BF Entron WELDSTAR WS2003 User manual

Introduction to WELDSTAR
model WS2003
Spot/Seam control,monitor and machine sequencer
for 50/60Hz and MF resistance welding.
For s/w version 1.69
Document revision 0

WS2003 V1.69
2
BF Entron Ltd.
Castle Mill Works,
Birmingham new road,
Dudley,
West Midlands,
DY1 4DA
England.
Tel: +44 (0)1384 455401
Fax: +44 (0)1384 455551
Email: [email protected]
Web site: www.bfentron.co.uk
Manufacturers of
advanced welding
controls
•Welding controls.
•Thyristors and power supplies
•Power Inverters.
•Meters and Monitors.
•Training and Support.
•Consultancy.
BF Entron Ltd.

WS2003 V1.69
3
Table of contents
4. WELDSTAR model WS2003
System
5. Introduction and overview
6. Functions
7. …functions
8. …functions
9. Global parameters
10. Program parameters (x64)
11. Multiweld parameters
12. Mounting
13. Connectors
14. Users connections
(discrete)
18. Operation with a fieldbus
19. ...operation with a fieldbus
20. Keypad
21. Menus
22. ..menus
23. Diagnostic screen 1
24. Diagnostic screen 2
25. Status / error codes
29. Configuration menu
30. Edit configuration
33. Edit calibration
36. Edit output map
37. Edit input map
38. Set-up Adapters
39. Backup/Restore
40. Initialise all data
41. System set-up menu
42. Main menu
43. Edit program (AC)
44. Edit program (MF)
46. Edit program (seam)
47. Edit limits
48. Edit Events
49. Electrode menu
50. Stepper status
51. Edit stepper
52. Stepper presets
53. Edit counter
54. ..edit counter(tip-dressing)
55. Sequencer
56. Sequencer Menu
57. Edit sequence
59. Example sequence
60. Weld log
61. View log screen 1
62. View log screen 2
63. Copy program
64. Copy Electrode
65. I/O status
66. Fieldbus input status
67. Analog status
68. Program selection
69. OHMA (Air over oil) system
71. Disabling edits
72. Pop-up current meter
73. Replacing a WS2000 timer
74. Operation: basic spot weld – no
weld faults.
75. Operation: basic spot weld – weld
fault
76. Operation: repeat spot weld
77. Operation: pulsation spot weld
78. Operation: upslope and
downslope
79. Operation: roll-spot welding
80. Operation: seam welding (dual
heat)
81. Operation: seam welding (pre-
heat)
82. Operation: EOS signal
83. Operation: Retract
84. Operation: Hi-lift
-----------------------------------------------------------
85. Multiwelding
86. Configuring for multiwelding
87. Electrode/Transformer assignment
88. Assigning a weld program to an
electrode
89. Multi-gun operation
90. Multi-gun cascade operation
92. Program selection (multiweld)
-----------------------------------------------------------
93. WS98-2003 PC software

WS2003 V1.69
4
WELDSTAR model WS2003 System
LOGIC SEQUENCER
EVENT TIMER
Ethernet
WS2003
WELDING
CONTROL
WSP3
PROGRAMMING
PENDANT
WS2003 TIMER
*Optional Ethernet adapter
required for connection to
Ethernet
WELDSTAR
2000
compatible !
*Optional Plug-in adapter
cards for special functions.
WS98-2003
Software for PC

WS2003 V1.69
5
Introduction and overview
A new programming pendant , type WSP3 is available, and provides a
larger multi-line display, making programming easy.
A powerful built-in logic sequencer program provides the timer with a
flexible means of fully controlling small machines or tooling
arrangements, without the need for additional hardware.
A plug-in option board provides a 10/100Base-T Ethernet connection.
Units may then be networked to a PC running WS98-2003 software
for programming and monitoring purposes.
Fieldbus operation (Profibus, Interbus, DeviceNet Modbus etc.) is
supported via plug-in option boards.
The new WELDSTAR model WS2003 is a direct plug-in replacement for the original WS2000. It
will fit into existing cabinets, and will work with the existing power supply. Existing connections
are duplicated, including outputs at 110V AC or 24VDC. MF operation is also supported.
This manual details the features of the WS2003 timer, and shows how
to program the timer using the WSP3 programmer.
This manual details the features of the WS2003 timer, and shows how
to program the timer using the WSP3 programmer.
F
WSP3
BF
ENTRON

WS2003 V1.69
6
Functions
•Compatible with original Weldstar 2000
• AC 50/60Hz and MFDC (medium frequency) welding all supported.
• Spot / Repeat /Roll-spot / Seam (dual heat) / Seam (pre-heat) welding.
• Single, dual or OHMA (Air over Oil) gun operation.
• Multiwelding with up to 16 SCR/transformers
• Retract/high-lift control.
• Dual weld intervals plus pulsation, upslope and downslope.
• Constant current regulation.
• Up to 64 programmes with internal or external selection.
• Current monitoring with high, low and pre limits. Programmable blocking and weld
retry functions.
• Proportional valve controller (0..10V or 4..20mA).
• Programmable outputs (events).
• Machine sequencer logic
• Welding programmes may be linked together to form complex spot schedules.

WS2003 V1.69
7
…functions
• Contactor timer.
• Head-lock function.
• Analog output of current waveform.
• Electrode management including stepping, counting and tip-dressing
functions, with programmable blocking and preset curves.
• Outputs will drive 24V DC or 110V AC loads.
• Primary or Secondary feedback via Toroid.
• Toroid and PV calibration functions.
• Toroid test function.
• Disable edit function.
• External plug-in programming pendant with large backlit 4x20 lcd display,
and data backup facility.
• RS232 port, for PC communications.
• Expandable via plug-in option cards
• (Ethernet, Profibus, DeviceNet, Interbus, Modbus TCP/IP, Ethernet/IP
etc).

WS2003 V1.69
8
…functions
In early 2008, a number of new circuits were added to the original design.
These are used to provide the following additional features:
• 0..10v or 4..20mA input for pressure monitoring.
• Two general purpose 0..10V inputs can be used by the sequencer. One of
these inputs may be used to connect a CT for current measurement.
Note that these features are not available when running this firmware on the
original design.

WS2003 V1.69
9
Global parameters
Configuration
•Sequence (Spot / Roll-spot / Seam(2-heat) / Seam(pre-heat)
•Single gun / Dual gun / OHMA gun / Multi-gun / Multi-gun cascade.
•Discrete/Fieldbus I/O
•Retract (x2): (Simple / Hi-lift+ / Hi-lift- / Maintained / OHMA)
•Program select (Binary / 1-of-4 )
•SCR select (Binary / 1-of-4)
•Frequency (AC 50 Hz / AC 60 Hz / MF 50Hz / MF 60Hz)
•Contactor time (0..200 s)
•Blanking (On/Off)
•Toroid test (On/Off)
•Sensor (Toroid / CT)
•Heat range (Wide/High/Low)
•EOS mode (Cancel/fixed)
•If fault (Head-lock/Stop/Continue/EOS/No EOS)
•Sequencer (On/Off)
•Toroid attenuation factor (1..4)
•Count/Log sync (On/Off)
•Pressure units (kN/lb)
•Analog output (PV/Current).
•Sensor sensitivity(100..60000 mV/kA)
•S/P ratio (1:1..199:1)
•S/P offset (-10kA..+10kA)
•Pressure (2 points, kN/V)
•Inverter (2 points, kA/%heat)
•Analog output scale (0..60kA).
•Analog input gain (0.9..2.5)
•Analog input offset(-9.99…+9.99)
Calibration (x2)
• Actual count (0..9999).
• Terminal count(0..9999).
• Stop/continue at end.
• Tip dressing (on/off)
• Dressings (0..9999)
• Dress when new (on/off)
Counter (x2)
• Stepper on/off.
• Stop /continue at end
• Curve(10 point, interpolated)
Stepper (x2)
Sequencer
•Up to 250 statements
Output Map
•Normal/Event/Sequencer/Fieldbus (x12)
Input Map
• Normal/Sequencer (x14)

WS2003 V1.69
10
Program parameters (x64)
Weld program
•Pre-squeeze (0..99 cycles)
•Squeeze (0..99 cycles)
•Weld1 (0..99 cycles)
•Cool1(0..99 cycles)
•Weld2(0..99 cycles)
•Cool2(0..99 cycles)
•Pulses(0..99)
•Hold(0..99 cycles)
•Off(0..99 cycles)
•Pressure (0..100%)
•Heat 1(0..99.9%)
•Heat 2(0..99.9%)
•Current 1 (0..60kA)
•Current 2 (0..60kA)
•Balance (seam only)
•Normal/Link program
•Upslope(0..99 cycles)
•Downslope(0..99 cycles)
•Current monitor (On/Off)
•Current low limit,weld1 (0..99%)
•Current high limit,weld1 (0..99%)
•Current pre-limit,weld1 (0..99%)
•Current low limit,weld2 (0..99%)
•Current high limit,weld2 (0..99%)
•Current pre-limit,weld2 (0..99%)
•Pre-limit count (0..99)
•Retry (On/Off)
•Pressure monitor (On/Off)
•Wait for pressure (On/Off)
•Pressure high limit (0..100%)
•Pressure low limit (0..100%)
Monitor limits
Events
•4 x 4 trigger points
•OHMA gun open (0..99 cycles)
•OHMA gun close (0..99 cycles)
•OHMA retract open (0..99 cycles)
•OHMA retract delay (0..99 cycles)
•OHMA retract close (0..99 cycles)
Additional parameters for OHMA gun

WS2003 V1.69
11
Multiweld parameters
Transformers
•Electrode number (1..16) for each transformer (x16).
Calibration (extended to x16)
Counter (extended to x16)
Stepper (extended to x16)
•See ‘Global parameters’ for parameter list.
•See ‘Global parameters’ for parameter list.
•See ‘Global parameters’ for parameter list.
When either multi-gun or multi-gun cascade modes are selected, the following additional
parameters are available:
Weld program (x64)
•Electrode number(1..16).

WS2003 V1.69
12
Mounting
If you have purchased a complete
system including the WS2003 timer, then
the timer will already be mounted in the
case.
If you have purchased a timer only kit,
then you will need to mount the timer to
the rest of your equipment.
The timer is supplied complete with two
metal mounting brackets. These
brackets need to be fixed to a flat
surface, as shown in the diagram.
It is recommended that the four holes for
the top bracket are made into vertical
slots. The position of the bracket may
then be adjusted to give the best fit to
the timer.
66.5 66.597.0
375
4.5 dia.
Top bracket
Bottom
bracket

WS2003 V1.69
13
Connectors
Connectors P1,P2,P3,P4,P7,P13 and P14
are two-part terminals, for use with wires
up to 1mm2.
Connectors P5 and P6 are used internally
via ribbon cable assemblies, and are not
used for users connections.
Connector P7 is the preferred connection
for the current measurement toroid. If the
WS2003 timer is being retrofitted into an
older system, there may already be a toroid
connected and routed internally via ribbon
P6. In this case, no connection should be
made to P7. However, if possible, an
existing toroid should be re-routed to P7.
P13 and P14 are not present on units
produced before early 2008.

WS2003 V1.69
14
Users connections (discrete)

WS2003 V1.69
15
…users connections

WS2003 V1.69
16
…users connections

WS2003 V1.69
17
…users connections

WS2003 V1.69
18
Operation with a fieldbus
WS2003 can be operated on a fieldbus,
instead of through the discrete I/O
connections.
An optional adapter card is required to
interface to the required fieldbus. Adapter
cards are available for all popular fieldbus
types: (Profibus-DP, Interbus-S, DeviceNet,
Ethernet TCP/IP/MODBUS, etc.)
The diagram opposite shows, schematically,
how the I/O is arranged. Selection between
Discrete or Fieldbus operation is via the timer
configuration.
The tables on the next page show the fieldbus
bit assignments for both single gun/multi-gun
and dual-gun operation.
Physical
inputs Mux
Sequencer
Timer
F24V, SCR STAT
14
16
2
14
14
32
32
Fieldbus
inputs
Input
Map
INPUTS
WS2003 I/O routing
Physical
outputs Mux
Sequencer
Timer
12
12
16
16
32
12
Fieldbus
outputs
Output
Map
OUTPUTS
Events
16
Pressure
Error code
Output
8
8
12
8

WS2003 V1.69
19
...operation with a fieldbus
*The discrete Weld on input must also be on to enable welding.
Dual gun
INPUT from bus to timer OUTPUT from timer to bus
Bit No. Function Bit No. Function
0 START 1 0 End of stepper 2
1 START 2 1 End of stepper 1
2 START 3 2 End of count 2
3 START 4 3 End of count 1
4 2nd Stage 4 Contactor
5 Weld on* 5 Not ready
6 Reserved 6 Fault
7 Reserved 7 End of sequence (EOS)
8 Reset counter 1 8 Weld air valve 1 (WAV 1)
9 Reset stepper 1 9 Weld air valve 2 (WAV 2)
10 Retract 1 10 Retract air valve 1 (HAV 1)
11 Reset counter 2 11 Retract air valve 2 (HAV 2)
12 Reset stepper 2 12 Discrete input I10
13 Retract 2 13 Discrete input I11
14 Reserved 14 Discrete input I12
15 Reset fault 15 Discrete input I13
16 Program bit 1 16 Error code bit 1
17 Program bit 2 17 Error code bit 2
18 Program bit 4 18 Error code bit 4
19 Program bit 8 19 Error code bit 8
20 Program bit 16 20 Error code bit 16
21 Program bit 32 21 Error code bit 32
22 Reserved 22 Error code bit 64
23 Reserved 23 Error code bit 128
Map=1 Map=2
24 Discrete output Q01 24 Pressure bit 1 Discrete input I1
25 Discrete output Q02 25 Pressure bit 2 Discrete input I2
26 Discrete output Q03 26 Pressure bit 4 Discrete input I3
27 Discrete output Q04 27 Pressure bit 8 Discrete input I4
28 Discrete output Q05 28 Pressure bit 16 Discrete input I5
29 Discrete output Q06 29 Pressure bit 32 Discrete input I6
30 Discrete output Q07 30 Pressure bit 64 Discrete input I7
31 Discrete output Q08 31 Pressure bit 128 Discrete input I8
Single gun /Multi-gun
INPUT from bus to timer OUTPUT from timer to bus
Bit No. Function Bit No. Function
0 START 1 0 Prewarning
1 START 2 1 End of stepper
2 START 3 2 Reserved
3 START 4 3 End of count
4 2nd Stage 4 Contactor
5 Weld on* 5 Not ready
6 Reserved 6 Fault
7 Reserved 7 End of sequence (EOS)
8 Reset counter 8 Weld air valve 1 (WAV 1)
9 Reset stepper 9 Low force air valve (LFAV) / Motor
10 Retract 1 / Reset All 10 Retract air valve 1 (HAV 1)
11 Reserved 11 Reserved
12 Reserved 12 Discrete input I10
13 Reserved 13 Discrete input I11
14 Reserved 14 Discrete input I12
15 Reset fault 15 Discrete input I13
16 Program bit 1 16 Error code bit 1
17 Program bit 2 17 Error code bit 2
18 Program bit 4 18 Error code bit 4
19 Program bit 8 19 Error code bit 8
20 Program bit 16 20 Error code bit 16
21 Program bit 32 21 Error code bit 32
22 Reserved 22 Error code bit 64
23 Reserved 23 Error code bit 128
Map=1 Map=2
24 Discrete output Q01 24 Pressure bit 1 Discrete input I1
25 Discrete output Q02 25 Pressure bit 2 Discrete input I2
26 Discrete output Q03 26 Pressure bit 4 Discrete input I3
27 Discrete output Q04 27 Pressure bit 8 Discrete input I4
28 Discrete output Q05 28 Pressure bit 16 Discrete input I5
29 Discrete output Q06 29 Pressure bit 32 Discrete input I6
30 Discrete output Q07 30 Pressure bit 64 Discrete input I7
31 Discrete output Q08 31 Pressure bit 128 Discrete input I8

WS2003 V1.69
20
Keypad
F
ENTRON
BF
WSP3
Using the keypad
•Press the F(function) key to return to the previous
screen, or to move between menu screens (see
menus).
•The selected function or parameter will flash.
•Use the keys to select a different
function or parameter. The visible window will scroll
when required.
•Press the key to access the selected function.
•Press the +or -keys to alter the selected
parameter. Press +and –together to set a
parameter to 0 or its minimum value.
•On some screens, certain keys can have a special
function. These are noted on the page describing
that screen.
Table of contents
Other BF Entron Controllers manuals
Popular Controllers manuals by other brands
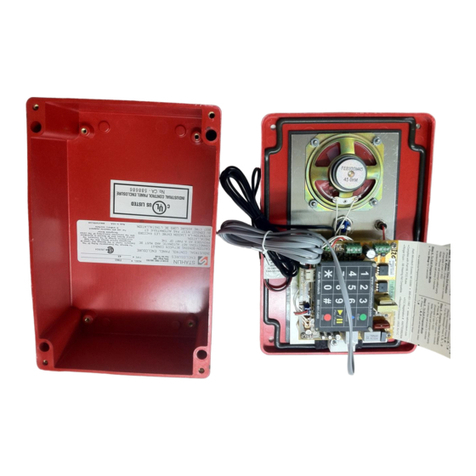
RATH MICROTECH
RATH MICROTECH SmartPhone VI manual
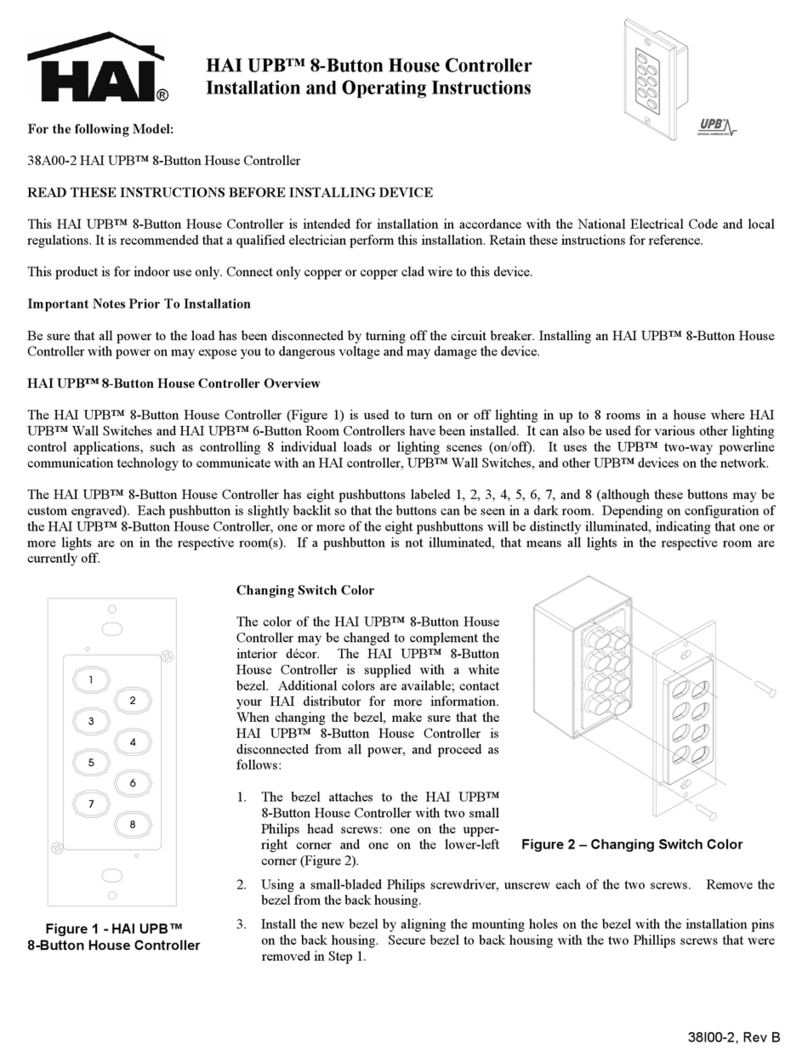
HAI
HAI 38A00-2 UPB Installation and operating instructions

AUDAC
AUDAC NCP105 Hardware manual
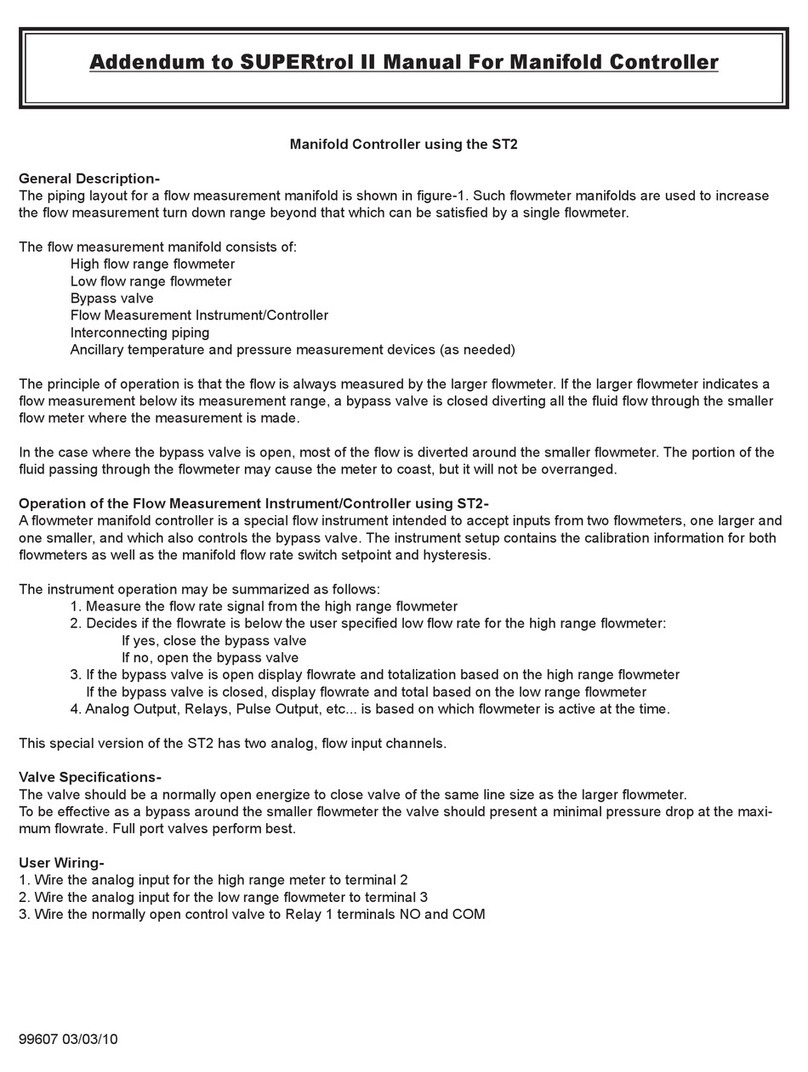
Kessler-Ellis Products
Kessler-Ellis Products SUPERtrol II Addendum to Manual
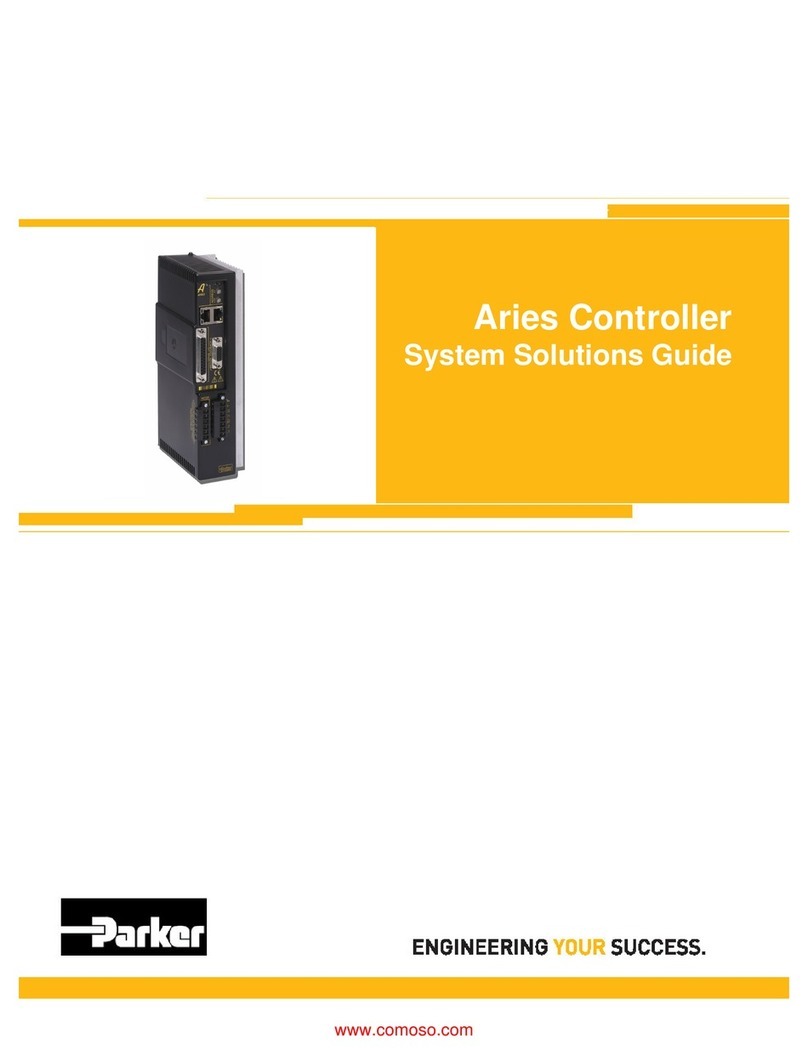
Parker
Parker Aries System solutions guide

Nexmosphere
Nexmosphere XPERIENCE XC-860 quick start guide