ASYS Totech EU SUPER DRY XSDB-1402-53 1416 201 User manual

Operation Manual Touchscreen
Applies to all cabinets of the -24, -54 and -57
series with Touchscreen
(From LOGO software version upward of 1-24)
OPERATING THE DEVICE
All mechanical and electrical connections should be checked for tight fit and tightness prior to
commissioning, as well as to remove any soil.
Insert the plug into a grounded electrical outlet. If the device does not start instantly, it is in the
standby state. Please press the activation icon on the screen.
The initialization program of the cabinet now starts. When the initialization is complete, the display
shows the home screen and the fans start running.

Operation Manual Touchscreen
OPERATING THE DEVICE 1
1. HOME DISPLAY 4
1.1 Regeneration 4
2. ALARM 5
Use [Delete] to delete the complete alarm list. 5
3. TIMER (OPTION) 5
3.1 COUNTDOWN 5
3.2 FLT-RESET 5
4. GRAPH DISPLAY 6
MENU 7
5. SERVICE 7
6. SETTINGS 7
6.1 SETTINGS 1/4 7
6.1.1 SETPOINT HUMIDITY 8
6.1.2 HUMIDITY ALARM LIMIT 8
6.1.2.1 ALARM 8
6.1.3 HUMIDITY ALARM DELAY 8
6.1.4 SETPOINT TEMPERATURE 8
6.1.5 TEMPERATURE DEVIATION 8
6.1.6 TEMPERATURE ALARM DELAY 8
6.1.7 Diagnose 8
6.2 SETTINGS 2/4 9
6.2.1 OFFSET, LOCK, FIRMWARE 9
6.3 SETTINGS 3/4 10
6.3.1 SYSTEM TIME, DATA LOGGER 10
6.4 SETTINGS 4/4 11
MANUAL REGENERATION AND REGENERATION TIMER 11
7. LANGUAGE 11
8. STANDBY 12
9. DATA LOGGING 12
10. CALIBRATION 12
11. NETWORKING CONFIGURATION 13
11.1 CHANGE THE IP ADDRESS OF THE LOGO! BASE MODULE 13

Operation Manual Touchscreen
11.2 CHANGE THE IP ADDRESS OF THE DISPLAY 13
11.3 SELECT THE LOGO! BASE MODULE IP ADDRESS 14
12. Calibration 14
13. Maintenance 14
14. Troubleshooting 15
14.1 For malfunction 15
14.2 Measuring faults 15
14.3 Communication error via Ethernet 15
14.4 Display indicates “BM no resp Press ESC” 15
14.5 No indication on Display 15
14.6 Logic module and extension module checking 15
14.7 Humidity too high 16
14.8 Temperature too low 16
15. Warranty and Liability 17
15.1 Warranty and liability 17
15.5 Guidelines for the RMA procedure of Totech Europe B.V. 18
16. Serial numbers 19
16.1 Cabinet serial numbers 19
16.2 Dry-unit serial numbers
17. CE-declaration 20

Operation Manual Touchscreen
1. HOME DISPLAY
The display shows the relative humidity and temperature inside the cabinet / room in the left window.
In the right-hand window you will find the displayed setpoints with arrows and the remote display at
the bottom, as well as a bar graph for the current measured values in direct comparison.
1.1 Regeneration
When the display is reading Regeneration in yellow in the top left corner, the program has started a
regeneration of the desiccant material inside the drying unit.
The humidity alarm light (optional) signals this state with a flashing green signal. After completion of
the regeneration, the device switches to the drying mode which is signaled by a green continuous
signal. After commissioning, the cabinet can be used immediately, and the full drying capacity is
achieved after 24 hours.

Operation Manual Touchscreen
2. ALARM
If an alarm is triggered, the display background flashes red. Use the [Alarm] key to go to the alarm
display. All alarms with date, time and type are recorded from start to end.
Press [Alarm Acknowledge] to reset the alarm delay. The optical and acoustic alarm signal switches
off. If the alarm is still active, the alarm activates again after the set delay time.
The alarm delay for the door alarm is preprogrammed to 90 seconds and can not be changed.
The alarm indication in the display and the alarm light indication (option) are automatically deleted
after elimination of the alarm cause. Use the arrows to scroll through the alarm messages.
Use [Delete] to delete the complete alarm list.
3. TIMER (OPTION)
3.1 COUNTDOWN
The countdown timer allows to change the humidity and temperature values for a limited time.
Specify the temporary values and settings and press [Next] to enter the timer. Here you can set the
time, start, stop and reset the countdown. When the timer has elapsed, you will automatically return
to the timer screen. The alarm will go off after the timer has finished. The optical and acoustic alarm
can be acknowledged with the [Quit alarm] button.
3.2 FLT-RESET
With the reset function of the floor lifetime of electronic components, you have the possibility to
automatically determine the rest time by means of the component specification.
After entering the Floor Lifetime reset menu by pressing [FLT-Reset] you have to specify some values.
First of all, determine the place of the components in the cabinet. By default there is room to specify
10 different components. Select the place of the component by pressing the number. The column will
get highlighted in white. Select the housing body thickness [thick], IPC-Level [level] and the
conditions under which the components are drying with [Reset conditions]. The display will
automatically calculate the time needed for the component to dry. After entering all the needed
information for the component, make sure the column is still highlighted and press [Set]. The time will
be set under [(time) left]. Press [Start] and the timer for that component will start. After starting the
timer you can leave the timer display with [Home]. The home screen will show “Timer active” to show
that the timer is running. When the timer has finished you will be automatically returned to the
FLT-Reset menu.
(NOTE: During an active timer, you won’t be able to change any [Settings])

Operation Manual Touchscreen
4. GRAPH DISPLAY
With this display, a trend graph for humidity and temperature profile is recorded.
The display shows the relative humidity (blue) and temperature (red) as a trend graph. The dashed
lines indicate the respective alarm limits. The zoom buttons allow you to adjust the displayed time
window.
To scroll to the past, you must stop the current recording with [Stop]. They can then move with the
arrow keys in the time axis. Press the [Start] button to return to the current trend display.
In the right-hand window you will find the displayed setpoints with arrows and the remote display at
the bottom, as well as a bar graph for the current measured values in direct comparison.

Operation Manual Touchscreen
MENU
5. SERVICE
The service function is used to set the control parameters and is used exclusively by the
manufacturer. Access only with service password.
6. SETTINGS
Press the [Settings] key in the menu to enter the password prompt.
Here you have the option to display only the settings (white representation of the values), or by
entering the security code via Enter to set the values (blue representation of the values).
In the delivery state, no password is assigned, so you enter the settings directly with Enter.
6.1 SETTINGS 1/4
On the first page, you can set the setpoints for humidity and temperature.
If you click on the current value, an input window opens. Here you can change the value by entering
a new value, within the value range. Press [Enter] to confirm the value for this setting.

Operation Manual Touchscreen
6.1.1 SETPOINT HUMIDITY
In the "Humidity" setpoint menu, the desired relative humidity is entered as a percentage when the
active drying is stopped. If the setpoint exceeds 15 minutes, the device automatically performs a
regeneration.
If "0" is entered, the continuous operation of the drying unit is activated. The maximum residual
moisture is achieved by maximum energy consumption. If the fixed value of 0.5% RH is exceeded
more than 15 minutes, the device automatically performs a regeneration.
In order to avoid overloading the drying unit, there is a break between two automatic regenerations of
3 hours. This pause can only be skipped by initiating a manual regeneration (see 6.4).
No active humidification is installed in the cabinet. As a result, a longer time can be passed before this
is reached when the change from low humidity to a higher setpoint occurs. By deliberately opening
the door, this process can be accelerated.
6.1.2 HUMIDITY ALARM LIMIT
This is where the humidity alarm threshold is set, when the acoustic and the optional optical alarm are
activated.
6.1.2.1 ALARM
The alarm activates an acoustic signal and turns on the red background light in the text display. The
red flashing light is activated when the optional alarm light is used. The acoustic alarm can be
acknowledged by pressing the [Alarm] button, followed up with [Quit Alarm]. This is then active again
when the alarm is re-activated. The alarm message in the display and the traffic light message are
automatically ended after elimination of the alarm cause.
6.1.3 HUMIDITY ALARM DELAY
To ensure that every short-term increase in the humidity does not trigger an alarm, the alarm delay
for the humidity is set with this value.
6.1.4 SETPOINT TEMPERATURE
The menu items 6.1.4 to 6.1.6 are only visible if an optional heating / cooling system has been
installed. You can select the required temperature for the cabinet in this menu.
If the selected setpoint is below the temperature limit / ambient temperature, the heating remains
inactive. This also applies to an optional cooling system.
6.1.5 TEMPERATURE DEVIATION
The deviation (difference) to the temperature setpoint is defined here, and the acoustic and the
optional optical alarm are activated when the signal is exceeded (see 6.1.2.1).
6.1.6 TEMPERATURE ALARM DELAY
In order to prevent an alarm from being triggered by every short-term drop or increase in
temperature, the alarm delay for the temperature drop out is set with this value.
Please note that heating is deactivated during regeneration. This can lead to a short-term drop
(maximum 20 minutes) of the cut-off temperature.
6.1.7 DIAGNOSE
On the first page is access to the diagnosis of the display. You can also find the status overview of the
LOGO! logic module.

Operation Manual Touchscreen
6.2 SETTINGS 2/4
6.2.1 OFFSET, LOCK, FIRMWARE
Pressing [Next] will bring you to the next page. Here you can calibrate the sensor values by offset and
also assign a password which can be used to protect the setting values.
On this page is the [USB Boot] function. If you have inserted a program update on a USB memory
stick you can carry out the transfer by pressing this button. After pressing, the display reboots and
uses the firmware which is on the USB stick for this startup. This is simultaneously transferred into
the memory of the display and overwrites the last current firmware.

Operation Manual Touchscreen
6.3 SETTINGS 3/4
6.3.1 SYSTEM TIME, DATA LOGGER
Continue to the third setting page by pressing [Next].
The current system time is displayed and you have the option to change it. To do this, activate the
value to be changed under "
Set system time
" and enter the desired value in the input window.
In addition to the setting for the acoustic alarm in the display, you can deactivate the logging function
here as well. (See 9. Data Logging)
The [Offline] button is used to stop the program and you will be taken to the setting functions of the
display itself. Here you can set the IP address and many other functions.
(See 11. Network configuration)

Operation Manual Touchscreen
6.4 SETTINGS 4/4
MANUAL REGENERATION AND REGENERATION TIMER
Continue to the fourth setting page by pressing [Next]. This page contains the regenerations timer.
Here you can define up to three times, in which a regeneration is to be started. Dynamic regeneration
remains active so that additional generations are performed automatically. If this is not desired, the
dynamic regeneration on the service menu has to be deactivated.
With Manual Regeneration, the user can start an immediate regeneration.
This function is only available during the drying phase. The [man.Reg] button initiates a regeneration.
The necessary strength of the regeneration is determined automatically.
7. LANGUAGE
In the menu you will find the Language option. Here you have the possibility to choose your country
language. The following languages are available:
German - English
Other languages are available upon request.

Operation Manual Touchscreen
8. STANDBY
To put the drying cabinet in standby mode, press the [Standby] button via [Menu] and then [Activate
standby].
While the standby mode is activated, the backlighting of the display and the drying unit are
deactivated. The fan of the optional heater can only be stopped by a complete power disconnect.
During regeneration, standby mode is not available.
ATTENTION: Always disconnect the power supply during maintenance!
9. DATA LOGGING
The values for humidity and temperature are logged every minute. In addition, relevant events are
logged as: cabinet opening, alarm releases, alarm acknowledgments, ...)
One file is automatically created per day in the "SAMP02" folder. The file name is named after the
current date in the format: SAmmddy (example: 3.21.2017 SA03217).
The locking works only with a plugged USB storage medium!
The file can either be read directly from the USB stick or downloaded via FTP.
ftp://[IP address of display] in the web browser.
To read out the csv file, Excel program can be used by Windows. The free Totech Viewer offers the
ability to download the data graphically.
10. CALIBRATION
Totech recommends to check the calibration once a year or to recalibrate the system by replacing the
sensor.
To calibrate the sensor, we recommend the following two possibilities:
1. Replacing the sensor by a factory-calibrated sensor. After detaching the screw-fastened retaining
ring, the plug-in sensor can simply be unplugged. The replacement sensor is mounted in reverse
order. Since all settings have been stored in the sensor, its replacement will serve to recalibrate the
dehumidifier's overall measuring. Additional measurement equipment or software is not required. After
replacing the sensor for the new calibrated sensor, the old sensor has to be returned to the factory.
You do not need any further measuring devices or software.
2. Define deviations by means of a calibrated reference dew point meter (minimum accuracy
±0.2%RH or higher), and calibrate the sensor via the software's calibration function. This proceeding
requires data connection to PC and software (for detailed instructions, please refer to the Software
Manual of the manufacturer). (see 6.2.1 Offset, Lock, Firmware).

Operation Manual Touchscreen

Operation Manual Touchscreen
11. NETWORKING CONFIGURATION
ATTENTION: The user can only use the configuration menu for the settings described in this manual.
Any further changes can lead to a malfunction!
The drying cabinet or drying unit is pre-configured from the factory with the following IP settings. To
establish a connection to your network, the address configuration must be adapted accordingly.
Factory default settings:
Component
Address
BM (LOGO! Base module)
10.31.0.xxx
TDE (LOGO! Display)
10.31.0.xxx
Subnet
255.255.255.0
Gateway
10.31.0.1
11.1 CHANGE THE IP ADDRESS OF THE LOGO! BASE MODULE
To integrate the cabinet into your network, proceed as follows:
Before starting with this procedure, please determine 2 IP addresses which can be used for the
cabinet in your local network, and write them down:
Component
Address
BM (LOGO! Base module)
TDE (LOGO! Display)
Subnet
Gateway
If you do not know which IP addresses can be used, please ask your local IT administrator.
To change the IP address of the LOGO! Base module, you’ll need to download our free Totech Viewer
from our website: http://www.superdry-totech.com/
For the following steps, you’ll need to have the cabinet connected to the network. You can also
connect the cabinet directly to a PC or laptop using an Ethernet cable. Make sure that the PC or laptop
running the Totech Viewer software is set in the same range as the current IP address of the cabinet
before changing the IP address, or it won’t work:
Open the software, press [File] → [Download data] → [Refresh]
The software will show the current IP address of the cabinet.
Right click on the IP address → [Change IP address]
Change the addresses in the pop-up window and confirm with [OK]
Press [Refresh] again and the cabinet should show up with the new set IP address.
11.2 CHANGE THE IP ADDRESS OF THE DISPLAY
The IP address in the display must also be adapted for communication with the LOGO control. The IP
address of the LOGO! Base module and the display must be in the same subnet.
To do this, go to the [Setting] menu on the 3rd page and press [Offline].
After a few seconds, the home menu of the display will be displayed.
Now proceed in the following order:
Press [Main Unit] → [Ethernet] ⇒ The IP address for the display can be changed here.
Follow up with pressing [Back] → [Save] → [Yes] → [Exit] → [Yes]
The [Port] number specified here is used for setup via Ethernet, for transfer of project files, and for
communication with Pro-Server EX. Do not change the initial value [8000].

Operation Manual Touchscreen
11.3 SELECT THE LOGO! BASE MODULE IP ADDRESS
To make sure the display is connected to the LOGO! Base module in the drying unit, the IP address of
the base module has to be specified in the display:
To do this, go to the [Setting] menu on the 3rd page and press [Offline].
Press [Peripheral] →[Device/PLC Settings] →[Siemens AG SIMATIC S7 Ethernet] →[Device] →
“DEST IP ADDRESS” ⇒Here you have to enter the IP address which you have given to the LOGO!
base module.
(NOTE: Depending on the display type and firmware, the display may vary slightly.)
12. Calibration
Totech recommends annual calibration inspection or the system's calibration by sensor replacement,
respectively. For the drying unit's calibration, we recommend the following two options:
1. Replacing the sensor by a factory-calibrated sensor. After detaching the screw-fastened
retaining ring, the plug-in sensor can simply be unplugged. The replacement sensor is
mounted in reverse order. Since all settings have been stored in the sensor, its replacement
will serve to calibrate the dehumidifier overall measuring. Additional measurement equipment
or software is not required.
2. Define deviations by means of a calibrated reference dew point meter (minimum accuracy
±0.2%RH or higher), and calibrate the sensor via the software's calibration function. This
proceeding requires data connection to PC and software (for detailed instructions, please refer
to the Software Manual of the manufacturer).
13. Maintenance
Ensure to generally disconnect the dehumidifier from the electrical power supply before opening or
disassembling the device.
Ensure all motors - in particular ventilators - are at standstill before reaching inside the device!
In case the dehumidifier was in operation, please allow a cooling time of at least 30 minutes before
disassembling the device!
General maintenance; Dehumidifier U-5000 has been designed for maintenance-free long-term
operation. A maintenance schedule does thus not exist.
Sensor replacement and calibration; please proceed as described under item 7.
Repair works are to be performed by qualified Totech service engineers or adequately trained
personnel only. Please contact your local Totech dealer, or Totech EU directly at the service portal
found on the website: http://service.superdry-totech.com/

Operation Manual Touchscreen
14. Troubleshooting
14.1 For malfunction
✓Disconnect device from power supply completely, and restart after 10 seconds.
✓Check logic module and extension module as described under item 9.6.
14.2 Measuring faults
✓Unplug the sensor and check plug connector.
✓Check the sensor pins.
14.3 Communication error via Ethernet
✓No communication: Check TCP/IP settings, see item 4.12.
14.4 Display indicates “BM no resp Press ESC”
✓Malfunctioning connection between display and logic module.
Check plug connections of display, drying unit, and logic module.
(For checking, the display can be directly connected to the drying unit with a standard
Ethernet cable).
✓Check logic module as described under item 9.6.
14.5 No indication on Display
✓Check plug connections.
✓Check mains fuse in port, and replace if necessary.
✓Check LED for illumination on power supply unit.
a) No LED illuminated ⇒check input-side power supply unit (230VAC); if present, the
logic module needs to be replaced.
b) Red LED illuminated ⇒disconnect secondary power supply unit. If red color remains,
the power supply unit is to be replaced.
c) If illumination switches to green, identify and remedy cause for short-circuit fault.
✓Disconnect external optional equipment (alarm signal light, heater, N2, …) and re-check
✓Disconnect display and re-check
14.6 Logic module and extension module checking
✓Green LED illuminated ⇒ proper function.
✓Red LED illuminated ⇒software update via Ethernet module required. If the respective state
remains, the logic module is to be replaced.
✓No LED illuminated ⇒check voltage supply (24VDC); if present, the logic module is to be
replaced.

Operation Manual Touchscreen
14.7 Humidity too high
✓At first startup, wait at least 24 hours for the cabinet to stabilize.
✓The cabinet is in a regeneration cycle, it is normal the humidity will rise during this procedure.
✓Unplug the cabinet, wait 5 seconds and power up the cabinet. Wait at least 6 hours to check
if the humidity decreases.
✓Check the cabinet for any leakage, check the doors and any open connections to the
environment.
✓Check if the cabinet is fully loaded with wet components, the cabinet needs time to dry these
components.
✓Insufficient air flow ⇒ convections vents covered.
✓Fan failure ⇒ replace drying unit.
14.8 Temperature too low
✓Heating module switched off ⇒ switch on heating module.
✓Heating module power supply interrupted ⇒ check mains connection.
✓Plug connection to drying unit disconnected ⇒ check plug connection.
✓Heater or ventilator failure ⇒ replace defect components.

Operation Manual Touchscreen
15. Warranty and Liability
15.1 Warranty and liability
Principally, we apply our "General Terms & Conditions", which the operator has been provided with
upon contract conclusion at the latest. Warranty and liability claims in relation to personal injury and
property damage shall be excluded if the same arise from one or more of the causes below:
✓the dehumidifiers unintended use;
✓the dehumidifiers improper and inappropriate installation, commissioning, operation, and/or
maintenance;
✓operation with defect safety devices or non-functional safety and protective devices;
✓unauthorized modification or unauthorized alteration of the technical design;
✓repair works performed in an inappropriate manner;
✓disaster situations, impact by foreign objects, and events of force majeure.
After purchase, we provide warranty on all our new products, unless agreed differently.
Full Warranty valid during the first year after purchase of the new product
All Drying Cabinets, Vacuum machines & spare parts (including dry-units).
Full warranty:
The end user will receive the defective part replaced at no costs. The transport costs are to be paid by
the end user. The defective part has to be returned after it is replaced with the new one.
Actual replacement is done by the end user with support from Totech technical support if needed.
Exchange warranty valid during the second year after purchase of the new product
Only U-5000 series & U-7000 series.
Exchange warranty:
The end user will receive the defective part at a lower price. The old part will be returned by the end
user to Totech EU as soon as the defective part is replaced with the new one.
Actual replacement is done by the end user with support from Totech technical support if needed.
Third year warranty valid during the third year after purchase of a new product
Only U-5000 series & U-7000 series.
Third year warranty:
Each case will be evaluated by the technical support department, and the Part(s) will be provided
under leniency circumstances. The end user will receive the defective part at an especially quoted
price by Totech EU sales department. The old part will be returned by the end user to Totech EU as
soon as the defective part is replaced with the new one.
Actual replacement is done by the end user with support from Totech technical support if needed.
Please note: all the parts needs to be shipped back to Totech Europe B.V. within 30 days of
receiving the warranty parts. If not, you will be invoiced for the normal price.

Operation Manual Touchscreen
15.5 Guidelines for the RMA procedure of Totech Europe B.V.
Please provide us as much as possible details to speed up the process.
✓Navigate to our service portal at http://service.superdry-totech.com/
✓Totech Europe B.V. will only accept tickets filed in our service portal.
✓We will provide you the warranty and/or repair parts as soon as possible.
Shipping the parts to Totech Europe B.V.
✓Each part must have its own RMA form attached.
✓All parts must be shipped back in original packaging as much as possible, and ESD safe.
✓Those parts that are returned to Totech EU without any proper packaging will not be accepted
for warranty or repair.
✓Broken or damaged parts due to shipping, or bad packaging, will not be accepted for
warranty.
Send all parts to:
Totech Europe B.V.
To: Technical support department
Paxtonstraat 11
8013 RP Zwolle
The Netherlands

Operation Manual Touchscreen
16. Serial numbers
16.1 Cabinet serial numbers
Explanation how the serial number of the cabinet is identified:
16.2 Dry-unit serial numbers
Explanation how the serial number of the Drying Unit is identified:
This manual suits for next models
1
Table of contents
Popular Touchscreen manuals by other brands

Elo TouchSystems
Elo TouchSystems E744255 Quick installation guide
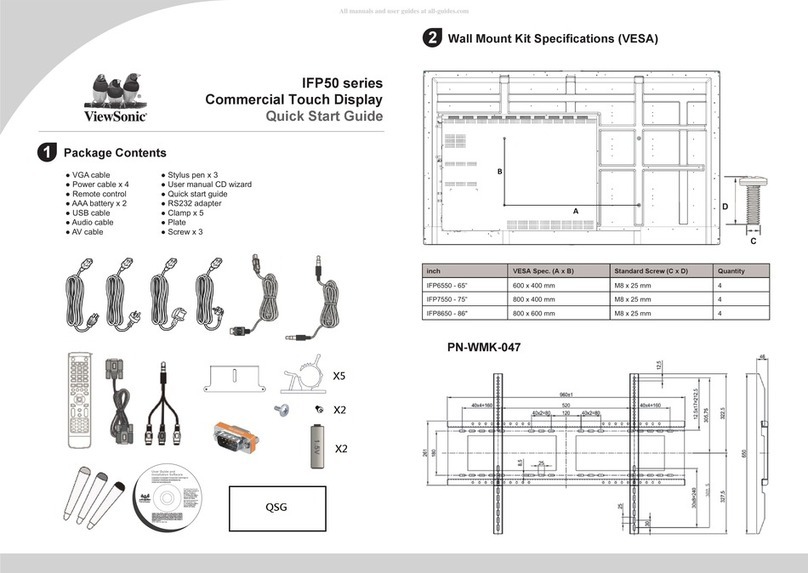
ViewSonic
ViewSonic ViewBoard IFP50 Series quick start guide
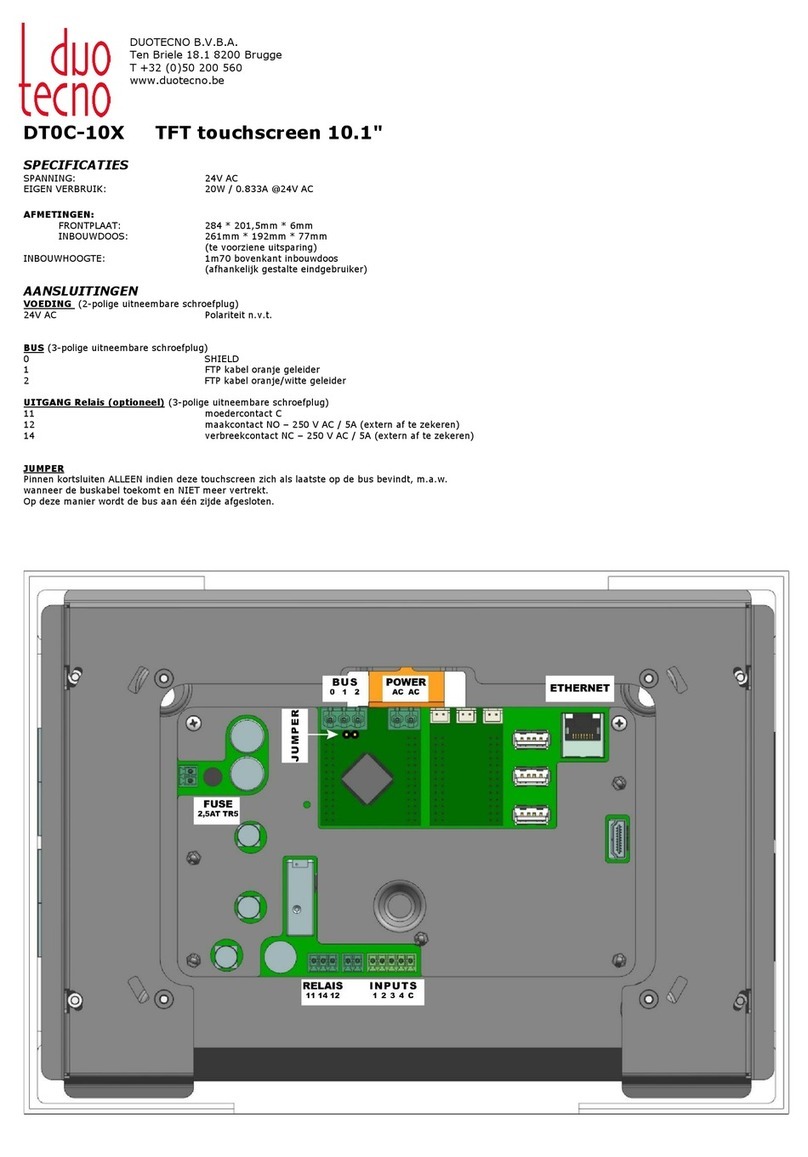
DUOTECNO
DUOTECNO DT0C-10X quick start guide
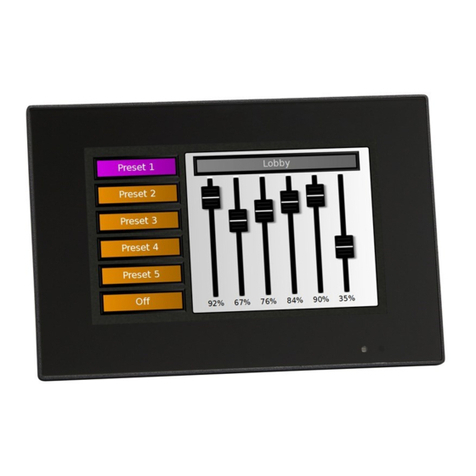
ETC
ETC Unison Paradigm P-TS7 user manual
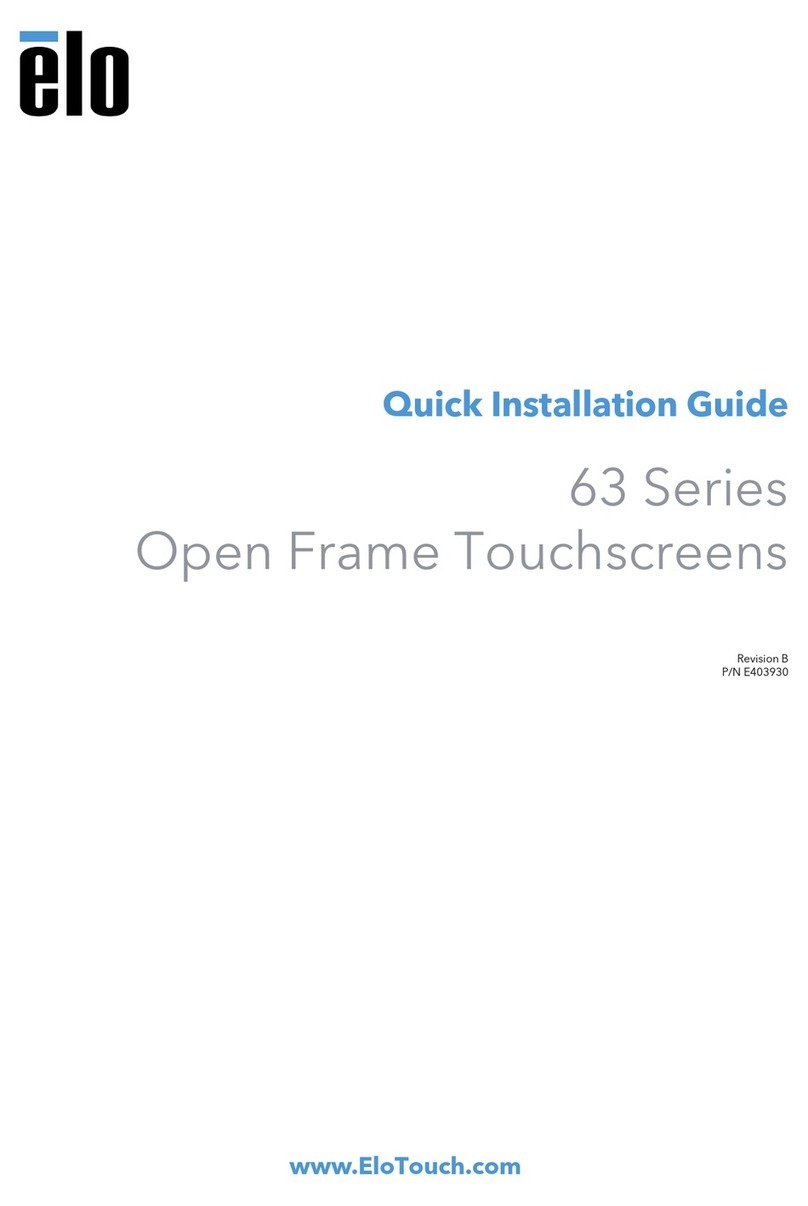
Elo TouchSystems
Elo TouchSystems 63 Series Quick installation guide
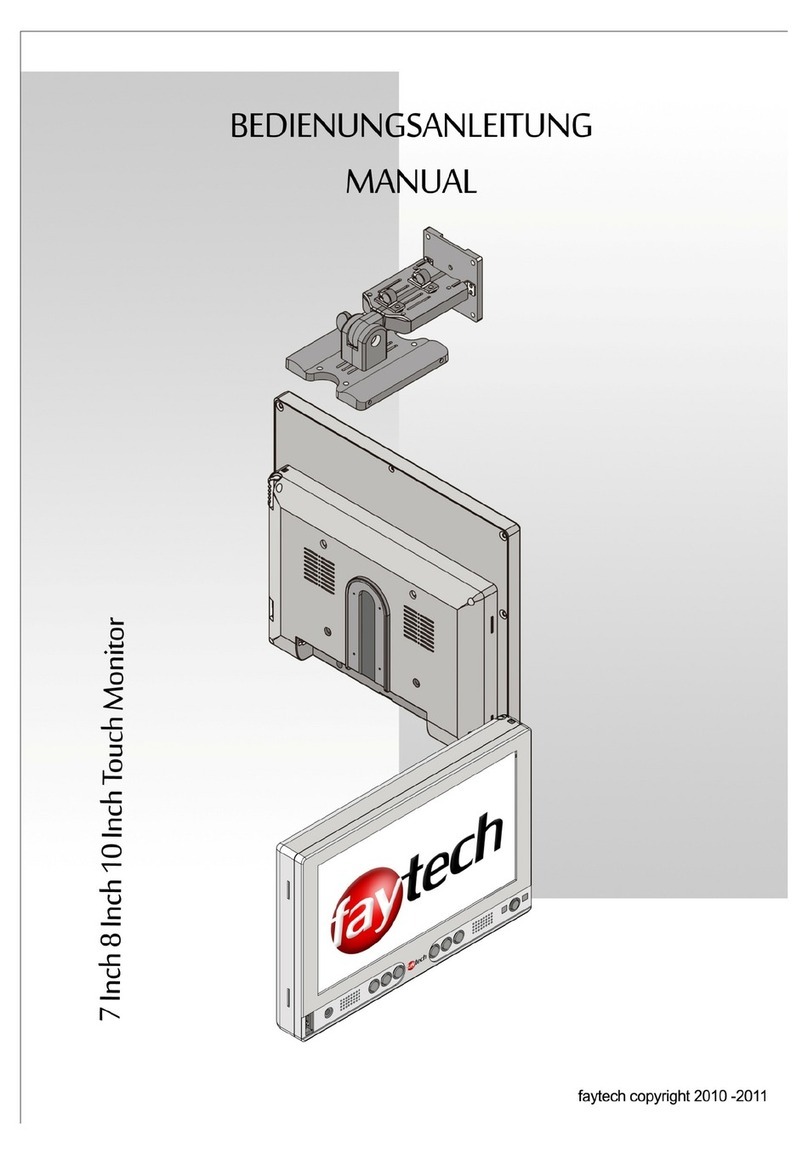
Faytech
Faytech 7 Inch user manual