Bryant 524J Series Dimensions and installation guide

Manufacturer reserves the right to discontinue, or change at any time, specifications or designs without notice and without incurring obligations.
Catalog No.: 04-53524002-01 Printed in U.S.A. Form No.: II524J-25-30-01 Rev. B Pg 1 7-22 Replaces: II524J-07
Installation, Start-up and
Service Instructions
CONTENTS
Page
SAFETY CONSIDERATIONS . . . . . . . . . . . . . . . . . . . . . . 1
PRE-INSTALLATION . . . . . . . . . . . . . . . . . . . . . . . . . . . . 2
Moving and Storage . . . . . . . . . . . . . . . . . . . . . . . . . . . . . . . 2
Rigging . . . . . . . . . . . . . . . . . . . . . . . . . . . . . . . . . . . . . . . . . . 2
INSTALLATION . . . . . . . . . . . . . . . . . . . . . . . . . . . . . . . . . 2
General . . . . . . . . . . . . . . . . . . . . . . . . . . . . . . . . . . . . . . . . . . 2
Uncrating . . . . . . . . . . . . . . . . . . . . . . . . . . . . . . . . . . . . . . . . 2
Accessories . . . . . . . . . . . . . . . . . . . . . . . . . . . . . . . . . . . . . . . 2
Unit Positioning . . . . . . . . . . . . . . . . . . . . . . . . . . . . . . . . . . 11
Unit Isolation . . . . . . . . . . . . . . . . . . . . . . . . . . . . . . . . . . . . 12
Refrigerant Piping Access . . . . . . . . . . . . . . . . . . . . . . . . . 12
Refrigerant Piping . . . . . . . . . . . . . . . . . . . . . . . . . . . . . . . 12
Condensate Drain . . . . . . . . . . . . . . . . . . . . . . . . . . . . . . . . 16
Fan Motors and Drives . . . . . . . . . . . . . . . . . . . . . . . . . . . . 16
Power Supply and Wiring . . . . . . . . . . . . . . . . . . . . . . . . . 17
Connecting Ductwork . . . . . . . . . . . . . . . . . . . . . . . . . . . . . 19
• DISCHARGE CONNECTIONS
• RETURN CONNECTIONS
• OUTDOOR-AIR INLET CONNECTIONS
Return-Air Filters . . . . . . . . . . . . . . . . . . . . . . . . . . . . . . . . 19
START-UP . . . . . . . . . . . . . . . . . . . . . . . . . . . . . . . . . . . . . 21
Adjusting TXV for Superheat . . . . . . . . . . . . . . . . . . . . . . 21
SERVICE . . . . . . . . . . . . . . . . . . . . . . . . . . . . . . . . . . . . . . . 21
Panels . . . . . . . . . . . . . . . . . . . . . . . . . . . . . . . . . . . . . . . . . . 21
Fan Motor Lubrication . . . . . . . . . . . . . . . . . . . . . . . . . . . 22
Fan Shaft Bearings . . . . . . . . . . . . . . . . . . . . . . . . . . . . . . . 22
Centering Fan Wheel . . . . . . . . . . . . . . . . . . . . . . . . . . . . . 22
Fan Shaft Position Adjustment . . . . . . . . . . . . . . . . . . . . . 22
Individual Fan Wheel Adjustment . . . . . . . . . . . . . . . . . . 23
Fan Belts . . . . . . . . . . . . . . . . . . . . . . . . . . . . . . . . . . . . . . . 23
Fan Rotation . . . . . . . . . . . . . . . . . . . . . . . . . . . . . . . . . . . . 23
Fan Pulley Alignment . . . . . . . . . . . . . . . . . . . . . . . . . . . . . 23
Pulley and Drive Adjustment . . . . . . . . . . . . . . . . . . . . . . 24
Condensate Drains . . . . . . . . . . . . . . . . . . . . . . . . . . . . . . . 24
Return-Air Filters . . . . . . . . . . . . . . . . . . . . . . . . . . . . . . . . 24
Coil Removal . . . . . . . . . . . . . . . . . . . . . . . . . . . . . . . . . . . . 24
Cleaning Cooling Coil . . . . . . . . . . . . . . . . . . . . . . . . . . . . . 24
Cleaning Insulation . . . . . . . . . . . . . . . . . . . . . . . . . . . . . . . 24
Replacing Filters . . . . . . . . . . . . . . . . . . . . . . . . . . . . . . . . . 24
START-UP CHECKLIST. . . . . . . . . . . . . . . . . . . . . . . .CL-1
SAFETY CONSIDERATIONS
Installation and servicing of air-conditioning equipment can be
hazardous due to system pressure and electrical components.
Only trained and qualified service personnel should install,
repair, or service air-conditioning equipment.
Untrained personnel can perform basic maintenance functions
of cleaning coils and filters and replacing filters. All other
operations should be performed by trained service personnel.
When working on air-conditioning equipment, observe
precautions in the literature, tags and labels attached to the
unit, and other safety precautions that may apply.
Follow all local building codes and appropriate national
electrical codes (in USA, ANSI/NFPA70, National Electrical
Code (NEC); in Canada, CSA C22.1) for special requirements.
Wear safety glasses and work gloves. Use quenching cloth for
unbrazing operations. Have fire extinguisher available for all
brazing operations.
It is important to recognize safety information. This is the
safety-alert symbol . When you see this symbol on the unit
and in instructions or manuals, be alert to the potential for
personal injury.
Understand the signal words DANGER, WARNING,
CAUTION, and NOTE. These words are used with the safety-
alert symbol. DANGER identifies the most serious hazards
which will result in severe personal injury or death.
WARNING signifies hazards which could result in personal
injury or death. CAUTION is used to identify unsafe practices,
which may result in minor personal injury or product and
property damage. NOTE is used to highlight suggestions
which will result in enhanced installation, reliability, or
operation.
WARNING
ELECTRICAL SHOCK HAZARD
Failure to follow this warning could cause in personal injury
or death.
Before performing service or maintenance operations on unit,
always turn off main power switch to unit and install lockout
tag. Unit may have more than one power switch.
WARNING
UNIT OPERATION AND SAFETY HAZARD
Failure to follow this warning could cause in personal injury,
death and/or equipment damage.
Puron® (R-410A) refrigerant systems operate at higher pres-
sures than standard R-22 systems. Do not use R-22 service
equipment or components on Puron refrigerant equipment.
52 4 J*25- 3 0
Pa c kage d Air- H andli ng Un i ts
wit h Pu r o n® (R - 410A ) Refr i gera n t
60 Hz

2
PRE-INSTALLATION
1. The power supply (v, ph, and Hz) must correspond to that
specified on unit rating plate.
2. The electrical supply provided by the utility must be suffi-
cient to handle load imposed by this unit.
3. Refer to Installation, General section (page 2) and Fig. 1
and 2 for locations of electrical inlets, condensate drain, duct
connections, and required clearances before setting unit in
place.
4. This installation must conform with local building codes and
with the NEC (National Electrical Code) or ANSI (American
National Standards Institute)/NFPA (National Fire Protection
Association) latest revision. Refer to provincial and local
plumbing or wastewater codes and other applicable local
codes.
Moving and Storage
To transfer unit from truck to storage site, use a fork truck. Do
not stack units more than 2 high during storage. If unit is to be
stored for more than 2 weeks before installation, choose a lev-
el, dry storage site free from vibration. Do not remove plastic
wrap or skid from unit until final installation.
Rigging
All 524J Series units can be rigged by using the shipping skid.
Units are shipped fully assembled. Do not remove shipping
skids or protective covering until unit is ready for final place-
ment; damage to bottom panels can result. Use slings and
spreader bars as applicable to lift unit.
INSTALLATION
General
Allow the following clearances for service access and airflow:
• Rear: 3 ft (914 mm) [2-1/2 ft (762 mm) with electric heat
accessory]
• Front: 2-1/2 ft (762 mm)
• Right Side: 3-1/2 ft (1067 mm)
• Left Side: 2-1/2 ft (762 mm)
For units equipped with an economizer, refer to the accessory
installation instructions for additional clearance requirements.
Be sure floor, wall, or ceiling can support unit weight
(Tables 1-4). See Fig. 1 and 2 for dimensions.
Uncrating
Move unit as near as possible to final location before removing
shipping skid.
Remove metal banding, top skid, and plastic wrap. Examine
unit for shipping damage. If shipping damage is evident, file
claim with transportation agency. Remove base skid just prior
to actual installation.
Check nameplate information against available power supply
and model number description in Fig. 3.
NOTE: Be sure to remove the styrofoam shipping pad from the
thermostatic expansion valve (TXV). Verify that it has been
removed. (See Fig. 4.)
Accessories
Refer to instructions shipped with each accessory for specific
information.
WARNING
PERSONAL INJURY AND ENVIRONMENTAL
HAZARD
Failure to follow this warning could cause in personal injury
or death.
Relieve pressure and recover all refrigerant before system
repair or final unit disposal.
Wear safety glasses and gloves when handling refrigerants.
Keep torches and other ignition sources away from refriger-
ants and oils.
CAUTION
CUT HAZARD
Failure to follow this caution may result in personal injury.
Sheet metal parts may have sharp edges or burrs. Use care and
wear appropriate protective clothing, safety glasses and gloves
when handling parts and servicing 524J units.
WARNING
UNIT OPERATION HAZARD
Failure to follow this caution could cause equipment damage.
Ensure voltage listed on unit data plate agrees with electrical
supply provided for the unit.

3
Fig. 1 — Dimensions — Size 25

4
Fig. 1 — Dimensions — Size 25 (cont)

5
Fig. 2 — Dimensions — Size 28 and 30

6
Fig. 2 — Dimensions — Size 28 and 30 (cont)

7
LEGEND
Table 1 — 524J***A Physical Data, English — Cooling Units
UNIT 524J* 25A 28A 30A
NOMINAL CAPACITY (Tons) 20 25 30
OPERATING WEIGHT (lb)
Base Unit with TXV 730 1050 1062
Plenum 225 325 325
FANS
Qty...Diam. (in.) 2...15 2...18 2...18
Nominal Airflow (cfm) 8,000 10,000 12,000
Airflow Range (cfm) 6,000-10,000 7,500-12,500 9,000-15,000
Nominal Motor Hp (Standard Motor)
208/230-60 and 460-3-60 5.0 7.5 10.0
575-3-60 5.0 7.5 10.0
Motor Speed (rpm)
208/230-3-60 and 460-3-60 1745 1745 1745
575-3-60 1745 1755 1755
REFRIGERANT R-410A
Operating Charge (lb)
(approx per circuit)a
NOTE(S):
a. Units are shipped without refrigerant charge.
3.5 4.5 5.0
DIRECT — EXPANSION COIL Enhanced Copper Tubes, Aluminum Sine-Wave Fins
Maximum Working Pressure (psig) 650
Face Area (sq ft) 19.88 24.86 29.83
No. of Splits 222
No. of Circuits per Split 18 20 24
Split Type...Percentage Face...50/50
Rows...Fins/in. 4...15 4...15 4...15
PIPING CONNECTIONS
Quantity...Size (in.)
DX Coil — Suction (ODF) 2...1-1/8 2...1-3/82...1-3/8
DX Coil — Liquid Refrigerant (ODF) 2...5/8
Steam Coil, In (MPT) 1...2-1/2
Steam Coil, Out (MPT) 1...1/2
Hot Water Coil, In (MPT) 1...2
Hot Water Coil, Out (MPT) 1...2
Condensate (PVC) 1...1-1/4 ODM/1 IDF
FILTERS Throwaway — Factory Supplied
Quantity...Size (in.) 4...16 x 20 x 2
4...16 x 24 x 2
4...20 x 24 x 2
4...20 x 25 x 2
Access Location Either Side
STEAM COILb
b. Field-installed accessory only.
Maximum Working Pressure (psig at 260°F) 20
Total Face Area (sq ft) 13.33 15.0 15.0
Rows...Fins/in. 1...10 1...10 1...10
HOT WATER COILb
Maximum Working Pressure (psig) 150
Total Face Area (sq ft) 13.33 15.0 15.0
Rows...Fins/in. 2...8.5 2...12.5 2...12.5
Water Volume
(gal) 13.9 14.3
(ft3)1.86 1.90
DX — Direct Expansion
IDF — Inside Diameter, Female
ODF — Outside Diameter, Female
ODM — Outside Diameter, Male
TXV — Thermostatic Expansion Valve

8
LEGEND
Table 2 — 524J***A Physical Data, SI — Cooling Units
UNIT 524J* 25A 28A 30A
NOMINAL CAPACITY (kW) 70 87 105
OPERATING WEIGHT (kg)
Base Unit with TXV 331 477 482
Plenum 102 148 148
FANS
Qty...Diam. (mm) 2...381 2...457 2...457
Nominal Airflow (L/s) 3775 4119 5663
Airflow Range (L/s) 2831-4719 3539-5899 4247-7079
Nominal Motor kW (Standard Motor)
208/230-3-60 and 460-3-60 3.73 5.60 7.46
575-3-60 3.73 5.60 7.46
Motor Speed (r/s)
208/230-3-60 and 460-3-60 29.1 29.1 29.1
575-3-60 29.1 29.3 29.3
REFRIGERANT R-410A
Operating Charge (kg)
(approx per circuit)a
NOTE(S):
a. Units are shipped without refrigerant charge.
1.59 2.04 2.27
DIRECT — EXPANSION COIL Enhanced Copper Tubes, Aluminum Sine-Wave Fins
Maximum Working Pressure (kPag) 4481
Face Area (sq m) 1.85 2.30 2.77
No. of Splits 222
No. of Circuits per Split 18 20 24
Split Type...Percentage Face...50/50
Rows...Fins/m 4...591 4...591 4...591
PIPING CONNECTIONS
Quantity...Size (in.)
DX Coil — Suction (ODF) 2...1-1/8 2...1-3/8 2...1-3/8
DX Coil — Liquid Refrigerant (ODF) 2...5/8
Steam Coil, In (MPT) 1...2-1/2
Steam Coil, Out (MPT) 1...1/2
Hot Water Coil, In (MPT) 1...2
Hot Water Coil, Out (MPT) 1...2
Condensate (PVC) 1...1-1/4 ODM/1 IDF
FILTERS Throwaway — Factory Supplied
Quantity...Size (mm) 4... 406 x 508 x 51
4...406 x 610 x 51
4...508 x 610 x 51
4...508 x 635 x 51
Access Location Either Side
STEAM COILb
b. Field-installed accessory only.
Maximum Working Pressure (kPag at
126°C) 138
Total Face Area (sq m) 1.24 1.39 1.39
Rows...Fins/m 1...394 1...394 1...394
HOT WATER COILb
Maximum Working Pressure (kPag) 1034
Total Face Area (sq ft) 1.24 1.39 1.39
Rows...Fins/in. 2...335 2...335 2...335
Water Volume
(L) 52.6 54.1
(m3)0.052 0.054
DX — Direct Expansion
IDF — Inside Diameter, Female
ODF — Outside Diameter, Female
ODM — Outside Diameter, Male
TXV — Thermostatic Expansion Valve

9
LEGEND
Table 3 — 524J*25H Physical Data, English — Heat Pump Units
UNIT 524J* 25H
NOMINAL CAPACITY (Tons) 20
OPERATING WEIGHT (lb)
Base Unit with TXV 730
Plenum 225
FANS
Qty...Diam. (in) 2...15
Nominal Airflow (cfm) 8,000
Airflow Range (cfm) 6,000-10,000
Nominal Motor kW (Standard Motor)
208/230-3-60 and 460-3-60 5.0
575-3-60 5.0
Motor Speed (rpm)
208/230-3-60 and 460-3-60 1745
575-3-60 1745
REFRIGERANT R-410A
Operating Charge (lb)
(approx per circuit)a
NOTE(S):
a. Units are shipped without refrigerant charge.
3.5/3.5
DIRECT — EXPANSION COIL Enhanced Copper Tubes, Aluminum Sine-Wave Fins
Maximum Working Pressure (psig) 650
Face Area (sq ft) 19.9
No. of Splits 2
No. of Circuits per Split 2
Split Type...Percentage Face....50/50
Rows...Fins/in. 4...15
PIPING CONNECTIONS
Quantity...Size (in.)
DX Coil — Suction (ODF) 2...1-1/8
DX Coil — Liquid Refrigerant (ODF) 2...5/8
Steam Coil, In (MPT) 1...2-1/2
Steam Coil, Out (MPT) 1...1-1/2
Hot Water Coil, In (MPT) 1...2
Hot Water Coil, Out (MPT) 1...2
Condensate (PVC) 1...1-1/4 ODM/1 IDF
FILTERS Throwaway — Factory Supplied
Quantity...Size (in.) 4...16 x 20 x 2
4...16 x 24 x 2
Access Location Right or Left Side
STEAM COILb
b. Field-installed accessory only.
Maximum Working Pressure (psig at 260°F) 20
Total Face Area (sq ft) 13.33
Rows...Fins/in. 1...10
HOT WATER COILb
Maximum Working Pressure (psig) 150
Total Face Area (sq ft) 13.33
Rows...Fins/in. 2...8.5
Water Volume
(gal) 13.9
(ft3)1.85
DX — Direct Expansion
IDF — Inside Diameter, Female
ODF — Outside Diameter, Female
ODM — Outside Diameter, Male
TXV — Thermostatic Expansion Valve

10
LEGEND
Table 4 — 524J*25H Physical Data, SI — Heat Pump Units
UNIT 524J* 25H
NOMINAL CAPACITY (kW) 70
OPERATING WEIGHT (kg)
Base Unit with TXV 326
Plenum 44
FANS
Qty...Diam. (mm) 2...381
Nominal Airflow (L/s) 3775
Airflow Range (L/s) 2831-4719
Nominal Motor kW (Standard Motor)
208/230-3-60 and 460-3-60 3.73
575-3-60 3.73
Motor Speed (r/s)
208/230-3-60 and 460-3-60 29.1
575-3-60 29.1
REFRIGERANT R-410A
Operating Charge (kg)
(approx per circuit)a1.59 /1.59
DIRECT — EXPANSION COIL Enhanced Copper Tubes, Aluminum Sine-Wave Fins
Maximum Working Pressure (kPag) 4482
Face Area (sq m) 1.85
No. of Splits 2
No. of Circuits per Split 2
Split Type...Percentage Face...50/50
Rows...Fins/m 591
PIPING CONNECTIONS
Quantity...Size (in.)
DX Coil — Suction (ODF) 2...1-1/8
DX Coil — Liquid Refrigerant (ODF) 2...5/8
Steam Coil, In (MPT) 1...2-1/2
Steam Coil, Out (MPT) 1...1-1/2
Hot Water Coil, In (MPT) 1...2
Hot Water Coil, Out (MPT) 1...2
Condensate (PVC) 1...1-1/4 ODM/1 IDF
FILTERS Throwaway — Factory Supplied
Quantity...Size (mm) 4... 406 x 508 x 51
4...406 x 610 x 51
Access Location Right or Left Side
STEAM COILb
Maximum Working Pressure (kPag at 126°C) 138
Total Face Area (sq m) 1.24
Rows...Fins/m 1...394
HOT WATER COILb
Maximum Working Pressure (kPag) 1034
Total Face Area (sq ft) 1.24
Rows...Fins/in. 2...335
Water Volume
(L) 52.6
(m3)0.052
NOTE(S):
a. Units are shipped without refrigerant charge.
b. Field-installed accessory only.
DX — Direct Expansion
IDF — Inside Diameter, Female
ODF — Outside Diameter, Female
ODM — Outside Diameter, Male
TXV — Thermostatic Expansion Valve

11
Fig. 3 — Model Number Nomenclature
Fig. 4 — Foam Block Location
Unit Positioning
The unit can be mounted on the floor for vertical application
with return air entering the face of the unit and supply air
discharging vertically through the top of the unit. The unit can
also be applied in a horizontal arrangement with return air
entering horizontally and the supply air discharging
horizontally. When applying the unit in a horizontal
arrangement, ensure the condensate drain pan is located at the
bottom center of the unit for adequate condensate disposal. See
Fig. 5 for condensate connections for each unit position.
Typical positioning and alternate return air locations are shown
in Fig. 5. Alternate return air locations can be used by moving
the unit panel from the alternate return air location to the
standard return air location. Refer to overhead suspension
accessory drawing. (See Fig. 6.) for preferred suspension
technique. The unit needs support underneath to prevent
sagging.
NOTE: Maintain recommended clearances per Fig. 1 and 2.
Fig. 5 — Typical Unit Positioning
1234567891011121314151617
5 2 4 J E 2 5 A 0 0 0 A 2 0 A A A
_____________
Model Type Packaging
524J = Bryant Fan Coil
Puron®R-410A Refrigerant
A=Standard
Type of Coil
Service Options
H = DX Coil for Heat Pump Duty (size 25 only)
A = Standard Direct Expansion (DX) Coil
A = None
B = Painted Cabinet
Indoor Fan Options
1 = Fan Drive and Motor — Low / Motor Efficiency — Std
2 = Fan Drive and Motor — Med / Motor Efficiency — Std
Not Used
A = Not Used
Not Used
0 = Not Used
Not Used
0 = Not Used
Coil Options
A=Al/Cu
Not Used
0 = Not Used
Not Used
0 = Not Used
3 = Fan Drive and Motor — High / Motor Efficency — Std
Voltage
E = 460-3-60
P = 208/230-3-60
T = 575-3-60
____
Nominal Tonnage
25 = 20 Tons
28 = 25 Tons
30 = 30 Tons
TXV Coil
Remove Foam Block
LEGEND
TXV — Thermostatic Expansion Valve
IMPORTANT: Do NOT attempt to install unit with return air
entering top panel of unit. Condensate will not drain from
unit.
LEGEND
Accessory Line
Alternate Air Intake and Discharge
Air Intake and Discharge
Plug
Plug Condensate Drain

12
Fig. 6 — Preferred Suspension Technique
Unit Isolation
Where extremely quiet operation is essential, install isolators
between floor and base of unit, or between ceiling and top sec-
tion of unit.
Be sure that unit is level and adequately supported. Use chan-
nels at front and sides of unit for reference points when
leveling.
Refrigerant Piping Access
The 524J Series units come with standard knockouts for refrig-
erant and chilled water piping. These knockouts are located on
both sides of the unit for installation flexibility. The standard
knockouts provide sufficient access to the unit’s coils for all
524J*25A, 28A, and 30A units. 524J*25H units, require addi-
tional holes which must be field-fabricated to accommodate
the piping. See Fig. 7 for the positions and dimensions of the
additional access holes required. Recommended access hole
use is also listed for all units. Note that Fig. 7 shows the access
holes on the control-box side of the unit; this is the side of the
unit with the coil headers, so it is used most often for piping
access.
Refrigerant Piping
See Tables 1-4 for refrigerant pipe connection sizes. For ease in
brazing, it is recommended that all internal solder joints be
made before unit is placed in final position.
The 524J direct-expansion units have internal factory-installed
thermostatic expansion valves (TXVs), distributors, and noz-
zles for use with R-410A. See Table 5 for part numbers.
Knockouts are provided in the unit corner posts for 524J refrig-
erant piping. See Fig. 7, which also lists recommended knock-
outs and access holes to use for each 524J unit size. Recom-
mended fittings are listed in Table 6.
The sensor bulb capillary tubes must be routed from the TXVs
inside the unit through one of the piping access holes. Clamp
NOTE: Dimensions in [ ] are millimeters
OVERHEAD SUSPENSION ACCESSORY — UNIT SIZE 25
OVERHEAD SUSPENSION ACCESSORY — UNIT SIZES 28, 30
IMPORTANT: Do not bury refrigerant piping underground.

13
the TXV sensor bulb on a vertical portion of the suction line,
outside the unit. (See Fig. 8.)
NOTE: Be sure to remove the styrofoam shipping pad from the
TXV. Verify that it has been removed. (See Fig. 4.)
The 524J Series evaporator coils have a face-split design. En-
sure that lower circuit of coil is first on/last off when connected
to the condensing unit and/or system controls. (See Fig. 9.)
External TXV equalizer connections are provided and factory-
brazed into the coil suction manifolds.
If suction line must be horizontal, clamp bulb to suction line at
least 45 degrees above bottom, at approximately the 4 o’clock
or 8 o’clock position. (See Fig. 10.)
Fig. 7 — Refrigerant Piping Access Holes
IMPORTANT: Never attach the sensor to the suction
manifold. Do NOT mount the sensor on a trapped portion of
the suction line.
4
3
2
1
7
6
5
ABCD
8
UNIT USE HOLE
NO.a
FIELD-FABRICATED HOLE DIAMETERS
in (mm)
FIELD-FABRICATED HOLE POSITION
DIMENSIONS in (mm)
NO. 5 NO. 6 NO.7 NO.8 A B C D
524J*25A,28A,30A 1,2,3,4 — — — — — — — —
524J*25H 3b,5,6,7 1-1/8 (28.6) 1-1/8 (28.6) 1-3/4 (44.5) — 3.25 (82.6) 6.125 (155.6) 10.38 (263.7)
NOTE(S):
a. Access hole knockouts 1-4 are factory-supplied.
b. Must be enlarged from 1-1/8 in. (28.6mm) to 1-3/4 in. (44.5mm)

14
Fig. 8 — Face-Split Coil and Liquid Line Piping (Typical)
Fig. 9 — Typical Evaporator Coil Connections (524J)
Fig. 10 — TXV Sensing Bulb Location
LEGEND
TXV – Thermostatic Expansion Valve
NOTE: Component location arrangement shown for field installation of
sight glasses, solenoid valves, filter driers, and TXV sensing bulbs.
The TXVs and equilizer lines are factory installed.
Upper
Split
Airflow
Lower
Split
Airflow
15 Diams
Min 10
Diams
8 Diams
Min
TXV
Sensing
Bulb
Equalizer Line
Sight
Glass
TXV
Solenoid
Valve
Filter
Drier
TXV
Sensing
Bulb
TXV
8 Diams
Min
15 Diams
Min 10
Diams
Indoor
Coil
Equalizer
Line
First On/Last Off = B
Vertical Installation
First On/Last Off = A
Horizontal Installation
AA
BB
Liquid Line
Connection
Liquid Line
Connection
Suction-Vapor
Connection
Suction-Vapor
Connection
Condensate
Drain
Connection
Condensate
Drain
Connection
AA
BB
Condensate Drain Connection
LEGEND
TXV — Thermostatic Expansion Valve
NOTE: The 8 o’clock position is shown above.
Vapor LineVapor Line
45°45°
StrapStrap
TVX BulbTVX Bulb

15
Table 5 — Factory-Installed Nozzle and Distributor Dataa
NOTE(S):
a. Hot gas bypass applications require field-supplied auxiliary side connector.
UNIT COIL TYPE STD TXV QTY...PART NO. DISTRIBUTOR QTY...
PART NO.
FEEDER TUBES PER
DISTRIBUTORb
QTY...SIZE (IN.)
b. Feeder tube size is 1/4 in. (6.35 mm).
NOZZLE QTY...PART NO.
524J*25A 4 Row 2...BBIZE-8-GA 2...D196-18-3/16 18...3/16 2...G6
524J*28A 4 Row 2...BBIZE-15-GA 2...1126 20...3/16 2...C15
524J*30A 4 Row 2...BBIZE-15-GA 2...1126 24...3/16 2...C17
524J*25H 4 Row 2...BBIZE-12.5-GA 2...113-12-3/16 2-12...3/16 2...G8
Table 6 — Fitting Requirements
UNIT ACCESS HOLD NO.a
NOTE(S):
a. Fittings are listed on order from header or tee stub connection out to access hole in corner support post.
CONNECTION TYPE CIRCUIT FITTING REQUIREDb (IN.)
b. See Fig. 7 for access hole location by number.
524J*25A
1 Suction Lower
1-1/8 Street Elbow
1-1/8 Nipple, 7-5/8 L
1-1/8 Long Radius Elbow
2 Liquid Lower
5/8 Street Elbow
5/8 Nipple, 6-1/2 L
5/8 Long Radius Elbow
3 Liquid Upper
5/8 Street Elbow
5/8 Nipple, 9-1/2 L
5/8 Long Radius Elbow
4 Suction Upper
1-1/8 Nipple, 5-5/8 L
1-1/8 Long Radius Elbow
1-1/8 Nipple, 11 L
1-1/8 Long Radius Elbow
524J*25H
3 Suction Lower 1-1/8 Nipple, 3 L
1-1/8 Long Radius Elbow
5 Suction Lower
5/8 Nipple, 2-7/8 L
5/8 45° Elbow
5/8 Nipple, 1-5/8 L
5/8 Long Radius Elbow
6 Liquid Upper
5/8 Nipple, 2-7/8 L
5/8 45° Elbow
5/8 Nipple, 4-1/4 L
5/8 Long Radius Elbow
7 Suction Upper
1-1/8 Nipple, 5 L
1-1/8 45° Elbow
1-1/8 Nipple, 8-3/4 L
1-1/8 Long Radius Elbow
524J*28A
1 Suction Lower
1-3/8 Street Elbow
1-3/8 Nipple, 11 L
1-3/8 Long Radius Elbow
2 Liquid Lower
5/8 Street Elbow
5/8 Nipple, 1-1/2 L
5/8 Long Radius Elbow
3 Liquid Upper
5/8 Street Elbow
5/8 Nipple, 19-1/2 L
5/8 Long Radius Elbow
4 Suction Upper
1-3/8 Nipple, 43/16 L
1-3/8 Long Radius Elbow
1-3/8 Nipple, 23-1/4 L
1-3/8 Long Radius Elbow
524J*30A
1 Suction Lower
1-3/8 Street Elbow
1-3/8 Nipple, 3 L
1-3/8 Long Radius Elbow
2 Liquid Lower
5/8 Street Elbow
5/8 Nipple, 7-3/4 L
5/8 Long Radius Elbow
3 Liquid Upper
5/8 Street Elbow
5/8 Nipple, 18-1/2 L
5/8 Long Radius Elbow
4 Suction Upper
1-3/8 Nipple, 43/16 L
1-3/8 Long Radius Elbow
1-3/8 Nipple, 19-1/4 L
1-3/8 Long Radius Elbow

16
Condensate Drain
Install a trapped condensate drain line to unit connection as
shown in Fig. 11. The unit drain connection is a PVC stub. (See
Fig. 12.) Some areas may require an adapter to connect to ei-
ther galvanized steel or copper pipe. For these applications, in-
stall a field-supplied threaded PVC adapter.
Fig. 11 — Condensate Drain
NOTE: A trap must be installed in the condensate drain line to
ensure that the static pressure of fans is balanced with the water
column in the drain line and that condensate can drain com-
pletely from pan. Without a trap, air can be drawn up drain line
until water level in condensate pan becomes equal to static
pressure created by fans, preventing complete drainage. Condi-
tions will worsen as filters become dirty.
Install clean-out plugs in trap. Pitch drain line downward to an
open floor drain or sump. Provide service clearance around
drain line to permit removal of unit panels. Observe all local
sanitary codes.
Fig. 12 — Drain Pan Slope Adjustment
As shipped, the unit’s condensate drain pan is NOT sloped to-
wards the drain connection. The pan slope must be changed to
pitch towards the side of the unit with the drain connection.
(See Fig. 12.) Loosen the 2 screws next to the drain outlet at
both ends of the unit, push drain pan down in the slots near the
drain connection, and up in the slots on the opposite end. Re-
tighten screws. The pan should have a pitch of at least 1/4 in.
over its length toward the drain connection.
Fan Motors and Drives
Motor and drive packages are factory installed in all units. The
motor and drive packages consist of the following items:
1 — Fan motor
1 — Adjustable motor pulley
1 — Fan pulley
2 — Matched fan belts
(524J*25A-30A and 524J*25H-30H units)
For instructions on changing fan rotation, changing drive
speeds and adjusting drives, see Pulley and Drive Adjustment
in the Service section.
3” MIN.
[76]
NOTE: Dimensions in [ ] are in millimeters
PlugPlug
3" Min.
[76]
3" Min.
[76]
From
Condensate
Pan
From
Condensate
Pan
Existing Floor
Drain, Sink, or
Hopper
Existing Floor
Drain, Sink, or
Hopper Unit
Condensate
Conn
Unit
Condensate
Conn
TrapTrap
Not Less Than 18" [457]
Long and Two Sizes
Larger Than Waste Pipe
Not Less Than 18" [457]
Long and Two Sizes
Larger Than Waste Pipe
To SewerTo Sewer
1" Min.1" Min.
PlugPlug
PlugPlug
3" Min.
[76]
3" Min.
[76]
3" Min.
[76]
3" Min.
[76]
TrapTrap
[25][25]
PlugPlug
Adjustment Slots
(Both Ends of Unit)
PVC Stub Unit
Drain Connection

17
Power Supply and Wiring
Check the unit data plate to ensure that available power supply
matches electrical characteristics of the unit. Provide a discon-
nect switch with an integrated lock-out feature of size required
to provide adequate fan motor starting current. See Tables 7-9
for unit electrical data.
Fig. 13 — Disconnect Switch and Unit
Install disconnect switch and power wiring in accordance with
all applicable local codes. See Fig. 13-15 and the unit label dia-
gram. Connect power wiring with 1/4 in. ring terminal.
Fig. 14 — Wiring and Service access
(Side Panel Removed)
Fan motors are factory-installed on all units. Indoor-fan
contactors are located in the fan contactor box behind the side
access panel. (See Fig. 14 and 15.) Wire the thermostat to the
24-v control circuit terminal block located in the side of the fan
contactor control box, according to Fig. 16 or the unit label
diagram. If the air handler is part of a split system, complete
the wiring from the condensing unit to the thermostat shown in
Fig. 16.
Fig. 15 — Fan Contactor Box and Terminal Block (Cover
Removed) (Typical)
WARNING
ELECTRICAL SHOCK HAZARD
Failure to follow this warning could result in personal injury
or death.
Do not use gas piping as an electrical ground. Unit cabinet
must have an uninterrupted, unbroken electrical ground to
minimize the possibility of personal injury if an electrical fault
should occur. This ground may consist of electrical wire con-
nected to unit ground lug in control compartment, or conduit
approved for electrical ground when installed in accordance
with NEC (National Electrical Code); ANSI/NFPA 70, latest
edition (in Canada, Canadian Electrical Code CSA [Canadian
Standards Association] C22.1), and local electrical codes.
WARNING
FIRE HAZARD
Failure to follow this warning could result in intermittent oper-
ation or performance satisfaction.
Do not connect aluminum wire between disconnect switch
and fan coil unit. Use only copper wire. (See Fig. 13.)
Copper
Wire Only
Electric
Disconnect
Switch
Aluminum
Wire
Filter
Elements
Filter
Retainer
Clip
Fan Scroll
Condensate
Drain
Connection
(Horizontal)
Motor
and Drive
Fan
Contactor
Box
Wire
Access
Coil
Fan Drive
Pulley
TXV Bulb
Access
Refrigerant
Piping Access
Condensate
Drain
Connection
(Vertical)
LEGEND
TXV —Thermostatic Expansion Valve
23
22
21
1
3
1
2
1
1
105°C600V R JA
W
Fan
Contactor
24V
Terminal
Block
Power
Wiring
Knockout

18
Example: Supply voltage is 230-3-60
Determine maximum deviation from average voltage.
(AB) 227-224 = 3 v
(BC) 231-227 = 4 v
(AC) 227-226 = 1 v
Maximum deviation is 4 v.
Determine percent of voltage imbalance.
This amount of phase imbalance is satisfactory as it is below the
maximum allowable 2%.
Table 7 — Electrical Data, Standard Motors
UNITa, b v-Ph-Hz VOLTAGE
LIMITSc
FAN MOTOR POWER SUPPLYd
Hp (kW)
FULL LOAD
AMPS
(FLA)e
MINIMUM
CIRCUIT AMPS
(MCA)
MAXIMUM
OVERCURRENT
PROTECTION
(MOCP)
524J*25A
424J*25H
208/230-3-60 187-253 5.0 (3.73) 14.7/13.6 18.4/17.0 30/25
460-3-60 414-506 5.0 (3.73) 6.8 8.5 15
575-3-60 518-632 5.0 (3.73) 5.1 6.4 15
524J*28A
208/230-3-60 187-253 7.5 (5.59) 21.4/19.4 26.9/24.3 45/40
460-3-60 414-506 7.5 (5.59) 9.7 12.1 20
575-3-60 518-632 7.5 (5.59) 7.8 9.8 15
524J*30A
208/230-3-60 187-253 10.0 (7.46) 28.0/25.2 35.0/31.5 60/50
460-3-60 414-506 10.0 (7.46) 12.6 15.8 25
575-3-60 518-632 10.0 (7.46) 10.3 12.9 20
Table 8 — Electrical Data, Alternate Motors
UNITa, b
NOTE(S):
a. Unbalanced 3-Phase Supply Voltage Never operate a motor where a phase imbalance in supply voltage is greater than 2%. Use the formula in the
example below to determine the percentage of voltage imbalance.
b. Installation with Accessory Electric Heaters Size the Field Power Wiring between the heater TB1 and the 524J indoor fan motor per NEC Article 430-
28 (1) or (2) (depends on length of conduit between heater enclosure and 524J power entry location). Install wires in field-installed conduit.
v-Ph-Hz VOLTAGE
LIMITSc
c. Motors are designed for satisfactory operation within 10% of normal voltage shown. Voltages should not exceed the limits shown in the Voltage
Limits column.
FAN MOTOR POWER SUPPLYd
d. Minimum circuit amps (MCA) and MOCP values are calculated in accordance with The NEC. Article 440.
Hp (kW) FULL LOAD AMPS
(FLA)e
e. Motor FLA values are established in accordance with Underwriters’ Laboratories (UL). Standard 1995.
MINIMUM
CIRCUIT AMPS
(MCA)
MAXIMUM
OVERCURRENT
PROTECTION
(MOCP)
524J*25A
524J*25H
208/230-3-60 187-253 7.5 (5.59) 21.4/19.4 26.9/24.3 45/40
460-3-60 414-506 7.5 (5.59) 9.7 12.1 20
575-3-60 518-632 7.5 (5.59) 7.8 9.8 15
524J*28A
524J*30A
208/230-3-60 187-253 10.0 (7.46) 28.0/25.2 35.0/31.5 60/50
460-3-60 414-506 10.0 (7.46) 12.6 15.8 25
575-3-60 518-632 10.0 (7.46) 10.3 12.9 20
% Voltage
Imbalance = 100 x max voltage deviation from average voltage
average voltage
AB = 224 v
BC = 231 v
AC = 226 v
Average Voltage = (224 + 231 + 226) =681 = 227
3 3
% Voltage Imbalance = 100x 4= 1.78%
227
IMPORTANT: If the supply voltage phase imbalance is more than 2%,
contact your local electric utility company immediately.
ABC
MOTOR

19
Fig. 16 — Unit Wiring
Connecting Ductwork
Refer to the Bryant System Design Manual for the recom-
mended design and layout of ductwork. Figure 17 shows rec-
ommended duct connection to units with 2 fans.
DISCHARGE CONNECTIONS
Duct flanges are factory-supplied; they are shipped inside the
unit attached to the hairpin end of the coil tube sheet for field
installation. Using the existing screws, install the duct flanges
on the unit’s fan deck. Each fan discharge requires 2 flanges;
each flange must be bent in the middle to conform to the
discharge opening. (See Fig. 18.) After flanges are installed,
connect them to the supply duct using a canvas connection to
prevent vibration. It is important that this connection be
properly fabricated to prevent high air friction losses and air
noise.
RETURN CONNECTIONS
When using return-air ductwork, route return-air duct to the
unit’s return air inlet near the filter rack, using a canvas
connection to prevent transmission of unit vibration. If the duct
blocks off the unit’s access panel, provide a slip joint in the
ductwork to permit removal for servicing.
OUTDOOR-AIR INLET CONNECTIONS
Connect outdoor-air inlet to field-installed accessory
economizer. Refer to Economizer Installation Instructions.
Return-Air Filters
Type and size of filters are shown in Tables 1-4 and are
factory-supplied and factory-installed. In all units with 2 fans,
a filter replacement tool (hook) is shipped inside the unit for
field use when replacing filters. See the Service section for
instructions on filter element replacement.
Table 9 — Fan Contactor Coil Data
UNIT 524J* VOLTAGE
(vac)
MAXIMUM
HOLDING VA
25A,25H,28A,30A 24 10
CAUTION
UNIT OPERATION HAZARD
Failure to follow this caution could cause equipment damage.
Do not operate unit without ductwork or discharge plenum
unless fan speed has been adjusted for external static pressure
of zero in. wg. Failure to do so may result in motor overload.

20
Fig. 17 — Typical Fan Discharge Connections for Multiple Fan Units
Fig. 18 — Duct Flange Installation
Duct Flanges
Other manuals for 524J Series
3
This manual suits for next models
7
Table of contents
Other Bryant Air Handler manuals
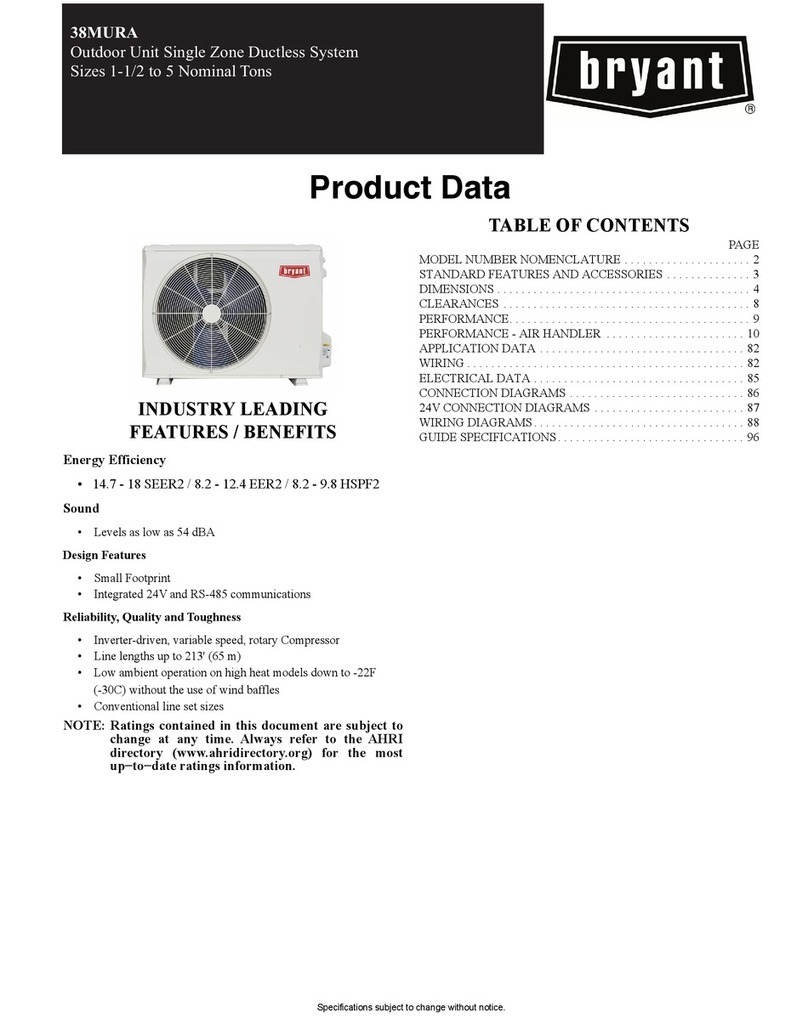
Bryant
Bryant 38MURA User manual
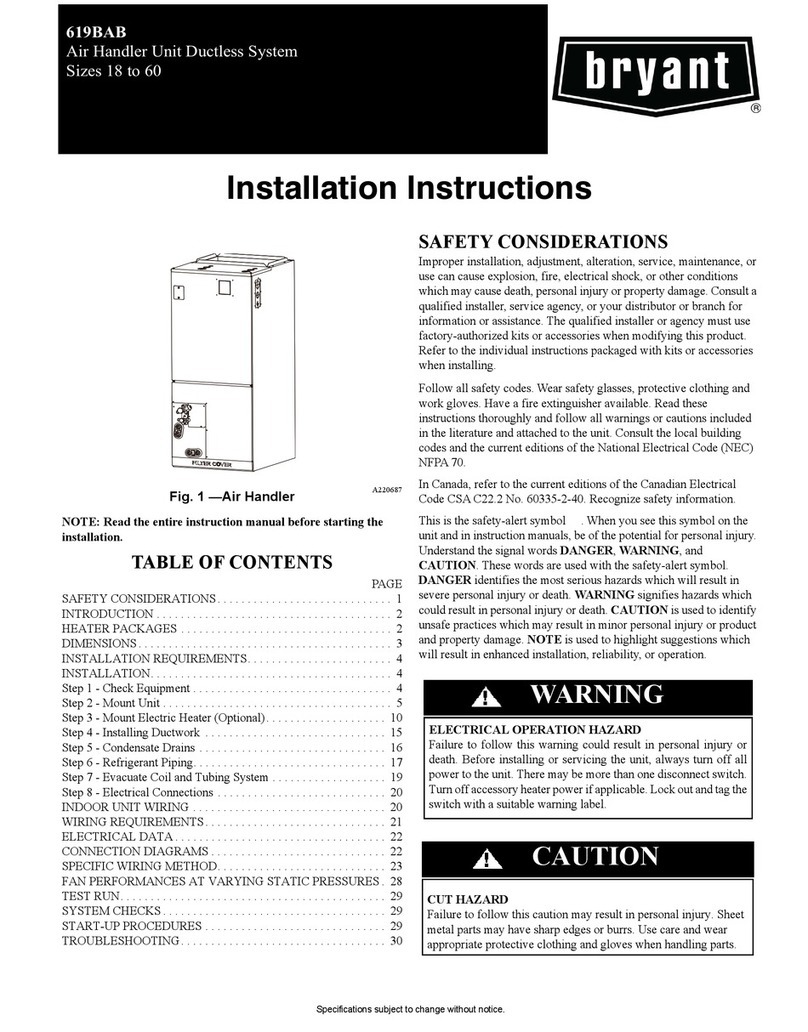
Bryant
Bryant 619BAB User manual
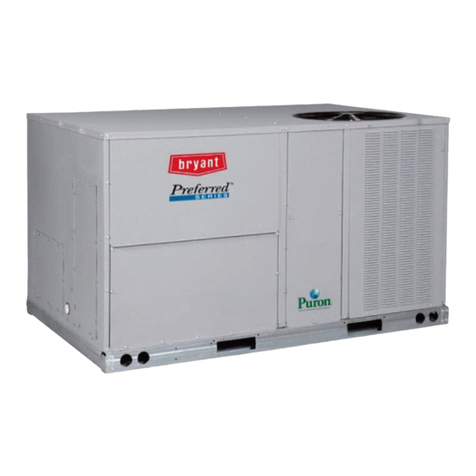
Bryant
Bryant Preferred 581J04-14 Installation and user guide
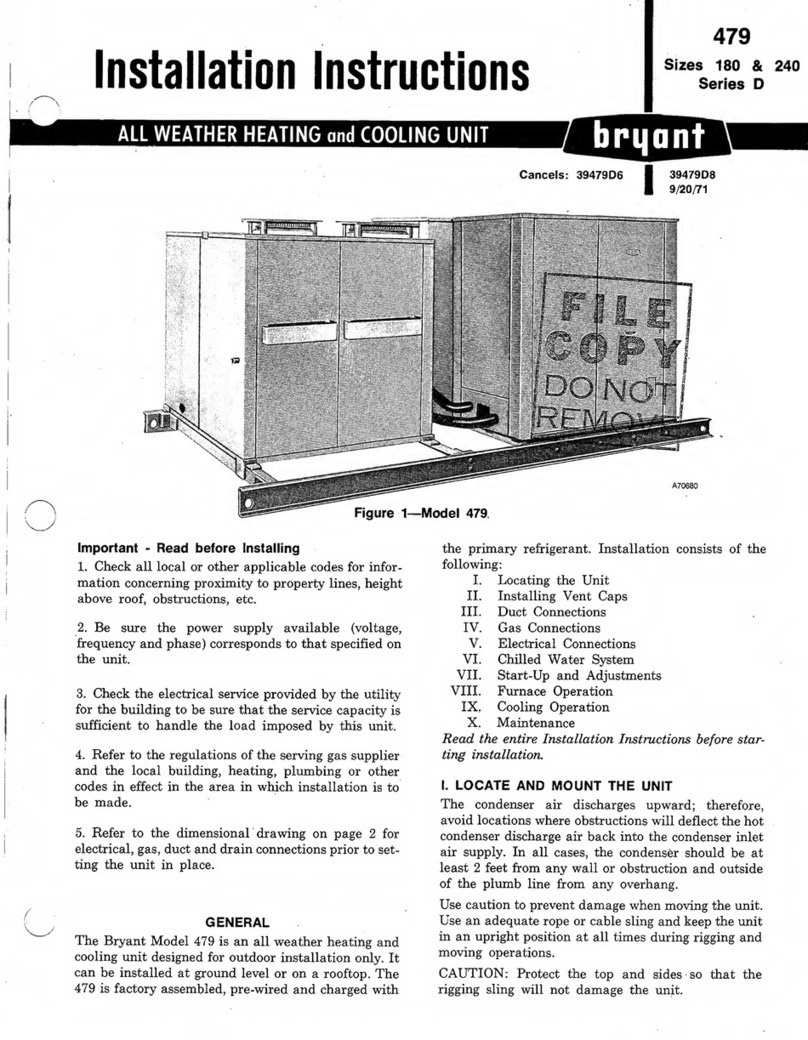
Bryant
Bryant 479 User manual
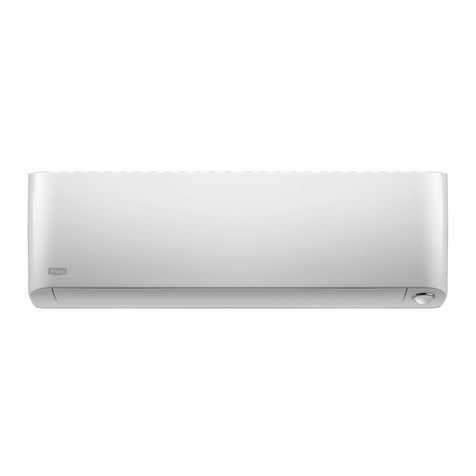
Bryant
Bryant 619PHA Series User manual

Bryant
Bryant Preferred 551J Installation and user guide
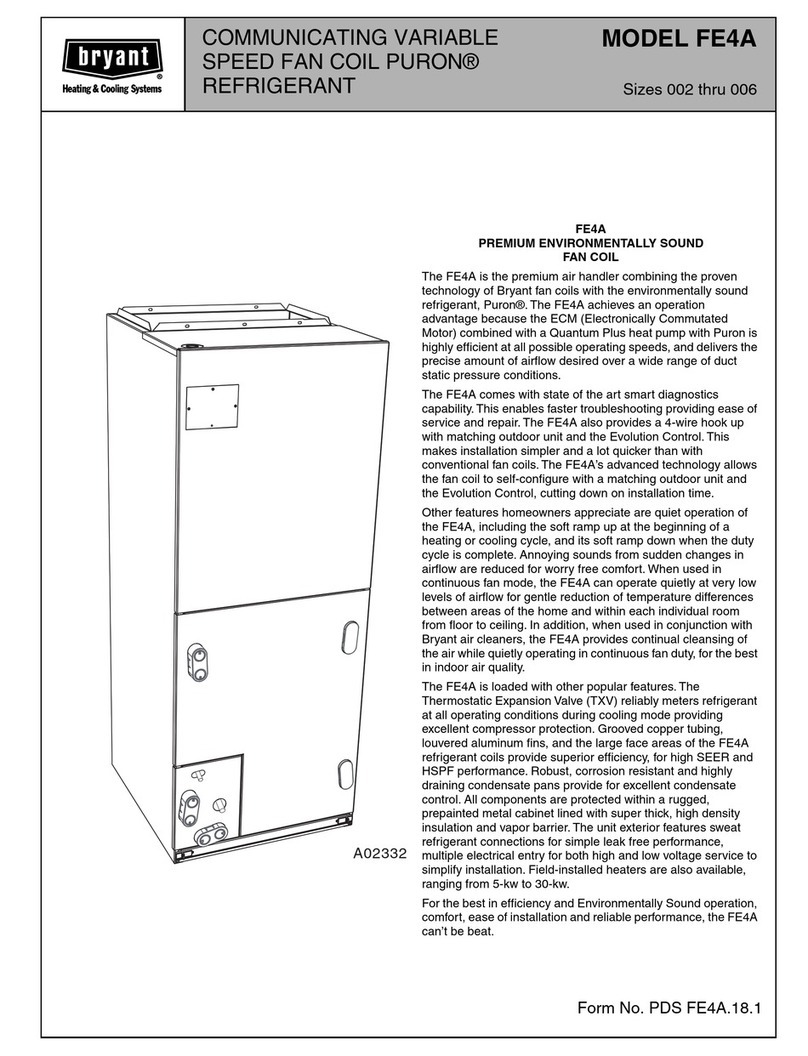
Bryant
Bryant fe4anf005 User manual
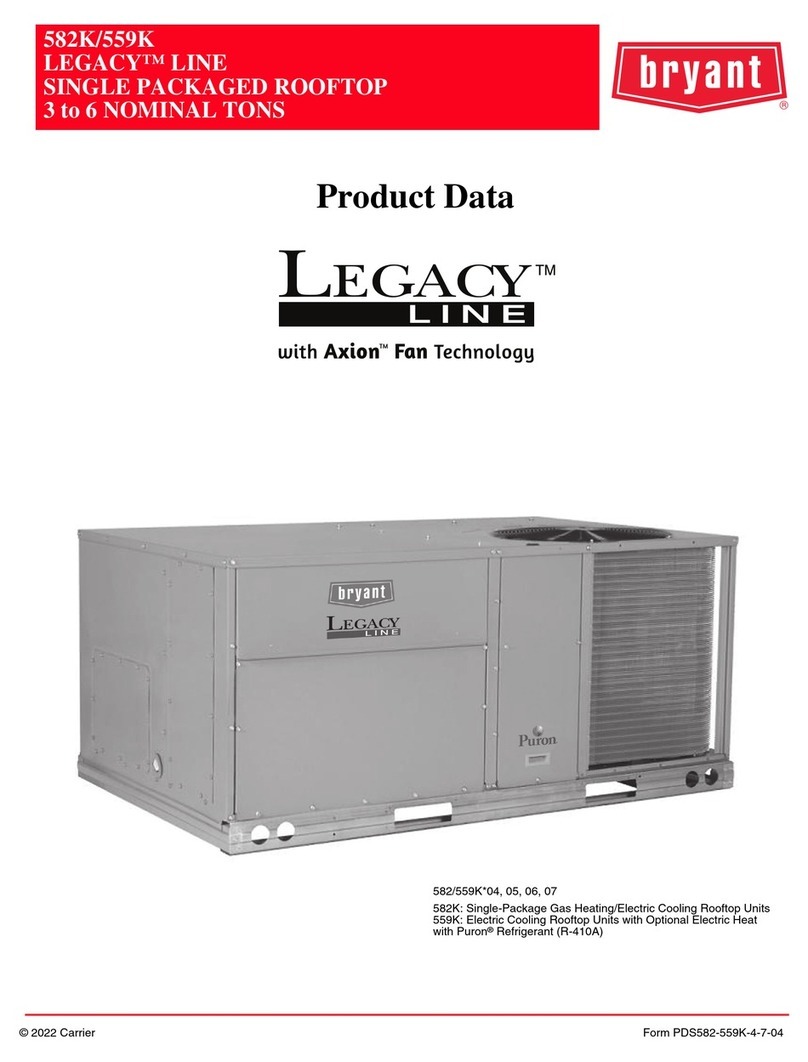
Bryant
Bryant 582K Operation manual
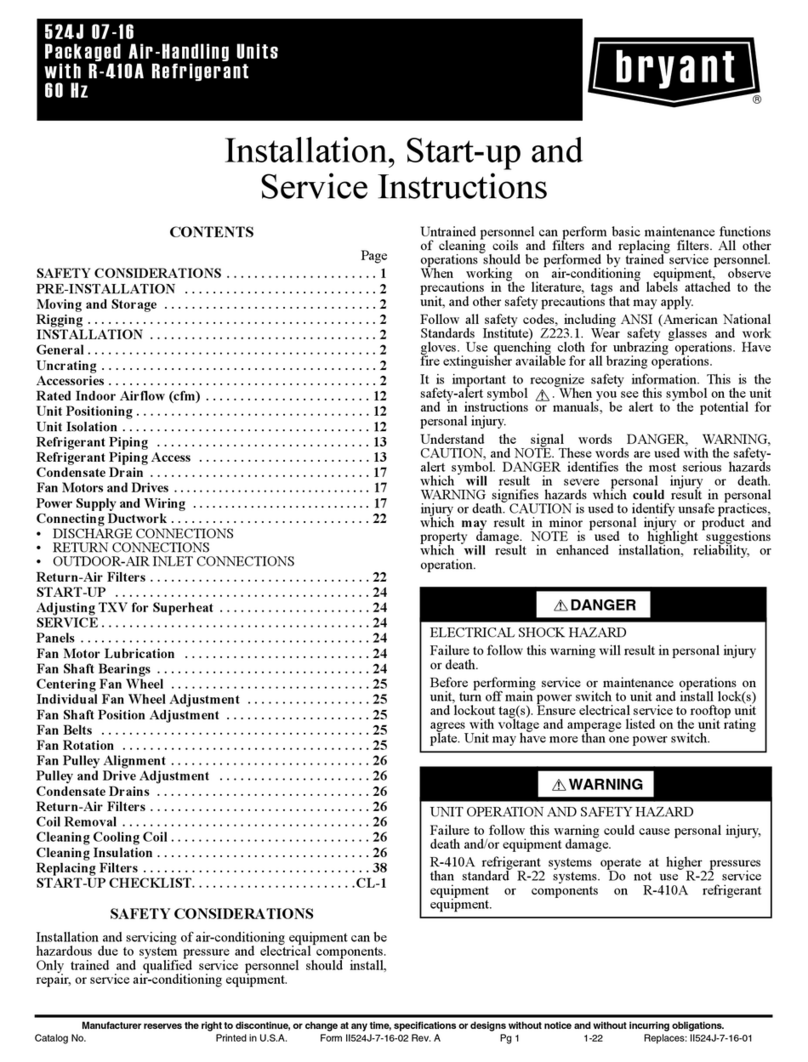
Bryant
Bryant 524J 07 Dimensions and installation guide