Baker Hughes XMTC User manual

XMTC
Thermal conductivity
binary gas transmitter
User’s manual

[no content intended for this page]
ii

XMTC
Thermal conductivity binary gas transmitter
User’s manual
910-217 Rev. G
October 2013
iii

[no content intended for this page]
iv

Information paragraphs
NOTE: These paragraphs provide information that provides a
deeper understanding of the situation, but is not essential to
the proper completion of the instructions.
IMPORTANT:
These paragraphs provide information that emphasizes
instructions that are essential to proper setup of the
equipment. Failure to follow these instructions carefully
may cause unreliable performance.
CAUTION!
text omitted, not replaced - remove caution?
WARNING!
This symbol indicates a risk of potential
serious personal injury, unless these
instructions are followed carefully.
Safety issues
WARNING!
It is the responsibility of the user to make sure
all local, county, state and national codes,
regulations, rules and laws related to safety
and safe operating conditions are met for
each installation.
Auxiliary equipment
Local safety standards
The user must make sure that he operates all auxiliary
equipment in accordance with local codes, standards,
regulations, or laws applicable to safety.
Working Area
WARNING!
Auxiliary equipment may have both manual
and automatic modes of operation. As
equipment can move suddenly and without
warning, do not enter the work cell of this
equipment during automatic operation,
and do not enter the work envelope of this
equipment during manual operation. If you
do, serious injury can result.
WARNING!
Make sure that power to the auxiliary
equipment is turned OFF and locked out
before you perform maintenance procedures
on the equipment.
Qualification of personnel
Make sure that all personnel have manufacturer-approved
training applicable to the auxiliary equipment.
Personal safety equipment
Make sure that operators and maintenance personnel have
all safety equipment applicable to the auxiliary equipment.
Examples include safety glasses, protective headgear,
safety shoes, etc.
Unauthorized operation
Make sure that unauthorized personnel cannot gain access
to the operation of the equipment.
v

Environmental compliance
Waste Electrical and Electronic Equipment (WEEE) directive
Panametrics is an active participant in Europe’s Waste
Electrical and Electronic Equipment (WEEE) take-back
initiative, directive 2012/19/EU.
The equipment that you bought has required the extraction
and use of natural resources for its production. It may
contain hazardous substances that could impact health
and the environment.
In order to avoid the dissemination of those substances
in our environment and to diminish the pressure on the
natural resources, we encourage you to use the appropriate
take-back systems. Those systems will reuse or recycle most
of the materials of your end life equipment in a sound way.
The crossed-out wheeled bin symbol invites you to use
those systems.
If you need more information on the collection, reuse and
recycling systems, please contact your local or regional
waste administration.
Visit https://www.bakerhughesds.com/health-safety-and-
environment-hse for take-back instructions and more
information about this initiative.
vi

Contents
Chapter 1. Features and capabilities .....................................................1
1.1 Introduction ......................................................................................1
1.2 Basic features ................................................................................... 2
1.3 Theory of operation ..............................................................................2
1.4 System description ..............................................................................3
1.4.1 Packaging and temperature rating .......................................................................3
1.4.2 2-port (sealed reference gas) version ....................................................................3
1.4.4 Sample system ...........................................................................................4
1.4.5 Extra cable (optional) .....................................................................................4
1.4.6 Power supply (optional)...................................................................................4
1.4.7 TMO2D-TC display (optional) .............................................................................4
1.4.8 XDP display (optional). . . . . . . . . . . . . . . . . . . . . . . . . . . . . . . . . . . . . . . . . . . . . . . . . . . . . . . . . . . . . . . . . . . . . . . . . . . . . . . . . . . . .4
1.5 Typical Applications .............................................................................5
Chapter 2. Installation ..................................................................7
2.1 Introduction ..................................................................................... 7
2.2 Mounting the XMTC transmitter .................................................................. 7
2.3 Mounting the sample system ....................................................................8
2.3.1 Manual, 2-port (sealed reference gas) sample system...................................................8
2.3.2 Manual, 4-port (flowing reference gas) sample system ..................................................8
2.3.3 Sample systems with automatic switching ...............................................................8
2.4 Wiring the XMTC transmitter .....................................................................9
2.4.1 Grounding the enclosure .................................................................................9
2.4.2 CE Mark compliance ......................................................................................9
2.4.3 Cable specifications ......................................................................................9
2.4.4 Wiring the signal connections ...........................................................................10
2.5 Connecting to other components ................................................................12
2.5.1 PS5R-C24 power Supply .................................................................................12
2.5.2 TMO2D display ...........................................................................................12
2.5.3 XDP display ..............................................................................................12
2.5.4 Moisture series analyzers ................................................................................12
Chapter 3. Operation and programming ............................................... 13
3.1 Introduction .....................................................................................13
3.2 Powering up the XMTC .......................................................................... 14
3.3 Starting the sample gas ........................................................................ 14
3.4 Programming with IDM™........................................................................ 14
vii

3.5 The edit functions menu ........................................................................ 14
3.6 Field cal......................................................................................... 15
3.6.1 Perform cal...............................................................................................15
3.6.2 Configure cal ............................................................................................16
3.6.3 Calibration drifts .........................................................................................17
3.6.4 Clear calibration .........................................................................................17
3.6.5 Hold last value ...........................................................................................17
3.7 4-20 mA output ................................................................................. 18
3.7.1 4-20 mA range ...........................................................................................18
3.7.2 4 and 20 mA cal..........................................................................................19
3.7.3 4-20 mA% test............................................................................................19
3.7.4 % gas test ................................................................................................19
3.8 Error handler....................................................................................20
3.8.1 Total drift error ..........................................................................................20
3.8.2 Drift/cal error.............................................................................................21
3.8.3 Gas mV under/over range ...............................................................................21
3.8.4 Gas % under/over range .................................................................................21
3.9 Factory cal......................................................................................22
3.9.1 Edit # of points .......................................................................................... 22
3.9.2 Edit point X .............................................................................................. 22
3.10 The advanced option ...........................................................................23
3.10.1 Fast response ........................................................................................... 23
3.10.2 Language ...............................................................................................24
3.10.3 Meter ID .................................................................................................24
Chapter 4. Calibration .................................................................27
4.1 Introduction ....................................................................................27
4.2 Gas ranges and types...........................................................................28
4.3 Required equipment and materials .............................................................28
4.4 Preparing the transmitter for calibration ........................................................29
4.5 2-port (sealed reference gas) calibration .......................................................29
4.6 4-port (flowing reference gas) calibration ......................................................29
Chapter 5. Specifications .............................................................. 31
5.1 Performance.....................................................................................31
5.2 Functional .......................................................................................31
5.3 Physical.........................................................................................32
5.4 Accessories.....................................................................................32
viii

Appendix A. Supplemental information ................................................33
A.1 Ordering information ...........................................................................33
A.2 Calibration specification ordering information ..................................................34
A.3 XMTC PCB subassemblies.......................................................................34
A.4 Sample calibration sheet .......................................................................35
A.5 Relative thermal conductivity of common gases................................................36
Appendix B. Typical applications.......................................................37
B.1 Hin Nin heat treat furnace atmospheres .....................................................37
B.1.1 Problem ..................................................................................................37
B.1.2 Equipment ..............................................................................................38
B.1.3 Basic operating procedure .............................................................................38
B.1.4 Permanent installation..................................................................................39
B.1.5 Specifications...........................................................................................39
B.1.6 Detailed operating procedure ..........................................................................39
B.2 Hpurity in H-cooled electricity generator......................................................40
B.2.1 Problem .................................................................................................40
B.2.2 Equipment ..............................................................................................40
B.2.3 Basic operating procedure ..............................................................................41
B.2.4 How previously handled .................................................................................41
B.2.5 Permanent installation...................................................................................41
B.2.6 Specifications............................................................................................41
B.2.7 Detailed operating procedure .......................................................................... 42
Appendix C. Installation and wiring diagrams..........................................43
Appendix D. The enhanced advanced option...........................................57
D.1 Entering the enhanced advanced option........................................................57
D.2 Heater ..........................................................................................58
D.3 Balance bridge .................................................................................59
D.4 Factory settings.................................................................................59
D.5 Temperature comp..............................................................................60
Appendix E. CE Mark compliance ...................................................... 61
E.1 CE Mark requirements .......................................................................... 61
E.2 EMI filter board..................................................................................62
E.3 Wiring the signal connections for the weatherproof version .....................................63
E.4 Wiring the signal connections for the explosion/flameproof version.............................64
ix

[no content intended for this page]
x

Chapter 1. Features
and capabilities
1.1 Introduction
This chapter introduces you to the features and capabilities
of the Panametrics XMTC thermal conductivity transmitter.
The following topics are discussed:
• Basic features of the XMTC thermal conductivity
transmitter
• Theory of operation
• A system description of the XMTC, available
options, and sample systems information on
optional components is also provided, including
a 24 VDC power supply, extra cable, and the
TMO2D-TC display.
• A brief discussion of typical XMTC applications
XMTC technical specifications can be found
in Chapter 5. Specifications on page 31.
Ordering information can be found in Appendix A.
Supplemental information on page 33.
1

1.2 Basic features
• The XMTC is a transmitter that measures the thermal
conductivity of a binary (or pseudo-binary) gas mixture
containing hydrogen, carbon dioxide, methane or helium,
and provides a 4-20 mA signal proportional to the
concentration of one of the gases in the mixture. It
offers several unique design features:
• Ultra-stable thermistors and a temperature-controlled
measuring cell (55°C/131°F standard, 70°C/158°F optional)
provide excellent zero and span stability, as well as
tolerance of ambient temperature variations.
• The measuring cell design makes it highly resistant to
contamination and flow vibrations. Since it has no moving
parts, the transmitter can handle the shock and vibration
found in many industrial applications.
• A 2-port version for measurement of zero-based gas
mixtures using a sealed reference gas (air or nitrogen)
and a 4-port version for measurement of zero-suppressed
gas mixtures (and some other special calibrations) using
a flowing reference gas are available.
• The XMTC modular construction means that the unit
can be field-calibrated quickly and easily. If desired,
the plug-in measuring cell can be replaced with a
pre-calibrated spare in minutes.
• The XMTC transmitter, with weatherproof or explosion-
proof packaging, is designed to be installed as close as
possible to the process sample point. It can be located
up to 4000 ft (1200 m) from a display or recorder, using
inexpensive unshielded cable.
1.3 Theory of operation
The XMTC measures the concentration of a gas in a binary
gas mixture by measuring the thermal conductivity of the
sample gas and comparing it to the thermal conductivity of
a selected reference gas.
Two ultra-stable, glass-coated thermistors are used: one in
contact with the sample gas, and the other in contact with a
selected reference gas. The thermistors are mounted so that
they are in close proximity to the stainless steel walls of the
sample chamber. The entire sensor is heated to 55°C/131°F,
(or 70°C/158°F) and the thermistors are heated above the
sensor temperature using a constant current source. The
thermistors lose heat to the walls of the sample chamber
at a rate that is proportional to the thermal conductivity
of the gas surrounding them. Thus, each thermistor will
reach a different equilibrium temperature. The temperature
difference between the two thermistors is detected in an
electrical bridge circuit. It is then amplified and converted to
a 4-20 mA output proportional to the concentration of one
of the constituents of the binary gas mixture. For example:
• To measure 0 to 25% H2in N2, the reference gas would
be air (2-port version, sealed reference gas), and for
calibration, the zero gas would be 100% N2(i.e. 0% H2)
and the span gas would be 25% H2in N2.
• To measure 90-100% H2in N2, the reference gas would
be 100% H2(4-port version, flowing reference gas),
the zero gas would be 90% H2in N2, and the span gas
would be 100% H2(the same as the reference gas).
NOTE: The XMTC has polarity adjustment jumpers which
permit the measurement of gases (such as CO2) that have
a relative thermal conductivity less than air/nitrogen.
Appendix A. Supplemental information on page 33,
contains a table of relative thermal conductivity of
common gases. Figure 1 below shows some of these
values graphically.
SO2
CO2
Air/N
2
CH4
Ne
He
H2
C
4
H6
0
1.0
2.0 3.0 4.0 5.0 6.0 7.0
Figure 1: Relative thermal conductivity of Some common gases
2

1.4 System description
The basic XMTC measurement system consists of an
XMTC transmitter mounted in a sample system. The
sample system is mandatory, and can either be provided
by Panametrics or constructed according to Panametrics
recommendations. The XMTC is supplied with a standard
10 ft (3 m), 4-wire cable for power and output connections,
with lengths up to 4000 ft (1200 m) available. Optionally
available from Panametrics are a 24-VDC power supply
to power the XMTC, a remote display with programming
and control capabilities, and several analyzers which
can be interfaced with the XMTC.
1.4.1 Packaging and temperature rating
The XMTC transmitter is self-contained, consisting of the
thermal conductivity sensor and associated electronics.
It requires 24 VDC power (1.2 A maximum at power-up),
and provides a 4-20 mA output signal proportional to
the concentration of one of the gases in the binary
sample gas mixture.
The XMTC is designed to be installed in a sample system
as close as possible to the process sample point. Thus,
it is available in two environmental packages:
• Weatherproof
• Explosion-proof (with the addition of flame arrestors
to the sample/reference gas inlet and outlet)
Each environmental package is available in a standard
2-port (sealed reference gas) version, or an optional
4-port (flowing reference gas) version.
The XMTC is supplied with a standard measurement
cell operating temperature of 55°C (131°F). An optional
70°C (158°F) cell operating temperature is available.
NOTE: The 70°C (158°F) operating temperature should
be selected only for high temperature applications,
because it results in reduced sensitivity.
1.4.2 2-port (sealed reference gas) version
This standard configuration (see Figure 2 below) is used
for zero-based ranges with air or nitrogen at atmospheric
pressure as the balance or background gas. It utilizes air
with desiccant in a factory sealed chamber as the reference
gas. The following standard ranges and gases are available:
Ranges: Gases:
0-2% H2in N2or air
0-5% CO2in N2or air (min. range 0-5% CO2)
0-10% SO2in air (min. range 0-2% SO2)
0-25% He in N2or air
0-50% Argon in N2or air
0-100%
50-100%
80-100%
90-100%
95-100%
98-100%
Figure 2: 2-port (sealed reference gas) XMTC
3

1.4.3 4-port (flowing reference gas) version
This optional configuration shown in Figure 3 below is
used for zero-suppressed ranges and some other special
applications. Typically, a flowing reference gas of 100% H2
or CO2is used. The following standard ranges and gases
are available:
Ranges: Gases:
90 to 100% H2in N2
80 to 100% CO2in N2or air
He in N2or air
NOTE: For factory calibration pricing on the standard ranges
and gases, or for pricing on other zero-suppressed ranges
and gases, please consult the factory.
Figure 3: 4-port (flowing reference gas) XMTC
1.4.4 Sample system
Use of a sample system is mandatory with the XMTC.
The design of the sample system depends on the
conditions of the sample gas and the requirements of
the application. In general, a sample system must deliver a
clean, representative sample to the XMTC at a temperature,
pressure and flow rate that are within acceptable limits.
Standard XMTC sample conditions are as follows:
• Temperature less than 50°C (122°F) for 55°C
cell operating temperature
• Atmospheric pressure
• Flow rate 0.5 SCFH (250 cc/min)
Panametrics offers sample systems for a wide variety
of applications. Two standard sample systems for the
XMTC are shown in Chapter 2. Installation on page 7.
For assistance in designing your own sample system,
please consult the factory.
1.4.5 Extra cable (optional)
Panametrics provides a 10 ft (3 m) length of 4-wire,
color-coded cable with each XMTC to connect the power
and outputs. Optional cables are available in lengths up to
4000 ft (1200 m). If you are using your own cable, refer
to Table 1: Panametrics 4-wire XMTC cable on page 9 for
recommendations.
1.4.6 Power supply (optional)
The XMTC requires 24 VDC at a maximum start-up
current of 1.2 A. The Panametrics PS5R-C24 power supply
converts 100/120/220/240 VAC to the required 24 VDC
for the XMTC.
1.4.7 TMO2D-TC display (optional)
The Panametrics TMO2D-TC display provides a two-line x
24 character back-lit LCD. It also features display and option
programming, recorder outputs, alarm relays, and relays
for driving sample system solenoids for automatic zero
and span calibration of the XMTC. For information on the
TMO2D-TC, please contact Panametrics.
1.4.8 XDP display (optional)
The Panametrics XDP explosion-proof display provides an
integral, voltage-stabilized 24 VDC power supply, a 3-digit
display with adjustable 4-20 mA input range, two SPDT
alarm relays rated for 1 A/250 VAC, and a 4-20 mA output
that is isolated from the input and adjustable to a second
independent range if required. For information on the XDP,
please contact Panametrics.
4

1.5 Typical Applications
The XMTC can be used in a wide variety of industrial
applications where it is necessary to measure the
concentration of one component of a binary gas mixture.
It can also be used in pseudo-binary gas mixtures where the
ratio of concentrations of the background gas components
remains constant, and in gaseous mixtures where the
thermal conductivity of the gas of interest is significantly
different from that of the background gas. Some typical
industries and applications include:
• Metals industry
H2in heat treat furnace atmospheres
• Electric power industry
H2in generator cooling systems
• Gas production industry
Purity monitoring of argon, hydrogen, nitrogen, helium
• Chemical industry
H2in ammonia synthesis gas
H2in methanol synthesis gas
H2in chlorine plants
• Food industry
CO2in fermentation processes
Ethylene Oxide (ETO) sterilization
• Steel industry
H2in blast furnace top gas
• Petroleum industry
H2in hydrocarbon streams
Two very common applications are:
• H2in N2in heat treat furnace atmospheres:
Zero-based 0-25% H2, 2-port
(sealed reference gas, air)
• H2 purity in H2 electricity generator cooling:
Zero-suppressed, 80-100% H2, 4-port
(flowing reference gas, 100% H2)
For more details on these applications, refer
to Appendix B. Typical applications on page 37.
For details on applications not shown in Appendix B,
or if you wish to discuss your own application, please
contact Panametrics.
5

[no content intended for this page]
6

Chapter 2. Installation
2.1 Introduction
This chapter describes how to install the XMTC transmitter
and its sample system. It also contains information on
connecting the XMTC to optional system components.
The following topics are discussed:
• Mounting the XMTC transmitter
• Installing a Panametrics sample system
• Wiring the XMTC transmitter
• Connecting the XMTC transmitter to optional components
2.2 Mounting the XMTC transmitter
This section applies only if you are mounting the
XMTC transmitter in a sample system that has not been
supplied by Panametrics.
Your sample system should deliver a clean, representative
sample to the XMTC at the proper temperature, pressure
and flow rate. This usually means a clean, dry sample
(free of solid and liquid particulates) at atmospheric
pressure; a temperature no greater than 50°C (122°F);
and a flow rate of approximately 0.5 SCFH (250 cc/min).
Since factory calibration of the sensor is at atmospheric
pressure and 0.5 SCFH, higher or lower operating pressure
may necessitate field-calibration adjustment.
A simple sample system for a 2-port XMTC might have
inlet and outlet flow-regulating needle valves, a flow meter,
and a pressure gauge, in addition to the XMTC transmitter.
The XMTC transmitter should be mounted in the sample
system so that it is upright and level to within ±15°. Also,
provide at least 9 in. (230 mm) of clearance above the top
cover of the transmitter to allow access to the transmitter
printed circuit board (PCB) for calibration and maintenance.
For a 2-port XMTC, connect the sample system sample
inlet and sample outlet ports to the appropriate XMTC port.
For a 4-port system, also connect the reference inlet and
reference outlet ports to the appropriate XMTC ports.
NOTE: Refer to Appendix C. Installation and wiring diagrams
on page 43, for port locations and other information.
WARNING!
Be sure your installation conforms to all
safety and electrical code requirements.
7

2.3 Mounting the sample system
You can order a complete sample system from the factory.
This includes the XMTC transmitter and all necessary
components and sample tubing mounted on a metal
panel. Several standard sample systems are available,
and custom-designed sample systems can be built to
your exact specifications.
Mount the sample system as close to the process sample
point as possible. Once the sample system is mounted,
connect all inlet and outlet lines via the 1/4” compression
fittings on the sample system. The sample line leading from
the process to the sample system should be of 1/4” stainless
steel tubing, and should be as short as possible in order to
ensure a representative sample.
Following are descriptions of two standard sample systems:
2.3.1 Manual, 2-port (sealed reference gas)
sample system
Figure 4 below shows a basic sample system for a 2-port
(sealed reference gas) XMTC. This sample system consists of
inlet needle valves for sample, zero, and span gases; a ball
valve; a 2-port XMTC; a pressure gauge; and a flowmeter.
All components are mounted on a painted steel plate. Other
components could be added for filtration (filter/coalescer),
pressure control (regulator), or flow control (pump).
9.00
(229.5)
(Min)
Sample
gas inlet
Sample
gas outlet
Zero
gas inlet
Span
gas inlet
Transmitter
Figure 4: Basic 2-port sample system (732-164)
2.3.2 Manual, 4-port (flowing reference gas)
sample system
Figure 5 below shows a basic sample system for a 4-port
(flowing reference gas) XMTC. This sample system consists
of inlet needle valves for sample, reference, and calibration
gases; a 4-port XMTC; two pressure gauges; and two flow
meters. All components are mounted on a painted steel
plate. Other components could be added for filtration
(filter/coalescer), pressure control (regulator), or flow
control (pump).
9.00
(229.5)
(Min)
Sample
inlet
N1
N2
N3
N4
Sample
outlet
Zero
gas inlet
Reference
gas inlet
Transmitter
Reference
gas outlet
Figure 5: Basic 4-port sample system (732-028)
2.3.3 Sample systems with automatic switching
Also available from Panametrics are sample systems with
electrically-actuated, three-way solenoid valves. When
used in conjunction with a TMO2D or XDP display (with the
auto cal option), these systems allow automatic switching
of sample, zero, span, and reference gases during operation
and calibration. Refer to Appendix B. Typical applications
on page 37, for details on sample systems designed by
Panametrics for specific applications.
8

2.4 Wiring the XMTC transmitter
CAUTION!
Always apply power to the XMTC immediately
after installation, especially when it is
mounted outdoors or in a humid area.
This section describes how to wire the XMTC for 24 VDC
power, RS232 communication, 4-20 mA output, and
optional devices.
2.4.1 Grounding the enclosure
WARNING!
The XMTC transmitter enclosure must be
properly grounded.
Connect the external ground screw on the XMTC enclosure
(see Figure 6 below) to a suitable earth ground.
External ground screw
Figure 6: Ground screw location
2.4.2 CE Mark compliance
WARNING!
To meet CE Mark requirements, you must
shield and ground all electrical cables as
described in Appendix E. CE Mark compliance
on page 61.
WARNING!
CE Mark compliance is required for all units
installed in EU countries.
WARNING!
Cable entries of an approved flameproof
design are required. These must be installed
according to the manufacturer’s instructions
the choice of cable entry device may limit
the overall installation category achieved.
2.4.3 Cable specifications
Table 1 below shows the transmitter wiring connections for
the standard Panametrics XMTC cable, P/N X4(10). This cable
can be used for distances up to 4000 ft (1200 m).
Table 1: Panametrics 4-wire XMTC cable
Lead Color AWG Terminal
+24 VDC line Red 22 TB1-1
24 VDC return Black 22 TB1-2
4-20 mA (+) White 22 TB1-3
4-20 mA (-) Green 22 TB1-4
9

If you are using your own cable to wire the XMTC, refer to
Table 2 below for the cable requirements.
Table 2: Non-Panametrics 4-wire XMTC cable
Maximum cable length Wire size
ft mAWG mm2
450 130 22 0.35
700 200 20 0.60
1,050 320 18 1.00
1,700 500 16 1.20
2,800 850 14 2.00
4,000 1,200 12 3.00
Table 3 below shows the connections for the Panametrics
standard 3-wire RS232 cable (P/N 704-668), which is
available with a male or female DB-9 or a DB-25 connector.
This cable is available in standard lengths of 6 ft (2 m) and
12 ft (4 m).
Table 3: Panametrics 3-wire RS232 cable
Lead Color AWG Terminal
RX Red 226. TB2-1
TX White 22 TB2-2
GND Green 22 TB2-3
NOTE: See EIA-RS serial communications (document
916-054) for detailed RS232 wiring instructions.
2.4.4 Wiring the signal connections
The XMTC power input, analog output, and RS232
connections are made to terminal blocks TB1 and TB2,
which are accessed by removing the XMTC cover. See
Figure 7 below for the location and pin designations for
terminal blocks TB1 and TB2. Also refer to Appendix C.
Installation and wiring diagrams on page 43.
CAUTION!
Do not make any connections to unassigned
or unused terminals.
+24VDC line (red) 1
24VDC return (black) 2
+4 to 20 mA (white) 3
-4 to 20 mA (green) 4
RS232 RX (red) 1
RS232 TX (white) 2
RS232 GND (green) 3
TB1
TB2
Signal connections
Figure 7: XMTC Signal wiring connections
10
Table of contents
Other Baker Hughes Transmitter manuals
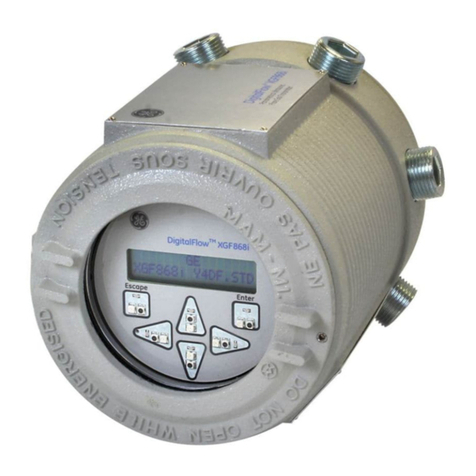
Baker Hughes
Baker Hughes DigitalFlow XGF868i User manual
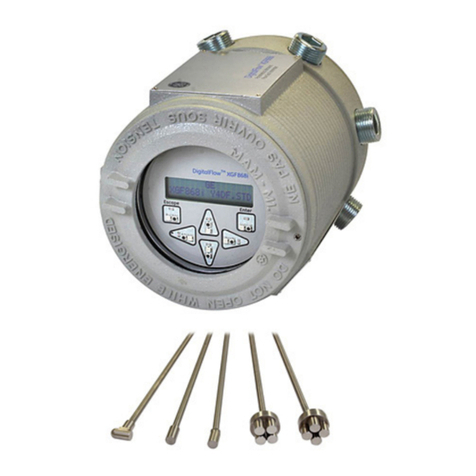
Baker Hughes
Baker Hughes DigitalFlow XGF868i Owner's manual
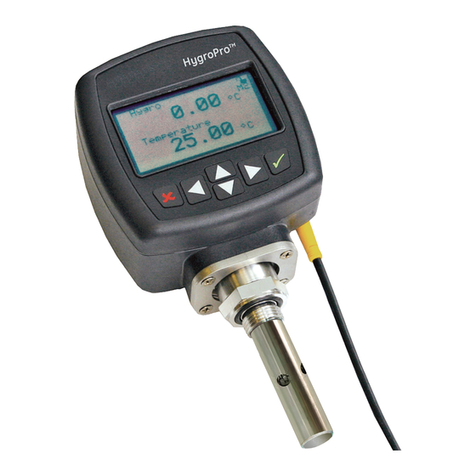
Baker Hughes
Baker Hughes Panametrics HygroPro User manual
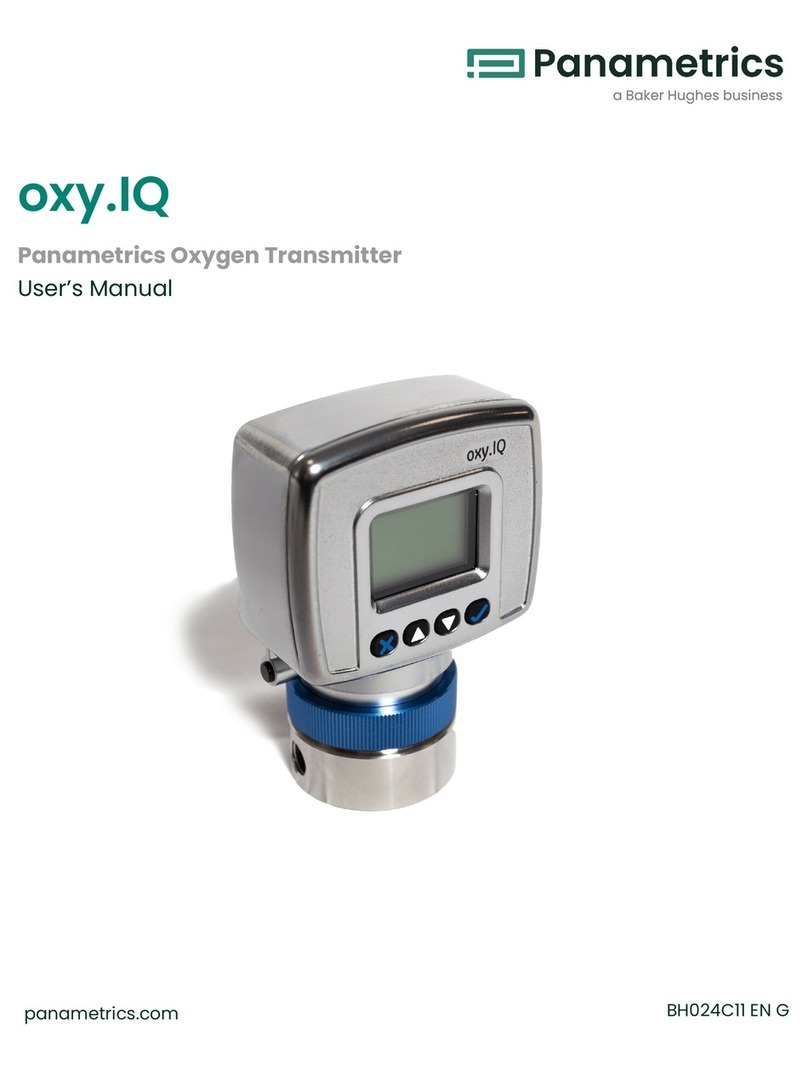
Baker Hughes
Baker Hughes Panametrics oxy.IQ User manual
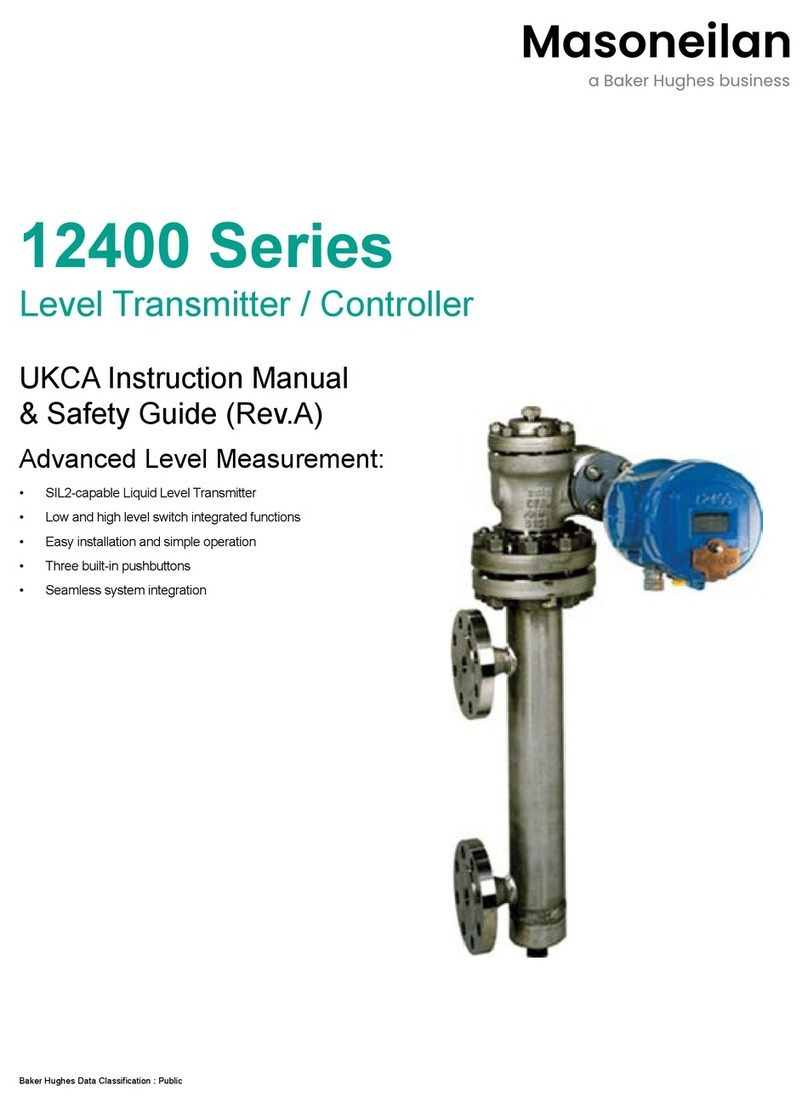
Baker Hughes
Baker Hughes Masoneilan 12400 Series User manual
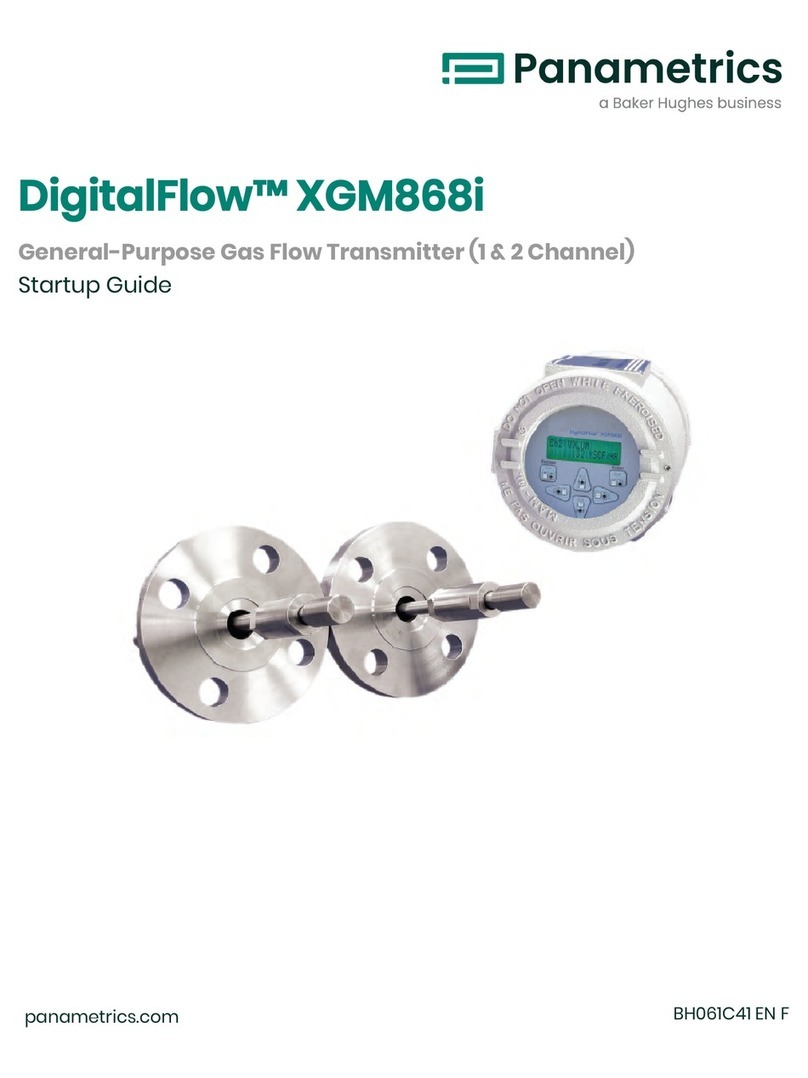
Baker Hughes
Baker Hughes Panametrics DigitalFlow XGM868i User guide