John Crane API PLAN 74 STEAM Guide

Installation, Operation & Maintenance Instructions
1
API PLAN 74 STEAM
SEAL SYSTEMS - STEAM
1. General
1.1 Introduction
Plan 74 Steam control panel may only be installed, commissioned and
maintained by an authorized plant machinery specialist, paying close
attention to these instructions and all other relevant regulations. Failure
to do this relieves the manufactures from any liability or warranties.
This Instruction Manual is provided to familiarize the user with the Plan
74 Steam control panel arrangement and its use. The instructions must
be read and applied whenever work is done on the Plan 74 Steam control
panel and must be available to the operating and maintenance personnel.
These instructions will help to avoid danger and increase reliability. They
should be used with the appropriate mechanical seal Instruction Manual.
The following important terms and definitions are used in this document.
1.2 European and/or UK Declaration of Incorporation
(Machinery Directive 2006/42/EC, and UK SI 2008 No. 1597)
If appropriate this is attached.
1.3 European Declaration of Conformity
(Pressure Equipment Directive, 2014/68/EU)
This directive is not applicable to Plan 74 Steam control panel.
1.4 European and/or UK Declaration of Conformity
(ATEX 2014/34/EU, and Equipment and UK SI 2016 No. 1107)
These instructions are intended for use with system operating in
Equipment Group II, category 2GD.
The Declaration covers the complete seal and system and the Maximum
Surface temperature is recorded in the Mechanical Seal Instruction Manual.
If appropriate this is attached.
2. Safety and Environment
The safety notes refer to the system supplied. They can never be exclusive,
and must be used in connection with the relevant safety regulations for the
machine, auxiliary equipment, plant and sealed product.
2.1 Warning symbols
The following symbols are used in this instruction manual to highlight
information of particular importance:
Danger
Mandatory instructions designed to prevent personal
injury or extensive damage.
Warning of electric current
ATTENTION Special instructions or information to avoid damage to
the system or its surroundings.
NOTE Information for easy installation and efficient operation.
Environmental note
Compliance is required with any additional warning signs affixed to the system.
2.2 Safety instructions
ATTENTION
Every working practice that compromises personal safety is to be
avoided. All safety requirements in this document must be strictly
adhered to.
In the event of an operating problem, the machinery must be switched off
immediately and made safe! Problems must be solved promptly.
Ensure suitable protective clothing is used when maintaining the system.
Plan 74 Steam control panel systems are commonly used with dual
mechanical seal configurations to reduce the hazard potential from
flammable, explosive, toxic or lethal process fluids. The intermediate,
protective steam barrier, in certain failure modes, may risk being
contaminated by the process fluid. During any maintenance operation
operators must thus assume they will be exposed to the liquid or
gaseous properties of the process fluid and have suitable protective
gloves, clothing, respirators and equipment.
Particular note must be taken of the relevant guidelines for the electrical
installations.
A slight leakage will occur during normal seal operation. Depending on
the duty, this leakage can appear as a gas, a liquid or a solid. In case of
a worn or defective seal the leakage will increase. The leakage may be
hazardous or toxic, and a safe collection system is required.
Surface temperatures above 60°C/140°F should be protected against
accidental contact. The panels may be mounted in a protective enclosure
for this purpose.
The equipment sealed by this seal system must be operated within its
recommended design limits.
Compounds containing PTFE, fluorocarbons and perfluoroelastomers
should never be burnt as the fumes and residues are highly toxic. If this
accidentally occurs protective equipment should be worn as hydrofluoric
acid may be present
Additional equipment/flanges/joint seals used within the system are to
be rated for the appropriate electrical and pressure requirements and are
to be chemically compatible with the buffer gas and process fluid.
• During venting or draining of the buffer region it should be piped to a
vent or reservoir where it can be safely contained or disposed.
• All above according to the local legislation.
• For further information and safe operating limits contact John Crane
• All periodical maintenance checks have to be in accordance with local
legislation and rules.
All welding or cutting operations are forbidden without permission from
John Crane.
If you are in any doubt please contact your local John Crane office for
further information before proceeding
2.3 Environmental aspects
2.3.1 Company policy extract
“It is the policy of John Crane to manage its business activities in an
environmentally responsible manner, comply with all relevant laws and
regulations, prevent pollution, and continually improve its environmental
performance, certification to the latest issue of ISO 14001 ensures compliance.”

Installation, Operation & Maintenance Instructions
2
API PLAN 74 STEAM
SEAL SYSTEMS - STEAM
John Crane adopts the ‘Design For the Environment’ (DFE)
principle in making this product. Using this product will benefit
the environment directly by:
• Reducing waste of precious resources through decreasing
the risk of leakage and minimizing energy consumption
• Preventing pollution through controlling harmful
emissions to the atmosphere and ground contamination
• Preserving valuable materials through the use of high
quality durable materials.
2.3.2 Recycling
Product refurbishment
This product has been designed for long life.
Disposal
When the product is considered to be beyond economical repair and
potential reuse, it should be disposed of by environmentally beneficial
means. The product can be disassembled with ease.
Scrapped components
These should be handled with extra care due to possible contamination.
They should be recycled through local industrial recycling plants.
Packaging
All packaging materials used are made from recyclable,
environmentally friendly materials.
When in doubt or for further information and advice on this subject,
please consult John Crane.
3. Transportation and Storage
Transport and store the system where possible in its original packaging.
It is necessary to protect and preserve the integrity of the equipment
between shipment and installation/start-up at site. This is particularly
important when extended periods of storage are envisaged.
Plan 74 Steam control panel systems may be shipped first to the rotating
equipment vendor to be mounted on the rotating equipment baseplate
complete with the connecting pipework. In this event follow the
instructions as given in the rotating equipment IOM.
Plan 74 Steam control panel systems, which are to be mounted off the
rotating equipment baseplate, shall be shipped directly to site and shall
be packed in suitable crates or cases to protect them from damage
during shipment. All openings to the system are closed and sealed for
shipping. In this event follow the following instructions.
On arrival at site and before unloading for storage, a visual inspection
of the crate/case should be carried out for signs of damage during
shipment. In the event of any damage the crate/case must be opened,
and the contents thoroughly examined for signs of equipment damage.
If any seals are broken, then the system is assumed to be contaminated
and shall be cleaned accordingly.
If the parts are considered acceptable with no visual signs of damage,
the crate/case should be properly closed again prior to storage.
After checking for shipment damage, the following recommendations
should be undertaken to prevent deterioration arising from long term
storage.
• Plan 74 Steam control panel system should be replaced in their
original packaging and if possible the crate/case should be stored
away from direct sunlight, in a well-ventilated building with a hard
floor.
• Temperature control is not normally necessary, but large temperature
fluctuations (>40°C/72°F) should be avoided.
• If stored outdoors, it is recommended that the crate/case be placed on
square timber bearers resting on a concrete or similar hard surface.
• The crate/case must then be wrapped with waterproof tarpaulin to
prevent ingress of water and dirt.
• Loose components or accessories in the case should be stored as
above, after proper itemization.
• A weekly visual external inspection of the protection and preservation
should be undertaken and any deficiencies noticed should be corrected
without delay.
• The system must be stored far from backwater to avoid the MIC
phenomenon (microbial corrosion).
NOTE Should water, condensation, sand, dirt or other contaminant
enter the system, through package/tarpaulin damage or
improperly positioned covers, the cause of the problem must
be eliminated and the equipment thoroughly dried and cleaned
before re-storing.
If used system parts are to be transported to the manufacturer or a third
party they have to be cleaned, decontaminated and require safe handling
instructions externally attached.
ATTENTION The system normally does not require any preservatives;
it is resistant against most environmental conditions.
Ensure preservatives and cleaning agents do not affect
the elastomers.
4. Description of the System
4.1 Function of the system
Where rotating machines (pumps, fans or mixers) work with hazardous
fluids, it is common practice to install double mechanical seals which
prevent leakage of the process fluid escaping into the surrounding
environment.
Non contacting dry running gas seals are frequently used for this
purpose.
The barrier fluid is clean dry steam, constantly supplied to the
mechanical seal inter-space from a reliable source at a pressure greater
than 2 bar (30 psi) above the product pressure. The Plan 74 Steam
control panel is specifically designed for using steam as this barrier gas.
The Plan 74 Steam control panel must maintain the correct pressure for
the steam, and condition it to separate any condensate before delivery to
the seal, and prevent condensate forming within the seal.
The Plan 74 Steam control panel consists of two panels, one upstream
of the mechanical seal, and one downstream of the mechanical seal.
The upstream panel includes a separating chamber to ensure that the
steam supply to the seal is free of condensate particulates. A steam trap
is present at the lowest point of the panel to release any condensate
from the separation chamber. A check-valve between the upstream panel

Installation, Operation & Maintenance Instructions
3
API PLAN 74 STEAM
SEAL SYSTEMS - STEAM
and the seal prevents contamination of the steam supply in an upset
condition. Seal operating pressure is set by adjusting the control panel
regulator in conjunction with the system pressure transmitter LCD read-
out, and/or pressure gauges if fitted.
The downstream panel serves the purpose of allowing any condensate
which forms in the seal to be routed to a steam trap to be released. The
downstream panel is normally the location for the pressure indicating
transmitter, and an additional pressure gauge.
Steam flows are visually monitored using the panel mounted pressure
transmitter to provide a common signal indicating loss of gas supply
pressure.
4.2 Instrumentation and fittings
The system is usually supplied with the following:
• Upstream steam supply inlet (flanged or threaded)
• Upstream panel outlet to seal (flanged or threaded)
• Upstream steam trap outlet (flanged or threaded)
• Upstream manual steam drain (flanged or threaded)
• Upstream pressure gauge (PG)
• Downstream steam inlet from seal (flanged or threaded)
• Alternative downstream steam inlet from seal - blanked (flanged or
threaded)
• Downstream steam trap outlet (flanged or threaded)
• Downstream manual steam drain (flanged or threaded)
• Downstream pressure gauge (PG)
• Downstream pressure indicating transmitter (PIT)
And, upon request with the following options:
• Pressure switch (PS) instead of a PIT
• Temperature indicating transmitter (TIT) mounted on pipe extension.
Supplied loose
5. Installation and Assembly
5.1 Before installation
Prior to installation ensure that internally all connecting pipe work
has been thoroughly cleaned. Remove protection caps from pipes and
connections. Check all fittings/connections for damage replacing if
necessary.
5.2 Control panel mounting
Refer to the appropriate arrangement drawing for mounting details.
It is recommended that piping between the each panel and the
mechanical seal should be kept below 2 meters/72 inches in length
wherever possible. If this length is exceeded consideration should be
given to increased frictional losses and if necessary allowances must be
made when setting the seal pressure.
The downstream panel must be mounted so that the steam inlet from the
seal, and the downstream steam traps are below the mechanical seal,
and the interconnecting pipework to the downstream panel must allow
condensate to gravity drain to the steam traps.
With the steam supply isolated, connect the steam supply piping to the
inlet connection on the upstream panel, connect the upstream panel
outlet connection to the mechanical seal gas barrier in (GBI) connection.
If a TIT is supplied, this must be mounted between the upstream outlet
connection and the mechanical seal. Connect the mechanical seal gas
barrier out (GBO) connection to the inlet connection of the downstream
panel. Do not open steam supply at this time.
Route the outlets to the steam traps and vent valve to a safe location to
expel steam and condensate.
It is recommended that all pipework be lagged, in
order to maintain the steam temperature, and to
protect personnel from accidental contact. Lagging
should be applied around all pipework and components
MECHANICAL
SEAL
UPSTREAM
STEAM OUTLET
TO MECHANICAL SEAL
DOWNSTREAM STEAM OUTLET
FROM MECHANICAL SEAL
PITPG
UPSTREAM STEAM
INLET PORT
PCV
PG
GLOBE
VALVE
OPTIONAL
NC
NCNO NO
NO
OPTIONAL
TW TE TIT
UPSTREAM
MANUAL
DRAIN
DOWNSTREAM
MANUAL
DRAIN
DOWNSTREAM
STEAM TRAP
OUTLET
UPSTREAM
STEAM TRAP
OUTLET
GLOBE
VALVE

Installation, Operation & Maintenance Instructions
4
API PLAN 74 STEAM
SEAL SYSTEMS - STEAM
during installation and assembly, leaving room to
read instruments and operative valves. If a protective
enclosure is supplied, this should also be fitted before
the system is brought up to temperature.
5.3 Electrical connections
Only authorized and qualified personnel are permitted to
carry out work on electrical systems. International and
local safety regulations must be followed in all cases.
Before connecting cables, check the electrical data on the name plate
matches the available power supply and complies with the area hazard
classification.
Refer to the diagrams in the terminal housing and the supplier's
instruction manual for wiring instructions. Connect the electrical
component using flexible conduit or armoured cable to assist removal of
the component for maintenance purposes.
If passive switching elements are installed in potentially explosive areas
you should add suitable protective devices, following the pertinent rules.
5.4 Leak check
During transit, tube fittings may work loose, check all fittings/
connections for tightness. First checking that the buffer gas supply
pressure is within the limits of the control panel slowly open the buffer
gas supply line isolation valves allowing the control panel to pressurize.
Using a suitable leak testing liquid, check all joints and if necessary,
rectify any leaks found.
6. Commissioning and Decommissioning
6.1 Commissioning
Before starting the machine (pump or mixer) carry out the following
operations:
ATTENTION Before commencing the start-up procedure, review
and become familiar with all the available instructions
concerning the equipment, especially the safety
warnings.
a) Set the operating pressure to the ‘operating pressure’ on the
nameplate (typically 2 barg/30 psig greater than the process pressure)
by adjusting the regulator valve until the correct pressure is shown on
the pressure transmitter LCD (and/or pressure gauge if fitted). Turning
the regulator adjuster clockwise increases pressure and counter-
clockwise decreases pressure.
b) Check that the pressure transmitter/switch set points are correctly
adjusted to suit the duty: Refer to the table below.
TABLE 1. Alarm Signals
Alarm Name Instrument Set Point Notes
Low Pressure
/Shutdown
Required
Pressure Indicating
Transmitter (PIT) or
Pressure Switch (PS)
If steam pressure drops
below the operating pressure
on the nameplate
REQUIRED
NOTE High flow alarms are not recommended on Plan 74 Steam
control panels with steam barrier gas, as the flow includes
both the consumption of the mechanical seal, condensation of
the steam and the steam/condensate released by the steam
traps, therefore flow monitoring is an unreliable method to
monitor performance of the mechanical seal.
c) Slowly open the drain valve and allow steam to flow through the system
d) Close the drain valve once the surface temperature of the piping
reaches 120°C/250°F
e) Verify the operating pressure is set at the correct pressure
f) Start the machine
g) During initial start-up, it is recommended that the steam pressure is
regularly monitored for correct operation. Fine tune pressure setting if
necessary.
6.2 Normal running
The equipment shall be kept clean and free from debris to allow ease
of access and reading of the instrumentation. Care should be taken to
prevent damage to the system from accidental knocks and/or exposure
to excessive sources or heat. Disconnection of any part of the system
should not be undertaken without the appropriate authorization and until
all pressure has been completely discharged and system allowed to
cool. All joints broken for maintenance should be plugged off to prevent
ingress of dirt.
During normal operation the only attention required is to monitor the
barrier steam pressure, and operation of the steam traps. Periodic visual
checking (at least every 48 hours) of the pressure within the system is
recommended.
6.3 Decommissioning
Work on the seal or system must only be carried out
when the machine is stationary, and secured against
any unforeseen start-up. Isolation from connections to
pressurization sources must be carried out.
Before carrying out any work on the seal or system, the equipment must
be shut down and the buffer region must be fully depressurized. Once
this has been done the buffer gas supply to the panel can be isolated.
Do not isolate the steam barrier supply before the pump is made
safe and the temperature has reduced to levels safe for handling.
Once the steam barrier supply is isolated carefully vent any residual
pressure from the Plan 74 Steam control panel and interconnecting pipe
work and drain any liquids before carrying out any maintenance.
If the pump/panel is to be removed cover any open tubing fittings/
connections to prevent contamination.
NOTE It is recommended that a pressure test is carried out on
the system after any repair and before operation on the
equipment.
7. Maintenance
7.1 Routine maintenance
Check the following as part of regular site walk-around checks for
trouble-free operation:

Installation, Operation & Maintenance Instructions
5
API PLAN 74 STEAM
SEAL SYSTEMS - STEAM
• Check the condition of the steam traps (see Section 7.2).
• Barrier pressure. Compare with the operating pressure on the
nameplate.
• Condition of alarm signals (see Section 7.3)
7.2 Steam traps
Steam traps have a finite life, the duration of which is determined by the
quantity of condensate to be released from the system. If a steam trap
has reached the end of its life, it will no longer operate, and condensate
will begin to build up in the system.
To check the operation, visually check for signs that condensate is being
released, and then slightly crack open the manual steam drain valve. If
condensate is released, this indicates that the steam trap is no longer
operating and liquid is building up inside the system. The steam trap(s)
should then be replaced at the earliest opportunity.
While operating the manual drain, the system is
pressurized with high temperature steam. Correct PPE
must be worn, the drain must be directed to a safe
location for the release of hot steam, and the valve
should be opened by the absolute minimum to reduce
the quantity of steam released, for personnel safety,
and to prevent a loss of pressure in the Plan 74 Steam
control panel.
It is recommended that the steam traps are checked after the first month
of operation and thereafter at monthly intervals.
Irrespective of visual condition, it is recommended that the steam traps
are replaced annually.
7.3 Signals and alarms
The instrumentation on the system has the specific purpose of signalling
eventual malfunction of the mechanical seals. Possible alarm signals
indicating a malfunction are as shown in Table 2.
TABLE 2. Possible Alarm Signals Indicating a Malfunction
Effect Instrument Action Cause
Falling Pressure
Pressure Gauge (PG)
or Pressure Indicating
Transmitter (PIT)
A C to E
Low Pressure/
Shutdown Required
Pressure Indicating
Transmitter (PIT) or
Pressure Switch (PS)
B C to E
Actions
A Investigate cause and monitor to ensure values do not breach
safe limits
B Shut down machine to prevent damage or loss of containment
Causes
C Excessive leakage across the inboard seal or outboard seal
D Pipe work/joint failure
E Drop in the barrier gas supply pressure/flow
The signal from the pressure transmitter can be used either:
• LOCALLY (with a Klaxon and/or beacon)
• REMOTELY (in the control room)
Consult the specific instrument manufacturers manual should there be a
malfunction.
If necessary for safety, the alarm signals could be used as a
trip function.
7.4 Instrument maintenance
All instruments require regular calibration, following local processes
and regulations. See the supplier's instruction manual for and additional
instructions for maintenance of electrical instruments.
7.5 Spare parts
Spare parts must conform to the established technical specifications of the
manufacturer. This is guaranteed with John Crane spare parts.
You are advised to stock the most important wear parts on site.
The following data is necessary for spare part orders:
• John Crane code/part number
• John Crane order/ref no.
• Part description
• Quantity
7.6 Annual maintenance checks
Disconnection shall be made by plant person in charge of authorization.
Before any maintenance operation the system, the machine must be
stopped and depressurized, the barrier pressure must be fully discharged,
and the equipment allowed to cool to ambient temperature.
A suitable container should be available to contain any liquid drained
from the barrier system.
All parts requiring maintenance must be thoroughly decontaminated prior
to any work commencing.
All joints should be checked for tightness and signs of steam barrier
leakage. If present, all flange joints should be checked for tightness and,
if necessary, gaskets changed using replacements available from John
Crane.
8. Accompanying Documents
Installation Drawing (job specific) or Typical Drawing and Operational
Data Sheet.
A name and data plate is fitted to each Plan 74 Steam control panel.
It contains references and part numbers which must be quoted in any
communication.
For replacement parts please contact your local John Crane
office, quoting the system code number.

6
Installation, Operation & Maintenance Instructions
If the products featured will be used in a potentially dangerous and/or hazardous process, your John Crane representative should be consulted prior to
their selection and use. In the interest of continuous development, John Crane Companies reserve the right to alter designs and specifications without
prior notice. It is dangerous to smoke while handling products made from PTFE. Old and new PTFE products must not be incinerated. ISO 9001 and
ISO14001 Certified, details available on request.
©2022 John Crane 02/22 johncrane.com IOM-APIPlan74Steam
North America
United States of America
Tel: 1-847-967-2400
Europe
United Kingdom
Tel: 44-1753-224000
Latin America
Brazil
Tel: 55-11-3371-2500
Middle East & Africa
United Arab Emirates
Tel: 971-481-27800
Asia Pacific
Singapore
Tel: 65-6518-1800
API PLAN 74 STEAM
SEAL SYSTEMS - STEAM
9. Cold Environments
For environments with low ambient temperatures, winterization features
may be added to the Plan 74 Steam control panel. These may include:
• The panel may be supplied mounted in a heated enclosure. The heating
element requires electrical connection as part of the installation and
assembly procedure (see Section 6.2)
• Heat tracing and/or insulation may be required to maintain the
temperature of the steam in the Plan 74 Steam control panel. This
heat tracing and/or insulation may be supplied with the Plan 74 Steam
control panel, or may be applied on site around all pipework and
components during installation and assembly, leaving room to read
instruments and operative valves.
• Heat tracing is likely to only be required during start-up or standby
conditions.
• Care must be taken during commissioning and operation, that the
Plan 74 Steam control panel is brought up to operating temperature
before the machine is started, and the correct temperature is
maintained throughout operation.
Table of contents
Popular Control System manuals by other brands
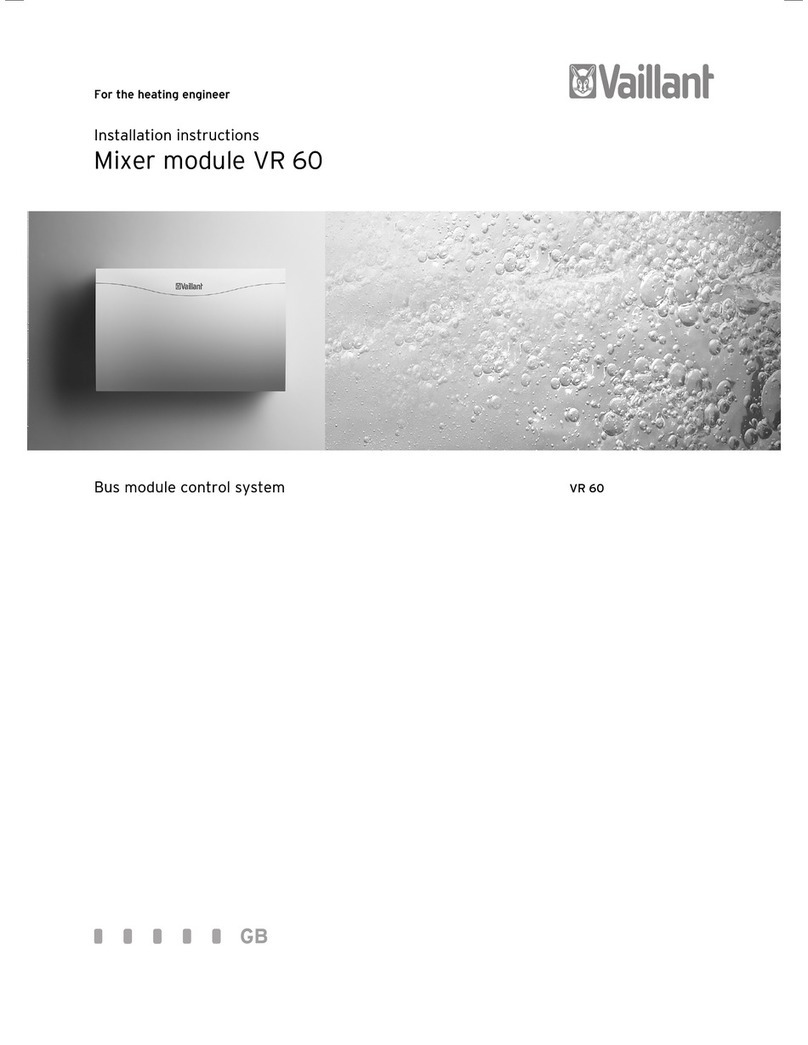
Vaillant
Vaillant Mixer module VR 60 installation instructions
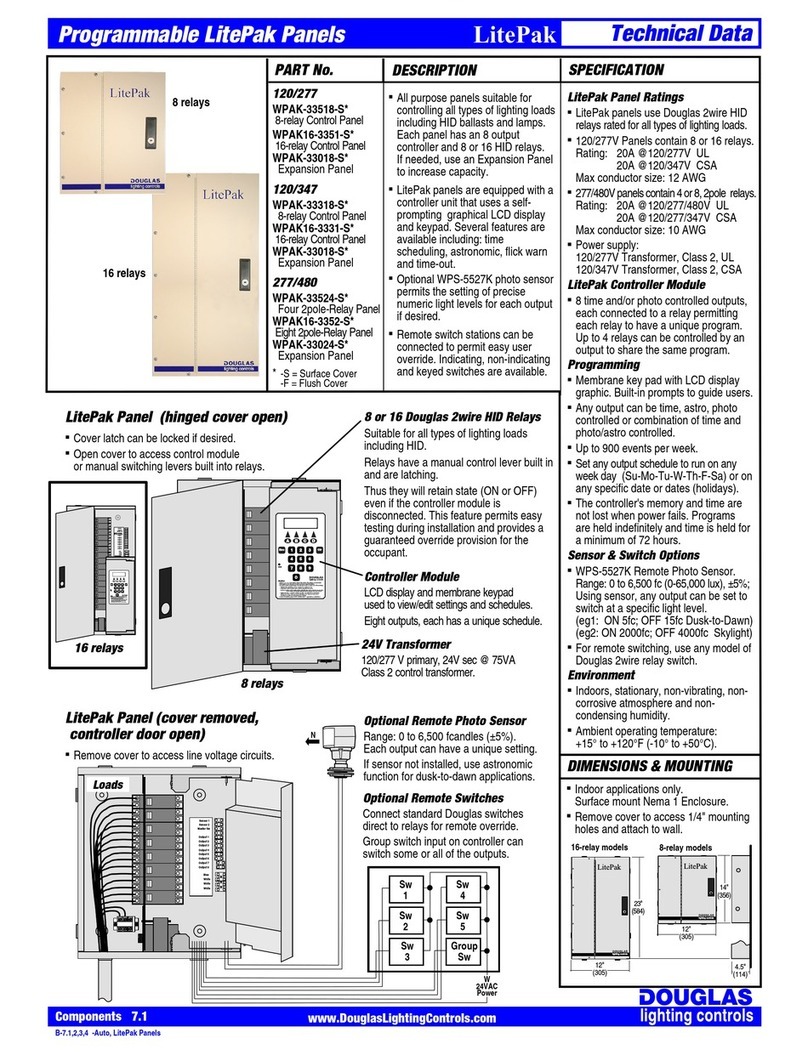
Douglas Lighting Controls
Douglas Lighting Controls LitePak WPAK-33518-S Technical data
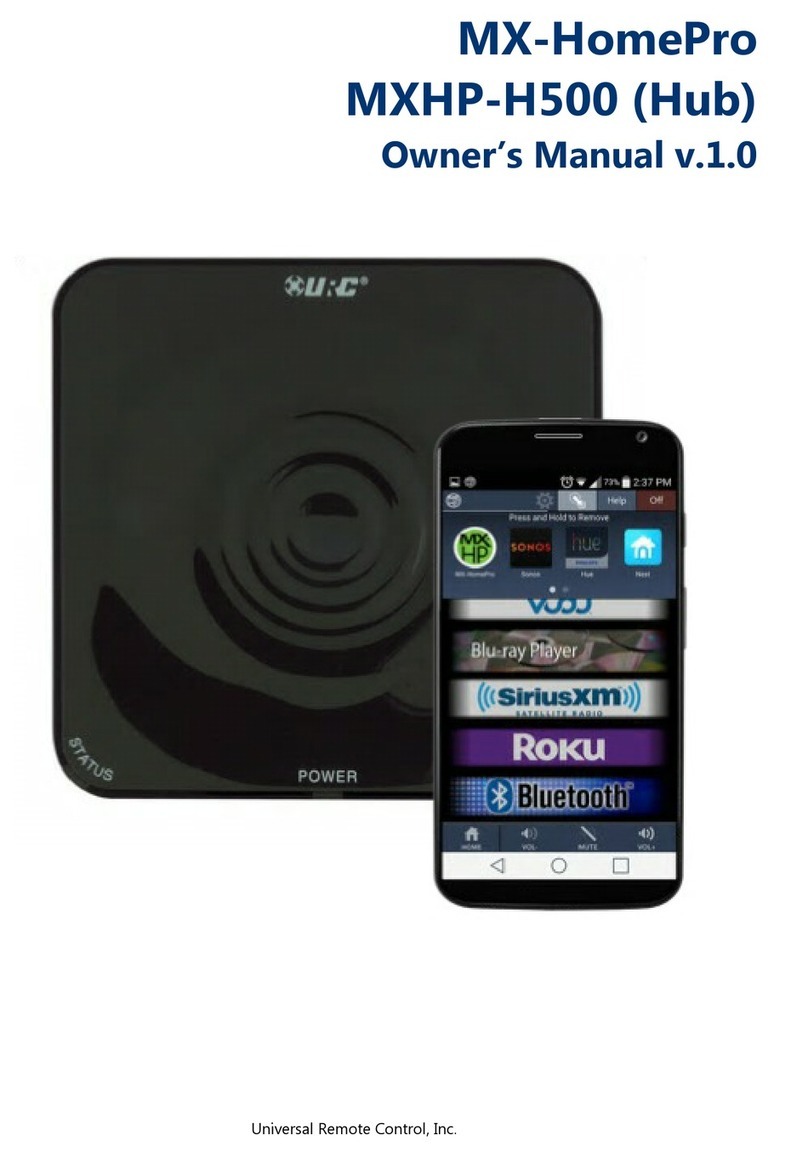
URC
URC MX-HomePro owner's manual
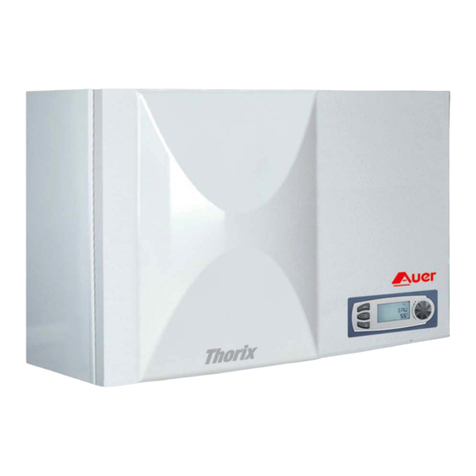
auer
auer Thorix EVOLUTION 2C Installation and operating instructions
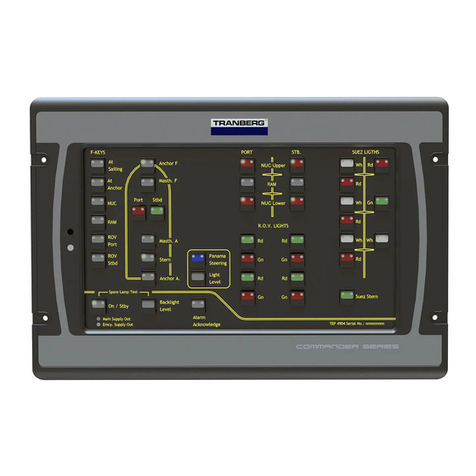
Tranberg
Tranberg TEF 4900 Installation and user manual
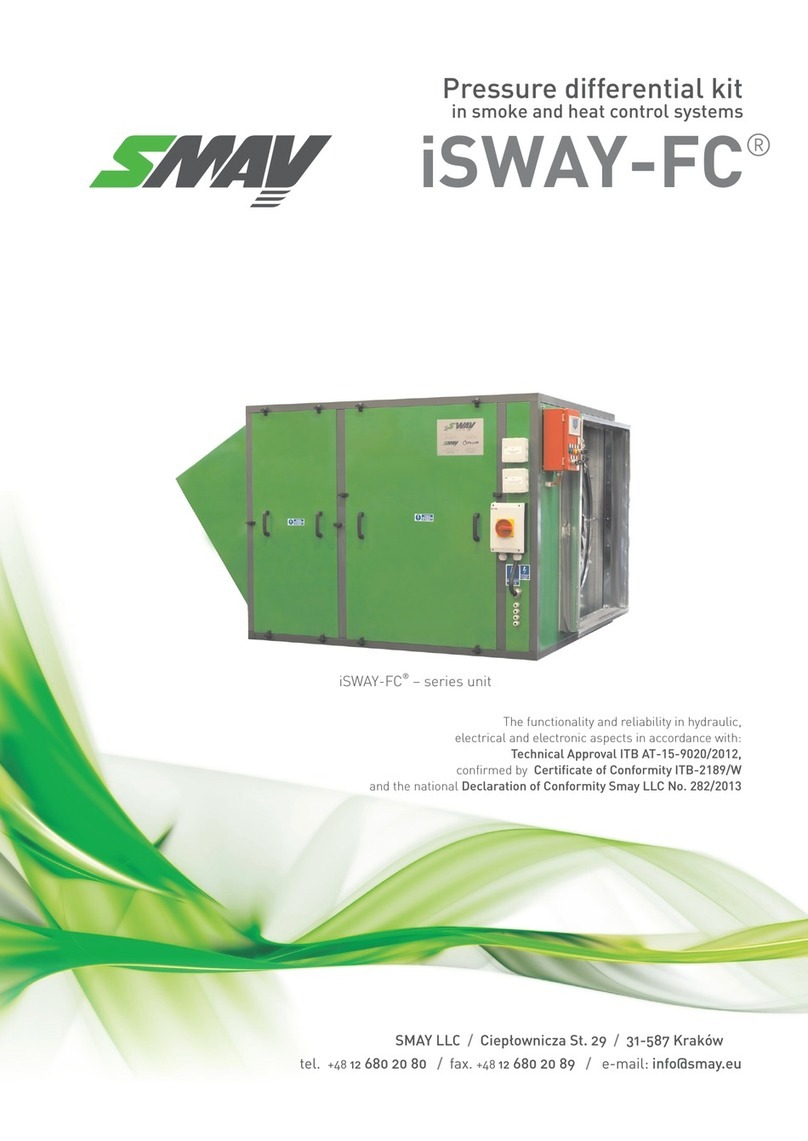
SMAY
SMAY iSWAY-FC manual