Burster 8655 User manual

OPERATION MANUAL
DIGIVISION
Torque
Manufacturer:
© 2023
burster
präzisionsmesstechnik gmbh & co kg
burster
präzisionsmesstechnik gmbh & co kg
All rights reserved
Talstrasse 1 - 5
Postfach 1432
76593 Gernsbach
Germany
76587 Gernsbach
Germany
Valid from:
September 14, 2023
Tel.: +49 7224 645-0
Fax: +49 7224 645-88
Email: info@burster.de
www.burster.de
4453-BADIGIVISIONDMDE-5999-111534

2of 39
Warranty disclaimer
All information in the present documentation was prepared and compiled with great care and reproduced
in accordance with effective control measures. No warranty is provided for freedom from errors. We
reserve the right to make technical changes. The present information as well as the corresponding
technical data can change without notice. Reproduction of any part of this documentation or its
processing or revision using electronic systems is prohibited without the manufacturer’s prior written
approval.
Components, devices and measurement sensors made by burster präzisionsmesstechnik (hereinafter
referred to as the “product”) are the result of targeted development and meticulous research. From the
date of delivery, burster provides a warranty for the proper condition and functioning of these products
covering material and production defects for the period specified in the warranty document accompanying
the product. However, burster waives any guarantee or warranty obligations or any additional liability for
consequential damages caused by improper use of the product, in particular the implied guarantee of
success in the market as well as the suitability of the product for a particular purpose. Furthermore,
burster assumes no liability for direct, indirect or incidental damages or for consequential or other
damages arising from the provision and use of the present documentation.

3of 39
Contents
1Symbols used in the operation manual ................................................................................... 5
1.1 Signal words................................................................................................................................. 5
1.2 Pictograms ................................................................................................................................... 5
2Introduction ................................................................................................................................ 6
2.1 Intended use ................................................................................................................................ 6
2.2 Customer service ......................................................................................................................... 6
2.2.1 Customer service department.......................................................................................... 6
2.2.2 Contact person ................................................................................................................ 6
3Non-rotating torque sensors, model 8625/8630/8631, USB version ..................................... 7
3.1 Electrical connection .................................................................................................................... 7
3.2 Power supply................................................................................................................................ 7
3.3 Connector pin-out......................................................................................................................... 8
3.4 Ground connection....................................................................................................................... 8
3.5 Running cables ............................................................................................................................ 9
4Rotating torque sensors, model 8655/8656/8661, USB version .......................................... 10
4.1 Electrical connection .................................................................................................................. 10
4.2 Power supply.............................................................................................................................. 11
4.3 Connector pin-out....................................................................................................................... 11
4.4 Ground connection..................................................................................................................... 11
4.5 Running cables .......................................................................................................................... 12
5DigiVision software.................................................................................................................. 13
5.1 Device list / Device detection ..................................................................................................... 13
5.2 Device settings........................................................................................................................... 13
5.3 Setup .......................................................................................................................................... 15
5.3.1 Setting up rotating sensors ............................................................................................ 15
5.3.2 Setting up non-rotating sensors..................................................................................... 16
5.4 Limits .......................................................................................................................................... 17
5.5 Properties ................................................................................................................................... 17
6Properties, measurement rate etc. ......................................................................................... 19
6.1 General settings ......................................................................................................................... 19
6.2 Measurement mode and data acquisition .................................................................................. 21
6.3 Measurement mode settings...................................................................................................... 22
6.4 Basic configuration..................................................................................................................... 23
6.5 Channel settings ........................................................................................................................ 24
6.6 Trigger ........................................................................................................................................ 24
6.6.1 Repeat measurement after time interval ....................................................................... 25
6.6.2 Start-trigger setting ........................................................................................................ 25

4of 39
6.6.3 Stop-trigger setting......................................................................................................... 25
6.6.4 Recording in a range...................................................................................................... 25
6.7 Documentation ........................................................................................................................... 25
6.8 Display........................................................................................................................................ 26
6.9 Start and stop measurement...................................................................................................... 28
6.10 Measurement reports ................................................................................................................. 29
6.10.1 Measurement report finder............................................................................................. 29
6.10.2 Archive viewer................................................................................................................ 31
6.10.3 Export measurement reports to Excel ........................................................................... 31
6.10.4 Print measurement reports ............................................................................................ 32
7Installing DigiVision ................................................................................................................. 35
7.1 System requirements ................................................................................................................. 35
7.2 Software installation ................................................................................................................... 35
7.3 Driver installation........................................................................................................................ 35
7.4 Virtual COM port installation ................................................. Fehler! Textmarke nicht definiert.
7.5 Data storage............................................................................................................................... 35
8Software version and licensing .............................................................................................. 37
8.1 DigiVision Light........................................................................................................................... 37
8.2 86xx-P100, Standard version..................................................................................................... 37
8.3 86xx-P200, Professional version................................................................................................ 37
8.4 Licensing .................................................................................................................................... 37
8.5 Uninstall...................................................................................................................................... 38
9Disposal .................................................................................................................................... 39

5of 39
1 Symbols used in the operation manual
1.1 Signal words
The following signal words are used in the operation manual according to the specified hazard
classification.
DANGER
High degree of risk: indicates a hazardous situation which, if not avoided, will result in death or
serious injury.
WARNING
Moderate degree of risk: indicates a hazardous situation which, if not avoided, may result in death or
serious injury.
CAUTION
Low degree of risk: indicates a hazardous situation which, if not avoided, could result in minor or
moderate injury.
NOTICE
Note: It is important to heed these safety notices in order to ensure correct handling of the sensors.
IMPORTANT: Follow the information given in the operation manual.
1.2 Pictograms
Electric shock hazard.
Observe the advice for protecting the instrument.

6of 39
2 Introduction
IMPORTANT: Read the operation manual carefully before using the equipment, and keep it for future
reference.
2.1 Intended use
The DigiVision software can be used to configure various burster sensors and devices, and to carry out
measurements. This operation manual relates exclusively to torque sensors. If using other sensors or
devices, please refer to the respective operation manual.
2.2 Customer service
2.2.1 Customer service department
If you have repair inquiries or software problems, please call our customer service department on
+49 7224 645-53.
2.2.2 Contact person
If you have any questions, please contact your representative or go directly to burster
präzisionsmesstechnik gmbh & co. kg.
Headquarters
burster präzisionsmesstechnik
gmbh & co kg
Talstrasse 1 - 5
76593 Gernsbach
Germany
Phone: +49 7224 645-0
Fax: +49 7224 645-88
Email: info@burster.de

7of 39
3 Non-rotating torque sensors, model
8625/8630/8631, USB version
3.1 Electrical connection
NOTICE
The USB socket is supplied with a protective dust cap fitted. Before putting the sensor
into use, this cap must be levered off, without damaging it. It is not meant to be cut off!
1. Take the cap off the USB socket.
2. Connect the torque sensor to a computer using the supplied USB cable.
3. Please be sure to follow the instructions in section 3.2 Power supply on page 7.
3.2 Power supply
The device draws 200 mA from the USB port. Usually this is not a problem for desktop PCs.
For laptops, however, several USB ports may share one power supply that is additionally loaded by other
connected USB devices (mouse etc.) Therefore, under some circumstances, the torque sensor may be
supplied with too little power and cannot register its presence. In this case, you need to connect the
torque sensor to the laptop via an active USB hub.

8of 39
3.3 Connector pin-out
The USB interface complies with the USB 2.0 standard and the pin assignment is as usual. The built-in
connector on the torque sensor is for a “Micro USB” plug.
Pin Name
Figure 1: Micro USB [mm]
1 +5 V
2 Data -
3 Data +
4 ID (not used)
5 GND
The connector fitted on the supplied cable is a “USB Type A” plug.
Pin Name
Figure 2: USB A [mm]
3.4 Ground connection
The common ground connection “Digital Ground GND” is shared by:
•USB plug casing
•Shield
•Sensor housing
•Protective ground

9of 39
Figure 3: Ground connection
3.5 Running cables
In general the following applies:
•The torque sensor must be grounded via its mounting screws.
•The USB cable length should not exceed 2 m. For longer cables it may be necessary to
connect an active USB hub in the cable link to avoid losing the USB connection.

10 of 39
4 Rotating torque sensors, model 8655/8656/8661,
USB version
4.1 Electrical connection
The USB socket is supplied with a protective dust cap fitted. Before putting the sensor into use, this cap
must be levered off with a suitable tool, without damaging it. It is not meant to be cut off!
1. Carefully prise off the protective cap using a pointed tool.
2. Take the cap off the USB socket.
3. Connect the torque sensor to a computer using the supplied USB cable.
4. Please be sure to follow the instructions in section 3.2 Power supply on page 7.
5. The torque sensor goes through a self-test mode lasting 4 seconds after power-up.
Once the self-test has finished, all the LEDs – if fitted – light up solidly for about 1 s.
Then the sensor is ready for operation.

11 of 39
4.2 Power supply
After the torque sensor is connected to the USB port, the sensor identifies itself as a “high power device”.
In this case, the device draws 495 mA from the USB port. Usually this is not a problem for desktop PCs.
For laptops, however, several USB ports may share one power supply that is additionally loaded by other
connected USB devices (mouse etc.) Therefore, under some circumstances, the torque sensor may be
supplied with too little power and cannot register its presence. In this case, you need to connect the
torque sensor to the laptop via an active USB hub.
Note: The actual power consumption is: P = 5 V * 0.35 A = 1.75 VA.
4.3 Connector pin-out
The USB interface complies with the USB 2.0 standard and the pin assignment is as usual. The built-in
connector on the torque sensor is a “USB Mini B” plug.
Pin Name
Figure 4: USB Mini B [mm]
1 +5 V
2 Data -
3 Data +
4 ID (not used)
5 GND
The connector fitted on the supplied cable is a “USB Type A” plug.
Pin Name
Figure 5: USB A [mm]
1 +5 V
2 Data -
3 Data +
4 GND
4.4 Ground connection
The common ground connection “Digital Ground GND” is shared by:
•USB plug casing
•Shield
•Sensor housing
•Protective ground

12 of 39
Figure 6: Ground connection
4.5 Running cables
In general the following applies:
•The torque sensor must be grounded via its mounting screws.
•The USB cable length should not exceed 2 m. For longer cables it may be necessary to
connect an active USB hub in the cable link to avoid losing the USB connection.

13 of 39
5 DigiVision software
5.1 Device list / Device detection
1. Open DigiVision.
2. Go to “File” > “Find devices…”.
3. As soon as the torque sensor has been detected, it is displayed under the associated
port.
5.2 Device settings
You can access the “Device settings” menu from the DigiVision device list.

14 of 39
1. Open the device list in DigiVision.
2. Select the torque sensor and click “Parameterization”.
3. You can now configure the sensor-specific settings.

15 of 39
5.3 Setup
5.3.1 Setting up rotating sensors
On the “Settings” tab, you can specify the units and conversion factors to be used for the relevant
measurement channels. Units suitable for the measured variable should be selected, otherwise errors
may occur when displaying the measured value and in its interpretation.
With “Number of Averages” you can set the number of individual measured values to be used to form an
arithmetic mean. The value can be set in the range N = 1 to N = 20. When N = 1, averaging is not
performed. In this case, the value at the output is refreshed every 10 µs. This corresponds to 100 000
digitizations per second. So if you select N = 20, for example, then a measuring time of 200 µs is needed
for a new value at the output (20 x 10 = 200 µs). The averaging has a direct effect on the measured
values per second. The higher the averaging value, the fewer measured values per second are possible.
If the torque sensor includes the speed/angle measurement option, you can switch between these two
measurement modes on this tab.
If the torque sensor is the optional dual-range version, you can also select the required measurement
range here. Applying the settings saves them in the sensor.
Figure 7: Settings for rotating sensors

16 of 39
5.3.2 Setting up non-rotating sensors
On the “Settings” tab, you can specify the units and conversion factors to be used for the relevant
measurement channels. It is important to select units that make sense and are suitable for the measured
variables, otherwise errors may occur when displaying the measured value.
With “Number of Averages” you can set the number of individual measured values to be used to form an
arithmetic mean. The value can be set in the range N = 1 to N = 50 000. When N = 1, averaging is not
performed. In this case, the voltage value at the output is refreshed every 10 µs. This corresponds to
100 000 digitizations per second. So if you select N = 50 000, for example, then a measuring time of
5 seconds is needed for a new voltage value at the output (50 000 x 10 = 0,5 s). The averaging has a
direct effect on the measured values per second. The higher the averaging value, the fewer measured
values per second are possible.
Disable the low-pass filter if you set a value N ≠ 1.
Filter settings: Set the averaging value to N = 1 if you select a cut-off frequency ≠ OFF.
The low-pass filter is a digital filter designed as a first-order low-pass filter.
Apart from the “OFF” setting, you can select various cut-off frequencies. The cut-off frequency is the
frequency at which the output signal is attenuated by -3 dB, corresponding to about 70.7 % of the signal
at very low frequencies.
If the torque sensor is the optional dual-range version, you can also select the required measurement
range here, or activate switching by a voltage level.
Applying the settings saves them in the sensor.
Figure 8: Settings for non-rotating sensors

17 of 39
5.4 Limits
The “Limits” tab is where you can set the sensor limits you require. Select the level for the limit, the
channel reference for this limit and whether you wish to monitor the measurement signal for ≥ or ≤.
Figure 9: Limits
5.5 Properties
The “Properties” tab contains information about the torque sensor being used. This is where you can find
the software version, device type, serial number, device option and calibration date. You can also add
comments for documentation purposes.

18 of 39
Figure 10: Properties

19 of 39
6 Properties, measurement rate etc.
You can use the “Properties” button to make additional general settings. For instance you can set the
measurement rate for the torque sensor here.
1. Open the device list in DigiVision.
2. Select the torque sensor and click “Properties”.
3. You can now configure additional general settings.
6.1 General settings
The “General information” tab contains general information about the torque sensor being used. You can
also enter a station name for the torque sensor, i.e. a name identifying the device.

20 of 39
Figure 11: General settings
Other manuals for 8655
1
This manual suits for next models
2
Table of contents
Popular Security Sensor manuals by other brands
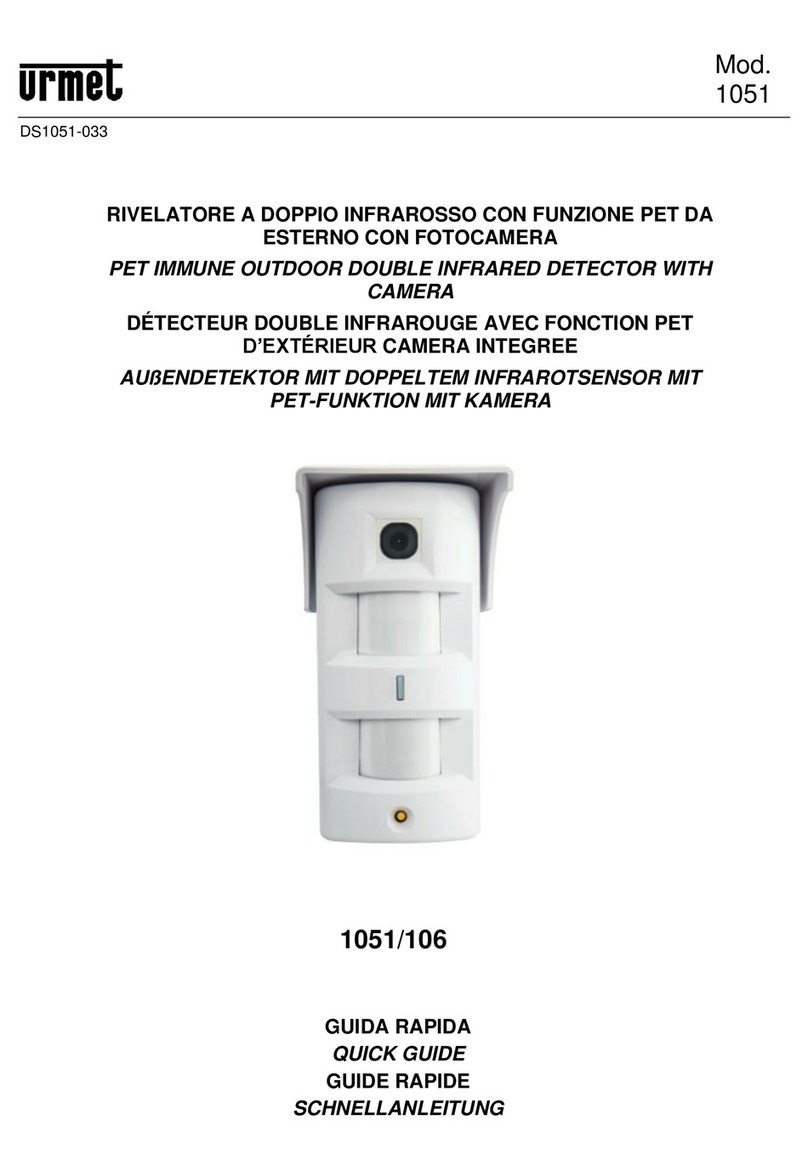
urmet domus
urmet domus 1051 quick guide
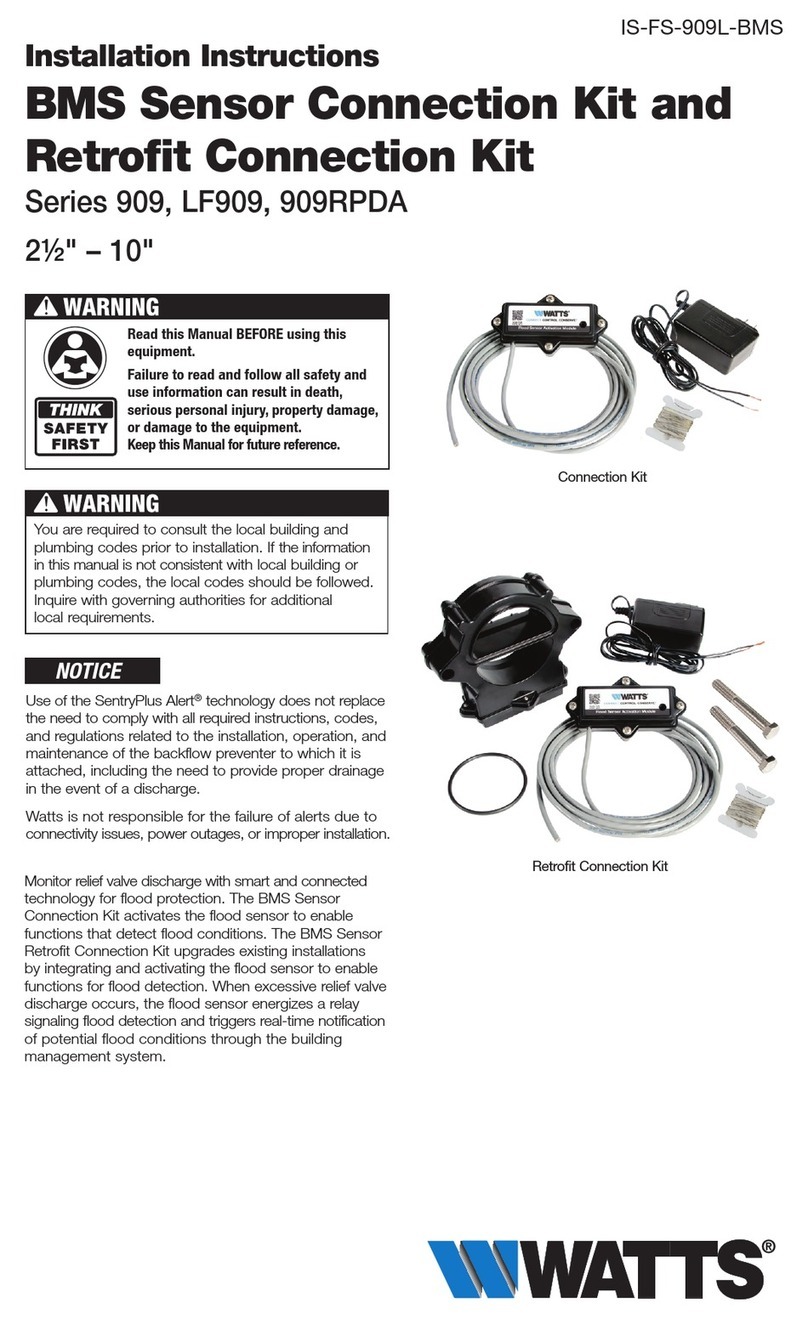
Watts
Watts 909 Series installation instructions
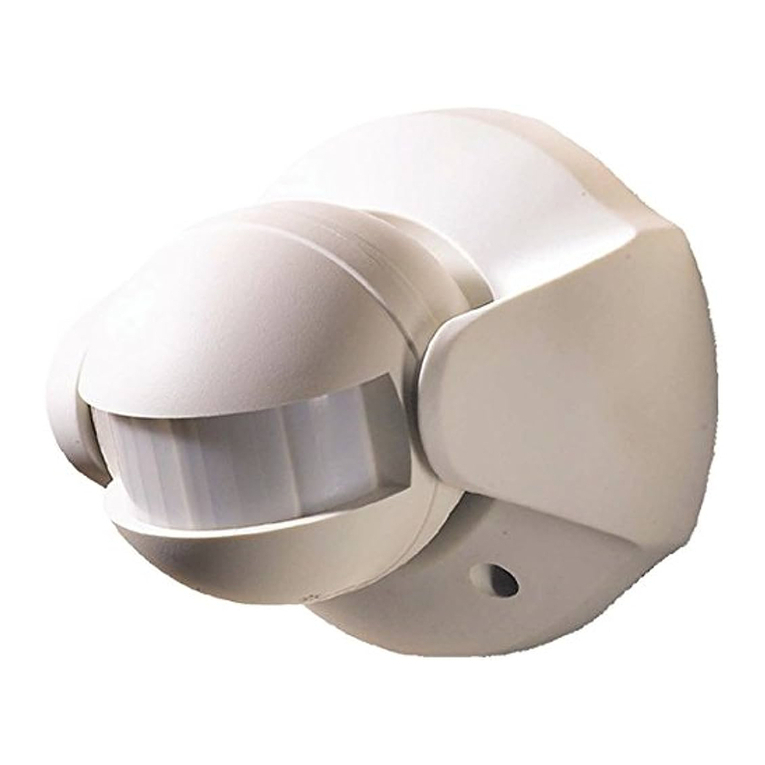
Titan
Titan TRS22TX quick start guide
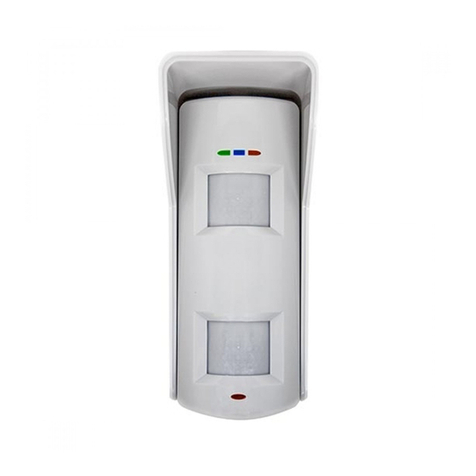
Pyronix
Pyronix XDH10TT-WE quick start guide
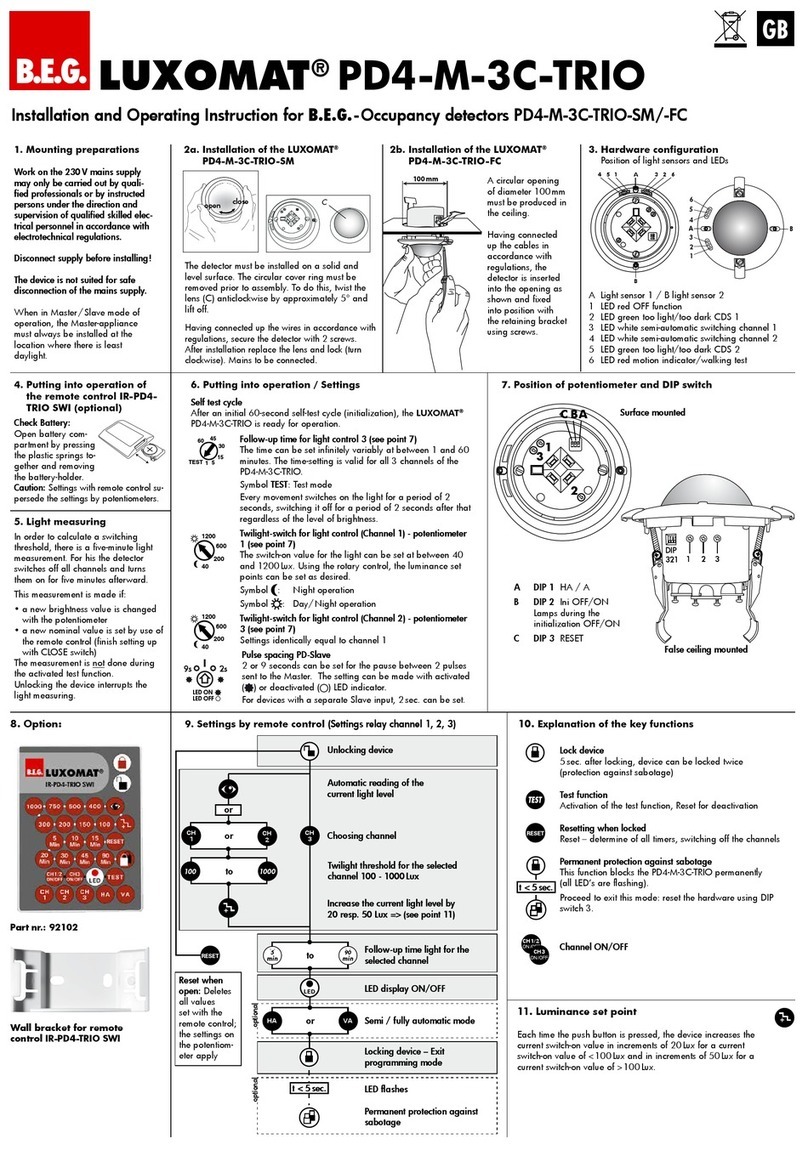
B.E.G.
B.E.G. LUXOMAT PD4-M-3C-TRIO Series Installation and operating instruction
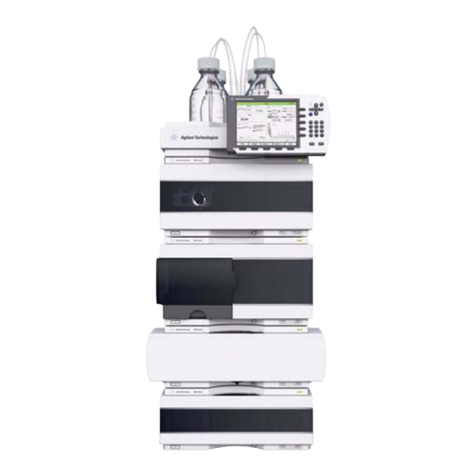
Agilent Technologies
Agilent Technologies 1200 Infinity Series user manual