Case 445CT Operating instructions

REPAIR MANUAL
WORKING ARM
435
445CT
445
39747 1 04/05/2005
H

WORKING ARM - H
SINGLE ARM Lift - 40.B
435
445CT
445
39750 1 04/05/2005
H.40.B / 1

Contents
WORKING ARM - H
SINGLE ARM Lift - 40.B
TECHNICAL DATA
Control valve
Control valve - General specification (H.40.B.13 - D.40.A.10)
435, 445
4
Control valve - General specification (H.40.B.13 - D.40.A.10)
445CT
4
Cylinder
Cylinder - Torque (H.40.B.26 - D.20.A.10)
435, 445, 445CT
5
Accumulator
Accumulator - General specification (H.40.B.30 - D.40.A.10)
435, 445, 445CT
6
Accumulator - Special tools (H.40.B.30 - D.20.A.40)
435, 445, 445CT
6
FUNCTIONAL DATA
Cylinder
Cylinder - Sectional view (H.40.B.26 - C.10.A.30)
435, 445, 445CT
7
SERVICE
SINGLE ARM Lift - Cleaning (H.40.B - F.30.A.10)
435, 445, 445CT
8
SINGLE ARM Lift - Decontaminating (H.40.B - F.30.A.60)
435, 445, 445CT
12
SINGLE ARM Lift - Remove (H.40.B - F.10.A.10)
435, 445, 445CT
14
SINGLE ARM Lift - Visual inspection (H.40.B - F.40.A.10)
435, 445, 445CT
18
SINGLE ARM Lift - Install (H.40.B - F.10.A.15)
435, 445, 445CT
21
Command
Command Lever - Adjust (H.40.B.05.05 - F.45.A.01)
435, 445, 445CT
25
Control valve
Control valve - Remove (H.40.B.13 - F.10.A.10)
435, 445, 445CT
27
Control valve - Install (H.40.B.13 - F.10.A.15)
435, 445, 445CT
29
Ride control valve
Ride control valve - Remove (H.40.B.14 - F.10.A.10)
435, 445, 445CT
31
Ride control valve - Install (H.40.B.14 - F.10.A.15)
435, 445, 445CT
33
Relief valve
39750 1 04/05/2005
H.40.B / 2

Relief valve - Pressure test (H.40.B.16 - F.40.A.30)
435, 445, 445CT
35
Relief valve - Flow test (H.40.B.16 - F.40.A.45)
435, 445, 445CT
36
Cylinder
Cylinder - Disassemble (H.40.B.26 - F.10.A.25)
435, 445, 445CT
37
Cylinder - Visual inspection (H.40.B.26 - F.40.A.10)
435, 445, 445CT
40
Cylinder - Assemble (H.40.B.26 - F.10.A.20)
435, 445, 445CT
42
Accumulator
Accumulator - Remove (H.40.B.30 - F.10.A.10)
435, 445, 445CT
44
Accumulator - Install (H.40.B.30 - F.10.A.15)
435, 445, 445CT
47
Accumulator - Charging (H.40.B.30 - F.60.A.30)
435, 445, 445CT
50
Accumulator - Depressurising (H.40.B.30 - F.35.A.51)
435, 445, 445CT
52
Accumulator - Disassemble (H.40.B.30 - F.10.A.25)
435, 445, 445CT
53
Accumulator - Visual inspection (H.40.B.30 - F.40.A.10)
435, 445, 445CT
54
Accumulator - Assemble (H.40.B.30 - F.10.A.20)
435, 445, 445CT
56
Accumulator - Pressure test (H.40.B.30 - F.40.A.30)
435, 445, 445CT
58
39750 1 04/05/2005
H.40.B / 3

WORKING ARM - SINGLE ARM Lift
Control valve - General specification (H.40.B.13 - D.40.A.10)
435, 445
Port Relief Valve Cartridge Pressures at 2.84 L/min (0.75 US gpm)
465 Machines
(Equipped with
Standard Auxiliary
Hydraulics.)
450 Machines and
465 Machines
(Equipped with
Electro - Hydraulic)
445 Machines 435 Machines
Port A1 None None None None
Port B1 23097 kPa (3350 psi) 23097 kPa (3350 psi) 23097 kPa (3350 psi) 23097 kPa (3350 psi)
Port A2 Shut-Off Plug 26200 kPa (3800 psi) Shut-Off Plug Shut-Off Plug
Port B2 Anti-Void 23097 kPa (3350 psi) Anti-Void Anti-Void
Control valve - General specification (H.40.B.13 - D.40.A.10)
445CT
Port Relief Valve Cartridge Pressures at 2.84 L/min (0.75 US gpm)
450CT Machines 445CT Machines
Port A1 26200 kPa (3800 psi) 26200 kPa (3800 psi)
Port B1 21734 kPa (3100 psi) 21734 kPa (3100 psi)
Port A2 26200 kPa (3800 psi) 26200 kPa (3800 psi)
Port B2 21734 kPa (3100 psi) 21734 kPa (3100 psi)
1 04/05/2005
H.40.B / 4

WORKING ARM - SINGLE ARM Lift
Cylinder - Torque (H.40.B.26 - D.20.A.10)
435, 445, 445CT
Piston Bolt Torque
Loader Lift Cylinder 365-460Nm(270 - 340 lb ft)
Packing Gland Torque
Loader Lift Cylinder 407 Nm ±68 Nm (300 lb ft ±50 lb ft)
1 04/05/2005
H.40.B / 5

WORKING ARM - SINGLE ARM Lift
Accumulator - General specification (H.40.B.30 - D.40.A.10)
435, 445, 445CT
Accumulator Charging Valve Cap Torque 10 lb in
Weight (Approximate) 3.73 kg (8.2 lb)
Fluid Capacity 740 L (45 in³)
Maximum Operating Pressure 20700 kPa (3000 psi)
Accumulator - Special tools (H.40.B.30 - D.20.A.40)
435, 445, 445CT
CAS10899-2 1
CAS10899 - Nitrogen Charging Kit
1 04/05/2005
H.40.B / 6

WORKING ARM - SINGLE ARM Lift
Cylinder - Sectional view (H.40.B.26 - C.10.A.30)
435, 445, 445CT
BT97F008 1
Cross Section View of Lift Cylinder
1. Tube 6. Seal 11. Wiper
2. Washer 7. Wear ring 12. Piston rod end
3. Bolt 8. Piston rod 13. O-ring
4. Piston 9. Backup seal 14. Packing gland
5. Backup ring 10. O-ring 15. Grease fitting
1 04/05/2005
H.40.B / 7

WORKING ARM - SINGLE ARM Lift
SINGLE ARM Lift - Cleaning (H.40.B - F.30.A.10)
435, 445, 445CT
1. Contamination in the hydraulic system is a major
cause of the malfunction of hydraulic components.
Contamination is any foreign material in the
hydraulic oil. Contamination can enter the hydraulic
system in several ways.
(A) When you drain the oil or disconnect any line.
(B) When you disassemble a component.
(C) From normal wear of the hydraulic components.
(D) From damaged or worn seals.
(E) From a damaged component in the hydraulic
system.
2. All hydraulic systems operate with some
contamination. The design of the components in
this hydraulic system permits efficient operation with
a small amount of contamination. An increase in
this amount of contamination can cause problems
in the hydraulic system. The following list includes
some of these problems.
(A) Cylinder rod seals leak.
(B) Control valve spools do not return to neutral.
(C) Movement of control valve spools is difficult.
(D) Hydraulic oil becomes too hot.
(E) Pump gears, housing, and other parts wear
rapidly.
(F) Relief valves or check valves held open by dirt.
(G) Quick failure of components that have been
repaired.
(H) Cycle times are slow; machine does not have
enough power.
3. If your machine has any of these problems, check
the hydraulic oil for contamination. See types of
contamination below. If you find contamination, use
the Portable Filter to clean the hydraulic system.
NOTE: There are two types of contamination, microscopic
and visible.
4. Microscopic contamination occurs when very fine
particles of foreign material are in suspension in the
hydraulic oil.
5. These particles are too small to see or feel.
Microscopic contamination can be found by
identification of the following problems or by testing
in a laboratory. Examples of the problems:
(A) Cylinder rod seal leak.
(B) Control valve spools do not return to NEUTRAL.
(C) The hydraulic system has a high operating
temperature.
1 04/05/2005
H.40.B / 8

WORKING ARM - SINGLE ARM Lift
6. Visible contamination is foreign material that can be
found by sight, touch, or odor. Visible contamination
can cause a sudden failure of components.
Examples of visible contamination:
(A) Particles of metal or dirt in the oil.
(B) Air in the oil.
(C) The oil is dark and thick.
(D)The oil has an odor of burned oil.
(E) Water in the oil.
NOTE: The hydrostatic system uses a third port bypass
filter system. If the filter becomes plugged it bypasses
back to the reservoir to stop contamination from entering
the hydrostatic system. Upon completion of cleaning the
hydraulic system replace the hydrostatic system filter.
NOTE: Use the following procedure for Cleaning the
Hydraulic System.
7. Prepare the portable filter CAS10162A by doing the
following steps:
(A) Remove all the hydraulic oil from the inlet and
outlet hoses for the portable filter.
(B) Remove the filter element from the portable filter.
(C) Remove all hydraulic oil from the portable filter.
(D) Clean the inside of the housing for the filter
element.
(E) Install a new filter element in the portable filter.
8. Determine whether the contamination is microscopic
or visible. Refer to: PRIMARY HYDRAULIC
POWER SYSTEM - Decontaminating (A.10.A -
F.30.A.60)
9. If the contamination is microscopic:
(A) Check the maintenance schedule for the
machine to learn if the hydraulic oil must be
changed. If necessary, change the hydraulic oil.
Change the hydraulic filter.
(B) Do steps 12 through 41.
10. If the contamination is visible, do the following steps:
(A) Change the hydraulic oil and hydraulic filter.
(B) Do steps 11 through 41.
11. Check the amount of contamination in the hydraulic
system by doing the following steps:
(A) Disassemble one cylinder in two different
circuits. Check for damage to seals, scoring of the
cylinder wall, etc. Repair the cylinders as necessary.
(B) If, in your judgment, the damage to the cylinders
was caused by sever contamination and is not the
result of normal wear, it is necessary to remove,
clean and repair all valves, pumps, lines, cylinders,
hydraulic reservoir, etc. in the hydraulic system.
To clean the lines refer to the following procedure:
TRANSMISSION Hydrostatic - Cleaning (C.20.F -
F.30.A.10)
12. Remove the cap from the reservoir and install
the CAS1871 adapter on the reservoir. Start the
vacuum pump.
13. Connect the CAS10192vacuum pump to the
adapter. Reservoir - Apply vacuum (A.10.A.22 -
F.35.A.50)
1 04/05/2005
H.40.B / 9

WORKING ARM - SINGLE ARM Lift
14. Start the vacuum pump.
15. The hydraulic reservoir is locate3d on the left rear
side of the machine. Loosen and remove the drain
plug from the reservoir.
16. Using the fitting kit CAS10508, install the valve in
the hole for the drain plug. Make sure that the valve
is closed.
17. Stop the vacuum pump.
18. Connect the inlet hose for the portable filter to the
valve that is installed in the hole for the drain plug.
19. Disconnect the vacuum pump.
20. Install the outlet hose for the portable filter in the
hydraulic reservoir filler neck.
21. Open the valve that is installed in the hole for the
drain plug.
22. Move the switch for the portable filter to the ON
position.
23. Start and run the engine at half throttle.
24. Run the portable filter for 10 minutes with the engine
running at half throttle.
25.Continue to run the portable filter. Increase the
engine speed to full throttle. Do the following to heat
the oil to operating temperature:
(A)Increase the engine speed to full throttle.
(B) Hold the bucket control lever in the ROLLBACK
position for five seconds.
(C)Return the blade control lever in the NEUTRAL
position for five seconds.
(D) Repeat steps 25B and 25C until the oil is at
operating temperature.
26. With the engine running at full throttle and the
portable filter running, completely extend and retract
the lift cylinders and the bucket cylinders. Continue
to operate the cylinders two times, one after the
other for 30 minutes
27. Decrease the engine speed to low idle.
28. Continue to run the portable filter for 10 minutes.
During this time, move the hose up and down to
help mix the oil in the reservoir.
29. Stop the portable filter
30. Stop the engine.
31. Remove the hose from the hydraulic reservoir.
32. Reservoir - Apply vacuum (A.10.A.22 - F.35.A.50)
33. Close the valve that is installed in the hole for the
drain plug.
34. Disconnect the inlet hose for the portable filter from
the valve.
35. Start the vacuum pump. .
36. Remove the valve from the hole for the drain plug.
37. Install and tighten the drain plug.
1 04/05/2005
H.40.B / 10

WORKING ARM - SINGLE ARM Lift
38. Stop the vacuum pump.
39. Disconnect the vacuum pump from the opening in
the reservoir.
40. Install new hydraulic and hydrostatic filter elements
on the machine.
41. Start the engine. Check for oil leakage around the
new hydraulic and hydrostatic filters.
42. Stop the engine.
43. Check the level of the oil in the reservoir and add
oil as required. Reservoir - Filling (A.10.A.22 -
F.60.A.10)
1 04/05/2005
H.40.B / 11

WORKING ARM - SINGLE ARM Lift
SINGLE ARM Lift - Decontaminating (H.40.B - F.30.A.60)
435, 445, 445CT
1. Start and run the engine at 1500 rpm (r/min).
2. Completely retract the cylinders of all attachments
on the machine. Angle the blade to the right, the
right cylinder will be fully retracted and the left will
be fully extended. Stop the engine.
WARNING
39-4 - If retracting the cylinder rods causes the
attachment to be raised, block the attachment in place
before proceeding to the next step.
3. Move each control lever in both directions to release
pressure in the hydraulic circuits.
4. Loosen and remove the filler cap from the reservoir.
5. Drain the hydraulic oil from the reservoir.
(A) Have available acceptable equipment to drain
the hydraulic oil.
(B) Remove the drain plug from the bottom of the
reservoir.
6. Remove the hydraulic and hydrostatic filter elements
from the machine.
7. Install new hydraulic and hydrostatic filter elements
on the machine.
8. Install the drain plug in the bottom of the reservoir.
9. Fill the hydraulic reservoir. Reservoir - Filling
(A.10.A.22 - F.60.A.10)
10. Disconnect the line from the OPEN end and
CLOSED end of each cylinder.
11. BesureallcontrolleversareintheNEUTRAL
position.
12. Start and run the engine at low idle.
IMPORTANT: Check the oil level in the hydraulic reservoir
frequently while doing step 13. Have another person hold
a container under the hydraulic lines while you do step 13.
13. Slowly move each control lever in both directions
until oil begins to flow from the open line. Hold the
control lever in place until clean oil flows from the
open line.
14. Stop the engine.
15. Connect the system line to the CLOSED end of
each cylinder.
16. Connect a suitable drain line to the OPEN end
of each cylinder and place the other end in an
acceptable container for contaminated oil.
17. Start the engine and run the engine at low idle.
1 04/05/2005
H.40.B / 12

WORKING ARM - SINGLE ARM Lift
18. Slowly and completely extend all cylinders. As the
piston rod comes in/out of the cylinder, oil will be
pushed out of the OPEN end of the cylinders.
IMPORTANT: Any attachment or part of an attachment
that is raised must be supported with acceptable
equipment to prevent the attachment from falling.
19. Support any attachments that will be in the RAISED
position.
20. Stop the engine.
21. Disconnect the drain lines and connect the system
lines to the cylinders.
22. Check the oil level in the hydraulic reservoir. Add
oil as required.
23. Install the filler cap on the reservoir.
24. Remove the hydraulic and hydrostatic filter elements
from the machine.
25. Install new hydraulic and hydrostatic filter elements
on the machine.
26. Start and run the engine at 1500 rpm (r/min),
operate each hydraulic circuit to completely extend
and retract the cylinders.
27. Stop the engine and check for leaks. Check the oil
level in the hydraulic reservoir. Add oil as required.
Reservoir - Filling (A.10.A.22 - F.60.A.10)
1 04/05/2005
H.40.B / 13

WORKING ARM - SINGLE ARM Lift
SINGLE ARM Lift - Remove (H.40.B - F.10.A.10)
435, 445, 445CT
1. Park the machine on a level surface.
2. Clean any dirt and grease from the hydraulic
connections for the bucket and lift cylinders. If the
machine is equipped with auxiliary hydraulic circuits
at the rear of the machine, clean any dirt and grease
from the hydraulic connections.
3. Raise the rear of the machine off the ground far
enough to remove the rear wheels.
4. Place the machine on acceptable stands.
5. Remove the rear wheels from the machine.
6. Attach acceptable lifting slings to the loader arms
on each side of the loader frame towards the rear
of the machine.
7. Remove the bolts (4 and 7), washers (5),special
nuts (6 and 8) and the step plate (3) from the tube
between the loader arms, refer to the illustration of
the Loader Frame.
8. Attach an acceptable lifting sling to the center of the
tube between the loader arms.
9. Attach the lifting slings to acceptable lifting
equipment.
10. Relieve any pressure from the hydraulic system
by moving the hydraulic bypass control lever to
the bypass position and moving the loader control
levers in both directions.
11. Raise the upper rear access door to gain access to
the hydraulic lines that operate the loader and the
auxiliary and high flow hydraulic systems.
12. Tags all hydraulic lines and couplings for use during
assembly procedure.
13. Loosen and remove all the hydraulic lines that pass
through both uprights of the chassis.
14. Plug and cap the fittings and coupling to minimize
the loss of hydraulic oil and to prevent contamination
from entering the hydraulic system.
15. Remove the retaining rings (if equipped) from the
hydraulic couplings on each side of the uprights and
push the hydraulic couplings into the center of the
uprights.
IMPORTANT: Be sure all of the hydraulic couplings are
out of the mounting holes in the chassis uprights before
attempting to remove the loader frame from the chassis.
16. Loosen and remove the grease fitting (18) from right
lift cylinder pivot pin (14), refer to the illustration of
Loader Frame.
17. Remove the bolt (16), washer (17),spacer(15),
pin (14) and bushing (20) from the right hand link
assembly (19). Use an acceptable support and
attach the lift cylinder to the loader frame.
1 04/05/2005
H.40.B / 14

WORKING ARM - SINGLE ARM Lift
18. Loosen and remove the grease fitting (18) from the
left lift cylinder pivot pin (14).
19. Remove the bolt (16), washer (17),spacer(15),
pin (14) and bushing (22) from the left hand link
assembly (21). Use an acceptable support and
attach the lift cylinder to the loader frame.
20. Remove the bolt (9), lock nuts (10),pin(8), bushings
(2) and spacer (3) from the right-hand side of the
loader H-frame arm assembly (1), refer to the
illustration of Loader H-Frame Arm Assembly.
21. Remove the bolt (9), lock nuts (10),pin(8), bushings
(2) and spacer (3) from the left-hand side of the
loader H-frame arm assembly (1).
22. Use the lifting equipment and remove the loader
frame from the chassis.
1 04/05/2005
H.40.B / 15

WORKING ARM - SINGLE ARM Lift
BT98D110 1
Loader Frame
1. Frame assembly 9. Bucket tilt cylinder 17. Washer 25. Bolt
2. Bushing 10. PIN 18. Grease fitting 26. Lock nut
3. Upper step plate 11. Bolt 19. RH link assembly 27. PIN
4. Bolt 12. Lock nut 20. Bushing 28. Bolt
5. Washer 13. Loader lift cylinder 21. LH link assembly 29. Lock nut
6. Special nut 14. PIN 22. Bushing
7. Bolt 15. Spacer 23. PIN
8. Special nut 16. Bolt 24. Grease fitting
1 04/05/2005
H.40.B / 16

WORKING ARM - SINGLE ARM Lift
bs04d136 2
Loader H-Frame Arm Assembly
1. Arm assembly 5. Bolt 9. Bolt
2. Bushing 6. Lock nut 10. Lock nut
3. Spacer 7. Grease fitting 11. Grease fitting
4. PIN 8. PIN
1 04/05/2005
H.40.B / 17

WORKING ARM - SINGLE ARM Lift
SINGLE ARM Lift - Visual inspection (H.40.B - F.40.A.10)
435, 445, 445CT
1. Inspect the loader frame (1) for cracks, corrosion,
and any other damage, refer to the illustration in
Figure 1. Use new parts as required.
2. Inspect the pins (14) removed from the loader lift
frame (1) for wear, cracks, corrosion, and any other
damage. Use new parts as required.
3. Inspect the loader lift pin bushings (20 and 22) and
spacers (15) for wear, cracks, corrosion, and any
other damage. Use new parts as required.
4. Inspect the loader H-frame arm assembly (1) for
cracks, corrosion, and any other damage, refer
to the illustration in Figure 2. Use new parts as
required.
5. Inspect the pins (8) removed from the loader
H-frame arm assembly (1) for wear, cracks,
corrosion, and any other damage. Use new parts
as required.
6. Inspect the loader H-frame arm assembly bushings
(2) and spacers (3) for wear, cracks, corrosion, and
any other damage. Use new parts as required.
1 04/05/2005
H.40.B / 18
Other manuals for 445CT
1
This manual suits for next models
2
Table of contents
Other Case Front End Loader manuals
Popular Front End Loader manuals by other brands
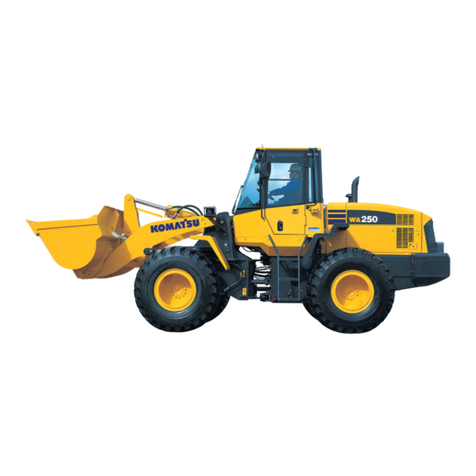
Komatsu
Komatsu WA250-3 Operation & maintenance manual
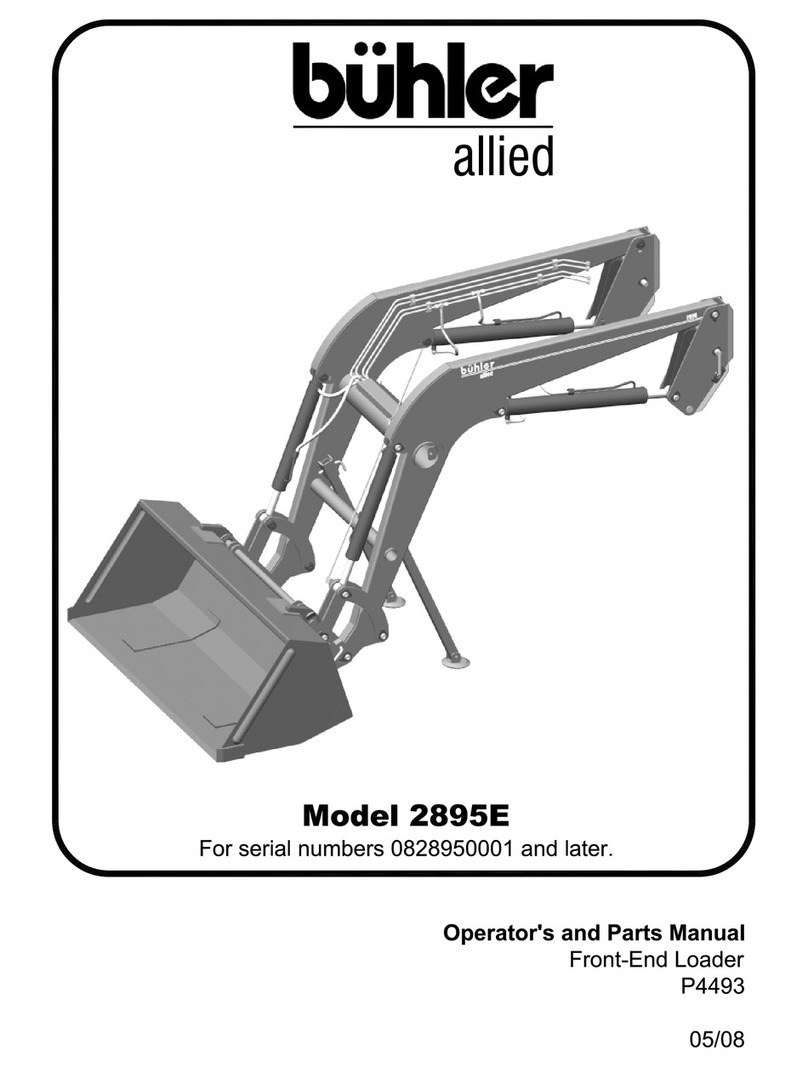
Buhler
Buhler 2895E Operator and parts manual
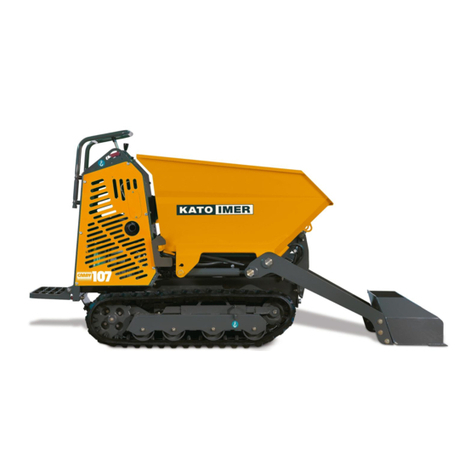
Kato Imer
Kato Imer CARRY 107 operating instructions
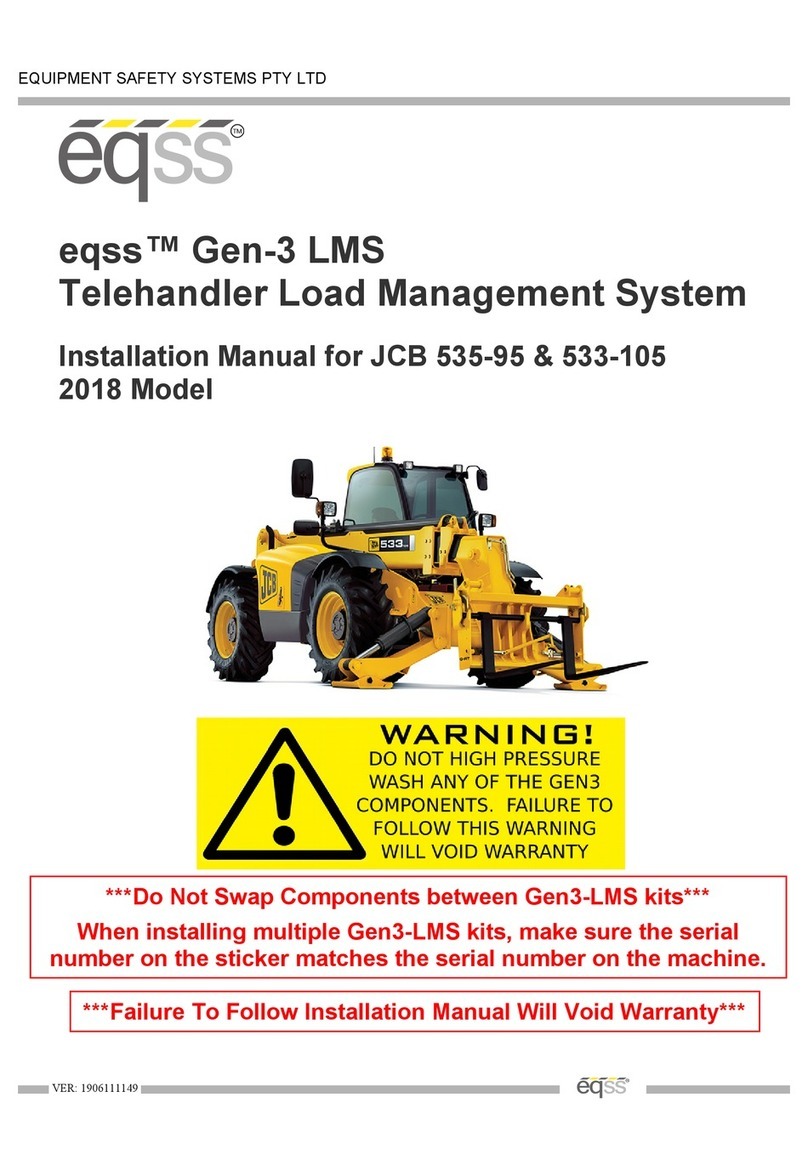
eqss
eqss Gen-3 LMS installation manual

Komatsu
Komatsu GALEO WA250PTL-5 Installation operation & maintenance

Ingersoll-Rand
Ingersoll-Rand BL-275 Service manual