CENTENT CN0170 User manual

USER GUIDE
CN0170
2 AXIS MOTION CONTROLLER

CENTENT COMPANY
This manual contains information for installing and operating the
following Centent Company product:
•CN0170 Motion Controller
Centent and the Centent Company logo are trademarks of Centent
Company. Other trademarks, tradenames, and service marks owned or
registered by any other company and used in this manual are the
property of their respective companies.
Copyright ©2019 Centent Company
3879 South Main Street
Santa Ana, CA 97207
All Rights Reserved


GENERAL DESCRIPTION:
The CN0170 is a two axis programmable motion control computer for step
motor systems. It is designed to operate with a host computer or as a stand-
alone controller. When connected to a host PC or terminal the CN0170 serves
as a peripheral device, receiving instructions and returning data via a
standard RS-232 serial port. Operating alone, the CN0170 can recall up to
3000 random x,y co-ordinates.
The CN0170 is a CMOS Z80A microprocessor based system. A CMOS RAM
stores motor operating parameters and application programs. The RAM is
battery backed-up, allowing retention of program and parameters in the event
of power interruption. Extensive use of CMOS circuitry insures minimum
power consumption and maximum noise immunity.
The CN0170 motion controller can generate 65,535 different speeds and
acceleration rates. The internal position registers of the controller have a range
of 4,194,304 full steps. This covers most practical applications. Position is
calculated to 1/1024 of a full step regardless of the pulse rate selected.
Velocity is resolved in ¼ step per second increments. Acceleration resolution is
64 steps per second squared.

2 CN0170 MOTION CONTROLLER
In addition to linear acceleration, the CN0170 offers the option of “stored
profile” acceleration or user defined acceleration. The controller contains 16
stored profiles corresponding to the speed-torque curves of the most common
step motors available. By selecting the curve that most closely matches the
motor used, it is possible to take maximum advantage of the available motor
power, yielding the shortest time-to-speed ratio. The user may choose from
these 16 predefined profiles or enter a custom profile of his own specification.
For motion systems requiring more than two step motors, multiple CN0170s
may be linked together in a “daisy-chain” configuration and controlled by the
host via a single serial port. A maximum of ten step controllers (20 axis) may
be linked in this fashion. The host synchronizes the positioning of the various
motors in the system by querying each controller's status on the serial
interface. Linear and circular interpolation is possible with motors operated by
the same CN0170 within the system. Point-to-point moves are possible
between any motors in the system.
The CN0170 comes enclosed in a compact black anodized aluminum case. All
connections to the controller are by “D” type plugs located along one edge of
the unit. Separate connectors are provided for each motor drive, the serial
interface, and for control functions (limit switches etc.). LED indicators,
showing the status of the controller, are visible through a window on the top
surface of the case. Legends on the case identify these LEDs and provide
hook-up information. Mounting holes are provided in each corner of the
bottom plate, which also serves as a heat sink. Overall package size is small,
measuring 9.375 inches wide, 5.5 inches deep, and .875 inches high.
PROGRAMMING THE CN0170
The CN0170 comes with a built in operating system and high level language
for motion control. Through the use of the serial interface the host can send
the programming instructions and control the program operation. All
operating commands and program instructions are comprised of ASCII
character strings, utilizing simple mnemonics, that may be written and
maintained with a word processor. The CN0170 can also be operated by a
dumb terminal or any program that can communicate in ASCII format.
The CN0170 may be operated in any one of three modes. Mode 3 is the
Operate Mode, where stored programs are executed. Mode 2 is the Program
Mode for loading instructions into the program queue. Mode 1 is the
Immediate Mode, where instructions are executed as soon as they are
received. Mode 1 instructions are not stored in the program queue.

CENTENT COMPANY 3
Commands or instructions always begin with the letter unique to it followed
by operators and parameters where required. Illegal instructions or syntax
errors result in the controller echoing the entire input string back to the host,
indicating that no instruction was accepted. When a legal command or
instruction is received, the controller executes it (Immediate Mode), or
compresses it and stores it in the program queue (Program Mode).
The Operate Mode is selected to operate programs stored in the program
queue. Operation in this mode begins with a “Go” command. It is not
necessary to maintain the serial link between the host and the motion
controller while running from Operate Mode.
Operating system commands are not normally loaded to the program queue.
They direct the CN0170 at the operating system level and are executed
immediately. Included are commands to select mode of operation, assign and
select unit numbers, start and stop program operation, and set or query the
real time clock. Some commands may be placed in the program queue. When
program operation reaches these commands they execute as they would if
entered by the host on the serial interface.
Program instructions are divided into three groups; motor parameter, motor
positioning, and input/output control. Input/output instructions control the
analog and digital I/O functions of the CN0170. Motor positioning instructions
cause the step motors to move. Motor parameter instructions define the
performance envelope for motor operation.
The two motor outputs of the CN0170 may be controlled independently or
treated as a two axis co-ordinate system. Instructions are included for point to
point, linear and circular interpolation. Home routines feature built-in
algorithms to accurately reference the motors to their limit switches. Other
positioning instructions include jogging, where the motors are controlled by a
joystick or other analog input, and speed control operation, where the motor
runs at an exact speed.
Another method of positioning the motors involves the use of the Ratio
instructions. This servos one motor to the other at a precise speed ratio. When
the master motor is instructed to move, the slave motor also moves at the
specified percentage of the master's speed. This allows the host to “gear” one
motor to the other. Instructions are included to specify whether the slave
motor moves in the same or opposite direction as the master motor. The Ratio
instruction is canceled when the host sends a motion instruction to the slave
motor, taking it out of Ratio mode.

4 CN0170 MOTION CONTROLLER
Motor parameter instructions do not directly cause the motors to move. These
include instructions for velocity, acceleration, joystick enable, home direction,
driver resolution, and position preset. These parameters may be changed at
any time in the program, affecting the motion instructions that follow. The
host may query the status of various parameters during motor operation.
Instructions are included for querying motor position, velocity, acceleration
rate, acceleration profile, and ratio rate.
By utilizing the joystick feature of the CN0170 in conjunction with the position
query instructions, the host may implement a teach/learn scheme for motion
control. Motors may be manually jogged to desired locations and the co-
ordinates recorded by the host. By sending the position data back to the
controller in the form of motor positioning instructions, the system is able to
recall the points on the x,y plane provided by the joystick.
Unit numbers are used in systems consisting of more than one motion
controller. In systems requiring only one CN0170, unit numbers may be
ignored. Each CN0170 in the system is assigned a number (0-9) to distinguish
it from the other units in the system. The host then selects one (and only one)
active unit. All commands and instructions are directed to the active unit.
Information sent back to the host is preceded by the unit number of the
controller transmitting the data.
The CN0170 motion controller has an internal time clock that includes day,
month and year as well as time of day function. The clock is set by the host
and remains operational while power is supplied to the controller. The host
uses the clock for real time reference of the machine process. The host must
re-program the clock after power interruption.
The instruction set is listed on page 12 through page 15 of this guide. For a
more detailed explanation consult the CN0170 Operating Manual.
USER INTERFACE (RS-232)
Communication between the step controller and the host is via
serial interface. The CN0170 contains two complete serial ports
brought out to a single “D25” plug connector. The primary
channel is connected to the host processor while the secondary
channel connects to another CN0170 if more than 2 axis of
motion are required. “Unit ID” numbers allow the host to direct
the program instructions to the various controllers in the system,
and to differentiate the data returned to the host by the
controllers. Each CN0170 reads only the instructions intended
for it and relays other data down the chain on its secondary
channel.
SERIAL
TxD B
GND 114
RxD A
TxD A
GND
RTS A
CTS B 13 25
RxD B
RTS B
CTS A

CENTENT COMPANY 5
It is possible to connect the secondary RS-232 channel of the last CN0170 in
the daisy-chain to any other RS-232 device. Instructions not trapped by the
CN0170s in the system will pass through to the other device (printer etc.).
Each controller in the chain will transmit on the secondary channel at the
same baud rate as the data received on the primary channel.
The baud rate is automatically set by the CN0170. The host initiates this
process by sending a carriage return to the controller. The controller uses this
character to measure the baud rate. The host's baud rate is maintained and
does not have to set again unless a different rate is desired. Standard baud
rates from 300 to 9600 baud are available. The ports operate in full duplex
with eight data bits, one stop bit and no parity bit.
STEP MOTOR DRIVE INTERFACE
The controller provides a “D9” plug connector for each motor
drive and has the necessary signals to interface the CN0170
to most step motor drives. The “STEP” and “DIR” outputs can
sink 100 milliamps of drive current. The “I SET” output allows
standby current reduction for drives with this feature. This
reduces motor and drive heating while the motor is at rest.
When used in conjunction with Centent step motor drives,
straight pin to pin cables simplify the interface. Drives from
other manufacturers may be used, assuming they have the
same input requirements. Legends are provided on the
CN0170 to distinguish the “X-AXIS” from the “Y-AXIS”.
X AXIS
16
I RET
I SET
5VDC
STEP
DIR
59GND
STEP MOTOR DRIVE OPTIONS
The CN0170 is intended for use with full step, half step or
microstep drives. It simultaneously generates the pulse rates
necessary for 125 microstep, 10 microstep, half step and full
step drives. Jumper options on the board allow the user to
select the rate that matches the drive in use. All motor speeds
are derived from a crystal controlled oscillator; thus the
controller has an absolute accuracy equivalent to that of the
oscillator.
A-HALF STEP
B-10 MICROSTEP
C-FULL STEP
D-125 MICROSTEP
MOTOR DRIVE OPTIONS
(INTERNAL)
A B C D A B C D
XY
Centent Company manufactures a line of step motor drives that are ideally
suited to the CN0170. These include full and half step drives as well as 10
microstep and high resolution microstep drives.

6 CN0170 MOTION CONTROLLER
The CN0142 & CN0143 are 10 microstep (per full step), high frequency
“chopper” type drives that feature anti-resonance circuitry and opto-isolated
step and direction inputs. They compensate for both low speed vibration and
mid-band instability. A high efficiency switching “H” Bridge output utilizing
power MOSFETs keeps heating to a minimum.
The CN0152 & CN0153 are full/half step versions of these microstep drives
and share much of the same circuitry. The CN0142 & CN0152 are intended
for hybrid PM step motors with current ratings from .75 to 7 amps per phase.
The CN0143 & CN0153 are for motors rated from 1.5 to 14 amps per phase.
These drives are small, measuring 4" x 4.5" x .8" and weigh only 1.2 lbs.
In a slightly larger (4.0" x 4.75" x .85") package is the CN0162 high resolution
microstep drive. This drive may be configured to deliver step rates from full
step to 256 microsteps. It is also a high efficiency, high frequency “chopper”
type drive. The CN0162 is designed for motors rated from .1 to 14 amps per
phase.
For motors rated from .1 to 2 amps per phase, Centent offers the CN0124 half
step motor drive. This is a very economical, compact (3" x 2" x .8") drive. Anti-
resonance circuitry and opto-isolation are also featured in this drive. The
CN0124 operates from 10 VDC to 46 VDC; the power supply may be
unregulated.
CONTROL INTERFACE
In addition to the motor driver output, the CN0170 provides
analog input and digital input/output to facilitate the motion
system design. These functions are combined with the power
supply inputs on the CONTROL connector. Digital inputs and
outputs are TTL compatible. The analog inputs have an input
voltage range of 0-5 VDC or 2-3 VDC. A jumper option on the
printed circuit board selects between the ranges. The
conversion resolution of the A/D converter is 8 bits.
CONTROL
IN 1
IN 2 114
BSY Y
FLT Y
HME Y
RUN Y
SPD X
RUN X
OUT 1
ALG Y
ALG X
5VDC
GND
GND 13 25
BSY X
FLT X
HME X
STB X
SPD X
OUT 2
STB Y
ALG 2
ALG 1
+VDC
+VDC
Each motor has dedicated inputs for a limit switch and a fault switch. The
limit switch, if used, establishes the “Home” position of the step motor. The
fault input interrupts the step pulse train to the drive in the event of an error
condition. This prevents over-travel of the motor and damage to the system.
More than one switch may be connected to the fault input (in parallel) to
define the boundary regions of motor travel.

CENTENT COMPANY 7
The Busy/Ready input is used in conjunction with the Position Strobe output
to provide TTL handshaking for interfacing the CN0170 to external devices.
This allows synchronization of motor positioning and machine function.
Additionally, the “Run/Stop” and “At Speed” outputs provide logic level status
of each motor.
Two general purpose digital inputs and two general purpose digital outputs
are also provided. These are the “Aux. Input” and “Aux. Output” connections
on the Control Connector as designated on the cover of the CN0170. The
status of the inputs is always available to the host on the serial interface.
Program commands for turning the outputs on or off are provided in the
instruction set. Status LEDs also indicate the condition of these inputs and
outputs.
The analog input consists of a dedicated channel for each motor and two
general purpose channels. The dedicated channels are normally connected to
a joystick for manually jogging the motors. The general purpose channels
provide access to other analog devices. The status of all analog inputs may be
sampled (via RS-232) at any time.
CONTROL STATUS LED ARRAY
The digital inputs and outputs are mapped to an
LED indicator visible through a window in the case
of the CN0170. Legends identify the various
functions represented. This provides the user with a
convenient tool for evaluating the status of the
controller during program operation or
development.
The following page illustrates an example of a
positioning system utilizing the Centent CN0170 Two Axis Step Motor
Controller in conjunction with Centent CN0143 and CN0162 step motor
drives. This is provided as a guide to the user, specific systems will differ in
configuration.
The CN0162 in this example utilizes its built-in Standby Set function as well
as the ISET of the controller. The CN0162 Standby Set goes active .1 seconds
after the motor has stopped. The user controls the CN0170 ISET time period via
the serial interface. With ISET connected directly to the Current Set input of the
drive, current reduction is 100% when active. The Current Set Tables list
resistor values for the Current Set Resistor and Current Standby resistors of
50%, 25%, and 10% of full current. These values are rounded off to the
nearest standard 5% resistor.

5
K
O
H
M
S
JOYSTICK
X
Y
11
5
5
4
4
3
3
2
2
1
1
11
12 13
910
14
2
19
20
16
3
13
13
25
8
7
17
14
16
1
4
8
20
23
22
3
12
12
1
+
+
HOME
(Start Input)
FAULT
IN 2
HOME
IN 1
X AXIS
Y AXIS
FAULT
OUT 1
OUT 2
ALG 1
ALG 2
GROUND
GROUND
INDEXER
POWER
SUPPLY
(8-12 VDC)
TTL
TTL
2 TxD 3 TxD
20 DTR 4 DTR
3 RxD 2 RxD
8 DCD 1 DCD
5 CTS 8 CTS
6 DSR 6 DSR
7 GND. 5 GND.
(D25) (D9)
HOST (RS232)
2 RxD
20 CTS
3 TxD
8 RTS
7 GND.
TxD 14
RTS 19
RxD 16
CTS 13
GND. 1
CN0170 (daisychain)
(Port A) (Port B)
RSTB
Mode of
Operation Current Set Resistors
Series
Parallel RSET 25%50%
__
__
__
__
__
__
__
__
____
____
__
__
__
__
____
____
__
__
__
__
____
____
__
__
__
__
____
____
__
__
__
__
__
__
__
__
__
__
__
10%
CN0143 CURRENT SET TABLE
RSTB
SeriesParallel
Mode of
Operation RSET
Current Set Resistors
25%50%
__ __ __
__
__
__
__
__
__
__
__
__
__
10%
CN0162 CURRENT SET TABLE
CENTENT CN0162
X-AXIS Y-AXIS
A
-HALF STEP
B-10 MICROSTEP
C-FULL STEP
D-125 MICROSTEP
MOTOR DRIVE OPTIONS
(INTERNAL)
A B C D A B C D
XY
SERIAL CONTROL
X AXIS Y AXIS SERIAL CONTROL
IN 1TxD B IN 2GND 1
11
114
66
14
BSY YRxD A FLT YTxD A HME Y
RUN YI RETI RET SPD XI SETI SET RUN X5VDC5VDC GND OUT 1STEPSTEP RTS A ALG YDIRDIR ALG X
5VDC
GND
GNDCTS B 13
55
13 25
99
25
BSY X
FLT XRxD B HME X
STB X
SPD XRTS B OUT 2CTS A STB YGNDGND ALG 2
ALG 1
+VDC
+VDC
2 AXIS STEP MOTOR
MOTION CONTROLLER
CENTENT CN0170


10 CN0170 MOTION CONTROLLER
Centent step motor drivers are designed to operate 4, 6, and 8 wire motors in
a low performance or a high performance configuration (a 4 wire motor is
considered as high performance configuration). Please consult the driver's
operating manual to determine the best configuration for your application.
The high performance configuration is called half-
winding operation in a 6 wire motor and parallel
operation in an 8 wire motor. Both 6 and 8 wire motors
in this configuration are commonly referred to as being
operated in parallel. The following tables show the wire
color codes for various manufacturer's motors operated
in the high performance configuration.
MANUFACTURER
SUPERIOR ELECTRIC
RAPIDSYN
IMC
EASTERN AIR DEV.
PACIFIC SCIENTIFIC
WARNER ELECTRIC
VEXTA
JAPAN SERVO
HALF WINDING OPERATION - 6 WIRE MOTORS
MOTOR TERMINAL
* white wires are not interchangeable, use ohm meter to find white-blue & white-green pairs
3
WHITE
WHITE
WHITE
WHITE
BLACK
BLACK
BLUE
BLUE
4
GREEN
GREEN
GREEN
GREEN
ORANGE/BLK
ORANGE
WHITE
WHITE*
5
BLACK
BLACK
BLACK
BLACK
RED
RED
YELLO W
WHITE*
6
RED
RED
RED
RED
RED/YELLOW
WHITE
GREEN
GREEN
MANUFACTURER
SUPERIOR ELEC TRIC
PAC IFIC SCIENTIFIC
BODINE
PORTESCAP
DIGITAL MOTOR
PARALLEL WINDING OPERATION - 8 WIRE MOTORS
MOTOR TERMINAL
3
RED
WHITE
BLACK
ORANGE/WHT
BROWN
ORANGE/WHT
BROWN
ORANGE
BLACK
ORANGE/WHT
4
BLACK
RED/WHITE
BLACK/WHT
ORANGE
BROWN/WHT
ORANGE
BROWN/WHT
ORANGE/WHT
BLACK/WHT
ORANGE
5
GREEN
BLACK/WHT
RED
YELLO W/ WHT
RED/WHITE
YELLO W
RED
YELLO W
RED
YELLO W/ WHT
6
ORANGE
GREEN/WHT
RED/WHITE
YELLO W
RED
YEL/ WHT
RED/WHITE
YEL/ WHT
RED/WHITE
YELLO W
The low performance configuration is called full-winding operation in a 6 wire

CENTENT COMPANY 11
motor and series operation in an 8 wire motor.
Both 6 and 8 wire motors in this configuration are
commonly referred to as being operated in series.
The following tables show the wire color codes for
various manufacturer's motors operated in the low
performance configuration.
The CN0170 Instruction Set is listed on page 12-15 for quick reference. For
more explanation, consult the CN0170 OPERATING MANUAL. The CN0170
includes a diskette with RUN170.EXE; a program to operate the controller
from an IBM PC or compatible. The disk includes updates, programming
examples, and a text file of the manual.
MANUFACTURER
SUPERIOR ELECTRIC
RAPIDSYN
IMC
EASTERN AIR DEV.
PACIFIC SCIENTIFIC
WARNER ELEC TRIC
VEXTA
JAPAN SERVO
FULL WINDING OPERATION - 6 WIRE MOTORS
MOTOR TERMINAL
3
GREEN/WHITE
GREEN/WHITE
GREEN/WHITE
GREEN/WHITE
BLACK
BROWN
BLUE
BLUE
4
GREEN
GREEN
GREEN
GREEN
ORANGE
ORANGE
RED
RED
5
RED/WHITE
RED/WHITE
RED/WHITE
RED/WHITE
RED
RED
BLACK
YELLOW
6
RED
RED
RED
RED
YELLOW
YELLOW
GREEN
GREEN
MANUFACTURER
SUPERIOR ELEC TRIC
PAC IFIC SCIENTIFIC
BODINE
PORTESCAP
DIGITAL MOTOR
SERIES WINDING OPERATION - 8 WIRE MOTORS
MOTOR TERMINAL
3
RED
BLACK
BROWN
BROWN
BLACK
(BLACK WHITE)
(BLK/WHT ORG/WHT)
(BRN/WHT ORG/WHT)
(BROWN/WHITE ORANGE)
(BLK/WHT ORG/WHT)
(ORANGE BLK/WHT)
(RED/WHT YEL/ WHT)
(RED/WHT YEL/ WHT)
(RED/WHITE YELLOW)
(RED/WHT YEL/ WHT)
4
RED/WHITE
ORANGE
ORANGE
ORANGE/WHT
ORANGE
5
GREEN
RED
RED
RED
RED
6
GREEN/WHT
YELLO W
YELLO W
YELLO W/WHT
YELLO W

12 CN0170 MOTION CONTROLLER
CN0170 COMMAND SUMMARY
MODE
IMMEDIATE M1 instruction executes when received
M1\+ RTS prevents queue overflow
M1\- message on queue overflow
PROGRAM M2 instruction loads to program queue
OPERATE M3 operates from program queue
QUERY M? “what is the mode ?”
(reply) Mn where “n” is 1-3
PROGRAM OPERATION
GO G run program
Gn “n“ = positioning instructions to run
HALT H stop program operation
QUIT Q stop motors, reset program
KILL K interrupt pulse train, relay command
(reply) K relayed on 2nd RS-232 channel
UNIT NUMBERS
ASSIGNMENT
DIRECT.U=n where “n” is 0-9
ABSOLUTE .Un=n where “n” is 0-9
(reply) [Un] where “n” is 0-9
RELATIVE .U+i=n where “i” is 0-8 and “n” is 0-9
(reply) .U+j=n relayed on 2nd channel “j” is “i”-1
SELECTION .Un where “n” is 0-9
QUERY .U? request unit # (all units respond)
(reply) [Un] where “n” is 0-9
.U? relayed on 2nd channel
REAL TIME CLOCK
TIME SET T=hh:mm.ss hh = hours (24 hour clock)
mm = min. ss = sec. (opt.)
TIME QUERY T?
(reply) hh:mm.ss
DATE SET D=mm/dd/yy mm=mo. dd=day yy=yr.
DATE QUERY D?
(reply) mm/dd/yy

CENTENT COMPANY 13
CN0170 INSTRUCTION SUMMARY
MOTOR POSITIONING INSTRUCTIONS (where shown for X; same for Y)
HOME XH home single axis
XYH home both axis
SPEED CONTROL
X++ run one motor CW direction
X-- run one motor CCW direction
X++n (CW) where “n” is temp. velocity
X--n (CCW) where “n” is temp. velocity
SINGLE AXIS
ABSOLUTE X=n where “n” is motor position
RELATIVE X+n “n” adds to current position
X-n “n” subtracts from current position
POINT to POINT (axis velocity and accel. rates & profile)
ABSOLUTE X=n & Y=n X must come first
RELATIVE X+n & Y+n may be “-” for either axis
MIXED X=n & Y+n any mix of abs. & rel.
LINEAR INTERPOLATION (vector vel., x-axis accel. & profile)
ABSOLUTE X=n,Y=nX must come first
RELATIVE X+n,Y+nmay be “-” for either axis
MIXED X=n,Y+nany mix of abs. & rel.
CIRCULAR INTERPOLATION (present position is p1))
ABSOLUTE X=n,Y=n ^ X=m,Y=m “n” = p2 “m” = p3
RELATIVE X+n,Y+n ^ X+m,Y+m may be “+” or “-”
MIXED X=n,Y+n ^ X=m,Y+m any mix of abs. & rel.

14 CN0170 MOTION CONTROLLER
MOTOR PARAMETER INSTRUCTIONS (where shown for X, same for Y)
POSITION SET XP=n preset position to “n”
POS. QUERY XP? (reply is 4 byte hexidecimal value)
(reply) X=n “=” implies motor is at rest
X+n “+” implies motor moving CW
X-n “-” implies motor moving CCW
VELOCITY
SET AXIS XV=b,m where “b” = base & “m” = max. vel.
XV=b where “b” = base vel.
XV=,m where “m” = max. vel.
SET VECTOR XYV=b,m where “b” = base & “m” = max.
XYV=b where “b” = base vel.
XYV=,m where “m” = max. vel.
QUERY XV? (reply is 2 byte hexidecimal value)
(reply) XV=n where “n” = current velocity
XYV?
(reply) XYV=n
ACCEL. SET XA=n set acceleration rate
ACCEL. QUERY XA? (reply is 2 byte hexidecimal value)
(reply) XA=n
ACCELERATION PROFILE SELECT
LINEAR XC\L select linear profile
PARABOLIC XC\P select parabolic profile
STORED XCn select profile (“n” = 1-16)
USER CURVE XC\U select user curve
ENTER USER
CURVE DATA XC(i)=n where “i” = 1-16
“n” = 1 byte hexidecimal value
QUERY XC?
(REPLY) XC=L linear profile is active
XC=P parabolic profile is active
XC=n stored profile “n” is active
XC=U user profile is active
RATIO ENABLE Y/X+ slave/master - direction is the same
X/Y+
Y/X- slave/master - direction is opposite
X/Y-
RATIO DISABLE Y+0 (or any motion command)
RATIO % Y/X=.nn value of ratio (number less than 1)

CENTENT COMPANY 15
RATIO QUERY Y/X?
(reply) Y/x=nn “nn” is 2 byte hexadecimal value
JOYSTICK SEL. XJn where “n” = 1-7
DISABLE XJ0 (or any motion command)
BUSY/READY XB+ busy input active
XB- busy input inactive
TRIGGERS
POSITION XP+ prompt when motor in position
XP- disable position trigger
VELOCITY XV+ prompt when motor at max. velocity
XV- disable velocity trigger
I/O LINKAGE XL+ I/O waits for completion of move
XL- I/O independent of motor moves
I SET STANDBY XI=s “s” is delay (sec.) to standby
XI=0 standby disabled
MOTOR HOME XH- home routine starts CCW
XH+ home routine starts CW
RESOLUTION XRn “n” = 1, 2, 10, 125 step/full step
MODULO QUIT XM+ turns on modulo quit for X axis
XM- shuts modulo quit off for X axis
INPUT/OUTPUT INSTRUCTIONS
DIGITAL I/O
OUTPUT P3=n where “n” = 1 (on) or “n” = 0 (off)
P4=n
QUERY Pn? query input (n=1,2); output (n=3,4)
P1 DEFINE P1\G P1 configured for “GO” command
P1\I P1 configured for general purpose
ANALOG CHANNELS
QUERY An? read analog input (“n” 1,2)
A\X? read x-axis joystick
A\Y? read y-axis joystick
(reply) An=n “n” = 1 byte hexadecimal number
A\X=n or A\Y=n
AUX. PORT I/O
INPUT SET P\I set aux. Port to all inputs
OUTPUT SET P\O set aux. Port to all outputs
BIT CONTROL P\nnH set aux. Port to bit control
OUTPUT P=nnH output to aux. port
QUERY P? query the aux. Port


16
X-AXIS Y-AXIS
A
-HALF STEP
B-10 MICROSTEP
C-FULL STEP
D-125 MICROSTEP
MOTOR DRIVE OPTIONS
(INTERNAL)
A B C D A B C D
XY
SERIAL CONTROL
X AXIS Y AXIS SERIAL CONTROL
IN 1TxD B IN 2GND 1
11
114
66
14
BSY YRxD A FLT YTxD A HME Y
RUN YI RETI RET SPD XI SETI SET RUN X5VDC5VDC GND OUT 1STEPSTEP RTS A ALG YDIRDIR ALG X
5VDC
GND
GNDCTS B 13
55
13 25
99
25
BSY X
FLT XRxD B HME X
STB X
SPD XRTS B OUT 2CTS A STB YGNDGND ALG 2
ALG 1
+VDC
+VDC
2 AXIS STEP MOTOR
MOTION CONTROLLER
CENTENT CN0170
SPECIFICATIONS
PARAMETER MIN. MAX. UNITS
POSITION Range
Resolution 0
1/1024 4,194,304
1/1024 full steps
full steps
VELOCITY Range
Resolution
Available speeds
0
0
0
0
.25
16,383.75
32,767.50
163,837.5
2,047,969
.25
65,536
full-step/sec.
half-step/sec.
10 µ step/sec.
125 µ
step/sec.
full-step/sec.
ACCELERATION Range
Resolution
Acceleration time
(decel. mirrors accel.)
0
64
.004
4,194,304
64
1024
full step/sec2
full step/sec2
sec.
OPERATING REQ. Supply voltage
Supply current
Operating temp.
8
20
0 (32)
12
400
70 (158)
VDC
mA
°C (°F)
MECHANICAL Mounting holes 3.875 W 9.0 L in.
Mounting screws #6 #8 in.
Size .875 H x 5.6 W x 9.4 L in.
Other manuals for CN0170
1
Table of contents
Other CENTENT Controllers manuals
Popular Controllers manuals by other brands
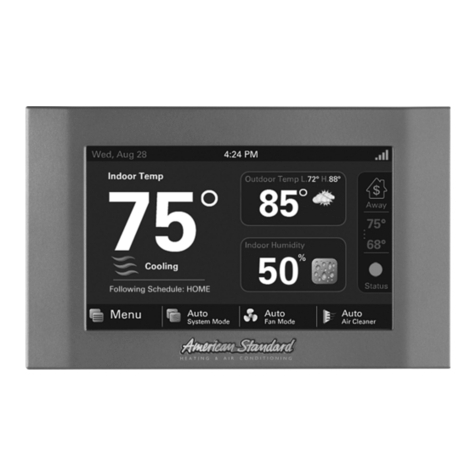
American Standard
American Standard AccuLink Platinum 850 user guide
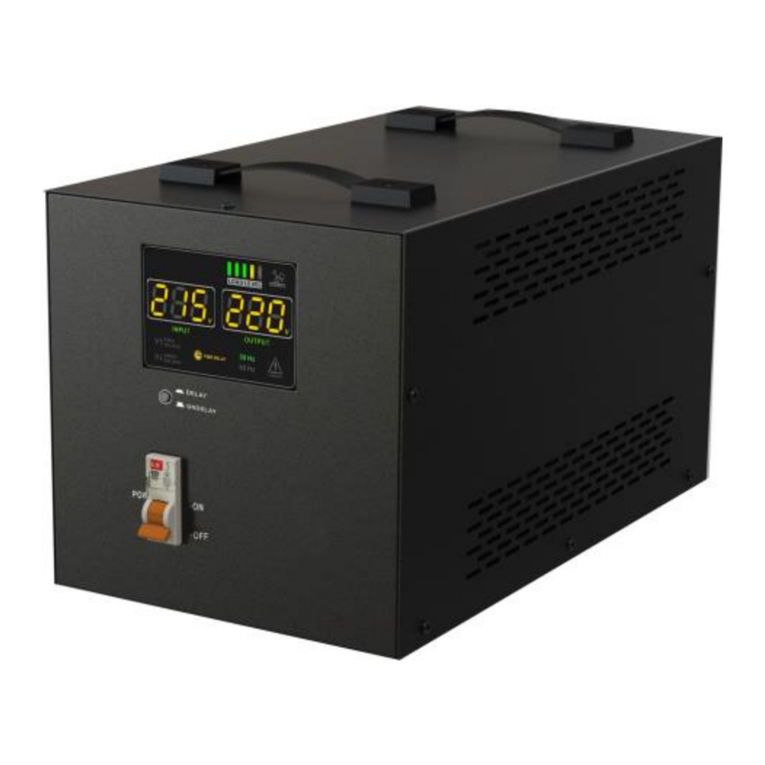
Voltronic Power
Voltronic Power AVR 5K user manual
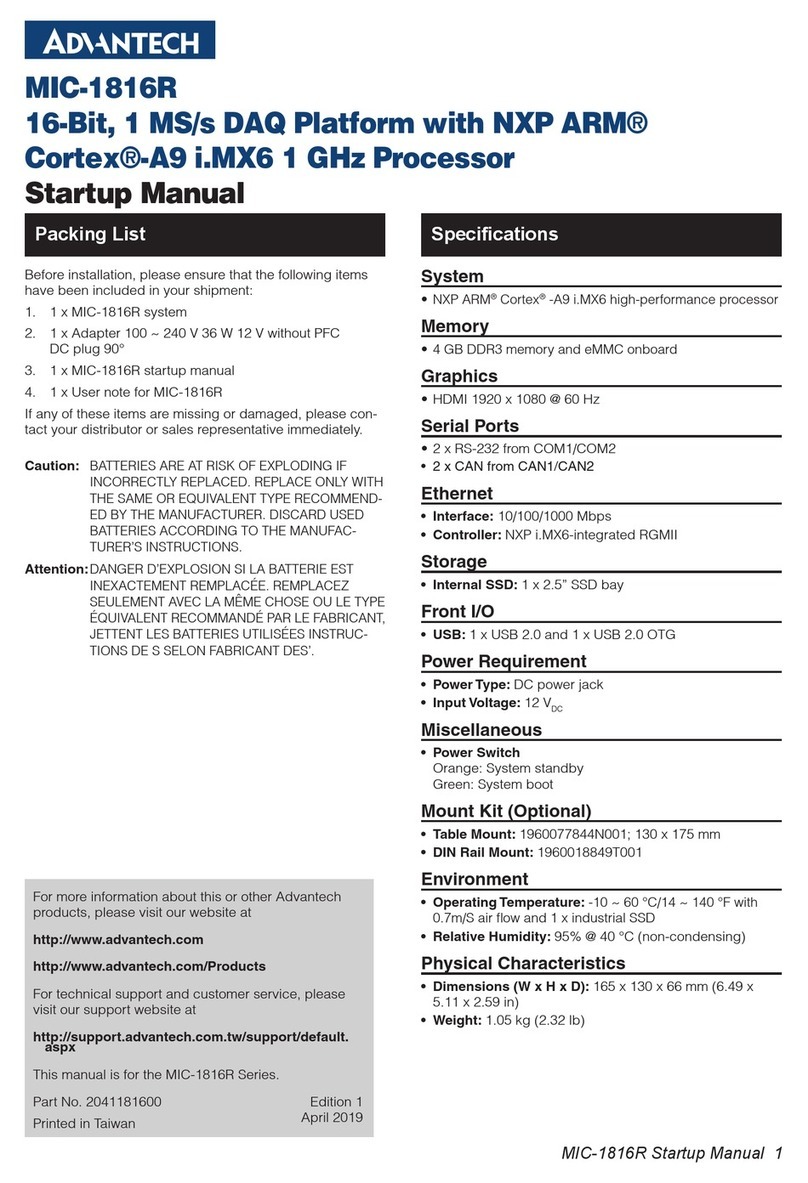
Advantech
Advantech MIC-1816R Startup manual
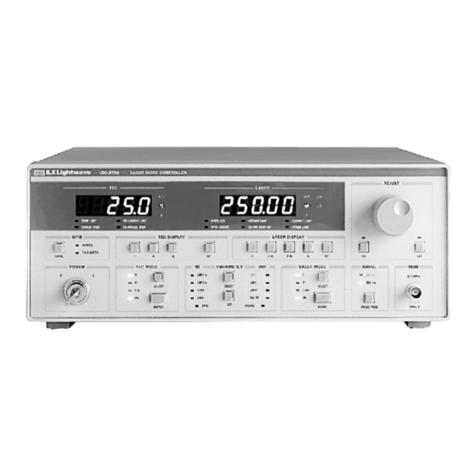
ILX Lightwave
ILX Lightwave LDC-3700B Series user guide
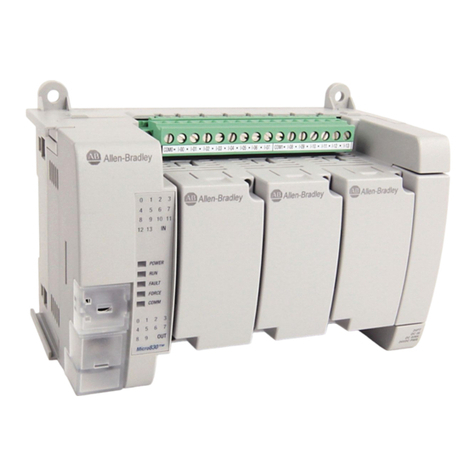
Rockwell Automation
Rockwell Automation Micro830 user manual
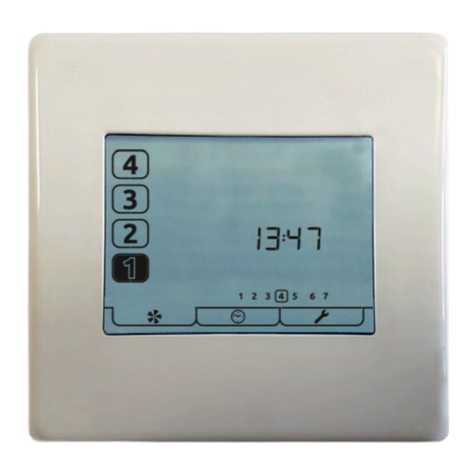
Titon
Titon aura-t HMB Commissioning Guide