Cattron Safe-E-Stop User manual

SAFE-E-STOP™
Personal Safety System
User Guide
9M02-8978-A001-EN

2
Version 17
Safe-E-Stop™
User Guide
Revision History
VERSION
DATE
NOTES
13
1/28/2018
Added cautions, updated Fault finding and simplified frequency selection
14
Dec 2018
Updated to include changes made in Safe-E-Stop Version 2 and changed part number
to 9M02-8978-A001 instead of 9M02-8681-A001
15
March 2019
Changed part numbering to reflect country code and added band J plus Black PSDs,
corrected Fig 14
16
05/2019
Document rebranded and contact and DOC information updated
17
7/2019
Added DOC link
Any information furnished by Cattron™ and its agents is believed to be accurate and reliable. All specifications are subject to change without notice.
Responsibilityfortheuseandapplication
ofCattronproductsrestswiththeendusersinceCattronanditsagentscannotbeawareofallpotentialuses.
Cattron makes no warranties as to non-infringement nor as to the fitness, merchantability, or sustainability of any Cattron products for any
specificorgeneral uses. Cattron Holdings, Inc., oranyofits affiliates oragentsshallnot beliableforincidental
or consequentialdamages of any
kind.AllCattronproductsaresold pursuanttotheTermsandConditionsofSale,a copyof whichwillbe furnisheduponrequest.Whenusedas atradename
herein, Cattron means Cattron Holdings, Inc. or one or more subsidiaries of Cattron Holdings, Inc. Cattron™, corresponding logos, and other
marks are trademarks or registered trademarksofCattronHoldings,Inc.Othermarksmaybethepropertyofthirdparties.Nothinghereinprovides
alicenseunderanyCattronoranythirdpartyintellectualpropertyright.

3
Version 17
Safe-E-Stop™
User Guide
Contents
1. Introduction 8
1.1 Terminology 8
2. Warnings and Cautions 9
2.1 MSD wiring 9
2.2 Verification of correct device 9
2.3 Verification of correct linking 9
2.4 Placement of PSD in charger 9
2.5 No serviceable parts 10
2.6 Regulatory Compliance 10
2.7 Awareness of PSD range and Hazards around the machine 10
2.8 The system may cause an unexpected stop of the machine 11
2.9 The safety analysis shall consider the reaction time of the system 11
2.10 Ethernet may not be used for safety-critical function 11
2.11 Frequency Change 11
2.12 Master Address Usage 11
2.13 General Safety Information 11
2.14 Intended Use 12
2.15 Improper Use 12
2.16 Equipment rating warning 13
2.17 Equipment Installation 13
2.18 Configuration Changes 13
3. Operating Principle 14
3.1 General 14
3.2 Radio Transmission 14
3.2.1 Continuous Transmission 14
3.2.2 Radio Interference 14
3.3 Telegram Security 15
3.3.1 System Address 15
3.3.2 CRC 15
3.3.3 Frame Counter 15
4. Frequency Selection 16
4.1 Rules for Frequency selection 16
4.2 Site Planning 17
5. PSD and MSD Configuration Parameters 18
5.1 PSD Configuration 18

4
Version 17
Safe-E-Stop™
User Guide
5.2 MSD Configuration 19
2.19 Configuration Part Number 20
PSD Configuration 20
MSD Configuration 20
6. PSD 21
6.1 PSD Overview 21
6.2 PSD Status Indications 21
6.2.1 PSD LEDs 22
6.2.1.1 PSD LCD 22
6.2.1.2 Radio signal level Monitoring 22
6.2.1.3 Battery Monitoring 22
6.2.1.4 General Status Monitoring 23
6.3 Joining an E-Stop Group 23
6.4 Normal Operation 26
6.4.1 Communication Loss 26
6.4.2 Communication Loss Recovery Stage 1 26
6.4.3 Communication Loss Recovery Stage 2 26
6.4.4 Issuing an E-Stop 26
6.4.5 Recovery of an E-Stop 27
6.5 Leaving an E-Stop Group 27
6.6 Switching OFF the PSD 27
6.7 Charging the Battery 27
6.7.1 Battery Capacity and Operating Life 27
6.8 PSD Belt Clip 28
7. Battery Chargers 30
7.1 General Information 30
7.2 Caution 30
7.3 Single Bay Charger 31
7.4 Six-Bay Charger 31
7.5 Battery Charger Status and Indicators 33
8. MSD 34
8.1 MSD Overview 34
8.2 MSD Connections 35
8.2.1 Single Channel Connections Example when using the COMM LOSS Relays 36
8.2.2 Single-Channel Connections Example when not using the COMM LOSS Relays 37
8.2.3 Dual-Channel Connections Example when not using the COMM LOSS Relays 38
8.2.4 Dual-Channel Connection Example using E-Stop relays and the COMM LOSS relays 39

5
Version 17
Safe-E-Stop™
User Guide
8.3 MSD Status Indicators 40
MSD LEDs 41
MSD LCD 41
8.4 MSD Operational States 41
8.5 MSD Information and Setup 42
8.6 MSD Ethernet Address Configuration 43
8.6.1 Ethernet Telegram Content 44
8.7 MSD Operation 44
8.8 MSD Installation 44
8.8.1 Safety Instructions for Installation 44
8.8.2 MSD Installation Notes on Enclosure 44
8.8.2.1 MSD Dimensions 45
8.8.2.2 Secondary Enclosure Option Kit (2OPT-8637-A102) Dimensions 46
8.8.3 General Rules for Mounting the MSD 47
8.8.4 MSD Connections 48
8.8.5 MSD Terminals 48
8.8.5.1 Terminal and Wire Specifications 48
8.8.6 Connecting the Antenna 49
9. System Commissioning 50
10. System Decommissioning 51
11. Parts Lists 52
11.1 Part Numbers 52
12. Maintenance 54
12.1 PSD Maintenance 54
12.2 MSD Maintenance 55
12.3 Spare MSD 55
Appendix A: PSD and MSD Configuration 56
A.1 General 56
A.2 Benefits of using the configuration tool 56
Master Address Change 56
A.3 Installing the Configuration Tool 57
A.4 Using the Configuration Tool 58
Appendix B: RF Channel Number vs Operating Frequency 68
Band B (433-434MHz) 68
Band B Channel Spacing Rules 68
Band D (450-470MHz) 68
Band D Channel Spacing Rules 68

6
Version 17
Safe-E-Stop™
User Guide
Band F (902-927MHz) 68
Band F Channel Spacing Rules 68
Band J (929MHz) 69
Band J Channel Spacing Rules 69
Appendix C: Approvals and Compliance Notifications 70
FCC Caution 70
EU Caution 70
Equipment Rating 70
Declaration of Conformity 70
Appendix D: Ethernet Configuration & Data Mapping 71
EtherNet/IP 71
Modbus TCP Configuration 74
PROFINET Configuration 76
Electronic Data Sheet (GSD File) 76
Appendix E: Troubleshooting 79
Communication Losses 79
Required Operating Range is Too Long 79
Bad Antenna or Coaxial Cable 79
RF Interference 79
MSD Radio is Faulty 79
PSD 80
Error Light is Flashing 80
Error 1 Shown on LCD 80
Error 2 Shown on LCD 80
Error 3 Shown on LCD 80
Battery Operating Time is Shorter than Expected 80
Cannot Link to MSD 80
MSD Not Seen 80
Operating Range is Short 81
MSD 81
Error Light is Flashing 81
No Power 81
Operating Range is Short 81
Cannot Reset Unit after a PSD Communication Loss 81
Battery Charger 81
Appendix F: Technical Data and Specifications PSD and MSD 82
Appendix G: Technical Data and Specifications Battery Charger 82

8
Version 17
Safe-E-Stop™
User Guide
1. Introduction
This manual provides guidance to installers and users of the Cattron Safe-E-Stop Personal Safety System.
1.1 Terminology
The following represent important acronyms and long form used in this document:
PSD
Personal Safety Device (the unit worn by a machine operator)
MSD
Machine Safety Device (the unit connected into the hard-wired E-Stop wiring and monitoring
systems)
PSS
Personal Safety System (the entire E-Stop System)
PLC
Programmable Logic Controller
MASTER-ADDRESS
The Primary address used by the system to ensure adjacent systems is unique and will not cross talk
SUB-ADDRESS
The appended address used to identify specific PSDs within a system
COMM LOSS
A loss of RF communication between PSD and MSD
LINKING
Associating a PSD with an MSD and placing into operation as an active E-Stop device
UNLINKING
Disassociating a PSD from an MSD and removing from an active E-Stop group
DIN
Deutsches Institut fur Normung, i.e. German Institute for Standardization.
PL
Performance Level
SIL
System Integrity Level
SC
Systematic Capability

9
Version 17
Safe-E-Stop™
User Guide
2. Warnings and Cautions
WARNING and CAUTION statements are strategically placed throughout all text prior to operating or
maintenance procedures, practices, or conditions considered essential to the protection of personnel or
equipment and property. Before starting any task, review and understand the WARNINGS or CAUTIONS included
in the text. All WARNINGS and CAUTIONS appearing in this manual are included below.
WARNING SYMBOL
Meaning: CAUTION
Function: Indicates that caution is necessary relative to the associated content and that the current information
must be followed in order to avoid undesirable consequences.
2.1 MSD wiring
WARNING
The MSD must be hard-wired in series with at least one E-Stop switch so that an E-Stop is still available when
no PSDs are connected.
Failure to comply with the above warning may result in serious injury or death to personnel and damage to
equipment.
2.2 Verification of correct device
WARNING
More than one PSD may be used in, around, or near your machine; therefore, before using any PSD, you must
ensure that the correct unit has been selected and that it matches the machine being protected.by checking the
configuration ID or other means of identification.
If the PSD is not associated with the machine you are using, it may still link to another MSD on an adjacent
machine and may not be providing the protection you are expecting and need.
Failure to comply with the above warnings may result in no protection being provided to stop your machine,
which in turn could result in loss of ability to stop an impending emergency situation and may lead to injury or
death.
2.3 Verification of correct linking
WARNING
After linking the PSD to the machine, there should be a means for the operator to verify the connection; several
methods can be used including color coding, numbering, or using the EtherNet connection with a PLC,
pressing the green button on the PSD, and ensuring the indicator (light or buzzer) on the machine confirms
your connection.
Failure to comply with the above may result in no protection being provided to stop your machine, which in turn
could result in loss of ability to stop an impending emergency situation and may lead to injury or death.
2.4 Placement of PSD in charger
WARNING

10
Version 17
Safe-E-Stop™
User Guide
Unlinked PSDs should not be visible to personnel in the area and potentially confused for an available E-Stop
switch. If PSDs in chargers are unlinked, they should not be visible. The easiest way to do this is to place the
charger within a secondary enclosure or position it so that the E-Stop switch faces toward a wall and away from
personnel.
Failure to comply with the above may result in no immediate available protection being provided to stop your
machine, which in turn could result in loss of ability to stop an impending emergency situation and may lead to
injury or death.
2.5 No serviceable parts
WARNING
There are no user serviceable parts in this PSD / MSD system; please return damaged units to Cattron or a
Cattron authorized service center for service and do not attempt to repair these units.
Unauthorized repairs will void the unit’s safety rating and could compromise the unit’s ability to stop your
machine, which in turn could result in loss of ability to stop an impending emergency situation and may lead to
injury or death.
2.6 Regulatory Compliance
WARNING
Observe the statutory regulations and directives applicable for the intended purpose, e.g.:
▪Accident prevention regulations
▪Safety rules and directives
▪Standards
▪Generally applicable statutory and other binding regulations for accident prevention and environmental
protection, and general safety and health requirements.
2.7 Awareness of PSD range and Hazards around the machine
WARNING
The operators and the personnel in general should be trained to know the operational range limits of the PSD
and the surrounding hazards.

11
Version 17
Safe-E-Stop™
User Guide
2.8 The system may cause an unexpected stop of the machine
WARNING
The design of the machine shall consider the risk associated with an unexpected stop of the machine.
2.9 The safety analysis shall consider the reaction time of the system
WARNING
The safety analysis of the application shall consider the reaction time of the system.
2.10 Ethernet may not be used for safety-critical function
WARNING
Ethernet data must only be used for informational purposes. The functionality of the green PSD button that is
available in the Ethernet data should not be used for any safety-critical functionality such as restarting the
machine.
2.11 Frequency Change
WARNING
Selection of the correct operating frequency is entirely the responsibility of the user and Cattron accepts no
responsibility for incorrect frequency selection and configuration.
The frequency selected must strictly conform to channel setting rules shown in section 4 of this manual or the
system may not function correctly.
For licensed frequencies the channel set must also have a valid FCC, IC, or other license, or the user may be
subject to Federal license infringement fines.
Verify correct system operation prior to putting the system into use.
2.12 Master Address Usage
WARNING
Users should ensure that when a system includes one or more spare MSDs, that only one is powered on at a
time or the system will not operate without errors.
All users must ensure that only one Master Address is used in one location, i.e. do not use one MSD and some
associated PSDs in one location and a spare MSD, plus other associated PSDs in another location.
Authorized users must ensure the above is adhered to by associating only one Master Address per user
location.
Verify correct system operation prior to putting the system into use.
2.13 General Safety Information
▪Persons under the influence of drugs, alcohol and/or other medicine that impairs reaction may not install,
repair, or operate this product.

12
Version 17
Safe-E-Stop™
User Guide
▪All installations must conform to the relevant safety requirements. Only qualified, trained, authorized
personnel may perform work on the equipment, in accordance with the relevant safety requirements.
▪In the event of malfunction and/or visible defects or irregularities, the operation must be protected by other
PSDs or alternate external means. The PSD/MSD system must be returned to good working order before
being returned once more to operational service.
▪The operating manual should be permanently accessible at the place of product use.
▪Personnel assigned to work with the product must have read and understood the operating manual and the
safety instructions.
▪The safety instructions should be supplemented with work instructions concerning the job organization, work
sequences, qualified personnel, etc.
▪All repairs made during the warranty period must be carried out by the manufacturer or appointed authorized
service center. Failure to comply will invalidate the warranty.
▪Only trained personnel may perform maintenance and repair on the product.
▪All repairs made by these authorized agents should be carried out in a suitably clean, static-safe
environment, free from contaminants such as metal filings, water, oil, etc.
▪It is the user’s responsibility to ensure that the product is maintained in good condition and that all applicable
safety requirements and regulations are observed.
▪Product modifications may not be carried out.
▪Only original spare units from Cattron must be used.
▪Periodical inspections either required by law or prescribed in this user manual shall be carried out within the
prescribed intervals.
2.14 Intended Use
Only use the product in good condition, by trained personnel, and subject to the compliance with the applicable
operating safety and accident prevention rules and regulations.
2.15 Improper Use
Certain use and work on/with the product are not permitted, in particular:
▪Deviating from the voltage / frequency data on the type plate
▪Working on live components
▪Insufficient maintenance
▪Failure to observe the operating temperature range

13
Version 17
Safe-E-Stop™
User Guide
2.16 Equipment rating warning
CAUTION
Damage of the device
The PSD is rated at IP67 and an operating temperature range of -20°C to +60°C; do not use the PSD for
conditions beyond these limits.
The PSD battery cannot be charged if its temperature exceeds 40°C.
The MSD is rated at IP30 and a temperature range of -20°C to +60°C, up to 90% non-condensing RH; for
environments harsher than this, use an appropriate secondary enclosure.
Exceeding these ratings could compromise the unit’s ability to stop your machine, which in turn could result in
loss of ability to stop an impending emergency situation and may lead to injury or death.
2.17 Equipment Installation
CAUTION
The choice of connection will be determined by the safety level required for the target application and machine.
To achieve SIL3 capable safety levels, a dual channel connection approach will be required and is
recommended, but single channels are optional for lower safety levels and are also illustrated.
Additionally, it must be remembered that the Ethernet port is not safety-critical, only informational, therefore the
functionality of the green button on the PSD should not be used for safety-critical functionality such as
restarting the machine.
Use of the green button for safety-critical functions could result in unexpected actuation of function and may
lead to injury or death.
2.18 Configuration Changes
WARNING
Users should ensure that whenever a configuration change is made or an additional PSD or MSD is configured
for a system, that the system is tested thoroughly for correct operation before being put into operation.

14
Version 17
Safe-E-Stop™
User Guide
3. Operating Principle
3.1 General
The MSD has two safety relays that are wired in series with an external hard-wired E-Stop circuit that provides a
machine with the ability to run. The MSD safety relays are changeover types that are held energized in normal
(non-e-stop/run) operation. If the MSD power were removed, the relays would revert to their unpowered state and
the machine would be brought to a halt as though an E-Stop had been pressed.
The MSD is a complex safety PLC. In the event of any fault it will de-energize its safety relays; in its normal
operating mode, it will maintain these safety relays in an energized state.
A normal operating mode can be maintained in the absence of any online PSD, as well as with one or more PSDs
in a linked and normal operating state.
PSDs can come and go as required without affecting the MSD E-Stop safety relays, provided that the PSDs join
and leave the system by the deliberate act and process of linking and leaving the active group. (Patent Pending)
When a PSD is part of the active group, it will trigger an E-Stop if it has its E-Stop switch pressed or if it loses the
RF link to the MSD either because a) it goes out of range, b) it shuts down due to low battery, c) it has a fault, or
d) it has its RF link blocked by interference.
Both the MSD and PSDs feature fully redundant hardware and safety-critical software. They individually and
jointly meet the safety level of SIL3 according to ISO61508.
The MSD polls the PSDs in turn and assigns a PSD an active slot if one is available. The linked PSDs return the
poll after each MSD poll, forming a closed loop safety system.
3.2 Radio Transmission
The connection between the MSD and PSDs is performed by means of radio communication. With regard to the
actual radio frequency that is used, there are several radio frequency bands available.
A specific RF frequency band and channel is selected prior to delivery of the system.
Depending on the frequency band, a defined number of RF channels are available.
The MSD and PSDs must operate on the same RF channel in order to be able to communicate.
Some systems use two RF channels in a frequency diversity mode to increase immunity to RF interference.
3.2.1 Continuous Transmission
Once the units are linked, transmission between MSD and PSD must be continuous. The MSD uses this as part
of the information required to maintain its E-Stop safety relays in a closed state. If the MSD does not receive a
valid telegram from a linked PSD after a short time, it turns off the E-Stop safety relays.
In order to ensure optimum communication between the MSD and PSD, operate the PSD with line-of-sight to the
MSD antenna as far as possible. Avoid total shielding of the signal path by extensive metal and other thick solid
obstructions.
3.2.2 Radio Interference
Signals from other RF-emitting sources might interfere with the radio communication between the MSD and PSD.
If the radio link reliability is affected by interference, changing the RF channel or even the RF band may be
necessary.

15
Version 17
Safe-E-Stop™
User Guide
3.3 Telegram Security
The transmitted telegram contains several security features.
3.3.1 System Address
Your Personal Safety System uses 32,768 unique Master Addresses, and 15 Sub Addresses per MSD (one per
each possible associated PSD).
This system address is contained in every telegram sent between the MSD and PSD. The data is considered
valid only when the address combination matches. This is a safety measure to ensure that the MSD will act only
upon its assigned PSDs.
3.3.2 CRC
The telegram is checked for integrity by the use of a 16-bit CRC. Frames containing a mismatched CRC will be
rejected.
3.3.3 Frame Counter
Each message has an embedded frame counter that changes with every data frame. This prevents frozen data
and data frame hacking.

16
Version 17
Safe-E-Stop™
User Guide
4. Frequency Selection
Reliable operation of the Safe-E-Stop system is dependent on the correct selection of one or more interference
free RF channels; inappropriate selection may lead to unexpected machine shut down. The Safe-E-Stop system
operating frequency is user configurable using a factory supplied program that can be run on a PC.
Depending on your region there may be licensed channels and/or license exempt channels available:
▪Licensed channels provide the greatest level of signal reliability because issuance of channels is regulated
and controlled within the geographic region. When using licensed frequencies, it is absolutely critical that
only the RF channel assigned by your operating license be selected or you will be in violation of your Federal
licensing agreement and could be subject to Federally defined penalties.
▪License-exempt channels are not regulated and hence the user needs to monitor and control frequencies in
use in their facility to prevent duplication within a building; there may also be other users off site but close by,
and these may be sources of interference; however, operation within a steel clad building will provide a high
level of isolation from these external sources. In an open site, however, you may be better off using licensed
channels.
It is the user’s responsibility to maintain a frequency plan to ensure interference free operation of the Safe-E-Stop
and other RF equipment on site. Selection of an appropriate operating frequency requires both knowledge of RF
channels in use and the application of the rules set out below.
Table 1: Frequency Spacing by RF band
BAND
START FREQ HZ
END FREQ
HZ
CH SPACING KHZ
START CHANNEL
END CHANNEL
CH,
SPACING
A
418,000,000
B
433,077,500
434,777,500
25
A00
A68
2 (50kHz)
C
447,000,000
D
450,000,000
470,000,000
12.5
A00
Q00
4 (50kHz)
E
868,000,000
F
902,600,000
927,500,000
100
A00
C49
2 (200kHz)
Table 1 defines the six operating bands; currently Cattron has only released the B, D, and F bands.
▪In North America, the D band is licensed and the F band is license exempt.
▪Europe and many other regions including Brazil use the license exempt band B.
4.1 Rules for Frequency selection
1. A channel can be any frequency between the Start Freq. and the End Freq. that is wholly divisible by the
CH Spacing.
−Example: Band D channel 6 is 450,000,000 + (6*12,500) = 450,750,000.
And for any given frequency;
2. If any other systems (including other Safe-E-Stop systems) are operating within 10m of the location that
the Safe-E-Stop will be used, then a frequency that is at least as far away as is shown in the ‘CH
SPACING Separation’ column should be chosen.
−Example: If another system is operating on 450,700,000 required minimum separation, Table 1 is
50kHz so 450,700,000 –50,000 = 450,650,000 and 450,700,000 + 50,000 is 450,750,000. Both of
these are within the Band Start and Band End frequencies. Make sure it is a valid channel according
to rule 1 above.
3. Finally, make sure the derived frequency is not in the table below.

17
Version 17
Safe-E-Stop™
User Guide
Table 2: Frequencies That Are Not Supported
AVOID FREQUENCIES
Band B
Band D
Band F
434,177,500
466,937,500
902,600,000
912,100,000
921,600,000
902,700,000
912,200,000
921,700,000
902,800,000
912,300,000
921,800,000
902,900,000
921,100,000
921,900,000
911,700,000
921,200,000
922,000,000
911,800,000
921,300,000
922,100,000
911,900,000
921,400,000
912,000,000
921,500,000
Cattron can supply support and help with frequency selection if they are provided with a list of frequencies in use
in the immediate operating location.
4.2 Site Planning
As far as is practical, RF systems frequency separation should at least be as shown in the last column of the
table below.
Table 3: Channel Spacing for Adjacent Systems
BAND
START FREQ HZ
END FREQ
HZ
CH SPACING KHZ
START CHANNEL
END CHANNEL
CH,
SPACING
A
418,000,000
B
433,077,500
434,777,500
25
A00
A68
2 (50kHz)
C
447,000,000
D
450,000,000
470,000,000
12.5
A00
Q00
4 (50kHz)
E
868,000,000
F
902,600,000
927,500,000
100
A00
C49
2 (200kHz)
NB: channels are identified on the equipment by a three-digit identity xnn; see columns 5 and 6 above.
Channels run A00 through A99, and then B00 through B99 and so on until the End Channel is reached.
For the purposes of adjacent system channel spacing we can use the figure in the final column.
This somewhat simplifies the method of determining what channels should be chosen on a site.
When all available channels have been used with the designated channel spacing (not likely with 450MHz or
915MHz band), we can start using intermediate frequencies (one channel apart) provided that they are 100m
away from the systems one channel away.

18
Version 17
Safe-E-Stop™
User Guide
5. PSD and MSD Configuration Parameters
5.1 PSD Configuration
Your PSD has been manufactured to operate in a specific RF band, and has been built in a specific color housing.
●Within that band all users can configure the specific RF channel.
●Authorized users can set the System’s master address and the PSD’s specific sub-address.
●Various housing colors are available as options but red is standard.
Each PSDs configuration is identified on the unit’s LCD screen.
A system of one MSD and one or more PSDs must have a correct set of configuration parameters to be able to
operate. Most of the configuration details must match exactly; only the Sub-Address must be different between
PSDs.
In summary:
▪A PSD and MSD have one matching Master Address and each PSD has a different Sub-Address.
▪Both PSDs and MSD have one unique frequency and master address.
Figure 1: Red PSD
The PSD will show the frequency configuration on the LCD when first turned on.
As an additional aid to visual identification and differentiation, the following is available as an option:
▪A sheet of labels of various colors of Cattron logo as a user installation item.

19
Version 17
Safe-E-Stop™
User Guide
5.2 MSD Configuration
Your MSD has been manufactured to operate in a specific RF band and is fitted with a specific Ethernet option.
●Within that band all users can configure the specific RF channel.
●Authorized users can set the System master address.
●Ethernet options are None, EtherNet/IP or PROFINET
Each MSD’s configuration is identified on the unit’s LCD screen.
A system of one MSD and one or more PSDs must have a correct set of configuration parameters to be able to
operate. Most of the configuration details must match exactly; only the Sub-Address must be different between
PSDs.
In summary:
▪A PSD and MSD have one matching Master Address and each PSD has a different Sub-Address.
▪Both PSDs and MSD have one unique frequency and master address.
Figure 2: MSD
The MSD will show its configuration on the LCD when first turned on. The configuration can also be displayed by
scrolling down using the selection arrows.

20
Version 17
Safe-E-Stop™
User Guide
Table 4: Frequency Bands
BAND
FREQ MHZ
TYPICALLY USED IN
A
418
China
B
433
EU & Other
C
447
EU Licensed
D
450
NA and Other Licensed
E
869
EU
F
915
NA
J
429
Japan
2.19 Configuration Part Number
PSD Configuration
PSD-2-X-Y
Where 2 is the current version
Where X is the RF Band
Where Y is the color, R / G / Y / B / K (Red / Green / Yellow / Blue/ Black)
MSD Configuration
MSD-2-X-Y
Where 2 is the current version
Where X is the RF Band
Where Y is the Ethernet option, X, E, P (Excluded / EtherNet/IP / PROFINET)
Table 5: Examples of Configuration Number Use
SELLING PART #
DESCRIPTION
PSD-2-F-R
MSD-2-B-P
PSD version 2, 915MHz RF band, Red Body
MSD version 2, 433MHz RF band, PROFINET bus
Table of contents
Popular Security Sensor manuals by other brands
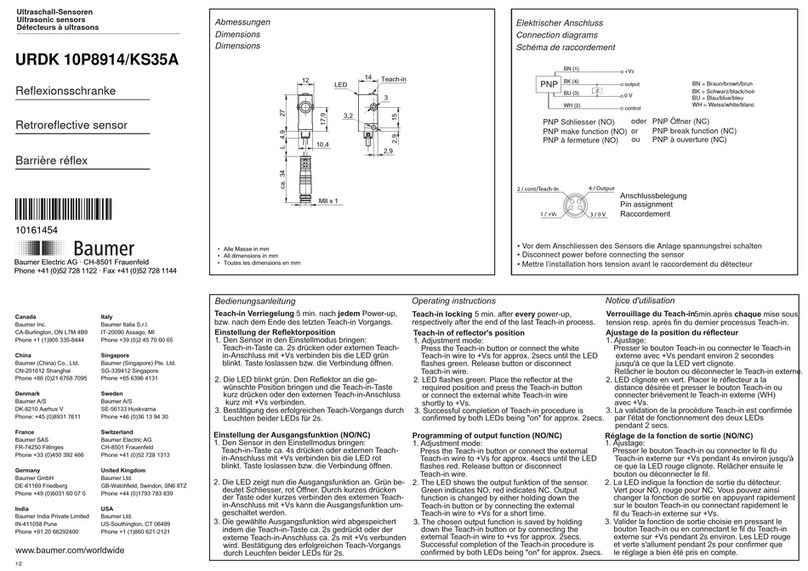
Baumer
Baumer URDK 10P8914/KS35A quick start guide
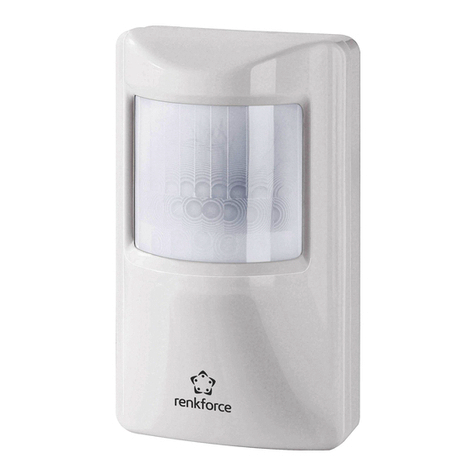
Renkforce
Renkforce 751560 operating instructions
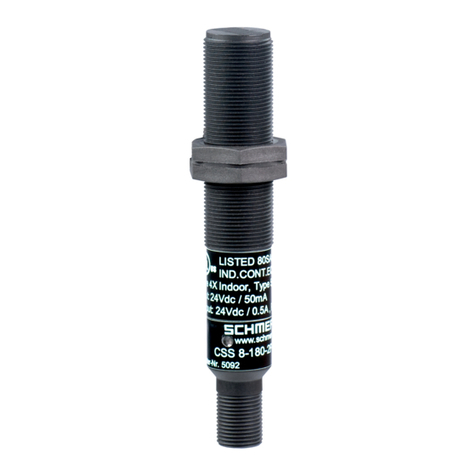
schmersal
schmersal CSS 8-180 operating instructions

Berker
Berker 7566 27 Series instructions
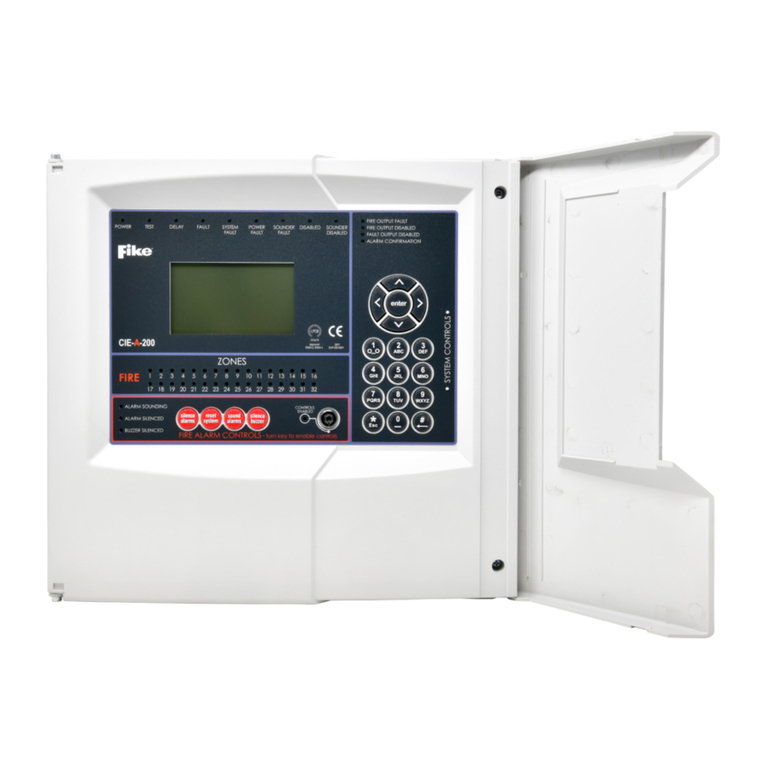
Fike
Fike CIE-A-200 Installation and maintenance instructions
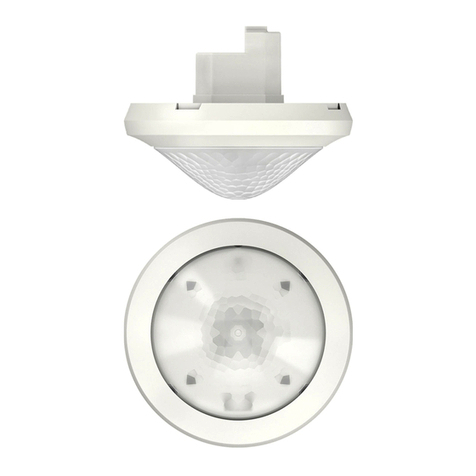
Theben
Theben theMova S360-101 DE WH operating instructions
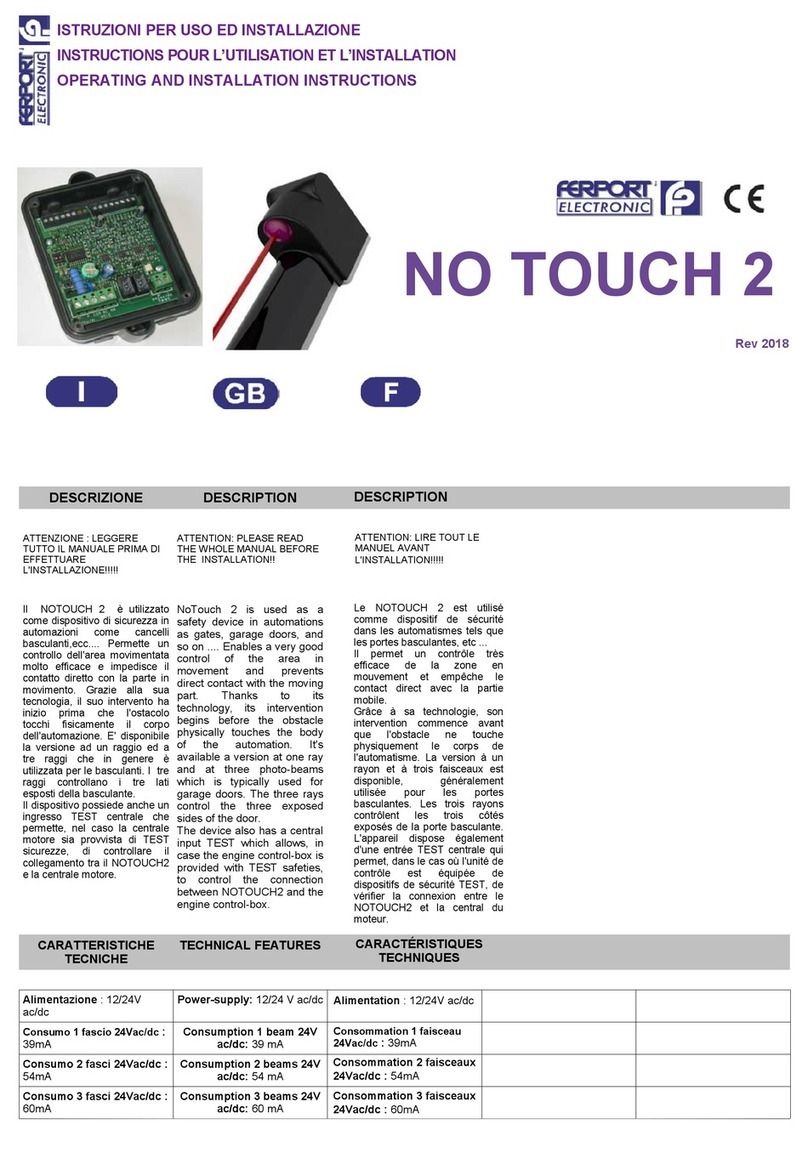
Ferport
Ferport NoTouch 2 Operating and installation instructions

IDEM SAFETY SWITCHES
IDEM SAFETY SWITCHES ES-P operating instructions

Beko
Beko METPOINT CID Operation manual

ADEMCO
ADEMCO 4278EX installation instructions
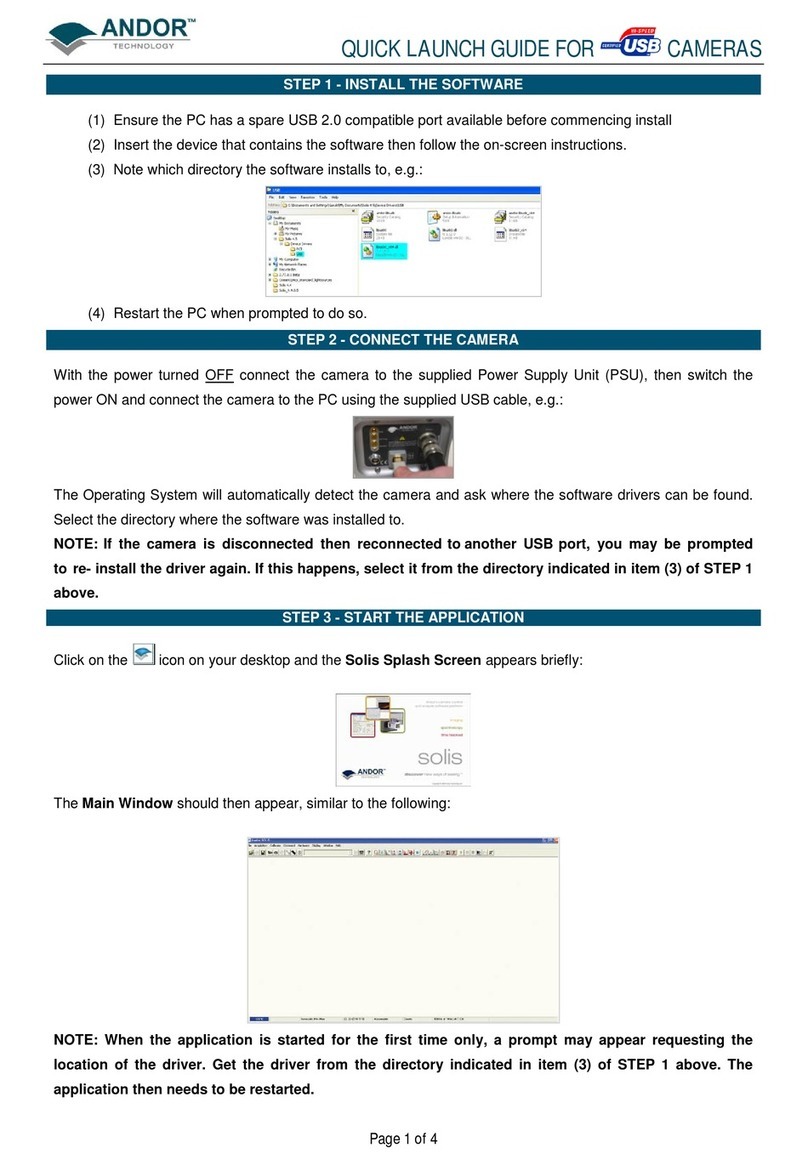
Andor Technology
Andor Technology AD02 QUICK LAUNCH GUIDE
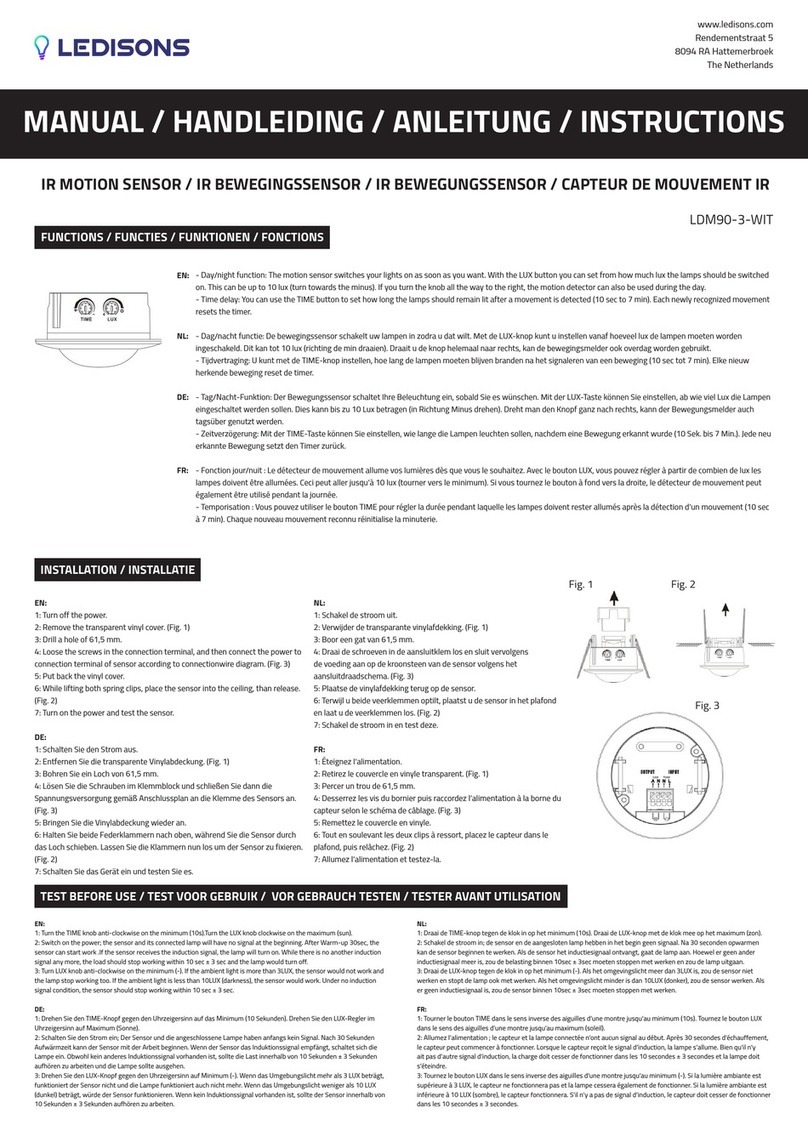
LEDISONS
LEDISONS LDM90-3-WIT manual