Conair Thermolator TW-1 User manual

Thermolator®
TW Series
Water Temperature Control Units
TW, TW-1 and TW-2
Corporate Office: 724.584.5500 | Instant Access 24/7 (Parts and Service): 800.458.1960 Parts and Service: 814.437.6861
USER GUIDE
UGH025-0504
www.conairgroup.com

Please record your equipment’s
model and serial number(s) and
the date you received it in the
spaces provided.
It’s a good idea to record the model and serial number(s) of your equipment and
the date you received it in the User Guide. Our service department uses this infor-
mation, along with the manual number, to provide help for the specific equipment
you installed.
Please keep this User Guide and all manuals, engineering prints and parts lists
together for documentation of your equipment.
Date:
Manual Number: UGH025-0504
Serial Number(s):
Model Number(s):
DISCLAIMER: Conair shall not be liable for errors contained in this User Guide or for incidental,
consequential damages in connection with the furnishing, performance or use of this information.
Conair makes no warranty of any kind with regard to this information, including, but not limited
to the implied warranties of merchantability and fitness for a particular purpose.
Copyright 2004 l Conair l All rights reserved

UGH025-0504 Thermolator TW Series
TABLE OF
CONTENTS
INTRODUCTION . . . . . . . . . . . . . . . . . . . .1-1
Purpose of the User Guide . . . . . . . . . . . . . . . . . . . . . . . . . .1-2
How the Guide is Organized . . . . . . . . . . . . . . . . . . . . . . . .1-2
Your Responsibility as a User . . . . . . . . . . . . . . . . . . . . . . . .1-2
ATTENTION: Read this so no one gets hurt . . . . . . . . . . . .1-3
DESCRIPTION . . . . . . . . . . . . . . . . . . . . .2-1
What is the Thermolator? . . . . . . . . . . . . . . . . . . . . . . . . . . .2-2
Typical Applications . . . . . . . . . . . . . . . . . . . . . . . . . . . . . . .2-2
How it Works: Direct Injection . . . . . . . . . . . . . . . . . . . . . . .2-3
How it Works: Closed Circuit . . . . . . . . . . . . . . . . . . . . . . .2-4
How it Works: Isolated Circuit . . . . . . . . . . . . . . . . . . . . . . .2-5
Specifications . . . . . . . . . . . . . . . . . . . . . . . . . . . . . . . . . . . .2-6
Features and Options . . . . . . . . . . . . . . . . . . . . . . . . . . . . . .2-8
INSTALLATION . . . . . . . . . . . . . . . . . . . . .3-1
Unpacking the Boxes . . . . . . . . . . . . . . . . . . . . . . . . . . . . . .3-2
Preparing for Installation . . . . . . . . . . . . . . . . . . . . . . . . . . .3-3
Connecting Process and Water Supply Lines . . . . . . . . . . . .3-4
Purge Valve Hookups . . . . . . . . . . . . . . . . . . . . . . . . . . . . . .3-5
Connecting the Main Power Supply . . . . . . . . . . . . . . . . . . .3-6
Testing the Installation TW Control . . . . . . . . . . . . . . . . . . .3-7
Testing the Installation TW-1, TW-2 Control . . . . . . . . . . . .3-8
TW Control Initial Setup . . . . . . . . . . . . . . . . . . . . . . . . . . .3-9
TW Control Changing Temperature Units . . . . . . . . . . . . .3-10
TW-1, TW-2 Control Initial Setup . . . . . . . . . . . . . . . . . . .3-11
TW-1, TW-2 Control Changing Temperature Units . . . . . .3-12
TW-1, TW-2 Control Passcode Protection . . . . . . . . . . . . .3-13
TW-2 Control Selecting the Temperature Control Point . .3-15
TW-1, TW-2 Control Entering Temperature
Deviation Alarm Parameters . . . . . . . . . . . . . . . . . . . . . .3-17
TW-2 Control Installing the Auto Start Feature . . . . . . . . .3-18
Positioning the TW-2 Control Panel . . . . . . . . . . . . . . . . . .3-20
OPERATION . . . . . . . . . . . . . . . . . . . . . . .4-1
TW Control Features . . . . . . . . . . . . . . . . . . . . . . . . . . . . . .4-2
TW Control Menu . . . . . . . . . . . . . . . . . . . . . . . . . . . . . . . . .4-3
TW-1 Control Features . . . . . . . . . . . . . . . . . . . . . . . . . . . . .4-4
TW-2 Control Features . . . . . . . . . . . . . . . . . . . . . . . . . . . . .4-5
Starting the TW . . . . . . . . . . . . . . . . . . . . . . . . . . . . . . . . . .4-6
Stopping the TW . . . . . . . . . . . . . . . . . . . . . . . . . . . . . . . . . .4-7
Starting the TW-1, TW-2 . . . . . . . . . . . . . . . . . . . . . . . . . . .4-8
Stopping the TW-2, TW-2 . . . . . . . . . . . . . . . . . . . . . . . . . .4-9
Using the TW Purge Option . . . . . . . . . . . . . . . . . . . . . . . .4-10
Using the TW-1 Purge Option . . . . . . . . . . . . . . . . . . . . . .4-11
Using the TW-2 Purge Option . . . . . . . . . . . . . . . . . . . . . .4-12
i

Thermolator TW Series UGH025-0504
TABLE OF
CONTENTS
OPERATION . . . . . . . . . . . . . . . . . . . . . .CONT’D
TW Control Performing an Auto Tune . . . . . . . . . . . . . . . .4-13
TW-1, TW-2 Control Performing an Auto Tune . . . . . . . .4-14
TW-1, TW-2 Control Entering Passcodes . . . . . . . . . . . . .4-16
MAINTENANCE . . . . . . . . . . . . . . . . . . . . .5-1
Preventative Maintenance Schedule . . . . . . . . . . . . . . . . . . .5-2
Accessing the Thermolator Enclosure . . . . . . . . . . . . . . . . .5-3
Checking Reservoir Fluid Levels (IC) . . . . . . . . . . . . . . . . .5-4
TW-1, TW-2 Control Performing System Tests . . . . . . . . . .5-5
TW-1, TW-2 Control Key/Display Test . . . . . . . . . . . . . . . .5-6
TW-1, TW-2 Control Input Test . . . . . . . . . . . . . . . . . . . . . .5-7
TW-1, TW-2 Control Output Test . . . . . . . . . . . . . . . . . . . . .5-8
TW-1, TW-2 Control Output Monitors . . . . . . . . . . . . . . . . .5-9
TW-1, TW-2 Control Calibrating Temperature Sensors . . .5-10
TW-1, TW-2 Control Logging Operating Hours . . . . . . . .5-12
TW-1, TW-2 Control Pulse Mode Description . . . . . . . . . .5-13
TW-1, TW-2 Control Pulse Mode Setup . . . . . . . . . . . . . .5-13
TW-1, TW-2 Control Pulse Mode Limits & Defaults . . . .5-14
TW Control Deviation Alarm/Band and Delay . . . . . . . . .5-14
TW-1, TW-2 Control Vent Timer Adjustment . . . . . . . . . .5-15
TROUBLESHOOTING . . . . . . . . . . . . . . . . .6-1
Before Beginning . . . . . . . . . . . . . . . . . . . . . . . . . . . . . . . . .6-2
A Few Words of Caution . . . . . . . . . . . . . . . . . . . . . . . . . . .6-2
Identifying the Cause of a Problem . . . . . . . . . . . . . . . . . . .6-3
TW Control Alarms . . . . . . . . . . . . . . . . . . . . . . . . . . . . . . .6-5
TW Control Mechanical/Electrical Alarms . . . . . . . . . . . .6-11
TW-1, TW-2 Control Shut Down Alarms . . . . . . . . . . . . . .6-12
TW-1, TW-2 Control Warning Alarms . . . . . . . . . . . . . . . .6-13
TW-1, TW-2 Control Other Warnings . . . . . . . . . . . . . . . .6-15
TW-1, TW-2 Control System Alarms . . . . . . . . . . . . . . . . .6-16
Thermolator Will Not Power Up . . . . . . . . . . . . . . . . . . . .6-17
Replacing the TW Control . . . . . . . . . . . . . . . . . . . . . . . . .6-18
Checking and Replacing Fuses . . . . . . . . . . . . . . . . . . . . . .6-19
Resetting Overloads . . . . . . . . . . . . . . . . . . . . . . . . . . . . . .6-20
Replacing Pump Overload . . . . . . . . . . . . . . . . . . . . . . . . .6-20
Replacing the Motherboard TW-1, TW-2 . . . . . . . . . . . . . .6-21
Replacing the Heater Contactor . . . . . . . . . . . . . . . . . . . . .6-22
Checking Thermocouples . . . . . . . . . . . . . . . . . . . . . . . . . .6-23
Replacing Thermocouples . . . . . . . . . . . . . . . . . . . . . . . . .6-23
PT1000 Sensor Test Readings TW . . . . . . . . . . . . . . . . . . .6-24
Repairing Cooling Valves . . . . . . . . . . . . . . . . . . . . . . . . . .6-25
Repairing Solenoid Valves . . . . . . . . . . . . . . . . . . . . . . . . .6-26
Repairing Motorized Valves . . . . . . . . . . . . . . . . . . . . . . . .6-27
Replacing Heater Elements . . . . . . . . . . . . . . . . . . . . . . . . .6-28
Removing the Pump . . . . . . . . . . . . . . . . . . . . . . . . . . . . . .6-30
Disassembling and Assembling 3/4 to 2 HP Pumps . . . . .6-31
Disassembling and Assembling 3 to 7.5 HP Pumps . . . . . .6-32
APPENDIX
Customer Service Information . . . . . . . . . . . . . . . . . . . . . . .A-1
Warranty/Guarantee Information . . . . . . . . . . . . . . . . . . . . .A-2
Pump Curves . . . . . . . . . . . . . . . . . . . . . . . . . . . . . . . . . . . .B-1
TW Control Default Parameters . . . . . . . . . . . . . . . . . . . . .C-1
TW-1, TW-2 SPI Commands and Status Words . . . . . . . . .D-1
PARTS/DIAGRAMS
TW-1 Circuit Board . . . . . . . . . . . . . . . . . . . . . . . . . . . . . .PD-3
TW-2 Circuit Board . . . . . . . . . . . . . . . . . . . . . . . . . . . . . .PD-4
ii

1-1
UGH025-0504 Thermolator TW Series
l
Purpose of the User Guide . . . .1-2
l
How the Guide is Organized . . .1-2
l
Your Responsibilities as a User 1-2
l
ATTENTION: Read this so
no one gets hurt . . . . . . . . . . . .1-3
INTRODUCTION

Thermolator TW Series UGH025-0504
1-2 INTRODUCTION
This User Guide describes the Conair Thermolator®TW
Series water temperature controllers and explains step-by-step
how to install, operate, maintain and repair this equipment.
Before installing this product, please take a few moments to
read the User Guide and review the diagrams and safety infor-
mation in the instruction packet. You also should review man-
uals covering associated equipment in your system. This
review won’t take long, and it could save you valuable instal-
lation and operating time later.
Symbols have been used to help organize the User Guide and
call your attention to important information regarding safe
installation and operation.
Symbols within triangles warn of conditions that could
be hazardous to users or could damage equipment.
Read and take precautions before proceeding.
Numbers within shaded squares indicate tasks or steps
to be performed by the user.
A diamond indicates the equipment’s response to an
action performed by the user.
An open box marks items in a checklist.
A shaded circle marks items in a list.
You must be familiar with all safety procedures concerning
installation, operation and maintenance of this equipment.
Responsible safety procedures include:
lThorough review of this User Guide, paying particular
attention to hazard warnings, appendices and related dia-
grams.
lThorough review of the equipment itself, with careful
attention to voltage requirements, intended uses and
warning labels.
lThorough review of instruction manuals for associated
equipment.
lStep-by-step adherence to instructions outlined in this
User Guide.
PURPOSE OF
THE USER
GUIDE
HOW THE
GUIDE IS
ORGANIZED
1
u
r
l
YOUR
RESPONSIBILITY
ASAUSER

UGH025-0504 Thermolator TW Series INTRODUCTION 1-3
We design equipment with the user’s safety in mind. You can
avoid the potential hazards identified on this machine by
following the procedures outlined below and elsewhere in the
User Guide.
ATTENTION:
READ THIS SO NO
ONE GETS HURT
WARNING: Improper installation,
operation or servicing may result in
equipment damage or personal injury.
This equipment should be installed, adjusted,
and serviced by qualified technical personnel
who are familiar with the construction, operation
and potential hazards of this type of equipment.
All wiring, disconnects and fuses should be
installed by qualified electrical technicians in
accordance with electrical codes in your region.
Always maintain a safe ground. A properly sized
conductive ground wire from the incoming
power supply must be connected to the chassis
ground terminal inside the electrical enclosure.
Improper grounding can result in personal injury
and erratic machine operation.
Do not operate the equipment at power levels
other than what is specified on the the equip-
ment serial tag and data plate.
WARNING: Electrical shock hazard
This equipment is powered by three-phase
main voltage, as specified on the machine seri-
al tag and data plate.
Always disconnect and lock out the incoming
main power source before opening the electrical
enclosure or performing non-standard operating
procedures, such as troubleshooting or mainte-
nance. Only qualified personnel should perform
procedures that require access to the electrical
enclosure while power is on.
CAUTION: Hot surfaces
Surface temperatures inside the Thermolator
can exceed 250°F (121°C). Always allow the
unit to cool to below 100°F (38°C) before open-
ing, servicing or disassembling the unit.

WARNING: Hazardous substance
The contactors used in the Thermolator are
mercury displacement relays. Mercury is con-
sidered a hazardous substance and must be
dealt with accordingly. See the Material Safety
Data Sheet which explains the potential haz-
ards, how to avoid them and how to clean up
and dispose of the mercury if it spills.
ATTENTION:
READ THIS SO NO
ONE GETS HURT
Thermolator TW Series UGH025-0504
1-4 INTRODUCTION

2-1
UGH025-0504 Thermolator TW Series
l
What is the Thermolator
TW Series? . . . . . . . . . . . . . . . .2-2
l
Typical Applications . . . . . . . . . .2-2
l
How it Works:
Direct Injection (DI) Models . . .2-3
l
How it Works:
Closed Circuit (CC) Models . . . .2-4
l
How it Works:
Isolated Circuit (IC) Models . . . .2-5
l
Specifications . . . . . . . . . . . . . . .2-6
l
Features and Options . . . . . . . . .2-8
DESCRIPTION

The Thermolator TW models circulate water at a temperature
higher than the available water supply, to add or remove heat
as needed to maintain a uniform temperature setpoint in the
process.
Conair TW Thermolators are available in single or dual-zone
configurations, using resistance heating and direct injection or
closed circuit cooling. Dual-zone models can control at two
different temperatures at different locations in the process.
Two-zone models have common cooling water manifolds and
electrical connections.
WHAT IS THE
THERMOLATOR?
Thermolator TW Series UGH025-0504
2-2 DESCRIPTION
TYPICAL
APPLICATIONS
IMPORTANT: Do not use
deionized water or glycol
mixtures containing additives
in a Thermolator. Softened
water or glycol mixtures with
additives, such as automo-
tive fluids, can damage the
Thermolator. Glycol/water
process loop mixtures should
use industrial-grade ethylene
glycol only.
The best model for your application depends on the process
temperature you need to maintain and the quality of the cool-
ing water supply.
Direct injection (DI) models control the temperature by
discharging heated process water and adding cooling water
directly from the water supply. DI models are designed for:
l Process temperatures up to 250°F (121°C).
l Use with chiller water or properly treated and filtered
tower or city water.
Closed circuit (CC) models add cooling water to the process
loop only during the initial filling or when make-up water is
needed. CC models are recommended for:
l Process temperatures up to 250°F (121°C).
l Use with contaminated cooling water.
Isolated circuit (IC) models separate the cooling water from
the process fluid, which is held in a reservoir. IC models are
recommended for:
l Process temperatures up to 180°F (82°C).
l Use with contaminated cooling water.
l When process and cooling fluids are different.

Direct injection models maintain the process temperature
by electrically heating and injecting cool water supplied to
the Thermolator by a chiller, tower or other water source.
HOW IT WORKS:
DIRECT INJECTION
UGH025-0504 Thermolator TW Series DESCRIPTION 2-3
A
B
The temperature of the process fluid is measured
as it leaves the unit’s heater tank. The fluid then
flows through the “To Process” line to the mold
or process. The fluid returns to the unit through the
“From Process” line for reheating or cooling.
1
A
B
C
If the process
temperature is
below the set-
point, the heater
elements inside
the heater tank
are energized.
E
F
4The pump moves water from the mixing
tank to the heater tank. Pressure is
measured before and after the pump .
NOTE: Some higher kW models have an
additional heater in the mixing tank
EF
The temperature of the process
fluid is measured as it flows into
the mixing tank through the
“From Process” line .
2
B
If the average temperature is
above the setpoint value, the cool-
ing valve opens. Cool water
enters the bottom of the mixing
tank via the “Cooling In” line .
Warm water flows out through the
“Cooling Out” line .
C
D
3b
3a
D

HOW ITWORKS:
CLOSED CIRCUIT
Thermolator TW Series UGH025-0504
2-4 DESCRIPTION
A
B
The temperature of the process
fluid is measured as it leaves
the unit’s heater tank. The fluid
then flows through the “To
Process” line to the mold or
process. The fluid returns to the
unit through the “From
Process” line for reheating
or cooling.
1
A
B
CD
3b If the process temperature
is below the setpoint, the
heater elements inside the
heater tank are energized.
E
F
4The pump moves water from the
mixing tank to the heater tank.
Pressure is measured before
and after the pump .
EF
The temperature of
the process fluid is
measured as it flows
into the cooling tank
through the “From
Process” line .
2
B
3a If the temperature is above
the setpoint value, the cooling
valve opens. Cool water
enters the cooling piping
and circulates through a tube
heat exchanger to cool the
process fluid. The cooling
valve allows warm fluid to
escape through the “Cooling
Out” line .
C
D
Closed Circuit models maintain the process temperature by
electrically heating and indirectly cooling fluid in the
process circuit. Cooling water supplied by a chiller, tower
or other water source, is mixed with the process fluid only
during the initial filling or when water is needed to make
up process fluid loss.

HOW ITWORKS:
ISOLATED CIRCUIT
UGH025-0504 Thermolator TW Series DESCRIPTION 2-5
Isolated Circuit models maintain the process temperature
by electrically heating and indirectly cooling fluid in the
process circuit. The process fluid, which is stored in a
reservoir, is isolated from cooling water supplied by a
chiller, tower or other source.
A
B
The temperature of the
process fluid is measured
as it leaves the unit’s
heater tank. The fluid then
flows through the “To
Process” line to the mold
or process. The fluid
returns to the unit through
the “From Process” line
for reheating or cooling.
1
A
B
CD
If the process temperature
is below the setpoint, the
heater elements inside the
heater tank are energized.
E
4The pump moves water
from the mixing tank to
the heater tank.
Pressure is measured
after the pump .
E
The temperature of
the process fluid is
measured as it flows
into the cooling tank
through the “From
Process” line .
2
B
If the temperature is
above the setpoint
value, the cooling valve
opens. Cool water
enters the cooling piping
and circulates through a
tube heat exchanger to
cool the process fluid.
C
G
The vent line allows warm
process fluid to expand to the
reservoir . The reservoir
supplies process fluid through
a make-up line as needed.
G
3b
3a

SPECIFICATIONS
Thermolator TW Series UGH025-0504
2-6 DESCRIPTION
CABINET STYLE REFERENCE
Heater Voltage Selection Single Zone Dual Zone
Direct Injection (DI)
9, 12, 18 or 24 kW 208, 230, 460, 575 A B
36 kW 230 C D
36 kW 460 or 575 A B
48 kW 230, 460, 575 C D
Closed Circuit (CC)
9 or 12 kW 208, 230, 460, 575 A B
18 or 24 kW 208, 230, 460, 575 C D
Isolated Circuit (IC)
9, 12, 18 or 24 kW 208, 230, 460, 575 C D
AB
CD
Dimensions and performance characteristics vary according to
the model, voltage and components selected. See the cabinet
style reference chart to determine dimensional information for
your specific model. Additional technical information can be
found in the Appendix of this User Guide.
Height
Width
Single Zone
Width
2- Zone
Depth
Width
Single Zone
Width
2- Zone
Height
Depth
NOTE: Dual zone models
have common wiring and
cooling water plumbing.
WATER CONNECTIONS
All models
NPT inches (female)
To/From process 1.25
Cooling water in/out 0.75

SPECIFICATIONS
UGH025-0504 Thermolator TW Series DESCRIPTION 2-7
Direct Injection (DI)
Closed Circuit (CC)
Isolated Circuit (IC)
PERFORMANCE CHARACTERISTICS -
*Lower operating temperatures can be obtained with larger cooling valves. Consult your Conair representative.
Models TW-DI TW-CC TW-IC
Minimum Setpoint Temperature °F {°C} 32 {0} 32 {0} 32 {0}
Maximum Setpoint Temperature °F {°C} 250 {121} 250 {121} 180 {82}
Minimum Operating Temperature °F {°C} Approximately 20° {11°} above the cooling water inlet temperature*
Standard Cooling Valve Size inches {mm} 1/4 {6.35} 3/4 {19.05} 3/4 {19.05}
Available pump sizes 0.75, 1, 2, 3, 5 or 7.5 Hp {0.56, 0.75, 1.49, 2.24, 3.73 or 5.59 kW}
Available heater sizes 9, 12, 18, 24, 36 or 48 kW 9, 12, 18 or 24 kW
PUMP PERFORMANCE -Consult your Conair representative for pump performance characteristics at other operating points.
Pump 3/4 HP {0.56 kW} 1 HP {0.75 kW} 2 HP {1.49 kW} 3 HP {2.24 kW} 5 HP {3.73 kW} 7.5 HP {5.59 kW}
Nominal Flow gpm {lpm} 40 {151} 45 {170} 55 {208} 80 {303} 100 {379} 115 {435}
Pressure@ Nominal Flow psi {kg/cm2} 17 {1.2} 18 {1.3} 31 {2.2} 35 {2.5} 43 {3} 51 {3.6}
TOTAL FULL LOAD AMPS PER ZONE All voltages are 3 phase, 60 Hz.
Heater 9 kW 12 kW 18 kW 24 kW 36 kW 48 kW
Voltage 208V 230V 460V 575V 208V 230V 460V 575V 208V 230V 460V 575V 208V 230V 460V 575V
Pump
0.75 HP {0.56 kW} 28.9 26.2 13.1 10.5 37.3 33.8 16.9 13.5 54.0 48.8 24.4 19.5 70.7 64.0 32 25.6
1 HP {0.75 kW} 29.4 26.6 13.3 10.6 37.8 34.2 17.1 13.7 54.4 49.2 24.6 19.7 71.2 64.4 32.2 25.8
2 HP {1.49 kW} 31.8 28.8 14.4 11.5 40.2 36.4 18.2 14.6 56.8 51.4 25.7 20.6 73.6 66.6 33.3 26.6
3 HP {2.24 kW} 34.7 31.4 15.7 12.6 43.1 39.0 19.5 15.6 59.7 54.0 27.0 21.6 76.5 69.2 34.6 27.7
5 HP {3.73 kW} 38.5 34.8 17.4 13.9 46.9 42.4 21.2 17.0 63.4 57.4 28.7 23 80.2 72.6 36.3 29.0
7.5 HP {5.59 kW} 45.7 41.4 20.7 16.6 54.1 49.0 24.5 19.6 70.7 64.0 32.0 25.6 87.5 79.2 39.6 31.7
SHIPPING WEIGHT RANGES lbs {kg} Weights vary depending on cabinet size and cooling type (DI, CC or IC).
Single Zone Dual Zone
Pump Min Max Min Max
0.75 HP {0.56 kW} 240 {109} 300 {136} 480 {218} 600 {272}
1 HP {0.75 kW} 240 {109} 300 {136} 480 {218} 600 {272}
2 HP {1.49 kW} 250 {113} 310 {141} 500 {226} 620 {282}
3 HP {2.24 kW} 260 {118} 320 {145} 520 {236} 640 {290}
5 HP {3.73 kW} 270 {122} 330 {150} 540 {244} 660 {300}
7.5 HP {5.59 kW} 280 {127} 340 {154} 560 {254} 680 {308}
DIMENSIONS in. {mm}
Cabinet Style A B C D
Height 28.0 {710} 28.0 {710} 43.0 {1090} 43.0 {1090}
Depth 22.5 {570} 22.5 {570} 31.5 {800} 31.5 {800}
Width 13.75 {350} 27.5 {700} 14.0 {355} 28.0 {710}
208V 230V 460V 575V 208V 230V 460V 575V
104.0 94.0 47.0 37.6 137.0 124.0 62.1 49.7
104.3 94.4 47.2 37.8 137.7 124.6 62.3 49.6
106.7 96.6 48.3 38.6 140 126.8 63.4 50.7
109.6 99.2 49.6 39.7 143 129.4 64.7 51.8
113.4 102.6 51.3 41.0 146.7 132.8 66.4 53.1
120.7 109.2 54.6 43.7 154 139.4 69.7 55.8
MODEL DESIGNATIONS
TOTAL FULL LOAD AMPS PER ZONE All voltages are 3 phase, 60 Hz.
Heater 0 heaters
Voltage 208V 230V 460V 575V
Pump
0.75 HP {0.56 kW} 3.9 3.6 2.3 1.5
1 HP {0.75 kW} 4.4 4.0 2.5 1.6
2 HP {1.49 kW} 6.8 6.2 3.6 2.5
3 HP {2.24 kW} 9.7 8.8 4.9 3.6
5 HP {3.73 kW} 13.5 12.2 6.6 4.9
7.5 HP {5.59 kW} 20.7 18.8 9.9 7.6
NOTE: Thermolators
can be ordered
without heaters for
certain applications.
TW

High efficiency pumps
from 3/4 to 7.5 Hp. Silicon
carbide seals are standard.
Pump seal flush line
continuously cleans the
pump seal for extended life.
Incoloy heaters
minimize chemical and
high temperature damage
Built-in sediment trap
settles contaminants away
from the pump seals.
Motor drip cover
protects motor windings
from moisture damage.
Two-piece cast
construction
Alarm packages
Add an audible or visual alarm to call
attention to alarm conditions.
Motorized Cooling Valve
Slow open/close cycle time eliminates ther-
mal shock and water hammer from your
process circuit.
Compressed Air Mold Purge
Quickly evacuates fluid from the process
circuit, allowing for faster, cleaner discon-
nection of the temperature controller from
molds and hoses.
Stacking Rack
Save floor space by stacking Thermolators
two-high. The stacking rack can be used
only with single-zone models in 28-inch
high cabinets.
OPTIONS
Thermolator TW Series UGH025-0504
2-8 DESCRIPTION
FEATURES AND
OPTIONS

3-1
UGH025-0504 Thermolator TW Series
l
Unpacking the Boxes . . . . . . . . . . . . .3-2
l
Preparing for Installation . . . . . . . . . .3-3
l
Connecting Process and
Water Supply Lines . . . . . . . . . . . . .3-4
l
purge Valve Hookups . . . . . . . . . . . . .3-5
l
Connecting the Main Power . . . . . . . .3-6
l
Testing the Installation TW Control .3-7
l
Testing the Installation
TW-1, TW-2 Controls . . . . . . . . . . . .3-8
l
TW Control Initial Setup . . . . . . . . . . .3-9
l
TW Control Changing
Temperature Units . . . . . . . . . . . . .3-10
l
TW-1, TW-2 Control Initial Setup . . .3-11
l
TW-1, TW-2 Control Changing
Temperature Units . . . . . . . . . . . . .3-12
l
TW-1, TW-2 Control Enabling and
Disabling Passcode Protection . . . .3-13
l
TW-2 Selecting the Temperature
Control Point . . . . . . . . . . . . . . . . .3-15
l
TW-1, TW-2 Control Entering
Temperature Deviation Alarm
Parameters . . . . . . . . . . . . . . . . . . . . .3-17
l
TW-2 Control Installing the
Auto Start Feature . . . . . . . . . . . . .3-18
l
Positioning the TW-2
Control Panel . . . . . . . . . . . . . . . . .3-20
INSTALLATION

UNPACKING THE
BOXES
Thermolator TW Series UGH025-0504
3-2 INSTALLATION
Carefully remove the Thermolator and
components from their shipping containers.
Remove all packing material, protective
paper, tape and plastic. Check inside the electrical enclo-
sure and behind the side panels for accessories or hard-
ware that may have been placed there for shipping.
Carefully inspect all components to make sure
no damage occurred during shipping, and that you have
all the necessary hardware. If damage is found, notify the
freight company immediately.
Take a moment to record serial numbers and
specifications in the blanks provided on the back of the
User Guide’s title page. The information will be helpful if
you ever need service or parts.
You are now ready to begin installation.
Complete the preparation steps on the next page.
Thermolator
1
2
3
4
5
Thermolator TW models come fully assembled. If they were
specified at the time of the order, the purge valve or motor-
ized cooling valve is factory-installed.

UGH025-0504 Thermolator TW Series INSTALLATION 3-3
The Thermolator is easy to install, if you plan the location and
prepare the area properly.
Position the Thermolator as close to the
process machine as possible.
Make sure the installation area provides:
rA three-phase power source supplying the correct
current for your Thermolator model. Check the serial tag
on the side of the electrical enclosure for the required
voltage, phase, frequency, full load amps, disconnect fuse
size and minimum wire connection size. Field wiring
should be completed by qualified personnel to the planned
location for the Thermolator. All electrical wiring should
comply with your region’s electrical codes.
r A clean, well-ventilated environment.
The room temperature should not exceed 120°F (48°C)
with 95% non-condensing humidity and should not fall
below 32°F (0°C).
r Minimum clearance for safe operation and main-
tenance. The diagram at right shows minimum clear-
ance for operation. You also need enough clearance in
the rear for water hookups. For maintenance, you
should move the Thermolator to provide at least 36 inches
on any side of the Thermolator.
r A source of water for cooling.
City, tower or chiller water may be used. The minimum
supply pressure is 25 psi and the maximum pressure is
shown in the following chart.
Install plumbing for process and cooling lines.
You will need two 11/4-inch NPT male fittings for the
process inlet and outlet and two 3/4-inch NPT male fit-
tings for the cooling inlet and outlet. Larger line sizes are
acceptable as long as they are reduced at the Thermolator
connections. Smaller line sizes are not recommended.
PREPARING FOR
INSTALLATION
1
TWMicroprocessorControl
HeatOn
CoolOn
HighTempAlarm
SetpointDeviationAlarm
CommunicationsActive
Process
Value
Set
Value
Err.H=OpenThermocouple
Err.L=ReversedThermocouple
Parameter
Access
IncreaseDecrease
Mode
StopPump
Start
Depressuntilventcycle
endsandpumpstarts
Alarm
Purge
PushOn/Off
ControlPower
PushOn/Off
Fault
PushToSilence
2
Process machine
Thermolator
Alternate
locations
3
12 inches
(305 mm)
12 inches
(305 mm) 20 inches
(508 mm)
Pump HP Max Cooling
3/4 HP 95 PSI
1 85
2 70
3 70
5 60
7 1/2 50

The Thermolator process inlets and outlets must be connected
to the plumbing that will circulate the temperature-controlled
water or fluid through the process. Cooling water inlets and
outlets are connected to the cooling water supply.
Remove the shipping pipe plug from the
female connections on the back of the Thermolator.
Install pipe to the rear of the Thermolator.
Use male 11/4-inch NPT piping for process connections
and male 3/4inch NPT piping for water connections. Pipe
and pipe threads must be clean and new. Clean threads
with solvent, removing all oil, grease and dirt. Allow the
threads to dry before proceeding.
Coat the pipe threads with thread sealant.
Follow the sealant manufacturer’s directions.
Connect the male pipe to the appropriate
female connection on the back of the unit. Start by hand
until the threads engage, then use a pipe wrench to tighten
the connection only enough to prevent leaks. Do not over-
tighten!
CONNECTING
PROCESS AND
WATER SUPPLY
LINES
Thermolator TW Series UGH025-0504
3-4 INSTALLATION
1
2
3
4
Tools for installation:
r Pipe wrench large enough
for a 2-inch pipe
r Premium quality Teflon
thread sealant
NOTE: We recommend
that you install an
external ball valve on
the cooling water inlet
of the Thermolator.
This valve is required
when the purge valve
option is installed. From
process
To
process
From
process
To
process
Cooling water out
Cooling water in
Cooling water in
DIRECT INJECTION CLOSED CIRCUIT
ISOLATED CIRCUIT
(BUT IN TALL CABINET)
Cooling water out
This manual suits for next models
2
Table of contents
Popular Control Unit manuals by other brands
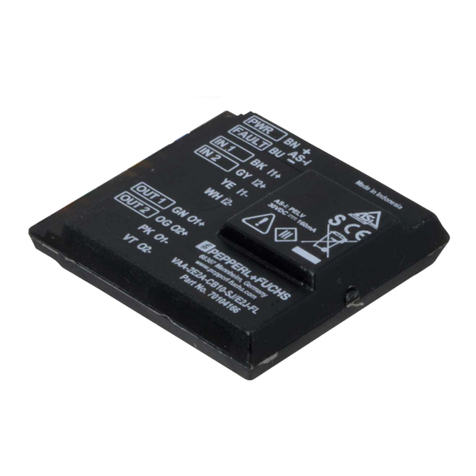
Pepperl+Fuchs
Pepperl+Fuchs VAA-2E1A-CB10-SJ/E2J-FL manual
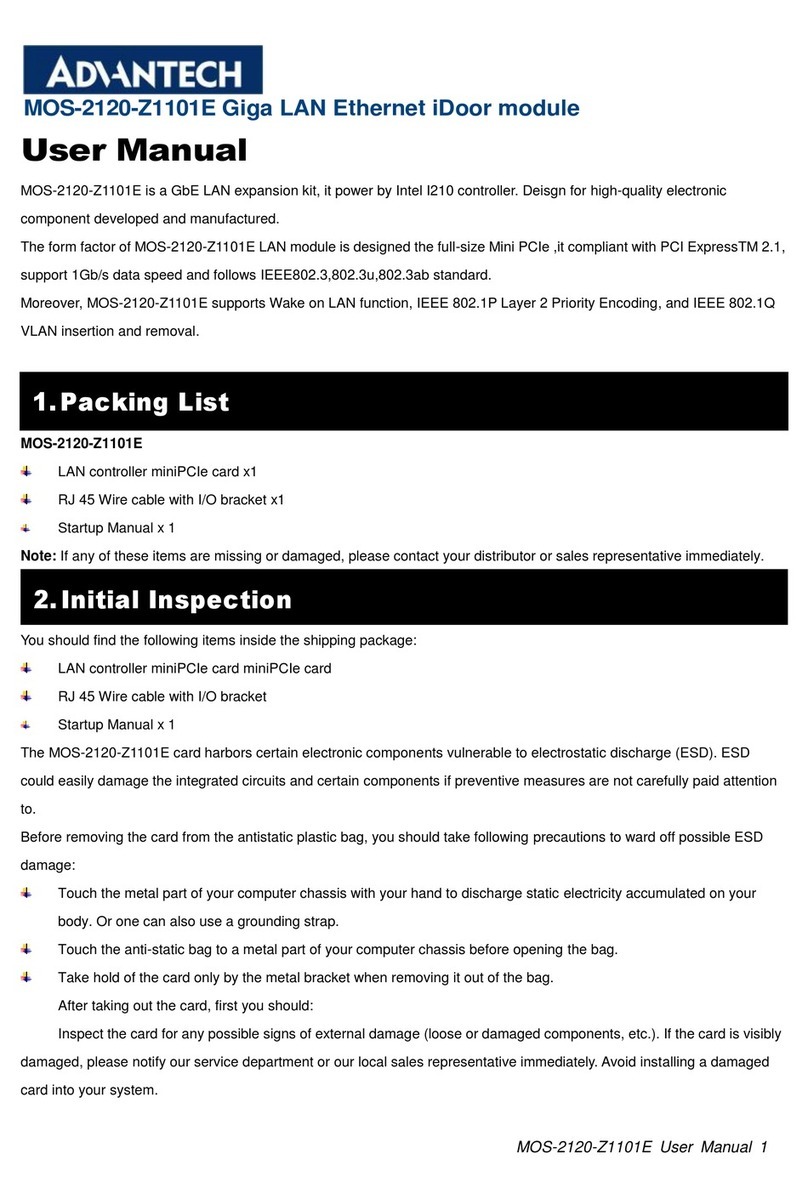
Advantech
Advantech MOS-2120-Z1101E user manual
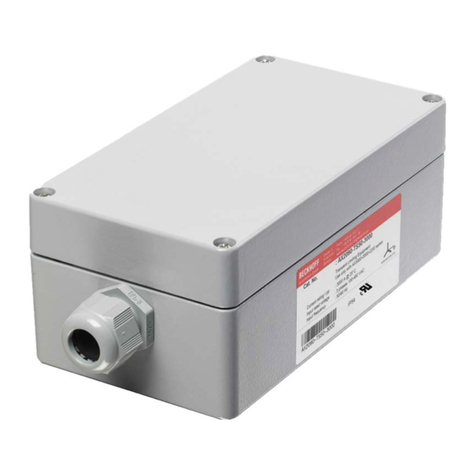
Beckhoff
Beckhoff AX2090-TS50-3000 Documentation
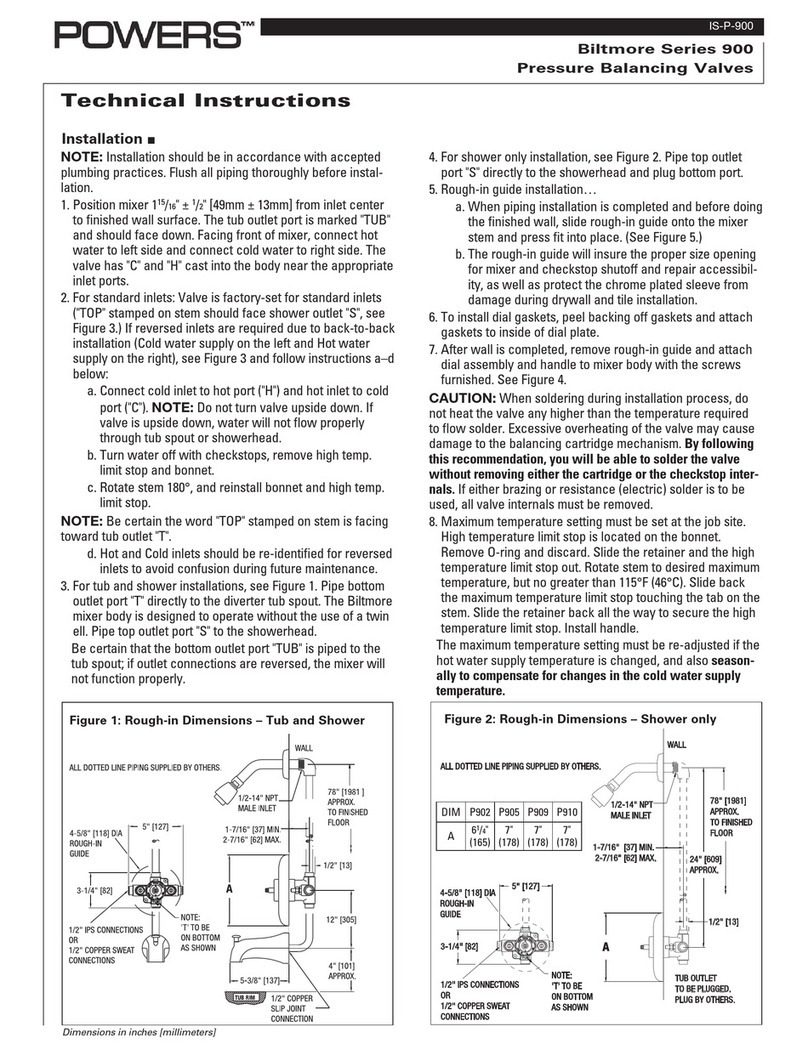
Powers
Powers Biltmore 900 Series Technical instructions
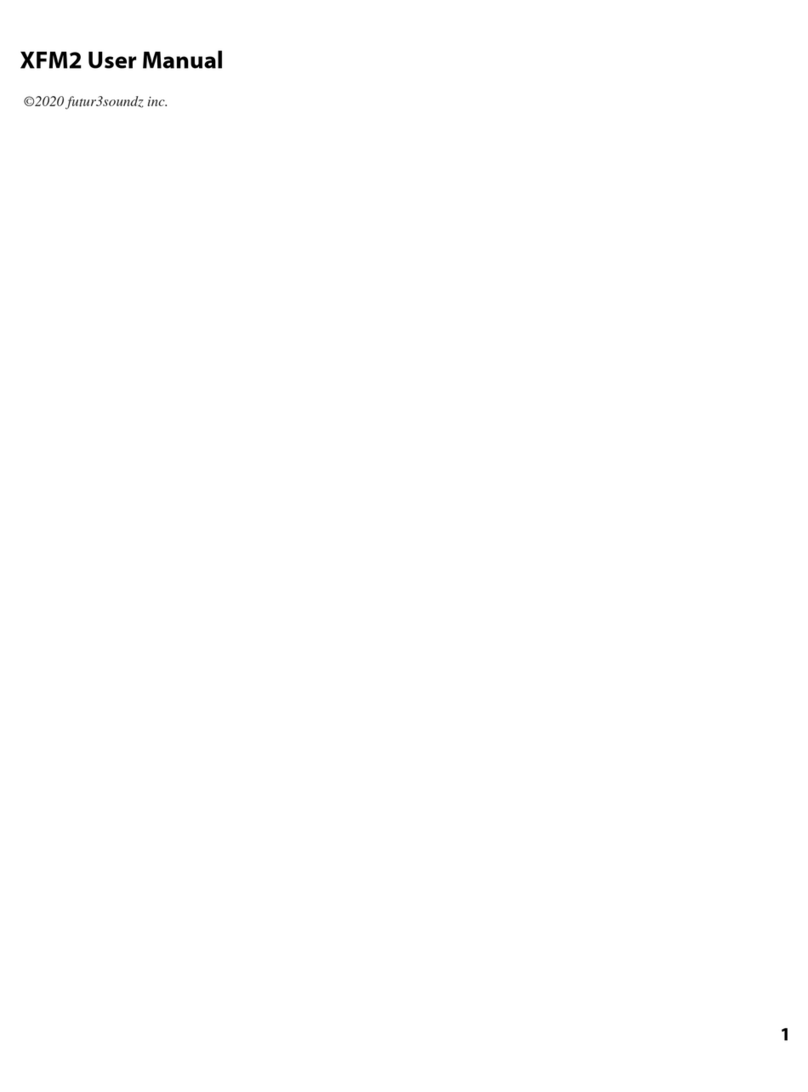
futur3soundz
futur3soundz XFM2 user manual
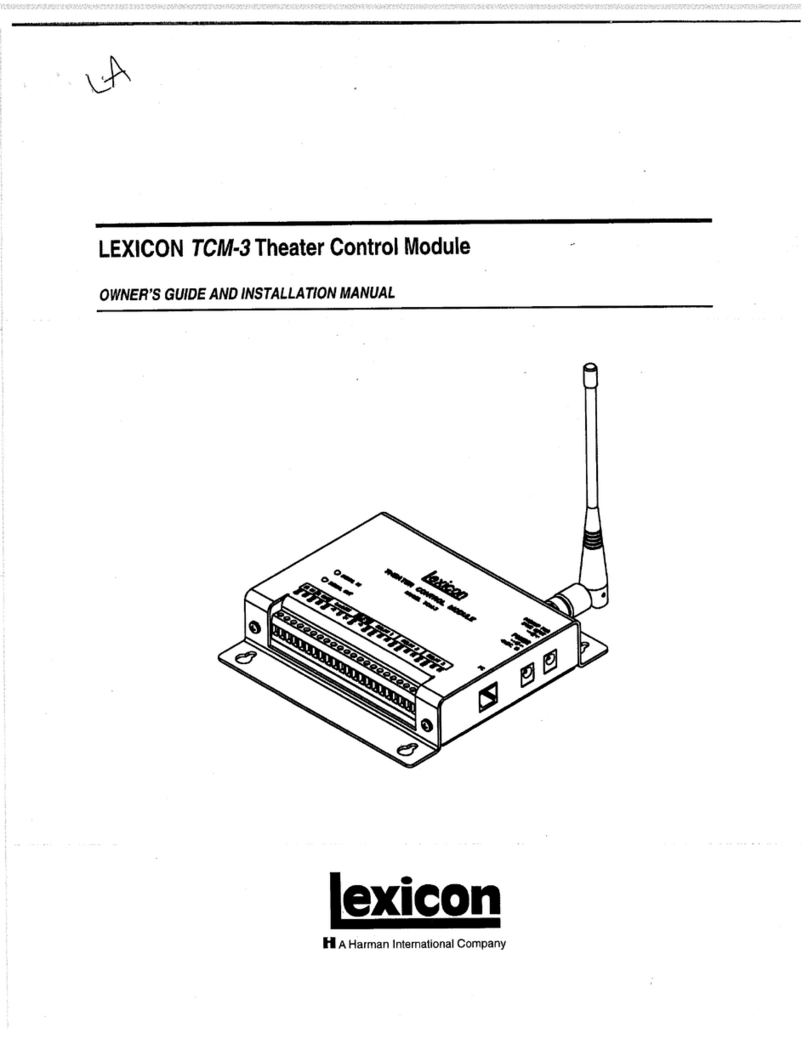
Lexicon
Lexicon TCM-3 Owner's manual and installation guide