CMA Dishmachines GR Series User manual

GR Painting Robot Series
Mechanical Maintenance Manual
Version No.:ZL-GR6150-002-V1
Issue Date:January 2020
The copyright is reserved for CMA (WUHU) Robotics Company Limited
For customer use only and any unauthorized use of this manual is strictly prohibited
CMA (WUHU) Robotics Company Limited
No.96, East Wanchun Road, Jiujiang Economic Development District, Wuhu, Anhui Province
TEL:400-052-8877
CMA
CMA (WUHU) Robotics Company Limited
Supplier of Intelligent Painting Robots

ZL-GR6150-002-V1 Mechanical Maintenance Manual
CMA (WUHU) Robotics Company Limited
Statement
Thank you for purchasing the painting robots designed by CMA (WUHU) Robotics Company Limited
(CMA, in short). The contents stated in the manual are directly related to your safety, lawful rights and
responsibilities. Please ensure to read through the manual and correctly set the operation parameters before
use. Any operation that does not strictly follow the instructions or the warnings of the manual might lead to
physical injury or property damage. All rights for explanation are reserved by CMA.
This manual is intended for technical reference only which makes no warranty to the entire application
of the robot system. Therefore, CMA accepts no responsibility for any accident, damage or industrial
copyright dispute that follows the use of the application system. It is strongly recommended that all the
professionals involved in operation, teaching, maintenance, and inspection should take CMA special training
before being authorized to use the robots.
Copyright and Brand name
The copyright of the manual is fully reserved by CMA and is intended for CMA users only. Neither can
the manual be reproduced nor should it be revealed to a third party without the written consent of CMA.
The manual should be well kept during the life circle of the robot. An optional copy can be ordered from
CMA if the original one is damaged or lost. The address of the new owner is required to be reported to CMA
if the robot is resold or transferred.
This manual is an indispensable part of the whole manual collection and all the professionals involved
in operation, teaching, maintenance, and inspection are required take CMA special training on the knowledge
instructed by the following manuals:
ZL-GR-001-V1:Safety Manual for GR Painting Robot Series
ZL-GR-002-V1:Maintenance Manual for GR Painting Robot Series
ZL-GR-003-V1:Explosion Protection Manual for GR Painting Robot Series
ZL-GR-004-V1:Remote Assistance Manual for GR Painting Robot Series
ZL-GR-005-V1:IO Communication Instruction Manual for GR Painting Robot Series
ZL-GR-006-V1:Program Editor Instruction Manual for GR Painting Robot Series
ZL-GR6150-001-V1:Installation and Connection Instruction Manual for GR6150 Robot
ZL-GR6150-002-V1:Mechanical Maintenance Manual for GR6150 Robot
ZL-GR6150-003-V1:Electrical Maintenance Manual for GR6150 Robot
ZL-GR6150-004-V1:Electrical Schematic Diagram for GR6150 Robot
All rights reserved by CMA. The manual and the relevant manuals are subject to change without prior
notice for the purpose of product improvement, specification change or instruction update. Please visit the
following website for the latest updates: www.cmarobot.com.cn.

ZL-GR6150-002-V1 Mechanical Maintenance Manual
CMA (WUHU) Robotics Company Limited
About the Manual
The target readers of the manual include professionals involved in robot operation, maintenance and
technical service.
This manual intends to explain the mechanical maintenance during use for all the GR6150 painting
robots designed by CMA.
In order to effectively draw the attention of the users of the manual to a specific subject or aspect, the
following symbols will be used, each with the following meanings.
Safety precautions in this manual are classified into four categories, “danger”, “caution”, “attention” and
“important” respectively.
Danger
Danger! This warning means death might occur, if an operation is not properly
performed.
Caution
Caution! This warning means death or server physical injury might occur, if an
operation is not properly performed.
Attention
Attention! This warning means minor physical injury or minor material damage
may occur, if an operation is not properly performed.
Important
Important! This warning means special attention should be paid to a certain
operation.
Warnings titled by “attention” might also lead to severe consequence in different cases. Therefore it is
strongly recommended that anything titled by “attention” should be handled with extreme caution.
Please read the manual and the files attached carefully and master all the required knowledge about
the robot and the safety instructions before use.
A cover or safety shied is taken out only for the purpose of illustration. Please ensure to restore
the cover or safety shield before any operation.
The figures and photos contained in this manual are for the purpose of illustration only and they
might be different from the product purchased.
The manual is subject to change without prior notice for the purpose of product improvement,
specification change and instruction update.
The manual will be reissued and a new version number will be specified if the contents are

ZL-GR6150-002-V1 Mechanical Maintenance Manual
CMA (WUHU) Robotics Company Limited
renewed.
If you need to order the manual due to damage, loss, etc., please contact our agent or the
nearest sales office on the back cover of the manual, and order according to the data number on the
cover.
CMA is not responsible for any consequence caused by any unauthorized modification or
change of the robot.

ZL-GR6150-002-V1 Mechanical Maintenance Manual
CMA (WUHU) Robotics Company Limited
Content
Chapter One: Safety.....................................................................................................................................................1
1.1 Instruction for Safe Use of Robots............................................................................................................... 1
1.1.1 Safety Precautions during Adjustment,Operation,Mainteance........................................................ 1
1.1.2 Safety Countermeasures of Robot Body.......................................................................................... 3
1.2 Shift,Transfer, and Sale of Robots................................................................................................................7
1.3 Abandonment of Robots............................................................................................................................... 7
Chapter Two: Basic Description...................................................................................................................................9
2.1 Robot System Composition.......................................................................................................................... 9
2.2 Unpacking Check..........................................................................................................................................9
2.3 Machine Body Nameplate.......................................................................................................................... 11
2.4 Body Part Composition and Identification of Each Axis...........................................................................13
2.5 Robot Axis Range Limit and Home Position.............................................................................................13
2.6 Robot Performance Parameters.................................................................................................................. 16
2.7 Allowable Value of Wirst Payload..............................................................................................................18
2.7.1 Allowable Weight...........................................................................................................................18
2.7.2 Allowable Maximum of Static Payload Torque.............................................................................18
2.7.3 Allowable Maximum of Moment of Inertia...................................................................................19
2.7.4 Allowable Payload Curve Diagram................................................................................................19
Chapter Three: Handling and Installation.................................................................................................................. 20
3.1 Robot Handling...........................................................................................................................................20
3.1.1 Handling Precautions......................................................................................................................20
3.1.2 Handling Method............................................................................................................................20
3.2 Robot Installation........................................................................................................................................22
3.2.1 Setting of Safety Fence...................................................................................................................22
3.2.2 Robot Installation Method..............................................................................................................22
3.2.3 Ground Mounting........................................................................................................................... 23
3.2.4 Supporter Installation..................................................................................................................... 24
3.2.5 Wall-mounted/ Suspended Installation.......................................................................................... 24
3.3 Installation Site and Environment.............................................................................................................. 25
3.4 Intergrated Application Installation Interface.............................................................................................26
3.4.1 Tool installation at the End of the Robot Wrist.....................................................................................26
3.4.2 Other Auxiliary Interfaces...................................................................................................................... 28
Chapter Four: Overhaul and Maintenance.................................................................................................................32
4.1 Preventive Maintenance..............................................................................................................................31
4.1.1 Daily Inspection..............................................................................................................................31
4.1.2 Quarterly Inspection....................................................................................................................... 31
4.1.3 Annual Inspection...........................................................................................................................32
4.1.4 Inspect Every Two Years............................................................................................................... 32
4.2 Overhaul of Main Bolts.............................................................................................................................. 32
4.3 Lubricant Inspection................................................................................................................................... 33
4.4 Change the Lubricant..................................................................................................................................34

ZL-GR6150-002-V1 Mechanical Maintenance Manual
CMA (WUHU) Robotics Company Limited
4.4.1 The Oil Supply Quantity of Lubricant........................................................................................... 34
4.4.2 Space Orientation of Lubrication................................................................................................... 34
4.4.3 Lubricant Replacement Steps for J1~J4 Axis Reducer and Wrist Parts........................................34
4.4.4 Release the Residual Pressure in Lubricating Oil Cavity.............................................................. 37
4.5 Robot Maintenance and Use Area..............................................................................................................37
4.6 Home Position Calibration......................................................................................................................... 38
4.6.1 Home Position Calibration Method................................................................................................38
4.6.2 Mechanical Home Position Calibration of Each Axis................................................................... 39
Appendix....................................................................................................................................................................42
ATightening Torque Table of Screws............................................................................................................... 41
BBackup List..................................................................................................................................................... 41

ZL-GR6150-002-V1 Mechanical Maintenance Manual
CMA (WUHU) Robotics Company Limited
1
Chapter One Safety
1.1 Instructions for Safe Use of Robots
Before performing installation, operation, maintenance, and overhaul operations, please be sure to read this
manual and other attached documents thoroughly and use this product correctly. Please fully grasp the equipment
knowledge, safety information and all precautions before using this product. This manual uses the following
symbols to indicate their importance.
1.1.1 Safety Precautions during Adjustment, Operation, Maintenance, etc.
(1)Operators must wear work clothes, safety helmets, safety shoes, etc.
(2)When turning on the power, make sure that there are no workers within the robot's operating range.
(3)The power must be cut off before entering the robot's range of motion for work.
(4)When overhaul, maintenance and other operations must be carried out under the power-on state, two persons
should work in a team at this time. One person maintains a posture that can immediately press the emergency stop
button, while the other person is within the robot's range of motion, staying vigilant and working quickly. In
addition, you should confirm the retreat path before proceeding.
(5)The load on the wrist and the robot arm must be controlled within the allowable carrying weight and torque.
If the allowable carrying weight and torque regulations are not observed, it will lead to abnormal action or
premature damage of mechanical components.
(6)It is forbidden to disassemble and work on parts not covered in the maintenance manual.
The robot is equipped with various self-diagnostic functions and abnormality detection functions, so that it
can stop safely even if an abnormality occurs. Even so, accidents caused by robots still occur from time to time.
Danger
It means that if the handling is wrong, it will cause the user's death or serious injury, and
the situation is very dangerous.
Warning
It indicates a situation that will cause death or serious injury to the user if the handling is
incorrect.
Attention
It indicates a situation that will cause minor injuries or property damage to the user if the
handling is incorrect.

ZL-GR6150-002-V1 Mechanical Maintenance Manual
CMA (WUHU) Robotics Company Limited
2
The above-mentioned accidents were all caused by the same reasons as "ignorance of safety operation
procedures" and "no idea that the robot would move suddenly". In other words, they are all accidents caused by
man-made unsafe behaviors such as "temporary negligence" and "failure to follow the prescribed steps."
"Emergency situations" make it too late for operators to implement "emergency stop", "flee" and other
behaviors to avoid the accident, which may lead to major accidents. "Emergency situations" generally have the
following types.
(1)Low-speed action suddenly becomes high-speed action.
(2)Other operators performed the operation.
(3)A different program was started due to an abnormality or program error in the peripheral equipment.
(4)Abnormal operation due to noise, malfunction, defect, etc.
(5)Misoperation.
(6)Originally planned to regenerate at low speed to perform the action, but it performed the high-speed action.
(7)The work pieces transported by the robot fall and scatter.
(8)When the work piece is in the stopped state of clamping and interlocking standby, it suddenly loses control.
(9)The next or behind robot performed the action.
The above are only some examples, and there are many forms of "emergency situations". In most cases, it is
impossible to "stop" or "escape" a robot that moves suddenly, so the following best countermeasures should be
implemented to avoid such accidents.
Danger
Most robot accidents are as follows:
1、The automatic operation was performed without confirming whether there is
anyone in the robot's motion range.
2、It enters the robot's motion range in the automatic operation state, and the robot
starts suddenly during the operation.
3、You just notice the robot in front of you, ignoring the others.
Danger
Be careful and approach the robot cautiously.
Danger
When the robot is not in use, measures such as "press the emergency stop button"
and "cut off the power" should be taken to prevent the robot from moving.

ZL-GR6150-002-V1 Mechanical Maintenance Manual
CMA (WUHU) Robotics Company Limited
3
In order to comply with these principles, it is necessary to fully understand the following precautions
and follow them.
1.1.2 Safety Countermeasures of Robot Body
Attention
The design of the robot should remove unnecessary protrusions or sharp parts, use
materials that adapt to the working environment, and adopt a fail-safe protection
structure that is not prone to damage or accidents during operation. In addition, it
should be equipped with misoperation detection stop function and emergency stop
function when the robot is in use, as well as interlocking function to prevent the
danger of the robot when the peripheral equipment is abnormal, so as to ensure
safe operation.
Warning
The main body of the robot is a multi-joint manipulator structure, and the angle of
each joint in the movement is constantly changing.
When you must approach the robot for teaching and other tasks, be careful not to
get caught by the joints. Because there are mechanical stops at the action ends of
the axis 1、2 and 3, which has a high risk of being clamped, so special attention
should be paid to it.
In addition, if the servo motor is removed or the brake is released, the robot arm
may fall due to its own weight or move in an uncertain direction. Therefore,
measures to prevent falling must be implemented, and the surrounding safety
conditions must be confirmed before operation.
Attention
When installing the attached machine on the end effector and the mechanical arm,
the size and quantity of screws specified in this book should be strictly observed,
and the torque wrench should be used to tighten according to the specified torque.
Unspecified tightening and imperfect methods will loosen the screws and cause
major accidents.
Danger
During the operation of the robot, please configure a monitor (the third party) who
can immediately press the emergency stop button to monitor the safety status.
Danger
During the operation of the robot, the operation should be carried out in a state
where the emergency stop button can be pressed immediately.

ZL-GR6150-002-V1 Mechanical Maintenance Manual
CMA (WUHU) Robotics Company Limited
4
Attention
When designing and manufacturing the end effector, it is controlled within the
allowable payload range of the robot wrist.
Attention
The fail-safe protection structure should be adopted, even if the power supply or
compressed air supply of the end effector is cut off, the installation object will not
be released or fly out, and the corner or protruding part should be treated to
prevent damage to people and objects.
Attention
The fail-safe protection structure should be adopted, even if the power supply or
compressed air supply of the end effector is cut off, the installation object will not
be released or fly out, and the corner or protruding part should be treated to
prevent damage to people and objects.
Attention
It is strictly forbidden to supply power, compressed air, and welding cooling water
outside the specifications, which will affect the performance of the robot and cause
abnormal operations, malfunctions, damage and other dangerous situations.
Attention
Although electromagnetic interference is related to its type or intensity, there is no
perfect countermeasure with current technology.
When the robot is in operation or when the power is on, the operation precautions
and regulations should be followed. Due to electromagnetic waves, other noises, and
substrate defects, the recorded data will be lost.
Therefore, please back up programs or frequently used data to an external storage
medium such as a Compact flash card.
Attention
In a large-scale system, multiple operators are involved in the work. When it is
necessary to talk at a distance, the intention should be correctly conveyed by means
of gestures, etc.
Factors such as noise in the environment can make it impossible to convey the
meaning correctly and cause accidents.

ZL-GR6150-002-V1 Mechanical Maintenance Manual
CMA (WUHU) Robotics Company Limited
5
Attention
Industrial robot gesture method (example)
1. Connect: Do the work
related to the connection
2. No way! Disconnect:
Raise your right hand
and wave vigorously left
and right
3. Is that OK? (to
confirm):Raise your right
hand up high forward
4. OK: Raise your right
hand up high forward
Use your thumb and
index finger to form a
circle
5. Wait a moment: The
right hand is facing the
opponent
Straight up arms
horizontally
6. Leave: Stretch your
right arm horizontally
and weave to the left
Attention
Operators should also maintain awareness of escape at all times during operations.
It must be ensured that in an emergency, you can escape immediately.
Attention
Always pay attention to the actions of the robot, and do not work with your back to
the robot.
Slow response to robot movements can also lead to accidents.
Attention
When an abnormality is found, the emergency stop button should be pressed
immediately.
This requirement must be thoroughly implemented.

ZL-GR6150-002-V1 Mechanical Maintenance Manual
CMA (WUHU) Robotics Company Limited
6
Attention
According to the setting place and operating content, the relevant operation
regulations and checklists such as starting method, operation method, solution in
case of abnormality, etc. of the robot should be compiled. And carry out the
operation according to the operating regulations. Operation only based on the
memory and knowledge of the operator can cause accidents due to forgetting and
mistakes.
Attention
For the completed program, use the storage protection function to prevent
accidental editing.
Attention
When teaching, confirm the program number or step number before proceeding.
Editing procedures and steps incorrectly can cause accidents.
Attention
When it is not necessary to make the robot move and operate, please turn off the
power before performing the work.
Attention
After the teaching operation is completed, the robot movement should be manually
checked at a low speed.
If you run at 100% speed in automatic mode immediately, accidents will occur due
to program errors and other factors.
Attention
After the teaching work is over, clean up and check if you have forgotten to take the
tool. The work area is contaminated by oil, and tools are forgotten, etc., which can
cause accidents such as falls.
Ensuring safety starts with tidying up.

ZL-GR6150-002-V1 Mechanical Maintenance Manual
CMA (WUHU) Robotics Company Limited
7
1.2 Shift, Transfer, and Sale of Robots
Attention
When the robot is shifted, transferred, or sold, it is necessary to ensure that the
auxiliary documents of the robot, such as the mechanical operation manual,
electrical maintenance manual, and robot programming manual, are transferred to
the new user.
When shifting, transferring, or selling to a foreign country, the customer must be
responsible for preparing mechanical operation manuals, electrical maintenance
manuals, and robot programming manuals in appropriate languages, modifying the
display language, and ensuring compliance with local laws and regulations.
The new user does not read the instruction manual and performs wrong operation
or unsafe operation, which may lead to accidents.
Attention
When the robot is shifted, transferred, or sold abroad, if there are no special
provisions in the contract terms at the time of the initial sale, the security-related
terms shall not be inherited by the new recipient.
The original customer and the new recipient must sign a new contract.
1.3 Abandonment of Robots
Attention
Do not decompose, heat or incinerate the batteries used for the control device and
robot body. Otherwise, fire, rupture and burning accidents will occur.
Attention
Do not disassemble the board and components of the control device before
discarding it.
Sharp parts such as cracks or cuts, wires, etc. may cause injury.
Attention
After the cables and external wiring are removed from the connector and junction
box, do not disassemble them further and then discard them. Otherwise, it may
cause injury to hands or eyes due to conductors, etc.

ZL-GR6150-002-V1 Mechanical Maintenance Manual
CMA (WUHU) Robotics Company Limited
8
Attention
When carrying out abandoned work, please pay full attention not to be pinched or
injured.
Attention
Waste products should be discarded in a safe state.

ZL-GR6150-002-V1 Mechanical Maintenance Manual
CMA (WUHU) Robotics Company Limited
9
Chapter Two Basic Description
2.1 Robot System Composition
The industrial robot is composed of the following components, See Figure 2-1:
Robot body
Robot electric control cabinet
Explosion-proof control cabinet
Teach pendant
Connection (power supply) cables, etc.
Air pipe, etc.
Fig. 2-1 Industrial Robot System Composition
2.2 Unpacking Check
1、Before unpacking, please confirm whether the outer packaging of the product is intact;
2、After unpacking, please confirm whether all parts of the robot are complete. If you find missing or
wrong parts, please contact the supplier in time.
robot body
air pipe
inter panel cable
explosion-proof cabinet
safety area explosion hazard
control cabinet
teach pendant

ZL-GR6150-002-V1 Mechanical Maintenance Manual
CMA (WUHU) Robotics Company Limited
10
GR6150 Robot Packing List
No.
Name
Configuration type
Quantity
Unit
Remarks
1
robot body
standard configuration
one
set
2
robot electric control
cabinet
standard configuration
one
set
3
explosion-proof control
cabinet
standard configuration
one
set
4
Connecting cable from
robot body to electric
control cabinet
code cable
one
set
5
power cable
one
set
6
Ground cable
one
piece
7
Connecting air pipe from
robot body to explosion
proof control cabinet
φ6
one
piece
8
φ10
one
piece
9
φ16
one
piece
10
robot teach pendant and
cable
standard configuration
one
set
11
robot pins
standard configuration
one
set
12
user's manual
standard configuration
one
set
13
factory inspection report
enterprise standard
one
piece
14
Product certification
enterprise standard
one
piece
15
robot accessory
accessory box
one
piece
16
380V main power
circular connector
standard configuration
one
set
In the
accessory
box
17
home position bolt
standard configuration
one
piece
In the
accessory
box

ZL-GR6150-002-V1 Mechanical Maintenance Manual
CMA (WUHU) Robotics Company Limited
11
Note: The above is the standard configuration list, excluding the case of customized models. For
details, please refer to the actual "GR6150 Robot Packing List".
2.3 Machine Body Nameplate
The name plate of the operator can be seen on the robot body, which contains the corresponding model
type, weight, voltage, production number,manufacturing date and explosion-proof parameters, etc. As shown in
Figure 2-2 below.
18
other
The body color is green; Fuses (in the robot electric control cabinet:
two in each 5A and 10A glass tube fuse; five 2A glass tube fuses; two
in each 2A and 32A fuse cores ); Attached an electrical schematic
diagram and three backup circular connector boards

ZL-GR6150-002-V1 Mechanical Maintenance Manual
CMA (WUHU) Robotics Company Limited
12
Fig. 2-2 Robot Body Nameplate

ZL-GR6150-002-V1 Mechanical Maintenance Manual
CMA (WUHU) Robotics Company Limited
13
2.4 Body Part Composition and Direction Identification of Each Axis
The robot mechanical body is mainly composed of base part , rotating part, upper arm part, functional
forearm part, and wrist part. The joints of the machine body are driven by servo motors, and the joints cooperate
with each other to realize the adjustment of the position and posture of the robot end in space.
The names of the various components of the machine body and the identification of each axis direction are
shown in Figure2-3:
Fig. 2-3 Components of the Machine Body of GR 6150
rotating part
functional
forearm part
upper arm part
base part
wrist part

ZL-GR6150-002-V1 Mechanical Maintenance Manual
CMA (WUHU) Robotics Company Limited
14
2.5 Robot Axis Range Limit and Home Position
Each axis of the robot body has a home position and range limit.When the robot system is running normally,
each axis of the robot is controlled to move within the allowable range. In addition, in order to ensure further
safety, mechanical end stops are provided on some axes(see Fig. 2-4) to prevent the robot from operating beyond
the allowable range when the robot (control) system is abnormal.
Fig.2-4 Mechanical End Stop Position and Home Position
mechanical end stop
of axis 1
home position of
axis 1
mechanical end
stop of axis 2
home position
of axis 2
calibration point of axis 3
mechanical end stop
of axis 3
home position of
axis 5
home position
of axis 4
home position
of axis 6
Other manuals for GR Series
2
This manual suits for next models
1
Table of contents
Other CMA Dishmachines Robotics manuals
Popular Robotics manuals by other brands
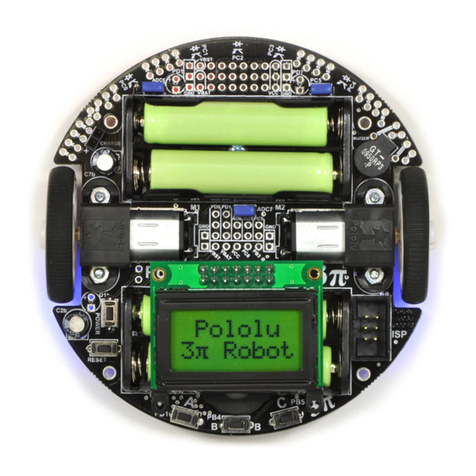
Pololu
Pololu 3pi Robot user guide
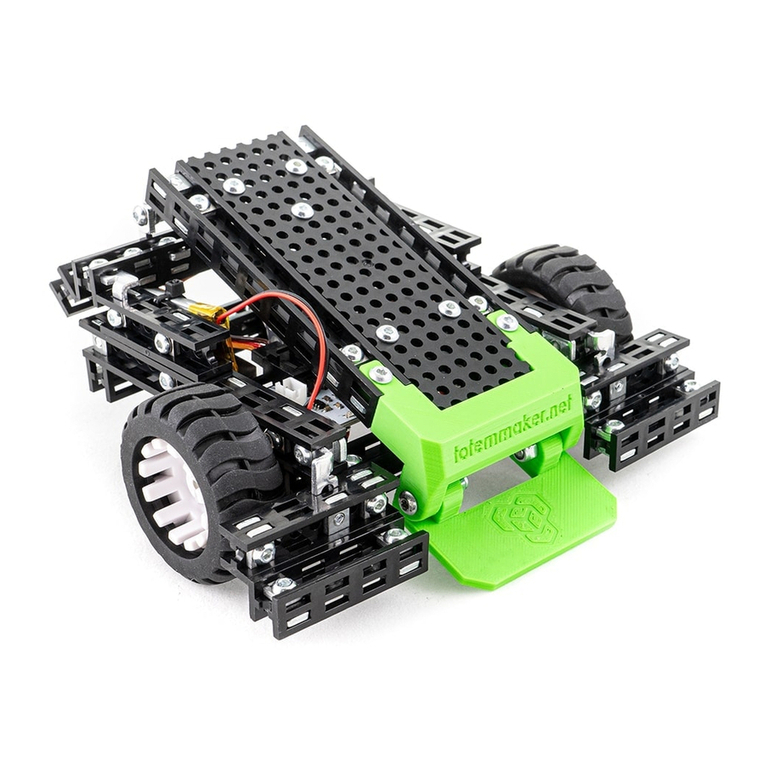
Totem
Totem Mini Trooper Assembly guide
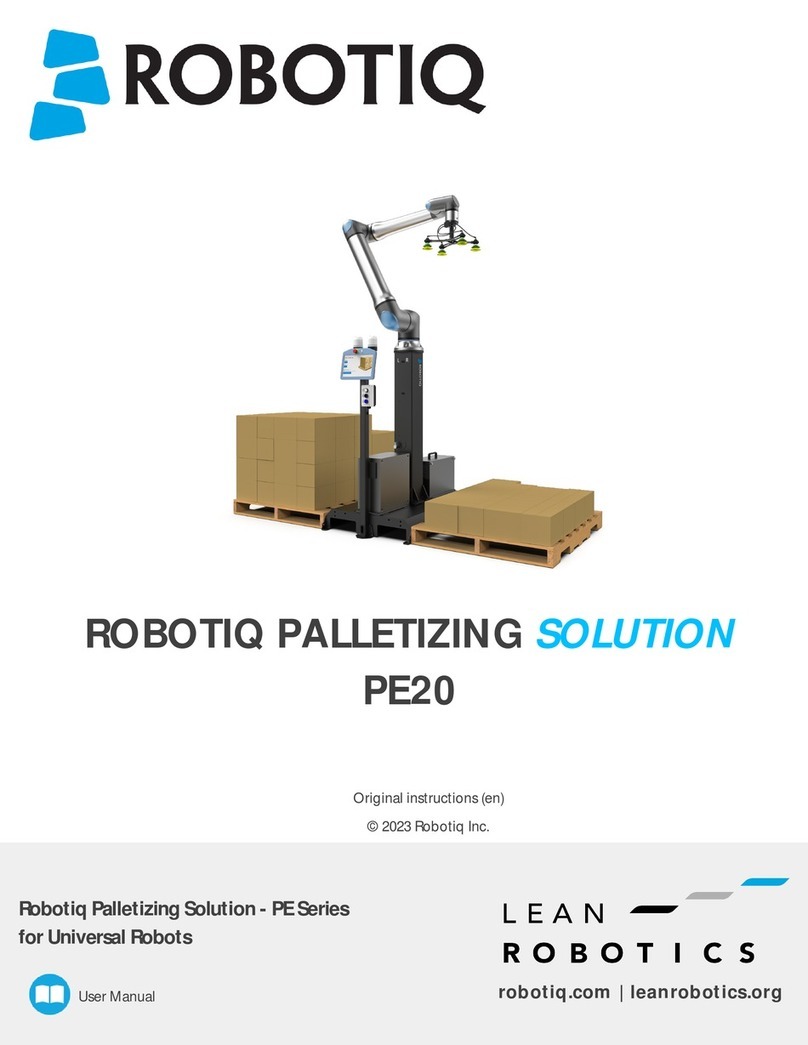
ROBOTIQ
ROBOTIQ PE20 Original instructions
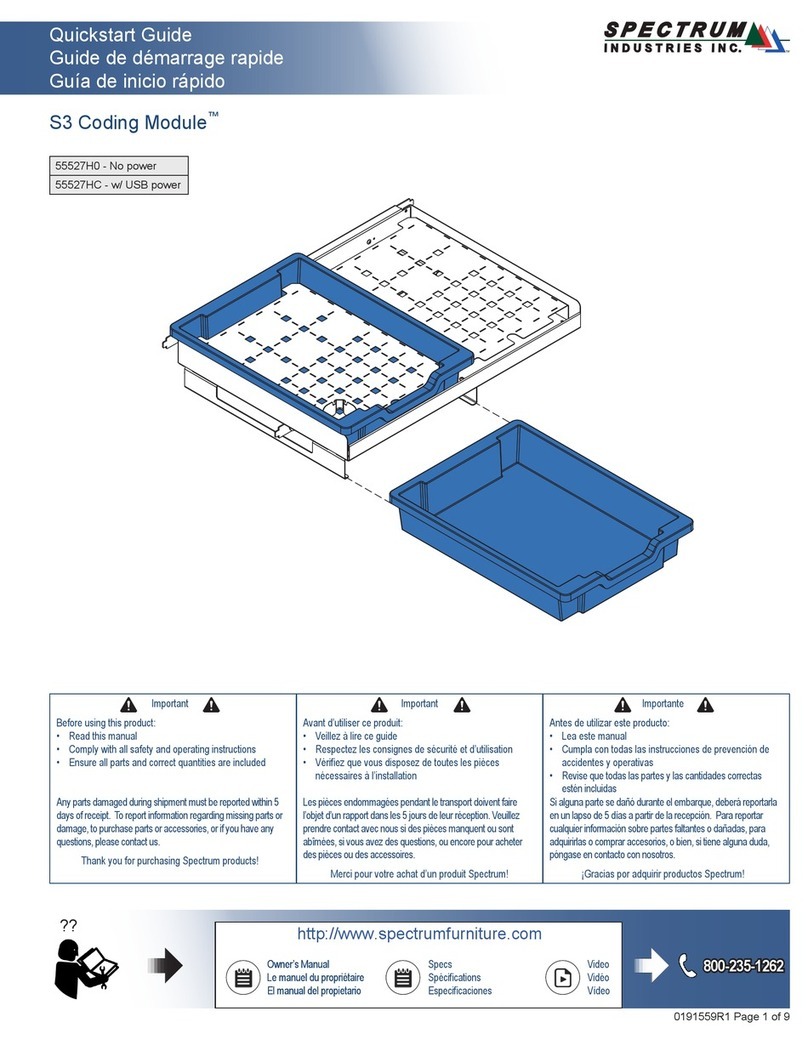
Spectrum Industries
Spectrum Industries S3 Coding Module 55527H0 quick start guide
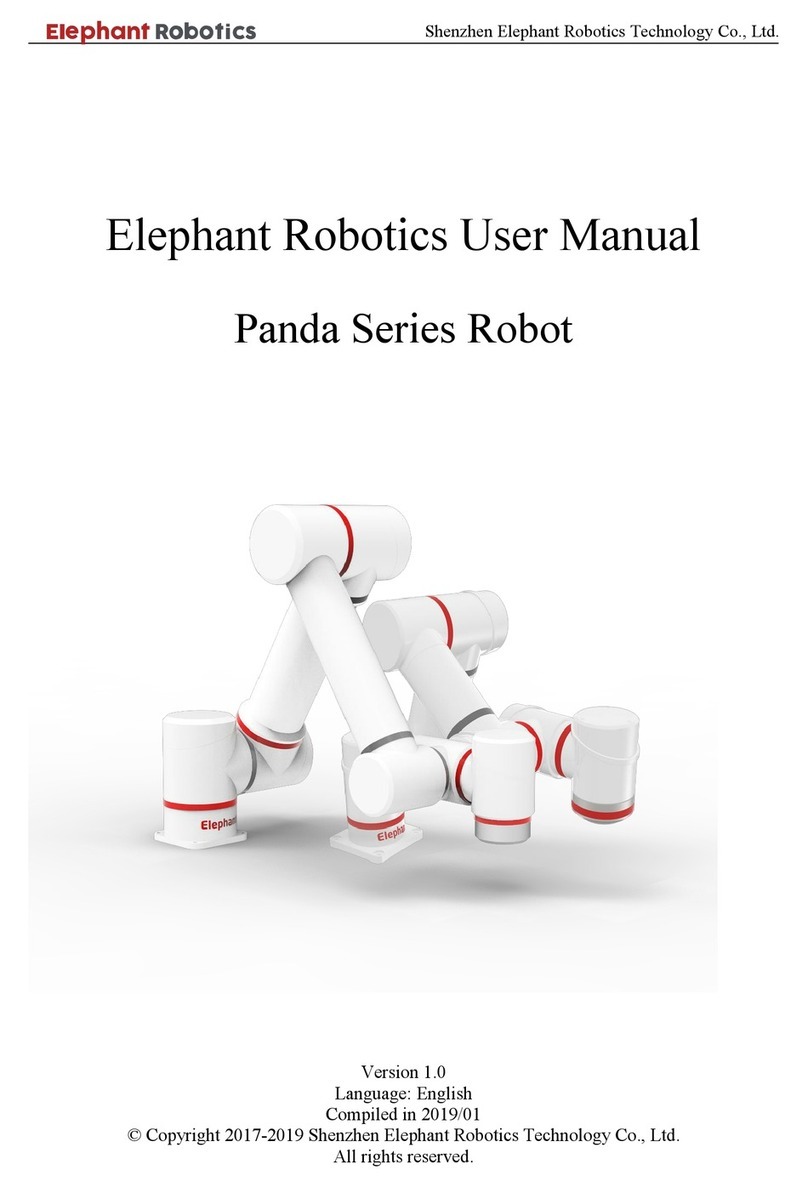
Elephant Robotics
Elephant Robotics Panda Series user manual
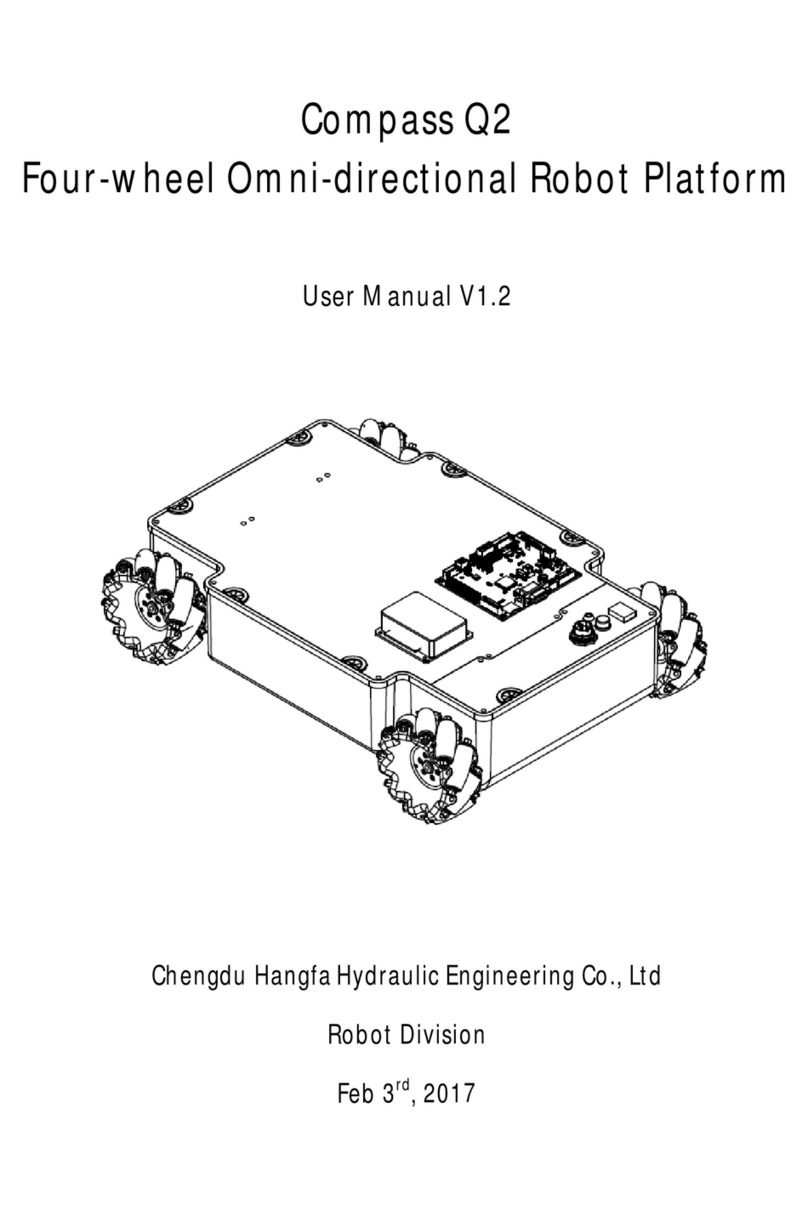
Chengdu Hangfa Hydraulic Engineering Co., Ltd
Chengdu Hangfa Hydraulic Engineering Co., Ltd Compass Q2 user manual