AWS 915 User manual

CONTENTS
DUAL CHECK VALVE
Revision status: 03/05/2022 Index number: D0-115
1PREFACE.......................................................................................................................1
1.1 General....................................................................................................................................... 1
1.2 Target group.............................................................................................................................. 1
1.2.1 Personnel qualification.......................................................................................................... 1
1.3 Applicable documents.............................................................................................................. 1
1.4 Warranty..................................................................................................................................... 1
2SAFETY INSTRUCTIONS ..............................................................................................2
2.1 Warnings.................................................................................................................................... 2
2.2 Intended use.............................................................................................................................. 2
2.3 Requirements for the user....................................................................................................... 2
2.4 General safety instructions...................................................................................................... 3
3VALVE DESCRIPTION...................................................................................................5
3.1 Product lines.............................................................................................................................. 6
3.2 Intended use.............................................................................................................................. 6
3.3 Description of function.............................................................................................................. 6
3.4 Pressure test of the valve........................................................................................................ 7
3.5 Scope of delivery ...................................................................................................................... 7
4TYPE PLATES................................................................................................................8
4.1 Article description breakdown................................................................................................. 8
4.2 Type code .................................................................................................................................. 9
5STORAGE AND TRANSPORT.....................................................................................10
6INSTALLATION............................................................................................................11
6.1 Prepare installation................................................................................................................. 11
6.2 Installation instruction............................................................................................................. 12
7COMMISSIONING, DECOMMISSIONING, MAINTENANCE ........................................15
7.1 Commissioning........................................................................................................................ 15
7.2 Decommissioning.................................................................................................................... 15
7.3 Maintenance............................................................................................................................ 15
7.4 Remove pollutants.................................................................................................................. 15
7.5 Correct malfunctions and defects......................................................................................... 16
8REMOVAL....................................................................................................................17
8.1 Prepare removal...................................................................................................................... 17
8.2 Removal instructions.............................................................................................................. 17
9STORE / REUSE VALVE..............................................................................................17
10 DISPOSAL....................................................................................................................18
11 DECLARATION OF CONFORMITY..............................................................................18

1 PREFACE
Revision status: 03/05/2022 1 Index number: D0-115
1 PREFACE
This operating instruction supports the user in the appropriate, safe and economical use of
the following valves:
Dual check valve of the product line 915 and 916.
1.1 General
These operating instructions apply to all the above-mentioned valves. To guarantee safe and
smooth use, the entire manual must be read and understood before installation and
commissioning. These instructions are intended to assist the user during installation,
operation, maintenance and removal. In addition to the instructions in this manual, all
applicable accident prevention regulations, safety rules, country-specific or system-specific
regulations and instructions must be observed. These operating instructions are an essential
part of the valve and must be kept available by the operator at the place of use, also for a
later use.
1.2 Target group
This instruction is intended for any person who is involved in work of any kind on the valve. In
particular, the operating instructions are intended for trained and qualified personnel.
1.2.1 Personnel qualification
All work on the valve must be carried out by qualified personnel only. If the personnel do not
have the required qualifications, they have to be trained. This must be ensured by the
operator. Persons without the required knowledge and skills are not permitted to work on the
valve.
1.3 Applicable documents
This includes the corresponding data sheet and the declaration of conformity of the above
mentioned valves. If necessary, these are to be requested from the manufacturer or
downloaded from the website.
1.4 Warranty
AWS Apparatebau Arnold GmbH does not assume any warranty in case the operator or third
parties:
disregard this document.
do not use the valve properly.
should carry out interventions of any kind (conversions, modifications, etc.) on the
valve.
Malfunctions due to pollution or wear of the valve as well as wearing parts (e.g. seals) are
not covered by the warranty.

2 SAFETY INSTRUCTIONS
Revision status: 03/05/2022 2 Index number: D0-115
2 SAFETY INSTRUCTIONS
2.1 Warnings
The following warnings are used in this manual. In order to protect you from accidents,
injuries and damage to property, it is important to read and observe these warnings.
DANGER
High risk
Indicates an immediate danger. If not avoided, death or serious
injury will result.
WARNING
Medium risk
Indicates a potentially dangerous situation. If not avoided,
death or serious injury may result.
CAUTION
Low risk
Indicates a potentially dangerous situation. If it is not avoided,
minor or slight injuries may result.
NOTICE
Commandment
Indicates a potentially harmful situation. If not avoided, property
damage may result.
2.2 Intended use
AWS valves may only be used within the approved pressure and temperature limits,
considering chemical and corrosive influences. The valves are not suitable for fluids
containing solids. Intended use includes observing and following the instructions in this
manual. Modifications, conversions or any use of the valve other than the intended use are
considered to be improper use.
2.3 Requirements for the user
It is the responsibility of the planner/installer and operator to ensure that:
the valve is used as described in chapter 2.2 Intended use.
the piping system is properly installed and its proper functioning is regularly checked.
only qualified personnel are used for installation, removal and maintenance.
the valve is only professionally installed if it is in perfect condition.
the operating instruction are taken into account by the personnel.
personnel receive regular instruction in industrial safety and environmental protection
(especially for pressurized pipes).

2 SAFETY INSTRUCTIONS
Revision status: 03/05/2022 3 Index number: D0-115
2.4 General safety instructions
The same regulations apply to all valves as to pipeline systems in which they are installed.
The national and international regulations with regard to accident prevention as well as
safety regulations must be observed by the operator.
DANGER
When working on the system
System must be switched off and secured against
unauthorized switch-on.
Pipeline must be pressureless to prevent uncontrolled
leakage of the medium.
Pipeline must have cooled down to approx. 20°C.
Medium must be completely removed from the valve
and pipeline.
Contaminated valve must be completely
decontaminated before work is performed.
Valves may only be installed, removed and maintained
by qualified personnel.
DANGER
When operating the system and the valve
In applications with explosion hazard, hot surfaces of
the system and valve parts can be a potential source of
ignition. This danger must be taken into account by the
operator.
WARNING
When working on the system
Any remaining liquid that may leak out during removal
must be collected and disposed of.
WARNING
When operating the system and the valve
Only media may be used which do not damage the
valve and its seals (suitable material pairing).
Otherwise, this can lead to leakage and leaking of the
medium.
When using media with a very low or very high
temperature, burns can occur when touching the
system parts or the valve housing. In this case, these
may only be touched with suitable protective equipment.
This must be done under the responsibility of the
operator of the system.
Pressure surges in the system can cause severe
damage and must be avoided. This is the responsibility
of the operator of the system.

2 SAFETY INSTRUCTIONS
Revision status: 03/05/2022 4 Index number: D0-115
CAUTION
Risk of minor injuries
Wear protective gloves during installation, removal and
maintenance to avoid injuries from cuts on sharp-edged
components.
Always secure the valve adequately during transport,
installation and removal.
NOTICE
Notice of property damage
The valve and the system can be damaged if the valve
is not installed correctly.
Do not subject the valve to pressure surges; otherwise
the valve may be damaged.

3 VALVE DESCRIPTION
Revision status: 03/05/2022 5 Index number: D0-115
3 VALVE DESCRIPTION
The following illustration describes the structure of the 915 and 916 product lines:
915
916 glandless
Pos.
Name
1
Body
2
Disc
3
Spring
4
Stem
5
Seat sealing
6
Spacer
7
Stem sealing
8
Screw
Pos.
Name
1
Body
2
Disc
3
Seat sealing
4
Spring
5+6
Stems
7+8
Spacer
9
Retaining plate
10
Fixing ring

3 VALVE DESCRIPTION
Revision status: 03/05/2022 6 Index number: D0-115
3.1 Product lines
Product line
Characteristics
915
From DN 50 to DN 900.
With gland.
Centring via the outer diameter of the
body.
916 glandless
From DN 50 to DN 600.
Glandless.
Centering via the outer diameter of the
body.
3.2 Intended use
Dual check valves are valves used for backflow prevention in piping systems. AWS check
valves are characterized by their simple design as well as their short installation lengths
(according to DIN EN 558, series 16 or API 594). They are designed for direct installation
between two connecting flanges. The mentioned valves are suitable for industrial use in
pipeline systems for the transport of liquid and gaseous fluids. The valves are not suitable for
solids. According to guideline 2014/68/EU (Pressure Equipment Guideline) they are suitable
for all fluids of group 1 and 2.
3.3 Description of function
Dual check valves are medium-controlled backflow preventers and open when the opening
force of the medium is greater than the closing force of the discs. In case of absence (e.g.
pump failure) or backflow of the medium, the valve closes automatically.

3 VALVE DESCRIPTION
Revision status: 03/05/2022 7 Index number: D0-115
3.4 Pressure test of the valve
The valve is leak-tested at the factory with air or water. Therefore the following warnings
must be observed:
CAUTION
Residues on the valve
Residues of the test medium may still be left on the
contact surfaces of the valve.
Be aware of possible reactions with the operating
medium.
During a system pressure test of the system, the following warning must be observed:
WARNING
Excess pressure of the valve
In a system pressure test of the system, the pressure
must not exceed 1.5 times the max. permissible
pressure PS of the valve.
3.5 Scope of delivery
The valve is supplied ready for installation.
For valves with the add-on option S79, an additional grounding cable is included in the scope
of delivery.

4 TYPE PLATES
Revision status: 03/05/2022 8 Index number: D0-115
4 TYPE PLATES
A type plate is attached to each valve. The features of the valve are listed on this type plate.
The following two illustrations show the structure of the different type plates of the 915 and
916 product lines.
Structure of a dual check valve type plate of the product line 915:
The flow direction of the valve is marked by an arrow on the body.
Structure of a dual check valve type plate of the product line 916:
The flow direction of the valve is indicated by the arrow on the left side of the type plate.
4.1 Article description breakdown
The following breakdown is an example of a standard valve for illustrative purposes.
Dual check valve type 915
Body: Stem:
Discs: Sealing:
Melting [Body/Discs]:
Order:
XQ12345
148560 /58 231 999
QX23658
1.4408
1.4408
1.4571
EPDM
915/ 100/ 1/ N/ F1
Material spring
= 1.4571
Material sealing
= NBR
Type
= Dual check valve
Design
= 1
Nominal size
= DN100

4 TYPE PLATES
Revision status: 03/05/2022 9 Index number: D0-115
4.2Type code
The type code of the valves is structured as follows:
DN
Material
Type
Nominal
size
Design
Body
Disc
Stem
Spring
Sealing
915
50 –900
1
EN-GJS-400-15*1
EN-GJS-400-15*²
1.4401
F1 = 1.4571
N = NBR
E = EPDM
F = FKM
2
EN-GJS-400-15*1
Aluminium bronze
1.4401
F1 = 1.4571
3
EN-GJS-400-15*1
1.4408
1.4401
F1 = 1.4571
4
1.4408
1.4408
1.4401
F1 = 1.4571
5
Aluminium bronze
Aluminium bronze
Aluminium bronze
F4 = Inconel 600
6
1.4469
1.4469
Inconel 600
F4 = Inconel 600
DN
Material
Type
Nominal
size
Design
Body
Disc
Stem
Spring
Sealing
916
50 –600
4
1.4408
1.4408
1.4401
F1= 1.4401*³
M = Metal
seated
N = NBR
E = EPDM
F = FKM
5.1
1.0619*1
1.4308
1.4301
F1 = 1.4401*³
7
1.4469
1.4469
1.4410
F9 = Inconel X-750
*1Epoxy coated
*2Nickel-plated
*3For metal seated valves, Inconel X-750 is used as the spring material

5 STORAGE AND TRANSPORT
Revision status: 03/05/2022 10 Index number: D0-115
5 STORAGE AND TRANSPORT
The valve is delivered in a ready-to-use condition. In the course of storing and transporting
the valve, there are some guidelines that the user must follow in order to guarantee proper
function of the valve.
Storage:
The valve must be stored in the original packaging in closed rooms.
During storage, the valve must be protected from harmful influences (e.g. moisture or
dirt).
Valves with sealing elements made of organic materials (e.g. EPDM) must be stored
away from sunlight and UV light to prevent faster aging.
During storage the valve must be protected against mechanical damage. Special
attention must be paid to the protection of the connection and sealing surfaces.
To achieve short storage times, existing stocks should be used first (first in - first out).
In the case of long storage periods, the seals may have aged considerably, which can
lead to malfunctions.
Transport:
During transport, the same guidelines apply as for storage.
When transporting over long distances, the valve must be transported in a suitable
packaging to protect it from mechanical damage and corrosion.
For valves with a large nominal size, which cannot be moved manually, the
appropriate sling must be used.
Only use slings on the body or on the eyebolt of the valve, not on the internal parts.
.

6 INSTALLATION
Revision status: 03/05/2022 11 Index number: D0-115
6 INSTALLATION
The operator of the system is generally responsible for the dimensioning of the piping and
the installation of the valve. The function can be affected by planning and installation errors.
6.1 Prepare installation
Remove the valve from the packaging.
Check complete valve for transport damage.
Check the mobility of the discs.
In case of damage contact the manufacturer.
Damaged valves / components must not be installed.
DANGER
Accident prevention measures before installation
Pipelines of the system must be pressureless.
Ensure that pipelines and valve have cooled down to
lukewarm.
System must be free of hazardous media.
System must be switched off and secured against
switching on again.
If necessary, use the suitable protective equipment.
DANGER
Incorrectly connected valve
Installation of the valve may only be carried out by
qualified personnel.
Flow direction arrow of the valve must match the flow
direction of the pipeline.
Only valves whose pressure class, chemical resistance,
connection and dimensions correspond to the operating
conditions may be installed.
Valve may only be used within the intended operating
limits.
Pipelines must be emptied and cleaned if necessary.
WARNING
Valve handling
Special attention must be paid to the risk of crushing or
pinching fingers when checking the mobility of the discs.

6 INSTALLATION
Revision status: 03/05/2022 12 Index number: D0-115
WARNING
Hoist for moving large valves
Lifting equipment may only be used by the personnel
instructed in it.
The appropriate sling must be used for the valve.
The lifting capacity of the hoist and sling must be
designed for at least the total weight of the valve.
Ensure that there are no persons under suspended
load.
NOTICE
Instructions for installing the valve
The system must be clean and free of contaminants at
the point of installation (flanges). Special attention must
be paid to the sealing surfaces.
It must be ensured that a calming distance of 5 x DN
(see 6.3 Installation instructions; calming distance) is
available before and after the valve.
Do not install directly on the pump flange.
6.2 Installation instruction
When installing the valve, the following steps must be followed:
Place one washer on each of the flange screws.
Insert two flange screws through the lower flange holes; these can serve as a
support in the installation position with horizontal flow. From the other side, place one
washer on each of the flange screws and fasten one nut on each of them.
Insert the valve between the flanges. Follow the installation instruction according to
the direction of flow, see following pages.
When installing in a horizontal pipeline, the valve can be placed on the two flange
screws first to ensure easier installation.
For large valves that cannot be moved manually, use a hoist to insert the valve.
Insert a suitable flange connection sealing between the flange and the valve in each
case; these are to be centered with the valve between the flanges.
Insert remaining flange screws through the flange bores.
Put remaining washers on the flange screws from the other side.
Place the remaining nuts on the flange screws and tighten them lightly.
Center the valve between the flanges using the eyebolt. When installing in horizontal
pipelines, lift the valve slightly if necessary.
Tighten flange screws crosswise with the appropriate tightening torque (for guide
values, see table: Tightening torques of the flange connection).

6 INSTALLATION
Revision status: 03/05/2022 13 Index number: D0-115
Tightening torques of the flange connection
The tightening torques given below are to be understood as guide values, as they depend on
various factors, such as the material and strength class of the screws or the flange gasket
used
The valve can be installed for flow directions in horizontal as well as vertical direction.
Observe the following instruction, which apply to horizontal and vertical flow directions, to
guarantee an optimal function.
Installation instruction for horizontal flow direction
NOTICE
Malfunctions/damage due to incorrect installation position
The valve must be installed in the correct installation
position and properly centered between the two
pipelines.
The correct installation position can be seen from the
position of the eyebolt as well as the flow direction
arrow on the type plate.
The valve should be installed with the stems in a
vertical position (see following illustration). If the valve
has an eyebolt, it should point upwards.
Screw
Tightening torque
[Nm]
Screw
Tightening torque
[Nm]
M10
30
M27
600
M12
50
M30
850
M16
130
M33
1100
M20
250
M36
1500
M24
420
Flange screw
Washer
Seal
Valve
Flange
Nut

6 INSTALLATION
Revision status: 03/05/2022 14 Index number: D0-115
X
Installation instruction for vertical flow direction
NOTICE
Malfunctions/damage due to incorrect installation position
The valve must be installed in the correct installation
position and properly centered between the two
pipelines.
The correct installation position can be seen from the
flow direction arrow on the type plate.
If there is a pipe bend in front of the valve, the valve
must be installed in such a way that the stems of the
valve are parallel to the horizontal pipeline in front of the
pipe bend (see illustration).
For flow direction from top to bottom, first check the
suitability of the valve.
Calming distance
The illustration shows options of how the valve should be installed in the piping system. The
calming distance of 5 x DN is shown as well as the correct positioning. This is necessary to
guarantee correct functioning of the valve.
X
X

7 COMMISSIONING, DECOMISSIONING, MAINTENANCE
Revision status: 03/05/2022 15 Index number: D0-115
7 COMMISSIONING, DECOMMISSIONING, MAINTENANCE
7.1 Commissioning
Before commissioning, compare the operating data and materials of the valve with those of
the piping system. This allows the durability of the system to be checked. In the case of new
systems or repairs, the entire piping system must be rinsed to remove foreign substances
from the system. Before commissioning, ensure that the valve is properly installed and all
connections are properly connected. No work may be carried out on the valve during its
operation.
7.2 Decommissioning
During decommissioning and long downtimes, media that change their aggregate state must
be drained or removed from the system. If necessary, the system must be flushed out.
7.3 Maintenance
AWS dual check valves are maintenance-free. However, they can be checked for function
and safety to avoid unforeseen downtimes. The interval time is to be determined by the
operator.
DANGER
Danger due to work on the system
During operation, no work (e.g. maintenance work) may
be carried out on the valve.
7.4 Remove pollutants
When working on the valve, there is a risk of coming into contact with hazardous substances.
The following warnings must be observed:
DANGER
Danger from contaminants on the valve due to use in
contaminated areas
Work on contaminated valves is only permitted for
qualified personnel.
The valve must be completely decontaminated before
any work is performed on it.
The required protective equipment must always be worn
in the contaminated area. In addition, all safety
measures must be followed when handling the
respective hazardous substances.
Plastic parts may be so heavily contaminated that
cleaning is no longer sufficient.

7 COMMISSIONING, DECOMISSIONING, MAINTENANCE
Revision status: 03/05/2022 16 Index number: D0-115
7.5 Correct malfunctions and defects
Malfunctions or defects may occur during operation. The following table shows possible
causes and the appropriate solution. If malfunctions/defects are not listed, please contact the
manufacturer.
Malfunction/Defect
Cause
Solution
High noise emission
Discs hits against pipeline
Realign valve
Use suitable valve for the
pipeline
Calming distance too low/not
respected
Install valve in suitable
position with sufficient
calming distance
Wings oscillate due to unstable
volume flow
Increase the volume flow by
increasing the pump capacity
No flow rate present
Valve installed the wrong way
round
Align flow direction arrow with
flow direction
Flow rate too low;
Closing force greater than
opening force
Increase pressure or flow rate
Closing spring too strong ,
valve cannot open
Use a weaker closing spring
Leakage rate too high
Seat sealing damaged
Replace the body or the
complete valve
Disc deformed
Replace the disc
Sealing surface damaged
Rework sealing surface,
replace affected component if
necessary
Sealing surface dirty
Clean the sealing surface
Wear
Replace affected components
Closing spring worn/defective
Replace closing spring
Flange leakage
Flanges not sufficiently braced
Check fastening elements
and retighten with appropriate
torque if necessary
Sealing surface/seal damaged
Rework sealing surface,
replace body if necessary,
Replace seal
Sealing surface/seal dirty
Clean sealing surface/seal

8 REMOVAL / 9 STORE / REUSE VALVE
Revision status: 03/05/2022 17 Index number: D0-115
8 REMOVAL
When removing the valve from the pipeline, all previously mentioned warnings and
instructions apply. Pay special attention to chapter 6 Installation and chapter 7
Commissioning, decommissioning, maintenance.
8.1 Prepare removal
Before removal, the following steps must be observed:
Pipelines must be emptied and cleaned if necessary.
Provide collection container if there is a residue of the medium in the pipeline.
Observe applicable warnings and instructions to ensure safe and successful work.
8.2 Removal instructions
The following aspects must be observed during removal:
Loosen nuts of all flange screws.
Completely remove all nuts and washers from the flange screws.
Pull the flange screws out of the flange holes.
For horizontal flow, the lower flange screws can remain inserted to facilitate removal.
Secure valve against falling down.
Remove the valve from the flange using the eyebolt. For large valves, use a hoist and
suitable sling.
Remove the remaining flange screws from the flange holes.
Place the valve on a suitable surface.
9 STORE / REUSE VALVE
After the removal, the valve can be stored or used in another system.
The following guidelines must be observed:
There must be no residues of the medium in the valve.
Make sure that the valve is in perfect condition before reusing it.
Valve must be designed for the given operating conditions when reused.
In case of storage, the information in chapter 5 Storage and transport must be taken
into account.
NOTICE
Environmental pollution due to residues
Ensure that the valve is free of residues of the medium
before storage.
All materials are to be disposed of properly in
accordance with applicable regulations.

10 DISPOSAL / 11 DECLARATION OF CONFORMITY
Revision status: 03/05/2022 18 Index number: D0-115
10 DISPOSAL
The following regulations must be observed when disposing the valve:
NOTICE
Disposal of the valve
All valve parts must be disposed of in accordance with
the disposal regulations / environmental protection
regulations.
Pay attention to any residual buildup and outgassing of
the flow media.
11 DECLARATION OF CONFORMITY
The valves are compliant with Directive 2014/68/EU (Pressure Equipment Directive). The
declaration of conformity can be accessed and downloaded from the website www.aws-
apparatebau.de.
This manual suits for next models
1
Table of contents
Other AWS Control Unit manuals
Popular Control Unit manuals by other brands
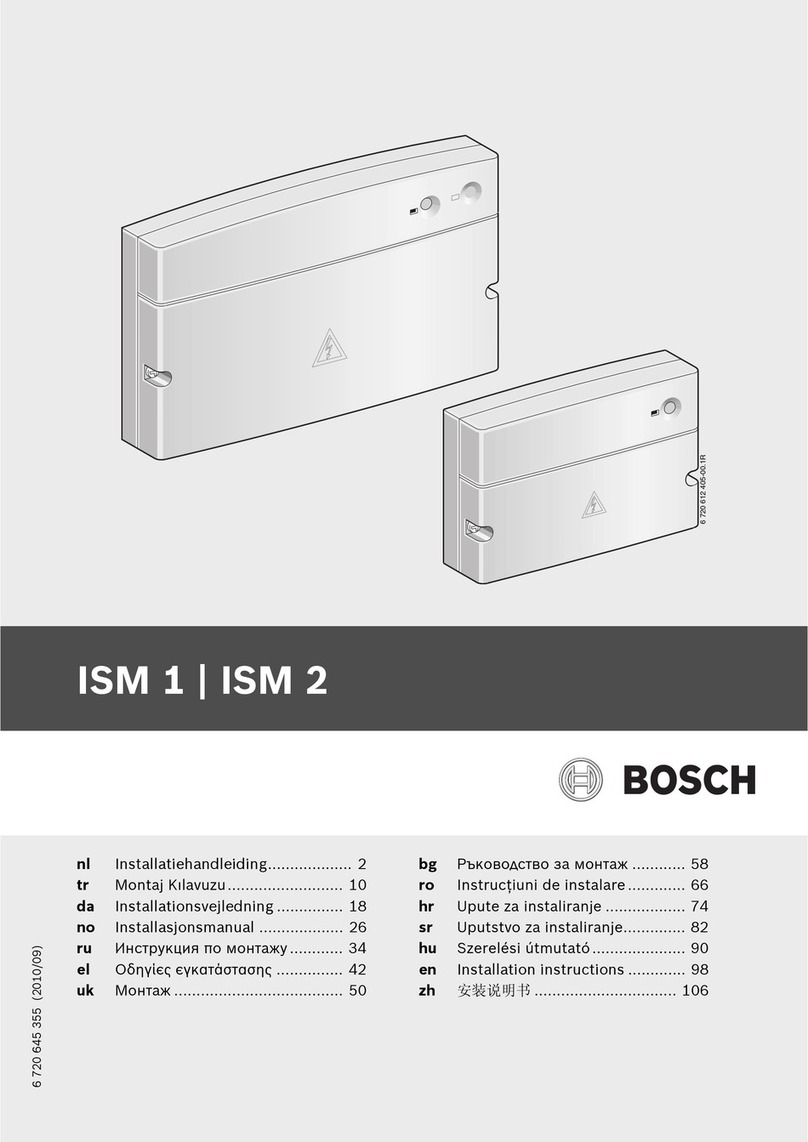
Bosch
Bosch ISM 1 installation instructions
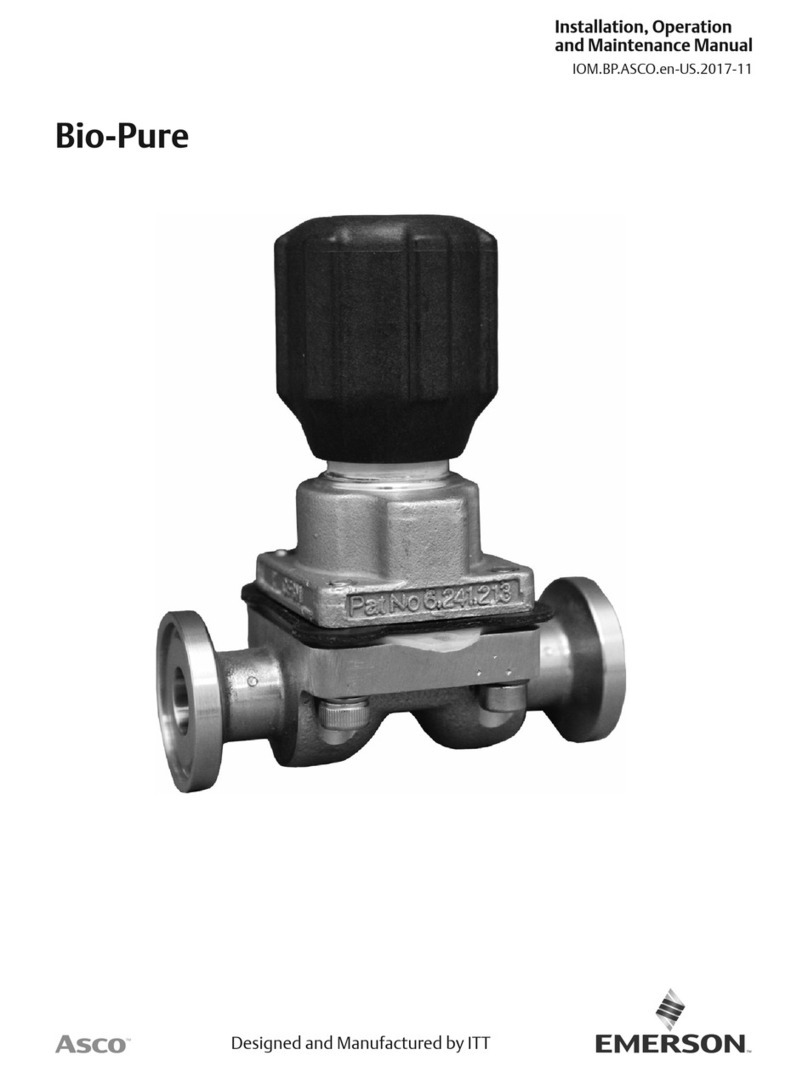
Emerson
Emerson Asco Bio-Pure Installation, operation and maintenance manual
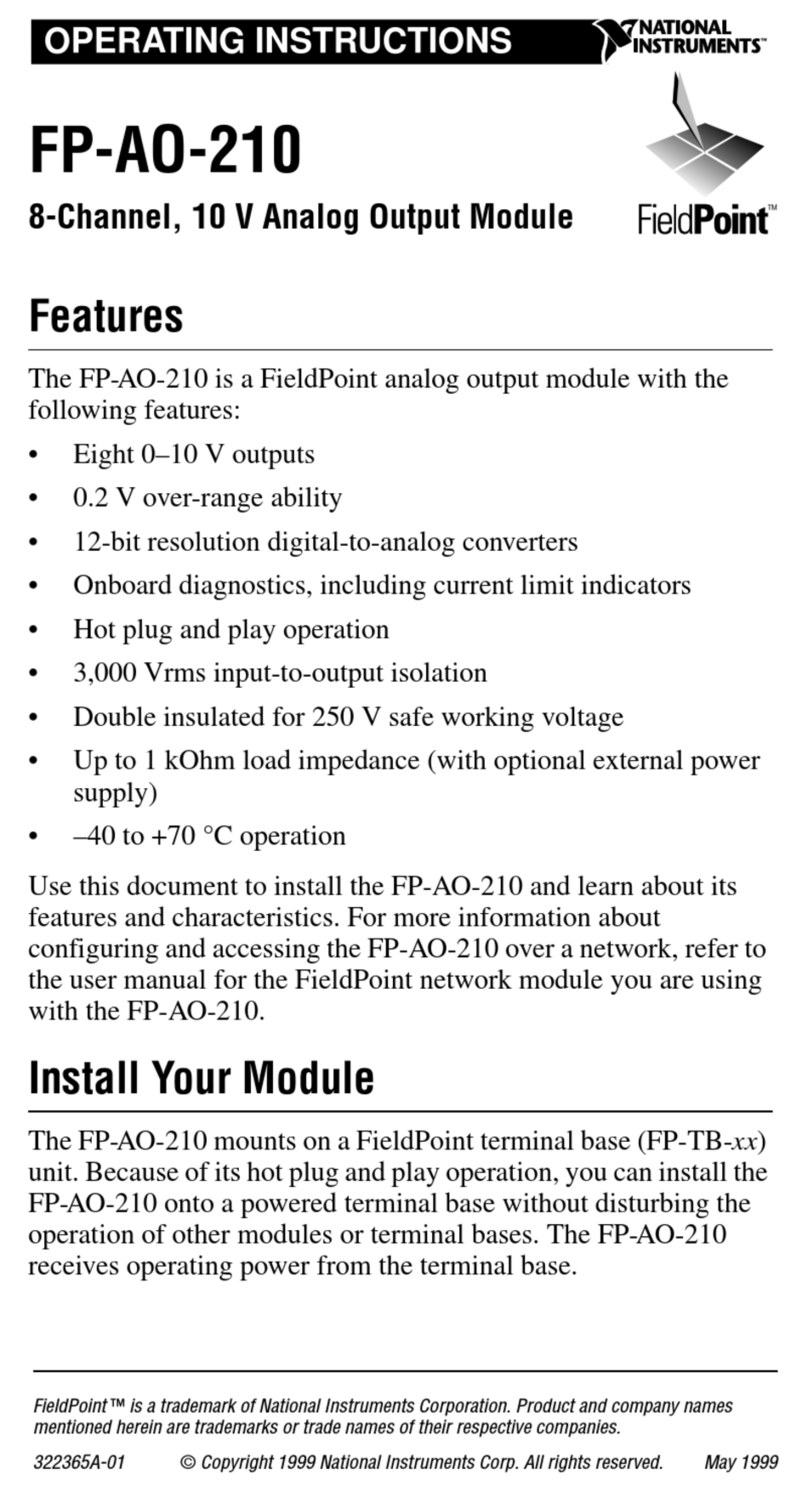
National Instruments
National Instruments FieldPoint FP-AO-210 operating instructions
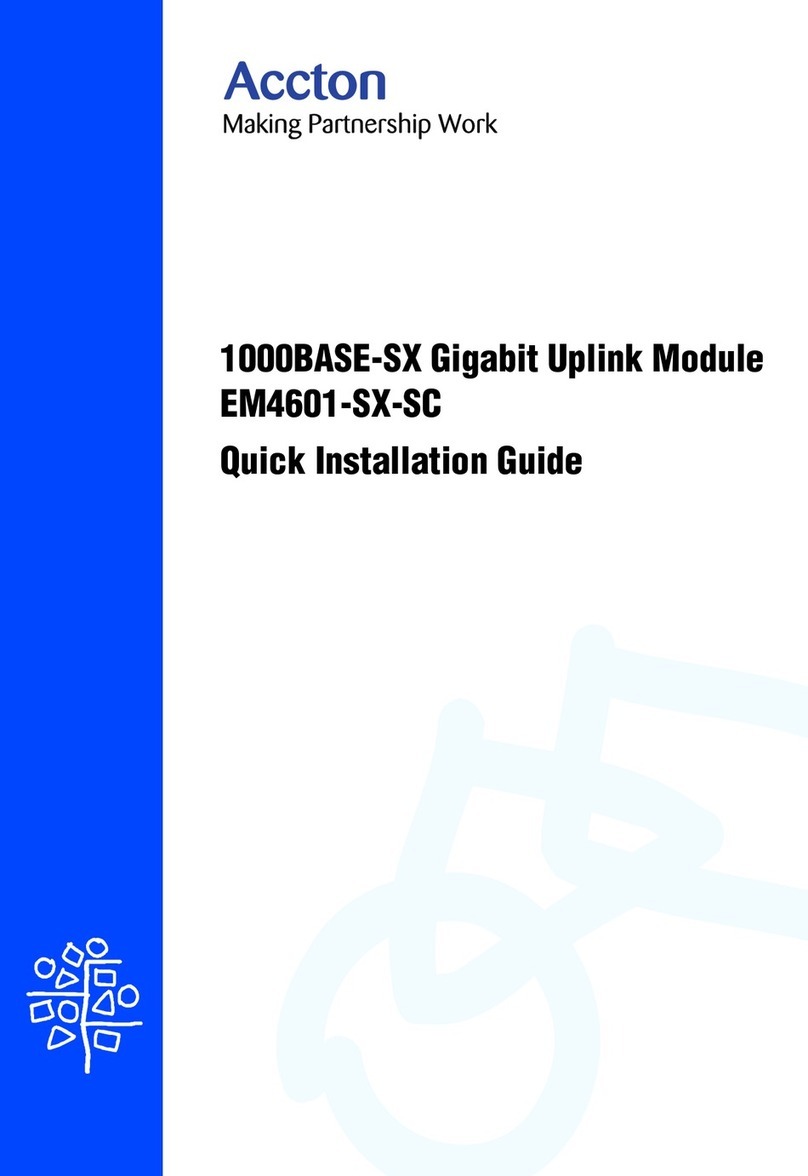
Accton Technology
Accton Technology EM4601-SX-SC Quick installation guide
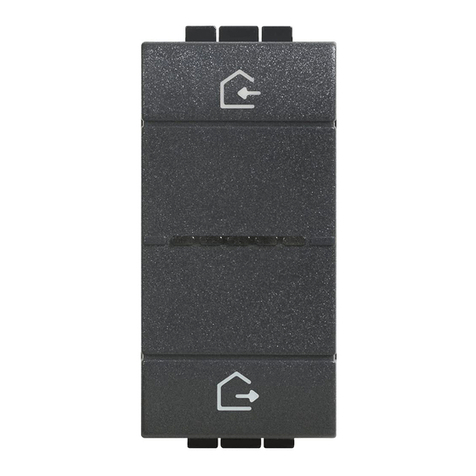
Bticino
Bticino LN4570CWI quick start guide
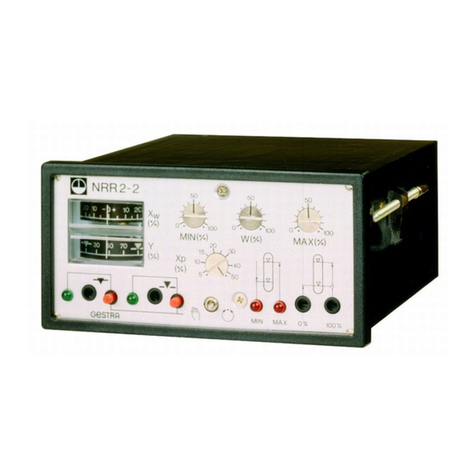
GESTRA
GESTRA NRR 2-2e Installation and service instructions