accepted rules of safety.
Nevertheless residual risks remain that require careful handling.
The residual risks and the resulting behaviours and measures are
listed below.
2.5.1 Basic dangers at the workplace
DANGER!
Life-threatening danger due to failure to
comply with the rules of behaviour specified
for hazardous areas!
Depending on the version the valve can be used in
hazardous areas. There is life-threatening danger
if the rules of behaviour are not complied with
within these areas.
– Ensure that tasks on the valve can be executed
at the installation site.
Torque switch
Emergency actuation of the electric
actuator
Fig. 4: Emergency actuation
Hazardous areas
Safety
Residual risks > Basic dangers at the workplace
20.05.2021High pressure globe valve DVA and DVR14

CAUTION!
Danger of injury due to tripping up!
There is a danger of fall injuries in the area of use
of the valve.
– Install cable and connection lines in such a
manner that there are no trip hazards.
2.5.2 Electric shock hazard
DANGER!
Risk of fatal injury from electric shock!
There is a risk of fatal injury when touching live
components of the actuator. Switched-on electrical
components can execute uncontrolled movements
and can cause serious injuries.
– Prior to starting work, switch off the supply of
electricity and definitively disconnect it.
– Only have an electrician perform tasks on elec-
trical lines and components.
2.5.3 Danger due to hydraulics
WARNING!
Danger of injury due to hydraulic energy!
Hydraulically-powered components of the valve, as
well as the triggering of the overpressure valve can
cause severe injuries.
– Only have specialised personnel perform tasks
on the hydraulic system.
– Prior to starting the tasks on the hydraulic
system ensure that it is completely depressur-
ised. Completely depressurise pressure accu-
mulators.
– Operate the valve in a frost-free environment to
prevent the body from bursting.
– Wear personal protective equipment.
Trip hazard
Electric shock
Fluid under high pressure
Safety
Residual risks > Danger due to hydraulics
20.05.2021 High pressure globe valve DVA and DVR 15

2.5.4 Hazards associated with the pneumatic system
WARNING!
Danger of injury due to pneumatic energy!
Pneumatically-powered components of the valve,
can cause severe injuries.
– Only have pneumatic specialists perform tasks
on the pneumatic equipment.
– Prior to starting the tasks on the pneumatic
equipment ensure that it is completely depres-
surised. Completely depressurise pressure
accumulators.
– Wear personal protective equipment.
2.5.5 Mechanical hazards
WARNING!
Danger of injury due to the heavy weight of the
valve!
The heavy weight of the valve, and of its compo-
nents, can result in severe injuries.
– Transport valves with a suitable hoist or forklift.
– Don not lift valves via the handwheel.
– Do not lift valves via the actuator.
– If possible, lift valves via the bonnet.
– Use approved and functional sling gear.
– Safeguard valves and components from falling
over.
WARNING!
Danger of injury on moving parts!
Danger of injury exists on moving parts (stems/
anti-twist devices).
– When the valve is in operation do not grasp
moving parts.
– Wear personal protective equipment.
Hazards associated with the pneu-
matic system
Heavy weight of the valve
Danger of crushing on stems
Safety
Residual risks > Mechanical hazards
20.05.2021High pressure globe valve DVA and DVR16

2.5.6 Thermal dangers
WARNING!
Danger of injury due to high/low temperatures!
Depending on the insert of the valve or of the pipe,
injuries can occur due to the high or low tempera-
ture of the components.
– When working on components or activating final
control equipment, wear protective equipment:
Protective gloves, protective goggles.
– Prior to performing tasks on these components,
allow them to cool down/warm up to ambient
temperature.
– Have the protective insulation provided by the
operating company attached.
WARNING!
Danger of injury due to pipes shattering at
freezing temperatures!
As a result of pipes shattering at freezing tempera-
tures, severe injuries can be caused by fluid under
high pressure.
– Ensure that the valve is completely empty
before it is taken out of service.
– Never operate valves at temperatures close to,
or below the freezing point of the pumping
medium.
2.5.7 Dangers due to hazardous substances and operating materials
WARNING!
Danger of injury due to pumping medium under
pressure!
In operating status, as well as in decommissioned
status, depending on the version of the valve, inju-
ries can occur due to medium escaping under high
pressure.
– Do not unscrew threaded connections.
– If threaded connections are loose, inform the
operating company and have the pipe section in
question shut-off.
– If threaded connections are loose have the
cause for this clarified and eliminated. If neces-
sary have the manufacturer check the valve.
Thermal dangers
Danger of freezing
Pumping medium
Safety
Residual risks > Dangers due to hazardous substances and operating materials
20.05.2021 High pressure globe valve DVA and DVR 17

WARNING!
Pumping medium is a health hazard!
Contact with the pumping medium can have health
implications.
– Handle pumping medium in accordance with the
instructions in the manufacturer’s safety data
sheet.
– Wear protective equipment: Protective gloves,
safety footwear, protective goggles, protective
work clothing.
– Soak up escaped pumping medium without
delay and dispose of it in an environmentally
responsible manner.
WARNING!
Pickling medium is a health hazard!
Direct contact with the pickling medium used can
have health implications.
– Handle pickling medium in accordance with the
instructions in the manufacturer’s safety data
sheet.
– Wear protective equipment: Protective gloves,
safety footwear, protective goggles, protective
work clothing.
– Soak up escaped pickling medium without delay
and dispose of it in an environmentally respon-
sible manner.
WARNING!
Operating materials are a health hazard!
Contact with operating materials/lubricants can
have health implications.
– Handle operating materials and lubricants in
accordance with the instructions in the manufac-
turer’s safety data sheet.
– Wear personal protective equipment: Protective
gloves, safety footwear, protective goggles, pro-
tective work clothing.
– Soak up escaped operating materials/lubricants
without delay and dispose of them in an envi-
ronmentally responsible manner.
Pickling medium
Lubricating grease
Safety
Residual risks > Dangers due to hazardous substances and operating materials
20.05.2021High pressure globe valve DVA and DVR18

WARNING!
Anticorrosive is a health hazard!
Direct contact with the anticorrosive used can have
health implications.
– Handle anticorrosive in accordance with the
instructions in the manufacturer’s safety data
sheet.
– Wear protective equipment: Protective gloves,
safety footwear, protective goggles, protective
work clothing.
– Soak up escaped anticorrosive without delay
and dispose of it in an environmentally respon-
sible manner.
NOTICE!
Damage of sealing surfaces and slide faces
due to the metallic processing of sealing sur-
faces and slide faces!
The metallic processing of sealing surfaces and
slide faces and valve parts can result in material
damage and malfunctions of the valve.
– Sealing surfaces and slide faces of gaskets
must not be
– scratched with a scraper,
– processed with wire brushes.
– Sealing surfaces and slide faces must be
– pulled off with emery cloth,
– processed with suitable abrasive tools or
– scraped off with plastic tools/wooden tools.
NOTICE!
Material damage due to excessive use as throt-
tling valve!
Excessive use of the valve as throttling valve can
result in malfunction and material damage due to
overstressing of the components.
– Only use the valve briefly as throttling valve.
– In normal operation use the valve as open/close
valve.
– Have the maintenance and replacement inter-
vals shortened by the operating company
depending on the use of the valve.
Anticorrosive
Damage of sealing surfaces and
slide faces
Increased wear
Safety
Residual risks > Dangers due to hazardous substances and operating materials
20.05.2021 High pressure globe valve DVA and DVR 19

2.6 Behaviour in the event of an emergency
See also
Ä
Chapter 7.3 “Operating the valve in an emergency”
on page 57.
1. Shut off the pipe sections affected.
2. Comply with the in-house regulations.
2.7 Responsibility of the operating company
The operating company is the company that operates the valve for
commercial or economic purposes itself or that provides it to a third
party for use, and that, during operation, bears the legal product
responsibility for protection of the user, personnel or third parties.
The valve is used commercially. The operating company of the
valve is therefore subject to the legal occupational health and
safety obligations.
In addition to the safety instructions in this manual, the local occu-
pational health and safety, accident prevention and environmental
protection regulations that apply to the valve’s area of application
must be observed.
In this regard, the following applies in particular:
nThe operating company is responsible for the installation and
operation of the valve in the pipe.
nThe operating company must ensure that any dangerous situa-
tions caused by the operating conditions are avoided by instal-
ling additional safety systems.
nThe operating company must obtain information about the appli-
cable occupational health and safety regulations and, in a
hazard assessment, identify the additional hazards that may
exist at the installation site of the valve due to the specific
working conditions. The operating company must integrate this
information into operating instructions for the operation of the
valve.
nThe operating company must ensure that the operating instruc-
tions it has drawn up comply with the currently applicable legis-
lation throughout the operating period of the valve and, if neces-
sary, adapt the operating instructions.
nThe operating company must clearly define and assign the
responsibilities for installation, operation, fault correction, main-
tenance and cleaning.
nAfter the installation, the operating company must ensure the
proper pickling of the valve.
nThe operating company must draw up an emergency stop con-
cept for the overall system: specifying whether opening or
closing of the valve is necessary in an emergency.
nThe operating company must provide devices that ensure the
safe transition of the valve into a depressurised state.
Operating company
Obligations of the operating com-
pany
Safety
Responsibility of the operating company
20.05.2021High pressure globe valve DVA and DVR20
This manual suits for next models
5
Table of contents
Other PERSTA Control Unit manuals
Popular Control Unit manuals by other brands

UTC Fire and Security
UTC Fire and Security FenwalNET 8000-ML Installation, operation and maintenance manual

Magnescale
Magnescale MG70-PN instruction manual
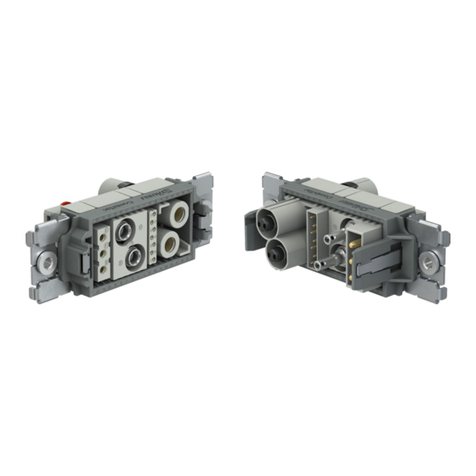
Staubli
Staubli CombiTac direqt Assembly instructions

Emerson
Emerson Fisher GX instruction manual
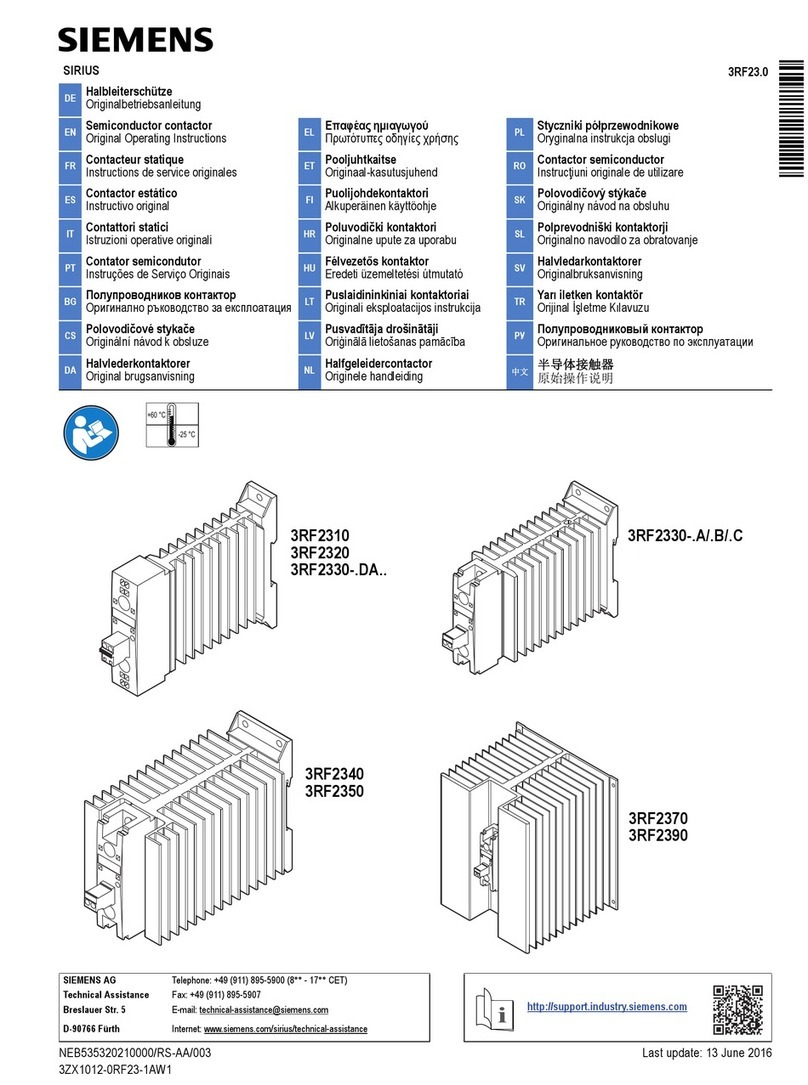
Siemens
Siemens SIRIUS 3RF2330-DA Series Original operating instructions

Waeco
Waeco MagicTouch MT2000 installation manual