auer 6P10 PILOT User manual

Made in France
Manual réf. : 1898468
N° édition : 22.29
Installation manual 6P10
78 liters - 10 hydraulic outlets
6kW electrical back-up
Ref. 753040
The information contained in this document is non-contractual. Auer reserves the right to modify the technical specifications or characteristics of any of their appliances without prior notice.
6P10 PILOT
Hydraulic pilot for heat pumps

- 6P10 PILOT MANUAL -
2
SOMMAIRE
1-SAFETY ............................................................. 4
2 -PLEASE READ IMMEDIATELY......................... 6
2.1 - Conservation of documents ............................................................6
2.2 - Symbols used........................................................................................6
2.3 - Abbreviations and acronyms...........................................................6
2.4 - Delivery terms and conditions........................................................6
2.5 - Storage and transport........................................................................6
2.6 - Unpacking..............................................................................................6
2.7 - Rating plate............................................................................................6
2.8 - End of life of the appliance...............................................................6
3 - INTRODUCTION ............................................. 7
3.1 - General information ...........................................................................7
3.2 - Packaging...............................................................................................7
3.3 - Accessories (included) .......................................................................7
3.4 - Accessories available as optional extras......................................7
3.5 - Operating principles...........................................................................8
4 - INSTALLATION................................................ 8
4.1 - Placement choice.................................................................................8
4.1.1 - Appropriate placement choice............................................................................8
4.1.2 - Fixation......................................................................................................................... 8
4.1.3 - Dimensions.................................................................................................................9
4.2 - Hydraulic installation..........................................................................9
4.2.1 - Recommendations...................................................................................................9
4.2.1.1 - Backow prevention device................................................................. 9
4.2.1.2 - Cross sections, purging of the heating circuits............................. 9
4.2.1.3 - Desludging tank....................................................................................... 9
4.2.1.4 - Preparing the hydraulic circuit (rinsing) .......................................... 9
4.2.1.5 - Insulation of the pipes ...........................................................................9
4.2.1.6 - Expansion vessel ......................................................................................9
4.2.1.7 - Frost protection......................................................................................10
4.2.1.8 - Thermostatic valves...............................................................................10
4.2.1.9 - Treatment of the water in the heating circuit..............................10
4.2.1.9.1 - Filling water..........................................................................10
4.2.1.9.2 - Treatment of the heating circuit...................................10
4.2.1.10 - Installation of the DHW circuit........................................................11
4.2.1.11 - Purging the installation.....................................................................11
4.2.1.12 - Connecting the pressure relief valve............................................11
4.2.1.13 - Filter on the water inlet of each heat pump (supplied).........12
4.2.2 - Hydraulic connections..........................................................................................12
4.2.2.1 - Back-up boiler connection .................................................................12
4.2.2.2 - Distribution circuits connection (DHW/heating)........................13
4.2.2.2.1 - Hydraulic circuits sizing between HRC70 pilot
and water tanks primary coils .......................................13
4.2.2.3 - UPMXL 25-125 circulator for heat pump circuits
and distribution (DHW/heating) ......................................................13
4.2.2.3.1 - Manometric height/Flow rate .......................................13
4.2.2.3.2 - Setting of the circulator pump
on the CP3 constant pressure mode...........................13
4.3 - Electrical connections......................................................................14
4.3.1 - Power electrical connections .............................................................................14
4.3.2 - Prior recommandations before power electrical connections ..............14
4.3.3 - Power electrical connection of the pilot..................................................................14
4.3.4 - Power connection of the HRC70 heat pump ........................................................15
4.3.5 - Control connection of the heat pump............................................................15
4.3.6 - Cascade of heat pumps........................................................................................16
4.4 - Connection of circuits and accessories......................................17
4.4.1 - Room thermostat ...................................................................................................17
4.4.2 - Exterior sensor.........................................................................................................17
4.4.3 - Domestic water aquastat.....................................................................................17
4.4.4 - Domestic water sensor.........................................................................................17
5 - SET-UP........................................................... 18
5.1 - Before set-up............................................................................................................... 18
5.2 - Check watertightness.......................................................................18
5.3 - Starting set-up ....................................................................................18
5.3.1 - Step 1 : Number of heat pump..........................................................................18
5.3.2 - Step 2 : Circuits choice..........................................................................................18
5.3.3 - Step 3 : Filling...........................................................................................................19
5.3.4 - Step 4 : Purging the installation........................................................................19
5.3.6 - Step 6 : Finishing set-up.......................................................................................19
5.3.5 - Step 5 : Choosing the back-up...........................................................................19
5.4 - First use..................................................................................................19
6 - SETTINGS AND FUNCTIONS .......................20
6.1 - Control panel.......................................................................................20
6.1.1 - Keypad........................................................................................................................20
6.1.2 - Display........................................................................................................................20
6.2 - Menus ....................................................................................................21
6.3 - Actions to be activated using a combination of buttons....21
6.4 - List of parameters which can be set ..........................................22
6.5 - Description of functionalities........................................................25
6.5.1 - Functions related to heating..............................................................................25
6.5.1.1 - AUTO temperature (heat curve) .......................................................25
6.5.1.2 - Lowering of the temperature ............................................................25
6.5.1.3 - Auto-adaptability...................................................................................25
6.5.1.4 - Ambient temperature reactivity.......................................................25
6.5.2 - Programming and timeout functions.............................................................25
6.5.2.1 - Anticipation of return from holiday................................................25
6.5.2.2 - Automatic summer/winter changeover................................................................26

- 6P10 PILOT MANUAL -3
6.5.3 - Ambient temperature and heating circulation control functions ........26
6.5.3.1 - Ambient temperature sensor hysteresis........................................26
6.5.3.2 - Circulator pump speed........................................................................26
6.5.3.3 - Heating circulator control...................................................................26
6.5.3.4 - Anti-cold radiators.................................................................................26
6.5.4 - Functions related to the production of domestic hot water ..................26
6.5.4.1 - Domestic priority sharing ...................................................................26
6.5.4.2 - Anti-legionellosis protection.............................................................26
6.6 - Heat pump circulator speed..........................................................26
7 - MAINTENANCE AND TROUBLESHOOTING...27
7.1- Diagnostics............................................................................................27
7.1.1 - Loading the operating history...........................................................................27
7.1.2 - Consulting the current operating state of the system..............................27
7.1.3 - Water sensors...........................................................................................................28
7.1.4 - Exterior sensor.........................................................................................................28
7.1.5 - Consulting the counters.......................................................................................28
7.1.6 - Manual forcing of components.........................................................................28
7.1.6.1 - Circulator pump .....................................................................................28
7.1.6.2 - Electrical back-up...................................................................................28
7.1.6.3 - Back-up boiler .........................................................................................28
7.1.7 - Errors indicated by the pilot...............................................................................29
8 - SPARE PARTS ................................................32
9 - WARRANTY ................................................... 33
9.1 - Warranty coverage ............................................................................33
9.2 - Limitations of warranty....................................................................33
9.2.1 - General information ..............................................................................................33
9.2.2 - Cases (not limited to) for exclusion from warranty ....................................33
9.2.2.1 - Usages........................................................................................................33
9.2.2.2 - Handling....................................................................................................33
9.2.2.3 - Installation site........................................................................................33
9.2.2.4 - Electrical connections ..........................................................................33
9.2.2.5 - Hydraulic connections .........................................................................33
9.2.2.6 - Accessories...............................................................................................33
9.2.2.7 - Maintenance...........................................................................................33
APPENDIX ..........................................................34
A1 - Technical specications....................................................................34
A1.1 - General characteristics...........................................................................................34
A1.2 - UE declaration...........................................................................................................34
A1.3 - Dimensions.................................................................................................................34
A2 - Schémas de principe hydraulique................................................35
A2.1 - CASE n°1 - 1 HRC70 heat pump + 1 heating circuit.....................................36
A2.2 - CASE n°2 - 1 HRC70 heat pumps + 2 heating circuits..................................37
A2.3 - CASE n°3 - 1 HRC70 heat pump + 1 DHW tank + 1 heating circuit......38
A2.5 - CASE n°5 - 1 HRC70 heat pumps + 2 DHW tanks + 1 heating circuit ..39
A2.6 - CASE n°6 - 1 HRC70 heat pumps + 1 DHW tank..........................................40
A2.7 - CASE n°7 - 1 HRC70 heat pumps + 2 DHW tanks........................................41
A2.8 - CASE n°8 - 1 HRC70 heat pumps + 3 DHW tanks........................................42
A2.9 - CASE n°9 - 2 HRC70 heat pumps + 1 heating circuit..................................43
A2.10 - CASE n°10 - 2 HRC70 heat pumps + 2 heating circuits...........................44
A2.11 - CASE n°11 - 2 HRC70 heat pumps + 3 heating circuits...........................45
A2.13 - CASE n°13 - 2 HRC70 heat pumps + 1 DHW tank
+ 1 heating circuit .................................................................................................46
A2.16 - CASE n°16 - 2 HRC70 heat pumps + 2 DHW tanks
+ 1 heating circuit ..................................................................................................47
A2.18 - CASE n°18 - 2 HRC70 heat pumps + 1 DHW tank......................................48
A2.19 - CASE n°19 - 2 HRC70 heat pumps + 2 DHW tanks....................................49
A2.20 - CASE n°20 - 2 HRC70 heat pumps + 3 DHW tanks....................................50
A2.22 - CASE n°22 - 3 HRC70 heat pumps + 1 heating circuit.............................51
A2.23 - CASE n°23 - 3 HRC70 heat pumps + 2 heating circuits...........................52
A2.24 - CASE n°24 - 3 HRC70 heat pumps + 3 heating circuits...........................53
A2.25 - CASE n°25 - 3 HRC70 heat pumps + 1 DHW tank......................................54
A2.26 - CASE n°26 - 3 HRC70 heat pumps + 2 DHW tanks....................................55
A2.27 - CASE n°27 - 3 HRC70 heat pumps + 3 DHW tanks....................................56
A3 - Wiring diagram....................................................................................57
A4 - Recap of functions .............................................................................58
A4.1 - Control panel............................................................................................................58
A4.1.1 - Keypad........................................................................................................58
A4.1.2 - Display........................................................................................................58
A.4.2 - Menus.........................................................................................................................59
A.4.3 - Actions through key combinations.................................................................59

- 6P10 PILOT MANUAL -
4
Danger of death if the pressure relief valves
are missing or defective
A defective pressure relief valve may prove
dangerous and could lead to burns or other
injuries by, for example, the pipes bursting.
The information presented in this document does
not contain all of the schematic diagrams needed
for a professional installation of the pressure relief
valves.
• Install the necessary pressure relief valves on
the circuit.
• Inform the user concerning the function and
the placement of the pressure relief valves.
• Respect all applicable national and international
regulations, standards and decrees.
Risk of corrosion
The appliance should be installed in an area
where it is not exposed to humidity and without
any risk of being splashed by water.
Risk of damage related to frost
The pilot MUST be installed in an area where it is
not subject to frost or freezing.
Risk of material damage
The pilot can only work when lled with water.
Never switch on the appliance if it is not
completely lled with water and purged of air.
Rules and regulations (decrees, standards,
laws)
Once the appliance is installed and switched
on, all decrees, directives, technical rules, safety
measures and standards, must be respected in
their current version in eect.
The electrical supply must conform to all
applicable regulations in the country of
installation, as well as the NFC 15-100 standard.
• A methodofdisconnection ensuringa complete
cut-o must be installed in the xed piping to
conform to installation regulations (do not use
a movable outlet).
•Protect the appliance with a 2-pole circuit
breaker with a minimum contact opening of
3mm and must be grounded.
If the electrical supply cable is damaged, it must
be replaced by the manufacturer, their customer
service technicians, or by a qualied professional
to prevent any risk of injury or danger.
• The devices for electrical cut-o must remain
accessible.
•Water and/or R290 ammable gas can ow
through the discharge pipe of the pressure
limiting device (safety valve). This pipe must
be kept open outside the building. The end
of this pipe must be placed downwards
(see § Connecting the pressure relief valve).
1-SAFETY
Danger resulting from improper qualications
• Any work carried out by an unqualied person
can result in damage to the installation or in
physical injury.
• Do not perform maintenance on this appliance
unless you are a qualied professional.
• If the appliance is malfunctioning or not
working, cut the electricicty supply to the
electrical components and seek advice from a
qualied professional.
Danger resulting from improper use
This appliance should not be used by anyone
(including children under the age of 8 years
old)with reduced physical, sensory or mental
capabilities, or by anyone with insufficient
experience or knowledge of the appliance; unless
they are being supervised by someone who is
responsible for their safety and in possession of
the operating instructions of the appliance, or if
they have been instructed in the proper use and
in the risks of operating the appliance.
Children must not play with the appliance.
Cleaning and maintenance of the appliance
must not be undertaken by children without
supervision.
Applicable areas of use
The appliance is intended for use an appliance
for the production of domestic hot water: it must
be connected to a heating installation, and while
complying with the instructions, connected to
the drinking water network.
The intended use of the appliance includes the
following points:
•Following the instructions for operating,
installing and maintaining this appliance and
all of its components.
• Ensuring the compliance of the appliance to all
inspection and maintenance conditions which
are listed in this manual.
Danger of death by electrocution
• Touching live electrical wires can cause severe
bodily injury, and lead to death by electrocution.
All installation and maintenance work must be
carried out with the appliance switched o and
by a qualied professional. Before carrying out
any work on the appliance:
-Cut-o the electricity supply.
- Ensure that there is no possibility of the power
supply becoming active again.
-Wait at least 5 minutes for the capacitors to
lose their charge.
• Do not get water on any of the control or
electrical components. Always disconnect the
appliance from the electricity supply before
carrying out work on any of the electrical
components.

- 6P10 PILOT MANUAL -5
Maintenance - Troubleshooting
Maintenance and cleaning of the pilot must be
carried out at least once a year by a qualied
professional.
This appliance is in compliance with the
international standards concerning electrical
safety CEI 60335-1, CEI 60335-2-102. The
CE branding on the appliance attests to its
compliance with the following directives:
- Low voltage (LV): 2014/35/UE
- Electromagnetic compatibility(CEM):
2014/125/CE
- Ecodesign concerning products related to
energy: 2013-813-UE

- 6P10 PILOT MANUAL -
6
2 -PLEASE READ
IMMEDIATELY
This technical installation manual forms part of the appliance which
it refers to. In order for the warranty to be valid, the instructions must
be read prior to using the appliance.
The safety advice and instructions provided in this manual must be
strictly respected.
Our society is not liable for any damages caused from not following
the instructions provided, or improper handling, installation or use.
This technical installation manual can be modied without prior
notice.
This manual must be safeguarded and passed on to successive users
for future reference.
It will be considered as evidence in case of litigation.
2.1 - Conservation of documents
DHW.......Domestic Hot Water
DCW .......Domestic Cold Water
T°..............Temperature
HP............Heat pump
2.3 - Abbreviations and acronyms
2.4 - Delivery terms and conditions
In general, the material is transported at the recipient’s own risk.
It is important to ensure that all components have been received and
that no damage has been sustained during transport upon receipt
of the appliance, and before beginning the installation procedures
Indicates warnings and important recommendations.
2.2 - Symbols used
Contains regulated substances, do not throw in the
garbage. If disposing, please respect all regulations
pertaining to the recovery of electric and electronic
equipment.
Maximum working pressure.
PSmax
Consult the installation manual before any intervention
on the product, before handling, installation, use , and
maintenance.
Heat power output produced.
Indicates the maximum water temperature in operation.
Admissible storage and transport temperatures are from -20°C to
+60°C.
The 6P10 Pilot must be stored on its original pallet. It must be
transported on its pallet, empty of water, horizontally. It must remain
screwed to the pallet during the transport.
2.5 - Storage and transport
2.6 - Unpacking
On reception of the Pilot, check the state of the packaging as well
as the general state of the product.
Then, take o the plastic protection and unscrew the pilot from its
pallet.
The pilot is screwed with 4 woodscrews at the bottom and at the
top at plates level.
2.8 - End of life of the appliance
Our products are designed and manufactured using
components made of recyclable materials.
The appliance must never, in any case, be disposed
of with household waste, or in a dump.
The dismantling and recycling of the appliances
must be taken charge of by a qualied professional
and in compliance with all local and national
standards in eect.
2.7 - Rating plate
Rating plate

- 6P10 PILOT MANUAL -7
3.2 - Packaging
Weight
(kg)
Number
of
packages
W
(mm)
H
(mm)
P
(mm)
6P10 67 - 800 686 1600
Each Pilot is delivered with (non-mounted) :
• Exterior sensor
Gives the pilote the outside temperature to
adapt its heating set point
• USB memory stick
Allows downloading of the operating
history
Ensure to keep the original delivered USB ash drive.
It will facilitate your exchanges with your technical contacts.
3.3 - Accessories (included)
3 - INTRODUCTION
6P10 is a hydraulic pilot which ensures working installations with
high power heat pumps. Its integrated tank ensures the decoupling
of the heat pumps circuits as well as the air bleeding and the
evacuation of the sludges.
If the required installation power is higher than the delivered power
by the heat pump, the 6kW electrical back-up or the boiler back-up
can be started by the pilot.
6P10 pilot is equipped with :
- One 78 liters wall tank with air bleed, pressure sensor, pilot
sensor, 6kW electrical back-up, 6bars pressure relief valve and
settling valve.
- One electronic control ensuring the working of the installation.
Optional distribution branches can be added (up to 2 branches) for
installation including several circuits or heat pumps :
- up to 3 heat pumps and 1 distribution circuit
- up to 3 sanitary circuits and 1 heat pump
- 1 heating circuit
The distribution branches dedicated to heat pumps ensure the
circulation in HRC70 25kW, HRC70 32kW or less power heat pumps.
They must not be connected in the case of heat pumps which have
their own circulator (HRC70 40kW or higher power).
3.1 - General information
• DHW sensor (for water tanks connected as circuits
1 et 2)
For the production of domestic hot water
(
Réf. 710029)
• DHW aquastat (for water tank connected as circuit
3)
For the production of domestic hot water
(Réf. 752202)
3.4 - Accessories available as optional
extras
• Ambient temperature thermostat radio non-
chronoproportional -(THRnc)-
(on/o type). Wireless, programmable thermostat,
transmitting through radio-frequency. Necessary when a wired
connection between the Pilot and the ambient temperature
thermostat is not possible
(
Ref.770001)
• Hydraulic distribution branch
(Ref. 755823)
• Shielded bus wire - 20 m long
(
Réf. 753102)
• Shielded bus wire - 50 m long
(
Réf. 754103)
• Additional multi-circuit box
For adding circuits of the same type
(
Réf. 754104)
• Ambient temperature thermostat (TA)
2 wires - allows to control the temperature in
the heating zone
(
Ref. 710043)

- 6P10 PILOT MANUAL -
8
1. 78L buer tank
2. Heat pump circulator pump
(except for HRC70 40kW)
3. Distribution circuit
circulator pump
4. 6kW electrical back-up
5. Electronic control
6. Power electronic card
7. Distribution circuit
8. Drain
9. Heat pump circuit
3.5 - Operating principles
4 - INSTALLATION
4.1 - Placement choice
4.1.1 - Appropriate placement choice
The Pilot must be placed in an area which is free from frost and
adverse weather conditions.
It must be placed as close as possible to the heat pump without
exceeding the maximum distance.
The maximum distance depends on the diameter of piping and the
number of elbows used (see «Hydraulic connection» tables).
The 2-core sheathed cable which connects the Pilot and the heat
pump is 10m long. There is a 20m length available as an optional
extra (Ref. 753102) or 50m (Ref. 754103).
The Pilot must be installed on a level
and stable base which is distanced from
appliances used for cooking and other heat
sources.
The Pilot lled with water can be heavy, watch
over the resistance of the wall stand.
The pilot must be xed on a resistant wall.
4.1.2 - Fixation

- 6P10 PILOT MANUAL -9
4.1.3 - Dimensions
The pilot must be placed at least 200mm above the oor or any
obstacle the enable it to be drained.
It must be placed at least 400mm under the ceiling to facilitate
the access to the air bleed and to the electrical back-up. 4.2.1 - Recommendations
A type CB backflow prevention device may be installed. This
device must be at dierent, non-regulated pressure zones. Check
your national laws and regulations to know if this is an obligatory
requirement. The backflow prevention device is designed to
prevent incoming heating water from entering the drinking water
circuit. It must be connected to the mains drainage system.
4.2.1.1 - Backow prevention device
A sucient ow rate should be ensured so that the dierence in
temperature between the outlet and inlet points does not exceed
6°C. In an installation equipped with thermostatic mixing valves, this
inspection must be done with all taps/valves open.
The output actually needed determines the water ow rate of
the heating circuit and allows to calculate the dimensions of the
distribution network.
Adapt the speed of the circulator pump to the hydraulic
characteristics using the ow rate/pressure curve provided.
All necessary measures must be taken to ensure that the installation
can be continuously purged. Automatic air purging valves should be
placed at each high point of the installation, and manual air purging
valves should be installed on each radiator.
4.2.1.2 - Cross sections, purging of the
heating circuits
4.2 - Hydraulic installation
Consult the hydraulic schematic diagrams in the appendix.
Plan for a desludging tank with a suicient volume at a low point
on the inlet of the heating circuit. This tank must be equipped
with a drain so it can collect the oxides, particles, and calamines
which detach from the inner walls of the heating circuit while it is
in operation.
4.2.1.3 - Desludging tank
Before placing the pilot and heat pump, it is necessary to rinse the
installation with an appropriate product.This allows to eliminate all
traces of soldering waste, joint ller, grease, sludge, metallic particles,
etc... in the radiators, underoor heating, etc...
4.2.1.4 - Preparing the hydraulic circuit
(rinsing)
4.2.1.5 - Insulation of the pipes
Insulators must be in accordance with DTU 67.1.
All the apparent pipes and accessories (circulator, expansion vessel,
valve, ...) must be insulated or placed in insulated box.
4.2.1.6 - Expansion vessel
The installation must be equipped with an expansion vessel with
a sucient capacity (which depends on the static height of the
installation, the blowing-up pressure of the expansion vessel and
the volume of the installation)

- 6P10 PILOT MANUAL -
10
It is IMPERATIVE to refer to the
installation instructions for the initial
installation of the ambient temperature
thermostat to ensure satisfactory operation.
In an installation with both
thermostatic valves and a room
temperature thermostat, the radiator(s) in
the room in which the thermostat is located
MUST be equipped with a manual valve(s).
Thermostatic valves: these valves should prioritise rooms with
higher levels of heat gain.
4.2.1.8 - Thermostatic valves
4.2.1.9 - Treatment of the water in the
heating circuit
It is MANDATORY to read the additional
document concerning the quality of
water used for lling the installation.This
document is included with this manual as well as
in the packet with the warranty information.
This document also contains information which is
PERTINENT to the WARRANTY of the material.
Central heating installations must be cleaned
in order to eliminate debris (copper, lings,
soldering waste) related to the set-up of the
installation or from chemical reactions between the
metals.
Futhermore, it is important to protect the
central heating installations from risks of
corrosion, limescale, and microbiological
development through use of a corrosion inhibitor
which is suitable for all kinds of installations (steel or
cast-iron radiators, PEX underoor heating).
PRODUCTS USED FOR HEATING WATER
TREATMENT MUST BE APPROVED BY THE
LOCAL OR NATIONAL PUBLIC HYGIENE
AND HEALTH AUTHORITY.
4.2.1.9.1 - Filling water
The materials used for producing a heating circuit are of dierent
natures. Instances of corrosion may occur through galvanic coupling
in both new and existing installations.
The lling of the heating circuit must only be done with untreated water
(no water softener) from the drinking water network. Water from any other
source )rain-water, well-water, etc...), must be analysed and MUST have
the following properties:
8,5 UPH (acidity) U9,5
Chlorides U60 mg / litre
Conductivity < 1000 μS / cm
5 UTH (hardness in French °) U15
We recommend the use of products in the SENTINEL range by GE
BETZ for preventative and curative treatment of the heating circuit.
• For new installations : (less than 6 months old):
- Clean the installation with a universal cleaner to eliminate
the debris from the installation (copper, bres, soldering
uxes) Example : SENTINEL X300
- Throughly rinse the installation until the water runs clear,
with no traces of impurities left.
- Protect the installation against corrosion with a corrosion
inhibitor, example: SENTINEL X100. Or against corrosion
and freezing with an inhibitor with an anti-freeze additive.
Example :SENTINEL X500.
• For existing installations:
- Desludge the installation with a desludging product
to eliminate any sludge from the installation. Example:
SENTINEL X400.
- Throughly rinse the installation until the water runs clear,
with no traces of impurities left.
- Protect the installation against corrosion with a corrosion
inhibitor, example: SENTINEL X100. Or against corrosion
and freezing with an inhibitor with an anti-freeze additive.
Example : SENTINEL X500.
4.2.1.9.2 - Treatment of the heating circuit
Corrosion inhibitor :
- protects against the formation of limescale
- prevents «pinhole» type corrosion
- prevents, in new installations, the formation of sludge
and the proliferation of bacteria
(in low temperature networks: algae)
- prevents the formation of hydrogen
- eliminates the sound of the generators
Treatment products from other manufacturers can be used if they
guarantee that the product is appropriate for all the materials used
in the appliance and oers ecient resistance to corrosion. To nd
this information refer to their user manual.
Frost protection is necessary if the pilot is switched o during the
winter months (ex: secondary residence, etc...).
4.2.1.7 - Frost protection
If the appliance is connected to an
electricity supply, the heating circuit is
protected from freezing. It is IMPERATIVE
to drain the domestic hot water circuit however.
If the pilot is not being supplied with electricity
(electrical cut-o for example), or it is defective
and there is a risk of freezing, it is IMPERATIVE to
completely drain the appliance (heating and hot
water).

- 6P10 PILOT MANUAL -11
It is mandatory to refer to the technical manual provided with each water tank.
It is mandatory to install a safety group on the cold water inlet of each water tank.
Do not place a stop valve between the safety group and the water tank.
• The number of elbows and pressure losses will have to be minimize, focets will have to be adapted.
• Areas in which domestic water is rich in limestone (HT > 15), we advise the installation of an anti-scale device on the domestic water inlet. The
hydrotimetric title has to be less than 15.
• The concentration in chlorides in DHW has to be less than 60mg/L (required quality for drinkable water intented for human consumption).
Domestic Hot Water can reach more than 60°C, (especially during the anti-legionelosis protection), it is
mandatory to install a thermostatic valve on the DHW outlet to avoid any risk of burn.
4.2.1.10 - Installation of the DHW circuit
4.2.1.11 - Purging the installation
The oxygen present in the air is extremely corrosive. All necessary measures must be taken to ensure that the installation can be continuously
purged. Automatic air purging valves should be placed at each high point of the installation, and manual air purging valves should be installed
on each radiator.
Any deterioration of the appliance due to inappropriate lling water, and/or corrosion in the absence
oftheuseoftreatmentproducts,and/orimproperpurgingof theinstallation, willrenderthewarranty
null and void.
RENDERINGTHEWARRANTY NULL AND VOID
The Heat Pump and the Pilot are both equipped with pressure-relief valves. The Pilot’s pressure-relief valve is set at 3 bars.
The pressure-relief valve on the Heat Pump sets the maximum acceptable pressure in the installation (2.5 bars when hot).The maximum service
pressure in the Heat Pump must, consequently, be lower than 2.5 bars.
Example : If the Heat Pump is positioned 5m below the Pilot, the pressure reading on the Pilot would be 0.5 bars less than the real pressure of the
water in the Heat Pump. In this case, the maximum service pressure for the Pilot would be 2 bars.
Therefore it would be advisable to ll the heating circuit at an intermediary pressure (between 1 and 1.5 bars).
For safety reasons (potential presence of ammable R290 gas), drainage of the Pilot’s pressure-relief valve must MANDATORILY be done
outside the building. The outlet of the drainage pipe (4m length provided with the pilot) must be placed downwards in order to avoid any
introduction of water inside, any risk of obstruction due to frozen water or any other pollution (see drawing).
If the provided drainage pipe is too short, it’s mandatory to use a well-adapted length (can by supplied on demand). It will have to be installed
as well as there will be no pinch on it, it will then ensure the drainage of the overpressure from the 3 bar safety valve outside the building.
4.2.1.12 - Connecting the pressure relief valve
ThePilot’spressure-relief valvedrainagepipe
must be properly secured until the outside of
the building without any pinching zone.
WARNING
Failure to comply with this requirement
concerning the evacuation of overpressure outside
the building releases the heat pump manufacturer
from any liability in case of incident.

- 6P10 PILOT MANUAL -
12
As a reminder, depending on your installation, it is possible to rotate
the pilot’s buer tank to place 1 to 6 plumbing ttings on the right
and 7 to 10 ones on the left :
4.2.2.1 - Back-up boiler connection
CAR : Check valve
Cch : Boiler circulator pump (controlled by the boiler)
CH : Boiler
Sch : Boiler pressure relief valve
VA : Stop valve
VCB : Desludging valve
VE : Expansion vessel
4.2.2 - Hydraulic connections
1’’1/2 plumbing ttings apart from drain valve (1’’1/4).
Left side Right side
• Clean the lter at least once a year.
4.2.1.13 - Filter on the water inlet of each
heat pump (supplied)
It is mandatory to install the 1’’1/4 lter with incorporated 500μm
lter on the water inlet pipe of each heat pump :
• Mind the ow direction of the lter. (arrow).
Clean the lter several times when the
circulator pump of each heat pump is
working for the rst time. (do not forget to stop the
circulator pump of each heat pump when cleaning).
• It is mandatory ti install the 500μm lter
provided with the heat pump to prevent the
heat pump’s exchanger from clogging.
• Before heat pump(s) hydraulic connections, you
have to desludge and to rince the installation.

- 6P10 PILOT MANUAL -13
4.2.2.2.1 - Hydraulic circuits sizing between
HRC70 pilot and water tanks
primary coils
Water tanks are characterized by their sanitary capacity, their
exchange surface (power) and their insulation (thermic losses).
Given : Q1 the HRC70 heat pumps total primary ow rate.
Q2 the sanitary exchangers total primary ow rate.
Q2 total ow rate must be sucient in order to ensure heating in
less than 8 hours of all the DHW tanks and it must be as following :
0,90 x Q1 < Q2 < Q1.
«d2» distance between hydraulic pilot and water tanks primary
exchangers must have a hydraulic section will have to be sucient.
With the following tables, determine the minimum interior diameter
of the pipes according to the d2 distance.
Ballon
sanitaire
Surface
échangeur Qprimaire
Perte
de charge
à Qprimaire
Puissance*
à Qprimaire
Pertes
à l'arrêt UA
Consommation
d'entretien
litre m²m
3
/
hmCE kW W/K kWh/24h
300
353000
3,15 1,5 0,23 41 1,77 2,52
500
342104
4,10 1,5 0,30 67 2,78 3,00
750
342150
3,76 2,0 1,34 69 2,77 3,32
1000
342151
5,20 3,0 3,80 100 3,16 3,79
1500
342152
5,60 3,0 4,10 107 3,66 4,39
2000
342153
5,60 3,0 4,10 107 4,06 4,87
2500
342154
7,00 3,0 5,20 132 4,42 5,30
3000
342155
7,00 3,0 5,20 132 4,70 5,64
Réf.
AUER
* Primaire à 68°C et Sanitaire 10 à 45°C
4.2.2.2 - Distribution circuits connection
(DHW/heating)
4.2.2.3.2 - Setting of the circulator pump
on the CP3 constant pressure
mode
CP3 constant pressure is factory set.
However, in order to verify set is correct or in the case of a change
of circulator pump, it can be necessary to set it correctly.
Speed selector enables de choose 2 control modes «PP» or «CP» :
• 3 proportionnal pressure curves (PP)
• 3
constant pressure curves (CP)
The circulator pump must be obligatorily set in constant
pressure mode and «speed» 3, that is to say CP3 :
• Press «speed» selector during 2 seconds :
- The circulator pump is in setting mode, LED is ashing.
• Flashing mode :
- Fast : Proportionnal pressure (PP),
-
Slow : Constant pressure (CP).
• Every new press on the selector triggers a change of the set :
- Command curve and control mode are changed. (see
diagram below) :
• After 10 seconds without pressing the button :
- Set is selected
- Heat pump is in operation mode.
• LED 1 or 2 or 3 is permanently lighted up :
- Heat pump must work with the selected curve and the
selected mode. (Constant pressure CP3)
4.2.2.3.1 - Manometric height/Flow rate
4.2.2.3 - UPMXL 25-125 circulator for heat
pump circuits and distribution (DHW/
heating)
clignotement rapide
PP1
clignotement rapide
PP2
clignotement rapide
PP3
clignotement lent
CP1
clignotement lent
CP2
clignotement lent
CP3
quick blinking
quick blinking
quick blinking
low blinking
low blinking
low blinking
quick blinking
low blinking

- 6P10 PILOT MANUAL -
14
4.3 - Electrical connections
4.3.1 - Power electrical connections
• During the transport, an accidental
loosening of the electrical connections can
occur.
• In order to eliminate any risk of anomalous
overheating, a control of the tightening of the
connections is strongly recommanded.
See § «Spare parts list - electrical boxes»
The rules and regulations in the country of
installation MUST be respected (standard
C15-100).
• The electrical lines for general power supply to
the circuits must be made in compliance with your
country’s current rules and regulations (standard
C15-100).
• Standard C15-100 determines the cable section to
be used based on acceptable currents.
• Standard C15-100 determines the cable section to
be used based on the following elements:
- Nature of the conductor :
. type of insulation, number of strands, etc...
- Installation mode :
. inuence of conductor and cable groups
. ambient temperature
. tightly or non-tightly installed
. length of cables, etc...
4.3.3 - Power electrical connection of the pilot
Electrical supply must be protected by an omni-polar power cut-
o device having a 3mm minimum spacing (EN 60335.1) : fuses or
circuit breakers must be calibrated according to the power of the
pilot.
Electrical protection - 6P10 (with electrical back-up)
Number of
circulator
pumps
Supply
voltage
Cable cross-
section
Maximum
intensity
called
Circuit
braker
2
230V mono 3 G 6 mm² to
3 G 10 mm² 27,9 A 32 A
400V tri 5 G 2.5 mm²
to 5 G 4 mm² 9,3 A 16 A
3
230V mono 6 to 10 mm² 28,7 A 32 A
400V tri 2,5 to 4 mm² 9,5 A 16 A
4
230V mono 6 to 10 mm² 29,4 A 32 A
400V tri 2,5 to 4 mm² 9,8 A 16 A
Plan for a circuit breaker dedicated to the power supply of the Pilot
on the electrical panel. It must be able to completely cut-o the
electrical supply from the network (all-pole) to eliminate any danger
when carrying out maintenance on the appliance.
How to proceed:
• Check that the «ground» cable is connected properly to the
grounding peg or grounding network of the building.
• Connect the Pilot’s electrical cable to the dedicated plug,
equipped with a circuit breaker.
• Leave the pilot switched o until set-up.
• If a back-up boiler has to be connected ensure it is powered
o before any action.
The proper voltage is: 230 V (+10% / -15%).
Each appliance is delivered from the factory completely pre-wired.
However, it is necessary to connect the following elements to the
relevant terminals:
• The general electricity supply.
• The dierent sensors or thermostats on the Pilot.
•The 2-core shielded cable connecting the Pilot and the Heat
pump (10m length supplied).
• The back-up boiler (optional)
For three phase 400V electrical connection, refer to § «Electrical
Power Connection»
Under no circumstances will the manufacturer be held liable for
any problems which may arise due to improper installation and/or
choice of power supply cable.
4.3.2 - Prior recommandations before power
electrical connections
Check:
• The power consumption
• Number and thickness of the power supply
cables
• Fuse or circuit breaker ratings
The power supply must come from an electrical protection and
sectioning device which complies with all current rules and
regulation in eect in the country of use.
This CE-approved unit complies with all the essential requirements
of the following directives:
- Low voltage n°2006/95/CE
- Electromagnetic compatibility n° 2004/108/CE
Ensure that the installation is equipped with a properly sized and
connected grounding cable.
Ensure that the voltage and frequency of the general power supply
ts requirements.
The acceptable variation in voltage is:
230 V -10% to +6% 50Hz for single-phase + Ground models.
400V -10% to +6% 50Hz for three-phase + Neutral + Ground models
Under no circumstances will the manufacturer be held liable for
any problems which may arise due to improper installation and/or
choice of power supply cable.
Electrical supply of each device must be done power off by a
qualied professional.

- 6P10 PILOT MANUAL -15
4.3.4 - Power connection of the HRC70 heat
pump
Itismandatorytoreadtheinstallationmanual
provided with each HRC
70
heat pump.
The terminals connection are «Cage Clamp» terminals spring.
For Handling, use the following :
- for 2.5mm² or 4mm² control terminals, use a
3.5 x 0.5mm at-head screwdriver.
- for 6mm² power terminal, use a 5.5 x 0.8mm
at-head screwdriver.
- for 10mm² power terminal, use a 5.5 x 0.8mm
at-head screwdriver.
1: Insert the screwdriver into the rectangular
window located on top of the terminal block.
2: Insert the wire ito the «Cage Clamp» when the
ap is open.
3: Remove the screwdriver.
Note : The wires must be stripped to the following lengths :
- For 2,5mm² control terminals : between 10 et 12mm
- For principal powers terminals : between 18 et 20mm
- For intermediate powers terminals : between 11 et 13mm
4.3.5 - Control connection of the heat pump
• Distance between the pilot and the heat
pump must not be higher than 100m
•Inordertoavoiddisruptionsrelatedtothevalues
of the sensors read by the controller, control and
power lines must be wired independently. Avoid
junction boxes.
•Conductorsmustbemadeof electrolyticcopper.
• Telephone wire use is forbidden.
• Control cross-section cables must be between
0,5 and 1mm².
Single phase power supply :
• Connect the power supply to the main terminal block on the power
board. Use only the Ph1 terminal (brown wire below above) for
phase connection.
• Make sure that the internal cable between the Ph1 terminal and
the Power Electronics Board (red cable) is connected to the last
terminal (marked P3) of the power board.
The phase must be connected to the Ph1
terminal on the main terminal block,
which in connected to the P3 terminal
on the power board with the red internal
cable.
Make sure these connections are followed
before powering on.
Three phase power supply :
• Connect the power supply to the main terminal block on the power
board. Each phase must be connected to one of the terminals P1,
P2, P3 (remove the bridge between terminals P1 and P2).
• Remove the X2 and X3 connector bridges.
Do not power up without rst checking
that the connectors X2 and X3 and the
bridge between terminals P1 and P2 have
been removed.
Terminal block

- 6P10 PILOT MANUAL -
16
- Connect the two wires of the connecting cable on terminals A
and Bof the «Modbus» terminal while taking care to respect
the polarity A/B (terminal Aof the Pilot to be connected to
terminal Aof the heat pump; the same for terminal B).
- Connect:
- the brown wire to A
- the white wire to B
- the black wire to GND on both appliances.
- If you are using a dierent cable, respect the polarity of A and B as
well as the connection of the shielding on 0V on both appliances.
Plan for the appropriate length of cable between the pilot
and the heat pump. Do not hesitate to cut the cable to
the appropriate length to AVOID LOOPS.
4.3.6 - Cascade of heat pumps
Black wire must
be imperatively
be connected on
the terminal.
Use the communication wire connected on the heat pump to realize the connections
between the heat pumps. The communication wire must be cut to avoid loop and
must be connected to the closest heat pump.
Congure the addresses of the heat pumps
thanks to the red selector on the heat pump
electronic card.
Pay attention to respect the numbering (address 1 for
HP1, address 2 for HP2,...)
address = 1
Heat Pump n°1
address = 2
Heat Pump n°2
address = 3
Heat Pump n°3
Ensure that the connecting cable is distanced
from any source of electrical disturbance
(ex:
washing machine, neon lighting, power
supply cable....)

- 6P10 PILOT MANUAL -17
4.4 - Connection of circuits and accessories
Sensors and accessories details :
1-2 = Zone 1 control (ambience thermostat or water tank sensor )
3-4 = Zone 2 control (ambience thermostat or water tank aquastat)
5-6 = Zone 3 control (water tank sensor)
7-8 = Peak hours contact
9-10 = Outdoor sensor
11-12 = Back-up boiler command (To connect to the thermostat input
of the boiler)
In an installation with both thermostatic valves and a room
temperature thermostat, the radiator(s) in the room in which the
thermostat is located MUST be equipped with a manual valve(s).
It is mandatory to install the ambient temperature control on an
interior wall of the room and not a wall that lets out onto the outside
of the building.
Installation against an exterior facing wall is prohibited.
Do not place the ambient temperature controller too close to a
window, a curtain, or a door. Avoid placing it in an alcove, a closet,
or behind drapes.
Do not place above a heat source (radiator,...)or against a wall with
a chimney.
Do not place in reach of sun’s rays, or near powerful lighting.
Place the sensor 1.50m above oor level, and at least 50cm away
from neighboring walls. Insulate the extremeties of the electrical
cabling of the installation on the side of the appliance to prevent
air currents from inuencing the measures taken.
EXCLUSIVELY connect the AMBIENT
TEMPERATURE RADIO THERMOSTAT
(Ref.770001).
All other thermostats which are
chronoproportional may cause malfunctioning
and render the warranty null and void.
4.4.1 - Room thermostat
The connection of the exterior sensor is recommended (if it is not the
heat curve is calculated using the temperature read by the air sensor).
Place the sensor on the coldest exterior wall of the building (usually
the north-facing wall). It must not be exposed to the morning sun.
It is preferred to mount the exterior sensor in the middle of the wall of
the building or of the heating zone, at least 2.5m above ground level.
Do not place the sensor:
- above windows, doors, air exhausts, or other heat sources,
- beneath balconies or gutters
To prevent mistakes in the temperatures measured due to air
circulation, insulate the extremities of the sensor’s electrical conduit.
Do not paint the exterior sensor.
4.4.2 - Exterior sensor
Note :
After connection, go to the «DISPLAY» menu and check that the
«EXTERIOR» screen appears with the value read by the probe.
If not, check the connection of the probe or the pilot connector.
4.4.4 - Domestic water sensor
EXCLUSIVELY connect the water sensor
(Ref. 710029).
If DHW is produced by a domestic hot water tank:
- Place the sensor in the well of the tank to inspect the
temperature of the hot water immediately available.
- Connect the water sensor to the terminals of the Pilot.
4.4.3 - Domestic water aquastat
EXCLUSIVELY connect the water sensor
(Ref. 752202).
If DHW is produced by a domestic hot water tank:
- Place the aquastat bulb in the well of the tank to inspect the
temperature of the hot water immediately available.
- Connect the aquastat to the terminals of the Pilot.
Note1 :
For DHW tanks equipped with an aquastat, the setting of the
temperature target corresponds to the temperature of the tank
circulating in the exchanger. For DHW tanks equipped with a
water sensor, the setting of the temperature target corresponds
to the water temperature in the tank.
If the water temperature is controlled by aquastat, the
temperature target set to the pilot must be 5°C to 10°C higher
than the temperature target set to the aquastat.
Note2 :
The thermostat (in the case of a heating circuit) or the aquastat
(in the case of a DHW circuit) connected to terminals 1 and 2 must
be able to withstand a voltage of 230V.

- 6P10 PILOT MANUAL -
18
5.3.2 - Step 2 : Circuits choice
Select the type of circuit which is
connected (DHW, radiators).
RADIAtoRs
C-1
5.3.1 - Step 1 : Number of heat pump
Indicate the number of heat
pump(s)
HP NUMBER
1
5 - SET-UP
Set-up must be done by a qualied
professional.
Inspect the entirety of the hydraulic connections (nuts with washers,
toric joints or anything assembled with glue) which may loosen
during transport or during the installation process, and tighten if
necessary.
After pressurising the appliance, it is important to check the
watertightness (both visually and by any lowering of pressure) of
all internal and external connections.
Any deterioration of the appliance due
to a lack of watertightness renders the
warranty null and void.
5.2 - Check watertightness
The pilot is factory congured to work with :
- Heat pump without back-up boiler
- 1 heating circuit
This conguration can be modied, if necessary, in the Installer
menu.
5.3 - Starting set-up
When the Pilot is turned on for the rst time, it will ask you to conrm
the language of use (French, English, German, Italian, Spanish, or
Polish), and will request to start set-up:
Choose yes and conrm by pressing .
COMMISSIO.
NOTE: If you choose not to start set-up (NO) this option remains
accessible in the expert menu, by the COMMISSIO. sub-menu.
Ensure that:
- All work carried out on the hydraulic circuits and the electrical
circuits are in compliance with the regulations in effect
(inspection by a qualied professional)
-The pressure relief valve on the cold water inlet of the domestic
hot water tank is working properly and is properly connected
to a drain in complaince with the regulations in eect.
- All piping is watertight.
- All hydraulic connections are properly tightened.
- The correct voltage at the mains switch.
- All of the valves are open and nothing is obstructing the
circulation of water in the exchanger and in the hydraulic
circuit.
- The installation is equipped with a lter valve or a lter on its
inlet and that the lter is not clogged.
- The automatic air purger’s cap is open.
- The exterior sensor and the ambient temperature control (if
present on the installation) are connected properly.
-If using an ambient thermostat, ensure that it is actually being
used and set to be on demand (turn it to its maximum set point).
Once all of these checks have been done, turn on the heat pump
and Pilot.
5.1 - Beforeset-up
Installation should not be started
WITHOUT WATER inside

- 6P10 PILOT MANUAL -19
5.3.5 - Step 5 : Choosing the back-up
It is possible to select the electrical back-up, the back-up boiler or
not to declare a back-up.
5.3.4 - Step 4 : Purging the installation
During the cycle, check that the automatic purgers are open and
regularly activate the manual purgers.
If the pressure in the circuit becomes insucient due to the volume
of air purged, the Pilot will indicate it and will pause the purging
cycle.
Activate the backow prevention device or the lling valve to raise
the pressure.The purging cycle will resume automatically once there
is sucient pressure.
The purging cycle is launched for a duration of 30 minutes and will
automatically stop after that time is up.
At any time during the cycle, you can:
- Interrupt (or resume) the cycle by pressing on .
- End the cycle and continue to the next step by pressing
During the purging cycle, the screen
indicates the countdown until the
automatic stop of the cycle as well as
the pressure in the circuit.
The purging cycle activates thecirculator
pump at an alternating rhythm to allow
the displacement and purging of any
air bubbles accumulated at high points
of the installation using the Pilot’s
automatic purger.
AIR BLEED
Activate the backow prevention device of the installation to ll the
heating circuit to just over 1.5 bars of pressure.
The Pilot automatically conrms the lling of the installation once
the pressure reaches 1.6 bars.
A manual conrmation (press ) is possible starting at 0.6
bars of pressure.
5.3.3 - Step 3 : Filling
During the filling stage, the Pilot
indicates the pressure measured in the
heating circuit.
FILLING
The Pilot will indicate when set-up has been achieved:
And will automatically put itself in standby mode.
The Pilot can be left in this state until rst use.
5.3.6 - Step 6 : Finishing set-up
5.4 - First use
To turn on the Pilot, press .
Long pressing puts the Pilot in standby mode.
When the pilot is switched on for the rst time, if heating function
doesn’t work, maybe the pilot is not in «WINTER» mode. You can
verify in the «INSTALLER» menu and change it if necessary.
Do not leave a lling pressure upper than
1.6 bar + 0.1 x (height of the lowest heat
pump relative to the pilot) when the pilot
is standstill.
Pmax = 1,6 + 0,1 x (-2)
= 1,4 bar
=-2m
Pmax = 1,6 + 0,1 x 2
= 1,8 bar
=2m

- 6P10 PILOT MANUAL -
20
6.1 - Control panel
6.1.1 - Keypad
Primary function
(short press)
Secondary function
(long press)
- menu access
- return / cancel
locking / unlocking of the
keypad
- switch on standby mode
- setting the
temperatures
program scheduled
comfort modes
- increase the setting
- scroll up
activate temporary
comfort mode
- conrm / remove error
- display pressure or T°
information on
temperatures and current
operating state
- decrease the setting
- scroll down activation of holiday mode
6.1.2 - Display
c9 character message
eDay of the week: (1= Monday; 2= Tuesday...)
fDisplay zone: temperatures, pressure, settings, time...
dCurrent comfort mode
Programming
active Comfort mode Eco mode
Frost protection
mode Holiday mode
b
c
d
ef
defrosting in progress circulating pump working
ventilator working domestic hot water acti-
vated
compressor working heating activated
power level keypad locked
electrical back-up installer menu
back-up boiler
bSymbols of current operating state
Button Primary function
ex.: decrease / scroll down
Secondary function
ex.: holiday mode
6 - SETTINGS AND FUNCTIONS
This manual suits for next models
1
Table of contents
Popular Controllers manuals by other brands

FIBER SENSYS
FIBER SENSYS Fiber Defender FD508 user manual
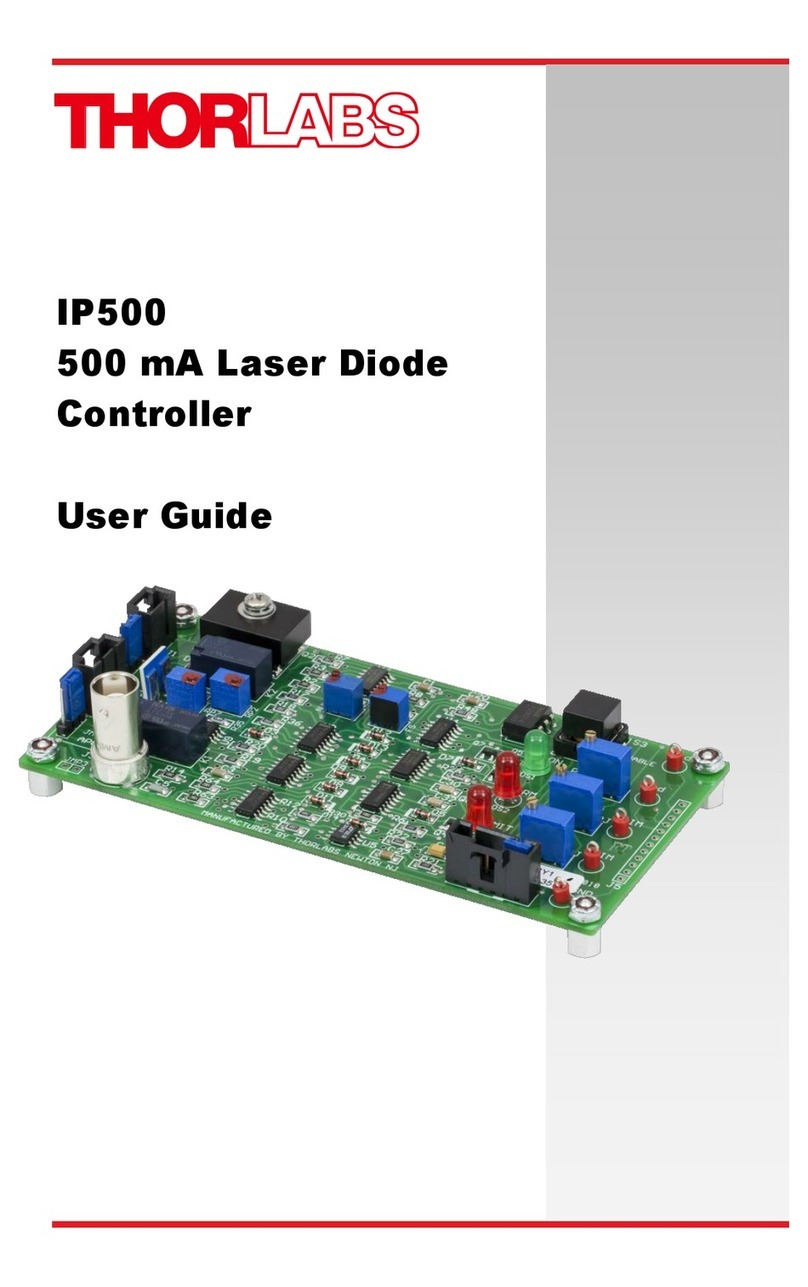
THORLABS
THORLABS IP500 user guide
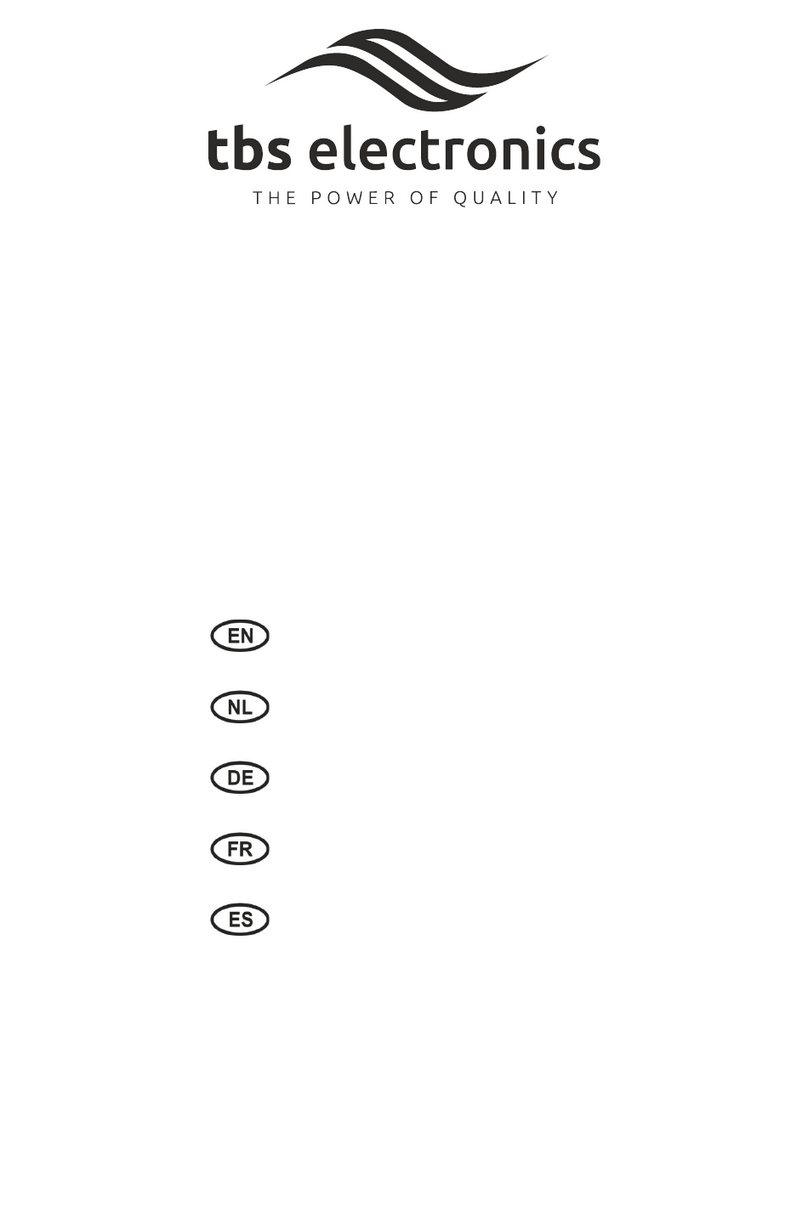
tbs electronics
tbs electronics Omnicharge Solar OCS 150-60 owner's manual
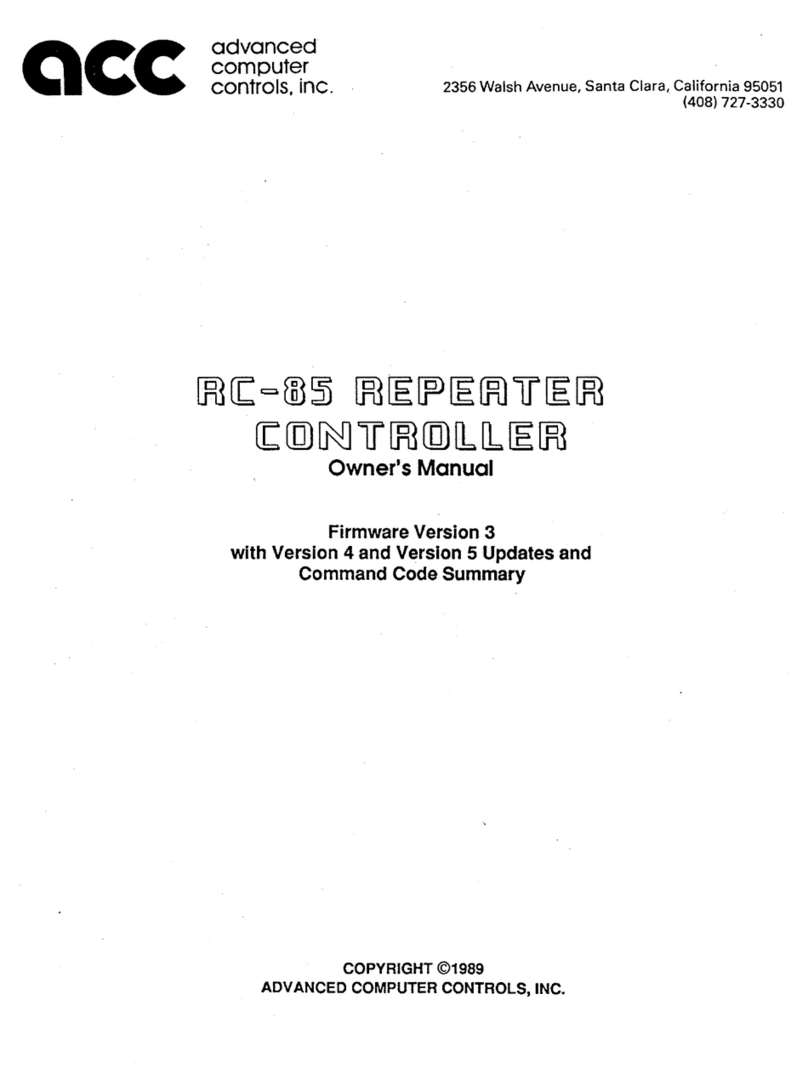
ACC
ACC RC-85 owner's manual
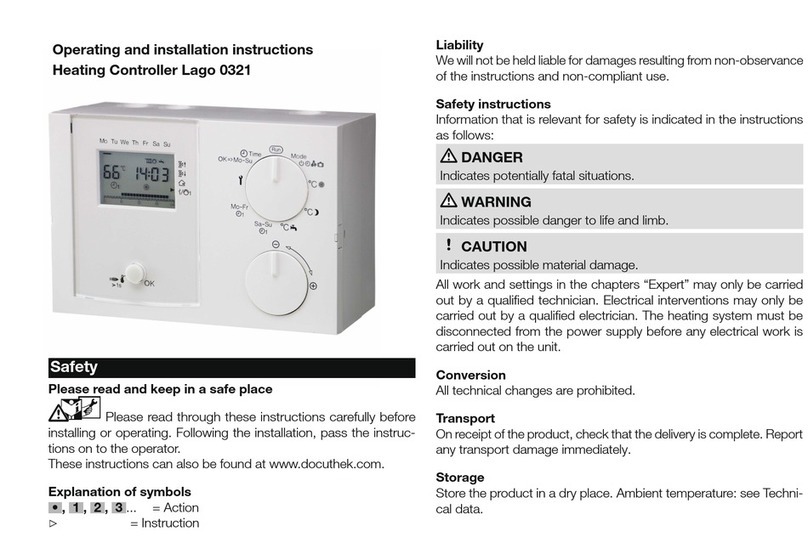
brummerhoop
brummerhoop Lago 0321 Operating and installation instructions
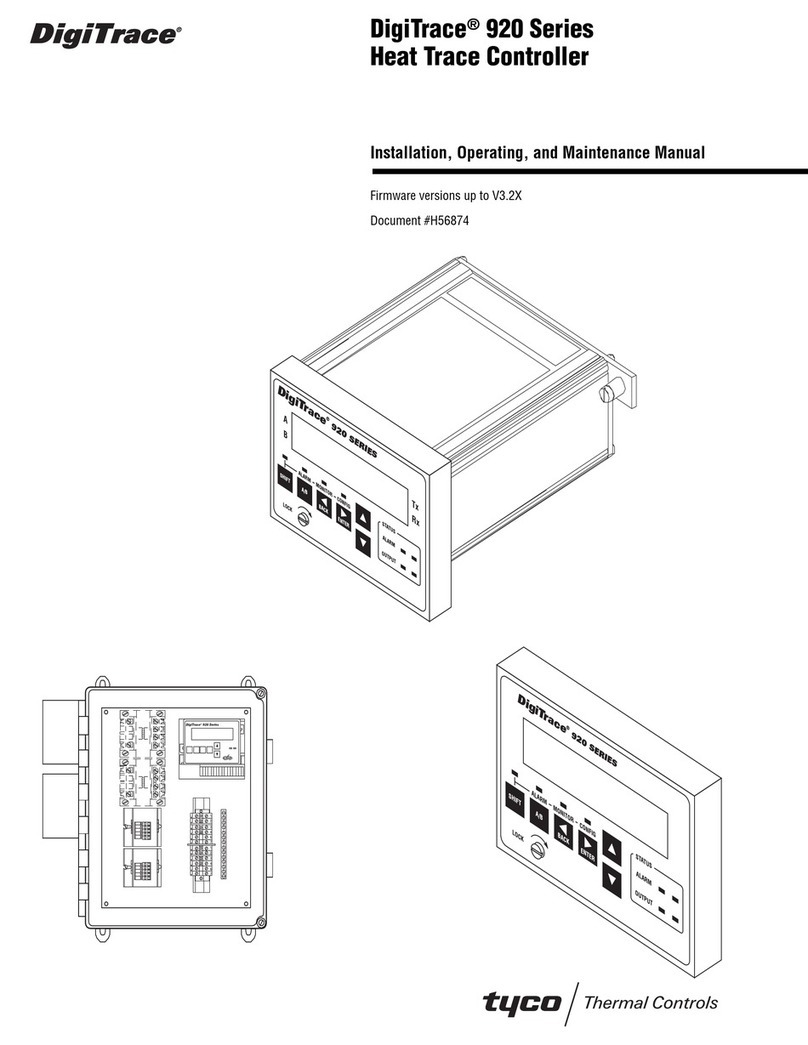
Tyco
Tyco DigiTrace 920 Series Installation, operating and maintenance manual