Centroid Acorn KP-3 User manual

Page 1
Centroid KP-3 CNC Touch Probe
CNC Software version: CNC12 V.4.5+
Models: Acorn CNC
3
5
Components
Connections to Acorn
KP-3
CNC Touch Probe
2
Specications
7
Acorn KP-3 Wizard Setup
9
Stylus Installation
11
Testing
13
Styli Diameter Pre-travel Calculation
centroid_kp-3_cnc_touch_probe.pdf rev 11 11-18-20
Probe Alignment
18
Use with other CNC controls 25
Oak and Allin1DC setup 22

Page 2
KP-3 Specications
The KP-3 is a CNC Touch Probe intended for probing to nd part zero’s, reference positions, locate bores, bases, corners
etc., and digitizing which allows for the copying of surfaces and shaped objects. The user should rst become familiar
with the various parts and features of the probe as shown below to facilitate assembly, installation, operation and calibra-
tion. Read the stylus installation and alignment procedures section before attempting assembly. Review the over-travel
limits shown in the specications. Exceeding the limits will damage the probe and stylus.
KP-3 Description
• Probing directions X+/-, Y+/-, Z-
• Unidirectional repeatability (2 sigma) 0.00006” (1.5 micron)
• Practical use on good milling machine .0005”
• Probe deection force (X,Y) 3 ounce minimum with 40mm stylus
• Probe deection force (Z) 15 ounce minimum
• Probe body diameter and length D= 1.35” (34.3mm) L= 2.16” (54.9mm)
• Mounting shank diameter and length D= 0.5” (12.7mm) L= 1.47” (37.3mm)
• Stylus mount thread M3 thread
• Power supply required none
• LED status indicator red when triggered (powered by input 1ma)
• Weight of probe and ½”shank 0.40 lb
• Over travel limit angle (X,Y) +/- 12 degrees from vertical
• Over travel limit (Z-) 0.25” (6.25mm)
• Environmental IP64
• Patented concentric alignment (spindle/tool holder/probe body run out adjustment)
Removable Mounting Shank
1/2” diameter
KP-3 Body
1.35” Diameter
1.5”
2.16”
.22”
12 degrees
.25”

Page 3
KP-3 Acorn Kit Components
KP-3 Acorn kit part# 14947
- KP-3 probe
- 2.5 mm x 40mm carbide stem, ruby tipped stylus
- Stylus wrench
- KP-3 to Acorn hookup cable
- KP-3 to Acorn schematic download
Mounting: The standard 1/2” mounting shank design allows installation in commonly available tool holders. Other mount-
ing options can be created by the user and installed on the KP-3 by loosening the run-out adjustment screws and remov-
ing the stock 1/2” mounting shank from the body of the probe.
KP-3 Acorn kit part# 14947

Page 4
KP-3 Identication
Mounting Shank
Concentricity adjustment screws. 3/32” hex
RED LED indicator light
Off = ready
ON = Probe Tripped
End Cap
Stylus mount boss
2.5 mm carbide stem ruby
tipped stylus
Concentricity adjustment screws. 3/32” hex
Electrical connector
Probe Body
Stylus tighten hole
Stylus stem
Manufacturing Bar Code
Serial Number
Stylus tip

Page 5
PROBE SIGNAL
PROBE DETECT
+24VDC
PROBE
KP-3
PN:14912
WHT
200507 CEM
Sheet 1 of 1
3
S15020.DWG
Date:
Filename:
Drawn by:
Title:
Ver:
ACORN_rev4, KP-3 PROBE
SHIELDED ETHERNET CABLE FROM PC
+24VDC +24VDC
YEL
BLK COM
V1 (+5 VDC) 2.2A
N
LMEANWELL
RD-35B
V2 (+24 VDC) 1.0A
110VAC
BLK
WHT
GRN
GRN
ETHERNET
IN3
IN2
IN1
IN4
IN7
IN6
IN5
IN8
24 IN
24 IN
H8 H9
H4
H1
H6
H2 H3
+24
EN3
ST4
EN4
DR3
COM
DR4
COM
ST3
EN1
ST2
EN2
DR1
COM
DR2
COM
ST1
5
1
6
9
P10
P10
PIN 1 = N/C
PIN 2 = COM
PIN 3 = Z\
PIN 4 = A\
PIN 5 = B\
PIN 9 = +5VDC
PIN 8 = B
PIN 7 = A
PIN 6 = Z
5
9
4
8
3
7
2
6
1
10
11
12
13
14
15
16
17
18
19
20
21
22
23
24
25
Output 1
Output 2
Output 3
Output 4
Step 1
Step 2
Step 3
Step 4
Direction 1
Direction 2
Direction 4
Direction 3
Input 5
Input 1
Input 2
Input 3
Input 4
COM
Chassis GND
H6
1
13
25
14
AN GND
AN OUT
+24VDC
COM
+24VDC
COM
CHASSIS
PN:14445
OUT1
OUT2
OUT3
OUT4
OUT5
OUT6
OUT7
OUT8
5V
H10
8 7 6 5 4 3 2 1
HB
COM
H10
OUTPUT
STATES
ACORN
190201
Acorn_rev3 has REMOVABLE green screw terminal blocks
Acorn_rev2 has FIXED green screw terminal blocks
How to tell the difference between Acorn_rev2, Acorn_rev3 and Acorn_rev4
Acorn_rev4 has LED indicators for the Inputs and Outputs
GROUNDS ARE
110VAC IS
GREEN
VIOLET
GND
IN1
IN2
IN3
IN4
IN5
IN6
IN7
IN8
VCC
RELAY BOARD
OUT3
OUT4
OUT5
OUT6
OUT7
OUT8
OUT2
OUT1
ACORN I/O 1 2 34
INPUTS
OUTPUTS
ACORN I/O 5678
INPUTS ProbeDetect ProbeTripped
OUTPUTS
RED
BLK
COM
COM
COM
CABLE PN:14947
INCLUDED WITH KP-3
KP-3 Wiring to Acorn
Download full size PDF’s of all Acorn schematics including this KP-3 to Acorn hookup schematic on the Acorn web page
https://www.centroidcnc.com/centroid_diy/acorn_cnc_controller.html
Often it is necessary to extend the KP-3 cable. Typically this can be accomplished several ways
1.) simply extend the ying lead wires by soldering and heat shrinking on additional length of similar wire.
2.) Run the ying lead wires to a terminal strip and use another piece of cable to run from the terminal strip to the Acorn.

Page 6
KP-3 Probe cable connector
Connect the 1/8” mini jack connector into the KP-3 body and fully seat the plug!
Incorrect, probe cable connector is not fully seated.
Correct! probe cable connector is fully seated.

Page 7
KP-3 Acorn Wizard conguration
1.) Select the Probe input type from the drop down box
2.) click and drag
“ProbeDetect” and
“ProbeTripped”
to inputs 6 and 7
respectively

Page 8
KP-3 Acorn Wizard conguration
1.) Select the Probe menu under “Touch Devices”
2.) Choose “KP-3” in the Probe Type Drop down menu.
3.) Press Write Settings to CNC control and follow the instructions on the screen.
1.)
2.)
3.)

Page 9
KP-3 Stylus installation
Step 1: Inspect the threads and mating surfaces of the stylus and stylus mount boss. They must be clean and free of
defects. The stylus mount boss is M3 thread. Only use M3 thread styli.
See the KP-3 Unboxing video for a demonstration on how to install the stylus in the KP-3
https://youtu.be/HbOMSKYuy6g
STEP 2: Thread the stylus into the probe stylus mount boss using ngers only. The shoulder of the stylus threads
should meet the face of the stylus mount boss with minimal twisting effort. If there is a gap between the shoulder of the
stylus threads and the boss face that can not be closed using just ngers to turn the stylus then remove the stylus and
clean and check threads. Be sure stylus is M3 thread! If gap still can not be closed try another stylus. DO NOT FORCE
THE THREADS! This step must be completed successfully before proceeding!

Page 10
STEP 3: Finish tightening the stylus by inserting the stylus wrench in the stylus wrench hole and slowly tighten. Snug
the stylus until the probe begins to deect and when you feel a mild but rm stop has been reached stop applying torque,
the stylus is now completely tight. Applying too much torque can damage the probe or stylus.
KP-3 Stylus installation
Stylus Removal: If the stylus must be removed insert a pin in the stylus wrench hole and slowly loosen. The stylus mount
boss will turn with the stylus and begin to retract into the probe then rmly stop. When the rm stop has been reached
apply a small amount of additional torque to break the threads free. If excessive torque is required grasp the stylus mount
boss with smooth jaw pliers to prevent damage to the probe. If the stylus was installed correctly it will not require exces-
sive force to remove it.

Page 11
Testing the KP-3
“Bench test” the KP-3, you can have the probe on the bench or in the spindle whatever is safest.
1.) Enter into the CNC12 Probing Cycle menu, F1 Setup, F1 Part, F5 Probe, pick F1 Bore probing cycle.
2.) With the KP-3 plugged in (make sure Plug is FULLY seated!), manually trigger the probe by gently touching the stylus
to trigger the probe observe the Probe state indicator graphic on the screen. If the probe is congured and wired properly
the Probe tripped graphic on the screen will indicate that the probe has been tripped.
Gently trigger with nger while running a probing cycle
in air to test probe before using the Touch Probe

Page 12
Test before every use!
Even after the initial setup and operational verication it is always good practice to get in the habit of manually checking
the probe to conrm that it is functioning every time BEFORE running a probing cycle to prevent a Probe crash. This
quick test is easy and will save you heart ache by verifying that the probe is plugged in and functioning before running an
automatic probing cycle.
To manually test a Touch Probe using a Automatic probing cycle.
1.) With the KP-3 plugged in (make sure Plug is FULLY seated!) and in the machine tool. Turn down the Feed Rate Over-
ride to 10 or 20%.
2.) Position the Touch Probe in the center of the X Y travel of the machine tool.
3.) With the Touch Probe in clear space start the Center of Bore probing cycle, the probe will begin to move to seek out
the edges of the bore at the quadrants, at this slow speed you’ll have plenty of time to trip the probe with your ngers to
verify that it is working. No need to complete the probing cycle, cancel at anytime once the probe functionality has been
veried.

Page 13
C
L
Now that you know the probe works and is triggering properly along with a probing cycle we need to make sure the probe
stylus tip is concentric with the spindle and then the probe will be ready to use!
Probe Alignment: Center the Ball of the stylus so that it is concentric with the spindle
Using an indicator and the three run out adjustment screws on the body of the probe we will adjust the concentricity of
stylus ball to be concentric with the spindle. This adjustment will place the center of the stylus ball in center of the spindle
axis (stylus tip run-out)
Touch Probe Alignment

Page 14
Touch Probe Concentricity
Probe “run-out” is the amount the probe tip moves an indicator as the spindle is rotated. Run-out adjustment is necessary
to ensure that the center of the probe tip is aligned with the center of the spindle rotation axis. This eliminates any unde-
sired off-sets between the probe and the cutting tool centers when digitizing or doing automated part set-up.
When to Check Probe Run Out:
Any time the probe is removed from its holder, the stylus is changed or the probe is used in a different machine, the align-
ment procedure should be repeated to ensure accuracy. The user should also repeat the alignment procedure if the unit is
dropped or receives any sudden external shock. It is good practice to periodically check alignment for quality control and
to establish a base line maintenance schedule.
Probe to Spindle alignment adjustment
The run-out adjustment procedure is necessary to ensure that the center of the probe tip is aligned with the center of the
spindle rotation axis. This eliminates any undesired off-sets between the probe and the cutting tool centers when digitiz-
ing or doing automated part set-up.
Required Tools:
3/32” hex wrench
0.001” or better Test Indicator with Magnetic Base
0.500” Dedicated Tool Holder
Run Out
0

Page 15
Touch Probe Concentricity alignment
STEP 1: Install the KP-3 Probe into the dedicated 0.500” tool holder in the machine spindle.
STEP 2: Position the dial indicator, as shown in the photo below, with the nger of the dial indicator on the front and
center of the stylus ball. Insert the 3/32” hex wrench in the run-out adjustment set screw directly above the nger of the
dial indicator. Loosen the set screw by turning the hex wrench counter clockwise while watching the dial indicator reading
decrease. Turn the hex wrench clockwise and watch the dial indicator reading increase.
Run Out
0
STEP 3: Rotate the spindle by hand (without touching the probe) so that the probe spins through a full 360 de-
grees and watch the dial indicator to locate the high and low run-out rotation positions of the stylus. Adjust the dial indica-
tor so that the entire run-out of the tip can be seen on the dial. If the run-out exceeds the range of the dial then begin at
the highest point of the run-out and set the dial indicator so it is at the limit of its range at this point.

Page 16
STEP 4: Rotate the probe so that the nearest run-out adjustment set screw is above the nger tip of the indicator.
Using the 3/32” hex wrench slowly turn the setscrew directly above the indicator nger, in the counter clock-wise direction,
the dial indicator will show the reduction in the run-out. Stop loosening this set screw and tighten the set screw that was
nearest the low run-out position. Do not allow the probe to become loose on the mounting shank by adjusting in small
increments. Adjust in increments that are about one third of the remaining run-out.
Run Out
0

Page 17
STEP 5: Repeat steps 4 until no run-out of the tip is visible on the dial indicator needle. If a set screws become too tight
before you have nished the adjustment, do not force them, instead loosen the setscrew that corresponds with the highest
reading on the dial indicator, and tighten the set screw at the lowest reading. Only adjust a set screw when it is directly
above the indicator nger. This way you can see the full effect of the adjustment you are making. The nal small adjust-
ment is best made by loosening a set screw at the high point of run-out.
Turning the set screw Clockwise moves the
screw in,
Causing the probe body to move out.
Turning the set screw Counter Clockwise
moves the screw out,
causing the probe body to move in.

Page 18
Touch Probe “Pre-Travel” stylus diameter calibration procedure.
Calibrate the probe stylus diameter for the tool library. Just entering the value of the probe tip diameter in the tool library
will not produce accurate results unless they are corrected for stylus pre-travel.
Pre-travel is the amount of deection of the stylus tip before the probe detects the surface. This value varies depending
on the length of the stylus and the speed and direction that the stylus tip is moving when it makes contact with the surface
being probed or digitized. Pre-travel variation amount should be stated in probe specications relative to stylus length and
direction of travel limitations. A probe that has small pre-travel variation with no restriction on stylus length and direction
of travel will be quite expensive. Machine characteristics including lash and input latency also contribute to the need to
calibrate the stylus diameter. Each stylus has its own
Stylus diameter calibration procedure.
1.) Fixture a precision ring gauge on the machine tool. The ring must lie at on the work table/vise with the center line of
the bore aligned with the center line of the probe stylus/spindle. Make sure the probe is plugged in and working and test
before use! Go to the Tool Library Offset menu and set the diameter for the Probe Tool Number to 0.0000 in our case Tool
10 is the Probe Tool number so we set Diameter 10 to 0.0000
2.) Jog the probe over the center (roughly) of the ring gauge, and then slowly jog the Z-axis down until the tip of the probe
is inside the bore and not touching anything.
3.) From the main screen of CNC12, press <F1-Setup>, then <F1-part>, then <F5-Probing>, then <F1-Bore>,and nally
<Cycle Start>. The control will jog the stylus to and probe each quadrant of the bore. It will then return to the center of the
bore. The message box will appear on the screen displaying the measured bore diameter.

Page 19
Subtract this number from the known diameter of the gauge bore. The resulting number will be the calibrated diameter of
the probe stylus tip with the pre travel taken into consideration.
For example with a 1” ring gauge (ours measures .99996”) and a 2.5 mm (.0984252”) probe tip. and with the measured
diameter in step 3 is displayed as: .9199”
.99996 -.9199” = .08006” The calibrated probe tip diameter with probe pretravel compensated for is .08006” for this sty-
lus.
4.) Test the new Probe Diameter. Go back to the tool library and enter .08006” for the Diameter of Tool 10 (the probe tool
number) and run the Bore Probing cycle again! CNC12 will round the diameter number to .0801”
A message box will appear on the screen that will display the measured diameter of the bore.

Page 20
You can tweak the probe stylus pretravel calibration diameter and repeat as needed to obtain as close a measurement
as possible to the actual ring gauge diameter. Assuming the machine has low backlash and the probe is accurate, it is
possible to obtained +/- .0002” repeatability when measuring the ring gauge diameter with a good probe and a machine in
good condition.
The Probe Stylus Calibration is now complete. Probe is ready for probing and digitizing!
Each different Stylus will have a different pretravel compensated calibration diameter. Do this procedure for each stylus.
Make a table and record the calibrated diameter values for each stylus. Be sure to update the Probe Diameter in the Tool
Library to match the stylus being used when swapping out to a new stylus!
Table of contents
Popular Measuring Instrument manuals by other brands
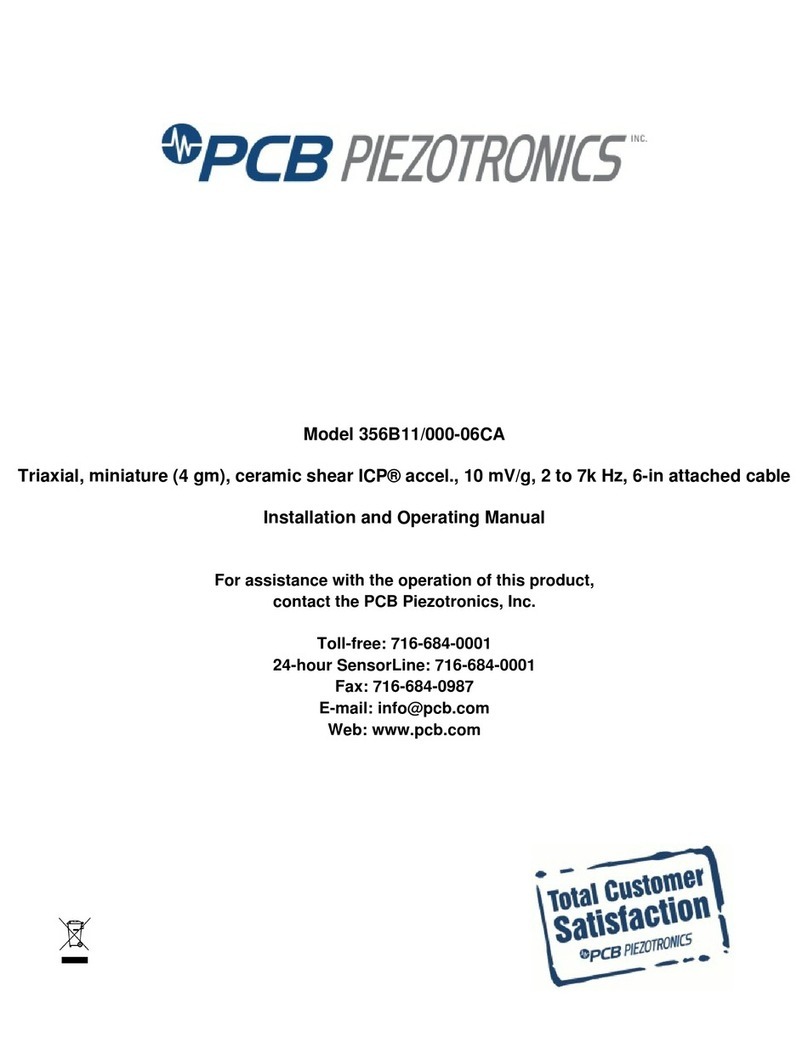
PCB Piezotronics
PCB Piezotronics ICP 356B11/000-06CA Installation and operating manual
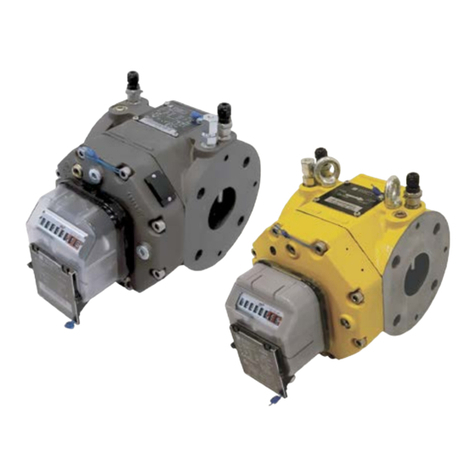
PIETRO FIORENTINI
PIETRO FIORENTINI IM-RM G10 Use and maintenance manual
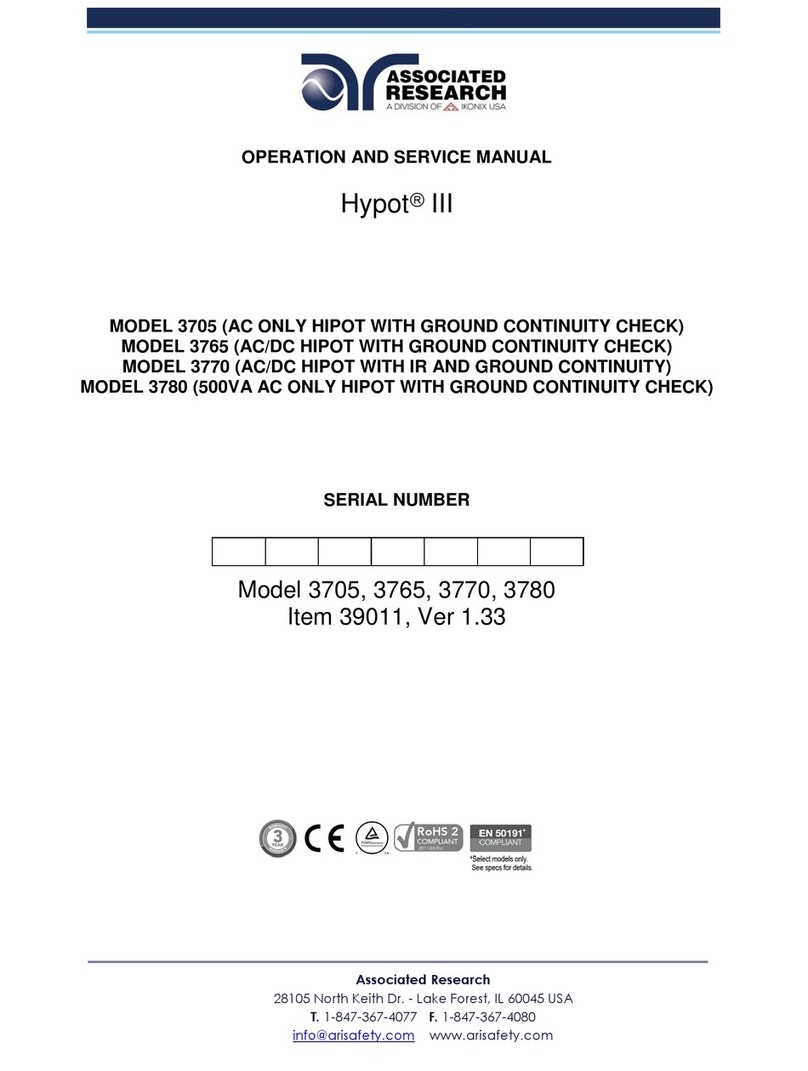
IKONIX
IKONIX Associated Research Hypot III Operation and service manual
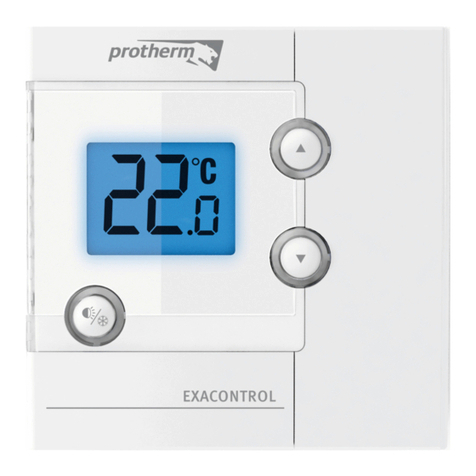
Protherm
Protherm Exacontrol operating instructions
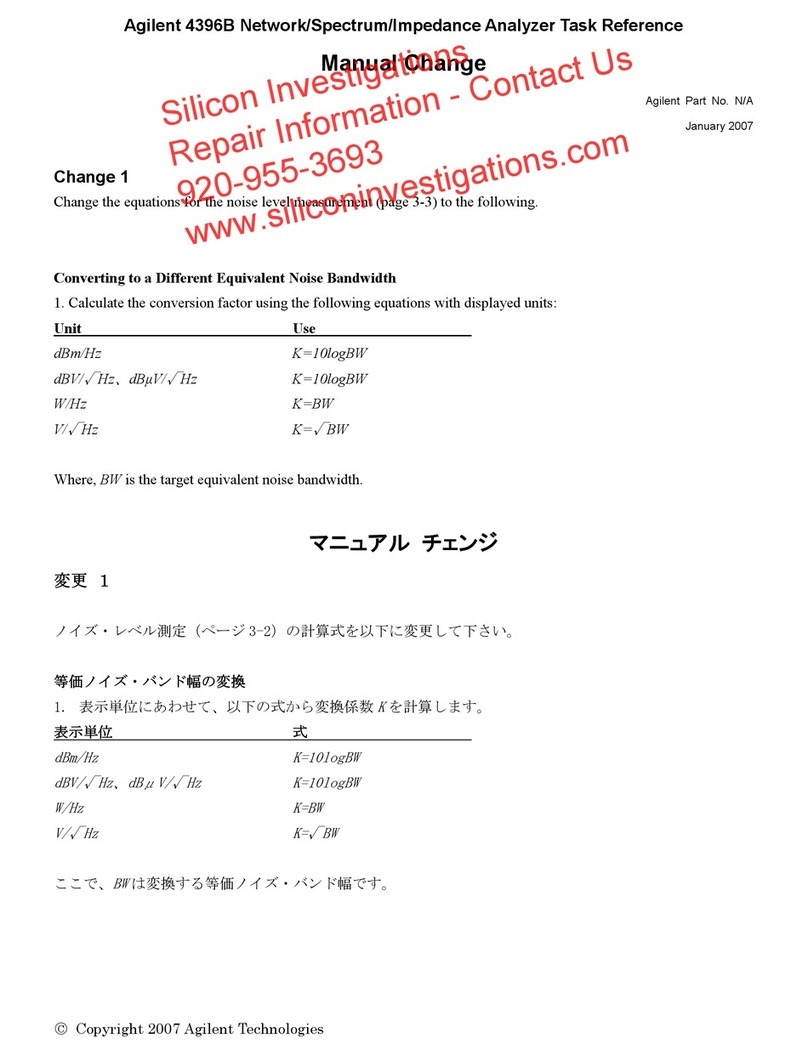
Agilent Technologies
Agilent Technologies Agilent 4396B manual

Projoy Electric
Projoy Electric PEEM-S100 user manual
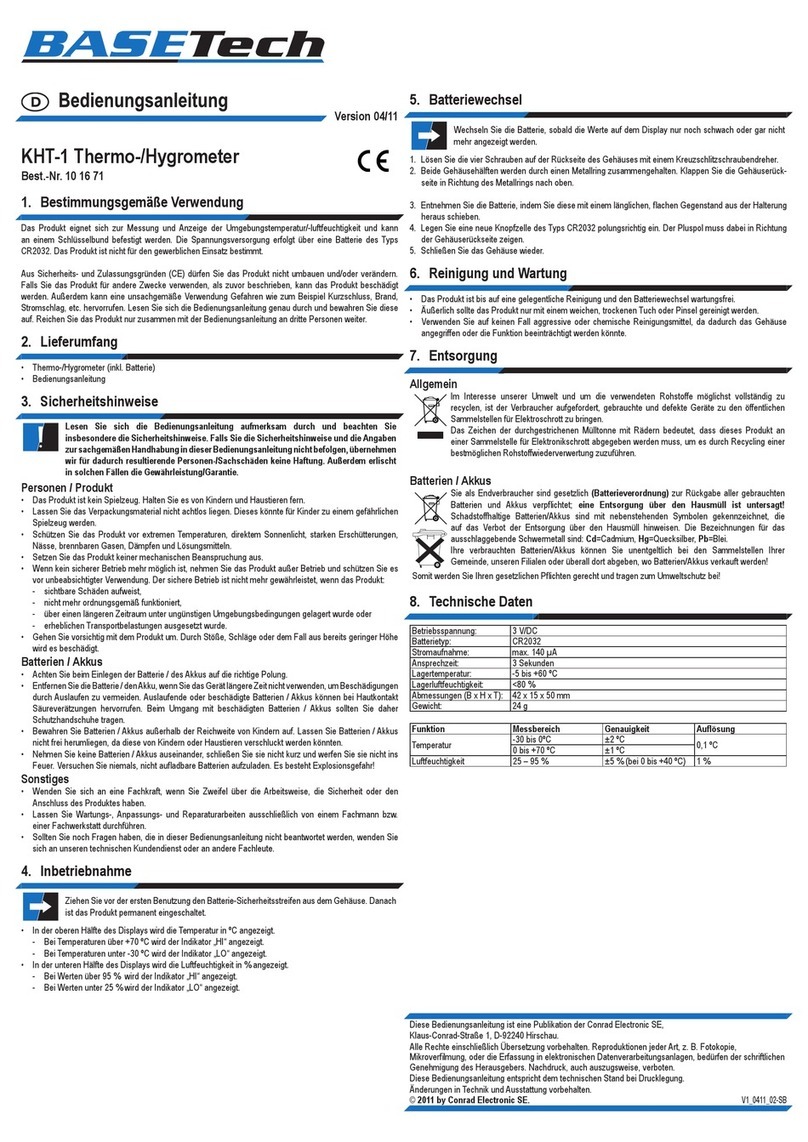
BASETech
BASETech KHT-1 operating instructions
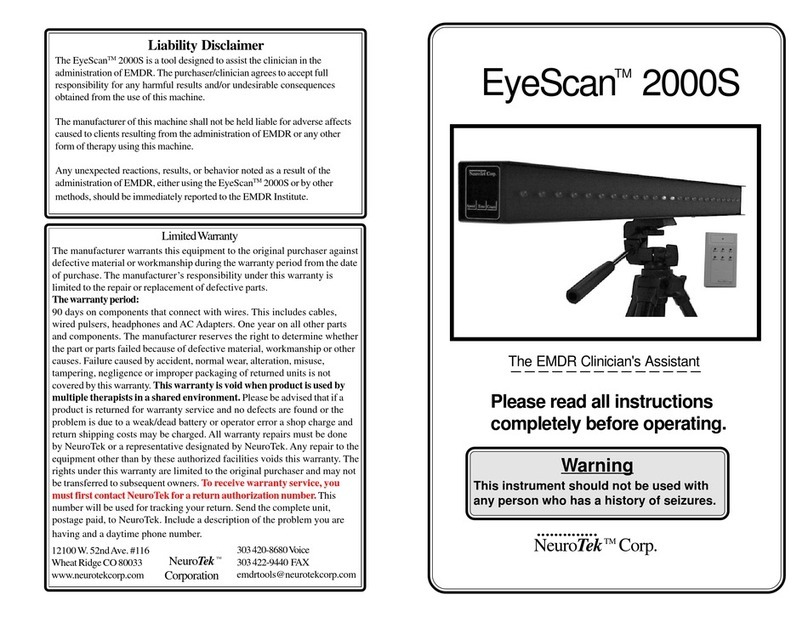
NeuroTek
NeuroTek EyeScan 2000S operating instructions
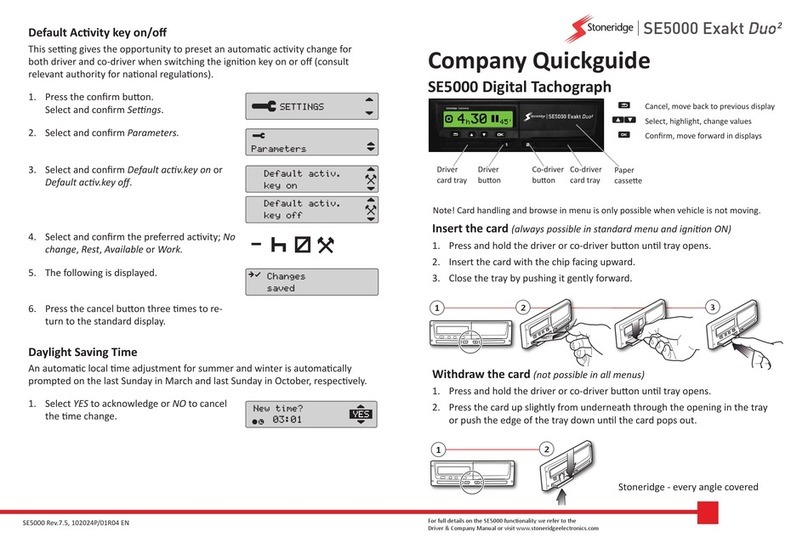
Stoneridge
Stoneridge SE5000 quick guide
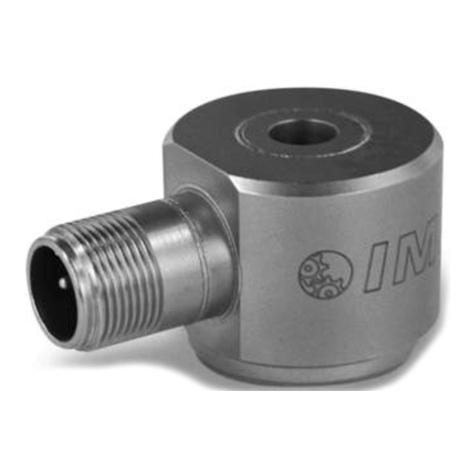
PCB Piezotronics
PCB Piezotronics IMI SENSORS 625B00 Installation and operating manual
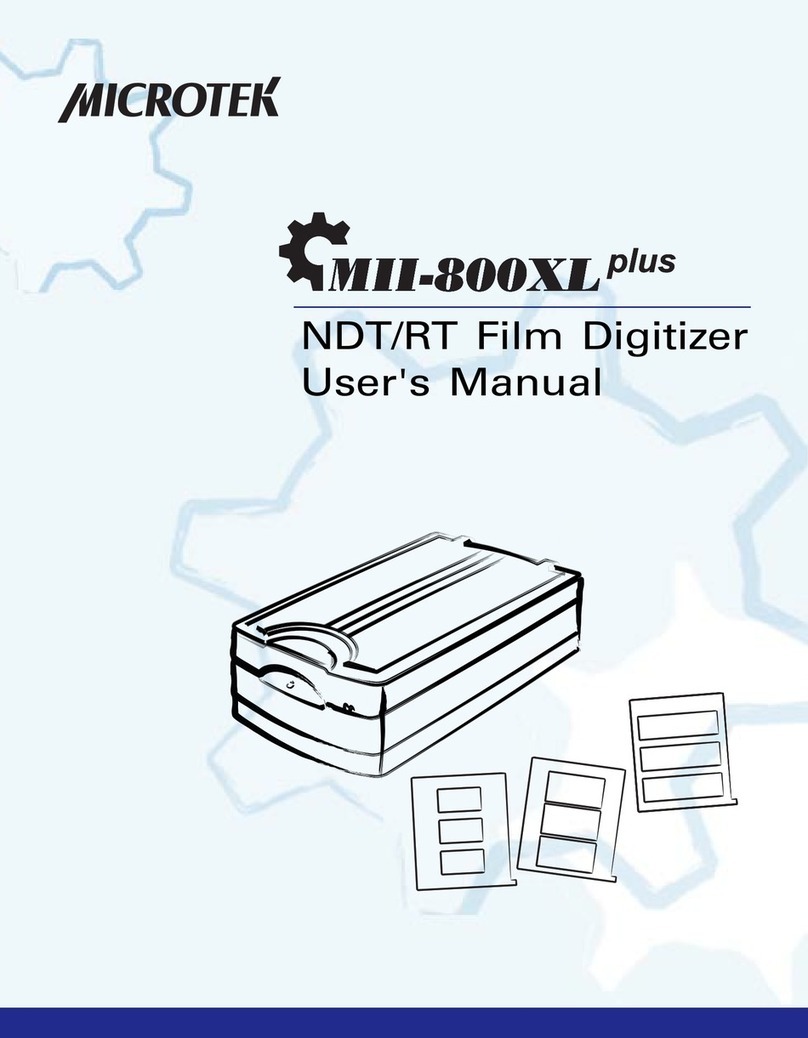
Microtek
Microtek MIL-800XL Plus user manual

Dräger
Dräger P7-TD Quick reference guide