BONFIGLIOLI Active Cube Instructions for use

ACTIVE CUBE
Application Manual
Spindle Drive
Frequency inverter 230 V / 400 V


1General Information about the Documentation 7
1.1 This document ......................................................................................................... 7
1.2 Warranty and liability.............................................................................................. 8
1.3Obligation ................................................................................................................ 8
1.4 Copyright ................................................................................................................. 8
1.5 Storage .................................................................................................................... 9
2General safety instructions and information on use 10
2.1 Terminology........................................................................................................... 10
2.2 Designated use ...................................................................................................... 11
2.3 Misuse.................................................................................................................... 11
2.3.1 Explosion protection.................................................................................................11
2.4 Residual risks......................................................................................................... 12
2.5 Safety and warning signs on frequency inverter................................................... 12
2.6 Warning information and symbols used in the Operating Instructions................ 13
2.6.1 Hazard classes .........................................................................................................13
2.6.2 Hazard symbols........................................................................................................13
2.6.3 Prohibition signs.......................................................................................................13
2.6.4 Personal safety equipment........................................................................................13
2.6.5 Recycling.................................................................................................................14
2.6.6 Grounding symbol ....................................................................................................14
2.6.7 ESD symbol .............................................................................................................14
2.6.8 Information signs.....................................................................................................14
2.6.9 Font style in documentation......................................................................................14
2.7 Directives and guidelines to be adhered to by the operator ................................. 15
2.8 Operator's general plant documentation .............................................................. 15
2.9 Operator's/operating staff's responsibilities ........................................................ 15
2.9.1 Selection and qualification of staff.............................................................................15
2.9.2 General work safety..................................................................................................15
2.10 Organizational measures.................................................................................... 16
2.10.1 General....................................................................................................................16
2.10.2 Use in combination with third-party products .............................................................16
2.10.3 Transport and storage ..............................................................................................16
2.11 Handling and installation ................................................................................... 17
2.11.1 Electrical connections ...............................................................................................17
2.11.1.1 The five safety rules ..........................................................................................17
2.11.2 Safe operation..........................................................................................................18
2.11.3 Maintenance and service/troubleshooting ..................................................................19
2.11.4 Final decommissioning..............................................................................................19
3Introductory information about spindle applications 20
3.1 Configurations for spindle applications................................................................. 20
3.2 Software identification.......................................................................................... 21
3.3 Operating characteristics ...................................................................................... 22
3.4 Control inputs and outputs.................................................................................... 23
3.4.1 Control terminals......................................................................................................23
11/13
ACU
Spindle Applications 5

•
4Start-up procedure 24
4.1 Turn mains voltage on........................................................................................... 24
4.2 Motor setup............................................................................................................ 24
4.3 Check speed sensors for sign error ....................................................................... 25
4.4 For Configuration 806 (PMSM): Self-configuration of resolver offset .................. 26
4.4.1 Carrying out of the self-setup....................................................................................26
4.4.2 Safety measures before self-configuration of resolver offset........................................27
4.4.3 Adjustment Parameter 383 .......................................................................................27
5Operation 28
5.1 Permanent magnet synchronous machine (PMSM) .............................................. 28
– Configuration 806......................................................................................................... 28
5.1.1 Operation without encoder........................................................................................28
5.1.1.1 Start .................................................................................................................28
5.1.1.2 Isd current........................................................................................................28
5.1.1.3 Determination of the flux direction at startup ......................................................29
5.1.1.4 Operation with field weakening...........................................................................30
5.1.2 Operation with encoder ............................................................................................30
5.1.2.1 Start .................................................................................................................31
5.1.2.2 Speed sensor configuration ................................................................................31
5.1.2.3 Determination of the flux direction at startup ......................................................31
5.1.2.4 Adjustment of resolver offset..............................................................................32
5.1.2.5 Act. speed source..............................................................................................32
5.1.2.6 Speed sensor monitoring....................................................................................33
5.1.2.7 Speed control with two operating ranges ...........................................................33
5.1.3 Brake chopper monitoring.........................................................................................34
5.1.4 Detection of spindle with inverse behavior .................................................................35
5.2 Asynchronous machine (ASM) – Configuration 804.............................................. 36
5.2.1 Operation without encoder........................................................................................36
5.2.2 Operation with encoder ............................................................................................36
5.2.2.1 Act. speed source..............................................................................................36
5.2.2.2 Speed sensor monitoring....................................................................................36
5.2.2.3 Limit for changeover of speed control.................................................................36
5.3 Axle positioning ..................................................................................................... 36
5.3.1 Identification of reference point position....................................................................37
5.3.2 Definition of sense of rotation for axle positioning ......................................................37
5.3.3 Status message “Target Position Reached” ................................................................38
5.3.4 Sources of axle positioning........................................................................................38
5.3.5 Actual value parameter 805 ......................................................................................38
5.4 Control of acceleration ramps via digital input ..................................................... 39
5.4.1 Switching ramp mode on or off .................................................................................39
5.4.2 Selection of digital source .........................................................................................39
5.4.3 Evaluation of digital input .........................................................................................39
6Overview of sources 40
7Actual values 40
8Parameter 41
Index 42
6
ACU
Spindle Applications 11/13

1General Information about the Documentation
For better clarity, the documentation of the frequency inverter is structured according to the custom-
er-specific requirements.
The present document was created in German. The German document is the original document. Other
language versions are translations.
Quick Start Guide
The “Quick Start Guide” describes the basic steps required for mechanical and electrical installation of
the frequency inverter. The guided commissioning supports you in the selection of necessary parame-
ters and the configuration of the software of the frequency inverter.
Operating Instructions
The Operating Instructions document the complete functionality of the frequency inverter. The pa-
rameters required for special purposes, for adjustment to the application and the numerous additional
functions are described in detail.
Separate Operating Instructions are supplied for optional components for the frequency inverter.
These manuals complement the operating instructions and the “Quick Start Guide” for the frequency
inverter.
Application manual
The application manual complements the documentation to ensure goal-directed installation and
commissioning of the frequency inverter. Information on various topics in connection with the use of
the frequency inverter is described in context with the specific application.
Installation instructions
The Installation Instructions describe the installation and use of devices, complementing the “Quick
Start Guide” and the Operating Instructions.
1.1 This document
This application manual describes the extensions of the standard software 5.4.0.14 for spindle applica-
tions.
The extension for spindle applications is based on the software for ACU series frequency inverters. All
standard features of the ACU are also available in the context of the spindle software. For the ACU
standard features, please refer to the Operating Instructions.
WARNING
Compliance with the documentation is required to ensure safe operation of the frequen-
cy inverter. BONFIGLIOLI VECTRON
GmbH shall not be held liable for any damage
caused by any non-compliance with the documentation.
In case any problems occur which are not covered by the documentation sufficiently,
please contact the manufacturer.
11/13
ACU
Spindle Applications 7

•
1.2 Warranty and liability
BONFIGLIOLI VECTRON GmbH would like to point out that the contents of these Operating Instruc-
tions do not form part of any previous or existing agreement, assurance or legal relationship. Neither
are they intended to supplement or replace such agreements, assurances or legal relationships. Any
obligations of the manufacturer shall solely be based on the relevant purchase agreement which also
includes the complete and solely valid warranty stipulations. These contractual warranty provisions are
neither extended nor limited by the specifications contained in this documentation.
The manufacturer reserves the right to correct or amend the specifications, product information and
omissions in these Operating Instructions without notice. The manufacturer shall not be liable for any
damage, injuries or costs which may be caused by the aforementioned reasons.
Furthermore, BONFIGLIOLI VECTRON GmbH excludes any warranty/liability claims for any personal
and/or material damage if such damage is due to one or more of the following causes:
−inappropriate use of the frequency inverter,
−non-compliance with the instructions, warnings and prohibitions contained in the documentation,
−unauthorized modifications of the frequency inverter,
−insufficient monitoring of parts of the machine/plant which are subject to wear,
−repair work at the machine/plant not carried out properly or in time,
−catastrophes by external impact and force majeure.
1.3 Obligation
These Operating Instructions must be read before commissioning and complied with. Anybody en-
trusted with tasks in connection with the
−transport,
−assembly,
−installation of the frequency inverter and
−operation of the frequency inverter
must have read and understood the Operating Instructions and, in particular, the safety instructions in
order to prevent personal and material losses.
1.4 Copyright
In accordance with applicable law against unfair competition, these Operating Instructions shall be
considered to be a certificate. Any copyrights relating to it shall remain with
Bonfiglioli Vectron GmbH
Europark Fichtenhain B6
47807 Krefeld
Deutschland
These Operating Instructions are intended for the operator of the frequency inverter. Any disclosure
or copying of this document, exploitation and communication of its contents (as hardcopy or electron-
ically) shall be forbidden, unless permitted expressly.
Any non-compliance will constitute an offense against the copyright law dated 09 September 1965,
the law against unfair competition and the Civil Code and may result in claims for damages. All rights
relating to patent, utility model or design registration reserved.
8
ACU
Spindle Applications 11/13

1.5 Storage
The documentation form an integral part of the frequency inverter. It must be stored such that it is
accessible to operating staff at all times. If the frequency inverter is sold on to other users, then the
documentation must also be handed over.
11/13
ACU
Spindle Applications 9

•
2General safety instructions and information on use
The chapter "General safety instructions and information on use" contains general safety instructions
for the Operator and the Operating Staff. At the beginning of certain main chapters, some safety in-
structions are included which apply to all work described in the relevant chapter. Special work-specific
safety instructions are provided before each safety-relevant work step.
2.1 Terminology
According to the documentation, different activities must be performed by certain persons with certain
qualifications.
The groups of persons with the required qualification are defined as follows:
Operator
This is the entrepreneur/company who/which operates the frequency inverter and uses it as per the
specifications or has it operated by qualified and Instructed Persons.
Operating staff
The term Operating Staff covers persons instructed by the Operator of the frequency inverter and
assigned the task of operating the frequency inverter.
Skilled Personnel
The term Skilled Personnel covers staff that are assigned special tasks by the Operator of the fre-
quency inverter, e.g. installation, maintenance and service/repair and troubleshooting. Based on their
qualification and/or know-how, Skilled Personnel must be capable of identifying defects and assessing
functions.
Qualified Electrician
The term Qualified Electrician covers qualified and trained staff that have special technical know-how
and experience with electrical installations. In addition, Qualified Electricians must be familiar with the
applicable standards and regulations, they must be able to assess the assigned tasks properly and
identify and eliminate potential hazards.
Instructed Person
The term Instructed Person covers staff that are instructed and trained about/in the assigned tasks
and the potential hazards that might result from inappropriate behavior. In addition, Instructed Per-
sons must have been instructed in the required protection provisions, protective measures, the appli-
cable directives, accident prevention regulations as well as the operating conditions and verified their
qualification.
Expert
The term Expert covers qualified and trained staff that have special technical know-how and experi-
ence relating to frequency inverter. Experts must be familiar with the applicable government work
safety directives, accident prevention regulations, guidelines and generally accepted rules of technolo-
gy in order to assess the operationally safe condition of the frequency inverter.
10
ACU
Spindle Applications 11/13

2.2 Designated use
The frequency inverter is designed according to the state of the art and recognized safety regulations.
The frequency inverters are electrical drive components intended for installation in industrial plants or
machines. Commissioning and start of operation is not allowed until it has been verified that the ma-
chine meets the requirements of the EC Machinery Directive 2006/42/EC and DIN EN 60204-1.
The frequency inverters meet the requirements of the low voltage directive 2006/95/EEC and DIN
EN 61800-5-1. CE-labeling is based on these standards. Responsibility for compliance with the EMC
Directive 2004/108/EC lies with the operator. Frequency inverters are only available at specialized
dealers and are exclusively intended for commercial use as per EN 61000-3-2.
No capacitive loads may be connected to the frequency inverter.
The technical data, connection specifications and information on ambient conditions are indicated on
the rating plate and in the documentation and must be complied with at all times.
2.3 Misuse
Any use other than that described in "Designated use" shall not be permissible and shall be consid-
ered as misuse.
For, example, the machine/plant must not be operated
−by uninstructed staff,
−while it is not in perfect condition,
−without protection enclosure (e.g. covers),
−without safety equipment or with safety equipment deactivated.
The manufacturer shall not be held liable for any damage resulting from such misuse. The sole risk
shall be borne by the operator.
2.3.1 Explosion protection
The frequency inverter is an IP 20 ingress protection rating device. For this reason, use of the device
in explosive atmospheres is not permitted.
11/13
ACU
Spindle Applications 11

•
2.4 Residual risks
Residual risks are special hazards involved in handling of the frequency inverter which cannot be elim-
inated despite the safety-compliant design of the device. Residual risks are not obviously identifiable
and can be a potential source of injury or health hazard.
Typical residual hazards include:
Electrical hazard
Danger of contact with energized components due to a defect, opened covers or enclosures or im-
proper working on electrical equipment.
Danger of contact with energized components in frequency inverter if no external disconnection de-
vice was installed by the operator.
Electrostatic charging
Touching electronic components entails the risk of electrostatic discharges.
Thermal hazards
Risk of accidents by hot machine/plant surfaces, e.g. heat sink, transformer, fuse or sine filter.
Charged capacitors in DC link
The DC-link may have dangerous voltage levels even up to three minutes after shutdown.
Danger of equipment falling down/over, e.g. during transport
Center of gravity is not the middle of the electrical cabinet modules.
2.5 Safety and warning signs on frequency inverter
•Comply with all safety instructions and danger information provided on the frequency inverter.
•Safety information and warnings on the frequency inverter must not be removed.
12
ACU
Spindle Applications 11/13

2.6 Warning information and symbols used in the Operating Instruc-
tions
2.6.1 Hazard classes
The following hazard identifications and symbols are used in the Operating Instructions to mark par-
ticularly important information:
DANGER
Identification of immediate threat holding a high
risk of death or serious injury if not
avoided.
WARNING
Identification of immediate threat holding a medium
risk of death or serious injury if
not avoided.
CAUTION
Identification of immediate threat holding a low
risk of minor or moderate physical
injury if not avoided.
NOTE
Identification of a threat holding a risk of material damage if not avoided.
2.6.2 Hazard symbols
Symbol Meaning Symbol Meaning
General hazard
Suspended load
Electrical voltage
Hot surfaces
2.6.3 Prohibition signs
Symbol Meaning
No switching; it is forbidden to switch the ma-
chine/plant, assembly on
2.6.4 Personal safety equipment
Symbol Meaning
Wear body protection
11/13
ACU
Spindle Applications 13

•
2.6.5 Recycling
Symbol Meaning
Recycling, to avoid waste, collect all materials for
reuse
2.6.6 Grounding symbol
Symbol Meaning
Ground connection
2.6.7 ESD symbol
Symbol Meaning
ESD: Components and assemblies sensitive to
electrostatic energy
2.6.8 Information signs
Symbol Meaning
Tips and information making using the frequency
inverter easier.
2.6.9 Font style in documentation
Example
Font style
Use
1234
bold
Representation of parameter numbers
Parameter
italic, Font Times
New Roman
Representation of parameter names
P.1234
bold
Representation of parameter numbers without name, e.g. in
formulas
Q.1234
bold
Representation of source numbers
14
ACU
Spindle Applications 11/13

2.7 Directives and guidelines to be adhered to by the operator
The operator must follow the following directives and regulations:
•Ensure that the applicable workplace-related accident prevention regulations as well as other ap-
plicable national regulation are accessible to the staff.
•An authorized person must ensure, before using the frequency inverter, that the device is used in
compliance with its designated use and that all safety requirements are met.
•Additionally, comply with the applicable laws, regulations and directives of the country in which
the frequency inverter is used.
Any additional guidelines and directives that may be required additionally shall be defined by the op-
erator of the machine/plant considering the operating environment.
2.8 Operator's general plant documentation
•In addition to the Operating Instructions, the operator should issue separate internal user manu-
als for the frequency inverter. The Operating Instructions of the frequency inverter must be in-
cluded in the Operating Instructions of the whole plant.
2.9 Operator's/operating staff's responsibilities
2.9.1 Selection and qualification of staff
•Any work on the frequency inverter may only be carried out by Skilled Personnel. The staff must
not be under the influence of any drugs. Note the minimum age required by law. Define the staff's
responsibility in connection with all work on the frequency inverter clearly.
•Work on the electrical components may only be performed by a qualified electrician according to
the applicable rules of electrical engineering.
•The operating staff must be trained for the relevant work to be performed.
2.9.2 General work safety
•In addition to the Operating Instructions of the machine/plant, any applicable legal or other regu-
lations relating to accident prevention and environmental protection must be complied with. The
staff must be instructed accordingly.
Such regulations and/or requirements may include, for example, handling of hazardous media and
materials or provision/use of personal protective equipment.
•In addition to these Operating Instructions, issue any additional directives that may be required to
meet specific operating requirements, including supervision and reporting requirements, e.g. di-
rectives relating to work organization, workflow and employed staff.
•Unless approved of expressly by the manufacturer, do not modify the frequency inverter in any
way, including addition of attachments or retrofits.
•Only use the frequency inverter if the rated connection and setup values specified by the manu-
facturer are met.
•Provide appropriate tools as may be required for performing all work on the frequency inverter
properly.
11/13
ACU
Spindle Applications 15

•
2.10 Organizational measures
2.10.1 General
•Train your staff in the handling and use of the frequency inverter and the machine/plant as well
as the risks involved.
•Use of any individual parts or components of the frequency inverter in other parts of the opera-
tor's machine/plant is prohibited.
•Optional components for the frequency inverter must be used in accordance with their designated
use and in compliance with the relevant documentation.
2.10.2 Use in combination with third-party products
•Please note that BONFIGLIOLI VECTRON GmbH will not accept any responsibility for compatibility
with third-party products (e.g. motors, cables or filters).
•In order to enable optimum system compatibility, BONFIGLIOLI VECTRON GmbH offers compo-
nents facilitating commissioning and providing optimum synchronization of the machine/plant
parts in operation.
•If you use the frequency inverter in combination with third-party products, you do so at your own
risk.
2.10.3 Transport and storage
•The frequency inverters must be transported and stored in an appropriate way. During transport
and storage the devices must remain in their original packaging.
•The units may only be stored in dry rooms which are protected against dust and moisture and are
exposed to small temperature deviations only. The requirements of DIN EN 60721-3-1 for storage,
DIN EN 60721-3-2 for transport and labeling on the packaging must be met.
•The duration of storage without connection to the permissible nominal voltage may not exceed
one year.
16
ACU
Spindle Applications 11/13

2.11 Handling and installation
•Do not commission any damaged or destroyed components.
•Prevent any mechanical overloading of the frequency inverter. Do not bend any components and
never change the isolation distances.
•Do not touch any electronic construction elements and contacts. The frequency inverter is
equipped with components which are sensitive to electrostatic energy and can be damaged if
handled improperly. Any use of damaged or destroyed components will endanger the ma-
chine/plant safety and shall be considered as non-compliance with the applicable standards.
•Only install the frequency inverter in a suitable operating environment. The frequency inverter is
exclusively designed for installation in industrial environments.
•If seals are removed from the case, this can result in the warranty becoming null and void.
2.11.1 Electrical connections
•The five safety rules must be complied with.
•Never touch live terminals. The DC-link may have dangerous voltage levels even up to three
minutes after shutdown.
•When performing any work on/with the frequency inverter, always comply with the applicable
national and international regulations/laws on work on electrical equipment/plants of the country
in which the frequency inverter is used.
•The cables connected to the frequency inverters may not be subjected to high-voltage insulation
tests unless appropriate circuitry measures are taken before.
•Only connect the frequency inverter to suitable supply mains.
2.11.1.1 The five safety rules
When working on/in electrical plants, always follow the five safety rules:
1. Isolate
2. Secure to prevent restarting
3. Check isolation
4. Earth and short-circuit,
5. Cover or shield neighboring live parts.
11/13
ACU
Spindle Applications 17

•
2.11.2 Safe operation
•During operation of the frequency inverter, always comply with the applicable national and inter-
national regulations/laws on work on electrical equipment/plants.
•Before commissioning and the start of the operation, make sure to fix all covers and check the
terminals. Check the additional monitoring and protective devices according to the applicable na-
tional and international safety directives.
•During operation, never open the machine/plant
•Do not connect/disconnect any components/equipment during operation.
•The machine/plant holds high voltage levels during operation, is equipped with rotating parts
(fan) and has hot surfaces. Any unauthorized removal of covers, improper use, wrong installation
or operation may result in serious injuries or material damage.
•Some components, e.g. the heat sink or brake resistor, may be hot even some time after the ma-
chine/plant was shut down. Don't touch any surfaces directly after shutdown. Wear safety gloves
where necessary.
•The frequency inverter may hold dangerous voltage levels until the capacitor in the DC link is
discharged. Wait for at least 3 minutes after shutdown before starting electrical or mechanical
work on the frequency inverter. Even after this waiting time, make sure that the equipment is
deenergized in accordance with the safety rules before starting the work.
•In order to avoid accidents or damage, only qualified staff and electricians may carry out the work
such as installation, commissioning or setup.
•In the case of a defect of terminals and/or cables, immediately disconnect the frequency inverter
from mains supply.
•Persons not familiar with the operation of frequency inverters must not have access to the fre-
quency inverter. Do not bypass or decommission any protective facilities.
•The frequency inverter may be connected to power supply every 60 s. This must be considered
when operating a mains contactor in jog operation mode. For commissioning or after an emer-
gency stop, a non-recurrent, direct restart is permissible.
•After a failure and restoration of the power supply, the motor may start unexpectedly if the Auto-
Start function is activated.
If staff are endangered, a restart of the motor must be prevented by means of external circuitry.
•Before commissioning and the start of the operation, make sure to fix all covers and check the
terminals. Check the additional monitoring and protective devices according to EN 60204 and ap-
plicable the safety directives (e.g. Working Machines Act or Accident Prevention Directives).
18
ACU
Spindle Applications 11/13

2.11.3 Maintenance and service/troubleshooting
•Visually inspect the frequency inverter when carrying out the required maintenance work and
inspections at the machine/plant.
•Perform the maintenance work and inspections prescribed for the machine carefully, including the
specifications on parts/equipment replacement.
•Work on the electrical components may only be performed by a qualified electrician according to
the applicable rules of electrical engineering. Only use original spare parts.
•Unauthorized opening and improper interventions in the machine/plant can lead to personal injury
or material damage. Repairs on the frequency inverters may only be carried out by the manufac-
turer or persons authorized by the manufacturer. Check protective equipment regularly.
•Before performing any maintenance work, the machine/plant must be disconnected from mains
supply and secured against restarting. The five safety rules must be complied with.
2.11.4 Final decommissioning
Unless separate return or disposal agreements were made, recycle the disassembled frequency in-
verter components:
•Scrap metal materials
•Recycle plastic elements
•Sort and dispose of other component materials
Electric scrap, electronic components, lubricants and other utility materials must be
treated as special waste and may only be disposed of by specialized companies.
In any case, comply with any applicable national disposal regulations as regards envi-
ronmentally compatible disposal of the frequency inverter. For more details, contact the
competent local authorities.
11/13
ACU
Spindle Applications 19

•
3Introductory information about spindle applications
The configurations for spindle applications typically control milling machines with asynchronous ma-
chine (ASM) or permanent magnet synchronous machine (PMSM)
Operation is without encoder at high speeds. In order to enable finer setting of the speed controller
when tools with large diameters are used, using an encoder is possible. When an encoder is used, the
axle can be positioned for tool replacement.
For safe operation in the field weakening range, PMSM, require a brake chopper.
In the field weakening operation will be checked automatically if a brake chopper is available. It`s de-
tected only an existing brake chopper, but not the necessary dimensioning.
This must be performed by the user.
3.1 Configurations for spindle applications
For spindle applications, the following configurations are available:
−804: Spindle application with field-oriented speed control of asynchronous machine (ASM)
−806: Spindle application with field-oriented speed control of permanent magnet synchronous ma-
chine (PMSM)
Configurations 804 and 806 are based on Configurations 410 (sensor-less field-oriented
control of asynchronous machine) and 610 (sensor-less field-oriented control of a syn-
chronous machine, speed controlled).
This application manual describes the changes compared to the underlying configura-
tions. For more information on Configurations 410 and 610, please refer to the Operat-
ing Instructions of the ACU series of frequency inverters.
20
ACU
Spindle Applications 11/13

3.2 Software identification
The software installed can be identified via Parameter Inverter Software Version 012 .
Example of Software identifier:
Further information about the software can be obtained via the following parameters:
Parameter
No.
Identifier
000
Serial Number
001
Optional Modules
015
Copyright
028
Control Level
029
User Name
030
Configuration
033
Language
5 . a . b . cc / 086 - xx
5: stands for Frequency inverter range ACU
a . b . cc: running version, third point is variable
086: stands for spindle application
xx: counter,
11/13
ACU
Spindle Applications 21

•
3.3 Operating characteristics
Parameter Local Remote 412 defines the operating characteristics and enables choosing control via
contacts/control unit and/or the interface.
Parameter
Unit
Setting range
Default settings
No.
Identifier
412 Local Remote - Selection
44 - Ctrl. Cont.+KP,
Dir. Cont.+KP
Operation Modes of Parameter 412
0 - Control via Contacts
Commands Start and Stop as well as definition of
sense of rotation via digital signals.
1 - Control via Statemachine
Commands Start and Stop as well as definition of
sense of rotation via DRIVECOM statemachine of
communication interface.
2 - Control via Remote-Contacts
Commands Start and Stop as well as definition of
sense of rotation via logic signals through the commu-
nication protocol
3 - Ctrl. KP, direction Contacts
Commands Start and Stop from the control unit, defi-
nition of sense of rotation via digital signals.
4 - Ctrl. KP+Cont., direction Cont.
Commands Start and Stop from the control unit or via
digital signals, definition of sense of rotation only via
digital signals.
5 - Ctrl. 3-Wire, direction Cont.
3-wire; control of sense of rotation and the signal
Start 3-wire ctrl. 87 via digital signals.
13
- Control via KP, Direction KP
Commands Start and Stop as well as definition of
sense of rotation via control unit.
14
- Control KP+Cont., Direction KP
Commands Start and Stop via the control unit or digi-
tal signals, definition of sense of rotation only via con-
trol unit.
20
- Control Contacts, Clockw.
Commands Start and Stop via digital signals. Fixed
definition of sense of rotation: clockwise only.
23
- Control Keypad, Clockw.
Commands Start and Stop via control unit. Fixed defi-
nition of sense of rotation: clockwise only.
24
- Control Cont. + KP, Clockw.
Commands Start and Stop via control unit or digital
signals. Fixed definition of sense of rotation: clockwise
only.
30
- Control Contacts, Anticl.
Commands Start and Stop via digital signals. Fixed
definition of sense of rotation, anticlockwise rotation
only.
33
- Control Keypad, Anticl.
Commands Start and Stop via control unit. Fixed defi-
nition of sense of rotation, anticlockwise rotation only.
34
- Control Cont. + KP, Anticl.
Commands Start and Stop via control unit or digital
signals. Fixed definition of sense of rotation, anti-
clockwise rotation only.
43
- Ctrl. KP, Dir. Cont. + KP
Commands Start and Stop via control unit, Definition
of sense of rotation via control unit or digital signals.
44
- Ctrl. Cont.+KP, Dir. Cont.+KP
Commands Start and Stop as well as definition of
sense of rotation via control unit or via digital signals.
46
- Ctrl. 3-Wire+KP, Dir. Cont.+KP
3-wire and control unit. Control of sense of rotation
and signal Start 3-Wire Ctrl 87 via digital signals or
control unit.
22
ACU
Spindle Applications 11/13
Other manuals for Active Cube
3
Table of contents
Other BONFIGLIOLI Inverter manuals

BONFIGLIOLI
BONFIGLIOLI DGM MPM User manual
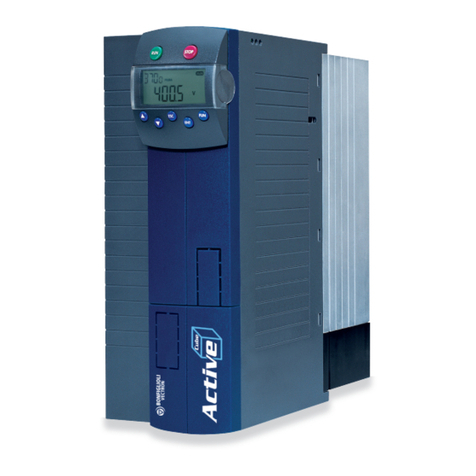
BONFIGLIOLI
BONFIGLIOLI ACTIVE Cube ACU 201-01 User manual
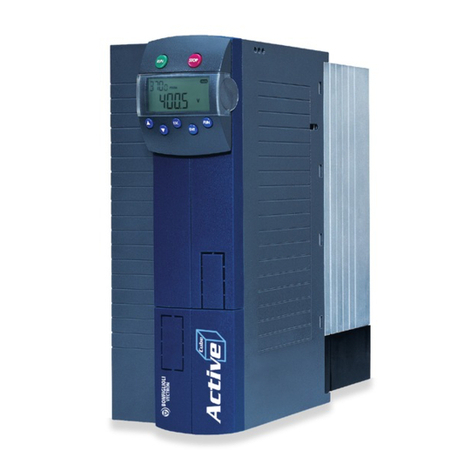
BONFIGLIOLI
BONFIGLIOLI Active Cube User manual
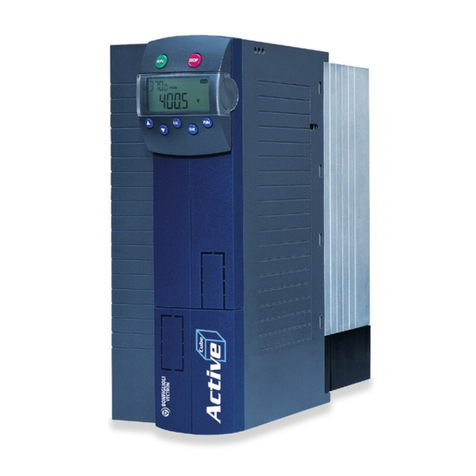
BONFIGLIOLI
BONFIGLIOLI Active Cube Instructions for use
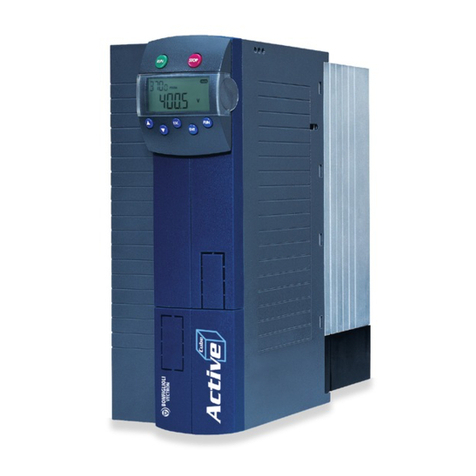
BONFIGLIOLI
BONFIGLIOLI Active Cube User manual
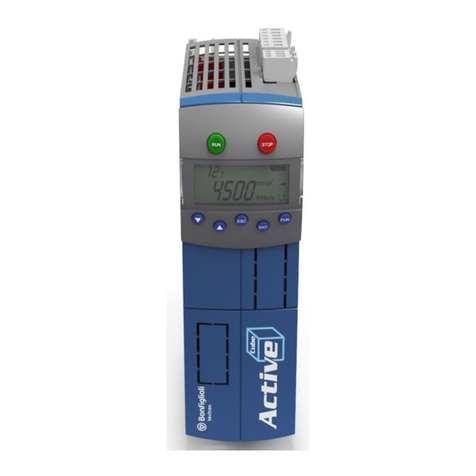
BONFIGLIOLI
BONFIGLIOLI ACTIVE CUBE Series Instructions for use
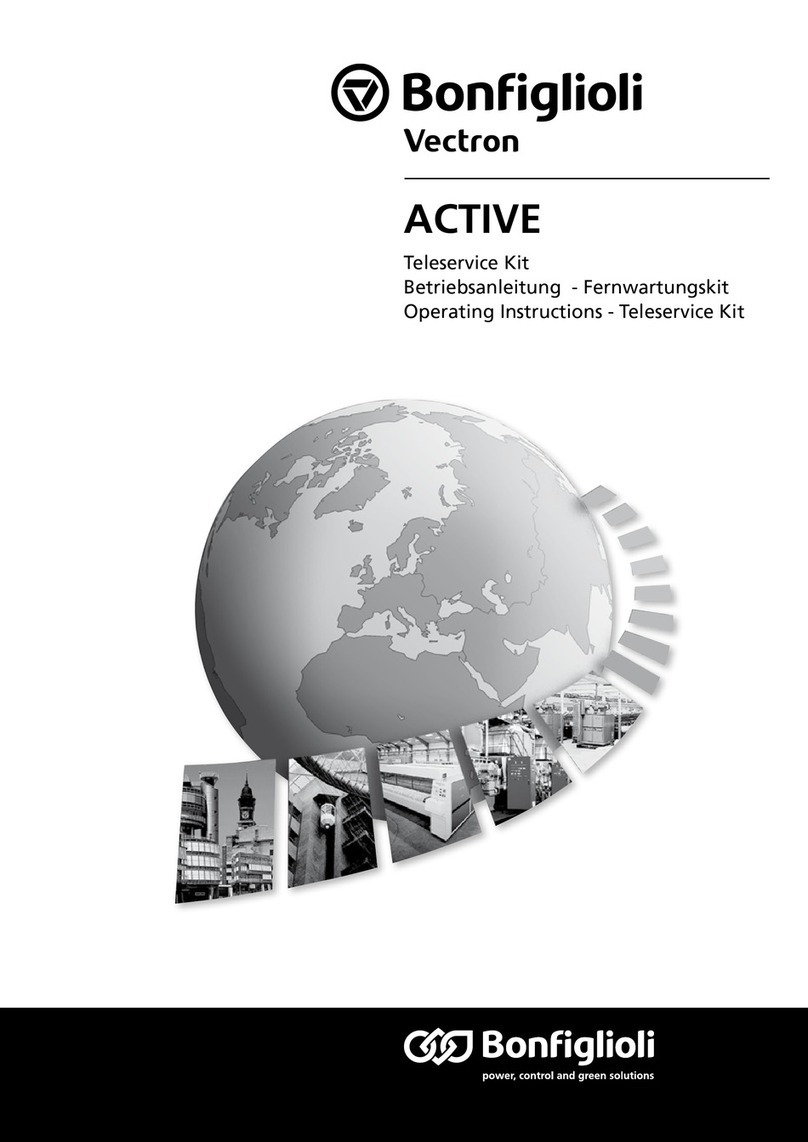
BONFIGLIOLI
BONFIGLIOLI active User manual
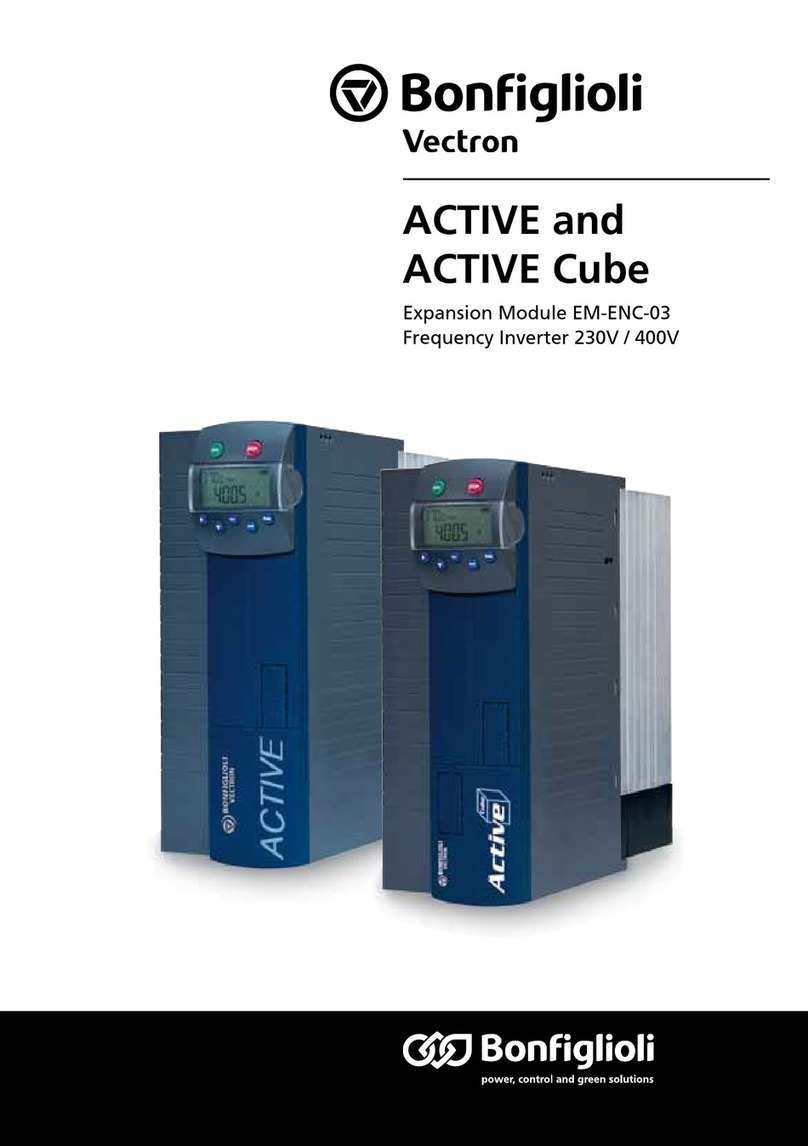
BONFIGLIOLI
BONFIGLIOLI actice User manual