CDS CDS-ECW Series User manual

CDS-ECW
Purchase Guide
Operation Manual
and
DC Servo Motor Driver
Series
(QP0907-2)

Table of Contents
(1) Installation.................................................................................................................. P1
(2) Specifications...................................................................................................... P2~P3
(3) Layout of PC Board Components............................................................................ P4
(4) Block diagram............................................................................................................. P5
(5) Instruction of Power Supply.................................................................................... P6
(6) Selection and Match of Specification for Speed Feedback Voltage............... P7
(7) Instruction of Signals/Wiring.......................................................................... P8~P16
(8) Protection Function and Status Instruction............................................... P17~P18
(9) Adjustment........................................................................................................ P19~P21
(10) Function of Options.............................................................................................. P22
(11) Standard function:feed back failed (optional) mode: F ......................... P23
(12) Trouble-shooting............................................................................... P24~P25
DC BRUSHED SERVO MOTOR DRIVER
CDS-ECW SERIES
□

(1) The ambient temterature shall not exceed the limit of 0~50℃.
(2) The relative humidity shall not exceed the limit of 10~90%RH (not dew).
(3) Environment with corrosive and inflammable gases shall be avoided.
(4) Environment with dust, salt ,and ferrousdust shall be avoided.
(5) Environment possible for water,oil and chemical spray shall be avoided.
(6) No big vibration and impaction.
(7) Good ventilation is required.
INSTALLATION
1
Notices for installation environment:
V COM
ZERO
SPEED
AC GAIN
GC GAIN
RESET
ENA
LIMIT +
LIMIT -
OL/MS/OH
T.F
T.G
LIMIT
ENABLE
READY
-15V
0V
}
}
}
}
}
246mm
151mm 58mm
5mm
227mm
31mm
257mm
MA IN POWE R
SY S. POWE R
MO TOR
FU SE
F. G
}
}
}
52.5mm
ECW Series

2
TABLE OF SPECIFICATIONS
Type Code:
Option Code F : Trip-ff protection at
Continuous Voltage (DC)
Continuous Current (DC)
Series Title
Example : CDS - 05 10 F EL
Specifications of this driver :
MODE CDS-EW CDS-EW CDS-EW CDS-EW
RMS
RMS
PEAK
RMS
(KG)
SPEC
CONT. CURRENT (A)
CONT. OUTPUT DCV
MAX. OUTPUT DCV
NET WT. EL
EC
PEAK CURRENT (A)
0510 0515
57
16
10 15
23
20
13
100
113
1.21.2 1.2 1.2
1.91.9 1.9
1.7
113 113 113
180 180 180
150 150 150100 100 100
0710 0715 1010 1015 1510
Appearance C : With Case
Continuous Current:5A (Peak Current:13A)
Continupus Voltage:100VDC (Maximum Voltage 113VDC)
Trip-off Protection at Abnormal Feedback
EL : L board without case
Functions of options and specifications
(Refer to the instruction of options before selection)
Abnormal Feedback.
CDS -05 10 F E C W

NOTE OF SPECIFICATIONS
3
●Type of Control : PWM effective switching frequency of:
●Entry of Speed Command : DC±10V /Rated Speed.
●Voltage Feedback Gradient DC :
(It can be selected by JUMPS in PC board.Other custom-made specifications
can also be accepted.)
●Variance ratio of rotating speed under 0.1%
(variance ratio of load: 0~100%)
●Standard Protection Device:
Overloading,overheated in the driver,short-circuit in the motor, regenerative
voltage absorption circuit.
●Option F:Trip-off Protection at Abnormal Feedback.
(Especially for the link between PC board and master
board. Refer to page 23)
CDS-0510E & CDS-0515E
CDS-0710E & CDS-0715E
CDS-1010E & CDS-1015E
CDS-1510E
20KHZ
20KHZ
16KHZ
16KHZ
7V/1000 rpm
9.5V/1000 rpm
13.5V/1000 rpm

4
+
+
-
+
CP
SD 4
SD 5
SD 7
SD 9
SR 7
SR 6
SC 18
SC 19
SC 21
CN 8
SC 20
SU 1
SC 22
SV R
JP 1
TF OFF
SR
CC
FL 1
SD 8
SD 6
C3 4
C3 2
C6 8
VR 11
U1 1
C3 5
SD 1
SD 2
SD 3
SR 5
TRANS2
SR 9
SR 8
C6 0
C5 9
Z2 6Z2 0
Z1 9
Z2 7Z2 1
P1 2P1 1P1 3
R1 31
D3 8
R1 08
R1 00
R5 2
R7 9
D1 3
D3 2
D8
D4 8
C1 9
C4 8
C8 0
C1
C3
C2
C43
CN3
C41
P1 0
CN 4
CN 1
D9
D3 3
C2 2
D1 9
D2 2
VR 3
VR 12
RS T
R2 04
R3 7
R8 5
R4 6
R9 9
R1 52
R4 5
C6 3
C5 C 31
R2 05
R2 03
Z1 5
FL 2
U1 0
R1 04
R2 06
R1 06
R1 40
Q1 0
P1 4
D1 6
R1 47
R6 2
R5 8
R5 3
R5 4
R1 26
R1 36
D1 8
D4
D1 7
D2
D4
R1 37
R1 38
R4 0
R6 3
R7 0
R2 01
RP 145
R3 6
RP 144
R7 6
R3 4
R1 5
R2 4
R2 8
R2 7
R2 9
R3 0
R9 4
RP 10
RP 11
RP 7
RP 8
R9 6
Z9D2 0
D1 0
D5
D3
D1 4
D1 5
Z5
Z6
R3 9
R8 4
R2 6
R1 51
RP 66
RP 67
R1 27
R1 39
R3 3
R6 9
R3 2
R5 7
R5 6
RS T
R3 8
R9 7
R1 6
R1 7
R1 4
R8 1
R8 0
R8 2
R8 3
R6 8
R3 1
R3 5
R1 13
R9 2
R1 29
R6 1
R1 28
R7 1
D1 1
Z1 7
Z2 2
Z1 8
D6
D7
D4 2
D1 2
C2 7
C2 5
C5 3
C3 7
C4 5
C6 2
2W1E
104/630
C6 1
C4 0
C9
C1 5
C3 3
C1 3
C1 2
C2 3
C4 7
C4
C4 6
C1 1
C4 4
C3 0
C2 9
C1 0
C6
Z2
Z1
Z3
Z4
Z7
C7
C2 4
C1 6
C1 8
72 5
C2 0
C1 4
C8
Z1 6
Z2 4
Z2 3
C3 6
C3 1
C2 1
C2 8
TQJP
C1 7
U5
U1 4
U2
U1 6
U1 5
U1 7
U1 3
U4
VR 8
R5 5
R7 2
R1 0
R4 8
R4 9
R9
J1
J2
J3
R7
R1 3
R3 9
R2
R3
R4
R1 1
R1 2
RP 6
RP 5
RP 4
RP 2
RP 3
RP 1
R4 4
OP 07
OP 07 R50
R5 1
R4 7
R8 C 26
RP 59
VR7
FB
VR5
VR6
VR95
VRF
CS
VR4
U7
U8
U6
U9
U3 P6
C3 9
C3 8
Q9Q7
Q6Q8
SR 4
SC 9
SC 6
SC 3
SC 4
SC 5
SC 24
SC 23
R5
R4 2
R5 9
R6 0
R4 1
R2 00
TN R3
TN R1
TN R2
SC 7
SC 11
SC 12
SC 16
C4 2
PC923PC923PC923
PC923
SC 17
SC 13
R1 01
R1 12
R1 11
R1 34
R1 43
R1 42
R9 8
R2 02
R1 05
Z2 5
R1 41
R1 33
R1 32
RP65
R153
RP64
RP 60
FL 3
VC
RY1
SC 8
SQ 1
SR 2
SR 3
SR 1
SC 10
VB
RD
+
-
SC 14
CA C B
SC 15
CHOCK2
CHOCK
FUSE2
FUSE1
BRIDGE2
M—
M+
T
B
2
T
B
1
GND
(1A)
(20A)
CT
SP1
+
+
-
-
393
393
393
393
TL082
TL082
S-P
+
+15
-15 F
L3 L4 L5 L2 L1
+ + + + +
M—
M+
M- +
4078
4044
4081
TL084
4049
4049
4073
VR 2 VR1
CDS-07SW
2003/8/25
REV.1
+
0.L
TG-
TG+
CDS-EW : CIRCUIT BOARD COMPONENTS LAYOUT DIAGRAM

5
OVER HEADED
DEVICE
CURRENT
FEEDBACK
T . G FEEDBACK
INPUT
V COMMAND
UNPUT
OP
AMP
AC GAIN
DC GAIN
CONTROL
BALANCE
ADJUST
DEVICE
(OPTIONAL)
PROTECT FUNCTION
AND LIMIT DEVICE
F
SERVO
ENABLE
CONTROL
SIGNAL
SWICHING
DRIVER
CIRCUIT
H TYPE
CIRCUIT
BRIDGE
RECTIFIER
OF
MAIN
POWER
T .G FEEDBACK
FUSE ACV OR DCV
U1 , V1
SERVO
MOT OR
ABSORPTION
CIRCUIT
OF
RET URN
VOLTAGE
SYSTEM
POWER
SUPPLY
FUSE
ACV (ONLY)
U2 , V2
Block diagram

6
INSTRUCTION OF POWER SUPPLY
Supplying AC power to CDS-E Series shall be fine since the Series is equipped
with built-in rectifying system. On the panel board of driver : U1V1 is the main
power, U2V2 is power supply terminal of control system.
Specifications of Supply Voltage
AC110V , 50/60HZ
Max. allowable change: AC90V~128V
Input current 0.7A (min)
or higher
V1
V2
U2
U1
EXAMPLE:CDS - □□10 FECW
Input voltagr 30~70VAC (max.tolerance 15% or below)
EXAMPLE:CDS-□□15 FECW
Input voltagr 30~7110VAC (max.tolerance 15% or below)
(1) Voltage stabilizer should be installed in environment with great current and voltage variance.
(2) The driver will trip-off if breaking occure on the main input current and voltage of U1V1 alone (the
T.F. LED on the panel board lights up). After the problem is corrected,the power will be supplied
through automatic reset. If the power supply is over AC80V,the rectifying system or power unit
may be damaged. In case that the power supply is below or upon critical AC25V, voltage decrease
may occur during heavy load. So the driver may not be able to run smoothly owing to the abnormal
feedback. (The motor will vibrate with low frequency, make noises, or stop intermittently.) In
more serious cases, the situations shall be deem as breaking on U1.V1, leading to the tripping-off
of T,F with lit LED. After the problem is corrected, the power will be supplied through automatic
reset.
(3) If the power supply for the control system, U2,V2, is over AC128V, it may cause damages to
internal elements. If the power is below AC90V, the driver can not operate. (If the power supply is
about the lower critical limit, unstable enable may occur intermittently).
(4) Generally speaking, power improvement device (e.g.:isolated transformer) should be installed at
the front end of main power supply in order to improve the quality of supplied power.
(5) Proper treatments should also be performed in environment with worse quality of power supply
for better performance. For example, the power input terminal should not be for use with other
equipment; cables with strong signal interference should avoid from put in same wireduct and
should be grounded accurately; or filter and surge absorber should be installed otherwise.
Note:
T
B
2
(Please refer the page 8)

7
SELECTION AND MATCH OF SPEED FEEDBACK VOLTAGE
(While it is ready to leave the factory, otherwise, T/G gradient will be set at 7V/1000rpm)
TACHOGENERATOR (T.G.) can be adopted for the speed feedback of CDS-E
Series. Analog voltage input (F/V) converted from Frequency can also be used.
Three corresponding specifications are frequently adopted for standard
product.
Three optional sockets are separately placed on the PC board for each suitable
return voltage, as follows:
7V/1000rpm 9.5V/1000rpm 13.5V/1000rpm
J1 J3J2
If the motor is equipped with TG device internally, the
conduit socket on the PC Board should be selected based
on the TG specifications of motor and should be installed
by short-circuit plate.
(1) In case that the specifications of feedback voltage does not correspond to
those set up in the driver, the matching of revolution of the motor will be
difficult. If necessary, please pay attention to maximum
speed of motor, not to run over-speed.
(2) The maximum feedback voltage shall not exceed 70VDC. It will damage the
elements inside the feedback system otherwise.
(3) Two or more types of corresponding specifications should not be
installed at the same time.
(4) Diagram of JUMPER selected for specifications of feedback voltage, as the
page 4.
Note:

8
SIGNAL DESCRIPTION DIAGRAM (CDS-E)
CDS-E SERVO DRIVER
SIGNAL DESCRIPTION
1
2
3
4
5
6
7
8
9
10
11
12
U1
V1
U2
V2
FG
M+
M-
+/- 10V
COM. 0V
T.G
T.G 0V
+ LIMIT
- LIMIT
OUTPUT +15V
ENA INPUT
IN
OUT
OUTPUT -15V
OUTPUT 0V
ZERO ADJ.
ENABLE
V COM. INPUT
T.G FEEDBACK
SERVO READY (MAX. DC24V,60mA)
AC INPUT MAIN RESOURCE (AC30~110V)
AC INPUT CONTROL RESOURCE (AC110V)
MOTOR
FG
(DC100V SERIES AC30~70V)
OUTPUT -15V (LOAD CURRENT 20mA MAX.)
OUTPUT 0V (LOAD CURRENT 20mA MAX.)
+ LIMIT SW.
- LIMIT SW.
COMMON
LIMIT RT.
LIMIT LT.
OVER LOAD/MOTOR SHORT/OVER HEAT
POWER FAILED (U1,V1)
T.G FEEDBACK FAILED (OPTIONAL)
SPEED ADJ.
AC GAIN ADJ.
DC GAIN ADJ.
RESET
ENA
L+
L-
O.L
T.F
}
}
}
}
}
}
REMARK:UNLESS SPECIFIED, ABOVE FIGURE ALL SIGNALS ARE DCV.
T
B
1
T
B
2

9
1
2
3
4
5
6
7
8
9
10
11
12
U1
V1
U2
V2
FG
M+
M-
+/- 10V
COM. 0V
T.G
T.G 0V
+ LIMIT
- LIMIT
OUTPUT +15V
ENA INPUT
IN
OUT
OUTPUT -15V
OUTPUT 0V
ZERO ADJ.
ENABLE
V COM. INPUT
T.G FEEDBACK
SERVO READY (MAX. DC24V,60mA)
AC INPUT MAIN RESOURCE (AC30~110V)
AC INPUT CONTROL RESOURCE (AC110V)
MOTOR
FG
(DC100V SERIES AC30~70V)
OUTPUT -15V (LOAD CURRENT 20mA MAX.)
OUTPUT 0V (LOAD CURRENT 20mA MAX.)
+ LIMIT SW.
- LIMIT SW.
COMMON
LIMIT RT.
LIMIT LT.
OVER LOAD/MOTOR SHORT/OVER HEAT
POWER FAILED (U1,V1)
T.G FEEDBACK FAILED (OPTIONAL)
SPEED ADJ.
AC GAIN ADJ.
DC GAIN ADJ.
RESET
ENA
L+
L-
O.L
T.F
}
}
}
}
}
T
B
1
T
B
2
1
10K VR
23
DESCRIPTION DIAGRAM OF VR SPEED ADJUSTMENT
WIRING (CDS-E)
CDS-E SERVO DRIVER V SERIES
SIGNAL DESCRIPTION
REMARK:UNLESS SPECIFIED, ABOVE FIGURE ALL SIGNALS ARE DCV.
CW SW. NO.
CCW SW. NO.
CCW SW. NC.
CW SW. NC.

10
APPENDIX OF SIGNAL DESCRIPTION
CDS-E-TB1 I/O TERMINAL WIRING DIAGRAM
CDS-E SERVO DRIVER V SERIES
+
-
1
2
3
4
5
6
7
8
9
10
11
12
OUTPUT +15V
(LIMITL ,NO SERIES OR PARALLEL
WITH OTHER LOADS)
V COMMAND
(INPUT IMPEDANCE ABOUT 25KΩ)
TG
(MAX. FEEDBACK VOLTAGE 70VDC)
COMMON
SERVO ENABLE (12-24VDC)
SERVO READY (MAX. DC24V、60mA)
OUTPUT -15V (LOAD CURRENT 20mA MAX.)
OUTPUT 0V (LOAD CURRENT 20mA MAX.)
IN
OUT
LIMIT
LIMIT
OUTPUT -15V
OUTPUT 0V
T
B
1
+
-
}
}
}
REMARK :
※ The above figure shall use DCV as unit.
※ If the Limit is longer than 10m, and please use 224/50v condenser
to connect 5th, 6th PIN and 12th PIN of TB1 in parallel.
※ If ENA is using the external power, do not connect the 7th PIN of
TB1 in the servo driver.
5
224/50V
224/50V
6
12
TB1

11
APPENDIX OF SIGNAL DESCRIPTION
LAYOUT OF ISOLATING NET WIRING
1
2
3
4
8
7
12
9
10
1
1
1
2
2
2
TB1
TB1
V COM
T.G FEEDBACK
SERVO ON
SERVO READY
Power of Controller Signal 0V
Terminals of
Controller Signal
Insulation should be exactly performed after the shield is connected.
Insulation should be exactly performed after the shield is connected.
Digram of Multi-axlia Wiring
(environment of the same isolating line)
CDS X AXIS X COMMAND
Shield of controller
Shield of controller
Shield of controller
Z COMMAND
Y COMMAND
CDS Y AXIS
CDS Z AXIS
(SHIELD)
SHIELD
SHIELD
SHIELD
0V
﹥
﹤

12
APPENDIX:SIGNAL INSTRUCTION
PIN NO.1 AND 2 OF TB1
APPENDIX:SIGNAL INSTRUCTION
PIN NO.3 AND 4 OF TB1
APPENDIX:LIMIT SIGNAL INPUT END
PIN NO.、5、6、7 OF TB1
The input command of speed voltage ,DC±10V,makes the set value of "SPEED"
adjustment button and the 10V command correspond.
Normally it is from the command terminal of controller to the command input
terminal of driver (PIN No.1 and 2 of TB1).
The isolating line with isolating net should be adopted to perform direct input
through the shortest channel (junction transfer should be avoided). The quality of
command voltage should be properly maintained.
If interfered by impure signals, the motor would vibrate with high frequency or
unusual floating might occur upon HOLDING.
If the motor is equipped with T'G inside, the isolating line and net should be
adopted for the TG cable to perform direct input to PIN No.3 and 4 of TB1
through the shortest channel (junction transfer should be avoided).
The quality of speed feedback voltage should be properly maintained.
If interfered by impure signals, the motor would vibrate or unusual floating
condition of OFFSET, or even too weak for HOLDING , might occur.
The body of TG should also be maintained properly.
Oil, humidity, or unusual object should also be avoided.
Note:
Short-circuit should be prevented between the T.G cable and housing.
Otherwise, it may lead to faulty detection of the system or unusual
lighting of LED lights on the panel board.
This limit control always in normal close status If this function is not required,
please short-circuit these 3 points and insulate them properly.
Note:
1. Limit wiring please don't series or parallel with other loads.
2. Simultaneously, the 7th pin supply the signal to the 8th pin
(ENAINPUT).

13
WIRING EXAMPLES OF SIGNAL INSTRUCTION
OF SERVO ENABLE
EXAMPLE:PIN NO. 7 AND 8 OF TB1
Connecting these two points means "SERVO ON", while disconnecting
means "SERVO OFF".
(Refer Example 3 and 4-B for enabling through external signal)
Example 1:Direct Enabling:
Example 2:Enabling Controlled by Relay Transfer:
Example 3:Enabling through External Signal
7
8
TB1
External enabling switch or PLC joint
7
8
TB1
Controller or wiring system
Transfer Ry
Controller or PLC Contactor External power supply(0V)
No Connection
Controller or other external power supply
(+12V~+24VDC)
Advantage : The Relay can placed close to the driver to
avoid unnecessary interference caused by wiring.
7
8
12
TB1

14
73
1
2
4
8
TB1
Optical coupling of controller
Example 4:Enabling Through Optical Coupling of Controller
A. Using the power supply of the driver
B. Using External power supply
7
8
12
TB1
3
1
2
4
Optical coupling of controller
No Connection
External power supply:DC+12~24V
External power supply:0V
Note:
Special attention should be paid to the driving power of optical
coupling in order to avoid situations which can not be enabled.
Refer to the following example for the input current needed for pin No.8
Above 4.5mA while the external power supply is 12VDC.
Above 6mA while the external power supply is 15VDC.
Above 10mA while the external power supply is 24VDC.

15
WIRING EXAMPLES OF SIGNAL INSTRUCTION
OF SERVO REDAY
This is a self-diagnosis function of the driver.If the driver trips off or fails, these two points
will break for the convenience of control system judgement.
(Pay attention to the direction of current)
5V:510 ohm~1K ohm
12V:1.2K ohm~2K ohm
24V:2.7K ohm~5k ohm
EXAMPLE:PIN NO.9 AND OF TB1
Example 1:Situation judged as "OK" in Status "1":
Example 2:Situation judged as
"OK" in Status "0":
(L0 Electrical potential)
(HI Electrical potential)
9
10
TB1
0.1u Capacitor
CNC Controller
External power supply 0V
Place RC as close as possible
to the output Terminal
of Status Detector
External power supply 0V
Setting of loading resistance as above.
Externally added loading resistance
Output terminal of Status Detect
External power supply +5V~+24VDC
9
10
TB1 CNC Controller
Output Terminal of Status Detector
External power supply +5V~+24VDC
0.1u Capacitor
9
10
TB1
0.1u Capacitor
CNC Controller
External power supply 0V
The current is set above 5mA to effectively lower down the strength
of impure signals and to prevent faulty action.
Direction of current
Direction of current
Output Terminal of Status Detector
External power supply +5V~+24VDC
NOTE:Example 1 and 2

Optical Coupling of Controller
power supply of wiring system 0V
or connecting serially other loading.
A. LED Display
B. Lights or Other Alarm Device, through Relay
Transfer Method (DC Relay below 24VDC)
16
Example 3:Situation for Optical Coupling Motion of Controller:
Example 4:Situation for Externally added Display or Alarm Device:
9
10
TB1
CNC Controller
9
10
TB1 External power supply +5V~+24VDC
External power supply 0V
DC Relay (mini-type)
External power supply 0V
(This Diode should be installed)
IN4007 Transfer other Relay or Device
(Parallel TNR as the diagram
if an inductive is used)
Limiting Current Resistance
12V : 1K~2K
24V : 2K~3.9K
9
10
TB1 External power supply +5V~+24VDC
※NOTE:
The coil current of relay shold be confirmed because the input current for pin NO.9 and
10 should not exceed 60mA. Calculation of coil current of relay:
Continuous current of coil÷direct current resistance of coil (refer to the stated value or
measured by triple-usage voltmeter)=coil current
E.g:If the continuous current of coil is 24V,direct current resistance of coil is 500 ohm.
Then the value of coil current should be
24÷500=0.048(A)=48mA
Which means this Relay is appropriate.

17
Protective Functions and Status Instructions (LED Indicator)
(1) ENA Enabling Display (LED ON):Enable driver's function.
(2) L+ Prositive Limit Display(LED ON):
Indicate positive rotation limit is achieved,allow reverse roation only
(RESET function is ineffective)
(3)L- Negative Limit Display (LED ON):
Indicate negative rotation limit is achieved,allow reverse rotation only
(RESET function is ineffective)
(4) O.L Overload Display and it's Reason(LED ON):
These instructions includes O.L.、M.S. and O.H instructions.
(A) O.L (Overload Display)
(B) M.S (Motor Short-circuit Display)
(C) O.H (Driver Overheated Display)
Note:80℃ over , below 65℃ will automatically reset.
(Please refer to page 24 Trouble-Shooting)
1. Overloading for a long-period of time
2. Loading exceeds the continuous current.(5~6 sec.)
3. Inappropriate acceleration/deceleration.
4. Loading exceeds the max current.(1.6 sec.)
1. Motor short-circuit.
2. Motor cable M+、M- short-circuit.
3. Motor malfunction.
4. Motor brushes were invaded by outside objects (The brush shall be
disassembled and cleaned up.)
5. Impural signals are strong, the motor's F.G connections shall be
inspected.
1. The tempersture of operating environments is too high or poor
ventilation (add fans to improve ventilation).
2. Overloading for a long-period of time (improper overload position
adjustment).
3. Driver doesn't match with the specification of the motor.(The
continuos current of the motor is bigger than that of the driver.
4. Regenerative voltage is abnormal (Deceleration time is too short.).

18
(5) T.F Abnormal Speed feedback Display (LED ON):
Trip-off protections of abnormal speed feedback can be classiffollied
into the following two categories.
(The trip-off protection at uncontrolled speed is OPTIONAL, the
corresponding model code is F .)
1. First category:when the power supply voltages of main power U1,V1
reach lower limits, the trip-off protections will be activated (T.F LED on).
The disconnection of main power supply is also included in this protetion
function. When the fuses of main power on panel board is burn down or have
connection problems or the voltage is close to or below AC25V,
then motor will vibrate or accompanied with noises and intermittent stops in
preliminary stage. If severly, it will treat as U1,V1 short -circuit and cause the
trip-out T.F LED light on. After conditions being solved, reset to enabling
automatically.(Build-in standard type).
Note:Main power fuse locates at the panel(Fuse 1 locates at L board),
if fuse burns once heavy load applied,please check fuse specification.
On the other hand, if fuse burns once load applied or Power on, and fuse
likely to be seriously burned, it is potentially, the rectifier inside driver is
damaged, please send to us for repairement.
2. Second category:trip-off protection at uncontrolled speed with T.F LED
light on (the function of OPTIONAL F shall be installed if needed).
Whether the function F is equipped or not, please refer to the instruction of trip-
off protection on page 22. You can take it as the identification of operational
abnormality or, if you're still doubtful of the listing items in the instructions, you
can purchase the protective device at any times afterward. And please refer to
the F function installation diagram of PC board on page 23 to customize
installation by yourself, or to send it back to us to install for you. After problem
is solved, don't forget to press RESET button for enabling reset function.
Note:Normally, when servo driver enable, T.F. Indicator light on, and
motor complete motionless . It apperars and can be judged U1.V1.
power supply ceased, fuse open, M+.M- wiring mistake or motor out of
order. On the other hand, when driver enable, motor runs
instantaneously then stop, at this time indicator of T.F. light on.It
apperears and can be judged, T.G. wiring open, T.G wiring shorted or
T.G. malfunction.
□
□
□
This manual suits for next models
7
Table of contents
Popular Servo Drive manuals by other brands
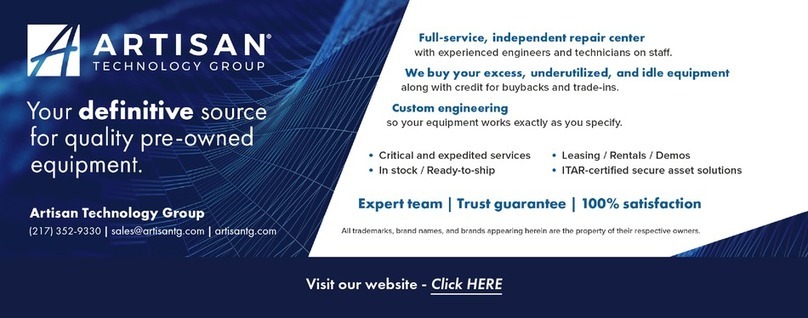
Mitsubishi
Mitsubishi MELSERVO-SO instruction manual
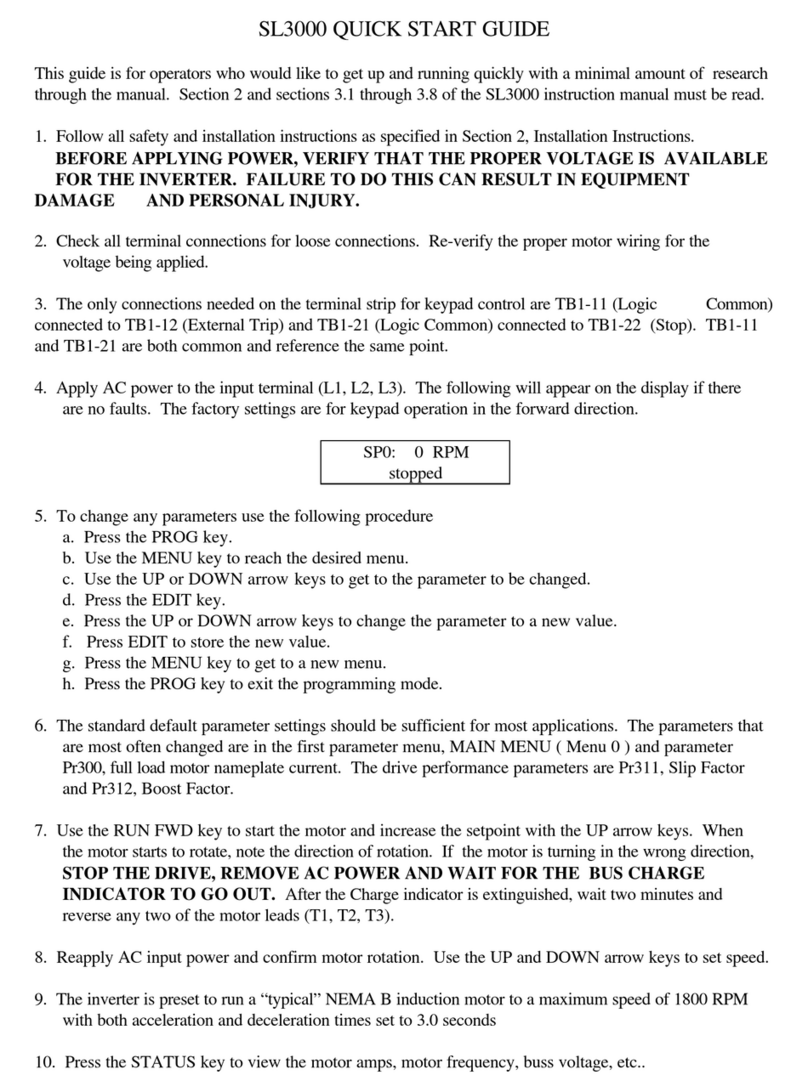
Kollmorgen
Kollmorgen SL3000 quick start guide
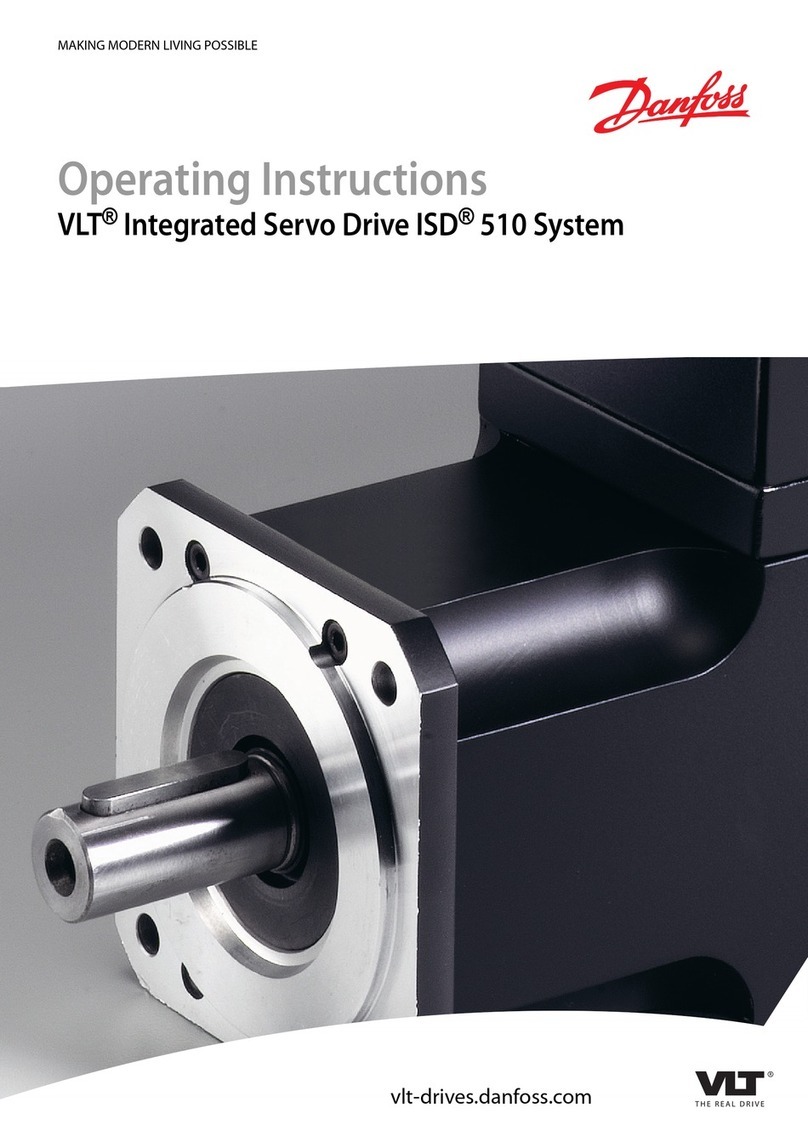
Danfoss
Danfoss VLT Integrated Servo Drive ISD 510 System operating instructions
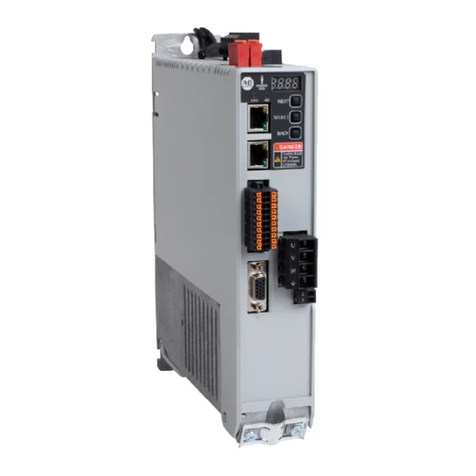
Rockwell Automation
Rockwell Automation Allen-Bradley Kinetix 5100 user manual
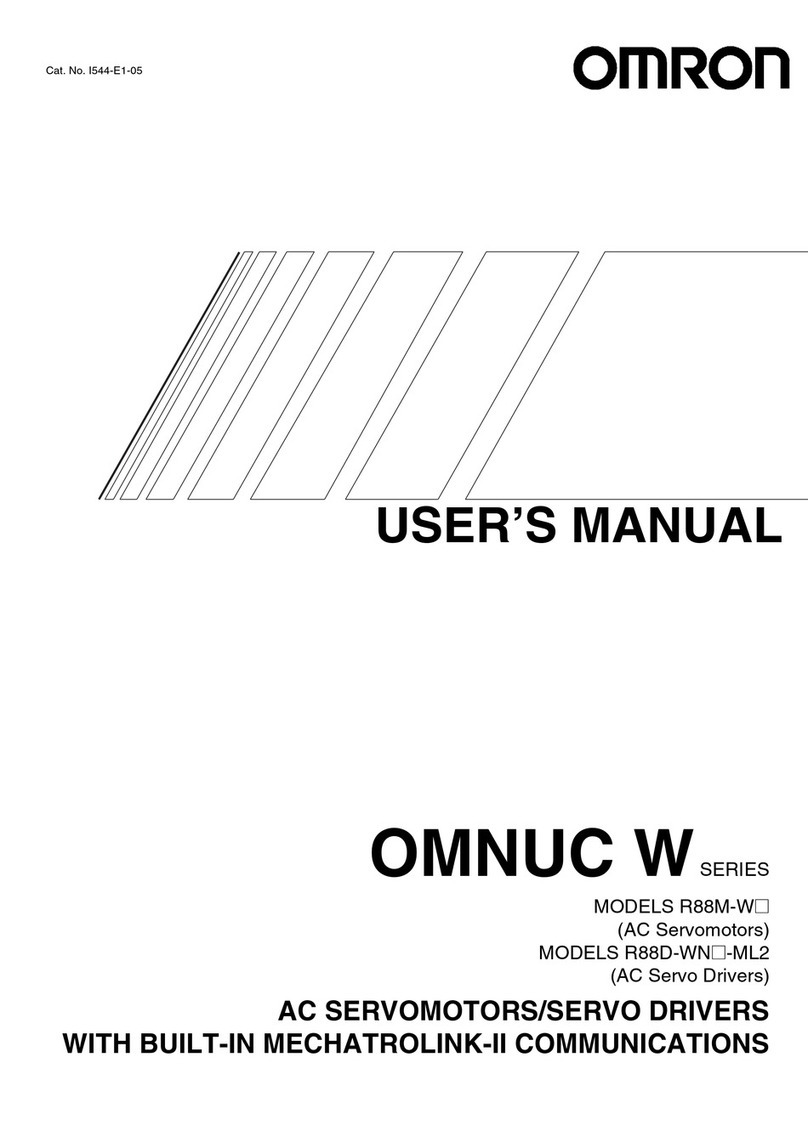
Omron
Omron R88M-W60010T user manual

Sumitomo
Sumitomo Cyclo BBB4 quick start guide