Baugh & Weedon Audit 207 User manual

Issue 2: 2016 SERVICE & GUARANTEE
The quality standards applied to the inspection, test
and calibration of AUDIT Ultrasonic Thickness Gauges
are in accordance with ISO 9001: 2008 quality control
procedures and all measurements are traceable to
national standards.
Page 20
Issue 2: 2016 INTRODUCTION
1. INTRODUCTION.
The AUDIT 207 is a Precision Ultrasonic Thickness
handheld gauge for fast and accurate metric or Imperial
measurement of the thickness of a wide range of metals
and plastics materials, performed with access to only one
side of the material being measured.
This handbook describes the instrument and how to
use it to its best advantage.
1.1 Cautionary information.
The AUDIT 207 is intended to satisfy a wide range of
applications, including corrosion monitoring.
However, the user should be aware that corrosion in a
pipeline or vessel is not uniform and thickness readings
taken on a sampling basis, example testing to a grid
pattern may not indicate the most severely corroded
areas.
It is therefore important that inspection schedules
should be developed by competent engineers and that
measurement of the integrity of a pipeline or vessel
should take account of this factor. In addition, users
should be properly trained in the use of ultrasonic
thickness gauges and be made aware of the limitations
of the equipment and the proposed testing schedule.
Page 2
Issue 2: 2016 INDEX
Page
1. INTRODUCTION 2
1.1 Cautionary information 2
1.2 Standard Schedule of Equipment 3
1.3 Optional Equipment 4
2. TECHNICAL SPECIFICATION 4
2.1 Thickness Range 4
2.2 Accuracy & Calibration 4
2.3 Power Supply 4
2.4 Temperature Range 5
2.5 Environmental Protection 5
2.6 Electromagnetic Compatibility 5
3. PRINCIPLE OF OPERATION 6
4. DIRECTIONS FOR USE 7
4.1 Preparation 7
4.2 Transducer ZERU Calibration 7
4.3 Thickness Measurement 8
4.4 Two point Calibration 8
4.5 Metric – Imperial Mode change 9
4.6 Scan Mode 9
4.7 Fit Batteries 10
4.8 Other Indications During Use 10
4.9 Limitations 10
5. OPERATION AND APPLICATION INFORMATION 11
5.1 Basic Technique 11
5.2 Effect of Surface and Hot Conditions 12
5.3 Painted Parts 13
5.4 Couplant 14
5.5 Transducer Wear 14
6. CARE & MAINTENANCE 15
7. HEALTH AND SAFETY 16
8. SERVICE AND GUARANTEE OF EQUIPMENT 17
8.1 Guarantee 17
8.2 How to make a Guarantee Claim 18
8.3 Service Repairs and Maintenance 19
8.4 Certification 20
Page 1
Issue 2: 2016 SERVICE & MAINTENANCE
8.3 Service Repairs and Maintenance
Repairs not covered by the guarantee or carried out
after the guarantee period will be charged at the current
hourly service rate, plus the cost of materials.
Goods for repair must be sent at the Purchaser's
expense and be accompanied by the Purchaser's
written order describing the defect and authorising the
company to invoice the purchaser for labour, materials
and return delivery costs.
No guarantee or service work will be undertaken until a
written order is received.
Baugh & Weedon undertakes to offer repair and
maintenance services to the AUDIT 207 thickness
gauge for a period of not less than five (5) years from
the date of original dispatch.
The Company cannot make any such undertaking after
that period although it will use its best endeavours in
every case.
Page 19

Issue 2: 2016 SERVICE & GUARANTEE
8.2 How to make a Guarantee Claim
On receipt of the goods and order the Company will
examine the goods and determine the nature and
cause of the defect. If the defect is covered by the
guarantee a replacement or repair will be effected at
the Company's expense. If the defect is not covered by
the guarantee the Company will quote the Purchaser
for the replacement or repair, and will not proceed until
written acceptance of such quotation is received.
During the first year of the guarantee the Company will
bear the cost of returning guarantee replacement or
repaired goods to the purchaser's premises in the
country to which the goods were originally delivered.
At the purchaser's request and expense, the Company
will return goods to other countries.
During the second to the fifth year of the guarantee the
return of guarantee replacement or repaired goods
shall be at the Purchaser's expense.
Always adhere to safe local regulatory disposal practise
for alkaline batteries used within the AUDIT Instrument.
Care should be taken that the couplant used is neither
harmful to the operator nor will it attack the probe. For
advice please contact Baugh & Weedon.
Page 18
Issue 2: 2016 OPTIONAL EQUIPMENT
1.3 Optional Equipment
Item
Transducer type 2.5MHz BD52 DT35 5MHz/0.25”
Transducer type 7.5MHz BD17 DT37 7.5MHz/0.87”
Transducer type 5.0MHz BD25 DT39 Hi-Temp
2. TECHNICAL SPECIFICATION
2.1 Thickness Range Interface Echo technique
Minimum 0.63mm Maximum 500.0mm
0.025” 19.0 in
2.2 Accuracy & Calibration
Velocity Range 1200m/s to 10000ms
0.0492 in/µs to 0.3930in/µs
. Resolution: 0.01mm. (0.001”
Accuracy: ± 0.01millimeters ±0.001inches
Material dependent
2.3 Power Supply
Source: 2 x LR6( AA) Alkaline Batteries or
rechargeable equivalents
Battery life: 50 hours continuous (alkaline dry batteries)
Auto power off timer: 5 Minutes.
Page 4
Issue 2: 2016 INTRODUCTION
Before using the equipment, operators should make
themselves fully conversant with the operating
procedures as laid out in this handbook
1.2 Standard Schedule of Equipment
Dimension 121 x 70.3 x 32.3mm
Weight 295g including batteries
The standard equipment package consists of the
following.
Product
AUDIT 207 Thickness Gauge. 0704/A207
Complete with two AA alkaline batteries
• Plastic Transit/Carrying Case 0704/0175.
• Probe type 5MHz BD25 DT35 5MHz
• Operator Handbook. 0704/0201
• Ultrasonic Coupling Agent 0704/185
Page 3
Issue 2: 2016 SERVICE & GUARANTEE
8. SERVICE & GUARANTEE OF EQUIPMENT
8.1 Guarantee
AUDIT 207 is guaranteed for five (5) years, excluding
batteries and transducers which have been subject to
wear.
Baugh & Weedon ("the company") undertakes to make
good by sending a replacement or, at it's option, by
repairing defects arising from faulty design, material or
workmanship within a five (5) year period from the date
of dispatch.
Your existing consumer rights are not affected by these
guarantees and conditions.
Always adhere to site rules and guidelines concerning
Health & Safety when using the AUDIT 207 Instrument.
Always wear safety equipment appropriate to the area
where the measurement is to be made.
There are no user serviceable parts inside the
instrument case of the AUDIT 207 Service work should
only be carried out by qualified personnel .
Page 17

Issue 2: 2016 HEALTH AND SAFETY
Some organic materials may attack plastic parts and
cause early degradation. Contact with such materials
should be avoided.
7. HEALTH AND SAFETY
AUDIT 207 thickness gauge and accessories are NOT
intrinsically safe or flameproof, and should not be used
in hazardous areas without the necessary local
precautions being enforced for the use of non-
intrinsically safe equipment.
Always adhere to site rules and guidelines concerning
Health & Safety when using the AUDIT Instrument.
Always wear safety equipment appropriate to the area
where the measurement is to be made.
There are no user serviceable parts inside the
instrument case of the AUDIT 207 Service work should
only be carried out by qualified personnel.
Care should be taken that the couplant used is neither
harmful to the operator nor will it attack the probe. For
advice please contact Baugh & Weedon.
Ultrasonic Coupling Agent (Hydrophilic Type)
SURTEST UCA-2. Safety Data Sheets supplied on
request.
Page 16
Issue 2: 2016 PRINCIPLE OF OPERATION
EC Declaration of Conformity
UNIT Audit 207 Ultrasonic Thickness Gauge
WEE compliance Registration No WEE/FK0103WV
The equipment is supplied in a single commercial
carton, containing the items previously detailed, ensure
that all the items of equipment are accounted for when
unpacking.
Equipment should be examined for signs of transit
damage. Damaged equipment SHOULD NOT BE
USED. Retain the carton in the event the equipment
has to be returned to the manufacturer for period
certification.
3. PRINCIPLE OF OPERATION
AUDIT 207 measures thickness by injection of a short
burst of high frequency sound (ultrasound) into the
work piece and measuring the time taken for the burst
to travel through the material and be reflected back
from the far surface. As the velocity at which the sound
travels is constant for a given material the thickness
can be computed and displayed.
Thickness readings are held for 5 Minutes after the
probe is removed from the work piece.
Page 6
Issue 2: 2016 TECHNICAL SPECIFICATION
Backlight is operated by the UNIT key, selectable on/off
Low battery is indicated by the battery symbol located
at the top right of the display.10 hours use available. In
normal use battery life will be much greater than the
above specification. This is due to the intermittent use
of the instrument rather than a continuous test ,
detailed above.
2.4 Temperature Range
Operational -20 to + 50˚C
Case : Extruded aluminium body, Anodized aluminium.
2.5 Environmental Protection
Sealed and rating to IP54
2.6 Electromagnetic Compatibility
Radiated Emission Standard EN61000-6-4
EN61000-6-2 (Electric discharge)
EN61000-4-2 Criterion A
EN61000-6-2 (Electric fields)
Radiated EM field Immunity
EN61000-4-3 Criterion B
Page 5
Issue 2: 2016 CARE AND MAINTENANCE
6. CARE & MAINTENANCE
This equipment is protected against hostile
environments as defined in section 2.5 and is designed
for prolonged use in the field without any special
maintenance other than routine cleaning.
All connectors should be kept free of foreign matter and
the transducer face regularly cleaned with soft material
such as tissue paper.
To ensure trouble free operation, when not in use the
AUDIT 207 thickness gauge should be returned to the
carrying case in a clean condition.
This equipment should only be operated by qualified
personnel.
Transducers and leads are consumable items and are
subject to wear and deterioration during use. The life
of these parts can be much extended by keeping them
in a dry, clean condition, and storing them in suitable
protective containers. During use avoid 'scrubbing' the
probe face on the work piece. Only take spot
measurements at the selected locations.
Page 15

Issue 2: 2016 COUPLANT
5.4 Couplant
For all applications the AUDIT 207 Instrument must
have it's transducer coupled to the work piece using a
suitable coupling fluid.
In practice this can be a variety of fluids such as oil,
water, or other types of proprietary ultrasonic couplant
preparations.
We the manufacturers of AUDIT 207 supply within the
standard schedule of equipment.
Ultrasonic Coupling Agent (Hydrophilic Type) Trade
Name SURTEST UCA-2. (See section 7)
5.5 Transducer Wear
Care should be exercised when taking readings not to
"scrub or drag" the transducer face material over the
surface of the work piece. This resultant wear causes
the length of the transducer tip to reduce and can
cause the probe faces to become uneven. This can
cause poor coupling, making stable readings harder to
obtain. Be careful when using transducer in SCAN
mode use plenty of couplant and slide the transducer
face carefully across material.
Spare transducer are available from the manufacturers
and it is recommended that a seriously worn transducer
be replaced.
Page 14
Issue 2: 2016 PRINCIPLE OF OPERATION
Do not attempt to carry out this Transducer to gauge
ZERO check on any other test block or material other
than the test block mounted on the top panel, as this
will lead to a discrepancy in the thickness readings.
4.3 Thickness Measurement
Place probe on 10mm mild steel step wedge ( or any
known test block ) press CAL key, adjust the up down
keys to display 10.00mm, press CAL key, the set
velocity is displayed.
Press CAL key place probe and read thickness ,if the
display thickness is well out of specification, press CAL
key until velocity value is visible, using up down keys
adjust velocity required.
4.4 Two Point Calibration
1. Place the probe on the highest known thickness of
the test part.
2. Press CAL key until (set thickness is displayed) ,
using up down keys to display the known thickness.
Page 8
Issue 2: 2016 DIRECTION FOR USE
The velocity used for calculation is that of steel. It is a
simple matter to convert the reading for other common
materials by using the appropriate Velocity. Through
the CAL key operation.
Fit batteries see section 4.4. Connect transducer to
sockets top plate.
4. DIRECTIONS FOR USE
4.1 Preparation
Press the ON/OFF key. Start up Display information.
Active software Version. Followed by B&W LOGO
5 thick bars visible across screen plus and at top left gain
stability level. Bottom left velocity and bottom right mm
(metric) or in (Imperial) mode.
4.2 Transducer ZERO Calibration
At this stage a check to match the transducer with the
gauge is required, by placing the transducer on the
battery and ZERO calibration cap, using a suitable
couplant a stable count will be displayed, press ZERO
key.
Page 7
Issue 2: 2016 OPERATION
measurement., it is recommended that the user perform
a calibration procedure on a sample piece of known
thickness, which is at, or near, the temperature of the
work piece.
There is a point, however, when the signal strength is
marginal.
Under these conditions the AUDIT 207 may display a
small amount of signals within the stability indicator.
The user will be aware of this situation because it is
likely that the effect will change dramatically if the
location of the probe on the work piece is changed
slightly.
Apply more couplant or clean the surface more
thoroughly. Attempt to take readings at other points
close to and around the original location.
5.3 Painted Parts
If the paint is thin in relation to the work piece as a
whole and is well bonded, very little error will be
observed in displayed thickness reading. A poor bond
between the paint and metal however, may result in
AUDIT 207 trying to read the thickness of the paint
layer only.
Page 13

Issue 2: 2016 OPERATION
If at any point while taking readings a low battery
symbol is displayed at the top right of the display, this
is an indication that the batteries need to be changed
within the next 10 hours of operation. If the batteries
are not changed the AUDIT 207 will stop functioning
at a pre-set voltage and the display will blank, the
instrument will remain in calibration throughout shut
down.
It is good practice to carry out transducer to gauge
ZERO calibration check after batteries are fitted, see
section 4.2
When switching off, the gauge retains all of its settings.
5.2 Effect of Surface and Hot Conditions
A rough front surface may affect the coupling of sound
between the probe and the work piece. A rough rear
surface will possibly scatter the measuring beam rather
than reflect it. In consequence, rough surfaces tend to
reduce the reflected signals required for measurement.
Observe the Stability indicator as to the strength of the
received signals.
Hot temperatures above 100°C the change in sound-
velocity of the material being measured starts to have a
noticeable effect upon the accuracy of ultrasonic
Page 12
Issue 2: 2016 PREPARATION
4.7 Fit Batteries
Locate battery compartment cover and ZERO calibration
cap at top of gauge and unscrew cap.
Referring to battery polarity instructions on rear panel of
gauge, Negative to top cap, insert batteries into gauge
ensuring correct polarity.
Replace battery compartment cover cap.
4.8 Other Indications During Use
Low Battery warning Symbol Top right of Display.
First appearance indicates that there are approximately
10 Hours of continuous battery life left.
Audit 207 retains all of its settings after switch off.
4.9 Limitations
With all types of Ultrasonic Thickness Gauges, the
ability to obtain thickness readings is dependent on the
capability of the transmitted signal to penetrate
completely through and return from the rear surface of
the material under test, it is possible due to the
composition and or grain structure, of some materials
plastics, cast iron etc that limitations to the thickness
range is possible, as the material is too attenuative for
the ultrasound to penetrate.
Page 10
Issue 2: 2016 PREPARATION
3. Press ZERO key.
4. Place the probe on the thinner known thickness of
the test part. followed by the CAL key (2nd
thickness display)is indicated, using up down keys
set this thickness press CAL key. Velocity will
automatically enter measurement screen. The Audit
207 is now ready to take readings.
4.5 Metric -Imperial Mode change
For Mode change Press UNIT key, you have the
capability to display mm or in 6.0mm single decimal
point or a second press of UNIT key operation to display
6.00mm high
resolution, additional repeated presses of the UNIT key
changes calibration from mm to in. low or high
resolution.
4.6 Scan Mode
SCAN Identifies the minimum thickness measurement
obtained whilst the probe is in scanning contact with the
material being measured as displayed at the top of the
display with live measurements displayed in the centre
section, the gauge memorises the lowest measurement it
finds.
Page 9
Issue 2: 2016 PREPARATION
AUDIT 207 can tolerate large changes in signal
strength, but ultimately, under very poor conditions,
insufficient signal will be received to make a
measurement as displayed by the stability indicator for
strength of signals.
5. OPERATION AND APPLICATION INFORMATION
5.1 Basic Technique
The surface of the work piece to be measured should
be cleaned to remove all fouling and other
contamination. Surfaces do not have to be entirely flat
or smooth, but in general the poorer the surface the
less satisfactory it will be for accurate measurements.
Prepare AUDIT 207 for use (as previously described).
Apply a liberal amount of couplant to the work piece at
the point to be measured. lightly press the transducer
squarely against the surface and read the thickness
value from the digital display. The reading will remain
on the display for 5 minutes after the probe is removed
from the work piece.
Page 11

AUDIT 207 Two Point Calibration
1 Place the probe on the highest known thickness of the
test part.
2 Press CAL key until (set thickness is displayed), adjust
up down keys to display the known thickness.
3 Press ZERO key.
4 Place the probe on thinner known section followed by the
CAL key (2nd thickness is displayed), using up down
keys set this thickness displayed to match thinner section.
press CAL key Velocity will automatically enter
measurement screen.
The Audit 207 is now ready to take readings.
AUDIT 207 Two Point Calibration
1 Place the probe on the highest known thickness of the
test part.
2 Press CAL key until (set thickness is displayed), adjust
up down keys to display the known thickness.
3 Press ZERO key.
4 Place the probe on thinner known section followed by the
CAL key (2nd thickness is displayed), using up down
keys set this thickness displayed to match thinner section.
press CAL key Velocity will automatically enter
measurement screen.
The Audit 207 is now ready to take readings.
AUDIT 207 Two Point Calibration
1 Place the probe on the highest known thickness of the
test part.
2 Press CAL key until (set thickness is displayed), adjust
up down keys to display the known thickness.
3 Press ZERO key.
4 Place the probe on thinner known section followed by the
CAL key (2nd thickness is displayed), using up down
keys set this thickness displayed to match thinner section.
press CAL key Velocity will automatically enter
measurement screen.
The Audit 207 is now ready to take readings.
AUDIT 207 Two Point Calibration
1 Place the probe on the highest known thickness of the
test part.
2 Press CAL key until (set thickness is displayed), adjust
up down keys to display the known thickness.
3 Press ZERO key.
4 Place the probe on thinner known section followed by the
CAL key (2nd thickness is displayed), using up down
keys set this thickness displayed to match thinner section.
press CAL key Velocity will automatically enter
measurement screen.
The Audit 207 is now ready to take readings.
AUDIT 207 Two Point Calibration
1 Place the probe on the highest known thickness of the
test part.
2 Press CAL key until (set thickness is displayed), adjust
up down keys to display the known thickness.
3 Press ZERO key.
4 Place the probe on thinner known section followed by the
CAL key (2nd thickness is displayed), using up down
keys set this thickness displayed to match thinner section.
press CAL key Velocity will automatically enter
measurement screen.
The Audit 207 is now ready to take readings.

"Alpine Components" is the abbreviated trading name for "Alpine Components Limited"
The company has been trading since 1991 and was incorporated on 13/11/2006 in the United Kingdom
Company Registration Number: 05996485
VAT Number: GB583598190
ALPINE
COMPONENTS
Postal Address
Alpine Components Ltd
Innovation Centre, Highfield Drive
Churchfields
St. Leonards-on-
Sea
TN38 9UH
United Kingdom
Telephone
01424 858118
Website
Address
www.alpine-
components.co.uk
Table of contents
Popular Measuring Instrument manuals by other brands

ALGE-Timing
ALGE-Timing Windspeed WS2 manual
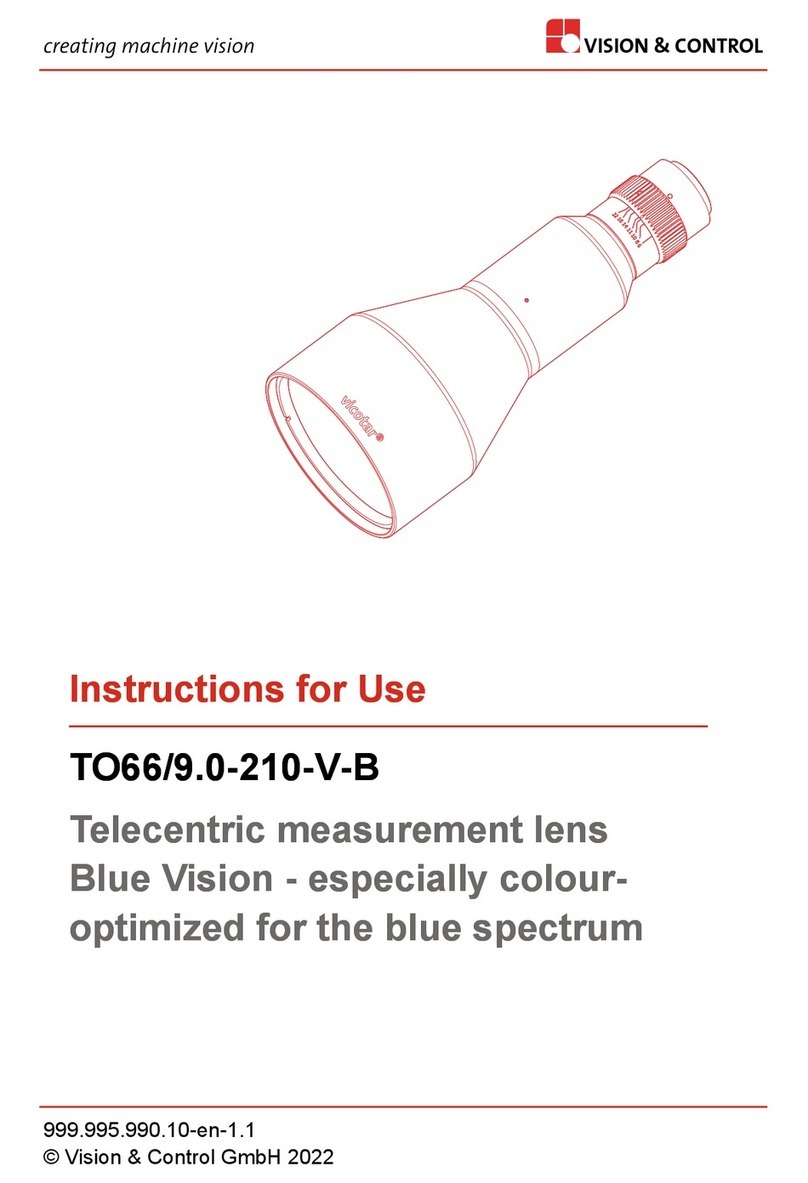
Vision & Control
Vision & Control TO66/9.0-210-V-B Instructions for use
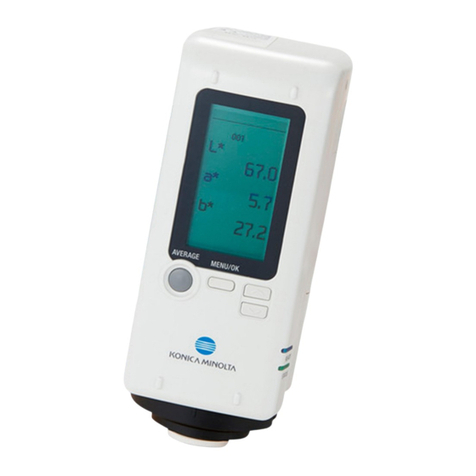
Konica Minolta
Konica Minolta CR-20 instruction manual
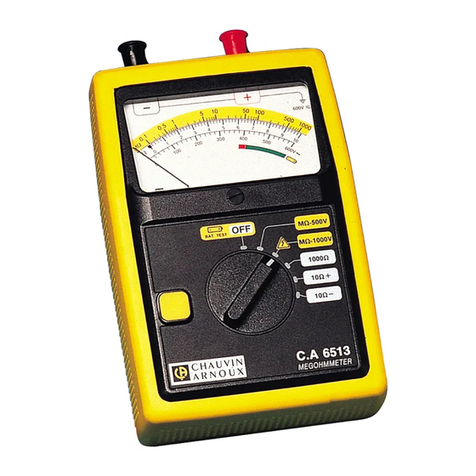
Chauvin Arnoux
Chauvin Arnoux C.A 6513 user manual
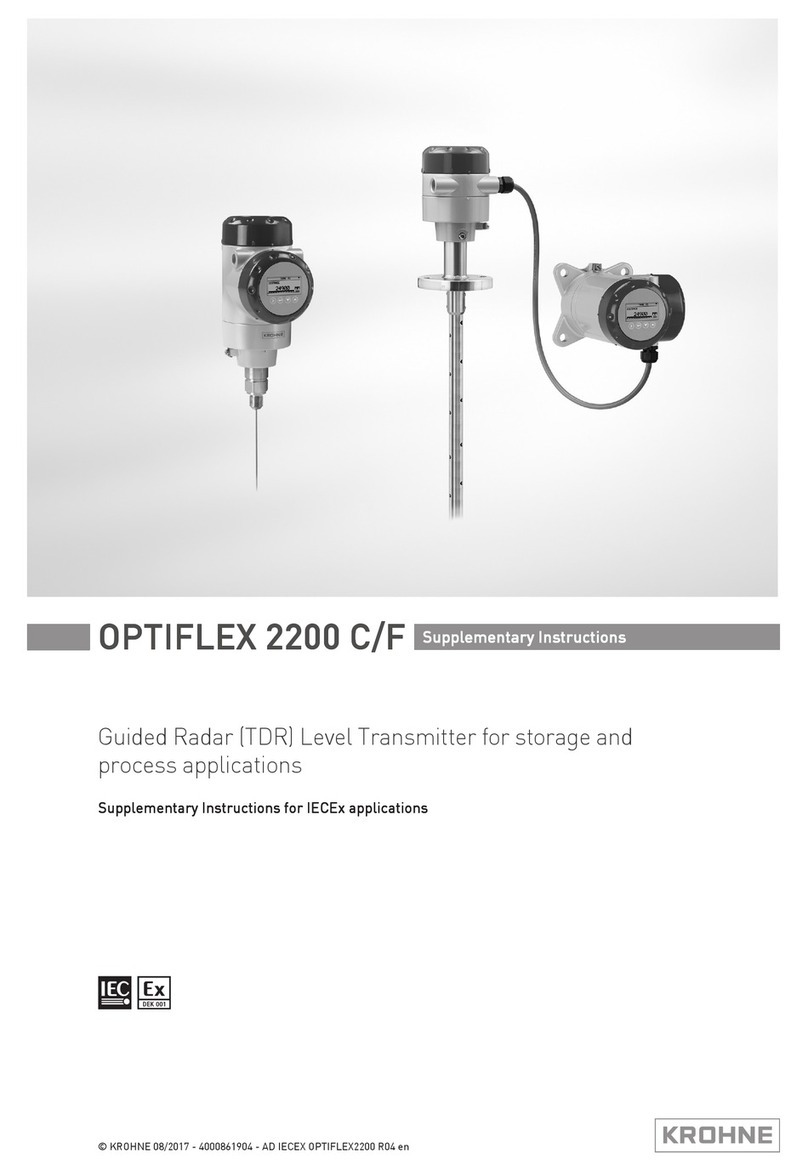
KROHNE
KROHNE OPTIFLEX 2200 C/F Supplementary instructions
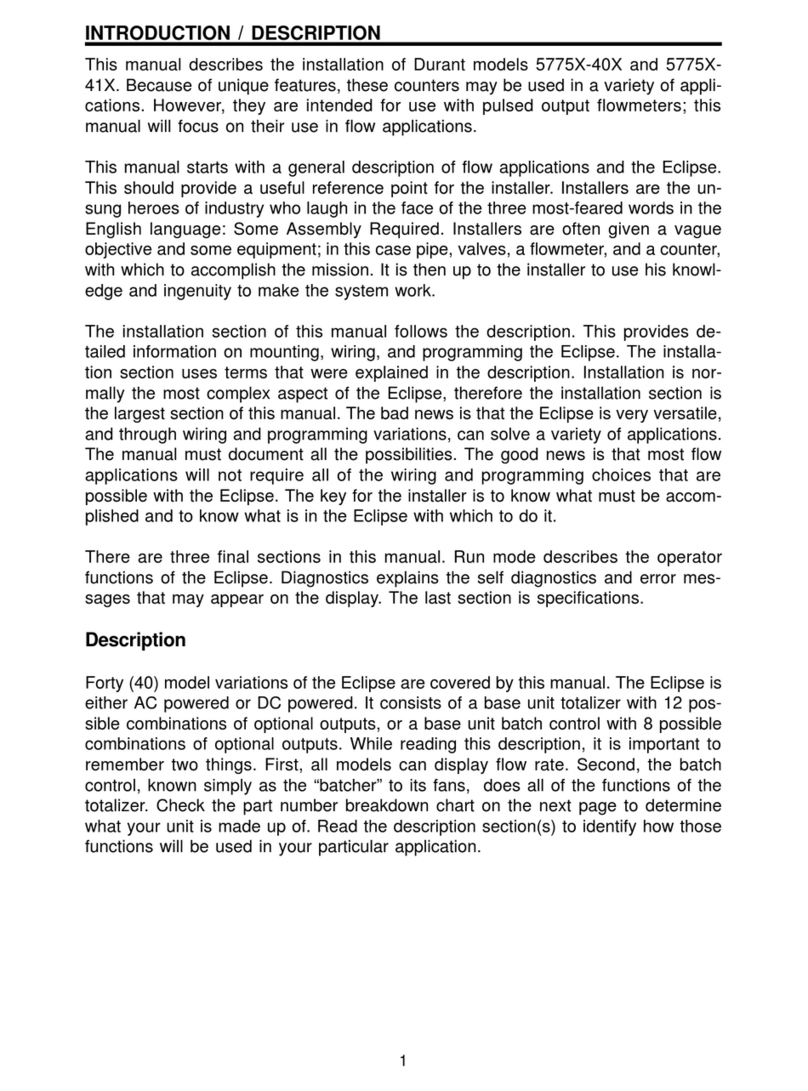
Eaton
Eaton Durant Eclipse 5775X-40 Series Installation and operation manual