COMECO TC800 User manual

EIGHT-CHANNEL INDICATOR
TC800
Operation manual
Version: 4.2 revised: June 2012
Please read this manual BEFORE INSTALLATION!
COMECO Inc., P.O.Box 378, 4000 Plovdiv, Bulgaria
tel. +359 32 646523, 646524; fax +359 32 634089
e-mail: [email protected]rg, www.comecogroup.com

2
1. INTRODUCTION
1.1. Application
The multi-channel indicator/controller TC800 is used for indicating, monitoring, and controlling various
technological variables. With its compact size and up-to-eight inputs, the device may be successfully used
as a multi-channel limit monitor. TC800 may also serve as a two-, three-, and multi-stage ON/OFF controller, and,
thanks to its limit output relays, it may be also be used to control motorized valves.
1.2. Main features
Thermoresistive (RTD), thermocouple, and standard current and voltage signal inputs;
Discrete input for external channel selection;
Various programmable modes of operation;
A rich set of parameters for controller programming;
Protection against unauthorized access;
Software compensation of RTD sensor line resistance;
Cold-junction temperature compensation;
Sensor and sensor-line break monitoring;
Full self-testing;
Saving all parameters in nonvolatile memory; restoring at power-on;
Communication with PC via digital interface; connection of several devices into one network.
2. TECHNICAL SPECIFICATIONS
Analog inputs (up to 8 analog inputs):
SENSOR TYPE
LINEARISED INPUT SIGNAL RANGE
according to customer tables
thermoresistance (RTD) Pt50, Pt100, Pt500, Pt1000
-100.0...200.0 °C
thermoresistance (RTD) Cu50, Cu53, Cu100
0.0...200.0 °C
thermoresistance (RTD) Cu50, Cu53, Cu100
-50.0...200.0 °C
thermoresistance (RTD) Ni100
-60.0...200.0 °C
thermoresistance (RTD) Pt50, Pt100, Pt500, Pt1000
- 200...850 °C
thermoresistance (RTD) Ni100
-60...200 °C
voltage linear (Rin 1 GΩ)
0...2 V
voltage linear (Rin 1 GΩ)
0...5 V
voltage linear
0...10 V
custom voltage linear (on request)
within the limits 0...10 V
current linear (Rin 10 Ω)
0...20 mA
current linear (Rin 10 Ω)
4...20 mA
custom current linear (on request) (Rin 10 Ω)
within the limits 0...50 mA
thermocouple NiCr-Ni - type "K" (DIN)
0...1200 °C
thermocouple Fe-CuNi - type "J" (DIN)
0...800 °C
thermocouple Pt10%Rh-Pt - type "S" (DIN)
0...1600 °C
thermocouple NiCr-CuNi - type "E" (DIN)
0...1000 °C
thermocouple NiCr-CuNi - type "L" (GOST)
0...600 °C
thermocouple Cu-CuNi - type "T" (BDS)
0...400 °C
thermocouple Pt30%Rh-Pt6%Rh - type "B" (DIN)
200...1800 °C

3
When thermocouple inputs are ordered, a special temperature sensor is mounted near the input terminal
block. This temperature input is used by the device for cold-junction temperature compensation.
With a corresponding user configuration, this input may be used as any other input for displaying and alarm
functions, and may for instance signal device overheating.
Discrete inputs (2 discrete inputs):
DESCRIPTION
PARAMETERS
non-isolated TTL –
may be used as an "active" or "passive" input
for "passive" input: '0' at R < 50 Ω, '1' at R > 5 kΩ
for "active" input: '0' at U < 0.8 V, '1' at U > 2.4 V
Relay outputs (up to 8 programmable relay outputs):
DESCRIPTION
PARAMETERS
electromechanical relay (EMR)
max. 250 V, 3 A, NO or NO/NC
solid state relay (SSR)
max. 250 V AC, 1 A
MOS gate
max. 60 V, 0.1 A, optically isolated
output for external SSR
5...24 V, max. 30 mA
System alarm (1 system alarm):
DESCRIPTION
PARAMETERS
electromechanical relay (EMR)
max. 250 V, 3 A, NO/NC
Auxiliary supply voltage for external transmitters: 10…30 V, max. 40 mA (non-isolated)
Digital interface (optional): optically isolated RS485 with ASCII or Bynary protocol
Measurement error: 0.4% from span
Temperature drift: 0.005% from span for 1 °C
Cold junction compensation: 1 °C, automatic software
RTD line compensation: software
3. MOUNTING
Before starting any mounting and wiring operations, please read carefully chapter "Protection from electro-
magnetic disturbances". The requirements stated are important for normal and trouble-free device operation.
3.1. Protection from electromagnetic disturbances
For proper device functioning, some mounting and wiring requirements must be observed. The aim is
to reduce undesirable electromagnetic interference. Recommendations may include:
- Never lay signal wires close in parallel with power supply or actuator wires.
- Only similar signals may be run close together. Package input signal wires in twisted couples and shield.
- Signal cable branching and terminals are susceptible to noise and should be arranged away from noise sources.
- Connect reliably the ground at measurement point and
controller ground with thick stranded wire.
- All shields must be reliably grounded at one end, preferably
at your device end.
- Avoid sharing supply lines with powerful consumers,
especially inductive loads switched on and off.
- Use shielded 1:1 isolation transformer. A high quality anti-
interference filter may also prove useful.
Fig. 3.1
LINE
LINE
TO DEVICE
SUPPLY
TERM IN ALS
FROM
POWER
SUPPLY
TO DEVICE
SUPPLY
TERM IN ALS
NEUTRAL
NEUTRAL

4
To suppress high-voltage spikes, connect a metal-oxide varistor (MOV) in parallel with and as closer
as possible to the inductance (Fig. 3.2). An RC network in parallel with the varistor is highly recommended.
It should constitute of a 220 Ω resistor in series with a 0.5 μF / 1000 V capacitor. Select resistor power in relation
to the inductance voltage. Always use wire wound or carbon resistor. Keep RC network leads short.
INDUCTANCE
VOLTAGE, V
RESISTOR
POWER, W
115
0.25
230
1
460
3
550
4
When a contact opens and breaks inductive load circuit, a certain amount of
energy stored in the inductance has to be released. This causes both
electromagnetic interference and contact life shortening. To 'quieten' the
arc, connect an RC network in parallel with the contact (Fig. 3.3). For
circuits up to 3A / 300 V, the RC network should be made of a 47 Ω
resistor in series with a 0.1 μF / 1000 V capacitor. In cases of voltages
higher than 200 V, add MOV in parallel.
Please note that at 230 V, 50 Hz supply, up to 7 mA current may flow through the network.
Fig. 3.2 Fig. 3.3 Fig. 3.4
In parallel with the inductive load, connect a network consisting of a diode in series with a resistor. Mind that
the resistance should be less than that of the inductive load (Fig. 3.4).
3.2. Mounting
Select mounting location far from strong electrostatic or magnetic fields and protected from excessive heat
and moisture to ensure normal device operation. Place the device into a 90x90 mm panel cut-out and tightened
into place using the enclosed mounting brackets.
MOV
MOV
Fig. 3.5

5
3.3. Wiring
To wire, use the plug-in terminals on the back of the unit (Fig. 3.5).
Connect the analog inputs according to Fig. 3.6 and the discrete input – according to Fig. 3.7. To connect
the outputs, follow the diagram on Fig. 3.8.
Wire the digital interface as shown on Fig. 3.9, the main power supply – as shown on Fig. 3.10,
and the transmitter power supply – according to Fig. 3.11.
Fig. 3.6
Fig. 3.7 Fig. 3.8 Fig. 3.9
Fig. 3.10 Fig. 3.11
WARNING!
Auxiliary supply load capability
is max. 40 mA!

6
4. PRINCIPLE OF OPERATION, FEATURES, ALGORITHMS
The controller has up to 8 analog inputs (according to the customer order) plus (if thermocouple inputs are
present) a cold-junction temperature sensor input. All inputs are shown on display one after the other at regular
intervals. The upper display shows input channel number (the cold-junction temperature is coded with c), while
the lower display shows the measured value for that channel. When the input is thermoresistance (RTD),
thermocouple or cold-junction temperature sensor, the input range is fixed. In case of linear input, the operator
should configure the correspondence between display readings and lower and upper input analog signal values.
The controller may operate in 3 operating modes. In Auto mode, the rate of channel cycling on the display
is programmed by the operator. The operator selects which channels to be scanned and which of them to be
shown on the display. In Pseudo-manual mode, all inputs are scanned and all alarm limits are checked.
The display shows only one input channel. In manual mode, only one input is shown on the display and only
the alarms assigned to it are functioning.
There are 16 alarm limits (limit comparators) available. Each alarm may be assigned to any input and
may activate any relay output K1...8. The alarms and their assignations are freely user-programmable. Depending
on the selected alarm types, various functions may be configured, such as: 8-channel indicator
with 8 alarm outputs, 8 ON/OFF controllers, 4 ON/OFF controllers with 4 alarm outputs, etc.
If an alarm limit is exceeded, a corresponding LED is lit-up.
TC800 signals for any system failure or unexpected emergency situation by displaying a message and
activating relay output K9.
When digital interface is ordered, the device sends the required information at request over the interface.
Operation with the digital interface is described in the "Communication Protocol" section of this manual.
5. OPERATION
5.1. Device power-up
After power-on, TC800 performs an initial self-test, during which, all front-panel LEDs and display indicators
light up. This is intended to help eliminate a defective indication. At this moment, configuration mode may be entered
(see chapter 7). If no operator action is taken, though, the controller enters normal operation mode.
5.2. NORMAL OPERATION (default operation mode)
The device enters normal operation mode after the power supply has been turned on, the self-test has
finished and no operator action has been taken during that self-test.
A TC800 in normal operation mode is either in Auto, Pseudo-manual, or Manual mode. Note that, throughout
this document, Normal Operation means device operating in any of the stated 3 modes
with no failure message displayed and no programming state entered.
In case of system failure, a corresponding failure message is displayed regardless of the mode.
5.2.1. Auto mode
The upper display shows the number (the code) of the input channel, while the lower display shows the
measured value. The inputs are displayed cyclically one after another at regular, user-programmable intervals.
Although the display shows only one channel at a time, all inputs are measured and all alarm limits are
monitored constantly. If any alarm limit is exceeded, the corresponding LEDs light up and the relays assigned
to that alarm activate.

7
5.2.2. Pseudo-manual mode
To switch between Auto and Pseudo-auto modes, press . In Pseudo-auto mode, on its upper display,
TC800 indicates the sign = on the left of the input number (e.g., for input 6, the upper display will show =6, and
for the cold-junction temperature input – =c). In this mode, the cyclic displaying of the input channels stops
and only the last displayed input measurement stays on the display. To select manually which input to be shown
on the display, use or .
In this mode, the device continues to measure all inputs and to monitor all alarm limits.
The LEDs corresponding to the active alarm for the currently displayed input blink.
5.2.3. Manual mode
Entering this mode is possible from either Auto or Pseudo-manual mode by pressing while holding
( & ). If an access-control discrete input is configured to disable Manual mode, the message
d2 Prot is displayed for a while. If no such input is configured, but a password is assigned, TC800 enters
Manual mode only after the correct password has been entered. (see chapter 6.2).
While the device is in Manual mode, the sign Z blinks on the left of the input number on the upper display.
In Manual mode, the device functions as a single-channel indicator/controller. Only the currently
displayed input is measured, and only the alarms assigned to the currently displayed input are monitored.
To change the currently displayed input, use the key combinations & and & .
5.3. Relay output indication
The state of the relay outputs is indicated via LEDs on the front panel. When a relay is active, its
corresponding LED is lit up.
6. PROGRAMMING
6.1. Device internal organization
Device operation is controlled by the values of a number of parameters, sorted in the following groups:
CONFIGURATION, FAILURE STATES PROGRAMMING, DEFAULT THERMOCOUPLE COLD-JUNCTION
TEMPERATURE, INPUT CYCLING CHANGE RATE, SKIPPING OF SELECTED INPUTS IN THE DISPLAYED
SEQUENCE, and INFORMATION.
Fig. 6.1 shows all the parameter groups and the way they may be accessed.

8
6.2. Protection against unauthorized access
The operator may protect the controller from the attempts of unauthorized individuals to alter its programming.
The right of modifications may be restricted either by external key-operated switch or via a password. The access
to the configuration mode is always enabled, in case the password is forgotten. In cases, in which the operator
has no right of legitimate access, the parameter values are still readable, but cannot be changed!
6.2.1. External key for unauthorized access protection
A mechanical contact connected to a discrete input is used for access protection. An open circuit means
ACCESS ENABLED (changes may be made); a closed contact means ACCESS DISABLED (read-only access).
The external access authorization contact has a priority to password, i.e. if access authorization contact input
is configured, the password is disabled.
If the external contact is closed (access disabled), and an attempt to switch to Manual mode is made
( & ), d2 Prot is displayed and the mode remains the same. Similarly, when alarm programming
( & ) or cold-junction default temperature ( & , see also chapter 9) programming is started, the
parameters are displayed as usual, but their values cannot be changed.
POWER ON
CONFIGURATION
SELF-TEST
PASSWORD
NORMAL OPERATION
INDICATION OF MEASURED
VARIABLES
MODE SELECTION
PROGRAMMING: PREIOD OF INPUT CHANGE ON
DISPLAY, SKIPPING INPUTS IN DISPLAY SEQUENCE
PROGRAMMING: DEFAULT COLD JUNCTION
TEMPERATURE
FAILURE MESSAGES
PARAMETER PROGRAMMING
POWER ON

9
6.2.2. Password use
When no access authorization discrete input is configured, the access for parameter change may be
restricted by using a password. The password is in fact a number – the value of the parameter PASS from
the configuration parameter group. If the value is 0000, no password is required. For a password-protected
access, a value different from 0000 should be entered.
When the password is non-zero, at an attempt to switch from Auto to Manual mode ( & ),
or to enter parameter programming ( & or & ), TC800 requires the password.
Enter the password as you would any other parameter value (see chapters 6.6...6.10). If, when attempting
to switch to Manual mode, the entered password is INCORRECT, the mode change is not performed.
If an attempt to start programming with incorrect password is made, the parameter values cannot be changed.
When alarm programming is entered, the lower display shows the right for change: chnG – correct password
or rEAd – incorrect password (read-only mode).
A correctly entered password is valid 5 minutes after the last key pressing. This allows the operator
to enter the password only once and use it for the whole programming and testing session.
6.3. The tree arrangement of parameter groups
The groups of parameters concerning configuration, programming, and information contain a large number of
parameters. Therefore, these parameters are ordered in a tree-like arrangement.
A group consists of subgroups. Each subgroup may have its subgroups and so on. A subgroup that has no sub-
groups is in fact a parameter. Fig. 6.2 shows a typical tree-like parameter structure. The rectangles contain the names
of the groups, subgroups, and parameters, while the lines show which is part of which. To access a parameter, first
select the subgroup it is part of. The "movement" along the "tree" to access a parameter should follow the lines.
Group
Subgroup
Subgroup
Fig. 6.2
Subgroup
6.4. Moving along the parameter tree; accessing parameters
The tree unfolds to the right and downwards. This means that movement down and right leads to
a parameter, while moving left and up returns to the root of the tree. To move in any direction, use the respective key:
up
left
down
right
right
The messages that appear on the display with the movement along the tree and entering groups, subgroups,
and parameter programming are discussed in chapters "Programming", "Configuration", and "Device information".

10
6.5. Entering a parameter (parameter value adjustment)
After reaching a parameter by moving along the tree, press to read its value on the lower display.
If changing parameter value is possible, one or more of the digits are blinking.
Each parameter has a range of acceptable values. If an attempt to enter an unacceptable parameter value
has been made, the controller shows {++} , <__>, or ----on the lower display. If the change
is allowed, with the pressing of , the parameter is assigned its default value. This value may be changed and,
if acceptable, may be saved in controller memory.
6.6. Changing parameter value
Changing parameter value is possible only if the operator has the right (access) to do so! If the value or part
of it is blinking, it may be changed. If nothing is blinking on the display, no changes of the value are possible.
The decimal point of some of the parameters may be moved. This is indicated by the blinking of the dot itself.
The acceptable (allowed) values for a parameter are defined either by a minimum-to-maximum range or
a table of all acceptable values.
The blinking symbols may be changed by pressing or . When a certain set of acceptable values is
defined, the key selects the next value and the key – the previous value.
To select another digit for change, i.e. change the blinking digit, use and .
To move a blinking decimal dot to the left, press & ; to move it to the right, use & .
The decimal point may be moved to the right of the rightmost digit. The moving of the decimal dot does not
change the digits of the value.
6.7. Direct selection of minimum, maximum, and default value
&
minimum value
&
maximum value
default value
As a result, the position of the decimal point may also change.
6.8. Canceling parameter value change
Before the new value is saved in controller memory, the change may be cancelled and the initial value of the
parameter restored. To cancel the value change, press & .
It is possible to restore an old parameter value even after has been pressed (see 6.11).

11
6.9. Entering new parameter value
To set the parameter value shown on the display, press . If the new value is acceptable, the controller
saves it in its memory and exits parameter value adjustment. If the new value is not within the allowed limits, it is
not memorized, parameter value adjustment does not finish, and, instead of the value, {++} (too big) or
<__> (too small) blinks on the display. Press to display the default value. This value may be changed
and, if acceptable, successfully entered into controller memory.
Please note that new parameter values do not affect controller operation until the whole parameter
group programming is finished and the parameter group is exited!
6.10. Finishing parameter value changing / viewing
Press . If the value has been changed, pressing would also save the new value in memory (see 6.9).
6.11. Canceling the programming of whole group of parameters
As long as a parameter group has not been exited, all changes may be cancelled and the old values of all
the parameters from the group restored. This could be done with & , while anywhere on the parameter
tree, if no parameter value is shown on the display (you would have to quit parameter value adjustment first by
pressing the same key combination). The message LoAd on the lower display shows restoring of old values.
6.12. Finishing parameter group programming
Please note that until parameter group programming is exited, the newly set parameter values are not
actually stored into the permanent, nonvolatile controller memory. To not loose all changes, exit parameter group
programming by pressing & (if no parameter value is shown on the display; otherwise, first finish
parameter adjustment). When the changing of parameter values is allowed, at exiting the parameter group, TC800
checks all values, writes them into its permanent memory, and starts using them. The message Stor stays on
the lower display during the storing into the memory. Then the controller returns to normal operation.
If, for some reason, there is a parameter with unacceptable value in the group, the new values are not stored into
the permanent memory and group programming does NOT complete! The message Er shows on the upper display,
while the lower display shows the name of the parameter with unacceptable value. Press any key to start
parameter value adjustment and correct the value. It is possible for all parameters to have acceptable values by them-
selves, but the combinations of values to be unacceptable. Controller behavior is then similar. The group programming
does not finish. In this case, the message on the upper display is FL, while the lower one shows the type of the error.
The operator should press any key to start programming the value of the unacceptable parameter. The limitations
that are imposed on groups of parameters are described in the chapter discussing each of the parameter groups.
Please note that if the group is not exited via & , 5 minutes after the last key pressing the group
programming is automatically exited (time-out) and no parameter change is saved. The same canceling of parameter
changes will occur in case of a power-down or powerful electromagnetic disturbance causing controller reset.

12
6.13. Recommended sequence of device programming
It is recommended that the initial device programming be carried out in the following sequence:
Configuring
Switching to Manual mode (if the device is not already in it)
Alarm programming
Programming of cold-junction default temperature if there are thermocouple inputs
Setting rate of input display change
Disabling input visualization (skipping inputs on display)
7. CONFIGURATION
Configuring means programming parameters that rarely need to be changed and that are usually defined
once – at installation – such as the parameters defining input use, RTD line resistance, and linear input ranges.
7.1. Entering configuration mode
At start-up, after the self-test, all LEDs blink for a moment. To enter configuration mode, press
& while the LEDs are blinking. To exit configuration mode, use the same combination of keys.
Changing the values of the parameters from the configuration parameter group is always possible and is
NOT protected by a password or external access restriction contact.
7.2. Main parameter tree of configuration
cF
yc*
Q1
Q#
s1
Fig. 7.1
s2
* the parameter yc is present only if the device has at least one thermocouple input.
# denotes analog input number (1...8); it depends on the number of inputs actually present in the device.
After configuration mode is entered, cF appears on the upper display, while the lower one shows
the name of the first input - yc or Q1. To browse the list of input types, use and , and to select
an input, press . The name of the selected input stays on the upper display as long as all its parameters are
being programmed, except for the PASS parameter, during whose adjustment the upper display shows PA.
The device may be equipped with up to 8 analog and 2 discrete inputs (various numbers may be ordered).
When thermocouple inputs are present, there is also a cold-junction temperature input present.

13
7.3. Cold-junction temperature input configuration
This input is present if the device has a thermocouple input. It is automatically used for cold-junction temperature
compensation. The parameter yc defines whether this input (its measurements) would also be available for
assignation to alarms and indication on front panel display in normal mode.
parameter yc
VALUE
COMMENT
YES
The input for compensation of cold-junction thermocouple temperature is also used
for alarms and is displayed in normal mode.
no
The input is used only for compensation of cold-junction thermocouple temperature.
It is not available for alarms and is not displayed in normal mode.
default value: no
7.4. Analog input configuration
Each analog input must first be programmed as enabled (to indicate that it will be used).
Q#
uSE
Fig. 7.2
7.4.1. Enabling / disabling of analog inputs
parameter uSE
VALUE
COMMENT
YES
Input enabled (in use)
no
Input disabled (not in use – nothing connected to it)
default value: no
If the parameter is set to YES, more parameters might automatically appear depending on the type of the
input.
7.4.2. Offsetting the input value of non-linear input
When the device has a non-linear input (thermoresistance or thermocouple), the parameter oF is used
to offset the input value.
The parameter tree is:
Q#
uSE
=YES
Fig. 7.3
oF
PARAMETER
MINIMUM
MAXIMUM
UNIT
DEFAULT
oF
-100
100
selected by operator
0

14
7.4.3. Line resistance of RTD (thermoresistance) input
When the device has a thermoresistance input, the parameter Ri is used to define the line resistance
(the resistance of the copper cable connecting the sensor). This resistance must first be measured during installation.
The parameter tree for RTD input is:
Q#
uSE
=YES
oF
Fig. 7.4
Ri
PARAMETER
MINIMUM
MAXIMUM
UNIT
DEFAULT
Ri
)0
(9
)0
With line resistances over 3 Ω, the measurement range gets narrower with as many degrees Celsius
as the temperature corresponding to the surplus resistance!
7.4.4. Programming the range of linear inputs
In case of a linear input, the parameter Lo is used to specify the value corresponding to the lowest input
current or voltage. Similarly, hi defines the value corresponding to the highest input current or voltage.
The parameter tree is:
Q#
uSE
=YES
Lo
Fig. 7.5
hi
Lower range limit of linear input
PARAMETER
MINIMUM
MAXIMUM
UNIT
DEFAULT
Lo
`999
9999
selected by operator
O
Upper range limit of linear input
PARAMETER
MINIMUM
MAXIMUM
UNIT
DEFAULT
hi
`999
9999
selected by operator
100
7.5. Programming of first discrete input to switch the channels
externally
When the device has 1 discrete input, the parameter s1 is used to enable the input and define its use.
parameter s1
VALUE
COMMENT
YES
The input is used for external switching of the channels.
no
The input is not used (not used for external switching of the channels)
default value: no

15
7.6. Programming of second discrete input
for enabling / disabling parameter programming
(unauthorized access protection)
When 2 discrete inputs are ordered, the parameter s2 is used to define whether the parameter
programming would be protected by an external switch or not. If this option is used, a closed contact would mean
"parameter changes disabled", while an open contact would mean "parameter changes enabled".
Configuration parameters are not protected by this input!
parameter s2
VALUE
COMMENT
YES
Use an external switch (key lock) to protect parameter changes.
no
Do not use an external switch (key lock) to protect parameter changes.
default value: no
7.7. Password configuration
When parameter s2 value is no, the operator may still protect parameters from unauthorized access by
using a password. The password value is a number that is set by programming the value of the parameter PASS.
cF
s2
=no
Fig. 7.6
PASS
The password is an integer positive number.
PARAMETER
MINIMUM
MAXIMUM
DEFAULT
PASS
0000
9999
0000
If the value is 0000 or a discrete input for unauthorized protection is configured, the password is not used
(no password).
7.8. Limitations in configuration
The only limitation is that there should be at least one enabled input. Otherwise, when exiting the parameter
group is attempted, the device displays the messages FL nOQi and waits for the operator to enable an input.
8. ALARM PARAMETER PROGRAMMING
8.1. Starting alarm parameter programming
To start alarm programming, press & . Protection from authorized access may be active (see 6.2).
To exit alarm parameter programming, use the same key combination.

16
8.2. Selecting alarm; entering new parameter values
After entering alarm programming, select one of the available alarms. Read the currently selected alarm
number on the upper display, and rEAd (read-only) or chnG (change possible) on the lower one.
Use and to select any of the 16 alarms. When the desired alarm number is shown on the upper
display, press to strat the programming of the selected alarm. Alarm parameters are arranged
in a parameter tree. Move along the parameter tree and change values as described in chapters 6.4...6.10.
During the parameter programming for the selected alarm, the alarm number stays on the upper display.
After programming the parameters of the alarm, confirm that alarm parameter group by pressing & .
The controller stores the parameters in its permanent memory (see 6.12) and starts using the new values.
The device then waits for another alarm to be selected and its parameters reprogrammed.
8.3. Alarm parameter tree – general view
##
uSE
Fig. 8.1
Depending on the value of the parameter uSE, the alarm parameter tree may change automatically.
8.4. Alarm parameter programming
When an alarm is programmed, first it should be either enabled or disabled via the uSE parameter.
parameter uSE
VALUE
MEANING
no
Alarm not used
YES
Alarm used
default value: no
8.4.1. Disabling an alarm
If the value of the parameter uSE is programmed to no, the function of the alarm is disabled and all its
functions are cancelled. To use the alarm again, change the parameter uSE value back to YES. This will
restore all other parameters of the alarm to their old values.
8.4.2. Enabling and using an alarm
If the value of the parameter uSE is YES, other parameters appear in the tree to allow the operator to
assign the alarm to some input, program its type and limits, and assign its output to some relay output.
The parameter tree is:
##
uSE
=YES
inP
Fig. 8.2
tYPE
## is the alarm number
from 1 to 16.

17
8.5. Alarm input
If the parameter uSE is set to YES, the next parameter – inP – is used to select the input number.
parameter inP
PARAMETER
MINIMUM
MAXIMUM
DEFAULT
inP
yxin / Qim1*
Qim #
Qim1
* depending on whether the device has a cold-junction temperature input or not.
The sign # denotes the number of actually ordered inputs (from 1 to 8).
8.6. Alarm type
The parameter tYPE is used for defining alarm type.
parameter tYPE
VALUE
COMMENT
__g+
Upper limit alarm type
+7__
Lower limit alarm type
_g7_
Window type alarm (active between limits)
7__g
Inverted window type alarm (active outside the limits)
8.6.1. Upper limit alarm type
When the parameter tYPE value is __g+, the parameter tree becomes:
##
uSE
=YES
inP
tYPE
=__g+
AlL
hYSt
hoLd
Fig. 8.3
outP
The static correspondence between alarm input and alarm state is shown on Fig. 8.4.
Fig. 8.4

18
The following parameters are to be programmed:
8.6.1.1. Alarm limit
parameter AlL
PARAMETER
MIN.
MAX.
UNIT
DEFAULT
AlL
`999
9999
depending on the selected input in inP
0000
8.6.1.2. Hysteresis
parameter hYSt
PARAMETER
MIN.
MAX.
UNIT
DEFAULT
hYSt
0000
9999
depending on the selected input in inP
0000
8.6.1.3. Hold time
parameter hoLd
PARAMETER
MIN.
MAX.
UNIT
DEFAULT
hoLd
0)0
1@0
seconds
0)0
This parameter is assigned to hold the alarm reaction for certain period of time for eliminating undesirable
switches of the alarm output.
8.6.1.4. Relay connected to alarm output
parameter outP
VALUE
COMMENT
nonE
No relay is assined to alarm output (only front-panel LED is used)
rEL1 -rEL8
Relay number
Only the actually mounted relays are available.
Relay K9, if installed, cannot be assigned to an alarm output, but is used to signal system failure.
Be aware that it might be activated not only by the alarm, but also because of some other failure.
8.6.2. Low limit alarm type
When the parameter tYPE value is +7__,the parameter tree becomes the same as that for
the upper limit type alarm. The parameters have the same meaning. The only difference is in the static
correspondence between alarm input and alarm state (Fig. 8.5).
Fig. 8.5

19
8.6.3. Window alarm type
The static correspondence between alarm input and alarm state is shown on Fig. 8.7
When the parameter tYPE value is _g7_, the parameter tree becomes:
##
uSE
=YES
inP
tYPE
=_g7_
LOL
hIL
hYSt
hoLd
Fig. 8.6
outP
The parameters hYSt,hoLd, and outP have the same meaning as for upper and lower limit
alarm.
Fig. 8.7
The following parameters are to be programmed:
8.6.3.1. Lower alarm window limit
parameter LOL
PARAMETER
MIN.
MAX.
UNIT
DEFAULT
LOL
`999
9999
depending on the selected input in inP
0000
8.6.3.2. Upper alarm window limit
parameter hIL
PARAMETER
MIN.
MAX.
UNIT
DEFAULT
hIL
`999
9999
depending on the selected input in inP
0000

20
8.6.4. Inverted window alarm type
Fig. 8.8
When the parameter tYPE value is 7__g,the parameter tree becomes the same as that for
the window type alarm. The parameters have the same meaning. The only difference is in the static
correspondence between alarm input and alarm state (Fig. 8.8).
8.7. Limitations of alarm programming
These are limitations concerning unacceptable correspondence among parameters or among parameters
and measured input value limit. If such a limitation is violated, at an attempt to finish current alarm parameter
programming, one of the following FL messages is displayed:
inP - alarm is assigned to an input that is not enabled. Assign the alarm to another input or configure
this input as enabled (used) – see chapter 7.
lGWH - for window or inverted window alarm type, the lower limit is higher than upper limit. Correct one
of the limits or interchange their values.
rnfL - alarm limit is lower than the lowest measurable input value. Increase the AlL or LOL value.
rnfH - alarm limit is higher than the highest measurable input value. Decrease the AlL or LOL value.
HYSt - alarm limits are inside the measurable range but the hysteresis value is outside the input
measurement range. Decrease hysteresis value or change an alarm limit.
9. PROGRAMMING OF THERMOCOUPLE COLD-JUNCTION
TEMPERATURE DEFAULT VALUE
This parameter is accessible from normal operation mode and only if the device has at least one thermocouple
input. To display the parameter, press & . The value of this parameter is used in the very rare cases of
cold-junction temperature sensor failure. The sensor is located near the back-panel input terminals.
parameter sc
PARAMETER
MIN.
MAX.
UNIT
DEFAULT
sc
-2)0
10)0
C
2%0
The access to this parameter may be restricted as described in chapter 6.2. If change is not allowed,
the parameter would be only visible to read. At an attempt for changing the parameter on a TC800 without
thermocouple inputs, the device displays the no yxin message.
Table of contents
Other COMECO Measuring Instrument manuals
Popular Measuring Instrument manuals by other brands
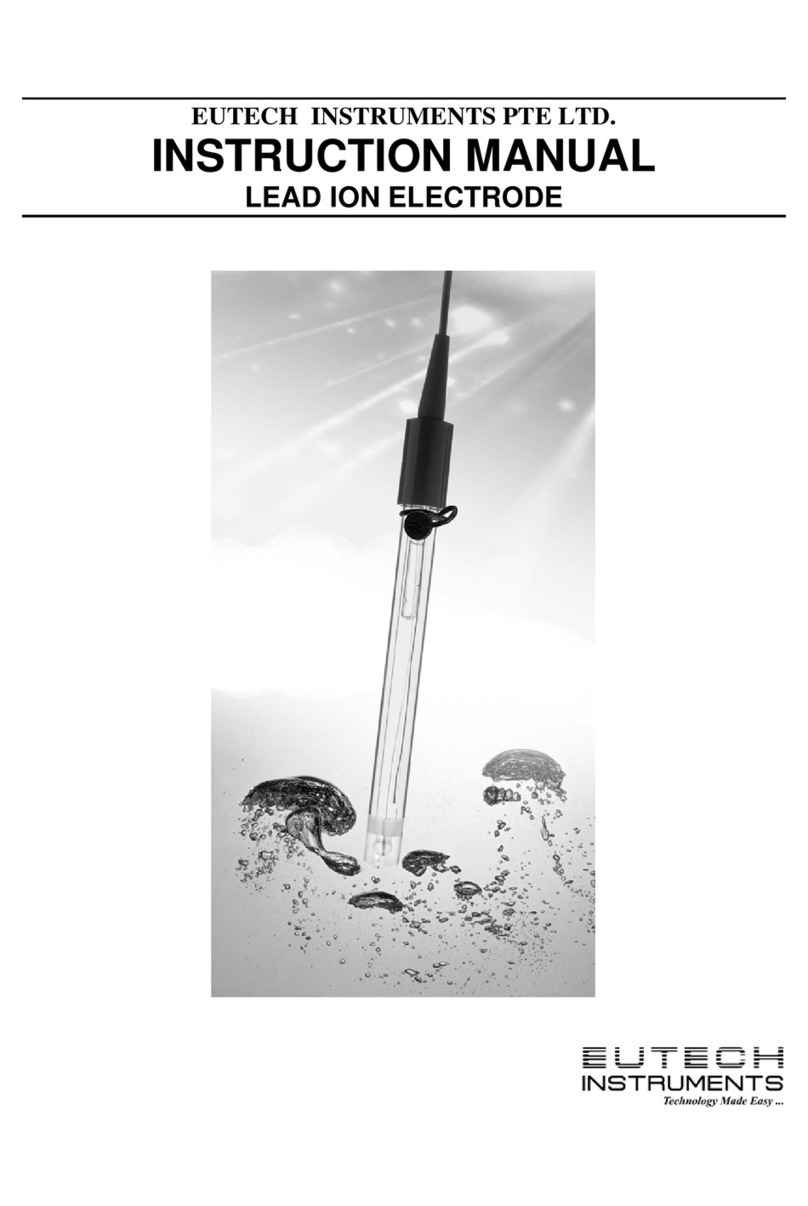
EUTECH INSTRUMENTS
EUTECH INSTRUMENTS LEAD EPOXY instruction manual
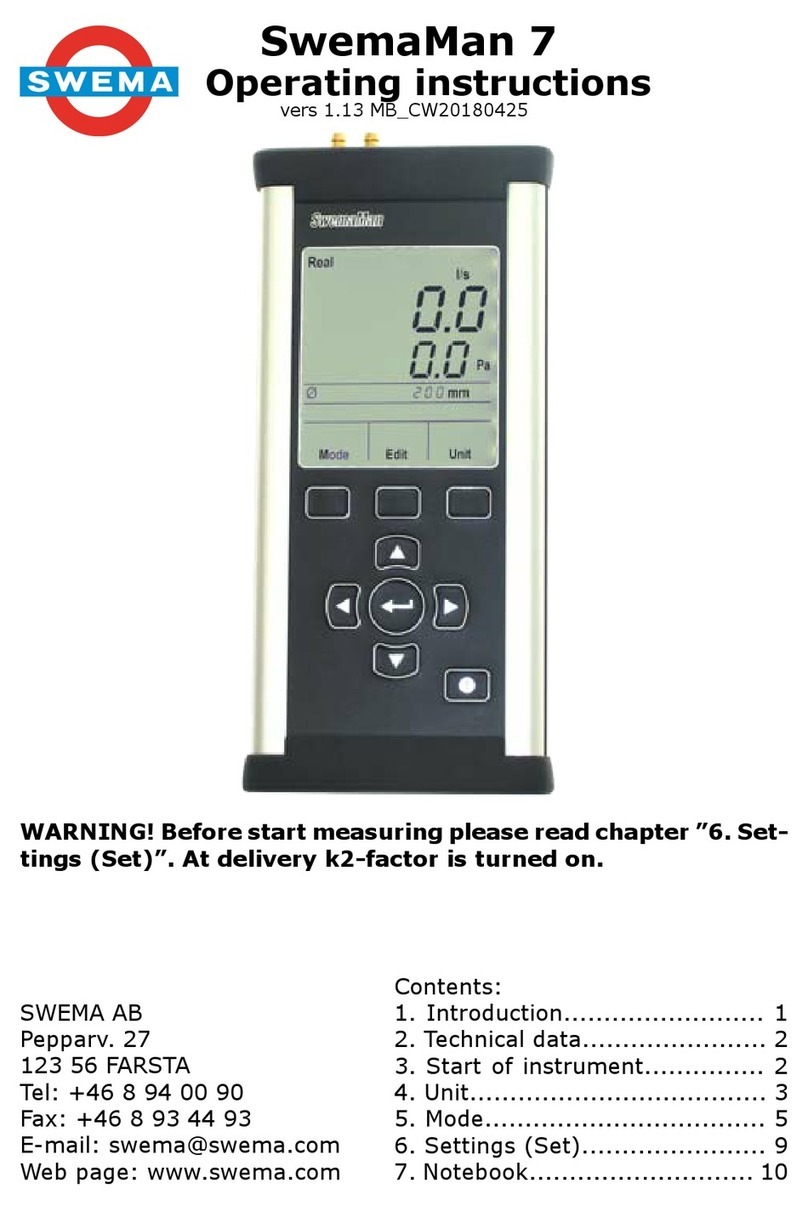
Swema
Swema SwemaMan 7 operating instructions
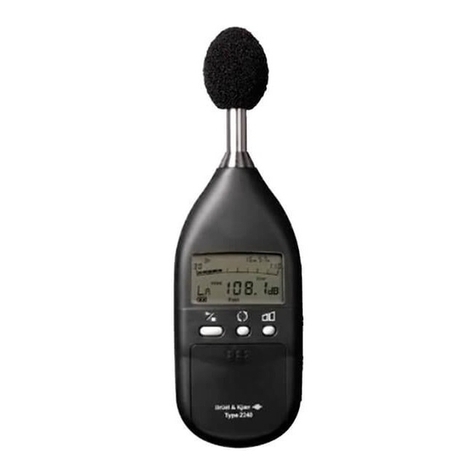
BRUEL & KJAER
BRUEL & KJAER 2240 user guide
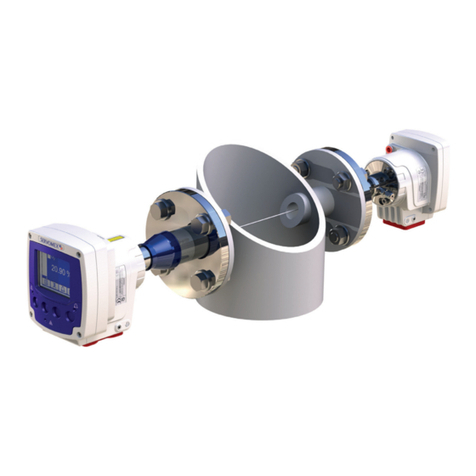
Servomex
Servomex SERVOTOUGH LaserSPII mini Operator's manual
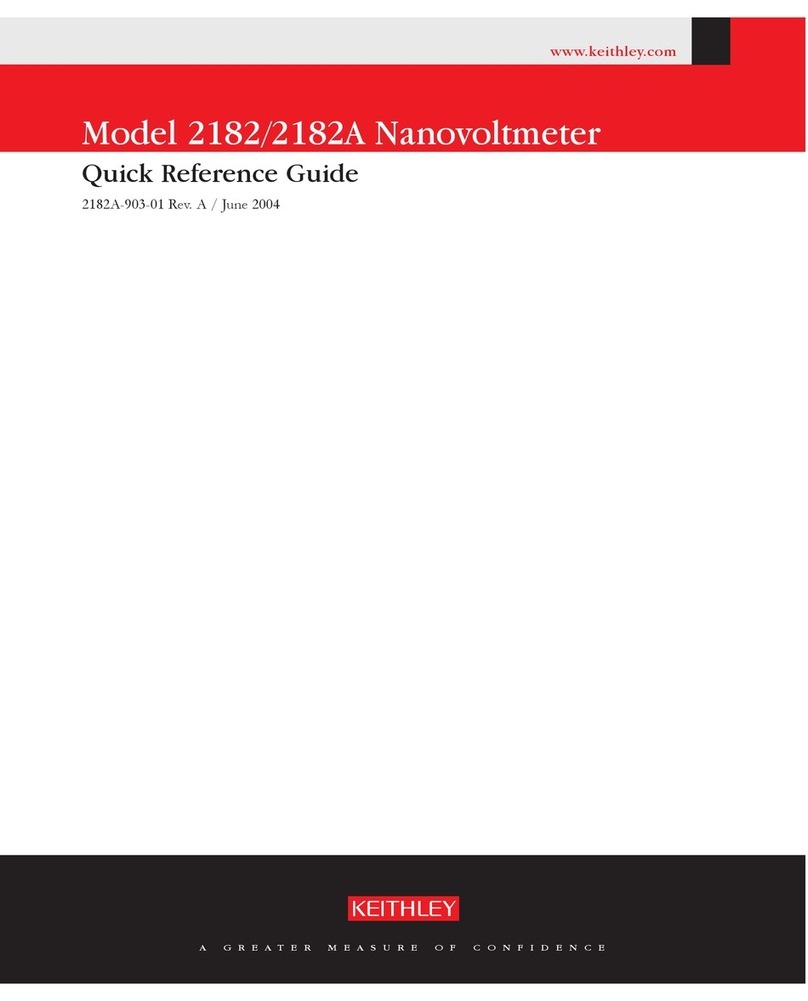
Keithley
Keithley 2182 Quick reference guide

novomatics
novomatics Turbitronic P Operation manual
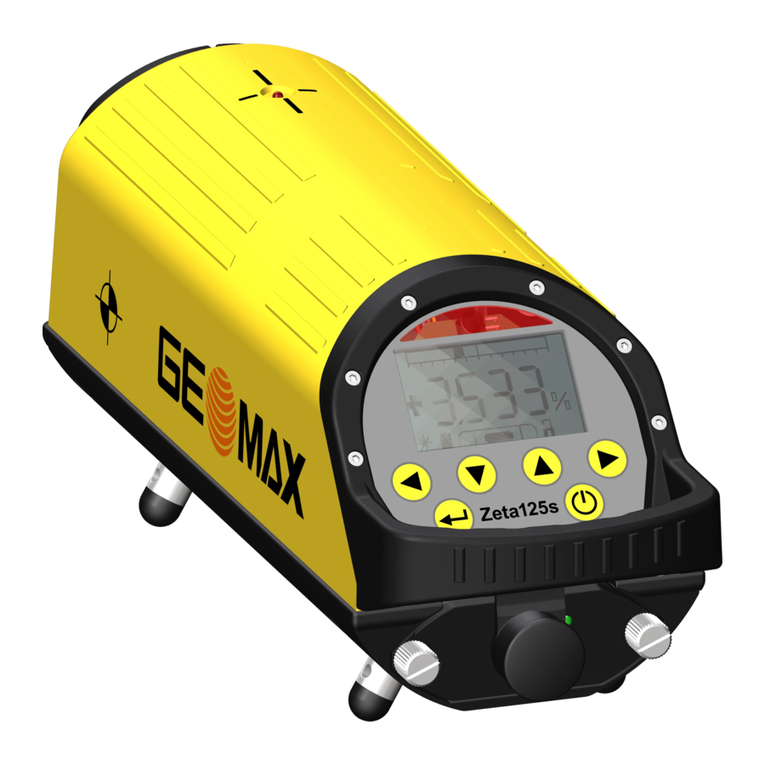
GeoMax
GeoMax Zeta125 user manual
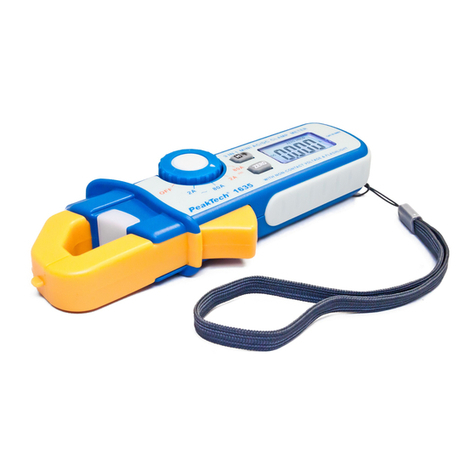
PeakTech
PeakTech 1635 Operation manual
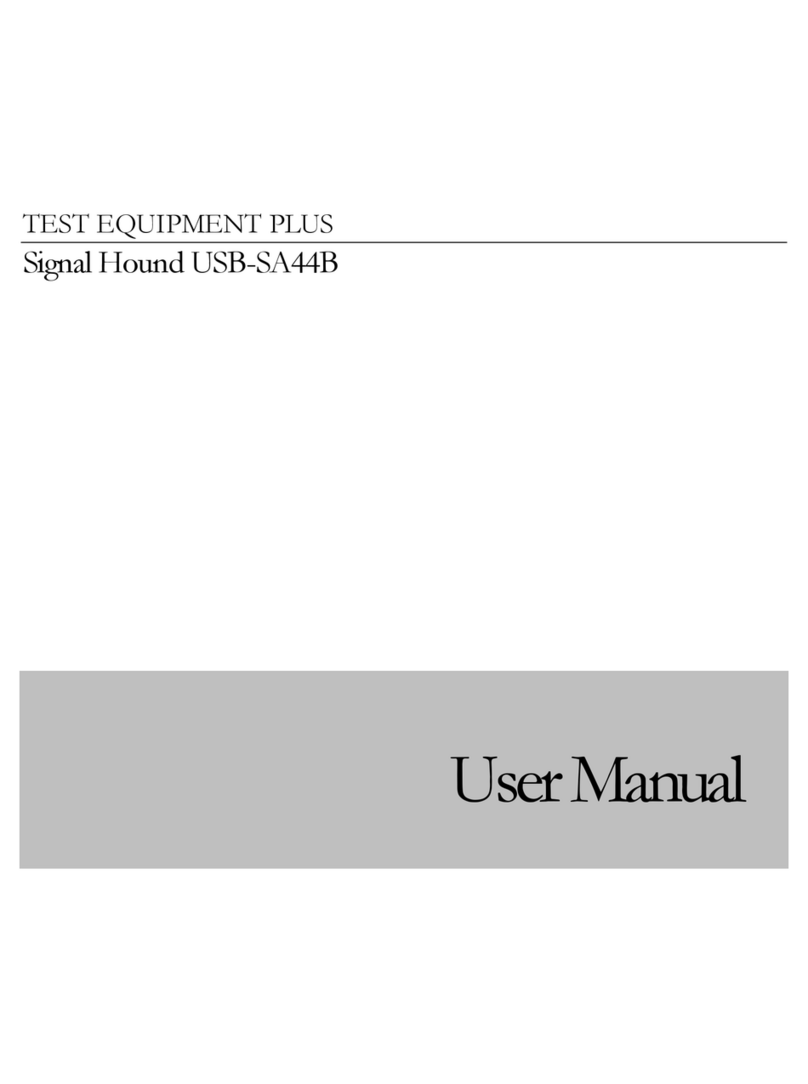
Test Equipment Plus
Test Equipment Plus Signal Hound USB-SA44B user manual
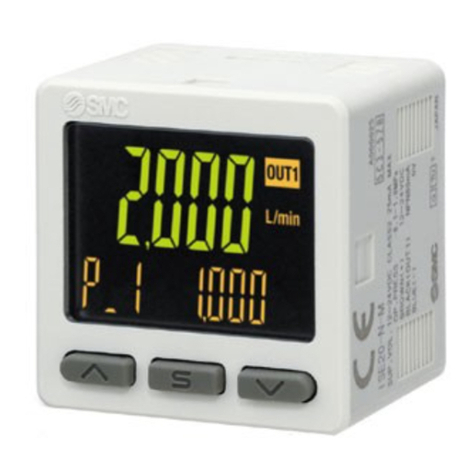
SMC Networks
SMC Networks PFG3 0 Series Operation manual
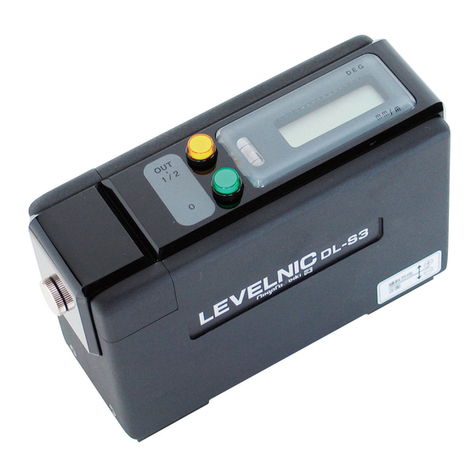
Niigata seiki
Niigata seiki LEVELNIC DL-S3 DL-BW Operation manual

Greenlee
Greenlee 500XP instruction manual