BEA Br3 User manual

Br3
USER’S GUIDE
PROGRAMMABLE 3-RELAY LOGIC MODULE
1 Description
75.5501.02 EN 20091102 (75.5500) Page 1 of 15
The Br3 is a programmable 3 relay logic module that may be used for
multiple applications, including simple timing, door mounted sensor
inhibiting and advanced relay sequencing. The Br3 contains 12
different programmable functions which allow the technician to carry
one and only one module.
In addition to the ability to provide up to 3 Amps through the rst
two relays and 1 Amp through the third relay used in ‘‘DRY’’ mode,
the Br3 provides the ability to select a ‘WET’ voltage output of
up to 1 Amp on Relay 1 to power electric strikes and magnetic
locks without the need for an external power supply. This feature
can greatly simplify the installation (as long as the power supply
powering the Br3 is rated for 1 Amp).
The ‘WET’ output can also be set using jumpers to output DC if the Br3 is supplied with AC, otherwise it will just pass the AC voltage that is
supplied. Similarly if powered by DC, the ‘WET’ output will only output DC.
The module provides removable screw terminal connectors which help to reduce extra wiring.
Another feature of the Br3 is that it also provides an easy 2-button digital programming with a user-friendly display, hold times being adjustable
from 0 to 60 seconds, and delay times being adjustable from 0 to 60 seconds with ¼, ½ and ¾ also available to the applicable functions.
Programming
Push
Buttons
‘WET’ Output Selector
Inputs / Outputs
Br3 APPLICATIONS GUIDE
(Refer to the corresponding page number for a more detailed description and programming of each function.)
FUNCTION SUBJECT DESCRIPTION PAGE
1 0
(MC10)
Simple Timer Provides an activation of Relay 1 triggered by Input 1. The function also provides an option for
reverse-logic on the activation of Input 1. 4
1 1
(MC11)
Ratchet/Latching Provides a ratcheting/latching of Relay 1 triggered by Input 1. Each trigger of Input 1 will change the
state of Relay 1. 4
2 1
(LE21)
Inhibitor w/Door
Position Input Provides an activation of Relay 1 with an inhibitor of activation of Input 1 until Input 2, Input 3 or
‘WET’ Input is triggered, which all activate Relay 1. Additionally Input 4 provides a door position switch
input for which closing it will re-inhibit Input 1. 5
2 2
(LE22)
2 Relay Sequence
Inhibitor w/Door
Position Input
Provides a sequence for Relay 1 and/or Relay 2 with an inhibitor of activation of Input 1 until Input
2, Input 3 or ‘WET’ Input is triggered, which all activate the sequence. Additionally Input 4 provides
a door position switch input for which closing it will re-inhibit Input 1. Simply put this function is a
combination between a LE21 and MC25.
6
2 5
(MC25)
2 Relay Sequence Provides a sequence for Relay 1 and/or Relay 2 triggered by Input 1 or ‘WET’ Input.
7
2 8
(MC28)
2 Relay Sequence
w/Door Position
Input
Provides a sequence for Relay 1 and/or Relay 2 triggered by Input 1 or ‘WET’ Input. Additionally Input
2 provides a door position switch input which allows the delay to run when Input 2 is opened, but not
run when closed. Simply put, this function is an MC25 with a normally opened door position switch
input to determine if the delay should run.
8
2 9
(MC29)
Relay 1
Deactivation
Timer
Provides a sequence for Relay 1 and/or Relay 2 triggered by Input 1 or ‘WET’ Input. Additionally Input
2 provides a door position switch input which allows Relay 1 to deactivate once Input 2 is opened after
the sequence has run. Input 2 also allows the delay to run when Input 2 is opened, but not run when
closed, as in the MC28. Input 3 provides an input to disable the sequence whose input logic is also
selectable. Simply put Relay 1 will be active the entire time until the normally opened door position
switch signies that the door has come closed again.
9
3 5
(MC35)
3 Relay Sequence Provides a sequence for Relay 1 and/or Relay 2 and/or Relay 3 triggered by Input 1 or ‘WET’ Input.
Simply put this function is a MC25 with three relays instead of two. 10
5 0
(MC50)
Interlock Timer
w/Door Position
Inputs
Provides an interlock of Relay 1 and Relay 2 triggered by Inputs 1 and 2, with door position switch
inputs on Input 3 for Input 1and Input 4 for Input 2. Only one relay will be allowed to operate at a
time thus making the two relays interlocked or mutually exclusive. In order to activate a relay, its
corresponding position switch input must be closed.
11
5 5
(MC55)
Interlock Ratchet
w/Door Position
Inputs
Provides an interlock ratchet of Relay 1 and Relay 2 triggered by Inputs 1 and 2, with door position
switch inputs on Input 3 for Input 1 and Input 4 for Input 2. Only one Relay will be allowed to operate
at a time thus making the two relays interlocked or mutually exclusive. In order to activate a relay, its
corresponding position switch input must be closed. Each trigger of an input will change the state of its
respective relay.
12
6 5
(MC65)
2-Way, 2 Relay
Sequence Provides a two-way sequencer to sequence Relay 1 and/or Relay 2 triggered by Input 1. Similarly, it
also provides a sequence in the opposite direction to sequence Relay 2 and/or Relay 1 triggered by
Input 2. Inputs 3 and 4 also trigger Relays 1 and 2 individually. 13
7 5
(MC75)
2 Relay Sequence Provides a sequence for Relay 1 and/or Relay 2 triggered by Input 1 or ‘WET’ Input.
14

Page 2 of 15 75.5501.02 EN 20091102 (75.5500)
2 Specications
3 Precautions
Shut off all power before attempting any wiring procedures.
Maintain a clean & safe environment when working in public areas.
Constantly be aware of pedestrian trafc around the door area.
Always stop pedestrian trafc through the doorway when performing tests that may result in unexpected reactions by the door.
ESD: Circuit boards are vulnerable to damage by electrostatic discharge. Before handling ensure you dissipate your body’s
charge.
Always check placement of components before powering up so that moving parts will not catch any wires or cause damage to
equipment.
Ensure compliance with all applicable safety standards (i.e. ANSI A156.10 / 19) upon completion of installation.
When preparing to wire multiple devices together for a ‘system’ conguration, it is best to ensure the correct operation of each
device independently before starting to help reduce troubleshooting time later, in the event of a discrepancy.
When applying equipment on a new installation, utilizing new electrical supply circuits, always ensure that correct line voltage
exists and is stable. Remember to shut the power back off once this is checked, before performing any wiring to the system.
DO NOT attempt any internal repair of the sensor. All repairs and/or component replacements must be performed by BEA, Inc.
Unauthorized disassembly or repair:
1. May jeopardize personal safety and may expose one to the risk of electrical shock.
2. May adversely affect the safe and reliable performance of the product resulting in a voided warranty.
*NOTE: If the Br3 is powered with AC voltage and is using the ‘WET” output to convert to DC, and the current draw of the device is greater
than .9 amps the upper temperature range is +130°F (54°C).
DESCRIPTION SPECIFICATION DESCRIPTION SPECIFICATION
Supply Voltage 12 to 24 VAC/VDC: +/- 10% Contact Rating ‘DRY’ - Relay 1
- Relay 2
- Relay 3
Contact Rating ‘WET’ - Relay 1
3 A at 24 VAC; 3 A at 30 VDC
3 A at 24 VAC; 3 A at 30 VDC
1 A at 24 VAC; 1 A at 30 VDC
1 A
Current Consumption 30 to 130 mA (‘DRY’ Output)
Temperature Range -15°F (-26°C) to +150°F (65°C)*Dimensions 5.2” (133mm) W x 2.2” (55mm) D x 1” (25mm) H
Input Specication Inputs 1 to 4: ‘DRY’ Contact
‘WET’ Input:
5 VAC/VDC to 24 VAC/VDC: +/- 10%
Housing Material ABS – Grey Translucent
4 Jumper Settings
1. The Br3 contains two (2) sets of jumpers. Both sets deal
with conguring Relay 1 options:
Jumper set 1 congures whether or not to output AC or
DC voltage if the ‘WET’ output is selected. Jumper set 2
congures whether or not the Relay 1 output is ‘WET’ or
‘DRY’. The ‘WET’ voltage output means that the module
will supply a voltage output of up to 1 Amp on Relay
1 to power electric strikes and magnetic locks without
the need for an external power supply. This feature can
greatly simplify the installation (as long as the power
supply powering the Br3 is rated for 1 Amp).
The ‘WET’ output can also be set using jumpers to output
DC if the Br3 is supplied with AC, otherwise it will just
pass the AC voltage that is supplied. Similarly if powered
by DC, the ‘WET’ output will only output DC.
• To set Relay 1 to output DC (if ‘WET’) move both shunts (2) on Jumper Set 1, to the two (2) lower pins.
• To set Relay 1 to output AC (if ‘WET’ and powered with AC) move both shunts (2) on Jumper Set 1, to the two (2) upper pins.
• To set Relay 1 to output ‘DRY’ (Jumper Set 1 becomes unused), move both shunts (2) on Jumper Set 2, to the two (2) lower pins.
• To set Relay 1 to output ‘WET’, move both shunts (2) on Jumper Set 2, to the two (2) upper pins.
GND
IN-1
GND
IN-2
GND
IN-3
GND
IN-4
1 2 3 4
WET
WET
WET
NC
NO
COM
NC
NO
COM
12-24V
AC/DC
RELAYS
1 2
POWER RELAY 1
INCR.
PARAM
SETUP
DC AC
DRY WET
INPUTS
00
NC
NO
COM
3
Br
3
CAUTION: RELAY 1 WET
OUTPUT OPTION
IS ACTIVE FOR
ALL FUNCTIONS.
NOTE: Default jumper settings make Relay 1 output
‘DRY’ only. All four jumpers set to lower pins.

Page 3 of 15 75.5501.02 EN 20091102 (75.5500)
4 Jumper Settings (Continued)
The following steps are to program the Br3 to select and congure the desired function.
1. When there is no function set, as is the case on an initial power on, or if you desire to change the function, the user must rst press and
hold both push buttons (INCR & PARAM) for three (3) seconds to activate the display. At this point the display will toggle between FF and
00 every one (1) second for ve (5) seconds after the last button has been pressed.
2. By pressing on the INCR button, the user can toggle through each function to select the function. A display of 10 corresponds to
function MC10, 11 corresponds to function MC11, etc. Once you reach the last function, 75, the list will rollover to the beginning.
NOTE: Selecting 00 disables the module.
3. After selecting the function, the user can then press the PARAM button to cycle through and set the parameters dened for that particular
function, if applicable. If there are any function parameters, the display will toggle between the parameter and its current value every
one (1) second for ve (5) seconds after the last button has been pressed. If there are no parameters, NP and -- will be displayed as a
parameter and its value for ve (5) seconds.
NOTE: Once the PARAM button has been pressed as to set the function’s respective parameters and values, the user will not be able to
go back and select a different function until the display goes inactive and the user repeats the above process starting with Step
1. This prevents the user from inadvertently changing functions or selecting variables from different functions.
4. After selecting the function’s parameter to change, the user can press the INCR button to increment the parameter’s value. A single
press of the INCR button will increment the value by one, but holding the increment button will allow for a rapid increment of the value.
5. Once all parameters for the function are set, wait the ve (5) seconds for the display to go inactive and the Br3 to save the updated
parameters. The Br3 is now programmed. As long as no relays are active, the display will show the function selected, otherwise it will
show those relays. Once the values are changed, they are only saved after the display goes inactive again (5 seconds).
NOTE: Remember that the INCR push button always increments the value of the parameter that you are looking at, and the PARAM
push button toggles through the available parameters.
NOTE: To change only the value of a parameter under the function, start the process with Step 3.
5 Selecting the Function
PRECAUTIONS TO OBSERVE WHEN USING A ‘WET’ OUTPUT
Never change the switch settings when the module has power connected to it or when a load is applied.
Never allow 2 different voltage sources to be connected to the load (electric strike for example) at the same time. This can result in serious
damage to equipment.
Always move both shunts when changing a jumper set.
If an EL device is being powered by a separate power source, DO NOT select the ‘WET’ output option on the Br3. If ‘WET’ is selected, the
next activation of the module will send a voltage to the load and if there is already a voltage being applied from another source, the Br3 and
possibly the load will be permanently damaged.
When using the ‘WET’ output option on the Br3, set all desired switch positions (‘WET’ – ‘DRY’ and AC – DC) before the module is powered
and before any loads are applied.
When DC ‘WET’ output is selected, COM terminal is positive(+) and the ground(-) is switched between NO and NC.
Ensure there is no other voltage connected to the load. Whatever the Input voltage is at the Br3, the output will correspond. The following
can also be observed:
1. If voltage Input at the Br3 is AC, then output selection can be AC or DC.
2. If voltage Input at the Br3 is DC, then output selection can only be DC.
3. The maximum load applied to Relay 1 should never exceed 1A. If more than one device is to be connected, add the consumption values
together for a total value. If current is excessive, damage to equipment can result.
4. On the Br3, the ‘WET’ output is only available at Relay 1.
When supplying Br3 with AC input voltage, and selecting ‘WET’ output on relay with DC conversion, you actually get rectied AC voltage,
which is identical to applying a bridge rectier to any AC voltage.
CAUTION: Relay 1 ‘WET’ OPTION IS ACTIVE FOR ALL FUNCTIONS!

The MC10 provides an activation of Relay 1 triggered by Input
1. The function also provides an option for reverse-logic for
the activation of Input 1. Adjustable parameters include H1 for
activation hold time of Relay 1 and RL for reverse logic for Input
1. A re-activation of Input 1 will re-start the hold timer and keep
the relay active. A maintained Input 1 will freeze the hold timer
thus keeping its relay active until the Input is released, which will
allow the hold timer to expire and deactivate the relay normally.
A reverse logic version of the timer function is also offered in
which the logic on Input 1 is reversed, thus to activate the timer,
the input must be opened.
A typical application is to have a push-plate to activate a door
controller. For this scenario the push-plate would be wired to
Input 1 and the door controller would be wired to Relay 1. An
example wiring diagram for this scenario is shown.
MC10 SETUP
1. Wire the Br3 accordingly.
2. Select the MC10 as the function according to the steps outlined in Section 5 – Selecting the Function.
• Press and hold both push buttons (INCR & PARAM) for three (3) seconds to activate the display.
• Press the INCR button to toggle through each function and select 10.
3. Set the MC10 parameters according to the steps outlined in Section 5 – Selecting the Function.
• Press PARAM button to cycle through and set the parameters.
• Press the INCR button to increment the parameter’s value.
Parameters for the MC10 function are shown in the chart. Set the parameters as needed for the application, and wait for the display to
become inactive to save the conguration.
PARAMETER
(PARAM Button)
DESCRIPTION POSSIBLE VALUES
(INCR Button)
H1 Relay 1 hold time ‘00’ through ‘60’. Relay 1 hold time will not begin counting down until the release of Input 1.
RL Activation Logic
Input
‘00’ = Normal Logic: The activation device at Input 1 must be normally opened
and close its contacts to trigger the timer.
‘01’ = Reverse Logic: The activation device at Input 1 must be normally
closed and open its contacts to trigger the timer.
4. Once programming is complete, test the Br3. Trigger the timer via Input 1. Ensure that Relay 1 activates and its hold time is as programmed.
The display will show R 1 when Relay 1 is energized and 1 0 when de-energized.
5. Upon completion of the above steps, walk test the door to ensure all functions, timers, sensors, etc. are working as intended, and that the
system is in compliance with all applicable standards (i.e. ANSI A156.10, A156.19).
75.5501.02 EN 20091102 (75.5500) Page 4 of 15
6A Function 10 - Timer Module (MC10)
GND
IN-1
GND
IN-2
GND
IN-3
GND
IN-4
1 2 3 4
WET
WET
WET
NC
NO
COM
NC
NO
COM
12-24V
AC/DC
RELAYS
1 2
POWER RELAY 1
INCR.
PARAM
SETUP
DC AC
DRY WET
INPUTS
1 0
NC
NO
COM
3
Br
3
CAUTION: RELAY 1 WET
OUTPUT OPTION
IS ACTIVE FOR
ALL FUNCTIONS.
12 to 24
VAC/VDC
+/- 10%
Directly to Activation
Circuit of Door Control
or Other Device.
Pushplate or other
Dry Contact device.
The MC11 function provides a ratcheting of Relay 1 triggered by
Input 1. Each trigger by Input 1 will change the state of Relay 1.
MC11 has NO adjustable parameters. If Input 1 is maintained,
Relay 1 will only change state once. Input 1 must then be opened
and re-closed for a relay change of state.
A typical application is to have a set of push-to-open and
push-to-close push-plates connected to a door in the instance
that a single hold time will not suit all users of the door. For
this scenario the push-to-open push-plate would be wired in
parallel with the push-to-close push-plate to Input 1 and the
door controller would be wired to Relay 1. An example wiring
diagram for this scenario is shown.
MC11 SETUP
1. Wire the Br3 accordingly.
2. Select the MC11 as the function according to the steps outlined in Section 5 – Selecting the Function.
• Press and hold both push buttons (INCR & PARAM) for three (3) seconds to activate the display.
• Press the INCR button to toggle through each function and select 11.
3. There are NO parameters to set for the MC11 as the state of Relay 1 is not based on time, so just wait for the display to become inactive to
save the conguration.
4. Once programming is complete, test the Br3. Trigger the ratchet via Input 1. Ensure that Relay 1 changes state and that it is maintained.
The display will show R1 when Relay 1 is energized. Trigger the ratchet again via Input 1 and ensure Relay 1 changes state again. The
display will show 11 when Relay 1 is de-energized.
5. Upon completion of the above steps, walk test the door to ensure all functions, timers, sensors, etc. are working as intended, and that the
system is in compliance with all applicable standards (ie. ANSI A 156.10, A156.19).
6B Function 11 - Ratchet (MC11)
GND
IN-1
GND
IN-2
GND
IN-3
GND
IN-4
1 2 3 4
WET
WET
WET
NC
NO
COM
NC
NO
COM
12-24V
AC/DC
RELAYS
1 2
POWER RELAY 1
INCR.
PARAM
SETUP
DC AC
DRY WET
INPUTS
1 1
NC
NO
COM
3
Br
3
CAUTION: RELAY 1 WET
OUTPUT OPTION
IS ACTIVE FOR
ALL FUNCTIONS.
12 to 24
VAC/VDC
+/- 10%
Directly to Activation
Circuit of Door Control
or Other Device.
Pushplate or other
Dry Contact device.

The LE21 function provides activation of Relay 1 with an inhibitor
of activation for Input 1 until Input 2, Input 3 or ‘WET’ Input is
triggered, which all activate Relay 1. Additionally Input 4 provides
a door position switch input for which closing it will re-inhibit Input 1.
Adjustable parameters include H1 for activation hold time of Relay 1.
NOTE: The door position switch must have a closed contact when
the door is closed and an opened contact when it is not.
A typical application is a ‘Low-Energy’ situation in which you
have only ‘Knowing-Act’ activation devices such as push-plates,
a re-activation device, such as a SuperScan, on the door for safety
and a door position switch. For this scenario the push-plates
would be wired to Inputs 2 and/or 3, the SuperScan would be
wired to Input 1, a door position switch on Input 4 and the door
controller on Relay 1. When the door position switch on Input 4
is closed, the SuperScan Input is ignored (inhibited) and only
becomes a re-activation device (uninhibited) after an activation
on Input 2 or Input 3. The SuperScan on Input 1 will remain
uninhibited until the door is closed again, closing Input 4.
An example wiring diagram for this scenario is shown.
NOTE: While the ‘WET’ Input is not involved in our typical application,
it will still function as Input 2 and Input 3.
LE21 SETUP
1. Wire the Br3 accordingly.
2. Select the LE21 as the function according to the steps outlined in Section 5 – Selecting the Function.
• Press and hold both push buttons (INCR & PARAM) for three (3) seconds to activate the display.
• Press the INCR button to toggle through each function and select 2 1.
3. Set the lone LE21 parameter according to the steps outlined in Section 5 – Selecting the Function.
• Press PARAM button to cycle through and set the parameters.
• Press the INCR button to increment the parameter’s value.
The single parameter for the LE21 function is shown in the chart. Set it as needed for the application, and wait for the display to become
inactive to save the conguration
PARAMETER
(PARAM Button)
DESCRIPTION POSSIBLE VALUES
(INCR Button)
H1 Relay 1 hold time ‘00’ through ‘60’. Relay 1 hold time will not begin counting down until the release of an
activation input.
4. Once programming is complete, test the Br3. Attempt to trigger the timer via the re-activation device tied to Input 1. Ensure that Relay 1 does
NOT energize as it should be inhibited. The display should still show 21 since Relay 1 is de-energized. Now trigger the timer via Input 2, Input
3 or ‘WET’ Input. Ensure that Relay 1 activates and its hold time and is as programmed. The display will show R1 when Relay 1 is energized.
Before the door closes attempt to re-activate the timer via the device tied to Input 1. The door should re-open and the timer should restart. Once
again observe the relay hold time and ensure that it is as programmed. Let the door close to close Input 4 via the door position switch. Once
again attempt to trigger the timer via the re-activation device tied to Input 1. Ensure that Relay 1 does NOT energize as it should be re-inhibited.
5. Upon completion of the above steps, walk test the door to ensure all functions, timers, sensors, etc. are working as intended, and that the system
is in compliance with all applicable standards (i.e. ANSI A156.10, A156.19).).
6C Function 21 - Inhibitor (LE21)
GND
IN-1
GND
IN-2
GND
IN-3
GND
IN-4
1 2 3 4
WET
WET
WET
NC
NO
COM
NC
NO
COM
12-24V
AC/DC
RELAYS
1 2
POWER RELAY 1
INCR.
PARAM
SETUP
DC AC
DRY WET
INPUTS
2 1
NC
NO
COM
3
Br
3
CAUTION: RELAY 1 WET
OUTPUT OPTION
IS ACTIVE FOR
ALL FUNCTIONS.
12 to 24
VAC/VDC
+/- 10%
Directly to Activation
Circuit of Door Control
or Other Device.
Inputs 2 & 3 can be used for Pushplate
input or other activation device.
Input 4 is for the door position switch.
Switch is closed when door is closed.
Input 1 for SuperScan
at approach side.
‘ W E T ’
12 to 24
VAC/VDC
+/- 10%
INPUT
+ -
Page 5 of 15 75.5501.02 EN 20091102 (75.5500)

75.5501.02 EN 20091102 (75.5500) Page 6 of 15
The LE22 function provides a sequence for Relay 1 and/or Relay
2 with an inhibitor of activation for Input 1 until Input 2, Input
3 or ‘WET’ Input is triggered, which all activate the sequence.
Additionally Input 4 provides a door position switch input for
which closing it will re-inhibit Input 1. Simply put this function is a
combination between a LE21 and MC25. Adjustable parameters
include H1 for activation hold time of Relay 1, H2 for activation
hold time of Relay 2 and D1 for delay between activation of
Relay 1 to Relay 2. A re-activation of the sequence before it
expires will re-start both hold timers and keep the relays active. A
maintained input will freeze both hold timers, thus keeping their
relays active until the input is released, which will allow the hold
timers to expire and deactivate the relays normally.
NOTE: The delay timer will only re one time during
initial activation or maintained input.
NOTE: The door position switch must have a closed
contact when the door is closed and an opened
contact when it is not.
A typical application is a ‘Low-Energy’ situation, which needs
security, in which you have only ‘Knowing-Act’ activation
devices such as push-plates and a re-activation device, such
as a SuperScan, on the door for safety and a door position
swtich. For this scenario the push-plates would be wired to
Inputs 2 and/or 3, the SuperScan would be wired to Input 1,
a door position switch on Input 4, a security device such as a
Maglock or electric strike on Relay 1 and the door controller on
Relay 2. When the door position switch on Input 4 is closed,
the SuperScan input is ignored (inhibited) and only becomes a re-activation device (uninhibited) after an activation on Input 2 or Input 3. The
SuperScan on Input 1 will remain uninhibited until the door is closed again closing Input 4. An example wiring diagram for this scenario is shown.
NOTE: While the ‘WET’ Input is not involved in our typical application, it will still function as Input 2 and Input 3 do if used.
LE22 SETUP
1. Wire the Br3 accordingly.
2. Select the LE22 as the function according to the steps outlined in Section 5 – Selecting the Function.
• Press and hold both push buttons (INCR & PARAM) for three (3) seconds to activate the display.
• Press the INCR button to toggle through each function and select 22.
3. Set the LE22 parameters according to the steps outlined in Section 5 – Selecting the Function.
• Press PARAM button to cycle through and set the parameters.
• Press the INCR button to increment the parameter’s value.
Parameters for the LE22 function are shown in the chart. Set the parameters as needed for the application and wait for the display to
become inactive to save the conguration.
PARAMETER
(PARAM Button)
DESCRIPTION POSSIBLE VALUES
(INCR Button)
H1 Relay 1 hold time ‘00’ through ‘60’. Relay 1 hold time will not begin counting down until the release of Input 1.
H2 Relay 2 hold time ‘00’ through ‘60’. Relay 2 hold time will not begin counting down until the delay between
Relay 1 and Relay 2 expires.
D1 Delay between
Relay 1 and Relay 2
‘00’, ‘_1’ (1/4), ‘_2’ (1/2), ‘_3’ (3/4), ‘01’ through ‘60’ seconds. The delay time will begin
counting down with activation of sequence.
4. Once programming is complete, test the Br3. Attempt to trigger the sequence via the re-activation device tied to Input 1. Ensure that
the sequence does NOT start as it should be inhibited. The display should still show 22 since Relay 1 is de-energized. Now trigger the
sequence via Input 2, Input 3 or ‘WET’ Input. Ensure that the sequence runs and the Relays activate and the timers are as programmed.
The display will show R1 when Relay 1 is energized, R2 when Relay 2 is energized or R= when both Relay 1 and Relay 2 are energized at the
same time. Before the door closes attempt to re-activate the sequence via the device tied to Input 1. The door should re-open immediately
and the relay hold timers should restart. Once again observe the relay hold times and ensure that it is as programmed. Let the door close
and trigger Input 4 via the door position switch. Once again attempt to trigger the sequence via the re-activation device tied to Input 1.
Ensure that sequence does NOT start as it should be re-inhibited.
5. Upon completion of the above steps, walk test the door to ensure all functions, timers, sensors, etc. are working as intended, and that the
system is in compliance with all applicable standards (i.e. ANSI A156.10, A156.19).
6D Function 22 - 2 Relay Sequence w/Inhibitor (LE22)
GND
IN-1
GND
IN-2
GND
IN-3
GND
IN-4
1 2 3 4
WET
WET
WET
NC
NO
COM
NC
NO
COM
12-24V
AC/DC
RELAYS
1 2
POWER RELAY 1
INCR.
PARAM
SETUP
DC AC
DRY WET
INPUTS
2 2
NC
NO
COM
3
Br
3
CAUTION: RELAY 1 WET
OUTPUT OPTION
IS ACTIVE FOR
ALL FUNCTIONS.
12 to 24
VAC/VDC
+/- 10%
Inputs 2 & 3 can be used for Pushplate
input or other activation device.
Input 4 is for the door position switch.
Switch is closed when door is closed.
Input 1 for SuperScan
at approach side.
‘ W E T ’
12 to 24
VAC/VDC
+/- 10%
INPUT
+ -
To Activation Circuit
of Door Control.
Typically Connected to Lock Device. When DC ‘WET’
Output is Selected for Relay 1, COM Terminal is Positive (+).

Page 7 of 15 75.5501.02 EN 20091102 (75.5500)
The MC25 function provides a sequence for Relay 1 and/
or Relay 2 triggered by Input 1 or ‘WET’ Input. Adjustable
parameters include H 1 for activation hold time of Relay 1, H 2
for activation hold time of Relay 2 and D 1 for delay between
activation of Relay 1 to Relay 2. A re-activation of Input 1 or
‘WET’ Input before the sequence expires will re-start both
hold timers and keep the relays active. A maintained input will
freeze both hold timers, thus keeping their relays active until the
input is released, which will allow the hold timers to expire and
deactivate the relays normally.
NOTE: The delay timer will only re one time during initial
activation or maintained input.
NOTE: The functionality for MC25 has changed slightly in this
version as it will also check the ‘WET’ Input.
A typical application is a security door in which you have a push-
plate to start the sequence to unlock the security device, such as
a Maglock or electric strike and then activate the door controller.
For this scenario the push-plate would be wired to Input 1, the
security device would be wired to Relay 1 and the door controller
would be wired to Relay 2. An example wiring diagram for this
scenario is shown.
NOTE: While the ‘WET’ Input is not involved in our typical
application, it will still function as Input 1 does if used
MC25 SETUP
1. Wire the Br3 accordingly.
2. Select the MC25 as the function according to the steps outlined in Section 5 – Selecting the Function.
• Press and hold both push buttons (INCR & PARAM) for three (3) seconds to activate the display.
• Press the INCR button to toggle through each function and select 25.
3. Set the MC25 parameters according to the steps outlined in Section 5 – Selecting the Function.
• Press PARAM button to cycle through and set the parameters.
• Press the INCR button to increment the parameter’s value.
Parameters for the MC25 function are shown in the chart. Set the parameters as needed for the application, and wait for the display to
become inactive to save the conguration.
PARAMETER
(PARAM Button)
DESCRIPTION POSSIBLE VALUES
(INCR Button)
H1 Relay 1 hold time ‘00’ through ‘60’ - Relay 1 hold time will not begin counting down until the release of Input 1 or
‘WET’ Input.
H2 Relay 2 hold time ‘00’ through ‘60’ - Relay 2 hold time will not begin counting down until the delay between
Relay 1 and Relay 2 expires.
D1 Delay between
Relay 1 and Relay 2
‘00’, ‘_1’ (1/4), ‘_2’ (1/2), ‘_3’ (3/4), ‘01’ through ‘60’ seconds. The delay time will begin
counting down with the activation of the sequence.
4. Once programming is complete, test the Br3. Trigger the sequence via Input 1 or ‘WET’ Input. Ensure that the sequence runs and the
relays activate and the timers are as programmed. The display will show R1 when Relay 1 is energized, R2 when Relay 2 is energized and R=
when both Relay 1 and Relay 2 are energized at the same time.
5. Upon completion of the above steps, walk test the door to ensure all functions, timers, sensors, etc. are working as intended, and that the
system is in compliance with all applicable standards (i.e. ANSI A156.10, A156.19).
6E Function 25 - 2 Relay Sequence (MC25)
GND
IN-1
GND
IN-2
GND
IN-3
GND
IN-4
1 2 3 4
WET
WET
WET
NC
NO
COM
NC
NO
COM
12-24V
AC/DC
RELAYS
1 2
POWER RELAY 1
INCR.
PARAM
SETUP
DC AC
DRY WET
INPUTS
2 5
NC
NO
COM
3
Br
3
CAUTION: RELAY 1 WET
OUTPUT OPTION
IS ACTIVE FOR
ALL FUNCTIONS.
12 to 24
VAC/VDC
+/- 10%
To Activation Circuit
of Door Control.
Pushplate or other
Dry Contact Device.
‘ W E T ’
12 to 24
VAC/VDC
+/- 10%
INPUT
+ -
Typically Connected to
Lock Device. When DC‘WET’
Output is Selected for Relay 1,
COM Terminal is Positive (+).

The MC28 function provides a sequence for Relay 1 and/
or Relay 2 triggered by Input 1 or ‘WET’ Input. Additionally
Input 2 provides a door position switch input which allows the
delay to run when Input 2 is opened, but not run when closed.
Simply put, this function is an MC25 with a normally opened
door position switch input to determine if the delay should run.
Adjustable parameters include H1 for activation hold time of
Relay 1, H2 for activation hold time of Relay 2 and D1 for delay
between activation of Relay 1 to Relay 2. A maintained input will
freeze both hold timers, thus keeping their relays active until the
input is released, which will allow the hold timers to expire and
deactivate the relays normally.
NOTE: The delay timer will only re when Input 2 is opened.
NOTE: The door position switch must have an opened contact
when the door is closed, and a closed contact when it is
not. (Position switch logic is different than 21, 22, 50 and
55.)
A typical application is a security door in which you have a push-
plate to start the sequence to unlock the security device, such as
a Maglock or electric strike and then activate the door controller
and an additional door position switch. For this scenario the
push-plate would be wired to Input 1, the position switch would
be wired to Input 2, the security device would be wired to Relay
1 and the door controller would be wired to Relay 2. An example
wiring diagram for this scenario is shown.
NOTE: While the ‘WET’ Input is not involved in our typical
application, it will still function as Input 1 does if used.
MC28 SETUP
1. Wire the Br3 accordingly.
2. Select the MC28 as the function according to the steps outlined in Section 5 – Selecting the Function.
• Press and hold both push buttons (INCR & PARAM) for three (3) seconds to activate the display.
• Press the INCR button to toggle through each function and select 28.
3. Set the MC28 parameters according to the steps outlined in Section 5 – Selecting the Function.
• Press PARAM button to cycle through and set the parameters.
• Press the INCR button to increment the parameter’s value.
Parameters for the MC28 function are shown in the chart. Set the parameters as needed for the application, and wait for the display to
become inactive to save the conguration.
PARAMETER
(PARAM Button)
DESCRIPTION POSSIBLE VALUES
(INCR Button)
H1 Relay 1 hold time ‘00’ through ‘60’ - Relay 1 hold time will not begin counting down until the release of Input 1 or
‘WET’ Input.
H2 Relay 2 hold time ‘00’ through ‘60’ - Relay 2 hold time will not begin counting down until the delay between
Relay 1 and Relay 2 expires.
D1 Delay between
Relay 1 and Relay 2
‘00’, ‘_1’ (1/4), ‘_2’ (1/2), ‘_3’ (3/4), ‘01’ through ‘60’ seconds. The delay time will begin
counting down with the activation of the sequence.
4. Once programming is complete, test the Br3. Trigger the sequence via Input 1 or ‘WET’ Input. Ensure that the sequence runs and the
relays activate and the timers are as programmed. The display will show R1 when Relay 1 is energized, R2 when Relay 2 is energized and
R= when both Relay 1 and Relay 2 are energized at the same time. Ensure that the delay between Relay 1 and Relay 2 runs when the
sequence starts from the door closed position. Now, re-run the sequence; however this time before the door reaches the closed position,
reactivate the door and ensure that the door reactivates immediately as the delay between timer, D1 does NOT run.
5. Upon completion of the above steps, walk test the door to ensure all functions, timers, sensors, etc. are working as intended and that the
system is in compliance with all applicable standards (i.e. ANSI A156.10, A156.19).
6F Function 28 - 2 Relay Sequence w/Position Input (MC28)
75.5501.02 EN 20091102 (75.5500) Page 8 of 15
GND
IN-1
GND
IN-2
GND
IN-3
GND
IN-4
1 2 3 4
WET
WET
WET
NC
NO
COM
NC
NO
COM
12-24V
AC/DC
RELAYS
1 2
POWER RELAY 1
INCR.
PARAM
SETUP
DC AC
DRY WET
INPUTS
2 8
NC
NO
COM
3
Br
3
CAUTION: RELAY 1 WET
OUTPUT OPTION
IS ACTIVE FOR
ALL FUNCTIONS.
12 to 24
VAC/VDC
+/- 10%
To Activation Circuit
of Door Control.
Pushplate or other
Dry Contact Device.
‘ W E T ’
12 to 24
VAC/VDC
+/- 10%
INPUT
+ -
Typically Connected to Lock Device. When DC ‘WET’
Output is Selected for Relay 1, COM Terminal is Positive (+).
Input 2 is for the Door Position Switch.
Switch is open when door is closed.

The MC29 function provides a sequence for Relay 1 and/or Relay
2 triggered by Input 1 or ‘WET’ Input. Additionally Input 2 provides
a door position switch input which allows the Relay 1 to deactivate
once Input 2 is opened after the sequence has run. Input 2 also
allows the delay to run when Input 2 is opened, but not run when
closed, as in the MC28. Input 3 provides an input to disable the
sequence whose logic is also selectable. Simply put Relay 1 will
be active the entire time until the normally opened door position
switch signies that the door has come closed again. Adjustable
parameters include H1 for activation hold time of Relay 1 after the
door position switch has closed, H2 for activation hold time of Relay
2, D1 for delay between activation of Relay 1 to Relay 2 and RL for
reverse logic for Input 3.
NOTE: The delay timer will only re one time during initial activation
or maintained input.
NOTE: The door position switch must have an opened contact
when the door is closed, and a closed contact when it is not.
(Position switch logic is different than 21, 22, 50 and 55.)
A typical application is a security door in which you have a push-
plate to start the sequence to unlock the Maglock, which you would
want unlocked for the entire sequence until the door becomes
closed again, then activate the door controller and an additional
door position switch. For this scenario the push-plate would be
wired to Input 1, the position switch would be wired to Input 2, the
Maglock would be wired to Relay 1 and the door controller would
be wired to Relay 2. An example wiring diagram for this scenario is
shown.
NOTE: While the ‘WET’ Input is not involved in our typical
application, it will still function as Input 1 does if used.
MC29 SETUP
1. Wire the Br3 accordingly.
2. Select the MC29 as the function according to the steps outlined in Section 5 – Selecting the Function.
• Press and hold both push buttons (INCR & PARAM) for three (3) seconds to activate the display.
• Press the INCR button to toggle through each function and select 29.
3. Set the MC29 parameters according to the steps outlined in Section 5 – Selecting the Function.
• Press PARAM button to cycle through and set the parameters.
• Press the INCR button to increment the parameter’s value.
Parameters for the MC29 function are shown in the chart. Set the parameters as needed for the application, and wait for the display to
become inactive to save the conguration.
PARAMETER
(PARAM Button)
DESCRIPTION POSSIBLE VALUES
(INCR Button)
H1 Relay 1 hold time ‘00’ through ‘60’ - Relay 1 hold time will not begin counting down until the release of Input 2.
H2 Relay 2 hold time ‘00’ through ‘60’ - Relay 2 hold time will not begin counting down until the delay between
Relay 1 and Relay 2 expires.
D1 Delay between
Relay 1 and Relay 2 ‘00’, ‘_1’ (1/4), ‘_2’ (1/2), ‘_3’ (3/4), ‘01’ through ‘60’ seconds. The delay time will begin counting
down with the activation of the sequence.
RL Input 3 Logic
‘00’ = Normal Logic: The activation device at Input 3 must be normally opened
and close it’s contacts to disable the sequence.
‘01’ = Reverse Logic: The activation device at Input 3 must be normally
closed and open it’s contacts to disable the sequence.
4. Once programming is complete, test the Br3. Trigger the sequence via Input 1 or ‘WET’ Input. Ensure that the sequence runs and the
relays activate and the timers are as programmed. The display will show R1 when Relay 1 is energized, R2 when Relay 2 is energized and
R= when both Relay 1 and Relay 2 are energized at the same time. Ensure that the delay between Relay 1 and Relay 2 runs when the
sequence starts from the door closed position. Ensure that Relay 1 stays active the entire time until the door returns to the closed position.
Now, re-run the sequence; however this time before the door reaches the closed position, reactivate the door and ensure that the door
reactivates immediately as the delay between timer, D1 does NOT run. Finally check the sequence disabling feature by triggering Input 3,
while at the same time attempting to run the sequence by triggering Input 1 or ‘WET’ Input. The sequence should NOT run again until Input
3 is released.
5. Upon completion of the above steps, walk test the door to ensure all functions, timers, sensors, etc. are working as intended and that the
system is in compliance with all applicable standards (i.e. ANSI A156.10, A156.19).
6G Function 29 - Relay 1 Deactivation Timer (MC29)
Page 9 of 15 75.5501.02 EN 20091102 (75.5500)
GND
IN-1
GND
IN-2
GND
IN-3
GND
IN-4
1 2 3 4
WET
WET
WET
NC
NO
COM
NC
NO
COM
12-24V
AC/DC
RELAYS
1 2
POWER RELAY 1
INCR.
PARAM
SETUP
DC AC
DRY WET
INPUTS
2 9
NC
NO
COM
3
Br
3
CAUTION: RELAY 1 WET
OUTPUT OPTION
IS ACTIVE FOR
ALL FUNCTIONS.
12 to 24
VAC/VDC
+/- 10%
To Activation Circuit
of Door Control.
Pushplate or other
Dry Contact Device.
‘ W E T ’
12 to 24
VAC/VDC
+/- 10%
INPUT
+ -
Typically Connected to Lock Device. When DC ‘WET’
Output is Selected for Relay 1, COM Terminal is Positive (+).
Input 2 is for the Door Position Switch.
Switch is open when door is closed.
Fire Alarm Input
Disables normal operation.
NOTE: Input logic is selectible by ( R L )Reverse Logic.

6H Function 35 - 3 Relay Sequence (MC35)
75.5501.02 EN 20091102 (75.5500) Page 10 of 15
GND
IN-1
GND
IN-2
GND
IN-3
GND
IN-4
1 2 3 4
WET
WET
WET
NC
NO
COM
NC
NO
COM
12-24V
AC/DC
RELAYS
1 2
POWER RELAY 1
INCR.
PARAM
SETUP
DC AC
DRY WET
INPUTS
3 5
NC
NO
COM
3
Br
3
CAUTION: RELAY 1 WET
OUTPUT OPTION
IS ACTIVE FOR
ALL FUNCTIONS.
12 to 24
VAC/VDC
+/- 10%
To Activation
Circuit of
Door Control 1
Pushplate or other
Dry Contact Device.
‘ W E T ’
12 to 24
VAC/VDC
+/- 10%
INPUT
+ -
Typically Connected to
Lock Device. When DC‘WET’
Output is Selected for Relay 1,
COM Terminal is Positive (+).
To Activation
Circuit of
Door Control 2
The MC35 function provides a sequence for Relay 1 and/or
Relay 2 and/or Relay 3 triggered by Input 1 or ‘WET’ Input.
Simply put this function is a MC25 with three relays instead of
two. Adjustable parameters include H1 for activation hold time of
Relay 1, H2 for activation hold time of Relay 2, H3 for activation
hold time of Relay 3, D1 for delay between activation of Relay 1 to
Relay 2 and D2 for delay between activation of Relay 1 to Relay
3. A re-activation of Input 1 or ‘WET’ Input before the sequence
expires will re-start all hold timers and keep the relays active.
A maintained input will freeze all hold timers thus keeping their
relays active until the input is released, which will allow the hold
timers to expire and deactivate the relays normally.
NOTE: The delay timer will only re one time during initial
activation or maintained input.
A typical application is a secure pair of doors with ush bolts in
which you have a push-plate to start the sequence to unlock
the security device, such as a Maglock or electric strike, then
activate the rst door controller and then activate the second
door controller. For this scenario the push-plate would be wired
to Input 1, the security device would be wired to Relay 1, the rst
door controller would be wired to Relay 2 and the second door
controller would be wired to Relay 3.
NOTE: While the ‘WET’ Input is not involved in our typical
application, it will still function as Input 1 does if used.
MC35 SETUP
1. Wire the Br3 accordingly.
2. Select the MC35 as the function according to the steps outlined in Section 5 – Selecting the Function.
• Press and hold both push buttons (INCR & PARAM) for three (3) seconds to activate the display.
• Press the INCR button to toggle through each function and select 35.
3. Set the MC35 parameters according to the steps outlined in Section 5 – Selecting the Function.
• Press PARAM button to cycle through and set the parameters.
• Press the INCR button to increment the parameter’s value.
Parameters for the MC35 function are shown in the chart. Set the parameters as needed for the application, and wait for the display to
become inactive to save the conguration.
PARAMETER
(PARAM Button)
DESCRIPTION POSSIBLE VALUES
(INCR Button)
H1 Relay 1 hold time ‘00’ through ‘60’ - Relay 1 hold time will not begin counting down until the release of Input 1 or
‘WET’ Input.
H2 Relay 2 hold time ‘00’ through ‘60’ - Relay 2 hold time will not begin counting down until the delay between
Relay 1 and Relay 2 expires.
H3 Relay 3 hold time ‘00’ through ‘60’ - Relay 3 hold time will not begin counting down until the delay between
Relay 1 and Relay 3 expires.
D1 Delay between
Relay 1 and Relay 2
‘00’, ‘_1’ (1/4), ‘_2’ (1/2), ‘_3’ (3/4), ‘01’ through ‘60’ seconds. The delay time will begin
counting down with the activation of the sequence.
D2 Delay between
Relay 1 and Relay 3
‘00’, ‘_1’ (1/4), ‘_2’ (1/2), ‘_3’ (3/4), ‘01’ through ‘60’ seconds. The delay time will begin
counting down with the activation of the sequence.
4. Once programming is complete, test the Br3. Trigger the sequence via Input 1 or ‘WET’ Input. Ensure that the sequence runs and the
relays activate and the timers are as programmed. The display will show R1 when Relay 1 is energized, R2 when Relay 2 is energized, R3
when Relay 3 is energized, R= when Relay 1 and Relay 2 are energized at the same time, R when all three relays are energized or R= when
Relay 1 and Relay 3 are energized at the same time.
5. Upon completion of the above steps, walk test the door to ensure all functions, timers, sensors, etc. are working as intended and that the
system is in compliance with all applicable standards (i.e. ANSI A156.10, A156.19).

The MC50 function provides an interlock of Relay 1 and Relay
2 triggered by Inputs 1 and 2, with door position switch inputs
on Input 3 for Input 1 and Input 4 for Input 2. Only one relay
will be allowed to operate at a time thus making the two relays
interlocked or mutually exclusive. In order to activate a relay, its
corresponding position switch input must be closed. Adjustable
parameters include H1 for activation hold time of Relay 1 and H2
for activation hold time of Relay 2. A re-activation or maintaining
of an input while its respective relay is activated will restart the
hold timer and keep the relay active.
NOTE: The door position switch must have a closed
contact when the door is closed and an opened
contact when it is not.
A typical application is to have a pair of doors on a clean room in
which only one door can be opened at a time. Each door would
have a push-plate and a door position switch. For this scenario
each door’s push-plate would be wired to Input 1 and Input
2, with the door position switches wired to Input 3 and Input 4
respectively, door controller 1 would be wired to Relay 1 and
door controller 2 would be wired to Relay 2. An example wiring
diagram for this scenario is shown.
MC50 SETUP
1. Wire the Br3 accordingly.
2. Select the MC50 as the function according to the steps outlined in Section 5 – Selecting the Function.
• Press and hold both push buttons (INCR & PARAM) for three (3) seconds to activate the display.
• Press the INCR button to toggle through each function and select 50.
3. Set the MC50 parameters according to the steps outlined in Section 5 – Selecting the Function.
• Press PARAM button to cycle through and set the parameters.
• Press the INCR button to increment the parameter’s value.
Parameters for the MC50 function are shown in the chart. Set the parameters as needed for the application, and wait for the display to
become inactive to save the conguration.
PARAMETER
(PARAM Button)
DESCRIPTION POSSIBLE VALUES
(INCR Button)
H1 Relay 1 hold time ‘00’ through ‘60’. Relay 1 hold time will not begin counting down until the release of Input 1.
H2 Relay 2 hold time ‘00’ through ‘60’. Relay 2 hold time will not begin counting down until the release of Input 2.
4. Once programming is complete, test the Br3. Wait until both doors are closed then trigger Relay 1 via Input 1. Ensure that Relay 1 changes
state and its hold time and is as programmed. The display will show R1 when Relay 1 is energized. Test the interlock by attempting to trigger
Relay 2 via Input 2 while door 1 is still open. Relay 2 should NOT activate due to the rst position switch being opened. Let Relay 1 timeout
and the door to close. The display will show 50 when Relay 1 is de-energized. Once the rst position switch is closed trigger Relay 2 via
Input 2. Ensure that Relay 2 changes state and its hold time and is as programmed. The display will show R2 when Relay 2 is energized.
Test the interlock by attempting to trigger Relay 1 via Input 1 while door 2 is still open. Relay 1 should NOT activate due to the second
position switch being opened. The display will show 50 when Relay 2 is de-energized.
5. Upon completion of the above steps, walk test the door to ensure all functions, timers, sensors, etc. are working as intended, and that the
system is in compliance with all applicable standards (i.e. ANSI A156.10, A156.19).
6I Function 50 - Interlock Timer (MC50)
Page 11 of 15 75.5501.02 EN 20091102 (75.5500)
GND
IN-1
GND
IN-2
GND
IN-3
GND
IN-4
1 2 3 4
WET
WET
WET
NC
NO
COM
NC
NO
COM
12-24V
AC/DC
RELAYS
1 2
POWER RELAY 1
INCR.
PARAM
SETUP
DC AC
DRY WET
INPUTS
5 0
NC
NO
COM
3
Br
3
CAUTION: RELAY 1 WET
OUTPUT OPTION
IS ACTIVE FOR
ALL FUNCTIONS.
12 to 24
VAC/VDC
+/- 10%
Directly to Activation Circuit of
Door Control #1 and Door Control
Activation Circuit of Door #2.
Inputs 1 & 2 are activation
inputs for Doors 1 & 2.
Inputs 3 & 4 are for the door position switch for inputs
1 & 2 respectively. Switch is closed when door is closed.

The MC55 function provides an interlock ratchet of Relay 1 and
Relay 2 triggered by Inputs 1 and 2, with door position switch
inputs on Input 3 for Input 1 and Input 4 for Input 2. Only one
relay will be allowed to operate at a time thus making the two
relays interlocked or mutually exclusive. In order to activate a
relay, its corresponding position switch input must be closed.
Each trigger of an input will change the state of its respective
relay. MC55 has NO adjustable parameters. If the input is
maintained, its relay will only change state once. The input must
then be opened and re-closed for a change of state.
NOTE: The door position switch must have a closed
contact when the door is closed and an opened
contact when it is not.
A typical application is to have a pair of doors on a clean room in
which only one door can be opened at a time. Each door would
have a set of push-plates connected to it in the instance that a
single hold time will not suit all users of the door. Each door would
also have a door position switch. For this scenario door number
1 and 2 push plates shall be wired in parallel to inputs 1 and 2
respectively, with the door position switches wired to Input 3 and
Input 4 respectively, door controller 1 would be wired to Relay
1 and door controller 2 would be wired to Relay 2. An example
wiring diagram for this scenario is shown below.
MC55 SETUP
1. Wire the Br3 accordingly.
2. Select the MC55 as the function according to the steps outlined in Section 5 – Selecting the Function.
• Press and hold both push buttons (INCR & PARAM) for three (3) seconds to activate the display.
• Press the INCR button to toggle through each function and select 55.
3. There are NO parameters to set for the MC55 as the state of Relay 1 and Relay 2 are not based on time, so just wait for the display to
become inactive to save the conguration.
4. Once programming is complete, test the Br3. Wait until both doors are closed then trigger Relay 1 via Input 1. Ensure that Relay 1 changes
state and that is maintained. The display will show R1 when Relay 1 is energized. Test the interlock by attempting to trigger Relay 2 via
Input 2. Relay 2 should NOT activate due to the rst position switch being opened. Now trigger Relay 1 again via Input 1 and ensure Relay
1 changes state again. The display will show 55 when Relay 1 is de-energized. Once the rst position switch is closed trigger Relay 2 via
Input 2. Ensure that Relay 2 changes state and that is maintained. The display will show R2 when Relay 2 is energized. Test the interlock
by attempting to trigger Relay 1 via Input 1. Relay 1 should NOT activate due to the second position switch being opened. Now trigger Relay
2 again via Input 2 and ensure Relay 2 changes state again. The display will show 55 when Relay 2 is de-energized.
5. Upon completion of the above steps, walk test the door to ensure all functions, timers, sensors, etc. are working as intended, and that the
system is in compliance with all applicable standards (i.e. ANSI A156.10, A156.19).
6J Function 55 - Interlock Ratchet (MC55)
75.5501.02 EN 20091102 (75.5500) Page 12 of 15
GND
IN-1
GND
IN-2
GND
IN-3
GND
IN-4
1 2 3 4
WET
WET
WET
NC
NO
COM
NC
NO
COM
12-24V
AC/DC
RELAYS
1 2
POWER RELAY 1
INCR.
PARAM
SETUP
DC AC
DRY WET
INPUTS
5 5
NC
NO
COM
3
Br
3
CAUTION: RELAY 1 WET
OUTPUT OPTION
IS ACTIVE FOR
ALL FUNCTIONS.
12 to 24
VAC/VDC
+/- 10%
Directly to Activation Circuit of
Door Control #1 and Door Control
Activation Circuit of Door #2.
Inputs 1 & 2 are activation
inputs for Doors 1 & 2.
Inputs 3 & 4 are for the door position switch for inputs
1 & 2 respectively. Switch is closed when door is closed.

The MC65 function provides a two-way sequencer to sequence
Relay 1 and/or Relay 2 triggered by Input 1. Similarly, it also
provides a sequence in the opposite direction to sequence
Relay 2 and/or Relay 1 triggered by Input 2. Inputs 3 and 4 also
trigger Relays 1 and 2 individually (non-sequenced). Adjustable
parameters include H1 for activation hold time of Relay 1, H2 for
activation hold time of Relay 2, D1 for delay between activation
of Relay 1 to Relay 2 and D2 for delay between activation of
Relay 2 to Relay 1. A re-activation of Input 1 or Input 2 before
the sequence expires will re-start both hold timers and keep the
relays active. A maintained input will freeze both hold timers,
thus keeping their relays active until the input is released, which
will allow the hold timers to expire and deactivate the relays
normally.
NOTE: The delay timer will only re one time during initial
activation or maintained input.
NOTE: The functionality for MC65 has changed slightly in this
version as you no longer have to wait for a sequence to
complete before running another sequence.
A typical application is an unsecured two door sequence vestibule
that allows two-way trafc in which you have a push-plate on the
entrance of each door to start the sequence and two push-plates
between the doors to activate the doors individually in case of
entrapment. For this scenario the push-plate for in-bound trafc
would be wired to Input 1, the push-plate for out-bound trafc
would be wired to Input 2, a push-plate for entrapment release
of door 1 would be wired to Input 3, a push-plate for entrapment
release of door 2 would be wired to Input 4, Relay 1 would be
wired to door controller 1 and Relay 2 would be wired to door
controller 2. An example wiring diagram for this scenario is shown.
MC65 SETUP
1. Wire the Br3 accordingly.
2. Select the MC65 as the function according to the steps outlined in Section 5 – Selecting the Function.
• Press and hold both push buttons (INCR & PARAM) for three (3) seconds to activate the display.
• Press the INCR button to toggle through each function and select 65.
3. Set the MC65 parameters according to the steps outlined in Section 5 – Selecting the Function.
• Press PARAM button to cycle through and set the parameters.
• Press the INCR button to increment the parameter’s value.
Parameters for the MC65 function are shown in the chart. Set the parameters as needed for the application, and wait for the display to
become inactive to save the conguration.
PARAMETER
(PARAM Button)
DESCRIPTION POSSIBLE VALUES
(INCR Button)
H1 Relay 1 hold time ‘00’ through ‘60’ - Relay 1 hold time will not begin counting down until the release of Input 1
for inbound or until the delay between Relay 2 and Relay 1 expires for outbound or until
the release of Input 3.
H2 Relay 2 hold time
‘00’ through ‘60’ - Relay 2 hold time will not begin counting down until the release of Input 2
for outbound or until the delay between Relay 1 and Relay 2 expires for
inbound or until the release of Input 4.
D1 Delay between
Relay 1 and Relay 2
‘00’, ‘_1’ (1/4), ‘_2’ (1/2), ‘_3’ (3/4), ‘01’ through ‘60’ seconds. The delay time will begin
counting down with the activation of the sequence.
D2 Delay between
Relay 2 and Relay 1
‘00’, ‘_1’ (1/4), ‘_2’ (1/2), ‘_3’ (3/4), ‘01’ through ‘60’ seconds. The delay time will begin
counting down with the activation of the sequence.
4. Once programming is complete, test the Br3. Trigger the sequence via Input 1. Ensure that the in-bound sequence runs and the relays
activate and the timers are as programmed. The display will show R1 when Relay 1 is energized, R2 when Relay 2 is energized and R= when
both Relay 1 and Relay 2 are energized at the same time. Trigger the sequence via Input 2. Ensure that the out-bound sequence runs and
the relays activate and the timers are as programmed. Trigger only door 1 via Input 3. Trigger only door 2 via Input 4.
5. Upon completion of the above steps, walk test the door to ensure all functions, timers, sensors, etc. are working as intended and that the
system is in compliance with all applicable standards (i.e. ANSI A156.10, A156.19).
6K Function 65 - 2 Way, 2 Relay Sequence (MC65)
Page 13 of 15 75.5501.02 EN 20091102 (75.5500)
GND
IN-1
GND
IN-2
GND
IN-3
GND
IN-4
1 2 3 4
WET
WET
WET
NC
NO
COM
NC
NO
COM
12-24V
AC/DC
RELAYS
1 2
POWER RELAY 1
INCR.
PARAM
SETUP
DC AC
DRY WET
INPUTS
6 5
NC
NO
COM
3
Br
3
CAUTION: RELAY 1 WET
OUTPUT OPTION
IS ACTIVE FOR
ALL FUNCTIONS.
12 to 24
VAC/VDC
+/- 10%
Directly to Activation Circuit of
Door Control #1 and Door Control
Activation Circuit of Door #2.
Input 4 allows Activation of Door #2 with NO Sequence to Door #1.
Input 3 allows Activation of Door #1 with NO Sequence to Door #2.
Input 2 allows Sequenced Activation from Door #2 to Door #1.
Input 1 allows Sequenced Activation from Door #1 to Door #2.

The MC75 function provides a sequence for Relay 1 and/
or Relay 2 triggered by Input 1 or ‘WET’ Input. Adjustable
parameters include H1 for activation hold time of Relay 1, H2
for activation hold time of Relay 2 and D1 for delay between
activation of Relay 1 to Relay 2. A re-activation of Input 1 or
‘WET’ Input before the sequence expires will re-start both
hold timers and keep the relays active. A maintained input will
freeze both hold timers, thus keeping their relays active until the
input is released, which will allow the hold timers to expire and
deactivate the relays normally.
NOTE: The delay timer will only re one time during initial
activation or maintained input.
A typical application is a security door in which you have a card-
reader that supplies an output voltage to start the sequence to
unlock the security device, such as a Maglock or electric strike
and then activate the door controller. For this scenario the card-
reader would be wired to ‘WET’ Input, the security device would
be wired to Relay 1 and the door controller would be wired to
Relay 2. An example wiring diagram for this scenario is shown
below. An example wiring diagram for this scenario is shown
below.
NOTE: While the Input 1 is not involved in our typical
application, it will still function as ‘WET’ Input does if
used.
MC75 SETUP
1. Wire the Br3 accordingly.
2. Select the MC75 as the function according to the steps outlined in Section 5 – Selecting the Function.
• Press and hold both push buttons (INCR & PARAM) for three (3) seconds to activate the display.
• Press the INCR button to toggle through each function and select 75.
3. Set the MC75 parameters according to the steps outlined in Section 5 – Selecting the Function.
• Press PARAM button to cycle through and set the parameters.
• Press the INCR button to increment the parameter’s value.
Parameters for the MC75 function are shown in the chart. Set the parameters as needed for the application, and wait for the display to
become inactive to save the conguration.
PARAMETER
(PARAM Button)
DESCRIPTION POSSIBLE VALUES
(INCR Button)
H1 Relay 1 hold time ‘00’ through ‘60’ - Relay 1 hold time will not begin counting down until the release of Input 1 or
‘WET’ Input.
H2 Relay 2 hold time ‘00’ through ‘60’ - Relay 2 hold time will not begin counting down until the delay between
Relay 1 and Relay 2 expires.
D1 Delay between
Relay 1 and Relay 2
‘00’, ‘_1’ (1/4), ‘_2’ (1/2), ‘_3’ (3/4), ‘01’ through ‘60’ seconds. The delay time will begin
counting down with the activation of the sequence.
4. Once programming is complete, test the Br3. Trigger the sequence via Input 1 or ‘WET’ Input. Ensure that the sequence runs and the
relays activate and the timers are as programmed. The display will show R1 when Relay 1 is energized, R2 when Relay 2 is energized and R=
when both Relay 1 and Relay 2 are energized at the same time.
5. Upon completion of the above steps, walk test the door to ensure all functions, timers, sensors, etc. are working as intended and that the
system is in compliance with all applicable standards (i.e. ANSI A156.10, A156.19).
6L Function 75 - 2 Relay Sequence (MC75)
75.5501.02 EN 20091102 (75.5500) Page 14 of 15
GND
IN-1
GND
IN-2
GND
IN-3
GND
IN-4
1 2 3 4
WET
WET
WET
NC
NO
COM
NC
NO
COM
12-24V
AC/DC
RELAYS
1 2
POWER RELAY 1
INCR.
PARAM
SETUP
DC AC
DRY WET
INPUTS
7 5
NC
NO
COM
3
Br
3
CAUTION: RELAY 1 WET
OUTPUT OPTION
IS ACTIVE FOR
ALL FUNCTIONS.
12 to 24
VAC/VDC
+/- 10%
To Activation Circuit
of Door Control.
Input 1 is for an
additional ‘Dry’
Input Device.
‘ W E T ’
12 to 24
VAC/VDC
+/- 10%
INPUT
+ -
Typically Connected to
Lock Device. When DC‘WET’
Output is Selected for Relay 1,
COM Terminal is Positive (+).

9 Company Contact
Do not leave problems unresolved. If a satisfactory solution cannot be achieved after troubleshooting a problem, please
call BEA, Inc. If you must wait for the following workday to call BEA, leave the door inoperable until satisfactory repairs
can be made. Never sacrice the safe operation of the automatic door or gate for an incomplete solution.
The following numbers can be called 24 hours a day, 7 days a week. For more information, visit www.beasensors.com.
East:
Canada and Texas:
1-866-249-7937
1-866-836-1863
Central:
West:
1-800-407-4545
1-888-419-2564
PROBLEM PROBABLE CAUSE CORRECTIVE ACTION
Module will NOT react to any input. 1. Incorrect Br3 power
2. Module not programmed
3. Incorrect wiring
4. Faulty module
1. Check the Br3’s power. It should be 12 to 24 volts AC or DC +/- 10%.
Ensure that input power is applied at the correct terminals.
2. Ensure a function has been programmed. If ‘00‘ is showing in the
display, the Br3 will need to be programmed.
3. Jumper an active Input and ensure that the fault is not within the wiring.
If module works when jumped, trace wiring from Inputs / relays.
4. Replace module.
Module reacts to input but has no
output.
1. Wrong outputs are
connected
2. Incorrect wiring
3. Incorrect jumper settings
4. Faulty module
1. Check to ensure that the proper outputs are connected per the function
selected.
2. Trace all wiring to ensure correct termination points.
3. Check that the jumpers are congured correctly for the application.
4. Replace module
8 Troubleshooting
1. Document all work. For future reference, be sure to record the Br3 Serial Number on your Work Order.
2. Educate the Owner / Manager as to the proper operation of the door and sensor system, and what to do to ensure safe use of the door in the
event of discovering a malfunction. Show the Owner / Manager how to perform a daily safety check of the system. You may also wish to provide
the owner/Manager a copy of an owners manual provided by AAADM for the type of door selected.
3. Be sure to obtain signatures on your work order for all work accomplished.
7 Documentation
Page 15 of 15 75.5501.02 EN 20091102 (75.5500)
Table of contents
Other BEA Other manuals
Popular Other manuals by other brands

Supra
Supra ActiveKEY quick start
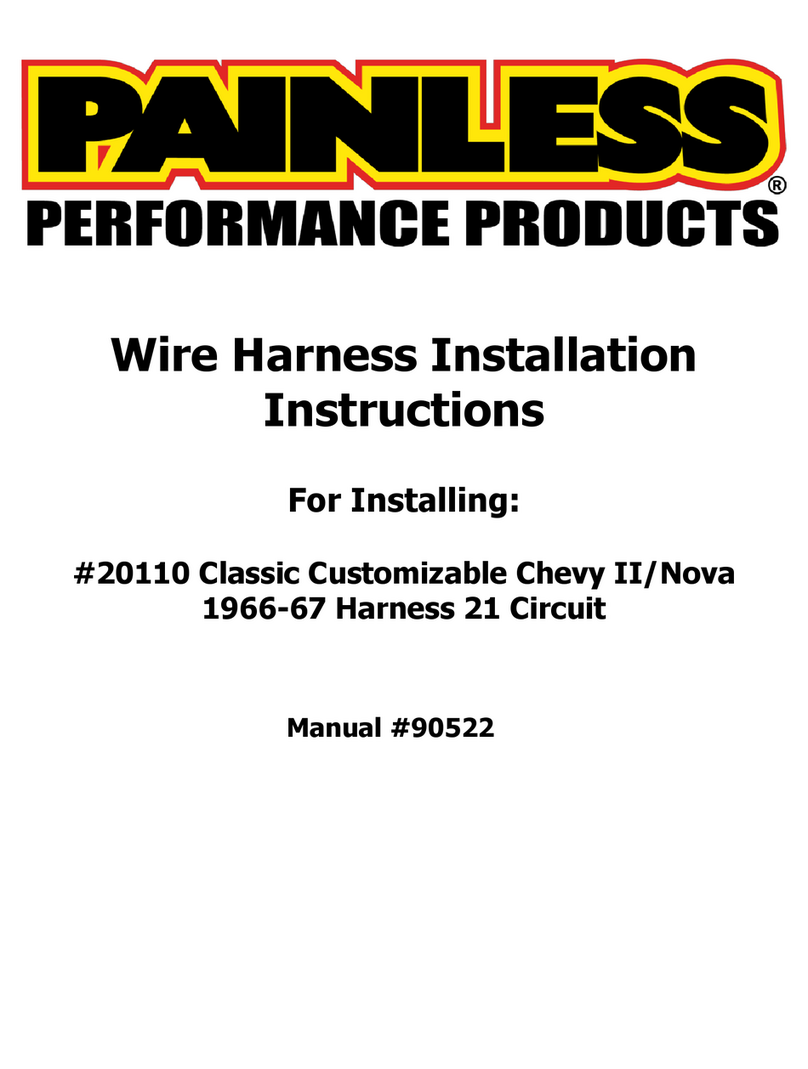
Painless Performance Products
Painless Performance Products 20110 installation instructions
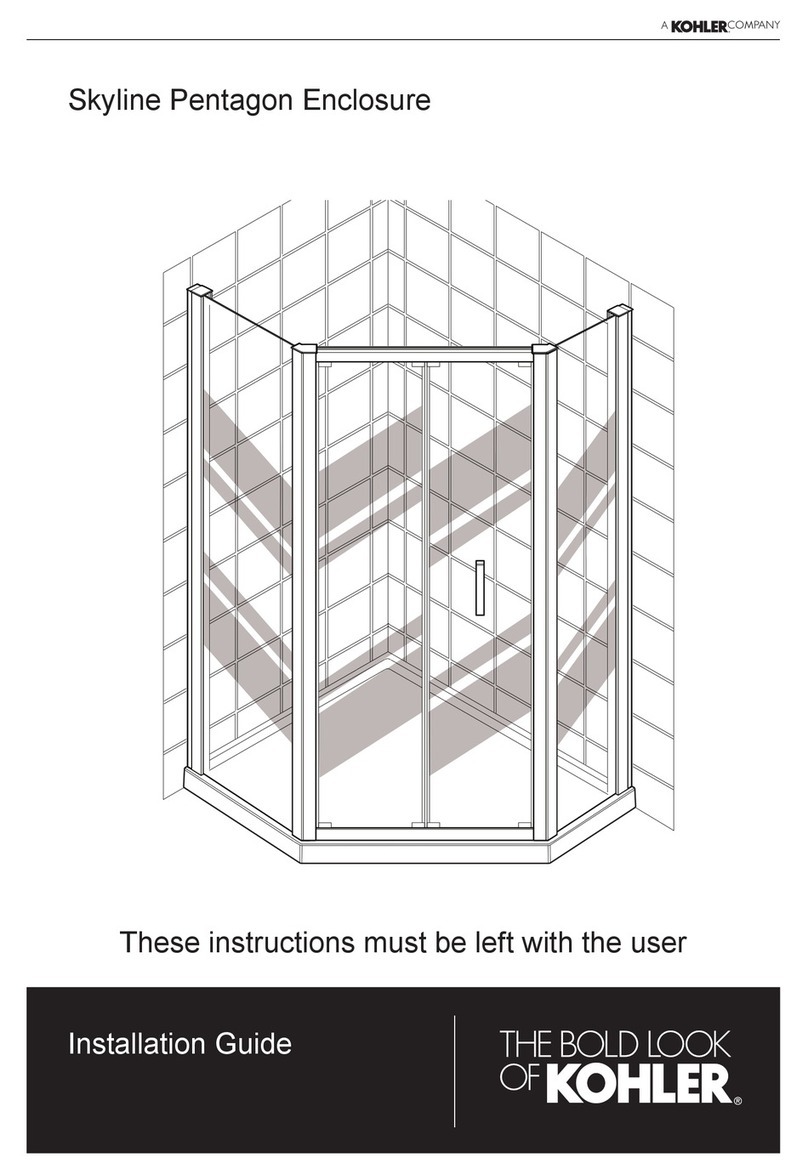
Kohler
Kohler Skyline Pivot Pentagon installation guide
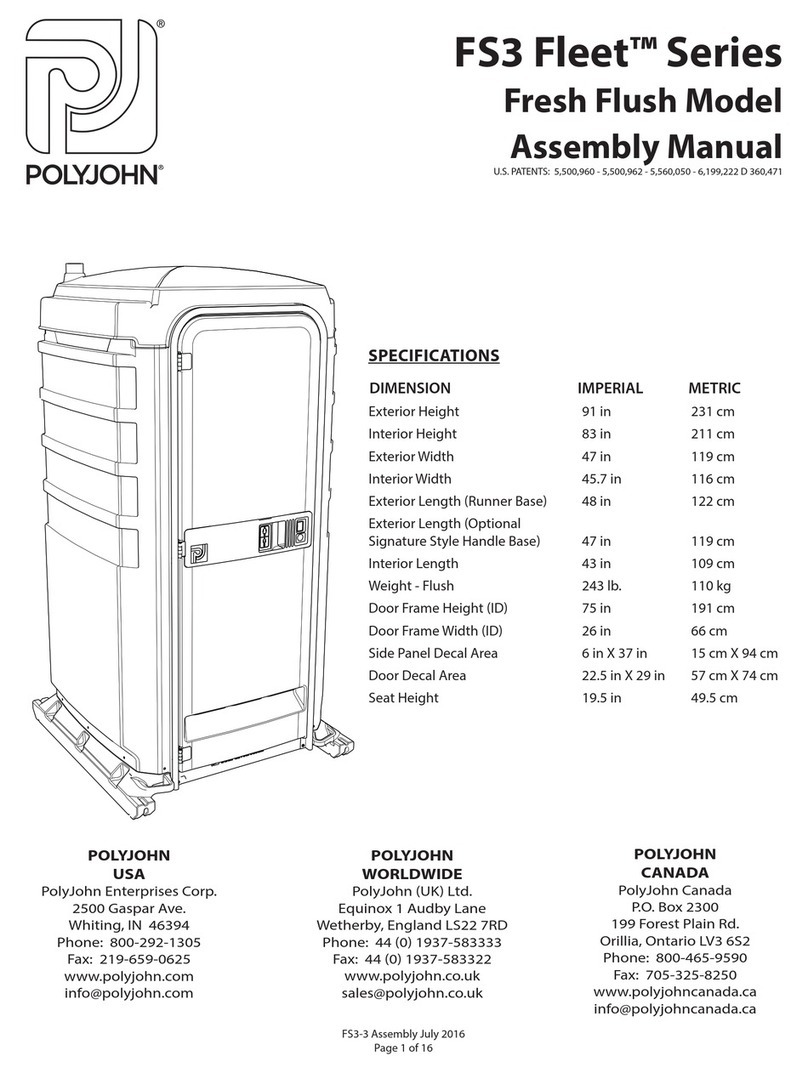
PolyJohn
PolyJohn FS3-3 Assembly manual

Parkside
Parkside 291642 Translation of the original instructions
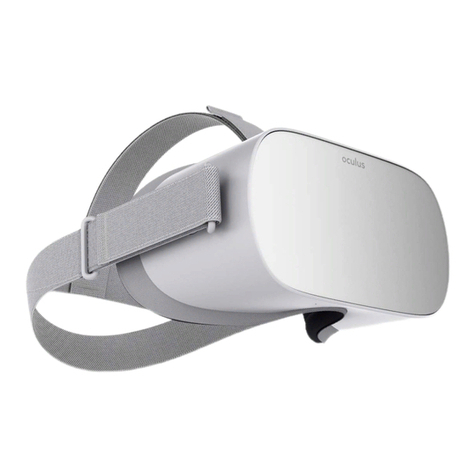
OCULUS
OCULUS Go Safety & warranty manual