Cissell CF 19 User manual

Manual
Hand foot operated
Utility Press
CISSELL MFG. CO.
831 South First St. / POB 32270
Louisville, Ky. 40232-2270
Phone: (502) 587-1292
Fax : (502) 585-3625
www.cissellmfg.com
Model: CF 19, 24, 41, 45, 47, 50, 52, 220, 226,
439, 441, 444, 446, 448, 487.
M:\HANDBOEK\CISSEL\CFeng
Part No. D0142

Table of contents
1. Machine surfey, operating functions and connections…………………..…... 3
2. Symbols………………………………………………………………………..….. 3
3. Introduction…………………………………………………………………………4
4. Technical data.........................…………………………………………………. 4
5. Installation.................................................................................................... 5
5.1 Transport and positioning……………………………………………………... 5
5.2 Connections……………………………………………………………………. 5
5.2.1 Steam…………………………………………………………………….. 5
5.2.2 Steamline systems……………………………………………….………. 5
5.2.3 Vakuum……………………………………………………………….….. 6
6. Put into operation………………………………………………………………… 6
7. How to operate…………………………………………………..……………. 7
7.1 User Directions…………………………………………………………..…….. 7
7.2 User Instruktions……………………………………………………………..… 7
7.3 Tips fot use…………………………………………………………………….. 7
8. Put out of operation……………………………………………………………… 7
9. Trouble Shooting…………………………………………………………………. 8
10.Maintenance and repairs…………………………………………………………8
10.1 Maintenance………………………………………………………………… 8
10.2 Repairs / Dismanting……………………………………………………….. 9
10.3 Adjustments…………………………………………………………………. 9
11. Spare parts……………………………………………………………………….. 10

1 Machine survey, operating functions and connections
1 Handle : Steaming
2 Wooden handle : Close Head
3 Head
4 Buck
5 Footpedal : Buck steam
6 Footpedal : Vakuum
7 Footpedal : Press and open
8 Adjusting bolt : Adjust footpedal (7)
9 Adjusting knob : Adjust pressure
A. Steam supply ½" BSP
B. Steam return ½" BSP
D. Vacuum line 2"
2 Symbols
Symbols for use, operation and warnings :
Attention!
Caution!
Follow the instructions
Caution, heat!
Do not touch!
Attention! Mind your hands when the press is
closing.
Very important!
Safety aspect!
English - 3

3 Introduction
The presses are for the pressing of all kinds of garments and laundry. This PRESS is hand and foot-
operated.
All the numbers and capitals in this manual indicated in brackets, refer to the numbers/capitals of the
differents machine drawings.
Important:
!Read this manual first before installation and before taking the machine into use.
!All the installation, repair, adjusting and maintenance activities should be carried out by experts.
The press can take a steam pressure of 6 bar maximum. A higher pressure could bring along safety
risks or lead to damage to the machine. Recommended working pressure: 6 bar.
A higher compressed air pressure than 6 bar is not allowed for an higher pressure could bring along
safety
risks or damage the machine. Recommended working pressure: 5 bar.
!Take care for good survey and create enough working space around the machine.
Advice: Keep the manual somewhere near the press.
4 Technical data
Model : CF 19, 24, 41, 45, 47, 50, 52, 220, 226, 439, 441, 444, 446, 448, 487
Type : ../81
../83
../93
Maximum allowed steam pressure :
6 bar
Weight CF 19, 24, 220, 226:
CF 41, 45, 47, 50, 52:
CF 439, 441, 444, 448, 487:
Floor surface CF 19, 24, 220, 226:
CF 41, 45, 47, 50, 52:
CF 439, 441, 444, 448, 487:
220 kg
260 kg
280 kg
945 x 1000 x 1255mm
945 x 1500 x 1255mm
945 x 1500 x 1255 mm
Temperature pressing shoes covered:
uncovered:
approx. 130 ºC
approx. 160 ºC
English - 4

5 Installation
5.1 Transport and positioning
Mind your safety! Wear safety shoes and working gloves.
• Leave the machine on the pallet for transport to its location.
• Avoid shakes.
• Use a lifting device for transport and for moving it into position.
• Handle the machine only by its frame.
• Take care for enough working space around the machine.
• Check the stability and fix the machine with 4 bolts (M10 x 100mm) in case of an uneven floor.
• Push the upper pressing shoe down and remove the rope whitch keeps the shoes together. After
that the upper pressing shoe will rise automatically.
5.2 Connections
When making the connections to the machine, take utmost care to ensure that no dirt or other
materials enter the lines, since this may cause the machine to malfunction.
5.2.1 Steam
Mind your safety! Wear working gloves!
Connection: ½" BSP
Maximum steam pressure: 9 bar.
Recommended working pressure: 6 bar
A : Steam supply X : Steam trap
B : Steam return Y : Blow off cock
W : Shut off valve Z : Non-return valve
Instructions to connect the steam lines:
• Connect the steam lines according to illustration 1.
• Avoid condensation to enter the machine:
Connect the branches of the supply and return Figure 1: Connecting steamlines
lines in such way that they run at least 300mm upward first.
• Flush the connected steam lines with steam from the steam supply.
• Install a steam trap and non-return valve as close as possible to the connection of the machine
(mark the entry and exit).
• Install a shut off valve in both supply and return lines in order to be able to shut off the machine
from the steam lines, for instance for repair activities.
• To get dry steam the connection of a steam trap with non-return valve on the lowest point of the
supply to the drainage (dotted line fig. 1) is recommended. Mark the marking 'entry' and 'exit'.
• Connect the machine to the steam lines.
5.2.2 Steamline systems
Open system
Mount a steamtrap (D) at the end of the stream supply line (B)
and at the end of each connected machine. The condensate will
be led to the watertank (E) through the condense return line (C).
The condensate in the watertank will be pumped in the boiler (A)
through pump (F).
Disadvantage of the open system is the loss of energy and an
increasing fault sensibility.
English - 5

Closed system
The condensate ends up in the boiler (A) through a down going
condense return line (C). The waterlevel of the boiler (A) has to
be lower than the lowest condensate output of the connected
machines!
There will be no loss of energy. The energy savings in regard to
the open system is approximately 33%.
This system gives the lowest installationcosts. When the system
works well, the system will work well for years.
Half open system
This system is conform the open system. The only difference is
that in this system at the end of the ringline (B,C) a steamtrap
has to be mounted. This steamtrap brings the condensate in a
watertank (E). The condensate in the watertank (E) will be
pumped in the boiler (A) through the pump (F). In this system
the waterlevel in the boiler (A) can be higher than the
condensate output of the connected machines.
The energy saving in regard to the open system is
approximately 20%.
This system will opperate fault free for years.
A : Boiler D : Steamtrap G : Work room
B : Steam supply line E : Watertank H : Boiler room
C : Condensate return line F : Pump M : Machine
5.2.3 Vacuum
• Connect the press with a 2" gas pipe to the main vacuum line (D). The connection is on the left of
the press, under the table.
6 Put into operation
Think of your own and other people's safety!
Creat a clean, surveyable and spacious working environment.
Make sure that nobody is standing behind the machine.
Check the following points daily!
It is possible that in view of transport, the centre footpedal (7) of de press has been removed. If so,
mount pedal as follows:
Place pedal (A) around pedal rod (B). Be sureto place the lip of the pedal under roll (C) of the latch lever (D). The
mount shaft (E) and cotter.
English - 6

7 How to operate
7.1 User directions
!Use the press only for the treatment of clothes.
!Maintenance and repair activities are to be executed by a qualified serviceman.
Not following the instructions of this manual may lead to injury or to damage to the machine!
Caution: After a while, the head (3) will get warm. The downside of the buck (4) and the
steam connections at the backside of the machine are hot. Do not touch these!
7.2 User instructions:
• Pressing.
The press is closed by pressing down the handbar (2) on the head (3). Pressure is obtain by
pressing down the footpedal (7). This footpedal is secured by a latch lever, witch keeps up the
pressure when releasing the pedal. The pedal plate is moveble. The locking mechanism is
released by pressing the frontside of the pedal slightly and the press will open.
• Head Steam.
By operating the valve (1) on the head, headsteam will be released.
• Buck Steam.
By operating the right footpedal (5), bucksteam will be released
• Buck Steam.
By operating the left footpedal (6), the vakuum valve is opened, so that the buch (4) can be
sucked off.
• Head Adjusting (code …/93).
If eventually through wear away of the padding the machine does not press well, you have to
adjust the head. This can be done by turning the adjusting bolts (8) on top of the head.
Adjustment of the latch lever, witch keeps the footpedal down, can be done, if necessary, by turning
the jam net and the set bolt (9) on the frontside of the frontplate.
7.3 Tips for use:
• Only press garments when they are damp.
• Short pressing duration for synthetic fibres, longer duration for cotton/linen.
• Advice: Take care for a maximum temperature of 35ºC on the operators position at an ambient
temperature of 25ºC and an relatively humdidity of 65%.
• Take care for sufficient ventilation.
• Take care for sufficient light on the workshop.
8 Put out of operation
• Remove vacuum.
• Close the steam shut off valve (W, see figure 1).
• Blow of steam by opening the blow off cock (Y).
• Cool down the machine.
English - 7

9 Trouble shooting
Mind your safety!
If you cannot solve the problems with the aid of table below, then call for an expert.
Table: Trouble shooting
English - 8
Trouble
Check / solution
Little or no head
steam.
1. Are the steam shut off cocks fully open?
2
. Check the steam pressure (maximum 6 bar).
Engineer:
3. Check steam valve cylinder (93), re-adjust if necessary (see chapter
'Adjustments')
Little or no up-steam
when operating foot
pedal (9).
1. Are the steam shut off cocks fully open?
2
. Check the steam pressure (maximum 6 bar).
Engineer:
3. Check steam valve cylinder (45), re-adjust if necessary (see chapter
'Adjustments').
Insufficient or no va-
cuum on buck (5) when
operating foot pedal
(11).
1. Check vacuum connection (D).
2
. Check covering, replace.
Engineer:
3. Check vacuum-unit.
10 Maintenance and repairs
10.1 Maintenance
Mind your safety!
Before starting maintenance activities:
• For steam heated machines: close the steam shut off valves (W, see figure 1), blow off steam
(Y).
• Let the machine cool down.
Spring rod
Graiser the spring rod regular
Oil-check
Fill up oil if necessary:
• Fill up the oil (Type: Univis HP22 ISO VG 22)
Covering
Do not wash the coverings!!!

10.2 Repairs/Dismantling
Mind your safety!
Before starting repair or dismantling activities:
• For steam heated machines: close the steam shut off valves (W, see figure 1), blow off steam (Y).
• Let the machine cool down.
All repair activities are to be carried out by a qualified serviceman.
For repair activities consult addition A containing detaildrawings with spare parts.
To be able to execute the repair activities, the parels mounted on the frame of the machine can be removed.
In case some parts have become defective, contact the distributor to order new parts (see table 'spare parts').
Use only original parts!
When the repairs have been completed, put the parels back into place before taking the machine into operation
again.
10.3 Adjustments
Mind your safety!
All adjustment activities are to be carried out by a qualified serviceman.
Steam quantity buck & head
The steamvalves are hot! Do not touch them. Use working gloves.
! Don't ever set the steam quantity to its maximum. Too much steam causes wet coverings and garments after
steaming and pressing.
• Steam quantity head (3):
1. Unscrew nut of steam valve (93).
2. Set the suitable steam quantity by adjusting the bolt.
-In = less steam
-Out = more steam
Check the steam quantity by starting the press.
3. Fasten the nut.
• Steam quantity buck (4):
1. Remove the cover.
2. Unscrew the nut of steam valve (45).
3. Set the suitable steam quantity by adjusting the bolt.
-In = less steam
-Out = more steam
Check the steam quantity by starting the press.
4. Fasten the nut.
5. Mount the cover.
English - 9

English - 10
11 Spare parts
Order spare parts by contacting your distributor.
Do not use any parts but original spare parts!
Table: Spare parts
Nr Onderdeel Art.nr. Nr
.
Onderdeel Art.nr.
1 Knob Assy 119227 40 Bearing 80945
2 Nut M12 41 Frame Shaft 95619
3 Ball Bearing 81018 42 Flexible Hose 80507
4 Plainwasher ø12 43 Check Valve 80021
5 Bushing 97139 44 Vacuum Valve Assembly 118652
6 Spindle 97138 45 Buck Valve Assy 118649
7 Adjusting Block 119199 46 Valve 35232
8 Head Lever 119198 47 Seat 15081
9 Adjusting Lever 119200 48 Top Link
For Lower Frame
95601
97392
10 Shaft 97147 49 Bearing 80944
11 Bearing 80973 50 Lever Link Pin 95604
12 Shaft 97147 51 Back Lever 923
13 Front Plate Assy
For Lower Frame
118646
119270
52 Front Lever Link 95602
14 Frame Assy
For Lower Frame
118644
119267
53 Bearing 80954
15 Head Lever Shaft 95277 54 Front Lever Link Pin 95611
16 Bearing 80945 55 Bearing 80953
17 Linkage Washer ø57xø36 56 Connector Pin 95606
18 Shaft Clamp 95253 57 Front Lever Pin 95618
19 Nut M12 (2x) 58 Bearing 80944
20 Foot Pedal Lh
For Lower Frame
118816
119268
59 Foot LeverLink Pin 95610
21 Foot Pedal Rh
For Lower Frame
118818
119269
60 Front Lever 917
22 Pedal Bush 80973 61 Oil Check Assy 118648
23 Pedal Rubber 30005 62 Bearing 80953
24 Lever Connecting Rod 95585 63 Pin 95608
25 Vacuum Valve Connecting
Rod
95255 64 Spring 50001
26 Set Collar 17858 65 Bearing 80954
27 Spacer 90879 66 Foot Lever Link Pin 95610
28 Spring 50025 67 Foot Pedal Lever Bumper 30872
29 Disc 20058 68 Latch Lever Pin 95609
30 Shouldered Bold 96078 69 Latch Lever Spring 50091
31 Locking Pin 12395 70 Trip Roll 95614
32 Bearing 80944 71 Roll Pin 95612
33 Pivot Shaft 95279 72 Pedal Latch Bumper 30274
34 Rod Head 918 73 Adjusting Sleeve Pin 95609
35 Bearing 80944 74 Foot Pedal 914
36 Spring Plug 911 75 Foot Lever 915
37 Balancer Plug 76 Latch Lever 916
38 Spring Plug 902 77 Latch Roll 95613
39 Screw Eye
Nut M12
95583 78 Adjusting Roll Pin 95616

English - 11
79 Latch Roll Adjusting Pin 95615
80 Ajusting Knob Assy 111693
81 Latch Roll Adjuster 920
82 Spring 50024
83 Front Plate Strap 118645
84 Bearing 80953
85 Pin 95605
86 Foot Lever Link 95603
87 Connecting Lver 118287
88 Wood Handle 118297
89 Frame Cover L 119261
90 Frame Cover R 119262
91 Handle Bracket 118296
92 Strip 94896
93 Head valve assy 118650




This manual suits for next models
14
Table of contents
Other Cissell Power Tools manuals
Popular Power Tools manuals by other brands
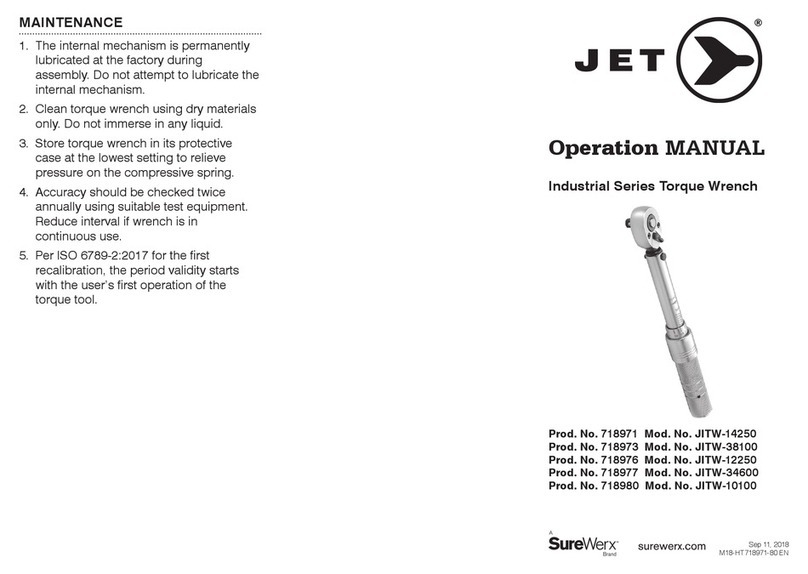
Surewerx
Surewerx Jet JITW-14250 Operation manual
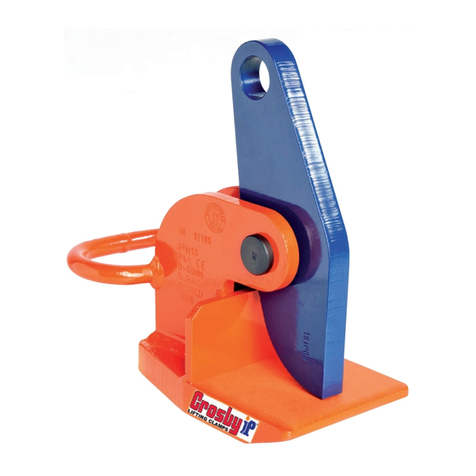
Crosby
Crosby IPH10 user manual
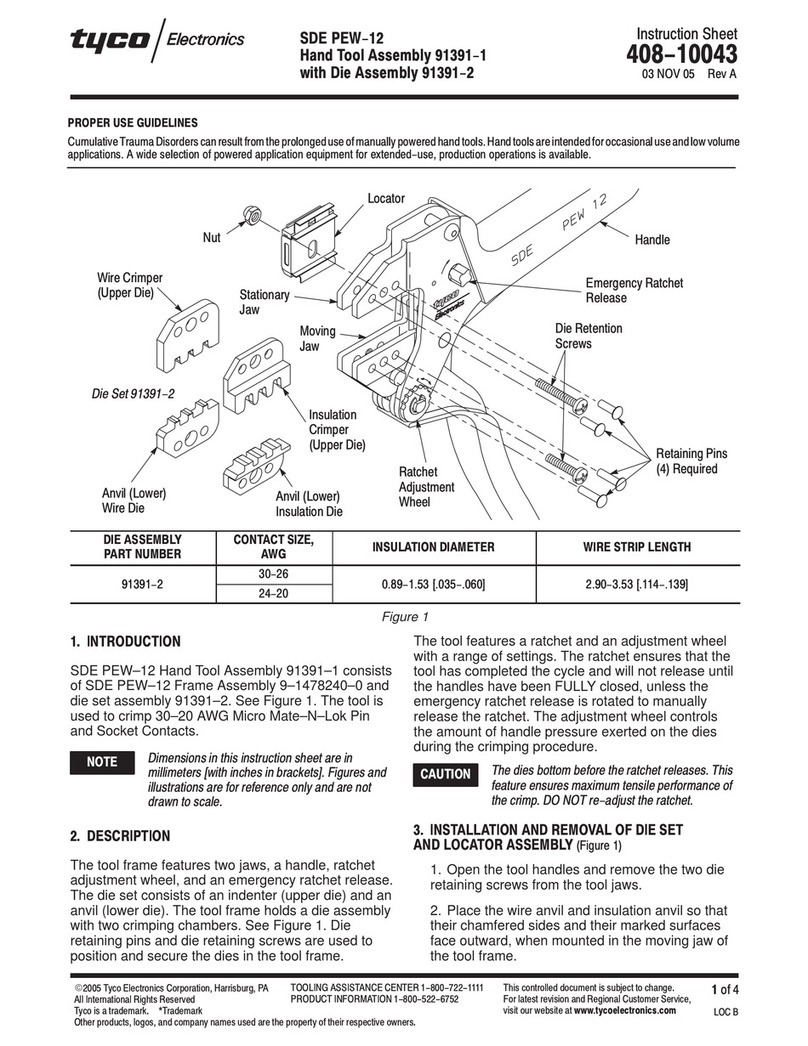
Tyco Electronics
Tyco Electronics 91391-1 instruction sheet

Powermate
Powermate 024-0079 instruction manual
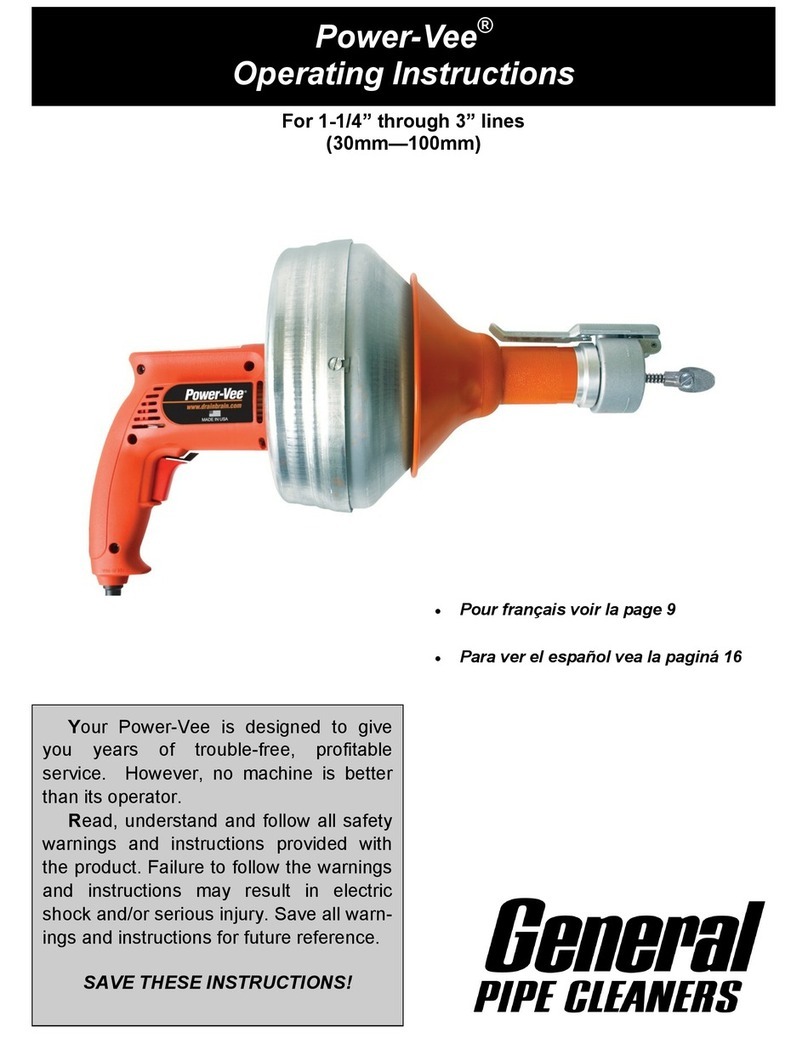
General Pipe Cleaners
General Pipe Cleaners Power-Vee operating instructions
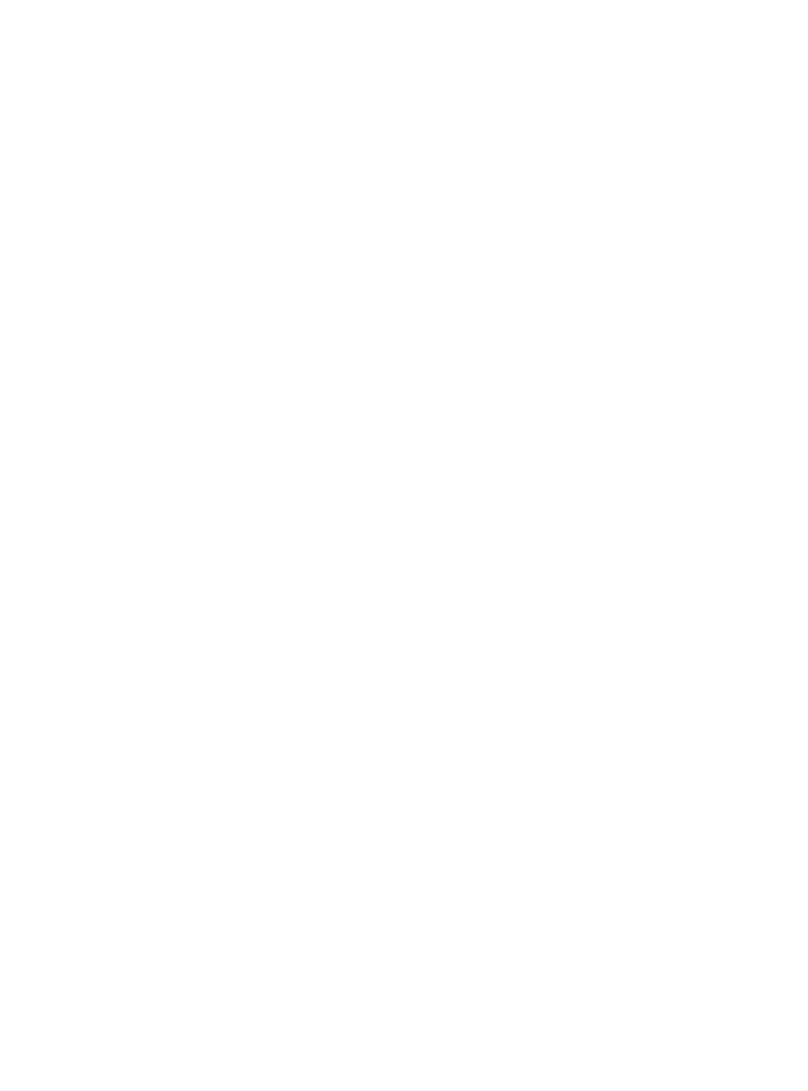
Swordfish
Swordfish Ikon operating instructions