AVI ASE-A8 User manual

ASE-A8
ENGINE
PERFORMANCE
Disclaimer of Warranties:
This manual contains test procedures and test information obtained by an AS Master Technician with known
good test equipment on real vehicles. Your tests may vary due to your test equipment or procedures. No warranty
can be made from the ideas presented due to personal testing procedures, nor does the author or anyone
connected with him or her assume any responsibilities or liabilities. The use of this manual is conditional on the
acceptance of this disclaimer. If the terms of this disclaimer are not acceptable, please return this manual.
Automotive Video 6280 Arc Way
Ft. Myers, FL 33966
1-800-71-TRA N (1-800-718-7246)
www.auto-video.com
! ! " $ "
$ % 4 $ ! " ! $
! # ! # !
50902


i
ENGINE PERFORMANCE
FOR ASE TEST A8
ASE A8 Task List . . . . . . . . . . . . . . . . . . . . . . . . . . . . . . . . . . . . . . . . ii
&hapter A: General Diagnosis. . . . . . . . . . . . . . . . . . . . . . . . . . . . . . .1
Chapter B: Ignition System Diagnosis and Repair . . . . . . . . . . . . . .34
Chapter C: Fuel, Air Induction and Exhaust Systems
Diagnosis and Repair . . . . . . . . . . . . . . . . . . . . . . . . . . . . . . . . . .53
Chapter D: Emission Control Systems Diagnosis and Repair. . . . .73
Chapter E: Computerized Engine Control Diagnosis
and Repair (Including OBD II) . . . . . . . . . . . . . . . . . . . . . . . . . . . .84
Index . . . . . . . . . . . . . . . . . . . . . . . . . . . . . . . . . . . . . . . . . . . . . . . .112
Sample Test . . . . . . . . . . . . . . . . . . . . . . . . . . . . . . . . . . . . . . . . . .115
Glossary . . . . . . . . . . . . . . . . . . . . . . . . . . . . . . . . . . . . . . . . . . . . 120
Test Answers . . . . . . . . . . . . . . . . . . . . . . . . . . . . . . . . . . . . . . . . .124
Contents

ASE A8TEST PREP TASK LIST
ii!
Content Area
Questions in Test
Percentage of Test
A. General Diagnosis
12
24%
B. Ignition System Diagnosis and Repair
8
16%
C. Fuel, Air Induction and Exhaust Systems
Diagnosis and Repair
9
18%
D. Emissions Control Systems Diagnosis and Repair
(Including OBD II)
1. Positive Crankcase Ventilation (1)
2. Exhaust Gas Recirculation (2)
3. Secondary Air Injections (AIR) and Catalytic
Converter (2)
4. Evaporative Emissions Controls (3)
8
16%
E. Computerized Engine Controls Diagnosis and
Repair (Including OBD II)
13
26%
A. General Diagnosis (12 questions)
1. Verify driver’s complaint, perform visual inspection, and/or road test vehicle; determine needed
action.
2. Research applicable vehicle and service information, such as engine management system operation,
vehicle service history, service precautions, technical service bulletins, and service
campaigns/recalls.
3. Diagnose noises and/or vibration problems related to engine performance; determine needed action.
4. Diagnose the cause of unusual exhaust color, odor, and sound; determine needed action.
5. Perform engine manifold vacuum or pressure tests; determine needed action.
6. Perform cylinder power balance test; determine needed action.
7. Perform cylinder cranking compression test; determine needed action.
8. Perform cylinder leakage/leak-down test; determine needed action.
9. Diagnose engine mechanical, electrical, electronic, fuel, and ignition problems with an oscilloscope,
engine analyzer, and/or scan tool; determine needed action.
10. Prepare and inspect vehicle for HC, CO, CO2, and O2 exhaust gas analysis; perform test and
interpret exhaust gas readings.
11. Verify valve adjustment on engines with mechanical or hydraulic lifters.
12. Verify camshaft timing (including engines equipped with variable valve timing); determine needed
action.
13. Verify engine operating temperature, check coolant level and condition, perform cooling system
pressure test; determine needed repairs.
14. Inspect and test mechanical/electrical fans, fan clutch, fan shroud/ducting, and fan control devices;
determine needed repairs.
15. Read and interpret electrical schematic diagrams and symbols.
16. Test and diagnose emissions or driveability problems caused by battery condition, connections, or
excessive key-off battery drain; determine needed repairs.
17. Perform starter current draw test; determine needed action.
18. Perform starter circuit voltage drop tests; determine needed action.
19. Inspect, test, and repair or replace components and wires in the starter control circuit.
20. Test and diagnose engine performance problems resulting from an undercharge, overcharge, or a no-
charge condition; determine needed action.
21. Inspect, adjust, and replace alternator (generator) drive belts, pulleys, tensioners and fans.
22. Inspect, test, and repair or replace charging circuit components, connectors and wires.

ASE A8TEST PREP TASK LIST
iii!
B. Ignition System Diagnosis and Repair (8 questions)
1. Diagnose ignition system related problems such as no-starting, hard starting, engine misfire, poor
driveability, spark knock, power loss, poor mileage, and emissions problems; determine root cause;
determine needed repairs.
2. Interpret ignition system related diagnostic trouble codes (DTCs); determine needed repairs.
3. Inspect, test, repair, or replace ignition primary circuit wiring and components.
4. Inspect, test, service, repair or replace ignition system secondary circuit wiring and components.
5. Inspect, test, and replace ignition coil(s).
6. Inspect, test, and replace ignition system sensors; adjust as necessary.
7. Inspect, test, and/or replace ignition control module (ICM)/powertrain/engine control module
(PCM/ECM); reprogram as needed.
C. Fuel, Air Induction, and Exhaust System
Diagnosis and Repair (9 questions)
1. Diagnose fuel system related problems, including hot or cold no-starting, hard starting, poor
driveability, incorrect idle speed, poor idle, flooding, hesitation, surging, engine misfire, power loss,
stalling, poor mileage, and emissions problems; determine root cause; determine needed action.
2. Interpret fuel or induction system related diagnostic trouble codes (DTCs); analyze fuel trim and other
scan tool data; determine needed repairs.
3. Inspect fuel tank, filler neck, and gas cap; inspect and replace fuel lines, fittings, and hoses; check
fuel for contaminants and quality.
4. Inspect, test, and replace fuel pump(s) and/or fuel pump assembly; inspect, service, and replace fuel
filters.
5. Inspect and test electric fuel pump control circuits and components; determine needed repairs.
6. Inspect, test, and repair or replace fuel pressure regulation system and components of fuel injection
systems; perform fuel pressure/volume test.
7. Inspect, remove, service or replace throttle assembly; make related adjustments.
8. Inspect, test, clean, and replace fuel injectors and fuel rails.
9. Inspect, service, and repair or replace air filtration system components.
10. Inspect throttle assembly, air induction system, intake manifold and gaskets for air/vacuum leaks
and/or unmetered air.
11. Remove, clean, inspect, test, and repair or replace fuel system vacuum and electrical components
and connections.
12. Inspect, service, and replace exhaust manifold, exhaust pipes, oxygen sensors, mufflers, catalytic
converters, resonators, tailpipes, and heat shields.
13. Test for exhaust system restriction or leaks; determine needed action.
14. Inspect, test, clean and repair or replace turbocharger or supercharger and system components.
D. Emissions Control Systems Diagnosis and Repair
(Including OBD II) (8 questions)
1. Positive Crankcase Ventilation (1 question)
1. Test and diagnose emissions or driveability problems caused by positive crank case ventilation (PCV)
system.
2. Inspect, service, and replace positive crankcase ventilation (PCV) filter/breather cap, valve, tubes,
orifice/metering device, and hoses.
2. Exhaust Gas Recirculation (2 questions)
1. Test and diagnose driveability problems caused by the exhaust gas recirculation (EGR) system.
2. Interpret exhaust gas recirculation (EGR) related scan tool data and diagnostic troublecodes (DTCs);
determine needed repairs.

ASE A8TEST PREP TASK LIST
iv!
3. Inspect, test, service, and replace components of the EGR system, including EGR valve, tubing,
passages, vacuum/pressure controls, filters, hoses, electrical/electronic sensors, controls, solenoids
and wiring of exhaust gas recirculation (EGR) systems.
3. Secondary Air Injection (AIR) And Catalytic Converter (2 questions)
1. Test and diagnose emissions or driveability problems caused by the secondary air injection or
catalytic converter systems.
2. Interpret secondary air injection system related scan tool data and diagnostic troublecodes (DTCs);
determine needed repairs.
3. Inspect, test, service, and replace mechanical components and electrical/electronically-operated
components and circuits of secondary air injection systems.
4. Inspect catalytic converter. Interpret catalytic converter related diagnostic trouble codes (DTCs);
analyze related scan tool data to determine root cause of DTCs; determine needed repairs.
4. Evaporative Emissions Controls (3 questions)
1. Test and diagnose emissions or driveability problems caused by the evaporative emissions control
system.
2. Interpret evaporative emissions-related scan tool data and diagnostic trouble codes (DTCs);
determine needed repairs.
3. Inspect, test, and replace canister, lines/hoses, mechanical and electrical components of the
evaporative emissions control system.
E. Computerized Engine Controls Diagnosis and Repair
(Including OBD II) (13 questions)
1. Retrieve and record diagnostic trouble codes (DTCs), OBD II monitor status and freeze frame data.
2. Diagnose the causes of emissions or driveability problems with stored or active diagnostic trouble
codes (DTCs).
3. Diagnose the causes of emissions or driveability problems without diagnostic troublecodes (DTCs).
4. Use a scan tool, digital multimeter (DMM), or digital storage oscilloscope (DSO) to inspect or test
computerized engine control system sensors, actuators, circuits, and powertrain/engine control
module (PCM/ECM); determine needed repairs.
5. Measure and interpret voltage, voltage drop, amperage, and resistance using digital multimeter
(DMM) readings.
6. Test, remove, inspect, clean, service, and repair or replace power and ground distribution circuits and
connections.
7. Remove and replace the powertrain/engine control module (PCM/ECM); reprogram as needed.
8. Diagnose driveability and emissions problems resulting from failures of interrelated systems (for
example: cruise control, security alarms/theft deterrent, torque controls, traction controls, torque
management, A/C, non-OEM installed accessories).
9. Clear diagnostic trouble codes (DTCs), run all OBD II monitors, and verify the repair.

1
Chapter A
GENERAL DIAGNOSIS
Poor engine performance can be the result of a long list
of problems. Performance, or driveability problems may
be indicated by customer complaints of no starting,
hard starting, loss of power, poor fuel mileage, engine
knock, or engine misfire. Begin diagnosis by getting
specific information from the customer. Find out the
exact nature of the problem, under what conditions it
occurs, and when the symptoms first started.
CUSTOMER INTERVIEW
This first step in the process is crucial to diagnosing au-
tomotive concerns as it helps you get a clear under-
standing of the situation. Use the following procedures
to begin every diagnosis:
•Verify the concern
•Research the history of the concern
•Ask the customer what they think the problem is
•Verify the information you have gathered
One of the most important steps in diagnosis is to veri-
fy the customer's concern. Often a driver's description
lacks some of the information necessary to begin prop-
er diagnosis. You might misunderstand the driver's de-
scription or the symptom may be caused by circum-
stances that you might not encounter during a typical
operation check or test drive.
The best solution is for the driver to demonstrate the
problem for you or the service advisor. If that is not prac-
tical, question the driver about exactly when the prob-
lem occurs. This information can lead you to drive the
vehicle under the same conditions and with an opera-
tional check, you can verify the concern and begin to
move to the proper subsystem to begin your diagnosis.
A rational diagnostic procedure must be followed to
successfully diagnose a customer's complaint. By fol-
lowing logical procedures you can use your time more
efficiently and replace or repair the right components.
Improper diagnosis leads to come-backs, dissatisfied
customers, a waste of your time and your customer's
time.
Before attempting to repair a performance problem,
make sure the engine is in sound mechanical condition.
In addition to internal engine defects, driveability prob-
lems may be caused by a malfunction in the electrical,
fuel, ignition, or emission control systems. Accurate
troubleshooting information for the vehicle being ser-
viced is essential for testing and evaluating all systems.
After determining that there is a driveability problem,
take a systematic approach to solving it. Work in a log-
ical manner to not only repair the problem, but also elim-
inate any other conditions that may have contributed to
the failure. To diagnose performance problems, follow
these four steps:
•Preliminary inspection
•Road test
•Review vehicle service history and applicable sup-
port materials
•Comprehensive engine testing
PRELIMINARY INSPECTION
Eliminate any obvious problems by performing an
under-hood inspection. The source of noise or vibration
complaints will often be revealed by a visual inspection.
Problems such as rough running or stalling may be
caused by a broken or disconnected vacuum hose or
electrical wire. When performing an inspection, check
for the following:
•Drive belts that are properly tensioned and free of
cracks, frayed edges, and glazing
•Electrical connections that are secure and clean. In-
spect harnesses for signs of brittle insulation, rub-
bing, and broken or damaged wires
•Engine-mounted accessories that are properly sup-
ported; look for loose or missing bolts, worn bush-
ings, and loose or broken support brackets
•Engine mounts, torque struts, and vibration
dampers that are in good condition and securely at-
tached
•Hoses, water and vacuum, that are tight and prop-
erly routed. Replace any that are loose, brittle,
kinked, broken, or otherwise damaged

Chapter A: General Diagnosis
2
•Fuel lines, hoses, and fittings that are free of leak-
age and damage
•Battery, cables, and connections that are tight and
free of corrosion. Also, check the battery electrolyte
level and state-of-charge
•Secondary ignition cables, as well as the distributor
cap and coils, that are free of cracks, insulation
damage, corrosion, and loose connections
•Air filter element and ductwork that are clear and
able to supply a good flow of unrestricted air
•Emission control system components that are prop-
erly installed and connected. Repair any brittle,
burned, or damaged hoses and loose fittings
Also look the engine over for any signs of leakage. Ver-
ify coolant leaks by pressure testing the cooling system.
Check the level of the engine oil and coolant, and look
for indications of dilution and contamination. Oil dilution
is generally caused by raw fuel entering the crankcase.
Look for a high fluid level and thin consistency accom-
panied by the odor of gasoline. Coolant leaking into the
crankcase mixes with the oil to create a milky, brown-
colored emulsion. Either condition, dilution or coolant
contamination, indicates internal engine problems.
Start the engine and allow it to idle while listening for any
unusual noises. A stethoscope is a handy tool for iso-
lating top-end and bottom-end engine noises. To isolate
difficult noises, connect a timing light and listen. Bot-
tom-end noise will cycle in time with the flashing of the
light. Top-end sounds will be audible with every other
flash of the light.
While the engine is running, check the exhaust for indi-
cations of internal engine problems. Check for:
• Black smoke. This is caused by a rich air-fuel ratio,
and is often accompanied by the "rotten egg" smell
of an overworked catalytic converter
•Blue smoke. This indicates excessive oil burning
and often gives off a pungent odor
•Cloudy white exhaust. This is often the result of en-
gine coolant leaking into the combustion chamber.
Burning coolant also produces a distinctive chemi-
cal odor. Check the temperature gauge for over-
heating
•Listen closely to the sound of the exhaust system.
Be especially conscious of irregular pulses or
whistling sounds that may indicate valve problems
or a restricted exhaust
If everything looks good and there are no obvious prob-
lems, the vehicle is ready for a road test.
ROAD TEST
Whenever possible, let the customer accompany you on
the road test. The customer knows the vehicle and can
point out abnormal sounds, vibrations, and other an-
noyances that might be overlooked or considered nor-
mal.
Conduct a thorough road test; one quick lap around the
block is not enough. The engine must be brought to nor-
mal operating temperature, and the test drive should in-
clude a stop-and-go city driving cycle and a period of
cruising at highway speed. Proper road testing is ex-
tremely important for vehicles equipped with onboard
diagnostics. An incomplete test may not record all of the
intermittent, or soft, fault codes. A complete road test
should take about 15 minutes. If possible, use the same
route for all tests so that performance can be compared
before and after service, as well as to the performance
of similar vehicles. If a dynamometer is available, use it
to simulate the road test.
When a problem occurs while driving, note the operat-
ing conditions. Modulate engine and road speed to help
isolate the symptoms. Use the nature of the problem to
determine which diagnostic tests to perform. The tests,
and the order in which they are performed, depend on if
the suspected problem is in the:
•Electrical or electronic system
• Internal engine
•Ignition system
• Fuel system
• Emission control system
VEHICLE SERVICE INFORMATION
Resource materials should be readily available when
performing diagnostic procedures. Resource materials
and information should include:
•Service History
•Service Manuals
•Diagnostic Manuals
•Wiring Diagrams
•Technical Service Bulletins
•Online Technical Support
The vehicle service history may be found in various
ways. Ask the customer if they have copies of repair or-
ders for previous service work. OEM warranty systems
track all repairs completed under warranty and provide
good details of the problems serviced in the past.

Chapter A: General Diagnosis
3
Most manufacturers also provide some type of Diag-
nostic Manual for the vehicle or vehicle family. Typically
these manuals are for specific automotive systems such
as electrical, fuel injection, and emissions/performance.
Technical
Service
Bulletin
SUBJECT:
Sags/Hesitation/Stumble/Start & Stall
OVERVIEW:
This bulletin involves selectively erasing and reprogramming the Powertrain Control
Module (PCM) with new software (calibration changes).
MODELS:
2003 Minivan and Truck
NOTE: THIS INFORMATION APPLIES TO VEHICLES EQUIPPED WITH A 3.34L ENGINE.
SYMPTOM/CONDITION:
Sags/Hesitation/Stumble or Start & Stall after a cold start in ambient temperatures of -7° -
30° C (20° - 86° F). The sag/hesitation or stumble may persist for up to a minute into a drive cycle
and is attributed to high driveability index (Dl) fuel.
DIAGNOSIS:
Using the Diagnostic System and or a Diagnostic Scan Tool with the appropriate Diagnosti
c
Procedures Manual, verify all engine/transmission systems are functioning as designed. I
f
Diagnostic Trouble Codes (DTC's) are present, record them on the repair order and repair as
necessary before proceeding further with this bulletin. If no DTC's are present and the custome
r
has described the above symptoms, perform the Repair Procedure.
NOTE: WHENEVER A POWERTRAIN CONTROL MODULE (PCM) IS REPLACED
DUE TO FAILURE, THE SOFTWARE OF THE REPLACEMENT CONTROLLER
MUST BE VERIFIED FOR THE LATEST REVISION LEVEL. USE THE FLASH
PROCEDURE TO UPDATE REPLACED CONTROLLERS AS NECESSARY.
PARTS REQUIRED:
1 14465020 Label, Authorized Software Update
1 54266086 Label, Authorized Modification
Fig. 1-1. Typical TSB.
Every vehicle has a specific Service Manual. These-
manuals contain general service information, and often
specific diagnostic and troubleshooting procedures for
each system within the vehicle, such as the emission or
fuel system.

Chapter A: General Diagnosis
4
Fuel and EVAP Pipe Caution
In order to reduce the risk of fire and personal injuryob-
serve the following items:
•Replace all nylon fuel pipes that are nicked,
scratched, or damaged during installation. Do not
attempt to repair the sections of the nylon fuel pipes
•Do not hammer directly on the fuel harness body
clips when installing new fuel pipes. Damage to the
nylon pipes may result in a fuel leak. Always cover
nylon vapor pipes with a wet towel before using a
torch near them
•Apply a few drops of clean engine oil to the male
pipe ends before connecting fuel pipe fittings. This
will ensure proper reconnection and prevent a pos-
sible fuel leak
Fuel Gauge Leak Caution
Wrap a shop towel around the fuel pressure connection
in order to reduce the risk of fire and personal injury. The
towel will absorb any fuel leakage that occurs during the
connection of the fuel pressure gauge. Place the towel
in an approved container when the connection of the
fuel pressure gauge is complete.
Relieving Fuel Pressure Caution
Relieve the fuel system pressure before servicing fuel
system components in order to reduce the risk of fire
and personal injury. After relieving the system pressure,
a small amount of fuel may be released when servicing
the fuel lines or connections. In order to reduce the
chance of personal injury, cover the regulator and the
fuel line fittings with a shop towel before disconnecting.
This will catch any fuel that may leak out.
Handling ESD Sensitive Parts Notice
Electrostatic discharge (ESD) can damage many solid-
state electrical components. ESD susceptible compo-
nents may or may not be labeled with the ESD symbol.
Handle all electrical components carefully. Use the fol-
lowing precautions in order to avoid ESD damage:
•Touch a metal ground point in order to remove your
body's static charge before servicing any electron-
ic component
•Do not touch exposed terminals. Terminals may
connect to circuits susceptible to ESD damage
•Do not allow tools to contact exposed terminals
when servicing connectors
•Do not remove components from their protective
packaging until necessary
These manuals are more in-depth than Service Manuals
as they provide component descriptions and operation
theory along with the applicable troubleshooting proce-
dures.
Some manufacturers dedicate separate publications for
wiring diagrams rather than include them in the other
manuals. Either way, the wiring diagrams or schematics
are required for making most every electrical or elec-
tronic repair throughout the vehicle.
Technical Service Bulletins (TSB's) cover information
discovered after the Service and/or Diagnostic Manuals
were printed, figure 1-1. Always consult TSB's for infor-
mation about known vehicle concerns or improvements
for the most up-to-date information available.
Today there are several online technical support ser-
vices that compile repair information and TSB's for
many vehicles. There is a nominal charge to access
these services however many times the benefit far out-
weighs the cost.
SERVICE PRECAUTIONS AND WARNINGS
Cautions and Warnings
The diagnosis and repair procedures in the vehicle Ser-
vice Manuals generally contain both general and spe-
cific cautions and/or warnings. The information is
placed at strategic locations throughout most Service
Manuals and is designed to prevent the following from
occurring:
•Serious bodily injury to the technician
•Serious bodily injury to the driver and/or passen-
ger(s) of the vehicle, if the vehicle has been improp-
erly repaired
Some manuals will contain more cautions and/or warn-
ings while others may have few included. Following are
a few examples of the cautions or warnings you may
see.
Battery Disconnect Caution
Before servicing any electrical component, the ignition
key must be in the OFF or LOCK position and all elec-
trical loads must be OFF, unless instructed otherwise in
these procedures. If a tool or equipment could easily
come in contact with a live exposed electrical terminal,
also disconnect the negative battery cable. Failure to
follow these precautions may cause personal injury
and/or damage to the vehicle or its components.

Chapter A: General Diagnosis
5
Avoid the following actions unless required by the diag-
nostic procedure:
•Jumpering or grounding of the components or con-
nectors
•Connecting test equipment probes to components
or connectors
•Connect the ground lead first when using test
probes
•Ground the protective packaging of any component
before opening
•Resting solid-state components on metal work-
benches, or on top of TVs, radios, or other electri-
cal devices
Ignition OFF When Disconnecting Battery
Always turn the ignition OFF when connecting or dis-
connecting battery cables, battery chargers, or jumper
cables. Failing to do so may damage the Powertrain
Control Module (PCM) or other electronic components.
Electric Coolant Fan Caution
An electric fan under the hood can start up even when
the engine is not running and can injure you. Keep
hands, clothing, and tools away from any underhood
electric fan.
COMPREHENSIVE ENGINE TESTING
It is important to follow instructions from both the vehi-
cle and the test equipment manufacturers when per-
forming engine tests. Some tests require the ignition to
be disabled while the starter motor cranks the engine.
Others may require bypassing the fuel pump relay, idle
speed controller, or some other electrical or electronic
component. The proper test equipment, and the knowl-
edge to use it correctly, are essential.
The following are general guidelines for performing
comprehensive engine tests. For some tests, more de-
tailed procedures can be found in other books in this
series. The tests here are not presented in any specific
order. The sequence in which they are performed will
vary.
Unusual Engine Noises
Engine noises can be divided into two general cater-
gories: those that originate in the top end of the engine,
and those that originate in the bottom end of the engine.
Begin engine noise diagnosis by determining where in
the engine the noise is coming from. Bottom end, or
crankcase, noises occur at crankshaft speed, so they
tend to produce a high-frequency knock or rumble. Top
end, or valve train, noises occur at a lower frequency
because these parts operate at one-half crankshaft
speed.
A stethoscope is a handy tool for isolating noises. You
can also use a timing light to determine whether a noise
is from the top or bottom end of the engine. Connect the
timing light and listen . If the engine noise cycles in time
with the flashing light, the sound is coming from the bot-
tom end. Sounds that are audible with every other flash
of the timing light originate in the top end of the engine.
Top-End Noises
The top end of a healthy engine produces a high
pitched, whirring noise with a very rapid and much
fainter sewing machine like clicking coming from the
valves. The more valves the engine has and the higher
the idle speed, the more the individual clicks will blend
into a consistent drone. Any deviation is abnormal and
indicates a problem. Listen for:
•An irregular clacking or knocking noise caused by
excessive camshaft endplay
•An irregular slapping or thumping at the front of the
engine caused by a loose timing belt. A tight belt
makes a whirring, whining, hum that rises and falls
in pitch with RPM
•A single, clear clack whenever a particular valve
opens can be a collapsed lifter or a broken valve
spring.
•A loud, cycling, valve rattle that you can hear over
the normal valve noise can indicate either worn
valve guides or rocker arm pivots
Low pressure or restricted oil flow will produce an ex-
cessively loud, rhythmic clatter
Bottom-End Noises
Healthy engines produce an evenly pitched, rapid,
whirring sound and nothing else. Knocking or thumping
noises are signs that something is wrong. In general,
bottom-end noise can be caused and indicated by:
•An irregular knock at idle that can be made louder
or fainter by playing with the clutch pedal indicates
too much crankshaft endplay
•A sharp clattering knock that may be continuous at
idle or only appear when the throttle closes sud-
denly, can indicate a bad connecting rod bearing.
The noise will diminish if the spark plug for the of-
fending cylinder is grounded
•A hollow metallic clatter that is loudest when the en-
gine is cold may be piston slap caused by too much
piston to cylinder wall clearance. Grounding the
spark plug of the affected cylinder will often make
piston slap louder because it eliminates the cush-

Chapter A: General Diagnosis
6
ioning of the extra gas pressure pushing on the pis-
ton
•A sharp knocking that stands out most at idle can
indicate a wrist pin that is loose in its bore. Ground-
ing the spark plug of the affected cylinder makes
the knock audible at top dead center as well as bot-
tom dead center. Retarding the spark decreases
wrist pin noise
•A rapid, steady dull pounding that increases with
load is typical of worn main bearings
Spark Knock
Spark knock, which is caused by uncontrolled combus-
tion, sounds like a metallic pinging noise. Spark knock
may be heard under a heavy load or on acceleration.
Detonation occurs when combustion of the air/fuel mix-
ture in the cylinder starts off correctly in response to ig-
nition by the spark plug, but one or more pockets of the
air/fuel mixture explode outside the envelope of the nor-
mal combustion. The collision of the two flame causes
a pinging noise. This can be caused by:
•Fuel with two low of octane rating
•Ignition timing that is to far advanced
•High engine operating temperature
•Excessive carbon build up in the combustion cham-
ber
Preignition occurs when the air/fuel mixture premature-
ly ignites before the spark plug fires. Then the spark plug
ignites the remaining mixture at the normal time. When
the two portions of burning mixture meet each other,
there is a sudden abnormal rise in cylinder pressure
causing engine vibration and a pinging noise. This can
be caused by:
•Hot spots in the combustion chamber
•Incorrect heat range spark plug
•Carbon deposits in the combustion chamber
Unusual Exhaust Color and Odor
Although a healthy catalytic converter can do a good job
of cleaning up the exhaust, you can tell something
about the internal engine condition by checking for un-
usual smoke or smells:
•Black exhaust smoke. This is caused by a rich
air/fuel mixture and is often accompanied by the
"rotten egg" smell of an overworked catalytic con-
verter
•Blue exhaust smoke indicates excessive oil burn-
ing, which gives off a pungent odor
•Cloudy white exhaust is often the result of engine
coolant leaking into the combustion chamber. Burn-
ing coolant also produces a distinctive chemical
odor. Check the temperature gauge for overheating
Keep in mind that oil vapor odors are not always the re-
sult of an internal engine problem. A clogged or mal-
functioning positive crankcase ventilation (PCV) system
can not only produce a burning oil smell, but can also
cause excessive crankcase vapor and increase oil con-
sumption. Always check all external sources before you
condemn the engine.
Internal Engine Diagnosis
Specific internal mechanical problems on a running en-
gine can be located by performing several basic tests.
To eliminate the possibility of internal engine problems,
performing the following tests:
•Intake manifold vacuum
•Cylinder compression
•Cylinder leakage
•Cylinder power balance
A brief description of standard test procedures and in-
terpreting results will be presented here.
Intake Manifold Vacuum Tests
Manifold vacuum tests are performed by connecting a
vacuum gauge to the intake manifold downstream of
the throttle plates. The gauge records the difference
between atmospheric pressure and manifold pressure.
Vacuum gauge readings can pinpoint manifold and
vacuum line leaks, valve and valve guide problems, in-
correct ignition and valve timing, exhaust restrictions,
and poor combustion chamber sealing.
A vacuum gauge is usually calibrated in inches of mer-
cury (in-Hg) or kilopascal (kPa). Normal vacuum at idle
is from 15 to 21 in-Hg (50 to 70 kPa) for most engines.
Gauge readings should be steady and decrease as the
throttle opens. Vacuum decreases as elevation in-
creases, and gauge readings must be corrected ac-
cordingly. Manufacturers provide specifications for
testing at sea level. To correct for altitude, subtract one
in-Hg (3.377 kPa) for every 1,000 feet (305 meters)
above sea level.
Some engines, especially if turbocharged or super-
charged, require a measure of manifold boost pressure
test. Boost pressure, also known as positive pressure,
specifications are provided by the manufacturer.
Gauges for reading manifold absolute pressure (MAP)
pressure may be calibrated differently than vacuum
gauges. Absolute pressure uses a reference point of
zero pressure, or total vacuum, regardless of atmos-
pheric pressure.
Refer to Book A1 "Engine Repair" in this series for more
detailed information on manifold vacuum test proce-
dures and results.

Chapter A: General Diagnosis
7
Cylinder Power Balance Test
The Powertrain Control Module (PCM) in most latemod-
el vehicles incorporates the ability to conduct a power
or cylinder balance test utilizing a diagnostic scan tool.
The scan tool commands the PCM to run the test either
automatically or manually at the operator's discretion.
Each cylinder is disabled by shutting off the fuel and in
some cases the spark to the cylinder being tested. The
average RPM drop is displayed on the scan tool screen
and can be related directly to the contribution of that
cylinder.
Most older engine analyzers have the capability of per-
forming a power balance test, figure 1-2. The balance
test shows if an individual cylinder or a group of cylin-
ders is not producing its share of power. During the test,
the spark plug is shorted so there are no power strokes
from the cylinder being tested. Results are measured in
terms of engine RPM drop, manifold vacuum drop, or a
combination of these factors.
If the changes in engine RPM and manifold vacuum are
about the same for each cylinder, the engine is in good
mechanical condition. If the changes for one or more
cylinders are noticeably different, the engine has a prob-
lem. The fault may be mechanical, or it may be in the ig-
nition or fuel systems.
A power balance test is not conclusive; further tests are
needed to pinpoint the problem. The procedure can be
a time saver because it is performed on a running en-
gine. An engine that passes a cylinder balance test will
have fairly even compression so there is usually no need
to perform compression and cylinder leakage tests.
Cylinder Compression Tests
The compression test reveals how well each cylinder is
sealed by the piston rings, valves, cylinder head gasket,
and the spark plug. Compression pressure is measured
in pounds per square inch (psi), kilopascal (kPa), or bars.
The following quantities are equal to each other: 14.5
psi, 100 kPa, and 1 bar. A compression gauge measures
the amount of air pressure that a cylinder is capable of
producing.
Compression test specifications and procedures for an
engine are normally provided in the vehicle Service
Manual. Follow the steps in the Service Manual to pre-
pare the engine for a compression test, then install the
compression tester, figure 1-3, and run the test.
In general, a compression test is performed with the en-
gine at normal operating temperature, all spark plugs re-
moved, the ignition disabled, the battery fully charged,
and the throttle held in wide-open position. Interpret
compression gauge readings as follows:
•Compression is normal when the gauge shows a
steady rise to the specified value with each com-
pression stroke
•If the compression is low on the first stroke and
builds up gradually with each succeeding stroke,
but not to specifications, the piston rings or cylinder
walls are probably worn
•A low compression reading on the first stroke that
builds up only slightly on the following strokes indi-
cates sticking or burned valves
•Two adjacent cylinders with equally low compres-
sion indicates a head gasket leak between them
•A higher than normal compression reading usually
means excessive carbon deposits have formed on
the piston top or in the combustion chamber. Fluid,
such as oil, coolant, or fuel in a cylinder also pro-
duces high compression pressure
Fig. 1-3. Compression tester gauge installed in the spark plug hole.
Fig. 1-2. Typical engine analyzer power balance panel.

Chapter A: General Diagnosis
8
Cylinder Leakage Test
A cylinder leakage tester, or leak-down tester, gives
more detailed results than a compression test. Used as
a follow-up to compression testing, a leakage test can
reveal:
•The exact location of a compression leak
•How serious the leak is in terms of a percentage
of total cylinder compression
The tester forces air into the combustion chamber
through the spark plug hole. A gauge installed in the air
line indicates how much pressure leaks out of the com-
bustion chamber. The gauge scale is graduated from 0
to 100 percent.
Calibrate the leakage tester according to the equipment
instructions before testing. To test a cylinder, the piston
must be at TDC of the compression stroke so that both
valves are closed. Install the test adapter in the spark
plug opening, connect the air hose, and pressurize the
cylinder. Note the percentage reading on the scale and
interpret as follows:
0-10 percent Good
10-20 percent Fair
20-30 percent Poor
30-100 percent Failed!
For cylinders with more than 20-percent leakage, pin-
point the cause of the leaks as follows:
•Air escaping through the air intake indicates a leak-
ing intake valve
•Air escaping through the exhaust indicates a leak-
ing exhaust valve
•Air escaping through the crankcase and PCV sys-
tem indicates worn or damaged piston rings, worn
cylinder walls, or a worn or cracked piston
•Air bubbles in the coolant indicates a leaking head
gasket or a crack in the engine block or cylinder
head casting
•High readings on two adjacent cylinders indicates
head gasket leakage or a casting crack between
cylinders
Ignition System Diagnosis
The automotive ignition system consists of a low-volt-
age primary circuit and a high-voltage secondary circuit.
Voltage varies within these circuits during operation. An
oscilloscope displays voltage changes during a period
of time, and is an ideal instrument for testing ignition
system operation.
Traditional automotive oscilloscopes are installed in
multifunction engine analyzer units that also contain
voltmeters, ammeters, ohmmeters, tach-dwell meters,
vacuum and pressure gauges, timing lights, and ex-
haust analyzers. Small hand-held oscilloscopes that can
also monitor the low-voltage signals of the engine man-
agement system are gaining in popularity.
All oscilloscopes work on the same principle; a voltage
trace of the system being tested is displayed on a view-
ing screen. Voltage traces are displayed as a graph of
voltage over time. The vertical scale on the screen rep-
resents voltage and the horizontal scale indicates time.
The voltage range of the scope is generally adjustable.
Primary circuits are measured in volts and secondary
circuits in kilovolts (kV), or thousands of volts. Time is
measured either as a percentage of one complete en-
gine cycle or in milliseconds (mS), thousandths of a sec-
ond.
An ignition system voltage trace, both primary and sec-
ondary, is divided into three sections, firing, intermedi-
ate, and dwell, figure 1-4. Deviations from a normal pat-
tern indicate a problem. In addition, most scopes will
display ignition traces in three different patterns. Each
pattern is best used to isolate and identify particular
kinds of malfunctions. The three basic patterns are:
•Superimposed pattern
•Parade pattern
•Stacked or raster pattern
In a superimposed pattern, voltage traces for all cylin-
ders are displayed one on top of another to form a sin-
gle pattern, figure 1-5. This display provides a quick
overall view of ignition system operation and can also
reveal certain major problems.
The parade pattern displays voltage traces for all cylin-
ders one after another across the screen from left to
Fig. 1-4. Primary and secondary ignition oscilloscope patterns.

Chapter A: General Diagnosis
9
right in firing order sequence, figure 1-6. This allows
easy comparison of voltage levels between cylinders. A
parade display is useful for diagnosing problems in the
secondary circuit.
A raster pattern shows the voltage traces for all cyliders
stacked one above another in firing order sequence, fig-
ure 1-7. This display allows you to compare the time pe-
riods of the three sections of a voltage trace.
Primary Ignition Patterns
Primary scope patterns are displayed as a low-voltage
trace moving from left to right across the screen. Elec-
tronic ignition patterns vary by system, so it is important
to know what is normal for the system being tested.
Scope manufacturers generally provide sample patterns
for comparison.
Firing Section
The firing section of the pattern corresponds to the
amount of time the spark plug is firing. The voltage trace
records induced voltage surges in the primary circuit as
secondary voltage is being dissipated from the coil. A
typical pattern begins with a vertical rise as spark is es-
tablished, which is followed by a series of diminishing
oscillations until the spark is extinguished, figure 1-8.
With some electronic ignition systems, there are no os-
cillations. Firing is displayed as a vertical spike followed
by a relatively flat line until the spark ends. In parade dis-
play, the height of the oscillations should not vary be-
tween cylinders.
FIRING
SECTION
INTERMEDIATE
SECTION
DWELL
SECTION
ALL CYLINDERS
90
60
80
50
70 60
40
50
30
40 30
20
20
10
4 CYL
6 CYL
8 CYL
0
0
0
45 40 35 30 25 20 15 10
FIRING ORDER
4
2
6
3
5
1
25
20
15
10
Fig. 1-7. The raster pattern stacks the cylinder traces on top of one
another.
Fig. 1-5. All cylinder traces are displayed one on top of another in a
superimposed pattern.
Fig. 1-6. Cylinder traces are displayed one after another in a parade
pattern.
Intermediate Section
The intermediate section begins when the spark stops
and continues until the primary circuit is switched on by
an electronic signal, figure 1-9. Some ignition systems
do not have an intermediate section, and the primary
circuit is switched on the moment the spark is extin-
guished.
The voltage trace is created by the dissipation of ener-
gy remaining in the coil after firing. A series of diminish-
ing oscillations, similar to the firing section but consid-
erably smaller, is normal.
Dwell Section
The dwell section is the time the primary circuit is com-
plete and a low-voltage current flow is building up the
magnetic field of the coil. The trace should drop sharply

Chapter A: General Diagnosis
10
to level off in a relatively flat horizontal line. Dwell ends
with the abrupt upward stroke of the first firing oscilla-
tion.
Use the raster pattern to compare the dwell period for
each cylinder. Dwell sections should not vary by more
than four to six degrees between cylinders. Variations
can be caused by a worn distributor, timing chain, or
faulty crankshaft position sensor (CKP).
Secondary Ignition Patterns
Secondary voltage traces also move left to right across
the screen in firing, intermediate, and dwell sequence.
Oscillations are displayed on a high-voltage scale. Nor-
mal firing voltage with an electronic ignition system can
exceed 40 kV.
Firing Section
The firing section of the secondary pattern begins with
a straight vertical line that indicates the amount of volt-
age required to create an arc across the spark plug air
gap. This is called the firing line or voltage spike. When
the arc is established, less voltage is required to main-
tain it and the trace drops to about one-quarter the
height of the voltage spike, then continues horizontally
as the sparkline. The sparkline, which represents con-
tinued current across the spark plug gap, may have a
series of very small oscillations.
Intermediate Section
The secondary intermediate trace indicates excess coil
voltage being dissipated and is similar to that of the pri-
mary ignition pattern. Look for a short vertical rise from
the sparkline followed by diminishing oscillations. Os-
cillations should be of relatively even width and taper
down gradually to a near horizontal line. The intermedi-
ate section ends as the primary circuit is switched on.
Dwell Section
The dwell section begins as the primary circuit is
switched on and continues until the firing section be-
gins. A typical trace pattern shows the switching as a
sharp downward spike followed by a series of small d
minishing oscillations that level off to a near flat line.
The length of the dwell section and the trace pattern
may be engine speed dependent, and varies for diffe
ent systems, figure 1-10. Some switching signals pro-
duce a series of oscillations; others do not. All begin
with a sharp vertical drop and continue as a nearly flat
horizontal line.
SPARK BEGINS
FIRING SECTION
SPARK ENDS
FIRING LINE
DIMINISHING
OSCILLATIONS
Fig. 1-8. A normal primary circuit firing trace.
PRIMARY CIRCUIT
SWITCHES ON
INTERMEDIATE
SECTION
SPARK ENDS
Fig. 1-9. The intermediate section begins as the spark extinguishes
and continues until the primary circuit is switched on.
Fig. 1-10. Dwell time increases with engine speed on some
electronic control systems.

Chapter A: General Diagnosis
11
Fuel System Diagnosis
Fuel system malfunctions can cause an assortment of
driveability problems, such as engine surging, stalling
and misfiring, hard or no starting, and poor fuel mileage.
A restriction somewhere in the fuel or air supply is often
the cause. Pressure testing is the most effective way to
locate fuel supply problems. Test procedures are cov-
ered in Chapter Three of this book.
The results of engine diagnostic tests, such as manifold
vacuum, cylinder power balance, oscilloscope analysis,
exhaust gas analysis, and onboard diagnostics, may in-
dicate fuel system problems.
When checking manifold vacuum, look for an oscillat-
ing needle with a reading slightly below normal at idle.
This indicates an incorrect fuel mixture. A defective port
fuel injector can cause a cylinder with good compres-
sion to show poor power balance test results. Onboard
diagnostic tests can reveal faults in the electronic cir-
cuits. For oscilloscope patterns that indicate fuel prob-
lems, refer to Ignition System Diagnosis discussed pre-
viously.
Electrical System Diagnosis
Hard starting, no start, and slow cranking speed can in-
dicate an electrical problem. Check the battery, starting
system, and charging system. Specific testing proce-
dures are covered in Chapter Six of this book. Most
minor electrical and electronic system malfunctions can
be detected by self-diagnostic and scan tool testing. In-
dividual components are tested with a digital multime-
ter (DMM), or oscilloscope. Component testing is de-
tailed in the subsequent chapters of this book.
Accessing and interpreting stored computer codes will
be discussed there as well.
Onboard Diagnostic Systems
The computers used in late-model engine control sys-
tems are programmed to check their own operation, as
well as the operation of each sensor, actuator, and cir-
cuit, figure 1-11. Whenever the computer recognizes a
Fig. 1-11. The onboard diagnostic system, which monitors sensor and actuator signals, records a DTC when a circuit abnormality occurs.

Chapter A: General Diagnosis
12
signal that is outside its limits, it records a diagnostic
trouble code (DTC) in its memory.
Generally, the computer is capable of recognizing the
following:
•A particular signal, such as engine speed, is not
being furnished
•A signal that is out of limits for too long, such as a
too-rich or too-lean oxygen sensor (HO2S) signal
•An improbable signal, such as input from a baro-
metric pressure sensor that indicates the vehicle is
being driven at an altitude of 25,000 feet
Some systems have the ability to test sensor or actua-
tor circuit continuity by sending out a test signal and
monitoring the voltage of the return signal.
When an out-of-range signal is detected, the computer
records it as either a continuous or intermittent fault. A
continuous, or hard, failure indicates that the malfunc-
tion occurred and is still present. These generally result
from the total failure of a component or subsystem. An
intermittent, or soft, failure indicates that the malfunc-
tion took place momentarily, then disappeared. This
type of code usually means that a component or sub-
system is functioning erratically, and is often caused by
a loose, dirty, or weak connection. Most systems will
store an intermittent DTC in the long-term memory for
50 to 60 engine-start cycles.
Retrieving Codes
Most vehicles have a diagnostic connector, or data link
connector (DLC), for accessing the computer memory.
On older model vehicles, the multi-plug connector can
be either under the hood or in the passenger compart-
ment. The DLC is always in the passenger compartment
on late-model, Onboard Diagnostic II (OBD-II)-compli-
ant vehicles. The DLC permits connection of a test
meter or jumper wire to trigger the diagnostic mode. A
DTC is displayed generally in one of four basic ways:
•Numerical display on a scan tool
•Pulsating voltmeter needle
•Pulsating instrument panel lamp
•On a digital instrument cluster display panel
The manner in which the program is activated, and the
sequence in which codes are displayed varies between
manufacturers. The preferred method of DTC retrieval is
with a scan tool, figure 1-12. However, not all systems
transmit codes to a scan tool, and codes must be read
some other way. Each manufacturer publishes a list of
trouble codes used with their systems and specific in-
structions for retrieving codes and clearing the comput-
er memory.
Interpreting Diagnostic Trouble Codes
When properly used, a DTC helps to organize an effi-
cient approach to isolating the source of a problem. Al-
though trouble codes are a valuable diagnostic aid, they
will not reveal the precise cause of a problem. Howev-
er, a DTC does indicate the particular circuit where a
malfunction took place. An accurate troubleshooting
chart from the manufacturer is required to determine
what may have set the code.
Stored codes are often the result of poor circuit con-
nections rather than a component failure. Engine sensor
systems operate on low voltage, usually 5.0 volts, and
relatively minor changes in resistance will interfere with
the signal. Stored codes may be the result of a me-
chanical problem, and additional engine tests are re-
quired to isolate the source. Always check the circuitry
and connections before replacing any electronic parts.
Simply disconnecting and reconnecting a multi-plug will
often clean the contacts, restore continuity, and elimi-
nate the code. When multiple codes are present, look
for a weak connection at a common grounding point. An
open circuit results in either a signal not being generat-
ed or received. Low-voltage signals can indicate a
shorted circuit.
Individual circuits, sensors, and actuators can be
checked by connecting a breakout box (BOB) to the
computer, figure 1-13. The breakout box allows you to
monitor the individual circuit signals with a digital multi-
meter (DMM) or oscilloscope. Procedures for testing
components are discussed in the appropriate chapters
of this book.
Exhaust Gas Analyzers
To properly diagnose fuel system concerns an exhaust
gas analyzer should be used, figure 1-14. The analyzers
Fig. 1-12. Retrieving codes with a scan tool.

Chapter A: General Diagnosis
13
are available in many styles and designs. Current mod-
els are designed to sample and analyze either four or five
gasses present in the exhaust from the vehicle. The
newest models are designed for five-gas detection and
normally provide digital and/or printed results of each
test. Either piece of equipment is generally suitable for
diagnosing basic fuel system abnormalities and drive-
ability problems. The five-gas units are required in many
jurisdictions to permit the technician to verify emissions
compliance of a vehicle.
Five-Gas Analyzers
Five-gas analyzers measure the parts per million (ppm)
of hydrocarbons (HC), the percentage of carbon monox-
ide (CO), the percentage of oxygen (O2), the percentage
of carbon dioxide (CO2), and the percentage of oxides
of nitrogen (NOx). Most properly tuned computer-con-
trolled vehicles will produce about 50 ppm of HC, less
than 0.5 percent CO, 1.0 to 2.0 percent O2, and 13.8 to
15.0 percent CO2.
Four-Gas Analyzers
Four-gas analyzers measure HC, CO, CO2, and O2.
They do not provide data as to the levels of NOx in the
exhaust.
Diagnosing Exhaust Gasses
To assist with the discussion that follows, refer to the di-
agnostic chart for problems that may cause abnormal
readings, figure 1-15.
For an accurate analysis of fuel combustion on catalyt-
ic converter-equipped vehicles, prevent the air injection
system from supplying oxygen into the exhaust stream.
This decreases the amount of O2 at the tailpipe, and
the efficiency of the converter. The air injection system
may be disabled by several means. On some vehicles,
disconnect the air injection pump or plugging the pulse
air injection system is effective. For others, the probe of
the analyzer can be connected to a port installed up-
stream of the catalytic converter or to the exhaust
opening for the EGR valve. Next, make sure that the
engine is at operating temperature, in closed loop, and
the HO2S is transmitting a variable signal. Sample the
exhaust gases both at idle and at 2,500 RPM. If a dy-
namometer is used, test under simulated highway load
conditions as described by the manufacturer.
Abnormal HC and CO Readings
High HC levels indicate unburned fuel in the exhaust
caused by incomplete combustion. The source of high
HC emissions can often be traced to the ignition sys-
tem, but mechanical or fuel system problems also can
increase HC emissions, figure 1-16. High levels of HC
emissions result from:
•Advanced ignition timing
•Ignition misfire from defective spark plug wires or
fouled spark plugs
•An excessively rich or lean air-fuel mixture
•Leaking vacuum hoses, vacuum controls, or seals
•Low engine compression
•Defective valves, valve guides, valve springs,
lifters, camshaft, or incorrect valve lash
•Defective rings, pistons, or cylinder walls
•Clogged fuel injectors causing a lean misfire
Fig. 1-13. Typical breakout box.
Fig. 1-14. Typical exhaust gas analyzer.

Chapter A: General Diagnosis
14
The amount of CO in the exhaust stream is directly pro-
portional to the amount of O2 contributing to the com-
bustion process. Richer air-fuel mixtures, with lower
oxygen content, produce higher CO levels; leaner air-
fuel mixtures, with higher oxygen content, produce
lower CO levels. High CO emissions may result from
one or more of the following abnormal conditions:
•Clogged or dirty intake air passages
•Plugged air filter element
•Throttle body coking
EMISSION IDLE OFF
IDLE
CRUISE
1800-2000
AIR-FUEL
RATIO
POSSIBLE CAUSES RELATED
SYMPTOMS
CO 3% 3% 3%
HC 250
ppm
280
ppm 300 ppm
CO2 7-9% 7-9% 7-9%
1
O2 .2% .2% .2%
Rich AFR
Below
10:1
Vacuum leak to map
sensor
Fuel injectors leaking
Bad Power Valve
(carburetor)
Excessive fuel rail
pressure
Vacuum diaphragm
bad
Black smoke or
sulfur
odor
Engine in open loop
Surge/hesitation
Engine not
preconditioned
CO 1.5% 1.5% 1.5%
HC 150
ppm
150
ppm 200 ppm
CO2 7-9% 7-9% 11-13%
2
O2 .2% CO .2%
Rich AFR
at low
speed
10-12:1
Engine oil diluted w/
fuel
Carburetor idle speed
Cold engine
Idle mixture too rich
Choke stuck shut
PCV valve defective
Fuel injectors leaking
Poor fuel economy
Sooty spark/black
smoke
Rough idle/surge
hesitation
Vapor canister purge
valve bad
Vapor canister
saturated
CO 0.5% 0.5% 1.0%
HC 200
ppm
200
ppm 250 ppm
CO2 7-9% 7-9% 7-9%
3
O2 4-5% 4-5% 4-5%
Lean AFR
Over 16:1
Check ignition
primary/secondary
Vacuum leak
Carburetor mixture lean
Poor cylinder sealing
Fuel injectors restricted
Improper timing
Exhaust valve leak
Rough idle
Misfire - high speed
Detonation cruise
2000 rpm)
Idle hunting
(computer)
Overheating
CO 2.5% 1.0% 0.8%
HC 100
ppm 80 ppm 50 ppm
CO2 7-9% 7-9% 7-9%
4
O2 2-3% 2-3% 2-3%
Lean AFR
at High
Speed
Over 16:1
Air cleaner heater door
closed
Internal carburetor
problem (float tuck,
wrong jet, metering rod
stuck)
Fuel injectors restricted
Fuel pump pressure
low
Rough idle
Misfire
Surging Hesitation
CO 0.3% 0.3% 0.3%
HC 100
ppm 80 ppm 50 ppm
CO2 10-12% 10-12% 10-12%
5
O2 2.5% 2.5% 2.5%
AFR
13 - 15:1
Engine not
preconditioned
Air management
system not disabled
Converter not warmed
None
No driveability
symptoms
Fig. 1-15. Four-gas exhaust emissions failure chart.
Table of contents
Popular Engine manuals by other brands
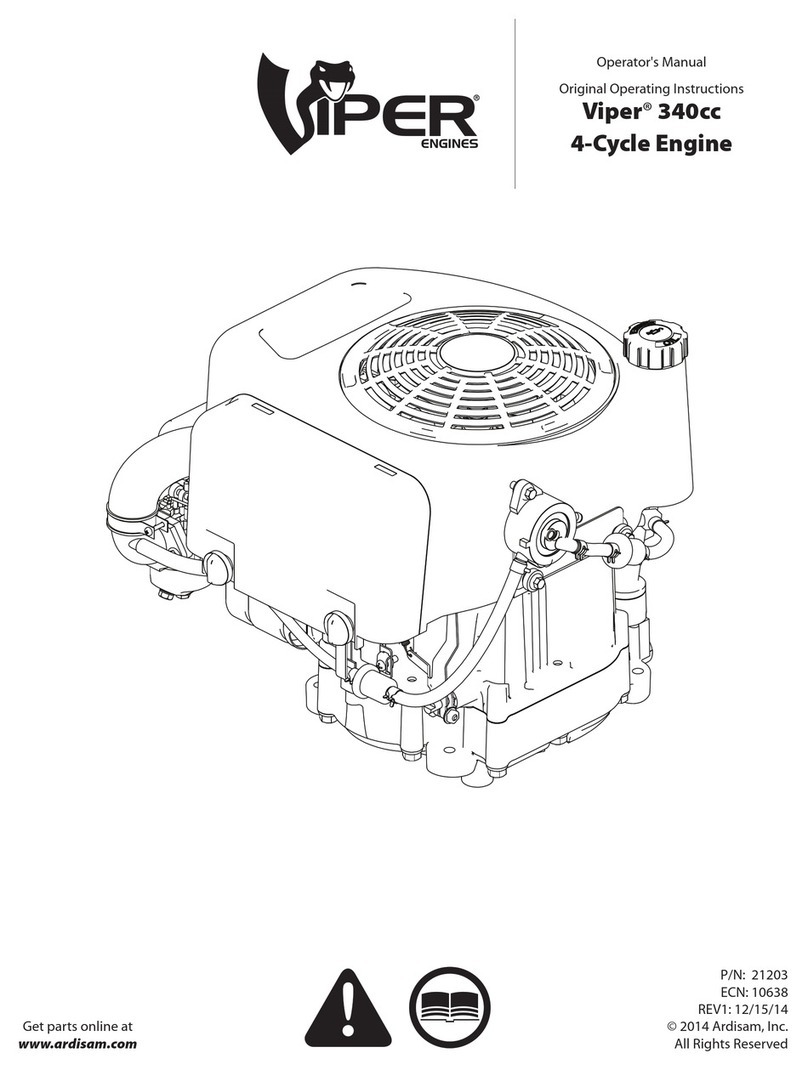
Viper
Viper 340cc 4-Cycle Engine Operator's manual
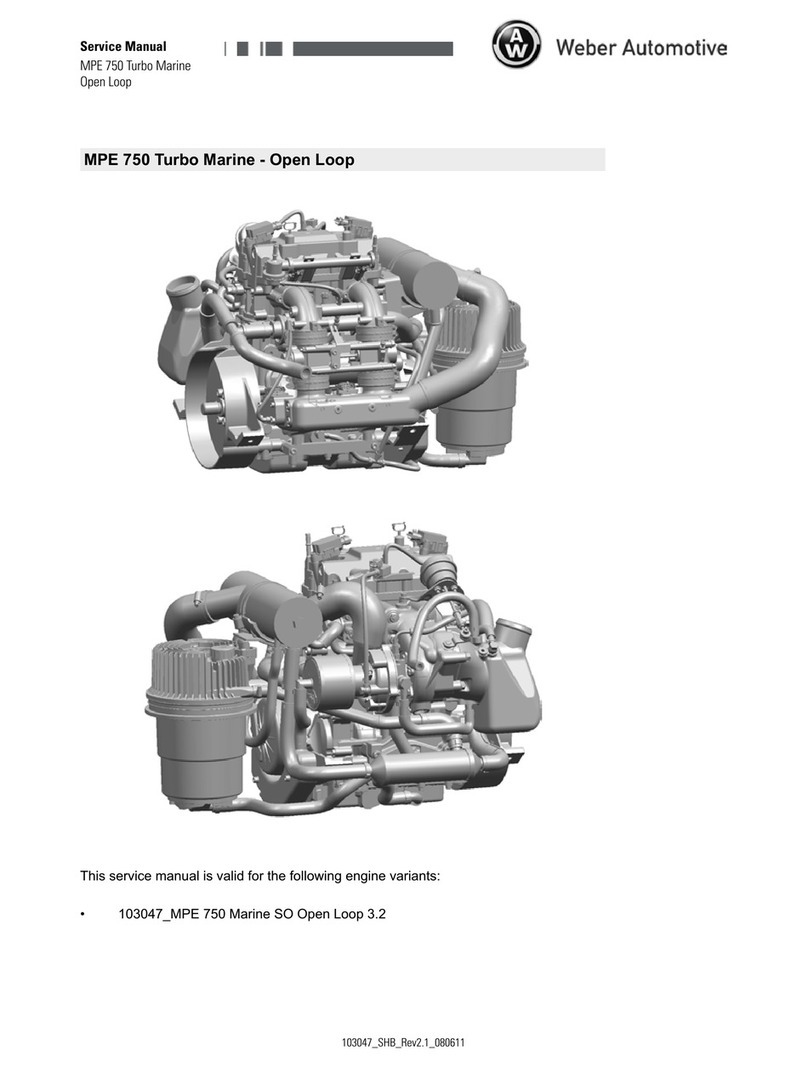
Weber
Weber MPE 750 Turbo Marine Service manual
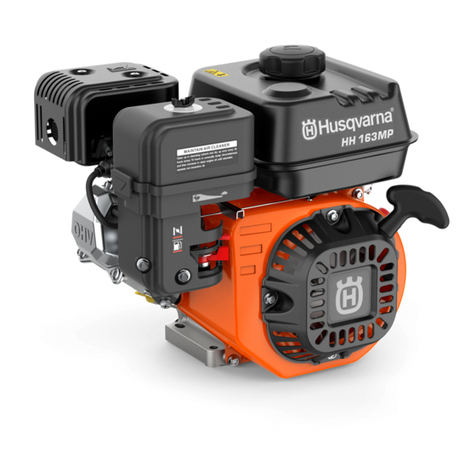
Husqvarna
Husqvarna HH 163MP Operator's manual

SEW-Eurodrive
SEW-Eurodrive DR..71 Series service and maintenance
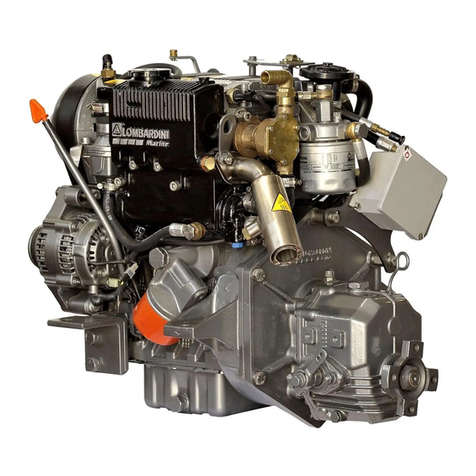
Lombardini
Lombardini LDW 502 M Use & maintenance
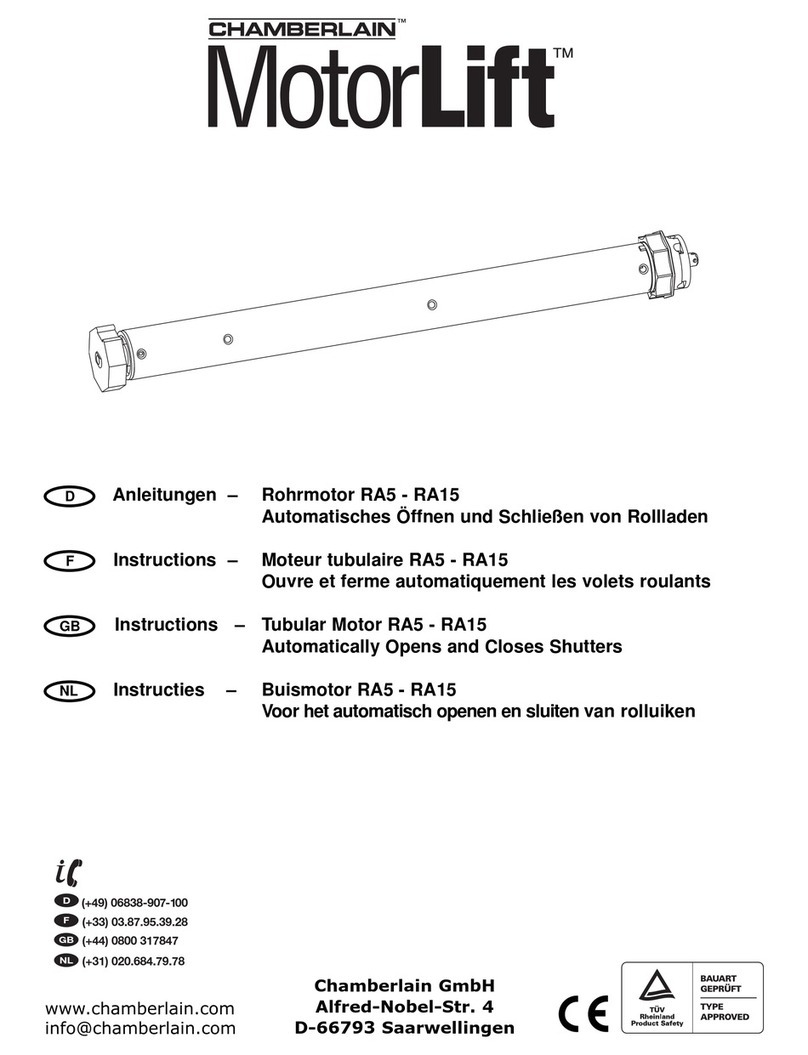
Chamberlain
Chamberlain MotorLift RA5 instructions