ComAp ID-FLX-Lite-PC User manual

Copyright © 2017 ComAp a.s.
Written by JURJ, RJZD
Prague, Czech Republic
ComAp a.s., U Uranie 1612/14a,
170 00 Prague 7, Czech Republic
Tel: +420 246 012 111
E-mail: info@comap-control.com, www.comap-control.com Global guide
ID-FLX-Lite-
IPC
Irrigation Pump Controller
SW version 1.2.1
1 Document information 7
2 System overview 10
3 Applications overview 15
4 Installation and wiring 16
5 Controller setup 42
6 Communication 69
7 Troubleshooting 78
8 Technical data 85
9 Function description 91
10 Appendix 109
11 Language support 211

InteliDrive Lite - 1.2.1 Global guide 2
Table of contents
1 Document information 7
1.1 Clarification of notation 7
1.2 About this guide 7
1.3 Legal notice 7
1.4 Conformity Declaration 9
2 System overview 10
2.1 Warnings 10
2.2 General description 10
2.3 Configurability and monitoring 11
2.3.1 Open connection from LiteEdit 11
2.3.2 Open connection from web browser 12
2.3.3 Open connection from WinScope 13
3 Applications overview 15
3.1 Single applications 15
4 Installation and wiring 16
4.1 Putting it into operation 16
4.1.1 How to install 16
4.1.2 Analog inputs 19
4.1.3 Binary inputs and outputs 25
4.1.4 Analog outputs 26
4.1.5 Remote modules - CAN bus connection 27
4.2 Mounting 28
4.3 Package contents 28
4.3.1 Software package 28
4.3.2 Components 29
4.4 Terminal diagram and dimension 29
4.5 Extension plug-in modules 30
4.5.1 Extensions plug-in modules installation 30
4.5.2 IL-NT AOUT8 31
4.5.3 IL-NT AIO 33
4.5.4 IL-NT IO1 34
4.5.5 IL-NT BIO8 34
4.6 Communication modules 35
4.6.1 IL-NT RS232 35
4.6.2 IL-NT RS233-485 36

InteliDrive Lite - 1.2.1 Global guide 3
4.6.3 IL-NT S-USB 36
4.6.4 IB-Lite 37
4.6.5 IL-NT GPRS 38
4.7 Remote modules 39
4.7.1 IL-NT RD (SW) 39
4.7.2 IGL-RA15 40
4.7.3 IB-NT 41
5 Controller setup 42
5.1 Front panel elements 42
5.2 Init screens 44
5.2.1 Init screen 44
5.2.2 Firmware screen 44
5.2.3 Languages screen 44
5.2.4 User interface screen 44
5.3 Display menus 45
5.3.1 Switching between User and Engineer menus 45
5.4 How to select the engine mode? 45
5.5 How to view measured data? 45
5.6 How to view and edit setpoints? 45
5.6.1 How to change the display contrast? 46
5.6.2 How to check software revision? 46
5.6.3 How to check serial number and choose interface? 46
5.6.4 How to change language? 46
5.7 How to find active alarms? 46
5.8 How to list History records? 47
5.9 MEASUREMENT screens description 47
5.9.1 Main measure screen 47
5.9.2 InteliDrive Lite Analog inputs screens 48
5.9.3 IL-NT-AIO Analog inputs screens 48
5.9.4 IL-NT-BIO8 Binary inputs screen 48
5.9.5 IL-NT-IO1 Binary inputs screen 49
5.9.6 ECU State 49
5.9.7 ECU Values 49
5.9.8 Statistic 50
5.9.9 ECU AlarmList 50
5.9.10 Alarm list 50
5.10 Display screens and pages structure 51
5.11 Binary input functions 53
5.11.1 Binary inputs InteliDrive Lite - default configuration 53

InteliDrive Lite - 1.2.1 Global guide 4
5.11.2 Configuration of binary inputs 53
5.11.3 Binary inputs list 54
5.12 Binary output functions 59
5.12.1 Binary outputs InteliDrive Lite - default 60
5.12.2 Binary outputs - list 60
6 Communication 69
6.1 Direct cable connection 69
6.2 Remote connection 70
6.2.1 Internet connection 70
6.2.2 AirGate connection 70
6.2.3 Modem connection 71
6.3 Modbus connection 71
6.3.1 Modbus step by step 71
6.4 ECU engine support 72
6.5 Choosing the ECU to configure 72
6.6 ECU Analog inputs 74
6.7 Tier4 final support 74
7 Troubleshooting 78
7.1 Alarm management 78
7.1.1 Sensor fail (Fls) 78
7.1.2 Warning (Wrn) 78
7.1.3 Cooldown (Cd) 78
7.1.4 Shut down (Sd) 79
7.1.5 List of possible alarms 79
7.2 HistoryFile 81
7.2.1 RecordStructure 81
7.3 Diagnostic Messages read from ECU 82
7.4 List of ECU Diagnostic Codes 82
7.5 Tier4 diagnostic codes 83
8 Technical data 85
8.1 IL-NT RS232 (Optional card) 87
8.2 IL-NT RS232-485 (optional card) 87
8.3 IL-NT S-USB (optional card) 87
8.4 IB-Lite (optional card) 88
8.5 IL-NT GPRS (optional card) 88
8.6 IL-NT AOUT8 (optional card) 88
8.7 IL-NT AIO (optional card) 88

InteliDrive Lite - 1.2.1 Global guide 5
8.8 IL-NT IO1 (optional card) 89
8.9 IL-NT BIO8 (optional card) 89
8.10 IL-NT BIO8 (optional Remote Annunciator) 89
8.10.1 Power supply 89
8.10.2 Operating conditions 89
8.10.3 Dimensions and weight 89
8.10.4 Horn output 90
9 Function description 91
9.1 Engine operation states 91
9.2 OFF mode 91
9.3 MAN mode 91
9.3.1 Start-stop sequence (simplified) 92
9.4 AUT mode 94
9.5 Engine without pickup operation 94
9.6 Engine timer 94
9.6.1 MAN mode 94
9.6.2 AUT mode 95
9.7 Protections 95
9.8 Engine RPM control in MAN mode 96
9.8.1 Engine RPM Idle - Nominal switching 97
9.8.2 Engine RPM two/three levels switching 97
9.8.3 Engine RPM by Up/Down buttons settings 97
9.8.4 Engine RPM continuous change (using potentiometer) 97
9.8.5 Speed request chart 98
9.9 AUT mode: Engine load limitation - overview 98
9.9.1 Functions 1 and 2 99
9.9.2 Functions 1 and 2 setpoints 100
9.9.3 Functions 1 and 2 examples 100
9.10 AUT mode: Engine regulation by RPM control - overview 104
9.10.1 Functions 3 and 4 106
9.10.2 Functions 3 and 4 setpoints 106
9.10.3 Functions 3 and 4 examples 106
10 Appendix 109
10.1 Setpoints 109
10.1.1 List of setpoint groups 109
10.1.2 List of setpoints 110
10.1.3 Group: Password 113
10.1.4 Group: Basic settings 113

InteliDrive Lite - 1.2.1 Global guide 6
10.1.5 Group: Basic settings 2 116
10.1.6 Group: Comms settings 121
10.1.7 Group: Engine params 128
10.1.8 Group: Engine params 2 133
10.1.9 Group: Regulator 144
10.1.10 Group: Regulator 2 147
10.1.11 Group:Load limit 150
10.1.12 Group: Engine protect 154
10.1.13 Group: Engine protect 2 172
10.1.14 Group: ATT Settings 181
10.1.15 Group: Date/Time 182
10.1.16 Group: Sensor spec 190
10.1.17 Group: AIO module 196
10.1.18 Group: SMS_E-Mail 201
10.2 Values 204
10.3 Accessibility of setpoints and values 206
10.3.1 Available setpoints 206
11 Language support 211

InteliDrive Lite - 1.2.1 Global guide 7
1 Document information
1.1 Clarification of notation 7
1.2 About this guide 7
1.3 Legal notice 7
1.4 Conformity Declaration 9
Revision number Related sw. version Date
3 1.2.1 17.4.2019
2 1.2.1 15.7.2016
Table 1.1 Document history
Note: ComAp believes that all information provided herein is correct and reliable and reserves the right to
update at any time. ComAp does not assume any responsibility for its use unless otherwise expressly
undertaken.
1.1 Clarification of notation
Note: This type of paragraph calls readers attention to a notice or related theme.
IMPORTANT: This type of paragraph highlights a procedure, adjustment etc., which can cause a
damage or improper function of the equipment if not performed correctly and may not be clear at
first sight.
Example: This type of paragraph contains information that is used to illustrate how a specific function
works.
1.2 About this guide
This manual contains important instructions for ID-FLX-Lite controllers family that shall be followed during
installation and maintenance of the InteliDrive Lite engine controllers.
This manual describes ID-FLX-Lite application examples for single engine applications.
This manual provides general information how to install and operate InteliDrive Lite controller.
This manual is intended for operators of engines, for engine control panel builders or for everybody who is
concerned with installation, operation and maintenance of the engine applications.
1.3 Legal notice
This End User's Guide/Manual as part of the Documentation is an inseparable part of ComAp’s Product and
may be used exclusively according to the conditions defined in the “END USER or Distributor LICENSE
AGREEMENT CONDITIONS – COMAP CONTROL SYSTEMS SOFTWARE” (License Agreement) and/or in
the “ComAp a.s. Global terms and conditions for sale of Products and provision of Services” (Terms) and/or in
the “Standardní podmínky projektů komplexního řešení ke smlouvě o dílo, Standard Conditions for Supply of
Complete Solutions” (Conditions) as applicable.

InteliDrive Lite - 1.2.1 Global guide 8
ComAp’s License Agreement is governed by the Czech Civil Code 89/2012 Col., by the Authorship Act
121/2000 Col., by international treaties and by other relevant legal documents regulating protection of the
intellectual properties (TRIPS).
The End User and/or ComAp’s Distributor shall only be permitted to use this End User's Guide/Manual with
ComAp Control System Registered Products. The Documentation is not intended and applicable for any other
purpose.
Official version of the ComAp’s End User's Guide/Manual is the version published in English. ComAp reserves
the right to update this End User's Guide/Manual at any time. ComAp does not assume any responsibility for its
use outside of the scope of the Terms or the Conditions and the License Agreement.
Licensed End User is entitled to make only necessary number of copies of the End User's Guide/Manual. Any
translation of this End User's Guide/Manual without the prior written consent of ComAp is expressly prohibited!
Even if the prior written consent from ComAp is acquired, ComAp does not take any responsibility for the
content, trustworthiness and quality of any such translation. ComAp will deem a translation equal to this End
User's Guide/Manual only if it agrees to verify such translation. The terms and conditions of such verification
must be agreed in the written form and in advance.
For more details relating to the Ownership, Extent of Permitted Reproductions Term of Use of the
Documentation and to the Confidentiality rules please review and comply with the ComAp’s License
Agreement, Terms and Conditions available on www.comap-control.com.
Security Risk Disclaimer
Pay attention to the following recommendations and measures to increase the level of security of ComAp
products and services.
Please note that possible cyber-attacks cannot be fully avoided by the below mentioned recommendations and
set of measures already performed by ComAp, but by following them the cyber-attacks can be considerably
reduced and thereby to reduce the risk of damage. ComAp does not take any responsibility for the actions of
persons responsible for cyber-attacks, nor for any damage caused by the cyber-attack. However, ComAp is
prepared to provide technical support to resolve problems arising from such actions, including but not limited to
restoring settings prior to the cyber-attacks, backing up data, recommending other preventive measures against
any further attacks.
Warning: Some forms of technical support may be provided against payment. There is no legal or factual
entitlement for technical services provided in connection to resolving problems arising from cyber-attack or
other unauthorized accesses to ComAp's Products or Services.
General security recommendations and set of measures
1. AccessCode
• Change the AccessCode BEFORE the device is connected to a network.
• Use a secure AccessCode – ideally a random string of 8 characters containing lowercase, uppercase letters
and digits.
• For each device use a different AccessCode.
2. Password
• Change the password BEFORE the device enters a regular operation.
• Do not leave displays or PC tools unattended if an user, especially administrator, is logged in.
3. Controller Web interface
• The controller web interface at port TCP/80 is based on http, not https, and thus it is intended to be used only
in closed private network infrastructures.
• Avoid exposing the port TCP/80 to the public Internet.

InteliDrive Lite - 1.2.1 Global guide 9
4. MODBUS/TCP
• The MODBUS/TCP protocol (port TCP/502) is an instrumentation protocol designed to exchange data
between locally connected devices like sensors, I/O modules, controllers etc. From it’s nature it does not
contain any kind of security – neither encryption nor authentication. Thus it is intended to be used only in closed
private network infrastructures.
• Avoid exposing the port TCP/502 to the public Internet.
5. SNMP
• The SNMP protocol (port UDP/161) version 1,2 is not encrypted. Thus it is intended to be used only in closed
private network infrastructures.
• Avoid exposing the port UDP/161 to the public Internet.
1.4 Conformity Declaration
The following described machine complies with the appropriate basic safety and
health requirement of the EC Low Voltage Directive No: 73/23 / EEC and EC
Electromagnetic Compatibility Directive 89/336 / EEC based on its design and type,
as brought into circulation by us.
6back to Document information

InteliDrive Lite - 1.2.1 Global guide 10
2 System overview
2.1 Warnings 10
2.2 General description 10
2.3 Configurability and monitoring 11
6back to Table of contents
2.1 Warnings
InteliDrive Lite controller can be remotely controlled. In case of the work on the engine check, that nobody can
remotely start the engine.
To be sure:
Disconnect remote control via RS232 line,
Disconnect input REM START/STOP or
Disconnect output STARTER
Note: Because of large variety of InteliDrive Lite parameters setting, it is not possible to describe all
combination. Some of InteliDrive Lite functions are subject of changes depend on SW version.
Note: The data in this manual only describes the product and are not warranty of performance or characteristic.
Note: SW and HW must be compatible (e.g. ID-FLX-Lite firmware and ID-FLX-Lite hardware) otherwise the
function will be disabled. If wrong software is uploaded the message HARDWARE INCOMPATIBLE appears
on the controller screen.
Note: In the case of using Boot load (jumper) programming – close Boot jumper, follow instruction in LiteEdit
and upload correct software.
2.2 General description
The key feature of InteliDrive Lite is its easy-to-use operation and installation. Predefined configurations for
typical applications are available as well as user-defined configurations for special applications.
InteliDrive Lite is a comprehensive controller for single engines with extended support of electronic engines and
plug-in modules.
InteliDrive Lite controllers are equipped with a powerful graphic display showing icons, symbols and bar-graphs
for intuitive operation, which sets, together with high functionality, new standards in engine controls.
InteliDrive Lite provides gas engine support without ventilation.
Controller supports WebSupervisor system. This system enables engine fleet and assets management as well
as pure monitoring. Visit www.comap-control.com and www.websupervisor.net for more details about
WebSupervisor
The key features are:
ECU support - for singlespeed and allspeed engines e.g. Cummins, Volvo, JohnDeer etc.
Flexibility - with our extension modules e.g. IL-NT-AIO, IL-NT-BIO8 etc.

InteliDrive Lite - 1.2.1 Global guide 11
Communication - via communication modules e.g. IL-NT-GPRS, IB-Lite, IL-NT-S-USB and PC tools
WebServer, WebSupervisor, InteliMonitor etc.
Process logic - active control of engine, history log, configuration-no programming
2.3 Configurability and monitoring
InteliDrive IPC is used as configuration, monitoring and controlling tool LiteEdit software. For simple
configuration, monitoring and controlling can be used InteliMonitor.
2.3.1 Open connection from LiteEdit
PC tool LiteEdit is used for monitoring, programming and configuration of ID-FLX-Lite controllers.
1. Go to menu Connection and select the type of connection you desire.
Image 2.1 LiteEdit - connection menu
2. Enter controller address and further information depending on the selected connection type.
Note: For direct connection enter controller address

InteliDrive Lite - 1.2.1 Global guide 12
Note: For internet connection enter controller adress, IP adress of the IB-LITE Module fitted in the
controller you want to reach, acces code
3. You will see the Control window and you can continue with configuration of setpoints, inputs, outputs etc.
Image 2.2 LiteEdit control window
Note: For detail description of LiteEdit and InteliMonitor PC tools see the LiteEdit Reference Guide,
InteliMonitor Reference Guide and InteliDrive Communication Guide
2.3.2 Open connection from web browser
It is possible to connect from a web browser to InteliDrive IPC controllers, mounted with IB-Lite module (or IB-
NT with specific conditions) and connected to internet.
1. Open web browser
2. Enter IP address from controller Comms Settings: IBLite IP Addr
3. Access verification page appears

InteliDrive Lite - 1.2.1 Global guide 13
Image 2.3 Access verification page
4. Enter access code and Scada page appears
Image 2.4 Scada page
Note: You can try the WebServer from ComAp webpage. The access code is 0.
Note: WebSupervisor is possible to use as a control and monitor tool. For access is necessary to be registered.
Connection setting and other information you can find in the WebSupervisor Reference Guide.
2.3.3 Open connection from WinScope
WinScope is powerful PC tool for observation of controller’s states and measurements.
1. Go to menu Connection →Open connection... and select the type of connection you desire in Open
connection window (Inteli controllers).

InteliDrive Lite - 1.2.1 Global guide 15
3 Applications overview
3.1 Single applications
Basic wiring scheme for single engine, all engine data are transferred from ECU via CAN J1939 interface in
example below.
Note: The extension IGL-RA15 modules can be connected to CAN bus together with ECU.
Image 3.1 application description
6back to Table of contents

InteliDrive Lite - 1.2.1 Global guide 16
4 Installation and wiring
4.1 Putting it into operation 16
4.2 Mounting 28
4.3 Package contents 28
4.4 Terminal diagram and dimension 29
4.5 Extension plug-in modules 30
4.6 Communication modules 35
4.7 Remote modules 39
6back to Table of contents
4.1 Putting it into operation
4.1.1 How to install
To ensure proper function:
Wiring for binary inputs and analog inputs must not be run with power cables.
Analog and binary inputs should use shielded cables, especially when length >3m.
Note: During the configuration of controller or setpoints changes is required a password to the controller. The
default password from ComAp is “0”.
Grounding
To ensure proper function:
Use cable min. 2,5mm2.
Brass M4x10 screw with star washer securing ring type grounding terminal shall be used.
The negative “-“terminal of the battery has to be properly grounded.
Switchboard and engine has to be grounded in common spot.
Use cable as short as possible to the grounding point.
Wiring
Tightening torque, allowable wire size and type, for the Field-Wiring Terminals:
Based on terminal type PA256:
Specified tightening torque 0.5Nm (4.4 In-lb) 2EDGK:

InteliDrive Lite - 1.2.1 Global guide 17
Specified tightening torque 0.4Nm (3.5 In-lb)
For field type terminals:
Use only diameter 2.0-0.5mm (12-26AWG) conductor, rated for 75°C minimum.
For Generator Voltage terminals
Use only diameter 2.0-0.5mm (12-26AWG) conductor, rated for 90°C minimum.
Use copper conductors only.
Power supply
Use minimally power supply cable of 1.5 mm2.
IMPORTANT: Maximum continuous DC power supply voltage is 36VDC.
IMPORTANT: Maximum allowable DC power supply voltage is 39VDC.
The InteliDrive IPC power supply terminals are protected against large pulse power disturbances. When there is
a potential risk the controller being subjected to conditions outside its capabilities, an outside protection device
should be used.
Note: The InteliDrive IPC controller should be grounded properly in order to protect against lighting strikes!! The
maximum allowable current through the controller’s negative terminal is 4A (this is dependent on binary output
load).
For the connections with 12VDC power supply, the InteliDrive IPC includes internal capacitors that allow the
controller to continue operation during cranking if the battery voltage dip occurs. If the voltage before dip is 12V,
after 150ms the voltage recovers to 7V, the controller continues operating. During this voltage dip the controller
screen backlight can turn off and on but the controller keeps operating.
It is possible to further support the controller by connecting the external capacitor or I-LBA module.
The capacitor size depends on required time. It shall be approximately thousands of uF (microFarads). The
capacitor size should be 5000 uF to with stand 150 ms voltage dip under following conditions:
Voltage before dip is 12 V, after 150 ms the voltage recovers to minimum allowed voltage i.e. 8V
The I-LBA module ensures minimally 350 ms voltage dip under following conditions:

InteliDrive Lite - 1.2.1 Global guide 18
RS232 and other plug-in module is connected. Voltage before dip is 12 V and after 350 ms the voltage recovers
to minimum allowed voltage 5 V. The I-LBA enables controller operation from 5 V (for 10 to 30 sec). The wiring
resistance from battery should be up to 0.1 Ohm for I-LBA proper function.
Power supply fusing
A 1 A fuse should be connected in-line with the battery positive terminal to the controller and modules.
These items should never be connected directly to the starting battery.
Fuse value and type depends on number of connected devices and wire length. Recommended fuse (not fast)
type - T1A. Not fast due to internal capacitors charging during power up.
Binary output protections
Do not connect binary outputs directly to DC relays without protection diodes, even if they are not
connected directly to controller outputs.
Magnetic pick-up
To ensure proper function:
Use a shielded cable
Be aware of interference signal from Speed governor, if one speed pick up is used.
If engine will not start:

InteliDrive Lite - 1.2.1 Global guide 19
Check ground connection from pick-up to controllers, eventually disconnect ground connection to one of
them
Galvanic separate InteliDrive IPC RPM input using ComAp separation transformer RPM-ISO (1:1)
Use separate pick-up for Speed governor and InteliDrive IPC
Note: If RPM > 2 then the controller is in the state Not ready and the engine will not be allowed to start.
4.1.2 Analog inputs
On the InteliDrive IPC controller nine analog inputs are available. See the two tables here bellow with specific
characteristics.
All properties mentioned here can be modified by LiteEdit PC tool only, in the window Modify
Table of controller analog inputs
Input Range Default use Configurability of default use
AIN1 0 - 2,4 kW Oil pressure NO
AIN2 0 - 2,4 kW Engine temperature YES
AIN3 0 - 2,4 kW Fuel level YES
AIN4 0 - 40 V PumpSuction YES
AIN5 0 - 40 V PumpDischarge YES
AIN6 0 - 10 V PumpFlow YES
Note: The nominal range of Analog inputs measuring resistivity is 0- 2,4 kOhm, nevertheless the input is able to
measure up to 15 kOhm, but with lower precision.
Note: When Engine Control Unit is connected, it is possible to read InteliDrive IPC Analog inputs values AIN1,
2, 3 from CAN bus (J1939).

InteliDrive Lite - 1.2.1 Global guide 20
Table of analog inputs options
LiteEdit Modify Possibility
Type
Not used
Alarm
Monitoring
Analog input is not used
Analog input is used for monitoring and protection
Analog input is used only for monitoring
Name ... text
Name in history
Up to 14 ASCII characters
Up to 4 ASCII characters for the name used in history records
Config
Analog
Binary
Tri state
ECU
Analog measuring in specified range.
Binary: open/close - threshold 750 Ω or 2VDC (AIN6-AIN9)
Three (Triple)-state: open/close - threshold 750 Ω (only AIN1-
AIN3), failure <10 Ω or > 2400 Ω
Only for AIN1, 2 values are read from ECU unit
Alarm
properties
Direction
Under limit
Under step. Sensor fail does not activate protection.
Over limit
Overstep. Sensor fail does not activate protection.
UnderLimit+Fls
Under step and Sensor fail activates protection.
OverLimit+Fls
Overstep and Sensor fail activates protection.
Window prot.
Combination of Under and Over protection at the same analog
input
Type
Sensor fail
Warning
Wrn+Sd
CoolDown
Engine running
only
Check box: Alarms are valid only for running engines, if box is
checked
Sensor
Sensor name ... text
Resulotion: number of decimal points
Dimension: bar, %, °C, etc.
Table and graph: customize curves
Contact
type
NC
NO
Valid only for binary and three-state inputs
Valid only for binary and three-state inputs
Table of contents
Other ComAp Control System manuals
Popular Control System manuals by other brands
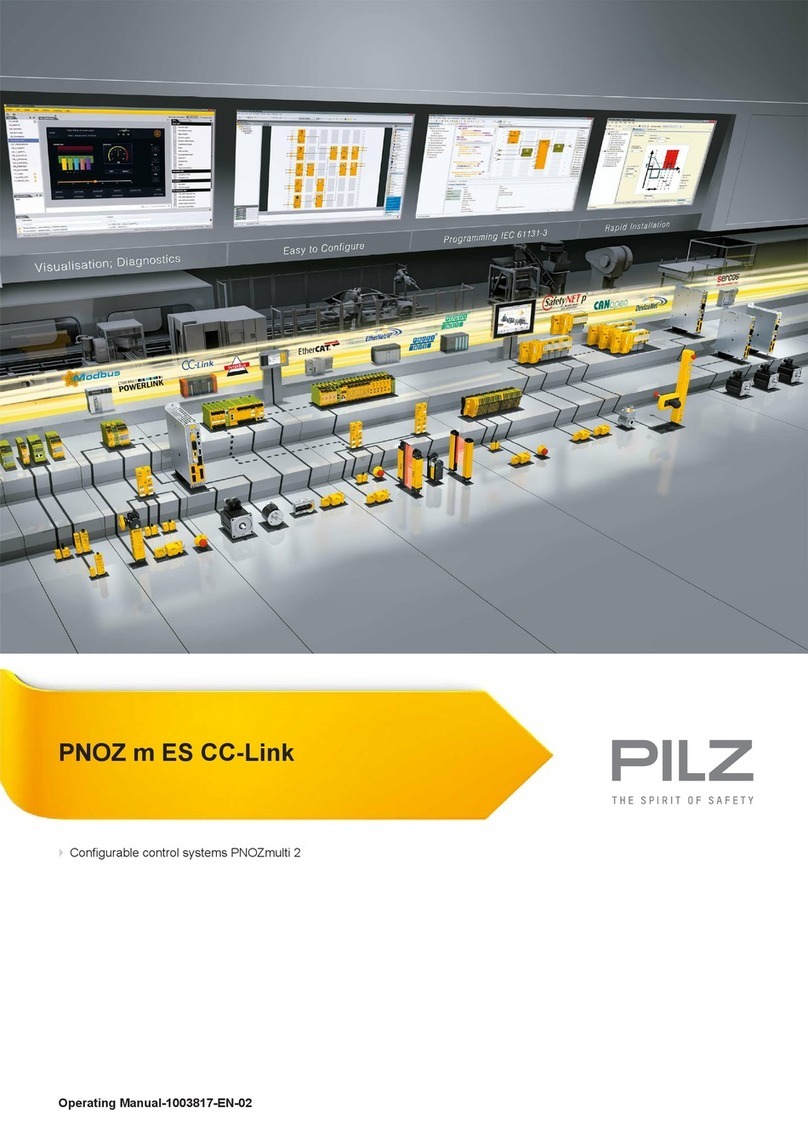
Pilz
Pilz PNOZ m ES CC-Link operating manual
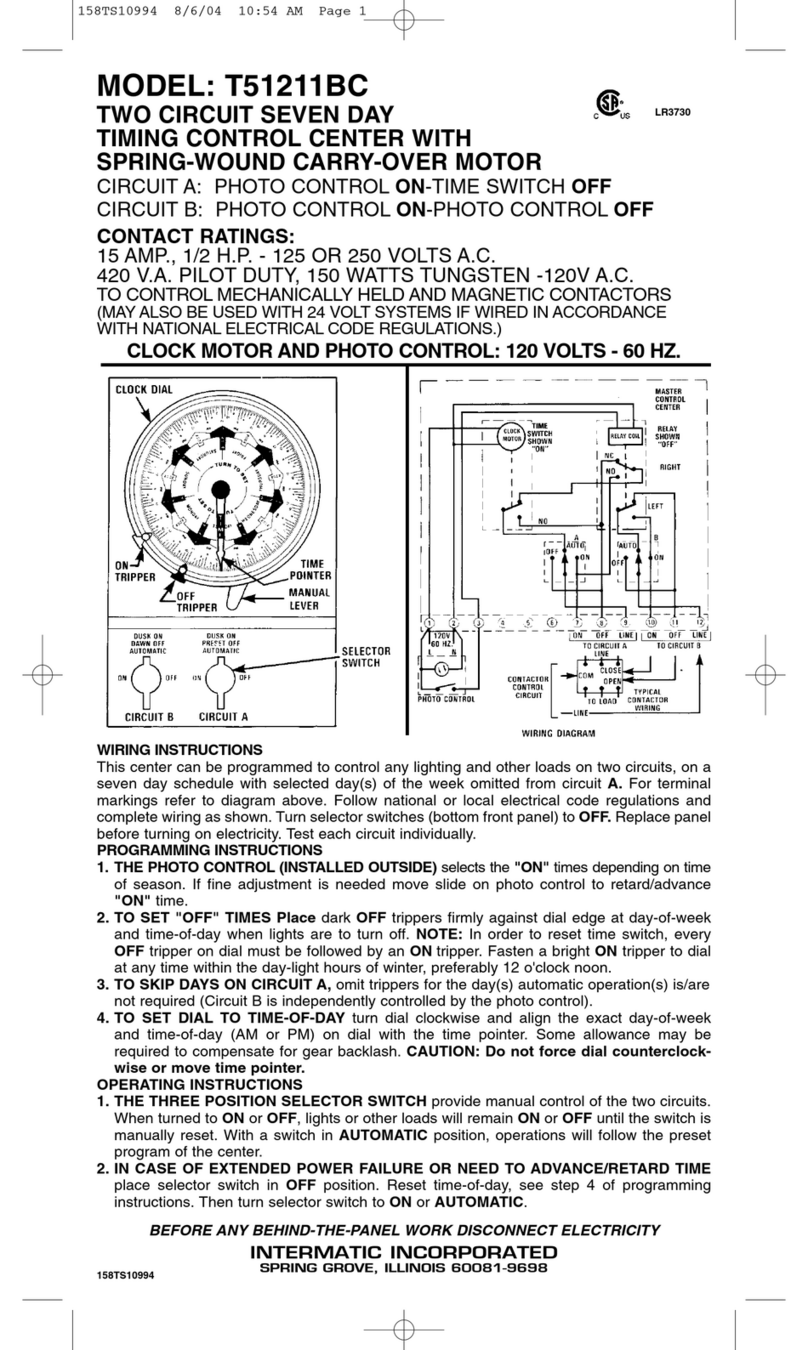
Intermatic
Intermatic T51211BC supplementary guide

Norac
Norac UC4.5 installation manual
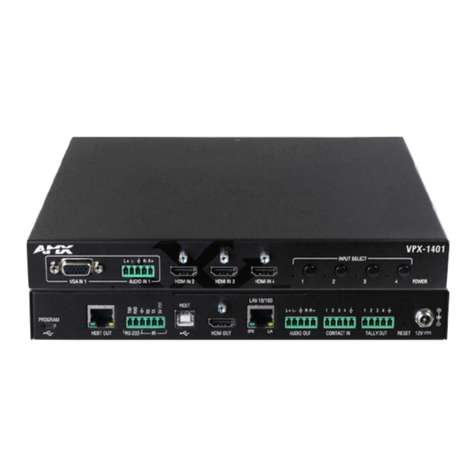
Harman
Harman AMX VPX-1401 user manual
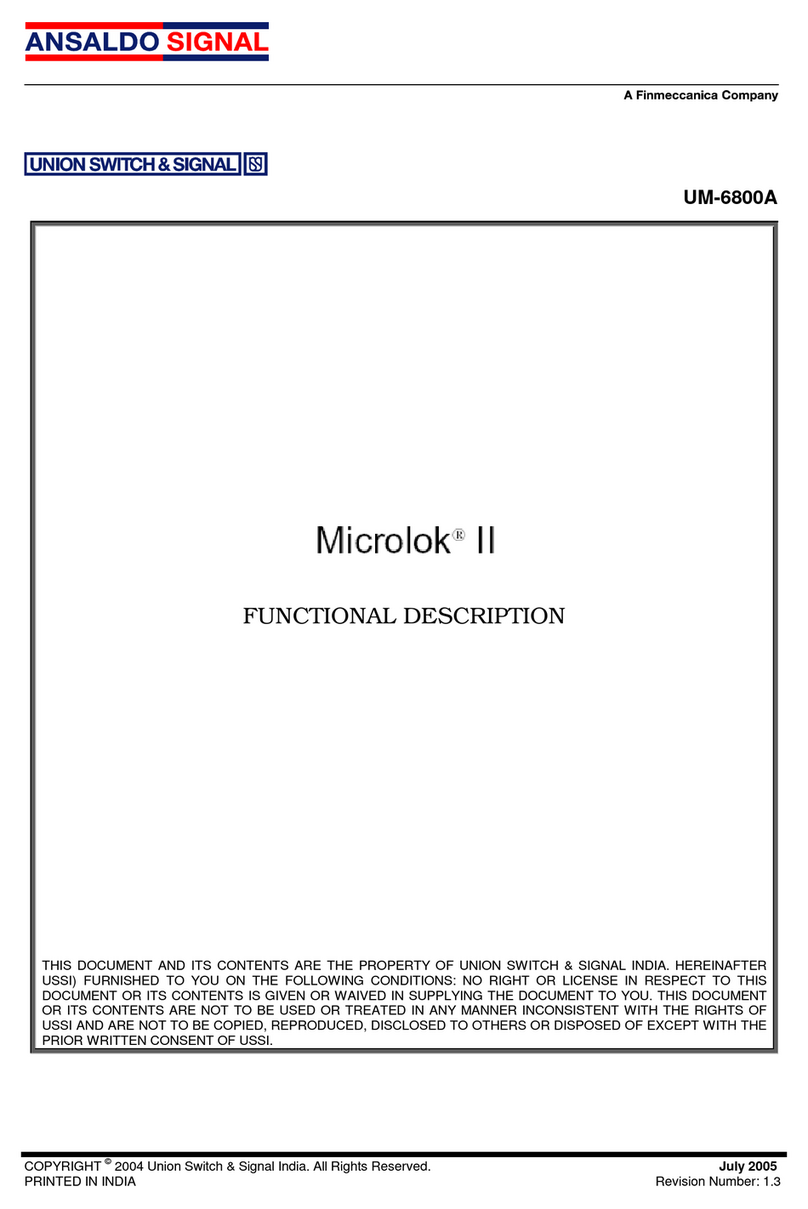
Union Switch & Signal
Union Switch & Signal Microlok II Functional description
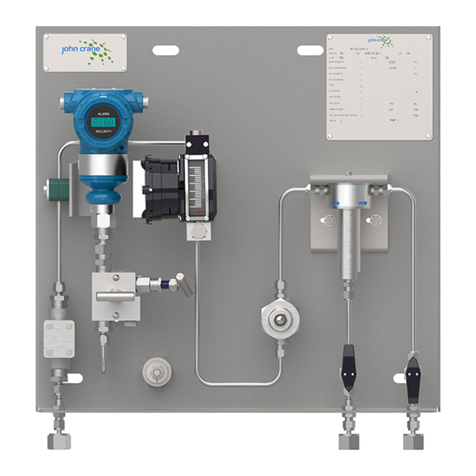
John Crane
John Crane API PLAN 74 STEAM Installation, operation & maintenance instructions