Chziri ZJR1 Series User manual

ZJR1 SERIES
SOFTSTART USER'S MANUAL

Thank you for your purchaseof ZJR1 seriesof motor softstarter produced by
Ziri Electrical TechnologyCo.,Ltd. (hereinafter referredto as ZIRICompany).
This manual introduces the installation,operation, function setting,trouble
shooting and etc.of ZJR1 motorsoft starter.
Incorrect installation oruse may resultin damage orother accidents.
Do read allinstructions in detailbefore installing, andfollow this manual
strictly during installing,wiring and operating.
Please keep thismanual handy forquick reference inthe future.
If there areany doubts orquestions, please contactthe Technical Service
Center of ZIRICompany.
Foreword Table of Contents
Chapter 1 Introductionto the Product.............................................1
1.1 Safety Instructions....................................................1
1.2 Product Inspectionupon Arrival..................................2
1.3 Demonstration ofthe Specifications Label and Model...2
1.4 Outline ofthe Product............................................... 3
1.5 Models andSpecifications......................................... 4
1.6 Technical Indications.................................................5
Chapter 2 Installationand Wiring...................................................6
2.1 Operating Conditions................................................6
2.2 Installation............................................................... 6
2.3 Wiring................................................................. 7-12
2.4 Selection of Peripheral Appliances............................13
Chapter 3 Operation Panel and Display....................................... 14
3.1 Operation Panel Instructions.................................... 14
3.2 Panel Operation................................................. 14-15
3.3 Panel Display Instructions........................................16
Chapter 4 Operation...................................................................17
4.1 Inspection before Operation.....................................17
4.2 Operation...............................................................17
Chapter 5 Description of Function Parameters............................. 18
5.1 Schedule of Function Parameters.............................18
5.2 Detailed Description of Function Parameters.........19-26
Chapter 6 Trouble Protection & Treatment.................................... 27
6.1 Schedule of Protection Operating..............................27
6.2 Trouble Diagnosis and Troubleshooting.....................28
Chapter 7 Structure and Sizes................................................29-30
Chapter 8 Quality Warranty..........................................................31
Appendix....................................................................................32

Chapter 1 Introduction to Product
The installation and wiring of motor soft starter should be
operated only by professional technicians who should read this
manual in detail before installing and wiring.
Do not perform wiring while the motor soft starter is POWER
ON. Be sureto perform this step onlyafter the power is
disconnected. Otherwise, there is the danger of electric shock.
Be sure the motor chosen should be matched with the motor
soft starter. Do follow this manual while perform installing and
wiring.
While wiring, the three-phase input power supply should be
connected to the terminals R, S and T. The output wire of the motor
should be connected to the terminals U, V and W. Otherwise, it may
cause severe damage to the motor soft starter.
Do not install any capacitor between the output terminals U, V
and Wand the motor. Otherwise, it may cause damage to the motor
soft starter.
The electronic elements inside the motor soft starter are very
sensitive to static. Do not touch the appliances on the circuit board
by hand before anti-static measures are taken.
The ground terminal ( G) should be properly, solidly and
separately grounded .
Once the motor soft starter is installed, please cover pigtails
in the input and output ports with insulated sheath or tape.
When the motor soft starter is under remote control, do lock
the keyboard control to avoid accidence due to error operation.
Do cut off the power supply when the motor starter is in
maintenance to guarantee safety.
Chapter 1 Introduction to Product
1.2 Inspection upon Arrival
This product isguaranteed a highlevel of qualitywith strict outgoing
inspection, crushproof andshockproof packaging. Butthere is the
possibility of damagein transit bycarelessness. So itis necessary to
unpack the packageupon receipt ofthe product andperform the following
steps:
Check the motorsoft starter whetherthere is anydamage caused during
transit.
Check the specificationslabel of themotor soft starterand make sureit
matches the productpart number you ve ordered.
Check whether theitems in thepackage are inreadiness or not,which
include 1 motorsoft starter,1 user manualand 1 conformitycertificate.
In case thereis any problemwith the above-mentionedcontents, damage or
deficiency, please contact yourdealer or ZiriCompany immediately.
1.3 Demonstration of the Specifications Label and Model
1.3.1 Demonstration of the Specifications Label
Model
Power
Input Power Supply
Rated Electric Current
Name of Product
Production Ordinal
1.3.2 Demonstration of the Model
Biz Code
Motor Soft Starter
Design Serial Number
Indicated Voltage
Adaptive
Motor Power:

1.4 Outline ofthe Product
Chapter 1 Introduction to Product
Connect to the bypass contactor
(L21, L22, L23) Input Terminals of Power
Supply (R, S,T)
Operation Panel
Control Terminal
Connect to themotor
(U, V, W)
Nameplate
Base
Circuit Board Cabinet
Connect to the bypass contactor
(L21, L22, L23)
Input Terminals of Power
Supply (R, S,T)
Operation Panel
Base
Control Terminal
Connect to themotor
(U, V, W)
Circuit Board Cabinet
Chapter 1 Introduction to Product
1.5 Models and Specifications
Schedule of Models & Specifications
Product Model
Max Adaptive
Motor
Power(KW)
Input Voltage
(V)
Rated Current
(A)
Weight of
Type Z Kg

Chapter 1 Introduction to Product
1.6 Technical Indications
Item Item Description
Input
Power
Supply
Input Voltage
Frequency
Adaptive Motor
Starting Times
Control Modes
Start Modes
Stop Modes
Protective
Functions
Three-phase 380V-15% 415+10%
50/60Hz
Squirrel-cage three-phase asynchronousmotor
It is recommendednot to exceed20 times perhour
1) Operation panelcontrol; 2) Operation panel + external
control; 3) Externalcontrol; 4) External control + COM
control; 5) Operationpanel + external + COM control; 6)
Operation panel +COM control; 7) COM control; 8) No start
or stop operation.
1) Current-limiting start;2) Voltage ramp start; 3) Kick
start + current-limitingstart; 4) Kick start + voltage
ramp start; 5)Current ramp start; 6) Voltage current-
limiting double closed-loopstart.
1) Soft stop;2) Free stop.
1) Open loopprotection for external instantaneous stopterminals; 2)
Over-heat protection for soft starter; 3) Protection for too long starting
time; 4) Inputopen phase protection; 5) Outputopen-phase protection;
6) Unbalanced three-phase protection; 7)starting overcurrent
protection; 8) Running overload protection; 9) Undervoltageprotection
for power voltage;10) Overvoltage protection for powervoltage; 11)
Protection for faultparameter setting; 12) Load shortcircuit protection;
13) Autorestart or incorrectwiring protection; 14) Incorrect wiring
protection of external control stopterminals.
Ambient
Structure
Place to be
used
Altitude
Ambient
Temperature
Ambient
Humidity
Vibration
Protection
Class
Cooling
Pattern
Indoor location withgood ventilation free from corrosive gas
and conductive dust.
Below 1,000M. Deratingshould be performed before use
if the altitudeis higher than 1,000M.
-10 +40
90%RH without dewcondensation.
<0.5G
IP20
Natural wind cooling.
Chapter 2 Installation and Wiring
2.1 Operating Conditions
Use the motorsoft starter in the following environmental conditions:
Altitude: Maximum 1000mabove sea level. Derating should be performed
before use ifthe altitude is higher than 1,000M.
Ambient Temperature:-10~+40
Ambient Humidity: =90%RH (Non-condensing)
Place to beused: Indoor places free from direct exposure to sunlight,dust,
corrosive gas, flammablegas, oil mist, steam, drip and salt.
Vibration: <0.5G
Starting Times:=20 times per hour.
2.2 Installation
The motor softstarter shall beinstalled vertically.DO NOT turnupside
down, lay diagonallyor horizontally while installing. Be surethe base is
fixed solidly andevenly.
Toget better coolingeffect and forthe convenience of maintenance,
the motor softstarter shall be installed with enoughspace left, referto the
figure below.
Unit in theFigure: mm Air Outlet
Air Inlet

Chapter 2 Installation and Wiring
2.3 Wiring
The wiring ofmotor soft startershould be operated only by professionals
experienced in highand low voltageelectric circuit andshould read this
manual in detailbefore wiring.
2.3.1 Standard Wiring Diagram
Basic Wiring
Diagram
Circuit Breaker
(MCCB) or Leakage
Circuit Breaker
ELCB
Main Circuit
Bypass Magnetic Contactor
Full VoltageOutput
Delay Output
(Programmable)
Failure Output
Control Circuit
RS485 COM
Analog Output
DC 0-20mA
Instantaneous Stop
Stop
Start
Common Port
Chapter 2 Installation and Wiring
2.3.2 Description of Main Circuit Terminals
TerminalMark TerminalName Functional Description
Main Circuit InputTerminal
Main Circuit OutputTerminal
Bypass Connection
Ground Terminal
Connect to three-phaseinput power
supply.
Connect to three-phaseelectric motor.
Connect to bypasscontactor
Soft starter cabinetground terminal
1 Input Terminals (R, S,T)
Three-phase input power supply should be connected to the input terminals R, S
and T of the motor soft starter after it goes through the circuit breaker. Three-phase
power supply doesnot differ on phase sequence and can be arbitrarily connected.
While wiring, DOconnect three-phase input power supply to the terminals R, S
and T. Otherwise, itmay result in severe damage to the motor soft starter.
It is recommendednot to shutdown the machine by disconnecting the main circuit
power supply orinstall an electromagnetic contactor between the input terminals R,
S, T and the power supply to run or stop the motor soft starter. Do selectRUN or
STOP keys on the operation panel or external control terminals to run or stopthe
motor soft starter.
2 Output Terminals (U, V, W)
The output terminals U, Vand W should be connected to the three-phase motor. If
the motor counterrotates (reverses), just change arbitrarily two phases of U, V and
W.
Do not installa capacitor orsurge absorber betweenthe output terminals U, V, W
and the three-phasemotor. Otherwise,it may result in failure of the motor soft
starter or damageto the devices.
Too long connectingline between the motor and the motor soft starter may result
in overcurrent trip,increase of cutoff current, lowaccuracy of current display of the
motor soft starter. So, it is suggested to use a line not exceeding 50m.
3) Bypass Connection(L21, L22, L23)
The bypass connectionterminals L21, L22and L23 should be connected to the
electromagnetic contactor.No wrong connectionor incorrect phase sequence!
When the startingof the softstarter is finished, the main loop power device (SCR)
will log outand the bypasselectromagnetic contactor willrun simultaneously. At this
time, the motoris brought intonormal service.
4) Ground Terminal ( G)
The ground terminalof motor softstarter should be properly connected to the
ground to avoidelectric shock orfire. The ground wire cannot share a ground point
with any otherstrong current load.They must be connected respectively, and the
ground wire isthe shorter thebetter

Chapter 2 Installation and WiringChapter 2 Installation and Wiring
2.3.3 Main Circuit Connection Diagram
Power Supply
Circuit Breaker orLeakage Circuit
Breaker MCCB or ELCB
Soft Starter
(ZJR1)
AC Contactor
Three-phase Asynchronous Motor
2.3.4 Description of Control Circuit Terminals
1) Cautions forControl Circuit Wiring:
The connecting wire of thecontrol circuit shallbe shielded wireor twisted
pair wire, whichmust be wiredseparately from themain circuit andthe power
circuit. If theconnecting wire ofthe control circuitmust crosscut the main
circuit, they shallintersect at anangle of 90.
The length of the wireshall be asshort as possible(not exceed 30mgenerally)
because the controlcircuit is easilyinfluenced by externalinterference.
2
The recommended wire size ofthe control circuitconnecting wire is 0.75mm .
When external terminalsare selected togive control over start and stop
functions of thesoft starter,please set the code P9 to External Control Enabled .
If there isa request fornon-local control, thetwo-wire control mode is suggested.
2) Diagram of Control Terminals
Bypass
Output
Delayed
Output
Failure
Output Instantaneous
Stop Start Analog Output
Common Port
Terminal
Mark
Terminal
Name Functional Description
Bypass
Output
Operation
Output
(Delayed)
Switch on 01and 02 after soft starter is
completely started tocontrol bypass contactor.
03 and 04 indicate programmable relay output whose
functions are set by the code Pb. If they are set to be the
make contacts (normally open) and output voltage of
the soft starter is enabled to start the motor, then 03, 04
will be switched on. (Contact capacity: AC250V/3A)
Failure
Output
05, 06 indicate programmable failure relay output which
will be closed (switched on) if there is failure of the softer
starter or power, and open (switched off) when energized.
Instantaneous
Stop Input
If 07 isdisconnected from10 or connected to the break
contact (normally closed)of any other protectors, the motor
will stop immediately.
Soft Stop Input
Start Input
Common Port
Analog Output
RS485 COM
When 08 and10 are switchedoff, the motorwill perform
decelerated soft stopor free stop.
Close 09 and10, the motor begins starting andrunning.
10 indicates commonterminal of the contact input signal.
11 and 12indicate AC(0~20mA) analog output usedto monitor
operating current of themotor. Whenthe value is 20mA,which
means the output currentis 4 times asnominal current capacity
of the motor,an external DC ammeter(0~20mA) can be
connected,and the maximum valueof output load resistance
will be 300 .
RS485 COM input/outputterminal, used to connect multiple
soft starters.

Chapter 2 Installation and Wiring
2.3.5 External Control Wiring Modes
Thee-phase Control Mode
Instantaneous Stop
Stop
Start
Common Port
Control Terminal Lead
Two-wire Control Mode
Instantaneous Stop
Stop
Start
Common Port
Switch K on,motor starts; switchK off, motor stops.
Chapter 2 Installation and Wiring
Instantaneous Stop
Stop
Start
Common Port
Instantaneous Stop
Stop
Start
Common Port
2.3.6 Relay & Non-local Control Wiring Diagram
Relay Control Mode
Relay Control Mode
K is connectedto the break contact (normally close)of a protector, i.e., athermal protector.
The factory defaultsetting of K is shorted.

Chapter 2 Installation and Wiring
2.4 Selection List of Peripheral Appliances
Option list ofthe motor softstarter peripheral breakers,electromagnetic
contactors and cables, shownas below:
Soft Starter Models Motor Rated
Current (A)
Motor
Power(KW)
Breaker
Specifications
(A)
Electromagnetic
contactor
Specifications (A)
Cable
Sizes
2
(mm )
Options in the above table are for reference only.
Chapter 3 Operation Panel
3.1 Description of Operation Panel
1) Outline Drawingof Operation Panel
Functional Code Data Code Unit Indicator
Ready Run Failure
Add/Substract
Key
Start Key
Stop Key
Programming Key Confirm Key
Operation Panel KeySet Description
Symbols Key Set Name Functional Description
Run Key
Stop Key
Programming
Key
Confirm Key
Add Key
Substract Key
When "REAdy" is displayed,press this key tobegin starting the
machine, and the startingstate " XXXX" will be displayed.
1) When the machine is in normal operation, press this key to stop and
"_XXXX" will be displayed once the machine stops completely.
2) This key also performs the function of failure state resetting.
When "REAdy" is displayed,press this keyto set the manual. When
"P0030" is displayed,repress this key. When ":"flashes, press
to modify parameters.
1) After parameters are modified in programming, press this key to save. If
there is the indication of "good" with 2 sounds, this indicates the data has been
saved. Repress this key or press the stop key to exit.
2) Press this key when the machine is in operation, the voltage of input power
supply will be displayed.
3) When the power is on, press this key and the parameters you've set will be
restored to the factory default value
1) When entering intomanual setting, press thiskey to modify parameters.
(When the colon doesnot flicker, thiskey is used tomodify the functional code;
when the colon flickers,this key is usedto modify the datavalue.)
2) When the machineis in operation, pressthis key to keepan eye on the
display of current (A),power (P) and overloadheat balance (H).
When the lastdecimal behind the three-figure data > 999 is lightened,then "0"shall
be added behindthe mantissa.
The tone beepswhile pressing any of these keys. Otherwise, this actionis invalid.

Chapter 3 Operation Panel
3.3 Description of Panel Display
Codes
Displayed Description
This indicates thepower is ON.
This indicates themotor soft starteris getting readyand the readiness
LED turns on.
This indicates themotor is inthe state of getting started.
This indicates themotor is inthe running state and the running indicator
turns on.
This indicates themotor is inthe state of soft stop.
This indicates athree-figure voltmeter usedto detect thevoltage of three-
phase ACpower supply.
The specification ofthis soft starteris 22KW/380V.
This indicates thelast failure tip.F:04 indicates aninput open phase occurs.
This indicates nofailure.
This presents thesoftware version ofthe product is Ver3.0.
This indicates totaltimes of successfulstarting.
This indicates theduration of thelast soft starting,regardless of success or
failure.
Note: H1~H9 referto save 9 recently occurred failure tips in arecursive way.
If entering settingmode in none soft start/stop mode, you may gettips.
Press , thenpress to readtips.
Press Enter orStop key in the state of help, you mayexit the help mode.
Chapter 3 Operation Panel
3.2 Panel Operation
Parameter Modification Example
Eg. If thecontrol mode ischanged to externalterminal control, just set
the code P9to 02.
Ordinal No.
Action Display Description
Power on.
Press
Press
for 9 times.
Press
Press Twice.
Press
Getting started.
Enter into thestate of programming.
Enter into functionalselection mode ofthe code P9.
The range ofsetting can bemodified when colon
flashes.
02 indicates externalterminal control.
The data modifiedhas been saved.The action is
escaped to thedefault state and"REAdy" is displayed.
Note: While pressingany of thesekeys, the beeper inside the soft starter will
give out abeep tone.
Power On
Display Display Display Display
DisplayDisplay

Chapter 4 Operation
4.1 Check beforeoperation.
The following stepsshould be inspected and confirmed beforethe soft starteris put
into operation:
Be sure thatthe application ambient and the inputpower supply complywith the
requirements in thismanual.
Be sure thatthe main circuit is properly wired:The input powersupply must be
connected to theterminals R, S and T; theoutput terminals U, V and W must be
connected to themotor; the bypass electromagnetic contactor isinstalled and properly
connected; the groundterminal is reliably and properly grounded.
Be sure thereis no short cutting or shortto ground ofall terminals and electrified
parts. Allterminals, connectors and screws are tightlyfastened.
4.2 Operation
Now start atrial operation after all the inspection steps in 4.1have been done. While in
trial operation, itis suggested that the motor has vacant load. Ifeverything is OK, then
perform on-load running.
Be careful toselect an optimum mode of operation in accordance withspecific
operational requirements. Seethe detail below:
The factory defaultsetting of theproduct operation mode is operation panel control.
The value ofrated power currentPC should be set to the same as theone on the
motor's specifications label.
Press to startthe motor and press to endit.
Be sure themotor has a smooth running without whistler or vibration.
If the motorstarting is not good enough, just change settings ofthe basic functions
of P1.
If the motor'sstarting torque is not powerful enough, just change theinception
voltage code P0(indicating voltage mode enabled) or the current-limiting value code
P3 (indicating currentmode enabled) to raise the torque.
Be sure themotor rotates in the correct direction.
Only after makingsure there is no anomaly,can the motor be put into formal operation.
Notes:
1) If thereis any anomaly of the soft starter or themotor, or there is adisplay of the
fault code F XX, juststop operation immediatelyand deal withit in accordance with
the protective requirementsin Chapter 6.
2) If theon-spot ambient temperature is lower than -10 , please restartthe machine
more than 30minutes lather after it is energizedand preheated.
Chapter 5 Description of Function Parameters
5.1 Schedule of Function Parameters
Function
Code Function Name Setting Range Default
Value MEMO
Inception Voltage
Period of Starting
Period of SoftStop
Starting limitation Current
Max. WorkingCurrent
Undervoltage Protection
Overvoltage Protection
Starting Modes
Protection Classes
Control Modes
Parameter Protection
Programming Output
Motor Rated Current
Motor Protection
00: current limiting;01: voltage
ramp; 02: kick+ current-limiting;
03: kick +voltage ramp; 04:
current ramp; 05:voltage and
current-limiting double closedloop
00: primary; 01:light load; 02:
standard; 03: heavyload; 04:
advanced
00: operation panel control;
01: operation panel +external control;
02: external control;
03: external control +COM control;
04: operation panel+ external + COM
control;
05: operation panel +COM control;
06: COM control;
07: start/stop disabled
00: parameter modification disabled;
01: parameter modification enabled
00~19 detailed in Page24 Functional
Code Pb
Set according to
specifications.
Notes:
1) Idle keysfor over 2 minutes, the machinewill escape from the setting state
automatically.
2) Do notset parameters during soft start orsoft stop. Set them in otherstates.

Chapter 5 Description of Function Parameters
5.2 Detailed Description of Function Parameters
Functional Code P0 Inception Voltage Setting Range:30~70% Factory DefaultSetting: 30%
Functional description: Thisfunction is used to set thevoltage value of motor soft starter when
it is beingstarted.
Note: Voltage ramp modeis enabled; Set the code P7to "1", thevalue can be modified; Set P7 to
"0",. the inceptionvoltage will be40%.
Functional Code P1 Soft Starting Time Setting Range:2~60S Factory Default Setting: 16S
Functional description: Thisfunction is used to set thetime spent by the motor from inception
voltage to ratedvoltage.
Note: Voltage ramp modeis enabled; Set the code P7to "1", thevalue can be modified.
Functional Code P2 Soft Stop Time Setting Range: 0~60S Factory Default Setting: 00
Functional description: Thisfunction is usedto set the time spent by the motor from
being just stoppedat rated speed to full stop.Set this valueto "0", there is a free stop.
Note: There aretwo stop modesfor motor soft starter: soft stop and free stop.If the
machine has anone-to-multi system, then set the valueto "0".
1 Soft Stop
If the codeP2 is not set to "0",then soft stopmode is selected. The figure belowis the
output current waveform inthe mode ofsoft stop. Underthis condition, the motor is
powered by athyristor shifted from a bypass contactorto a softstarter; the output
voltage of thissoft starter gradually decreasedfrom full voltage till it stops completely,
thus the motordecelerates smoothly and mechanicaloscillation can be avoided. The
output cut-off voltageof soft stopis equal to the Inception Voltage.
In the modeof soft stop, surf of waterpump loads canbe reduced or even removed,
and large currentimpulse caused bysoft stop can be reduced. Thecurrent limitation
value of softstop is a percentage reckoned on thestarting current-limiting value.
Chapter 5 Description of Function Parameters
2 Free Stop
If the codeP2 is set to "0", thenfree stop modeis selected.
In this stopmode, once stop command is received,the soft starterwill disconnect the
bypass contactor anddisable voltage output of the thyristor. Then themotor will
gradually shutdown dueto load inertia. To avoid open phaseerror report, P2should be
set to thismode if the soft starter adoptsone-to-multi wiring method.
Toextend the servicelife of soft starter, free stop mode isgenerally preferred ifthere
is no needto adopt soft stop mode. Infree stop mode,instantaneous output is
completely disabled, thusinstantaneous impulse of heavy current canbe avoided. ZJR1
series of softstarters provide 6 working modes applicableto various kindsof motors
and loads. Sousers should choose a proper oneaccording to different applications.
Functional Code P3 Starting Limitation Current Setting Range: 50~500%Default Setting: 400%
Functional description: Thisfunction is usedto set the peak output currentvalue of a
motor soft starterwhen it is starting. The formulais: set value motor rated current
(Function PC)= peakcurrent (unit: A) that islimited by a motor softer starter to be output.
Note: Current limitingmode enabled; If the code P7is set to "0", the modification will be
valid; If P7is set to "1", the currentlimiting value willbe 400%.
Functional Code P4 Max. Working Current Setting Range: 50~200% Default Setting: 100%
Functional description: Maximumworking current refers to maximum current
performing sustainable operationwhose value is reckoned on thebasis of theset
value in thefunctional code PC. If the currentexceeds the maxvalue, there will be an
inverse-time thermal reliefprotection.
Note: Modification willbe valid if the code P7is set to"0".
Functional Code P5 Undervoltage Protection Setting Range: 60~90% Default Setting: 80%
Functional description: Whenthe actual workingvoltage is lowerthan the set
value, then protectionfor motor soft starter is disabled and the LEDdisplay F09.
Functional Code P6 Overvoltage Protection Setting Range: 100~130% Default Setting: 120%
Functional description: Whenthe actual workingvoltage is higherthan the set
value, then protectionfor the motor soft starter is disabled and theLED display F10.
Functional Code P7 Starting Mode Setting Range: 00~05 Default Setting: 01
1) Current-limiting Start
If the codeP7 is set to "0" (indicatingcurrent limiting), thencurrent starting
mode is selected.The figure belowis a current change waveform of a motor inthe
mode of current-limitingstart. "l1" in the figure refersto the setvalue of starting
current-limiting. When themotor starts, theoutput voltage will rise rapidly tillthe
motor current reachesthe set current-limiting value "l1" and

Chapter 5 Description of Function Parameters
will not goup any more. Then, with gradualraise of output value, the motorwill
accelerate gradually.When the motorspeed reaches the rated speed ofrotation, the
bypass contactor willattract (kick on) and the output current will godown rapidly to the
motor rated current"le" or below. Thus thestarting process is finished.
Even if themotor has a light load or the set valueof current-limiting is big, there is
still the possibilitythat the maximum current of the motor during startcan not reach the
set value ofcurrent-limiting. Current-limiting start mode is usually applied on the
occasion where strictlimitation of current is required.
2) Voltage Ramp Start
When the code P7 is set to "1"(voltage), then voltagestart mode is selected. The figure
below is awaveform of output voltage during voltage limiting ramp start.U1 in the figure is
the starting inceptionvoltage. When the motor isstarted and itscurrent does not excess
400% of itsrated value, the output voltage of soft starter willjump up to U1, then the output
voltage will risegradually as the set starting parameter, and themotor will accelerate with
voltage rise. When the voltage reaches the ratedvoltage Ue, themotor will run at rated
rotation speed andthe bypass contactor will pickup, thus the start-up procedurewill be
completed.
Starting Time:T is the control parameter derived by standard load under standard
experimental conditions, basedon which the soft starter is able to acceleratethe motor
smoothly to completestarting process through the control over output voltage butnot
through the mechanicalcontrol over time (t) regardless of whether the motoris accelerated
steadily. Therefore, if thereis a light load, the starting time will tendto be lessthan the set
starting time. Itis normal if the machine can be started smoothly. Generally speaking,
voltage ramp startmode is applicable to the occasion where there isno strict requirement on
starting current buta high requirement on the stability of starting.
Chapter 5 Description of Function Parameters
3) Kick Start
When the code P7 is set to "2"(kick + current-limiting) or "3" (kick + voltage),then
kick start modeis selected. The figure belowis the change waveform of output in kick
start mode. This start mode can be selectedin case there is a failure start of themotor
due to influenceof the machine's static friction force on theoccasion of heavy loads.
While the machineis just started, DO feed afixed higher voltage to the motor and keep
it for ashort period of time so asto smooth awaystatic friction force of motorloads and
enable the motorrotate, and then select a startmode of current-limiting or voltage
ramp.
Before selecting this mode, it is strongly recommended to startthe motor bynon-
kick starting. Then select this mode ONLYAFTER the motorfailed to start.DO keep
clear of kickstart as possible to reduce unnecessary impulse ofstrong current.
4) Current RampStart
When the codeP7 is setto "4" (current ramp), then currentramp start modeis selected.
The figure belowis a waveform of output currentin the modeof current ramp start. "l1"
in this figurestands for current-limiting value set bythe code P3,and T1 standsfor time
set by thecode P1.
Current ramp startmode is applicable to bipolar motorowing to its strong
accelerating capacity.This mode canalso shorten thestarting period of time within a
certain range.

Chapter 5 Description of Function Parameters
Functional Code PA ParameterProtection Setting Range:00~01 Factory Default Setting: 01
Functional Description: Thisfunction is usedto set whether the internal parameters
of the motorsoft starter are allowed to bemodified.
00: Parameter modificationdisabled; 01: Parameter modification enabled.
Functional Code Pb Programmable Output Setting Range: 00~19 Factory Default Setting: 07
Code Pb isused to set the action time for operation outputrelay.
The output functionof programmable relayprovides 2 working modes:
programmable sequential outputand programmable status output.
When Pb isset to 0~4 (10~14), programmable output works in themode of time
output0. The setstarting moment ofthis output is seen in the table below:
Valuesset by Pb
Moment of
Programmabl
Output
When ordering
the command
of start
When being
started
When bypass
runs
When ordering
the command of
stop
When
shutdown is
completed
This working mode is used in an immediatestate and therelay acts at the moment
when the stateset by Pb just begins. The reset momentof this output will be completed1
second s later afterthis state ends up. Eg.: The factory defaultsetting value ofPb is 7,
which means thesoft starter is in a hold mode when energized and therelay attracts
at the sametime. If the soft starter receivesstart command atthis moment, then the relay
will be disconnected.
Programmable sequential output mode takes the whole processof a startas its control
cycle. If themotor is restarted, the previous programmingoutput will automaticallybe
interrupted and thisprocedure shall be preceded again.
If Pb isset to 5~9, the programmable outputworking and stateoutput mode, and the
set working stateoutput will be shown in thetable below:
Valuesset by Pb
Moment of
Programmabl
Output
Fault State Operation
State
Hold State Starting State Bypass State
Programmable state output is used to indicate theworking state ofsoft starter. The
factory default setting value of Pb is 7,which indicates holdmode of softer starter. In
this state, themotor can be started. When programmable output isin fault state, it
indicates motor failure (-F05, -F06, -F07, -F08, -F12), which is different from the
function of failureoutput terminals. Operation state refersto non-hold or non-fault
state, including suchthree procedures as start, bypass andsoft stop.
If Pb>9, thereset state of programmable output ( external terminals) changes
from open toclose, that is, reversed phase output.Flexible use ofprogrammable relay
output functions cansimplify external control logic circuit.
Chapter 5 Description of Function Parameters
5) Voltage and Current-limitingDouble-closed Loop Start
When the codeP7 is setto "5" (double closed-loop), then thisstart mode is
selected. Voltage and current-limitingdouble-closed loop startmode, with
adoption of voltageramp and current-limiting double-closed loop control,is a kind
of comprehensive startmode that both steady start andstrict current-limiting are
required. It usesa pre-reckoning method for estimating theworking state of the
motor.
The waveform ofoutput voltage inthis mode always fluctuates according to
different conditions ofthe motor andloads.
Functional Code P8 Protective Class SettingRange: 00~04 FactoryDefault Setting: 04
To adaptto different applications,this motor softstarter provides 5 protection classes,
namely, 0:primary class; 1:light load; 2: standard, 3 heavyload; 4: advanced,which
are set bythe code P8.
Primary protection, disablingthe function ofexternal instantaneous terminalsand only
remaining overheat protection,shortcut protection andinput open phaseprotection
while starting, isapplied to some emergency occasions, i.e.,fire pump etc..
Light load, standardand heavy load protection classes havefull protection functions.
Their distinguish liesin different timecurves of motor's overload heat protection.
Refer to thetable below and the figure inpage 26 to see time parametersfor motor heat
protection.
The protection standardfor advanced protectionis even stricter. Functional parameters
for the restprotection classes are set the sameas the standard protection. See thetable
below for differentprotection classes andheat protection set by the codeP8.
P8 Setting 0 (Primary
Class)
1 (Light
Load)
2
(Standard)
3 (Heavy
Load)
4
(Advanced) Description
Overload
Running
Protection
Classes
Overcurrent
Starting
Protection
Time
Class 2 Class10 Class 20 Class 10
3S 15S 30S 15S
In accordance
with
IEC60947-4-2
standard.
Based on that
the starting
current is more
than 5 times the
set value.
Overload
Running
Trip Time
Lists
Current
Multiple
(l/le)
Trip Time(S)
Numerical
values in
this table
are typical
ones.
Functional Code P9 Control Modes SettingRange: 00~07 FactoryDefault Setting: 01
00: operation panelcontrol;01: operation panel + external control;02: external
control;03: external control+ COM control;04: operation panel + external + COM
control;05: operation panel+ COM control;06: COM control;07: start/stop
disabled

Chapter 5 Description of Function Parameters
Functional Code PC Motor Rated Current Setting Range: 11~1200
Factory Default Setting:Set according to the specifications
Function Description: Thisparameter should beset in conformity with rated current
value displayed onspecifications label of the motor.Otherwise, it may cause big
deviation between startingcurrent and protective current. The motorrated current
set by PCshould not be 20% lower thanthe nominal currentof soft starter. The
flexibility tolerance ofprotective trip action will increase ifthere is less motor rated
current set byPC.
Functional Code Pd Motor Protection Setting Range: 00~90 Factory Default Setting: 00
1) Descriptions ofProtective Functions
This motor softstarter has perfect protective functions toguarantee safety whileusing
soft starter andmotor. Whilein use, DO set proper protectionclasses and protection
parameters according todifferent circumstances.
Soft Starter OverheatProtection: Overheat protection enabled when temperaturerises
to 90 5 and disabled whentemperature falls to 60 (lowest).
Input open phaseprotection lag time: <3S
Output open phaseprotection lag time: <3S
Three-phase Unbalance ProtectionTime: <3S. Based on therule that all phases of
current deviation islarger than 50 10%, when loadcurrent is 30% lower than the
nominal rated valueof softer starter, the decisiondatum deviation will be enhanced.
Overcurrent Starting ProtectionTime: Thisrefers to the protection time thatis
successively 5 timeslonger than the maximum working currentset by thecode P4. See
protection TimeTable in Page 23.
Overload Running ProtectionTime: Thisrefers to the inverse time thermalrelief
protection based onthe maximum working current set bythe code P4.See the curve of
trip protection timein the figure on page 26.
Power Supply UndervoltageProtection Lag Time: When powersupply voltage is40%
lower than limitvalue, the protection time will beless than 0.5second; when the
power supply voltageis lower than the set value,the protection timewill be less than 3
seconds.
Power Supply OvervoltageProtection Lag Time: When powersupply voltage is130%
higher than limitvalue, the protection time will beless than 0.5second; when the
power supply voltageis higher than the set value,the protection timewill be less than
3 seconds.
Load Shortcut ProtectionRetarding Time: <01 second. Ifthe current is 10 times or
more as nominalrated current of the soft starter, than afuse or shortcut device shall be
used.
The above timeparameters are set for the periodfrom valid signalsare detected to trip
protection command isgiven. They arefor reference only.
If protective functionsof this soft starter do notcomply with users needs, then
special protective devicesshall be used to insure safety.
Chapter 5 Description of Function Parameters
2) Protective Trip Curve
T(S)
Level 10
Level 20
Level 2
Motor Thermal ProtectionTrip Time Curve (HeatState)

Chapter 6 Trouble Protection & Treatment
6.2 TroubleDiagnosis and Troubleshooting
Anomalies Items to Check Solutions
The motor
can't rotate.
Check if thereis abnormal
wiring. Be surethat power
lines are connectedto input
terminals (R, S,T).
Perform correct wiring.Cut off power
supply and thenperform rewiring.
Check if bypasscontactor
works. Be sureterminals 01,
02 have signals.
Check the connectionof bypass contactor.
Check the controland connection ofthe coil
loop of bypasscontactor.
Check if thereis abnormal
display on theoperation
panel.
Refer to page27 "Schedule ofProtection
Operating".
Check if themotor is locked
or there istoo heavy load.
Unlock the motoror lighten theloads.
Keyboard
starting is
disabled.
Check if thereis error tipon
the operation panel.Be sure
that the terminals07, 10 are
open and settingsof the
code P9 iscorrect.
If no errortip is displayed,check the input
power supply.If error tipis displayed, checkif
the terminals 07,08 and 10are open; check
external wiring ofthe terminals andset
parameters of P9properly.
External control
starting is
disabled.
Check if thecode P9 is
set to externalcontrol.
If open circuitsoccur among the terminals 07,
08 and 10,check external wiring of terminals;
set parameters ofP9 properly.Be sure
external control hasbeen set.
The motor rotates
but its speed
cannot be raised.
Check if thereis too heavy
load.
Lighten the loads.Modify parameters;
increase the inceptionvoltage or starting
current.
Starting time is
too long.
Check if thereis too heavy
load. Be sureparameter
settings of thesoft starter are
proper and themotor model
is correct.
Lighten the loads.Set P0 (inception
voltage) P3 (starting limitationcurrent)
and P1 (softstart time) properly. Check
model descriptions ofsoft starter andits
specifications label.
Starting time
is too short.
Check if thereis light
load or tooshort starting
time.
When there isa light load,the starting time
is generally shorterthan the setvalue. It will
be normal ifthere is abalanced start. Set the
starting time ofP1. (current modeinvalid)
Sudden
shutdown
occurs during
operation.
Check external input
terminals.
Check if thereis any loosenconnection
between the terminal 07and 10. Ifthere is an
external protector, checkif the breakcontact
works. Check ifthere is loosenconnecting
wire of externalstop button.
Chapter 6 Trouble Protection & Treatment
6.1 Schedule ofProtection Operating
Protective functions enabledwith an immediate tripping once anomalyof the soft
starter occurs. Referto the descriptions below for warningsand relevant contents
displayed on LED.
Panel Display Warnings Actions & Treatment
Fault cleared!
Faults such asundervoltage, overvoltage, overcurrent,
instantaneous terminal openetc. have been eliminated.
Everything turns tonormal and now the LED "ready" lights
up, indicating themotor can be
started after reset.
External
instantaneous
terminals open
Check the connectionbetween terminal 07 and terminal 10,
or check breakcontacts of other protective devices.
Soft starter
overheat
Check if startingis too frequently operated or the motor
power doesn't matchthe soft starter.
Starting time
too long
Check if startingparameters are improperly set; the load
is too heavyor the power capacity is insufficient.
Input open phase
Check if three-phasepower supply issolidly connected, the
bypass contactor ischucked on theclosed position, the SCR
is shortcut andthe ground wire(G) is properly connected.
Output open
phase
Check if connectingwires of output loop and the motor is
firm, the bypasscontactor is chucked on the closed position,
the SCR isshortcut and the ground wire (G) is properly
connected.
Three phases
unbalanced Check if thereis anomaly of input three-phase power supply
or the loadmotor.
Starting
overcurrent
Check if theload is too heavy or the motor power doesn't
match the softstarter.
Operating overload
protection Check if thereis any too heavy load or improper parameter
set by thecode P4 and PC.
Power supply
voltage below level
Check if thereis error input power supply voltage or
improper parameter setby the code P5.
Power supply
voltage too high
Check if thereis error input power supply voltage or
improper parameter setby the code P6.
Parameter
setting error
Modify settings orpress to restoreto the
default settings ofsoft starter when it is energized.
Load shortcut Check the loador the motor;check if the SCR is shortcut
or over loaded.
Auto restart
wiring error
Check the externalcontrol start andstop terminals if they
are in two-wirecontrol mode.
External control stop
terminal wiring error
When external control mode is enabled, external control
stop terminals willopen, which leadto failure start of the
motor.
Notes:
1)Some faults are correlative,i.e., if there isa report of F02(soft starter overheat), thismay be
concerned with starting overcurrentor load shortcut.Therefore, full considerations shouldbe
taken to have anexact judge on faultsduring troubleshooting.
2)When the soft starterstarts the motor,the operation LED inthe middle of thepanel lights up,
which indicates the machineis in thestate of bypass operation.If bypass contactor failsto
pickup at this time,which results in stopof the motor,check if there isany error or badcontact of
the bypass contactor andrelevant connecting wires.
3)If any protective actionoccurs, press STOP/RESETkey to remove failurestate after
troubleshooting, then restart themachine.

Chapter 7 Structure and Sizes
Chapter 7 Structure and Sizes
7.1 Outline Sizes & Install Sizes
d( )Install a screw
Models Rated
Power(KW)
Rated
Current(A)
Outline Sizes Install Sizes
Net
Weight
(Kg)
Made to Order
Models Rated
Power(KW)
Rated
Current(A)
Outline Sizes Install Sizes
Net
Weight
(Kg)
Notes:
The rated powerand rated currentin the tableabove are the maximum values of a soft starter.
Generally, ratedcurrent matching the motor that hassame power shouldnot excess the rated
current values listedin this table.
If outline sizesdiffer from thevalues above, pleaserefer to actualsizes.
Notes:
The rated powerand rated currentin the tableabove are the maximum values of a soft starter.
Generally, ratedcurrent matching the motor that hassame power shouldnot excess the rated
current values listedin this table.
If outline sizesdiffer from thevalues above, pleaserefer to actualsizes.

Chapter 8 Quality Warranty
1) Warranty Period Under Normal Conditions
We provide guarantees for repair, replacement and return of the
purchase in 1 month from the date of use.
We provide guarantees for repair and replacement in 3 months
from the date of use.
We provide guarantee for repair in 12 months from the date of
use or 18 months from the date of ex-factory.
2) The purchaser enjoys life-long paid service whenever and
wherever he uses a motor soft starter made in our company.
3) Service in the following cases, even within the warranty period,
shall be charged to the purchaser:
Problems caused by mal-operation in violation of this manual,
or caused by unauthorized repair or renovation.
Problems caused by improper use of soft starter that is off
standard and requirement;
Malfunction or damage caused by improper transit or storage
after purchase;
Induced failure or aging of the device due to poor ambient;
Malfunction or damage caused by fire, flood, thunder,
earthquake, abnormal voltage or other natural disasters;
Unidentifiable nameplate, mark and ORD number due to
intentional spoilage;
Delayed or unsatisfied payment in violation of purchase
appointment;
Fail to give an objective description on the use of installation,
wiring, operation, maintenance or else;
4) Defective products should be sent to us for repair, replacement
and return, which can be proceeded only after verifying the
burden of liability.
5) In case there is any quality problem or accident, we merely
promise to bear the above-mentioned responsibilities. Ifa user
needs more guarantees for liabilities, please assure on the
insurance company voluntarily.
Appendix
1 Varieties of Application Loads
This soft startcan meet the requirements of mostheavy loads. Thetable below isfor
reference only.
Varietiesof
Application Loads
Start Ramp
Time (S)
Stop Ramp
Time (S)
Inception
Voltage (%)
VoltageStart
(Maximum Current-
limiting Value)
Current-
limiting
Start
2) RS485 Communication
This soft starter can be connected to PC, PLC or other hosts through a
built-in RS485 standard interface to perform serial communication
(COM). The host can give a command to start or stop the soft starter,
monitor the operation state of the soft starter and modify its functional
parameters. For details of this communication, please refer to RS485
Operating Manual. By using RS485 COM of the soft starter, remote
operation can be realized via a computer such as input of run command,
management on operation state, and one-step writing of functional codes
for multiple soft starters to realize simplified operation while inputting
functional codes.
Main Functions of RS485 COM:
Inputting start or stop command;
Monitoring operation status;
Real-time tracing (i.e., table display of running information);
Once-step reading and writing of functional codes, and saving to the
file;
A separate agreement shall be signed between the two parties of us for
communication software.
Centrifugal Pump
Ball Grinder
Fan
Piston Type
Compressor
Light Load Motor
Elevating
Mechanism
Mixer
Crusher
Screw Compressor
Spiral Conveyor
Leather Belt Conveyer
Heat Pump
Table of contents
Other Chziri Controllers manuals
Popular Controllers manuals by other brands
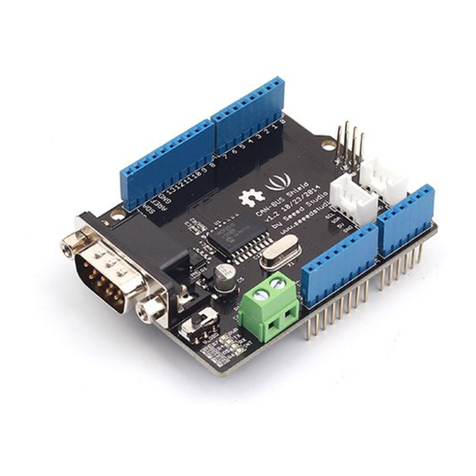
seeed studio
seeed studio CAN-BUS Shield V1.2 manual
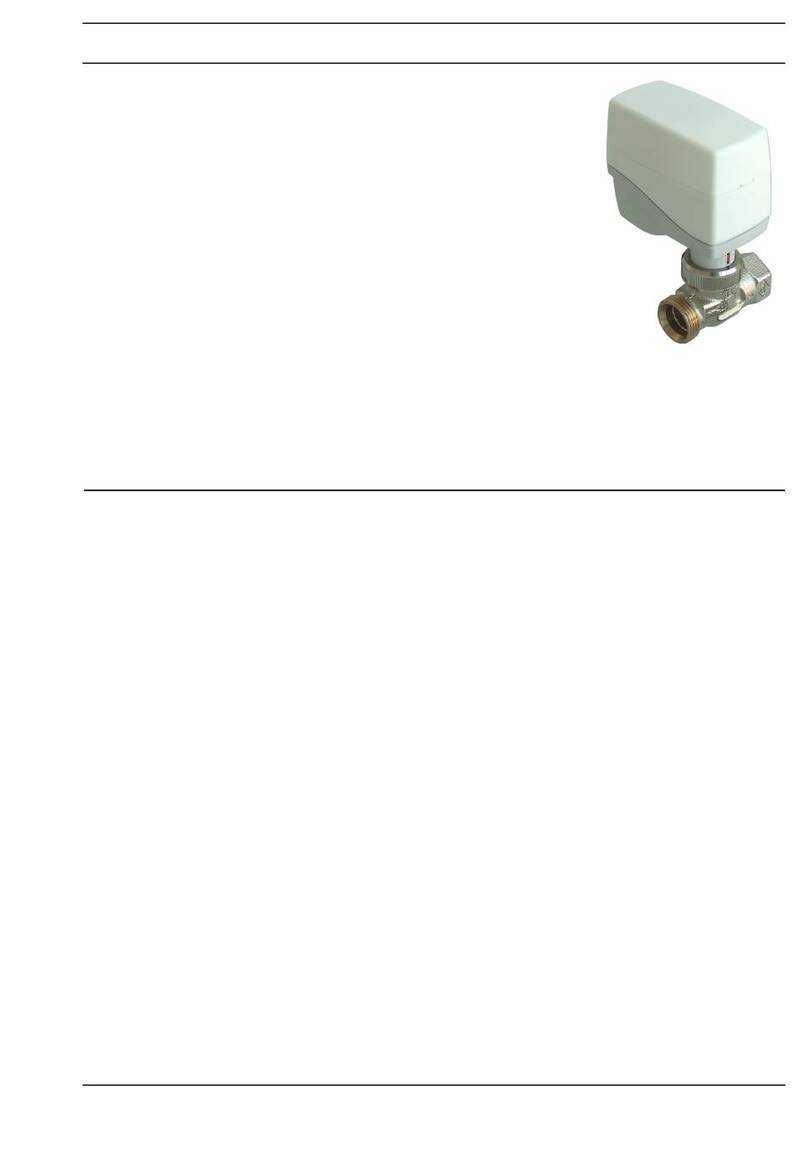
Kieback&Peter
Kieback&Peter MD15-FTL-315 user manual

MB QUART
MB QUART Hifonics TPS-BT1 Quick start installation guide
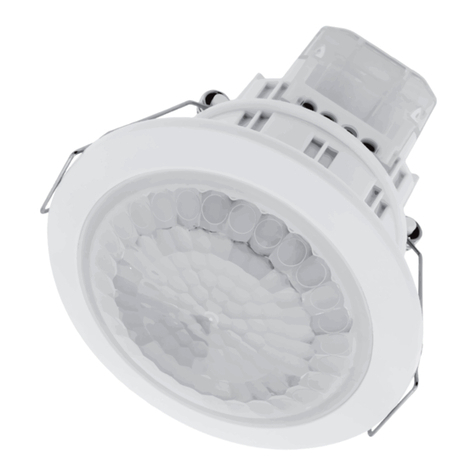
Timeguard
Timeguard PDFM1500N Installation & operating instructions
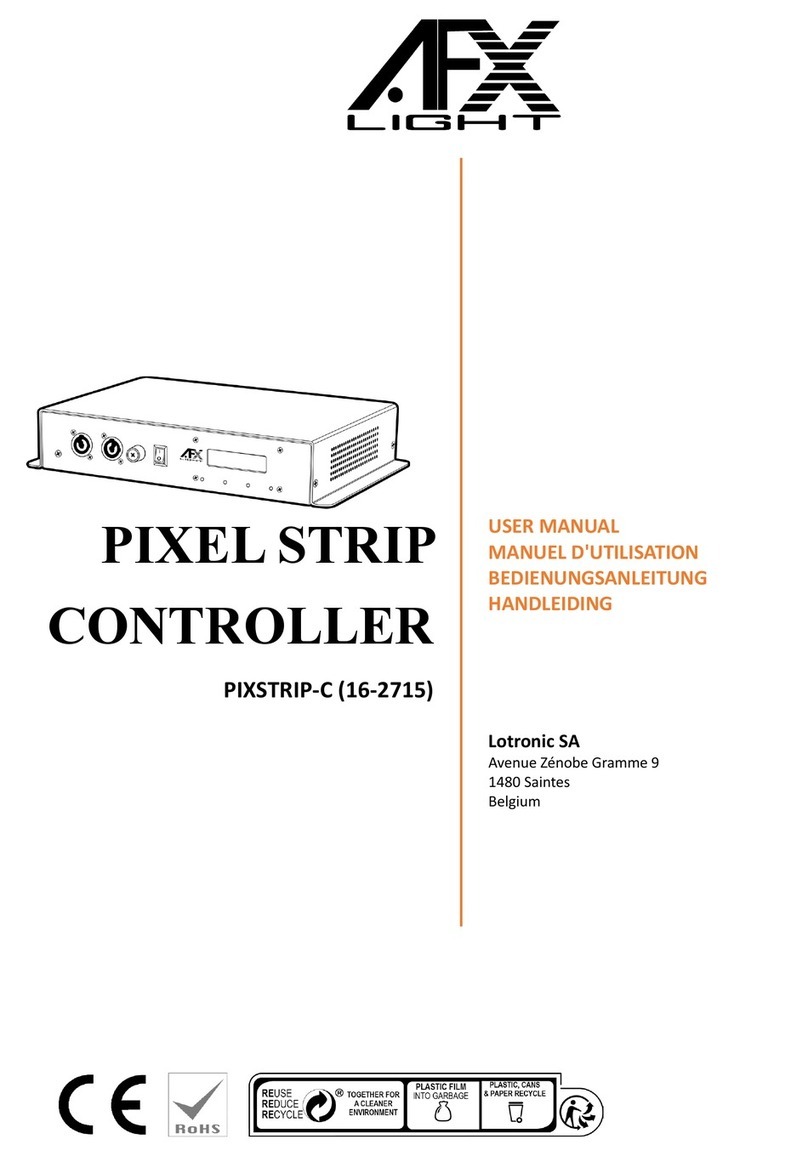
afx light
afx light 16-2715 user manual
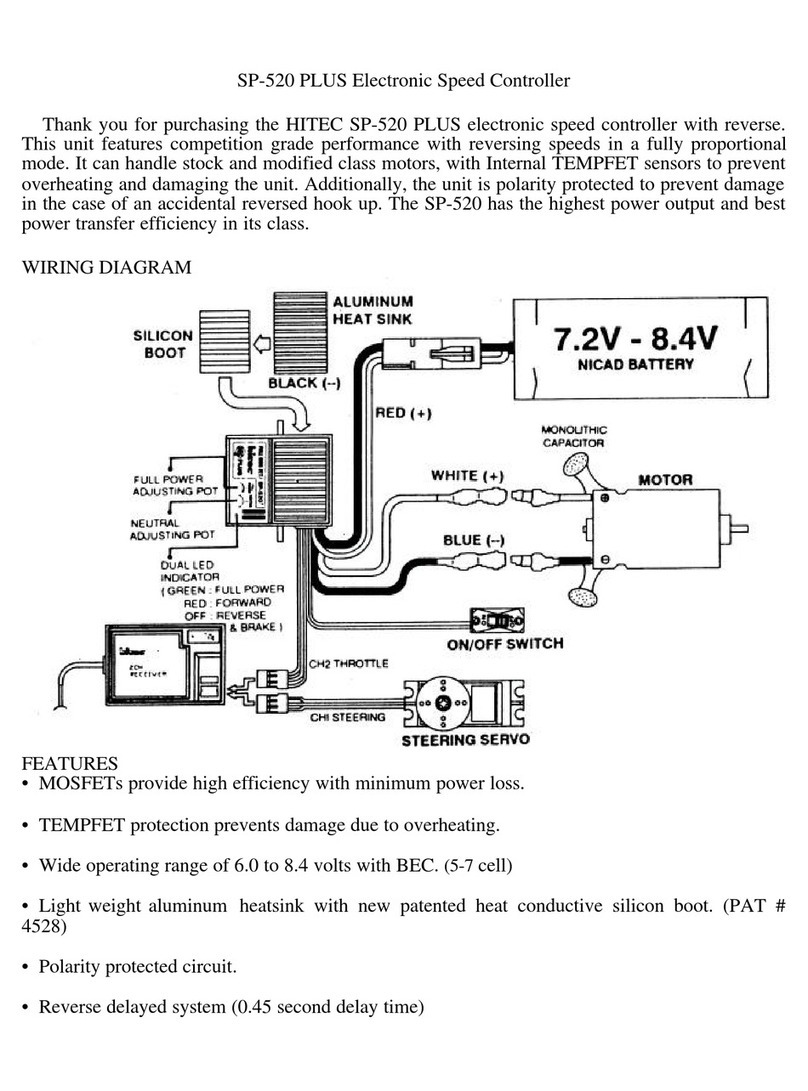
Hi-Tec
Hi-Tec SP-520 PLUS manual